О. Й. Любич, В. О. Пчелінцев Фізичні основи металургії кольорових І рідкоземельних металів
Вид материала | Документы |
- З дисципліни «Теоретичні основи ливарного виробництва» для студентів заочного факультету, 390.98kb.
- Програма, методичні вказівки та контрольні завдання з дисципліни " виробництво виливків, 797.9kb.
- Нова технологія утилізації гальваношламів машинобудівних підприємств з одержанням комплексних, 26.76kb.
- І містять у собі чорні або кольорові метали чи їх сплави, а також вироби з металу,, 462.13kb.
- Наказом Державного комітету України з питань регуляторної політики та підприємництва,, 341.66kb.
- Розробка базових теплотехнічних І конструктивних рішень, а також технологічних схем, 24.73kb.
- Назва реферату: Зварювання кольорових металів Розділ, 29.07kb.
- Робоча програма загальні методичні вказівки та індивідуальні завдання до вивчення дисципліни, 156.9kb.
- Типова програма кандидатського іспиту із спеціальності, 95.6kb.
- Державна митна служба україни, 19.16kb.
3.2.3 Переробка окиснюваних нікелевих руд
Переробка окиснюваних нікелевих руд базується на тому, що у нікелю спорідненість до сірки більший, ніж у заліза. У цьому випадку при відновному плавленні в шихту додають пірит або гіпс. Сірчисті добавки сульфідують залізо і нікель. У результаті одержують штейн, що є сплавом Ni3S2 і FeS, і залізистими шлаками. Залізо відокремлюється від нікелю при продуванні штейну повітрям або киснем.
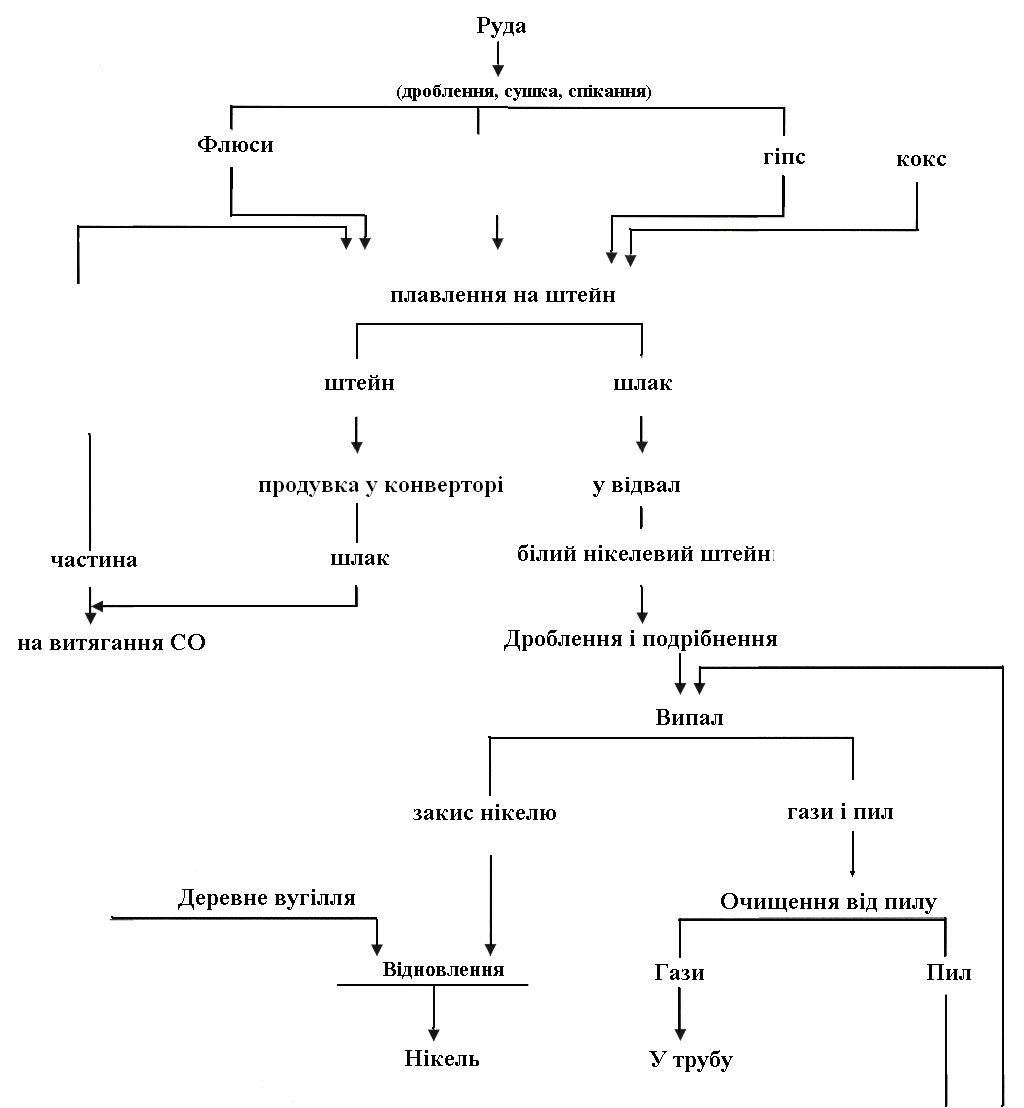
Рисунок 3.3 – Схема виплавлення нікелю із окисних руд
Таким чином, у конверторі відбувається вибіркове окиснення заліза і переведення його у шлак разом з кремнеземом і кварцовим флюсом, що додається. Одержуваний білий нікелевий штейн розливають, подрібнюють і піддають окиснювальному випаленню, у результаті якого утворюється закис нікелю, що переплавляється після змішування з деревним у електропечі на рідкий нікель. Схема переробки окиснюваних руд наведена на рис. 18, а окремі її стадії описані нижче.
