Курс лекций для специальности 140104 «Промышленная теплоэнергетика» москва 2011
Вид материала | Курс лекций |
- Курс лекций для специальности 140104 «Промышленная теплоэнергетика» москва 2011, 1206.2kb.
- Курс лекций для студентов специальности 140104 «Промышленная теплоэнергетика» москва, 1244.1kb.
- Курс лекций для студентов специальности 140104 «Промышленная теплоэнергетика» москва, 877kb.
- Курс лекций для студентов специальности 140104 «Промышленная теплоэнергетика», 1246.47kb.
- Рабочая программа для студентов Vкурса по специальности 140104 промышленная теплоэнергетика, 69.12kb.
- Рабочая программа для студентов IV курса специальности 100700 промышленная теплоэнергетика, 243.31kb.
- Рабочая программа для студентов Vкурса специальности 290800. Промышленная теплоэнергетика, 63.46kb.
- Нисаев Игорь Петрович, д т. н., профессор учебно-методический комплекс, 356.38kb.
- Нисаев Игорь Петрович, д т. н., профессор учебно-методический комплекс, 329.37kb.
- Учебно-методический комплекс по дисциплине «экономика» Для студентов специальностей:, 1055.87kb.
6.6. Печи графитации
Печи графитации (графитировочные печи) относятся к группе электрических однофазных печей сопротивления прямого нагрева. В настоящее время в промышленности используются две характерные конструкции печей графитации: нормальные (прямые) (или печи Ачесона) и П-образные печи. Наибольшее распространение получили нормальные прямые печи, которые различаются по конструктивному оформлению токоподводящего пакета, пода, способу охлаждения печи и т. д. П-образная печь представляет собой две нормальные печи, расположенные рядом и последовательно соединенные. Нормальные печи работают как на переменном, так и на постоянном токе, П-образные печи применяются только на мощных установках, работающих на постоянном токе.
На рисунке 6.7 показана конструкция нормальной прямой печи графитации. Печь имеет прочное основание в форме прямоугольного корыта 1 и две торцевые стенки 2. В торцевых стенках созданы проемы для укладки токоподводящих электродных пакетов 3, к которым подводится электрический ток от мощных источников. В основание печи (корыто) набивают специальную подину, состоящую из смеси порошкообразных углеродистых материалов и песка. На подготовленную подину загружают изделия (например, электроды) 4, подвергающиеся графитации. Боковые стенки 5 служат для того, чтобы удержать загрузку печи. Эти стенки разборные, их каждую кампанию разбирают и собирают. Используются также печи с неразборными или с одной неразборной стенкой (в зависимости от удобства обслуживания печи при разгрузке и загрузке). Боковые стенки выкладывают из шамотного кирпича (для печей малых размеров) или из блоков жаропрочного бетона для больших печей.
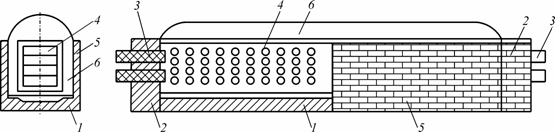
Рис. 6.7. Графитировочная печь нормальная прямая:
1 – подина; 2 – торцевая стенка; 3 – токоподводящие электроды;
4 – заготовки; 5 – боковые стенки; 6 –теплоизоляционная шихта
Электрическая энергия подводится к рабочему объему (керну) при помощи электродов. Токоподводящие электроды, заделанные в торцевую стенку, называют электродным пакетом. Сила тока в современных печах достигает нескольких десятков тысяч ампер, поэтому электродный пакет должен быть составлен из такого числа электродов, чтобы общее их сечение удовлетворяло требованиям по допустимой плотности тока. Чаще всего используются графитированные электроды, т. к. они обладают высокой электропроводимостью и допускают высокие плотности тока (до 12 А/см2). Токопроводящие электроды являются одновременно проводниками электрического тока в печь и проводниками теплоты, идущей из печи, поэтому их орошают водой и устанавливают под небольшим углом, чтобы вода не затекала в стенку. Размеры печи графитации зависят от величины загрузки, а также от геометрических размеров графитируемых изделий. Ниже приведены данные по длине керна и мощности графитировочных печей (табл. 6.4).
Таблица 6.4 Характеристики графитировочных печей
|
В промышленной практике печи графитации длиннее 20 м (по керну) не строят.
