Курс лекций для специальности 140104 «Промышленная теплоэнергетика» москва 2011
Вид материала | Курс лекций |
- Курс лекций для специальности 140104 «Промышленная теплоэнергетика» москва 2011, 1206.2kb.
- Курс лекций для студентов специальности 140104 «Промышленная теплоэнергетика» москва, 1244.1kb.
- Курс лекций для студентов специальности 140104 «Промышленная теплоэнергетика» москва, 877kb.
- Курс лекций для студентов специальности 140104 «Промышленная теплоэнергетика», 1246.47kb.
- Рабочая программа для студентов Vкурса по специальности 140104 промышленная теплоэнергетика, 69.12kb.
- Рабочая программа для студентов IV курса специальности 100700 промышленная теплоэнергетика, 243.31kb.
- Рабочая программа для студентов Vкурса специальности 290800. Промышленная теплоэнергетика, 63.46kb.
- Нисаев Игорь Петрович, д т. н., профессор учебно-методический комплекс, 356.38kb.
- Нисаев Игорь Петрович, д т. н., профессор учебно-методический комплекс, 329.37kb.
- Учебно-методический комплекс по дисциплине «экономика» Для студентов специальностей:, 1055.87kb.
6.3. Печи для выплавки электрокорунда
В промышленном производстве плавленолитых огнеупоров применяют только электродуговые печи, источником тепловой энергии в которых является электрическая дуга. В результате концентрированного выделения энергии в малых объемах в дуговых печах достигаются высокие температуры, необходимые для плавления шихт на основе тугоплавких оксидов Al2O3, ZrO2, Cr2O3, MgO, SiO2 и др. Электрическая дуга обеспечивает большую скорость нагрева, высокую производительность установок и требуемую чистоту выплавляемых изделий. Электрокорунд нормальный выплавляют в электрических дуговых трехфазных печах.
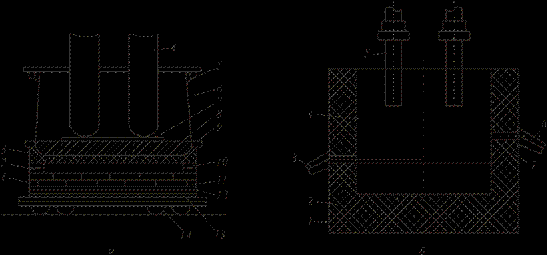
Рис. 6.4. Печи для плавки электрокорунда нормального:
а) подвижная: 1 – огнеупорная футеровка; 2 – углеродистый материал;
3 – корундовый слой; 4 – электрод; 5 – труба для водоохлаждения;
6 – стальной кожух; 7 – углеродный материал для розжига печи;
8 – слой боксита; 9 –водосборный желоб; 10 – магнезитовый кирпич;
11 –шамотный кирпич; 12 – шамотная подсыпка; 13 – асбест листовой; 14 – тележка;
б) стационарная: 1 – стальной кожух; 2 – под; 3 – летка для ферросплава;
4 – ванна; 5 – электрод; 6 – летка для электрокорунда; 7 – футеровка стенок печи
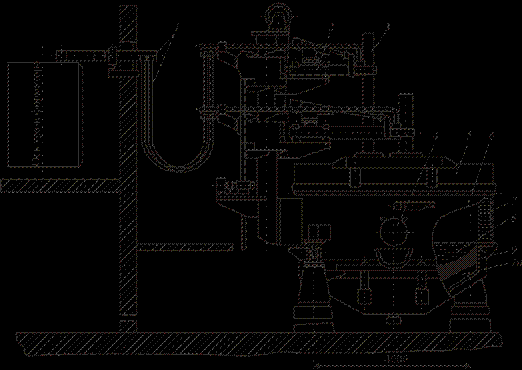
Рис. 6.5. Электродуговая печь РКЗ–6:
1 – короткая сеть; 2 – электрододержатель; 3 – электрод; 4 – заслонка сливного отверстия; 5 – свод; 6 – кожух; 7 – огнеупорная футеровка; 8 – расплав; 9 – гарнисаж; 10 – подина
Плавку «на блок» ведут в электропечах мощностью 1,0–4,5 мВ · А, «на выпуск» – в электропечах мощностью 10,5–16,5 мВ · А. Для плавки «на блок» используют подвижные электропечи. Печь (рис. 6.4, а) состоит из пода 1–3, 10–13, кожуха 6, электродного хозяйства (прессованных или набивных самоспекающихся непрерывно действующих электродов 4, электродных зажимов, электродных лебедок), тележки 14 и электрической короткой сети. Тележка рассчитана так, чтобы выдерживать массу наплавленного электрокорунда и всей непроплавленной шихты, а также массу электродов.
