Десятые академические чтения раасн, 2006 г
Вид материала | Документы |
- Десятые академические чтения раасн, 2006, 1266.3kb.
- Десятые академические чтения раасн, 2006, 1519.63kb.
- Концепция устойчивого развития в стратегии градостроительства франции 05. 23. 22 Градостроительство,, 332.07kb.
- Резолюция районной детской экологической конференции Десятые Басарукинские чтения, 39.32kb.
- План организационно-педагогической деятельности с детьми, имеющими ярко-выраженные, 77.33kb.
- Новосибирский государственный педагогический университет, 43.06kb.
- Академические программы и экзаменационные курсы в австралии международные центры Embassy, 146.35kb.
- Экология человек общество, 371.15kb.
- Министерство образования и науки российской федерации московский государственный областной, 2810.15kb.
- Рассказывайте детям о ценности чтения. Показывайте связь чтения с их успехами в учебе, 97.26kb.

ДЕСЯТЫЕ АКАДЕМИЧЕСКИЕ ЧТЕНИЯ РААСН, 2006 г.
УДК 666.97.035.5
Синельников Д.С., аспирант, Губарев В.Я., канд. техн. наук, доцент, Соловьев В.Г., аспирант
Липецкий государственный технический университет
О ЦЕНКА ЭФФЕКТИВНОСТИ ЭНЕРГОИСПОЛЬЗОВАНИЯ
ПРИ ТЕПЛОВЛАЖНОСТНОЙ ОБРАБОТКЕ БЕТОНА
Энергетическая эффективность работы пропарочных камер зависит от многих внешних и внутренних факторов. Тепловую эффективность производства сборного бетона можно существенно повысить, снизив тепловые потери, связанные с неудовлетворительным состоянием пропарочных камер, тепловых сетей, запорной арматуры и средств контроля расхода пара, а также применяя беспаровые способы тепловой обработки.
В данной статье рассмотрим основные энергозатраты при тепловлажностной обработке бетона в традиционной пропарочной камере и камере тепловой обработки продуктами сгорания природного газа.
Оценка энергетической эффективности может быть найдена при сравнении тепловых балансов вышеназванных тепловых камер.
Для расчета тепловых балансов традиционной пропарочной камеры и камеры тепловой обработки бетона продуктами сгорания природного газа принимаются одинаковые значения размеров камеры, теплоты, идущей на нагрев бетона, форм, ограждений и арматуры, потери тепла в окружающую среду через стенки камеры, неплотности, режима тепловлажностной обработки бетона и т.д.
Основная энергетическая схема технологического процесса тепловлажностной обработки бетона в традиционных пропарочных камерах состоит из:
водоподготовки;
производства пара в паровых котлах;
- транспортировки пара;
- пропаривания бетона в камерах тепловлажностной обработки.
Подготовка воды для получения пара в паровых котлах является весьма ответственной задачей, так как от качества ее в большей степени зависит надежность и экономичность эксплуатации оборудования. Одним из основных факторов, способствующих повышению эффективности процессов очистки, является подогрев воды до 40ºС.
Основным оборудованием, вырабатывающим тепловую энергию являются паровые и водогрейные котлы со своими стандартными потерями и коэффициентами полезного действия.
После выработки пара в котле, его транспортируют по паропроводу к пропарочным камерам. Основным показателем потерь тепла при транспортировке пара является расстояние от места выработки до камеры тепловлажностной обработки бетона при условии надлежащей изоляции и способа прокладки трубопровода.
Тепловая обработка бетонных изделий в пропарочных камерах производится до достижения ими требуемой отпускной прочности, т.е. заданной проектной марки бетона.
Из теплового баланса технологического процесса тепловлажностной обработки бетона в традиционной пропарочной камере следует, что только четверть всех статей расхода при технологическом процессе тепловлажностной обработки бетона паром идет на пропаривание (25,9%). Основной статьей расхода является нагрев сырой воды до 40˚С при водоподготовке (31,3%), а также потери в котле при производстве пара (5,8%) и транспортировка теплоносителя от котельной до пропарочной камеры (0,9%). В сумме эти три статьи расхода составят 38,0%, что является большей частью расхода от всего технологического процесса тепловлажностной обработки бетона. Остальные статьи расхода происходят непосредственно в пропарочной камере за счет потерь в окружающую среду, сброса грязного конденсата и расхода тепла на нагрев технических частей. В сумме эти статьи расхода составят 36,1%.
