Алтгту управление качеством образования, продукции и окружающей среды Материалы 2-й Всероссийской научно-практической конференции 5 6 июля 2007 года Бийск 2007
Вид материала | Документы |
- Актуальные социально-экономические и правовые аспекты устойчивого развития региона., 2089.17kb.
- «Научно методическое сопровождение развития воспитательной системы школы», 1236.2kb.
- Материалы Всероссийской научно-практической конференции Часть I москва Челябинск 2010, 4034.01kb.
- Д. Г. Кайрак из аула Себеляк: новый памятник сибирско-татарской эпиграфики*, 117.2kb.
- Брюссельская декларация о панъевропейской повестке дня предстоящей белградской конференции, 214.8kb.
- Статьи Общественные науки Философия, 2270.54kb.
- Ассоциация гимназий санкт-петербурга воспитательные подходы и системы в современном, 7121.33kb.
- Программа всероссийской научно-практической конференции «ребенок в современном обществе», 215.18kb.
- Отчет по научно-исследовательской работе студентов автф за 2007, 1838.43kb.
- Материалы ii-ой региональной научно-практической конференции, посвященной 20-летию, 2422.21kb.
Поиск путей управления качеством сборочных процессов с использованием имитационного моделирования
Е.А. Воронина, Е.Ю. Татаркин, А.А. Панов
Алтайский государственный технический университет
им. И.И. Ползунова, г. Барнаул
Дано описание разработанной системы моделирования процесса формирования погрешности замыкающего звена размерных цепей, позволяющей путем виртуальных экспериментов проверять при исследованиях уровень достоверности теоретических зависимостей.
При исследовании процесса формирования точностных параметров замыкающих звеньев размерных цепей необходима экспериментальная проверка полученных теоретических зависимостей. Так как в реальных условиях данный эксперимент провести весьма сложно из-за трудоемкости и больших временных затрат, то была создана имитационная математическая модель.
Система моделирования процесса формирования погрешности замыкающего звена размерных цепей (SMPFP) предназначена для моделирования процесса формирования погрешности замыкающего звена размерных цепей и реализует все процедуры, связанные с созданием исходных массивов значений размеров (отклонений) составляющих звеньев и массива размеров замыкающего звена.
Для создания математической модели была выбрана среда программирования Borland Delphi, которая является объектно-ориентированной средой разработки 32-битных приложений, с большим числом библиотек, содержащих огромное количество функций, мощным графическим ядром и библиотекой визуальных компонентов. Среда позволяет формировать массивы по любым заданным формулам, сводить данные в таблицы и отображать полученные данные на графиках, причем написанные программы имеют удобный и понятный для любого пользователя интерфейс. Совместимые с Windows-приложениями результаты, полученные в программах, написанных в этой среде, легко сохраняются для их возможного дальнейшего использования.
Разработанная модель состоит из управляющей программы и ряда независимых программ, каждая из которых способна выполнять поставленные перед нею задачи. Связи по информации между автономными программами осуществляются через буфер обмена, связи по управлению – через управляющую программу.
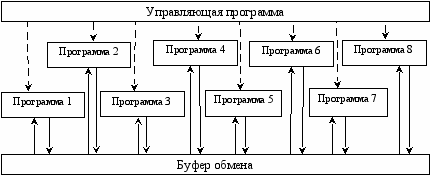
Рисунок 1 – Структура программного обеспечения
Описание программы 1. Формирование размеров. Программа предназначена для формирования массивов размеров по указанному в диалоге закону, графического отображения полученных результатов, а также вывода их в текстовом виде. Программа реализует задачи упорядочивания и перемешивания массивов.
Описание программы 2. Формирование групп. Программа предназначена для формирования групповых массивов путем разбиения заданного массива на указанное число групп, перемешивания элементов массива внутри групп, построения гистограмм, печати полученных результатов графически и в текстовом виде.
Описание программы 3. Распределение Хи-квадрат. В программе реализована задача статистического анализа распределения, то есть вычисления критерия 2 и оценка соответствия любому из указанных законов.
Описание программы 4. Суммирование векторов. Программа предназначена для формирования случайной величины R, которая является радиус-вектором при двумерном распределении.
Описание программы 5. Теорема косинусов. Программа предназначена для формирования суммарного вектора из двух исходных с заданными направлениями путем сложения исходных векторов по теореме косинусов.
Описание программы 6. Суммирование векторов через проекции. Программа предназначена для формирования суммарного вектора из двух исходных путем сложения проекций исходных векторов на координатные оси.
