Десятые академические чтения раасн, 2006 г
Вид материала | Документы |
- Десятые академические чтения раасн, 2006, 1092.49kb.
- Десятые академические чтения раасн, 2006, 1266.3kb.
- Концепция устойчивого развития в стратегии градостроительства франции 05. 23. 22 Градостроительство,, 332.07kb.
- Резолюция районной детской экологической конференции Десятые Басарукинские чтения, 39.32kb.
- План организационно-педагогической деятельности с детьми, имеющими ярко-выраженные, 77.33kb.
- Новосибирский государственный педагогический университет, 43.06kb.
- Академические программы и экзаменационные курсы в австралии международные центры Embassy, 146.35kb.
- Экология человек общество, 371.15kb.
- Министерство образования и науки российской федерации московский государственный областной, 2810.15kb.
- Рассказывайте детям о ценности чтения. Показывайте связь чтения с их успехами в учебе, 97.26kb.
СПИСОК литературЫ
- Белоусов Е.Д., Линде Е.М., А.С. Быков Полы жилых и общественных зданий – Москва: Стройиздат, 1974, 337 с.
- Дегтев И.А. Современные технологии устройства и ремонта полов: Уч. пособие/ И.А. Дегтев, О.М. Донченко, М.В. Кафтаева.-М.:АСВ.2004, 144 с.
- СНиП 23-02-2003 Тепловая защита зданий.
- СП 23-101-2000 Проектирование тепловой защиты зданий.
УДК691. 3:620. 197. 6(035. 5)
Логанина В. И., д-р техн. наук, профессор, Саденко С. М., канд. тех. наук., профессор, Голубев В. В. Пензенский государственный университет архитектуры и строительства
ЗАКОНОМЕРНОСТИ ФОРМИРОВАНИЯ КАЧЕСТВА ВНЕШНЕГО ВИДА ЛАКОКРАСОЧНЫХ ПОКРЫТИЙ В ЗАВИСИМОСТИ ОТ ПОРИСТОСТИ ПОДЛОЖКИ
И РЕОЛОГИЧЕСКИХ СВОЙСТВ КРАСОЧНЫХ СОСТАВОВ
В соответствии с ГОСТ 9. 032 - 74 ** «Единая система защиты от коррозии и старения. Покрытия лакокрасочные. Группы, технические требования и обозначения» определены семь классов качества внешнего вида покрытий на металлической подложке в зависимости от наличия неровностей, включений, разнотонности, шагрени, потеков, волнистости и т.д.
Условия получения и качество внешнего вида покрытий во многом зависят от реологических свойств исходных красочных составов и определяются процессами смачивания и растекания, на которые, в свою очередь, оказывает влияние качество подложки. Результаты проведенных ранее исследований показали, что для оценки качества внешнего вида покрытий может быть использована методика, основанная на определении и анализе шероховатости их поверхности [1]. Для установления связи показателей качества внешнего вида покрытий с реологическими свойствами лакокрасочных составов, пористостью цементной подложки был проделан следующий эксперимент. Исследуемые краски наносились на растворную подложку в два слоя с промежуточной сушкой в течение 20 минут. Перед нанесением красочных составов поверхность подложки загрунтовывалась. В процессе проведения испытаний использовали растворные образцы с объемной пористостью 24%, 28%, 32%. Для снижения поверхностной пористости часть подложек выравнивалась шпаклевочными составами. Реологические свойства красок оценивали по показателю их условной динамической вязкости и поверхностному натяжению. Растекание красок оценивали по значению краевого угла смачивания красочных составов. В работе применяли следующие красочные составы: эмаль алкидная марки ПФ-115, масляная краска марки МА-15, акриловая вододисперсионная (фасадная) краска. Шероховатость поверхности покрытия определяли с помощью прибора профилографа марки TR-100. Результаты исследований приведены в табл.1,2.
