Курс лекций для специальности 140104 «Промышленная теплоэнергетика» москва 2011
Вид материала | Курс лекций |
- Курс лекций для специальности 140104 «Промышленная теплоэнергетика» москва 2011, 1206.2kb.
- Курс лекций для студентов специальности 140104 «Промышленная теплоэнергетика» москва, 1244.1kb.
- Курс лекций для студентов специальности 140104 «Промышленная теплоэнергетика» москва, 877kb.
- Курс лекций для студентов специальности 140104 «Промышленная теплоэнергетика», 1246.47kb.
- Рабочая программа для студентов Vкурса по специальности 140104 промышленная теплоэнергетика, 69.12kb.
- Рабочая программа для студентов IV курса специальности 100700 промышленная теплоэнергетика, 243.31kb.
- Рабочая программа для студентов Vкурса специальности 290800. Промышленная теплоэнергетика, 63.46kb.
- Нисаев Игорь Петрович, д т. н., профессор учебно-методический комплекс, 356.38kb.
- Нисаев Игорь Петрович, д т. н., профессор учебно-методический комплекс, 329.37kb.
- Учебно-методический комплекс по дисциплине «экономика» Для студентов специальностей:, 1055.87kb.
Основная литература
Высокотемпературные теплотехнические процессы и установки. Под ред. Ключникова А.Д., М.: Энергоатомиздат, 1989, 336 с.
Промышленная теплоэнергетика и теплотехника. Справочник. (Теплоэнергетика и теплотехника; Кн.4), 4-е издание. Под общей ред. Клименко А.В. и Зорина В.М. М.: Изд-во МЭИ, 2007 г. 632 с.
-
Несенчук А.П., Жмакин Н.П., Кальтман И.И. Пламенные печи для нагрева и термообработки металла: Учеб. пособие для вузов. – Минск: Вышэйшая школа, 1973. – 352 с.
Тимошпольский В.И., Несенчук А.П., Трусова И.А. Промышленные теплотехнологии. – Кн. 3. – Мн.: Высшая школа, 1998.
-
Мастрюков Б.С. Теплотехнические расчёты промышленных печей. – М.: Металлургия. 1972.
Промышленная теплоэнергетика и теплотехника: Справочник. – Кн. 4 / Под общ. ред. В.А. Григорьева, В.М. Зорина. – М.: Энергоатомиздат, 1991.
-
Аверин С.И., Гольфарб Э.М., и др. Расчёт нагревательных печей / Под ред. д.т.н., проф. Н.Ю. Тайца – Киев: Техника, 1969.
Высокотемпературные теплотехнологические процессы и установки Текст. / АП. Несенчук [и др.]; под общ ред. ВГ. Лисиенко. Мн.: Вышейшая школа, 1988.-320 с.
-
Высокотемпературные теплотехнологические процессы и установки Текст./ И.И. Перелетов и [др.]; под ред. А.Д. Ключникова. М.: Энергоатомиздат, 1989.-336 с.
Дополнительная литература
Вальченко Н.А., Гурко В.В. Практическое пособие по выполнению курсового проекта по курсу «Высокотемпературные теплотехнические процессы и установки» для студентов специальности Т.01.02.00 «Теплоэнергетика». - ГГТУ, 2001.
-
Теплотехника / Под ред. И.Н. Сушкина. – М.: Металлургия, 1973. - 478 с.
Зобнин, Б.Ф. Нагревательные печи (теория и расчет) Текст./ Б.Ф. Зобнин. -М.: Машиностроение, 1964. - 311 с.
-
Ключников, А.Д. Теплотехническая оптимизация топливных печей Текст./ А.Д. Ключников. -М.: Энергия, 1974. - 344 с.
Адрианов В. Н. - Основы радиационного и сложного теплообмена. - М.: Энергия, 1972. - 464 с.
-
Ключников А.Д., Иванцов Г.П. Теплопередача излучением в огнетехнических установках (инженерные решения задач).- М.: Энергия, 1970.- 400 с.
