А. В. Строкович управление проектами издательство нуа народная украинская академия а. В. Строкович управление проектами учебное пособие
Вид материала | Учебное пособие |
- Е. А. Подольская управление социальными процессами издательство нуа народная украинская, 3428.66kb.
- Программа курса «управление проектами» Часть І. Основы управления проектами (8 акад, 1033.59kb.
- И. В. Головнева психологические основы кадрового менеджмента издательство нуа народная, 2824.07kb.
- Календарно-сетевое планирование и управление «Методология» управления проектами Управление, 9.71kb.
- Календарно-сетевое планирование и управление «Методология» управления проектами Управление, 10.14kb.
- Программа дисциплины История и методология управления проектами для направления 080200., 199.5kb.
- Гергерт Дмитрий Владимирович Оценка и управление финансами проекта (на примере конкретной, 40.6kb.
- Гергерт Дмитрий Владимирович Оценка и управление финансами проекта (на примере конкретной, 43.14kb.
- Гергерт Дмитрий Владимирович Оценка и управление финансами проекта (на примере конкретной, 40.51kb.
- Учебно-методический комплекс дисциплины: Управление проектами Специальность, 2083.48kb.
1. Концепция управления качеством.
2. Метод системного управления качеством. Виды затрат по обеспечению качества проекта.
3. Система стандартов ISO. Система стандартизации и сертификации в Украине.
1. Концепция управления качеством
Раннее существовавшая политика сменилась новой, изначально нацеленной на обеспечение высокого качества продукции. Новая политика основывается, прежде всего, на понимание всеми участниками реализуемых проектов жизненной необходимости выпуска качественной продукции.
Основополагающими принципами концепции качества является то, что [22]:
– качество – неотъемлемый элемент проекта в целом (а не самостоятельная функция управления);
– качество – это то, что говорит потребитель, а не изготовитель;
– ответственность за качество должна быть адресной;
– для реального повышения качества нужны новые технологии;
– повысить качество можно только усилиями всех работников предприятия;
– контролировать процесс всегда эффективнее, чем результат;
– политика в области качества должна быть частью общей политики предприятия.
На этих принципах основан наиболее популярный сейчас метод системного управления качеством или всеобщего управления качеством (Total Quality Management TQM) .
Качество – это целостная совокупность характеристик объекта, относящаяся к его способности удовлетворять установленные или предполагаемые потребности [23]. Обычно потребности формируются при помощи установленных характеристик или критериев. Потребности могут включать, например, эксплуатационные характеристики, функциональную пригодность, надежность, безопасность, воздействие на окружающую среду, экономические, эстетические и культурно–исторические требования.
Понятие «качество» следует отличать от понятия «градация» (сорт, класс и т. д.). Градация – это категория или разряд, присвоенный объектам, имеющим тоже функциональное применение, но иные требования по качеству. Низкое качество – это всегда проблема, низкий сорт – не обязательно.
Принято различать четыре ключевых аспекта качества [22]:
- качество, обусловленное соответствием рыночным потребностям и ожиданиям. Этот аспект качества достигается благодаря эффективному определению и актуализации потребностей и ожиданий потребителя в целях их удовлетворения требований потребителя и точному анализу возможностей рынка;
- качество разработки и планирования проекта;
- качество выполнения работ в соответствии с плановой документацией;
- качество материально–технического обеспечения проекта.
Принципы TQM являются основой разнообразных концепций менеджмента качества, таких как ИСО 9000, многих национальных государственных моделей управления качеством, а также явились базой для выработки системы менеджмента проекта.
Сертификация системы качества на соответствие стандартам ИСО серии 9000 свидетельствует лишь о соответствии минимальным требованиям, на основании которых потребитель оценивает возможность заключения с организацией партнерских отношений, и не более. Практика показывает, что для успешной деятельности одной сертификации системы качества недостаточно, необходимо разрабатывать и развивать эту систему, основываясь на методах и принципах TQM, чтобы достичь долгосрочного успеха.
В разработку системы управления в соответствии с принципами TQM вовлекается большинство сотрудников организации, а полное воплощение этой системы должно производиться с применением современных технологий (организационных, управленческих, информационных и др.). Этот процесс требует перестройки всей деятельности организации, согласованной работы всех структурных подразделений, а также длительного периода времени.
Практика показывает, что квалифицированное использование методологии TQM обеспечивает:
1. Увеличение степени удовлетворенности клиентов продуктами и услугами. В условиях TQM обязательным является удовлетворение всех клиентов, а также дополнительные усилия по предупреждению их ожиданий.
2. Улучшение имиджа и репутации фирмы.
3. Повышение производительности труда. Оно наступает автома-тически, как только работники становятся партнерами по внедрению TQM.
4. Увеличение прибыли.
5.Повышение качества и конкурентоспособности продукции и услуг.
6. Обеспечение экономической устойчивости предприятия, а также рационального использования всех видов ресурсов.
7. Повышение качества управленческих решений.
8. Внедрение новейших достижений в технике и технологиях.