Под печи представляет собой кожух, диаметр которого на 300–500 мм больше кожуха печи. Футеровка пода многослойная. На днище подового кожуха укладываются: 3–4 листа асбеста общей толщиной 10–20 мм, шамотная подсыпка толщиной 40–50 мм, шамотный кирпич – 200–250 мм, отсевы мелочи (до 50 мм) электрокорунда – до верха пода. На подготовленный под устанавливают кожух печи. Кожух обычно имеет форму усеченного конуса с разницей в диаметре верха и низа 150–200 мм. Сверху кожух имеет реборду, выступающую на 150–200 мм. Под ребордой установлена труба с отверстиями для водяного охлаждения кожуха. Несколько выше нижнего края кожуха (200–250 мм) к кожуху приварен водосборный лоток. Кожух не футеруется, футеровкой служит гарнисаж 9 (рис. 6.5) – непроплавленная шихта между кожухом и расплавом в печи, образующаяся вследствие водяного охлаждения кожуха.
Плавку «на выпуск» ведут в стационарных дуговых печах (рис. 6.4, б и рис. 6.5).
На рис. 6.5. представлена печь РКЗ–6. Печь наклоняющаяся, закрытая сводом, снабжена тремя графитированными электродами, расположенными в ванне печи по вершинам равностороннего треугольника. Загрузка печи производится труботечкой через отверстие, расположенное в центре свода.
Основными частями печи являются кожух, который служит для формирования футеровки ванны и на котором устанавливаются узлы печи; свод; направляющие стойки электрододержателей и приводы механизмов перемещения электродов. Кожух сварной из толстолистового металла, составлен по высоте из двух соосно расположенных частей с разными диаметрами. Днище кожуха выполнено в виде усеченного конуса. В кожухе имеется отверстие для слива расплава, которое закрывается дверцей при помощи пневмопривода, и окно для выравнивания поверхности шихты, выемки огарков электродов и других технологических целей, закрываемое водоохлаждаемой дверцей.
Характеристика электродуговой печи РКЗ–6: установленная мощность трансформатора 8000 кВ · А; номинальная мощность печи 6000 кВ · А; пределы напряжения 120–318 В; максимальный ток на электродах 11–13 кА; диаметр распада электродов (диаметр окружности, проведенной через центры электродов) 1100–1300 мм; диаметр электродов 300 мм; масса расплава по сливу 5 т; внутренние размеры кожуха печи: диаметр нижней части 4500 мм, диаметр верхней части 5000 мм, высота 3300 мм; размеры плавильного пространства: диаметр ванны 3300 мм, глубина ванны 500 мм, общая высота 2200 мм; расход воды на охлаждение 120 м3/ч.
Ванна печи круглая, стены футерованы высокоглиноземистым кирпичом, подину набивают шлифзерном плавленого корунда. За счет интенсивного охлаждения на всей поверхности ванны из расплава образуется гарнисаж. Свод обеспечивает работу печи в закрытом режиме и снижает тепловые потери. Свод футерован слоем огнеупорной замазки, имеет пять отверстий: три для электродов, по одному для загрузки шихты и для выпуска газа.
Для слива расплава печь наклоняют на угол до 30о механизмом наклона, работающим в ручном и автоматическом режиме.
Короткая сеть и гибкий токопровод служат для передачи тока от выводов обмоток низкого напряжения от одного печного трансформатора к токоведущим трубам электрододержателей. Система водоохлаждения электропечи включает элементы охлаждения электрододержателей и гибкого токоподвода, свода и кожуха печи.
6.4. Выбор рабочих токов, напряжений и геометрических размеров ванн руднотермических печей
Значения токов и напряжений электропечных трансформаторов являются важнейшими параметрами руднотермических печей, т. к. они не только обеспечивают рациональные технологические режимы печей, но и позволяют рассчитать их геометрические размеры. При расчете токов и напряжений целесообразнее всего использовать уравнение
Uп =

