Анализ и обобщение опыта и тенденций создания промышленных роботов в отечественной и зарубежной робототехнике показывает, что все большее распространение получает электромеханический привод промышленных роботов. Впоследние год
Вид материала | Документы |
- Дипломная работа студента, 601.76kb.
- Исать собственные приложения для управления роботами на примере Lego nxt, а также использовать, 76.9kb.
- С применением grid-технологий, 81.79kb.
- История роботов, написанная роботом, 101.24kb.
- Sdfield> Самостоятельная подготовка, 455.42kb.
- Вдокладе описывается технология обучения распределенной системы автономных мобильных, 45.47kb.
- Внушающих уверенность жилищ люди живут в обличии роботов-суррогатов сексуальных, физически, 367.79kb.
- Возможное участие родителей, 108.84kb.
- Анализ работы шмо учителей физики, химии, биологии за 2010-2011 учебный год, 113.58kb.
- Лега В. П. Наука и вера, 152.3kb.
5.9. Экономическая эффективность применения промышленных роботов
Экономическая эффективность промышленных роботов — очень важный, хотя и не единственный показатель возможности и целесообразности применения промышленных роботов в промышленности и народном хозяйстве СССР.
Рассмотрим методику расчета экономической эффективности от внедрения промышленных роботов на предприятиях машиностроительной промышленности.
Внедрение промышленных роботов в машиностроении требует выполнения определенных технических и организационных мероприятий, затраты на которые должны учитываться при расчете экономической эффективности. К ним относятся:
1) предварительная технологическая подготовка (анализ изделий, технологических процессов и оборудования);
2) модернизация основного технологического оборудования с целью подготовки его к применению промышленных роботов;
3) создание специального или специализированного оборудования для ориентированного хранения (либо транспортирования) заготовок и деталей;
4) создание специальной или специализированной оснастки и инструмента;
5) перепланировка производственных участков.
Расчет экономической эффективности и выбор баз сравнения следует проводить с учетом принадлежности ПР к роботизированному технологическому комплексу.
Основными источниками экономической эффективности промышленных роботов и РТК являются:
1. Повышение производительности оборудования, т. е. объема выпускаемой продукции с основного технологического оборудования, обслуживаемого роботом, или повышение производительности труда на операциях, выполняемых промышленным роботом.
2. Повышение производительности труда в результате замены ручного труда на вспомогательных, транспортных операциях (загрузка-разгрузка деталей и инструмента, транспортирование деталей и т. д.) и основных технологических операциях (сварка, сборка, окраска и пр.).
3. Повышение ритмичности производства.
4. Повышение коэффициента сменности оборудования без увеличения численности рабочих.
5. Уменьшение потерь, связанных с субъективными особенностями человека (постоянство режима работы в течение смены).
6. Снижение процента брака и повышение стабильности качества продукции.
7. Уменьшение размеров оборотных средств в незавершенном производстве.
Применение промышленных роботов, кроме того, позволяет решить в народном хозяйстве ряд социальных задач, а именно: изменить характер труда и создать новые условия труда рабочего в промышленности; снизить травматизм и возможность возникновения профессиональных заболеваний; уменьшить текучесть кадров; облегчить общую демографическую проблему нехватки рабочей силы в народном хозяйстве; уменьшить затраты на жилищное и культурно-бытовое строительство и т. д.
При расчете экономической эффективности нужно правильно выбрать базовый, сопоставимый вариант. Сравнивать необходимо по объему и качеству выпускаемой продукции, режиму работы, уровню цен, используемым тарифам и комплексу специальных факторов. Сопоставляют варианты по годовому объему продукции, как правило, при условии двухсменной работы оборудования. В особых случаях, связанных с непрерывным технологическим процессом, а также для случая, когда число смен оговорено заданием заказчика, экономический эффект определяют для заданного режима производства.
Оптовую цену оборудования действующего производства (базовый вариант) для сопоставимости нужно привести к современному уровню цен (с 01.01.1982 г.) применением следующих коэффициентов: 1,6—к оборудованию, изготовленному до 1967 г.; 1,2 — к оборудованию, изготовленному в 1968—1972 гг. Цены базового оборудования, которое изготовлено в 1973—1981 гг., но не вошло в прейскуранты, введенные в действие с 01.01.1982 г., принимают с коэффициентами по справочнику «Изменение средних оптовых цен в связи с введением 01.01.1982 г. новых прейскурантов» (М., 1981) или по иным нормативным документам.
Определение экономической эффективности разработки и создания промышленных роботов и роботизированных технологических комплексов. При создании новых роботов и РТК расчет экономической эффективности проводят на следующих этапах:
1) разработка технико-экономического обоснования создания ПР и РТК;
2) разработка технического задания (ТЗ);
3) разработка технического проекта;
4) разработка рабочей документации;
5) приемка опытного образца.
Расчеты на первом и втором этапах носят предварительный характер. На всех последующих этапах проводят уточненные расчеты в связи с изменением некоторых параметров и уточнением цен. При приемке опытного образца расчет должен учитывать сравнительную производительность, указанную в акте приемки, и проектируемую оптовую цену.
В качестве базового варианта для сравнения на этапе создания промышленного робота принимают лучшие образцы, выпускаемые серийно в СССР или за рубежом, которые имеют сопоставимые технические показатели и технологические возможности. В случае отсутствия аналога в СССР или за рубежом в качестве базы принимают: 1) для производственных роботизированных комплексов — передовое специальное технологическое оборудование, используемое для аналогичных операций в СССР (с ручными операциями); 2) для технологических роботизированных комплексов, рассчитанных на работу с технологическим оборудованием определенного назначения,— то же оборудование с ручным обслуживанием. При этом из номенклатуры оборудования, которое может обслуживать промышленный робот, нужно выбрать одну модель со средними показателями или модель, занимающую значительный удельный объем в выпуске.
Для универсальных промышленных роботов расчет должен проводиться в условиях преимущественного использования роботов с назначением соответствующих баз сравнения. Для РТК в качестве базы сравнения принимают основное технологическое оборудование, входящее в состав данного комплекса, который обслуживается другим промышленным роботом, выпускаемым серийно в СССР или за рубежом, либо то же оборудование с ручным обслуживанием. При создании роботизированных комплексов, в состав которых входят технологические роботы (сборочные, сварочные и др.), в качестве базы сравнения принимают лучшее аналогичное оборудование или действующий технологический процесс, реализуемый с применением ручного труда.
При создании промышленных роботов экономический эффект рассчитывают с учетом использования их в составе соответствующего роботизированного комплекса. Известно, что применение РТК позволяет сократить организационные потери и время простоев оборудования, повысить равномерность выпуска продукции, упорядочить планирование и диспетчеризацию. В связи с этим коэффициент загрузки оборудования принимают равным 0,85, а для базового варианта — 0,6.. .0,7.
