Анализ и обобщение опыта и тенденций создания промышленных роботов в отечественной и зарубежной робототехнике показывает, что все большее распространение получает электромеханический привод промышленных роботов. Впоследние год
Вид материала | Документы |
- Дипломная работа студента, 601.76kb.
- Исать собственные приложения для управления роботами на примере Lego nxt, а также использовать, 76.9kb.
- С применением grid-технологий, 81.79kb.
- История роботов, написанная роботом, 101.24kb.
- Sdfield> Самостоятельная подготовка, 455.42kb.
- Вдокладе описывается технология обучения распределенной системы автономных мобильных, 45.47kb.
- Внушающих уверенность жилищ люди живут в обличии роботов-суррогатов сексуальных, физически, 367.79kb.
- Возможное участие родителей, 108.84kb.
- Анализ работы шмо учителей физики, химии, биологии за 2010-2011 учебный год, 113.58kb.
- Лега В. П. Наука и вера, 152.3kb.
ГИБКИЕ ПРОИЗВОДСТВЕННЫЕ СИСТЕМЫ
6.1. Классификация, общие положения
Гибкие производственные системы (ГПС) — новая, весьма совершенная форма автоматизации мелкосерийного и серийного машиностроительного производства. В рамках этой новой проблемы имеется много спорных вопросов по научным, техническим, экономическим, социальным и терминологическим аспектам. Несмотря на отсутствие единой, установившейся системы взглядов, существует достаточно четкое определение: «Гибкая производственная система — это совокупность в разных сочетаниях оборудования с ЧПУ, роботизированных технологических комплексов, гибких производственных модулей, отдельных единиц технологического оборудования и систем обеспечения их функционирования в автоматическом режиме в течение заданного интервала времени, обладающая свойством автоматизированной переналадки при производстве изделий произвольной номенклатуры в установленных пределах значений их характеристик» (ГОСТ 26228—85).
По организационным признакам гибкие производственные системы подразделяются на гибкие автоматизированные линии (ГАЛ), гибкие автоматизированные участки (ГАУ) и гибкие автоматизированные цехи (ГАЦ).
Гибкая автоматизированная линия — это ГПС, в которой технологическое оборудование расположено в принятой последовательности технологических операций.
Гибкий автоматизированный участок — это ГПС, функционирующая по технологическому маршруту, в котором предусмотрена возможность изменения последовательности использования технологического оборудования.
Гибкий автоматизированный цех — это ГПС, представляющая собой в различных сочетаниях совокупность гибких автоматизированных линий, роботизированных технологических линий, гибких автоматизированных участков, роботизированных технологических участков для изготовления изделий заданной номенклатуры.
В соответствии с ГССТ 26228—85 в состав ГПС входят:
— гибкий производственный модуль (ГПМ) — единица технологического оборудования для производства изделий произвольной номенклатуры в установленных пределах значений их характеристик с программным управлением, автономно функционирующая, автоматически осуществляющая все функции, связанные с их изготовлением, имеющая возможность встраивания в гибкую производственную систему;
— роботизированный технологический комплекс (РТК) — совокупность единицы технологического оборудования, промышленного робота и средств оснащения, автономно функционирующая и осуществляющая многократные циклы;
— система обеспечения функционирования ГПС — совокупность в общем случае взаимосвязанных автоматизированных систем, обеспечивающих проектирование изделий, технологическую подготовку их производства, управление гибкий производственной системой при помоши ЭВМ и автоматическое перемещение предметов производства и технологической системы.
В общем случае основные составляющие системы обеспечения функционирования ГПС:
— автоматизированная транспортно-складская система (АТСС);
— автоматизированная система инструментального обеспечения (АСИО);
— автоматизированная система удаления отходов (АСУО);
— автоматизированная система управления технологическими процессами (АСУТП);
— автоматизированная система научных исследований (АСНИ);
— система автоматизированного проектирования (САПР);
— автоматизированная система технологической подготовки производства (АСТПП);
— автоматизированная система управления [АСУ] и т. д.
На рис. 6.1 приведена обобщенная структурная схема гибкой производственной системы.
На современном этапе развития машиностроительного комплекса наметились следующие главные тенденции:
1) широкое применение концентрации (совмещения) операций, способствующее повышению производительности обработки при снижении ее трудоемкости и стоимости;
2) применение ресурсосберегающих (малоотходных и безотходных) технологий, повышающих коэффициент использования металла и сокращающих расход энергии;
3) агрегатно-модульный принцип построения станков и другого технологического оборудования, станочных модулей, автоматических станочных систем и их элементов, что повышает степень унификации и надежность работы оборудования, качество его изготовления и сборки, сокращает сроки и затраты на изготовление;
4) сокращение кинематических цепей, замена механических цепей электрическими за счет средств ЧПУ, что повышает жесткость и точность станков, качество обработки деталей и снижает металлоемкость оборудования при тех же и более высоких мощностях;
5) стремление к так называемой «безлюдной технологии» за счет комплексной гибкой автоматизации, широкой роботизации, применения диагностических систем, что повышает коэффициент сменности и гибкость станков, станочных модулей и систем;
6) миниатюризация систем управления и контроля;
7) эффективное использование станков с ЧПУ в массовом многономенклатурном производстве.