где Uп – полезное напряжение на электроде (падение напряжения между электродом и подом печи);
Рп – полезная мощность (мощность на электроде);
С и n – постоянные, определяемые экспериментально на действующих печах (для руднотермических печей n = 0,250,33).
Для определения тока и напряжения электропечного трансформатора с учетом активного r и реактивного x сопротивлений электропечного контура уравнение (5.1) представляется в следующей форме:
Uп = C(Pфhcosj)n, (6.2)
где Рф – полная мощность фазы; h – электрический кпд; cosj – коэффициент мощности.
Введем обозначение g =

Uф =

откуда

Зная g, легко определить остальные величины, описывающие характеристики печной установки:
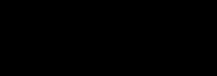
Фазная мощность определяется из уравнения
Рф =
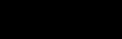
где Q – годовая производительность, т;
q – удельный расход электроэнергии, МВт · ч/т;
КВ =

tр, tк – рабочее и календарное время;
КМ =

Рср, Рмакс – средняя и максимальная активная мощность, МВт; n – число фаз.
Знание основных электрических параметров позволяет рассчитать геометрические размеры ванны печи. Их следует выбирать так, чтобы во всем объеме нормально протекал технологический процесс, в печи отсутствовали зоны перегрева, а футеровка печи не испытывала повышенных тепловых нагрузок.
Основные размеры при расчете печи: диаметр ванны Dв, диаметр распада Dр, диаметр тигля Dт и высота ванны (горна). Принято все основные размеры выражать через диаметр электрода, т. е. Dв = КвDэл; Dр = КрDэл; Dт = = КтDэл; Нг = КгDр = КрDэл.
Диаметр электрода рассчитывают по уравнению
Dэл =

где Iэл – ток в электроде;
jэл – допустимая плотность тока в электроде.
Для самоспекающихся электродов jэл ≈ 4


В зависимости от значений Кт и Кр тигли либо не соприкасаются между собой, либо соприкасаются, но в центре остается «холодная» зона, либо эта зона отсутствует, но существуют зоны перегрева. Значения Кт зависят от теплофизических характеристик шихты и процесса плавки. Оптимальным вариантом для фосфорных печей является Кр = 2,5, при этом реакционные зоны пересекаются и вместо «холодной» образуется «горячая» зона, улучшающая ведение технологического процесса.
Для электротехнических расчетов необходимо знать удельное сопротивление (удельную электропроводность) в отдельных зонах печи. Зависимость активной удельной проводимости c гетерогенных систем от параметров жидкости и твердого материала описывается уравнением
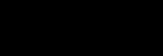
где c1 – удельная электропроводимость жидкой фазы, См;
c2 – удельная электропроводимость твердой фазы, См;
d – средний диаметр кусков твердой фазы.
Приведенное уравнение содержит три коэффициента – А, В и С. Такие факторы, как давление, форма и характер поверхности твердых частиц определяют значения коэффициентов А и С. Коэффициент В зависит от свойств среды, находящейся в узких зазорах между твердыми поверхностями, и отвечает за влияние этой среды на контактные сопротивления. F – структурный фактор,

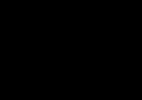
Для полидисперсных сред можно применять уравнения Брюггемана (6.10) или Мередита и Тобиаса (6.11):

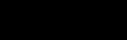
Уравнение (5.8) хорошо описывает экспериментальные данные по проводимости двухфазных систем проводящий углеродистый материал (антрацит, кокс)–раствор электролита в интервале соотношений

