О. Й. Любич, В. О. Пчелінцев Фізичні основи металургії кольорових І рідкоземельних металів
Вид материала | Документы |
- З дисципліни «Теоретичні основи ливарного виробництва» для студентів заочного факультету, 390.98kb.
- Програма, методичні вказівки та контрольні завдання з дисципліни " виробництво виливків, 797.9kb.
- Нова технологія утилізації гальваношламів машинобудівних підприємств з одержанням комплексних, 26.76kb.
- І містять у собі чорні або кольорові метали чи їх сплави, а також вироби з металу,, 462.13kb.
- Наказом Державного комітету України з питань регуляторної політики та підприємництва,, 341.66kb.
- Розробка базових теплотехнічних І конструктивних рішень, а також технологічних схем, 24.73kb.
- Назва реферату: Зварювання кольорових металів Розділ, 29.07kb.
- Робоча програма загальні методичні вказівки та індивідуальні завдання до вивчення дисципліни, 156.9kb.
- Типова програма кандидатського іспиту із спеціальності, 95.6kb.
- Державна митна служба україни, 19.16kb.
1. 5 Металургійне паливо
Високі температури, необхідні для багатьох металургійних переділів, досягаються спалюванням палива і (поки рідше) електронагріванням.
Паливом служать горючі речовини, які вигідно спалювати для отримання тепла. Вони бувають твердими (вугілля, торф, дрова, кокс), рідкими (нафта, мазут, гас, бензин), або газоподібними (природний й інші горючі гази).
До складу будь-якого палива входять пальні складові -вуглець, водень, вуглеводні, наприклад метан СН4 та інші, описувані в загальному вигляді формулою Сn Нm, а також негорючі – мінеральні речовини і волога.
Мінеральні домішки при згоранні палива дають золу; вона складається з оксидів алюмінію, заліза, кремнію, кальцію та інших елементів. Зола поглинає порівняно трохи тепла; проте чим більше в паливі золи, тим менше складових. Зола обволікає частинки палива, утрудняючи доступ кисню до них, а отже, і спалювання палива. Особливо небажана легкоплавка зола, плівки розплаву якої на паливі найбільш щільні.
У табл. 5 показано теплотворення і зольність деяких видів палива.
Таблиця 5 - Характеристика деяких видів палива
Паливо | Зола, % (за масою) | Теплотворна здатність | |||
кДж/кг | ккал/кг | кДж/м3 | ккал/м3 | ||
Дрова | 0,7 – 2,0 | 18800 | 4500 | - | - |
Торф | До 10 | 23400 | 5600 | - | - |
Кам’яне вугілля | До 10 | 21000- 29000 | 5000- 7000 | - | - |
Нафта | 0,2 - 0,3 | 41900- 46000 | 10000- 11000 | - | - |
Природний газ | Немає | - | - | 35600- 37700 | 8500- 9000 |
У металургії паливо часто спалюють в тому ж пічному просторі, де переробляється руда. Для кращого використання печей об'єм палива і його витрата повинні бути малими. Для металургії потрібне висококалорійне і малозольне паливо: зола може забруднювати продукти переробки. Кращі види металургійного палива: газ, мазут, кокс і висококалорійне кам'яне вугілля.
Природний газ. Природний газ містить від 50 до 97% метану й інших горючих вуглеводнів складу СnHm, негорючих домішок в ньому, як правило, не більше 3-10% (Со2, N2 та ін.). Газифікація кольорової металургії була почата в 1958 р. Сучасна потреба кольорової металургії в газі ще невелика, але вона вже оцінюється в 10 млрд м3 газу на рік. Ширшому використанню газу в металургії поки перешкоджає відсутність розгалуженої мережі газопроводів, будівництво якої швидко продовжується.
Нафта. Нафта складається з суміші різних вуглеводнів. Вона служить не тільки паливом, але і цінною сировиною для хімічної промисловості. Спочатку нафту перегонять, витягуючи легкокиплячі цінні речовини: бензин, гас, лігроїн і газойль. Залишок від перегонки – мазут містить близько 85% вуглецю і 12% водню. Мазут – прекрасне рідке паливо з теплотворною здатністю близько 41800 кдж/кг (10000 ккал/кг) і цінна сировина для подальшої переробки на змащувальні масла і гудрон, тому із застосуванням мазуту в багатьох металургійних переділах можна погодитися тільки до широкого освоєння природного газу.