Первые две тенденции предопределяют работы, связанные с поиском новых технологических принципов, замену дробной технологии обработки на многих однооперационных станках (принцип дифференциации) концентрацией операций за счет использования многооперационных станков.
Актуальность вопросов экономного расходования материальных ресурсов и энергии обусловлена большим ростом производства продукции машиностроения, который вызывает необходимость вовлечения в производство огромных сырьевых, топливно-энергетических и других материальных ресурсов. Решение этой проблемы связано с применением заготовок, приближающихся по форме к готовым деталям, что во многих случаях требует замены резания другими видами малоотходной обработки.
Планируется взамен ежегодного выпуска одноцелевых станков соответствующего качества перейти к выпуску многоцелевых станков, что позволит существенно снизить расход металла.
Третья и четвертая тенденции требуют изменения структуры, компоновки и схемных решений станков с ЧПУ.
Пятая тенденция в настоящее время особенно четко просматривается в том, что на смену развития механизации и жестких систем автоматизации пришла роботизация производственных и технологических процессов с компьютеризацией управления, позволяющаясущественно сократить затраты ручного труда и автоматизировать умственный труд человека.
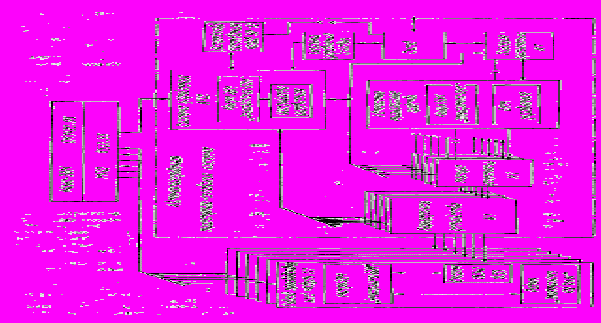
Рис. 6.1. Обобщенная структурная схема ГПС
В этом плане особую роль должны сыграть гибкие автоматизированные производства и гибкие производственные системы, оснащенные самым современным технологическим оборудованием, вычислительной техникой и роботизированными технологическими комплексами. В общем эти понятия близки между собой, хотя понятие «гибкое автоматизированное производство» больше отражает тип производства, а понятие «гибкая производственная система» определяет конкретный тип системы, ее состав и назначение.
Развитие автоматизации производственных процессов в историческом плане рассмотрено в гл. 5 «Роботизированные технологические комплексы», где, в частности, было сказано, что гибкие производственные системы являются высшей формой комплексной автоматизации машиностроения.
С целью уточнения основных положений по гибким производственным системам и формулированию некоторых перспектив их развития на ближайшие годы рассмотрим эту проблему по следующим основным критериям: научно-технический аспект; производственные показатели; технико-экономическая эффективность; социальный аспект.
Научно-технический аспект ГПС, Гибкие производственные системы, а в дальнейшем и гибкие автоматизированные производства — это качественно более совершенный этап комплексной автоматизации производства. Благодаря быстрому научно-техническому прогрессу в таких областях, как автоматика, радиоэлектроника, вычислительная техника, информатика, появилась возможность рассматривать комплексную автоматизацию производственных процессов по-новому — как систему автоматизации, охватывающую все производства от проектирования изделий и технологии до изготовления продукции и ее упаковки. Это автоматизация инженерного труда и процесса изготовления изделий. Такая качественно новая постановка задачи автоматизации позволяет получить рациональные, а в некоторых случаях и оптимальные по выбранным критериям качества инженерные решения.
Системы автоматизированного проектирования (САПР), используемые в ГПС, охватывают две фазы проектирования — конструирование изделий и проектирование технологии его обработки. На первых стадиях создания САПР автоматизации подвергались отдельные задачи проектирования, в основном расчетного характера, затем — функционально законченные фрагменты проектных работ, такие, как конструирование детали, узла или изделия.
Современный этап развития САПР характеризуется информационной и технической интеграцией проектно-конструкторских работ в единую цепочку «исследование — конструирование — технологическая подготовка». Основа информационной интеграции в САПР — машинная графика. Под машинной графикой понимают применение ЭВМ для восприятия, хранения, преобразования и выдачи информации в графическом виде. Специфика машинной графики САПР заключается в тесной взаимосвязи ее с геометрическим моделированием объектов проектирования. Это объясняется тем, что чаще всего любое проектирование опирается на язык графических образов.
Поэтому в современном понимании технический комплекс САПР — это компьютерная система, оснащенная развитыми программными и техническими средствами машинной графики, инженерных расчетов, математического моделирования и документирования проектной информации.
