Десятые академические чтения раасн, 2006 г
Вид материала | Документы |
- Десятые академические чтения раасн, 2006, 1266.3kb.
- Десятые академические чтения раасн, 2006, 1519.63kb.
- Концепция устойчивого развития в стратегии градостроительства франции 05. 23. 22 Градостроительство,, 332.07kb.
- Резолюция районной детской экологической конференции Десятые Басарукинские чтения, 39.32kb.
- План организационно-педагогической деятельности с детьми, имеющими ярко-выраженные, 77.33kb.
- Новосибирский государственный педагогический университет, 43.06kb.
- Академические программы и экзаменационные курсы в австралии международные центры Embassy, 146.35kb.
- Экология человек общество, 371.15kb.
- Министерство образования и науки российской федерации московский государственный областной, 2810.15kb.
- Рассказывайте детям о ценности чтения. Показывайте связь чтения с их успехами в учебе, 97.26kb.
ПЕРСПЕКТИВЫ ИСПОЛЬЗОВАНИЯ ОТРАБОТАННОГО ГЛИНОЗЕМИСТОГО КАТАЛИЗАТОРА В ПРОИЗВОДСТВЕ СУХИХ СТРОИТЕЛЬНЫХ СМЕСЕЙ
В химической промышленности широко распространено применение активного оксида алюминия в качестве эффективного осушителя газов и паров и катализатора многих химических реакций. Особенно в больших объемах используются катализаторы в процессах реформинга, изомеризации и других процессах нефтепереработки. Активный оксид алюминия -Al2O3, имея развитую поверхность и гидрофильность, обладает прекрасными адсорбционными свойствами и используется как эффективный осушитель и поглотитель ряда веществ.
Главным промышленным процессом, катализуемым оксидом алюминия, является процесс Клауса по добыче серы из сероводорода.
Обычно процесс Клауса протекает в две стадии:
1. Термическое окисление одной трети начального количества H2S в высокотемпературной горелке при 1000 °С по реакции:
H2S + 1/2 О2 SО2 + Н2О
2. Каталитическое окисление оставшихся двух третей H2S по реакции Клауса при температуре 250 °С:
2H2S + О2 3/nSn + 2Н2О
В процессе эксплуатации свойства катализатора меняются и они становятся непригодными для каталитических процессов, в конечном итоге образуется значительный объём отработанных катализаторов, не представляющих интереса для химической промышленности.
Отработанные катализаторы отличаются от исходных: по химическому составу - наличием примесей; удельной поверхности - меньшей удельной поверхностью; структуре поверхностного слоя - снижением открытой пористости.
В химическом составе отработанных катализаторов преобладает огнеупорный оксид алюминия разной активности: наименьшей - на поверхности, и почти исходной - в центральной части гранул. Основной процесс, в котором применяется активный оксид алюминия, - это процесс Клауса по добыче серы из сероводорода. После него в отработанном катализаторе присутствует сера в качестве примеси. Таким образом, отработанный катализатор представляет собой (в исходном виде и после низкотемпературной обработки) -Al2O3 -ценное глинозёмсодержащее сырьё, пригодное для использования в сухих строительных смесях стремительно развивающейся отрасли строительных материалов.
Нами были выделено перспективное направление использования отработанных глиноземистых катализаторов (ОГК) в производстве сухих строительных смесей для получения расширяющей добавки к портладцементу. Это позволит получать цементы с компенсированной усадкой, а на их основе производить высококачественные самонивелирующиеся сухие строительные смеси для полов, а также ремонтные смеси.
В настоящее время при производстве сухих смесей специального назначения (расширяющихся композиций) существует недостаток расширяющихся добавок. Объема производимых добавок ИР-1, Цемдекор (Подольский цементный завод) не хватает для удовлетворения потребности рынка сухих смесей.
В процессе твердения цемента обязательно возникают усадочные явления, хотя в первый момент есть небольшое, обычно не фиксируемое расширение. Многие факторы, влияющие на величину усадки и расширения, достаточно хорошо известны. Для устранения усадочных явлений предложены различные расширяющиеся и напрягающие цементы. Эффект расширения в большинстве составов обусловлен образованием в процессе твердения гидросульфоалюмината кальция (ГСАК) - эттрингита. В таких композициях основную роль играет оксид алюминия как необходимый структурный элемент ГСАК.