Суммарные статьи расхода при тепловлажностной обработке бетона представлены на рисунке 1.
Для беспарового способа обработки бетона продуктами сгорания природного газа рассмотрим тепловую камеру. Для поддержания необходимого влажностного режима используется «водяная ванна», обогреваемая снизу продуктами сгорания природного газа. Все технологические процессы тепловлажностной обработки бетона происходят в одной камере.
Из данных теплового баланса камеры тепловой обработки продуктами сгорания природного газа следует, что основная статья полезного расхода тепловой энергии, как и следовало бы ожидать, идет на тепловую обработку бетона (45,5 %). Однако большая часть статей расхода связана в первую очередь с потерями тепла через ограждающие поверхности камеры тепловой обработки (15,0%), и с уходящими газами с температурой продуктов сгорания 85˚С (2,4 %). Для поддержания высокой влажности в тепловой камере (90…100% во время изотермического прогрева) тепловая энергия расходуется на нагрев воды до 85˚С в «водяной ванне» (1,9%) и ее испарения (16,2%). Остальные статьи расхода тепловой энергии остаются постоянными и связаны с особенностями тепловой камеры – идут на нагрев ограждающих конструкций (7,7%), арматуры, закладных частей (2,6%) и форм (8,7%).
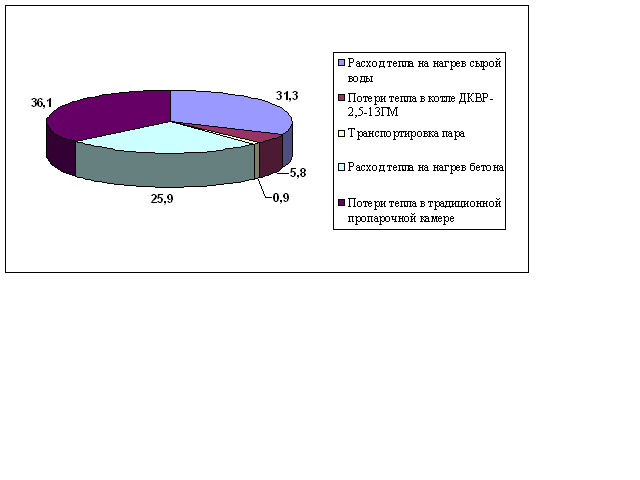
Рис.1. Суммарные статьи расхода каждой из технологических установок при тепловлажностной обработке бетона.
Статьи расхода в камере тепловой обработки бетона продуктами сгорания природного газа представлены на рисунке 2.
Согласно расчету теплового баланса технологического процесса тепловлажностной обработки бетона в традиционной пропарочной камере получили, что на 1 м3 бетона расходуется 0,55*106 кДж тепловой энергии, а в камере тепловой обработки бетона продуктами сгорания природного газа – 0,31*106 кДж тепловой энергии.
В результате сравнения двух тепловых балансов тепловлажностной обработки бетона получаем, что в камере тепловой обработки бетона продуктами сгорания природного газа экономия составляет 0,24*106 кДж с каждого кубического метра бетона, что представляет собой 44% от общего технологического процесса обработки бетона в традиционных пропарочных камерах.
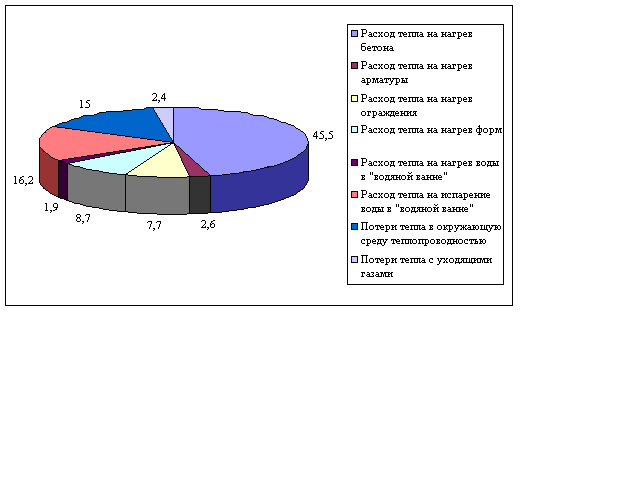
Рис.2. Статьи расхода технологического процесса в камере тепловой обработки бетона продуктами сгорания природного газа.