В послевоенные годы в СССР были заложены основные принципы TQM (например, системный подход к управлению, роль руководства, принятие решений, основанных на фактах, вовлечение работников). Предприятия начали разрабатывать и развивать методы управления качеством еще в 1950–е годы. Первая попытка была сделана саратовскими машиностроителями, создавшими свою системы БИП (бездефектного изготовления продукции), затем появилась ее львовская модификация СБТ (система бездефектного труда), горьковская система КАНАРСПИ (качество, надежность, ресурс с первого предъявления), ярославская система НОРМ (научная организация работ по повышению моторесурса), КС УКП (комплексная система управления качеством продукции). КС УКП была разработана в ходе научно–практического эксперимента рядом ярославских предприятий совместно с НИИ Госстандарта СССР. Эта система стала базой для управления качеством во многих отраслях промышленности СССР.
Вся система менеджмента работает лучше, если организация рассматривается как единое целое, единая система. В данном случае для повышения эффективности деятельности и оптимизации процессов необходимо соблюдение основных принципов TQM.
1. Ориентация организации на заказчика.
Организация всецело зависит от своих заказчиков и поэтому понимать потребности заказчика, выполнять его требования и стремиться превзойти его ожидания. Даже система качества, отвечающая минимальным требованиям, должна быть ориентирована в первую очередь на требования потребителя. Системный подход к ориентации на потребности клиента начинается со сбора и анализа жалоб и претензий заказчиков. Это необходимо для предотвращения таких проблем в будущем.
Практику анализа жалоб и претензий ведут многие организации, не имеющие системы качества. Но в условиях применения TQM информация должна поступать систематически из многих источников и интегрироваться в процесс, позволяющий получить точные и обоснованные выводы относительно потребностей и желаний, как конкретного заказчика, так и рынка в целом.
В организациях, внедряющих у себя TQM, вся информация и данные должны распространяться по всей организации. В данном случае внедряются процессы, направленные на определение потребительской оценки деятельности организации и на изменение представления заказчиков о том, насколько организация может удовлетворить их потребности.
2. Ведущая роль руководства.
Руководители организации устанавливают единые цели и основные направления деятельности, а также способы реализации целей. Они должны создать в организации такой микроклимат, при котором сотрудники будут максимально вовлечены в процесс достижения поставленных целей.
Для любого направления деятельности обеспечивается такое руководство, при котором гарантируется построение всех процессов таким образом, чтобы получить максимальную производительность и наиболее полно удовлетворить потребности заказчиков.
Установление целей и анализ их выполнения со стороны руководства должны быть постоянной составляющей деятельности руководителей, равно как планы по качеству должны быть включены в стратегические планы развития организации.
3. Вовлечение сотрудников.
Весь персонал – от высшего руководства до рабочего – должен быть вовлечен в деятельность по управлению качеством. Персонал рассматривается как самое большое богатство организации, и создаются все необходимые условия для того, чтобы максимально раскрыть и использовать его творческий потенциал.
Сотрудники, вовлекаемые в процесс реализации целей организации, должны иметь соответствующую квалификацию для выполнения возложенных на них обязанностей. Также руководство организации должно стремиться к тому, чтобы цели отдельных сотрудников были максимально приближены к целям самой организации. Огромную роль здесь играет материальное и моральное поощрение сотрудников.
Персонал организации должен владеть методами работы в команде. Работы по постоянному улучшению преимущественно организуются и проводятся группами. При этом достигается синергетический эффект, при котором совокупный результат работы команды существенно превосходит сумму результатов отдельных исполнителей.
4. Процессный подход.
Для достижения наилучшего результата соответствующие ресурсы и деятельность, в которую они вовлечены, нужно рассматривать как процесс.
Процессная модель предприятия состоит из множества бизнес–процессов, участниками которых являются структурные подразделения и должностные лица организационной структуры предприятия.
Под бизнес–процессом понимают совокупность различных видов деятельности, которые вместе создают результат, имеющий ценность для самой организации, потребителя, клиента или заказчика. Обычно на практике применяются следующие виды бизнес–процессов:
- основной, на базе которого осуществляется выполнение функций по текущей деятельности предприятия по производству продукции или оказанию услуг;
- обслуживающий, на базе которого осуществляется обеспечение производственной и управленческой деятельности организации.
Бизнес–процессы реализуются посредством осуществления бизнес–функций.
При применении процессного подхода структура управления предприятием включает два уровня:
- управление в рамках каждого бизнес–процесса;
- управление группой бизнес–процессов на уровне всей организации.
Основой управления отдельным бизнес–процессом и группой бизнес–процессов являются показатели эффективности, среди которых можно выделить:
- затраты на осуществление бизнес–процесса;
- расчет времени на осуществление бизнес–процесса;
- показатели качества бизнес–процесса.
На основе этого принципа организация должна определить процессы проектирования, производства и поставки продукции или услуги. С помощью управления процессами достигается удовлетворение потребностей заказчиков. В итоге, управление результатами процесса переходит в управление самим процессом. Также ИСО 9001 предлагает внедрить и некоторые другие процессы (анализ со стороны руководства, корректирующие и предупреждающие действия, внутренние проверки системы качества и т. д.)
Следующим этапом на пути к TQM является оптимизация использования ресурсов в каждом выделенном процессе. Это означает строгий контроль за использованием каждого вида ресурсов и поиск возможностей для снижения затрат на производство продукции или оказание услуг.
5. Системный подход к управлению.