При создании полностью автоматизированных комплексов, снабженных системой автоматической диагностики и устранения неисправностей, смены инструмента, контроля и т. д., которые обеспечивают безотказную работу в течение трех смен, в расчетах принимают трехсменный режим работы, а для базового варианта в этом случае — двухсменный.
Решение о целесообразности создания промышленного робота или роботизированного технологического комплекса принимают на основании расчета экономического эффекта от производства и использования выпуска этого оборудования в расчетном году:
Э = ЭедА2 (5.2)
где Э — годовой экономический эффект, р.; Эед — экономический эффект от производства и использования одного (единицы) промышленного робота или роботизированного технологического комплекса, р.; А2 — выпуск промышленных роботов в расчетном году, шт.; индексы «1» и «2» в формуле (5.2) и в последующих формулах относятся соответственно к базовому и новому оборудованию, а величины без индексов относятся к обоим вариантам.
Если экономический эффект определяют для серийно выпускаемых промышленных роботов, то за расчетный год принимают второй год с начала их промышленного производства, а для очень сложных моделей роботов — третий. Начало серийного производства исчисляют от первого года включения роботов в план производства и, как правило, после изготовления установочной серии.
Экономический эффект от производства и применения одного промышленного робота определяют по формуле
Эед=(Ц1*В2/В1(Р1+Ен)/(Р2+Ен))+((И1-И2)-Ен*(К2-К1))/(Рам+Ен)-Ц2 (5.3)
где Ц1, Ц2 — стоимость оборудования, p.; B2/B1 — коэффициент, учитывающий рост производительности единицы нового оборудования по сравнению с базовым; В1, В2 — годовой объем продукции, производимой при использовании единицы базового и нового оборудования, в натуральных единицах; Р1, Р2— доля отчислений от балансовой стоимости на полное восстановление базового и нового оборудования, р. (рассчитывают как величину, обратную сроку службы оборудования, определяемому с учетом морального износа оборудования); Ен— нормативный коэффициент эффективности капитальных вложений, равный 0,15; (Р1+Ен)/(Р2+Ен) - коэффициент учета изменения сроков службы нового оборудования по сравнению с базовым, как правило, Р1 = Р2, тогда
(Р1+Ен)/(Р2+Ен)=1
Р1 и Р2 могут иметь разное значение только в тех случаях, когда изменение этих параметров обусловлено требованиями заказчика в его заявке на разработку новой продукции и отражено в нормативно-технической документации; Рам — доля (коэффициент) отчислений на реновацию (амортизацию) при использовании потребителем нового оборудования, р. (рассчитывают как величину, обратную сроку службы Тс нового оборудования, определяемому с учетом морального износа; средние прогнозируемые сроки службы промышленных роботов составляют 8 лет, при этом Рам = 0,0874); И1 и И2 — годовые эксплуатационные издержки потребителя при использовании базового и нового оборудования в расчете на годовой объем продукции, производимой с помощью нового оборудования, р. (амортизационные отчисления на оборудование учитываются в этих издержках только в части, предназначенной на его капитальный ремонт, т. е. без учета средств на реновацию; в издержках учитываются также амортизационные отчисления по соответствующим капитальным вложениям потребителя); К1; К2 — соответствующие капитальные вложения потребителя (без стоимости оборудования) при использовании базового и нового оборудования в расчете на годовой объем продукции, производимой с помощью нового оборудования, р.
Сопутствующие капитальные вложения К' представляют собой сумму единовременных затрат потребителя новой техники на основные и оборотные фонды (без стоимости новой техники):
К' = Км + Кзд + Ксл +Кнз + Кпр + Кп.у + Ктех + Кж (5.4)
где Км — затраты по установке и доставке оборудования; Кзд — стоимость помещения, занимаемого оборудованием; Ксл — стоимость служебно-бытовых помещений; Кнз— оборотные средства в незавершенном производстве; Кпр — стоимость специальных приспособлений; Кп.у — стоимость программ управления; Ктех — затраты на проектные работы по привязке промышленного робота и роботизированного технологического комплекса к условиям заказчика; Кж — стоимость жилищного и культурно-бытового строительства.
Расчет сопутствующих капитальных вложений ведут на единицу нового оборудования и эквивалентное количество оборудования базового варианта.
Годовые эксплуатационные издержки потребители И определяют суммированием изменяющихся прямых затрат и расходов на содержание и эксплуатацию оборудования:
И = Ииз + Ип.у + Ипр + Иу.с.п + Им - Ипл + Исл + Ир + Иу + Иэ + Ив (5.5)
где Ииз — годовая зарплата условно высвобождаемых рабочих (со всеми начислениями); Ип.у — годовые затраты на подготовку и возобновление программ управления; Ипр — годовые затраты на амортизацию и ремонт специальных приспособлений; Иу.сп — годовые затраты на прокат универсально-сборочных приспособлений; Им — годовые амортизационные отчисления на полное восстановление по сопутствующим капитальным вложениям (затраты по доставке и установке оборудования); Ипл — годовые затраты на амортизацию и содержание помещения, занимаемого оборудованием; Исл — годовые затраты на амортизацию и содержание служебно-бытовых помещений; Ир — годовые затраты на ремонт (включая капитальный) и техническое обслуживание оборудования (кроме устройств ЧПУ); Иу — годовые затраты на техническое обслуживание и «ремонт ЧПУ; Иэ — годовые затраты на силовую электроэнергию; И„ — годовые затраты на сжатый воздух. Для отдельных типов промышленных роботов некоторые статьи могут быть исключены или добавлены в зависимости от конкретных производств.
Основная статья экономии эксплуатационных издержек при использовании промышленных роботов, роботизированных комплексов и линий — заработная плата условно высвобождаемых рабочих, которую можно определить умножением среднегодовой заработной платы одного рабочего на количество высвобождаемых рабочих. В расчетах экономической эффективности следует учитывать реальную заработную плату по профессиям и разрядам с учетом коэффициентов выполнения норм, премий, дополнительной заработной платы и отчислений на соцстрах. На стадии создания промышленного робота заработную плату рабочих целесообразно рассчитывать
на основании нормативов. При отсутствии таких нормативов, а также на этапе внедрения заработную плату принимают по данным конкретных предприятий. К. расчетному фонду основной и дополнительной заработной платы (без отчислений на соцстрах) по сравниваемым вариантам на всех этапах расчета вводят коэффициент k =1,49, учитывающий общественные фонды потребления.
Определение экономической эффективности внедрения роботизированных комплексов. Основной экономический эффект может быть получен при внедрении промышленных роботов и роботизированных комплексов на конкретных заводах и предприятиях-потребителях. Экономическую эффективность внедрения рассчитывают для следующих этапов:
1) определение целесообразности внедрения;
2) определение фактического экономического эффекта от внедрения.
В случае, когда внедрение происходит в порядке модернизации существующего технологического процесса и сопровождается заменой устаревшего оборудования, экономическую эффективность оценивают сравнением показателей по трем вариантам производства: роботизированный комплекс; технологическое оборудование, входящее в состав комплекса с ручным обслуживанием; заменяемое оборудование. Решение о целесообразности внедрения той или иной новой техники принимают по минимуму приведенных затрат в сравниваемых вариантах. Фактическую экономию определяют сравнением с заменяемой техникой.
