О. Й. Любич, В. О. Пчелінцев Фізичні основи металургії кольорових І рідкоземельних металів
Вид материала | Документы |
- З дисципліни «Теоретичні основи ливарного виробництва» для студентів заочного факультету, 390.98kb.
- Програма, методичні вказівки та контрольні завдання з дисципліни " виробництво виливків, 797.9kb.
- Нова технологія утилізації гальваношламів машинобудівних підприємств з одержанням комплексних, 26.76kb.
- І містять у собі чорні або кольорові метали чи їх сплави, а також вироби з металу,, 462.13kb.
- Наказом Державного комітету України з питань регуляторної політики та підприємництва,, 341.66kb.
- Розробка базових теплотехнічних І конструктивних рішень, а також технологічних схем, 24.73kb.
- Назва реферату: Зварювання кольорових металів Розділ, 29.07kb.
- Робоча програма загальні методичні вказівки та індивідуальні завдання до вивчення дисципліни, 156.9kb.
- Типова програма кандидатського іспиту із спеціальності, 95.6kb.
- Державна митна служба україни, 19.16kb.
3.4.3 Випалення цинкових концентратів
Основна реакція випалення сульфіду цинку
2ZnS + СO2 → 2ZnO + 2SO2. (3.38)
Попутно при каталітичній дії оксидів металів сірчистий газ частково окиснюється до SО3:
2SO2 + O2 ↔ 2SO3. (3.39)
Сірчаний ангідрид зв'язує окисел цинку і сульфат:
2ZnO + SO3↔ ZnSO4. (3.40)
При випаленні для дистиляції утворення сульфату небажане: він відновлюється до сульфіду і залишається у раймуванні або шлаку. Для гідрометалургії наявність в недогарку невеликих кількостей сульфатів необхідно: на вилуговування їх не витрачається сірчана кислота, регенерована електролізом, тому втрати її у виробництві заповнюються. Утворенню сульфатів сприяють високі концентрації SО2 і О2 в обпалювальних газах і порівняно низькі температури випалення. Цим в основному і відрізняються умови випалення цинкових концентратів, що переробляються далі гідрометалургійним способом.
Окисел цинку здатний взаємодіяти з Fе2О3 за реакцією
ZnO + Fe2O3 → Zn(FeO2)2. (3.41)
Отриманий ферит цинку легко відновлюється вуглецем, при дистиляції він не небезпечний. Разом з цим у розбавленій сірчаній кислоті Zn(FeO2)2 розчиняється повільно і втрачається у нерозчинному залишку, тому для гідрометалургії утворення його небажане.
Зміна умов випалення мало впливає на вихід феритів; краще за все повніше відділення мінералів заліза при збагаченні.
Температура запалювання ZnS залежить від природних особливостей мінералу і його розмірів; практично її можна вважати такою, що дорівнює 550-600°С. Швидкість горіння зростає з температурою, можливість підвищення якої обмежена небезпекою оплавлення частинок.
Домішки інших сульфідів при випаленні окиснюються до Fе2O3, Fе3О4, СuО, СdO, Sb2О3, Аs2О3, свинець утворює РbSО4.
Окисли миш'яку і сурми частково сублімуються, а частково окиснюються до вищих, менш летких оксидів. Окиснені мінерали пустої породи мало змінюють свій склад; відбувається лише їх кальцинація – видалення хімічно зв'язаної води і вуглекислоти.
Кислотні оксиди: SО3, Аs2О5, Sb3О5, Fе2О3, SiO реагують з основними оксидами і карбонатами: з FеО, СuO, РbО, ZnО, а також з СаО і МgО, утворюючи відповідні солі – сульфати, арсенати, антимонати, ферити і силікати. Можливі тут численні реакції звичайно не завершуються через стехіометричну невідповідність між реагуючими речовинами, порушення контакту між ними або малі швидкості взаємодії. Суттєвішими побічними реакціями випалення потрібно вважати утворення феритів цинку, силікатів свинцю і цинку. Останні, взаємодіючи з сірчаною кислотою при вилуговуванні, виділяють колоїдну кременеву кислоту, що утруднює фільтрування і відпаювання пульп.
Всі цинкові концентрати обпалюють у печах киплячого шару.
