Десятые академические чтения раасн, 2006 г
Вид материала | Документы |
- Десятые академические чтения раасн, 2006, 1266.3kb.
- Десятые академические чтения раасн, 2006, 1519.63kb.
- Концепция устойчивого развития в стратегии градостроительства франции 05. 23. 22 Градостроительство,, 332.07kb.
- Резолюция районной детской экологической конференции Десятые Басарукинские чтения, 39.32kb.
- План организационно-педагогической деятельности с детьми, имеющими ярко-выраженные, 77.33kb.
- Новосибирский государственный педагогический университет, 43.06kb.
- Академические программы и экзаменационные курсы в австралии международные центры Embassy, 146.35kb.
- Экология человек общество, 371.15kb.
- Министерство образования и науки российской федерации московский государственный областной, 2810.15kb.
- Рассказывайте детям о ценности чтения. Показывайте связь чтения с их успехами в учебе, 97.26kb.
СПИСОК литературЫ
1. Ратинов В.Б. Розенберг Т.И. Добавки в бетон. – М.: Стройиздат, 1989. – 188 стр.
2. Цементные материалы с ускоряющими и противоморозными добавками на основе вторичного сырья. – Пенза, изд-во ПГАСА, 2003. – 425 стр.
УДК 666.974.2
Тотурбиев Б.Д., д-р техн. наук, профессор, Мантуров З.А., канд.техн.наук, доцент
Дагестанский государственный технический университет
НАУЧНО-ПРАКТИЧЕСКИЕ ОСНОВЫ ПОЛУЧЕНИЯ БЕЗОБЖИГОВЫХ ЖАРОСТОЙКИХ
ТЕПЛОИЗОЛЯЦИОННЫХ МАТЕРИАЛОВ НА ПЕНОСИЛИКАТ-НАТРИЕВЫХ КОМПОЗИЦИЯХ
Современное состояние производства и применения теплоизоляционных материалов показывает, что развитие промышленности теплоизоляционных материалов в связи с программой экономики топливно-энергетических ресурсов относится к сфере высших народнохозяйственных приоритетов страны.
Здесь особое место занимают теплоизоляционные материалы и изделия, предназначенные для тепловой изоляции горячих поверхностей с температурой 600-1600 0С. На практике для этих целей используют в основном высокопористые керамические теплоизоляционные материалы, получаемые путем введения и выжигания выгорающих добавок, введением высокопористых наполнителей, способами газового вспучивания (газообразованием) и пенообразования. При этом окончательное закрепление полученной высокопористой структуры и придание прочности изделиям во всех случаях достигается в процессе высокотемпературного обжига.
Однако высокая энергоемкость традиционных обжиговых высокопористых керамических теплоизоляционных материалов и большие капитальные вложения на их производство диктуют острую необходимость разработки и реализации новых эффективных жаростойких теплоизоляционных материалов, прежде всего безобжиговых, для высокотемпературной изоляции тепловых агрегатов различного назначения.
В этой связи большой интерес представляют многолетние научные исследования, проведенные в Дагестанском государственном техническом университете совместно с Московским государственным строительным университетом и НИИЖБ Госстроя РФ 1, 2. В результате всесторонних теоретических и экспериментальных исследований получены эффективные виды жаростойких безводных силикат-натриевых композиционных вяжущих на основе тонкодиспергированных безводного силиката натрия (БСН) и различных огнеупорных веществ (шамот, магнезит, динас, карборунд, хромомагнезит и т.д.).
Достаточно высокая огнеупорность этих вяжущих позволила разработать на их основе жаростойкие бетоны с температурой службы до 1600 0С, используя в качестве заполнителя различные огнеупорные материалы.
Обобщая результаты исследований по применению безводных силикатов натрия, было сделано предположение возможности разработки нового класса жаростойких материалов на БСН, получаемых по энергосберегающим технологиям, а именно безобжиговых высокопористых жаростойких теплоизоляционных материалов.
Научно-практические основы этих исследований заключаются в том, что формирование омоноличивающих новообразований в структуре материала из БСН принципиально отличаются от образования связующей пленки из традиционных вяжущих веществ (цементы, жидкое стекло и т.п.), связка из БСН характеризуется высокой плотностью и клеящей способностью, что может обеспечить повышенную прочность межпоровых перегородок (пленок) в высокопористой структуре теплоизоляционного материала.
