О. Й. Любич, В. О. Пчелінцев Фізичні основи металургії кольорових І рідкоземельних металів
Вид материала | Документы |
- З дисципліни «Теоретичні основи ливарного виробництва» для студентів заочного факультету, 390.98kb.
- Програма, методичні вказівки та контрольні завдання з дисципліни " виробництво виливків, 797.9kb.
- Нова технологія утилізації гальваношламів машинобудівних підприємств з одержанням комплексних, 26.76kb.
- І містять у собі чорні або кольорові метали чи їх сплави, а також вироби з металу,, 462.13kb.
- Наказом Державного комітету України з питань регуляторної політики та підприємництва,, 341.66kb.
- Розробка базових теплотехнічних І конструктивних рішень, а також технологічних схем, 24.73kb.
- Назва реферату: Зварювання кольорових металів Розділ, 29.07kb.
- Робоча програма загальні методичні вказівки та індивідуальні завдання до вивчення дисципліни, 156.9kb.
- Типова програма кандидатського іспиту із спеціальності, 95.6kb.
- Державна митна служба україни, 19.16kb.
4.2.2 Мінерали срібла
Як і золото, срібло зустрічається в природі в самородному стані. Однак значно частіше воно знаходиться у рудах у формі мінералів, що є хімічними сполуками, що обумовлене більшою хімічною активністю цього металу порівняно із золотом.
Відомо понад 60 мінералів срібла, які можна розділити на такі основні групи:
1) самородне срібло і природні сплави срібла із золотом (кюстеліт, електрум);
2) сульфіди, наприклад, аргентит Аg2S шромейєрит АgСuS;
3) сульфосолі, наприклад, піраргірит Аg3SbS3, прустит Аg3АsS3, стефаніт Аg5SbS4 та ін.;
4) антимоніди і арсеніди, наприклад, дискразит Аg3Sb;
5) телуриди і селиніди: гесит Аg2Те, науманит Аg2Sе, петцит Аg3АuТе2 та ін.;
6) галоїди і сульфати: кераргірит АgС1, аргентоярозит АgFе3(ВІН)6(SО4)2 та ін. Найважливішими мінералами срібла, що мають промислове значення, є самородне срібло і його природні сплави із золотом, аргентит, прустит, кераргірит. Крім того, срібло часто наявне в сульфідних рудах кольорових металів як домішка в галеніті РbS, бляклих рудах (ізоморфний ряд мінералів - сульфосолей із загальною формулою Сu12Х4S13, де X - Аs, Sb, в якому миш'як і сурма можуть ізоморфно заміщати один одного. Як домішка в бляклих рудах часто міститься срібло, що ізоморфно заміщає мідь) та інших мінералах.
4.2.3 Підготовка руд до добування срібла
У даний час срібло добувають з корінних руд або за допомогою гідрометалургійних процесів, або із застосуванням комбінованих схем, в яких велику роль виконують прийоми збагачення різними методами. Оскільки добута руда є великими шматками (до 500 мм, а іноді і крупніше), то її передусім дроблять і подрібнюють.
Задача цих операцій – повне або часткове розкриття зерен срібловмісних мінералів, в основному, частинок самородного срібла і приведення руди до стану, що забезпечує успішне проходження подальших збагачувальних і гідрометалургійних процесів.
Оскільки основний прийом добування срібла для більшості руд - гідрометалургійні операції, то необхідний ступінь подрібнення повинен забезпечити можливість контакту розчинів з розкритими зернами срібних мінералів. Достатність розкриття цих мінералів для даної руди звичайно визначається попередніми лабораторними технологічними випробуваннями щодо добування благородних металів. Для цього проби руди піддають технологічній обробці після різного ступеня подрібнення з одночасним визначенням добування срібла.
Економічно доцільний ступінь подрібнення встановлюють з урахуванням ряду факторів:
1) ступеня добування металу з руди;
2) зростання витрати реагентів при інтенсивнішому подрібненні;
3) витрат на додаткове подрібнення при доведенні руди до заданих розмірів;
4) погіршення згущуваності і фільтрованості тонкоподрібнених руд і пов'язаних з цим додаткових витрат на операції згущування і фільтрування.
Схеми дроблення і подрібнення варіюють залежно від речовинного складу руд і їх фізичних властивостей. Як правило, руду спочатку піддають великому і середньому дробленню в щічних і конусних дробарках з перевірочним грохоченням. Іноді застосовують третю стадію дрібного дроблення, здійснювану в короткоконусних дробарках. Після двостадійного дроблення звичайно одержують матеріал крупністю - 20 мм, після тристадійного крупність матеріалу іноді знижується до 6 мм.
Роздроблений матеріал надходить на мокре подрібнення, яке найчастіше здійснюють у кульових і стрижневих млинах. Руди звичайно подрібнюють у декілька стадій. Найбільшого поширення набуло двостадійне подрібнення, причому, для першої стадії вважають за краще використовувати стрижневі млини, які дають більш рівномірний за розмірами продукт з меншим його переподріб-ненням.
У даний час на золотодобувних підприємствах у циклі рудопідготовки значне поширення одержало рудне і рудно-галечне самоподрібнення. При рудному самоподрібненні подрібнювальним середовищем є некласифіковані за розмірами шматки самої подрібнюваної руди, передбачений тільки деякий контроль за верхнім розміром шматків. У разі рудно-галечного самоподрібнення подрібнювальним середовищем є спеціально виділена за розмірами і міцністю фракція шматків подрібнюваної руди (галька).
Рудне самоподрібнення здійснюється у повітряному або водному середовищі у спеціальних млинах, у яких порівняно із звичайними кульовими млинами співвідношення діаметра до довжини млина збільшене. Оскільки подрібнювальна дія шматків руди гірша, ніж сталевих куль, діаметр млинів самоподрібнення досягає 5,5-11,0 м.
