О. Й. Любич, В. О. Пчелінцев Фізичні основи металургії кольорових І рідкоземельних металів
Вид материала | Документы |
- З дисципліни «Теоретичні основи ливарного виробництва» для студентів заочного факультету, 390.98kb.
- Програма, методичні вказівки та контрольні завдання з дисципліни " виробництво виливків, 797.9kb.
- Нова технологія утилізації гальваношламів машинобудівних підприємств з одержанням комплексних, 26.76kb.
- І містять у собі чорні або кольорові метали чи їх сплави, а також вироби з металу,, 462.13kb.
- Наказом Державного комітету України з питань регуляторної політики та підприємництва,, 341.66kb.
- Розробка базових теплотехнічних І конструктивних рішень, а також технологічних схем, 24.73kb.
- Назва реферату: Зварювання кольорових металів Розділ, 29.07kb.
- Робоча програма загальні методичні вказівки та індивідуальні завдання до вивчення дисципліни, 156.9kb.
- Типова програма кандидатського іспиту із спеціальності, 95.6kb.
- Державна митна служба україни, 19.16kb.
2.2 Фізико-металургійні основи титану
2.2.1 Отримання титану з ільменітових руд
Сировиною для отримання титану є титано-магнетитові руди, з яких виділяють ільменітовий концентрат, що містить 40-45% ТіО2, близько 30% FeO, 20 % Fe2О3 і 5-7 % пустої породи. Назву цей концентрат одержав за наявності у ньому мінералу ільменіту FeO·TiO2. Важливим джерелом ільменіту є титаномагнетит FeTiO2.
В Україні титанові руди розвідані в межах Українського кристалічного щита. Іршанське родовище (Житомирська область), на базі якого працює Іршанський комбінат із збагачення ільменіту, є одним з наймогутніших. Значний інтерес становить родовище титанових руд у Дніпропетровській області (у басейні р. Самоткан), де запаси їх практично необмежені.
Відомо декілька способів отримання титану з руд. Одна з часто застосовуваних схем наведена на рис. 2.4.
Основним матеріалом для виробництва титану є ільменітова руда.
Титанові руди піддають збагаченню, в результаті якого одержують концентрати з підвищеним вмістом TiО2. При переробці ільменітових руд кількість TiО2 в концентратах досягає 60%. Зразковий склад ільменітового концентрату: 50,8 % TiО2, 36,40 % FeO, 7,86 % Fe2O3, 1,18 % А12О3, 0,05 % Cr2O3, 1,86 % SiO2, 0,69 % МаО, 0,68 % МnО, 0,18 % СаО.
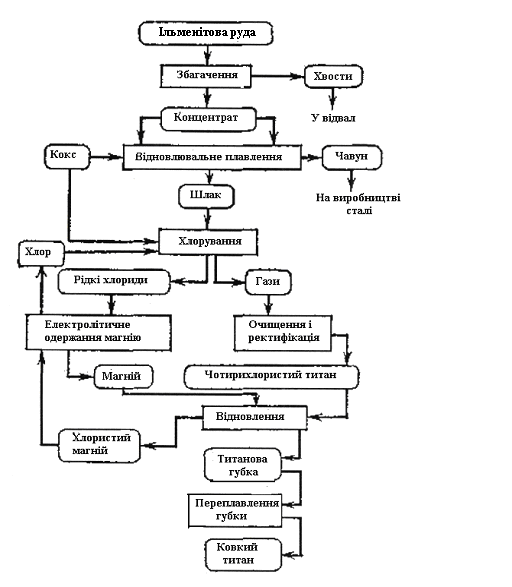
Рисунок 2.4 - Схема отримання титану з ільменітової руди
Одержаний після збагачення руди електромагнітним або гравітаційним способом концентрат у суміші з деревним вугіллям, антрацитом піддають відновному плавленню в електродуговій печі з метою видалення оксидів заліза. Для цього концентрат суміші з коксом плавлять і витримують в печі при 17000С. У результаті зіткнення з вуглецевомістким і матеріалами оксиди заліза і титана відновлюються за реакцією
3(FeO·TiO2)+ 4С = 3Fe + Ti3O5 + 4CO. (2.5)
При цьому залізо відновлюється, навуглецьовується і утворює побічний продукт - чавун, який збирається на дні ванни печі, відділяючись від решти маси шлаку, внаслідок відмінності їх питомої ваги, а оксид титану TiO2 переходить у шлак. Чавун і шлак розливають окремо у виливниці. Основний продукт цього процесу - титановий шлак – містить 80-90 % ТiO2,2-5 % FeO і домішки - SiO2, Al2O3, СаО та ін. Побічний продукт цього процесу – чавун – використовують у металургійному виробництві.