Швидке спалювання палива сприяє отриманню високих температур; при цьому менше тепла встигає вийти через стіни печі в зовнішнє середовище. Для швидкого спалювання мазут пульверизують стиснутим повітрям і вдувають у печі розпилювачем – форсункою.
Кам'яне вугілля. Кам'яне вугілля має багато різновидів, що відрізняються вмістом вільного вуглецю, вуглеводнів, золи і смолоподібних речовин – бітумів. При нагріванні кам'яного вугілля без доступу повітря вуглеводні випаровуються, а при доступі повітря згорають, утворюючи полум'я. Вугілля з високим вмістом вуглеводнів відносить до довгополум'яного (до 45% летких), а при малому їх вмісті - до нелетких. Якщо потрібні високі температури, кам'яне вугілля, переважно довгополум'яне, спалюють в пилоподібному стані.
Для деяких металургійних печей потрібне тверде кускове паливо. Воно повинне бути міцним, а для швидкого згорання – і пористим. Ці вимоги задовольняє кокс. Кокс роблять з особливих сортів кам'яного вугілля, що містять бітуми. Вугілля подрібнюють до величини близько 5 мм, зволожують і завантажують в камери коксових печей. Герметично закриті камери нагрівають зовні до 900-1000° С. Леткі речовини відводяться у холодильники, де з них конденсуються цінні хімічні продукти (смоли, бензол, толуол та ін.), а горючий коксовий газ виводиться з холодильника.
Від розплавлення і подальшого твердіння бітумів вугілля в камерах спікається в суцільну пористу масу – кокс. Вивантажений кокс гасять – охолоджують водою і подрібнюють, після чого він виходить у вигляді міцних пористих шматків сріблясто-сірого кольору з теплотвірною здатністю близько 26170 кДж/кг (6500 ккал/кг).
Коксовий газ, що складається з водню (50%), метану (27%) й інших вуглеводнів, може служити хорошим паливом, теплотворна здатність його близько 18800 кДж/м3 (4500 ккал/м3). Частина коксового газу йде на нагрівання коскових печей, останню використовують як паливо для інших потреб.
1.6 Вогнетривкі матеріали
Вогнетривкими називають будівельні матеріали, не плавкі при високих температурах, до 1600°С. Вогнетривкість визначають за характером початкової деформації зразка стандартної форми, що нагрівається при поступово зростаючій температурі.
Крім вогнетривкості, ці матеріали повинні володіти термічною стійкістю – не розтріскуватися при різких змінах температури, і хімічною стійкістю проти дії шлакових і сольових розплавів. Залежно від застосування оцінюють також щільність, теплопровідність і електропровідність вогнетривких матеріалів.
Сировиною для виробництва найбільш ходових вогнетривких виробів служать тугоплавкі оксиди, а також хімічні сполуки оксидів алюмінію і кремнію, отримувані прожаренням вогнетривких глин. Наприклад, температури плавлення А12О3 - 2050°C; SiO2 -1713°C; MgO - 2800°C; СaО - 2570°C; Сr2O3 - 2275°С.
Для виготовлення цеглини або інших виробів початкові оксиди змішують з невеликими кількостями зв’язувальних речовин - глиною або іншими речовинами і зволожують. З отриманої після гарного перемішування однорідної маси пресують вироби, які потім поступово сушать, уникаючи розтріскування, і обпалюють в особливих печах, поступово підвищуючи температуру до 1350-1600°C (залежно від складу і сорту). Після витримування при цій температурі слідує повільне охолоджування.
Хімічна природа оксидів, що входять у вогнетривкі матеріали, різна. Оксиди кальцію і магнію – основи, двоокис кремнію має кислотні властивості, а окисел алюмінію амфотерний: залежно від середовища вона проявляє або кислотні, або основні властивості.