Печі для випалення у киплячому шарі бувають круглі або прямокутні; на рис. 3.8 показана кругла піч. Стіни і звід її викладають з вогнетривкої цегли, а під роблять з жаротривкого бетону. Для подачі повітря і рівномірного розподілу його по череню служать сопла.
Концентрат подають з одного боку печі, і він, утворюючи киплячий шар, безперервно «зливається» з іншого боку у розвантажувальний жолоб, час перебування в шарі 10-12 год. Найтонші частинки несуться газами і повністю обпалюються «на льоту», залишаючись у печі всього 5-20 с. Винесення досягає 35% від завантаженого. Дев'ять десятих пилу осідає у циклонах, а інший – у наступних за ними електрофільтрах. Пил добре обпалений і містить більше сульфатів, ніж недогарок: температура у пиловловлювачах і газоходах нижча, ніж у печі. Змінюючи подачу пилу на вилуговування, легко регулювати баланс сірчаної кислоти.

Рисунок 3.8 – Креслення печі для випалення цинкових концентратів в киплячому шарі (а) і її череня (б): 1 – під з повітряними соплами; 2 – повітряні коробки; 3 – газоходи; 4 – пристрій для завантаження сирого концентрату; 5 – кесони для відведення надлишку тепла
Тепла, що виділяється при випаленні сульфідами, що горять, цілком достатньо для отримання у киплячому шарі температури від 900 до 950°С. Надлишок тепла відводять водяними холодильниками. Автоматичне регулювання дозволяє підтримувати температуру в межах ±10 град.
При випаленні для подальшої дистиляції температура досягає 1100°С. Випалення тут звичайно проводять у дві стадії, закінчуючи його на спікальних машинах отриманням безсірчистого агломерату.
Концентрати, що надходять на випалення в киплячому шарі, можуть мати високу вологість і навіть подаватися у піч у вигляді пульпи.
Важлива перевага «киплячого» випалення для гідрометалургії цинку – в дещо меншому утворенні феритів і силікатів: можливість контакту між твердими оксидами цинку, кремнію і заліза тут істотно менша, ніж в багатоподових печах.
При рівних габаритах печі киплячого шару більше ніж у три рази продуктивніші за багатоподові; піч діаметром 6,5 м обпалює 150 т концентрату за добу. Питома продуктивність, вимірювана відношенням добової продуктивності до площі киплячого шару, досягає 5 т/м2 за добу.
Завдяки швидкому згорянню сульфідів у киплячому шарі випалення можна проводити з малими надлишками повітря і одержувати високі концентрації SО2 в газах (8-10%) замість 1-7% - у багатоподових печах. Ще багатші гази одержують при підвищенні продуктивності випалення, застосовуючи повітря, збагачене киснем. Це поки що обмежено деякими труднощами.
3.4.4 Вилуговування обпалених концентратів
Усі сполуки цинку, наявні в обпаленому концентраті, здатні реагувати з сірчаною кислотою і давати водорозчинний сульфат цинку. Нерозчинним є тільки не окислений випаленням сульфід ZnS.
Сполуки заліза, міді, кадмію, миш'яку, сурми і кобальту взаємодіють з сірчаною кислотою з утворенням водорозчинних сульфатів або інших розчинних у воді сполук, наприклад:
FeO + H2SO4 → FeSO4 + H2O, (3.42)
CuO + H2SO4 → CuSO4 + H2O, (3.43)
Cu2O + H2SO4 → CuSO4 + Cu + H2O, (3.44)
CdO + H2SO4 → CdSO4 + H2O, (3.45)
FeAs2O + H2SO4 + H2O → FeSO4 + 2H3AsO4, (3.46)
FeSb2O + H2SO4 + H2O → FeSO4 + 2H3SbO4, (3.47)
CoO + H2SO4 → CoSO4 + H2O. (3.48)
Як вже було сказано, силікати свинцю і цинку розкладаються сірчаною кислотою з утворенням колоїдної кременевої кислоти, що утруднює згодом згущування і фільтрування розчинів, наприклад
ZnSiO3 + Н2SО4 → ZnS04 + Н2SiО3. (3.49)
Майже повне вилуговування окислу цинку і разом з цим порівняно мале розширення домішок обумовлені відмінністю швидкостей реакцій оксидів з сірчаною кислотою. Особливо повільно розчиняються ферит цинку Zn(FeO2) і окисел заліза Fе2О3, тому іонів Fе3+ в розчинах мало.