Одержаний титановий шлак брикетують з коксом і піддають хлоруванню у спеціальних шахтних печах електроопору (рис. 2.5) при температурі 600°С.
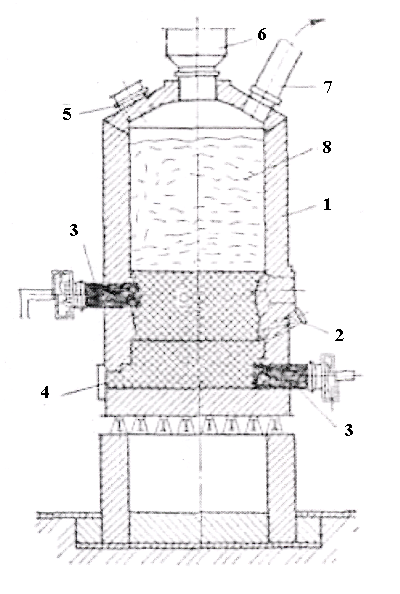
Рисунок 2.5 – Схема електропечі для хлорування титану:
1 – корпус з шамотним футеруванням; 2 – графітові електроди;
3 – завантажувальний пристрій; 4 – патрубок для відводу парогазової суміші; 5 – брикети шихти; 6 – вугільна набивка електроопору; 7 – патрубок для подачі хлору
У нижній частині печі розташовують вугільну насадку, що нагрівається при пропусканні через неї електричного струму. У піч подають брикети титанового шлаку, а через фурми всередину печі - хлор.
За наявності вугілля титан з діоксиду переходить в тетрахлорид:
TiO2 + 2Сl2 + С = TiCl4 + СО2. (2.6)
Тетрахлорид титану плавиться при температурі - 23°С і кипить при +136°С. Тому в умовах печі він інтенсивно випаровується і, захоплюючи за собою летючі хлориди домішок (SiCl4, MgCl2, FeCl3 та ін.), прямує в конденсаційну установку. Наявність в установці ряду секцій з різним
перепадом температур дозволяє розділити хлориди завдяки відмінності температур кипіння і таким чином виділити чотирихлористий титан, який далі піддають очищенню методом ректифікації у спеціальних установках.
Малолеткі хлориди магнію, кальцію та інших металів утворюють рідину, з якої електролізом одержують магній і хлор.
Найважливішу технологічну операцію - отримання металевого титану – здійснюють такими методами: розкладанням чотирихлористого титану натрієм або магнієм; відновленням двоокису і тетрахлориду титану кальцієм; електролізом хлористих і фтористих сполук титану.
У даний час металевий титан досить часто одержують відновленням чотирихлористого титану магнієм.
Чотирихлористий титан T1CI4 відновлюють у сталевих ретортах діаметром до 1,5 і заввишки до 3 м. Реторта встановлюється в електропіч опору, з неї відкачується повітря і замість нього подається аргон. Потім піч нагрівають до 750-800°С і в реторту заливають рідкий тетрахлорид титану і магній.
Титан відновлюється за реакцією
TiCl4 + 2Mg = Ti + 2MgCl2. (2.5)
Після інтенсивного розвитку реакції вимикають нагрів і підтримують температуру в межах 750-850°С, регулюючи швидкість подачі тетрахлориду титану. Тверді частинки відновленого титану спікаються в пористу масу - губку, що відкладається на стінках реторти. Рідкий хлористий магній періодично випускають через патрубок у днищі реторти, оскільки його об'єм в 10 разів перевищує об'єм одержуваної титанової губки. За один раз зливають 100-200 кг хлористого магнію, який направляють в електролізний цех для отримання металевого магнію.
Після введення розрахункової кількості ТіСl4 і загасання реакції включають обігрів і витримують реторту ще протягом 1 години при температурі 900°С для завершення відновлення.