6.7. О режимах работы руднотермических печей
Эффективность работы руднотермических печей, в которых протекает химическая реакция между компонентами, один из которых находится в твердой фазе, а другой в виде жидкого расплава, образовавшегося
в печи в результате плавления исходного твердого сырья, в настоящее время оценивается показателями, характерными для аппаратов непрерывного действия: производительностью по готовому продукту, расходом сырья, потребляемой мощностью и др. Расчеты печей обычно проводятся на основании балансовых уравнений либо дифференциальных уравнений, содержащих только стационарные составляющие, ссылаясь на длительность переходных процессов, протекающих в печи.
Однако опыт эксплуатации руднотермических печей указывает на значительные колебания режимных параметров, что зачастую является причиной неполадок и аварийных ситуаций.
В настоящее время существуют иные подходы к оценке эффективности, и предлагается иное математическое описание при расчетах процессов в руднотермических печах. В основе этих подходов лежит положение о том, что руднотермическая печь не является реактором непрерывного действия даже при постоянном сливе шлаков. Одной из возможных причин появления нестационарности является особый циклический режим плавления шихты, который приводит к импульсной подаче шихты из труботечки на колошник печи. Сущность циклического режима плавления шихты заключается в том, что при контакте свежих порций «холодной» шихты с расплавом начинается не плавление шихты, а кристаллизация заключенного между слоями шихты расплава, вплоть до полного затвердевания последнего. Затвердевший расплав тормозит поступление новых порций шихты, и истечение из труботечки прекращается. С течением времени затвердевший слой плавится благодаря тепловому контакту с горячей реакционной зоной, в определенный момент под действием веса вышележащего слоя шихты взламывается, и новая порция «холодной» шихты обрушивается в расплав.
Расчеты по математической модели, построенной для однокомпонентной системы, показали, что циклический режим плавления реализуется при превышении высоты погруженной в расплав шихты некоторого критического значения. В этом случае при отсутствии тепловыделения в расплаве, заключенном между зернами шихты, его полная кристаллизация происходит при условии:

где ст – теплоемкость твердой шихты;
rт, rж – соответственно плотность твердой шихты и расплава;
ε – объемная доля расплава в затопленной шихте;
Тф, Т0 – соответственно температура фазового перехода и «холодной» шихты;
rф – теплота фазового перехода.
Таким образом, расплав полностью кристаллизуется в том случае, если время кристаллизации верхних охлажденных слоев расплава меньше времени движения тепловой волны от действующего под слоем шихты источника энергии (электродов). Время продвижения тепловой волны в свою очередь зависит от глубины погруженной в расплав шихты. Расчеты по математической модели, описывающей затвердевание расплава между частицами шихты и последующее плавление застывшего слоя, показали, что время существования корки соизмеримо, а в некоторых случаях и превышает время ее образования. Расчеты показали также, что первоначальное обрушение шихты и образование застывшей «корки» приводит к установлению циклического режима, состоящего из следующих периодов: обрушение шихты в расплав, образование «корки», плавление застывшего слоя. В результате формируется дискретный характер загрузки шихты в руднотермическую печь.
Периодический слив шлаков или быстрое понижение уровня расплава является дополнительным побудителем к резкому истечению шихты из загрузочной течки.
Изменение уровня расплава в результате периодического слива и последующее постепенное накопление шлаков в печи, ведущее к повышению уровня расплава, приводит к изменению во времени ширины и положения активной зоны печи, что также является дестабилизирующим фактором.
Периодичность загрузки исходных компонентов в руднотермическую печь даже при постоянном сливе шлаков является веским доводом для того, чтобы не рассматривать руднотермическую печь как реактор непрерывного действия и оценивать работу печи на основе нестационарной модели.
7. Вращающиеся печи для производства строительных материалов
Наиболее важным процессом в производстве строительных материалов (извести, цемента, керамзита) является обжиг исходного сырья. При этом в сырье происходит множество физических и химических превращений, таких, например, как сушка, дегидратация, декарбонизация (кальцинация), спекание, вспучивание и др.
Ввиду схожести основных сырьевых материалов
(в производстве извести – известняк, в производстве цемента – известняк и глина, в производстве керамзита – глина), а также процессов при их термической обработке в этих производствах применяется однотипное Лабораторное оборудование. Это Лабораторное оборудование отличается только размерами и набором вспомогательных устройств, входящих в состав печного агрегата.