Практическая применимость уравнения для расчета удельного сопротивления как сухих засыпок проводящего материала, так и для гетерогенных смесей была подтверждена на основании математической обработки многочисленных литературных и экспериментальных данных, при этом расхождение между расчетом и экспериментом составляло не более 10–15 %.
Таблица 6.3 Состав шихты для плавки технического кремния
|
6.5. Печи для производства карбида кремния
Для производства карбида кремния служат керновые печи сопротивления, которые могут быть стационарными или передвижными. В настоящее время в основном используются самоходные печи. Самоходная электрическая печь сопротивления (рис. 5.6) состоит из пода, боковых и торцевых стенок, смонтированных на подвижной платформе. Платформа сварена из швеллеров, имеет ходовую часть из 6–8 колесных пар. На платформе установлены чугунные колосники, образующие под гамачного типа. Колосники изолированы от платформы шамотными кирпичами. Боковыми стенками печи служат чугунные перфорированные щиты, укладываемые на закраины пода. Щиты крепятся с помощью стоек, между отдельными щитами выкладываются электроизолирующие слои из шамотного кирпича. Торцевые стенки печи представляют собой железобетонный каркас, заполненный кладкой из шамотного кирпича. В каркасе монтируют рабочие и изолирующие электроды. Для прочности кладка торцов стягивается металлическими накладками. Рабочим электродом является пакет из четырех угольных блоков размером 400


Мощность самоходных печей, эксплуатируемых на отечественных заводах, в настоящее время 3–4 МВт. Увеличение мощности печей за последние годы происходило за счет увеличения длины при сохранении неизменного поперечного сечения (ширина загрузки 2,4–2,6 м, ширина керна 0,8–1,0 м). Благодаря такому подходу стало легче осваивать новые, более мощные печи, поскольку тепловой режим существенных изменений не претерпевал, но при этом значительно возросло рабочее напряжение электрического тока. Так, при повышении мощности от 1,8 до 3,0 МВт напряжение на печи увеличилось с 250 до 400 В.
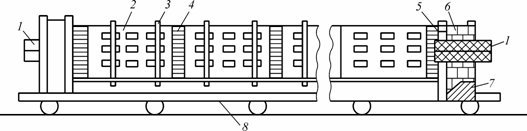
Рис. 6.6. Самоходная печь для производства карбида кремния:
1 – рабочие электроды; 2 – боковые щиты; 3 – стойки боковых щитов; 4 – изолирующая кирпичная кладка; 5 – изолирующие угольные прокладки; 6 – торцевая стенка из огнеупорного кирпича; 7 – бетонный корпус торцевой стенки; 8 – тележка
Дальнейшее увеличение мощности по этому принципу нецелесообразно, т. к. значительно возрастут расходы на специальную высоковольтную аппаратуру для работы в условиях высоких температур в запыленной и влажной среде, увеличится опасность шунтирования тока по корпусу печи, а также затруднится обслуживание печей во время производственного процесса.
Основное сырье для производства карбида кремния – кремнеземсодержащий материал и углеродистый восстановитель, а также древесные опилки или подсолнечная лузга и поваренная соль (для зеленого карбида кремния). Кроме того, используют некоторые вспомогательные (угольные электроды, огнеупорный кирпич) и возвратные (аморф, старая шихта) материалы.
Расчет электрических характеристик печи проводится следующим образом.
Для определения мощности трансформатора служит формула
Nф =
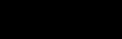
где Q – годовая производительность, т;
q – удельный расход электроэнергии, МВт · ч/т;
КВ =

tр, tк – рабочее и календарное время;
КМ =

Nср, Nмакс – средняя и максимальная активная мощность, МВт;
n – число фаз.
Производительность Q принимается равной Q =

где А – производительность всего производства, а n – количество устанавливаемых печных трансформаторов. Величину n принимают кратным трем (3, 6, 9) и подбирают так, чтобы мощность печного трансформатора соответствовала достигнутому уровню техники создания печей карбида кремния (4000–5000 кВ А). Значение cosj для данного типа печей равно 0,9–0,95. Коэффициент использования времени КВ можно принимать равным 0,90–0,93. Коэффициент использования мощности определяют по формуле:
КМ =