Производственные показатели ГПС. Основные показатели гибких производственных систем предназначены для определения производственных возможностей ГПС в машиностроении и объективного сравнения различных вариантов их исполнения и включают в себя: тип и габаритные размеры обрабатываемых изделий; технологические возможности ГПС; станкоемкость ГПС; стоимость часа работы: каждой единицы основного технологического оборудования; степень безлюдности ГПС; гибкость и степень оснащенности ГПС высокоавтоматизированными элементами системы АСУ (САПР, АСУП, АСТПП, АСУ ТП).
В каждом изделии габаритные размеры основных деталей (корпусов, валов, фланцев и т. п.) находятся в определенном соотношении. Поэтому оборудование ГПС целесообразно подбирать или создавать новое под определенные типоразмеры узлов. Необходимо по возможности использовать принцип групповой обработки деталей. На заводах, имеющих небольшой объем производства и широкую номенклатуру обрабатываемых деталей, целесообразно применять ГПС смешанного типа, состоящие из нескольких типов оборудования для полной комплексной обработки деталей узлов определенного типоразмера. В этом случае связующим звеном ГПС является склад, в котором могут находиться спутники для корпусных деталей и палеты для валов и фланцев.
Многоцелевые модули ГПС должны иметь высокую производительность при максимальной гибкости, т. е. возможность обрабатывать широкую номенклатуру деталей без вмешательства обслуживающего перегнала. Это достигается за счет широкого применения модулей со встроенными шпиндельными головками, контроля элементов детали в процессе обработки и стабильности качества инструмента.
Гибкость достигается автоматизацией, дающей возможность легко переходить от обработки одной детали к другой благодаря применению устройств числового программного управления. Гибкая производственная система операционного типа должна иметь от 5 до 122 многоцелевых модулей, имеющих магазины на 30...40 инструментов. При однотипных модулях возможно создание в некоторых случаях централизованной системы замены инструмента в магазинах модулей.
Автоматизированная транспортно-складская система (АТСС) — это система взаимосвязанных, автоматизированных, управляемых от ЭВМ транспортных и складских устройств для укладки,
хранения, временного накопления, разгрузки и доставки деталей и технологической оснастки. Предметы перемещаются АТСС уложенными в стандартную тару (спутники, поддоны).
Применяют АТСС трех типов: с накопителями, с центральным складом и комбинированные. Транспортирование грузов может осуществляться по линейной, многорядной и кольцевой схемам.
К вспомогательному оборудованию относятся моечные машины, установки ТВЧ, машины для клеймения, контрольно-измерительные машины и т. д. Все это оборудование должно охватываться общей транспортной системой и работать в автоматическом режиме. В зависимости от технологического процесса и требований к качеству обработки деталь может поступать на мойку 1...3 раза за весь процесс обработки.
Гибкие производственные системы механообрабатывающих производств обязательно должны иметь отделения для хранения и комплектации ГПС инструментом и приспособлениями. Отделения содержат стеллажи для режущего и вспомогательного инструмента и технологической оснастки, приборы для настройки инструмента вне станка, стенды для сборки и проверки приспособлений, тележки для транспортировки собранных инструментов и приспособлений.
При проектировании приспособлений необходимо стремиться к тому, чтобы установка и зажим деталей в приспособлении производились роботом.
Узлы и отдельные детали, предназначенные для обработки и сборки на высокоавтоматизированных ГПС, должны быть тщательно отработаны на технологичность по изготовлению и сборке. Конструкция деталей должна учитывать возможности металлорежущих станков с ЧПУ, при этом надо стремиться к уменьшению количества деталей в узле.
При создании ГПС особое внимание необходимо уделять заготовительным системам, в которых желательно шире применять прогрессивные методы получения заготовок для малоотходных технологических процессов (литье под давлением, литье по выплавляемым моделям, жидкую штамповку с последующей чеканкой, поперечно-винтовую прокатку, радиальный обжим и т. п.). Обязательное условие — стабильность качества заготовок как по размерам, так н по структуре материала.
В ГПС необходимо использовать прогрессивные технологические процессы с широким внедрением лазерной техники для обработки поверхностей, закалки элементов деталей и контроля обработанных деталей. Инструмент для ГПС должен отвечать таким требованиям по стабильности качества, как взаимозаменяемость, отсутствие сколов и трещин, стабильная стойкость. Для этого целесообразно применять твердосплавный инструмент с покрытием, минералокерамику и сверхтвердые материалы.
Степень автоматизации ГПС должна быть тщательно обоснована. Наличие обслуживающего персонала иногда позволяет в значительной степени упростить систему в части механики и управления, повысить ее надежность и соответственно увеличить эффективность эксплуатации.
Гибкие производственные модули, вспомогательное оборудование и элементы АТСС должны иметь стандартные сопрягающие устройства для соединения их между собой и с управляющими ЭВМ. С этой целью предусматривается опережающая разработка нормативно-технической документации. Для сокращения числа спутников в системе целесообразно малотрудоемкие детали обрабатывать в первую смену, а наиболее трудоемкие — во вторую и третью.