Для сравнения прочностных характеристик бетона, полученных в экспериментальной камере, проводились серии экспериментов. В результате проведения опытов по производству бетона в экспериментальной камере тепловой обработки продуктами сгорания природного газа при 5-часовом цикле тепловлажностной обработки бетона получили, что прочностные свойства бетона улучшились на 10%, по сравнению с традиционной пропарочной камерой.
На основании вышеизложенного следует, что переход на беспаровые способы тепловой обработки бетона экономически выгоден и энергетически эффективен.
СПИСОК литературЫ
- Баженов Ю.М., Комар А.Г. Технология бетонных и железобетонных изделий: Учебник для вузов. – М.: Стройиздат, 1984. – 672 с., ил.
- Румянцев Б.М., Журба В.П. Тепловые установки в производстве строительных материалов и изделий: Учебное пособие для строительных вузов по спец. «Производство строительных изделий и конструкций». – М.: Высш. шк., 1991. – 160 с., ил.
- Пособие по тепловой обработке железобетонных изделий продуктами сгорания природного газа (к СНиП 3.09.01-85) / НИИЖБ Госстроя СССР. – М.: Прейскурантиздат, 1988. – 32 с.
- Шмитько Е.И., Черкасов С.В. Особенности твердения бетона в газовой среде с пониженной и низкой влажностью // Вопросы эффективности производства сборного железобетона: Сб. докл. обл. конф. по бетону и железобетону. – Воронеж. – 1988. – с.35-40.
УДК 691.3
Смоликов А. А. канд. техн. наук, с. н. с.
Белгородский государственный технологический университет им. В. Г. Шухова
НОВЫЙ КОМПОЗИЦИОННЫЙ МАТЕРИАЛ ДЛЯ БИОЛОГИЧЕСКОЙ ЗАЩИТЫ
В ЯДЕРНО-ЭНЕРГЕТИЧЕСКОМ КОМПЛЕКСЕ
Составной частью любой ядерной установки является биологическая защита [1]. Основное назначение биологической защиты реактора – замедление быстрых нейтронов и поглощение всех видов ионизирующего излучения как реактора, его технологическом оборудовании, так и в самой защите для обеспечения безопасных условий работы обслуживающего персонала. Сверхтяжёлый радиационнозащитный бетон используют как в монолитных, так и сборных элементах [2].
Ослабление потоков γ-квантов и нейтронов происходит в результате взаимодействий с электронами атомов или ядрами материала защиты. Поглощающая способность излучений различного вида и энергий у различных материалов различна, следовательно, создание высокоэффективной биологической защиты возможно только при комплексном применении соответствующих высокоэффективных поглотителей ионизирующих излучений.
Ослабление потоков нейтронов происходит в результате замедления быстрых нейтронов и поглощения замедлившихся и медленных нейтронов.
Для увеличения вероятности захвата тепловых нейтронов без выхода жёсткого γ-излучения желательно в бетон ввести бор или литий. Однако большинство доступных соединений бора растворимы в воде, и введение их в бетон вызывает отрицательные эффекты: замедляется твердение, снижается прочность.
Введение в состав бетонов карбида бора в количестве 1...5 масс. % не вызывает нежелательных последствий. Однако карбид бора, как и литий, – дорогостоящие материалы, поэтому использование их в бетоне ограничено. При монтаже толстых монолитных защит необязательно вводить бор в бетон.
Наиболее эффективным замедлителем тепловых нейтронов является водород, так как уменьшение энергии нейтронов в результате одного столкновения обратно пропорционально массе сталкивающихся частиц. Вследствие равенства масс нейтрона и ядра водорода (протона) в одном акте рассеяния энергии нейтрона на водороде в среднем теряется половина энергии нейтрона.
Процесс захвата тепловых и надтепловых нейтронов ядрами практически всех элементов сопровождается γ-излучением. Желательно не применять в защите элементов, испускающих γ-кванты высоких энергий и в большом количестве на один захват. Захватившее нейтрон ядро становится радиоактивным, поэтому желательно не применять элементы, образующие при захвате нейтронов долгоживущие изотопы, что сильно затрудняет ремонтные работы, связанные с демонтажом защиты. Все эти требования трудно реализуемы, поэтому целесообразно вводить в защиту элементы с высоким сечением захвата тепловых и надтепловых нейтронов, захват нейтронов которыми не сопровождается испусканием γ-излучения.