Описание программы 7. Суммирование координат. Программа предназначена для суммирования координат xi и yi исходных радиус-векторов.
Описание программы 8. Расчет смешанных цепей. Программа предназначена для формирования массива значений размеров замыкающего звена смешанных размерных цепей, в состав которых входят статические и динамические звенья. Расчет ведется вероятностным методом. Количество звеньев, входящих в состав размерной цепи, не ограничено.
Управляющая программа, является связующим звеном всех вышеперечисленных программ.
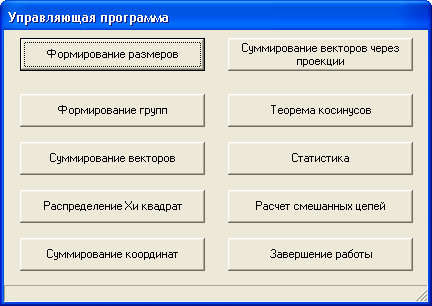
Рисунок 2 – Диалог управляющей программы
На разработанное программное обеспечение получено свидетельство об официальной регистрации № 2006610055 от 10.01.2006 года.
Управление качеством при шлифовании деталей с износостойкими покрытиями
Я. Г. Мостовая, А. А. Ситников
Алтайский государственный технический университет
им. И.И. Ползунова, г. Барнаул
Экспериментальные исследования шлифования деталей с износостойкими покрытиями выявили зависимости параметров шероховатости и силы резания от режимов резания и характеристик инструмента.
Износостойкие покрытия подвергаются различным видами механической обработки – точению, шлифованию, хонингованию, суперфинишированию, полированию и другим. Наибольшее распространение получила обработка шлифованием, так как позволяет обеспечить требуемые параметры качества детали при высокой производительности. Однако в связи с особенностями физико-механических свойств износостойких покрытий шлифование имеет существенные отличия, обусловленные выбором характеристик инструмента и режимов резания.
Анализ имеющихся в литературе исследований операции шлифования деталей с покрытиями показал, что приведенные сведения о параметрах качества имеют разрозненный характер, не представлены исследования силы резания при шлифовании.
Для установления необходимых закономерностей были проведены экспериментальные исследования. Эксперименты проводились в лабораториях кафедр технологии автоматизированных производств и технологии машиностроения Алтайского государственного технического университета имени И.И. Ползунова. Опыты выполнялись на кроглошлифовальном станке 3Е153. В качестве объектов исследования использовались следующие образцы: валики – длина L = 320 мм и 180 мм, диаметр d = 20 мм и 75 мм, материал – сталь 20. На образцы напыляли покрытия из порошкового материала Al2O3.
Условия проведения экспериментов: твердость круга С1 и СМ2, минутная подача Sn = 0,57 и 0,26 мм/мин; скорость детали Vд = 36,4 и 12,8 м/мин и зернистость 400…320 мкм для электрокорунда белого 24А и 400…50 мкм для карбида кремния зеленого 64С.
Образцы с плазменно-напыленным оксидом алюминия обрабатывали кругами с различной зернистостью и связкой АС4 160/125 Б1 100, АС4 125/100 Б1 100, АС4 80/63 Б1 100, АС4 40/28 Р1 50. Глубину резания варьировали на трех уровнях: тонкое шлифование t =0,005…0,01 мм, чистовое шлифование t =0,02…0,08 мм, черновое шлифование t = 0,1…0,2 мм. Скорость шлифовального круга 35 м/с, скорость изделия (продольная подача) Vи = 5 и 10 мм/мин, поперечная подача стола Sпоп = 3 и 5 мм/ход.
С целью повышения производительности сбора и обработки экспериментальных данных была сконструирована и изготовлена автоматизированная система, которая включает в себя следующее: объект исследования (деталь, инструмент), методическое, программное, информационное обеспечение, аппаратные средства, специальную оснастку.
В состав аппаратных средств входят: первичные измерительные средства (динамометр, датчик профилографирования, датчик фазового положения); тензометрический усилитель; АЦП «многофункциональная плата ввода/вывода ЛА-70МЗ»- 6; компьютер; принтер. Специальная оснастка представляет собой устройства для размещения и крепления измерительных преобразователей, оправок, устройства для медленного вращения детали при записи профиля обработанной поверхности. Для контроля параметров шероховатости поверхности образцов применялся профилограф - профилометр модели 250 завода «Калибр». Он позволяет получать за один проход измерительного щупа сразу несколько показателей (Ra, Rz, Rmax и другие). Для измерения сил резания при круглом шлифовании используются тензоцентра.
