Десятые академические чтения раасн, 2006 г
Вид материала | Документы |
- Десятые академические чтения раасн, 2006, 1092.49kb.
- Десятые академические чтения раасн, 2006, 1266.3kb.
- Концепция устойчивого развития в стратегии градостроительства франции 05. 23. 22 Градостроительство,, 332.07kb.
- Резолюция районной детской экологической конференции Десятые Басарукинские чтения, 39.32kb.
- План организационно-педагогической деятельности с детьми, имеющими ярко-выраженные, 77.33kb.
- Новосибирский государственный педагогический университет, 43.06kb.
- Академические программы и экзаменационные курсы в австралии международные центры Embassy, 146.35kb.
- Экология человек общество, 371.15kb.
- Министерство образования и науки российской федерации московский государственный областной, 2810.15kb.
- Рассказывайте детям о ценности чтения. Показывайте связь чтения с их успехами в учебе, 97.26kb.
СПИСОК литературЫ
1. Гончаров Ю.И., Иванов А.С., Гончарова М.Ю., Евтушенко Е.И..Особенности фазовой и структурной неравновесности металлургических шлаков // Изв. вузов. Строительство.- 2002.- №4.- С.50 – 53.
2. Гончаров Ю.И., Иванов А.С., Малькова М.Ю. Исследование процессов спекания металлургических шлаков // Изв. вузов. Строительство.- 2003.- №7.- С.51 – 55.
3. Малькова М.Ю., Бельмаз Н.С., Брагина Т.И. Разработка жаростойких безобжиговых изделий на основе недефицитного сырья // Вестник БГТУ им. В.Г. Шухова.- 2005.- №10.- С.180 – 183.
4. Огнеупорные бетоны: справочник / Замятин С.Р., Пургин А.К., Хорошавин Л.Б. и др.- М.: Металлургия, 1982.- 192с.
УДК 671.131
Мальцева И.Н., канд. техн. наук, доцент, Уфумцев В.М., канд. техн. наук, доцент,
Мальцев Н.В. студент
Уральский государственный технический университет - УПИ
КОНСТРУКТИВНОЕ РЕШЕНИЕ НАРУЖНЫХ СТЕН
ИЗ ЯЧЕИСТОГО БЕТОНА ДЛЯ МАЛОЭТАЖНОГО
СТРОИТЕЛЬСТВА
При оценке эффективности применения различных стеновых материалов и технологий при возведении тепловой оболочки зданий в соответствии с новыми нормами по теплоизоляции и следует учитывать также долговечность и экологическую безопасность в обычных и экстремальных условиях. Широко используемые эффективные плитные утеплители из минеральной ваты и пенополистирола не всегда сохраняют свои свойства в течении всего периода эксплуатации. Это приводит к увеличению теплопотерь, снижению температуры на внутренней поверхности стены и возможности выпадения конденсата в толще ограждения. Эти обстоятельства делают более привлекательными ячеистые бетоны, имеющие высокую степень долговечности, обладающие коэффициентом теплопроводности в несколько раз ниже чем у кирпичной кладки или керамзитобетона и являющиеся несгораемыми и экологически безопасными материалами при более низких стоимостных показателях.
В практике существуют две технологии возведения наружных стен из неавтоклавного ячеистого бетона. Первая - заводское изготовление ячеистых камней и кладка стен из них на объекте – включает технологическую линию на которой производятся изделия из газо- или пенобетона неавтоклавного твердения с плотностью 600-700 кг/м3 и прочностью 0,3 - 0,4 МПа. Технология предусматривает формование массивов размером в плане 1200х1500 мм, высотой 400 и 600 мм с последующей резкой на изделия требуемых размеров. [1]. Данная технология имеет свои преимущества: изготовление изделий большой точности
(отклонение размеров изделий от номинальных после резки составляет 1,5 мм). недостатком является то, что вследствие низкой прочности, часть камней ячеистой структуры повреждается при доставке и теряет свои потребительские свойства.
Вторая технология заключается в возведении стен из монолитного газобетона непосредственно на строительной площадке. Основная проблема та же: низкие прочностные характеристики, особенно в ранние сроки, которые не позволяют использовать съёмную или скользящую опалубку. Следовательно, стеновые конструкции из неавтоклавного активированного газобетона целесообразно возводить с использованием несъёмной опалубки.
На современном строительном рынке представлено большое количество материалов, которые могли бы служить несъёмной опалубкой для возведения наружных ненесущих стен каркасных зданий различного функционального назначения. В качестве фасадной опалубки можно использовать плоские асбестоцементные или фиброцементные панели с декоративным покрытием из минеральной или пластиковой крошки различной крупности ( например, систем «ФАССТ», «РИМ», «Сем-Колор», «Сем-Стоун» и др.) или кирпичная кладка из лицевого кирпича толщиной 120 мм, что сразу создаст декоративный эффект и надежную защиту газобетона от атмосферных воздействий. В качестве внутренней опалубки можно использовать плоские асбестоцементные листы, водостойкие гипсоволокнистые листы или термопанели системы «Кнауф».