В качестве дешёвого тяжёлого элемента в защите обычно применяют железо, которое обладает высокими защитными свойствами по отношению и к γ-излу-чению, и к быстрым нейтронам, потому что имеет большое сечение неупругого рассеяния быстрых нейтронов. Но захват железом тепловых или надтепловых нейтронов сопровождается вторичным жёстким γ-излучением. Присутствие бора в защите в значительной степени снижает выход этого захватного γ-излучения.
γ-Излучение обычно чаще, чем нейтроны, определяет необходимую толщину бетонной защиты реактора. Задача проектировщиков состоит в правильном выборе толщины и состава бетонной защиты, которая могла бы обеспечить ослабление потоков ионизирующих излучений до безопасного уровня при минимальных затратах на сооружение реакторной установки.
Многие из требований к материалу биологической защиты для обеспечения им высоких защитных свойств противоречивы. В природе нет материалов, удовлетворяющих сразу всем требованиям. Так, при применении в защите материала с высокой плотностью трудно обеспечить высокое содержание в защите лёгких элементов, особенно водорода. Применение водородсодержащих материалов не обеспечивает эффективного ослабления потоков γ-квантов и быстрых нейтронов.
Итак, высокоэффективный материал защиты реактора должен иметь в своём составе тяжёлые элементы, водородсодержащие вещества, и, желательно, бор для уменьшения выхода захватного γ-излучения. Все эти вещества могут быть применены в защите в виде чередующихся слоёв, но лучше в виде равномерной смеси. Радиационнозащитный бетон представляет собой именно такую равномерную смесь из элементов с различными массовыми числами: тяжёлые материалы вводятся в бетон или в виде тяжёлого (баритового) цемента, в виде руд, или в виде металлических заполнителей. Водородсодержащим компонентом в бетоне является вода, химически связанная затвердевшим цементом или входящая в состав заполнителей бетона. Серьезной трудностью эксплуатации бетонной защиты является обеспечение в её составе необходимой концентрации воды, поэтому этот вопрос заслуживает специального обсуждения.
Вопрос о необходимом количестве воды в бетоне рассматривался во многих работах. Введение в состав бетона большого количества воды не вызывает больших трудностей, однако сохранение её в процессе эксплуатации бетонной защиты представляет сложную задачу, так как бетон в биологической защите реактора работает при высоких температурах и постепенно теряет содержащуюся в нём воду, что приводит к ухудшению его защитных свойств. Потеря воды при эксплуатации особенно опасна для тяжёлых бетонов с железосодержащим заполнителем, так как это может привести к очень большому накоплению промежуточных нейтронов в толстой бетонной защите и защита сама станет источником ионизирующих излучений [3].
Рабочая температура защиты ядерных энергетических установок с водо – водяными реакторами 300 °С. Гидросиликаты цементного камня при этой температуре дегидратируются на 85±3 %, следовательно, с целью сохранения бетоном защитных свойств по отношению к тепловым нейтронам наполнители бетонов такой защиты должны при указанной температуре дегидратироваться в течение всего периода эксплуатации незначительно. При определении пригодности того или иного природного материала для применения в защите, кроме требования содержать определённое количество связанной воды, важна и доступность материала. Многие породы и минералы по своему химическому составу, интересные с точки зрения использования их в защите, были отклонены именно по причине малой распространённости. Среди широкодоступных природных минералов, содержащих более 10 % структурной воды, следует отметить гидробораты, каолинит, серпентин и брусит. Из этих минералов наиболее доступны каолинит и серпентин. Каолинит – высокодисперсный набухающий глинистый минерал. В количестве более 3 % заметно снижает прочность бетонов, в связи с чем, в соответствии с требованиями ГОСТа, его введение в бетон в больших количествах недопустимо. Серпентин, как и каолинит, – слоистый гидросиликат, но ненабухающий, благодаря чему он нашёл широкое применение в бетонах биологической защиты. С точки зрения использования в защите серпентин интересен тем, что он содержит 12-14 масс. % структурной воды и пригоден как высокотемпературный заполнитель бетона. Бетон на серпентинитовом заполнителе сохраняет свои защитные свойства в условиях длительной эксплуатации при температурах до 480 °С. Благодаря этому серпентинитовый бетон можно использовать в качестве эффективного материала в конструкциях биологической защиты ядерных энергетических установок без специального охлаждения.