Шамотні вироби роблять з вогнетривкої глини, головна складова якої каолініт А12O3 · 2SiO2 ·2H2O. Глину обпалюють при 1400°C, тому вона втрачає воду і перетворюється на шамот, хімічна формула якого 3Аl2О3 • 2SiO2. При змочуванні водою шамот вже не стає пластичним, подібно до глини. Подрібнений шамот змішують з водою і свіжою глиною, що служать для зв'язування. Отриману при цьому густу масу мнуть і подають на формування, сушіння і випалення.
Вогнетривкість шамотних виробів порівняно невелика – не перевищує 1730°C, але вони дешеві і знаходять широке застосування в металургії. За хімічними властивостями шамот нейтральний. Чим більший вміст Аl2О3 в шамоті, тим вище його вогнетривкість. Для отримання найбільш вогнетривкого високоглиноземистого шамоту до складу сирої маси додають технічний глинозем Аl2О3.
Магнезитові вироби отримують з природного магнезиту, який для видалення вуглекислоти спочатку обпалюють при температурі 1600°C:

Зв'язувальною речовиною служить також окисел магнію, що отриманий випаленням при 900°С. Переділи, необхідні для виготовлення виробів, такі самі: м'яття, формування, сушіння і випалення.
Магнезитові вироби стійкі до 2000°C, вони мають хімічні властивості основ. Відмітні особливості магнезитових виробів: мала термостійкість (погано переносять різкі зміни температури) і порівняно висока щільність (3,65 г/см3).
Динасові вироби отримують з чистого кварцового піску. Як невелику зв'язувальну добавку застосовують вогнетривку глину. Динас – це вогнетрив кислотного характеру з вогнетривкістю близько 1710°C і з високою термостійкістю.
1.7 Вимоги до металургійного процесу і його
структури
Технологічні процеси, які існують на підприємствах, у більшості випадків не цілком задовольняють сучасні вимоги. Ряд процесів та їх апаратурне оформлення застаріли і повинні бути замінені на нові, більш досконалі.
Сучасні металургійні процеси одержання кольорових металів і тим більше процеси найближчого майбутнього повинні задовольняти щонайменше ці основні вимоги:
1) висока питома продуктивність застосовуваних апаратів;
2) висока продуктивність праці (випуск продукції на одного робітника);
3) високий ступінь вилучення всіх цінних складових;
4) високий ступінь комплексності використання сировини;
5) мінімальні енергетичні витрати за рахунок використання зовнішніх джерел теплової енергії або електрики;
6) максимальне використання повторних енергоресурсів;
7) забезпечення можливості комплексної механізації й автоматизації всіх операцій;
8) використання простої, дешевої, довговічної і зручної в роботі, пуск, налагодження і ремонт апаратури;
9) забезпечення можливості створення безупинних, потокових, цілком автоматизованих технологічних ліній, одержання металів із частковим або повним програмним керуванням;
10) забезпечення безпечних і нешкідливих умов праці й охорони навколишнього середовища.
Удосконалення існуючих і створення нових технологій і апаратів, що максимально задовольняють вимоги сучасності, можливо, лише за умови глибокого розуміння структури металургійних процесів і можливостей керування швидкостями їх перебігу.
Будь-який металургійний процес становить складний комплекс послідовних фізико-хімічних перетворень, що проходять одночасно, і взаємодій - елементарних стадій.
За своїм характером фізико-хімічні перетворення і взаємодії в пірометалургії визначають три групи явищ:
1) перетворення, пов'язані тільки з дією високих температур. До них відносять нагрів, сушіння, термічну дисоціацію, плавлення і т.п.
2) перетворення, пов'язані з дією газової фази на тверді і рідкі речовини. Характер таких перетворень залежить від властивостей газового середовища. В окисній атмосфері, що містить кисень або інші окиснювачі, відбуваються реакції окиснювання сульфідів, металів, горіння вуглецю і т.п. Якщо середовище буде відновним, тобто коли у газовій фазі багато оксиду вуглецю або водню, то будуть проходити реакції відновлення оксидів металів, сульфатів, оксиду сірки і т.д. Нейтральна атмосфера, що не містить окиснювачів або відновлювачів у помітних кількостях, істотно не впливатиме на перероблювані матеріали.