Установлено, что ОГК в составах добавок к цементам, расширяющихся за счет образования при гидратации эттрингита, выполняет функции глиноземсодержащего компонента.
На основе ОГК разработана добавка, которая в композиции с портландцементным клинкером приводит к компенсированию усадки цементного камня и упрочнению растворов на основе сухих строительных смесей.
Состав расширяющей добавки к портландцементу принят следующий: гипс строительный 5-8% (от массы цемента), известь негашеная молотая – 3…5 %, ОГК – 7…9 %. Полученные результаты после 28 суток твердения позволят отнести испытанный состав к добавкам для получения цементов с компенсированной усадкой.
В настоящий момент происходит апробация изученных составов на промышленном производстве, а также ведутся поиски по оптимизации составов с целью получения цементов с больших эффектом расширения, а также самонапрягающихся цементов.
УДК 691:614.841.332
Суровцев И.С., д-р техн. наук, профессор,
Никулина Т.Д., Перцев В.Т., д-р техн. наук, профессор,
Рудаков О.Б., д-р. хим. наук, профессор
Воронежский государственный архитектурно-строительный университет
ТЕРМОСТОЙКИЕ ПОКРЫТИЯ для металлических
конструкций НА ОСНОВЕ СИЛИКАТОВ ЩЕЛОЧНЫХ МЕТАЛЛОВ
В работе представлены результаты исследования влияния минеральных наполнителей на свойства силикатного связующего с целью получения термостойких защитных покрытий для металлических конструкций, используемых в гражданском и промышленном строительстве, а также в изготовлении строительных, дорожных и технологических машин.
На безопасность эксплуатации металлических конструкций существенное влияние оказывает наличие термостойких покрытий, которые обеспечивают их защиту от действия высоких температур [1].
По механизму действия в высокотемпературных условиях защитные покрытия классифицируются на горючие, трудногорючие, негорючие невспучивающиеся и вспучивающиеся. Наиболее эффективными являются вспучивающиеся покрытия, так как при высокотемпературном воздействии они плавятся и вспучиваются за счет выделения негорючих газов, а образующийся вспененный слой (пенококс) защищает подложку от внешнего теплового потока. Толщина покрытия увеличиваются в 2-200 раз, а теплопередача в сторону металла уменьшается примерно в 100 раз [2]. Толщина, структура и особенности термического поведения образовавшегося пенококса обусловлены составом соотношением основных ингредиентов композиции термостойкого покрытия.
Проблема разработки эффективных вспучивающихся термостойких покрытий (ВТП), оказывающих также антикоррозионное действие, являющихся экологически безопасными, весьма актуальна. Вспучивающиеся термостойкие покрытия являются уникальными покрытиями, защищающими металл не только от высоких температур, но и от воздействия кислорода и агрессивных газов промышленной зоны [3,4]. Необходимо отметить, что в настоящее время ассортимент эффективных ВТП представлен дорогостоящими композициями, в большинстве которых применяются синтетические смолы, разлагающиеся с выделением токсичных продуктов пиролиза. Их получение связано с использованием органических мономеров и растворителей, вредных с экологической точки зрения, что в конечном итоге усложняет технологию их получения.
Для определения возможности использования горных пород и отходов промышленного производства Центрально-Черноземного региона для создания ВТП были проведены теоретические и экспериментальные исследования.
Целью данных исследований явилась разработка оптимальных составов ВТП для конкретных материалов и температурных границ с высокими теплоизолирующими свойствами. В задачи исследований входило изучение влияние минеральных наполнителей разных генетических классов на свойства силикатов щелочных металлов. В изучаемых композициях исходным связующим явился калиево-натриевый силикат (жидкое стекло), которое при температурном воздействии разлагается с выделением воды и относится к классу экологически безопасных самовспучивающихся связующих.
Минеральные наполнители вводились в состав силикатного связующего, смесь тщательно перетиралась и наносилась на исследуемые металлические пластинки размером 10х10х0,1 см для определения прочности, адгезии. Коэффициент вспучивания и плотность определялись на образцах, получаемых в специальной форме 2х2х2 см. Исследовалось влияние минеральных наполнителей на свойства силикатного связующего в диапазоне температур от 20 до 1000С. Для проведения экспресс-метода оценки термозащитных вспучивающихся свойств композиций была собрана специальная установка, которая состояла из электрической печи, хромель-алюмелевой термопары и электронного потенциометра.