Результаты экспериментов показали, что при шлифовании алмазными кругами глубина резания, скорости поперечной и продольной подачи не являются доминирующими в формировании параметров качества плазменного покрытия. При изменении глубины резания в широких пределах, соответствующих режимам тонкого, чистового и чернового шлифования (у инструмента с одной зернистостью), параметр среднего арифметического отклонения профиля Ra оставался в пределах одного класса. Существенного снижения шероховатости можно достичь использованием кругов на каучуковой связке Р51. В основном высотные и шаговые параметры микронеровностей определяются формой и размерами пор, а также характером их распределения в объеме материала.
Проведенные экспериментальные исследования операции шлифования деталей с износостойкими покрытиями позволили исследовать влияние режимов резания и характеристик инструмента на силу резания и шероховатость поверхности. Полученные результаты исследования позволяют управлять качеством деталей с износостойкими покрытиями на этапе проектирования операции шлифования путем назначения оптимальных режимов резания и выбора инструмента.
Стохастическое моделирование процесса шлифования деталей с износостойкими покрытиями
Я. Г. Мостовая
Алтайский государственный технический университет
им. И.И. Ползунова, г. Барнаул
Модель расчета шероховатости при шлифовании деталей с износостойким покрытиями позволяет учесть особенности обработки покрытий, назначить оптимальные режимы резания, выбрать характеристику инструмента и в конечном итоге обеспечить качество продукции.
Одним из ответственных этапов в технологии получения деталей с покрытиями является их окончательная механическая обработка. Износостойкие покрытия подвергаются различным видам механической обработке – точению, шлифованию, хонингованию, суперфинишированию, полированию и др. Шлифование широко используется при изготовлении деталей с износостойкими газотермическими покрытиями, так как позволяет обеспечить требуемые параметры качества при высокой производительности. Покрытия на основе карбидов вольфрама и керамики могут быть эффективно обработаны только шлифованием.
При проектировании операции шлифования и выборе режимов шлифования следует учитывать, что обработка покрытий отличается от обработки материалов, имеющих аналогичных химический состав, но полученных другими способами. Это определяется физико-механическими характеристиками напыленных материалов, наличием пористости в покрытии, особенностями процессов, происходящих при нанесении покрытий, различной прочностью сцепления с основой и другими факторами.
Одним из способов уменьшения затрат на проведение большого объема экспериментальных работ является создание математической модели, которая, учитывая механику процесса алмазно-абразивной обработки, позволит имитировать эксперимент. Это класс имитационных моделей. Естественно, что имитационные модели основываются на экспериментальных данных. Однако объем экспериментов для их построения значительно меньше, чем при разработке эмпирических зависимостей, так как требуется не столько получение численных значений каких-либо параметров процесса, сколько выяснение и описание механизма происходящих явлений. Таким образом, построение имитационных моделей является предпочтительным.
Процесс шлифования износостойких покрытий сопровождается двумя явлениями: объемного разрушения (рисунок 1 а, б) и микрорезания (рисунок 1 в, г).
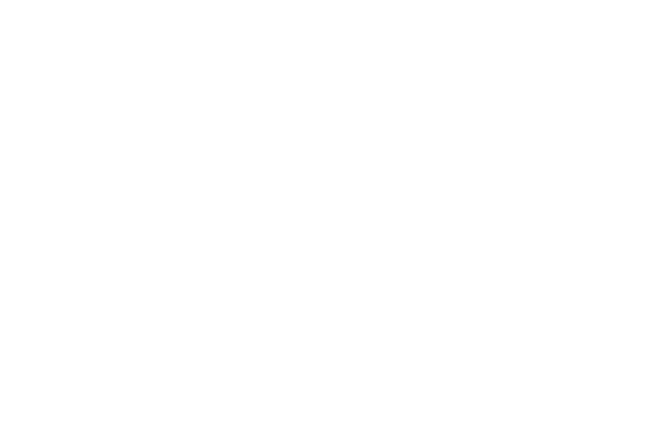
Рисунок 1 – Механизм образования микрорельефа поверхности
износостойкого покрытия при шлифовании
Поскольку размеры режущей части зерен в десятки раз меньше, что размеры пор, можно сделать предположение, что на параметры шероховатости обработанной детали процесс непосредственного срезания зернами шлифовального круга материала покрытия (микрорезания) будет оказывать минимальное влияние.