ГПС найдут наибольшее применение на тех предприятиях, где характер производства требует смены продукции, выпускаемой преимущественно повторяющимися партиями. Степень гибкости определяется в первую очередь частотой смены продукции.
Габаритные размеры изделий, которые могут быть рекомендованы для обработки в ГПС, находятся в пределах 60... 1200 мм, габаритные размеры корпусных деталей — 100... 1000 мм, длина валов — 50...1250 мм, диаметры валов — 20...320 мм.
Технико-экономическая эффективность ГПС. Эффективность ГАП и ГПС определяется на основании:
— общего анализа затрат и потерь для существующих способов производства;
— общего анализа затрат и экономии, получаемых в результате перехода на гибкое производство;
— сравнительного количественного анализа ГПС по экономическим критериям;
— анализа риска и чувствительности экономических решений.
Анализ существующего способа производства связан с определением показателей себестоимости продукции, степени использования технологического оборудования, качества продукции, затрат ручного труда, производительности оборудования, уровня запасов материалов, сырья и т. д. Он необходим в качестве отправной точки для последующего обоснования капиталовложений в новую технологию.
Анализ затрат и экономии от внедрения гибкой технологии основан на оценке количественных и качественных показателей производства. Имеется несколько основных категорий таких оценок:
— показатели прямой экономии, в основном имеющие количественный характер;
— показатели косвенной экономии, сочетающие количественные и качественные оценки;
— факторы экономии, имеющие качественный характер. Показатели прямой экономии обычно рассчитываются просто и связаны главным образом с результатами автоматизации производства, сопровождаемой заменой существующего оборудования на автоматически действующее. Как правило, новое оборудование более высокопроизводительно, что и приводит к увеличению объемов производства. Использование автоматического управления способствует безоператорной работе с увеличением сменности функционирования оборудования. Многофункциональность оборудования уменьшает его общее количество и занимаемую им площадь. Главными статьями экономии становятся меньшие затраты:
— на прямую оплату труда;
— на обеспечение производства энергией, топливом, обслуживанием;
— на движение материалов, сырья, обработку отходов;
— на амортизацию помещений и оборудования.
В ГПС автоматизируются не только оборудование и технологические процессы, но и обработка информации, организационное управление, обслуживание производства. Поэтому более значительной оказывается косвенная экономия, основные статьи которой являются результатом:
— ускорения производственного цикла с уменьшением главным образом межоперационных и транспортных запаздываний;
— снижения уровня незавершенного производства в связи с увеличением производительности и ускорением производственного цикла;
— снижения уровня складских запасов и затрат на их хранение;
— уменьшения затрат на оплату труда в сфере ремонта, обслуживания и эксплуатации меньшего парка станков, хотя оплата труда может возрасти в связи с необходимостью использования при диагностике, контроле, обслуживании более высококвалифицированного персонала (инженеров и квалифицированных техников-операторов, программистов и специалистов по электронной технике);
— повышения эффективности обработки информации, проектирования, планирования, организационного управления, всех видов инженерного труда;
— снижения затрат на реконструкцию и модернизацию производства.
Наиболее сложны для квантификации качественные факторы экономии, так как их влияние не поддается оценке в чисто экономических терминах, а проявляется в форме воздействий, имеющих главным образом социальное значение. В данной категории оценок экономия появляется в результате:
— улучшения качества продукции, повышения ее конкурентоспособности и возможностей для удовлетворения потребительского спроса на более высоком уровне;
— повышения гибкости производства к быстрым изменениям производимых изделий, а также серийности изготовления продукции;
— улучшения условий труда за счет автоматизации физических работ и устранения таких форм труда человека, которые необходимо совершать в тяжелой, опасной или вредной для здоровья производственной среде;
— повышения эффективности межотраслевых связей и кооперации на основе более динамичных дисциплин взаимных поставок сырья, материалов, готовых изделий;
— снижения затрат в социальной сфере по мере углубления автоматизации производства и уменьшения численности работающих.
Анализ эффективности ГАП по экономическим критериям направлен главным образом на определение себестоимости продукции, производительности труда, сроков окупаемости капиталовложений и других показателей производства. Оценка производится на основании стандартных методик, имеющих законодательную силу для отдельных предприятий одной отрасли, для групп отраслей или народного хозяйства в целом. Стабильность методик оценки связана со стабильностью способов и методов производства, поэтому методики пересматриваются только после тщательного исследования и апробирования на практике.
В условиях интенсификации производства и перевода его на гибкие способы автоматизации приходится существенно изменять методики оценки эффективности, добавляя новые критерии и корректируя их взаимосвязи (особенно критерии оценки показателей косвенной экономии).