Клеящая способность у нее в 3-5 раз выше, чем у традиционных вяжущих веществ, что предполагает эффективность использования безводной силикат-натриевой композиции для получения высокопористых жаростойких теплоизоляционных материалов. Кроме того, при взаимодействии БСН с водой вначале происходит гидратация катиона Na, который сорбируется на поверхности огнеупорного наполнителя и активизирует его. Особенно значительная активизация будет наблюдаться для алюмосиликатных огнеупорных наполнителей. В результате должно возрасти адгезионное взаимодействие клеящей связки с тонкомолотым наполнителем и формирование длинных и прочных цепей кремниевого полимера типа Si-O-Si, т.е. сильных поликонденсационных явлений.
Придание вяжущих свойств композиции из БСН и последующее ее упрочнение осуществляется в процессе низкотемпературной обработки (90 – 180 0С). Следовательно, отсутствие необходимости предварительного обжига при высоких температурах обуславливает экономическую эффективность получения безобжиговых высокопористых жаростойких теплоизоляционных материалов.
Использование в качестве связки сухого зернистого медленно гидратирующего БСН позволяет добиться высокой степени гомогенизации его в смеси даже при низкой дозировке его в составе массы. Концентрация связующего компонента в этом случае определяется не условиями гомогенизации и уплотнения смеси, т.е. не технологическими, а только факторами эксплуатационной стойкости. Это открывает возможность значительного снижения концентрации силиката натрия в массе, и как следствие, снижения в жаростойком материале содержания плавня, что в конечном счете должно привести к улучшению огнеупорных свойств материала на БСН.
Проведенными экспериментальными исследованиями установлен характер влияния происходящих физико-химических процессов на устойчивость пеноструктуры, в целом на структурированную систему, обладающую определенной жесткостью (упругостью) формы, способную длительное время сохранять свой первоначальный объем без разрушения. Эти процессы прослеживаются изменениями физико-механических свойств: усадкой, плотностью, механической прочностью на сжатие в зависимости от условий растворения и содержания Na2SiO3 в пеносиликат-натриевой композиции.
Таким образом, резюмируя теоретические положения и результаты предварительно проведенных экспериментальных исследований для получения безобжиговых жаростойких теплоизоляционных материалов можно отметить следующее:
- основными факторами влияющими на растворение БСН, следовательно, на вяжущие свойства пеносиликат-натриевой композиции являются: кремнеземистый модуль, дисперсность и равномерное распределение, количество воды, температура, продолжительность растворения;
- для исключения усадочных деформаций и связанных с ним деструктивных процессов при растворении БСН непосредственно в пеносиликат-натриевой композиции при низкотемпературной обработке 80-90 0С), необходимо произвести предварительный разогрев силикат-натриевой композиции до введения пены, для получения высоковязкой устойчивой пеносиликат-натриевой структуры;
- водный раствор БСН (жидкое стекло) образованный в силикат-натриевой смеси в процессе предварительного разогрева при соответствующем режиме тепловой обработки (80-90 0С) являясь высоковязким затворителем смеси повысит в целом вязкость пеносиликат-натриевой композиции, следовательно, устойчивость поровой структуры смеси (после введения пены) до последующего упрочнения ее обезвоживанием, путем подъема температуры сушки (180 0С).
СПИСОК литературЫ
1. Жаростойкие бетоны на основе композиций из природных и техногенных стекол / Ю.П. Горлов, А.П. Меркин, М.И. Зейфман, Б.Д. Тотурбиев. –М.: Стройиздат, 1986. –С. 144.
2. Тотурбиев Б.Д. Строительные материалы на основе силикат-натриевых композиций. –М.: Стройиздат, 1988. –С. 208.
УДК 691.327:666.972.3:620.169.1
Трошкина Е.А., аспирант
Магнитогорский государственный технический университет им. Г.И.Носова
ПРОГНОЗИРОВАНИЕ ДОЛГОВЕЧНОСТИ БЕТОНА С ПЛАСТИФИЦИРУЮЩИМИ ДОБАВКАМИ
С точки зрения термодинамики долговечность строительного материала означает устойчивость его структуры, т.е. способность сохранять свои признаки и свойства под воздействием как внутренних, так и внешних факторов.