Результативность и эффективность деятельности организации, в соответствии с принципами TQM, могут быть повышены за счет создания, обеспечения и управления системой взаимосвязанных процессов. Это означает, что организация должна стремиться к объединению процессов создания продукции или услуг с процессами, позволяющими отследить соответствие продукции или услуги потребностям заказчика.
Только при системном подходе к управлению станет возможным полное использование обратной связи с заказчиком для выработки стратегических планов и интегрированных в них планов по качеству.
6. Постоянное улучшение.
В этой области организация должна не только отслеживать возникающие проблемы, но и, после тщательного анализа со стороны руководства, предпринимать необходимые корректирующие и предупреждающие действия для предотвращения таких проблем в дальнейшем.
Цели и задачи основываются на результатах оценки степени удовлетворенности заказчика (полученной в ходе обратной связи) и на показателях деятельности самой организации. Улучшение должно сопровождаться участием руководства в этом процессе, а также обеспечением всеми ресурсами, необходимыми для реализации поставленных целей.
7. Подход к принятию решений, основанный на фактах.
Эффективные решения основываются только на достоверных данных. Источниками таких данных могут быть результаты внутренних проверок системы качества, корректирующих и предупреждающих действий, жалоб и пожеланий заказчиков и т. д. Также информация может основываться на анализе идей и предложений, поступающих от сотрудников организации и направленных на повышение производительности, снижение расходов и т. д.
8. Отношения с поставщиками.
Так как организация тесно связана со своими поставщиками, целесообразно налаживать с ними взаимовыгодные отношения с целью дальнейшего расширения возможностей деятельности. На данном этапе устанавливаются документированные процедуры, обязательные для соблюдения поставщиком на всех этапах сотрудничества.
9. Минимизация потерь, связанных с некачественной работой.
Минимизация потерь, связанных с некачественной работой, обеспечивает возможность предлагать продукцию за меньшую цену при прочих равных условиях. Стандартом работы является отсутствие дефектов или – «делай правильно с первого раза».
- Метод системного управления качеством. Виды затрат по обеспечению качества проекта.
QFD (Quality Function Deployment – технология развертывания функций качества). Данный метод представляет собой технологию проектирования изделий и процессов, позволяющую преобразовывать пожелания потребителя в технические требования к изделиям и параметрам процессов их производств. Метод QFD – это экспертный метод, использующий табличный способ представления данных, причем со специфической формой таблиц, которые получили название «домиков качества». Основная идея технологии QFD заключается в осознании того, что между потребительскими свойствами («фактическими показателями качества») и установленными в стандартах параметрами продукта («вспомогательными показателями качества») существует большое различие. Вспомогательные показатели качества важны для производителя, но не всегда существенны для потребителя. Идеальным случаем был бы такой, когда производитель мог проконтролировать качество продукции непосредственно по фактическим показателям, но это, как правило, невозможно, поэтому он пользуется вспомогательными показателями. Технология QFD – это последовательность действий производителя по преобразованию фактических показателей качества изделия в технические требования к продукции, процессам и оборудованию. Основным инструментом технологии QFD является специальная схема, представленная на рис. 8.1, получившая название «домик качества». В данной схеме отображается связь между фактическими показателями качества (потребительскими свойствами) и вспомогательными показателями (техническими требованиями).

Рис. 8.1. Схема технологии развертывания функций качества [31]
Применение метода QFD позволяет учитывать требования потребителя на всех стадиях производства готовой продукции, для всех элементов системы качества организации и, таким образом, повысить степень удовлетворенности потребителя, снизить затраты на процессы проектирования и подготовки изделий к производству.
ФСА (функционально–стоимостной анализ). Метод ФСА представляет собой технологию анализа затрат на выполнение изделием его функций; ФСА проводится для существующих продуктов и процессов с целью снижения затрат, а также для разрабатываемых продуктов с целью снижения их себестоимости.
Метод ФСА начал активно применяться в промышленности с 1960-х годов, прежде всего в США. Его использование позволило снизить себестоимость многих видов продукции без снижения ее качества и оптимизировать затраты на изготовление. Сейчас ФСА является одним из самых популярных видов анализа изделий и процессов. ФСА – один из методов функционального анализа технических объектов и систем, к этой же группе методов относятся ФФА (функционально–физический анализ) и FMEA–анализ.
При проведении функционально–стоимостного анализа определяют функции элементов технического объекта или системы и проводят оценку затрат на реализацию этих функций с тем, чтобы эти затраты снизить.
Проведение ФСА включает следующие основные этапы:
1. Последовательное построение моделей объекта ФСА (компонентной, структурной, функциональной). Модели обычно могут быть представлены в табличной (матричной) форме.
2. Исследование моделей и разработка предложений по совершенствованию объекта анализа.
Эти же этапы характерны и для других методов функционального анализа – ФФА и FMEA.
FMEA-анализ (Failure Mode and Effects Analysis). FMEA-анализ представляет собой технологию анализа возможности возникновения дефектов и их влияния на потребителя. FMEA-анализ проводится для разрабатываемых продуктов и процессов с целью снижения риска потребителя от потенциальных дефектов.
FMEA-анализ в настоящее время является одной из стандартных технологий анализа качества изделий и процессов, поэтому в процессе его развития выработаны типовые формы представления результатов анализа и правила его проведения.
Данный вид функционального анализа используется как в комбинации с функционально-стоимостным и функционально-физическим анализом, так и самостоятельно. Он позволяет снизить затраты и уменьшить риск возникновения дефектов.
