Курс лекций для специальности 140104 «Промышленная теплоэнергетика» москва 2011
Вид материала | Курс лекций |
- Курс лекций для специальности 140104 «Промышленная теплоэнергетика» москва 2011, 1206.2kb.
- Курс лекций для студентов специальности 140104 «Промышленная теплоэнергетика» москва, 1244.1kb.
- Курс лекций для студентов специальности 140104 «Промышленная теплоэнергетика» москва, 877kb.
- Курс лекций для студентов специальности 140104 «Промышленная теплоэнергетика», 1246.47kb.
- Рабочая программа для студентов Vкурса по специальности 140104 промышленная теплоэнергетика, 69.12kb.
- Рабочая программа для студентов IV курса специальности 100700 промышленная теплоэнергетика, 243.31kb.
- Рабочая программа для студентов Vкурса специальности 290800. Промышленная теплоэнергетика, 63.46kb.
- Нисаев Игорь Петрович, д т. н., профессор учебно-методический комплекс, 356.38kb.
- Нисаев Игорь Петрович, д т. н., профессор учебно-методический комплекс, 329.37kb.
- Учебно-методический комплекс по дисциплине «экономика» Для студентов специальностей:, 1055.87kb.
7.6. Печи кипящего слоя и циклонные печи
Для ускорения процесса обжига в последнее время все чаще используют печи кипящего слоя и циклонные печи. В кипящем слое продолжительность обжига исчисляется минутами, во взвешенном состоянии – секундами или долями секунды. Особенностями печей кипящего слоя и циклонных печей являются большая удельная поверхность материала и высокие значения коэффициентов теплоотдачи. Однако, несмотря на неоспоримые преимущества этого типа печей, до сих пор в производстве огнеупоров они не нашли широкого применения. Это связано прежде всего с некоторыми конструктивными и технологическими трудностями. В настоящее время имеется несколько промышленных установок по обжигу извести в кипящем слое.
Для обжига извести в кипящем слое обычно применяют печи с несколькими подовыми решетками, что позволяет наиболее полно использовать тепло газового потока. В печах кипящего слоя получается известь высокого качества. Углекислый кальций при обжиге разлагается почти полностью.
Печь для обжига извести в кипящем слое показана на рис. 7.7. Обжиг огнеупорного сырья происходит при более высоких температурах (1250–1400 °С). При этом может происходить сваривание отдельных зерен обжигаемого материала в крупные куски, которые, выпадая на подовую решетку, нарушают процесс. Более перспективными в этом случае могут являться каскадные печи с фонтанирующим слоем.
Для обжига тонкодисперсных материалов используются циклонные (вихревые) печи. На рис. 7.8, а
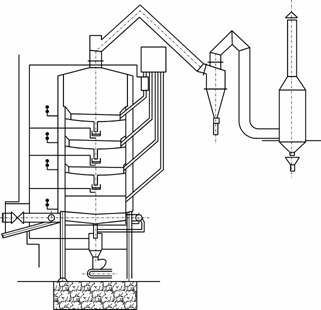
Рис. 7.7. Схема печи для обжига извести в кипящем слое
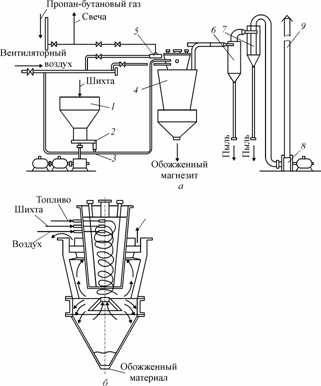
Рис. 7.8. Схема циклонной (вихревой) установки (а)
и вихревая обжиговая печь (б)
показана вихревая установка для обжига каустического магнезита, разработанная ВНИИМТ. Установка состоит из шихтового бункера 1, тарельчатого питателя шихты 2, эжекторного смесителя 3, вихревой обжиговой камеры 4, горелки 5, циклонов НИИОгаз 6, батареи мультициклонов 7, дымососа 8 и дымовой трубы 9.
Вихревая обжиговая печь (рис. 7.8, б) выполнена по типу «камера в камере». Внутренняя (рабочая) камера предназначена для обжига каустического магнезита.
Производительность опытной установки активирующего обжига каустического магнезита 0,85 т/(м3 · час), кпд 80–85 %.
7.7. Принципы расчета при проектировании вращающихся печей
Теплотехнический расчет любой вращающейся печи сводится к следующему:
а) расчет материального баланса;
б) расчет теплового баланса (из теплового баланса определяется удельный расход топлива на обжиг);
в) определение диаметра и длины вращающейся печи при заданной производительности;
г) расчет внутренних теплообменных устройств для печей мокрого способа производства и запечных теплообменников для печей сухого способа производства;
д) расчет горелочных устройств;
е) аэродинамический расчет;
ж) расчет колосникового холодильника.
7.7.1. Материальный баланс
Материальный баланс составляется на один килограмм клинкера.
Теоретический расход сухого сырья, кг/кг:
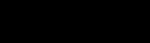
где GТ – расход рабочего твердого топлива, кг/кг;
х – доля присадки золы топлива к клинкеру;

