Курс лекций для специальности 140104 «Промышленная теплоэнергетика» москва 2011
Вид материала | Курс лекций |
- Курс лекций для специальности 140104 «Промышленная теплоэнергетика» москва 2011, 1206.2kb.
- Курс лекций для студентов специальности 140104 «Промышленная теплоэнергетика» москва, 1244.1kb.
- Курс лекций для студентов специальности 140104 «Промышленная теплоэнергетика» москва, 877kb.
- Курс лекций для студентов специальности 140104 «Промышленная теплоэнергетика», 1246.47kb.
- Рабочая программа для студентов Vкурса по специальности 140104 промышленная теплоэнергетика, 69.12kb.
- Рабочая программа для студентов IV курса специальности 100700 промышленная теплоэнергетика, 243.31kb.
- Рабочая программа для студентов Vкурса специальности 290800. Промышленная теплоэнергетика, 63.46kb.
- Нисаев Игорь Петрович, д т. н., профессор учебно-методический комплекс, 356.38kb.
- Нисаев Игорь Петрович, д т. н., профессор учебно-методический комплекс, 329.37kb.
- Учебно-методический комплекс по дисциплине «экономика» Для студентов специальностей:, 1055.87kb.
7.2.2. Встроенные теплообменники
Интенсификация теплообмена в зонах дегидратации и подогрева может быть достигнута за счет установки встроенных теплообменников.
В настоящее время только в сравнительно небольшом количестве печей (главным образом за рубежом) в печах установлены металлические теплообменники, несмотря на их значительную эффективность. Это в основном объясняется тем, что они конструктивно несовершенны, недолговечны и изготавливаются из высококачественных легированных сталей.
В отечественной промышленности широко используются цепные теплообменники – «коврики». По существу они являются гирляндной цепной завесой с малой стрелой провисания, т. е. практически прижаты к футеровке. Цепи омываются газовым потоком больше времени, чем в обычных цепных завесах, что благоприятно сказывается на регенеративном теплообмене. В цепных теплообменниках

Длина цепного теплообменника ограничивается только жаропрочностью цепей. Обычно их устанавливают непосредственно за цепной завесой и продлевают до того сечения печи, где температура пылегазового потока достигает 1300 0С.
7.2.3. Теплообменники печей сухого способа производства
Для интенсификации теплообмена к печам сухого способа устанавливаются запечные теплообменники. Поиски интенсивных способов передачи тепла материалу в печах сухого способа производства привели к разработке методов организации теплообмена во взвешенном состоянии материала и вынесении процесса декарбонизации из вращающейся печи в отдельный аппарат – декарбонизатор.
Практически используется три типа запечных теплообменников:
1. Запечные теплообменники циклонного типа. Схема печи с таким теплообменником показана на рис. 7.3. Установка состоит из четырех ступеней циклонов, соединенных между собой газоходами. Может быть и пять ступеней. Сухую сырьевую муку подают в газоход между третьей и четвертой ступенями циклонов, и поток газов выносит ее в циклон четвертой ступени. Осевшая в циклоне четвертой ступени сырьевая мука поступает в газоход между второй и третьей ступенями циклонов, а газы с неосевшей мелкой пылью направляются в систему пылеочистки или поступают в сырьевую мельницу для сушки влажной сырьевой смеси. Далее мука таким же образом поступает в циклоны третьей, второй и первой ступеней, а затем во вращающуюся печь.