3.2.4 Виплавка нікелевого штейну
Штейн з окускованих окиснених нікелевих руд звичайно виплавляють у шахтних печах. За будовою і розмірами вони подібні до печей, призначених для мідного шахтного плавлення. Ширина печі 1,6-1,7, довжина 10-16, висота від до колошникового майданчика близько 7 м. Піч звичайно забезпечують 12-18 щілиноподібними хурами розміром 70х1200 мм. До хур підводять повітря під надмірним тиском 16-20 кПа. Витрата повітря становить 45-55 м3/хв на 1 м2 перетину печі (при нормальному тиску і комплексній температурі).
Дуття, що подається у піч, звичайно не підігрівають, хоча абсолютно очевидна доцільність його нагрівання. Це повинно, крім поліпшення показників плавлення, привести до підвищення температури в горні, що має велике значення для попередження заростань горна феронікелем, що утворюються інколи у кількості, що перевищує величину його розчинності в штейні. Досліди, проведені на комбінаті «Юмуронікель», показали, що підігрів на 29% підвищує продуктивність. Плавлення є відновною, її проводять з високою витратою коксу (25-30% від маси агломерату). У піч завантажують шихту, що складається з агломерату або брикетів, гіпсу або піриту, вапняку і коксу. У горні кокс згорає до утворення СО і у фурменій зоні газ містить до 35% СО. Температура у фокусі горіння досягає 1450-1500°С. Гази, що підіймаються назустріч шихті, віддають частину їх хімічної і теплової енергії і в результаті в колошниковому газі вміст окислу вуглецю становить 12-16% і двоокиси вуглецю 15-30%, а температура і відновне середовище сприяють відновленню оксидів до отримання губчастого заліза.
Губчасте залізо з'єднується з сірою газовою фазою і у результаті утворюється FeS. Вапняк розкладається за реакцією CaCO3 = CaO + CO2, а вапно, що виходить, утворює силікати.
Гіпс CaSO4 · 2H2O, що втратив гідратну вологу, відновлюють до CaS: CaSO4 + 4CO(c)= CaS + 4CO2(CO). Якщо в шихті наявний пірит, то він розкладається при 600-700°С за реакцією 2FeS2 = 2FeS + S2.
FeS і CaS у цих реакціях сульфідують нікель у розплаві.
3NiO + 3CaS = Ni3S2 + 3CaO + 1/2 S2; (3.22)
3NiO + 2FeS = Ni3S2 + FeO + 1/2 S2. (3.23)
Таким чином, у печі виходить штейн-сплав сульфірів Ni3S2 і FeS, в якому в невеликих кількостях розчинені вільні метали – залізо і нікель. Вихід штейну становить 5-8% від маси агломерату. У штейні міститься 12-30 % Ni, 45-60% Fe, 17-23% S і невелика кількість кобальту.
Другим рідким продуктом є шлак, що містить, %: 40-43 SiO2, 6-8 Al2O3, 10-16 FeO, 18-20 CaO, 8-12 MgO і близько 0,15 Ni, головним чином у вигляді корольків штейну. Вихід шлаку становить 100-120% від маси агломерату. Шлаки можуть бути використані в будівельній промисловості. Нікель, що в цьому випадку залишився в них, зникає, отже, необхідно підбирати рухливі шлаки, створювати умови для інтенсивного перемішування шлакового розплаву з подальшим відстоюванням для того, щоб знизити втрати нікелю з відвальними шлаками.
Для прискорення процесу шахтного плавлення нікелевих руд корисно дуття збагатити киснем. Досліди показали, що збагачення дуття киснем до 40% дозволяє збільшити продуктивність майже в два рази. Одночасно майже на 50% знижується витрата коксу.
Найвигіднішим способом зниження витрати коксом є підігрів дуття, що повинно бути особливо ефективним при використанні у перспективі природного газу.
3.2.5 Конверторний метод переробки штейну
Для продування нікелевих штейнів застосовують конвертори.