В УГТУ –УПИ на малогабаритной промышленной установке «Цикл» производительностью 0,5-0,7 м3/ час возможно производить газобетон со средней плотностью 440-490 кг/м3 прочностью в возрасте 28 суток 0,6-0,9 МПа и коэффициентом теплопроводности l=0,113÷0,115Вт/м×°С. В работе использовали портландцемент М «400» ОАО «Сухоложскцемент», имеющий на момент использования гидравлическую активность 35,5 МПа. В качестве газообразователя использовали алюминиевую пудру ПАП-1. Для ускорения газообразования и твердения смеси в нее вводили добавку-активатор. Продолжительность активации составляла 10-15 минут. Подвижность заливаемой смеси составляла 280-300мм по вискозиметру Суттарда. Процесс поризации смеси завершался в течении одного часа после заливки.
Учитывая требования СНиП 23-02-2003 «Тепловая защита зданий», приняв температуру внутреннего пространства жилых зданий 21°С (СНиП 31-01-2003 «Здания жилые многоквартирные» и СНиП 31-02-2001 «Дома жилые одноквартирные») , для Екатеринбурга и региона показатель Dd составил
6210 °С×сутки, а требуемое сопротивление теплопередаче R0reg = 3,57 м2 оС/Вт. Следовательно, для конструктивного решения слоистых наружных стен представленных на рис.1, толщина газозолобетонного слоя составляет от 240 до 360мм. На рисунке приведены только три варианта конструктивных решений стенового ограждения, но их может быть больше.
Р
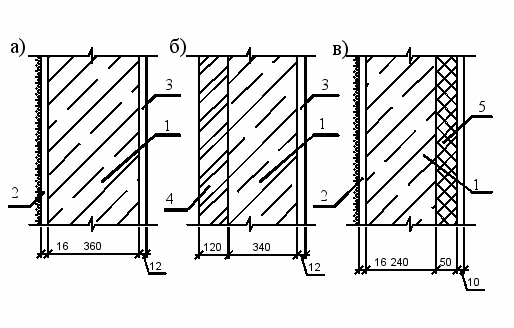
ис 1. Конструктивное решение стен из монолитного газобетона
1. газобетон (g = 440-490кг/м3 и l=0,113-0,115Вт/м°С); 2. асбестоцементные или фиброцементные панели с минеральной крошкой; 3. водонепроницаемые гипсоволокнистые листы системы «Кнауф»; 4. кирпичная кладка; 5. термопанель системы « Кнауф
Таким образом, наиболее целесообразным технологическим решением, с нашей точки зрения, является возведение ограждающих конструкций из монолитного неавтоклавного активированного газобетона в несъемной опалубке различного типа из современных материалов.
СПИСОК литературЫ
1. Гиндин М.Н., В.И. Синянский и [др]. Новая технологическая линия по производству неавтоклавного ячеистого бетона // Технологии бетонов, 2005. №5. С. 42-44.
УДК 691.215.1:666.762.38
Маноха А.М., ассистент, Козлова В.К., д-р техн. наук., профессор,
Гущина Е.Н., Сутула И.Г., аспиранты
Алтайский государственный технический университет им. И.И. Ползунова
РАЗРАБОТКА СПОСОБОВ КОМПЛЕКСНОГО ИСПОЛЬЗОВАНИЯ ДОЛОМИТОВ
Доломиты распространены в природе значительно больше, чем магнезиты. В Западной Сибири высококачественные доломиты находятся в Горной Шории – это месторождения Большая Гора и Таензинское. Запасы доломитов в этих месторождениях составляют более 140 млн. т. Имеются залежи доломита в северной части Кузнецкого Алатау, на Урюпинском участке. На территории Сибирской платформы по берегам рек выходят тысячеметровые толщи доломитовых пород ордовика и силура. В Туве в составе девонских отложений залегают мощные пласты доломитовой муки.
Сдерживающими факторами широкого внедрения магнезиальных вяжущих веществ в настоящее время являются небольшой объем производства каустического магнезита и каустического доломита, а также высокая стоимость и дефицитность солей магния.