ПППм – потери при прокаливании сырьевой смеси, %.
Теоретический расход гидратной воды, кг/кг:

где

Теоретический расход CaCO3-сырья, кг/кг:
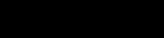
где CaOм – содержание оксида кальция в сухом сырье, кг/кг.
Теоретический расход MgCO3-сырья, кг/кг:

Выход физической воды сырья, кг/кг:
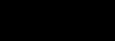
где W – влажность сырьевого шлама.
Расчет материального баланса процесса горения производится по общепринятой методике. В последнее время в практику стала входить упрощенная методика расчета материального баланса процесса горения. В ней расходные коэффициенты связаны с теплотой сгорания топлива, в отличие от общепринятой методики расчета, в которой они связаны с химическим составом топлива.
Поскольку упрощенная методика расчета пока не нашла широкого распространения, целесообразно привести ее в данном Справочнике.
Упрощенная методика представлена в.
Выход продуктов горения и требуемое количество воздуха определяется по следующим формулам.
Выход сухих продуктов горения

где Vспг – теоретический объем сухих продуктов горения при нормальных условиях, м3 /м3 или м3 /кг;

Выход влажных продуктов горения

где V – теоретический объем влажных продуктов горения при нормальных условиях, м3 /м3 или м3 /кг.
Выход водяных паров


где

Выход RO2:
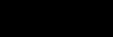
где


Количество воздуха для горения
Vв = α

где Vв – объем воздуха для горения при нормальных условиях, м3/м3 или м3/кг;
α – коэффициент избытка воздуха.
Значения коэффициентов в формулах приведены в табл. 7.5.
Таблица 6.5 Значения расчетных коэффициентов для материального баланса
|
7.7.2. Тепловой баланс
В тепловом балансе следует отметить две статьи расхода.
Расход тепла Qрасх:
– тепловой эффект процесса клинкерообразования. Этот эффект равен количеству тепла, необходимого для того, чтобы из сухого сырья с температурой 0 0С получить без материальных и тепловых потерь 1 кг клинкера с температурой 0 0С;
– потери тепла с охлаждающими топливными газами.
Тепловой эффект клинкерообразования.
Расход тепла:
– на дегидратацию qдег = 1600[

– на декарбонизацию CaCO3


– на декарбонизацию MgCO3


Расход тепла на образование жидкой фазы принимается 50 ккал/кг (перевод в СИ: 1 кал = 4,19 Дж).
Приход тепла Qпр:
– экзотермический эффект образования клинкерных минералов – qкл.о.
Минералогический состав клинкера рассчитывается по формулам:
C4AF = 3,04Fe2O3;
C3A = 2,65 Al2O3 – 1,69Fe2O3;
C3S = 4,07CaO – 7,6 SiO2 – 6,72 Al2O3 – 1,43 Fe2O3;
C2S = 8,6 SiO2 – 3,07 CaO + 5,1 Al2O3 + 1,08 Fe2O3;
qкл.мин = 0,01(126 C3S + 171 C2S + 14,5 C3A + 26 C4AF).
Приход тепла от застывания жидкой фазы qз.жф принимается 28 ккал/кг:
qкл.о = Qрасх – Qпр.
Тепловой эффект клинкерообразования можно рассчитать и по упрощенной формуле
Q к.об = 7,64 CaO + 6,7 MgO + 4,11 Al2O3 – 5,11 SiO2 – 0,59 Fe2O3 – 22.
Таблица 7.6 Значения расчетных коэффициентов для теплового баланса
|
Потери тепла с отходящими топливными газами по упрощенной методике рассчитываются следующим образом.
Располагая материальным балансом, можно определить водяное число (VC) продуктов горения, суммируя произведение объемной доли каждого компонента на соответствующую теплоемкость.
Например, при температуре 400 оС водяное число (VC) продуктов горения природного газа составит:
(VC)400 = [0,12 · 0,4628 + 0,88 · 0,3143 + 0,22 · 0,3739 + 1,11( – 1) 0,3235]


В общем виде формула для расчета водяного числа продуктов горения может быть записана в виде:
(VC)t = (a + b)

Значения коэффициентов a и b для различных видов топлива приведены в табл. 7.6.
7.7.3. Определение конструктивных параметров вращающихся печей мокрого способа производства
В подготовительных зонах вращающейся печи вплоть до зоны спекания скорость обжига определяется интенсивностью теплообмена, поэтому длина этих зон определяется следующей формулой:
Lп =