3) хімічні взаємодії між наявними в перероблюваних матеріалах компонентами.
У гідрометалургії фізико-хімічні взаємодії проходять на межі поділу твердої і рідкої фаз, часто за участі газоподібного реагенту. В основному вони спрямовані на розчинення твердої речовини або, навпаки, на виділення твердої фази з розчину.
Кожний металургійний процес характеризується власною, що відрізняється від інших процесів, структурою. Знання структури процесу дуже важливо для металургів, тому що це дозволяє грамотно керувати процесом, намічати шляхи його подальшого удосконалення або інтенсифікації.
Різноманіття застосовуваних у кольоровій металургії процесів не дозволяє розглянути в даному розділі структуру кожного з них.
Найважливіші металургійні процеси будуть проаналізовані з цих позицій при розгляді технології одержання конкретних металів. Зупинимося лише на загальній характеристиці елементарних стадій найбільш складного за своєю структурою процесу металургійної плавки рудної сировини. Рудні плавки включають такі елементарні стадії:
1) нагрів і сушіння перероблюваних матеріалів;
2) термічну дисоціацію хитких хімічних сполук;
3) окиснювання сульфідів або відновлення оксидів (залежно від виду плавки);
4) розплавлення легкоплавких компонентів з утворенням первинних розплавів;
5) розчинення більш тугоплавких складових у первинних розплавах з утворенням штейну або чорнового металу і шлаку;
6) розподіл цінних компонентів між продуктами плавки;
7) поділ рідких продуктів плавки.
Усі перелічені стадії рудної плавки проходять послідовно або одночасно з різними швидкостями і повнотою завершення. Найповільніша з елементарних стадій в кінцевому підсумку визначатиме сумарну швидкість плавки, а отже, і кінцеву продуктивність застосовуваного агрегату.
Слід відзначити, що з елементарних стадій плавки рудної сировини найбільш повільною буде остання - поділ рідких продуктів плавки. Цю стадію, здійснювану звичайно відстоюванням, можна прискорити шляхом інтенсивного перемішування розплавів, що приведе до збільшення питомої продуктивності плавильної печі.
Тестові питання
1. З чого складаються метали?
2. Як називається зв’язок між іонами і електронами?
3. Чим забезпечується пластичність металів?
4. Що характеризує теплопровідність металів?
5. Чим характерне поліморфне перетворення?
6. Від чого залежить відновна здатність і хімічна активність металу?
7. Від чого залежить спорідненість елементів до кисню?
8. В якому випадку твердий вуглець може бути енергійним відновником?
9. Як називають процеси отримання металів у результаті хімічних реакцій між сульфідами і оксидами?
10. Що таке позапічна металотермія?
11. Які катіони в першу чергу розряджаються на катоді під час електролізу водних розчинів?
12. Що є продукцією кольорової металургії?
13. Який процент виходу шлаків отримуємо при плавленні руд або концентратів?
14. Що таке штейн?
15. Які основні компоненти технологічних газів?
16. Що є основними продуктами гідрометалургійних процесів?
17. Що являють собою пеки?
18. Скільки і які види кеків буває?
19. Які основні технологічні процеси використовують при виробництві кольорових металів?
20. Які види випалювальних процесів використовують у кольоровій металургії?
21. Скільки видів і які бувають рудні плавки?
22. Які існують різновиди рафінувальних плавок?
23. З яких стадій складається гідрометалургійний процес?
24. Що служить паливом для кольорової металургії?
25. Що є сировиною для виробництва вогнетривких виробів?
26. Які основні вимоги повинні задовольняти сучасні металургійні процеси?
2 ФІЗИКО-МЕТАЛУРГІЙНІ ОСНОВИ
ЛЕГКИХ МЕТАЛІВ
2.1 Фізико-металургійні основи алюмінію
2.1.1 Виробництво алюмінію
За поширеністю в природі алюміній посідає перше місце серед металів; його вміст у земній корі становить 7,45%. Однак, незважаючи на значну поширеність у природі, алюміній до кінця XІ століття належав до рідких металів. У чистому вигляді алюміній не зустрічається внаслідок своєї високої хімічної активності. Він переважно зустрічається у вигляді сполук із киснем і кремнієм - алюмосилікатів.