Экспериментальные исследования показали, что плотность жидкого стекла существенно влияет на его коэффициент вспучивания. Жидкое стекло с плотностью 1,64 г/см3 имеет коэффициент вспучивания 60, с плотностью 1,3 г/см3 – 20, с плотностью 1,1 г/см3 – 4 [5]. Для получения термостойких покрытий малярной консистенции использовалось жидкое стекло с плотностью 1,3 г/см3. С целью улучшения физико-механических, специальных свойств силикатного связующего в его состав вводили тонкодисперсные и волокнистые минеральные наполнители (см. рис. 1, рис. 2, рис. 3). Установлено, что введение тонкодисперсных минеральных наполнителей увеличивает среднюю плотность силикатного связующего на 20-30 %, а волокнистого наполнителя на 2,0-15,0 % (рис.1).
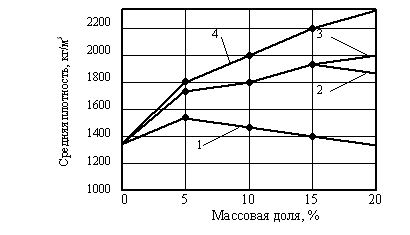
Рис. 1. Влияние процентного содержания минеральных наполнителей на среднюю плотность силикатного связующего в естественных условиях.
1 – минеральная вата; 2 – мел; 3 – трепел; 4 – зола
Введение минеральных тонкодисперсных и волокнистых наполнителей в количестве от 10 до 20 % приводило к увеличению прочности (рис. 2). Трепел, зола, мел увеличивают предел прочности силикатного связующего в 24,5 раза. Максимальная величина прочности получена при введении 20 % трепела. Введение волокнистого наполнителя в количестве 10-20 % увеличивает прочность композиции в 2 раза.
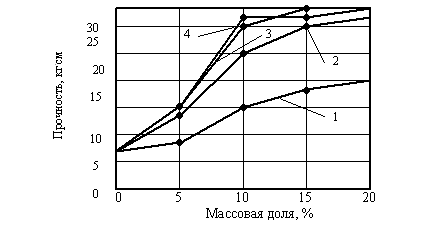
Рис. 2. Влияние минеральных наполнителей на прочность силикатного связующего.
1 – минеральная вата; 2 – мел; 3 – трепел; 4 – зола.
Анализ полученных зависимостей показывает, что введение золы и мела приводит к уменьшению коэффициента вспучивания, а введение трепела и волокнистого наполнителя увеличивает коэффициент вспучивания на 20-25 % (рис. 3). Дальнейшее увеличение количества вводимого трепела и волокнистого наполнителя в состав силикатного связующего приводит к снижению коэффициента вспучивания, но его величина даже при 20 % содержания трепела выше коэффициента вспучивания жидкого стекла.
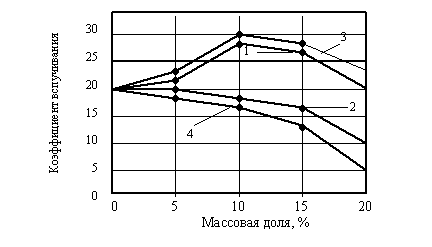
Рис. 3. Влияние минеральных наполнителей на коэффициент вспучивания силикатного связующего
1 – минеральная вата; 2 – мел; 3 – трепел; 4 – зола
Увеличение коэффициента вспучивания при введении трепела связано с тем, что трепел, являясь аморфной формой кремнезема, испаряет свободную и химически связанную воду, способствуя вспучиванию силикатного связующего.
Трепел и минеральная вата увеличивают коэффициент вспучивания силикатного связующего до температуры равной 400С. Образующийся пенококс не уменьшается по объему до температуры 600С, а затем наблюдается его выгорание и разрушение.
С целью стабилизации пенококса в состав данной композиции дополнительно вводили фосфатный антипирен. Данные дифференциально-термического и рентгенофазового анализа показывают, что в диапазоне температур 120600С вспучивание системы идет за счет термических превращений: дегидратации и взаимодействия отдельных компонентов. При температуре 600С начинается образование новой составляющей композиции – альбита. Это приводит к образованию прочного вспененного слоя невыгорающего при температуре 600-1000С.