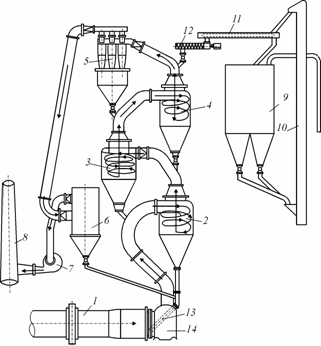
Рис. 7.3. Схема циклонных теплообменников вращающейся печи:
1 – вращающаяся печь; 2–5 – циклоны 1, 2, 3 и 4-й ступеней;
6 – пылеосадительные циклоны; 7 – дымосос; 8 – дымовая труба; 9 – бункер сырьевой муки; 10 – элеватор сырьевой муки; 11 – транспортер;
12 – питающий шнек; 13 – течка для материала; 14 – соединительная головка
2. Запечные теплообменники с выносным декарбонизатором. Схема декарбонизатора показана на рис. 7.4. Декарбонизатор встроен между циклонами второй и первой ступеней. Он состоит из трех частей – вихревой топки (форкамеры), вихревого кальцинатора и смесительной камеры. Сырьевая мука из циклонов второй ступени попадает в патрубок форкамеры, подхватывается горячим воздухом и выносится в рабочий объем декарбонизатора, где происходит теплообмен между продуктами сгорания топлива и сырьевым материалом. Воздух на горение подается по отдельному трубопроводу от холодильника в тангенциально расположенные патрубки форкамеры и декарбонизатора. Степень декарбонизации собственно в декарбонизаторе достигает примерно 45 %. Пылегазовый поток с температурой около 900 0С по нисходящему газоходу попадает в смесительную камеру, в которой он интенсивно перемешивается с газовым потоком, выходящим из печи. Из смесительной камеры пылегазовый поток выносится в циклоны первой ступени. Поскольку в выносных декарбонизаторах процесс сжигания топлива регулируется автономно, то в нем сжигается до 60 % топлива, расходуемого на обжиг. Этого количества топлива достаточно для того, чтобы степень декарбонизации материала на входе в печь составляла 85–95 % при температуре материала до 900 С. Более глубокую подготовку материала в печах с декарбонизаторами не производят, т. к. незначительное повышение количества тепла, переданного в полностью декарбонизированный материал, вызывает резкое повышение его температуры, и это приводит к образованию настылей в нижней ступени циклонного теплообменника. При сжигании топлива в запечном декарбонизаторе можно либо уменьшить тепловую нагрузку зоны горения вращающейся печи и сохранить ее производительность, либо сохранить прежний уровень тепловой нагрузки. Первое решение позволяет повысить стойкость футеровки и снизить расход огнеупоров. Второе решение приводит к увеличению производительности печи в два и более раз. Обычно на практике используется второе решение. Следует отметить, что в выносных декарбонизаторах можно применять низкосортные сорта топлива (вплоть до отходов) и, благодаря более низкой температуре горения топлива, уменьшить выбросы токсичных газов (оксидов азота).
3. Встроенные декарбонизаторы. В этих системах дополнительная топка монтируется в нижнюю часть газохода, соединяющего теплообменник с печью. Воздух на горение подается через печь, поэтому количество сжигаемого топлива ограничено 30 % от общего расхода, т. к. при большом расходе топлива и, соответственно, воздуха, условия сжигания топлива в печи ухудшаются из-за повышенного коэффициента избытка воздуха.
7.3. Теплообменники и вращающиеся печи для огнеупоров
Установку того или иного типа теплообменника производят с учетом вида обжигаемого сырья, его зернового состава и подготовки, температуры отходящих газов и т.п. В настоящее время большинство внешних теплообменников, за исключением котлов-утилизаторов и экономайзеров, в производстве огнеупоров применяют только в опытных и полупромышленных установках. Для обжига материалов, требующих высоких температyp спекания, представляет интерес установка для высокотемпературного обжига, разработанная Восточным институтом огнеупоров. На рис. 7.4 показана установка для обжига чистых магнезитов и доломитов.
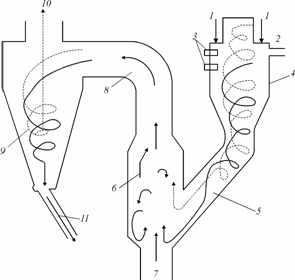
Рис. 7.4. Схема теплообменника RSP:
1 – подача материала из верхних ступеней теплообменника; 2 – вихревая форсунка; 3 – форсунки; 4 – вихревой кальцинатор; 5 – выходной боров кальцинатора; 6 – смесительная камера; 7 – газоход от печи; 8 – газоход от смесительной камеры; 9 – циклон; 10 – подача газа в верхние ступени
теплообменника; 11 – подача материала во вращающуюся
печь (сплошные стрелки – движение материала, штриховые – потоки газов)
Установка состоит из двух ступенчато расположенных вращающихся печей с самостоятельной подачей топлива и подогретого воздуха.
