Курс лекций для специальности 140104 «Промышленная теплоэнергетика» москва 2011
Вид материала | Курс лекций |
- Курс лекций для специальности 140104 «Промышленная теплоэнергетика» москва 2011, 1206.2kb.
- Курс лекций для студентов специальности 140104 «Промышленная теплоэнергетика» москва, 1244.1kb.
- Курс лекций для студентов специальности 140104 «Промышленная теплоэнергетика» москва, 877kb.
- Курс лекций для студентов специальности 140104 «Промышленная теплоэнергетика», 1246.47kb.
- Рабочая программа для студентов Vкурса по специальности 140104 промышленная теплоэнергетика, 69.12kb.
- Рабочая программа для студентов IV курса специальности 100700 промышленная теплоэнергетика, 243.31kb.
- Рабочая программа для студентов Vкурса специальности 290800. Промышленная теплоэнергетика, 63.46kb.
- Нисаев Игорь Петрович, д т. н., профессор учебно-методический комплекс, 356.38kb.
- Нисаев Игорь Петрович, д т. н., профессор учебно-методический комплекс, 329.37kb.
- Учебно-методический комплекс по дисциплине «экономика» Для студентов специальностей:, 1055.87kb.
7.7.6. Принципы расчета циклонных теплообменников и декарбонизаторов
Отдача тепла горячими газами мелкодисперсному материалу в циклонном теплообменнике происходит весьма интенсивно, вследствие чего теплообмен не ограничивает скорость протекания процессов, происходящих в циклонах. Поэтому теплообмен в циклонных теплообменниках не рассчитывается, а необходимые данные для определения размеров циклонов и газоходов определяются на основе материального и теплового балансов как установки в целом, так и отдельных ее элементов, а также в результате аэродинамических расчетов.
При составлении материальных и тепловых балансов принимаются следующие исходные данные, которые дополняют данные, обычно принимаемые для составления материальных и тепловых балансов:
– η – значения коэффициентов пылеосаждения циклонов η(Iст) = 0,80, η(IIст) = 0,85, η(IIIст) = 0,90, η(IVст) = 0,95;
– коэффициент избытка воздуха: за циклоном Iст – 1,15; IIст – 1,2; IIIст – 1,25; IVст – 1,35;
– степень декарбонизации в декарбонизаторе 45 %;
– степень декарбонизации материала, поступающего в печь, – 90 %;
– температура пылегазового потока на выходе из декарбонизатора – 950 0С;
– температура пылегазового потока на выходе из системы (за IV ступенью теплообменников) – 350 0С.
Скорости в газоходах принимаются в пределах 19–21 м/с, а во входных патрубках циклонов 20–22 м/с.
В результате проведенных расчетов по ступеням циклонов определяются:
– количество материала, проходящего по системе циклонного теплообменника;
– количество газов и их запыленность;
– температура пылегазового потока.
Конструктивные размеры элементов циклонного теплообменника определяются на основе зависимостей, полученных в результате эксплуатации и испытаний вращающихся печей с циклонными теплообменниками.
Диаметр цилиндрической части циклона в свету определяется по формуле

где Vог – секундный расход газов, поступающих в циклон, м3/с;
kвх =

где Fвх – сечение входного патрубка, м2;
Fу – сечение цилиндрической части циклона, м2;
v – входная скорость газов, м/с.
Высота цилиндрической части циклона
Hц = (0,5 – 0,6)Dц, м.
Декарбонизатор рассчитывается по нормированному тепловому напряжению, которое в среднем составляет 800 000 ккал/(м3 ч).
Соотношение

7.7.7. Принципы расчета вращающихся печей для производства извести и керамзита
Для производства извести по мокрому способу применяются вращающиеся печи, выпускаемые отечественной промышленностью для обжига цементного клинкера, поэтому конструктивные размеры вращающихся печей для производства извести определяются по методике расчета печей для обжига цементного клинкера, т. е. диаметр печи определяется по формуле
Q = 2,4 D2,5. (7.6)
Для производства извести по сухому способу, когда обжигается дробленный известняк, применяются вращающиеся печи с запечными теплообменниками (конвейерные решетки, котлы-утилизаторы).