Для сухого самоподрібнення застосовують млин Аерофол (рис. 4.2). Він має короткий барабан 1, встановлений на масивному фундаменті. На внутрішній поверхні барабана уздовж її твірної встановлені на деякій відстані одна від одної полиці 2 з двотаврових балок або рейок, які при обертанні барабана піднімають шматки руди. Падаючи, шматки дроблять руду, що знаходиться внизу, і, крім того, ударяючись об полиці при падінні, великі шматки розколюються. На торцевих кришках 3 барабани укріплені напрямними кільцями 4 трикутного перетину, призначення яких зводиться до спрямування шматків у середину барабана. Швидкість обертання млина становить 80-85% критичної.
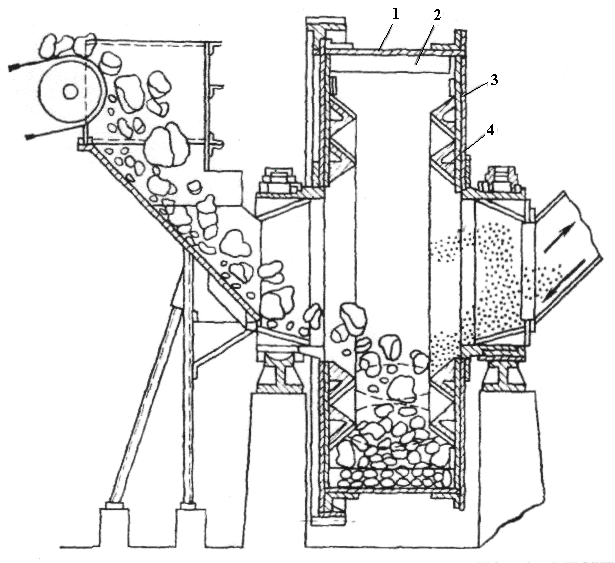
Рисунок 4.2 – Млин Аерофол для сухого самоподрібнення руди
Подрібнення руд у млинах Аерофол забезпечує отримання однорідного за розмірами продукту порівняно з подрібненням у звичайних кульових млинах. У млинах Аерофол знижується переподрібнення руди, що покращує фільтрованість і сгущуваність одержуваних пульп. Після подрібнення у цих млинах поліпшуються також показники гідрометалургійної обробки: знижується витрата реагентів (ціаніду) на 35%, підвищується добування срібла (до 4%). Сухе безкулькове подрібнення срібних руд у ряді випадків економічніше. Проте воно ставить жорсткі вимоги до вмісту вологи в руді (не більше 1,5-2 %). Підвищення вологості різко знижує ефективність процесів подрібнення і класифікації. Крім того, сухе подрібнення супроводжується великим пилоутворенням, що вимагає розвиненої системи пиловловлювання і погіршує умови праці. Тому поширенішим є самоподрібнення у водному середовищі.
Мокре рудне самоподрібнення здійснюється у млинах Каскад (рис. 4.3).
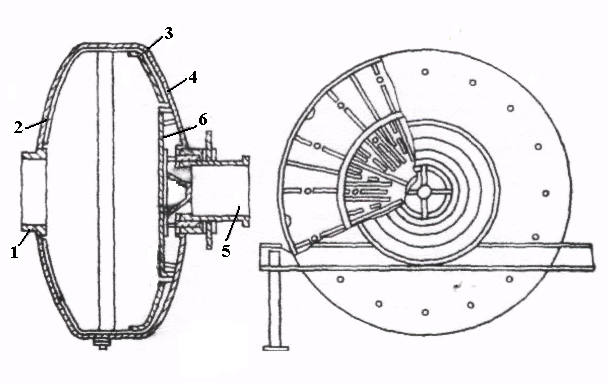
Рисунок 4.3 – Млин «Каскад» для мокрого самоподрібнення
Цей млин має короткий барабан 3 з конічними торцевими кришками 2 і 4. Пустотілими цапфами 1 і 5 барабан спирається на підшипники. Руда з млина розвантажується через гратки 6. Млини «Каскад» працюють у замкнутому циклі з механічним класифікатором або гідроциклонами. Рудно-галечне самоподрібнення здійснюється, як правило, у водному середовищі. Конструкції рудно-галечних і кульових млинів з розвантаженням через гратки схожі. Крупність рудної гальки, використовуваної як подрібнювальне середовище, визначається стадією подрібнення. На першій стадії подрібнення звичайно використовують гальки крупністю – 300+100 мм, на другий -100+25 мм. Відсівання гальки виконують на грохотах. Форма гальки для подрібнення не має значення. Для підвищення продуктивності млинів застосовують іноді довантаження куль (7-8 %), а також видалення уламків рудної гальки.
Застосування самоподрібнення при переробці срібловмісних руд має ряд суттєвих переваг порівняно із стандартними способами: 1) у ряді випадків дозволяє відмовитися від середнього і дрібного дроблення руди; 2) зменшує витрату сталі (куль, стрижнів) на подрібнення руди; 3) знижує витрату реагентів при подальшій переробці подрібненої руди; 4) зменшує питому витрату електроенергії; 5) підвищує продуктивність праці; 6) збільшує добування срібла.
Срібні руди перед гідрометалургійною обробкою або збагаченням флотацією знешламлюють, якщо шлами збіднені сріблом і негативно впливають на технологічні операції. Для знешламлювання використовують гідроциклони або згущувачі. Такими прийомами іноді віддаляється у відвал до 30-40 % різко збідненого матеріалу, що не тільки покращує технологічні показники, але і скорочує об'єм апаратури для проведення подальших операцій.