На этапе внедрения расчеты экономического эффекта выполняет завод, приобретающий промышленные роботы, или по его поручению организация-разработчик и утверждает главный инженер этого завода.
На всех этапах внедрения годовой экономический эффект определяют по формуле
Э2 = (31 - 32) = (С1+ЕнК1) - (С2 + ЕнК2) (5.6)
где Э2 — экономический эффект от использования промышленных роботов и роботизированных комплексов за один год эксплуатации; З1 — приведенные затраты потребителя по базовому варианту, рассчитанные на годовой выпуск продукции, которая производится при использовании роботизированного комплекса; 32 — приведенные затраты потребителя при использовании роботизированного комплекса; d — себестоимость по базовому варианту, рассчитанная на годовой выпуск продукции, которая производится при использовании роботизированного комплекса; С2 — себестоимость годового выпуска продукции, производимой на роботизированном комплексе; K1— капитальные вложения потребителя по базовому варианту, рассчитанные на годовой выпуск продукции, которая производится при использовании роботизированных комплексов; К2 — капитальные вложения потребителя при использовании роботизированного комплекса; Ен — нормативный коэффициент эффективности, равный 0,15.
Эффективность внедрения будет иметь место в случае положительной разности приведенных затрат З1 — 32. При этом срок окупаемости должен быть менее 6...7 лет.
Срок окупаемости дополнительных капитальных вложений определяют по формуле
Ток=(К2-К1)/(С1-С2) (5.7)
Капитальные вложения потребителя определяют так:
К = Кб + Кзд + Кол + Кнз + Кпр + Кп.у + Ктех + Кж, (5.8)
где Кб — балансовая стоимость оборудования.
Если в качестве базового принимают современное оборудование, то балансовую стоимость рассчитывают по формуле
Кб=Ц1iPпіα,
гдеЦ1i— оптовая цена конкретной модели базового оборудования; а — коэффициент, учитывающий затраты на доставку и установку оборудования, включая пусконаладочные работы; Pпіα— принятое количество оборудования.
Если в качестве базового принимают оборудование действующего предприятия, то при расчете Кб не учитывают, а под ним понимают балансовую стоимость конкретной модели базового оборудования по данным заказчика.
Балансовую стоимость роботизированного комплекса Кб2 определяют либо умножением его стоимости Цз на коэффициент а, либо по фактическим данным предприятия (если комплекс введен в эксплуатацию).
Себестоимость годового выпуска продукции определяют по формуле
С = Из + Ип.у + Ипр + Иу.с.п + Иб + Ипл + Исл + Ир + Иу + Иэ + Ив, (5.9)
где Иб — годовые амортизационные отчисления на полное восстановление оборудования,
И6 = КбР (5.10)
Здесь Р — амортизационные отчисления на полное восстановление ' оборудования в долях единицы.
В настоящей методике, как и в методике для станков с числовым программным управлением, годовые амортизационные отчисления от стоимости оборудования учитывают следующим образом:
— на полное восстановление оборудования — в процентах к балансовой стоимости по формуле (5.10);
— на капитальный ремонт — в зависимости от ремонтной сложности оборудования и разработанных нормативов годовых затрат на единицу ремонтной сложности по всем видам ремонта, включая капитальный.
Определяя целесообразность приобретения промышленных роботов и роботизированных комплексов, используют расчетные показатели (годовую программу выпуска деталей, количество наименований обрабатываемых деталей и т. д.) и нормативные данные. Стоимость проектных работ по привязке промышленных роботов к конкретным условиям заказчика принимают по смете к договору либо по данным заказчика.
Чтобы рассчитать фактическую экономическую эффективность внедрения промышленных роботов и роботизированных комплексов, нужно иметь данные, характеризующие фактическую номенклатуру деталей, обрабатываемых на этом оборудовании, фактическую годовую программу выпуска каждой детали. Фактические данные по эксплуатации роботизированного комплекса в сравнении с базовым вариантом должны быть утверждены заводом-заказчиком.
Стоимость роботизированного комплекса принимают по балансовой стоимости по данным бухгалтерии завода с учетом фактических затрат на проектные работы.
Чтобы рассчитать экономическую эффективность промышленных роботов, можно пользоваться «Инструкцией по оценке экономической эффективности создания и использования автоматических манипуляторов с программным управлением (промышленных роботов)» (М. : НИИМаш Минстанкопрома, 1983.— 84 с).
Полезные материалы приведены в «Межотраслевой методике определения экономической эффективности новых направлений технического прогресса на примере внедрения гибких производственных систем», подготовленной межотраслевым советом по роботам в области экономики и выпущенной в серии «Межотраслевая экономика и совершенствование хозяйственного механизма» (Вып. 1., М., 1986).
5.10. Надежность промышленных роботов и РТК
Общие положения. Надежность промышленных роботов — это свойство сохранять во времени в установленных пределах значения всех параметров, характеризующих способность выполнять двигательные и управляющие функции с заданной точностью позиционирования.
Известно, что надежность — сложное свойство, характеризующееся четырьмя составляющими: безотказностью, ремонтопригодностью, сохраняемостью и долговечностью. Каждой составляющей надежности соответствует некоторая пара взаимно исключающих состояний. Для безотказности и ремонтопригодности такими состояниями являются работоспособное и неработоспособное состояния, для долговечности — допредельное и предельное состояния, для сохраняемости — состояния сохранности и несохранности. Конкретное состояние робота определяется с помощью набора параметров, причем для каждой составляющей надежности это должен быть (в общем случае) свой набор параметров.
Перейдем к более подробному рассмотрению каждой составляющей надежности. Начнем с самой важной — безотказности.
Известно, что безотказность есть свойство объекта непрерывно сохранять работоспособное состояние в течение некоторого времени или некоторой наработки.
Промышленные роботы, как правило, функционируют в циклическом режиме. Время одного цикла может быть представлено в виде двух интервалов: интервала ожидания tож и интервала непосредственного выполнения своих функций tф.
Выше было отмечено, что безотказность связана с двумя состояниями: работоспособным и неработоспособным. Событие, заключающееся в переходе от работоспособного состояния к неработоспособному, называется отказом.
Отказы робота могут быть классифицированы по различным признакам. Качественно отказы делятся на два вида: отказы вида «прекращение функционирования» и отказы вида «неправильное функционирование». По способу проявления отказы делятся на явные и скрытые. Отказы вида «прекращение функционирования» считаются явными, если они произошли на интервале tф и скрытыми, если они произошли на интервале tож . Отказы вида «неправильное функционирование» являются скрытыми только в том случае, если их проявление заключается в увеличении погрешности позиционирования. В остальных случаях эти отказы явные.