Печь 1 служит для нагрева и декарбонизации исходного сырья, печь 2 – для конечного обжига материала, поступающего из печи 1 по течке 7 пересыпной камеры 6, снабженной топочным устройством 10 для предварительного смешения топлива с воздухом. Последовательно с печью 2 установлен теплообменник барабанного типа 3 для высокотемпературного нагрева воздуха, идущего для сжигания топлива в зоне обжига печи 2. Печь 2 и теплообменник 3 соединены между собой пересыпной камерой 8, в которой установлены топливосжигающее устройство 11 и течка 9 для пересыпки обожженного материала из печи в теплообменник. Для конечного охлаждения готового продукта и низкотемпературного подогрева воздуха, поступающего в печь 1 и через пересыпную камеру 5 и теплообменник 3 в печь 2, служит теплообменник колосникового типа 4. Воздух на охлаждение готового продукта подают вентилятором 13 через трубопровод 12 и окна 14. Система отбора и очистки подогретого воздуха из колосникового холодильника состоит из окон 15, трубопроводов, циклонного пылеуловителя 16, вентилятора 17. Приемная воронка 18 служит для приема готового продукта и осажденной пыли из циклонов. Печь 1 со стороны загрузки сырья снабжена устройством 22 для разделения исходного сырья на крупные и мелкие фракции перед подачей в теплообменники 20 и 25. Теплообменник шахтного типа 20 служит для подогрева крупных фракций исходного сырья теплом отходящих газов из печи 1 по газоходу 19. Теплообменник циклонного типа 25 предназначен для подогрева мелких фракций исходного сырья, газоход 26 – для подвода газов, отходящих из печи 1, к теплообменнику 25 и частичного отвода подогретого материала в печь 1. Устройства 23 и 24 служат для подачи сырья в теплообменники, а течка 27 – для подачи материала из теплообменников в печь. Отходящие газы из теплообменников отводят по трубопроводам 21 и 28.
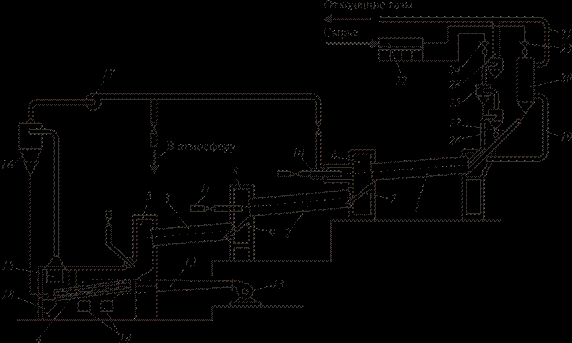
Рис. 7.5. Схема установки для высокотемпературного обжига во вращающихся печах
Таблица 7.3 Основные показатели работы
|
К основным преимуществам установки можно отнести возможность получения более высоких температур в зоне обжига без применения кислорода или других интенсификаторов в целях увеличения производительности и улучшения качества обожженного продукта; использование тепла отходящих газов для предварительного подогрева сырья, состоящего из смеси крупных и мелких фракций, за счет установки параллельно с шахтным теплообменником циклонных теплообменников, что снижает удельный расход топлива и повышает производительность установки при одновременном снижении пылеуноса; возможность полной автоматизации режима сжигания топлива.
Основные показатели работы и параметры вращающихся печей приведены в табл. 7.3 и 7.4.
Таблица 7.4 Параметры вращающихся печей
* Числитель – по сырью; знаменатель – по готовому продукту. |
7.4. Холодильники вращающихся печей
Существуют четыре основных типа холодильников:
– барабанные, расположенные под вращающейся печью;
– рекуператорные и планетарные, барабаны которых крепятся к корпусу печи и вращаются вместе с ней;
– колосниковые;
– шахтные.
Для вращающихся печей в подавляющем большинстве случаев используются колосниковые и планетарные холодильники.
7.4.1. Планетарные и рекуператорные холодильники
Рекуператорный холодильник состоит из нескольких сварных металлических барабанов (обычно 10–12 шт.), установленных на корпусе вращающейся печи. Каждый барабан на участке, составляющем примерно 50 % длины, футерован огнеупорным кирпичом, а остальная часть для интенсификации теплообмена оборудована цепными завесами, пересыпными полками или лопастями. Через отверстие в корпусе печи клинкер поступает в рекуперативный холодильник и охлаждается за счет просасывания через него воздуха, идущего на горение топлива в печи, поэтому количество воздуха ограниченно и недостаточно для полного охлаждения клинкера. Температура клинкера, выходящего из холодильника, составляет 300–500 0С. У рекуператорных холодильников отношение длины к диаметру

Планетарные холодильники – это те же рекуператорные холодильники с тем отличием, что за счет удлинения корпуса печи устанавливается дополнительная опора для поддержания удлиненного корпуса без снижения несущей способности корпуса вращающейся печи. За счет этого отношение

7.4.2. Колосниковые холодильники
Колосниковый холодильник состоит из ступенчатых колосниковых решеток, по которым движется клинкер, выходящий из печи. Колосниковая решетка комплектуется из чередующихся групп подвижных и неподвижных колосников. Решетки заключены в прямоугольную футерованную камеру. Неподвижные ступени заделаны в стену камеры, а подвижные связаны общей рамой, совершающей возвратно-поступательное движение.