Таблица 1
Шероховатость покрытий в зависимости от реологических свойств красочных составов
Вид красочного состава | Поверхностное натяжение, s, (мН/м2) | Динамическая вяз- кость, h ,(Па×с).103 | Краевой угол смачивания, q0 | Шероховатость покрытия, Ra,мкм |
1 | 2 | 3 | 4 | 5 |
ПФ-115 1 2 3 | 22,3 20,8 20 | 0,001 0,00065 0,00026 | 14,7 13,2 7 | 1,14 1,36 1,58 |
МА-15 1 2 3 | 23,1 22,4 18,3 | 0,0026 0,002 0,0014 | 62,5 48,2 42 | 1,2 1,56 2,02 |
ВД 1 2 3 | 36,37 33,5 29,1 | 0,0347 0,02317 0,013 | 74,8 65,1 56,1 | 2,5 3,37 4,35 |
Анализ экспериментальных данных (табл.1) свидетельствует о том, что для всех исследуемых составов наблюдается увеличение показателя шероховатости поверхности покрытий с уменьшением условной динамической вязкости (поверхность подложки зашпаклевана). Так, шероховатость поверхности покрытия на основе краски ПФ-115 составляет 1,14мкм при динамической вязкости краски 0,001.103 Пас, а при динамической вязкости 0,00026. 103Пас – 1,58 мкм.
Для каждого вида красочного состава существует оптимальное значение краевого угла смачивания, обеспечивающего его растекание с формированием покрытия с минимальным значением шероховатости поверхности. Так, оптимальное значение краевого угла смачивания для красочного состава МА-15 составляет 62,5о, для вододисперсионной краски -74,8о.
В соответствии с ISO 1302 существуют 12 классов шероховатости поверхности (от N1 до N12). Анализ данных, приведенных в табл.2, свидетельствует, что высокое качество внешнего вида покрытия (класс шероховатости N2) можно получить для пористости П=24% только при применении алкидной краски ПФ-115 с динамической вязкостью
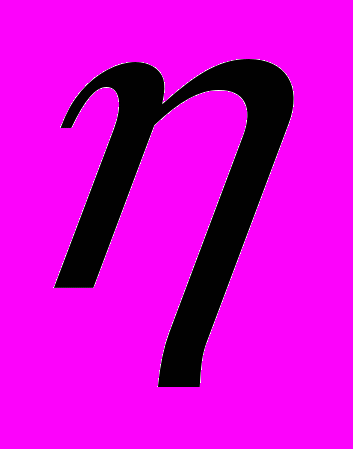
Таблица 2
Качество внешнего вида красочных покрытий в зависимости условной динамической вязкости и пористости подложки
Пористость, (%) | Вид краски | ||||||||
ПФ-115 | МА-15 | ВД | |||||||
Динамическая вязкость, ![]() | Динамическая вязкость, ![]() | Динамическая вязкость, ![]() | |||||||
h1=0,001.103 | h2=0,00065.103 | h3=0,00026.103 | h1=0,0026.103 | h2=0,0026.103 | h3=0,0014.103 | h1=0,0347.103 | h2=0,02317.103 | h3=0,013.103 | |
24 | 0,98(N2) | 2,05(N3) | 2,7(N3) | 3,53(N3) | 4,14(N4) | 4,54(N4) | 2,87(N3) | 3,13(N3) | 3,38(N3) |
28 | 1,7(N2) | 2,26(N3) | 3,0(N3) | 5,61(N4) | 6,5(N4) | 7,56(N4) | 3,1(N3) | 3,37(N3) | 3,55(N3) |
32 | 2,38(N3) | 2,86(N3) | 3,5(N3) | 7,76(N4) | 8,99(N5) | 9,26(N5) | 3,32(N3) | 3,55(N3) | 4,2(N4) |
Примечание. В скобках приведены значения класса шероховатости поверхности)
При проведении экспериментальных исследований применяли метод планирования эксперимента. Получены модели, графическая интерпретация которых представлена на рис.1
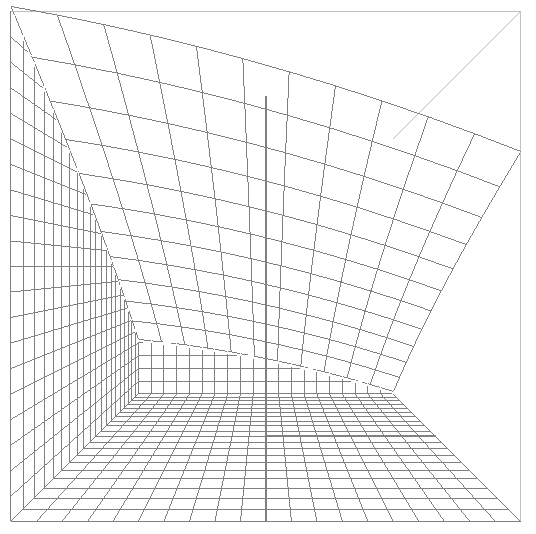
Рис. 1. Модель зависимости качества внешнего вида покрытий от реологических свойств красочного состава и пористости цементной подложки.