В
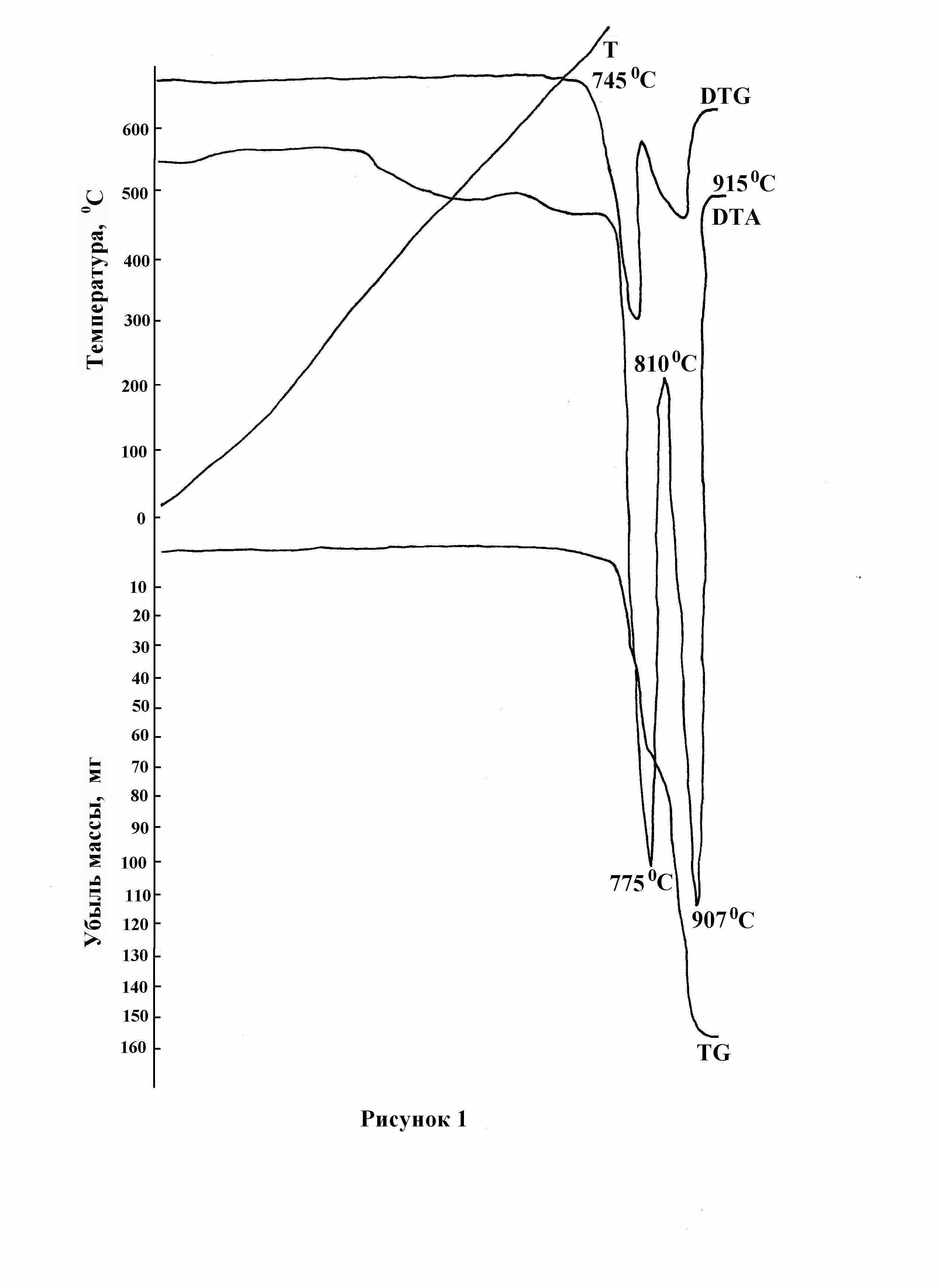
Проведенный дифференциально-термический анализ Таензинского доломита показал, что на термограмме имеется два глубоких эндотермических эффекта. Первый начинается при температуре 745 0С, достигая максимума при 775 0С, и заканчивается при 810 0С. При той же температуре начинается процесс разложения, характеризуемый другим эффектом, максимальная глубина которого соответствует температуре 907 0С (рисунок 1).
Было установлено, что из Таензинского доломита продукт, отвечающий требованиям к каустическому доломиту (п.п.п. – 30,0-35,0 %, MgO≥17,0 %, СаО≤2,5 %) получается двухчасовым обжигом при температуре 780 0С.
На основе результатов изучения поведения доломита при нагревании предложен графо-аналитический способ определения степени декарбонизации доломита по изменению соотношения средних плотностей обожженного (ρср. 2) и исходного продуктов (ρср. 1) (рисунок 2). При этом указанное соотношение может выступать в качестве контролирующего параметра при получении каустического доломита.