Штейн продувають поступово, тобто заливають порціями по 2-4 n з одночасною подачею кварцового флюсу для ошлакування заліза. Таким чином проходить період переважного окиснення заліза і накопичується кількість розплаву. Тривалість продування коливається від 15 до 45 хвилин. Основна реакція цього періоду має вигляд 2Fe + O2 + SiO2 = (FeO)2 ·SiO2. У результаті цієї екзотермічної реакції розплав розігрівається. Температуру рекомендується тримати на рівні 1300°С. Щоб не перевищувати цей рівень, в конвертор подають холодні присадки (феронікель, твердий штейн, оборотний шлак).
Нікель, поки не ошлакувалося залізо, окиснюватися не може, оскільки через вищу хімічну спорідненість нікелю до сірки у порівнянні з його спорідненістю до кисню закис нікелю, навіть якщо б вона утворилася, взаємодіятиме з сульфідом заліза і знову перейде в сульфід нікелю:
6NiO+6FeS+2O2+3SiO2=2Ni3S2+3(2FeO·SiO2)+2SiO2. (3.24)
Після накопичення у конвертері збідненого залізом штейну розпочинають другий період продування – окиснення сірчистого заліза. Основна реакція цього періоду також екзотермічна:
2FeS + 3O2 + SiO2 = (FeO)2 х SiO2 + 2SO2. (3.25)
Продування закінчують після отримання файнштейну, що є зразково евтектичний сплав Ni з Ni3S2. Спочатку зливають шлак, а потім файнштейн (у виливниці). Файнштейн містить близько 78% Ni, 20-23% S, 0,15-0,3% Fe і невелику кількість кобальту і міді.
Конверторний шлак містить 26-28% SiO, 55-60 FeO і близько 1,5% Ni. Кобальту в основній масі шлаку міститься близько 0,3%, а в останніх сплавах – до 1,5%. Така відмінність у вмісті кобальту пояснюється захисним впливом заліза. Дослідами встановлено, що енергійне окислення кобальту, що знаходиться у штейні, починається після зниження вмісту заліза до 10-12%.
Частину шлаку спрямовують на плавлення у шахтних печах як добавку до агломерату, а іншу (велику частину) після збіднення у конвертерах направляють у відвал. Пил, що виноситься з конвертерів, містить до 15-20% Ni. Її уловлюють у пиловловлювачах і повертають у конвертер при такому продуванні. Загальна тривалість однієї операції продування становить 18-20 год.
Виникає питання – чи не можна продування закінчувати не тоді, коли буде отриманий файнштейн, а доводити процес до утворення чорнового нікелю. При продуванні повітрям це зробити не вдається. По-перше, через нестачу тепла для нагрівання розплаву до 1700-1800°С і, по-друге, через те, що реакція Ni3S2 + 4NiO = 7Ni + 2SO2 при температурі процесу проходить дуже повільно. Проте якщо дуття збагатити киснем, то можна конвертерний процес довести до отримання чорнового нікелю.
3.2.6 Випалення білого штейну (файнштейну) і відновлення нікелю
Для видалення сірки з файнштейну настільки, щоб залишковий вміст її становив 0,02%, його піддають окиснювальному випаленню: Ni3S2 + 3ЅO2 = 3NiO + 2SO2. У деяких випадках випалення файнштейну проводять у дві стадії: спочатку в багатоходовій печі, а потім в трубчастій печі, що обертається.
Досконалішим є випалення файнштейну в киплячому шарі, принцип роботи якого вже був згаданий.
Випалення проводять, не допускаючи спікання при температурі 1000-1050°С, при коефіцієнті витрати повітря, рівному 2.0.
Після випалення отримують закис нікелю, що містить до 98% NiO і 0,01-0,02% S; крім того, у ньому містяться домішки СО, С і Fe. Закис нікелю дещо завантажений кремнеземом і глиноземом футерування печей.
Продуктивність печі становить 6-8 m/(м2·добу).
Відновне плавлення проводять у дугових електричних печах ємністю 3,5-10 m, аналогічних вживаним у сталеплавильному виробництві.
Як відновник краще за все брати деревне вугілля або нафтовий кокс, чисті за сіркою. При плавленні нікелю для подальшого рафінування іноді застосовують пековий кокс і навіть кам'яновугільний коксик.
Відновлення починається при 700-900°С і проходить за реакцією
NiO + CO = Ni + CO2, (3.26)
CO2 + С = 2CO, (3.27)
NiO + С = Ni + CO. (3.28)
Процес проводять з таким розрахунком, щоб отримати рідкий нікель, тому плавлення закінчують при температурі близько 1500°С. У рідкому нікелі розчиняється вуглець у вигляді карбіду нікелю Ni3C, вміст якого у рідкому металі досягає 2,2%. З одного боку, це сприятливе явище, оскільки знижує температуру плавлення нікелю. Але при застиганні рідкого нікелю карбід заліза розкладається з виділенням шматків графіту, що робить метал неміцним і крихким. Отже, бажано, щоб в нікелі, що випускається, був понижений вміст вуглецю. З цією метою у кінці плавлення проводять так звану операцію добавки – добавляють закис нікелю для окиснення надлишку вуглецю:
Ni3C + NiO = 4Ni + CO.