Теплоэнергетика и теплотехника: справ. серия в 4-х книгах / Под общ. ред. В. А. Григорьева, В. М. Зорина. - 2-е изд., перераб. - М.: Энергоатомиздат, 1987 - 1988. Кн. 1: Общие вопросы: справ. - 1987. - 456 с.
-
Невский А.С. Лучистый теплообмен в печах и топках. 2-е изд., испр. и доп. М.: Металлургия, 1971. 440 с.
Расчёты нагревательных печей: Учеб. пособие для вузов/ Под ред. Тайца Н.Ю. – К.: Технiка, 1969. – 540 с.
Расчет нагревательных и термических печей: Справ. изд. / Василькова С.Б., Генкина М.М., Гусовский В.Л. и др. / Под ред. Тымчака В.М. и Гусовского В.Л. – М.: Металлургия, 1983. – 480 с.
Теплотехника и теплоэнергетика металлургического производства: Учебник для вузов /Гущин С.Н. и др. – М.: Металлургия, 1993. – 366 с.
-
Амбразявичус А.Б., Литвинов В.К. Высокотемпературный теплообмен в плазменно-технологических аппаратах: Учеб. пособие. Свердловск: УПИ им. С.М. Кирова, 1986. 89 с.
-
Филипьев О.В. Промышленные печи и газовое хозяйство заводов: Учеб. пособие для вузов. – К.: Вища школа, 1976. – 240 с.
Арутюнов, В.А. Математическое моделирование тепловой работы промышленных печей Текст. / В.А. Арутюнов, В.В. Бухмиров, С.А. Крупенников. — М.: Металлургия, 1990. 239 с.
Лекция 1
1. Высокотемпературные химические реакторы (печи и плазмохимические реакторы)
Химический реактор, в котором источник энергии для проведения химического процесса (химической реакции или фазового превращения) вступает в непосредственный контакт с сырьевым материалом при температуре более 500 °С, называется печью. Основное отличие печи от классических химических реакторов заключается в наличии высокого температурного градиента и непосредственного контакта энергоносителя с сырьем и продуктами реакции. Первые печи появились более 10 000 лет назад. В это время источником энергии служила окислительная реакция при сжигании древесины на воздухе, сырьем — руды в смеси с древесным углем для получения металлов либо глина в смеси с кварцевым песком для получения керамических изделий. Принципиальная схема пламенных печей сохранилась практически неизменной до наших дней (рис. 1.1).
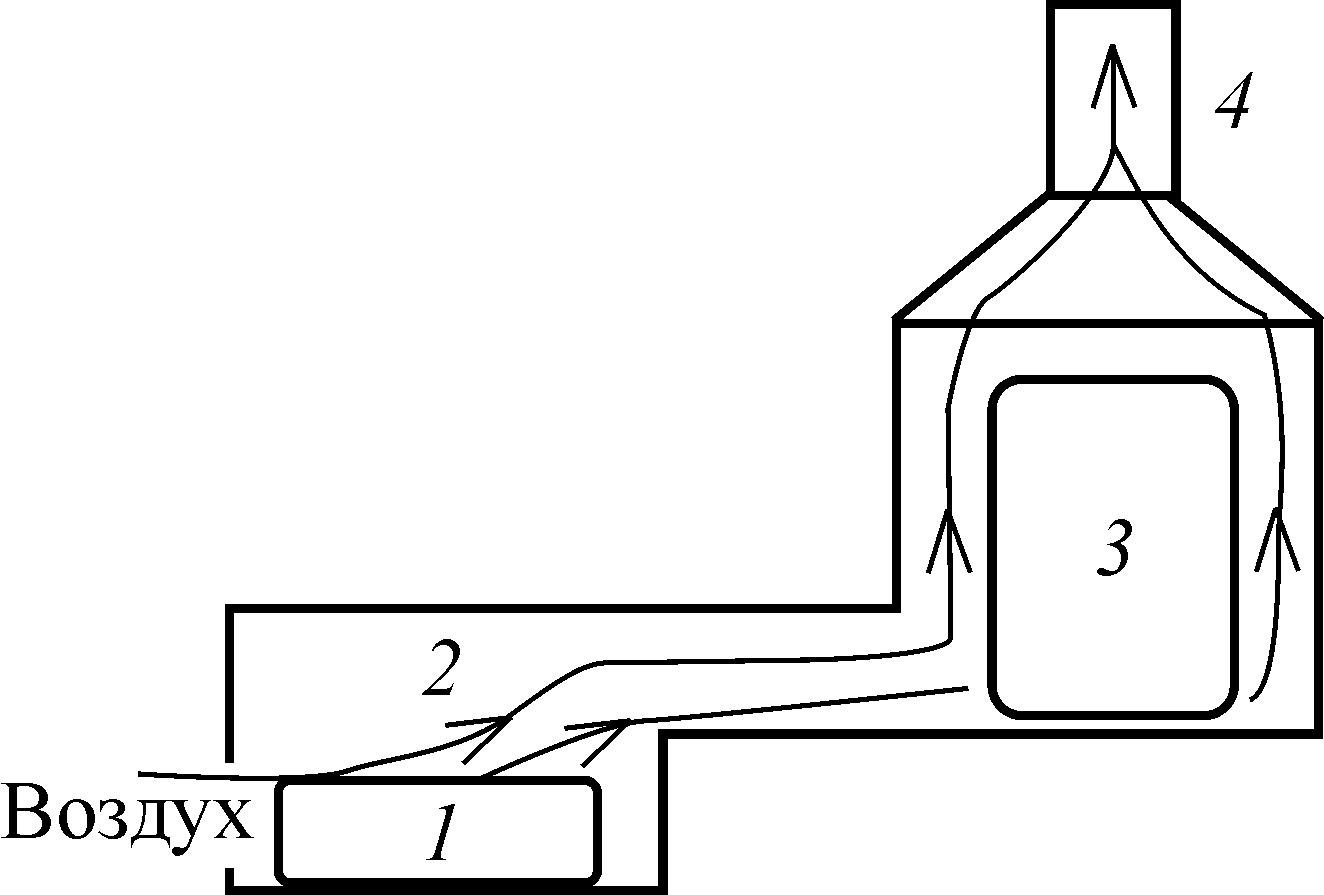
Рис. 1.1. Принципиальная схема первых печей:
1 — органическое топливо (древесина, древесный уголь); 2 — продукты сгорания (топочные газы); 3 — реакционная смесь; 4 — устройство для повышения скоростного напора топочных газов (труба)
Основная функция печи — обеспечить сырью требуемую температуру, поэтому реактор данного типа должен иметь устройство для получения энергии, устройство для доставки энергии сырьевым материалам и устройства контроля за процессами в сырье. Технический прогресс в области печестроения на всех исторических этапах развития техники характеризуется созданием специализированных печей для конкретного технологического процесса (или группы родственных процессов) и отказом от универсальных печных агрегатов. Только в этом случае можно избавиться от недостатков универсального печного агрегата, представленного на рис. 1.1: низкого коэффициента полезного действия (КПД), низких температур в обрабатываемом сырье, больших градиентов температур в сырье, длительного цикла загрузка—высокотемпературная обработка—разгрузка, вредного влияния компонентов топочных газов на химические