4.2.4 Сортування і первинне збагачення
великокускової руди
Звичайно у здобутій гірській масі разом із шматками срібловмісної руди знаходяться і шматки пустої породи, виключення якої з подальшої переробки може значно поліпшити техніко-економічні показники.
Для виведення пустої породи застосовують іноді ручне сортування. При цьому з гірської маси або видаляють пусту породу, або виділяють рудну фракцію, щоб збагатити сріблом. Загальним правилом сортування є те, що порода, що виводиться, за вмістом срібла не повинна бути багатше за хвости сріблодобувної фабрики.
Звичайно рудне сортування застосовують для матеріалу крупніше 40-50 мм.
Найбільш перспективне застосування збагачення у важких середовищах до сульфідних руд, в яких срібло пов'язане тільки з сульфідами, рівномірно розподілено, і його вміст у збагачувальній сировині, практично пропорційний вмісту сульфідів. Тому при збагаченні у важких середовищах срібло разом з сульфідами концентрується у важких фракціях; у легкі фракції відходять вмісні породи, майже не мінералізовані для цієї групи срібловмісних руд.
Одним з напрямів удосконалення процесу сортування є застосування автоматичного сортування, що базується на використанні відмінностей окремих шматків руди за кольором або радіоактивності (природної або наведеної). Сортування за кольором найбільш ефективне при великій контрастності кольорів срібловмісних мінералів і мінералів пустої породи, наприклад, при відділенні срібловмісного кварцу від сланців або озалізнених порід.
Однак автоматичне сортування вимагає складної дорогої апаратури, тому у промисловості до цього часу поширене мало.
4.2.5 Методи ціанування
Ціаністий процес увійшов до практики добувної промисловості в кінці минулого сторіччя, коли збагачувальної і гідрометалургійної апаратури ще не існувало. Вартість тонкого подрібнення у той час була висока, не були розроблені прийоми безперервного вилуговування, обезводнення і фільтрування великих мас тонкоподрібненого матеріалу. Тому в перший період розвитку ціаністого процесу використовували установки для обробки грубозернистого матеріалу методом просочування. Такий прийом обробки не допускав наявності у матеріалі глини, мулів і взагалі тонкодисперсних частинок. Тому перед вилуговуванням просочуванням подрібнену руду піддавали класифікації (відмулюванню) для відділення дрібних частинок (мулів). Зернисту частину (піски) обробляли методом просочування, а мули спрямовували у відвал або складували для обробки в майбутньому.
У міру вдосконалення гідрометалургійної апаратури (створення чанів з перемішуванням пульпи, фільтрів, згущувачів і т. д.) був впроваджений у практику і значно розширився процес так званого роздільного ціанування пісків і мулів. За цією схемою зернисту фракцію (піски) обробляли методом просочування (перколяцією), фракцію мулу – методом перемішування (агітацією).
З розвитком техніки подрібнення, згущування і фільтрування і з переходом до обробки руд з тонковкрапленим сріблом тонкому подрібненню сталі піддавати всю масу руди і вилуговували всю пульпу в чанах з інтенсивним перемішуванням. Такий процес називається повним мулом.
Ціанування просочуванням втратило своє минуле значення, і в даний час цей метод лише зрідка застосовують для добування золота і срібла із збіднених руд. Разом з тим останніми роками значно поширився метод купчастого вилуговування, що є, по суті, різновидом вилуговування просочуванням.
4.2.6 Купчасте вилуговування
За своєю сутністю процес купчастого вилуговування близький до процесу вилуговування просочуванням. Він полягає у тому, що руда, укладена у вигляді штабеля (купи) на спеціальній водонепроникній основі (майданчику) зрошується зверху ціаністим розчином. При повільному просочуванні розчину через шар руди відбувається вилуговування срібла. Стікаючий знизу розчин йде на осадження благородного металу.
Як і вилуговування просочуванням купчасте вилуговування придатне для переробки пористих проникних для ціаністого розчину руд, а також таких руд, в яких срібло сконцентроване в основному на внутрішній поверхні тріщин і тому доступно дії ціаністого розчину. Срібло в руді повинне бути досить дрібне.
Звичайно купчастому вилуговуванню піддають руду після дроблення до розмірів 5-20 мм. Однак інколи вилуговують і нероздроблену руду з розміром шматків до 100 мм і більше. Наявність глинистих речовин знижує проникність купи, сповільнює вилуговування і зменшує видобування срібла. У таких випадках рекомендується заздалегідь огрудковувати руду з невеликим додаванням цементу, ціаніду і лугу.
Процес купчастого вилуговування відрізняється простотою технологією, дуже низькими капітальними і експлуатаційними витратами. Разом з тим видобування срібла цим методом невисоке. З урахуванням цих факторів купчасте вилуговування застосовують для переробки збідненої сировини, що містить 1-2 г/т срібла, - забалансових руд, розкривних порід, старих відвалів підприємств і т.д. Застосування купчастого вилуговування економічно ефективне також для відпрацювання щодо багатих, але невеликих за запасами родовищ, для яких недоцільне будівництво фабрик.
З початку 70-х років установки для купчастого вилуговування набули значного поширення за кордоном і особливо у США. Це обумовлено тим, що у зв'язку з підвищенням цін на срібло до експлуатації стали залучати збіднену сировину і невеликі за запасами родовища, для яких купчасте вилуговування - найрентабельніший спосіб переробки.
