Курс лекций для специальности 140104 «Промышленная теплоэнергетика» москва 2011
Вид материала | Курс лекций |
- Курс лекций для специальности 140104 «Промышленная теплоэнергетика» москва 2011, 1206.2kb.
- Курс лекций для студентов специальности 140104 «Промышленная теплоэнергетика» москва, 1244.1kb.
- Курс лекций для студентов специальности 140104 «Промышленная теплоэнергетика» москва, 877kb.
- Курс лекций для студентов специальности 140104 «Промышленная теплоэнергетика», 1246.47kb.
- Рабочая программа для студентов Vкурса по специальности 140104 промышленная теплоэнергетика, 69.12kb.
- Рабочая программа для студентов IV курса специальности 100700 промышленная теплоэнергетика, 243.31kb.
- Рабочая программа для студентов Vкурса специальности 290800. Промышленная теплоэнергетика, 63.46kb.
- Нисаев Игорь Петрович, д т. н., профессор учебно-методический комплекс, 356.38kb.
- Нисаев Игорь Петрович, д т. н., профессор учебно-методический комплекс, 329.37kb.
- Учебно-методический комплекс по дисциплине «экономика» Для студентов специальностей:, 1055.87kb.
8.2. Струйные реакторы с ВЧ-плазмотронами
Применение ВЧ-плазмотронов позволяет перейти к безэлектродным разрядам и снизить скорость потока реакционной смеси до 1–20 м/с, что дает возможность использовать струйные реакторы с ВЧ-плазмотронами для получения особо чистых или химически агрессивных веществ. Корпус реакционной камеры тогда изготовляется из кварцевого стекла с двойными стенками для охлаждения водой или газом. Другим преимуществом ВЧ-плазмотронов является большой ресурс непрерывной работы (до 10 000 ч).
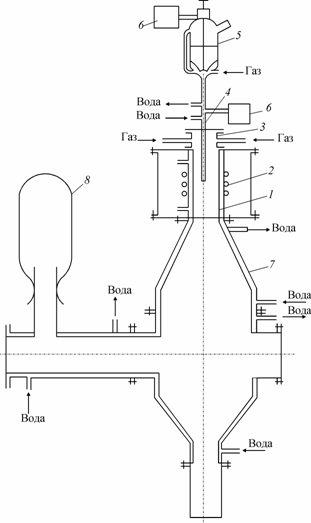
Рис. 8.8. Схема установки с ВЧ-плазмотроном
для получения ультрадисперсного порошка
монооксида кремния:
1 – водоохлаждаемая кварцевая камера ВЧ-плазмотрона
с внутренним диаметром 40 мм; 2 – индуктор; 3 – система подачи плазмообразующего газа (аргон); 4 – водоохлаждаемая трубка
для подачи порошкообразного сырья (SiO2 + Si с размером
частиц менее 40 мкм); 5 – дозатор сырья; 6 – вибратор; 7 – реактор;
8 – рукавный фильтр
Типичные схемы реакторов с ВЧ-плазмотронами представлены на рис. 8.8 (плазмотрон работает на плазмообразующем газе – аргоне – при частоте 20 МГц) и 8.9.
Реакторы с ВЧ-плазмотронами конструктивно имеют следующие особенности:
1) сырье всегда подается в смеси с транспортирующим газом, в качестве которого обычно используют плазмообразующий газ (чтобы не загрязнять реакционную смесь);
2) плазмообразующий газ подают в ВЧ-плазмотрон с помощью специального завихрителя, который направляет струи газа тангенциально вдоль кварцевых стенок плазмотрона и реактора (для их охлаждения и снижения скорости контаминации).