Нарушение устойчивости любого состояния связано с удалением последнего от равновесия, степень которого характеризуется величиной производства энтропии. При малых отклонениях от равновесия производство энтропии служит критерием для установления стационарного состояния, где эта величина минимальна, а в случае равновесности – равна нулю.
Когда система значительно удалена от равновесия, устойчивость структурных состояний определяется величиной и знаком избыточного производства энтропии. При δxP > 0 состояния, удаленные от равновесия, будут устойчивыми, а при обращении знака неравенства неустойчивыми. Величина избыточного производства энтропии определяется взаимодействующими процессами гидратообразования и структурообразования, а ее знак – соотношением скоростей и движущих сил указанных процессов.
В данной работе проведен термодинамический анализ твердения шлакопортландцемента М300 (В/Ц=0,3) с пластификаторами ЛПМ (лигносульфонатный пластификатор-модулятор) 2-х модификаций: ЛПМ сухая – пластифицирующая (0,4%), ЛПМ жидкая – пластифицирующе-воздухововлекающая (0,4%). В результате анализа определены основные термодинамические характеристики твердеющего вяжущего, произведен расчет термодинамической устойчивости структурных состояний цементного камня.
Как показали проведенные исследования, при введении в вяжущую систему добавок ЛПМ увеличивается длительность существования коагуляционной структуры, формирующейся в первый период твердения, т.к. происходит замедление процесса гидратообразования. Длительное существование коагуляционной структуры в цементной пасте с добавками приводит к увеличению ее термодинамической устойчивости (рисунок 1 и 2), что связано со стабилизирующим действием адсорбционных оболочек пластификатора и более упорядоченным расположением частиц твердой фазы в объеме вяжущей системы.
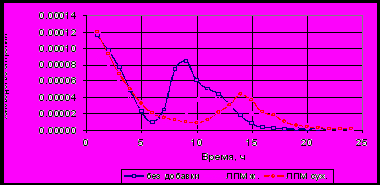
Рисунок 1 - Производство энтропии при твердении шлакопортландцемента
с добавками
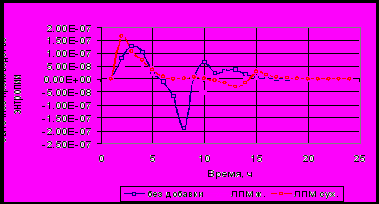
Рисунок 2 - Избыточное производство энтропии при твердении шлакопортландцемента с добавками
После окончания индукционного периода образуется термодинамически неустойчивая коагуляционно-конденсационная структура, которая представляет собой пространственно-временную диссипативную структуру (рисунок 2). Термодинамическая неустойчивость данного структурного состояния обусловлена совокупным действием процессов гидратообразования и структурообразования.
Шлакопортландцемент без добавки в меньшей степени перестраивает свою коагуляционную структуру, а это предопределяет и большую термодинамическую неустойчивость возникающей коагуляционно-конденсационной структуры (рисунок 1). Введение пластифицирующих добавок способствует увеличению упорядоченности коагуляционно-конденсационной структуры и росту ее термодинамической устойчивости (рисунок 1 и 2).
Кроме того, цементный камень, содержащий добавки ЛПМ, обладает более термодинамически устойчивой конденсационно-кристаллизационной структурой (рисунок 1). Высокая термодинамическая устойчивость конечной структуры предопределяет и ее высокую долговечность.
Данные термодинамического анализа подтверждаются испытаниями равноподвижных и равнопрочных бетонов с пластификаторами ЛПМ на морозостойкость. Добавки ЛПМ способствуют повышению морозостойкости бетона. Экспериментальные данные свидетельствуют, что бетон без добавки имеет марку по морозостойкости F100, с суперпластификатором С-3 – F150, с добавками ЛПМ – F400.
Таким образом, введение добавок ЛПМ приводит к увеличению термодинамической устойчивости структурных состояний цементного камня, что позволяет получать долговечные бетоны с высокими эксплуатационными свойствами.
УДК 691.421
Усачёв A.M., аспирант, Шмитько Е.И., д-р техн. наук, профессор,
Суслов А.А., канд. техн. наук, доцент
Воронежский государственный архитектурно-строительный университет
ОСНОВНЫЕ ЗАКОНОМЕРНОСТИ КИНЕТИКИ КОНТАКТНО-ДИФФУЗИОННОЙ СУШКИ
КЕРАМИЧЕСКИХ ИЗДЕЛИЙ
В связи с развитием и становлением индивидуального жилищного строительства сборные железобетонные конструкции все чаще уступают место штучным стеновым материалам, к которым в первую очередь относится лицевой керамический кирпич.
