Анализ и обобщение опыта и тенденций создания промышленных роботов в отечественной и зарубежной робототехнике показывает, что все большее распространение получает электромеханический привод промышленных роботов. Впоследние год
Вид материала | Документы |
СодержаниеУстройства управления промышленными*роботами 4.2. Цикловые устройства управления 4.3. Устройство управления УЦМ-663 |
- Дипломная работа студента, 601.76kb.
- Исать собственные приложения для управления роботами на примере Lego nxt, а также использовать, 76.9kb.
- С применением grid-технологий, 81.79kb.
- История роботов, написанная роботом, 101.24kb.
- Sdfield> Самостоятельная подготовка, 455.42kb.
- Вдокладе описывается технология обучения распределенной системы автономных мобильных, 45.47kb.
- Внушающих уверенность жилищ люди живут в обличии роботов-суррогатов сексуальных, физически, 367.79kb.
- Возможное участие родителей, 108.84kb.
- Анализ работы шмо учителей физики, химии, биологии за 2010-2011 учебный год, 113.58kb.
- Лега В. П. Наука и вера, 152.3kb.
УСТРОЙСТВА УПРАВЛЕНИЯ ПРОМЫШЛЕННЫМИ*РОБОТАМИ
4.1. Классификация устройств управления
В настоящее время создано много разнообразных устройств управления промышленными роботами, начиная от простейших электромеханических и кончая очень сложными в функциональном отношении с использованием интегральных схем. Чтобы внести ясность в широкий спектр устройств управления (УУ), выделим наиболее важные признаки и приведем классификацию этих устройств (рис. 4.1).
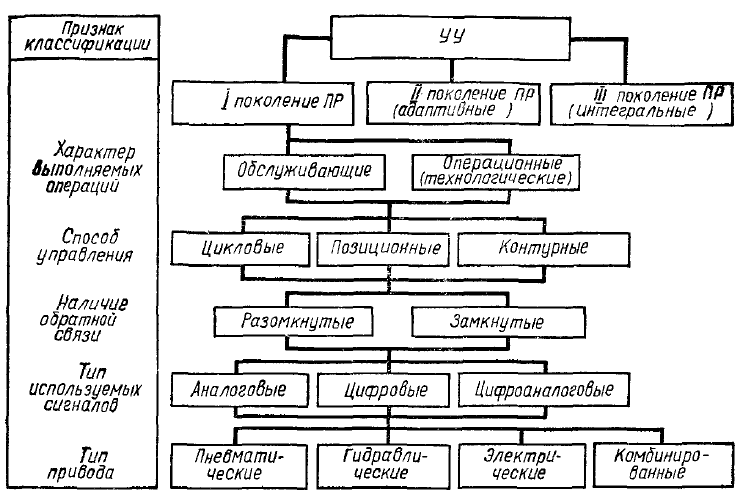
Рис. 4.1. Классификация устройств управления промышленными роботами
Следует отметить, что при разработке, создании и применении устройств управления ПР возникают все традиционные требования, предъявляемые к устройствам управления другими производственными процессами и оборудованием, как, например, к устройствам управления металлорежущими станками с числовым программным управлением. В частности, это касается надежности, быстродействия, объема памяти, элементно-конструктивной базы и стоимости. Подробное рассмотрение всех параметров не входит в задачу данного учебного пособия, так как обстоятельно изложено в соответствующих курсах. Здесь приведены в основном отличительные особенности устройств управления ПР.
Помимо приведенных признаков классификации (см. рис. 4.1) существуют признаки, отличающие устройства управления промышленными роботами от других, известных в настоящее время. Один из таких признаков — уровень управления (рис. 4.2).
I уровень (рис. 4.2, а). Каждую единицу технологического оборудования дополняют соответствующим промышленным роботом, выполняющим простые циклические операции — установку в оборудование заготовок, снятие деталей и т. д.
