О. Й. Любич, В. О. Пчелінцев Фізичні основи металургії кольорових І рідкоземельних металів
Вид материала | Документы |
- З дисципліни «Теоретичні основи ливарного виробництва» для студентів заочного факультету, 390.98kb.
- Програма, методичні вказівки та контрольні завдання з дисципліни " виробництво виливків, 797.9kb.
- Нова технологія утилізації гальваношламів машинобудівних підприємств з одержанням комплексних, 26.76kb.
- І містять у собі чорні або кольорові метали чи їх сплави, а також вироби з металу,, 462.13kb.
- Наказом Державного комітету України з питань регуляторної політики та підприємництва,, 341.66kb.
- Розробка базових теплотехнічних І конструктивних рішень, а також технологічних схем, 24.73kb.
- Назва реферату: Зварювання кольорових металів Розділ, 29.07kb.
- Робоча програма загальні методичні вказівки та індивідуальні завдання до вивчення дисципліни, 156.9kb.
- Типова програма кандидатського іспиту із спеціальності, 95.6kb.
- Державна митна служба україни, 19.16kb.
Тестові питання
1. Які породи можуть служити рудами алюмінію?
2. З яких основних стадій складається технологічний процес отримання алюмінію?
3. Які використовуються способи отримання глинозему?
4. За якою схемою отримуємо окис алюмінію за способом Байєра?
5. Які типи анодів застосовують при електролізі окислу алюмінію?
6. У чому полягає метод відновлення хлориду алюмінію марганцем?
7. У чому полягає сутність рафінування алюмінію методом тришарового електролізу?
8. Яким чином можна отримати високу чистоту алюмінію – номінально до Аl99,99999?
9. З яких стадій складається електротермічний спосіб отримання алюмінієво-кремнієвих сплавів?
10. Що входить до складу електролізу промислових алюмінієвих електролізерів?
11. Для чого первинний алюміній з електролізу передають у ливарне відділення?
12. Який вміст натрію не повинен перевищувати у первинному алюмінію?
13. Яким чином визначається чистота алюмінію, рафінованого за тришаровим методом?
14. У чому полягає принцип зонної плавки алюмінію?
15. Скільки каскадів зонної плавки є оптимальними?
16. Що є сировиною для отримання титану?
17. Яким чином проводять хлорування титанового шлаку?
18. При якій температурі плавиться тетрахлорид титану?
19. За якою реакцією відновлюється титан з чотирихлористого титану?
20. На якій установці проводять плавку титанової губки?
21. Якої чистоти отримують титан після переплавлення губки?
22. Які магнієві мінерали знаходяться у земній корі?
23. Які мінерали служать сировиною для отримання магнію?
24. Який основний спосіб отримання магнію?
25. Які солі застосовують для електроліту при отриманні магнію?
26. Яким чином видаляють магній з електролізера?
27. На чому ґрунтується карботермічний спосіб отримання магнію?
28. Чому картометрічний спосіб отримання не може конкурувати з електролітичним?
29. Яким чином проводять рафінування магнію?
30. Як проводять глибоке очищення магнію?
3 ФІЗИКО-МЕТАЛУРГІЙНІ ОСНОВИ
ВИРОБНИЦТВА ВАЖКИХ МЕТАЛІВ
3.1 Фізико-металургійні основи виробництва міді
3.1.1 Основи виробництва міді
Для отримання міді застосовують мідні руди, а також відходи міді та її сплавів. У рудах міститься 1-6% міді.
У рудах мідь звичайно знаходиться у вигляді сірчистих сполук (мідний колчедан або халькопірит CuFeS2, халькозин Cu2S, ковелін CuS), оксидів (куприт Сu2О, тенорит СuО) або гідрокарбонатів (малахіт СuСО3·Сu(ОН2), азурит 2СuСО3·Сu(ОН)2).
Порожня порода складається з піриту FeS, кварцу SiO2, карбонатів магнію і кальцію (МgСО3 і СаСО3), а також з різних силікатів, що містять AI2O3, CaO, MgO і оксиди заліза.