Для определения конструктивных размеров таких печей, а также вращающихся печей для обжига керамзита следует использовать следующие соотношения:

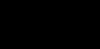
где Q – тепловая мощность печи, млн ккал/ч;
D – диаметр печи, м;
Рф – удельный съем клинкера с единицы поверхности печи, кг/(м2 · ч).
Индексом «1» обозначены параметры печи, принятой в качестве аналога, индексом «2» – проектируемой печи.
В качестве аналога принимается ближайшая по размеру вращающаяся печь.
8. Общие принципы работы и классификация плазмохимических реакторов
Плазмохимические реакторы используют для производства газообразных продуктов (ацетилена, оксида азота, дициана, фторуглеродов и т. п.) и порошков функционального назначения (например, пигментного диоксида титана, ультрадисперсного нитрида титана, нитрида кремния и т. п.). Эффективность использования плазмохимического процесса для получения таких продуктов обусловлена механизмом и кинетикой химических и фазовых превращений при высоких температурах, а также возможностью введения энергии непосредственно в реакционный объем.
В плазмохимических реакторах в качестве теплоносителя используется низкотемпературная плазма (с энергией до 10 эВ, что соответствует температуре ~11 200 К). Процессы в низкотемпературной плазме особенно перспективны для промышленной реализации химических реакций, у которых:
1) равновесие смещено в сторону высоких температур;
2) скорости резко возрастают с повышением температуры (продолжительность контакта сырья с теплоносителем в таких реакторах обычно ~10–3–10–5 с). С этим связана значительная миниатюризация реакторных устройств (например, плазмохимический реактор пиролиза метана производительностью по целевому продукту – ацетилену 0,9 кг/с имеет длину 65 см и диаметр ~15 см);
3) высокие выходы целевого продукта достигаются в существенно неравновесных условиях;
4) используется широкодоступное, малоценное, неустойчивое по составу сырье (например, в плазмохимическом пиролизе природного газа примеси к метану до 20–25 % не влияют на выход целевых продуктов);
5) для получения чистых и высокочистых (например, полупроводниковых) материалов, т. к. в плазмохимических процессах в ВЧ- и СВЧ-плазме чистота продуктов определяется только чистотой исходного сырья и даже может быть повышена в ходе процесса.
Так как плазмохимические реакции являются многоканальными (получение целевого продукта – лишь один из возможных каналов взаимодействия), то коэффициент выхода полезного продукта находится обычно в интервале 0,15–0,75 от теоретически возможного.
Схема типового плазмохимического реактора представлена на рис. 8.1.
При выборе плазмохимических реакторов следует учитывать, что:
1) подавляющее большинство представляющих практический интерес плазмохимических процессов с технологической точки зрения одностадийны;
2) плазмохимические процессы хорошо моделируются, оптимизируются и управляются;
3) управление низкотемпературной плазмой может быть осуществлено газо- и электродинамическими методами, применение которых позволяет снизить требования к конструкционным материалам плазмотрона и реактора.
Для получения плазмы используются специальные устройства – плазмотроны. Плазмотроны делятся по способу зажигания разряда в газовой среде на дуговые (работают на постоянном токе или токе промышленной частоты) и безэлектродные – высокочастотные. Электродуговые плазмотроны имеют мощность от 25 кВт до 10 МВт и выпускаются как серийно, так и в виде образцов, спроектированных специально для конкретного плазмохимического реактора. Дуговые плазмотроны работают обычно при давлениях 0,1–5 МПа, материалом катода в них служит либо вольфрам, либо графит (материал катода определяет атмосферу в реакторе и возможные загрязнения продукта). Высокочастотные (ВЧ) плазмотроны в свою очередь делятся на индукционные (ВЧИ), емкостные (ВЧЕ) и сверхвысокочастотные (СВЧ). ВЧ-плазмотроны работают в диапазоне частот 0,2–40 МГц, мощности разряда 0,2 кВт–3 МВт, расходе плазмообразующего газа до 0,3 кг/c. Главная особенность ВЧ-плазмотрона – отсутствие загрязняющих веществ при образовании плазмы (разряд безэлектродный), широкие возможности в выборе плазмообразующего газа и высокий ресурс работы.