Рудами алюмінію можуть служити лише породи, багаті глиноземом (А12О3) і такі, що залягають великими масами на поверхні землі. До таких порід відносять боксити, нефеліни - (Na, К)2О · Al2O3 · 2Sі2, алуніти – (Na, K)2SO4 ∙ ·A12(SO4)3·4A1(OH)3 і каоліни (глини), польовий шпат (ортоклаз) - K2О·А12О3·6SіO2.
Основною рудою для одержання алюмінію є боксити. Алюміній у них утримується у вигляді гідроокисів А1(OН), А1(OН)3, корунду А12О3 і каолініту А12О3·2SіO2·2Н2О. Хімічний склад бокситів складний: 28-70% глинозему; 0,5-20% кремнезему; 2-50% окису заліза; 0,1-10% окису титану. Останнім часом як руду стали застосовувати нефеліни – алуніти.
Нефелін (К·Na2O·А12О3·2SіО2) входить до складу апатитонефелінових порід (на Кольському півострові).
Уперше у вільному вигляді алюміній був виділений у 1825 р. датським фізиком Ерстедом шляхом впливу амальгами калію на хлорид алюмінію. У 1827 р. німецький хімік Велер удосконалив спосіб Ерстеда, замінивши амальгаму калію металевим калієм: АlСl3 + 3К → 3КС1 + А1 (реакція проходить з виділенням тепла). У 1854 р. Сент-Клер Девіль у Франції вперше застосував спосіб Велера для промислового виробництва алюмінію, використавши замість калію більш дешевий натрій, а замість гігроскопічного хлориду алюмінію - більш стійкий подвійний хлорид алюмінію й натрію. У 1865 р. російський фізик-хімік Н.Н.Бекетов показав можливість витиснення алюмінію магнієм з розплавленого кріоліту. Ця реакція у 1888 р. була використана для виробництва алюмінію на першому німецькому заводі в Гмелінгені. Виробництво алюмінію цими так названими "хімічними" способами здійснювалося з 1854 по 1890 рік. Протягом 35 років за допомогою цих способів було отримано в цілому близько 20 т алюмінію.
Наприкінці 80-х років позаминулого сторіччя хімічні способи замінив електролітичний спосіб, що дозволив різко знизити вартість алюмінію і створив передумови до швидкого розвитку алюмінієвої промисловості. Основоположники сучасного електролітичного способу виробництва алюмінію Еру у Франції і Хол у США незалежно один від одного подали у 1886 р. майже аналогічні заявки на патентування способу одержання алюмінію електролізом глинозему, розчиненого у розплавленому кріоліті. З моменту появи патентів Еру і Хола і починається сучасна алюмінієва промисловість, що більш ніж за 115 років свого існування виросла в одну з найбільших галузей металургії.
Технологічний процес одержання алюмінію складається із трьох основних стадій:
1) одержання глинозему з алюмінієвих руд;
2) одержання алюмінію із глинозему;
3) рафінування алюмінію.
2.1.2 Одержання глинозему з руд
Глинозем одержують трьома способами: лужним, кислотним і електролітичним. Найбільше поширення має лужний спосіб (метод К.І.Байєра, розроблений у Росії наприкінці позаминулого сторіччя й застосовуваний для перероблення високосортних бокситів з невеликою кількістю до 5-6% кремнезему). З того часу технічне виконання його було істотно поліпшене. Схема виробництва глинозему за способом Байєра подана на рис. 2.1.