Это обстоятельство объясняется несколькими причинами: кладка стен из мелкоштучных изделий производится вручную, поэтому для возведения стен не требуется мощное грузоподъемное оборудование; малый размер кирпича дает широкий простор проектировщику при выборе архитектурного решения; здание из кирпича отличается хорошими экологическими показателями микроклимата помещений.
Современное строительство невозможно представить без керамического кирпича. Его вклад в организацию архитектурного облика здания настолько велик, что не сопоставим ни с каким другим стеновым материалом.
Однако получить качественный лицевой кирпич не просто. При его производстве возникает множество технологических проблем, из которых наиболее острой является проблема растрескивания сырца в процессе сушки. На сегодняшний день в практике керамических производств накоплен богатый опыт использования высокочувствительного к сушке сырья, но проблему трещинообразования эти методы не всегда успешно могут решить.
В связи с изложенным, актуальной является проблема повышения качества сушильных процессов, которая в данной работе решается за счет использования принципиально нового способа сушки [1]. Сущность нового способа сушки заключается в следующем: отформованный сырец помещается на подложку из пористого материала с высокой влагоемкостью и накрывается сверху влагонепроницаемым колпаком. Подложка с тыльной стороны подвергается высушиванию теплоносителем. Тем самым осуществляется диффузия влаги из сырца в подложку, а за счет подачи и отбора сушильного агента происходит конвективное испарение влаги с поверхности подложки.
Контактно-диффузионная сушка изделий позволяет обеспечить управляемое протекание процесса, сократить время сушки, а также исключить образование сушильных трещин.
