Курс лекций для специальности 140104 «Промышленная теплоэнергетика» москва 2011
Вид материала | Курс лекций |
Содержание3.8. Определение ориентировочного срока службы нагревателей 3.9. Порядок расчета нагревателей 4. Типовые конструкции камерных и проходных печей 4.1. Камерные печи 4.2. Проходные печи |
- Курс лекций для специальности 140104 «Промышленная теплоэнергетика» москва 2011, 1206.2kb.
- Курс лекций для студентов специальности 140104 «Промышленная теплоэнергетика» москва, 1244.1kb.
- Курс лекций для студентов специальности 140104 «Промышленная теплоэнергетика» москва, 877kb.
- Курс лекций для студентов специальности 140104 «Промышленная теплоэнергетика», 1246.47kb.
- Рабочая программа для студентов Vкурса по специальности 140104 промышленная теплоэнергетика, 69.12kb.
- Рабочая программа для студентов IV курса специальности 100700 промышленная теплоэнергетика, 243.31kb.
- Рабочая программа для студентов Vкурса специальности 290800. Промышленная теплоэнергетика, 63.46kb.
- Нисаев Игорь Петрович, д т. н., профессор учебно-методический комплекс, 356.38kb.
- Нисаев Игорь Петрович, д т. н., профессор учебно-методический комплекс, 329.37kb.
- Учебно-методический комплекс по дисциплине «экономика» Для студентов специальностей:, 1055.87kb.
3.7. Расчет размеров нагревателей
При расчете нагревательных элементов ЭПС, работающих при температуре выше 600 0С, исходят из ряда предпосылок:
– вся забираемая электропечью из сети мощность Nц выделяется в ее нагревательных элементах в виде тепла, при этом питающее напряжение U постоянно:

– нагреватель имеет неизменную длину l и постоянное сечение S, удельное электрическое сопротивление r при работе печи в заданном температурном режиме неизменно, тогда его сопротивление:

– выделенная на нагревателе энергия передается изделиям и кладке печи излучением с поверхности нагревателя Fн. Удельная поверхностная мощность нагревателя:

Для определения размеров нагревателя необходимо найти соотношения между его геометрическими и электрическими параметрами. Для нагревателя круглого сечения (проволока, стержень и т. п.) диаметром d эти соотношения описываются уравнениями:



где М – масса нагревателя;
rн – плотность материала нагревателя.
Если нагреватель изготовлен из ленты прямоугольного сечения со сторонами a и в, так что в = а · m, тогда
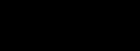
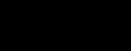

Используя в уравнениях (3.8), (3.9), (3.11), (3.12) в качестве W допустимую удельную поверхностную мощность, находим предельные минимальные значения массивности нагревателя.
После того как из уравнений (3.8) или (3.11) найдены d или а, необходимо подобрать проволоку или ленту из имеющегося сортамента материалов. Для этого следует взять ближайшие большие размеры. Далее необходимо повторить расчеты удельной поверхностной мощности с учетом конкретных выбранных геометрических параметров нагревателей.
Расчет геометрических размеров нагревательных элементов можно использовать для сравнения экономической целесообразности применения той или иной системы нагревателей. Например, можно сравнить капитальные затраты на материал, просчитав несколько вариантов систем нагревателей; можно сравнить эффективность различных электрических схем включения нагревателей, варьируя напряжением и сопротивлением отдельных фаз; можно выбрать оптимальное размещение нагревателей в рабочей зоне печи, найдя оптимальное соотношение длины и сечения нагревателя; можно подобрать электрические параметры для достижения заданной толщины нагревателя (заданного срока его службы) и т. д.
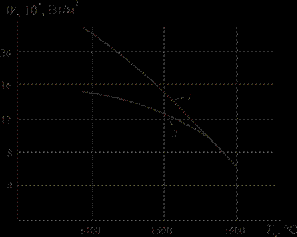
Рис. 3.9. Зависимость допустимой удельной поверхностной
мощности нагревателей из ДМ от температуры печи:
1 – при непрерывном регулировании; 2 – при релейном регулировании
3.8. Определение ориентировочного срока службы нагревателей
В процессе эксплуатации нагреватели «стареют», т. е. изменяют свои электрические параметры, что в конечном итоге приводит к необходимости их замены. Например, у нагревателей из хромоникелевых сплавов во время их работы в окислительной атмосфере увеличивается толщина окисленного слоя и уменьшается площадь токопроводящего сечения. Если принять скорость окисления vок постоянной во времени, тогда для круглого нагревателя
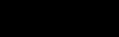
где n – отношение площади сечения окисленного слоя к первоначальной площади сечения нагревателя;
t – время работы нагревателя.