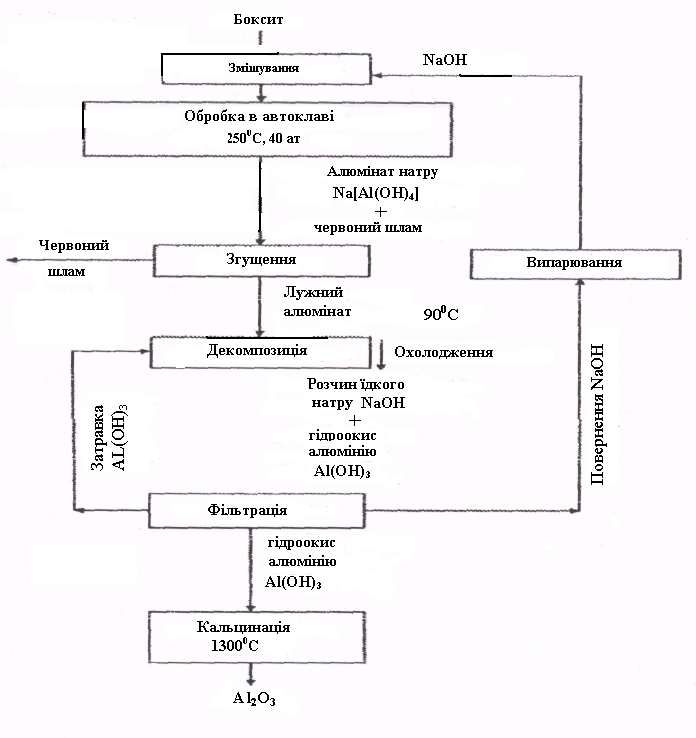
Рисунок 2.1 - Схема одержання окису алюмінію за способом Байєра
Сутність способу полягає в тому, що алюмінієві розчини швидко розкладаються при введенні в них гідроокису алюмінію, а розчин, що залишився від розкладання, після його випарювання в умовах інтенсивного перемішування при 169-170оС може знову розчиняти глинозем, що утримується в бокситах. Цей спосіб складається з таких основних операцій:
1) підготовки бокситу, що полягає в його дробленні й подрібнюванні у млинах; у млини подають боксит, їдкий луг і невелику кількість вапна, що поліпшує виділення А12О3; отриману пульпу подають на вилуджування;
2) вилуджування бокситу (останнім часом застосовувані до цього часу блоки автоклав круглої форми частково замінені трубчастими автоклавами, у яких при температурах 230-250°С (500-520 К) відбувається вилудження, що полягає в хімічному його розкладанні від взаємодії з водним розчином лугу; гідрати окису алюмінію при взаємодії з лугом переходять у розчин у вигляді алюмінату натрію:
AlOOH + NaOH → NaAl2+ Н2О,
Al(OH)3 + NaOH → NaAlО2 + 2H2O. (2.1)
Кремнезем, що міститься у бокситі, взаємодіє з лугом і переходить у розчин у вигляді силікату натрію:
SіО2 + 2NaOH →Na2SіО3 + H2O. (2.2)
У розчині алюмінат натрію й силікат натрію утворюють нерозчинний натрієвий алюмосилікат; у нерозчинний залишок переходять окисли титану й заліза, що віддають залишок червоного кольору; цей залишок називають червоним шламом. По закінченні розчинення отриманий алюмінат натрію розбавляють водним розчином лугу при одночасному зниженні температури на 100°С;
3) відділення алюмінатного розчину від червоного шламу звичайно здійснюється шляхом промивання у спеціальних згущувачах, у результаті цього червоний шлам осідає, а алюмінатний розчин зливають і потім фільтрують (освітлюють). В обмежених кількостях шлам знаходить застосування, наприклад, як добавка до цементу. Залежно від сорту бокситів на 1 т отриманого оксиду алюмінію припадає 0,6-1,0 т червоного шламу (сухого залишку);
4) розкладання алюмінатного розчину виконують шляхом фільтрації і перемішування у великих ємностях з мішалками (декомпозити). З пересиченого розчину при охолодженні на 60°С (330 К) і постійному перемішуванні видаляється гідрооксид алюмінію А1(ОН)3. Оскільки цей процес відбувається повільно й нерівномірно, а формування й ріст кристалів гідроокису алюмінію мають велике значення при її подальшій обробці, у декомпозити додають велику кількість твердого гідроокису - запалу:
Na2O·А12О3 + 4Н2О → Al(OH)3+2NaOH; (2.3)
5) виділення гідроокису алюмінію і його класифікації; це відбувається у гідроциклонах і вакуум-фільтрах, де від алюмінатного розчину виділяють осад, що містить 50-60% часток А1(ОН). Значну частину гідроокису повертають у процес декомпозиції як затравочний матеріал, що і залишається в обороті в незмінних кількостях. Залишок після промивання водою йде на кальцинацію, фільтрат також повертається в оборот (після концентрації у випарних апаратах - для вилуджування нових бокситів);
6) зневоднювання гідроокису алюмінію (кальцинації); це завершальна операція виробництва глинозему. Її здійснюють у трубчастих обертових печах, а останнім часом також у печах з турбулентним рухом матеріалу при температурі 1150-1300°С; сирий гідроокис алюмінію, проходячи через обертову піч, висушується й зневоднюється; при нагріванні відбуваються послідовно такі структурні перетворення:
A1(OH)3 →A1OOH → γ-А12О3 → α-А12О3
200 °С 950°С 1200°С.