И
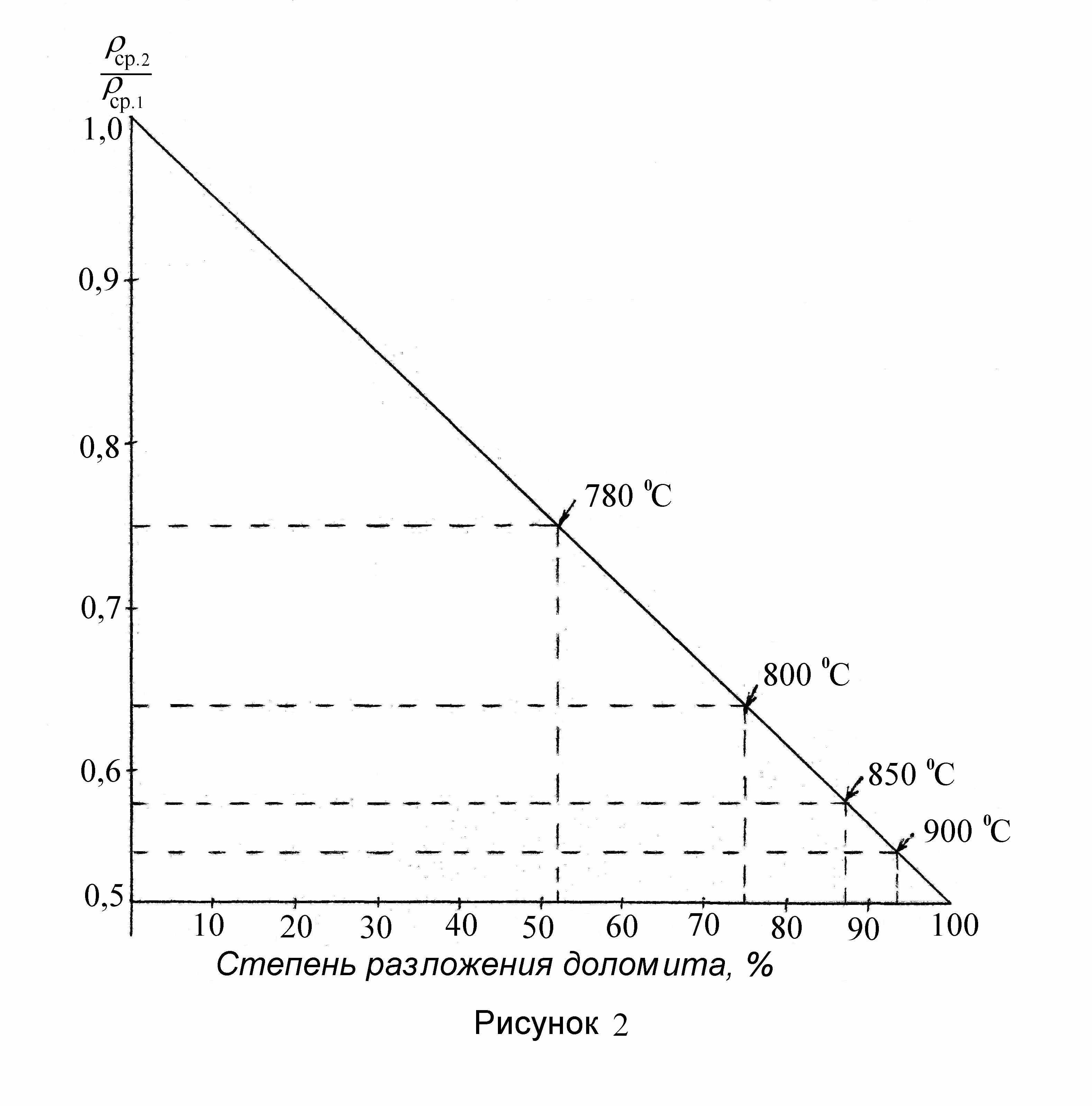
На основе каустического доломита разработаны составы и технологии производства теплоизоляционных материалов. С использованием органического заполнителя в виде отходов деревообработки получены сухие строительные смеси для изготовления бесшовных ксилолитовых полов. При средней плотности 1000-1500 кг/м3 ксилолит характеризуется пределом прочности при сжатии от 10,0 до 25,0 МПа, при изгибе - более 4,5 МПа.
С использованием различных видов пенообразователей на основе каустического доломита при затворении раствором MgCl2 получен пенодоломит средней плотности 450-700 кг/м3с пределом прочности при сжатии от 1,6 до 3,0 МПа. Возможно получение пенодоломита по двум технологиям: классической технологии получения пенобетонов и методом сухой минерализации. Метод сухой минерализации позволил получить пенодоломит с низкой средней плотностью
350-500 кг/м3. Кроме того, было установлено, что использование в производстве пенодоломита пены, приготовленной на растворах затворения, а именно на растворе MgCl2 (ρ=1170 кг/м3), позволяет получать пенобетон с более высокой прочностью. В качестве пенообразователей рекомендуется использовать "Унипор" и "ПБ-2000".