Процес плавлення – періодичний з тривалістю операції 5-7 годин. Для того, щоб ошлакувати домішки і десульфурації, додають вапняк, у результаті утворюється невелика кількість рідкого вапняного шлаку, що знімається перед операцією доведення. Нікель, що випускається з печі, гранулюють або розливають у виливниці.
3.2.7 Електролітичне рафінування нікелю
Чорновий нікель, отримуваний з окиснених руд, містить, %: 99,2-9,6 (Ni + Co); 0,3-0,8 Fe; до 0,02Si; до 0,4 С і 0,004-0,4Cu. Такий склад відповідає вимогам стандартів для нікелю нижчих марок. Тим часом чорновий нікель з сульфідних мідно-нікелевих руд не відповідає вимогам стандартів навіть для нижчих марок головним чином за вмістом заліза і міді. Він містить 1,3-2,5% Fe і 2-2,6% Cu проти 0,25 і 0,06-0,6%. Тому чорновий нікель, що виплавляється з сульфідних мідно-нікелевих руд, піддають електролітичному рафінуванню.
3.3 Фізико-металургійні основи виробництва
свинцю
3.3.1 Знаходження свинцю в природі та його
отримання
Вміст у земній корі 1,6-10-3 % за масою. Самородний свинець трапляється рідко. Входить до складу 80 різних мінералів. Найважливіші з них: галеніт РbS, церусит РbСО3, англезит РbSО4 і крокоїт РbСrО4. Завжди міститься в рудах урану і торію.
Основне джерело отримання свинцю – сульфідні поліметалічні руди, мінерал – галеніт РbS. На першому етапі руду збагачують. Отриманий концентрат піддають окиснювальному випаленню: 2РbS + 3О2 = 2РbО + 2SО2↑.
При випаленні додають флюси (СаСО3, Fе2О3, SiO2). Вони утворюють рідку фазу, що цементує шихту. Отриманий агломерат містить 35-45% Рb. Далі свинець і оксид міді, що містяться в агломераті відновлюють коксом:
РbО + С = Рb + СО↑ і РbО + СО = Рb + СО2↑. (3.29)
Чорновий свинець отримують взаємодією вихідної сульфідної руди з киснем (автогенний спосіб). Процес проходить в два етапи:
2РbS+3О2 = 2РbО+2SО2↑, РbS+2РbО = 3Рb+SО2↑. (3.30)
Для подальшого очищення чорнового свинцю від домішок Сu, Sb, Sn, А1, Вi, Аu, і аg його очищають пірометалургійним методом або електролізом.
Країни - найбільші виробники свинцю (включаючи вторинний свинець) на 2004 рік, тис. тонн:
ЄС | 2038, |
США | 1498, |
Китай | 1256, |
Корея | 219. |
3.3.2 Фізичні і хімічні властивості
Свинець – метал голубувато-сірого кольору з кубічною гранецентрованою граткою, а = 0,49389 нм. Щільність 11,3415 кг/дм3, температура плавлення 327,4-327,50°С, кипіння 1715-1745°С. Свинець м'який, легко прокатується в якнайтонші листи, свинцеву фольгу. Добре поглинає рентгенівські і γ-промені.
Хімічно свинець досить інертний. У вогкому повітрі поверхня свинцю темнішає, покриваючись спочатку оксидною плівкою, яка поступово переходить в основний карбонат 2РbСО3·Рb (ОН)2 (свинцеві білила).
З киснем свинець утворює оксиди:
- РbО (форми: жовтий масикот і червоний глет);
- коричнево-чорний РbО2;
- оранжево-червоний Рb3О4 (свинцевий сурик),
- коричневий Рb2О3;
- Рb12O17;
- Рb12O19.
Оксид РbО має амфотерні властивості. Реагує з кислотами: РbО + 2СН3СООН = Рb (СН3СОО)2 + Н2О і з розчинами лугів
РbО + КОН = К2РbО2 + Н2О. (3.31)
Плюмбат калію К2РbО2 утворюється також при взаємодії свинцю з розчином лугу:
Рb + 2КОН = К2РbО2 + Н2↑. (3.32)
У РbО2 переважають кислотні властивості, він є сильним окиснювачем. Оксид Рb3О4 можна розглядати як свинцеву сіль ортосвинцевої кислоти Рb2[РbО4].
