Конспект лекций минск 2011 удк 629. 3
Вид материала | Конспект |
Содержание5.4 Требования, предъявляемые к специализированному оборудованию 5.5 Управление качеством то и tp автомобилей на атп 5.6 Система организации и управления производством ТО и ремонта |
- Конспект лекций Омск 2002 удк 629. 424., 467.89kb.
- Конспект лекций 2011 г. Батычко В. Т. Семейное право. Конспект лекций. 2011, 1718.16kb.
- Конспект лекций 2011 г. Батычко Вл. Т. Конституционное право зарубежных стран. Конспект, 2667.54kb.
- Конспект лекций Соответствует государственному образовательному стандарту высшего профессионального, 899.55kb.
- Конспект лекций Батычко Вик. Т таганрог 2011, 2102.18kb.
- Конспект лекций Батычко Вик. Т. Таганрог 2011, 3565.99kb.
- Конспект лекций 2011 г. Батычко Вл. Т. Международное частное право. Конспект лекций., 3144.86kb.
- Краткий конспект лекций Кемерово 2002 удк: 744 (075), 1231.26kb.
- Тверская ул., д. 11, Москва, гсп-3, 125993. Тел. 629-32-39, 629-74-51, 216.76kb.
- Конспект лекций для студентов специальности 080504 Государственное и муниципальное, 962.37kb.
5.4 Требования, предъявляемые к специализированному оборудованию
Характеристики специализированного оборудования должны соответствовать типу, массовым и габаритным параметрам колесного транспортного средства или его систем, для которых это оборудование применяется.
- Специализированное оборудование должно обеспечивать выполнение требований безопасности, предусмотренных общими техническими регламентами.
- В конструкциях передвижного оборудования, предназначенного для монтажа, демонтажа, подъема и опускания, транспортирования сборочных единиц и агрегатов или колесного транспортного средства в целом, должно быть предусмотрено устройство, удерживающее оборудование от самопроизвольного смещения на ровном твердом покрытии.
4. В конструкциях органов управления, предназначенных для включения специализированного оборудования, должны быть предусмотрены средства защиты от случайного включения.
5. Специализированное оборудование с автоматическим
(программным) управлением не должно начинать выпол-
нение исполнительских технологических операций (вывод
диагностируемого колесного транспортного средства или
его системы на заданный режим, подкачка сжатого воздуха
в шины и проч.) без команды подтверждения персонала.
6. Предохранительные клапаны гидравлических домкратов с
ручным приводом, гидравлических, электрогидравличе-
ских и плунжерных подъемников, маслораздаточных коло-
нок (установок), шиномонтажных электрогидравлических
стендов не должны допускать превышения номинального
давления более чем на 12 %.
7. Окрасочное оборудование, установки для нанесения анти-
коррозионных покрытий и приборы для проверки расхода
топлива колесных транспортных средств, в состав которых
входят электрические цепи и узлы, должны быть изготовле-
ны во взрывозащищенном исполнении.
Автоматические бесконвейерные моечные автомобильные установки должны быть оснащены на въезде световой сигнализацией въезда-выезда.
- В конструкциях автоматических воздухораздаточных колонок должны быть предусмотрены узлы для автоматического прекращения накачки, сигнализаторы процесса накачки и достижения заданного давления в шинах.
- В конструкциях стационарных, передвижных и переносных специальных компрессоров с электроприводом и автоматическим управлением должно быть предусмотрено по меньшей мере одно устройство, отключающее электропривод при превышении установленного максимального давления с погрешностью срабатывания в пределах ± 0,05 МПа.
11.Электроприводные нагнетатели смазки и маслораздаточные колонки (установки) должны снабжаться предохранительным клапаном для ограничения давления и реле для автоматического отключения электропривода, которые устанавливаются на выходе нагнетателя и исключают превышение номинального давления более чем на 10 %.
12. Пневмоприводные нагнетатели смазки и маслораздаточные колонки (установки) должны снабжаться по меньшей мере одним конструктивным элементом для ограничения давления.