Весь процес відновлення, у заводських умовах займає 30-35 годин. Потім реторту витягують з печі краном і охолоджують на окремому стенді декілька годин до температури 20-40°С.
Для розділення продуктів реакції, що складаються з титанової губки (50-70%), залишку хлористого магнію (15-20%), що заповнює пори губки, і надлишку магнію (30-35%), користуються різницею тиску їх пари при температурі 900°С у вакуумі.
У цих умовах тиск пари титану дуже малий; тиск пари хлориду магнію - близько 1 кПа, металевого магнію – близько 10 кПа. Кришку реторти знімають і укріплюють замість неї охолоджуваний водою конденсатор.
Дистиляцію магнію і хлориду магнію проводять при температурі 900°С і залишковому тиску близько 0,1 Па протягом декількох десятків годин. Потім реторту знову повільно охолоджують, відкривають і пневматичними зубилами вибивають з неї титанову губку, оскільки вона часто щільно приварюється до стінок реторти. Відокремлений дистиляцією магній знову використовують як відновник титану.
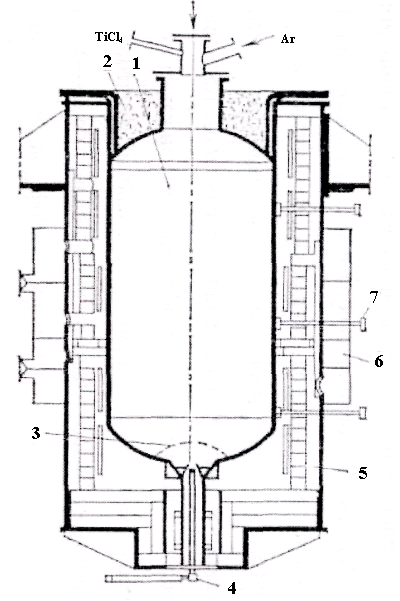
Рисунок 2.6 - Електропіч і реактор для відновлення тетрахлориду титану: 1 - реактор; 2- кришка з теплоізоляцією; 3 - патрубок для заливки магнію; 4- труба для введення чотирихлористого титану; 5 - електропіч опору; 6 - колектори для подачі охолоджуваного повітря; 7-замочний пристрій для зливу хлористого магнію
Титанову губку дроблять і ретельно сортують. Найчистішу губку спрямовують на переплавлення; низькосортну, що містить включення, хлоридів, брикетують і використовують як розкиснювач сталі у чорній металургії. Для отримання з титану і його сплавів відповідальних виробів дуже важливі його хороша пластичність і зварюваність, а також термостійкість. Тому в титановій губці не повинно бути більше 0,012 Cl2, 0,1% О2 і 0,04% N2.
2.2.2 Плавлення титанової губки
Для отримання компактних зливків титану губку плавлять у вакуумній дуговій печі, щоб уникнути забруднення титану газами повітря. Матеріал тигля також може забруднити титан, тому плавлення ведуть у мідному кристалізаторі, стінки якого охолоджуються водою. Твердіючи близько холодних стінок, титан не сплавляється з міддю.
Зливок титану, поміщений на піддон кристалізатора, служить одним полюсом дуга постійного струму; електрод, що витрачається, з пресованої губки титану служить звичайно іншим полюсом, який опускають в кристалізатор зверху. Титановий електрод плавиться і тому називається тим, що витрачається. Стабілізацію дуги в печі і перемішування рідкого металу здійснюють за допомогою соленоїда, що оточує плавильний простір кристалізатора. Схема вакуумної дугової печі (ВДП) для плавлення з електродами, що витрачаються, показана на рис. 2.7. Вона має пристрій для вертикального переміщення електрода, а іноді і опускання дна піддону мідного кристалізатора. Перед початком плавлення електрод, що витрачається, ретельно сушать і з плавильного простору печі відкачують повітря до залишкового тиску, що дорівнює ~7 Па. Опускаючи електрод, запалюють дугу і розтягують її полем соленоїда, проводячи плавлення при щільності струму 7-10 А/см2 (при діаметрі зливка 300-500 мм). Повільно опускаючи електрод, що витрачається, одержують зливок титану більшого перетину, який приварюють до утримувача електрода іншої печі, і повторюють переплавлення.