При кімнатній температурі свинець не реагує з сірчаною і соляною кислотами, оскільки на його поверхні при цьому утворюються погано розчинні сульфат свинцю РbSО4 і хлорид свинцю РbС12. Але з органічними кислотами (оцтовою і мурашиною), а також з розбавленою азотною свинець реагує, утворюючи солі свинцю:
3Рb+8НNО3 = 3Рb (МО3)2 + 2NO + 4Н2О. (3.33)
При взаємодії свинцю з оцтовою кислотою, з продуванням кисню, утворюється ацетат свинцю Рb (СН3СОО)2, так званий «свинцевий цукор», що має солодкий смак.
3.3.3 Застосування свинцю
До 45% свинцю йде на виготовлення пластин свинцево-кислотних акумуляторів, 20% - на виготовлення дротів, кабелів і покриттів до них. Екрани з свинцю служать для захисту від радіоактивного і рентгенівського випромінювання. Із свинцю і його сплавів виготовляють цеглу і контейнери для зберігання і захисту від радіоактивних речовин. Невеликі кількості свинцю постійно витрачаються для виробництва азиду свинцю як детонатор (первинної вибухової речовини).
Сплави свинцю з Sb, Sn і Сu використовують для виготовлення друкарських шрифтів, із сплавів свинцю з Sb і Аs виготовляють осердя куль, шрапнель, дріб.
Близько 5-20% свинцю йде на виготовлення тетраетилсвинцю (ТЕС) (СН3СН2)4Рb, який додають до бензину для підвищення октанового числа (у даний час не використовують, оскільки доведена його канцерогенність). Свинець використовується у виробництві пігментів, для будівництва сейсмостійких фундаментів.
Країни, найбільші споживачі свинцю у 2004 році, у тис. тонн:
Китай 1770;
ЄС 1553;
США 1273;
Корея 286.
Нітрат свинцю застосовується для виробництва могутніх сумішних вибухових речовин. Телурид свинцю широко застосовується як термоелектричний матеріал (термое.д.с 350 мкВ/К). Азид свинцю застосовується як найбільш застосовуваний детонатор (ініціююча вибухова речовина). Перхлорат свинцю використовується для приготування тяжкої рідини (щільність 2,6), використовуваної у флотаційному збагаченні руд, так само він іноді застосовується в сумішних вибухових речовинах як окиснювач. Фторид свинцю самостійно, а так само разом із фторидом вісмуту, міді, срібло застосовується як катодний матеріал у хімічних джерелах струму. Вісмутит свинцю, сульфід свинцю, йодид свинцю застосовуються як катодний матеріал у літієвих акумуляторних батареях, хлорид свинцю як катодний матеріал у резервних джерелах струму. Телурид свинцю найбільш широкозастосовуваний матеріал у виробництві термоелектрогенераторів і термоелектричних холодильників. Двоокис свинцю широко застосовується не тільки в свинцевому акумуляторі, але так само на її основі виробляються багато резервних хімічних джерел струму, наприклад, свинцево-хлорний елемент, свинцево-плавиковий елемент та ін.
Свинець дуже легко кується і прокатується. Вже при тиску 2 т/см2 свинцева стружка спресовується в суцільну монолітну масу. Із збільшенням тиску до 5 т/см2 твердий свинець переходить у текучий стан. Свинцевий дріт отримують, продавлюючи через фільєру твердий свинець.
3.4 Фізико-металургійні основи виробництва цинку
3.4.1 Сировина для отримання цинку
Цинкові мінерали, з яких добувають цинк, численні; це передусім сульфід цинку, названий сфалеритом, або цинковою обманкою, карбонат цинку – смітсоніт ZnСО3 і силікат складу Zn2SiO4·H2О – каламін. Інші мінерали трапляються рідко і промислового значення не мають. Цинкові руди містять 2,0-12% Zn, а також мідь, свинець і ряд інших цінних металів. Цинкові концентрати містять 47-60% Zn, 1,5-2,5% Рb, до 3,5% Сu, 3-10% Fе, до 0,25% Сd і 29-33% S, а також талій, індій, галій, германії, селен і телур. Зразковий мінералогічний склад цинкового концентрату (47.66% Zn), %:
сфалерит - 70,3
галеніт - 5,2
халькопірит - 3,1
пірит та інші сульфіди заліза - 11,3
силікати і карбонати - 10,1.
Цинкові концентрати є порошками, 50-95% частинок яких тонші 0,07 мм, а вміст зерен більше 0,6 мм не перевищує 0,1-0,3%.
При збагаченні окиснених руд виходять концентрати, що містять цинк переважно у вигляді смітсоніту і каламіну.
3.4.2 Способи отримання цинку
У даний час для добування цинку застосовують два способи: пірометалургійний (дистиляційний) і гідрометалургійний (електролітний). Перший з них був освоєний значно раніше другого. Поки що в зарубіжному світі близько половини усього цинку одержують дистиляційним способом.
Розвиток радянської металургії цинку відбувався переважно шляхом застосування електролітного способу, який став у нас основним.