II уровень (рис. 4.2, б). Технологически объединенную группу оборудования оснащают стационарным или подвижным промышленным роботом, который осуществляет установку и съем деталей, выполняя другие вспомогательные операции (измерение, контроль и т. д.); при этом поведение ПР определяется запросами от единицы оборудования и условиями выполнения программы обслуживания.
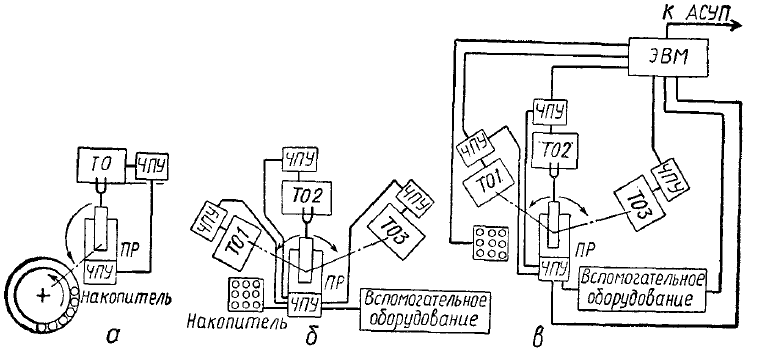
Рис. 4.2. Уровни управления промышленными роботами: «— I; в — II: в — III
III уровень (рис. 4.2, в). Высокая степень автоматизации на основе группового управления оборудованием и роботами от распределенной системы управления оборудованием или центральной ЭВМ, решающей также задачи диспетчеризации, управления складом, транспортными средствами и т. д.
С некоторым приближением можно сказать, что I уровень — это управление отдельным роботом или простейшим роботизированным технологическим комплексом, II — управление роботизированным технологическим комплексом средней и высокой сложности, III — управление гибкой производственной системой.
Наконец, различные устройства управления могут классифицироваться по степени сложности решаемых задач. Эта классификация в известной степени связана с методами обучения и дистанционным управлением роботами (рис. 4.3). На рисунке представлены четыре уровня взаимодействия человека-оператора с устройством управления роботом: интеллектуальный, стратегический, тактический и исполнительный (штриховкой показано качественное соотношение объемов информации).
Все три приведенные классификации не только не противоречат друг другу, но в известной степени и дополняют.
Можно сказать, что первая классификация отражает элементно-конструктивную базу, структуру и внутренние связи в устройствах управления, вторая — степень сложности в зависимости от количества единиц технологического и вспомогательного оборудования, третья — показывает уровень интеллектуальности устройств управления. Заметим, что III и IV уровни относятся к адаптивным роботам и роботам с искусственным интеллектом.
Стремление создать единую, всеобъемлющую классификацию устройств управления неизбежно приводит к неоправданному увеличению ее сложности, что значительно затрудняет восприятие и понимание такой классификации, поэтому автор приводит три классификации, отличающиеся в методическом плане.
Существующие в настоящее время устройства управления промышленными роботами (кроме цикловых) относятся к классу систем числового программного управления (ЧПУ).