Результаты проведенных исследований показывают возможность использования местных горных пород в качестве исходного сырья для получения вспучивающихся термостойких покрытий по металлу. Данные исследования являются составной частью научных работ по разработке универсальной рецептуры ВТП для металлических конструкций различного назначения.
СПИСОК литературЫ
1. Брушлинский Н.Н., Соколов С.В. Проблема пожаров в мире в начале ХХI столетия//Пожаровзрывобезопасность. – 2003. - №1. – С. 7-14.
2. Тадасиге К., Хидзе И. Огнестойкие краски. Тосо то торё, 1971, - №201, с. 167-172.
3.Vandersall H.L.//J. Firea Flam 1971. V.2. April, р. 97-100.
4. Романенков И.Г., Левитис Ф.А. Огнезащита строительных конструкций. М.: Стройиздат, 1991, 350 с.
5. Суровцев И.С., Рудаков О.Б., Перцев В.Т., Никулина Т.Д.Термостойкие покрытия на основе силикатов щелочных металлов//Proceedings V Intern. Conf. «Heavy Machinery, HM 2005», Kraljevo, 28 June -3 July 2005, p. III7-III10.
УДК 666.972.54
Сычев А.А., к.т.н., Кузнецов А.Т., к.т.н., Мурашов Д. Ю.
Казанский государственный архитектурно-строительный университет
ПРИМЕНЕНИЕ КОМПЛЕКСНОЙ
СУЛЬФОПОЛИМЕРНОЙ ДОБАВКИ В БЕТОНАХ
Создание новых видов вяжущих веществ, способных заменить традиционные, заставляет вести поиск в отходах промышленного производства.
В качестве модифицирующие добавки цементных композиций нами был применен отход производства тиокола казанского завода синтетического каучука.
Положительные результаты, полученные при использовании отхода в цементных композициях и растворных смесях [1,2], позволило предположить улучшение свойств бетонной смеси и бетона.
Проверка составов на подвижность показала, что образцы, приготовленные с применением добавки до 15-20 % от массы вяжущего, имеют показатель ОК в пределах 11-12 см или П3-П4, то есть, бетонные смеси без добавок с подвижностью 1-4 см перешли в категорию литых смесей, практически не нуждающихся в вибрации. На повышении прочности бетона выше расчетной сказывается эффект пластификации и соответствующее ему снижение В/Ц. Результаты приведены в таблице.1.
Образцы бетона номинального состава с различным содержанием добавки СПД после 28 суточной выдержки в нормальных условиях испытывали на сжатие. Результаты изменения прочности бетона представлены в табл. 1. и на рис. 1.
Таблица 1.
Результаты проверки состава бетонной смеси
№№ | Марка бетона | Состав, кг на 1 м3 | ОК, см | R28, МПа | |||||
Цемент | Песок | Гравий | Вода | СПД | |||||
% | л | ||||||||
1 | 250 | 265 | 551 | 1371 | 175 | - | - | 4,0 | 25,8 |
2 | 250 | 265 | 551 | 1371 | 167 | 3 | 8 | 5,8 | 26,2 |
3 | 250 | 265 | 551 | 1371 | 162 | 5 | 13 | 6,7 | 26,9 |
4 | 250 | 265 | 551 | 1371 | 149 | 10 | 26 | 9,0 | 27,8 |
5 | 250 | 265 | 551 | 1371 | 130 | 15 | 40 | 11,0 | 29,0 |
6 | 250 | 265 | 551 | 1371 | 122 | 20 | 53 | 12,0 | 29,4 |
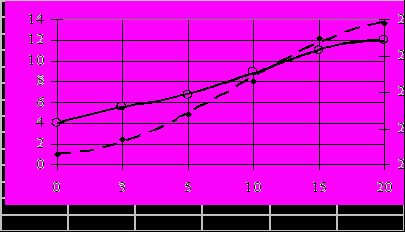
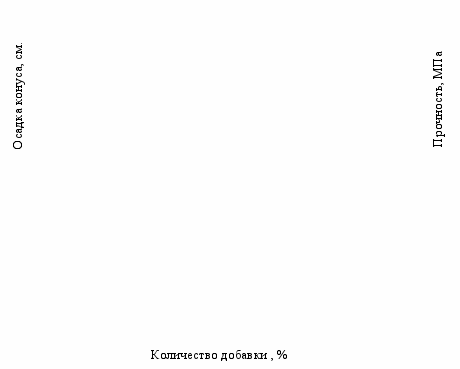
- подвижность, - прочность.