процессы в сырье. Для повышения коэффициента полезного действия и температуры в течение всего индустриального и постиндустриального исторического периода человеческой истории проводилось совершенствование топливно-сжигающего устройства (состав топлива, состав окислителя, устройство подачи окислителя и удаления топочных газов) и теплоизолирующей футеровки в топке и реакционном объеме печи. Ввиду того, что теплопередача от печных газов к конденсированному сырью имеет физические пределы как по температуре, так и по КПД, совершенствование специализированных печных агрегатов шло по двум направлениям: во-первых, пространственного сближения места окисления топлива и сырьевой смеси вплоть до совмещения в едином пространстве (например доменный процесс получения чугуна); во-вторых, поиска альтернативных источников энергии и способов подвода ее к сырью. Для повышения производительности процесса высокотемпературной обработки камерные печи периодического действия (рис. 1.2) заменяют на конструкции, в которых процесс нагрева в печи происходит непрерывно, а сырье двигается через зону нагрева (проходные печи). С целью устранения нежелательного химического взаимодействия компонентов печных газов строят либо печи, где теплопередача от топочных газов к сырью идет через стенку (муфельные печи), либо меняют источник энергии (замена твердого топлива на жидкое или газообразное либо переход на электрический нагрев или волновую энергию). Следует отметить, что любое повышение технических характеристик печи наряду с прямым положительным эффектом сужало специализацию печи. В результате печи становились все более узкоспециализированными (предназначенными для проведения одного конкретного химического процесса).
До середины XVIII в. технический прогресс в области совершенствования конструкций печей осуществлялся интуитивно-эмпирическим путем. Основоположниками теории промышленных печей стали М.В. Ломоносов (в 1742 г. дал научное определение причин движения газов в печи), Ж. Фурье (в 1822 г. создал математическую теорию распространения тепла внутри твердых тел), В.Е. Грум-Гржимайло (в 1905–1910 гг. сформулировал гидравлическую теорию пламенных печей и основные принципы конструирования печей с естественной тягой), М.В. Кирпичев (в 1936 г. создал теорию подобия и моделирования физических процессов).
Высокотемпературные реакторы стоят несколько особняком среди основной массы химических реакторов. Высокотемпературными процессами принято называть процессы химического взаимодействия и фазовые переходы, происходящие при температурах, когда энергообмен целевого продукта химико-технологической системы с окружающей средой протекает с возрастающим участием электромагнитных колебаний (в частности, светового излучения) и корпускулярного излучения. Граница между низкотемпературными и высокотемпературными процессами лежит в интервале 500–700 °С. В промышленности печи используются как для проведения химических реакций, так и для получения продуктов в результате высокотемпературных фазовых переходов (плавления, спекания, возгонки). Чаще всего в печи параллельно протекают все эти процессы, а конструкцию печи определяет целевой процесс.
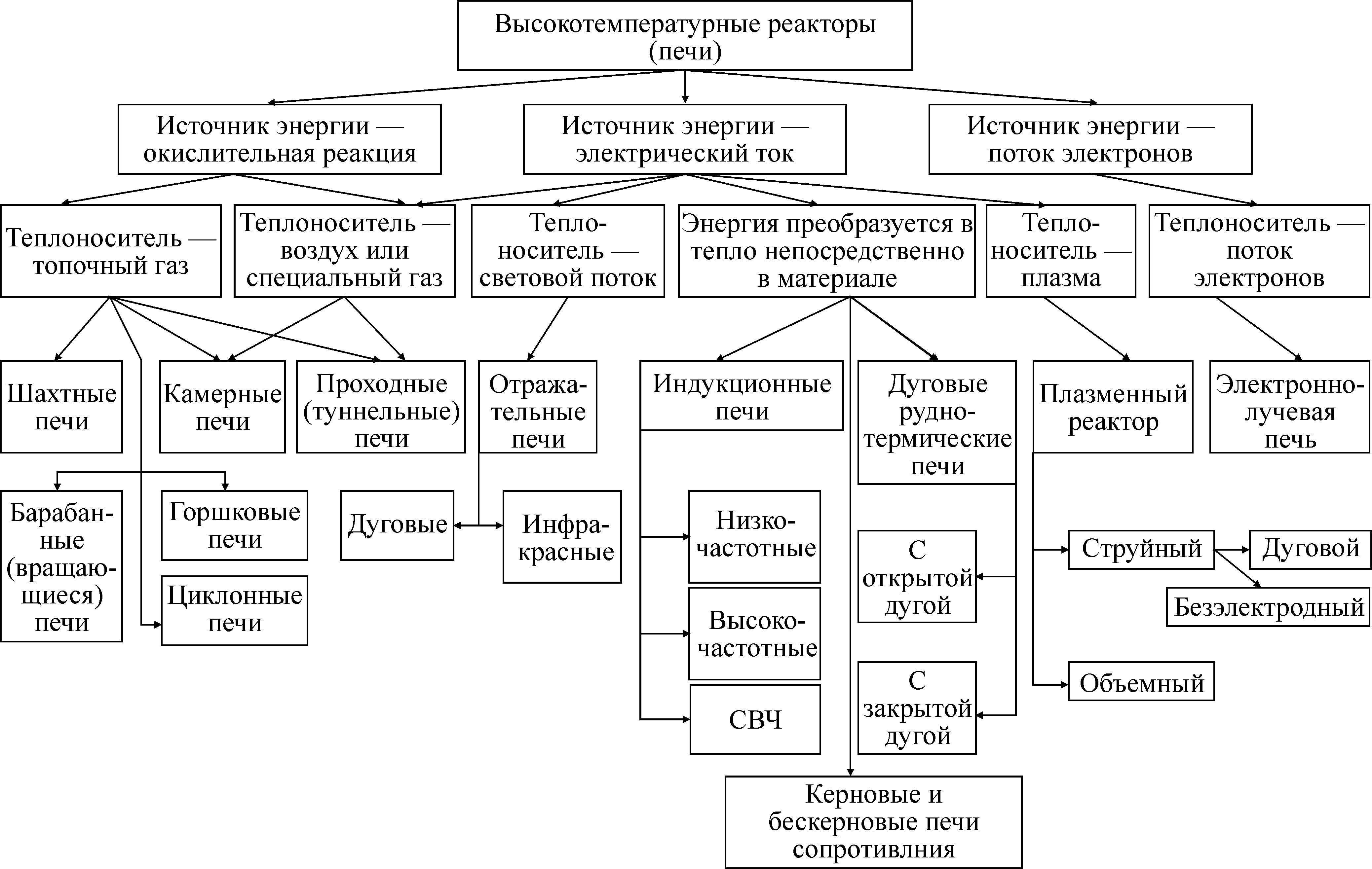