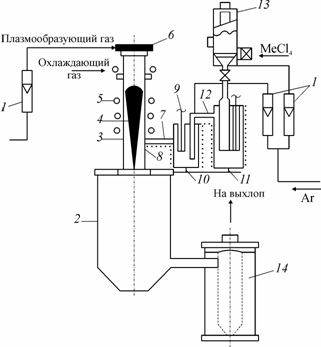
Рис. 8.9. Схема установки для получения порошков оксидов
и нитридов из летучих соединений (хлоридов переходных металлов):
1 – ротаметр; 2 – конденсатор (закалочное устройство); 3 – реактор; 4 – факел плазмы; 5 – индуктор; 6 – газораспределительная головка; 7 – трубка с дополнительным подогревом для транспортирования сырья в виде перегретого пара; 8 – сопло; 9 – термопара; 10 – перегреватель; 11 – переходник; 12 – испаритель; 13 – питатель для жидкого исходного сырья;
14 – рукавный фильтр
8.3. Объемные реакторы
В объемных реакторах характер и направление движения плазменной струи меняются. По общим характеристикам это реакторы идеального смешения. Обычно в объемных реакторах перерабатывается измельченное твердое сырье. Типовые схемы таких реакторов представлены на рис. 8.10–8.12.
Особенностью реакторов объемного типа является то, что принимаются специальные меры для увеличения плазменной области (обычно с помощью вращающегося электромагнитного поля). Недостатком этих реакторов являются высокие тепловые нагрузки на стенки (что требует организации их интенсивного охлаждения) и склонность к зарастанию технологических отверстий реактора конденсирующимися продуктами. Объемные реакторы нашли применение в основном для пирометаллургических процессов.
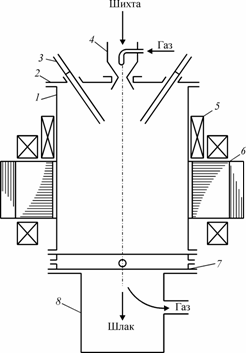
Рис. 8.10. Плазмохимический реактор с объемной зоной тепловыделения:
1 – реакционная камера; 2 – крышка реактора; 3 – стержневые электроды;
4 – распылители; 5 – соленоид; 6 – электромагнит с обмотками;
7 – переходная секция; 8 – шлакосборник
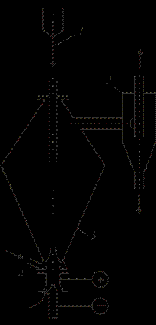
Рис. 8.11. Схема реактора фонтанирующего слоя:
1 – подача сырья; 2 – циклон; 3 – реактор;
4 – подача плазмообразующего газа
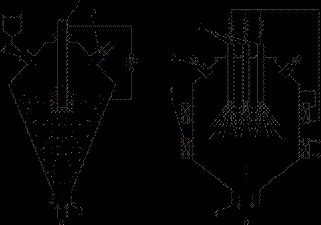
Рис. 8.12. Плазмохимический реактор объемного типа:
а) с ВЧ-разрядом в кипящем слое: 1 – электрод; 2 – отвод отходящих газов с дисперсным продуктом; 3 – ввод плазмообразующего газа; 4 – ввод сырья;
б) с трехфазным плазменно-дуговым разрядом: 1 – фазные электроды; 2 – ввод сырья; 3 – соленоиды; 4 – вывод продуктов реакции
8.4. Расчет исходных данных для проектирования плазмохимического реактора
Разработка исходных требований к реактору состоит из вычисления следующих величин: расхода сырья, теплового эффекта превращения сырья в целевой продукт, количества плазмообразующего и транспортирующего газа, мощности плазмотронов, объема реакторов, количества плазмотронов и реакторов, геометрических параметров реактора, параметров охлаждения реактора, параметров закалочного устройства, параметров плазмотрона (или разрядной трубки). Указанные расчеты базируются на данных задания на проектирование, которые включают в себя:
– состав и свойства исходного сырья (температура подачи сырья, скорость движения в трубопроводе, наличие фазовых переходов);
– температура плазменной струи и состав плазмообразующего газа;
– температура охлаждающей воды (воздуха) – начальная и на выходе;
– давление газов на входе и выходе из реактора;
– состав транспортирующего газа (для порошковых материалов);
– время реакции;
– скорость плазменной струи;
– температура реакции и ее кпд;
– скорость закалки и температура пара газовой смеси после закалки;
– состав продукта и его годовой выпуск;
– время непрерывной работы реактора;
– параметры работы плазмотрона.