По скорости проявления отказы делятся на внезапные и постепенные. Внезапные отказы заключаются в мгновенном переходе от работоспособного состояния к неработоспособному (например, поломка некоторого звена кинематической передачи манипулятора). При постепенном отказе процесс изменения состояния робота растянут во времени (например, постепенный износ зубьев зубчатых передач и, как следствие, появление ошибок позиционирования робота).
Из всего изложенного выше следует:
1) описание безотказности должно проводиться для каждого вида отказов отдельно;
2) возможность скрытых отказов побуждает ввести в техническое обслуживание такие процедуры, которые способствовали бы выявлению этих отказов и дальнейшему их устранению;
3) возможность постепенных отказов диктует необходимость периодической подрегулировки и восстановления тех узлов и механизмов, для которых свойственны эти отказы.
Теперь перейдем к номенклатуре показателей безотказности для промышленных роботов.
Наиболее универсальным показателем безотказности является вероятность выполнения заданной процедуры L (w). Считается, что процедура может быть выполнена, если промышленный робот был работоспособен в момент поступления запроса на его действия и оставался работоспособным во время выполнения требуемых операций.
В зависимости от условий и продолжительности времени ожидания и времени выполнения функций этот показатель может трансформироваться в следующие показатели: вероятность безотказной работы за время tф — если вероятность отказа за время ожидания запроса tож практически равна нулю; коэффициент готовности kг— если продолжительность tф настолько мала, что если запрос застал робота в работоспособном состоянии, то вероятность отказа во время запроса практически равна нулю.
Теперь перейдем к рассмотрению следующей составляющей надежности — ремонтопригодности.