Оксиди двовалентного заліза, міді, кадмії, миш'яку, сурми і кобальту майже повністю переходять в розчин. Наявність цих домішок утруднює подальший електроліз, тому отримані розчини необхідно очищати.
Очищення розчинів від заліза можливе одночасно з вилуговуванням. Іони Fе2+ окиснюють двоокисом марганцю. У результаті окиснення і подальшого гідролізу в осад випадає основний сульфат заліза:
2FeSO4+MnO2+2H2SO4→Fe2(SO4)3+MnSO4+2H2O, (3.50)
Fe2(SO4)3 + 2H2O → 2FeOHSO4 + 2H2SO4. (3.51)
Перша реакція проходить у кислому середовищі, тому залізо потрібно окисляти на початку вилуговування. Друга можлива тільки до кінця вилуговування, коли кислота вже витрачена і розчин майже нейтральний.
Одночасно із залізом з розчину видаляються домішки миш'яку, сурми і частково кременева кислота. Досить повного осадження миш'яку і сурми разом із залізом можна досягти, якщо останнього в 10-20 разів більше за масою, ніж миш'яку, і в 20-40 разів більше, ніж сурми. Для цього недостатню кількість заліза іноді вводять у розчин.
Для повного добування цинку потрібен надлишок сірчаної кислоти, але для очищення від заліза розчин до кінця вилуговування повинен бути нейтральним. Тому вилуговування проводять у дві стадії. Спочатку обпалений цинковий концентрат обробляють раніше одержаним слабокислим розчином ZnSO4, що містить близько 100-130 г/л цинку і 1-5 г/л вільної сірчаної кислоти. Такої кислотності недостатньо для повного вилуговування всього цинку, і лише частина його переходить в розчин, який стає нейтральним, а отже, і очищеним від заліза. Після нейтрального вилуговування в нерозчинному залишку ще багато цинку, тому його вилуговують повторно відпрацьованим електролітом, що містить близько 150-170 г/л H2SО4. До кінця кислого вилуговування концентрація сірчаної кислоти в розчині зменшується до 1-5 г/л, розчин відділяють від осаду і спрямовують на нейтральне вилуговування (рис. 3.9).
Двостадійне вилуговування вигідне при великому масштабі виробництва і постійному складі сировини; воно проводиться безперервним способом. При випаленні недогарок трохи спікається. Великі частинки, подані пеками сульфідів, феритів і силікатів, повільно реагують з сірчаною кислотою. З великих частин цинк переходить в розчин повільніше, ніж з дрібних: поверхня сполук його часто ізольована від розчину пустою породою. Тому великі зерна (піски) перед вилуговуванням подрібнюють, збільшуючи цим самим поверхню твердої речовини, що припадає на одиницю маси: швидкість розчинення пропорційна величині поверхні частинок.
Гарячий недогарок, що безперервно виходить з обпалювальних печей, спрямовують у жолоб, де він змішується із струменем розчину і несеться ним у класифікатори. Подальше роздільне вилуговування зливу і пісків показане на схемі рис. 3.9.