Разработан также способ получения высококачественного стенового и отделочного материала – доломитового кирпича (при использовании в качестве вяжущего каустического доломита), который заключается в следующем: смесь, состоящая из вяжущего и заполнителя, молотого сырого доломита или кварцевого песка, увлажнялась раствором MgCl2 (до влажности 8-9 %), изделия формовались прессованием при давлении 10,0-15,0 МПа. При твердении в нормальных условиях образцы достигают в течение суток предела прочности при сжатии, равного 9,0 МПа. При производстве доломитового кирпича наиболее эффективным заполнителем является молотый природный доломит фракции 0,5 – 1,0 мм (рисунок 3).
При изучении влияния процесса карбонизации на прочностные характеристики доломитового кирпича на основе каустического доломита установлено, что прочность образцов при сжатии увеличивается пропорционально росту степени карбонизации.
Исследование состава продуктов гидратации каустического доломита до и после принудительной карбонизации показало, что в большей степени подвергаются карбонизации образующиеся гидроксохлориды магния, гидроксид магния оказывается более устойчивым.
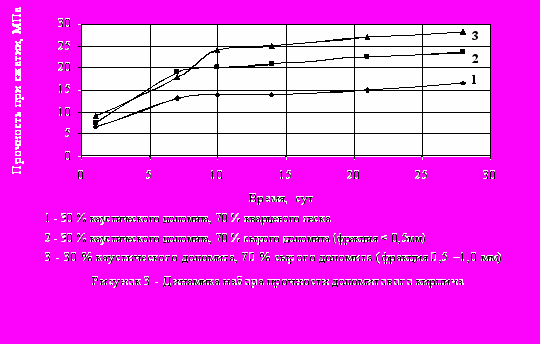
Кроме того, нами разработан способ получения сталеплавильного флюса на основе Таензинского доломита. Доломиты Таензинского месторождения являются трудноспекающимися, температура спекания в чистом виде составляет более 1700 0С. При получении офлюсованных доломитов с использованием трудноспекающегося сырья рекомендуется применение мокрого способа подготовки сырьевой смеси с последующим ее обжигом во вращающихся печах.
С целью достижения необходимых реологических свойств сырьевого шлама при влажности 32-36 % (растекаемость не менее 55 мм и оседаемость 10-15 %) предложено использование комплексной пластифицирующей добавки, состоящей из высокопластичной бентонитовой глины и суперпластификатора С-3. Установлено, что оптимальное количество бентонита составляет 1,5-2,0 %, оптимальное содержание суперпластификатора С-3 – 0,10-0,15 % от массы сырьевой смеси в расчете на сухое вещество.
В результате обжига при температуре 1400 0С был получен офлюсованный доломит требуемого химического состава со средней плотностью 2600 кг/м3, характеризующийся величиной потерь при прокаливании равной 1,6 %. Все характеристики полученного продукта отвечают требованиям технических условий на офлюсованный доломит.
Разработанные технологии производства каустического доломита, ксилолита, пенодоломита, доломитового кирпича и сталеплавильного флюса показывают возможность широкого использования доломитов Таензинского месторождения в производстве строительных материалов и в металлургической промышленности.
УДК 691.322
Мизюряев С.А., канд. техн. наук, доцент, Жигулина А.Ю., канд. техн. наук, доцент,
Иванова Н.В., аспирант
Самарский государственный архитектурно-строительный университет
ПОРИСТЫЙ ЗАПОЛНИТЕЛЬ С ИСПОЛЬЗОВАНИЕМ УГЛЕСОДЕРЖАЩИХ ОТХОДОВ
В современном строительстве доля легких бетонов увеличивается в связи с их эффективностью, обеспечением требуемых показателей надежности и экологической безопасности. Поэтому пористые заполнители с каждым годом производятся во всевозрастающих объемах.
Интенсивная разработка известных месторождений вспучивающегося глиносодержащего сырья привела к постепенному уменьшению их запасов и повлекла за собой снижение качества глин. В связи с этим появилась необходимость появления технологий производства заполнителя на альтернативной сырьевой базе. Такой сырьевой базой на современном этапе развития стройиндустрии могут стать отходы переработки углесодержащих пород.
В России ежегодно для складирования отходов добывающих, обогатительных и перерабатывающих комплексов отторгается более 2 тыс. га земель, в том числе пахотных.