Ремонтопригодность определяется как свойство объекта, заключающееся в приспособленности к предупреждению и обнаружению причин возникновения отказов, повреждений и поддержанию и восстановлению работоспособного состояния путем проведения технического обслуживания и ремонтов.
Ремонт — это комплекс операций по восстановлению исправности или работоспособности робота. Время восстановления определяется как сумма трех слагаемых:
Тв=Тоб+Трем+Тпров (5.11)
где Тоб— время обнаружения отказа; Трем— время непосредственного проведения восстановительных работ; Тпров— время проверки восстановленного робота.
Следует отметить, что если Трем и Тпров определяются в основном конструкцией робота, т. е. закладываются при проектировании, то То6 определяется главным образом режимом функционирования робота. Эта составляющая ремонтопригодности может корректироваться выбором режима и параметров технического обслуживания.
Для описания ремонтопригодности используют следующие показатели: среднее время восстановления
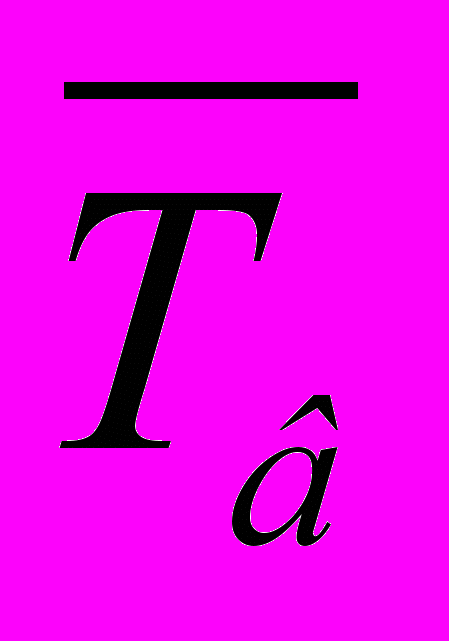
Техническое обслуживание (ТО) — это комплекс операций по поддержанию работоспособности или исправности робота.
Основными характеристиками ТО являются его периодичность Тп и длительность Тд.
Для совместного описания показателей безотказности и ремонтопригодности могут быть использованы такие показатели, как коэффициент готовности
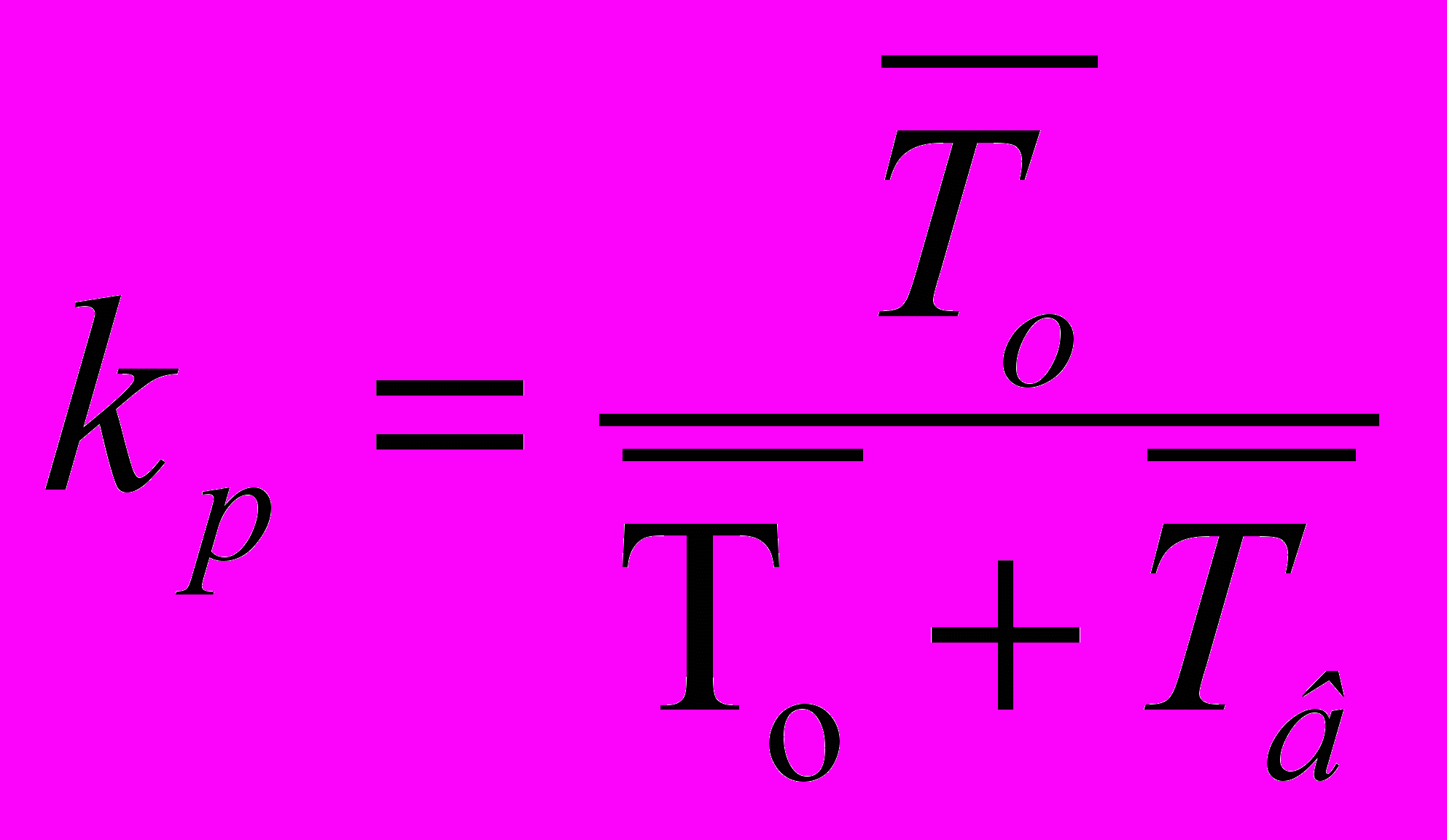
где
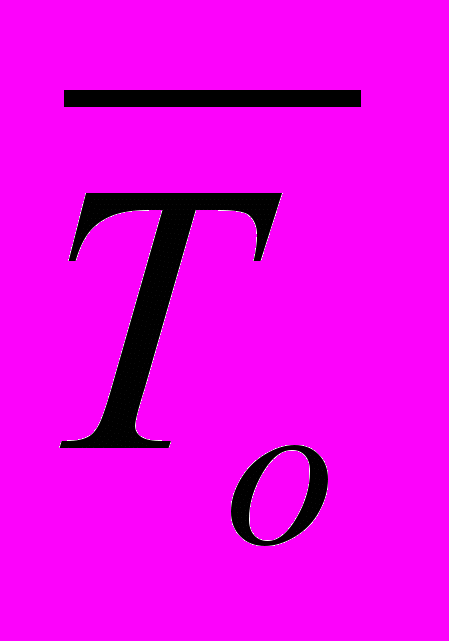
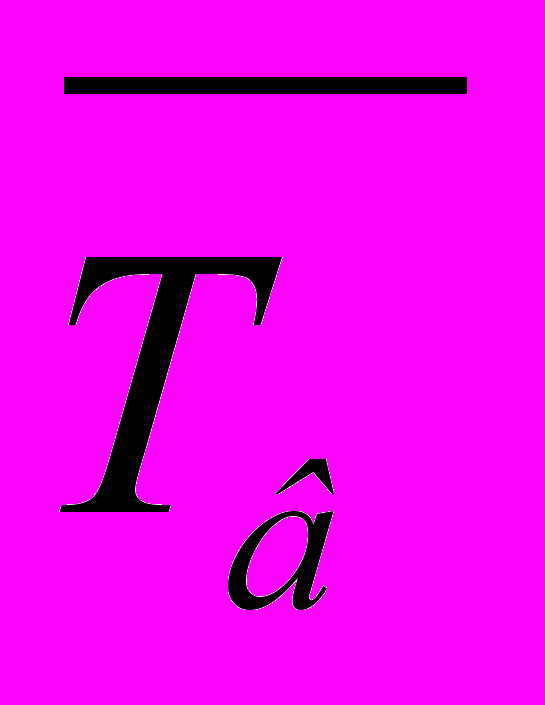
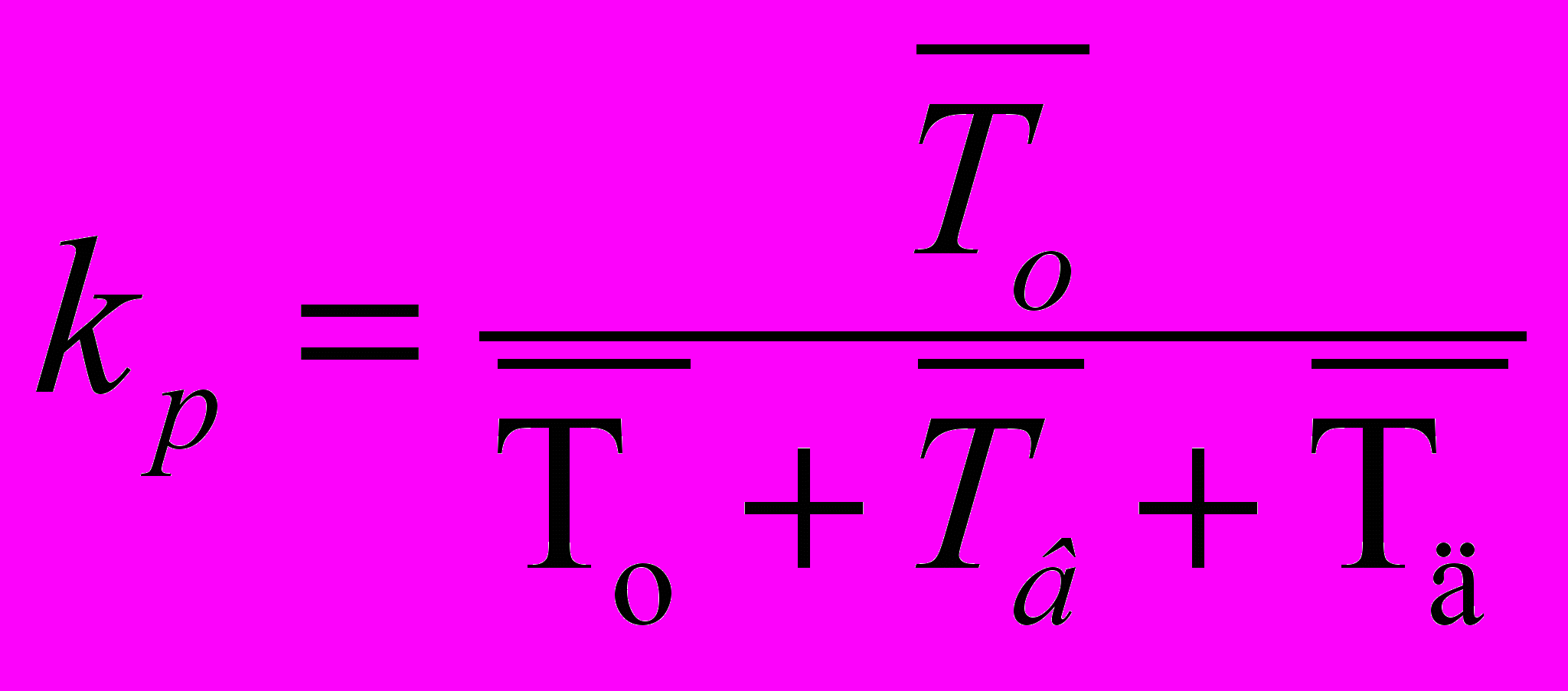
где
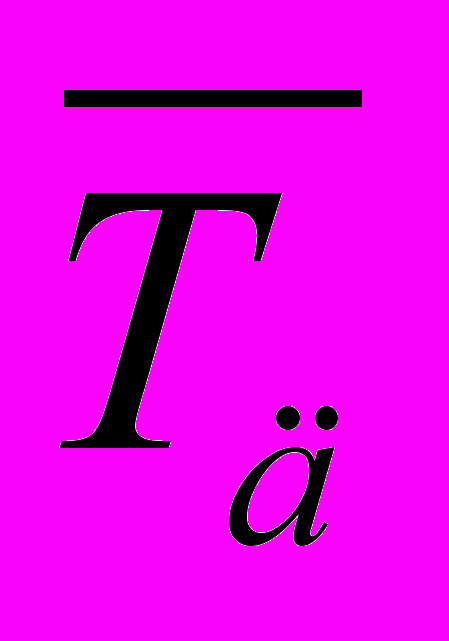
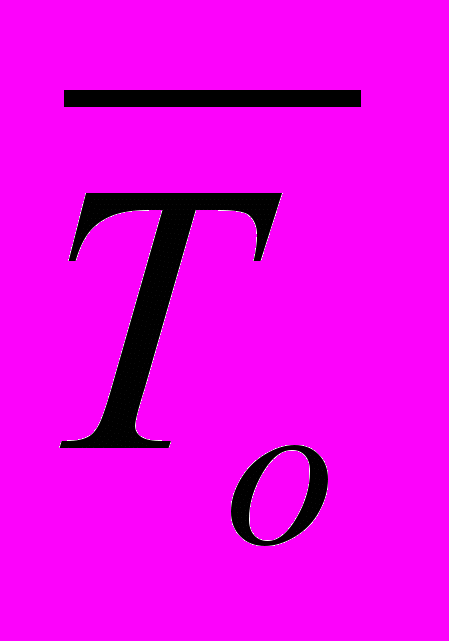
Сохраняемость робота определяет его способность к хранению и транспортированию. Роботы, как правило, транспортируются в упакованном состоянии, на месте производится монтаж и включение в работу. Поэтому эта составляющая надежности существенного значения для роботов не имеет.