Управление процессом сушки в нашем варианте может осуществляться через многие факторы, в том числе и через влагоемкостные характеристики посредника.
Центральным местом в понимании и количественной оценке интенсивности диффузионного влагопереноса от одного материала к другому является представление о потенциале переноса θ, который измеряется в массообменных градусах (°М).
Потенциал переноса влаги непосредственно связан с удельной изотермической влагоемкостью материала Сm. Понятие удельной изотермической влагоемкости аналогично понятию удельной теплоемкости и ее можно представить как:
Сm =(dU/dθ)T (1)
где (dU/dθ)T - частная производная от удельного влагосодержания по потенциалу влагопереноса при постоянной температуре.
Влагообмен между соприкасающимися телами будет происходить до состояния термодинамического равновесия. Тогда по аналогии с тепловым равновесием соприкасающихся тел, когда наступает равенство температур, можно считать, что в состоянии влажностного равновесия будет соблюдаться равенство:
θ1= θ2 , или
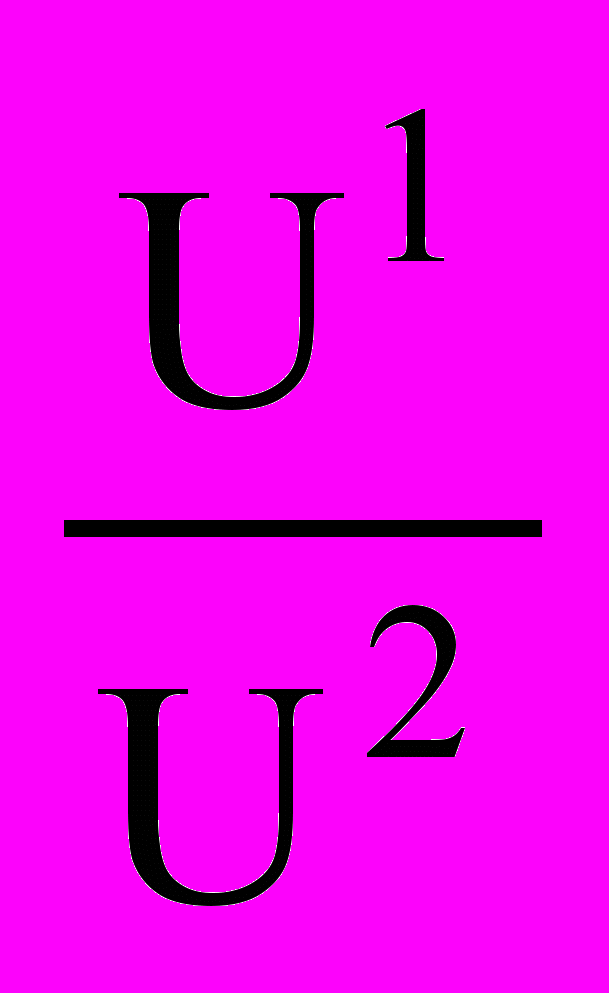
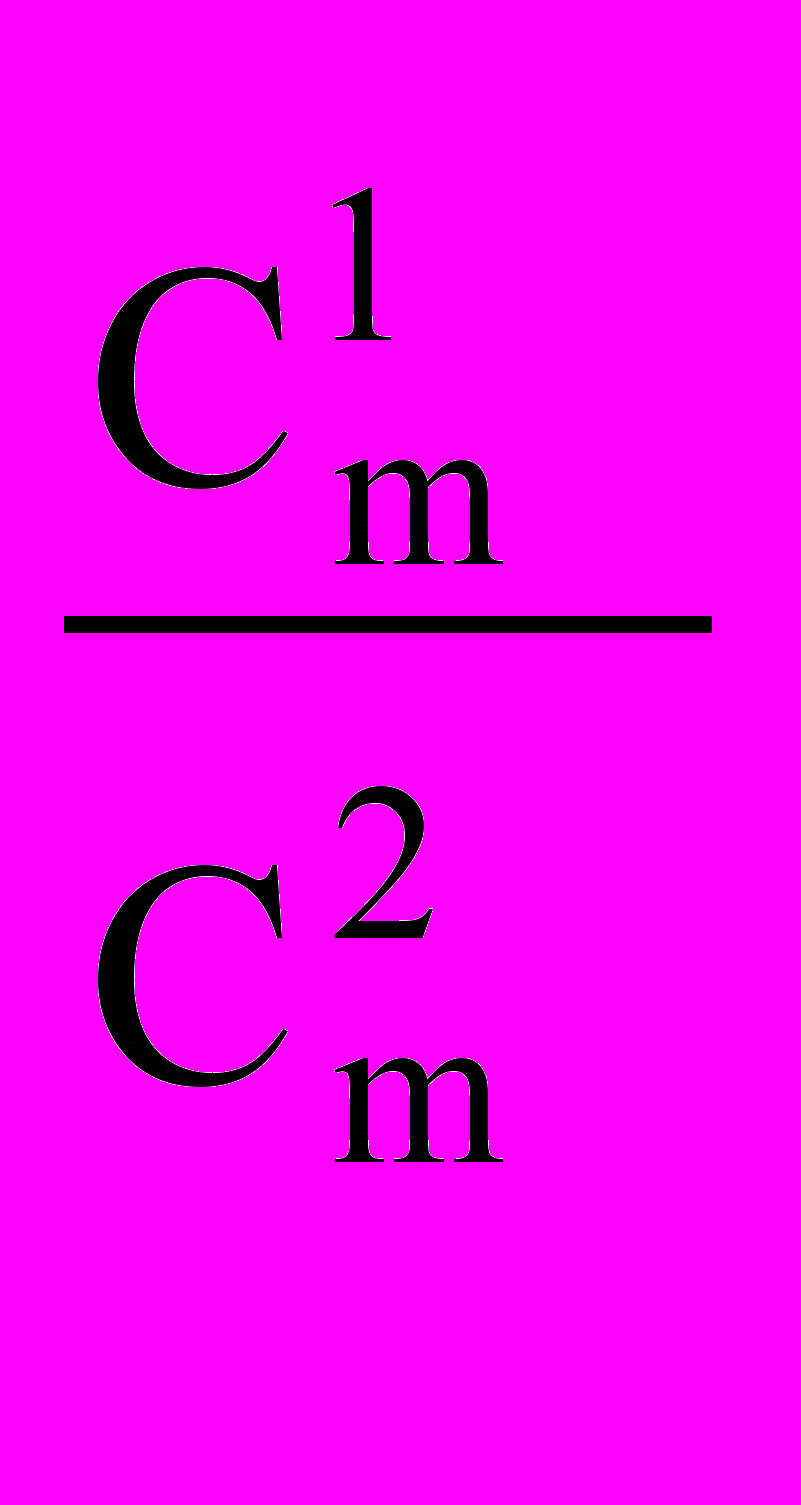
В плане достижения общей цели весьма важным этапом для нас является определение удельной влагосоемкости и потенциала переноса влаги наиболее вероятных в нашей постановке задачи посредников
В наши экспериментальные исследования были включены материалы, которые обладают довольно большими показателями открытой пористости и могут использоваться в качестве влагоемкой «подложки» при контактно-диффузионном способе сушки, В качестве таковых использовались: пеношамот со средней плотностью pm=300 кг/м3 и цементный камень с В/Ц 0,4. В качестве объекта сушки использовался образец-сырец пластического формования, изготовленный из высокочувствительной глины Семилукского месторождения.