Анализ риска и чувствительности экономических решений необходим для выявления сильнодействующих факторов, способных усиливать или ослаблять ожидаемые эффекты от крупных капиталовложений в производство. При экстенсивных методах развития социалистического способа производства анализ риска не имеет большого значения и практически не применяется, так как плановое регулирование инкрементально наращиваемой экономики исключает в значительной степени риск при принятии экономических решений.
Однако с переходом к интенсивным методам хозяйствования и, в частности, к гибким автоматизированным производствам происходит резкое ускорение темпов ввода новых или модернизированных мощностей. При этом, во-первых, техника и способы производства подвергаются не частичным изменениям, а полностью вытесняются новой техникой и технологией и, во-вторых, значительно повышается доля прогрессивной техники и автоматизированных методов управления, что ведет к существенному увеличению начальных капиталовложений.
В соответствии с такими новыми тенденциями даже при плановом регулировании инвестиций начинает возрастать риск отвлечения средств на неоптимальные варианты и направления развития. Поэтому анализ риска и чувствительности становится необходимым звеном в определении и тщательной проверке главных факторов, воздействующих на эффективность капиталовложений в новые формы автоматизации производства.
В частности, контролю подлежат факторы, влияющие на уменьшение ожидаемого объема производства, затягивание по времени ввода производственных мощностей, увеличение затрат на реализацию и внедрение средств автоматизации новых поколений. Действенный инструмент анализа чувствительности — имитационное моделирование гибкого производства в сочетании с экономическими моделями балансового типа.
На различных этапах создания и развития ГПС и РТК возникает ряд трудностей и ошибок. Основные из них могут быть сформулированы в виде проблем, к решению которых подключаются различные специалисты, инженеры и ученые, контрукторы-станкостроители, технологи, математики-программисты, механики, но меньше экономисты и организаторы производства.
В развитии техники можно наблюдать периодическую смену эволюционных и революционных периодов. Цикличное обновление техники осуществляется в форме смены машин. Скачок — массовость применения оборудования, оснащенного микропроцессором, станков с ЧПУ, многооперационных станков и т. д.
Одна из ошибок при внедрении ГПС на ряде предприятий — не революционный, а эволюционный подход, т. е. создание ГПС на базе старых производственных структур с заменой части технических систем новыми, присоединения транспортно-накопительных систем и ЭВМ. Среди причин можно отметить:
1) отставание экономистов, неумение проектировщиков и производственников перестраивать структуру производств с учетом современных принципов организации;
2) отсутствие методов групповой организации и технологии;
3) отсутствие должного учета и проработки важных вопросов концентрации и специализации производства, современных методов оптимизации структур ГПС, календарного планирования, оперативного обслуживания и управления.
При создании ГПС должны учитываться факторы, определяющие перевод структуры организации и управления в новое качество:
1) увеличение многообразия, сложности и масштабов разработки объектов новой техники;
2) частая сменяемость изделий, возрастание многономенклатурности обращающихся в производстве изделий и их частей;
3) снижение серийности выпуска отдельных изделий при увеличении общих объемов производства.
Под воздействием указанных факторов увеличиваются объем и потоки используемой информации.
Примером эволюционного подхода может служить создание ГПС в виде участков из специализированных токарных или фрезерных станков с ЧПУ, реализующих принцип дифференциации операций и не позволяющих получить на этих участках конечный продукт.
Надо создавать программно-целевые участки обработки валов, втулок, шестерен, цанг, подшипников и т. д. В настоящее время нужен не экстенсивный путь развития, а интенсивный.
Среди проблем создания ГПС можно выделить неравномерность развития различных типов изделий в механообработке: преимущественно в обработке корпусных деталей, затем тел вращения и листовых материалов. Это объясняется временем цикла обработки: для корпусных деталей оно больше, что уменьшает необходимость накопления большого запаса деталей на входе в модуль.
Основная проблема ГПС для обработки корпусных деталей связана с расширением номенклатуры продукции, обусловливающим повышенные требования к разнообразию инструмента и необходимому запасу палет. При использовании модулей для обработки тел вращения из-за малого времени обработки повышаются требования к создаваемым на входе заделам деталей и увеличиваются затраты на загрузочно-разгрузочные работы. Главное внимание сконцентрировано на разработке универсальной оснастки и загрузочно-разгрузочных устройств.
Социальные аспекты применения ГПС. Социальные причины необходимости создания ГПС можно разделить на две основные группы: дефицит трудовых ресурсов (в особенности станочников), имеющий тенденцию к росту, и необходимость освобождения работников от физически тяжелого, монотонного, непривлекательного труда. Анализ названных причин показывает, что приемлемым решением является ориентация на быстро переналаживаемые производства, базирующиеся на новых организационных и технологических принципах (групповые технологические процессы) и объединении роботизированных обрабатывающих и транспортно-складских комплексов методами и средствами вычислительной техники.