Из анализа полученных данных можно сделать выводы, что с целью обеспечения высокого качества внешнего вида защитно-декоративных покрытий необходимо создать банк данных, позволяющих проектировать систему «покрытие-подложка» в зависимости от пористости подложки и реологических свойств красочных составов. Это позволит избежать дополнительных материальных затрат на преждевременный ремонт окрашенной поверхности.
СПИСОК литературЫ
1. В.И. Логанина, Л.П.Орентлихер. Стойкость защитно-декоративных покрытий наружных стен зданий.- М.: Изд-во АСВ, 2001.
Удк 691:53/54
Лопаткин И.Г., аспирант, Яковлев Г.И., д-р техн. наук, профессор,
Плеханова Т.А., канд. техн. наук, доцент
Ижевский государственный технический университет
МАГНЕЗИАЛЬНЫЕ ЗАКЛАДОЧНЫЕ СМЕСИ НА ОСНОВЕ
КАУСТИЧЕСКОГО ДОЛОМИТА
Для приготовления закладочных составов, используемых для заполнения выработанных шахтных пространств, используются в основном смеси, включающие в качестве вяжущего портландцемент [1-3]. Практически отсутствуют данные об использовании магнезиальных вяжущих при приготовлении закладочных составов. Необходимо учитывать меньшие энергозатраты при производстве магнезиальных вяжущих (на 40 % - по сравнению с портландцементом [4]), высокую скорость твердения, высокую прочность, способность хорошо совмещаться с любыми видами заполнителей. В тоже время дефицитность каустического доломита исключает возможность его применения для производства в закладочных составах. Поэтому необходимо использование местных вяжущих для приготовления закладочных смесей на основе вскрышных доломитовых пород.
Для закладки выработанных пространств в горно-металлургической компании «Норильский Никель» были предложены составы, включающие магнезиальное вяжущее, модифированное карфосидеритом и ангидритом. Отсутствие каустического магнезита в Норильске, требует приготовления местного магнезиального вяжущего на основе вскрышных обожженных доломитовых пород. В качестве связующей матрицы использовался состав, включающий молотый ангидрит и каустический доломит, обожженный при температуре 750 ºС. Для структурирования магнезиального вяжущего применялся карфосидерит Fe3(SO4)2(OH)5·H2O в количестве 1 % от общей массы, в качестве поверхностно-активной добавки, способствующей равномерному распределению карфосидерита в объеме матрицы и, одновременно, для повышения пластичности смеси, применялся суперпластификатор С-3 в количестве 0,3 % от массы связующей матрицы. В качестве заполнителя использовался гранулированный отвальный шлака Надеждинского металлургического завода (НЗ). Затворитель – бишофит плотностью 1.16 г/мл.
Для приготовления магнезиального вяжущего применялся доломит Каларгонского месторождения [5], который подвергался предварительному дроблению до фракции 10 мм с последующим обжигом в интервале температур 650 – 850 ºС для достижения оптимальных физико-технических свойств. После обжига доломит измельчался в лабораторной дисковой мельнице.
Испытания образцов затвердевшего доломитового вяжущего на сжатие и изгиб проводились в возрасте 3 суток. Результаты испытаний приведены на рис. 1.
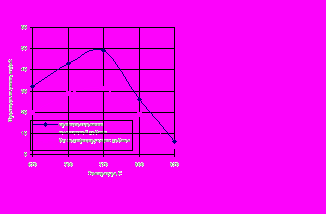
Рис. 1. Влияние температуры обжига доломита на прочность при сжатии затвердевшего доломитового вяжущего в возрасте 3 суток
Для выяснения природы изменения свойств доломитового вяжущего и для обоснования оптимального режима обжига доломита использовался метод рентгенофазового анализа обожженного доломита. С этой целью рентгеновские спектры доломита после обжига в лабораторной печи при температурах 650, 700, 750 и 850 оС анализировались по наличию в них вновь образовавшихся минералов.