FMEA-анализ, в отличие от ФСА, не анализирует прямо экономические показатели, в том числе затраты на недостаточно высокое качество, а позволяет выявить именно те дефекты, которые обусловливают наибольший риск потребителя, определить потенциальные причины их возникновения и выработать корректирующие действия по их устранению еще до того, как эти дефекты проявятся и, таким образом, предупредить затраты на исправление.
Обычно FMEA-анализ проводится для новой продукции или процесса. Может проводиться для процесса производства продукции и процесса эксплуатации изделия потребителем.
FMEA-анализ процесса производства обычно производится у изготовителя ответственными службами планирования производства, обеспечения качества или производства с участием соответствующих специализированных отделов изготовителя и, при необходимости, потребителя. Проведение FMEA-анализа процесса производства начинается на стадии технической подготовки производства и заканчивается своевременно до монтажа производственного оборудования. Целью FMEA-анализа процесса производства является обеспечение выполнения всех требований по качеству процесса производства и сборки путем внесения изменений в план процесса для технологических действий с повышенным риском.
FMEA-анализ бизнес-процессов обычно производится в подразделениях, выполняющих данный бизнес-процесс. В проведении анализа, кроме представителей этих подразделений, обычно принимают участие представители службы обеспечения качества, представители подразделений, являющихся внутренними потребителями результатов бизнес-процесса, и подразделений, участвующих в выполнении этапов бизнес-процесса. Целью этого вида анализа является обеспечение качества выполнения запланированного бизнес–процесса. Выявленные в ходе анализа потенциальные причины дефектов и несоответствий позволят определить причину неустойчивости системы. Выработанные корректирующие мероприятия должны обязательно предусматривать внедрение статистических методов в первую очередь для тех операций, где выявлен повышенный риск.
Этапы проведения FMEA-анализа:
1. Построение компонентной, структурной, функциональной и потоковой моделей объекта анализа. Если FMEA-анализ проводится совместно с функционально–стоимостным и функционально-физическим анализом, используются ранее построенные модели.
2. Исследование моделей. В ходе исследования моделей определяются:
– потенциальные дефекты для каждого из элементов компонентной модели объекта. Такие дефекты обычно связаны или с отказом функционального элемента (его разрушением, поломкой и т. д.), или с неправильным выполнением элементом его полезных функций (отказом по точности, производительности и т. д.), или с вредными функциями элемента. В качестве первого шага рекомендуется перепроверка предыдущего FMEA-анализа или анализ проблем, возникших за время гарантийного срока. Необходимо также рассматривать потенциальные дефекты, которые могут возникнуть при транспортировке, хранении, а также при изменении внешних условий (влажность, давление, температура);
– потенциальные причины дефектов. Для их выявления могут быть использованы диаграммы Ишикавы, которые строятся для каждой из функций объекта, связанных с появлением дефектов;
– потенциальные последствия дефектов для потребителя. Поскольку каждый из рассматриваемых дефектов может вызвать цепочку отказов в объекте, при анализе последствий используются структурная и потоковая модели объекта;
– возможности контроля появления дефектов. Определяется, может ли дефект быть выявленным до наступления последствий в результате предусмотренных в объекте мер по контролю, диагностике и др.
Ряд экспертных оценок.
Определяются следующие параметры:
а) параметр тяжести последствий для потребителя (проставляется обычно по 10-ти балльной шкале; наивысший балл для случаев, когда последствия дефекта влекут юридическую ответственность);
б) параметр частоты возникновения дефекта (проставляется по 10-ти балльной шкале; наивысший балл когда оценка частоты возникновения составляет 1/4 и выше);
в) параметр вероятности необнаружения дефекта (является 10-ти балльной экспертной оценкой; наивысший балл для «крытых» дефектов, которые не могут быть выявлены до наступления последствий);
г) параметр риска потребителя (показывает, в каких отношениях друг к другу в настоящее время находятся причины возникновения дефектов; дефекты с наибольшим коэффициентом приоритета риска подлежат устранению в первую очередь).
Результаты анализа заносятся в специальную таблицу. Выявленные «узкие места» подвергаются изменениям, то есть разрабатываются корректирующие мероприятия.
Часто разработанные мероприятия заносятся в последующую графу таблицы FMEA-анализа. Затем пересчитывается потенциальный риск после проведения корректировочных мероприятий. Если не удалось его снизить до приемлемых пределов, разрабатываются дополнительные корректирующие мероприятия и повторяются предыдущие шаги.
По результатам анализа для разработанных корректирующих мероприятий составляется план их внедрения. Для этого определяется:
- в какой временной последовательности следует внедрять эти мероприятия и сколько времени потребуется на проведение каждого мероприятия, через сколько времени после начала его проведения проявится запланированный эффект;
- кто будет отвечать за проведение каждого из этих мероприятий, кто будет конкретным его исполнителем;
- где (в каком структурном подразделении) мероприятия должны быть проведены;
- из какого источника будет производиться финансирование проведения мероприятия.
ФФА (функционально-физический анализ). Функционально–физический анализ был создан в 1970-е годы в результате работ, параллельно проводившихся учеными Германии и СССР.