Основная масса отходов – это твердые отходы угольного производства, объемы которых ежегодно увеличиваются на 1030 млн. м3. Отходы горного производства складируются в отвалы, выработки, ухудшают ландшафт местности, загрязняют водный и воздушный бассейны. На производство строительных материалов, отсыпку дорог и др. цели используется ежегодно лишь ничтожно малая их часть.
Применение углеотходов для производства строительных материалов, в частности для получения легкого заполнителя, сдерживается из-за большой неоднородности образующихся и складируемых отходов, а также высокого содержания углерода, который при количестве более 3% необходимо выжигать при 900…1000 градусов. Это ведет к очень большому расходу топливных ресурсов, а большинство углеотходов, таких как Донецкого, Кузнецкого, Печорского и других углебассейнов содержат углерода значительно более 3%, что препятствует вспучиванию материала при использовании керамзитовой технологии.
В СГАСУ разработана технология получения пористого заполнителя на основе жидкостекольной композиции, как основного вспучивающегося компонента. Одной из задач в проблеме заполнителя было получение шарообразных мелкопористых гранул с уплотненной внешней корочкой (по типу керамзитовой гранулы).
Экспериментально было установлено, что коагуляция жидкостекольных масс, приводящая к увеличению вязкости, способствует получению изделий заданной шаровидной формы. Так как вязкость жидкостекольных масс влияет на характер вспучиваемости, то в ходе исследований изучалось не только влияние введения различных модифицирующих (коагулируюших) добавок на способность жидкостекольных масс коагулироваться, но и вспучиваться при термообработке с образованием гранул шаровидной формы, имеющих корочку.
В результате испытаний было установлено, что наиболее эффективной, с этой точки зрения, добавкой является хлорид натрия. Введение его приводило к коагуляции жидкого стекла. Вязкость массы повышалась, она приобретала упруго-пластичные свойства, что позволяло формовать гранулы. Термообработка таких гранул приводила к их значительному вспучиванию с приобретением шарообразной формы и отвердеванию с сохранением приобретенной формы. Вспученные шарообразные гранулы имели равномерную высокопористую внутреннюю структуру с внешней уплотненной корочкой. Кроме того, среди испытанных веществ, хлорид натрия является наиболее доступным и дешевым материалом.
Технология заключается в следующем: в жидкое стекло вводится хлорид натрия при непрерывном перемешивании. Перемешивание продолжается в течение 3-5 минут. После этого модифицированная жидкостекольная сырьевая смесь выдерживается в течение 10-15 минут. При этом происходит коагуляция, а смесь приобретает вязко-упругие реологические характеристики, соответствующие скорости деформации 1,19…1,04 см/мин, что позволяет производить формование гранул. Для получения полуфабриката применяется метод грануляции в тарели с получением гранул в виде шариков.
Характеристики, полученного материала приведены в таблице 1.
Таблица 1.
№ п/п | Наименование показателя | Значение |
1 | Плотность в куске, г/cм3 | 0,2…0,6 |
2 | Насыпная плотность, кг/м3 | 150…550 |
2 | Прочность при раскалывании, МПа | 0,07…1,5 |
3 | Коэффициент водостойкости | 0,3 |
4 | Форма | шарообразная |
Для повышения прочности и водостойкости разрабатываемого заполнителя была изучено влияние введения в состав жидкостекольной композиции некоторых материалов. Было установлено, что наибольшей эффективностью с точки зрения повышения этих свойств являются материалы, содержащие оксиды железа, кремния, алюминия, например, такие как углесодержащие отходы.
Объясняется это тем, что подобные тонкомолотые добавки на этапе вспучивания выступают в качестве инертного наполнителя, оптимизируя вязкость жидкостекольных композиций и препятствуя тем самым чрезмерному росту поровой составляющей. Отмечено, что характер роста увеличения плотности практически не зависит от вида добавки.
В ходе исследования было установлено, что температура и продолжительность обжига практически не влияли на водостойкость, которая оставалась довольно низкой.
Для определения влияния режима охлаждения, обожженные в течение 10 минут гранулы, охлаждались с различной скоростью. Результаты представлены в таблице 2.
Таблица 2.
Показатели | Скорость охлаждения, оС/ мин. | |||
80 | 40 | 10 | 2 | |
Коэффициент водостойкости | 0,44 | 0,75 | 0,81 | 0,98 |
Снижение скорости охлаждения привело к значительному повышению водостойкости. При уменьшении скорости охлаждения от 80 до 2 оС/мин водостойкость увеличивается от 0,4 до 0,9 (в среднем в 2,2 раза). Это объясняется тем, что по мере уменьшения скорости охлаждения количество кристаллической фазы, имеющей низкую химическую активность, выпадающей из расплава, увеличивается, а стекловидной – уменьшается.