Дистиляційний спосіб. Дистиляцію виконують у горизонтальних і вертикальних ретортах. У горизонтальних ретортах цинковий концентрат обпалюють для перетворення сульфідів в оксиди, сфалерит окиснюється за реакцією
2ZnS + 3О2 → 2ZnО + 2SО2. (3.34)
Суміш обпаленого цинкового концентрату з дрібним антрацитом або дрібним коксом завантажують у реторти з шамоту (рис. 3.4), горизонтально встановлені у печі, нагріті до 1400°С.
У реторті цинк відновлюється за реакцією
ZnО + С → Zn (пар) + СО. (3.35)
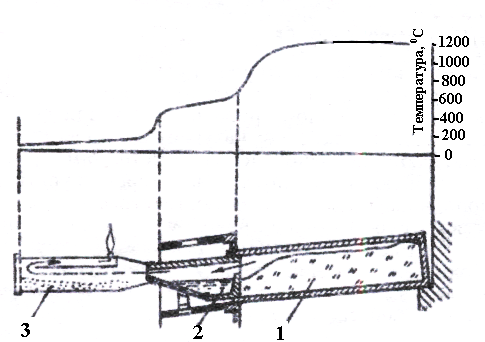
Рисунок 3.4 – Установка для дистиляції цинку в горизонтальній реторті: 1 – реторта; 2 – конденсатор; 3 - алонж
До основи реторти приєднується конденсатор з вогнетривкої глини; рідкий цинк з нього у міру накопичення вичерпують. Однак у конденсаторі не всі пари цинку встигають сконденсуватися, частина їх йде в залізний алонж, надітий на основу конденсатора. У алонжі цинк добувається у вигляді тонкого пилу – пусьєри.
У реторті можуть відновлюватися й інші метали, що містяться у шихті, наприклад, кадмій, свинець, мідь. Однак тільки кадмій і свинець випаровуються у значній кількості і можуть забруднювати цинк.
Після закінчення дистиляції конденсатор прибирають, а з реторти вивантажують залишок від дистиляції, що спікся, – раймування. У раймуванні 6-12% Zn, для його добування потрібна переробка раймування іншим способом.
Пірометалургійний спосіб отримання цинку в горизонтальних ретортах, по суті, простий, але малопродуктивний і дає цинк, забруднений свинцем і кадмієм.
Поперечник горизонтальної реторти не може перевищувати 300-370 мм, а товщина її стінки 30-50 мм. Із збільшенням цих розмірів значно погіршуються передача тепла всередину шихти і швидкість дистиляції. Довжина реторти не повинна перевищувати 1700-1900 мм, інакше при 1400°С вона не витримає навантаження на згин.
Реторта заданих розмірів вміщує 80-90 кг шихти, що містить близько 30 кг цинку. При тривалості циклу дистиляції 24 год. і виході рідкого цинку 80-83% одна реторта дає не більше 25 кг цинку за добу. Тому на середньому за потужністю сучасному заводі необхідно мати у дії декілька тисяч реторт. Обслуговуються реторти до цього часу вручну – спроби механізувати цю роботу не вдалися. Обслуговування реторти – це тяжка фізична праця.
Загальна схема дистиляційного отримання цинку показана на рис. 3.5; вона залишилася майже без змін до наших днів, хоча техніка дистиляції зазнала значних змін і тепер застосовується у декількох варіантах.
Електротермічним способом цинк одержують у високих шахтних печах (12-14 м), складених з високосортної вогнетривкої цегли. Шихта складається із пеку обпаленого концентрату і коксу. Струм підводиться графітними електродами, встановленими на відстані 8-10 м один від одного по висоті, і проходить через кокс. Між шматками коксу виникають численні електричні дуги, що нагрівають
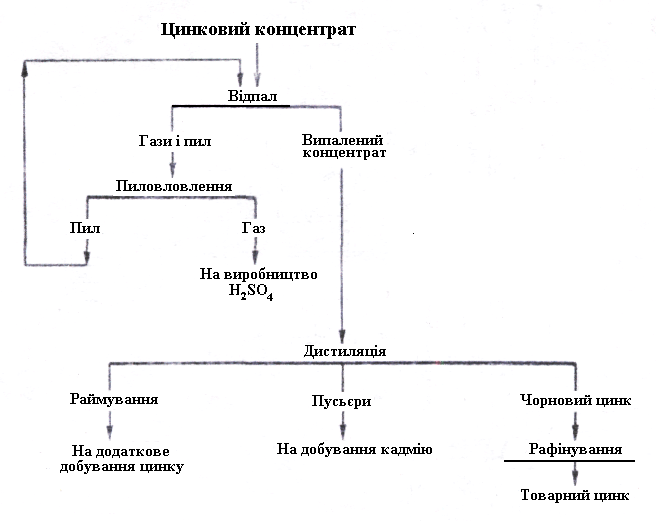
Рисунок 3.5 – Схема виробництва цинку дистиляцією
шихту в середньому до 1200°С. Раймування вивантажують безперервно, воно містить 15-16% Zn. Пари цинку конденсують і метал або спалюють до окислу, який і є кінцевим продуктом. Крім цинку, в раймуванні завжди залишаються свинець, мідь і благородні метали, тому воно вимагає додаткової переробки.