4.2.7 Ціанування перемішуванням
Ціанування перемішуванням – значно ефективніший процес в порівнянні з ціануванням просочуванням. Це пояснюється хорошим розкриттям вилуговуваного срібла (внаслідок тонкого подрібнення руди), сприятливими умовами дифузійного підведення іонів CN~ і молекул розчиненого кисню до поверхні срібла (внаслідок інтенсивного перемішування), і енергійним накиснюванням пульпи у процесі вилуговування. Тому за швидкістю вилуговування і повнотою видобування срібла ціанування перемішуванням значно перевершує ціанування просочуванням і купчасте вилуговування. Необхідний ступінь подрібнення руди залежить від крупності срібла. У деяких випадках (при тонковкрапленому сріблі) руду піддають дуже тонкому подрібненню до -0,074 і навіть -0,043 мм. Але якщо характер вкрапленості срібла не вимагає такого подрібнення, то ціанують пульпу з грубо подрібненим матеріалом, наприклад, до -0,3 мм.
Після подрібнення одержувана пульпа (злив класифікатора) сильно розріджена (Ж : Т = 5 : 1 і вище), тому для скорочення: потрібного об'єму гідрометалургійної апаратури її заздалегідь згущують. Згущений продукт піддають ціануванню перемішуванням при Ж : Т = (1-2) : 1. Срібловмісний розчин відділяють декантацією або фільтруванням і спрямовують на осадження срібла. Хвости після промивання йдуть у відвал.
Тонке подрібнення руди і фільтрування пульпи мулоенергоємні операції. Тому ціанування перемішуванням вимагає значно вищої витрати енергії порівняно з ціануванням просочуванням і купчастим вилуговуванням.
Згущування – наступний після подрібнення етап обробки пульпи. Воно полягає в частковому обезводненні пульпи відстоюванням – осіданням твердих частинок на дно чана-згущувача і зливом освітленого розчину. У більшості випадків у матеріалі, що осів, залишається близько 50% води, що відповідає відношенню Ж:Т = 1:1. Межа згущування залежить від розмірів, щільності та фізико-хімічних властивостей подрібнених частинок оброблюваної руди. Частинки, що містяться в пульпі, звичайно сильно відрізняються за розмірами. Разом з порівняно великими зернистими частинками (понад 0.1 мм) у пульпі звичайно міститься значна кількість частинок розміром у декілька мікрон і навіть дрібніше (<0,001 мм). Більші частинки осідають швидше, дрібні протягом тривалого часу утримуються у зваженому стані.
Тонкі частинки рудних пульп, що за розмірами не належать до істинних колоїдів, часто є носіями колоїдних властивостей. Такі властивості проявляють глинисті речовини, шламові фракції сульфідних мінералів, багато окиснених мінералів важких металів та ін. Пептизація таких мінеральних частинок сильно утруднює процес згущування рудних пульп.
Як відомо, пептизація виникає у результаті адсорбції на поверхні колоїдних частинок іонів одного й того самого знака. У результаті цього частинки набувають однойменних зарядів, а у рідкій фазі залишається надлишок іонів протилежного знака. Однойменно заряджені частинки, відштовхуючись, залишаються в зваженому стані і не осідають. У цьому випадку для поліпшення відстоювання необхідно збільшити частинки в агрегаті (пластівці). Агрегація може бути досягнута коагуляцією електролітами або флокуляцією полімерами.
Для коагуляції в пульпу вводять електроліт, що утворює у розчині іони, які мають здатність адсорбуватися на
поверхні частинок і заряд, протилежний заряду спочатку адсорбованих іонів, що створюють стійкість системи. При введенні коагуляції заряди дисперсних частинок нейтралізуються, і під дією сил Ван-дер-Ваальса частинки злипаються у великі, швидко осідаючі агрегати. Як коагуляцію у ціаністому процесі використовують вапно, що одночасно виконує роль захисного лугу.
Для флокуляції в пульпу вводять який-небудь полімер, великі молекули (або міцели) якого адсорбуються на активних ділянках одночасно декількох твердих частинок, зв'язуючи їх за допомогою «містків», що утворюються, у великі агрегати («місткова» флокуляція).
На підприємствах найбільшого поширення набули безперервно-діючі одноярусні згущувачі з центральним приводом.
Згущувач (рис. 4.4) є невисоким циліндровим чаном 9 з плоским або злегка конічним днищем і кільцевим жолобом 8 близько верхнього краю. Чани великих згущувачів виготовляють з бетону, малих – із сталевих листів або дерева. У центрі згущувача знаходиться підвісний вертикальний вал 4, до похилих радіальних граблинам 3 якого прикріплені короткі гребки 2. Вал обертається від приводного механізму 6 і разом з ним закріплений на фермі 7. Щоб уникнути поломок при перевантаженнях, вал може підійматися (автоматично або вручну) за допомогою механізму 5. Згущувана пульпа безперервно надходить у завантажувальний стакан 10. Нижній край останнього заглиблений на 0,5-1 м по відношенню до рівня зливу, завдяки чому запобігає змулювання пульпи. Осідаючий на дно згущувача матеріал за допомогою гребків поступово переміщається до розвантажувального отвору 1, з якого відкачується діафрагмовим або відцентровим пісковим насосом. Окружна швидкість руху гребків невелика (0,1 м/с), тому переміщення гребків по дну апарата не порушує процесу відстоювання. Освітлена рідина переливається в кільцевий жолоб і по ньому відводиться із згущувача.
Продуктивність згущувача залежить не від його висоти, а від швидкості осадження і вільної поверхні апарата. Тому згущувачі мають велику площу при відносно малій висоті.
У ціанистому процесі при згущуванні пульп, 75-90% зерен, що містять, -0,074 мм, і при початковому Ж : Т у діапазоні від 9 : 1 до 4 : 1 питома площа згущування становить 0,4-0,6 м на 1 т твердого на добу.