Рентгеновский спектр исходного доломита (рис. 2) до обжига показал наличие в нем доломита CaCO3·MgCO3 (da = 2,88; 2,19; 2,02; 1,79 Å), кальцита CaCO3 (da = 3,03; 2,27; 2,11; 1,91; 1,87 Å) и ангидрита CaSO4 (da = 3,49; 2,85; 2,48 Å). При обжиге доломита при температуре 650 оС на спектре отмечается наличие отражений с da = 2,11 и 1,49 Å, соответствующих оксиду магния MgO, при этом снижается интенсивность отражений, соответствующих доломиту.
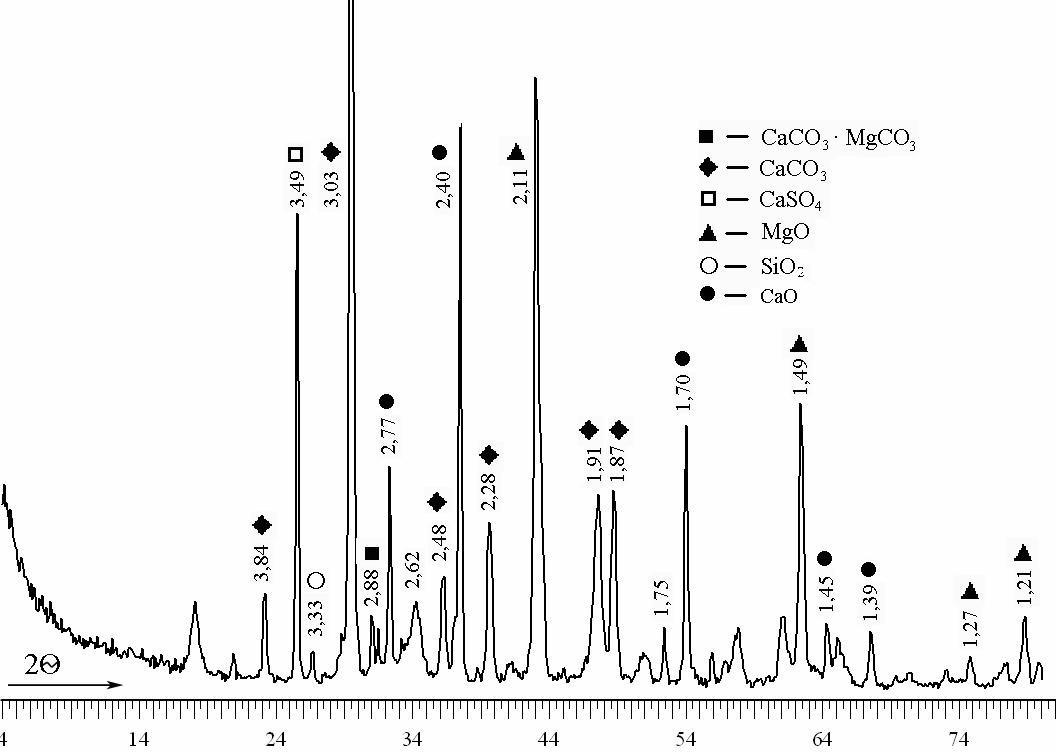
Рис. 2. Рентгенограмма необожженного доломита
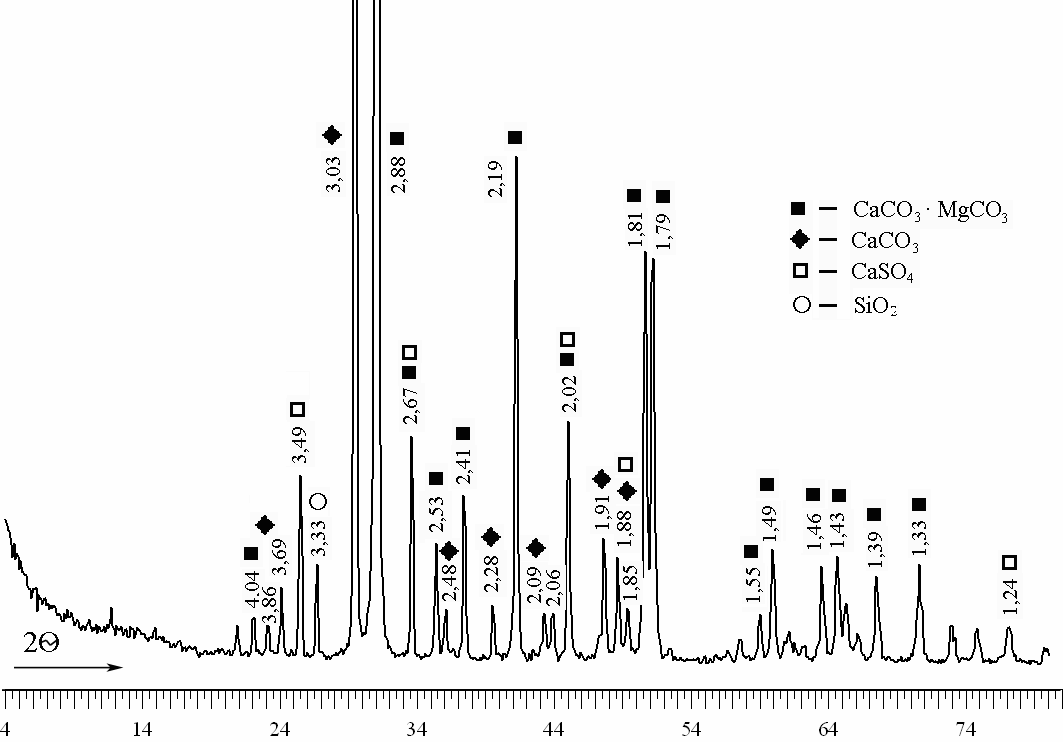
Рис. 3. Рентгенограмма доломитовой породы обожженной при температуре 750 ºС
При температуре 700 оС интенсивность линий, соответствующих оксиду магния MgO увеличивается, появляются отражения с da = 2,41 и 1,70 Å, которые говорят об образовании оксида кальция CaO. При достижении температуры 750 оС увеличивается интенсивность линий, соответствующих оксиду кальция, в тоже время интенсивность