Десятые академические чтения раасн, 2006 г
Вид материала | Документы |
- Десятые академические чтения раасн, 2006, 1092.49kb.
- Десятые академические чтения раасн, 2006, 1266.3kb.
- Концепция устойчивого развития в стратегии градостроительства франции 05. 23. 22 Градостроительство,, 332.07kb.
- Резолюция районной детской экологической конференции Десятые Басарукинские чтения, 39.32kb.
- План организационно-педагогической деятельности с детьми, имеющими ярко-выраженные, 77.33kb.
- Новосибирский государственный педагогический университет, 43.06kb.
- Академические программы и экзаменационные курсы в австралии международные центры Embassy, 146.35kb.
- Экология человек общество, 371.15kb.
- Министерство образования и науки российской федерации московский государственный областной, 2810.15kb.
- Рассказывайте детям о ценности чтения. Показывайте связь чтения с их успехами в учебе, 97.26kb.

ДЕСЯТЫЕ АКАДЕМИЧЕСКИЕ ЧТЕНИЯ РААСН, 2006 г.
УДК 691.002-404.9
Кузнецов Ю.С., канд. техн. наук, профессор, Калашников В.И., д-р. техн. наук, профессор,
Новокрещенова С.Ю., канд. техн. наук, доцент, Гаврилова Ю.В., аспирант
Пензенский государственный университет архитектуры и строительства
К ПРОБЛЕМЕ ПЕРЕМЕШИВАНИЯ СЫРЬЕВЫХ ШЛАМОВ В ПРОИЗВОДСТВЕ
КОМПОЗИЦИОННЫХ СТРОИТЕЛЬНЫХ МАТЕРИАЛОВ
Большинство сырьевых шламов, используемых в производстве вяжущих веществ, ячеистых бетонов, керамики и многих других строительных материалов, представляют собой высококонцентрированные суспензии. Суспензии – системы с твёрдой дисперсной фазой и жидкой дисперсионной средой. Они имеют ряд общих свойств с порошками; эти системы подобны по дисперсности. Если порошок поместить в жидкость и перемешать, то получится суспензия, а при высушивании суспензии она снова превращается в порошок. Концентрированные суспензии часто называют пастами, пульпами, шламами, шликерами.