где G – производительность печи, кг/ч;
qм – удельное количество тепла, переданного материалу, ккал/кг;
α – коэффициент теплопередачи, ккал/м2час оС;
T – среднелогарифмическая разность температур между газовым потоком и материалом, оС;
F – поверхность теплообмена, м2.
Существует методика позонного расчета вращающейся печи, основанная на применении общих законов теплопередачи. Однако она не нашла широкого применения в расчетной практике, т. к. принятые в ней допущения о структуре движущегося слоя, законах передачи тепла внутри него, а также запыленности газового потока, определяющего степень его черноты, и ряд других допущений не позволяют получить удовлетворительную для практики точность расчета.
В связи с этим при расчете вращающихся печей используются в основном статистические зависимости между определяющими величинами, полученные при обработке эксплуатационных данных и теплотехнических испытаний.
Существует несколько методик, используемых для расчета вращающихся печей: Е. И. Ходорова, Д. Я. Мазурова и А. З. Кисельгофа. Наибольшее применение нашла методика Е. И. Ходорова.
7.7.4. Методика расчета Е.И. Ходорова
Для вращающихся печей с внутренними теплообменными устройствами при мокром способе производства тепловая мощность печи Q определяется по формуле:
Q = 2,4D2,5 или D =

где Q – тепловая мощность, млн ккал/ч;
D – внутренний диаметр печи, м.
Поскольку тепловая мощность проектируемой печи задана, то известен и диаметр печи. При этом, в соответствии с формулой (6.1), удельное теплонапряжение сечения зоны горения qF (ккал/(м3 · ч)) пропорционально D0,5, а объемное теплонапряжение (ккал/(м3 · ч)) пропорционально D–0,5.
Для определения поверхности теплообмена, а следовательно, и длины печи, используется опытная зависимость, которая выражает отношение количества тепла, отданного в печи, к количеству выделенного в ней тепла как функцию двух величин:
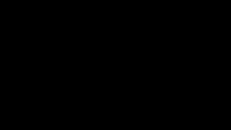
где q – тепло, выделенное топливом, ккал/кг;
qв –тепло воздуха, нагретого за счет охлаждения клинкера от максимальной температуры до температуры, с которой он выходит из холодильника, ккал/кг;
ψ – опытная величина;
Q – тепловая мощность печи, ккал/ч;
σ – коэффициент излучения абсолютно черного тела, ккал/(м2 · ч · К4);
T – теоретическая температура горения, К;
ω – скорость газов в зоне сушки, нм3/(м2 · сек);
Fп – общая поверхность печи, м2.
Из расчета цепной завесы известны суммарная поверхность цепей и футеровки и длина этой зоны. Вычитая из общей поверхности печи поверхность цепной завесы, получаем поверхность и длину полой части печи.
Длина зоны спекания определяется исходя из длительности пребывания материала, необходимой для завершения физико-химических процессов формирования цементного клинкера.
На основании опытных данных о работе вращающихся печей для обеспечения необходимого времени пребывания материала в зоне должно соблюдаться условие:
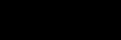
где Вкл – производительность печи, т/ч;
Dп – внутренний диаметр печи, м.
Как правило, при расчете вращающихся печей это условие соблюдается. В противном случае необходимо уменьшить расчетную производительность печи.
7.7.5. Определение конструктивных параметров вращающейся печи с циклонными теплообменниками
При проектировании печей для обжига клинкера по сухому способу производительность печи принимается в соответствии с паспортными данными завода-изготовителя. Отечественная промышленность выпускает следующие типоразмеры печей для сухого способа производства:
4,0 60 с циклонными теплообменниками производительностью 35 т/ч;
5,0 75 с циклонными теплообменниками производительностью 75 т/ч;
4,5 80 с циклонными теплообменниками и декарбонизатором производительностью 125 т/ч.
В цементной промышленности производится реконструкция печей мокрого способа с переводом их на сухой способ производства.
Реконструкция состоит в том, что длинная печь укорачивается и к ней пристраивается система циклонных теплообменников с декарбонизатором.
В этом случае известен диаметр печи, но неизвестны ее производительность и длина. Эти параметры определяются расчетом по приводимым ниже методикам.
Тепловая мощность печи определяется по формуле:
Q = 1,5 Dп2,5 или D =

По заданной тепловой мощности определяется диаметр печи.
Поверхность теплообмена определяется по формуле:
ηтеп = 0,124

Обозначения те же, что и для печей мокрого способа.
По известной поверхности определяется длина печи.
Для печи с циклонными теплообменниками также должно соблюдаться условие (7.1).
Для печей с декарбонизаторами это условие снимается.