Рис. 1.2. Типы высокотемпературных реакторов (печей)
С гидродинамической точки зрения печи (так же как и остальные химические реакторы) можно классифицировать на агрегаты с идеальным вытеснением (камерные и туннельные печи, струйные плазмохимические реакторы, вращающиеся печи и т. д.), с идеальным перемешиванием (плазмохимические реакторы объемного типа, дуговые печи для получения белого электрокорунда) и реакторы промежуточного типа (дуговые печи для производства фосфора, карбида кальция).
С термодинамической точки зрения печь — это открытая система, в которой происходит термодинамическое и химическое взаимодействие источника энергии, теплоносителя, сырья и продуктов химических реакций (в том числе и целевого продукта). Существует несколько принципов классификации печей. В их основе лежат:
- - принцип деления по источникам энергии;
- - характер рабочего тела-теплоносителя;
- - их конструктивные особенности;
- - технологическое назначение;
- - режим работы.
Схема классификации высокотемпературных реакторов по источникам энергии (с учетом остальных признаков) приведена на рис. 1.2. Выделение тепла может происходить как в самом нагреваемом материале (прямой нагрев), так и вне его с последующей теплопередачей (косвенный нагрев).
При выборе высокотемпературного реактора (печи) для конкретного технологического процесса факторы, принимаемые во внимание, располагаются в следующей последовательности по важности: характер целевого химического процесса и фазовый состав исходного сырья и продуктов реакции; химическое взаимодействие энергоносителя с сырьем и целевым продуктом; удельные затраты на получение нужной температуры при заданной производительности; соответствие температурного поля в рабочей зоне реактора технологическим требованиям; возможности автоматизации загрузки сырья и выгрузки готового продукта; выход годного продукта в соответствии с техническими требованиями на него; удельные затраты на отделение конечного продукта от побочных продуктов процесса; возможности полной автоматизации процесса; отходы и экологическая нагрузка на окружающую среду. Представленные на рис. 1.2 варианты печей в принципе позволяют решать почти любую технологическую задачу с использованием разных типов реакторов с различным технико-экономическим результатом.
2. Камерные и проходные печи
2.1. Тепловой расчет электрических печей сопротивления
Цель теплового расчета электрических печей сопротивления (ЭПС) – определение оптимальных параметров (энергетических, геометрических, экономических), при которых обеспечивается проведение заданного технологического процесса. По результатам расчета выбирают конструкцию футеровки печи, определяют установленную мощность печи, находят количество теплоты, необходимое для проведения физико-химических превращений в обрабатываемом материале, вычисляют тепловые потери печи. Для ЭПС непрерывного действия выбирают число тепловых зон и мощность каждой зоны печи. В некоторых случаях рассчитывают кривые нагрева и охлаждения загрузок.
Завершают тепловой расчет вычислением производительности печи, удельного расхода электроэнергии и теплового кпд.
Производительность садочных (периодических) ЭПС:

где G – производительность печи;
М – масса единовременной загрузки;
tц – время технологического цикла.
Время цикла включает в себя:

где tз,в – время загрузки и выгрузки;
tн – время нагрева;
tвыд – время изотермической выдержки;
tохл – время охлаждения.
Для ЭПС, работающих в непрерывном режиме, производительность удобно считать:

где L – длина печи; m – масса загрузки на единицу длины, кг/м.
При расчете производительности печей непрерывного действия во время цикла не включают время на загрузку и разгрузку печи. Такие печи удобно разбить на тепловые зоны и относить расчетные параметры на 1 м длины печи.
Из уравнений (2.1) и (2.3) видно, что производительность зависит от времени цикла. Для ее повышения необходимо сокращать составляющие времени цикла, однако tн, tвыд и tохл зачастую заданы условиями технологии. Если допускается проведение нагрева и охлаждения с максимальной скоростью, тогда можно воспользоваться тепловым расчетом для нахождения оптимальных энергетических характеристик процесса, обеспечивающих минимальное время цикла.
Знание удельного расхода электроэнергии позволяет оценить энергетическую эффективность процесса. Для вычисления используют уравнение:

где qэ – удельный расход электроэнергии;
Nпотр – мощность, потребляемая печью из сети.
Тепловой кпд характеризует работу печи как источника энергии:

где hт – тепловой кпд печи;
Nз – мощность, расходуемая на нагрев и физико-химические процессы в загруженном образце.
2.1.1. Определение установленной мощности
Установленная мощность Nу – это потребляемая электропечью (при заданном режиме термообработки) мощность, взятая с запасом, учитывающим «старение» нагревателей и возможное временное падение напряжения в сети:

где Nпотр – мощность, потребляемая из сети при заданном режиме;
kз – коэффициент запаса мощности (kз = 1,1÷1,2 – для ЭПС непрерывного действия, kз = 1,2÷1,4 – для ЭПС периодического действия).
Потребляемая мощность расходуется на нагрев загрузки и вспомогательных устройств, прогрев футеровки и атмосферы печи, на компенсацию тепловых потерь. Для печей, работающих в непрерывном режиме:

где Nз – мощность, необходимая для нагрева загрузки и прохождения физико-химических процессов в ней;
Nвсп – мощность, необходимая для нагрева вспомогательных приспособлений (лодочек, тиглей, конвейера и т. п.);
Nпот – мощность, необходимая для компенсации тепловых потерь.
Если печь работает в периодическом режиме, удобнее оперировать не мощностью, а количеством теплоты:

где Qпотр – энергия, потребленная печью за один цикл;
Qз – количество теплоты, необходимое для нагрева загрузки до заданной температуры и прохождения физико-химических процессов в ней;
Qвсп – количество теплоты, необходимое для нагрева вспомогательных приспособлений;
Qпот – тепловые потери;
Qак – количество теплоты, аккумулированное футеровкой печи.
2.1.2. Расчет полезной мощности
Теплоту, необходимую для нагрева загрузки и вспомогательных приспособлений, следует называть полезной Qпол, а соответствующую мощность – полезной мощностью Nпол.
Теплоту Qз рассчитывают исходя из термодинамики процессов, происходящих при термообработке загрузки. Если нагреваемый материал не испытывает химических и фазовых превращений, а поглощаемая теплота расходуется только на его нагрев, тогда:
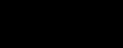
где Мм – масса одного моля вещества загрузки;
М – масса загрузки; с – теплоемкость загрузки;
Тн, Тк – начальная и конечная температуры загрузки.
В случае, когда функциональная зависимость теплоемкости от температуры неизвестна, можно приближенно принять:


где сс – усредненная теплоемкость загрузки;
сн – теплоемкость загрузки при Тн;
ск – теплоемкость загрузки при Тк.
Если в процессе термообработки происходят фазовые изменения в материале загрузки (плавление, испарение и т. п.), то следует учесть и теплоты, необходимые для этих процессов, тогда:
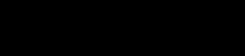
где Δiф – теплота фазового превращения;
Тф – температура фазового превращения;
с1 и с2 – теплоемкости исходной и образовавшейся фаз соответственно.
Теплоту, поглощаемую или выделяемую в результате химических реакций, находят исходя из уравнения (2.13):

где


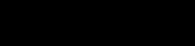
где

Для расчета соответствующих мощностей Nзн, Nзф, Nзх необходимо знать время нагрева загрузки tн до заданной температуры, тогда

Теплоту, необходимую для прогрева вспомогательных приспособлений (конвейер, лодочки, поддоны), рассчитывают суммированием по каждому элементу:

где Мi – масса i-го вспомогательного элемента;
сi – усредненная теплоемкость i-го элемента;
Ткi и Тнi – конечная и начальная температура i-го элемента.
Если через печь продувают специальную атмосферу, то следует учесть расход мощности на нагрев газа:

где qг – массовый расход газа;
сг – усредненная теплоемкость газа;
Тп » Тк – температура газа на выходе из печи;
Тн – температура газа на входе в печь.
Для садочных печей вся теплота, необходимая для нагрева газа:

где МГ – масса газа, прошедшего через печь за цикл термообработки.
В результате для полезной теплоты и полезной мощности имеем:


2.1.3. Расчет тепловых потерь
При расчете мощности, необходимой для компенсации тепловых потерь ЭПС, принимают, что печь работает в установившемся тепловом режиме, когда тепловые потоки постоянны во времени. Обычно ограничиваются расчетами потерь через стенки печи Nф и через отверстия Nотв:

где

Коэффициент запаса на неучтенные потери мощности (например, «старение» футеровки, потери через неплотности футеровки, через швы, тепловые короткие замыкания) принимают равным 1,2–1,4.
Расчет тепловых потерь в режиме стационарного переноса теплоты через стены печи сводится к решению задачи теплопередачи через многослойную плоскую либо цилиндрическую поверхность.
С достаточной для инженерных расчетов точностью можно перейти от идеального случая бесконечных поверхностей к реальной стенке печи, состоящей из j слоев футеровки, образующих i поверхностей с различной площадью. Например, для трех слоев теплоизоляции (см. рис. 2.1) уравнение, записанное для всей поверхности стенки, примет вид:
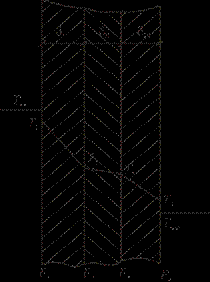
Рис. 2.1. Трехслойная плоская стенка:
Твн – температура внутри печи; Тi – температура на i-й поверхности теплоизолирующего слоя; Тнар – температура снаружи печи;
dj – толщина j-го слоя теплоизоляции; Fi – площадь i-й поверхности теплоизолирующего слоя
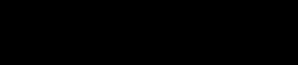
где aвн, aнар – коэффициенты теплоотдачи внутреннего (I) и наружного (III) слоев соответственно, Вт/м2 · К;
l J – коэффициент теплопроводности j-го слоя, Вт/м · К;
Fj – усредненная площадь j-го слоя, м2.
Так как l зависит от температуры материала футеровки, то в уравнение (2.22) подставляют усредненный коэффициент, взятый для средней температуры слоя, например, для III слоя

Поверхность Fj берут как среднее квадратичное площадей поверхности j-го слоя, например,

В частности, для трехслойной стенки (рис. 2.2) величина тепловых потерь примет вид:
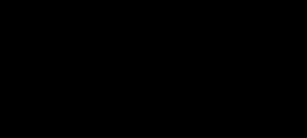
где di – диаметр i-й цилиндрической поверхности;
Нi – высота i-й цилиндрической поверхности;
Нj – усредненная высота j-го слоя футеровки.
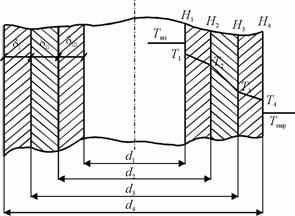
Рис. 2.2. Трехслойная цилиндрическая стенка
Высоту j-го слоя футеровки принимают как среднее арифметическое высот поверхностей этого слоя, например,