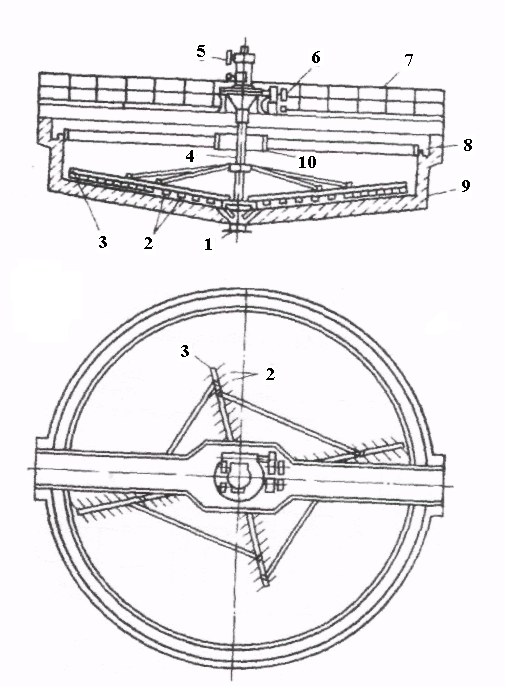
Рисунок 4.4 – Згущувач з центральним приводом
Перевагою згущувачів є безперервність дії, мала витрата електроенергії, простота конструкції і обслуговування. Основний недолік цих апаратів - - їх громіздкість і, отже, великий об'єм займаних виробничих площ. Тому, якщо дозволяють кліматичні умови, згущувачі встановлюють на відкритому повітрі.
Рудні пульпи, що надходять на ціанування перемішуванням, мають підвищену (в порівнянні з водними розчинами) в'язкість, що утруднює дифузію іонів СN- і молекул розчиненого кисню до поверхні серебрин, що розчиняються . Крім того, сульфідні мінерали, часто наявні в золотих рудах, досить легко окиснюються розчиненим киснем, внаслідок чого його концентрація в рідкій фазі пульпи може стати значно нижче рівноважної (при даній температурі і парціальному тиску кисню). Це також уповільнює розчинення золота. Тому при ціануванні тонкодисперсних пульп особливе значення має енергійне перемішування і безперервне насичення пульпи киснем повітря.
Процес проводять при концентрації NaСN, що становить 0,01-0,1% (частіше за все 0,02-0,05%) і концентрації СаО, що дорівнює 0,01-0,03% (рН 9-11). Ціаністі розчини неагресивні, тому для виготовлення обладнання застосовують такі доступні матеріали, як звичайна вуглецева сталь, чавун і т.п. Важливим параметром вилуговування є відношення Ж : Т в пульпі. Взагалі кажучи, доцільно проводити процес при мінімальному розрідженні пульпи, тому що при цьому потрібен мінімальний об'єм апаратури, скорочуються затрати на перемішування і фільтрування пульпи. Однак ціанування надмірно густих пульп проходить повільно і неповно внаслідок низької швидкості дифузії реагентів до поверхні золота. На практиці оптимальне відношення Ж : Т встановлюють емпірично, беручи до уваги перелічені фактори. Звичайно ціанування кварцових (кристалічних) руд проводять при Ж : Т = 1,2-(1,5:1). При ціануванні глинистих руд розрідження пульпи збільшують до Ж : Т = 2-(2,5 : 1).
Процес вилуговування здійснюють у періодичному або безперервному режимі. При ціануванні у періодичному режимі пульпу періодично окремими порціями закачують у паралельно працюючі апарати для вилуговування. Після перемішування протягом певного часу пульпу випускають або перекачують у чан-збірник, а у вилуговувальні апарати закачують нову порцію пульпи. У чані-збірнику вилуджена пульпа накопичується і підтримується у зваженому стані до надходження у подальшу стадію обробки (фільтрування). При безперервному вилуговуванні пульпа надходить у ланцюжок (каскад) з послідовно з’єднаних апаратів, де вона перемішується.
При малому числі апаратів значна частка частинок вилуговуваної руди «проскакує» всі апарати за час, недостатній для переведення всього срібла в розчин, а значна частина затримується у каскаді дуже довго, тобто довше, ніж необхідно для повного вилуговування срібла. І те, і інше небажане, тому що знижує видобування срібла і погіршує ефективність використання об'єму апаратури. Безперервно діюча система вилуговування звичайно з'єднується з безперервною системою відділення срібловмісного розчину.
Порівняно з періодичною безперервна система вилуговування має такі основні переваги: 1) можливість повної автоматизації; 2) менша кількість обслуговуючого персоналу; 3) ефективніше використання чанів (відсутні операції закачування і спорожнення); 4) менша потужність двигунів і насосів для перекачування пульпи. Тому в сучасній практиці у переважній більшості випадків застосовують схему безперервного вилуговування.
4.2.8 Афінаж срібла. Сировина і підготовка його до афінажу
Розділення срібла і отримання його у чистому вигляді здійснюють прийомами афінажу. Відомо декілька методів афінажу срібла. Найбільше поширення набули хлорний процес і електролітичне рафінування.
Афінаж здійснюють на спеціалізованих афінажних заводах. Сировина, що надходить сюди, відрізняється великою різноманітністю. Матеріали мають складний хімічний склад. Крім срібла, вони містять у вигляді домішок мідь, свинець, ртуть, миш'як, сурму, олово, вісмут та ін. елементи. Вміст домішок може досягати 200 проб і вище.
Срібло надходить, в основному, із заводів кольорової металургії у вигляді срібнозолотих сплавів (доре-метал), одержуваних при рафінуванні чорнового свинцю і переробці мідно-ектролітних шламів. Ці сплави звичайно містять 97-99 % суми срібла і золота.