линий, соответствующих оксиду магния, повышается незначительно. Вследствие термической диссоциации снижаются до уровня фона отражения, соответствующие доломиту и снижается интенсивность отражений, соответствующих карбонату кальция CaCO3 и CaSO4. Таким образом, оптимальная температура обжига доломита при получении каустического доломита находится в интервале 750 оС.
На графике интенсивности основных характеристических линий минералов в обжигаемом доломите в интервале температур 650 - 850 оС отражена кинетика изменения содержания оксида магния в процессе обжига (рис. 4)
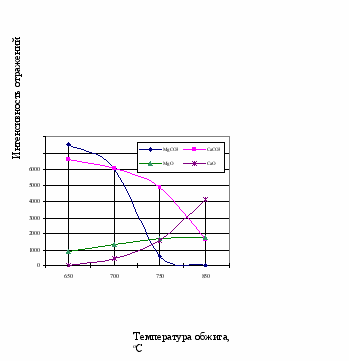
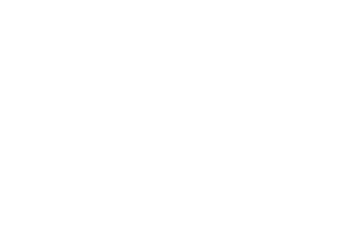
Рис. 4. Кинетика изменения содержания оксидов магния и кальция при обжиге доломита
Для установления содержания оксида магния в обожженном доломите был проведен количественный анализ рентгеновских спектров при температурах обжига 650, 700 и 750 оС. Полученные результаты приведены в табл. 1.
Таблица 1.