Для ленты прямоугольного сечения:
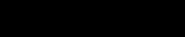
Скорость окисления vок для некоторых сплавов приведена на рис. 3.10.
Рекомендуется ориентировочный срок службы нагревателя принимать равным времени его работы, в течение которого сечение нагревателя окислится на 20% от первоначальной площади, т. е. когда n в уравнениях (3.14) и (3.15) достигнет 0,2. Исходя из этого условия срок службы нагревателя tс, будет равен:
– для нагревателя круглого сечения:
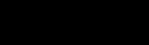
– для ленточного нагревателя:

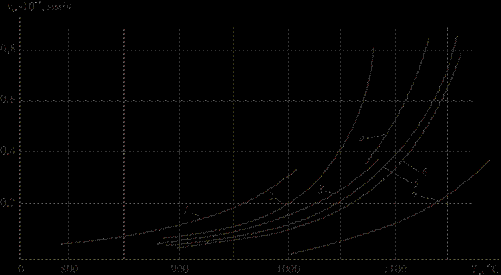
Рис. 3.10. Зависимость скорости окисления
от температуры нагревателя для различных сплавов:
1 – Х15Н60; 2 – Х25Н20; 3 – Х15Н60-Н; 4 – Х20Н80ТЗА;
5 – Х20Н80Т; 6 – Х20Н80; 7 – Х20Н80-Н
Срок службы нагревателей из железохромалюминиевых сплавов определяется уменьшением концентрации алюминия в их составе. Предельным состоянием сплава является момент, когда концентрация алюминия упадет до 1%. Для определения tс этих нагревателей используют уравнение:

где tс1 – срок службы нагревателя диаметром 1 мм.
Для нагревателей прямоугольного сечения под d подразумевают эквивалентный диаметр dэ, равный:

где


На рис. 3.11 приведены значения tс1 для ряда железохромоалюминиевых сплавов.
Срок службы нагревателей, работающих в различных средах, может быть рассчитан по такому же принципу, если известна скорость окисления, коррозии, изменения химического состава и электрических свойств материала нагревателя в этих средах. Скорость коррозии ряда металлических сплавов в углеродсодержащих средах приведена в справочной литературе, там же можно найти скорости испарения W, Mo, Nb и Ta в вакууме при различных температурах.
Срок службы нагревателей из дисилицида молибдена обычно до 10 000 ч при непрерывном регулировании, при периодическом режиме работы срок их службы уменьшается, что связано с термическим напряжением и частичным отслаиванием защитной пленки SiO2. Нагреватели из карборунда имеют срок службы от 500 до 2000 ч. Срок их службы зависит от температуры, режима работы и атмосферы. Так, например, чем выше температура нагревателя, тем больше скорость его «старения», при непрерывной работе срок службы значительно выше, чем при периодическом режиме, работа в восстановительной атмосфере снижает срок службы нагревателя.
Из формул (3.16)–(3.18) видно, что срок службы нагревателя тем больше, чем больше его диаметр или толщина. Следует также отметить, что на работу нагревателя с большим сечением меньше оказывают влияние дефекты сплава, из которого он изготовлен.
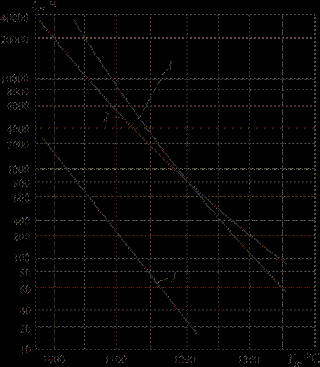
Рис. 3.11. Срок службы нагревателей из проволоки диаметром 1 мм
в зависимости от температуры для различных Fe–Cr–Al-сплавов:
1 – Х23Ю5; 2 – Х23Ю5Т; 3 – Х27Ю5Т
При выборе материала нагревателя и его сечения обычно ориентируются на такие условия эксплуатации, при которых срок его службы будет ориентировочно равен 10 000 ч.