Целью ФФА является анализ физических принципов действия, а также технических и физических противоречий в технических объектах для того, чтобы оценить качество принятых технических решений и предложить новые. При этом широко используются:
1. Эвристические приемы, то есть обобщенные правила изменения структуры и свойств технических объектов.
2. Анализ следствий из общих законов и частных закономерностей развития технических объектов; эти законы применительно к различным отраслям промышленности, установлены работами школы профессора Половинкина и др.
3. Синтез цепочек физических эффектов для получения новых физических принципов действия технических объектов; в настоящее время существуют программные продукты, автоматизирующие данный процесс.
Обычно функционально–физический анализ проводится в следующей последовательности:
1. Формулировка проблемы.
Для этого могут быть использованы результаты функционально–стоимостного анализа или FMEA–анализа. Описание проблемы должно включать назначение технического объекта, условия его функционирования и технические требования к нему.
2. Составление описания функций назначения технического объекта.
Описание базируется на анализе запросов потребителя и должно содержать четкую и краткую характеристику технического объекта, с помощью которой можно удовлетворить возникшую потребность. Описание функций технического объекта включает:
- действия, выполняемые им;
- объект, на который направлено действие;
- условия работы технического объекта на всех стадиях его жизненного цикла.
3. Проведение анализа надсистемы технического объекта. К надсистеме относится внешняя среда, в которой функционирует и с которой взаимодействует рассматриваемый объект. Анализ надсистемы производится с помощью структурной и потоковой модели технического объекта.
4. Составление списка технических требований к объекту. Данный список должен базироваться на анализе требований потребителей; на этой стадии целесообразно использовать приемы описанной технологии развертывания функций качества (QFD).
5. Построение функциональной модели технического объекта (обычно в виде функционально–логической схемы).
6. Анализ физических принципов действия функций технического объекта.
7. Определение технических и физических противоречий для функций технического объекта. Такие противоречия возникают между техническими параметрами объекта при попытке одновременно удовлетворить несколько требований потребителя.
8. Определение способов разрешения противоречий и направления совершенствования технического объекта. Для того чтобы реализовать совокупность потребительских свойств объекта, отраженных в его функциональной модели, модель преобразуется в функционально–идеальную; поиск вариантов технических решений часто производят с помощью морфологических таблиц.
9. Построение графиков, эквивалентных схем, математических моделей технического объекта. Важно, чтобы модель была продуктивной, т. е. позволяла найти новые возможные решения. К формированию морфологической таблицы целесообразно приступить тогда, когда появится несколько предлагаемых решений для различных функциональных элементов технического объекта.
Применение ФФА позволяет повысить качество проектных решений, создавать в короткие сроки высокоэффективные образцы техники и технологий и таким образом обеспечивать конкурентное преимущество организации.
Менеджмент качества в рамках управления проектом – это система методов, средств и видов деятельности, направленных на выполнение требований и ожиданий клиентов проекта к качеству самого проекта и его продукции.
Таким образом, можно выделить менеджмент качества самого проекта и менеджмент качества продукции проекта.
Планирование качества – выявление требований к качеству проекта и продукции проекта, а также определение путей их удовлетворения [23].
Для начала процесса планирования необходимо иметь информацию о политике проекта в области качества, содержании (предметной области) проекта, описание продукции (желательно в виде конкретных спецификаций, полученных от потребителя), стандарты и требования к качеству продукции, услуг, информации и реализации технологических процессов, документацию по системе качества.
В процессе планирования качества может применяться следующий инструментарий [23]:
– анализ затрат и выгод;
– установление желательного уровня показателей качества проекта исходя из сравнения с соответствующими показателями других проектов;
– диаграммы «причин–следствий», иллюстрирующие причинно–следственную связь различных причин и субпричин с потенциальными и реальными проблемами;
– блок–схемы, показывающие, как различные элементы системы или процесса взаимодействуют друг с другом;
– эксперименты.
В результате планирования качества появляется план качества (план организационно–технических мероприятий по обеспечению системы качества проекта), который должен описывать конкретные мероприятия по реализации политики в области качества с указанием сроков выполнения, ответственных за выполнение, критериев оценки, бюджета.
В план качества должны входить описания процедур проведения контрольных и испытательных мероприятий или указания на уже существующие, перечень контрольных показателей по всем работам и видам продукции.
В план качества могут также входить технологические карты отдельных сложных процессов и проверочные листы, предписывающие выполнение конкретных шагов процедур или процессов.
Обеспечение качества предполагает регулярную проверку хода реализации проекта в целях установления соответствия определенных ранее требованиям к качеству.
Обеспечение качества происходит исходя из ранее утвержденного плана качества, технологических карт, проверочных листов и иной документации по качеству, а также данных о качестве, полученных в результате контроля и испытаний.
Обеспечение качества происходит путем плановых и внеплановых проверок, инспекций и иных контрольных и испытательных мероприятий с последующей оценкой качества и идентификацией статуса контроля и испытаний. Статус контроля и испытаний является основой решения об улучшении качества проекта и его продукции.
Контроль качества – отслеживание конкретных результатов деятельности по проекту в целях определения их соответствия стандартам и требованиям по качеству и определения путей устранения причин реальных и потенциальных несоответствий [23].
Для контроля качества необходима информация о ходе реализации проекта, план качества, документация по качеству.