Рассчитанные по методике А.В. Лыкова значения потенциала переноса и изотермической влагоемкости представлены в таблице 1.
Таблица 1
Значения потенциалов переноса и удельной изотермической влагоемкости материалов подложек
Наименование материала | Удельная изотермическая влагоемкость Сmм-10-3,кг/(кг..°М) | Потенциал переноса θ , °М |
Пеношамот pm=300 кг/м3 | 0,234 | 47 |
Цементный камень с В/Ц=0,4 | 1,034 | 135 |
Сырец из Семилукской глины | 0,465 | 352 |
Полученные показатели удельной изотермической влагоемкости, на наш взгляд, достаточно объективно отражают особенности структуры исследуемых материалов. Цементный камень, в котором объем пор целиком состоит из мезо-капиллярной пористости, обладает наибольшей влагоемкостъю. Несколько меньшую способность поглощать влагу имеет пеношамот, что свидетельствует о преобладании в его структуре макропор. Сырец по величине удельной влагоемкости занимает промежуточное положение.
Полученные результаты потенциала переноса влаги материалов-подложек и глиняного сырца показывают, что при контакте этих материалов влага будет перетекать из изделия с большим потенциалом к телу с меньшим потенциалом, т.е. из сырца в подложку.
На рисунках 1 и 2 представлены экспериментальные данные по высушиванию глиняного сырца контактно-диффузионным способом на подложках из пеношамота и цементного камня с В/Ц=0,4, Сушка осуществлялась при температуре теплоносителя t=200C и относительной влажности воздуха ф=80%.
В ходе эксперимента непрерывно фиксировалось изменение влажности сырца, а также влажность подложек
Полученные кривые изменения влажности подложек (рис. 1 и 2 б) соотносятся с ранее определенными значениями удельной изотермической влагоемкости Сm и потенциала переноса в. Как говорилось выше, неравенство потенциалов влаги соприкасающихся материалов предопределяет направление влагопереноса - сырец, обладающий большим потенциалом, высыхает, теряя влагу (рис. 1 и 2 а), а подложка увлажняется, причем количество поглощенной влаги пропорционально величине удельной изотермической влагоемкости (рис. 1 и 2 б).
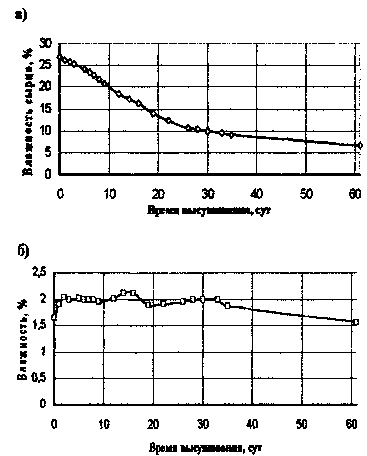
Рисунок 1 - Кривая сушки сырца а) и кривая изменения влажности
подложки из пеношамота с р=300 кг/м3 б) при параметрах теплоносителя t=20°C, ф=80%
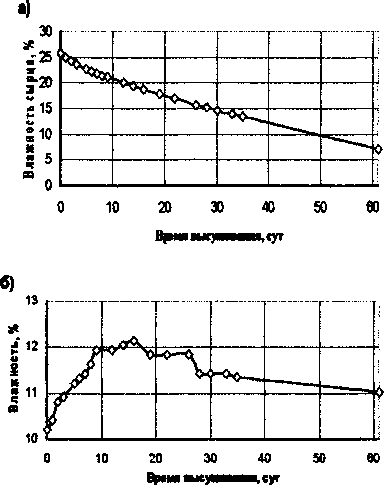
Рисунок 2 - Кривая сушки сырца а) и кривая изменения влажности
подложки из цементного камня с В/Ц=0,4 б) при параметрах теплоносителя t=20°C, ф=80%
Обладая самым большим значением удельной влагоемкости цементный камень в начальный срок интенсивно забирает влагу. Но через некоторое время устанавливается новый, более высокий уровень влажности (рис, 2 б), который свидетельствует о насыщении подложки влагой. При этом скорость диффузии влаги из сырца замедляется, процесс контактно-диффузионной сушки ослабевает и в дальнейшем идет, но очень медленными темпами. В отличие от цементного камня пеношамот в начальный период так же интенсивно поглощают влагу, но в то же время он сравнительно легко отдает ее. О чем свидетельствует почти одинаковый уровень влажности в начале и в конце процесса сушки (рис. 1 б). В этом случае процесс высушивания идет сравнительно быстро.