3.9. Порядок расчета нагревателей
Порядок расчета нагревателей ЭПС определяется характером заданий: исходными данными и целью расчета. Рассмотрим ряд возможных вариантов:
1. Если перед расчетом нагревателя был проведен тепловой расчет печи, то конструктору известны мощность нагревателя N и площадь поверхности, на которой он будет расположен. При этом обычно известно питающее напряжение, что позволяет выбрать электрическую схему включения нагревателей, а следовательно, известно напряжение на нагревателях U.
В этом случае расчет нагревателя начинают с определения допустимой удельной поверхностной мощности Wд. Во время этого расчета выбирают материал нагревателя и его конструкцию, обеспечивающую необходимую рабочую температуру в печи. Затем определяют электрические параметры нагревателя, находят его геометрические размеры, выбирают конкретный размер из предлагаемого промышленностью сортамента. В завершение расчета проверяют возможность размещения нагревателя в печи и срок его службы.
При такой схеме расчетов рекомендуется рассчитать несколько возможных вариантов материалов нагревателя и его конструкций и выбрать оптимальный (из соображений экономики или удобств эксплуатации).
Если удельная поверхностная мощность слишком высока (выше допустимой), что приводит к высокой температуре нагревателя, то обычно переходят к материалам с более высокой рабочей температурой либо используют свободную поверхность рабочего пространства в печи для размещения большего количества нагревателей с большей Fн. Если в результате расчета выбранный нагреватель невозможно разместить на заданной поверхности либо если он слишком массивен, то рекомендуется перейти к материалу, позволяющему повысить удельную поверхностную мощность. Часто подобное затруднение удается разрешить, перейдя от проволочного нагревателя к ленточному.
2. В ряде случаев расчет ведут в обратном порядке: выбирают материал и массивность нагревателя, а затем по температуре, рекомендуемой для выбранного материала и сечения, приближенно определяют максимальную удельную мощность. По известной мощности печи и рассчитанной Wд определяют необходимую площадь поверхности для размещения нагревателей, после чего конструируют рабочее пространство печи и ее теплоизоляцию.
3. В печах с низкой удельной мощностью на выбор нагревателей не оказывает существенного влияния площадь поверхности рабочего пространства печи. В этом случае для расчета нагревателей можно задаться экономически целесообразным сроком службы нагревателей (например, 1 год или равным сроку амортизации печи) и наиболее выгодными электрическими параметрами.
4. Типовые конструкции камерных и проходных печей
Печи обычно являются последним переделом, от работы которого зависит качество продукции, поэтому к печам предъявляются следующие требования:
1. Достаточная тепловая мощность, обеспечивающая необходимый температурный режим для прохождения всех физико-химических превращений в обжигаемых изделиях.
2. Конструкция печей должна обеспечить наиболее эффективное сжигание подаваемого топлива, высокий коэффициент использования тепла, минимальные удельные расходы топлива.
3. Высокая удельная производительность с обеспечением высокого качества продукции.
4. Простота обслуживания, контроля и регулирования процесса обжига, возможность быстрого перехода с основного топлива на резервное.
По принципу работы различают печи периодического и непрерывного действия.
4.1. Камерные печи
Камерные печи относятся к печам периодического действия. Загрузку изделий, обжиг, охлаждение и выгрузку проводят последовательно в одном рабочем пространстве печи. На рис. 4.1 показана камерная печь с выкатным подом. Наличие выкатного пода позволяет осуществлять загрузку и выгрузку изделий вне рабочей камеры.
Создание новых высокоэффективных изоляционных материалов позволило создавать камерные печи с более тонкой футеровкой. На рис. 4.2 показана камерная печь с использованием волокнистых изоляционных материалов.
Камерные печи просты по конструкции, позволяют вести обжиг изделий по любому индивидуальному режиму. Существует большое количество камерных печей различных конструкций и размеров, работающих как на жидком и газообразном топливе, так и с использованием электронагрева.
Недостатками камерных печей периодического действия являются относительно низкая производительность, тяжелый физический труд при загрузке и выгрузке изделий, большой удельный расход топлива на обжиг изделий, т. к. значительное количество тепла поглощается кладкой (10–20 %) и отходящими газами (35–40 %).