Крім перелічених видів сировини, на афінажні заводи надходять також різного роду сплави, побутовий і технічний лом, монети і т.д.
В окремих видах сировини у помітних кількостях можуть бути наявними платинові метали.
Матеріали, що надходять на афінажний завод, піддають приймальному плавленню для усереднювання і випробування окремих партій сировини. Її проводять в графітних тиглях в електричних індукційних печах. На великих афінажних заводах застосовують печі потужністю до 100 кВт з місткістю тигля до 280 кг золота. Для зведення до мінімуму втрат благородних металів за рахунок випаровування плавлення проводять під шаром шлаку, використовуючи як флюс соду і буру (1,5-3% маси завантаженого металу). З цією ж метою уникають зайвого перегріву металу. Плавлення золотосрібних сплавів проводять при 1040-1060°С для срібла. Високопробне срібло, здатне до розбризкування при застиганні внаслідок виділення поглиненого кисню, плавлять під шаром деревного вугілля, що створює відновну атмосферу. Залежно від застосовуваного методу афінажу розплавлений метал розливають у зливки, що йдуть на афінаж хлоруванням, або в аноди, що надходять на електролітичне рафінування.
Відібрану пробу відливають у виливницю у вигляді тонкого зливка. Швидке охолоджування такого зливка забезпечує достатню однорідність сплаву. Пробу для аналізу відбирають у вигляді стружок або тирси. Результати аналізу необхідні для точного обліку кількості благородних металів, що надійшли в афінаж, і розрахунку з постачальниками.
4.2.9 Хлорний процес
Хлорний процес базується на тому, що неблагородні метали і срібло окиснюються газоподібним хлором значно легше, ніж золото. Сутність цього методу полягає у продуванні хлору через розплавлене чорнове золото. Хлор в першу чергу взаємодіє з неблагородними металами і сріблом, золото і метали платинової групи реагують в останню чергу. Розплавлені хлориди неблагородних металів і срібла, що утворюються, не розчиняються в металевому золоті і, маючи меншу щільність, спливають на поверхню. Частина хлоридів неблагородних металів випаровується.
Метал, що надходить на афінаж, містить 88-90% Аu і 7-11% Аg. Основні домішки – мідь, свинець, залізо, цинк.
Процес проводять у графітних тиглях з корундовим футеруванням в індукційних електричних печах. Чорновий метал, що пройшов приймальне плавлення, у вигляді зливків завантажують у поміщений у піч тигель місткістю 500 кг (щодо золота). Для утворення шлаку в тигель завантажують невелику кількість суміші бури, кварцу і хлористого натрію. Тонкий шар шлаку, що утворюється, зменшує випаровування металу і оберігає стінки тигля від роз'їдання. Після розплавлення металу через кришку тигля у розплав вводять одну або дві фарфорові трубки, по яких подають газоподібний хлор. Для кращої диспергації хлору в стінках трубки зроблені отвори. Процес проводять при 1150°С.
Першими хлоруються залізо, цинк, свинець. Низькокиплячі хлориди заліза і цинку переходять у газову фазу. Хлорид свинцю частково випаровується, частково спливає на поверхню металу. Випаровування хлоридів викликає інтенсивне бурління розплаву, тому подачу хлору в цей період проводять повільно.
Мідь і срібло починають реагувати з хлором лише після того, як прохлорується основна маса заліза, цинку і свинцю. Температура кипіння АgС1 і СuСІ вища за температуру ведення процесу, тому хлориди срібла і міді залишаються у тиглі, утворюючи шар розплавлених хлоридів на поверхні золота. З огляду на те, що хлориди не випаровуються, подачу хлору в цей період можна збільшити, не побоюючись розбризкування розплаву.
Розплавлені хлориди, що накопичуються на поверхні металу, а також шлак періодично видаляють з тигля і завантажують нову порцію флюсу. До кінця процесу абсорбція хлору розплавом сповільнюється, тому швидкість подачі хлору зменшують. Кінець процесу визначають при появі жовтого нальоту золота на трубках, що підводять хлор, і при появі над розплавом червоного диму, забарвлення якого пояснюється наявністю в ньому хлориду золота. Після закінчення хлорування з поверхні металу видаляють залишки хлоридів і шлаку.
Розплав розшаровується на шар шлаку (зверху) і шар хлоридів. На поверхню розплаву окремими невеликими порціями завантажують соду, при цьому частина срібла відновлюється:
4АgС1 + 2N2СО3 = 4Аg + 4NаС1 + 2СО2 + О2 (4.16)
і, опускаючись у вигляді дрібних крапель на дно тигля, захоплює велику частину золота, що знаходиться у хлоридах.
Загальна кількість соди, що вводиться, становить близько 4% маси хлоридів, при цьому відновлюється приблизно п'ята частина срібла, що міститься у хлоридах, що забезпечує високий ступінь видобування золота. Одержаний срібнозолотий сплав знову надходить на хлорування разом з новою партією золота. Знезолочені хлориди служать сировиною для отримання срібла. Вони містять до 70% хлориду срібла, інше – хлориди міді, натрію, свинцю. Переробка хлоридів може здійснюватися різними методами. По одному з них хлориди дроблять до крупності 25 мм і багато разів обробляють в бочках, що обертаються, гарячим 5% розчином NаС1, що підкиснює соляною кислотою. Хлориди натрію і свинцю переходять в розчин; наявність в розчині іонів С1 сприяє вилуговуванню малорозчинного у воді хлориду СuС1.
Хлорид срібла, що залишається у нерозчинному залишку, відновлюють до металу за допомогою металевого заліза або цинку.