Долговечность роботов в основном ограничивается моральным износом и должна быть не менее 6 лет.
Итак, основными составляющими надежности роботов являются безотказность и ремонтопригодность, и поэтому в дальнейшем речь будет идти в основном об этих составляющих.
С надежностью непосредственно связана еще одна важная составляющая качества роботов — безопасность. С одной стороны, применение промышленных роботов освобождает человека от участия в сложных технологических операциях, протекающих в агрессивных или вредных средах либо выполняющихся в темпе, недоступном для человека. С другой стороны, в процессе эксплуатации промышленных роботов иногда могут возникнуть ситуации, представляющие опасность как для человека, так и для расположенного поблизости оборудования. К основным причинам таких ситуаций повышенной опасности относятся:
1) неправильные (непредусмотренные) движения манипулятора;
2) отказ технологического оборудования;
3) ошибочные действия оператора во время наладки и ремонта;
4) появление человека в рабочей зоне манипулятора при его работе в автоматическом режиме;
5) превышение номинальной грузоподъемности робота;
6) неудобное или недостаточно свободное размещение технологического оборудования, пультов управления, накопителей и транспортных средств;
7) отсутствие специального ограждения манипулятора и размещение пультов управления внутри его рабочего пространства;
8) отключение (в случае аварийной остановки манипулятора) устройств, перерыв в работе которых может вызвать травмы у обслуживающего персонала;
9) отсутствие своевременной и четкой информации об аварийных ситуациях и причинах возникновения неполадок.
Все эти причины могут быть сгруппированы следующим образом: I группа — ошибки обслуживающего и оперативного персонала (3, 4, 5); II группа — конструктивные недоработки (5, 6, 7, 9), III группа — отказы промышленного робота (1, 2, 8).
Среди всех перечисленных выше причин наиболее важны причины, относящиеся к III группе, так как они инициируются самим роботом. Если не предприняты соответствующие меры безопасности, то развитие ситуации повышенной опасности может привести к значительному материальному ущербу или к травмированию обслуживающего персонала. Назовем такой отказ опасным. (Сказанное выше относится в первую очередь к промышленным роботам средней и большой грузоподъемности.)
Меры безопасности по отношению к опасным отказам должны закладываться на этапе проектирования промышленных роботов. Алгоритм обеспечения безопасности может быть представлен следующим образом:
— составляется перечень ситуаций повышенной опасности, которые могут возникнуть из-за отказов в промышленном роботе или роботизированном технологическом комплексе;
— определяется перечень оборудования, отказы которого могут привести к такой ситуации, и создается модель «угрозы опасности»;
— конкретизируются виды отказов по названному выше оборудованию и в соответствии с моделью «угрозы опасности» определяется вероятность возникновения опасного отказа за некоторое расчетное время (например, за год, квартал и т. д.). Если полученное расчетное значение не удовлетворяет нормативам по безопасности, то принимаются меры по повышению надежности вышеназванного оборудования либо по защите персонала и оборудования от аварии.
Для описания надежности роботов по опасным отказам используют показатели, характеризующие:
— опасность возникновения ситуации в течение некоторого заданного интервала времени нормального функционирования робота;
— опасность возникновения ситуации в результате воздействия на робот внешнего экстремального фактора.
К этим показателям относятся:
— средняя наработка робота до возникновения j-й ситуации повышенной опасности при нормальных условиях функционирования робота
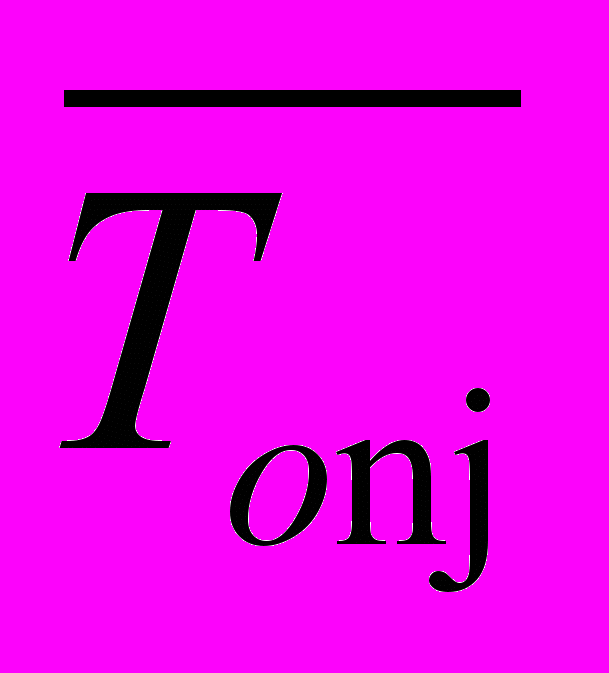
— вероятность возникновения j-й ситуации повышенной опасности в течение заданного времени τ при нормальных условиях функционирования Q/ (т);
— вероятность возникновения j-й ситуации повышенной опасности в результате воздействия s-гo экстремального фактора Фs — Qj(Фs).
В заключение отметим, что от надежности роботов в значительной степени зависит эффективность их эксплуатации. С другой стороны, обеспечение надежности также всегда связано с определенными затратами. Поэтому, чтобы иметь возможность сопоставлять эти два +показателя, предлагается воспользоваться следующими коэффициентами: коэффициентом снижения производительности из-за ненадежности робота
uпр=(N0-Np)/(N0)
где N0, Np — производительность абсолютнб надежного и реального роботов соответственно.