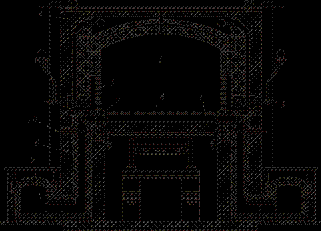
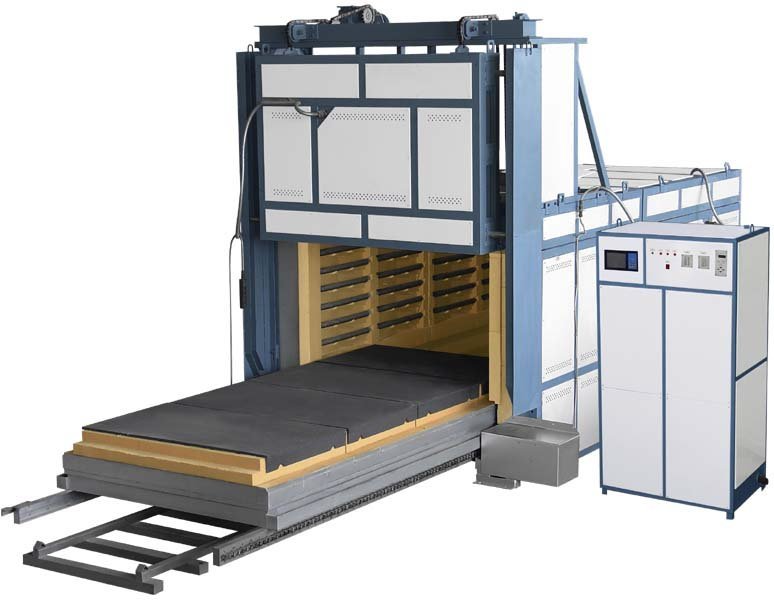
Рис. 4.1. Камерная печь с выкатным подом:
1 – вагонетка; 2 – рабочая камера; 3 – горелки; 4 – трубопровод горячего воздуха; 5 – распределительная решетка; 6 – решетчатый под вагонетки; 7 – окна для отвода газов; 8 – стояк; 9 – дымовой канал; 10 – шибер
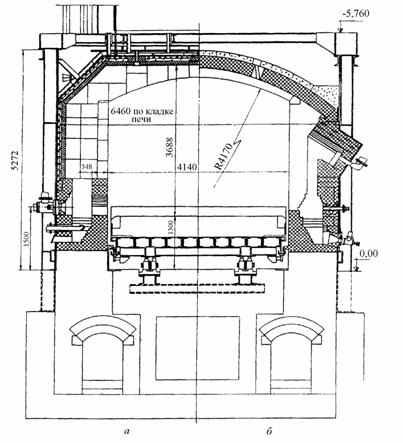
Рис. 4.2. Термическая печь с футеровкой из волокнистых материалов:
а) подвесной плоский свод; б) арочный свод
4.2. Проходные печи
Печи непрерывного действия (проходные) имеют большие преимущества перед печами периодического действия: более низкий удельный расход топлива, высокая производительность, лучшие условия труда.
Широкое распространение получили туннельные печи. Принципиальная схема туннельной печи показана на рис. 4.3. В зависимости от того, какие процессы протекают в печи, всю длину туннеля можно разделить на отдельные зоны. Обычно их четыре: сушки, подогрева, обжига и охлаждения. Каждая зона печи имеет свои конструктивные особенности и температурный режим, определенную длину в зависимости от вида обжигаемых изделий.
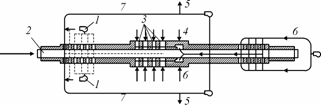
Рис. 4.3. Принципиальная схема туннельной печи.
1 – дымососы; 2 – загрузочный канал; 3 – окна подачи горячего воздуха в зону подогрева; 4 – окна подачи сжатого воздуха в эжекторы;
5 – коллектор выброса горячего воздуха; 6 – окна подачи топлива;
7 – трубопровод подачи горячего воздуха для сушилок
Зона сушки может работать как самостоятельное сушило, имеющее отдельный подвод и отвод сушильного агента, или как часть зоны подогрева, имеющая дымоотводящие каналы в стенках туннеля.
Зона подогрева начинается от сушила и кончается на границе с зоной обжига. Основное назначение зоны подогрева – равномерный подогрев изделий до температур, соответствующих графику обжига.
В зоне обжига, расположенной в средней части печи, поддерживают максимальные температуры, необходимые для завершения физико-химических процессов в изделиях. Воздух, необходимый для сжигания топлива, подают непосредственно по туннелю из зоны охлаждения (вторичный воздух). Продукты сгорания перемещаются по печному каналу навстречу движению вагонеток с изделиями и постепенно охлаждаются, передавая тепло изделиям.