Отримане губчасте срібло після промивання і сушіння переплавляють в аноди для подальшого електролітичного рафінування. Чистота металу в анодах - 998-999 проб.
До недоліків хлорного методу афінажу слід віднести суттєві втрати срібла і платинових металів.
4.2.10 Електролітичне рафінування срібла
Електролітичні методи афінажу найбільш досконалі і дозволяють одержувати метали високої чистоти при комплексному використанні всіх цінних компонентів, що входять до складу рафінувального металу.
При електролітичному рафінуванні срібло як розчинний анод використовує срібний рафінувальний сплав. Електролітом служить водний розчин азотно-кислого срібла з додаванням невеликої кількості азотної кислоти.
Наявність її збільшує електропровідність електроліту і відповідно зменшує витрату електроенергії. Разом з тим, надмірно висока концентрація азотної кислоти небажана, оскільки при цьому швидшає процес хімічного розчинення катодного срібла суттєвого розвитку набувають процеси катодного відновлення аніонів
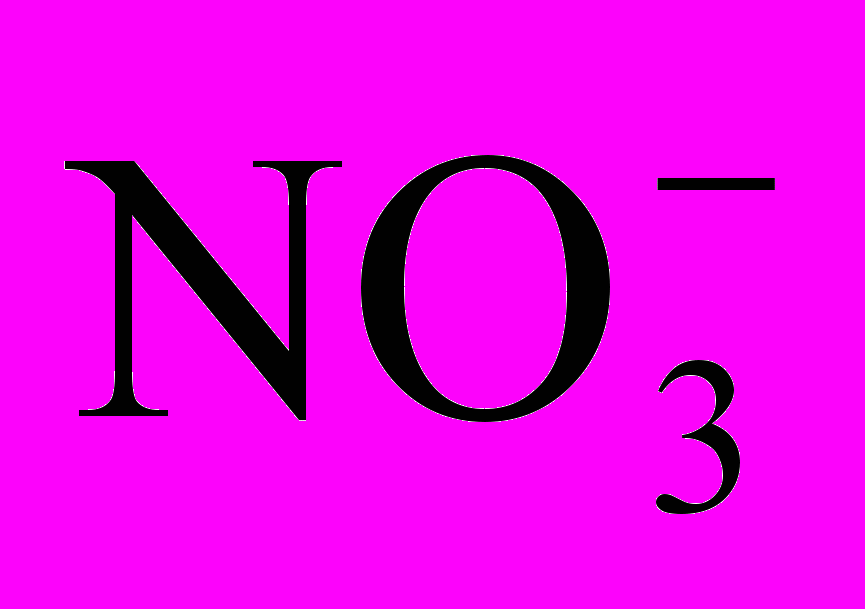
У анодах, крім срібла, як домішки завжди містяться золото, метали платинової групи і неблагородні метали – мідь, свинець, вісмут, цинк, залізо і т.д.
Електроліз срібла звичайно проводять в прямокутних ваннах, виготовлених з вініпласту або полівінілхлориду, і поміщених у каркас з дерева, фібергласу і т.д. (рис. 4.5). Місткість однієї ванни становить звичайно 300-600 л.
На анодній штанзі підвішують від одного до трьох анодів. Катод звичайно роблять один на всю ширину ванни. Як катоди застосовують тонкі листи корозійностійкої сталі, титану, алюмінію або срібла.
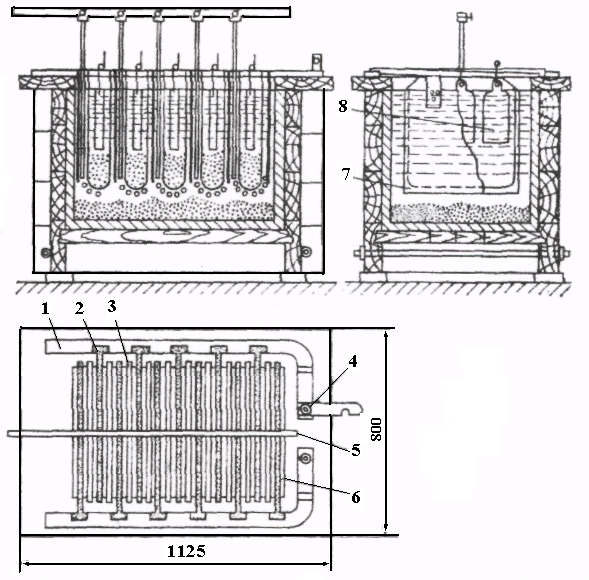
Рисунок 4.5 – Ванна для електролізу срібла з вертикальними електродами: 1 – шина; 2 – катодні штанги; 3 – чохли; 4 – вимикач; 5 – повітряна труба з відведеннями для перемішування; 6 – анодні штанги; 7 – катод; 8 – анод
Силові лінії при електролізі розподіляються нерівномірно, концентруючись в нижній частині електродів. Тому нижня частина анодів розчиняється швидше за верхній. Щоб уникнути цього, аноди інколи відливають потовщеними донизу. Для кращого контакту із струмопідвідними шинами і зниження виходу анодних залишків зручно користуватися суцільними анодами, відлитими разом з вушками для підвішування у ванну. Аноди масою до 10 кг розраховані на розчинення протягом 2-3 діб.
Процес електролізу проводять цілодобово. Срібло осідає на катоді у вигляді великокристалічного, нещільно пристає до катода осаду. Кристали срібла ростуть у напрямі до анода, прагнучи замкнути електроди. Тому їх періодично зчищають вручну лопатками або безперервно механічними шкрябаннями. Електроліт перемішують або за допомогою стиснутого повітря, що подається у ванну по вініпластових або скляних трубках, або механічними шкрябаннями одночасно із зняттям катодного осаду. Кристали срібла, що впали на дно ванни, періодично витягують дірчастими совками з алюмінію. Інколи одну з бокових стінок ванни роблять похилою і по ній скребком вигрібають катодне срібло. Застосовують і інші методи розвантаження, зокрема, безперервне механічне розвантаження за допомогою транспортера зі стрічкою з полотна.