Подколосниковое пространство разделено изолированными друг от друга камерами, в которые подается охлаждающий воздух. Проходя через слой материала, находящегося на решетке, воздух попадает в надрешеточное пространство.
Привод колосников осуществляется от двигателя с регулируемым числом оборотов. Рама делает 8–18 возвратно-поступательных ходов в минуту. Длина хода 100–120 мм. Ширина щелей для прохода воздуха 5–8 мм, живое сечение решетки около 10 %.
Воздух подается либо от общего дутьевого вентилятора с раздачей его по камерам, либо к каждой камере устанавливается свой дутьевой вентилятор.
Конструкция колосниковых холодильников позволяет использовать для охлаждения больше воздуха, чем нужно для горения топлива в печи. Это обеспечивает более глубокое охлаждение клинкера, чем в планетарных холодильниках. Температура клинкера на выходе из холодильника составляет 80–100 С.
Часть воздуха, необходимого для сжигания топлива, подается печным дымососом в печь, а избыточный воздух удаляется из холодильника через аспирационную систему в атмосферу или используется, например, для сушки угля.
Мелкие зерна клинкера, провалившиеся через колосниковую решетку, попадают в подрешеточное пространство, из которого удаляются танспортером скребкового типа. Существуют такие конструкции колосниковых холодильников, в которых под каждой камерой устанавливается бункер. Просыпь из бункера через систему шлюзовых затворов попадает на общий транспортер, проходящий под бункером холодильника.
На выходе из холодильника устанавливается молотковая дробилка, измельчающая крупные куски клинкера.
Существуют конструкции холодильника с установкой молотковой дробилки внутри холодильника, т.е. с промежуточным дроблением клинкера.
Тепловой кпд холодильника составляет 75–80 % для печей мокрого способа производства и 65–70 % – для печей сухого способа производства.
Теоретические расчеты и практика работы показали, что целесообразно применять двукратный просос воздуха через слой клинкера: сначала подать охлаждающий воздух в камеры, где проходит клинкер с более низкой температурой, а затем этот же воздух подать в «горячие» камеры. Однако, несмотря на эффективность, от двукратного прососа пришлось отказаться в основном по причине большой запыленности возвращаемого воздуха и высокой абразивности клинкерной пыли, поскольку вентилятор, транспортирующий возвращаемый воздух быстро выходит из строя.
7.5. Холодильниики печей для производства огнеупоров
Часто производительность вращающихся печей, особенно при обжиге материалов, требующих высоких температур обжига (магнезит, доломит), сдерживается работой холодильников. Материал после барабанных холодильников имеет высокую температуру. Увеличение длины холодильника или его диаметра в действующих печах не представляется возможным, поэтому после барабанных холодильников устанавливают теплообменники для охлаждения порошка фракции 0–10 мм и кусков размером более 10 мм. Схема установки и устройства теплообменников, разработанных Восточным институтом огнеупоров, для охлаждения магнезита показаны на рис. 7.6.
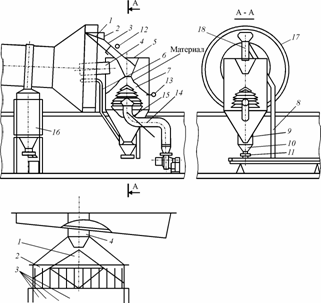
Рис. 7.6. Схемы теплообменников
для охлаждения магнезита:
а) для фракции 10–100 мм: 1 – решетка; 2 – приемная воронка;
3 – течка; 4 – воздухопровод горячего воздуха; 5 – корпус;
6 – воздухопровод отсоса горячего воздуха; 7 –колосниковая решетка;
8 – обводная течка; 9 – бункер; 10 – воронка; 11 – питатель;
12 – датчик верхнего уровня; 13 – датчик нижнего уровня;
14 – воздухопровод холодного воздуха; 15 – распылитель;
16 – теплообменник фракции 0–10 мм; 17 – элеватор; 18 – шибер;
б) для фракции 0–10 мм: 1 – распределитель;
2 – приемник; 3 – водоохлаждаемые секции; 4 – кожух