Результаты количественного анализа рентгеновских спектров обожженного доломита
№ /п | Фаза | Весовая доля фаз при температуре обжига доломита, % | ||
650 °С | 700 °С | 750 °С | ||
1 | MgO | 27,8 | 41,0 | 60,8 |
2 | CaO | - | 1,8 | 7,8 |
3 | CaSO4 | 1,0 | 3,4 | 3,1 |
4 | CaCO3 | 27,7 | 28,5 | 25,8 |
5 | CaCO3·MgCO3 | 43,5 | 25,2 | 2,5 |
Как видно из табл. 1, в интервале температур 750 оС происходит максимальная диссоциация доломита с образованием оксида магния.
Исследования составов магнезиальной закладочной смеси модифицированной комплексной добавкой показали значительные изменения микроструктуры (рис. 5).
При введении ангидрита и карфосидерита структура закладочной смеси приобретает более плотную структуру за счет уплотнения аморфных новообразований продуктами гидратации ангидрита, состоящих из пластинчатых кристаллов двуводного гипса (рис. 5а). Улучшается сцепление частиц металлургического шлака с магнезиальным вяжущим на границе раздела фаз (рис. 5б).
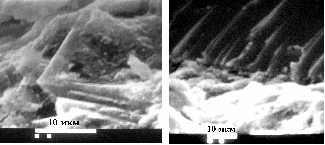
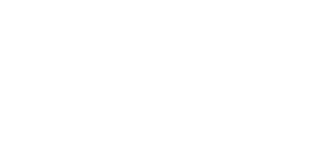
а) б)
Рис. 5. Микроструктура магнезиальной закладочной смеси: (а) – уплотнение магнезиального вяжущего продуктами гидратации ангидрита (пластинки двуводного гипса), (б) - граничный слой между вяжущим и наполнителем при добавлении ангидрита и карфосидерит
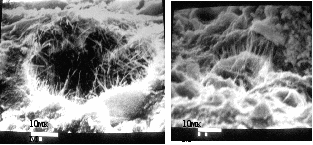
а) б)
Рис. 6. Микроструктура магнезиальной закладочной смеси модифицированной ангидритом и карфосидеритом: (а) – зарастание пор в вяжущей матрице в процессе твердения, (б) – зарастание межфазного слоя кристаллическими новообразованиями
Отмечено дополнительное уплотнение структуры за счет зарастания пор (рис. 6а) и межфазных слоев кристаллическими новообразованиями, что способствует повышению физико-механических характеристик (рис. 6б). Происходит «самозалечивание» дефектов структуры, что позволяет обеспечивать стабильные во времени физико-механические свойства закладочной смеси.
Разработанный состав имеет удовлетворительную кинетику твердения закладочной смеси. Подвижность свежеприготовленной смеси соответствует расплыву на приборе Суттарда равному 22 см, что гарантирует возможность транспортировки смесей по подземным трубопроводам и укладку в выработанные про-
странства. Состав [6] проходит лабораторно-производственныt испытания и будет использован в ЗФ ОАО ГМК «Норильский Никель» в качестве альтернативного варианта закладочным смесям на основе портландцемента.
СПИСОК литературЫ
1. Фрейдин А. М., Шалауров В. А., Анушенков А. Н. Особенности технологии приготовления твердеющей закладки из промышленных отходов // Материалы X Международной конференции по механике горных пород. — М., 1993.
2. Талгатбеков А.Т., Кожбанов К.Х. Применение отходов производства для приготовления закладочной смеси / «Горный журнал Казахстана» № 1, 2005 г.
3. Tagnit-Hamou A., Saric-Coric M., Patrice Rivard P. Internal deterioration of concrete by the oxidation of pyrrhotitic aggregates // Cement and Concrete Research, 35 (2005). – Р. 99–107.
4. Шелихов Н.С., Рахимов Р.З. Доломитовый цемент // Вторые Академические чтения РААСН. Современные проблемы строительного материаловедения. Часть 3. - Казань: Казанская государственная архитектурно-строительная академия, 1996. – с. 41–43.
5. Плеханова Т.А .Магнезиальные композиционные материалы, модифицированные сульфатными добавками. Автореферат диссертации на соискание ученой степени кандидата технических наук. – Казань, 2005. – 22 с.
6. Плеханова Т.А. Бесцементная композиция для закладки выработанных пространств на основе техногенных материалов // Химическая физика и мезоскопия. - 2005, № 1. - C. 104-112.