Таким образом, представленная технология позволяет, во-первых, расширить сырьевую базу и номенклатуру пористых заполнителей, а также вовлечь в производство заполнителей отходы переработки углесодержащих пород, позволяя тем самым сделать еще один шаг на пути решения актуальной проблемы переработки и утилизации отходов предприятий угольной промышленности.
УДК 691:53.217
Миронов В.А., д-р техн. наук, профессор, Белов В.В., д-р техн. наук, профессор,
Сухарев Ю.В., канд. техн. наук, доцент, Смирнов М.А., аспирант
Тверской государственный технический университет
ОПТИМИЗАЦИЯ ВЛАЖНОСТИ СЫРЬЕВЫХ СМЕСЕЙ ДЛЯ ИЗГОТОВЛЕНИЯ
СТРОИТЕЛЬНЫХ КОМПОЗИТОВ
Бетонные изделия, пользующиеся сегодня очень большим спросом, такие как дорожные и тротуарные камни, плиты и бортовые камни, в основном изготавливаются из полусухих бетонных смесей. Производство бетонных и железобетонных труб – еще одна важная область применения полусухих бетонных смесей. Кроме того, перспективным решением проблемы энерго- и ресурсосбережения является технология кирпича на цементном вяжущем с использованием высоких давлений прессования (гиперпрессования), которая позволяет исключить пропаривание за счет снижения количества макропор в изделии, увеличения сырцовой прочности, ускорения процесса формирования структуры цементного камня в нормальных условиях. При этой технологии наибольшее значение приобретает подбор составов композиций для изготовления прессованного мелкозернистого бетона, которые должны обеспечивать не только необходимое количество цементирующего вещества, но и оптимальное распределение его в представительском объеме композита, а также оптимальную гранулометрию заполнителя с целью достижения возможности наиболее плотной упаковки зерен, снижения упругого расширения прессовки после снятия давления и исключения перепрессовочных трещин. На сегодняшний день подбор состава и оптимизирование полусухих бетонных смесей происходят опытным путем, либо на основании гипотетических предположений.
Формирование структуры и свойств материалов гидратационного твердения имеет две стадии – первоначальное образование структуры из многокомпонентных и многофазных сырьевых смесей и последующее «укрепление» структуры в результате твердения материала [1]. Связь прочности цементных систем с начальным водоцементным отношением – основополагающий и давно обсуждаемый вопрос в строительном материаловедении. Обычно эту связь трактуют с точки зрения влияния пористости цементного камня, полученного из слитной (двухфазной) смеси цемента и воды, на его прочность, причем считается, что с увеличением В/Ц прочность цементного камня за счет увеличения пористости падает. А.В. Волженский [2] показал, что указанная связь имеет более сложный, экстремальный характер, обусловленный необходимостью создания начальной пористости при оптимальных значениях водоцементного отношения (0,27-0,35) для размещения цементирующих веществ (новообразований). Отклонение от оптимального водоцементного отношения в ту или иную сторону приводит к недоиспользованию потенциальных возможностей материала, а при переходе к системам с высокой концентрацией цементирующих веществ – даже к нарушению затвердевшей структуры.
В трехфазных (твердое-жидкость-газ) цементных сырьевых смесях при малых значениях водоцементного отношения – В/Ц, т.е. при неполном заполнении межзерновых пор цементной системы водой (и цементным тестом), что имеет место при получении изделий способом полусухого прессования, преобладающими силами взаимодействия между цементными частицами и зернами заполнителя в начальный момент после затворения являются силы капиллярного сцепления. Поэтому на взаимосвязь прочности затвердевшего материала с влажностью сырьевой смеси оказывают влияние процессы капиллярного структурообразования. Важнейшим процессом капиллярного структурообразования в системах, состоящих из грубодисперсной и тонкодисперсной фракций, к которым относятся смеси заполнителя и минерального вяжущего, является глобулирование. Оно выражается в налипании частиц вяжущего на поверхность зерен заполнителя с образованием агрегатов-глобул [3]. Временные структуры, возникающие на этих этапах, являются диссипативными (по Пригожину [4]), т.е. такими, которые характеризуются рассеянием энергии и ее переходом из одной формы в другую. В процессе глобулирования сырьевой смеси вяжущее концентрируется у поверхности заполнителей и в контактных зонах между ними. В этом одна из причин того, что при твердении цементной системы новообразования чешуйчатого и частично волокнисто-игольчатого строения вначале преимущественно образуются в наиболее тонких межчастичных контактах [5], т.е. в местах концентрации объемной воды – стыковых «манжетах» (по А.В. Лыкову [6]). В результате глобулирования прочность и плотность материала в указанных зонах повышается, что способствует увеличению прочности затвердевшего материала в целом. При разной влажности сырьевой смеси, т.е. начальном водотвердом отношении в ней, степень глобулирования, т.е. налипания частиц вяжущего на поверхность зерен заполнителя неодинакова, что неизбежно влияет на прочность прессованного бетона при его одинаковой первоначальной пористости [7].