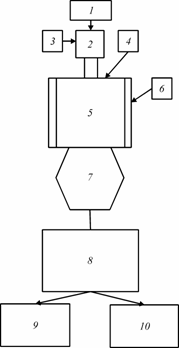
Рис. 8.1. Структурная схема плазмохимического реактора:
1 – источник электропитания; 2 – плазмотрон; 3 – плазмообразующий газ; 4 – сырье; 5 – смесительное устройство и реакционная камера; 6 – система охлаждения стенок реакционной камеры; 7 – закалочное устройство (система принудительного охлаждения продуктов реакции); 8 – блок разделения продуктов реакции; 9 – целевой продукт; 10 – побочные продукты
Энергетические возможности плазмотрона и, соответственно, плазмохимического реактора в первую очередь определяются плазмообразующим газом (см. рис. 8.2). Выбор плазмообразующего газа определяется его химическими и энергетическими характеристиками. Так как сложные газообразные соединения диссоциируют при плазменных температурах, реальный выбор плазмообразующего газа обычно невелик и сводится к элементарным газам.
К плазмотронам предъявляются следующие требования:
– обеспечение заданной (технологией целевого продукта) температуры плазмы;
– обеспечение достаточной для заданной производительности тепловой мощности;
– стабильные и регулируемые в широком диапазоне расход плазмообразующего газа и его температура;
– приемлемый по экономическим соображениям электрический и тепловой кпд;
– заданный ресурс непрерывной работы;
– минимум загрязнений реакционного пространства продуктами эрозии материалов плазмотрона.
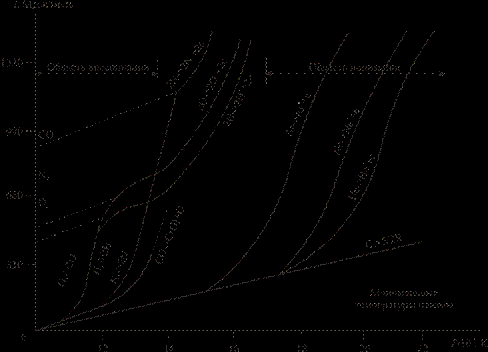
Рис. 8.2. Зависимость удельной энтальпии для различных газов от температуры
В плазмохимических реакторах подача энергоносителя (плазмы) и сырья производятся, как правило, раздельно. Смешение энергоносителя и сырья в этом случае имеет ряд особенностей:
1) плазменная струя имеет высокую температуру, компоненты плазмы диссоциированы, по плазменной струе наблюдаются высокие градиенты температуры (осевые градиенты температур до 400 К/мм, радиальные до 5000 К/мм);
2) смешение происходит в неизотермических (плазма имеет температуру около 3000 К, а сырье 300 К) условиях (в результате плотности компонентов значительно различаются);
3) процесс смешения сопровождается эндотермической реакцией, время протекания которой сопоставимо со временем смешения;
4) смешению сопутствуют различные рекомбинационные процессы со значительным энергетическим выходом.
По характеру перемешивания плазмохимические реакторы делятся на две группы: струйные и объемные. В струйных реакторах характер и направление движения плазменного потока в основном сохраняются и после смешения с сырьем (реактор идеального вытеснения). Струйные реакторы чаще всего используют для проведения гомогенных процессов. В объемных реакторах происходит резкое изменение всех параметров движения плазменной струи. Эти реакторы чаще всего соответствуют по свойствам реакторам идеального смешения. Объемные ректоры используются для проведения гетерогенных процессов. Принадлежность конкретного реактора к тому или иному типу можно определить по критерию перемешивания:
Kп = =

где Lp – длина реактора;
Dэф – эффективный коэффициент массообмена;
W – скорость химической реакции; С0 – исходная концентрация реагента.