Защитные свойства серпентинового бетона при нормальных температурных условиях не сильно отличаются от свойств обычного бетона, его преимущества выявляются при высоких температурах. Для повышения защитных качеств этого бетона в его состав вводят железо. У железосерпентинового бетона больше объёмная масса, он обладает повышенными защитными свойствами и сохраняет работоспособность при высоких температурах [4 и др.]. В блоках радиационной защиты сб. 11 реакторов РБМК применяется железобарийсерпентинитовый бетон плотностью 3700±100 кг/м3, марки 200, который приготовлялся из смеси барийсерпентинитового цемента с чугунным порошком путём затворения её с водой согласно инструкции НИКИЭТ И.325-74. В настоящее время этот материал не производится и возобновить его производство невозможно. Предстояло разработать ему замену. Выполненный обширный комплекс НИР по изучению различного вида железорудного сырья КМА при изготовлении материалов биологической защиты, позволил разработать способ и технологию производства композиционных радиационно-защитных бетонов для изготовления различных изделий для АЭС. Бетонные блоки различных размеров и формы можно изготавливать на типовых заводах железобетонных изделий, используя высокоалитовый портландцемент, магнетитовый железорудный концентрат и, ранее не применявшийся в бетонах биологической защиты реакторов, хризотил – волокнистую разновидность серпентина.
Основные физико-механические и защитные свойства товарного железо-магнетито-серпентинитового цементного бетона приведены в таблице:
Таблица
Наименование показателя | Размерность | Значение (средние в серии) |
1. Температура длительной эксплуатации, | °С | До 300 |
2. Объёмная масса высушенного при 110 °С бетона, | кг/м3 | 4000±100 |
3. Предел прочности при изгибе, | МПа | 7,7±0,3 |
4. Прочность при сжатии после 1 сут твердения (1 сутRсж), | МПа | 10±3 |
5. Прочность при сжатии после 3 сут твердения (3 сутRсж), | МПа | 25±4 |
6. Прочность при сжатии после 28 сут твердения (28 сутRсж), | МПа | 45±5 |
7. Прочность при сжатии после сушки при 110 °С, | МПа | 47±5 |
8. Прочность при сжатии после сушки при 300 °С, | МПа | 30±4 |
9. Количество воды в бетоне после 28 сут. твердения, | масс. % | 2,5±0,2 |
10. Количество химически связанной воды при 300 °С, | масс. % | 1,00±0,1 |
11. Коэффициент линейного расширения при 300 °С, | м ∙ град–1 | 8 ∙ 10–6 |
12. Коэффициент теплопроводности при 300 °С, | Вт/(м ∙ °К) | 3,85 |
13. Длина релаксации быстрых нейтронов Е > 1 МэВ, | см | 9,6±0,2 |
14. Длина релаксации мощности дозы гамма-излучения для б0Со; 137Cs; спектра нейтронов реактора, | см | 5,7±0,1; 4,4±0,1; 10,9±0,2 |
Технология нового, альтернативного железобарийсерпентиновому бетону, материала из Российского недефицитного сырья, по своим свойствам не уступающего ранее применявшемуся бетону, запатентована и начато его производство.
СПИСОК литературЫ
1. Биологическая защита ядерных реакторов. Справочник. Сокр. пер. с англ. Под ред. Ю. А. Егорова. – М.: Атомиздат, 1965. – 328 с.
2. Прошин А. П., Королёв Е. В., Болтышев С. А. Сверхтяжёлый бетон для защиты от радиации // Строительные материалы, оборудование, технологии 21 века. – 2003. – № 11. – С. 20–21.
3. Бетон в защите ядерных установок. Изд. 2. – М.: Атомиздат, 1973. – 319 с.
4. Радиационная защита на атомных электростанциях. – М.: Атомиздат., 1978. – 253 с.
УДК 666.97
Смоликов А. А. канд. техн. наук, с. н. с.