Свойства современных композиционных материалов строительного назначения в значительной мере зависят от степени гомогенизации сырьевых смесей. Операция перемешивания ставит перед собой цель достичь не только равномерного химического и вещественного состава, но и гранулометрического. Современное строительное материаловедение отводит значительную, а порою и определяющую роль гранулометрического состава твёрдой фазы в процессах структурообразования композиционных строительных материалов. Решить проблему оптимальной гомогенизации сырьевых смесей только за счёт конструктивных качеств смесительных аппаратов без учёта физико-химических особенностей процесса перемешивания невозможно. Важнейшей задачей является также одновременное снижение энергоёмкости процесса гомогенизации за счёт использования эффективных адсорбционно-активных сред.
В зависимости от дисперсности твёрдой фазы суспензии принято подразделять на грубые (диаметр частиц более 100 мкм), тонкие (от 100 до 0,5 мкм) и мути (от 0,5 до100 нм). Иногда в эту классификацию включают золи (коллоидные растворы) с размерами частиц менее 100 нм, хотя по ряду специфических признаков они представляют качественно отличающийся вид дисперсных систем.
Шламы и шликеры, используемые в технологии многих строительных материалов, следует отнести к тонким концентрированным суспензиям, так как частицы в них диаметром более 110 мкм практически не наблюдаются. Основная масса частиц имеет размеры менее 70 мкм. Часто предусматривается длительный процесс перемешивания шламов. Это связано с необходимостью достижения полной гомогенизации шлама по своим физико-химическим параметрам, особенно однородности распределения относительно крупных частиц по всему объёму.