В основе разработанной математической модели лежит имитационный подход, который заключается в следующем:
- профиль обработанной поверхности детали формируется в процессе трещинообразования в материале покрытия при взаимодействии инструмента и заготовки;
- в процессе трещинообразования участвуют поры напыленного слоя, линия роста микротрещины проходит от поры к поре;
- координаты пор покрытия являются случайными параметрами и распределяются по заданному закону распределения.
В качестве исходных данных для моделирования задается:
- L – длина обрабатываемого участка (определяется базовой длиной), мм;
- Н – толщина слоя покрытия, мм (должна превышать наибольшую высоту микронеровностей);
- Dср – средний диаметр пор в сечении шлифа (по ранее проведенным экспериментальным исследованиям, из литературы);
- Пористость материала П – величина пористости материала покрытия в процентах, %;
- t – глубина резания, мм;
- Зmax – наибольшая зернистость шлифовального круга;
- Зmin – наименьшая зернистость шлифовального круга;
- Закон распределения пор в материале покрытия.
При моделирование поры в покрытие располагаются случайным образом по закону распределения, таким образом, учитывается стохастичность процесса шлифования деталей с покрытиями.
На заданной плоскости покрытия длиной L и шириной H случайным образом по заданному закону распределения задается N пор – концентраторов напряжения. При этом координаты пор xi, yi запоминаются. Количество пор рассчитывается исходя из размеров пор и величины пористости покрытия.
Процесс распространения трещины начинается из левого верхнего угла рассматриваемой области. Далее процесс формирования трещины осуществляется по критерию:

где x0, y0 – координаты поры, из которой начинается микротрещина;
– коэффициент штрафа за развитие трещины в глубину покрытия.
При реализации модели осуществляется перебор всех пор, расположенных правее начальной: xi > x0. Далее выбирается такая точка, для которой значение критерия (1) наименьшее. Выбранная точка полагается начальной, и процесс формирования микропрофиля продолжается. Процесс моделирования развития микротрещины прекращается при x0 = xmax. В соответствии с этим строится профилограмма обработанной поверхности (рисунок 2), по которой рассчитывается параметр шероховатости Ra .
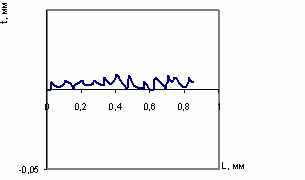
Рисунок 2 – Профилограмма обработанной поверхности
Разработанная модель расчета шероховатости при шлифовании деталей с износостойким покрытиями позволяет учесть особенности обработки покрытий, назначить оптимальные режимы резания, выбрать инструмент и получить требуемые параметры качества поверхности.
МЕТОДЫ УЛУЧШЕНИЯ КАЧЕСТВА ПРОИЗВОДСТВА ИЗДЕЛИЙ ИЗ СОРТОВОГО СТЕКЛА
Л.Ю. Алексеева
Бийский педагогический государственный университет
имени В.М. Шукшина, г. Бийск
Потребительские свойства и основные признаки ассортимента изделий из сортового стекла формируются на стадии проектирования и конструирования при создании опытных образцов и в процессе серийного изготовления. Качество изготовления изделий, зависит от соблюдения технологии производства.
При разработке новых изделий из сортового стекла художник учитывает условия их эксплуатации, метод формования, необходимость обеспечения удобства пользования и долговечности изделий, требования художественного стиля и моды. Исходя из этого, определяют состав и окраску стекла, конфигурацию изделий в целом и в деталях, толщину стенки, способ декорирования и др.
Производство стеклянных изделий состоит из обработки сырья, составления шихты, варки стекломассы, формования и отжига изделий, первичной и декоративной их обработки.
Сырьевые материалы стекольного производства подразделяют на основные (стеклообразующие) и вспомогательные.
С основными материалами в состав стекла вводят кислотные, щелочные и щелочно-земельные окиси.
Кремнезем (SiO2) вводят в стекло через кварцевый песок, песчаник или кварцит. Песок должен быть без примесей, особенно окрашивающих (окислы железа, титана, хрома), которые снижают его прозрачность. С повышением содержания диоксида кремния в стекле улучшаются механическая и термическая прочность, химическая устойчивость, но повышается температура варки. Окись бора (В2О3) вводят с борной кислотой или бурой. Он облегчает варку, улучшает физико-химические свойства стекла. Глинозем вводят в виде безводной и водной окиси алюминия (Аl2О3), полевых шпатов, коалина, глины, нефелина. Его добавка способствует повышению прочностных показателей и химической устойчивости стекла. Щелочные окиси Nа2О, К2О вводят через углекислые (сода, поташ) или серно-кислые соли. Они понижают температуру варки стекла, облегчают формование изделий, однако уменьшают прочность, термостойкость и химическую устойчивость. Щелочно-земельные окиси вводят обычно посредством углекислых солей. Так, окись кальция вводят через мел или известняк, окись магния – через магнезит или доломит, окись свинца – посредством свинцового сурика или свинцового глета. Окиси кальция, магния, цинка увеличивают химическую устойчивость и термостойкость изделий. Окиси бария, свинца и цинка повышают плотность, оптические свойства и поэтому применяются в производстве хрусталя. В производстве стекла широко используют горные щелочесодержащие породы, отходы горно-обогатительных комбинатов, цветной металлургии, доменные шлаки, в больших количествах – стекольный бой.