У рудах іноді міститься значна кількість інших металів: цинк, олово, нікель, золото, срібло, кремній та інші.
Руда ділиться на сульфідні, окислені і змішані. Сульфідні руди бувають звичайно первинного походження, а окислені руди утворилися у результаті окиснення металів сульфідних руд.
У невеликих кількостях зустрічаються так звані самородні руди, в яких мідь знаходиться у вільному вигляді.
Відомі два способи витягання міді з руд і концентратів: гідрометалургійний і пірометалургійній.
Перший з них не знайшов широкого застосування. Його використовують при переробці бідних окиснених і самородних руд. Цей спосіб на відміну від пірометалургійного не дозволяє добувати попутно з міддю дорогоцінні метали.
Другий спосіб придатний для переробки всіх руд і особливо ефективний у тому випадку, коли руди піддаються збагаченню.
Основу цього процесу становить плавка, при якій розплавлена маса розділяється на два рідкі шари: штейн-сплав сульфідів і шлак-сплав оксидів. У плавку надходять або мідна руда, або обпалені концентрати мідних руд. Випалення концентратів здійснюється з метою зниження вмісту сірки до оптимальних значень.
Рідкий штейн продувають в конвертерах повітрям для окиснення сірчистого заліза, перекладання заліза в шлак і виділення чорнової міді.
Чорнову мідь далі піддають рафінуванню - очищенню від домішок.
3.1.2 Підготовка руд до плавлення
Більшість мідних руд збагачують способом флотації. У результаті одержують мідний концентрат, що містить 8-35% Сі, 40-50% S, 30-35% Fe і пусту породу, головним чином складовою якої є SiO2, А12О3 і СаО.
Концентрати звичайно обпалюють у окиснювальному середовищі для того, щоб видалити близько 50% сірки і одержати обпалений концентрат із вмістом сірки, необхідним для отримання при плавці достатньо багато штейну.
Обпалюють концентрат при 750-850°С у повітряній атмосфері з метою окиснення сульфідів і зменшення вмісту сірки.
Прогресивним є випалення в киплячому шарі. Подрібнений концентрат завантажується у піч (рис. 3.1) через вікно 3. Знизу в піч по каналу 2 і отвори в піддоні подається повітря. Тиск повітря встановлюється таким, щоб частинки концентрату знаходилися у зваженому («киплячому») стані. Обпалений концентрат «переливається» через поріг 5 печі у вигляді недогарка. Сірчисті гази, що відходять, очищаються в циклонах 4 і спрямовують у сірчанокислотне виробництво.
Випалення забезпечує добре змішування всіх компонентів шихти і нагрівання її до високої температури, знижує витрату палива у відбивній печі в два рази. Проте при переплавленні обпаленої шихти дещо зростають втрати
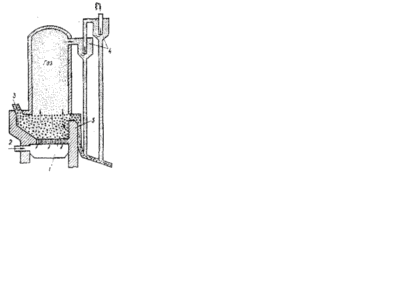
Рисунок 3.1 – Схема печі для випалення концентрату
міді в шлаку і віднесення пилу. Тому звичайно багаті мідні концентрати (25-35% Сu) плавлять без випалення, а бідні (8-25% Сu) піддають випаленню.
3.1.3 Виплавка мідного штейну
Мідний штейн, що складається в основному з сульфідів міді і заліза (Cu2S+FeS=80-90%) та інших сульфідів, а також оксидів заліза, кремнію, алюмінію і кальцію, виплавляють у печах різного типу.
Комплексні руди, що містять золото, срібло, селен і телур, доцільно збагатити так, щоб в концентрат була переведена не тільки мідь, але й ці метали. Концентрат переплавляють у штейн у відбивних або електричних печах.
Сірчисті, чисто мідні руди доцільно переробляти у шахтних печах.
При високому вмісті сірки в рудах доцільно застосовувати так званий процес мідно-сірчаного плавлення у шахтній печі з уловлюванням газів і витяганням з них елементарної сірки.