Методы и инструменты контроля:
– проверка;
– контрольные карты (см. рис.8.2), которые представляют собой графическое изображение результатов процесса;
– диаграммы Парето (см. рис. 8.3), которые представляют собой гистограммы появления различных причин несоответствий, упорядоченные по частоте;
– статистические выборки, анализ динамических рядов, корреляционно–регрессионный анализ и другие статистические методы;
–диаграммы причин-следствий (см. рис.8.4).
Контроль качества может завершиться следующими решениями:
– улучшение качества;
– принятие продукции;
– идентификация брака и реализации действий по управлению несоответствующей продукцией;
– переработка продукции с целью дальнейшего представления для контроля и испытаний, исправление процессов.
Согласно методу системного управления качеством, устанавливается единая схема разработки и внедрения:
1. Проводится обследование производства и подготавливается специальный доклад.
2. На основе обследования и анализа фактического состояния производства производится выбор системы управления качеством и разрабатывается Программа качества.
3. Разрабатывается Руководство по реализации Программы качества, в котором описывается сущность и механизм функционирования Системы управления качеством.
4. На специальном совещании с участием Специализированной фирмы обсуждаются детали, сроки и организация выполнения Программы качества и Руководства, вносятся только необходимые исправления, и принимаются решения.
5. Мероприятия из Программы и руководства включаются в общий план проекта.
Верхний допустимый предел значения контролируемого параметра | | | |
Среднее значение контролируемого параметра | ![]() | | |
Нижний допустимый предел значения контролируемого параметра | | | |
Рис. 8.2. Контрольная карта реализации проекта [23]
40 | | 100 |
3 ![]() | К ![]() | 75 |
20 | | 50 |
10 | Частота появления дефектов в зависимости от причины, шт. | 25 |
0 | | 0 |
Количество дефектов, шт. | | Количество дефектов, % |
Рис. 8.3. Диаграмма Парето [23]
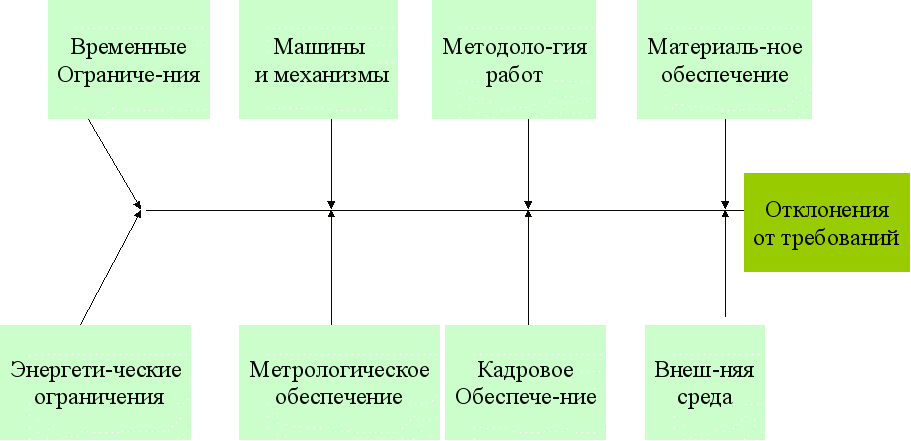
Рис. 8.4. Диаграмма причин–следствий [21, 23]
6. Программа качества и Руководство запускаются в производство, специализированная фирма проводит периодические проверки, документально оформляя их результаты и внося необходимые уточнения в указанные документы.
7. В ходе реализации Программы и Руководства специализированная фирма осуществляет поддержку системы и защиту интересов предприятия.
Обеспечением системы управления качеством занимается проект–менеджер. Суть работы проект–менеджера состоит в сравнении текущего уровня качества с запланированным. Информацию для такого сравнения дает учет и анализ затрат, связанных с обеспечением качества. Эти затраты обычно классифицируются следующим образом:
– предупредительные затраты. Направлены на изначальное удовлетворение требований заказчика по производству продукции без дефектов. К ним можно отнести затраты на обеспечение качества проекта изделия, обеспечение, программу качества и т. д.;
– информационные затраты связаны с желанием заказчика (потребителя) убедиться в том, что процесс развивается в нужном направлении. К ним можно отнести инспекционные проверки, лабораторный контроль, операционный контроль;
– затраты на устранение дефектов, связанных с внутренними проблемами, должны быть произведены для того, чтобы скорректировать процесс и сделать, несмотря на неудачи, продукцию приемлемой для заказчика (потребителя). К ним относятся расходы на отбраковку, ремонт, устранение дефектов;
– затраты на устранение дефектов, связанных с требованием заказчика (потребителя), вызваны тем, что его требования не были удовлетворены. К ним относятся расходы на возврат продукции, жалобы потребителя, необходимые ответные меры.
Данная классификация является адресной. На ее основе легко построить систему управления качеством. Значительную часть процесса управления качеством целесообразно компьютеризировать. Тогда возможно решение следующих задач:
– распределение во времени и по видам затрат на продукцию, связанных с обеспечением качества;
– определение видов и стоимости проектов, требующих повышенных затрат;
– динамика изменения себестоимости продукции;
– степень удовлетворенности потребителей продукцией проекта.
- Система стандартов ISO. Система стандартизации и сертификации в Украине
Развитие системы управления качеством в Украине началось сравнительно недавно, что позволяет учесть опыт других государств, достигших значительных успехов на этом пути.