Як при першому, так і при другому плавленні з електродом, що витрачається, довжину дуга витримують 20-35 мм, напругу 30 В. Для отримання сплавів титану з алюмінієм, марганцем, ванадієм, хромом та іншими металами легуючі добавки домішують до губки, що надходять на виготовлення електроду для першої плавки. При другому плавленні вони остаточно і досить рівномірно
![]() Рисунок 2.7 - Схема вакуумно-дугової печі з електродом, що витрачається: 1 – електрод, що витрачається; 2 – охолоджуваний водою кристалізатор; 3 – зливок титану; 4 – розплавлений титан; 5 – мідний охолоджуваний водою піддон; 6 - вакуумна камера; 7 – струмопровід | розподіляються в об'ємі зливка. Звичайна чистота титану, що отримують переплавленням губки, становить 99,6-99,7%. Для отримання чистішого металу потрібне додаткове рафінування. Титан з меншим вмістом домішок одержують методом йодидного очищення, що базується на термічній дисоціації чотирийодистого титану Тil4 на поверхні титанового дроту, нагрітого пропусканням електричного струму до 1300-1400°С. Титан, що виділяється при цьому, осідає на дроті, поступово перетворюючи її в пруток. Цей спосіб очищення дуже ефективний, але має малу продуктивність. Тому йодидний титан відрізняється високою вартістю. |
2.2.3 Отримання титану високої чистоти
Титан, отриманий переплавленням губки, становить 99,6-99,7%, однак потрібен і чистіший метал, що містить близько 99,9% титану. Чистий титан отримують у невеликих кількостях переробкою губки йодидним способом, що використовує оборотність реакції
Ti + 2l2 < = >Til4. (2.8)
При температурі 100-200°С реакція проходить вправо, а при 1300-1400 – вліво.
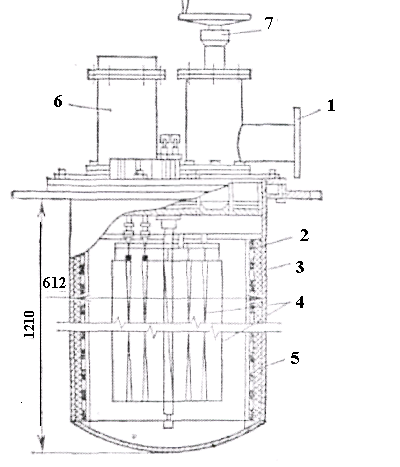
Рисунок 2.8 - Схема установки отримання титану високої чистоти 1 – фланець для приєднання до вакуумної системи; 2 – молібденова сітка; 3 – стінка реактора; 4 – багатопетльовий нагрівач з чистого титану; 5 – титанова губка; 6 – випарник для йоду; 7 – вентиль вакуумного насоса
Губку завантажують в кільцевий простір між стінкою реторти і молібденовою сіткою. На молібденових утримувачах зигзагоподібно закріплюють дріт з чистого титану діаметром 3-4 мм і завдовжки близько 10 м. Після герметизації кришки і відкачування повітря до залишкового тиску 0,1-0,001 Па реторту поміщають в термостат з температурою 100-200°С і всередині її особливим пристроєм розбивають ампулу з йодом. Пари йоду, заповнюючи весь простір реторти, реагують з титановою губкою, утворюючи пари йодного титану. Титановий дріт нагрівають до 1300-1400°С, пропускаючи через нього струм. На розжареному дроті ці пари розкладаються, утворюючи кристали чистого титану, і вивільняють йод, який знову реагує з холоднішою титановою губкою.