Равномерность нагрева изделий зависит от заполнения печного канала продуктами сгорания, равномерности и скорости прохождения по сечению садки.
Зона охлаждения служит для охлаждения обожженных изделий до температур, обеспечивающих целостность изделий при выходе из печи. В зоне охлаждения происходит утилизация тепла, отбираемого от разогретых изделий.
Конструкция туннельных печей выбирается в зависимости от вида обжигаемых изделий.
При малой высоте и большой ширине рабочего канала свод печи делают плоским (подвесным), позволяющим лучше использовать объем печи. Печи с высоким рабочим пространством имеют арочный свод. Обычно печи строят с арочным или плоскоподвесным сводом в зоне обжига и с плоскораспорным – в зонах подогрева и охлаждения. На рис. 4.4 показаны туннельные печи с различными конструкциями свода.
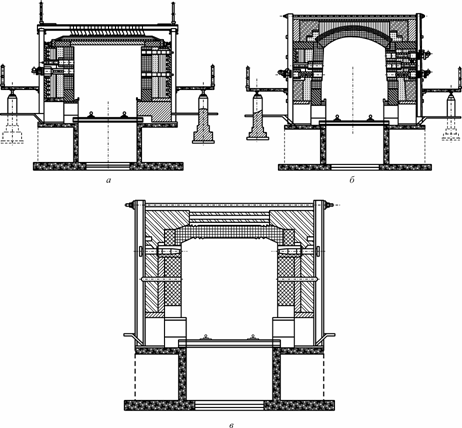
Рис. 4.4. Конструкция туннельных печей:
а) плоскоподвесной свод; б) арочный свод; в) плоскораспорный свод
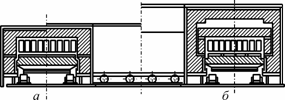
Рис. 4.5. Поперечный разрез кольцевой
туннельной печи по зонам:
а) сушки; б) обжига
Для герметизации печного канала туннельных печей применяют песочные или гидравлические затворы. Снижение до минимума подсосов холодного воздуха в рабочий канал обеспечивает конструкция кольцевой туннельной печи (рис. 4.5). Печь имеет горизонтальный кольцевой туннель с секциями сушки, разогрева, выдержки и охлаждения. Туннель установлен на опорной раме. Внутри туннеля расположен роторный под. Низкая садка и герметичность печи обеспечивают высокое качество и равномерность обжига. Одним из преимуществ подобных печей является рациональное использование площадей. Все тягодутьевые устройства могут размещаться в центре печи.
Возможность получения в зоне обжига температуры более 1900 0С обеспечивает конструкция печей с двойным сводом (рис. 4.6).
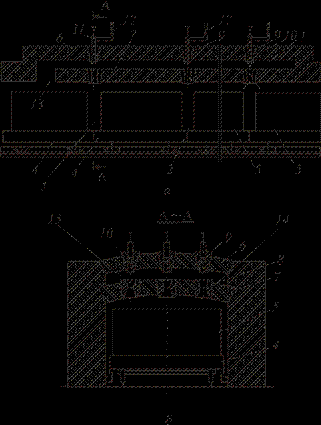
Рис. 4.6. Туннельная печь с двойным сводом:
а) продольный разрез; б) поперечный разрез
Туннельная печь имеет зону подогрева 1, зону обжига 2 и зону охлаждения 3. Внутри туннеля установлены вагонетки 4 с штабелями изделий 5. Туннель имеет в зоне обжига верхний 6 и нижний 7 своды, образующие горизонтальный сводовый канал 8. В верхнем своде
установлены горелочные камни 9 с горелками 10, которые снабжены устройствами 11 для регулирования выходного сечения сопел горелок и задвижками 12 для регулирования расхода газа. В нижнем своде выполнен проем 13 для подачи горячего воздуха из зоны охлаждения. Нижний свод содержит инжекторные устройства в виде горелочных камней 14 с отверстиями 15, расположенными соосно с горелками 10.
Для расширения диапазона регулирования температуры и повышения стойкости футеровки подобные туннельные печи снабжаются устройством для регулировки подачи горячего воздуха (рис. 4.7, б). В стенах печи на равных расстояниях друг от друга расположены вертикальные каналы с регулирующими устройствами, соединенные с горизонтальным сводовым каналом и устройствами для нагнетания холодного воздуха.