Отечественная система стандартизации направлена на обеспечение прав потребителя по вопросам предоставления конкурентоспособной, безопасной, качественной продукции и услуг, соответствующих развитию науки, техники и потребностей населения.
В соответствии с Декретом Кабинета Министров Украины «О стандартизации и сертификации» от 10.05.93г. № 46–93, был создан Комитет Украины по вопросам стандартизации метрологии и сертификации, который обеспечивает функционирование государственной системы стандартизации, осуществляет планирование, разработку, распространение и применение государственных стандартов.
С целью повышения качества и конкурентоспособности отечественной продукции и обеспечения защиты интересов потребителя 23 февраля 2001 года Президент издал указ «О мероприятиях по повышению качества отечественной продукции». В частности об «...осуществлении государственной поддержки во внедрении систем управления качеством на предприятиях согласно стандартам Международной организации по стандартизации (ISO) серии 9000», а также о «...проведении в Украине ежегодной Европейской недели качества и конкурса “100 лучших товаров Украины”».
В 1989 году была основана общественная организация – Украинская ассоциация качества (УАК), которая на сегодняшний день имеет такие технические комитеты, как «Качество пищевой промышленности и водоснабжения», «Качество окружающей среды и здоровья человека», «Обеспечение качества в металлургии», «Обеспечение качества в современном материаловедении», «Обеспечение качества в приборостроении», «Качество и сертификация в авиационной промышленности» и многие другие. В марте 1996 года Украина была принята в Европейскую организацию качества, где УАК стала ее официальным представителем.
Управление качеством проекта требует системного подхода, реализация которого в современной практике осуществляется в виде создания стандартизированных систем менеджмента качества, представляющих собой совокупность документированных методик и средств планирования, обеспечения и контроля качества, выполняемых специально назначенными структурными единицами организации или проекта.
В рамках управления отдельно взятым проектом как правило специальной системы менеджмента качества не разрабатывается, но при этом основные участники должны обладать такими системами, а также иметь документированное соглашение, в котором прописываются совместные решения по взаимодействию их систем менеджмента качества. В некоторых случаях целесообразно привлекать специализированные фирмы для внедрения и создания таких систем менеджмента качества.
Иерархия документации системы качества [23]:
- Руководство по качеству.
- Методологические инструкции.
- Рабочие и контрольные инструкции.
- Нормативная документация и техническая литература.
Руководство по качеству охватывает все применяемые элементы стандарта на систему качества, необходимые для предприятия. Примерное содержание руководства по качеству [22]:
- Общие положения.
- Заявление руководства предприятия.
- Характеристика предприятия.
- Элементы системы качества:
- Ответственность руководителей.
- Система качества.
- Анализ контрактов.
- Управление проектированием.
- Управление документацией и данными.
- Материально–техническое обеспечение проекта.
- Управление продукцией.
- Идентификация изделия.
- Управление процессом создания продукции.
- Контроль и испытания.
- Управление оборудованием для контроля, измерения и испытаний.
- Статус контроля и испытаний.
- Управление несоответствующей продукцией.
- Корректирующие и предупреждающие действия.
- Погрузочно–разгрузочные работы, хранение, упаковка, консервация и поставка.
- Управление регистрацией данных о качестве.
- Внутренние проверки качества.
- Подготовка кадров.
- Обслуживание.
- Статистические методы.
- Ответственность руководителей.
- Приложение.
Рабочие инструкции:
– технологические карты;
– специальные разделы проектов производства работ;
– схемы операционного контроля.
Контрольные инструкции:
– входной контроль проектной документации, материалов, деталей, оборудования;
– контроль качества производственных процессов;
– проведение авторского надзора.
Все работы по обеспечению качества основаны на использовании международных стандартов Международной организации по стандартизации (ISO), признанных в 1988 г. СССР в качестве национальных стандартов. В рамках систем управления качеством используют серию стандартов ISO 9000 и эквивалентную ей серию.
ISO образована в 1947 году со штаб–квартирой в Женеве. Это неправительственная организация, которая создавалась с целью разработки мировых стандартов, способствующих улучшению международных связей и кооперации, а также ускоренному развитию сбалансированной и равноправной международной торговли. В состав этой организации входит 91 страна мира, на долю которых приходится 95% мирового промышленного производства.
Вопросами качества в ISO ведает технический комитет ISO 176. Он координирует разработку и внедрение стандартов по системам контроля за качеством продукции, его повышения и обеспечения технологией, связанной со сферой качества.
Во введении технического комитета ISO 176 находятся стандарты серии ISO 9000 «Системы качества». Стандарты ISO 9000–9004 имеют самое широкое распространение в мире.
Основным документом, регулирующим систему качества в Украине является Декрет Кабинета Министров Украины «О стандартизации и сертификации».
Основными принципами стандартизации в Украине являются [1]:
– учет уровня развития науки и техники, экологических требований, экономической целесообразности и эффективности производства для производителя, полезности та безопасности для потребителей и государства в целом;
– гармонизация с международными, региональными, а в случае необходимости – с национальными стандартами других стран;
– обеспечение соответствия требованиям нормативных документов;
– участие в разработке нормативных документов всех заинтересованных сторон (разработчиков, изготовителей, потребителей, органов государственной исполнительной власти и т. д.);
– взаимосвязь и согласованность нормативных документов всех уровней;
– пригодность нормативных документов для сертификации продукции;
– открытость информации о действующих стандартах и программах работ из стандартизации с учетом требований действующего законодательства.