Реализация проектов ГПС в условиях среднесерийного и мелкосерийного производства, как показывает зарубежный и отечественный опыт, позволяет:
— обеспечить быструю перестройку производства на выпуск новой продукции за счет гибкости производственной системы, полнее удовлетворить запросы заказчиков;
— интенсифицировать технологический процесс — повысить коэффициент сменности (Ксм) и коэффициент загрузки (Кзаг) оборудования, оптимизировать режимы обработки, оперативно корректировать технологические процессы, исходя из текущей ситуации, сократить производственный цикл и «омертвленные» производственные запасы, существенно повысить производительность труда и экономию трудовых ресурсов;
— улучшить социальные условия труда — сократить число занятых во вторую и третью смены, сократить общий объем монотонного, тяжелого, ручного и другого непривлекательного труда за счет высвобождения кладовщиков, контролеров, стропальщиков, грузчиков и других вспомогательных рабочих;
— повысить качество продукции — размерно-геометрическую стабильность обработанных деталей, а также технологичность сборки;
— сократить объем документации (чертежей, технологических карт, рабочих нарядов, материальных карт и т. п.).
Вместе с тем создание автоматизированных (малолюдных) и автоматических (безлюдных) производств в условиях мелкосерийных и среднесерийных производств в 1,5...2 раза дороже, чем использование отдельных многоцелевых станков или другого программно-управляемого оборудования, и требует проведения разнообразных научно-исследовательских и опытно-конструкторских работ, всестороннего научно-технологического обеспечения и подготовки кадров.
При широком внедрении ГПС требуется освоение методов системного проектирования, взаимоувязанной отработки технологических объектов, интегрированных систем автоматизированного управления и подсистем внешнего обеспечения ГПС, создания индустриальной базы централизованного обеспечения и эксплуатационного сервиса.
6.2. Гибкая производственная система токарной обработки
Гибкая производственная система токарной обработки предназначена для автоматизированной обработки деталей типа тел вращения, имеющих наружные и внутренние цилиндрические поверхности со ступенчатым и фасонным профилем и резьбой. ГПС позволяет изготовлять детали из сталей любых марок и сплавов в условиях мелкосерийного и единичного производства при изменяющейся номенклатуре и исключает необходимость частой переналадки технологического процесса.
ГПС, показанная на рис. 6.2, создана Украинским филиалом НИАТ, К.ПО им. Артема (г. Киев), станкостроительным заводом «Комсомолец» (г. Бердичев) и другими организациями.
ГПС включает в себя: гибкие производственные модули токарной обработки в количестве 6 шт.; автоматизированную транспортно-складскую систему; систему управления ГПС; систему автоматизированного проектирования технологических процессов (САПР ТП) и управляющих программ.
Гибкий производственный модуль состоит из токарно-револ-верного станка модели 1В340Ф30, промышленного робота «Электроника НЦТМ-01», устройства смены кассет и системы управления модулем.
Оборудование модуля обеспечивает снятие кассеты с заготовками с транспортного робота-робокара, обработку деталей по заданной технологии, укладку их в кассеты с помощью промышленного робота и погрузку кассет на платформу робокара в автоматическом режиме.
Обеспечивается обработка деталей, имеющих следующие характеристики (рис. 6.3): максимальный диаметр 150 мм; максимальная длина обработки 100 мм; максимальная масса заготовки 3 кг.
В основу построения системы положена групповая технология механической обработки. При малой серийности деталей применяется высокая степень концентрации технологических переходов, последовательно выполняемых в операции, а при большой серийности — высокая степень дифференциации операций с одновременным совмещением переходов во времени.
Токарно-револьверный станок модели 1В340Ф30 оснащен крестовым суппортом с вертикальной осью револьверной головки, позволяющим производить все виды токарной обработки. Конструкция 8-позиционной револьверной головки обеспечивает высокую жесткость и быстродействие фиксации.