Щоб уникнути забруднення катодного срібла анодним шламом, аноди поміщають у чохли з хлорвінілової, териленової або іншої тканини. При розчиненні анода шлам збирається усередині чохла, звідки його періодично вивантажують.
Очевидно, що оскільки на катоді осідає тільки срібло, а на аноді розчиняються срібло і домішки, катодний вихід по струму помітно перевищує анодний. Це призводить до того, що електроліт протягом електролізу поступово обідняється сріблом і збагачується домішками. Відпрацьований електроліт виводять з ванн, замінюючи на свіжий.
При виборі густина струму виходить з умови отримання чистих катодних опадів. При високій густині струму унаслідок підвищеної анодної поляризації посилюється перехід платинових металів у розчин, а, отже, і їх осадження на катоді. Одночасно унаслідок поляризації катода можуть створюватися умови для відновлення на ньому міді і телуру. Практично процес проводять при густині струму від 200 до 600 А/м , при цьому чим брудніші аноди, тим нижча застосовувана густина струму. Температура електроліту за рахунок тепла, що виділяється при проходженні струму, становить 30-50°С.
Катодний вихід по струму при нормальному веденні процесу становить 94-96%, напруга на ванні 1-2,5 В. Витрати електроенергії коливаються від 0,3 до 0,6 кВт·тод на 1 кг афшованого срібла.
Срібло, вивантажене з ванн, промивають послідовно розбавленою азотною кислотою і гарячою водою, пресують для видалення вологи і плавлять в електричних високочастотних печах у зливки. Чистота катодного срібла після переплавлення становить 999,7-999,9 проб.
Перевагою процесу електролітичного рафінування срібла є не тільки можливість отримання високочистого металу, що задовольняє вимоги сучасної техніки, але і попутне видобування платинових металів, що втрачаються при афінажі хлоруванням.
4.2.11 Кислотні методи афінажу
Ці методи полягають в обробці сплавів благородних металів різними кислотами, причому домішки і один з благородних металів переходять у розчин, а другий залишається у нерозчинному залишку.
Спосіб очищення за допомогою азотної кислоти базується на виборчому розчиненні срібла. Для повного розділення металів необхідно, щоб вміст срібла в сплаві щонайменше в два (а краще в три) рази перевищував вміст золота. При цій умові обробка сплаву гарячою азотною кислотою дозволяє без остачі перевести срібло у розчин, а золото залишити у нерозчинному залишку. Такі домішки, як мідь, свинець, платина і паладій, також переходять в розчин. Якщо в сплаві наявні олово, сурма або миш'як, то його слід заздалегідь переплавити з селітрою або піддати купелюванню для відділення цих елементів.
Срібло, що перейшло в розчин, осаджують у вигляді хлориду, відновлюють металевим залізом або цинком і переплавляють у зливки.
Кислотні методи афінажу громіздкі, дорогі і не дозволяють отримувати благородні метали того ступеня чистоти, який необхідний для сучасної промисловості. Через ці недоліки кислотні методи в даний час застосовуються обмежено. Іноді їх використовують для попереднього розділення благородних металів перед остаточним афінажем їх електролітичним методом.
4.2.12 Застосування срібла
Срібло має чудові технологічні властивості, завдяки яким його широко застосовують у промисловості. Срібло відрізняється найширшою серед металів електро- і теплопровідністю, що поєднується з низькою хімічною активністю, пластичністю, великою відбивною здатністю. Дуже цінні властивості мають деякі сполуки срібла.
На відміну від золота, основну масу якого використовують у ювелірній і пов'язаній з нею галузях промисловості, срібло в основному витрачають на чисто технічні цілі.
Найважливішою сферою споживання срібла є виробництва світлочутливих матеріалів для кіно- і фотопромисловості. Витрата срібла на виробництво кіно- і фотоматеріалів неухильно зростає, однак, незважаючи на всі зусилля учених, повноцінних замінників срібла для цих цілей поки не знайдено.
Значними сферами застосування срібла є електротехніка і електроніка, де висока електропровідність срібла в поєднанні з хімічною стійкістю зумовили широке використання його для виготовлення контактів і провідників.
Значна кількість срібла витрачається на виготовлення припоїв для паяння різних металів і сплавів. Срібні припої дають міцні і пластичні спаї, що протистоять ударам і вібрації. Стійкість до окиснення зумовила широке застосування срібних припоїв в авіаційній і космічній техніці, а хороша електропровідність – в електротехніці.
Високі розрядні характеристики мають срібно-цинкові і срібно-кадмієві акумулятори, застосовувані в ракетній техніці, підводному флоті і т.д. Мініатюрні батареї, що містять хлорид срібла, використовують в електронних наручних годинниках, кінокамерах, калькуляторах.
Із сплаву срібла з кадмієм і індієм виготовляють регулюючі стрижні в ядерній техніці.
Срібло застосовують також для виробництва антифрикційних сплавів, нанесення покриттів, в медицині і т.д. Давно відомі бактерицидні властивості срібла, завдяки яким цей метал застосовують в установках знезараження питної води. Каталітичні властивості срібла і його сполук необхідні в сучасній хімії при отриманні ряду речовин.
Традиційною сферою застосування срібла є виробництво прикрас, столового посуду, пам'ятних медалей, предметів колекціонування і т.д.