Нормативные документы по стандартизации делятся на [1]:
– государственные стандарты Украины;
– отраслевые стандарты;
– стандарты научно-технических и инженерных обществ и союзов;
– технические условия;
– стандарты предприятий.
Государственные стандарты Украины содержат обязательные и рекомендованные требования. К обязательным относятся:
– требования, которые обеспечивают безопасность продукции для жизни, здоровье и имущества граждан, ее совместимость и взаимозаменяемость, охрану окружающей естественной среды и требования к методам испытаний этих показателей;
– требования техники безопасности и гигиены работы с ссылкой на соответствующие санитарные нормы и правила;
– метрологические нормы, правила, требования и положение, которые обеспечивают достоверность и единство измерений;
– положения, которые обеспечивают техническое единство во время разработки, изготовления, эксплуатации (применения) продукции.
Обязательные требования государственных стандартов подлежат безусловному выполнению органами государственной исполнительной власти, всеми предприятиями, их объединениями, учреждениями, организациями и гражданами – субъектами предпринимательской деятельности, на деятельность которых распространяется действие стандартов.
Рекомендованные требования государственных стандартов Украины подлежат безусловному выполнению, если:
– это предусмотрено действующими актами законодательства;
– эти требования включены к договорам на разработку, изготовление и поставку продукции;
– изготовителем (поставщиком) продукции сделано заявление о соответствии продукции этим стандартам.
Сертификация продукции в Украине делится на обязательную и добровольную.
Сертификация продукции осуществляется уполномоченными на то органами по сертификации – предприятиями, учреждениями и организациями с целью:
– предотвращения реализации продукции, опасной для жизни, здоровья и имущества граждан и окружающей естественной среды;
– содействия потребителю в компетентном выборе продукции;
– создания условий для участия субъектов предпринимательской деятельности в международном экономическом, научно–техническом сотрудничестве и международной торговле.
Государственную систему сертификации создает Государственный комитет Украины по стандартизации, метрологии и сертификации – национальный орган Украины по сертификации, который проводит и координирует работу относительно обеспечения ее функционирования, а именно:
– определяет основные принципы, структуру и правила системы сертификации в Украине;
– утверждает перечни продукции, которая подлежит обязательной сертификации, и определяет сроки ее внедрения;
– назначает органы по сертификации продукции;
– аккредитирует органы по сертификации и испытательные лаборатории (центры), аттестует экспертов–аудиторов;
– устанавливает правила признания сертификатов других стран;
– рассматривает спорные вопросы испытаний и соблюдения правил сертификации продукции;
– ведет Реестр государственной системы сертификации;
– организует информационное обеспечение по вопросам сертификации.
Государственный комитет Украины по стандартизации, метрологии и сертификации в границах своей компетенции несет ответственность за соблюдение правил и порядка сертификации продукции.
Сертификация на соответствие обязательным требованиям нормативных документов проводится исключительно в государственной системе сертификации.
Обязательная сертификация во всех случаях должна включать проверку и испытание продукции для определения ее характеристик и дальнейший государственный технический надзор за сертифицированной продукцией.
Испытания с целью обязательной сертификации должны проводиться аккредитованными испытательными лабораториями (центрами) методами, которые определены соответствующими нормативными документами, а из–за отсутствия этих документов –методами, которые определяются органом из сертификации, или органом, который выполняет его функции.
Во время проведения сертификации и в случае положительного решения органа по сертификации заявителю выдается сертификат и право маркировать продукцию специальным знаком соответствия.
Форма, размеры и технические требования к знаку соответствия определяются государственным стандартом.
Знак соответствия не может быть использован, если нарушат правила его использования.
Контрольные вопросы к восьмой теме
1. Охарактеризуйте основополагающие принципы концепции качества.
- Категория «качество». Ключевые аспекты качества.
- История применения основных принципов TQM.
- Охарактеризуйте технологию развертывания функций качества.
- Охарактеризуйте технологию осуществления функционально–стоимостного анализа.
- Охарактеризуйте технологию анализа возможности возникновения дефектов и их влияния на потребителя.
- Охарактеризуйте технологию осуществления функционально–физического анализа.
- Менеджмент, планирование, контроль качества.
- Методы контроля качества.
- Охарактеризуйте единую схему разработки и внедрения системы управления качеством.
- Перечислите виды затрат, направленные на обеспечение системы управления качеством.
- Государственное и общественное регулирование процесса повышения качества в Украине.
- Охарактеризуйте содержание руководства по качеству.
- Охарактеризуйте систему стандартизации и сертификации в Украине.
Упражнения к восьмой теме
1. Определите перечень принципов функционирования системы управления качеством проекта.
2. Сформируйте перечень требований потребителей на всех стадиях производства готовой продукции.
3. Проведите функционально–стоимостной анализ проекта.
4. Проанализируйте возможности возникновения дефектов и их влияние на потребителя.
5. Постройте диаграмму причин–следствий для реализуемого проекта.
6. Сформируйте контрольную карту реализации проекта.
7. Постройте диаграмму Парето.
8. Разработайте Программу качества.
- Разработайте Руководство по реализации Программы качества.