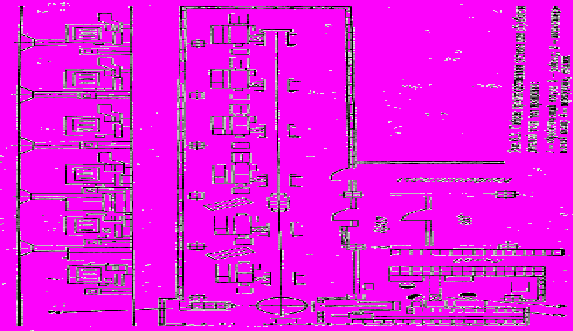
Рис. 6.2. Гибкая производственная система для обработки деталей типа тел вращения:
1 — обрабатывающий модуль; 2 — робокар; 3 — автоматизированный вклад; 4 — перегрузчик, стеллаж
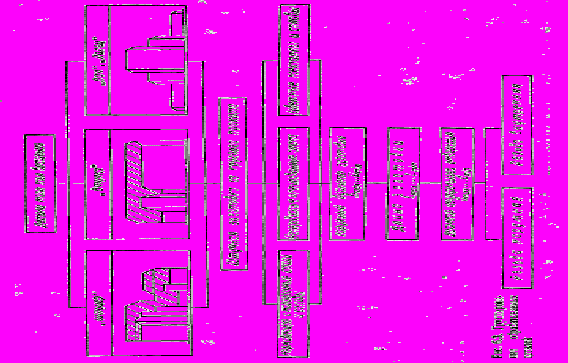
Рис. 6.3. Группирование обрабатываемых деталей
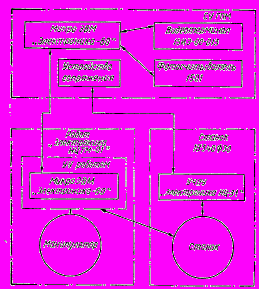
Рис. 6.4. Структурная схема модуля обработки
Промышленный робот «Электроника НЦТМ-01» имеет 5 степеней подвижности, двухкистевое захватное устройство и обеспечивает выбор заготовок из кассеты по двум координатам х и у с перемещением до 300 мм вдоль каждой из них и перенос заготовки в зону обработки с подъемом по оси г до 160 мм.съем обработанных деталей и укладку их в кассету.
Устройство смены кассет дает возможность автоматизировать прием (или выдачу) с транспортной платформы робокара и ориентацию кассет на станке.
Система управления модуля выполняется на базе микроЭВМ «Электроника-60» и позволяет модулю функционировать как в составе ГПС, так и в автономном режиме. Структурная схема модуля обработки показана на рис. 6.4.
Автоматизированная транспортно-складская система включает в себя модуль складирования, модуль транспортирования и систему управления.
Модуль складирования выполнен на базе роботизированного складского комплекса РСК-50 и имеет в своем составе: складской робот, стеллаж и устройство программного управления.
Основные технические характеристики модуля складирования:
Габаритные размеры, мм 8250х1712х3300
Размеры ячеек стеллажа, мм 530х395х315
Грузоподъемность, кг 50
Количество ячеек, шт 154
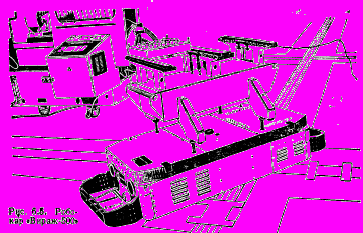
Рис. 6.5. Робокар «Вираж-500»
Транспортирование заготовок и деталей осуществляется с помощью транспортного робота-робокара «Вираж-500» (рис. 6.5). Ро-бокар смонтирован на шасси, имеющем 4 обрезиненных колеса, два из которых — ведущие, а два — рулевые с приводом от системы управления на базе микроЭВМ «Электроника-60». Слежение за трассой из наклеенных на пол алюминиевых полос производится индуктивными датчиками. Связь с центральной ЭВМ СМ 1420 осуществляется посредством оптоэлектронных разъемов, закрепленных в портах — устройствах, фиксирующих положение робокара в конечных положениях. Порты обеспечивают высокую точность позиционирования робокара и фиксацию транспортной платформы о кассетами.
Основные технические характеристики робокара «Вираж-500»: грузоподъемность 500 кг; регулируемая скорость движения не более 1 м/с; время работы без подзарядки аккумуляторной батареи не менее 4 ч; высота подъема пассивной грузовой платформы 80 мм; источники питания — три аккумуляторные батареи; бортовое напряжение 24 В.
Система управления ГПС (рис. 6.6) выполнена на базе мини-ЭВМ СМ 1420. Связь системы управления с основными составными частями ГПС осуществляется посредством стандартного интерфейса ИРПС.
На уровне управления комплексом система осуществляет следующие функции:
— получение суточного задания от автоматизированной системы управления производством (АСУП) или от оператора, хранение и контроль за его выполнением в течение суток;
— обмен информацией и управляющими программами с системами модулей токарной обработки и транспортно-складской системой;
— диспетчеризацию, оперативный контроль состояния и оперативное управление системами нижнего уровня;
— создание и ведение информационной модели роботизированного склада и архива управляющих программ;
— хранение информации о состоянии технологического оборудования и систем управления.
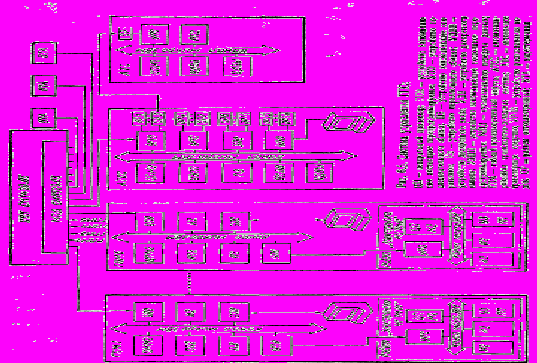
Рис. 6.6. Система управления ГПС:
ЦП – центральный процессор; ПП2 – устройство запоминающее постоянное перепрограммируемое; УПО – устройство последовательного обмена; ПЗ – устройство запоминающее оперативное; И2 – устройство параллельного обмена; УДВВ - устройство дискретного ввода; УДВ – устройство дискретного вывода; УЗПП – устройство запоминающее постоянного перепрограммируемое; МПД – мультипликатор передачи данных; ГПМ – гибкий производственный модуль; АТСС – автоматизированная транспортно-складская система; АТС – автономное транспортное средство; УР-12 – устройство распознавания кодов; ОР – разьем оптоэлектронный; ВТА – видеотерминал
Система визуального контроля, предназначенная для наблюдения за ходом перегрузочных операций на складе и процессов механической обработки, выполнена на базе стандартных телевизионных установок ПТУ-46 и ПТУ-52.