Коэффициент снижения экономичности из-за ненадежности робота
Uэ=(Ср-С0)/(С0)
где С0, Ср— стоимость обработки і-й детали с помощью абсолютно надежного и реального роботов соответственно.
Оценка надежности промышленных роботов. Промышленный робот представляет собой совокупность исполнительного механизма (механическая часть) и устройства управления. Рассмотрим каждую из этих составных частей с позиций надежности.
Механическая часть. По функциональному признаку механическую часть делят на несущую и исполнительную.
Три основных компонента несущей части — кисть, рука и стойка — в общем случае соединены под разными углами. Соединение их происходит за счет шарниров или направляющих, контактная жесткость которых меньше, чем жесткость других стыков. Из-за этого в узлах соединения возникают люфты, которые влияют на точность позиционирования манипулятора.
В исполнительной части снижение точности и увеличение времени позиционирования происходят из-за деформации механической системы под воздействием инерционной нагрузки. Деформация под действием инерционной нагрузки приводит к возникновению затухающих механических колебаний, ухудшающих качество позиционирования.
Таким образом, основными видами отказов механической части робота являются постепенные отказы, ухудшающие характеристики позиционирования робота.
При испытаниях робота «Универсал-50М» были выявлены следующие причины появления постепенных отказов:
— низкое качество изготовления отдельных элементов — разрушение зубчатого колеса привода поворота, утечка масла из соединений, люфт в механизме качания руки, низкая точность изготовления шариковой муфты передачи крутящего момента;
— низкое качество комплектующих изделий — утечка азота из гидроаккумуляторов, самопроизвольное движение золотников гидроусилителей;
— недостатки конструкции — отвинчивание стопорных гаек на штоке привода ЗУ, большое время прогрева масла.
Внезапные отказы, появляющиеся в механической части робота, в основном могут быть отнесены к категории отказов-сбоев, или самоустраняющихся отказов. К ним относятся: нестабильная работа клапанов, самопроизвольная остановка в точках позиционирования и т. д.
Показателем безотказной работы по постепенным отказам для механической части робота следует выбрать Р (τ) — вероятность безотказной работы за некоторое фиксированное время τ. В качестве τ могут быть использованы: продолжительность смены; продолжительность обработки одной партии деталей; время между двумя сеансами технического обслуживания и т. п.
Поскольку на точность позиционирования, как было показано выше, влияет большое количество факторов, причем изменения точности, вызываемые этими факторами, могут не только суммироваться, но и взаимно компенсировать друг друга, аналитическая оценка надежности по постепенным отказам практически нереальна и поэтому наиболее доступный способ оценки надежности — проведение специальных испытаний.
Наиболее эффективный способ повышения надежности в отношении постепенных отказов — проведение технического обслуживания. Техническое обслуживание механической части заключается в настройке и регулировке, устранении люфтов, замене изношенных деталей и т. д. Периодичность ТО, конкретная программа работ, выполняемых во время ТО, и его длительность для каждого вида робота определяется экспериментальным путем на этапе опытно-промышленной эксплуатации с учетом информации об изделиях-аналогах.
Теперь перейдем к устройствам управления.
Устройства управления (УУ) промышленного робота предназначены для формирования и выдачи управляющих воздействий исполнительному устройству в соответствии с управляющей программой.
Можно выделить два самостоятельных режима функционирования УУ — режим программирования и режим передачи управляющей программы на исполнение.
В режиме программирования выполняются ввод и отладка управляющей программы. Управляющая программа может быть составлена на основании расчета либо с помощью человека-оператора, осуществляющего обучение робота, при котором программа вводится в устройство управления.
В режиме передачи управляющей программы осуществляется управление исполнительным устройством в соответствии с заданной программой.
Режим программирования, как правило, заканчивается проверкой записанной программы путем изготовления опытного образца или выполнения проверочной операции, по которой судят о качестве записанной программы, поэтому можно считать, что как в режиме программирования, так и в режиме передачи управляющей программы задействовано все устройство управления.
Отказом устройства управления считается невыработка управляющего воздействия либо выработка ложного управляющего воздействия, т. е. в УУ существует два вида отказов: отказы типа «несрабатывание» и отказы типа «ложное срабатывание».
Для отказа типа «несрабатывание» конкретный выбор номенклатуры показателей надежности зависит от режима функционирования промышленного робота. Так, если на робот возлагается задача выполнить некоторую операцию (осуществить перемещение детали, произвести сварку в нескольких точках и т. д.), то устройство управления должно обеспечить выработку соответствующего управляющего воздействия, и поэтому безотказность данного устройства описывают показателем L (w) — вероятностью выполнения требуемой процедуры при поступлении запроса, где под запросом понимают сигнал, поступивший в УУ либо от датчиков, либо от оператора. Этот показатель следует понимать как вероятность того, что устройство управления будет работоспособным в момент поступления запроса на выполнение работы и сохранит работоспособность на протяжении всего времени отработки управляющего воздействия.
В зависимости от условий функционирования этот показатель может принимать вид Р (t) или kо.г. Если запросы поступают практически непрерывно и устройство управления должно быть работоспособным в течение вполне определенного времени (например, на протяжении смены или времени между сеансами технического обслуживания основного технологического оборудования и т. п.), то безотказность такого устройства следует описывать показателем Р (t). Если время ожидания запроса значительно превышает время его выполнения, то в качестве показателя, совместно характеризующего безотказность и ремонтопригодность УУ, может быть выбран коэффициент оперативной готовности kо.г или коэффициент готовности kr.