Белгородский государственный технологический университет им. В. Г. Шухова
К ПРОБЛЕМЕ ТЕХНОЛОГИИ КОМПОЗИЦИОННЫХ
БЕТОНОВ СПЕЦИАЛЬНОГО НАЗНАЧЕНИЯ
Развитие промышленности требует создания новых композиционных строительных материалов с заданным сочетанием свойств и низкой стоимостью [1]. Требуемые сочетания свойств наиболее легко достигаются созданием композиционных бетонов, компоненты которых при совместной работе способны проявлять синергетический эффект, например водорода с тяжёлыми элементами в радиационнозащитных бетонах. В технологии многокомпонентных композиционных бетонов сконцентрированы достижения современного строительного материаловедения [2]. По мере перехода в «век композиционных материалов» всё более настоятельной становится необходимость систематического выявления факторов, определяющих технологические и эксплуатационные свойства, а также потенциальные возможности их регулирования. К сожалению, обсуждение всех вопросов технологии (принципов выбора и сочетания компонентов, перспективах развития и эффективности применения) в объёме одной, даже очень большой статьи, – невозможно. Рассмотрим самые основные. Основу технологии композиционных материалов составляют три элемента – наполнитель, матрица и граница раздела между ними. Для получения материалов с заданными физико-механическими показателями каждый из этих элементов должен обладать оптимальным сочетанием физико-химических свойств, проявляющихся как индивидуально в каждом из них, так и при их, совместной работе. Физико-химическое взаимодействие связующего (матрицы) с наполнителями (химическая связь подробно рассмотрена в специальной литературе и здесь не обсуждается.) позволяет получать гетерофазные композиционные материалы, обладающие совершенно новым сочетанием технологических или эксплуатационных свойств, отличным от свойств исходных компонентов, но сохраняющие их индивидуальность. Компоненты бетонов по химической природе относятся к силикатам сложного состава и строения. Все они являются типичными гетеродесмическими соединениями, в которых реализуются одновременно различные типы химической связи: ионная, ковалентная, ионно-ковалентная, координационная, водородная и др. многоцентровые связи. В силикатах преобладает тот или иной вид связи. Кроме силы химической связи на прочность бетона влияет много других технологических и эксплутационных параметров: размер катионов и анионов, вязкость, хрупкость, пластичность наполнителей и матрицы, вид и количество микро- и макродефектов. Наличие на поверхности наполнителя слабых поверхностных плёнок и загрязнений. Наличие непрочных включений: слюда, глины, органические – полимеры, уголь.
Наполнители играют важную роль в производстве композиционных строительных материалов. Выбор наполнителя определяется в первую очередь доступностью, химическим составом (определяет поверхностные свойства в т. ч. реакционную способность), размерами частиц и их распределением по размерам (полидисперсностью), а также формой частиц и характером их упаковки. Широкое развитие производства новых видов высокопрочного бетона невозможно без применения наполнителей специального назначения. Традиционно особое внимание уделяют влиянию наполнителей на механическую прочность, что привело к распространённому их делению на усиливающие (армирующие) и неусиливающие (“инертные”). Наполнители способны оказывать много других эффектов, обуславливающих высокую эффективность их использования – поглощение ионизирующих излучений, понижение текучести и объёмной усадки, улучшение формуемости и формоустойчивости, теплофизических и других характеристик. Химические превращения в наполнителях при повышенных температурах (декарбонизация, дегидратация) имеют огромное значение при выборе наполнителей. Это, к сожалению, не всегда учитывается при создании композиций для длительной высокотемпературной эксплуатации. Химическая природа наполнителей определяет все процессы, протекающие на их поверхности, и связанные с ними эффекты. Поверхность, как правило, содержит химически активные группы (центры), способные реагировать с активными группами гидросиликатов цемента с образованием химических связей. Необходимо учитывать, что состав и свойства поверхности дисперсного наполнителя далеко не всегда соответствует его составу и свойствам в объёме и наоборот. Из сказанного вытекает настоятельная необходимость широкого и эффективного использования активных армирующих наполнителей, которые позволяют значительно уменьшить количество используемого цемента и улучшить свойства материалов на их основе. Дисперсные наполнители позволяют регулировать физико-химические свойства композиционных бетонов: прочность при растяжении и сжатии (зависят от характера упаковки частиц, их размеров и взаимодействия по границе раздела), удлинение при разрыве, ударную вязкость, реологические свойства и др. Возможность регулирования плотности упаковки частиц наполнителей не нашла ещё широкого промышленного применения.