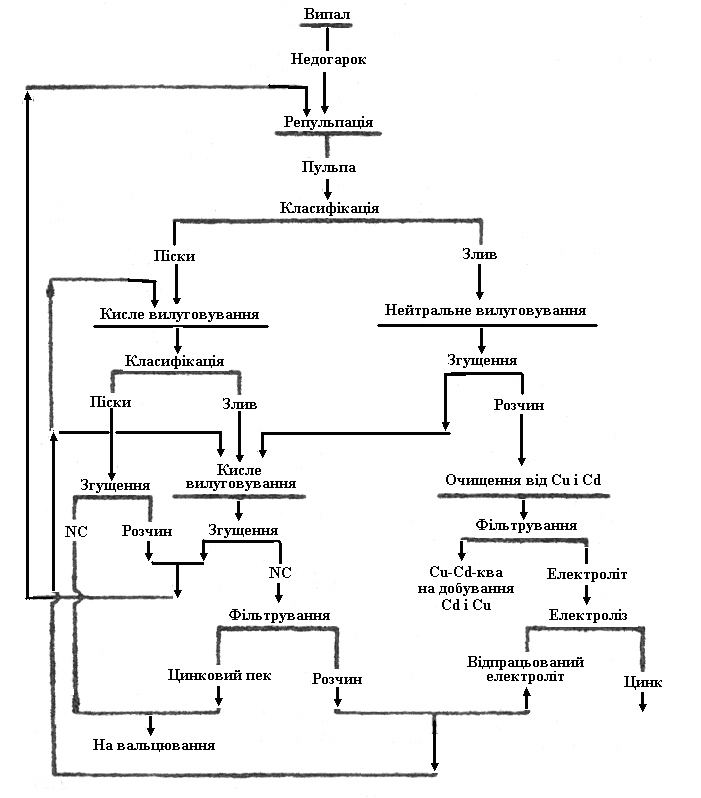
Рисунок 3.9 – Схема безперервного вилуговування недогарка
На деяких заводах віддають перевагу охолоджуванню недогарка і його класифікації на вібраційному грохоті. Відсівання великих розмірів подрібнюють і повертають на випалення. Дрібну фракцію вилуговують в один прийом відпрацьованим електролітом до повної нейтралізації розчину, необхідної для гідролізу солей тривалентного заліза. У цьому випадку вилуговування періодичне; воно зручніше, якщо склад сировини часто зміняються.
При вилуговуванні завжди необхідне перемішування пульпи, що підтримує тверді частинки в зваженому стані. Для цього застосовують апарати двох типів: пневматичні і механічні; в перших пульпа перемішується стиснутим повітрям, в других – мішалкою, що обертається.
3.4.5 Очищення нейтрального розчину сульфату
цинку від домішок
Домішки міді, кобальту, заліза, миш'яку і сурми навіть при невеликому вмісті їх в електроліті значно знижують вихід по струму. За наявності деяких іонів, наприклад, нікелю і кобальту, утворюються нерівні і нещільні катодні осади, при подальшому плавленні яких у результаті окиснення втрачається багато цинку.
Усі перелічені метали часто зустрічаються в цинкових концентратах, а при вилуговуванні в тому або іншому ступені переходять в розчин. Зразкові дані про склад неочищених нейтральних розчинів і сучасні вимоги, що ставляться до складу електроліту, наведені в табл. 3.1.
Очищення нейтрального розчину перед електролізом постійно необхідне для видалення міді і кадмію; очищення від кобальту і хлору потрібне не завжди. Кобальт і хлор виділяють з частини електроліту (що тимчасово виводиться з циркуляції) для того, щоб припинити накопичення їх в розчині.
Таблиця 3.1 – Зразкові дані про склад неочищених нейтральних розчинів
Домішки | Вміст, г/л | |||
Зразкове | що вимагається | |||
розчин I | розчин 2 | розчин 3 | ||
Сd | 0,35 | 0,15 | 0,25 | 0,002-0,004 |
Сu | 3,0 | 0,3 | 0.6 | 0,0001-0,0005 |
Fе | 0,03 | 0,03 | 0,002 | 0,02-0.03 |
As | - | 0,03 | 0,001 | 0,0001 |
Sb | - | 0,001 | 0,001 | 0,0001 |
Со | 0,003 | 0,001 | 0,07 | 0,003-0,007 |
Очищення розчину від міді і кадмію ґрунтується на реакціях цементації:
Сu2+ + Zn →↓ Сu + Zn2+, (3.52)
Сd2+ + Zn →↓ Сd + Zn2+. (3.53)
Для прискорення очищення цинк застосовують у вигляді пилу, отриманого розпилюванням рідкого металу або конденсацією його парою.
Витрата цинкового пилу перевищує стехіометричний: частина її розчиняється у результаті відновлення водневих іонів; крім того, осідання міді і кадмію, що утворюються на поверхні частинок цинкового пилу, перешкоджають повному її використанню.