Подготовка техпроцессов для ГПС осуществляется посредством системы автоматизированного проектирования технологического процесса САПР ТП, которая представляет собой человеко-машинную систему, позволяющую разрабатывать операционную технологию обработки на модулях деталей типа тел вращения.
В функции человека входит чтение чертежа и формирование технологического маршрута с указанием геометрических данных обрабатываемых деталей.
Мини-ЭВМ обеспечивает выдачу необходимой информации о технологических операциях, режимах обработки, технологических переходах.
Подготовка управляющих программ реализуется системой автоматизированного проектирования управляющих программ (САПР УП), которая обеспечивает взаимодействие технолога с системой в режиме диалога с помощью видеотерминалов, а также расчет данных для технологического оборудования ГПС.
Применение САПР УП сокращает сроки подготовки управляющих программ в 2...3 раза по сравнению с обычными методами, позволяет получить рациональные решения и снизить трудоемкость подготовки в 3...5 раз.
Гибкая производственная система создана на основе следующих системотехнических принципов:
— агрегатно-модульного построения из переналаживаемых компонентов;
— принципа интеграции;
— принципа иерархического построения и совместимости;
— возможности последующего наращивания (развития) системы.
Принцип агрегатно-модульного построения заключается в типизации, унификации и стандартизации компонентов и отдельных функциональных элементов ГПС, инвариантных к изготовляемым деталям. Такой принцип позволил сформировать состав технических и программных средств на основе применения стандартного аппаратно-программного интерфейса и скомпоновать систему на единой конструктивной базе и основании типовых проектных решений.
Принцип интеграции заключается в соединении систем проектирования деталей (САПР ТП) и управления технологическим процессом (АСУ ТП) в единый комплекс.
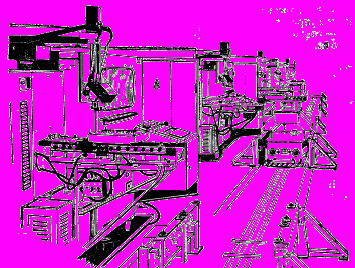
Рис. 6.7. Общий вид ГПС
Принцип иерархичности состоит в соподчинении функциональных элементов, составных частей и автоматизированных средств управления различных уровней и обеспечивает сочетание централизации управления и автономности функционирования отдельных составных частей.
Принцип совместимости, основанный на унификации сигналов, интерфейсов, присоединительных размеров и т. д., состоит в том, что языки, коды, информационные, программные, технические, методологические, энергетические и другие характеристики сопрягаемых элементов ГПС и структурных связей обеспечивают их совместное функционирование без доработки и необходимости внесения изменений.
Принцип развития состоит в обеспечении возможности пополнения, совершенствования и обновления системы и ее компонентов, возможности поэтапного развития ГПС как с точки зрения ее масштабов и организационной структуры, так и уровня автоматизации. В дальнейшем предполагается подключение новых модулей обработки на базе токарных станков ТПК-125, включение устройств контроля износа и поломки режущего инструмента и расширение номенклатуры изготовляемых изделий.
Контрольно-измерительные функции технологического процесса обработки деталей осуществляются за счет оснащения ГПС специальной щуповой головкой БВ, аналогичной щуповой головке, помещенной в револьверную головку станка. Измерения основаны на том, что устройство ЧПУ НЦ-31, управляя перемещением рабочих органов станка, получает сигнал от датчика в момент касания его наконечника с поверхностью измеряемой детали. Информация о координатах этих точек считывается с измерительного преобразователя и используется для расчета размеров и геометрической формы детали. Общий вид ГПС показан на рис. 6.7.
По результатам эксплуатации внедрение гибкой производственной системы такого типа обеспечивает:
— увеличение выпуска продукции в 2.5...3 раза;
— повышение коэффициента сменности работы оборудования Ксм до 2,4;
— повышение коэффициента загрузки станочного оборудования Кз, до 0,8...0,9;
— сокращение потерь рабочего времени;
— повышение качества продукции;
— быстрый переход от обработки деталей одной конфигурации и типоразмера к другой в пределах реализуемого банка управляющих программ и технологических возможностей оборудования.