В последней работе установлено, что пределы прочности на растяжение при изгибе и сжатие прессованного мелкозернистого (цементно-песчаного) бетона при одинаковой плотности по сухому веществу (постоянной пористости) с увеличением влажности сырьевой смеси до определенного предела Wмг, характерного для каждого состава смеси, достигают максимального значения, а затем снижаются.
При этих же значениях влажности наблюдается минимум насыпной плотности в пересчете на сухое вещество сырьевых смесей соответствующего состава.
Следовательно, экстремальный характер зависимостей прочности бетонных образцов при постоянной начальной пористости и одинаковом количестве цементирующего вещества (за возможным исключением наименьших значений влажности, при которых может ощущаться недостаток воды для гидратации цемента) от влажности сырьевой смеси объясняется влиянием капиллярного структурообразования в сырьевых смесях на структуру и свойства полученных из них готовых изделий. При оптимальной влажности сырьевой смеси Wмг в результате действия капиллярных сил тонкодисперсные частицы цемента сосредотачиваются на поверхности грубодисперсных зерен песка и в зонах контакта последних, образуя ячеисто-глобулярную структуру, признаком которой является минимум насыпной плотности сырьевой смеси в пересчете на сухое вещество. Это обуславливает оптимальную структуру композита, характеризующуюся наибольшей концентрацией вяжущего в зонах контакта заполнителя, и как следствие, повышенной прочностью контактных зон. Жидкая фаза в трехфазной сырьевой смеси при оптимальном содержании можно рассматриваться как усиливающий компонент, благодаря которому происходит упрочнение композита за счет перевода матричного компонента (цементирующего вещества) из объемного состояния в пленочное состояние с более высокой структурированностью и прочностью. Прочность полученного материала с оптимальной структурой при прочих равных условиях будет наибольшей. Данный подход позволяет на практике использовать результаты исследований полусухих бетонных смесей, проведенных в лабораторных условиях. На их основе предложены для производства эффективные и экономически рентабельные составы бетонов.
Бетоны высокой пластичности представляют собой также важнейшую тенденцию в технологии бетона. В отличие от традиционных виброуплотняемых бетонов область оптимального водосодержания высокопластичных бетонов с суперпластификаторами существенно ограничена и при этом сдвинута в сторону низких В/Ц. На сегодняшний день нет общепринятого метода для установления оптимального содержания воды и химических добавок в самоуплотняющихся бетонах. При разработке нового подхода в данной работе была принята гипотеза о формировании оптимальной структуры высокопластичных бетонов аналогично полусухим бетонным смесям. Эта оптимальная структура характеризуется наибольшей концентрацией вяжущего в зонах контакта заполнителя, и как следствие, повышенной прочностью контактных зон. Признаком этой структуры является минимум насыпной плотности сырьевой смеси в пересчете на сухое вещество при определенном водосодержании. В то время как полусухим бетонным смесям требуется интенсивное уплотнение для достижения заданной плотности, то высокопластичным бетонам для достижения этой цели необходима оптимальная добавка высокоэффективного суперпластификатора.
В таблице приведены результаты испытаний образцов-кубов размерами 7´7´7 см, изготовленных из пластичных песчано-цементных смесей состава 3 : 1 с расплывом конуса около 120 мм при малом водосодержании. Пластичность смесей достигалась оптимальной добавкой гиперпластификатора Melflux PP100F. В этой же таблице приведены значения насыпной плотности сырьевой смеси в пересчете на сухое вещество.
Результаты испытаний образцов пластичных песчано-цементных смесей состава 3 : 1 с расплывом конуса около 120 мм при малом водосодержании
Влажность смеси, % (В/Ц) | Количество добавки Melflux PP100F от массы цемента, % | Насыпная плотность сырьевой смеси в пересчете на сухое вещество, кг/м3 | Расплыв конуса, мм | Средняя плотность, кг/м3 | Предел прочности на сжатие в возрасте 7 суток, МПа |
6 (0,18) 7 (0,21) 8 (0,24) 9 (0,27) 10 (0,30) | 1,55 1,25 1,2 1,1 0,95 | 1135 1095 1075 1105 1150 | 117 118 118 119 118 | 2480 2490 2510 2490 2470 | 22,0 23,6 25,6 24,8 24,0 |
Новая методика может применяться для быстрого и практичного определения оптимального содержания воды и химических добавок при варьировании вида цемента, добавок, зернового состава и вида заполнителей, а также других технологических факторов.