2.3 Фізико-металургійні основи магнію
2.3.1 Магній в земній корі
Магній - один з найпоширеніших у земній корі елементів, він посідає VI місце після кисню, кремнію, алюмінію, заліза і кальцію. У літосфері (за А.П.Виноградовим) вміст магнію становить 2,1%. У природі магній зустрічається тільки у вигляді сполук. Він входить до складу багатьох мінералів: карбонатів, силікатів та ін. До найважливіших із таких мінералів відносять, зокрема, вуглекислі карбонатні породи, що створюють величезні масиви на суші і навіть цілі гірські хребти - магнезит MgCO3 і доломіт MgCO3(CaCO)3. Під шарами різних наносних порід разом з покладами кам'яної солі відомі колосальні поклади й іншого легкорозчинного магнійвмісного мінералу - карналіту MgC12(KC1·6H2O) (у Солікамську, наприклад, пласти карналіту досягають потужності до 100 м). Крім того, у багатьох мінералах магній тісно зв'язаний з кремнеземом, утворюючи, наприклад, олівін [(Mg, Fe)2SiO4] і, що рідше зустрічається, форстерит (Mg2SiO4). Інші магнійвмісні мінерали - це бруцит Mg(OH)2, кізерит MgSO4, епсоміт MgSO4·7H2O, каїніт MgSO4(KCl·3H2O). На поверхні Землі магній легко утворює водні силікати (тальк, азбест та ін.), зразком яких може служити серпентин 3MgO(2SiO2·2H2O); із відомих науці 1500 мінералів близько 200 (більше 13%) містять магній. Проте природні сполуки магнію широко зустрічаються і в розчиненому вигляді. Окрім різних мінералів і гірських порід, 0,13% магнію у вигляді MgCl2 постійно містяться у водах океану (його запаси тут невичерпні - близько 61016 т) і в солоних озерах і джерелах. У рослинних і тваринних організмах магній міститься в кількостях порядку сотих часток відсотка, а до складу хлорофілу входить до 2% Mg. Загальний вміст цього елемента в живій речовині Землі оцінюється величиною близько 1011 тонн. При нестачі магнію припиняються ріст і розвиток рослин. Накопичується він переважно у насінні. Введення магнієвих сполук у грунт помітно підвищує врожайність деяких культурних рослин (наприклад, буряка).
У компактній формі і у відчутних кількостях магній був уперше отриманий у 1828 р. Антуаном Олександром Брутом Буссі (1794-1882) шляхом нагрівання суміші безводного MgCl2 з калієм у скляній трубці. У результаті реакції калій з'єднався з хлором, витісняючи магній з утворенням КС1 і Mg. З цих дослідів почався перший етап металургії магнію, який повністю ґрунтувався на хімічних методах. За технологією, схожою з методом Брута Буссі, у Франції, Англії і Сполучених Штатах працювали невеликі заводи, що виробляли металевий магній. Таке виробництво існувало до кінця минулого століття, поки не був створений електролітичний спосіб отримання магнію. Конкурувати з ним хімічний спосіб не зміг, оскільки використовував дорогі відновники - металевий натрій і калій, крім того, при хімічному способі не вдавалося створити періодичний технологічний процес.
2.3.2 Електролітичний спосіб отримання магнію
У 1830 р. Майкл Фарадей отримав декілька грамів металевого магнію шляхом пропускання електричного струму через розплав MgCl2. У 1852 р. цей метод був детально досліджений і вдосконалений Робертом Бузеном (1811-1897рр.), який також здійснив перше масове виробництво магнію. За допомогою його електролізера, що складається з фарфорового тигля і двох вугільних електродів пилкоподібної форми, занурюваних зверху в розплав зневодненого MgCl2, йому вдавалося всього за декілька секунд отримувати «корольок» магнію вагою в декілька грам. Пилкоподібна форма електродів була необхідна для утримання капельок магнію, щоб уникнути їх підйому на поверхню і самозайманню. При цьому принципове значення для підвищення продуктивності грало повне зневоднення MgCl2.
Технологія електролітичного отримання магнію за час свого застосування піддалася значним удосконаленням,
проте її принципи, природно, залишилися без кардинальних змін.
Сучасне апаратурне оформлення електролітичного виробництва магнію принципово мало чим відрізняється від першого магнієвого електролізера промислового типу на 300 А, розробленого Гретцелем і застосованого їм уперше в 1883 р.
Основною сировиною для отримання магнію служать магнієві руди і карналіт MgCl2·KCl·6H2O, магнезит MgCl3, доломі MgCl3 ·CaCO3, бішофіт MgCl2·6H2O.
Найпоширеніший спосіб отримання магнію – електролітичний – складається з двох процесів – отримання хлористого магнію MgCl2 і його електролізу. Основна сировина для отримання магнію в нашій країні – карналіт. З метою збагачення подрібнений карналіт обробляють гарячою водою. При цьому хлориди MgCl2 і КСl переходять в розчин, охолоджуючи який одержують кристали штучного карналіту. Для видалення вологи його спочатку обпалюють у печах з «киплячим» шаром, а потім плавлять в електропечах.