На основе опытных данных рекомендуется принимать следующие величины степени превращения сырья в целевой продукт: æ = 0,65 – для производства ацетилена; æ = 0,75 – для производства порошков; æ = 0,28 – для коэффициента использования аммиака в реакциях азотирования; æ = 0,5 – для коэффициента использования азота в реакциях азотирования.
Расчет мощности плазмотрона начинают с вычисления затрат тепла на проведение целевой химческой реакции.
В случае синтеза ультрадисперсных порошков плазмохимическим методом исходные сырьевые компоненты используются в различных агрегатных состояниях, а плазмохимическая реакция происходит в газовой среде с последующей конденсацией твердого порошка при охлаждении. При этом следует учитывать энергию, затрачиваемую на фазовые превращения в сырье (если они происходят внутри реактора – плавление металла, испарение капель жидкого сырья) и на нагрев транспортирующего газа до температуры реакции. Под транспортирующим газом понимают вспомогательную газовую струю, обеспечивающую образование аэрозольного пылевого облака из порошкообразного сырья (эмпирически найденная норма расхода 0,3–0,4 м3/ч на 1 кг порошка). Исходя из необходимой полезной мощности и принятой единичной мощности плазмотрона, находят число плазмотронов и, следовательно, определяют количество реакторов и выделяемую в них мощность. Для обеспечения передачи мощности из плазмотрона в реактор рассчитывают количество плазмообразующего газа (с учетом его энтальпии при температуре реакции). При вычислении объема реактора необходимо учитывать увеличение суммарного объема газов при пиролизе сырья.
Диаметр трубки высокочастотного плазмотрона обычно равен диаметру реактора, который на практике служит ее продолжением. Размеры плазмохимического реактора обычно имеют соотношение: Lр = 10Dр.
Охлаждение стенок реактора можно осуществлять либо водой (αводы= 900 Вт/(м2 · К), скорость водного потока 0,1–0,5 м/с), либо воздухом (αвоздуха= 13 Вт/(м2 · К)), которые принудительно прокачивают между двойными стенками реактора.
Внутренняя стенка реактора с дуговым плазмотроном обычно выполняется из графита (λграф= 140 0,035( Тр – 273)), внешняя стенка реактора выполняется из стали марки ЭИ675Р с толщиной стенки dст = 0,012 м, теплопроводностью λ = 15,1 Вт/(м2 град).
Стенки индукционного плазмотрона выполняются из кварцевого стекла (dcтекла= 0,002; λстекла= 2,05 Вт/(м2 · К)), при этом надо учитывать загрязнения от пыли (dзагр= 0,001; λзагр= 25 Вт/(м2 · К)).
Для торможения реакции разложения целевого продукта после реакционной зоны в плазменную струю с продуктами реакции впрыскивается вода или вдувается газ. Этот участок плазмохимического реактора называется закалочным устройством.
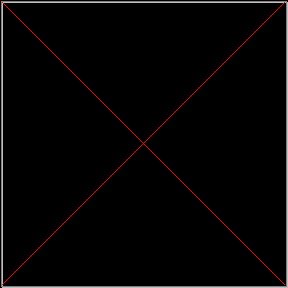
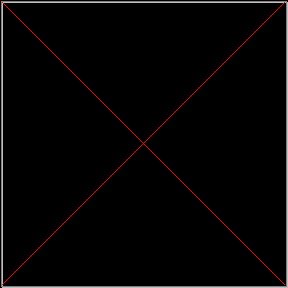
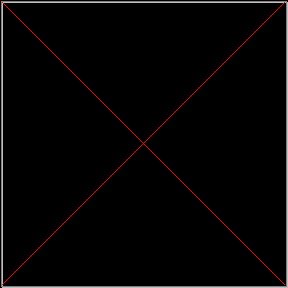