Очищення розчинів від міді і кадмію проводять у чанах ємністю 35-45 м2 з лопатевими мішалками. Чан заповнюють нейтральним розчином, що надходить із згущувачів нейтральної гілки і після додавання цинкового пилу перемішують протягом 40-50 хв. Осад, що випав, фільтрують на фільтр-пресах. Підігрівання розчину при очищенні дороге, тому осадження звичайно проводять при температурі, з якою розчин вийшов із згущувачів, тобто при 38-40°С. Застосовують також очищення в киплячому шарі частинок цинкового пилу, що є у розчині.
3.4.6 Електролітичне осадження цинку
На електроліз надходить очищений від домішок нейтральний розчин сірчанокислого цинку, що містить іони Zn2+,
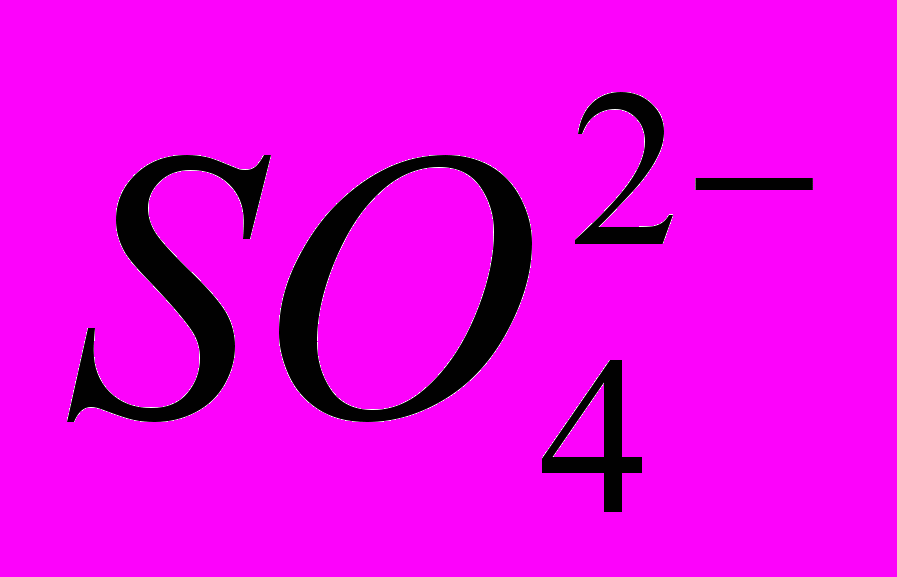
На катоді електролітної ванни можуть розряджатися іони цинку і водню:
Zn2+ + 2e → Zn; Е° = -0,70 в; (3.54)
2Н+ + 2е → Н2; Ео = ±0,00 в. (3.55)
Ґрунтуючись на величинах нормальних потенціалів, можна припустити, що на катоді виділятиметься лише водень, оскільки він електропозитивніше цинку.
Насправді цинк успішно осаджують електролізом кислих розчинів, користуючись тим, що фактичний потенціал розряду водневих іонів внаслідок перенапруження від’ємніше рівноважного. Чим менше водню виділиться на катоді разом з цинком, тим вище вихід цинку по струму. Практично при потенціалі розряду іонів цинку (близько -0,76 в) частка водню, що спільно виділяється, становить приблизно 5%.
Вихід по струму при електролізі цинку може бути зниженим, якщо не створені умови для високого перенапруження водню. Чим більша різниця потенціалів розряду іонів водню і цинку, тим менш вірогідне виділення водню на катоді разом з цинком. Отже, для отримання високих виходів по струму потрібно проводити електроліз так, щоб потенціал розряду іонів водню був можливо більш негативним, а потенціал розряду іонів цинку менш негативним.