В зарубежной и отечественной литературе системы числового программного управления принято делить на следующие типы:
— NC (Numerical control) — числовое программное управление обработкой на станке по программе, заданной в алфавитно-цифровом коде. Эти устройства работают по «жесткой логике», программа вводится, как правило, на перфоленте или магнитной ленте;
— HNC (Hand NC) — разновидность устройств ЧПУ с ручным заданием программы с пульта управления (на клавишах, переключателях и т. д.). В последнее время эти системы получили дальнейшее распространение и теперь выпускаются следующие их типы: TNC (Total NC) и VNC (Voice NC). Устройства типа TNC имеют в своем составе внешнюю память на гибких дисках (для хранения управляющих программ) и дисплеи для организации общения оператора с устройством ЧПУ. В устройствах ЧПУ типа VNC управляющая программа вводится непосредственно с голоса. Принятая информация затем отображается на дисплее, что обеспечивает визуальный контроль правильности ввода;
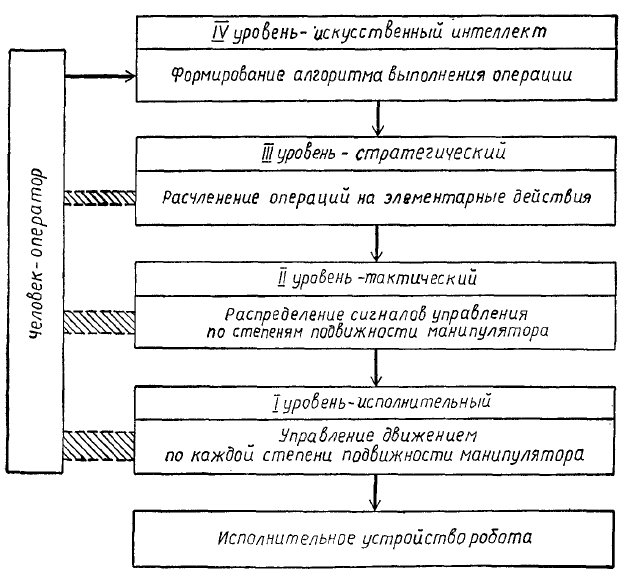
Рис. 4.3. Уровни взаимодействия человека-оператора в устройствами управления
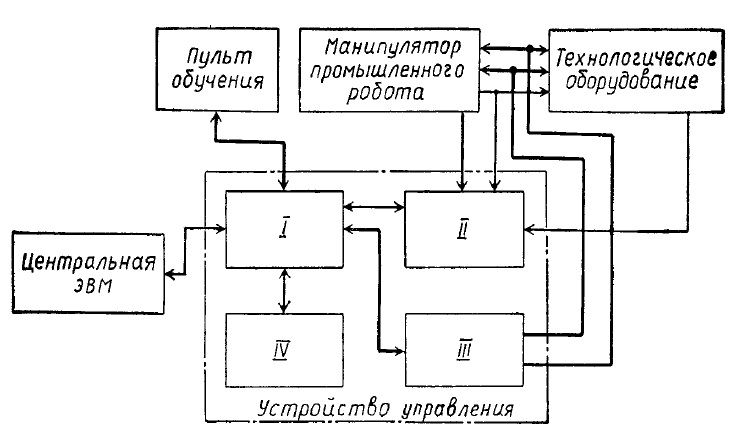
Рис. 4.4. Обобщенная структурная схема устройства управления промышленным роботом:
I — управляющий модуль; II — информационный; III —исполни ельный; IV — программозадающий; -основные сигналы программного управления: -сигналы адаптивного управления
— SNC (Speicher NC) и (или) MNC (Memory NC) — разновидность устройств ЧПУ, имеющих память для хранения всей управляющей программы;
— CNC (Computer NC) — автономное устройство ЧПУ, содержащее ЭВМ или процессор;
— DNC (Direct NC) — устройство для управления группой оборудования от ЭВМ, осуществляющее хранение программ и распределение их по запросам от локальных устройств управления оборудованием (на оборудовании могут быть установлены устройства типа NC, SNC, CNC). Устройства ЧПУ типа NC и HNC имеют постоянную структуру, а устройства типа SNC и CNC — переменную.
Несмотря на то, что эта классификация была создана для устройств числового программного управления металлорежущими станками, сейчас она применяется и для устройств управления промышленными роботами.
Описывая устройства числового программного управления промышленными роботами, следует хотя бы кратко остановиться на их структурной (функциональной) схеме.
В ряде опубликованных статей, монографий и учебных пособий встречаются разнообразные структурные схемы устройств управления роботами, но при внимательном рассмотрении оказывается, что между ними нет принципиальных различий. Как правило, они отличаются лишь степенью детализации модулей, связей и графической компоновкой.
На рис. 4.4 приведена обобщенная структурная схема устройства управления промышленным роботом.
Далее мы переходим к рассмотрению устройств управления ПР различного типа.
4.2. Цикловые устройства управления
В большинстве случаев перемещения манипулятора промышленного робота представляют собой определенную последовательность операций, направленных на выполнение заданной производственной, технологической задачи. Конечную последовательность движений рабочего органа манипулятора, после выполнения которой он занимает начальное положение, называют циклом, а устройства, обеспечивающие циклическую работу исполнительных, рабочих органов,— цикловыми.