Целью настоящего исследования является снижение времени перемешивания шлама за счёт повышения его кинетической и агрегативной устойчивости при введении добавок ПАВ, в том числе на основе промышленных отходов предприятий микробиологического синтеза.
Характерным общим свойством свободнодисперсных микрогетерогенных систем, особенно если они разбавлены, является склонность к оседанию или всплыванию частиц дисперсной фазы. Оседание частиц дисперсной фазы называется седиментацией, а всплывание частиц – обратной седиментацией. На каждую частицу в системе действует сила тяжести и сила Архимеда:
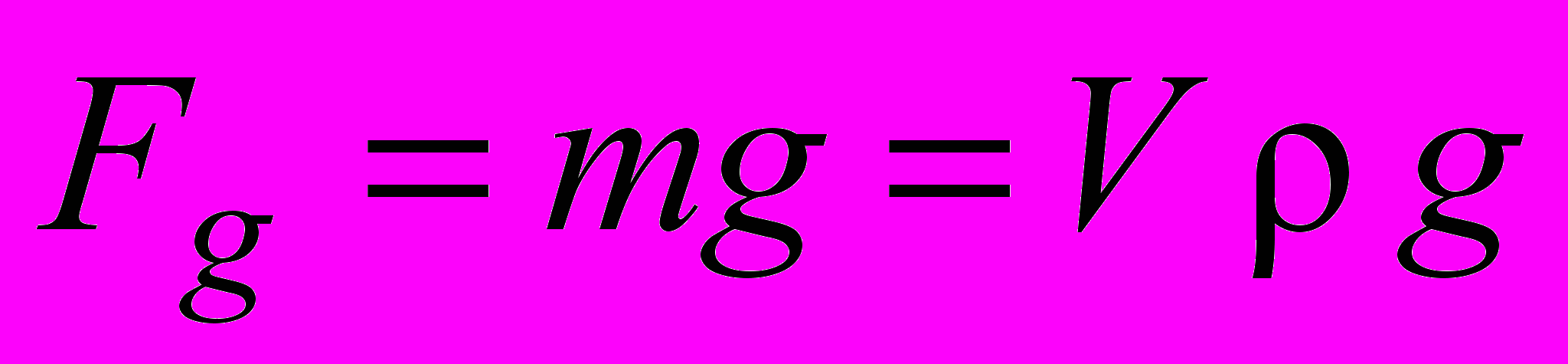
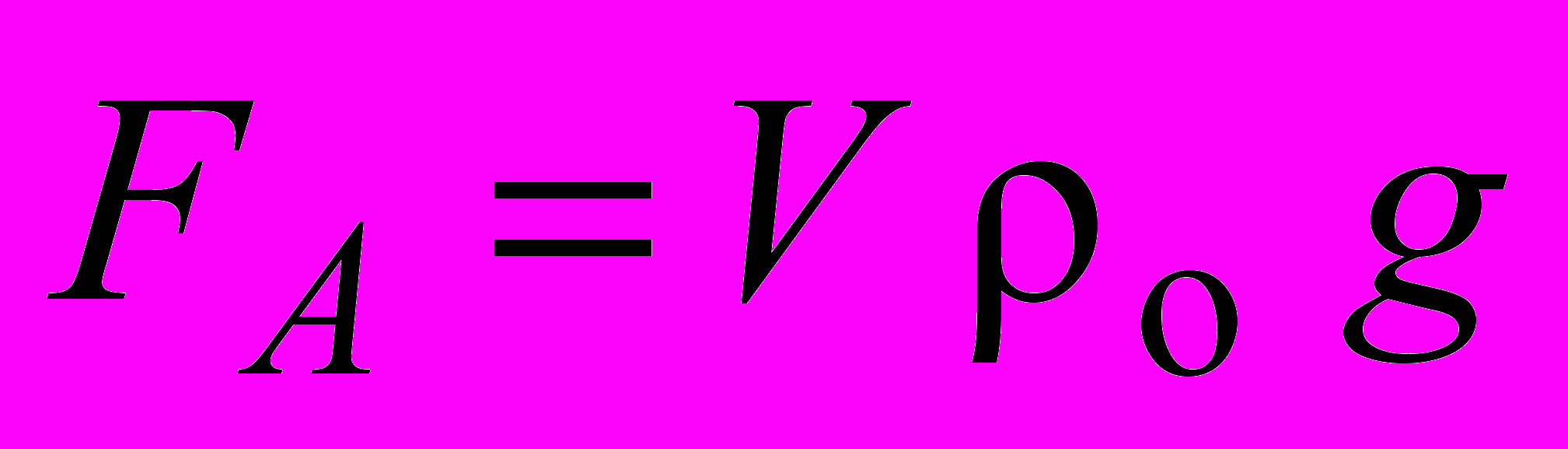
где m и V – масса и объём частицы; g- ускорение свободного падения;
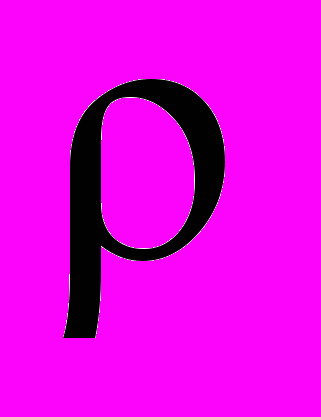
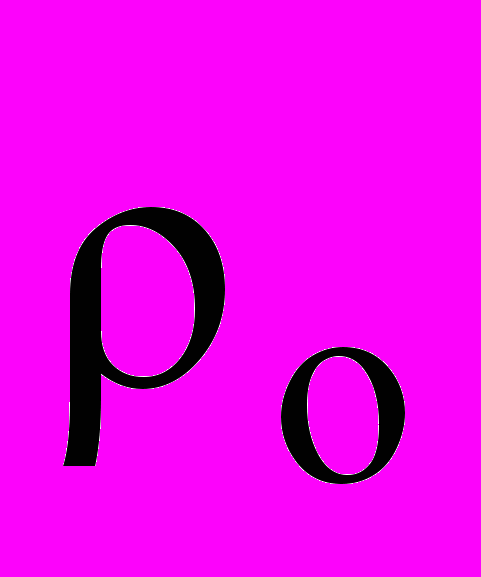
Эти силы постоянны и направлены в разные стороны. Равнодействующая сила, вызывающая седиментацию, равна:

где mот – относительная масса частицы (с учётом плотности среды
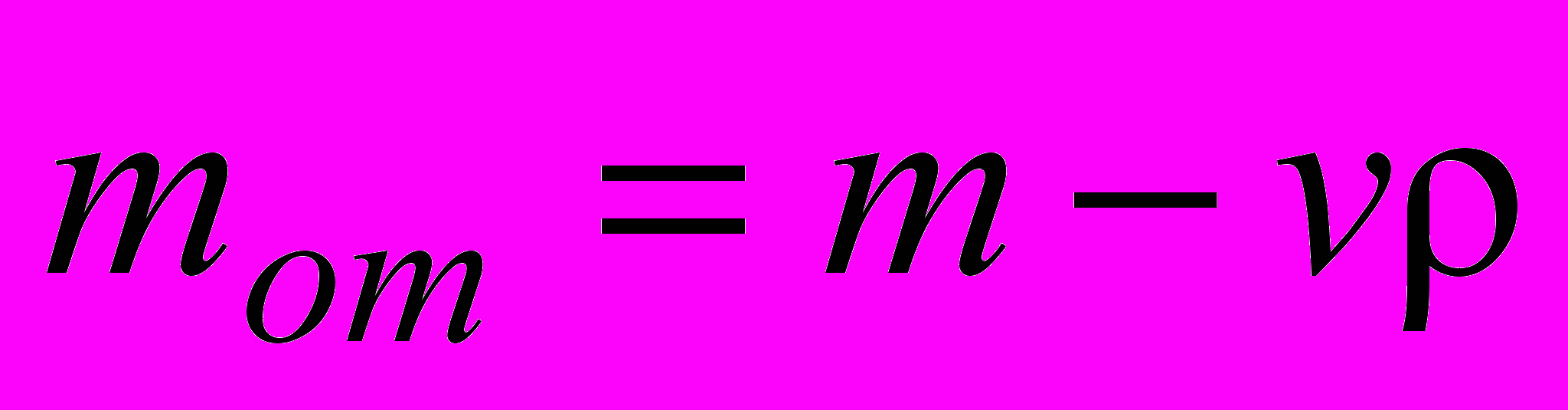
Если
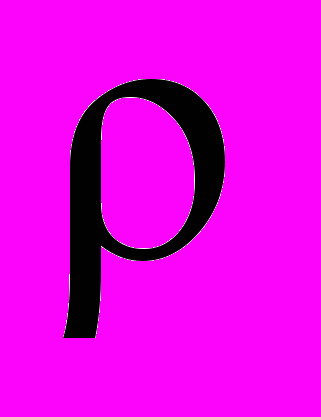
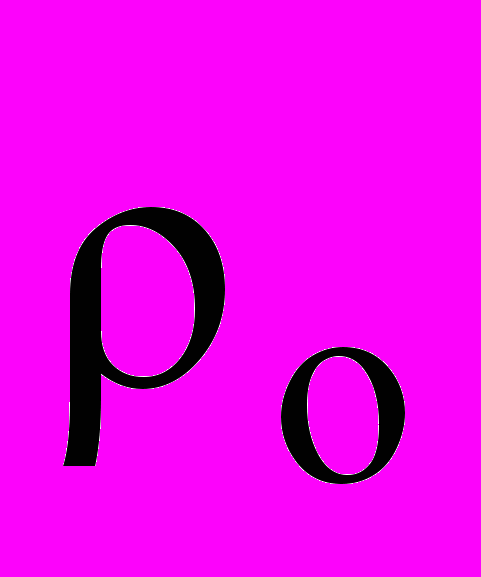
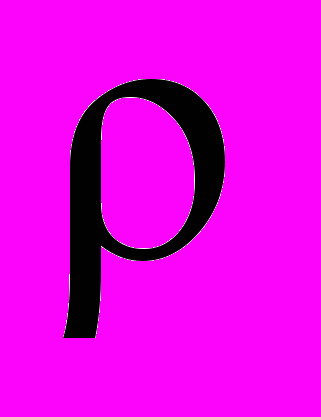
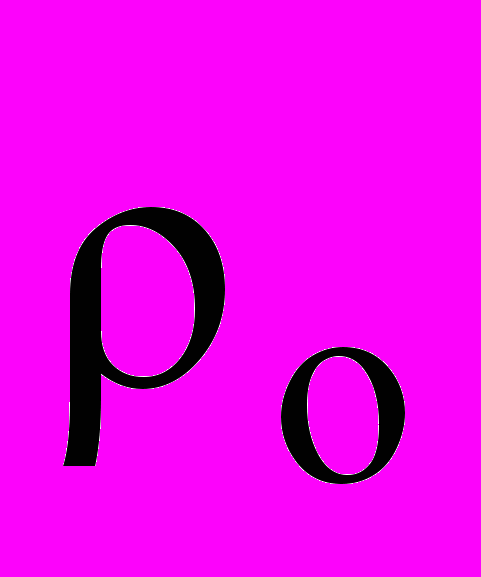
Так как седиментация происходит в определённой среде, то при ламинарном движении частицы возникает сопротивление в виде силы трения, пропорциональной скорости движения частицы:
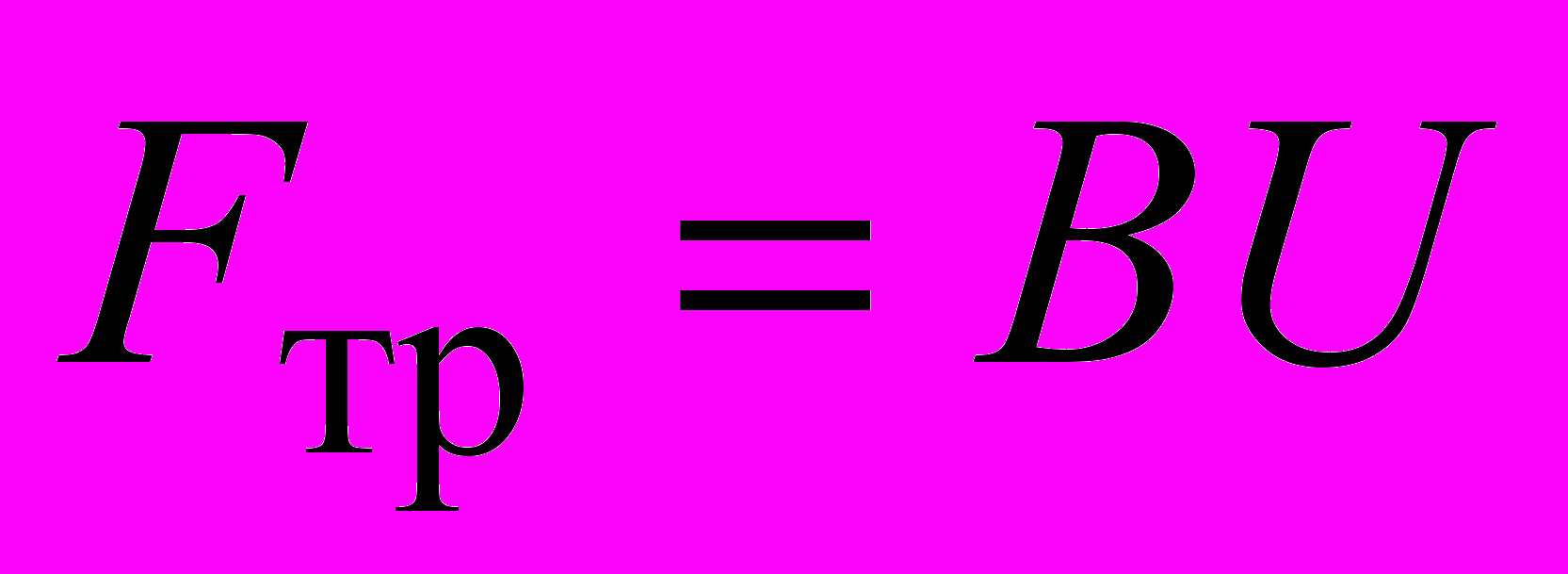
где В – коэффициент трения; U – скорость движения частицы.