13. Высота подъема воронки передвижных установок для сбора отработанных масел должна быть не менее 1700 мм над опорной поверхностью.
14. Отношение минимального размера основания к высоте передвижных стоек напольных одностоечных подъемников должно быть не менее 0,45.
15. Опорные поверхности подхватов и педалей домкратов должны быть рифлеными.
16. Максимальная скорость опускания и подъема автотранспортных средств напольными стационарными и передвижными подъемниками должна быть не более 0,1 м/с.
17. Конструкция подъемников с двумя плунжерами или стойками и более с высотой подъема более 300 мм должна обеспечивать синхронный подъем и опускание колесного транспортного средства с отклонениям и по высоте не более 10 % независимо от нагрузки, приходящейся на каждый плунжер или стойку.
18. Конструкция подъемников должна обеспечивать подъем и опускание колесного транспортного средства только при непосредственном воздействии оператора на органы управления.
19. В конструкциях подъемников должны быть предусмотрены по меньшей мере два независимых один от другого узла, один из которых страховочный, препятствующих самопроизвольному опусканию рабочих органов. Эти узлы должны быть снабжены по меньшей мере одним средством контроля их состояния. В конструкциях электромеханических подъемников одно из этих средств должно обеспечивать возможность непосредственного визуального контроля.
20. В конструкциях электромеханических подъемников и опрокидывателей колесных транспортных средств должно быть предусмотрено не менее двух концевых выключателей, фиксирующих крайние положения рабочих органов как с нагрузкой, так и без нагрузки.
21. Механические домкраты и электромеханические подъем-
ники должны выдерживать поднятый груз в течение 10 мин при перегрузке 25 % и три полных цикла подъема—опускания груза при перегрузке 10 %. При этом не допускается появление остаточных деформаций.
22. В конструкциях роликовых стендов для проверки тяго-
вых, тормозных и ходовых свойств должны быть преду-
смотрены страховочные устройства, предотвращающие
при диагностике самопроизвольный выезд колесного
транспортного средства со стенда в продольном направле-
нии и ограничивающих его перемещение в поперечном
направлении.
23. Конструкции роликовых стендов для проверки тяговых,
тормозных и ходовых свойств должны обеспечивать стати-
ческую и динамическую устойчивость колесного транс-
портного средства (предотвращение выезда или выброса со
стенда) во всем диапазоне режимов проверок.
24. Не допускается снижение коэффициента сцепления рабочих поверхностей роликов стенда с колесами при сухих чистых протекторах шин вследствие износа и загрязнения рифления или абразивного покрытия роликов до уровня менее 0,65 при проверке колесных транспортных средств категорий М, и менее 0,6 при проверке колесных транспортных средств категорий М2, М3, N,, N2, N3.
25.Пульты управления роликовыми стендами для проверки тяговых и тормозных качеств должны:
- исключать случайное срабатывание устройства въезда и выезда транспортного средства до полной остановки роликов;
- обеспечивать плавное изменение тормозного момента нагружающего устройства при ступенчатом переключении задаваемых значений (установок) регулируемого параметра в режиме его автоматической стабилизации.
26. Узлы и приборы, устанавливаемые на колеса колесного транспортного средства при диагностике, должны оснащаться зажимными и страховочными приспособлениями, препятствующими отсоединению и падению этих узлов и приборов.
27. Конструкция роликовых стендов для проверки тяговых свойств должна предусматривать сигнализацию пуска стенда
28. Средства технической диагностики двигателей с искровым зажиганием и воспламенением от сжатия должны исключать возможность возникновения искр и контакта топлива и его паров с горячими частями оборудования в процессе его работы, если такой контакт может стать причиной взрыва или пожара.
29. В состав тяговых стендов и прочего оборудования, применяемого при работающем двигателе в помещении, должно входить заборное устройство для отвода отработавших газов.
30. Конструкция заборного устройства должна предусматривать подключение зондов приборов для анализа состава отработавших газов, а также отвод отработавших газов в систему вытяжной вентиляции.