Большое количество промышленных роботов предназначено для выполнения относительно простых операций, сводящихся к процессу «взять — перенести — положить», и поэтому цикловые устройства управления различного типа широко применяются в промышленной робототехнике.
Работа цикловых устройств управления имеет дискретный характер. Рабочий цикл можно разбить на несколько интервалов — тактов, представляющих собой интервалы времени, в течение которых выполняется определенное перемещение по ранее заданному закону. Цикловые устройства многотактны и имеют обычно жесткую последовательность тактов. Применение в управляющей части специальных программных задающих устройств позволяет при необходимости изменять рабочий цикл, дает основание называть цикловые устройства устройствами программного управления. Цикловые устройства программного управления часто монтируют вместе с приводами и подчас трудно отделить собственно управляющую часть от исполнительной.
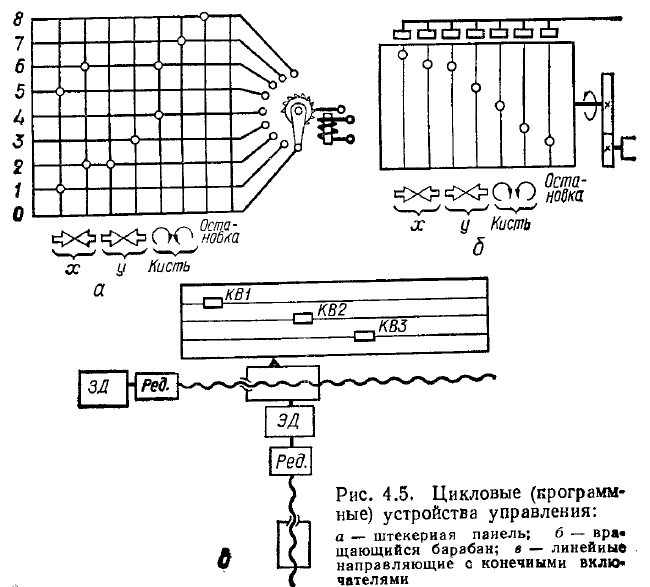
Рис. 4.5. Цикловые (программные) устройства управления: а — штекерная панель; 6 — вращающийся барабан; в — линейные направляющие о конечными включателями
По виду используемой энергии в приводной части устройства циклового программного управления могут быть пневматические, гидравлические, электрические и комбинированные.
Основное назначение задающего программного устройства — обеспечить последовательность выполнения технологических операций в соответствии с заданной программой, которая может периодически изменяться. В относительно простых случаях в качестве программного устройства используют штекерную панель (рис. 4.5, а). Рабочий цикл изменяют, переставляя штекеры. Таким образом, перекоммутируют линии связи между логическими элементами в соответствии с новым циклом. В более сложных случаях программное устройство может иметь вращающийся барабан (рис. 4.5, б) в виде кулачкового вала, воздействующего при вращении на командные элементы, или многоканальное золотниковое устройство. В качестве носителей программы могут использоваться также перфокарты или перфолента. Команды, заданные программным устройством, поступают на привод соответствующей координаты. Линейное перемещение рабочего органа определяется положением конечного выключателя (рис. 4.5, в).
В большинстве случаев программные задающие устройства — это оригинальные узлы в цикловых устройствах программного управления, хотя иногда их можно построить и на нормализованных элементах гидро- и пневмоаппаратуры.
4.3. Устройство управления УЦМ-663
В последние годы, по предложению нескольких организации принято обозначать тип устройства числового программного управления соответствующим образом. Например, УЦМ-663 расшифровывается так: У — унифицированное; Ц — цикловое; М — модульное, б — шестикоординатное; 6 — в том числе управляющее всеми шестью координатами одновременно; 3 — цифра, поясняющая выход на привод циклового устройства. УЦМ-663 предназначено для управления манипуляторами промышленных роботов с позиционированием по упорам и соответствующим технологическим оборудованием.