За іншим способом дистиляцію в електропечах проводять при повному розплавленні шихти. Обпалений концентрат плавлять у суміші з вугіллям і флюсами при 1300-13500С, отримуючи рідкий шлак, що служить тілом нагрівання, в нього занурені зверху графітні електроди.
При високій температурі ванни ще до початку плавлення шихти з неї відновлюють не лише оксиди міді і цинку, але й залізо. Залізо, розчиняючи в собі вуглець і мідь, утворює на поді шар мідистого чавуну, Загальне добування цинку в гази досягає 95%, але лише 4/5 його вдається отримати у вигляді металу, інший переходить в пил і оксиди.
Витрата енергії тут вища, ніж при дистиляції з твердої шихти, вона досягає 3300 кВт/год на тонну цинку замість 2550-2900 кВт/год за першим способом. Переваги дистиляції з розплавленням шихти – в менших вимогах до якості сировини і більшої комплексності його використання.
Дистиляція цинку в шахтних печах. При звичайному свинцевому відновному плавленні до 4/5 цинку залишається в шлаку і штейні, інший втрачається з газами. У нижній частині шахтної печі, де температура вища 10000С, цинк інтенсивно відновлюється за реакціями:
ZnО + С ↔ Zn + СО,
ZnО + СO↔Zn + СО2, (3.36)
Пари металу, підіймаючись з газами по шахті, знову окиснюються до окислу, що осідає на шматках шихти: із зниженням температури друга з наведених вище реакцій швидко проходить у зворотному напрямі справа наліво.
У Англії на заводі Евонмаут були знайдені умови плавлення, що дозволяють отримати цинк у вигляді металу. Шихту і кокс перед завантаженням у піч підігрівають до 800°С, а повітряне дуття – до 6000С. Плавлення проводять з підвищеною витратою коксу. У результаті цього в гази переходить до 90% цинку, і він не окиснюється: температура колошникових газів підтримується на рівні 10000С, також і у результаті спалювання частини оборотного конденсаторного газу. Гарячі гази, що містять 8-10% СО2 і 5 -6% пари цинку, надходять у великі конденсатори, де різко охолоджуються. Щоб попередити конденсацію цинку у вигляді пилу, в конденсаторах інтенсивно розбризкують рідкий свинець встановленими мішалками, що для цього обертаються. Конденсуючись на дрібних краплях свинцю, цинк утворює з ним сплав (2,26% Zn), який безперервно перекачують насосами в розділову ванну. Охолоджуючись тут, сплав розділяється на два шари: у нижньому з них 2,02% Zn, інше – свинець, а у верхньому близько 99,5% Zn. Нижній шар повертають у конденсатори, а верхній – на рафінування.
Для отримання 1 т цинку потрібне розбризкування в конденсаторах близько 400 т свинцю. При нормальному режимі роботи до 9/10 – цинку одержують з газів у вигляді рідкого металу і лише 1/10 – в порошку і оксидах; останні повертають в шихту. У шлаках шахтної плавки міститься 0,5% Рb і до 5% Zn. Схема установки показана на рис. 3.6.
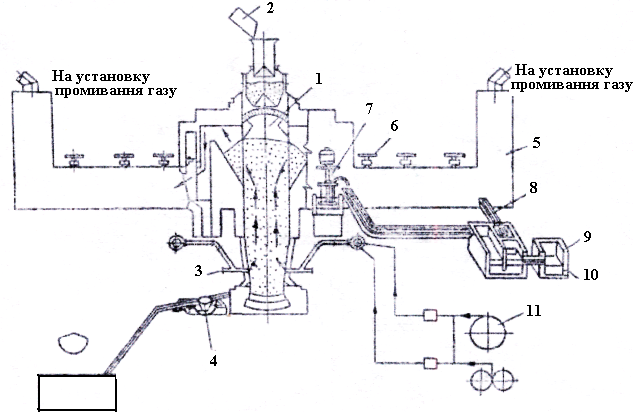
Рисунок 3.6 - Схема установки для дистиляції цинку в шахтній печі: 1 – шахтна піч з герметичним завантажувальним пристроєм: 2 – пристрій для завантаження гарячого агломерату і коксу; 3 – фурми; 4 – пристрій для випуску чорнового свинцю; 5 – конденсатори для цинку; 6 – ротори, що розбризкують свинець; 7 – насос, що перекачує сплав з конденсаторів в розділову ванну;
8 – жолоб для повернення свинцю в конденсатор: 9 – приймач для рідкого цинку; 10 – льотка для випускання цинку; 11 – повітронагрівачі
Дистиляція цинку в шахтних печах – нова прогресивна переробка; найближчими роками він може зайняти дуже важливе місце у практиці переробки свинцево-цинкових концентратів і шлаків.