31. В конструкциях стендов для монтажа и демонтажа шин, вулканизаторов, шинных борторасширителей должно быть не менее одного узла, предотвращающего повышение давления в пневмоприводе.
5.5 УПРАВЛЕНИЕ КАЧЕСТВОМ ТО И TP АВТОМОБИЛЕЙ НА АТП
Система управления качеством ТО и TP — это совокупность управляющих органов и объектов управления, взаимодействующих с помощью материально-технических и информационных средств.
Система управления качеством должна предусматривать совокупность взаимоувязанных организационных, технических, экономических и социальных мероприятий по обеспечению целей управления качеством технического состояния подвижного состава.
Системный подход к вопросам управления АТП требует рассматривать систему управления качеством ТО и TP как неотъемлемую (а не автономную) часть управления. Из этого, в частности, следует необходимость обеспечения: четкой постановки целей перед технической службой с указанием сроков их достижения; связи показателей и нормативов эффективности технической службы с эффективностью работы АТП в целом; постепенной детализации и уточнения цели по мере перехода от верхних к нижним уровням управления; конкретности и простоты нормативов, их четкого понимания непосредственными исполнителями, увязки систем морального и материального стимулирования персонала с достижением или перевыполнением ими нормативов качества; связи любых показателей качества ТО и TP с показателями эксплуатационной надежности автомобилей (например, наработкой на отказ и на простои, вероятностью этих событий, продолжительностью простоев в ремонте и др.); наличия объективной и своевременной информации для принятия решений по совершенствованию производства ТО и TP; назначения норматива качества с учетом достигнутого уровня, условий работы АТП, имеющихся ресурсов и т. д.
Реализация этих требований, сопровождающаяся широким использованием машиносчетной техники, средств связи и тщательно отработанного документооборота, представляет собой комплексную систему управления качеством ТО и TP, конечной целью которой является устойчивое обеспечение на заданном уровне коэффициента технической готовности парка (КТГ), безотказности и долговечности автомобилей, эффективного их использования с минимальными материальными и трудовыми затратами.
Создание и обеспечение успешного функционирования комплексной системы управления качеством ТО и TP автомобилей следует считать одной из основных задач инженерно-технической службы АТП. Однако пока еще в масштабах отрасли автомобильного транспорта не найдено унифицированного решения этой задачи. Это остается одной из важнейших проблем этой отрасли.
Степень полноты и качество отработки перечисленных выше мероприятий могут быть различными. Практически на различных АТП так и бывает. Соответственно оказываются различными и конечные показатели работы АТП по обеспечению качества ТО и TP подвижного состава.
Комплексная система управления качеством ТО и TP имеет большую практическую значимость, однако отсутствие широкого опыта применения такой системы не позволяет дать научно обоснованные, апробированные практикой, исчерпывающе и четкие материалы по ее организации и применению на АТП. В то же время нельзя не привести некоторые данные об имеющимся в отрасли передовом опыте, которые проиллюстрировали бы возможность решать задачу управления качеством ТО и TP на АТП.
Общая схема управления качеством (рис. )включает в себя комплекс
соответствующих мероприятий, основанных на системном подходе к вопросам управления АТП. При этом управление качеством ТО и TP имеет в своей основе конкретные значения нормативных показателей качества. Из рис. 5.3 видно, что с их помощью взаимосвязанно оценивается как техническое состояние автомобилей, так и качество их ТО и ТР.
Комплекс мероприятий по управлению качеством




Нормативные значения показателей качества


Оценка уровня качества
Оценка уровня качества







Показатели качества технического состояния автомобиля
Показатели качества процессов обслуживания и ремонта автомобиля


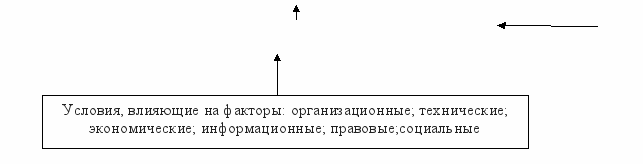

Факторы, влияющие на качество То и Р: исполнители; информация; предметы труда; средства труда
Рис.5.4 Схема управления качеством ТО и ТР
Указанные качества (ТО и TP автомобиля и его техническое состояние) физически обеспечиваются производственным процессом ТО и TP, на который оказывают свое влияние определенные факторы, также зависящие от ряда условий.