У разі використання як сировини магнезиту і доломіту їх спочатку обпалюють, а потім піддають хлоруванню за наявності вуглецю, одержуючи хлористий магній MgCl2.
Електроліз хлористого магнію здійснюють у футерованих шамотом електролізерах, що складаються з ряду комірок, що включають вугільний анод 4 (рис. 2.9) і два катоди у вигляді сталевих пластин 2. У верхній герметизуючій частині комірки анодний простір відокремлений від катодного шамотною перегородкою для збирання і відведення хлору, що виділяється. Електролітом для отримання магнію служить розплав солей MgCl2, СаCl2, NaCl, KCl з додаванням NaF і KF. Електроліз проводять при температурі 720°С, напруженні струму близько 3 В і силі 30-50 кА. Витрата електроенергії на отримання 1 т магнію становить 15-17 тис. кВт · год.
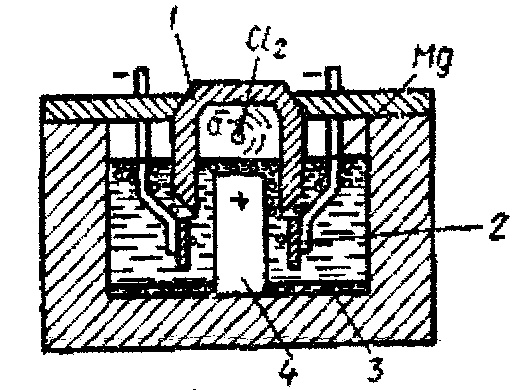
Рисунок 2.9 – Схема електролізера для отримання магнію
Іони магнію, що утворюються у результаті електролізу, розряджаються на катодних пластинах 2, збираються у краплі і спливають на поверхню електроліту. Рідкий магній періодично видаляють вакуум-ковшом. Іони хлору розряджаються на аноді і виходять на поверхню під перегородку 1, звідки відкачуються насосом. На дні ванни утворюється шлак 3.
2.3.3 Термічний спосіб отримання магнію
Думка про можливість отримання металевого магнію шляхом відновлення його оксиду за допомогою вугілля виникла порівняно давно – у 80- х рр. позаминулого століття, однак реалізація цього процесу у відчутних масштабах стала можливою тільки в 30-ті рр. минулого сторіччя. Карботермічний спосіб базується на оборотності реакції MgO+C+153 ккал CO+Mg, рівновага якої при дуже високих температурах вище 20000С зміщено вправо.
Основна методична перешкода, що виникала на шляху вирішення цієї проблеми, була пов'язана з тим, що коли суміш MgO і С нагрівали до високої температури, відновлення магнію дійсно відбувалося, але при поступовому охолоджуванні продуктів реакції (пароподібного Mg і С) знову утворювалися вихідні продукти – MgO і С. Було знайдено таке рішення: пароподібний магній і СО сталі розбавляти великим об'ємом холодних відновних газів при різкому зниженні температури з 25000С до 2000С. Таким чином здійснюється «гартування» продуктів реакції, що запобігає їх зворотній взаємодії, і в конденсаторі утворюється твердий порошкоподібний магній, так звана «пусьєра».
На даний час практично процес проводять, розжарюючи суміш MgO (одержуваної випаленням природного магнезиту) з антрацитом у дуговій електричній печі. Пари, що виділяються, негайно розбавляють великим об'ємом сильно охолодженого водню. Металевий магній (що містить домішки MgO і С), що звільняється у вигляді пилу, потім переплавляють. Отримуваний так само метал характеризується високою чистотою (99,97%).
Карботермічний спосіб не зіграв помітної ролі в історії виробництва магнію. Незважаючи на свою принципову простоту, він не зміг конкурувати з електролітичним способом з таких причин:
1) питома витрата електрики при застосуванні карботермічного способу виявилася не нижче, ніж в
електролітичному способі;
2) електролітичний процес безперервний на всіх стадіях, тоді як карботермічний періодичний;
3) операції з перероблення вибухонебезпечної пусьєри у компактний магній складні і трудомісткі.