У піч завантажують мідну руду, вапняк, кокс і оборотні продукти. Завантаження проводять окремими порціями сирих матеріалів і коксу.
У верхніх горизонтах шахти створюється відновне середовище, а в нижній частині печі - окиснювальне. Нижні шари шихти плавляться, і вона поступово опускається вниз назустріч потоку гарячих газів. Температура у фурм досягається 1500°С на верху печі вона дорівнює приблизно 450°С.
Така висока температура газів, що відходять, необхідна для того, щоб забезпечити можливість із очищення від пилу до початку конденсації пари сірки.
У нижній частині печі, головним чином біля фурм, проходять такі основні процеси:
а) спалювання вуглецю коксу
С + О2 = СО2 ; (3.1)
б) спалювання сірки сірчистого заліза
2FeS + 3O2 = 2FeO + 2SO2; (3.2)
в) утворення силікату заліза
2 FeO + SiO2 = (FeO)2 · SiO2. (3.3)
Гази, що містять СО2, SO2, надлишок кисню і азот, проходять вгору через стовп шихти. На цьому шляху газів відбувається теплообмін між шихтою і ними, а також взаємодія СО2 з вуглецем шихти. При високих температурах СО2 і SO2 відновлюються вуглецем коксу при цьому утворюються окисел вуглецю, сірковуглець і сіркоокис вуглецю:
СО2 + С = 2СО, (3.4)
2SO2 + 5С = 4СО + CS2, (3.5)
SO2 + 2С = COS + CO. (3.6)
У верхніх горизонтах печі пірит розкладається за реакцією:
FeS2 = Fe + S2. (3.7)
При температурі близько 1000°С плавляться найбільш легкоплавкі евтектики з FeS і Cu2S, внаслідок чого утворюється пориста маса.
У порах цієї маси розплавлений потік сульфідів зустрічається з висхідним потоком гарячих газів і при цьому проходять хімічні реакції, найважливіші з яких показані нижче:
а) утворення сульфіду міді із закису міді:
2Cu2O + 2FeS + SiO2 = (FeO)2 · SiO2 + 2Cu2S; (3.8)
б) утворення силікатів з оксидів заліза:
3Fe2O3 + FeS + 3,5SiO2 = 3,5(2FeO · SiO2)+ SO2; (3.9)
3Fe3O4 + FeS + 5SiO2 = 5(2FeO · SiO2)+ SO2; (3.10)
в) розкладання СаСО3 і утворення силікату:
СаСО3 + SiO2 = СаО · SiO2 + СО2; (3.11)
г) відновлення сірчистого газу до елементарної сірки
SO2 + С = СО2 + 1/2S2. (3.12)
У результаті плавлення виходять штейн, що містить 8-15% Сu, шлак, що складається в основному із силікатів заліза і вапна, колошниковий газ, що містить S2, COS, H2S, і СО2. З газу спочатку осаджують пил, потім з нього витягують сірку (до 80% S). Щоб підвищити вміст міді у штейні, його піддають скорочувальному плавленню. Плавлення здійснюють у таких самих шахтних печах. Штейн завантажують шматками розміром 30-100 мм разом із кварцовим флюсом, вапняком і коксом. Витрата коксу становить 7-8% від маси шихти. У результаті одержують збагачений міддю штейн (25-40% Сu) і шлак (0,4-0,8% Сu).
Для переплавки концентратів, як вже зазначалося, застосовують відбивні і електричні печі. Іноді обпалювальні печі розміщують безпосередньо над майданчиком відбивних печей для того, щоб не охолоджувати обпалені концентрати і використовувати їх тепло.
У міру нагрівання шихти в печі проходять такі реакції відновлення окислу міді і вищих оксидів заліза:
6CuO + FeS = 3Cu2O + SO2 + FeO; (3.13)
FeS + 3Fe3O4 + 5SiO2 = 5(2FeO·SiO2)+ SO2. (3.14)
У результаті реакції закису міді Cu2O, що утворюється, з FeS виходить Cu2S:
Cu2O + FeS = Cu2S + FeO. (3.15)
Сульфіди міді і заліза, сплавляючись між собою, утворюють первинний штейн, а розплавлені силікати заліза, стікаючи по поверхні укосів, розчиняють інші оксиди і утворюють шлак.