Теплоотдача от наружной стенки печи в окружающую среду носит сложный характер, поэтому для инженерных расчетов при условии Тнар = 20 0С и температуре поверхности печи (в описанных примерах это Т4), равной 40 0С, берут следующие значения коэффициента αнар:
– для вертикальной поверхности – 10,6 Вт/м2 · К;
– для верхней горизонтальной поверхности –12,0 Вт/м2 · К;
– для нижней горизонтальной поверхности –8,6 Вт/м2 · К.
Расчет футеровок проводят методом последовательных приближений:
1. Задают количество слоев, их толщину и материал футеровки, геометрические размеры печи и внутреннего пространства, температуру внутри печи (или на внутренней поверхности футеровки – Т1) и температуру снаружи.
2. Произвольно задаются значениями температур на i поверхностях теплоизолирующих слоев Тi.
3. Рассчитывают Fj или Нj и Тj.
4. По справочным данным на основании выбранной Тj определяют lj.
5. По уравнению (2.22) или (2.23) рассчитывают Nф.
6. Проверяют значения температур Тi, решая обратную задачу по отдельным слоям футеровки:
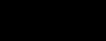
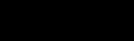

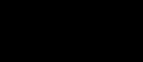
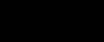
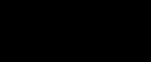
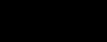
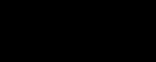
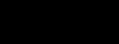
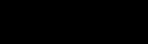
7. Сравнивают полученные значения Тi с заданными в начале расчета (п. 2). Если эти величины совпадают с достаточной точностью, то расчет считают законченным. В случае несовпадения задают новые Тi и расчет повторяют.
Тепловые потери через загрузочные и разгрузочные проемы, через отверстия в футеровке определяются составляющими теплообмена печного пространства с окружающей средой – конвекцией и излучением:
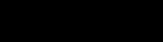

где Nотв.i – потери тепла через i-е отверстие;
Nк.i – потери тепла через i-е отверстие за счет конвекции;
Nи.i – потери тепла через i-е отверстие за счет излучения;
tоткр.i – время открытого состояния i-го отверстия, с;
tц – время термообработки загрузки (цикла).
Потери тепла через отверстие нагретой до 800–900 0С печи за счет конвекции можно определить по уравнению Доброхотова:
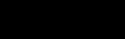
где Fотв – площадь сечения отверстия, м2;
h – высота отверстия, м;

Тп – температура печи, 0С.
Потери тепла через отверстие излучением описывает уравнение:
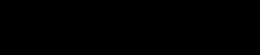
где εотв – коэффициент теплового излучения отверстия;
φ – коэффициент диафрагмирования.
Коэффициент теплового излучения для крупных отверстий и проемов (соизмеримых с размером печного пространства) берут равным 0,8, для мелких отверстий εотв = 1,0. Коэффициент диафрагмирования учитывает глубину отверстия и экранирующее действие его стенок (рис. 2.3).
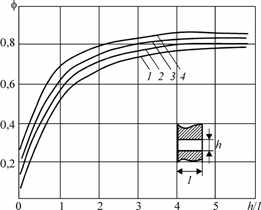
Рис. 2.3. Зависимость коэффициента
диафрагмирования от размеров отверстия:
1 – круглых; 2 – квадратных; 3 – прямоугольных с соотношением сторон 2 : 1; 4 – узких длинных щелей высотой h
Тепло, аккумулированное печью, находят по уравнению, исходя из теплоемкости и температур всех элементов конструкции печи:
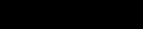
где Мi – масса i-го элемента конструкции;
сi – средняя теплоемкость i-го элемента конструкции;
Тi – средняя температура, до которой прогрет i-й элемент конструкции;
То – начальная температура элементов конструкции печи.