Потенціал розряду іонів цинку близький до визначуваного з рівняння Нернста:
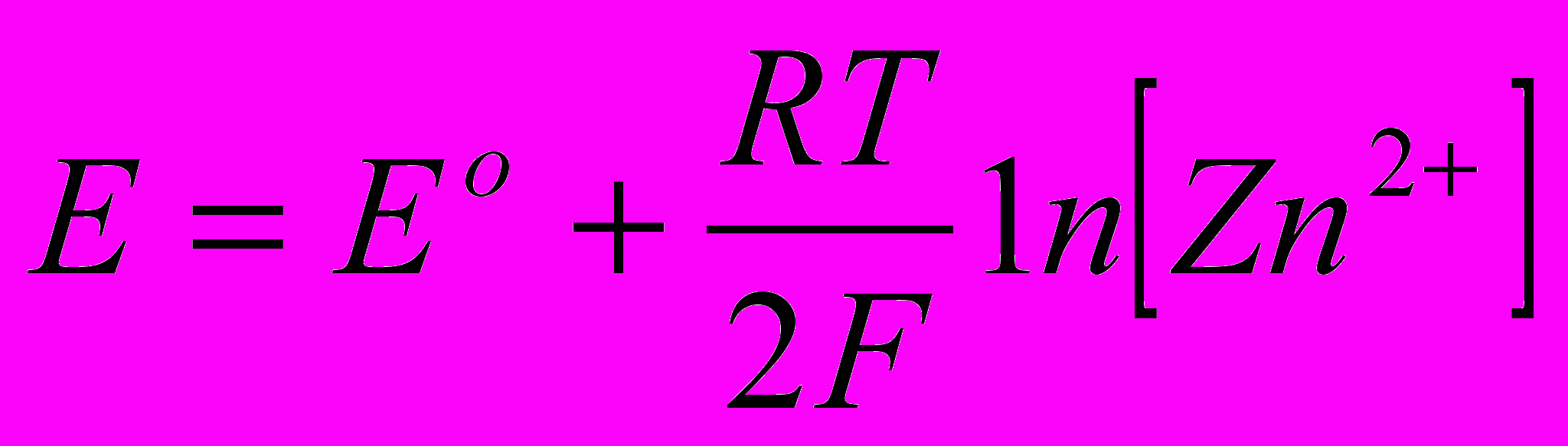
де Е° - нормальний потенціал, в;
[Zn2+] - концентрація цинку в розчині, моль/л.
Потенціал розряду іонів цинку тим позитивніше, чим більша концентрація цинку в розчині (точніше, активність іонів цинку).
Потенціал розряду іонів водню складається з рівноважного потенціалу і перенапруження:
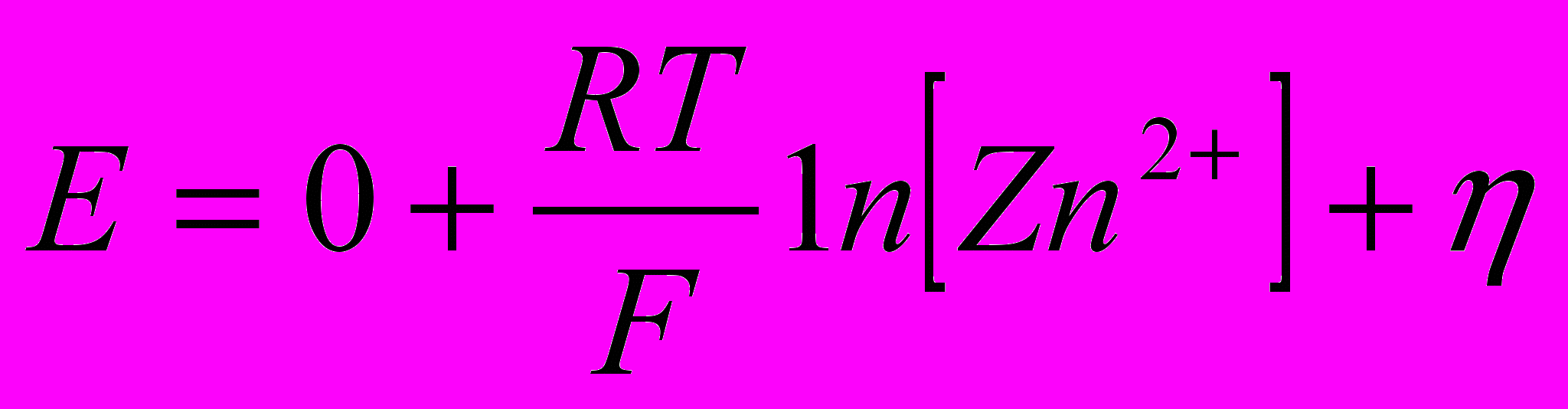
де η - перенапруження, в.