На наших заводах цинк поки одержують тільки дистиляцією в горизонтальних ретортах і в електропечах з розплавленням шихти.
Рафінування чорнового цинку. У цинку, одержуваному дистиляцією, звичайно містяться домішки в таких межах: 1-3% Рb; 0,03-0,5% Сd; 0.05-0.3% Fе; 0,05-0,1% Сu; 0,0003-0,05% As.
Найпростіше і найдешевше рафінування цинку ліквацією базується на зниженні розчинності домішок при охолоджуванні металу до 430-4500С. Після відстоювання протягом 24-36 год. рідкий чорновий цинк ділиться на три шари: нижній містить до 96% Рb, середній складається з твердих кристалів FеZn7, включає основну кількість домішок заліза, а верхній за складом придатний для багатьох споживачів – у ньому залишається до 1% Рb і 0,03- 0,04% Fе, що відповідає маркам Ц2 і ЦЗ ГОСТ 3840-65.
Ліквацію проводять у відбивних печах ємністю до 150 т. На поверхні ванни від окиснення цинку пічними газами утворюються порошкоподібні знімання, що повертаються на дистиляцію. Чорновий цинк періодично завантажують у ванну і зливають з неї верхній відстій. Відходи ванни, що накопичуються в нижніх шарах, видаляють періодично. Свинцевий сплав придатний для рафінування свинцю від благородних металів, а залізистий продукт повертають на дистиляцію. Кадмій цим способом не відділяється, а залишається у цинку і втрачається.
Інший спосіб рафінування - ректифікація - дозволяє одержати цинк чистотою 99,996% і добути з нього кадмій. Ректифікація - дорога переробка, а попит на такий дуже чистий цинк обмежений.
Гідрометалургія цинку. Паралельно розвитку техніки дистиляції цинку з 1915 р. почали впроваджувати у виробництво гідрометалургійний спосіб. Тоді він був привабливий можливістю отримання дуже чистого цинку.
Для гідрометалургійної переробки цинкові концентрати теж обпалюють, а потім вилуговують розбавленою сірчаною кислотою. Цинк переходить у розчин за реакцією
ZnO + H2SO4 → ZnSO4 + H2O. (3.37)
Кремнезем і основна маса оксидів заліза залишаються у нерозчинному залишку.
Одержаний розчин сірчанокислого цинку очищають від домішок і піддають електролізу. При цьому на катодах осідає чистий цинк, на анодах виділяється кисень, а в розчині накопичується сірчана кислота, знову придатна для вилуговування обпаленого концентрату.
Кількість сірчаної кислоти, що виділяється при електролізі, повинна відповідати витраті її на вилуговування недогарка. Цей баланс регулюють умовами відпалу, залишаючи частину сірки у вигляді ZnSO4 у недогарку, що не вимагає витрат кислоти при вилуговуванні і під час електролізу, що створює її.
Реакції електролізу можна показати такою короткою схемою:
на катоді 2Zn2 + 4е → 2Zn;
на аноді 2H2O – 4е → O2 + 4H+.
На рис. 3.7 наведена схема гідрометалургійного способу отримання цинку, яким отримують цинк марок ЦВ, ЦО, Ц1 (ГОСТ 3640-65), що містить відповідно Zn, %; 99,99; 99.975 і 99,95.
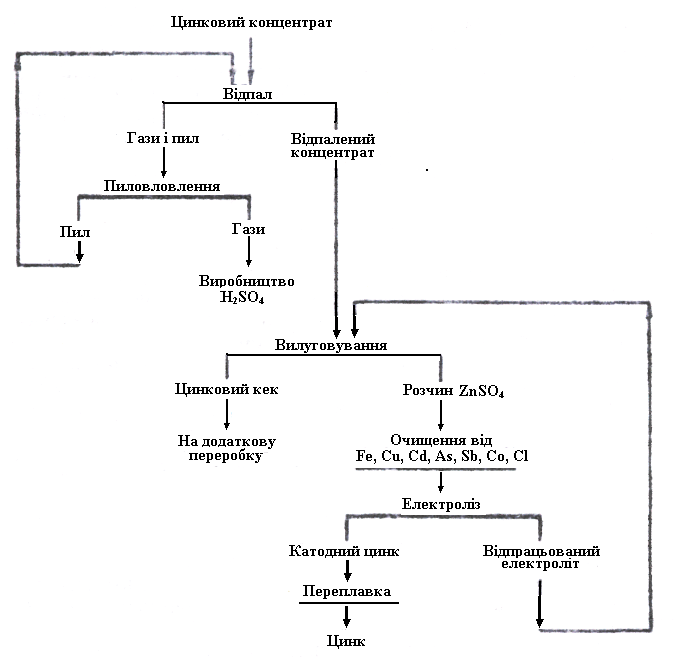
Рисунок 3.7 – Коротка схема гідрометалургійного виробництва цинку