Полученная с помощью нормативных значений показателей качества оценка технического состояния автомобилей и уровня работ по ТО и TP анализируется и используется для обоснованного суждения о работе производства и, в свою очередь, для определенных управляющих воздействий на последнее, как это указано на рис. 5.3
Эти воздействия состоят из комплекса административных, технологических, снабженческих, организационных, экономических, социальных и других целенаправленных мероприятий, обеспечивающих заданный уровень коэффициента технической готовности.
Основные показатели качества ТО и TP определяются через наработку в километрах пробега на выполненную операцию TP, нормированное предельное количество отказов за определенный пробег (или за время эксплуатации в днях), нормированное предельное количество брака или отклонений от технических условий в заранее определенной выборке автомобилей (работ), определяемых отделом технического контроля. При этом весь имеющийся на АТП подвижной состав подразделяется по величине пробега с начала эксплуатации на несколько групп. Например, на четыре группы автобусов с пробегом соответственно: до 50 тыс. км; от 51 до 200 тыс. км; от 201 до 350 тыс. км и свыше 350 тыс. км.
Для каждой такой группы, а также внутри них (по маркам и моделям) устанавливаются свои показатели качества, после чего показатели качества для всех групп считаются сравнимыми между собой. Это позволяет иметь сравнимые показатели качества по каждому автомобилю, каждой марке и модели автомобилей, каждой их группе и по АТП в целом. Указанное обстоятельство позволяет объективно решать вопросы морального и материального стимулирования персонала АТП, а также организовывать соревнования на основе унифицированных сравнимых показателей.
Нормативные показатели качества устанавливаются, а фактически получившиеся — выявляются и сравниваются с нормативными. Сначала нормативные показатели формируются на основе уже имеющихся, достигнутых внутрипроизводственных показателей. В дальнейшем они ужесточаются, периодически корректируются, чем обеспечивается устойчивая тенденция к повышению всех основных показателей работы АТП.
Такой нормативный показатель качества, как наработка в километрах пробега на выполненную операцию ремонта в начальной стадии функционирования системы, определяется статистически как средняя, достигнутая на данном АТП. Частное от деления фактически получившейся наработки (в километрах на операцию ремонта) на ее нормативную величину является численной характеристикой как уровня технического состояния объекта (автомобиля, агрегата, узла, системы и т. п.), так и качества выполненной работы.
Количество типичных ремонтных работ, определяющих по существу надежность подвижного состава, составляет 300-400 наименований. Сбор и механизированная обработка информации (рис.5.4) позволяют своевременно
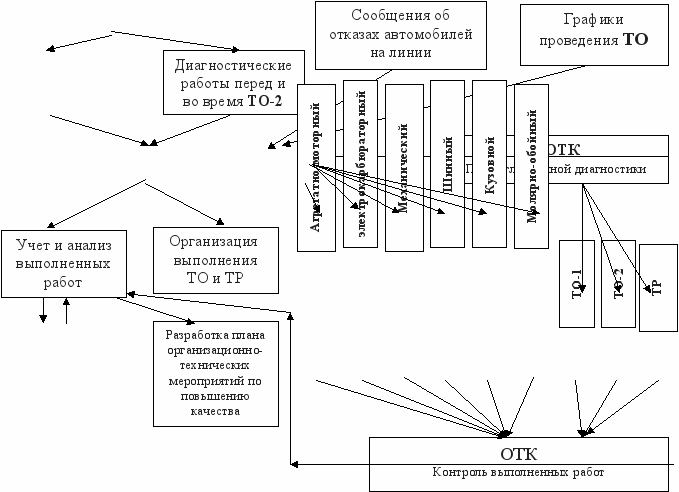
Отдел технического контроля
Контрольные работы ЕО
автомобилей
Центр управления производством
МСС
Механизированная обработка информации
Рис. 5.4 Схема сбора и обработки информации при реализации комплексной системы управления качеством ТО и ТР на АТП
по всем этим наименованиям получать данные, используемые для принятия управляющих решений, в том числе решений о моральном и материальном стимулировании конкретных работников.