Техническая характеристика УЦМ-663
Тип устройства цикловое
Число управляемых координат 6
Число одновременно управляемых координат 6
Число точек позиционирования:
по двум координатам 8
по четырем координатам 4
Число координат с режимом торможения 6
Число управляемых захватных устройств 6
Число выдаваемых технологических команд о возможностью подтверждения исполнения 12
Число одновременно выдаваемых технологических команд 2
Число воспринимаемых устройством внешних блокировочных сигналов
В том числе:
от манипулятора 12
от технологического оборудования 6
от ограждения манипулятора 1
от датчика давления гидропневмосети 1
Объем запоминающего устройства (количество единичных команд) 224
Количество программ, одновременно размещаемых в памяти
в пределах объема запоминающего устройства) 4
Число разветвлений в программе 8
Число условных обращений к подпрограммам 4
Число циклов в программе 2
Число повторений цикла 10
Число каналов управления золотниками манипулятора 28
Число каналов управления внешним оборудованием 12
Число каналов управления золотниками привода захватных устройств 4
Напряжение питания датчиков манипулятора и технологического оборудования, В 24±2
Питание устройства осуществляется от сети переменного тока: 38
напряжение, В 380±57
частота, Гц 50
Масса устройства, кг 113
Габаритные размеры устройства, мм:
высота 1221
ширина 480
глубина 475
При сохранении технических характеристик устройство Допускает непрерывную работу в течение 16 ч.
Работает устройство УЦМ-663 по принципу синхронного автомата с жестким циклом управления. Состоит УЦМ-663 из следующих основных функциональных блоков (рис. 4.6), которые осуществляют:
— блок управления — обработку информации по заданной программе и выдачу управляющих воздействий на манипулятор и технологическое оборудование;
— запоминающее устройство — хранение требуемой программы работы робота;
— встроенный пульт оператора — задание режимов работы устройства, выполнение операций включения — выключения питания, запуск в работу, а также ручное управление звеньями манипулятора;
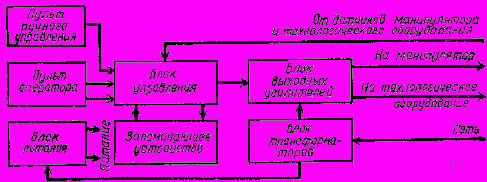
Рис. 4.6 - Структурная схема устройства управления УЦМ-663
— выносной пульт ручного управления — ручное управление звеньями манипулятора в наладочном режиме;
— блок усилителей — выдачу управляющих команд необходимой мощности на золотники манипулятора и технологическое оборудование;
— блок питания — питание электронного оборудования, датчиков обратной связи манипулятора и технологического оборудования;
— блок трансформаторов — включение и преобразование напряжения сети 380 В, подавление индустриальных помех, проникающих по каналу питания в устройство.
Основные режимы работы устройства УЦМ-663 следующие: «Ручной», «Наладка», «Кадр», «Команда», «Цикл», «Автомат», «Задание программы».
В ручном режиме команды управления звеньями манипулятора задают с пульта оператора или с ручного пульта. При этом блок управления выдает управляющую информацию на блок усилителей, включающих требуемые комбинации золотников манипулятора. Отрабатываются команды по получении сигналов от соответствующих датчиков манипулятора.
В режиме «Наладка» команды на манипулятор задают с пультов оператора или ручного управления. В отличие от ручного режима, выдача команд управления звеньями манипулятора прекращается после отпускания соответствующих кнопок на пульте оператора и ручного управления.
В режиме «Команда» устройство отрабатывает текущую команду кадра, хранящуюся в запоминающем устройстве. После отработки команды устройство останавливается.