При Kп 1 режим потоков в реакторе близок к режиму идеального перемешивания, а при Kп 1 – к режиму реактора идеального вытеснения. Основное конструктивное отличие плазмохимических реакторов от обычных реакторов идеального вытеснения заключается в использовании интенсивного принудительного охлаждения стенок, что приводит к значительным радиальным градиентам скорости потока. В результате скорость превращения сырья в целевой продукт снижается, и для компенсации требуется увеличение длины реактора. Однако такое решение приводит к снижению селективности реактора по отношению к побочным продуктам. Таким образом, требуются конструктивные решения, обеспечивающие защиту от теплового разрушения стенок реактора и минимизацию радиальных градиентов температуры. Второе отличие плазмохимических реакторов – турбулентная диффузия по оси реактора. Интенсивность смешения струй плазмы и сырья зависит от следующих факторов: характера линейного размера (калибр) и формы устьев струй, угла атаки струй, характеристики турбулентности струй, относительного шага между струями, отношения скоростных напоров струй, отношения диаметров устьев струй.
По способу ввода сырья струйные реакторы делятся на: спутные, с вводом сырья в поперечном потоке, спутно-вихревые и встречно-вихревые. Для характеристики соударяющихся струй используют критерий «гидродинамический параметр»:
q =

где – плотность газа; W – скорость потока; индекс «1» – плазменная струя; индекс «2» – холодное сырье.
Дальнобойность поперечной струи (расстояние в радиальном направлении, на котором струя повернется на 90) может быть рассчитана по эмпирическому уравнению:
h = 2,48d0q0,26,
а расстояние по оси, на котором струя развернется параллельно потоку:
y = 7,5d0q0,2
(d0 – диаметр струи в начальном состоянии). Сырье обычно вводится струями малого диаметра радиально (см. рис. 8.3). Смешение в поперечном потоке существенно улучшается с ростом гидродинамического параметра q (полное смешение на расстоянии менее 5 калибров при q = 100 и 3 калибров при q > 200).
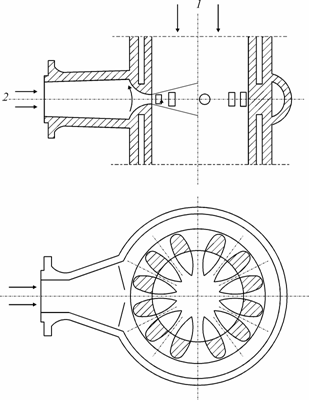
Рис. 8.3. Схема смесительной камеры плазмохимического
реактора с многоструйной поперечной подачей сырья (2)
в поток плазмы (1)
8.1. Струйные реакторы с электродуговыми плазмотронами
Для промышленных реакторов с электродуговыми плазмотронами обычно применяют ввод плазмы из нескольких плазмотронов (для создания агрегатов большой единичной мощности применяют подачу нескольких плазменных струй поперек потока сырья – см. рис. 8.4). Угол атаки плазменной струи потока сырья обычно делают менее 90 (чаще всего – 30).
Исторически первым плазмохимическим производством был пиролиз углеводородов с целью получения ацетилена, этилена и других продуктов (1940 г., Германия, завод в г. Хюльс; 1963 г., США, фирма «Дюпон де Немур»). В качестве плазмообразующего в плазменных реакторах этих фирм обычно используется природный газ.