Рівноважний потенціал Н визначається активністю водневих іонів; з пониженням кислотності він зростає, а від щільності струму майже не залежить. На перенапруження впливають температура і щільність струму: високе перенапруження водню досягається при великій щільності струму і низьких температурах. Таким чином, для отримання високих виходів по струму слід піддавати електролізу концентровані розчини сірчанокислого цинку і проводити електроліз при великій щільності струму і низьких температурах.
На свинцевому аноді електролітної ванни вірогідні такі електрохімічні реакції:




За величинами нормальних потенціалів видно, що тут найшвидше всього відбувається утворення сульфату свинцю, що покриває анод тонкою плівкою важкорозчинних кристалів. Відкрита поверхня свинцю при цьому зменшується, щільність струму зростає, а разом з нею збільшується і потенціал анода. Далі в порах плівки сульфату свинцю відкладається РbО2, а потім при новому підвищенні потенціалу анода починається виділення кисню – головний анодний процес. Розряд іонів
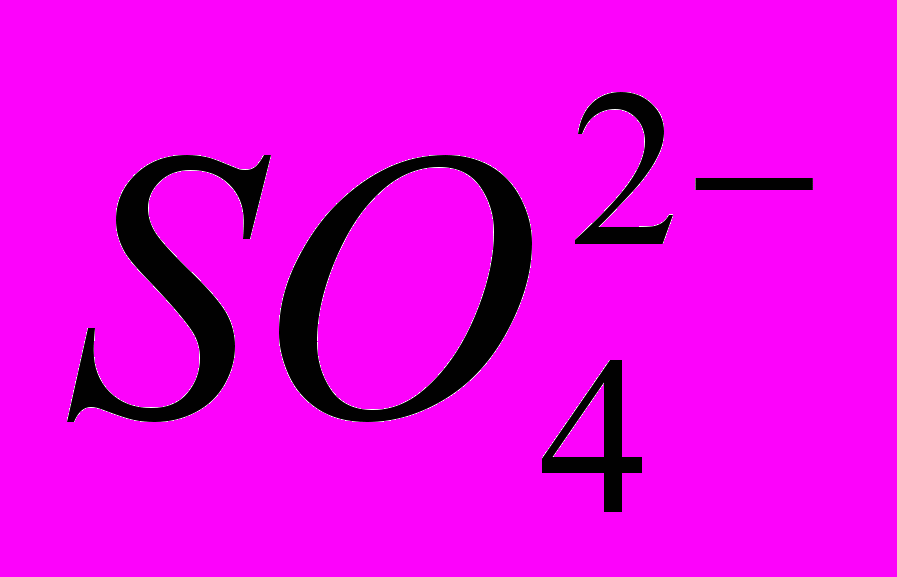
3.5 Фізико-металургійні основи отримання молібдену
3.5.1 Молібденові руди і їх збагачення
Мінерали, важливі для виробництва, численні, з них тільки молібденіт MоS2 первинного походження, інші – повеліт СаМоО4, молібдит Fe2(MoO4)3 і продукти вторинних перетворень сульфіду. Молібденіт, що має першорядне значення, чорного кольору, м'який, на папері залишає межу подібно до графіту; щільність мінералу 4700-4800 кг/мЗ.
Руди містять десяті і соті частки відсотка молібдену, вони поділяються на кварцові, комплексні за вольфрамітом; скарнові, у яких молібденіти інколи супроводжують шеєліт, пірит і халькопірит, а порода складається з кременистих вапняків. Мідно-молібденові руди колчеданового або вкрапленого типу - основний вид сировини. Молібденіт в них супроводжують пірит і халькопірит. Частіше переважає мідь, а молібден складає соті частки відсотка, але інколи його більше, ніж міді.
Збагачення базується переважно на флотації молібденіту, добування якого в концентрати, навіть з бідних руд, досягає 90% при вмісті близько 90% MоS2. Спочатку флотують всі сульфіди. Колективний концентрат після подрібнення розділяють повторною флотацією, пригнічуючи мінерали міді і заліза сірчистим або ціаністим натрієм при рН = 8,5. Збирачем для молібденіту служать гас і мінеральні масла, а як спінювач застосовують соснове масло. Шеєліт, якщо він наявний, виділяють з хвостів флотації, використовуючи як реагенти жирні кислоти і силікати натрію.