УДК 666.70
Лохова Н.А. канд. техн. наук, доцент, Вихрева Н.Е. аспирант, Нехода Д.В, Бородин Э.Г. магистранты
Братский государственный университет
ОЦЕНКА НЕКОТОРЫХ ЭКСПЛУАТАЦИОННЫХ СВОЙСТВ ЗОЛОКЕРАМИКИ НА ОСНОВЕ ВЫСОКОКАЛЬЦИЕВОЙ ЗОЛЫ
В БрГУ установлена возможность изготовления лицевых изделий на основе высококальциевой золы от сжигания бурых углей Ирша-Бородинского месторождения.
Для устранения негативного воздействия избыточных оксидов Са и Mg использовано корректирование составов добавками микрокремнезема [Патент РФ №2086517] и интенсификатора спекания (отработанная угольная футеровка электролизеров).
Введение ПАВ (моющее средство «Тайга») обеспечивает более плотную упаковку частиц в сырце.
Целью данной работы является оценка ряда эксплутационных свойств золокерамики на основе высококальциевой золы.
Результаты радиологического исследования и санитарно-химической оценки золокерамики, осуществленных Центром Госсанэпиднадзора г.Братска, приведены в табл. 1 и 2.
Таблица 1.
Радиологические исследования:
№ | Наименование показателя, ед. измерения | Результат измерений (А) | НД на методы исследований |
1. | Активность 226 RA, Бк/кг | 48,08 +- 6,30 | Методика измерения активности радионуклидов в счетных образцах на сцинтилляционном гамма спектрометре с использованием программного обеспечения "Прогресс" утверж. нач. ЦМИИ ГНМЦ ВНИИ ФТРИ о от 07.05.96. |
2. | Активность 40 К, Бк/кг | 77,67 +-33, 19 | |
3. | Активность 232 ТН, Бк/кг | 27,82 +- 5,40 |
Установлено, что эффективная активность ЕРН золокерамики составляет 91 ± 10 Бк/кг. Эффективная активность ЕРН для 1 класса строительных материалов – до 370 Бк/кг.
Таким образом, предлагаемый материал относится к первому классу строительных материалов в соответствии с критериями для принятия решения об использовании строительных материалов (Приложение А, ГОСТ 30108-94).
Таблица 2.
Санитарно - химические показатели
Наименование показателей | Значение по СанПиН 4630-88 | Фактическое значение | НТД на методы исследований |
Концентрация свинца, мг/л | 0,03 | 0,012 | ИСО 8288 |
Концентрация цинка, мг/л | 1,0 | 0,011 | ИСО 8288 |
Концентрация меди, мг/л | 1,0 | 0,05 | ИСО 8288 |
Концентрация кадмия, мг/л | 0,001 | 0,0006 | ИСО 8288 |
Концентрация никеля, мг/л | 0,1 | 0,006 | ИСО 8288 |
Концентрация фтора, мг/л | 1,5 | 0,25 | ГОСТ 43 86-89 |
Концентрация хрома, мг/л | 0,05 | Н/о | ИСО 9174-90Е |
Оценка возможности миграции токсичных элементов в модельной среде (дистиллированная вода) свидетельствует о соответствии золокерамики нормативным показателям.
Оценка стойкости материала в агрессивных средах осуществлена на образцах полусухого прессования (масса 40(60)г, удельное давление прессования 20 МПа, температура обжига 9500С).
Для сравнительного анализа дополнительно испытана партия керамических образцов из закарбонизованного суглинка Анзебинского месторождения.
Физико-механические характеристики представлены в табл. 3.
Таблица 3.
Физико-механические свойства
Состав шихты, мас.% | Средняя плотность, г/см3 | Прочность при сжатии, МПа | Огневая усадка, % | Морозостойкость, циклы |
1. Анзебинский суглинок | 1,896 | 53,2 | 0,95 | 15-25 (по данным Братского керамического завода) |
2. Зола-унос(65%), микрокремнезем (35%), отработанная угольная футеровка электролизеров (15% сверх 100% основной шихты), ПАВ (3% сверх 100% основной шихты) | 1,311 | 16,2 | 0,29 | Более 200 |