Таким образом сила, действующая на частицу, равна:

В первый момент начала движения частицы её скорость очень мала, и поэтому частица движется под действием силы F ускоренно. С ростом скорости при достаточно большом коэффициенте трения наступает момент, когда сила трения достигает силы, вызывающей седиментацию, и движущая сила F оказывается равной нулю. После этого момента скорость движения частицы становится постоянной, её можно определить из уравнения (4) при условии F=0:
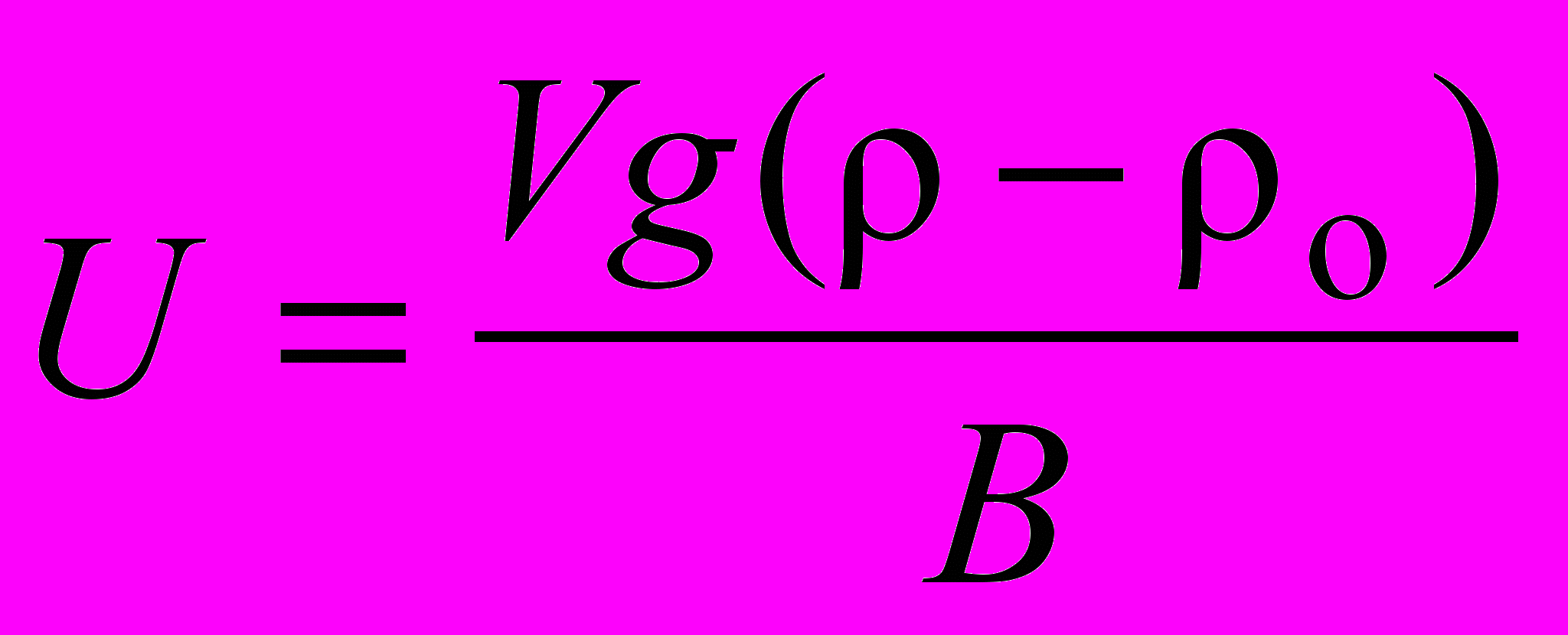
Выражения для силы трения (3) при движении сферических частиц можно представить в виде закона Стокса:
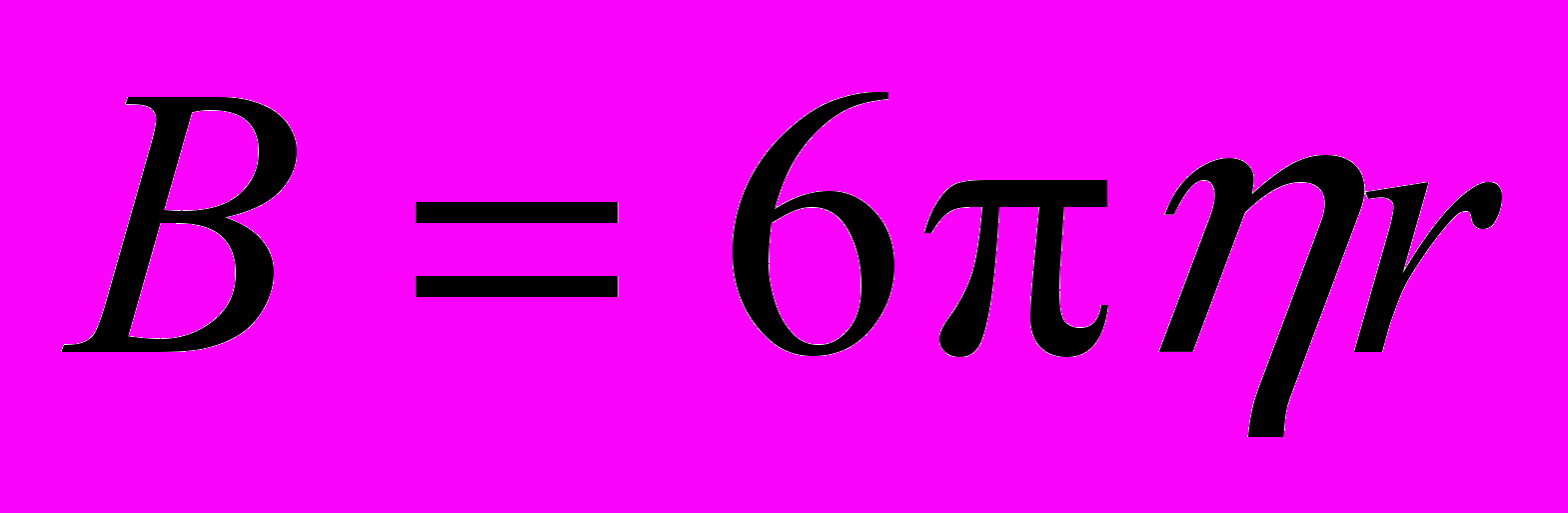
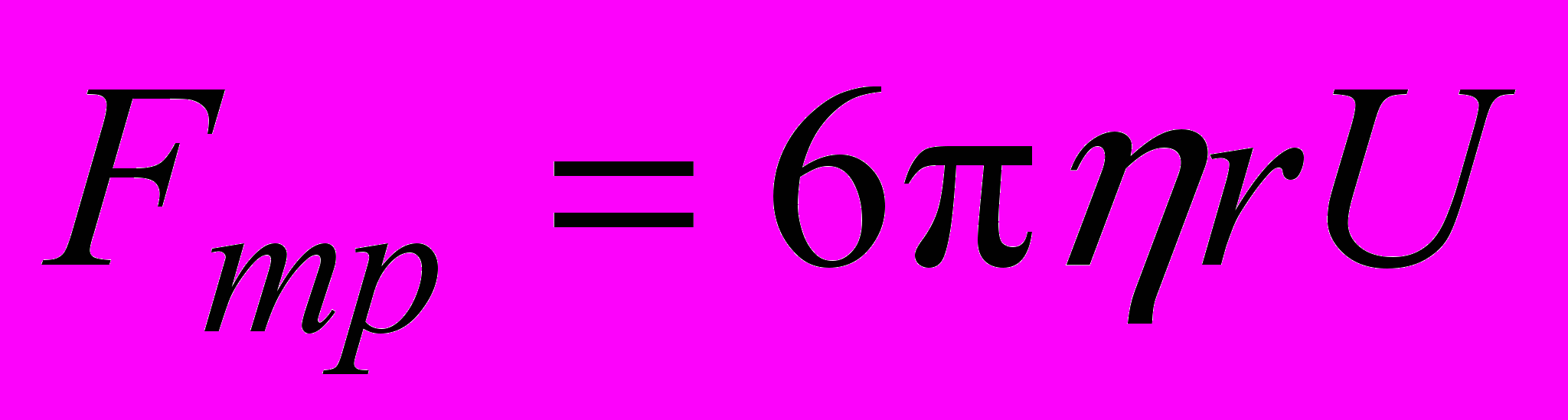
где η – динамическая вязкость среды; r – радиус частицы.