Своевременный документированный учет фактов и причин нарушения работоспособности и исправности автомобилей, а также выполнения операций ремонта и ТО включает в себя: фиксацию наименования операции, исполнителя работ, наименование ремонтируемого агрегата или узла автомобиля, вида обслуживания или ремонта; систематизированное накопление этих данных в специальных картах технического состояния автомобиля. Это позволяет для каждой операции ремонта определить конкретного виновника в появлении отказа (неисправности).
Частота появления отказов и неисправностей в значительной мере зависит от качества выполнения работ, входящих и ТО-1 и ТО-2. Поэтому формирование значений наработки на операцию ремонта, как показателя качества, производится за период между очередными ТО-2.
Показатель качества выполнения ТО-2 определится, если в знаменатель дроби поставить число операций, входящих в номенклатуру работ ТО-2, а в числитель — число операций, также входящих в эту номенклатуру, но потребовавших между очередными ТО-2 повторного выполнения. Для удобства пользования этим показателем полученную дробную величину вычитают из единицы и получают значение показателя качества меньше единицы.
Определение показателя качества ТО-2 производится ОТК методом приемочного контроля определенной выборки из общего числа автомобилей, подвергшихся ТО-2.
Полученный показатель сравнивается с аналогичным нормативным. Последний выявляется при разработке системы по средним статистическим данным АТП, а затем постепенно ужесточается.
Подобным образом решается и вопрос о качестве ТО-1.
ТО-2 и ТО-1 выполняются производственными коллективами. Поэтому после выявления показателей качества вопросы личной ответственности, а также морального и материального стимулирования решаются внутри коллектива.
Для работ TP расчет показателей качества труда определяется аналогичным образом исходя из соотношения числа повторно выполняемых операций ремонта к их общему числу (за период между ТО-2 или ТО-1). Аналогично выявляются нормативные показатели качества работ, выполняемых производственными участками, а также сопоставляются достигнутые показатели с нормативными Приведенный в табл. 8 состав показателей, используемых в ходе функционирования комплексной системы управления качеством ТО и TP, увязан с их управленческим использованием. Объективная,
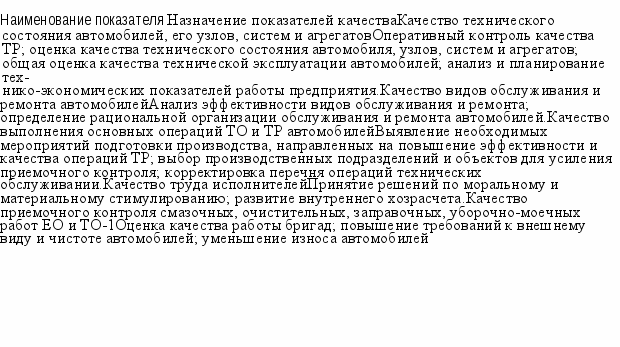
Таблица 5.3 Система показателей качества ТО и ТР автомобиля
оперативно проводимая оценка качества работ по ТО и TP автомобилей позволяет обоснованно и целенаправленно воздействовать на производство и отдельные аспекты деятельности инженерно-технической службы АТП..
5.6 Система организации и управления производством ТО и ремонта
Инженерно-техническая служба АТП в своей повседневной деятельности решает ряд вопросов планирования и управления производством, которые условно можно свести к следующим четырем комплексам взаимосвязанных задач:
- определение программы работ, т.е. числа автомобилей, планируемых к постановке на диагностирование и ТО, номенклатуры и объемов ремонтных работ;
- распределение автомобилей по производственным постам в зависимости от специализации, оснащенности и занятости;
- распределение наличных запасных частей и материалов по автомобилям, агрегатам, постам и пополнение их запасов;
- распределение заданий между ремонтными рабочими, постами и участками.