За счет регулирования подач горячего воздуха, идущего через проем в горизонтальный сводовый канал, и холодного воздуха, поступающего в этот канал через вертикальные каналы, достигается регулирование в широких пределах температуры и общего количества воздуха, идущего на горение.
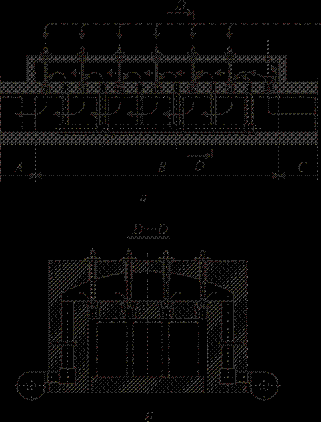
Рис. 4.7. Туннельная печь с устройствами
для регулировки подачи горячего воздуха:
а) продольный разрез; б) поперечный разрез
Преимуществом данной конструкции туннельной печи является возможность установления различных температурных режимов со сложным распределением температуры по длине печи.
Все описанные выше туннельные печи относятся к печам с периодическим проталкиванием вагонеток, что приводит к некоторой неравномерности обжига изделий.
Разработанная в Восточном институте огнеупоров конструкция туннельной печи с непрерывным движением вагонеток (рис. 4.8) обеспечивает равномерное распределение температуры по сечению печного канала как за счет непрерывного продвижения вагонеток, так и наличия сводовых коротко- и длиннопламенных горелок.
Туннельная печь имеет два параллельно расположенных печных канала 1 и 8, в которых происходит подогрев, обжиг и охлаждение изделий по заданному режиму. Каналы разделены стенкой 2 и имеют общий фундамент 3. Каналы перекрываются сводами 4, которые опираются на разделительную стенку и наружные стены 5. Внутри каналов имеются рельсовые пути 6, по которым транспортируют вагонетки 11 с изделиями 7 и 8. Перед сходным торцом каждого канала устанавливаются толкатели 9 и 10 с постоянной скоростью движения.
Капитальные затраты на строительство двухканальной туннельной печи снижаются примерно на 30 % по сравнению с капитальными затратами на строительство двух печей такой же производительности.
Кроме туннельных печей к проходным печам относятся роликовые и конвейерные печи.
Особенностью конвейерной печи прямого нагревания (рис. 4.9) является наличие плоского подвесного свода, что улучшает аэродинамический режим печи, уменьшает перепад температур в рабочем канале печи, сокращает расход топлива. Отопление печи производится с помощью шести инжекционных горелок. Тепловой коэффициент полезного действия составляет 24–26 %. Конвейерные печи прямого действия имеют удельный расход топлива почти в два раза ниже, чем
у конвейерных муфельных печей.
Схема роликовой печи показана на рис. 4.10. Конструктивно печной канал выполнен в виде щели с муфелем из карборундовых плит на всю длину. Изделия, установленные на поддоны из нержавеющей проволоки, перемещаются со скоростью 0,063 м/мин. Печь оборудована 16 инжекционными горелками с направлением продуктов сгорания под муфель и на него.