Благородні метали (золото і срібло) погано розчиняються в шлаку і практично майже повністю переходять в штейн.
Штейн виплавлення на 80-90% (за масою) складається з сульфідів міді і заліза. Він містить, %: 15-55 міді; 15-50 заліза; 20-30 сірки; 0,5-1,5 SiO2; 0,5-3,0 Al2O3; 0.5-2.0 (СаО + МgО); близько 2% Zn і невелику кількість золота і срібла. Шлак складається в основному з SiO2, FeO, СаО, Al2O3 і містить 0,1-0,5% міді. Добування міді і благородних металів у штейн досягає 96-99%.
3.1.4 Конвертація мідного штейну
У 1866 р. російський інженер Р.С.Семенніков запропонував застосувати конвертер типу бесемерівського для продування штейну. Продування штейну знизу повітрям забезпечило отримання лише напівсірчистої міді (близько 79% міді) - так званого білого штейну. Подальше продування призводило до затвердіння міді. У 1880 р. був запропонований конвертер для продування штейну з бічним дуттям, що і дозволило одержати чорнову мідь у конвертерах.
Чорнову мідь одержують при продуванні розплавленого штейну повітрям у конверторі – горизонтально розміщеній циліндричній посудині з листової сталі завдовжки 5-10 і діаметром 3-4 м, футерованому магнезитовою цеглою 2 (рис. 3.2). Повітряне дуття підводиться по трубах 3 і подається всередину конвертора через 40-50 фурм 4, розташованих на його твірній. Для заливки штейну в горловину і виплавлення продуктів плавлення конвертор повертають на роликах 5.
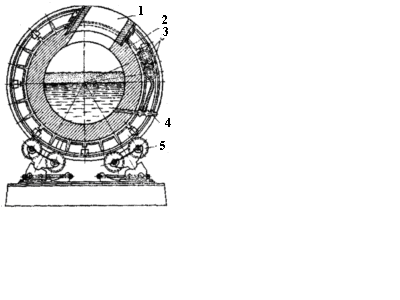
Рисунок 3.2 – Схема конвертора для отримання чорнової міді
Продуктивність за одну операцію становить 80-100 т. Футерують конвертор магнезитовою цеглою. Заливку розплавленого штейну і злив продуктів здійснюють через горловину конвертора, розміщену в середній частині його корпусу. Через ту саму горловину видаляють гази. Фурми для вдування повітря розташовані по поверхні твірної конвертора. Число фурм звичайно становить 46-52, а діаметр фурми - 50мм. Витрата повітря досягає 800 м2/хв. У конвертор заливають штейн і подають кварцовий флюс, що містить 70-80% SiO2, і звичайно деяку кількість золота. Його подають під час плавки, користуючись пневматичним завантаженням через круглий отвір в торцевій стінці конверторів, або ж завантажують через горловину конвертора.
Процес можна розділити на два періоди. Перший період (окиснення сульфіду заліза з отриманням білого штейну) триває від 624 годин залежно від вмісту міді в штейні. Завантаження кварцового флюсу починають з початку продування. У міру накопичення шлаку його частково видаляють і заливають в конвертор нову порцію початкового штейну, підтримуючи певний рівень штейну в конверторі.
У першому періоді проходять такі реакції окиснення сульфідів:
2FeS + 3О2 = 2FeO + 2SO2 + 930360 Дж, (3.16)
2Cu2S + 3O2 = 2Cu2O + 2SO2 + 765600 Дж. (3.17)
Поки існує FeS, закис міді не стійкий і перетворюється на сульфід:
Cu2O + FeS = Cu2S + FeO. (3.18)
Закис заліза шлакується кварцовим флюсом, що додається у конвертор:
2FeO + SiO2 = (FeO) · SiO2. (3.19)
При нестачі SiO2 закис заліза окиснюється до магнетиту, який переходить в шлак 6FeO + О2 = 2Fe3O4.