где W – потребление энергии за цикл;
tц – время нахождения печи под током в цикле;
Nмакс – максимальная активная мощность печи.
Исходные данные при расчете КМ применяют в соответствии с материалами данных эксплуатации, обычно КМ = 0,850,90. Удельный расход электроэнергии для черного карбида лежит в пределах 7500–8000 кВт · ч/т,
а для зеленого 9000–10000 (кВт · ч)/т.
Для определения геометрических параметров керна используют следующие зависимости:
Nк = 2wL(h + b); (6.14)
Nк =

где Nк – мощность на керне, Вт;
w – удельная мощность на поверхности керна, приведенная к размерам керна в начале электротермического процесса, Вт/м2;
L – длина керна, м;
h, b – высота и ширина поперечного сечения керна, м;
U – напряжение на керне, В;
r – удельное сопротивление материала керна, приведенное к размерам керна в начале электротермического процесса, Ом м.
В уравнении (6.14) керн рассматривается как источник тепловыделения, у которого с каждого 1 м2 поверхности выделяется w, Дж/с. В уравнении (6.15) керн рассматривается как проводник, в объеме которого теплота выделяется по закону Джоуля – Ленца.
Совместное решение уравнений (6.14) и (6.5) позволяет определять любые две величины, если заданы остальные входящие в них величины. Как правило, задаются следующие показатели:
– средняя мощность на керне Nк ср, которую определяют исходя из мощности печной установки N, ее электрического кпд h и cosj; значение h выбирают в интервале 0,90–0,95 в зависимости от активного сопротивления печи, короткой сети и печного трансформатора
Nк ср = N hcosj; (6.16)
– номинальная удельная мощность на керне w выбираемая в интервале 6–9 Вт/см2 в зависимости от крупности и химического состава сырья;
– удельное сопротивление материала керна r, значение которого практически принимают равным 0,10–0,20 (для начального периода) и 0,04–0,05 Ом м (для конечного);
– максимально допустимое напряжение на керне в начале процесса Uн, принимаемое равным 350–450 В;
– технически целесообразная высота керна h, равная 30–50 см.
Ширина керна при этом находится по заданной высоте h:
b =
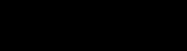
(где К – коэффициент, учитывающий изменение мощности в течение процесса; обычно для начальной стадии Кнач = 0,50,7, а для конечной Ккон = 1,01,2), а длина

Для определения электрических параметров печи в первую очередь находят активное сопротивление керна. Для этого существуют два метода: непосредственный расчет с использованием средних удельных сопротивлений материала и с применением обобщенных формул, полученных статистической обработкой экспериментальных данных.
В первом случае активное сопротивление печной установки Rпу определяют по формуле:
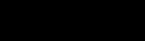
где RK – сопротивление керна;
RГ – сопротивление графита;
RSiC – сопротивление слоя карбида кремния, учитывая, что:
– для керна начальное rк = 0,200,22 Ом см, конечное rк = 0,06 Ом см;
– для графита rг = 0,81,2 Ом см;
– для карбида кремния rSiC = 0,33 Ом см.
По второму методу активное сопротивление печной установки находят по формуле
Rпу =

где rг = 0,22 Ом см – удельное сопротивление графита керна;
L – длина печи, м;
W – расход электроэнергии за время процесса, КВт ч;
d = (0,3 10–4–1,8 10–2)L – коэффициент, зависящий от длины;
Sг – поперечное сечение графитового керна в начале процесса, м2.
Например, активное сопротивление печи длиной 17 м в конце процесса составляет для керна сечением:
0,7x0,35 м – 18,5 МОм;
0,8x0,4 м – 14,5 МОм;
0,9x0,45 м – 12,3 МОм.
Отношения максимального сопротивления в начале процесса к конечному: К1 =


Типоразмер трансформатора выбирают следующим образом. Определив активные сопротивления шихты Rнач и Rкон, рассчитывают рабочие токи в конце и начале процесса:
Iкон =


где Nп = Nhcosj – максимальная полезная мощность печи, КСнач = 0,7 – коэффициент, учитывающий снижение мощности в начале процесса.
Затем находят значения рабочих напряжений в начале
Uнач =

и в конце процесса

Полученные величины позволяют выбрать типоразмер трансформатора.