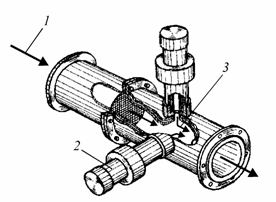
Рис. 8.4. Схема многодуговой камеры смешения плазмохимического реактора:
1 – сырье, 2 – плазмотрон, 3 – плазменная струя
Реактор фирмы «Хюльс» (см. рис. 8.5, а) имеет мощность 8200 кВт. Агрегат включает в себя два электродуговых реактора: работающий и резервный. Газ, подлежащий превращению, входит тангенциально в камеру 3 высотой 478 мм, диаметром 785 мм и поступает в трубчатый водоохлаждаемый анод 4 длиной 1,5 м, диаметром 85–105 мм. Дуга, общая длина которой ~1 м, горит между водоохлаждаемым колоколообразным катодом 1 и анодом 4, захватывая 40–50 см длины последнего. Поджиг дуги осуществляется с помощью пускового устройства 5. Между анодом и катодом установлен керамический изолятор 2. Напряжение на дуге 7 кВ, ток 1150 А. Закалку осуществляют двухступенчато – путем ввода углеводородов (900 кг/ч) в точке, где температура ~1770 К, и впрыском воды на выходе из реактора. Время реакции ~2 мкс, скорость газа ~1000 м/с. Электроды изготовлены из стали, ресурс работы анода ~150 ч, катода ~800 ч. Принимаются специальные меры для предотвращения закоксовывания электродов, поскольку такие отложения влияют на стабильность дуги. В качестве сырья используются: нефтезаводской газ, сжиженный нефтяной газ (С3, С4), легкие и тяжелые нефтяные фракции различного происхождения, природный газ, продукты рециркуляции. Товарными продуктами процесса являются: ацетилен, этилен, водород, циановодородная (синильная) кислота, диацетилен, сажа, которые последовательно разделяются
в блоке специальных установок.
Электродуговой реактор фирмы «Дюпон де Немур» (рис. 8.5, б) производительностью 22 000 т ацетилена в год введен в строй в 1963 г. В реакторе этой фирмы дуга постоянного тока 3100 А и напряжением 3500 В горит между расходуемым угольным катодом 1 и водоохлаждаемым анодом 2. Анод окружен электромагнитом 3, вращающим дугу со скоростью 7000 с–1. В нижней части реактора установлено приспособление для подачи воды на закалку. Рабочее давление 0,05 МПа. Сырье – жидкие углеводороды (бутановые фракции или газойль). Отложения сажи периодически удаляются с анода с помощью механического устройства.
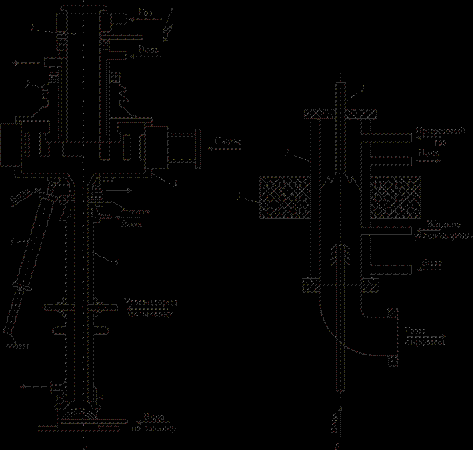
Рис. 8.5. Схема электродуговых реакторов пиролиза углеводородов фирмы «Хюльс» (а) и фирмы «Дюпон де Немур» (б)
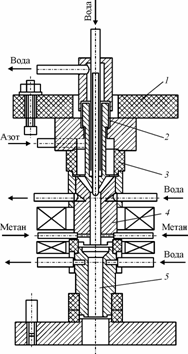
Рис. 8.6. Схема плазмохимического реактора для
синтеза газообразных продуктов из газообразного сырья:
1 – монтажные диэлектрические шайбы; 2 – изолятор; 3 – катод;
4 – анод; 5 – реакционный канал
Схема отечественного плазмохимического реактора для синтеза смеси ацетилена и цианистого водорода показана на рис. 8.6. В этом реакторе в качестве плазмообразующего газа используется азот, в качестве углеродсодержащего сырья – метан.
Для организации плазмохимического технологического процесса реактор должен быть соединен технологическими трактами с системой подготовки и подачи плазмообразующих газов, системой подготовки и подачи исходного сырья, блоком электропитания, блоком разделения и очистки продуктов реакции, системой датчиков и исполнительных механизмов для управления. Рис. 8.7 иллюстрирует такой технологический модуль на базе трехструйного плазмохимического реактора.