Таблица 4.1. Система команд устройства УЦМ-663
Команда | Обозначение на кнопках | 7 | 6 | 5 | 4 | 3 | 2 | 1 |
Движение | 0 | Направле-ние дви-жения | Номер координаты | Номер точки | ||||
Схват 1 открыть | Схв. 1 Откр. | 1 | 1 | 10 | 0 | 0 | 0 | 0 |
Схват 1 закрыть | Схв. 1 Закр. | 1 | 1 | 0 | 0 | 1 | 1 | 1 |
Схват 2 открыть | Схв. 2 Откр. | 1 | 1 | 0 | 1 | 0 | 0 | 0 |
Схват 2 закрыть | Схв. 2 Закр. | 1 | 1 | 0 | 1 | 1 | 1 | 1 |
Внешнее оборудование 1 | ВО 1 | 1 | 1 | 0 | 0 | Номер техкоманды | ||
Внешнее оборудование 2 | ВО 2 | 1 | 1 | 0 | 1 | Номер техкоманды | ||
Выдержка времени | ВВ | 1 | 0 | 1 | Выдержка времени | |||
Совместная обработка | СО | 1 | 1 | 1 | 1 | Число команд в кадре | ||
Условный переход | УП | 1 | 0 | 0 | 1 | Номер внешнего условия | ||
Конец программы | КП | 1 | 0 | 0 | 0 | 0 | Номер программы | |
Обращение к подпрограмме | ОПП | 1 | 0 | 0 | 0 | 1 | Номер подпрограммы | |
Конец подпрограммы | КПП | 1 | 1 | 1 | 0 | 1 | 1 | 0 |
Начало цикла | НЦ | 1 | 1 | 1 | 0 | 0 | 1 | №СЧЦ |
Конец цикла | КЦ | 1 | 1 | 1 | 0 | 0 | 0 | № СЧЦ |
Модификация | МОД | 1 | 1 | 1 | 0 | 1 | 0 | № СЧЦ |
Останов | ОСТ | 1 | 1 | 1 | 0 | 1 | 1 | 1 |
В режиме «Кадр» отрабатывается один кадр программы, хранящейся в запоминающем устройстве. После отработки кадра программы (т. е. отработки всех команд в кадре) устройство останавливается.
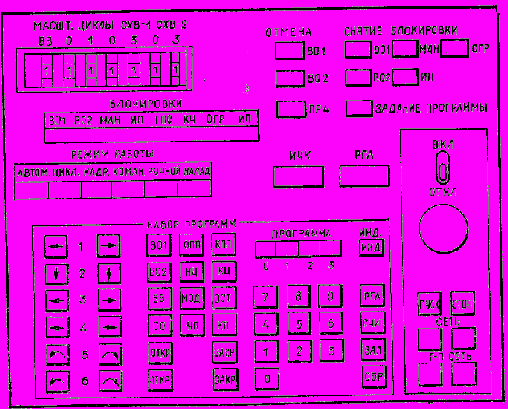
Рис. 4.7 – Вид пульта оператора УЦМ-663
В режиме «Цикл» однократно отрабатываются все кадры программы.
В режиме «Автомат» многократно отрабатывается рабочий цикл робота.
В режиме «Задание программы» осуществляются занесение в память команд программы и контроль информации, записанной в памяти.
В устройстве используется кадр переменной длины, состоящий из одной или нескольких команд. Система команд приведена в табл. 4.1.
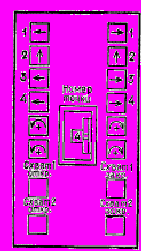
Рис. 4.8 – Вид пульта ручного управления УЦМ-663
Конструктивно устройство выполнено в виде напольного шкафа. Внутри шкафа размещены блоки трансформаторов, вентиляторов, питания и контейнер с платами блока управления, блока входных усилителей и запоминающего устройства. В верхней части шкафа расположен пульт оператора (рис. 4.7), предназначенный для набора программы работы устройства, ее контроля, индикации состояния устройства и ручного управления звеньями манипулятора.
Пульт ручного управления (рис. 4.8), предназначенный для управления звеньями манипулятора в наладочном режиме, конструктивно размещен в отдельном переносном корпусе и соединен со стойкой кабелем длиной 10 м.
Устройство УЦМ-663 выпускается серийно и является достаточно совершенным устройством этого класса.