Прочность композита, как известно, определяется прочностью матрицы (для бетона – цементной) и заполнителя, а также прочностью связи между ними. По данным А. М. Невилля теоретическая прочность цементного камня составляет 10,5 ГПа. Низкая фактическая прочность товарных бетонов обусловлена дефектностью структуры. Доказано, что различные включения в матрице, отличающиеся от неё по податливости (кристаллиты, поры, частицы наполнителя, волокна, царапины и трещины), являются концентраторами напряжений. Прочность поликристаллического материала зависит от силы (типа) химической связи между
агрегатами, слагающими поликристалл, количества этих связей, вида и количества дефектов. В зоне дислокаций обычный кристаллохимический порядок расположения молекул нарушается таким образом, что связи двух соседних молекул становятся ближе. Благодаря этому реакция начинается там, где есть дислокации. Необходимый уровень концентрации дислокаций в структуре можно обеспечить введением примесей, изменением условий кристаллизации, путём пластической деформации или, наоборот, отжигом, облучением, воздействием электрическим или магнитным полем, химической обработкой кристалла. Поверхностные дефекты интенсифицируют гетерогенные реакции, начинающиеся на поверхности твёрдых тел, в том числе хемосорбцию ПАВ. Структура с высокой концентрацией дефектов энергетически более выгодна, чем структура с внутренними порами, межкристаллитными границами и дислокациями. Механохимическое активирование твёрдых тел их измельчением связано в первую очередь с образованием дислокаций (активных центров), концентрация которых возрастает от 106 см–2 до 1012 см–2.
Отмечается [3] общемировая тенденция применения наиболее перспективных на сегодняшний день многокомпонентных бетонов самого разного назначения вместо обычных. В них используются индивидуальные химические модификаторы, изменяющие технологические характеристики бетонных смесей и, способствующие повышению физико-механических свойств бетона; комплексные модификаторы, включающие зачастую до нескольких десятков специальных химических добавок и активные минеральные компоненты различной дисперсности, а также другие индивидуальные вещества. Многокомпонентность бетонной смеси позволяет эффективно управлять структурообразованием на всех этапах технологии и получать бетон с различными требуемыми свойствами. Мелкозернистый бетон на портландцементе с добавлением в смесь 25-30 % микрокремнезёма и 2-3 % суперпластификатора, твердеющий при температуре +90 °С и атмосферном давлении в пропарочной камере, достигает прочности 200 МПа, а тот же бетон, но твердеющий при температуре +90 °С под давлением 50 МПа – прочности 650 МПа. В НИИЖБе получен высокопрочный мелкозернистый бетон с прочностью на сжатие 800 МПа [4].
Обязательный признак современной технологии бетона – управление струкутрообразованием материала на всех этапах производства бетона и конструкций. Увеличение плотности упаковки частиц за счёт уменьшения двойного электрического слоя коллоидной фазы гидратирующегося цемента. Снятие электрических потенциалов, возникающих на границе двух фаз при помоле, обусловливающих флокуллирование частиц (цемента) и образование двойного электрического слоя, который регулируется (сжимается) – солями, суперпластификаторами, электрокаогуляцией для уменьшения В : Т [5]. Для создания оптимальной структуры бетона, предназначенного для разных условий эксплуатации, широко используют специальные добавки-модификаторы структуры и свойств бетона [6]. Из химических добавок наибольшее распространение получили суперпластификаторы. Сравнительно недавно появились особо эффективные гиперпластификаторы, позволяющие снизить В/Т до 0,18-0,20. Эффективно введение 2-3 % суперпластификаторов совместно с комплексными органо-минеральными добавками [7] (струкутрообразующими, микропенообразующими, волокнами, микрокремнезёмом и др.) при помоле цемента. Нормальная густота уменьшается в 1,7-2 раза (например, с 28 % до 14 %), что позволяет использовать в производстве пластичные литые самоуплотняющиеся и нерасслаиваемые бетонные смеси с В/Ц 0,2-0,3 и получать широкую гамму особоплотных высокопрочных композиционных бетонов с требуемыми свойствами. Создание в структуре воздушных сферических микропор увеличивает долговечность бетонов [8].
Применение композиционных вяжущих веществ и комплексов химических и минеральных добавок является отличительной особенностью эффективных композиционных бетонов с заданным сочетанием свойств и хорошими экономическими показателями. На основании углублённого анализа перечисленных выше наиболее важных физико-химических процессов, происходящих при изготовлении компонентов бетона, при формовании, твердении и эксплуатации бетона выявлены основные факторы, определяющие его прочность, создана технология производства высокопрочного бетона на типовом оборудовании марок существенно выше марки применяемого портландцемента. Смеси характеризуются высокой удобоукладываемостью и высокой ранней прочностью, а бетоны – долговечностью.