Температура заливається штейну в результаті проходження цих екзотермічних реакцій підвищується з 1100-1200 до 1250-1350°С . Вища температура небажана, і тому при продуванні бідних штейнів, що містять багато FeS, додають охолоджувачі твердий – штейн, сплески міді.
З попереднього випливає, що у конверторі залишається головним чином так званий білий штейн, що складається з сульфідів міді, а шлак зливається в процесі плавки. Він складається в основному з різних оксидів заліза (магнетиту, закису заліза) і кремнезему, а також з невеликих кількостей глинозему, окислу кальцію і окислу магнію. У шлаку залишається 1,8-3,0% міді. Для її добування шлак в рідкому вигляді спрямовують у відбивну піч або в сурму шахтної печі.
У другому періоді, названому реакційним, тривалість якого становить 2-3 години, з білого штейну утворюється чорнова мідь. У цей період окиснюється сульфід міді і за обмінною реакцією виділяється мідь:
2Cu2S + 3О2 = 2Cu2O + 2SO2Cu2S + 2Cu2O = 6Cu + O2.
Таким чином, у результаті продування одержують чорнову мідь, що містить 98,4-99,4% міді, 0,01-0,04% заліза, 0,02-0,1% сірки, і невелику кількість нікелю, олова, миш'яку, срібла, золота і конверторного шлаку, що містить 22-30% SiO2, 47-70% FeO, близько 3% Al2O3 і 1.5-2.5% міді.
Для отримання міді необхідної чистоти чорнову мідь піддають вогняному і електролітичному рафінуванню і при цьому, крім видалення шкідливих домішок, можна добути також благородні метали. Вогняне рафінування чорнової міді проводять у печах, що нагадують відбивні печі, використовувані для виплавлення штейну з мідних концентратів. Електроліз проводять у ваннах, футерованих всередині свинцем або вінілпластом.
Вогняне рафінування полягає в окисненні домішок у відбивних печах при продуванні чорнової міді повітрям; при цьому кисень повітря з'єднується з міддю і утворює оксид Сu2О, який потім реагує з домішками металів (Me) за реакцією
Me + Сu2О = МеО + 2Сu. (3.20)
Одночасно окиснюється і сірка:
Cu2S + 2Cu2O = 6Cu + SO2. (3.21)
Після цього розпочинають розкиснення міді – відновлення Cu2O. Для цього мідь перемішують дерев'яними жердинами. Бурхливе виділення пари води і вуглеводнів сприяє видаленню газів і відновленню міді:
4Сu2О + СН4 = 8Сu + 2Н20 + СО2.
Після вогняного рафінування чистота міді досягає 99.99,5%. Електролітичне рафінування застосовують для отримання міді чистотою до 93,95%. Електроліз проводять у спеціальних ваннах. Анодами служать пластини з чорнової міді розміром 1х1 м і завтовшки 59 мм, катодами – листи завтовшки 0,5 мм з чистої міді, електролітом – водний розчин сірчаної кислоти і сірчанокислої міді. При проходженні струму напругою 2-3 В і густиною 100-400 А/м анод розчиняється, мідь переходить в розчин у вигляді катіонів, які потім розряджаються на катодах і відкладаються шаром чистої міді. При цьому домішки осідають на дно ванни у вигляді шламу. Іноді в шламі містяться до 35% Ag, 6% Se, 3% Fе, 1% Аu та інші цінні елементи. Тому шлами звичайно переробляють з метою добування цих елементів.
3.1.5 Нові методи добування міді
Останнім часом став швидко поширюватися метод видобутку міді за допомогою підземного вилуговування руди. Нова технологія збагачення мідної руди не вимагає її добування на поверхню і тому відрізняється високою економічною ефективністю. Переваги нової технології полягають у тому, що основні процеси перенесені під землю і відбуваються без участі людини, що різко підвищує ефективність виробництва. Традиційний дорогий процес замінений технологією, що базується на використовуванні слабких розчинів кислот, які ще під землею вступають у реакцію з рудою і збагачуються міддю.