Как показали исследования и опыт работы передовых АТП, наибольшая эффективность в решении вопросов организации производства может быть достигнута благодаря централизованной системе управления производством (системы ЦУП), основанной на централизации управления производством ТО и ремонта подвижного состава на АТП. Внедрение этой системы является первым этапом создания АСУ инженерно-технической службы АТП.
Система ЦУП строится на следующих принципах:
1. Четкое распределение административных и оперативных
функций между руководящим персоналом и сосредоточение функций оперативного управления в едином центре или отделе управления производством (ЦУП или ОУП). Основными задачами ЦУП являются сбор и автоматизированная обработка информации о состоянии производственных ресурсов и объемах работ, подлежащих выполнению, а также планирование и контроль за деятельностью производственных подразделений на основе анализа имеющейся информации.
Центр управления производством состоит, как правило, из двух подразделений: отдела (группы) оперативного управления (ООУ) и отдела обработки и анализа информации (ООАИ).
- Выполнение каждого вида технического воздействия при
организации производства ТО и ремонта подвижного со-
става специализированной бригадой или участком (брига-
ды ЕО, ТО-1, ТО-2, TP и др.) — технологический принцип формирования
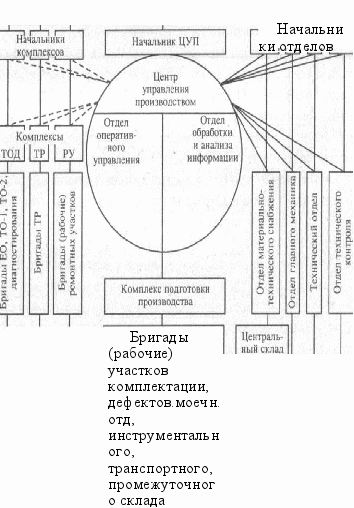
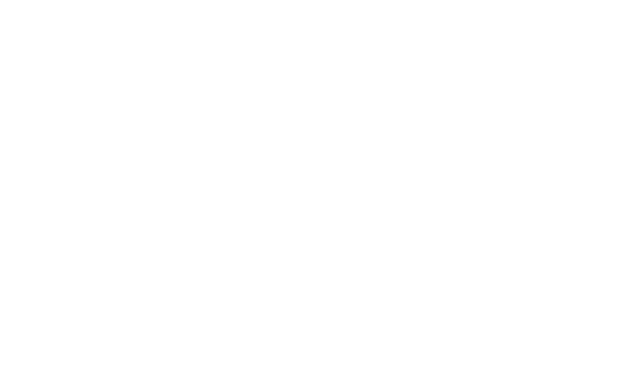
Главный инженер


















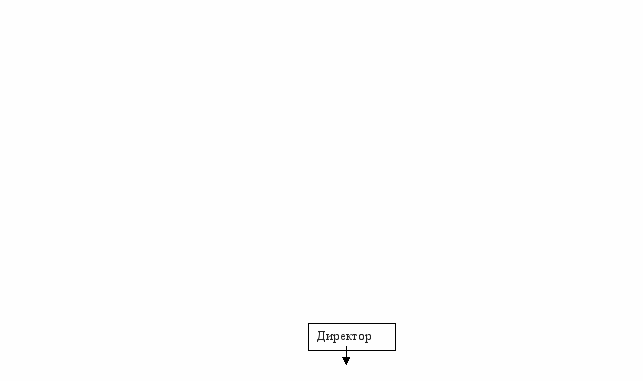










Рис. 5.5 Структура централизованного управления технической службой АТП
производственных подразделений, в наи-
большей степени отвечающий требованиям централизован-
ной системы управления.
- Объединение производственных подразделений (бригад, участков), выполняющих технологически однородные работы, в производственные комплексы в целях удобства управления ими.