Основным агрегатом для обжига является вращающаяся печь. В дальнейшем рассматривается вращающаяся печь для производства цементного клинкера, а различия в расчете вращающихся печей для производства извести и керамзита отражены в соответствующем разделе.
7.1. Вращающиеся печи для производства цементного клинкера
Существуют два способа производства цемента – мокрый и сухой. При мокром способе сырьевая смесь получается в виде сметанообразной массы (шлама) путем тонкого измельчения сырьевых материалов и корректирующих добавок с водой и содержит преимущественно 35–45 % воды.
По сухому способу сырьевые материалы предварительно высушиваются и измельчаются и сухая сырьевая смесь (сырьевая мука) подается в печной агрегат.
Сухой способ производства является более экономичным в отношении расхода топлива, поэтому цементная промышленность высокоразвитых стран Европы и Японии практически полностью использует сухой способ производства. Мокрый способ производства существует преимущественно в России, странах бывшего СССР и в США.
Цементный клинкер – полуфабрикат для производства цемента – обжигается во вращающихся печах, являющихся основным Лабораторное оборудованием печных агрегатов. Кроме печи печной агрегат включает в себя устройство для сжигания топлива, питатели, холодильник, пылеулавливающие аппараты и др.
Вращающаяся печь (рис. 7.1) – это полый барабан, сваренный из стальных обечаек, выложенных изнутри огнеупорным кирпичом (футеровкой). Корпус печи расположен наклонно (под углом 3–4°) к горизонту и вращается вокруг продольной оси с частотой вращения 1–3 мин–1. В верхнюю загрузочную часть подается сырьевая смесь, а в нижней разгрузочной части устанавливается топливосжигающее устройство. Во вращающихся печах преимущественно сжигается природный газ, пылевидное топливо (уголь или сланец) и мазут. Благодаря вращению наклонного барабана сырьевая смесь движется по направлению к головке печи и обожженный клинкер через соединительную камеру поступает в холодильник, установленный за печью. Если холодильник устанавливается на самой печи, то клинкер попадает в него через разгрузочные окна. Холодильники вращающихся печей имеют самостоятельный привод, частота вращения составляет 3–6 мин–1. Холодильник располагают или под вращающейся печью, или по одной линии ниже печи. Угол наклона холодильников 5–7°.

Рис. 7.1. Схема вращающейся печи мокрого способа производства:
1 – шламовая течка; 2 – фильтр-подогреватель; 3 – цепная завеса; 4 – теплообменник; 5 – бандаж; 6 – подбандажная обечайка; 7 – венцовый привод; 8 – охлаждающее устройство; 9 – горячая головка печи; 10 – клинкерный холодильник
Основные конструктивные характеристики вращающейся печи – это ее диаметр D и длина L.
Применяемые в цементной промышленности вращающиеся печи подразделяются на печи мокрого и сухого способа производства. Для мокрого способа применяются длинные вращающиеся печи с отношением

Для сухого способа производства применяются вращающиеся печи с запечными циклонными теплообменниками и вращающиеся печи с декарбонизаторами.
Печи с декарбонизаторами в свою очередь подразделяются на печи с выносными декарбонизаторами и встроенными декарбонизаторами.
Выносные декарбонизаторы представляют собой самостоятельный агрегат, соединенный с запечной системой теплообменников. Эти декарбонизаторы оснащены топкой, в которой сжигается либо такой же вид топлива, как и во вращающейся печи, либо низкосортное топливо, например промышленные отходы. Продукты сгорания топлива поступают в систему теплообменников.
Во встроенных декарбонизаторах топка размещена в нижней части газохода, соединяющего теплообменник с печью.
В соответствии с протекающими во вращающейся печи физико-химическими процессами она разбивается на ряд технологических зон. Между зонами нет строгих границ, в отдельных зонах протекающие реакции частично перекрывают друг друга или идут параллельно. В печи мокрого способа различают следующие зоны, показанные в табл. 7.1.
Таблица 7.1 Зонная структура вращающихся печей для мокрого способа производства клинкера
|
7.2. Типовые конструкции вращающихся печей
7.2.1. Теплообменные устройства печей мокрого способа производства Для интенсификации теплообмена между обжигаемым материалом и газовым потоком в зоне сушки устанавливаются цепные завесы.