Далі концентрований розчин підіймається на поверхню через систему відкачуваних свердловин, де чиста мідь виділяється з нього за допомогою технології екстракції міді з розчину за допомогою органічних реагентів. Виробничий цикл замкнений: після екстракції міді водний розчин знову збагачується кислотою і знову закінчується у гідротехнологічному полі.
3.2 Фізико-металургійні основи виробництва
нікелю
3.2.1 Сировина для отримання нікелю
Для виробництва нікелю застосовують сульфідні і окиснені руди. У сульфідних рудах нікель представлений головним чином ізоморфною сумішшю сульфідів заліза і нікелю (Ni, Fe)S, а пуста порода складається з силікатів заліза і магнію, піротину Fe7S8 та інших сполук. У цих рудах міститься 0,3-5,5% Ni і до 2,5 Cu, тому їх називають мідно-нікелевими. У рудах часто наявний кобальт (до 0,2 %), а також у невеликих кількостях метали платинової групи: платина, осмій, іридій, радій, рутеній і паладій.
Мідно-нікелеві руди збагачують флотаційними способами. Інколи отримують мідно-нікелевий концентрат, а інколи проводять селективне збагачення з виділенням двох концентратів – нікелевого і мідного. Проте отримати нікелевий концентрат, добре очищений від міді, не вдається, тому збагачення мідно-нікелевих руд проводять не за селективною схемою, а з розрахунку на отримання мідно-нікелевого концентрату. Плавлення руд із сумарним вмістом більше 4-5% міді і нікелю проводять без збагачення.
У окиснених рудах нікель перебуває у вигляді ізоморфної суміші силікатів нікелю і магнію – n – NiOSiO2 · MgOSiO2, пуста порода складається з алюмосилікатів, гідратованих оксидів заліза, кварцу і тальку – 3MgO·4SiO2·H2O. Вміст нікелю у цих рудах становить 1-7%.
Окиснені руди, як правило, глинисті і містять близько 30% вологи. Перед плавленням їх необхідно окусковувати, застосовуючи для цього брикетування або агломерацію, здійснювану на стрічкових агломераційних машинах. Шихту подрібнюють до шматків розміром 3-5 мм. Паливом служить коксик, витрата його становить 7,5-8,5% від маси шихти.
Гіпс, необхідний як сірчиста добавка для проведення подальшого процесу, у шихту не вводять, тому що сірка, що міститься у гіпсі, при спіканні значною мірою переходить у гази. Агломерат після дроблення сортують на грохоті з осередками 20 мм, фракцію розміром менше 20 мм повертають у шихту на спікання.
У деяких залізних рудах міститься близько 0,3, а інколи до 1% нікелю. У цих рудах наявний також хром. Руди переробляють на хромонікелевий чавун. Із руд з підвищеним вмістом нікелю і низьким вмістом заліза можна, здійснюючи виборче відновлення в трубчастих печах, що обертаються, отримати феронікелеву кричу, а з неї виплавляти збіднений феронікель, що містить близько 4% нікелю.
При виробництві нікелю застосовують також гіпс, пірит, вапняк, кварцовий флюс і деревне вугілля.
3.2.2 Переробка сульфідних мідно-нікелевих руд
Сульфідні мідно-нікелеві руди переробляють за технологією, схожою з пірометалургією міді.
Великокускові багаті руди і агломерат звичайно переплавляють у шахтних печах, а концентрати і дрібні руди – у відбивних і електричних печах.
Виплавляють мідно-нікелевий штейн, що містить, %: 6-11 Ni, 3-9 Cu, 48-56 Fe і близько 25 S, який потім продувають повітрям у конверторі для отримання так званого білого нікелевого штейну (файн-штейну), що містить, %: 20-60 Ni, і нікелевий, містить 65-68 Ni, 2-4 Cu.
Мідний концентрат спрямовують для добування міді вже розглянутими способами, а нікелевий обпалюють на агломераційних машинах або у печах киплячого шару, а потім переробляють його для добування нікелю (плавлення на аноди і електролітичне рафінування).