- Централизованная подготовка производства (комплектование оборотного фонда запасных частей и материалов, хранение и регулирование запасов, доставка агрегатов, узлов и деталей на рабочие посты, мойка и комплектование ремонтного фонда, обеспечение рабочих инструментом, а также перегон автомобилей в зонах ТО, ремонта и ожидания) осуществляется специальным комплексом. Централизация подготовки производства значительно сокращает непосредственные затраты времени ремонтных рабочих, управленческого персонала и в конечном счете простои автомобилей в ТО и ремонте.
- Использование средств связи, автоматики, телемеханики и вычислительной техники (система может активно работать лишь при наличии средств диспетчерской связи и оргтехники).
На рис. приведена схема структуры управления технической службой крупной АТП. В зависимости от мощности предприятия и условий внешней кооперации структура технической службы может изменяться при сохранении принципиальных положений. Центр управления производством возглавляется начальником, а основная оперативная работа по управлению выполняется диспетчером производства и его помощником — техником-оператором. Численность персонала ЦУП определяется общим объемом выполняемых им работ (числом автомобилей в АТП, числом смен работы, наличием технических средств управления и др.).
Оперативное руководство всеми работами по ТО и ремонту автомобилей осуществляется отделом оперативного управления (ООУ) ЦУП. Персонал ООУ выполняет следующие основные работы:
- принимает смену, т. е. фиксирует состояние производства, выполненную программу, размеры незавершенного производства, количество автомобилей в очереди на ремонт, имеющиеся помехи, отклонения;
- осуществляет оперативный контроль проведения диагностирования, ТО-1, ТО-2;
- осуществляет оперативное планирование, регулирование, учет и контроль выполнения ремонтов подвижного состава, т. е. принимает заявки на ремонт, устанавливает очередность выполнения работ, определяет плановое время, необходимое для выполнения намеченных работ, обеспечивает своевременную постановку автомобилей на посты ремонта, выдает задания непосредственным исполнителям, выдает задания персоналу комплекса подготовки производства по доставке на рабочие места необходимых запчастей и материалов, периодически контролирует ход выполнения работ;
- организует и контролирует выполнение работ по своевременной подготовке запасных частей и материалов для проведения регламентных работ и ремонтов, т. е. обеспечивает подготовку производства к проведению ТО и ремонтов, учитывая при этом результаты диагностирования;
• передает смену.
На ООАИ возлагается выполнение всех работ, связанных i организацией информационного обеспечения системы управления, с использованием технических и программных средств ПК. Основной задачей ООАИ является систематизация, обработка, анализ и хранение информации о деятельности всех подразделений технической службы, а также ведение учета пробегов автомобилей, движения основных агрегатов и планирование технических воздействий. ООАИ выполняет следующие основные работы:
- принимает первичные документы для обработки, осуществляет контроль правильности и полноты их заполнения и подготавливает информацию к дальнейшей обработке на электронных носителях;
- обрабатывает информацию с помощью персональных компьютеров, т. е. выполняет работы по формированию, сортировке и систематизации информации, накопление ее по соответствующим разрезам и формам — в зависимости от используемого на предприятии программного обеспечения ПК (выходные формы);
- производит анализ по результатам обработки информации и передает материалы руководству для принятия конкретных мер и разработки мероприятий по совершенствованию работы ИТС АТП;
- в лицевых карточках автомобиля ведет учет цепочки пробега, отмечает случаи замен основных агрегатов (двигателя, коробки передач, мостов и др.) при ремонте и отдельно учитывает их пробеги, на основании фактических пробегов планирует постановку автомобилей в ТО и на диагностирование.
Обеспечение комплексов ТО, диагностирования и TP запасными частями и материалами выполняется по указанию ЦУП комплексом подготовки производства (КПП). Оперативное руководство комплексом подготовки производства осуществляется диспетчером ЦУП через техника-оператора КПП (в небольших АТП — непосредственно) с помощью средств связи (телефона, селектора).