Значну роль в історії магнію зіграв інший
термічний спосіб його отримання – силікотермічний (відновлення MgO кремнієм з отриманням вільного Mg). У 1917 р. Гросвенов запропонував відновити MgO елементарним кремнієм при нормальному тиску в атмосфері Н2. Відновлення MgO кремнієм і кремнеалюмінієвими сплавами у вакуумі вперше досліджували в 1925 р. П.Ф.Антипін і А.А.Моїсєєв.
Силікотермічний спосіб виробництва магнію так само, як і карботермічний, почав запроваджуватися у промисловості перед Другою світовою війною і став широко застосовуватися під час війни, коли необхідно було швидко вводити в експлуатацію нові магнієві заводи. Цьому сприяли поширеність дешевої сировини для такого виробництва і порівняльна простота технології силікотермічного способу. У технології, прийнятій для промислового здійснення цього процесу, вихідною сировиною служить обпалений доломіт, а відновником - феросиліцій із вмістом не менше 75% Si. Суміш цих речовин розжарюють під сильно зменшеним тиском вище 2000С. Реакція в цих умовах йде за рівнянням 2(CaO(MgO)+Si)+124 ккал=Са2SiO4 + Мg причому єдиним летючим її продуктом є пари магнію.
За минулі з того часу десятиліття силікотермічний спосіб промислового отримання магнію був істотно вдосконалений - від малопродуктивних, періодично працюючих реторт із зовнішнім нагрівом до безперервно діючих електротермічних установок, обладнаних сучасними засобами механізації і автоматизації.
Можливість застосування поширеної і дешевої магнієвої сировини (магнезит, доломіт), різке скорочення шляху від руди до металу, нешкідливість виробництва, відсутність необхідності в постійному струмі й інші позитивні якості роблять силікотермічний спосіб виробництва магнію в його сучасному технологічному рішенні перспективним, причому, ймовірно, в першу чергу для тих країн, які не мають в своєму розпорядженні джерела хлормагнієвої сировини для електролізу.
Правда, сумарна витрата електроенергії на 1 кг силікотермічного магнію (внаслідок великої витрати її на виробництво відновника - феросиліцію) не нижча, а навіть декілька вища, ніж витрата електроенергії на 1 кг електролітичного магнію, тобто становить трохи більше 20 кВт·год електроенергії змінного струму на 1 кг товарного металу.
Ця обставина, а також надійність та масштабність електролітичного способу виробництва магнію не дозволяють поки успішно конкурувати з ним силікотермічному способу при нагоді вільного вибору між ними. Проте значення термічних методів отримання магнію з кожним роком зростає.
Отриманий чорновий магній містить до 2-5% різних домішок. Тому звичайно його піддають рафінуванню – переплавленню з флюсами, що містять хлориди магнію, барію, калію, натрію та ін. Переплавлення здійснюється в електропечах при температурі 720°С протягом 0,5-1 год. Перемішування розплаву сприяє розчиненню домішок у флюсі, спливанню їх і переходу в шлак. Чистота рафінованого магнію досягає 99,9 %.
Глибше очищення магнію можна здійснити його сублімацією (сублімацією) у вакуумі.
2.3.4 Застосування магнію
Найбільш ранньою галуззю застосування металевого магнію було, мабуть, використання його як відновника.
У 1965 р. Н.Н.Бекетов вперше застосував магній для витіснення з його допомогою алюмінію з розплавленого кріоліту. Цей процес у 80-ті роки минулого століття застосовувався промислово на першому німецькому алюмінієвому заводі в Гмелінгене.
Трохи пізніше почали використовувати здатність порошку магнію і тонкої магнієвої стрічки горіти сліпуче білим полум'ям з виділенням великої кількості тепла. Ця властивість магнію одержала застосування у фотографії для моментальних зйомок, а також у піротехніці і для військових цілей (для виготовлення освітлювальних ракет). У обох випадках магній звичайно змішується з речовинами, що легко віддають кисень. Ракетний освітлювальний склад, наприклад, може містити 45% Mg, 48% NaNO3 і 7% зв'язувальної органічної речовини.
Найважливішим практичним застосуванням магнію було використання його як основи різних легких сплавів. Потім він став використовуватися і в інших галузях техніки, завдяки своїм специфічним фізико-хімічним і механічним властивостям. У міру розвитку металургії магнію його одержували все у чистішому вигляді, що відкривало для цього металу нові галузі застосування.