Таким образом, установлено, что при тесном контакте посредника из рассмотренных материалов и глиняного сырца влага будет перетекать из тела с большим потенциалом к телу с меньшим потенциалом, т.е. из сырца к посреднику, что позволит обеспечить контактно-диффузионную сушку сырца; скорость контактно-диффузионной сушки зависит не только от пористости посредника и, как следствие, поглощающей способности, но от того с какой легкостью этот материал может отдавать поглощенную влагу в окружающую среду; сходя из полученных результатов, пеношамот возможно использовать для жестких режимов сушки, цементный камень необходимо применять для мягких режимов сушки для крупногабаритных изделий или изделий сложной конфигурации.
СПИСОК литературЫ
1. Заявка 017355 РФ, МПК С 04ВЗЗ/30. Способ сушки отформованного кирпича-сырца / Е.И. Шмитько, А.А. Суслов, А. М. Усачев, Р.А. Важинский (РФ). -№ 2004116165/03, дата подачи заявки 27.05.2004. Приоритет 27,05,2004.
УДК 666.9
Филин Д.В., аспирант
Красноярская государственная архитектурно-строительная академия
ТЯЖЕЛЫЙ БЕТОН С ПРОТИВОМОРОЗНОЙ ДОБАВКОЙ НА ОСНОВЕ
ОТХОДОВ ПРОМЫШЛЕННОСТИ
Актуальным вопросом технологии товарных и монолитных бетонов является обеспечение благоприятных условий твердения при низких положительных и отрицательных температурах, когда бетонирование конструкций производится на строительной площадке.
Известно, что при снижении температуры среды, в которой происходит твердение цементных бетонов до 5…00С, процесс гидратации минералов цемента резко замедляется, соответственно снижается темп набора прочности. При достижении температуры ниже 00С вода в цементном камне и бетоне замерзает, в результате чего полностью прекращается реакция гидратации и твердение цемента и бетона. Кроме этого, замерзающая вода, увеличиваясь в объеме, создает в теле бетона внутренние напряжения, которые могут привести к растрескиванию структуры и последующему разрушению бетона.
Для предотвращения замерзания воды в бетоне при проведении бетонных работ в зимних условиях существуют специальные методы: прогревные и беспрогревные. К прогревным методам относятся: предварительный разогрев бетонной смеси в процессе ее приготовления или транспортирования; метод «термоса» при выдерживании в термоизолированной опалубке; подогрев бетона в термоактивной опалубке или в тепляках; прогрев электрическим током с помощью специальных электродов. Основная проблема таких методов заключается в том, что все они требуют дополнительного технологического оборудования и высоких расходов электроэнергии.
Менее энергоемким методом зимнего бетонирования является беспрогревный метод, основанный на применении противоморозных добавок. К ним относятся специальные соли-электролиты, которые снижают температуру замерзания воды. Бетон с такими добавками способен твердеть и набирать прочность при отрицательных температурах.
Номенклатура противоморозных добавок разнообразна, вид и количество их для введения в бетонную смесь зависит от температуры, при которой будут проводиться бетонные работы, причем большинство таких добавок являются дефицитными и дорогостоящими.
Одним из способов решения этой проблемы является возможность применения жидких отходов металлургической промышленности.