Подставляя уравнение (6) в (5) и выражая объём частицы через её радиус, получим:
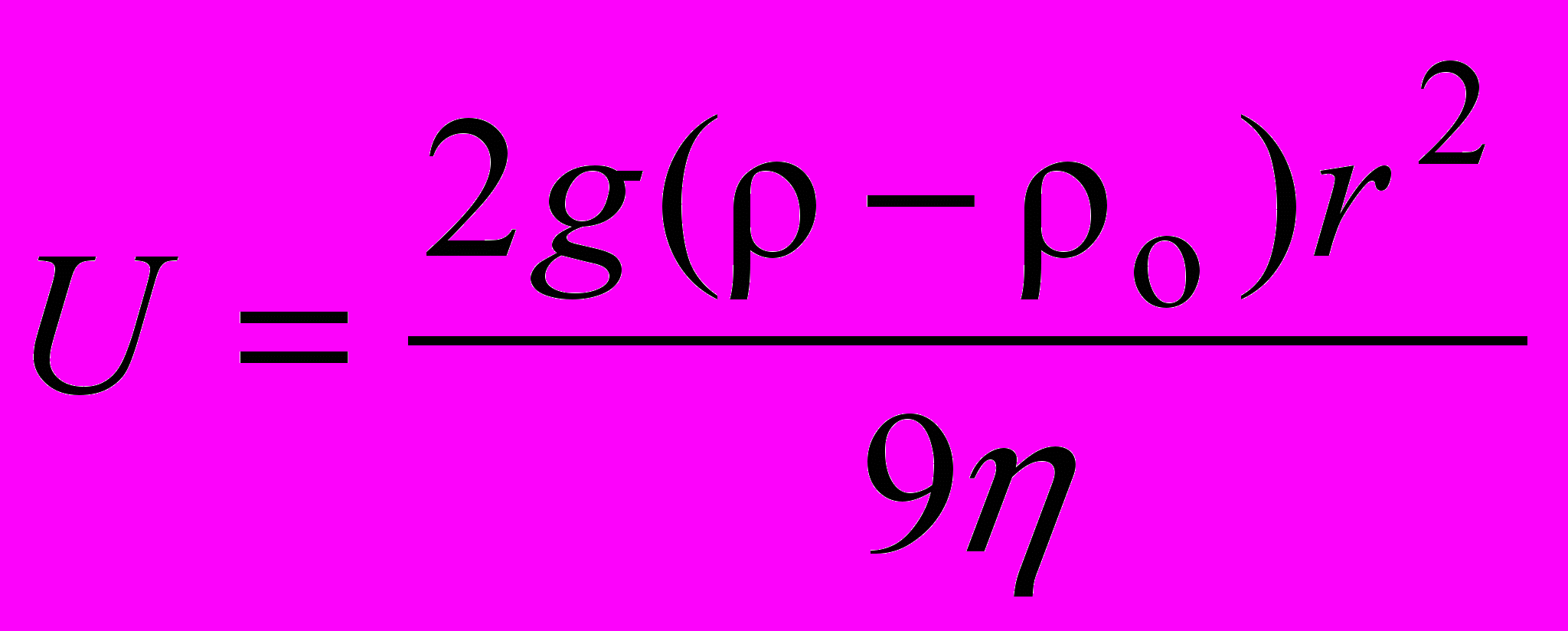
Соотношение (7) показывает, что постоянная скорость седиментации частицы пропорциональна квадрату её радиуса, разности плотностей частицы и среды, обратно пропорциональна вязкости среды. По такому закону происходит осаждение частиц в суспензиях, аэрозолях, эмульсиях.
Относительно радиуса частицы уравнение (7) принимает вид:
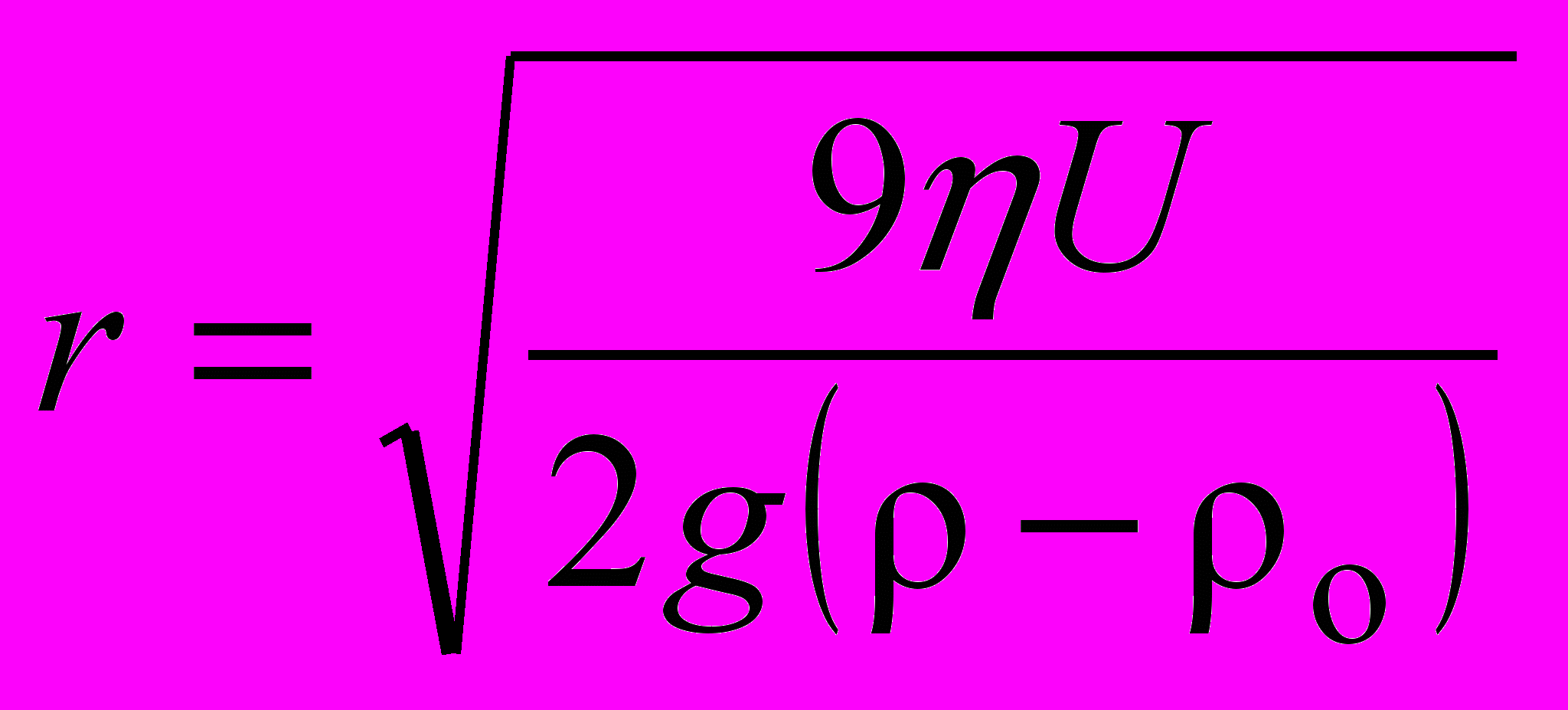
Определив экспериментально скорость седиментации и зная величины η,
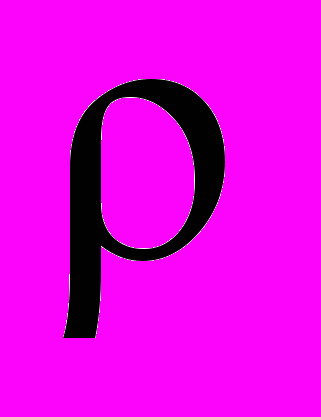
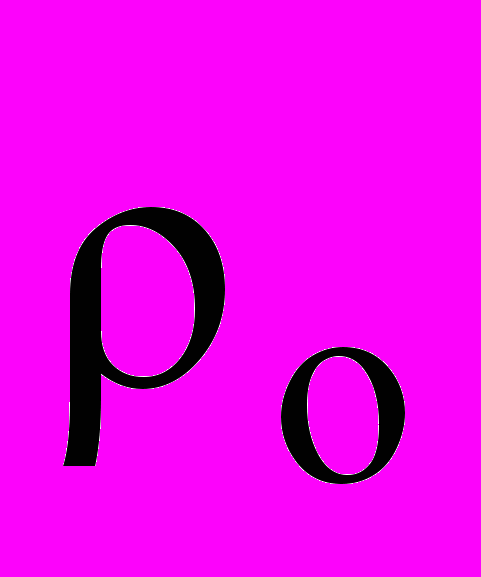
Способность к седиментации принято выражать через константу седиментации, которая определяется скоростью седиментации:
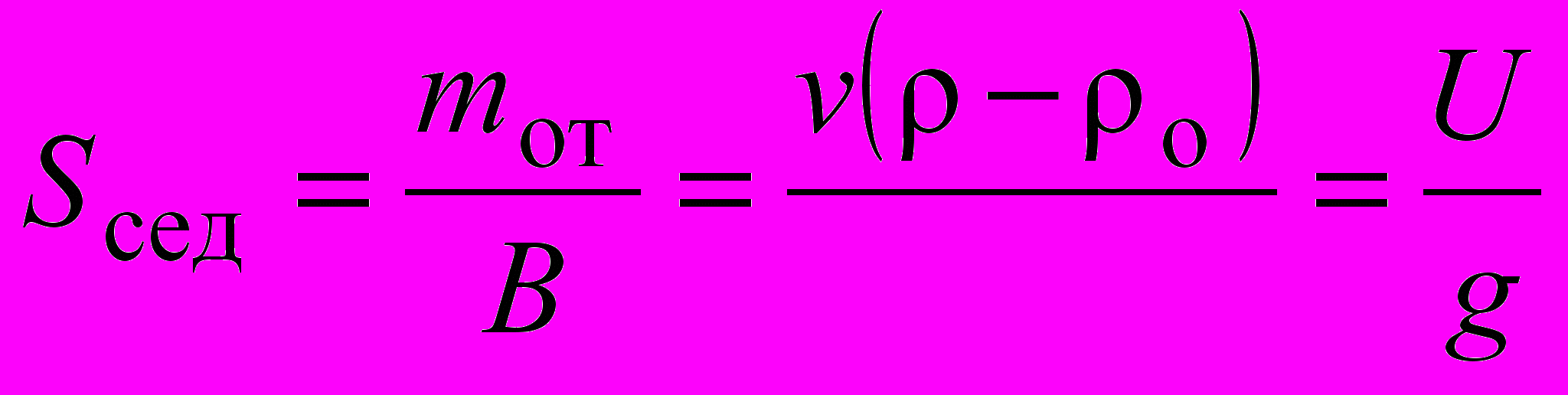