Рис. 1. Изменение подвижности бетонной смеси и прочности бетона на сжатие при введении СПД
Как видно из результатов, СПД является хорошим пластификатором – на участке от 5 до 15 % содержания добавки подвижность увеличивается с 4 до 11 см. При дальнейшем увеличении содержания добавки интенсивность роста пластифицирующего эффекта замедляется. Согласно принятой в России классификации добавок в бетон [34] увеличение подвижности бетонной смеси в присутствии СПД без снижения прочности бетона с П1 до П4 позволяет классифицировать добавку как регулятор реологических свойств пластифицирующего действия 2 группы эффективности.
Из таблицы видно, что с введением СПД до 15 % от массы вяжущего прочность бетона увеличилась на 12 % (с 25,8 до 29,0 МПа) по сравнению с контрольным составом без добавки. Практически те же прочностные показатели имеет бетон, содержащий 20 % СПД. Таким образом, количество добавки следует ограничить 15 % от массы цемента.
Переход к стандартному размеру куба с размером ребра 15 см позволил установить следующие прочностные показатели бетона:
25,8 * 0,95 = 24,5 МПа; 26,2 * 0,95 = 24,9 МПа; 26,9 * 0,95 = 25,6 МПа; 27,8 * 0,95 = 26,1 МПа; 29,0 * 0,95 = 26,8 МПа; 29,4 * 0,95 = 27,9 МПа.
Для оценки кинетики изменения ранней (распалубочной) прочности бетона серию образцов нормального твердения испытывали в возрасте 8, 16 и 24 часов. Результаты испытаний по пределу прочности при сжатии представлены на рис.2.
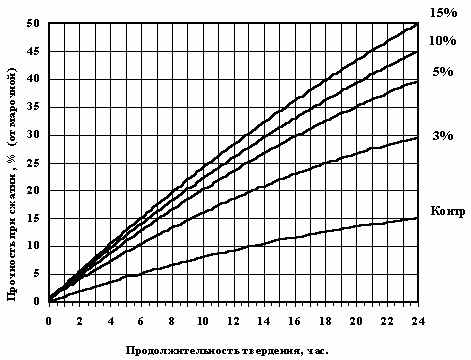
Рис. 2. Нарастание прочности бетона на ПЦ400-Д20 при введении СПД до 15% от массы цемента при нормальном режиме
Анализ результатов исследований показал, что введение СПД способствует интенсификации набора бетоном прочности в раннем возрасте, которая к суткам составляет от 30 до 50 % от проектной в зависимости от количества добавки. Согласно полученным данным СПД можно рассматривать как ускоритель твердения бетона.
Для установления влияния температуры на темпы твердения бетона была изготовлена партия бетонных образцов с добавкой СПД плотностью 1,056 - 40,0 л для 15% 40,0 х 0,007 = 0,28 л.
Также как и предыдущая партия, пропаренные образцы испытывались в возрасте 8, 16 и 24 часов. Результаты представлены на рис. 3.
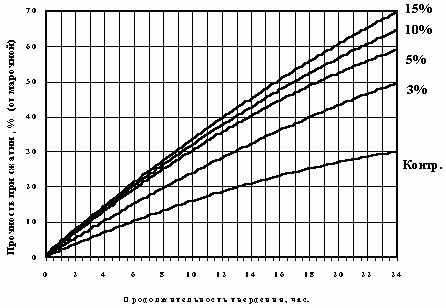
Рис. 3. Нарастание прочности бетона на ПЦ 400-Д20 при введении СПД до 15 % от массы цемента в условиях мягкого режима ТВО
Как видно из результатов эксперимента, через 8 часов после замеса, бетон имел прочность от 25 до 38 % от проектной, через 16 часов от 37 до 62 % и к 24 часам достигал прочности от 50 до 70 % в зависимости от количества добавки.
Влияние продолжительности изотермической выдержки на кинетику изменения прочности бетона проявляется в виде устойчивой тенденции ее роста с увеличением времени твердения бетона и повышением температуры ТВО. Для вяжущих с добавками-ускорителями при пропаривании эта тенденция устойчива, прирост прочности закономерно стабилен. Увеличение процента добавки обеспечивает при этом повышенный темп роста прочности бетона в первые 12-16 ч твердения, а затем ее прирост замедляется.