Вспомогательные материалы облегчают и ускоряют варку стекла, окрашивают или заглушают его. По назначению их подразделяют на осветлители, обесцвечиватели, глушители, красители, восстановители и окислители.
Осветлители способствуют удалению из стекломассы газов, образующихся при разложении сырьевых материалов. Обесцвечиватели погашают или ослабляют нежелательные цветные оттенки. Глушители (фториды и фосфаты) уменьшают прозрачность и обусловливают белую окраску стекла. Красители придают стеклу нужный цвет. В качестве красителей используют оксиды или сульфиды тяжелых металлов. Окрашивание может происходить также за счет выделения в стекле коллоидных частиц свободных металлов (меди, золота, сурьмы).
В синий цвет стекло окрашивают соединением кобальта, в голубой – окисью меди, в зеленый – окисями хрома или ванадия, в фиолетовый – перекисью марганца, а розовый – селеном, в сиреневый – окисью неодима, в желтый – окисью церия, сернистым кадмием, соединения золота – в красный до темно-красного (золотой рубин), соединения серебра – в золотисто-желтые цвета.
Приготовление шихты, т.е. сухой смеси материалов, состоит в отвешивании компонентов согласно рецептуре и тщательном их перемешивании до полной однородности. Более прогрессивным методом является изготовление из шихты брикетов и гранул; при этом сохраняется однородность шихты, ускоряется варка. В процессе варки шихты происходят сложные физико-химические превращения и взаимодействия сырьевых материалов с образованием и плавлением силикатов и свободного кремнезема. С помощью осветлителей стекломассу освобождают от газовых включений, тщательно перемешивают до достижения однородности по составу и вязкости.
При нарушениях режимов обработки сырья, приготовления шихты и варки образуются дефекты стекломассы в виде нежелательных цветных оттенков и посторонних включений – стекловидных (свиль, шлир), газовых (пузырь, мошка), кристаллических (камни).
Изделия из сортового стекла изготовляют ручным и свободным выдуванием, механизированным выдуванием, прессованием, прессовыдуванием, многостадийным методом, моллированием (гнутьем), центробежной формовкой. Возможные дефекты формования – кривизна изделий, несимметричная приставка деталей, разнотолщинность стенки, складки, морщины, царапины, мелкие трещины (посечки) поверхности и др.
При формовании, ввиду низкой теплопроводности стекла, резкого и неравномерного охлаждения в изделиях возникают остаточные напряжения, способные вызвать их самопроизвольное разрушение. Поэтому обязателен отжиг – термическая обработка, состоящая в нагревании изделий до 530–550°С, выдерживании при этой температуре и последующем медленном охлаждении. При отжиге остаточные напряжения ослабляются до безопасной величины и равномерно распределяются по сечению изделий.
Первичные обработки заключаются в удалении колпачка с изделий после ручного выдувания, обработке края и дна изделий, притирке пробок к горлу графинов и флаконов. В прессованных изделиях проводят огневую полировку поверхности.
Путем окончательной, декоративной обработки на изделия наносятся украшения разного характера (механическим, химическим и поверхностным способом). Декор в большой мере определяет эстетические достоинства посуды; он должен подчеркнуть прозрачность, блеск и игру света стекла, особенности формы изделий и иметь самостоятельную художественную ценность.
Литература
- Кропотов В.Н., Зайцев А.Г., Скавронский Б.И. Строительные материалы. Учеб. для архитектурных вузов. – М.: Высшая школа, 1973. – 384 с.
- Ланцетти А.Г., Нестеренко М.Л. Изготовление художественного стекла. Учебник. – М.: Высшая школа, 1972. – 280 с.
- Справочник по производству стекла. Т. 1 / Под ред. И.И. Китайгородского. – М.: Гостройиздат, 1963. – 1026 с.