Для сферических частиц эта константа равна
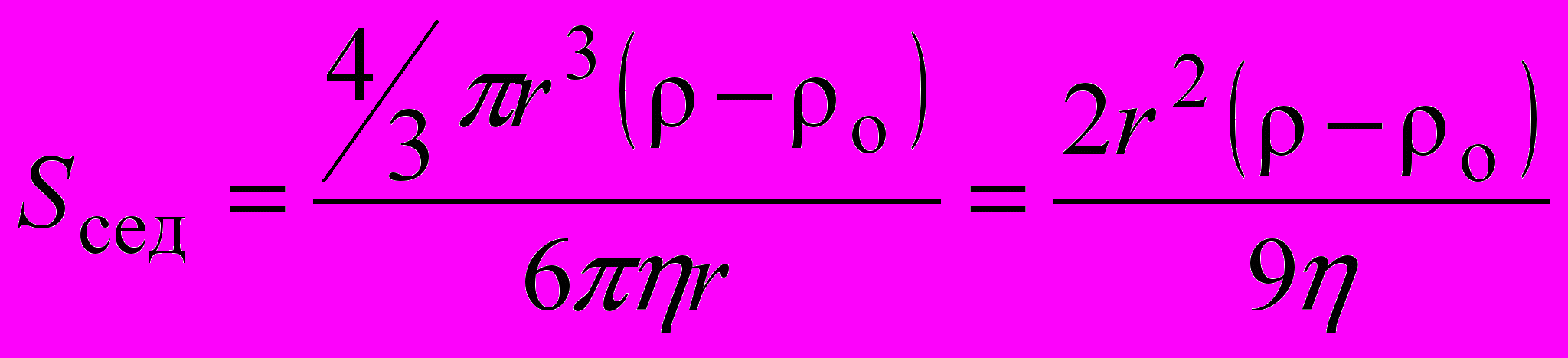
Из уравнения (10) следует, что константа седиментации зависит как от размеров частиц, так и от природы фаз. За единицу измерения константы седиментации принят сведберг (1 Сб=10–13 с). Для аэрозолей, суспензий и эмульсий в маловязких средах константа седиментации имеет очень большие значения, поэтому для таких систем ее удобнее измерять в мегасведбергах (1 МСб=106 Сб), гигасведбергах (1 ГСб=109 Сб) или же просто в секундах. Например, для частиц кварца (
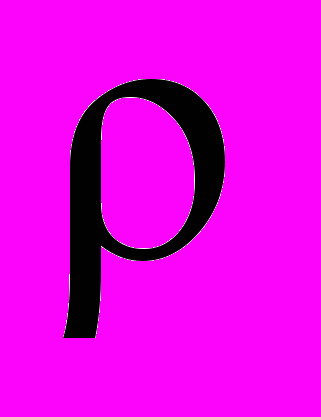
Если частицы в суспензиях очень малы и их размеры приближаются к размерам частиц золей, то седиментация только под действием гравитационных сил протекает очень медленно. Данные, рассчитанные по уравнению (5) приведены в табл.1.