У остаточно прожареному глиноземі утримується 30-50% α-А12О3 (корунд), інше γ-А12О3.
Цим способом витягується 85-87% від усього одержуваного глинозему. Отриманий окис алюмінію становить міцну хімічну сполуку з температурою плавлення 2050°С.
2.1.3 Одержання алюмінію з його окису
Електролітичне відновлення окису алюмінію, розчиненого в розплаві на основі кріоліту, здійснюється при 950-970°С у електролізері. Електолізер складається з футерованої вуглецевими блоками ванни, до поду якої підводиться електричний струм (рис.2.2).
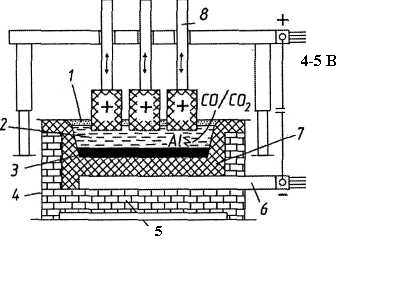
Рисунок 2.2 - Схема електролізної ванни: 1 - окис алюмінію (Al2O3); 2 - кріолітоглиноземний розплав; 3 - рідкий алюміній;
4 - ванна зі сталевого листа; 5 - шамот; 6 - струмопровідна шина; 7 - вугільні подові блоки; 8 – аноди
Рідкий алюміній, що виділився на поді, служить катодом важче розплаву солі електроліту, тому збирається на вугільній основі, звідки його періодично відкачують. Зверху в електроліт занурені вугільні аноди, які згоряють в атмосфері алюмінію, що виділяється з окису кисню, виділяючи окис вуглецю (СО) або двоокис вуглецю (СО2) (рис. 2.3) . На практиці знаходять застосування два типи анодів:
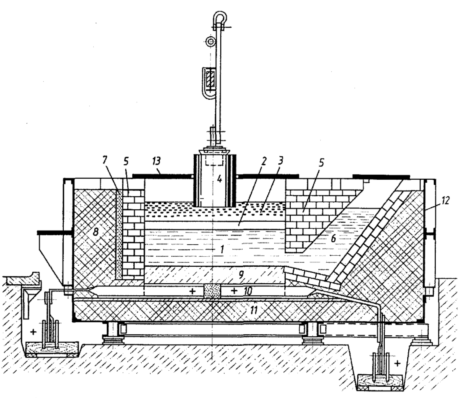
Рисунок 2.3 - Схема електролізера: 1 - алюмінієвий розплав;
2 - електроліт; 3 - рафінований алюміній високої чистоти;
4 - катод із графіту; 5 - магнезитова стіна; 6 - передній горн;
7 - ізолюючий шар; 8 - бічна ізоляція; 9 - вугільний под;
10 - анодний струмопідвід; 11 - ізоляція поду; 12 - залізний короб; 13 - кришка
а) аноди, що само обпалюються, складаються із брикетів, так званих "хлібів" маси Зедерберга (малозольне вугілля з 25-35% кам'яновугільного пеку), набитих в алюмінієву оболонку; під дією високої температури анодна маса обпалюється (спікається);
б) обпалені, або "безперервні", аноди з більших вугільних блоків (наприклад, 1900,600,500 мм масою близько 1,1 т).