Применение солевых стоков металлургической промышленности в составе бетонной смеси подтверждено патентом РФ №2233818 «Способ приготовления бетонной смеси» от 10. 09.2004г. и ТУ 2152-003-05055017-2002 «Стоки минерализованные».
Анализ химического состава солевых стоков металлургической промышленности показал, что основные компоненты, входящие в их состав, представлены хлоридами кальция и натрия, поэтому они могут являться противоморозными добавками, снижающими температуру замерзания воды.
Оценка эффективности действия любых химических добавок, применяемых в бетонах, в том числе и противоморозных, производится в соответствии с ГОСТ 30459-96 «Добавки для бетонов. Методы определения эффективности».
Эффективность противоморозной добавки определяют по набору прочности бетона, твердевшего при отрицательной температуре в сравнении с прочностью образцов, твердевших в нормальных условиях.
Изменение прочности бетона R в процентах после твердения при отрицательной температуре вычисляют по формуле:
R = RД28*100
RК28
где RД28 – прочность бетона основных составов после нахождения в морозильной камере в течение 28 сут и оттаивания на воздухе, МПа;
RК28 – прочность бетона контрольного состава после твердения в нормальных условиях, МПа.
В проведенной работе эффективность действия солевых стоков оценивали при твердении бетонов в условиях постоянной отрицательной температуры, создаваемой в лабораторной морозильной камере и в естественных условиях (в зимнее время года на улице), при колебании температур наружного воздуха от 0 до –18 0С.
Для сравнения применялись традиционные противоморозные добавки: нитрит натрия NaNO2 (ГОСТ 19906-87), поташ К2СО3 (ГОСТ10690-79) и рекомендуемые последними научно-техническими разработками: формиат технический пентаэритрита ФТП (ТУ 2432-011-00203803-98) и ПМП-1 (ТУ 5870-001-56025130), а также специально приготовленный синтезированный раствор солей хлорида кальция и
хлорида натрия, в котором соотношение между СаCl2 и NaCl было принято равным их соотношению в солевых стоках.
Кривая естественных отрицательных температур, при которых производились испытания. представлена на рис.1.
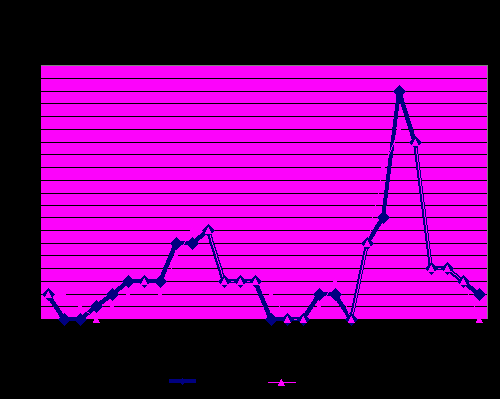
Рис.1
Полученные результаты испытаний представлены в табл. и на рис.2.
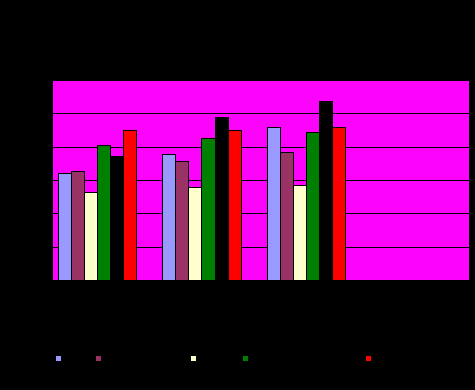
Рис.2
Таблица
Эффективность действия противоморозных добавок
Вид добавки | Эффективность R,%, при твердении, условия | |
постоянная отрицательная температура –1520С | естественная отрицательная температура | |
Формиат технический пентаэритрита (ФТП) | 70 | 82 |
Нитрит натрия | 85 | 93 |
Поташ (К2СО3) | 92 | 97 |
ПМП-1 (г. Новосибирск) | 91 | 96 |
Раствор ХК+ХН | 69 | 91 |
Солевые стоки | 98 | 98 |
Полученные результаты испытаний показали, что по эффекту действия солевые стоки не уступают традиционным добавкам, поэтому возможно их применение в качестве противоморозной добавки, что обеспечивает возможность проведения бетонных работ в зимних условиях с минимальными материальными затратами.
УДК 666.913.2
Фишер Х.-Б., канд. техн. наук
Университет строительных материалов, г. Веймар, Германия