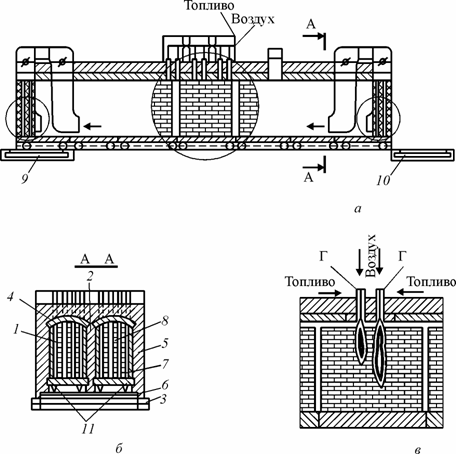
Рис. 4.8. Двухканальная туннельная печь с непрерывным движением вагонеток:
а) продольный разрез; б) поперечный разрез;
в) схема подачи топлива (Г – горелочные устройства)
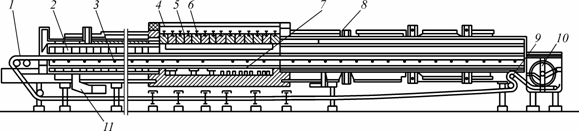
Рис. 4.9. Схема конвейерной печи прямого нагревания:
1 – металлическая лента конвейера; 2 – рабочий канал; 3 – ролик; 4 – двутавровая балка; 5 – свод; 6 – теплоизоляция; 7 – под печи; 8 – коробка отбора паров воды; 9 – натяжная станция; 10 – приводная станция;
11 – металлический дымоход
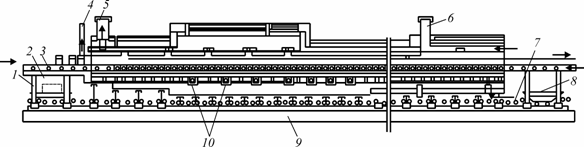
Рис. 4.10. Схема роликовой печи:
1 – каркас; 2 – привод нижнего рольганга; 3 и 7 – ролики; 4 – коробка отбора паров воды; 5 – коробка отбора печных газов; 6 – коллектор отбора горячего воздуха; 8 – конвейер возврата поддонов; 9 – фундамент; 10 – горелки

Рис. 4.11. Схема печи ПОК:
1 – патрубок для отбора дымовых газов; 2 – горелки; 3 – коллектор отбора горячего воздуха
Рабочий канал печи ПОК (печи обжиговые конвейерные скоростные конструкции НИИФ) выполнен в виде щелевидного туннеля, по которому перемещаются обжигаемые изделия, установленные на несущие столики конвейера. Рабочая поверхность столика представляет собой решетку из жаропрочного сплава Х20Н80. В зависимости от числа рядов столиков в печи различают однорядные (ПОК I) и двухрядные (ПОК II) печи. Печи типа ПОК представляют собой однотипные конструкции, различающиеся лишь размерами и системой отопления. Схема печи ПОК представлена на рис. 4.11. Все печи ПОК снабжены теплогенератором камерного типа, смонтированным на своде. Он предназначен для получения высокотемпературного теплоносителя, нагнетаемого в зону подсушки. Печи оборудованы 20 горелками ГНП-1. Для интенсивного и равномерного охлаждения обожженных изделий имеется устройство из нагнетающих и отсасывающих коробов, связанных с приточно-вытяжной вентиляцией.
Универсальной печью является разработанная НИИФ туннельная модульная печь. Особенностью данной печи является то, что она собирается из отдельных модулей, имеющих свое целевое назначение (модули обжига, подогрева и охлаждения). Таким образом, можно собрать печь с различными теплотехническими и технологическими характеристиками (длина печи; протяженность зон подогрева, обжига и охлаждения; конечная температура выдержки). Для строительства печи не требуется возведение фундаментов. В процессе работы любая секция печи (модуль) может быть быстро заменена или отремонтирована. Футеровка печи выполнена из высокоэффективных огнеупорных и теплоизоляционных материалов (в том числе волокнистых).
Модули подогрева и охлаждения конструктивно отличаются только тем, что в зоне подогрева имеются устройства для отбора дымовых газов, а в зоне охлаждения – устройства для подачи холодного воздуха. Модули зоны обжига снабжены горелочными устройствами. На рис. 4.12 показаны модуль обжига («а») и модуль подогрева (охлаждения) («б») универсальной модульной туннельной печи.
Данный вид туннельных печей позволяет не только снижать капитальные затраты при строительстве, но и без значительных затрат модернизировать производство при необходимости изменения ассортимента обжигаемых изделий.
Эффективность работы тепловых агрегатов в значительной мере зависит от конструкции топливосжигающих устройств. Конструкция горелок и форсунок зависит от типа печей и технологических задач, решаемых в процессе тепловой обработки, от производительности, требований техники безопасности и т. п.
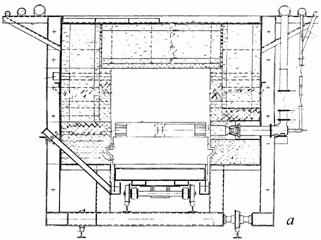
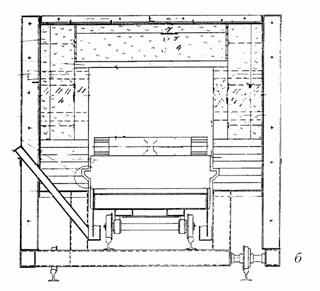
Рис. 4.12. Универсальная модульная туннельная печь:
а) зона обжига; б) зона подогрева (охлаждения)