Сила струму на електролізерах становить 150000 А. Вони включаються в мережу послідовно, тобто виходить система (серія) - довгий ряд електролізерів.
Робоча напруга на ванні, що становить 4-5 В, значно вища напруги, при якій відбувається розкладання окису алюмінію, оскільки в процесі роботи неминучі втрати напруги в різних частинах системи.
Окис алюмінію перетворюється спочатку у хлорид алюмінію. Потім у щільно ізольованій ванні відбувається електроліз АlСl3, розчиненого в розплаві солей КСl, NaCl. Хлор, що виділяється при цьому, відсмоктується й подається для вторинного використання; алюміній осаджується на катоді.
Перевагами даного методу перед існуючим електролізом рідкого кріолітоглиноземного розплаву (А12О3, розчинений в кріоліті Na3Al6) вважають: економію до 30% енергії; можливість застосування окису алюмінію, що не придатний для традиційного електролізу (наприклад, АlО3 з високим вмістом кремнію); заміну дорогого кріоліту більш дешевими солями; зникнення небезпеки виділення фтору.
2.1.4 Відновлення хлориду алюмінію марганцем
При відновленні марганцем із хлориду алюмінію звільняється алюміній.
За допомогою керованої конденсації з потоку хлориду марганцю виділяються пов'язані із хлором забруднення. При звільненні хлору хлорид марганцю окиснюється в окис марганцю, що потім відновлюється до марганцю, придатного до вторинного застосування.
2.1.5 Одержання рафінованого алюмінію
Для алюмінію рафінуючий електроліз з розкладанням водних сольових розчинів неможливий. Оскільки для деяких цілей ступінь очищення промислового алюмінію (А1 99,5 - А1 99,8), отриманого електролізом кріолітоглиноземного розплаву, недостатній, то із промислового алюмінію або відходів металу шляхом рафінування одержують ще більш чистий алюміній (А1 99, 99 R). Найбільш відомий метод рафінування - тришаровий електроліз.
2.1.5.1 Рафінування методом тришарового
електролізу
Обтягнута сталевим листом, що працює на постійному струмі, ванна для рафінування складається з вугільного поду із струмопідведеннями й теплоізоляційним магнезитовим футеруванням. На противагу електролізу кріолітоглиноземного розплаву анодом тут служить, як правило, розплавлений рафінуючий метал (нижній анодний шар). Електроліт складається із чистих фторидів або суміші хлориду барію й фторидів алюмінію й натрію (середній шар). Алюміній, що розчиняється з анодного шару в електроліті, виділяється над електролітом (верхній катодний шар). Чистий метал служить катодом. Підведення струму до катодного шару здійснюється графітовим електродом.
Ванна працює при температурі 750-800°С, витрата електроенергії становить 20 кВт/год на 1 кг чистого алюмінію, тобто трохи вище, ніж при звичайному електролізі алюмінію. Метал анода містить 25-35% Сu; 7-12% Zn; 6-9% Si; до 5% Fe і незначну кількість марганцю, нікелю, свинцю й олова, усе інше (40-55%) – алюміній. Всі важкі метали і кремній при рафінуванні залишаються в анодному шарі. Наявність магнію в електроліті приводить до небажаних змін складу електроліту чи до сильного його обшлакування. Для очищення від магнію шлаки, які містять магній, обробляються флюсами або газоподібним хлором.
У результаті рафінування одержують чистий алюміній (99,99%) і продукти сегрегації (зайгер-продукт), який містить важкі метали і кремній, вони виділяються у вигляді лужного розчину і кристалічного залишку. Лужний розчин є відходом, а твердий залишок застосовується для розкислення.
Рафінований алюміній звичайно має такий склад, %: Fe 0,0005-0,002; Si 0,002-0,005; Сu 0,0005-0,002; Zn 0,0005-0,002; Аl – усе інше.
Рафінований алюміній переробляють у напівфабрикат у зазначеному складі або легують магнієм.