Таблица 1
Скорость седиментации сферических частиц кварца в воде
Радиус частицы, мкм | Скорость седиментации, см/c | Время оседания частицы на 1 см |
10 1 0,1 0,01 0,001 | 3,6 х 10-2 3,6 х 10-4 3,6 х 10-6 3,6 х 10-8 3,6 х 10-10 | 28 с 46,5 мин 77,5 ч 323 дн 89 лет |
Данные таблицы 1 иллюстрируют влияние размеров частиц кварца на скорость их оседания в воде ( η = 10-3 Па·с).
Электрический потенциал и структура двойных электрических слоёв мало зависят от размеров частиц. Однако, увеличение удельной поверхности в дисперсной системе приводит к повышению концентрации противоионов двойного слоя, что в свою очередь может влиять на многие свойства системы, в том числе и на свойства этого слоя.
Если противоионами в двойном электрическом слое являются Н+ или ОН– ионы, то наблюдается так называемый суспензионный эффект, сущность которого состоит в том, что значение рНс отличается от значения рНф выделенного из неё фильтрата. Количественно суспензионный эффект характеризуется величиной рНсэ = рНс – рНф, которая возрастает с увеличением концентрации дисперсной фазы в суспензии, а при постоянной массовой концентрации дисперсной фазы – с увеличением её дисперсности, т.е. эффект повышается с увеличением межфазной поверхности в суспензии. Значение суспензионного эффекта уменьшается с повышением концентрации электролитов в системе, что ещё раз подтверждает причину возникновения этого эффекта. Знак суспензионного эффекта (рНсэ) совпадает со знаком заряда поверхности частицы.
Различие в размерах частиц дисперсной фазы отражается на молекулярно-кинетических свойствах дисперсных систем. Частицы суспензий не участвуют в броуновском движении, они не способны к диффузии и как следствие в отличие от лиозолей суспензии седиментационно не устойчивы и в них практически отсутствует осмотическое давление. Молекулярно-кинетическое движение частиц лиозолей обусловливает энтропийное отталкивание частиц, обеспечивает равномерное их распределение по объёму дисперсионной среды. Энтропийный фактор агрегативной устойчивости у суспензий отсутствует, скорость их коагуляции не зависит от броуновского движения и не может следовать закономерностям теории кинетики коагуляции Смолуховского, а связана в основном со свойствами прослоек дисперсионной среды. Действия других факторов агрегативной устойчивости в суспензиях и лиозолях имеют много общего.
Агрегативно устойчивые и неустойчивые суспензии и лиозоли проявляют существенные различия при образовании осадков в результате коагуляции. Они имеют разные седиментационные объёмы и структуры осадков. В агрегативно-устойчивых системах оседание частиц происходит медленно и образуется очень плотный осадок. Объясняется это тем, что поверхностные слои препятствуют агрегированию частиц; скользя друг по другу, частицы могут перейти в положение с минимальной потенциальной энергией. В агрегативно-неустойчивой системе оседание частиц происходит значительно быстрее вследствие образования агрегатов. Однако выделяющийся осадок занимает гораздо больший объём, так как частицы сохраняют то случайное взаимное расположение, в котором они оказались при первом же контакте, силы сцепления между ними соизмеримы с их силой тяжести или больше её.
Разница седиментационных объёмов агрегативно-устойчивых и неустойчивых систем наиболее чётко проявляется, если частицы имеют средние размеры. Крупные частицы неустойчивых систем благодаря заметной силе тяжести образуют более плотный осадок, а очень мелкие частицы в устойчивых системах оседают настолько медленно, что наблюдать за осаждением не представляется возможным. Причиной рыхлости осадков является анизотропия образующихся первичных агрегатов или флокул. Исследования показывают, что наиболее вероятны цепочечные и спиральные первоначальные образования, из которых затем получаются осадки с большим седиментационным объёмом. Осадки того или иного качества получают при осаждении и фильтрации суспензий в различных производствах. Их свойства обычно регулируют путём изменения рН, добавления поверхностно-активных веществ. Увеличение концентрации дисперсной фазы способствует образованию объёмной структуры в агрегативно-неустойчивых системах. Этот факт широко используется для предотвращения седиментации, в частности, при получении пластичных материалов и изделий из них.
Безусловно, явления агрегативной и седиментационной устойчивости промышленных шламов осложнены полидисперсной структурой, наличием коллоидной фракции, явлениями коагуляции и пептизации, характером механического перемешивания и др. Однако, бесспорным фактом является возможность управлять этими явлениями с помощью адсорбционно-активных сред. На кафедре технологии бетонов, керамики и вяжущих Пензенского государственного университета архитектуры и строительства в течение ряда лет ведутся исследования возможности интенсификации технологических процессов производства композиционных строительных материалов физико-химическими методами. В лабораторных условиях изучалось влияние на устойчивость минеральных суспензий как индивидуальных ПАВ, так и многочисленных побочных продуктов микробиологического синтеза и деревообработки.
Возможность сокращения времени перемешивания шлама проверялась и в производственных условиях. Специальным пробоотборником через каждый метр по высоте шламбассейна цеха по производству газобетона отбиралась проба песчаного шлама. Все пробы подвергались анализу гранулометрического состава на фотоседиментографе.
По результатам промышленного эксперимента можно сделать однозначный вывод: за счёт введения ПАВ представляется возможным снизить время перемешивания до 2-4 часов вместо 8-12, рекомендованных технологией. Более длительное перемешивание тихоходной лопастной мешалкой не способствует однородному распределению крупных частиц – они продолжают седиментировать даже в условиях перемешивания.
Оптимальным вариантом является использование ПАВ полифункционального действия, что позволяет получить от таких добавок многократный эффект. Вводя добавку ПАВ на начальной стадии технологического процесса непосредственно в шаровую мельницу, можно одновременно получить эффект адсорбционного понижения прочности и повысить производительность мельницы, эффект повышения кинетической и агрегативной устойчивости шлама на стадии его перемешивания, пластифицирующий эффект на стадии формования изделий из сырьевой ячеисто-бетонной массы.