Для генерация плазменного потока в модуле ЦПТ СибГГМА используются три электродуговых плазмотрона ЭДП-104А мощностью до 50 кВт каждый, установленные в камере смешения под углом 30 к оси реактора. Камера смешения соединена с секционированным водоохлаждаемым каналом реакционной камеры (с внутренним диаметром 0,046 м). Для подачи в реактор дисперсного сырья используется устройство для дозирования порошково-газовой смеси ДП-1, обеспечивающее стабильность подачи в пределах ±2 %. Образующаяся в дозаторе пылегазовая взвесь вводится по оси реактора в зону соударения истекающих из плазмотрона высокотемпературных газовых струй с помощью установленной в камере смешения водоохлаждаемой фурмы. Скорость ввода порошка в реактор при постоянном расходе транспортирующего газа регулируется изменением внутреннего диаметра фурмы с помощью насадок.
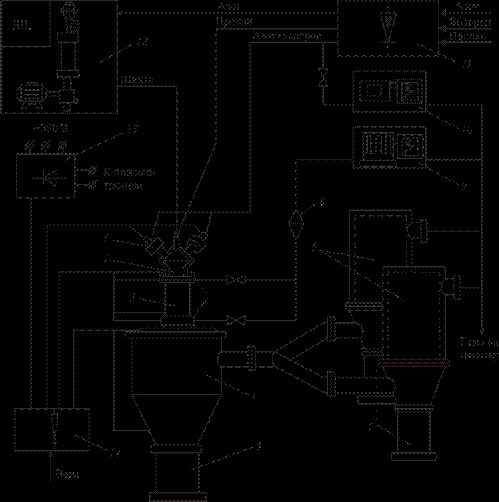
Рис. 8.7. Схема плазмохимического модуля Центра порошковых технологий СибГМА для восстановительного синтеза порошков карбидов, боридов и их композиций:
1 – плазмотроны ЭДП-104А; 2 – камера смешения; 3 – секция реактора; 4 – осадительная камера; 5 – бункеры-накопители; 6 – рукавные фильтры; 7 – фильтр тонкой очистки; 8 – зонды для отбора проб; 9 – хроматограф ЛХМ-8МД (ЦВЕТ-101); 10 – газоанализатор ЦИРКОН-М; 11 – система газоснабжения; 12 – порошковый дозатор; 13 – блок питания плазмотронов; 14 – система водоснабжения
Фурма используется также для подачи в реактор газообразного восстановителя. Для закалки обработанных в плазме материалов применяется закалочное кольцо, устанавливаемое на выходе из реактора и выполненное в виде полой металлической шайбы толщиной 0,008 м с внутренним диаметром 0,046 м, по которому равномерно расположены четыре отверстия диаметром 0,001 м для подачи в реактор холодного газа (азота). Конденсированные продукты обработки, выносимые из реактора отходящими газами, улавливаются в осадительной камере и в двух рукавных фильтрах. В качестве фильтрующей ткани используется нержавеющая сетка саржевого плетения. Площадь поверхности осаждения в камере 1 м2, а в рукавных фильтрах – 3 м2, что обеспечивает скорость фильтрования в пределах 0,001–0,002 м3/(м2 · с). При необходимости пылегазовый поток охлаждают до рабочей температуры фильтров (800–900 К) в теплообменнике ТК с площадью поверхности 1 м2.
Вода для охлаждения блока питания, балластных сопротивлений, катодов и анодов плазмотронов, реактора и осадительной камеры подается под давлением 3 · 105 Па. Расход воды регулируется с помощью расходомеров типа РСС-5 и РСС-7. Общий расход воды на охлаждение реактора и вспомогательного оборудования составляет 2,5 м3/ч.
Электродуговые плазмотроны обеспечивают скорость плазменного потока (а следовательно, реакционной смеси) от 300 до 1000 м/с, что усложняет работу блоков разделения и очистки как в циклонах, так и в рукавных и электрофильтрах. Кроме того, получаемые вещества зачастую загрязнены продуктами эрозии катода и материалами стенок технологического тракта.