Вітчизняні концентрати мають за ТУ марки КМ1, КМ2 і КМЗ, вміст молібдену в них відповідно: 50, 48, 47%. Головні домішки: 0,07-0,15% Р; 0,07% As; 0,5-2% Сі; 5-9% SiO2; 0,07% Sn.
3.5.2 Способи переробки концентратів
Продукти, одержувані з концентратів, різні за призначенням і складом: у чорну металургію надходять переважно феромолібден - сплав із залізом і молібдат кальцію. У хімічну промисловість і для отримання ковкого металу йдуть чисті сполуки: триокис молібдену, парамолібдат амонію, молібдати натрію і кальцію. Технологічні схеми першим переділом мають окиснення молібденіту випаленням, рідше азотною кислотою або киснем у автоклавах. На більшості підприємств поки застосовують випалення. Недогарок спрямовують на виплавку феромолібдену, переробляють гідрометалургійні, вилуговуючи МоО3 розчинами аміаку, соди або лугу або переганяють з нього триокис і уловлюють в пиловловлювачах.
Метал у вигляді порошку відновлюють з чистого триокису водню або вуглецем, подібно вольфраму.
3.5.3 Аміачний спосіб
Горіння молібденіту за хімізмом і кінетикою схоже з окисненням інших сульфідів у мідних, цинкових або свинцевих концентратах:
2MoS3 + 7O2 = 2МоО3 + 4SO2. (3.62)
При високих температурах МоО3 помітно випаровується, тиск пари його має такі величини:
температура, 0С 600 700 800 900
тиск, Н/м2 613-10-3 48 1679 6838
У недогарку необхідно залишити не більше 2% сірки, а температуру вище 600°С піднімати не можна через віднесення МоО3 газами. Випалення можна прискорити тільки подачею надлишку повітря і перемішуванням концентрату.
У багатоподових печах вдається підтримувати необхідну температуру (580-590°), якщо подів багато, наприклад 12, і повітря потрібно подавати на кожний з них окремо. Продуктивність за концентратом при цьому не вища 70 кг/(м2·добу).
У печах КШ (киплячий шар) молібденові концентрати почали обпалювати вперше у нашій країні; схема установки для цього показана на рис. 3.10 з поперечником до 3 мм. Цим зменшують винесення пилу, в якому залишається до 10% MoS2 і КШ необхідно обертати. Продуктивність досягає 1300 кг/(м2·добу), вона майже в 20 разів вища, ніж в багатоподових печах.
Для виробництва феромолібдену випалення КШ непридатне, в недогарку дуже багато сірки, зокрема 2% сульфатної, зв'язаної в CaSO4: сірка забруднює чавун і сталь. Випалення в багатоподових печах у цьому випадку краще: при тривалому контакті в шарі сульфати розкладаються триокисом молібдену:
2CaSO4 + 2MoO3 = 2CaMoO4 + 2SO2 +O2. (3.63)
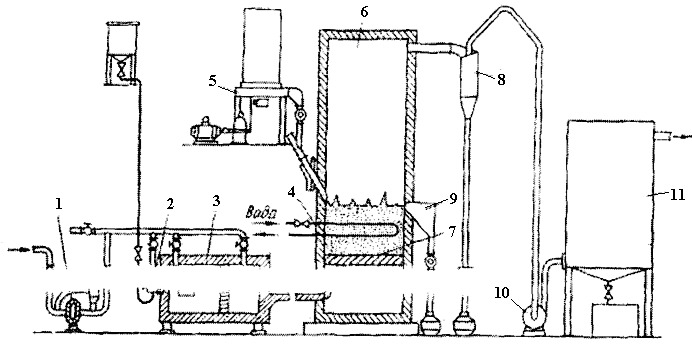
Рисунок 3.10 - Установка для випалення молібденових концентратів у киплячому шарі: 1 – повітронагрівач; 2 – форсунка;
3 – топка; 4 – холодильник регулювання температури КШ;
5 – завантажувальний бункер; 6 – піч; 7 – під КШ; 8 – циклон; 9 – розвантажувальний пристрій; 10 – димосос; 11 – електрофільтр