СПИСОК литературЫ
- С.С. Воюцкий. Курс коллоидной химии.- М.: Изд-во «Химия», 1964.- 574 с.
- Ю.С. Кузнецов, С.Ю. Тимофеева. Физико-химические методы снижения энергоёмкости производства ячеистых бетонов// Современные проблемы строительного материаловедения: четвёртые академические чтения РААСН, материалы международной НТК.- Пенза, 1998.- Часть П, С 187-188.
УДК 666.189.21.3.001.5
Кулаева Н.С., аспирант
Магнитогорский государственный технический университет
УСТАНОВЛЕНИИ ОПТИМАЛЬНЫХ ПАРАМЕТРОВ ИЗГОТОВЛЕНИЯ БРИКЕТОВ
ДЛЯ ПОЛУЧЕНИЯ ПЕНОСТЕКЛА
Производство ячеистого стекла – высокоэффективного универсального теплоизоляционного материала, относится к достаточно сложным и энергоемким процессам. Предварительное брикетирование пеностекольной шихты позволит отказаться от использования форм и тем самым упростить традиционный порошковый способ получения пеностекла.
Свойства брикетов и получаемого из них пеностекла зависят от ряда факторов, главными из которых являются давление прессования, вид и количество связки.
Для изготовления брикетов бесцветный стеклобой измельчали в центробежно-ударной мельнице до удельной поверхности 400 м2/кг. Преимущество центробежно-ударного измельчения по сравнению с помолом в шаровой мельнице заключается в получении порошка узкого гранулометрического состава с однородными по форме частицами высокой дефектности. Газообразователь - доломит (CaMg(CO3)) с удельной поверхностью 250 м2/кг.
В качестве технологических связок использовали водный раствор силиката натрия плотностью 1120 кг/м3 в количестве 8 - 12 % от массы сухого вещества, портландцемент М500 и молотую негашеную известь в количестве 1 - 9 % от массы сухого вещества. Оптимальную влажность определяли по изменению пластической прочности брикета 1.
Формование образцов-цилиндров диаметром 5 см и высотой 4,5-5 см осуществляли методом двустороннего прессования в скользящей пресс-форме. Брикеты сушили в нормальных условиях в течение 24 часов. Вспучивание производили при температуре 750 0С, скорость нагрева 4,8 0С/мин. Продолжительность выдержки при максимальной температуре 30 мин.
На рис.1 и 2 показано влияние давления прессования и количества связки на плотность брикетов и полученного из них пеностекла. При постоянном количестве связки с увеличением давления прессования плотность брикетов растет, т.к. степень деформации частиц возрастает и, как следствие, контактная поверхность увеличивается (рис.1). Сопоставление данных рис.1 и рис. 2 показывает, что из более плотных брикетов получается пеностекло меньшей плотности, т.к. чем лучше и равномернее уплотнена шихта, тем выше вероятность получения пеностекла (при прочих равных условиях) с более низкой плотностью и равномерно организованной структурой. Механические воздействия при брикетировании изменяют и активизируют процессы структурообразования, способствуя сближению частиц и увеличению площади контакта между ними, поэтому существенно снижаются потери газа, нежели при свободно засыпанной сырьевой шихте 2. Кроме того, при получении пеностекла предварительное уплотнение шихты в форме позволяет сформировать слой с равномерной пористостью по объему и с меньшим начальным размером пор, что способствует более равномерной поризации слоя при нагреве, интенсифицирует спекание шихты в период ее прогрева 3. Процесс поризации предопределяется теплофизическими свойствами шихты и прежде всего ее теплопроводностью, которая существенно возрастает при уплотнении [2]. Однако это утверждение справедливо только в том случае, когда увеличение плотности брикета достигается только изменением давления прессования. Увеличение содержания связки в шихте так же ведет к увеличению плотности брикета, т.к. жидкость смачивает и разделяет частицы, уменьшая трение между ними, однако плотность пеностекла в этом случае заметно возрастает.
Увеличение количества жидкостекольной связки в брикете повлекло за собой снижение вязкости и поверхностного натяжения стекломассы, что, в свою очередь, способствовало развитию процесса коалесценции пор и росту плотности пеностекла.
В случае использования известковой связки вспучиванию стекломассы препятствует процесс ожелезнения извести, который тем заметнее, чем больше извести в сырьевой шихте. Кроме того, в температурном диапазоне спекания шихты гидроксид кальция начинает терять воду, вследствие чего формируется пеностекло с неравномерной пористостью (рис. 3, а). Образующиеся пары воды разрывают поры и деформируют структуру пеностекла, увеличивая его плотность.
Спекание компонентов портландцемента в меньшей степени препятствует процессу вспучивания стекломассы. Химически связанную воду цемент теряет при температуре 200 0С, т.е. до температуры спекания шихты, пары воды беспрепятственно выходят из брикета, не нарушая его структуры. Формируется пеностекло с равномерной замкнутой пористостью (рис. 3, б).
Вид связки практически не влияет на плотность брикетов (рис. 1) При постоянном давлении прессования влияние вида связки заметно отражается на свойствах полученного пеностекла. Например: пеностекло плотностью 250 кг/м3 в случае использования жидкостекольной связки получается из брикетов плотностью 1360 кг/м3 с содержанием связки 8%; в случае использования цементной связки в количестве 1% из брикетов плотностью 1375 кг/м3; при использовании известковой связки решающее значение имеет только количество связки, которое не должно превышать 3,5%.
а | ![]() | а | ![]() | |
б | ![]() | б | ![]() | |
в | ![]() | в | ![]() | |
Рис. 1. Влияние давления прессования и количества связки на плотность брикетов, изготовленных на различных связках: а) жидкое стекло; б) портландцемент; в) известь | | | Рис. 2. Влияние давления прессования и количества связки на плотность пеностекла, изготовленного на различных связках: а) жидкое стекло; б) портландцемент; в) известь |
а | ![]() | б | ![]() |
Рис. 3. Структура пеностекла, полученного из брикетов на известковой (а) и цементной (б) связках |
Из всего вышесказанного следует, что пеностекло с минимальной плотностью и равномерной пористостью возможно получить из брикетов плотностью не менее 1350 кг/м3 с минимальным количеством связки, способным обеспечить брикетам прочность, необходимую для транспортировки в печь вспенивания.
Таким образом, изменяя давление прессования, вид связки и ее количество, можно направленно в широком диапазоне изменять характеристики и свойства пеностекла.