В зависимости от физических и реологических свойств шлама цепная завеса разделяется на три участка:
– участок текучего шлама – на этом участке шлам прилипает к цепям, за счет чего увеличивается поверхность шлама, омываемого газовым потоком;
– переходный участок – на этом участке интенсификация теплообмена происходит как за счет частичного налипания шлама на цепи, так и за счет погружения нагретых цепей в материал, а также образуются гранулы материала;
– на третьем участке передача тепла происходит при периодическом регенеративном процессе нагрева цепей и футеровки в газовом потоке и охлаждении их под слоем материала.
Во вращающихся печах применяют два типа цепных завес: с подвеской цепи в одной точке (свободно висящие цепные завесы) и с подвеской в двух точках (гирляндные цепные завесы).
Сопоставление особенностей и эффективности различных систем навески цепей показывают следующее: величина коэффициента теплопередачи (F) гирляндных цепей на 30–35 % выше, чем у завесы со свободно висящими концами; испарительная способность их также выше: так, у гирляндных завес она составляет 20–25 кг/м2 поверхности цепей против 10–12 кг/м2 у завесы со свободно висящими концами. В то же время у гирляндных цепных завес плотность навески ограниченна. Коэффициент плотности навески kF (м2/м2) – отношение площади поверхности цепей к площади поверхности футеровки – ограничен. Так, у цепной завесы со свободно висящими концами на отдельных участках kF = = 14 м2/м2 , а у гирляндных завес kF не более 8 м2/м2 .
За счет повышенного коэффициента плотности свободно висящие цепные завесы более эффективны в теплотехническом отношении и на сопоставимых участках могут передать материалу большее количество тепла, чем гирляндные цепные завесы. За счет более интенсивной теплопередачи в цепной завесе у вращающихся печей со свободно висящими цепями температура отходящих газов составляет 180–200 0С против 210–230 0С у вращающихся печей с гирляндными цепными завесами.
Большим преимуществом цепной завесы со свободно висящими концами является меньшая трудоемкость монтажа и ремонта и простота эксплуатации. При обрыве свободно висящих концов они беспрепятственно выходят из завесы с материалом, в то время как обрыв гирлянды приводит к образованию местных клубков из цепей. Гирляндные цепные завесы в меньшей степени стирают футеровку и лучше транспортируют материал. Свободно висящие концы способствуют лучшему разрушению шламовых колец в случае их образования. Основным преимуществом гирляндных цепных завес является их способность сохранять образующиеся гранулы материала. Как видно из рис. 7.2, темп нагрева материала в значительной степени зависит от его гранулометрического состава. Интенсивность теплообмена в полой части печи до определенного предела возрастает с увеличением крупности гранул. Поскольку гирляндные цепные завесы способствуют сохранению гранул, они обеспечивают более высокий коэффициент теплопередачи в полой части печи.
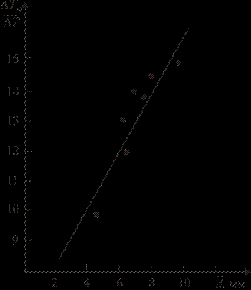
Рис. 7.2. Зависимость темпа нагрева материала

Таким образом, цепные завесы со свободно висящими концами в теплотехническом отношении более эффективны в зоне сушки, но из-за разрушения образовавшихся гранул менее эффективны в полой части печи. Гирляндные цепные завесы в теплотехническом отношении менее эффективны в зоне сушки, но обеспечивают лучшую теплопередачу в полой части печи. Поэтому нельзя сделать вывод об исключительном преимуществе одной из двух систем навески цепей. Большинство специалистов разделяют следующую точку зрения. Если материал в печи плохо гранулируется и образуются только мелкие гранулы, то следует применять цепные завесы со свободно висящими концами, и наоборот при хорошей грануляции материала предпочтение должно отдаваться гирляндным цепным завесам.
В промышленности применяются и комбинированные цепные завесы. В зоне жидкотекучего шлама навешиваются цепи со свободно висящими концами с высоким значением kF (10–14 м2/м2). На переходном участке также можно навешивать цепь со свободно висящими концами, но с пониженной плотностью kF (3–5 м2/м2). На участке, где шлам потерял пластичность, целесообразно применять гирляндную навеску цепей.
В заключение для примера приведены характеристики двух типов цепных завес для печи 4,5 170 м при относительно близком значении начальной влажности шлама (табл. 7.2).
Таблица 7.2 Характеристики типичных цепных завес
|