Безотказность по отказам типа «ложное срабатывание» может описываться таким показателем, как средняя наработка на «ложные срабатывания»
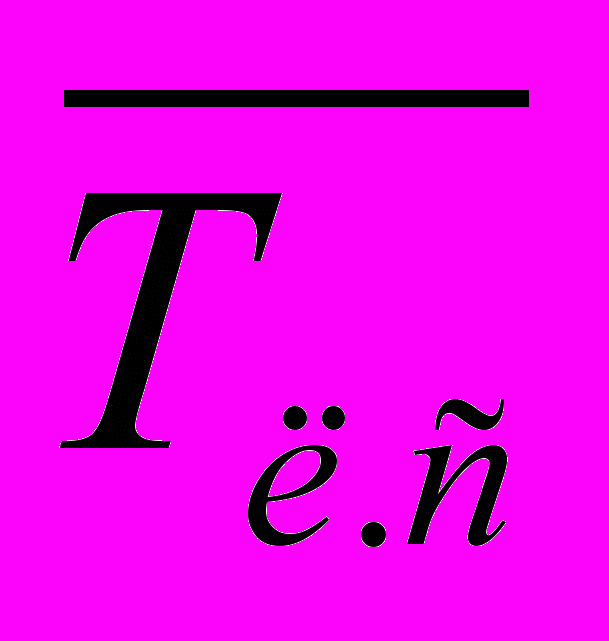
Если время восстановления не ограничено каким-то интервалом, связанным с режимом работы технологического оборудования и т. п., то возможно использование показателя
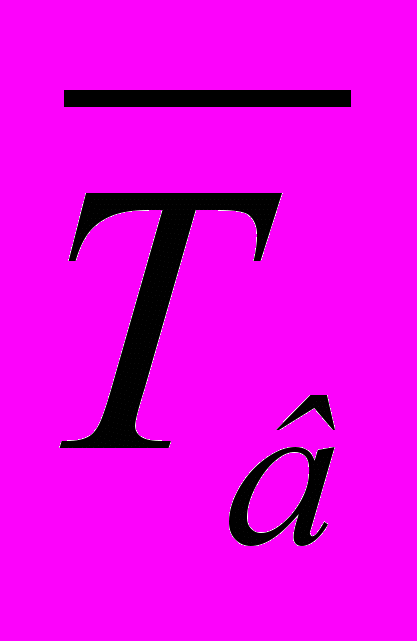
Для оценки показателей безотказности УУ используют все три группы методов: аналитические, статистического моделирования и экспериментальные (методы испытаний на надежность). В настоящем разделе остановимся на первых двух группах методов.
Исходными данными при использовании как аналитических методов, так и методов статистического моделирования служат данные о структуре УУ, надежности отдельных элементов структуры и условиях функционирования, если они отличаются от записанных в паспорте на элемент (например, УУ работает при повышенной температуре).
В основе двух названных разновидностей методов оценки надежности лежит понятие надежностно-функциональной схемы (НФС), представляющей собой ориентированный однонаправленный граф. Узлы графа — это элементы рассматриваемой системы (прямоугольники) и выполняемые системой функции (окружности). Ребра графа отображают взаимодействия элементов при выполнении заданной функции. В графах выделяются узлы высшего и низшего рангов: узел имеет высший (низший) ранг, если все связанные с ним ребра графа направлены только к нему (от него).
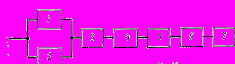
Рис. 5.24. Структура однонаправленного графа
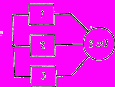
Рис. 5.25. Структура «2 из 3»
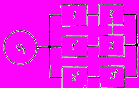
Рис. 5.26. Структура надежностно-функциональной схемы «2 из 3»
Путем в графе называется произвольная траектория движения от одного узла к другому вдоль ориентированных ребер. Узел графа проходим для путей, если соответствующий элемент УУ находится в состоянии работоспособности. Если элемент находится в неработоспособном состоянии, то соответствующий узел закрыт для путей в графе. Данный узел имеет путь наверх, если существует хотя бы один путь, соединяющий его с одним из узлов высшего ранга. Так, функция, изображенная на рис. 5.24, будет выполняться, если в работоспособном состоянии будут элементы 3...7 и один из двух элементов 1 или 2.
С помощью НФС можно отобразить и более сложные структуры, например соединение «2 из 3» (рис. 5.25).
Структура неработоспособна по отказам типа «несрабатывание» только в случае отказа всех трех элементов. В то же время структура устойчива к отказам типа «ложное срабатывание» — сигнал пройдет на выход только в том случае, если он появится не менее, чем в двух каналах.
Для НФС такой структуры вводятся так называемые «равноко-довые» элементы. Структура «2 из 3» с помощью равнокодовых элементов представлена на рис. 5.26. 1 и 1' — равнокодовые элементы. Физически это один и тот же элемент, поэтому отказы 1 и 1' наступают одновременно (аналогично 2 и 2', 3 и 3').
Оценка надежности УУ аналитическими методами может быть получена в том случае, если известно математическое выражение (или система математических выражений), связывающее значение искомого показателя надежности всего устройства с известными значениями показателей надежности его элементов.
Проиллюстрируем это на простейшем примере.
Пример. Определить значения показателей надежности для типового устройства управления.
Оцениваемые показатели надежности: вероятность безотказной работы по отказам типа «несрабатывание» в режиме «управление» за время t = 8 ч (продолжительность одной смены) Pl (t); вероятность безотказной работы по отказам типа «несрабатывание» в режиме «программирование» за время t = 1ч (продолжительность записи программы) Р2 (t); средняя наработка на «ложное срабатывание» Тл.с (табл. 5.2).
Таблица 5.2. Данные по безотказности элементов
-
Номер елемента
Тнеср, ч
Тл.с, ч
1
2200
-
2
2000
1000
3
10 000
-
4
5000
5000
5
1000
4000
6
2000
2000
7
30 000
-
Pi(t)=exp(-t/T)
Введем обозначения:
При t=8 Pi(t)= Pi1
При t=1 Pi(t)= Pi2
Тогда


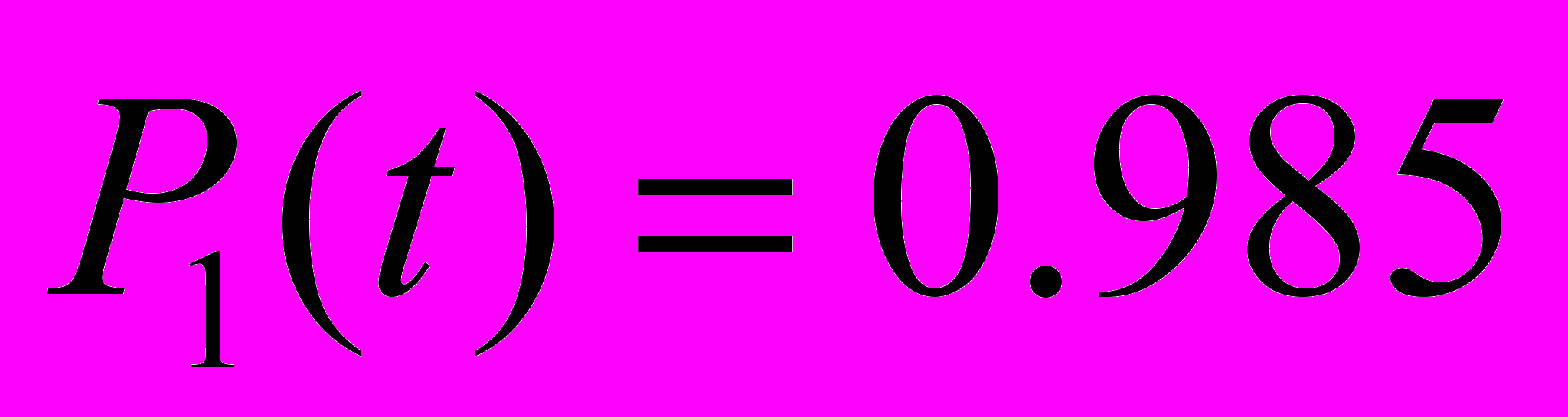
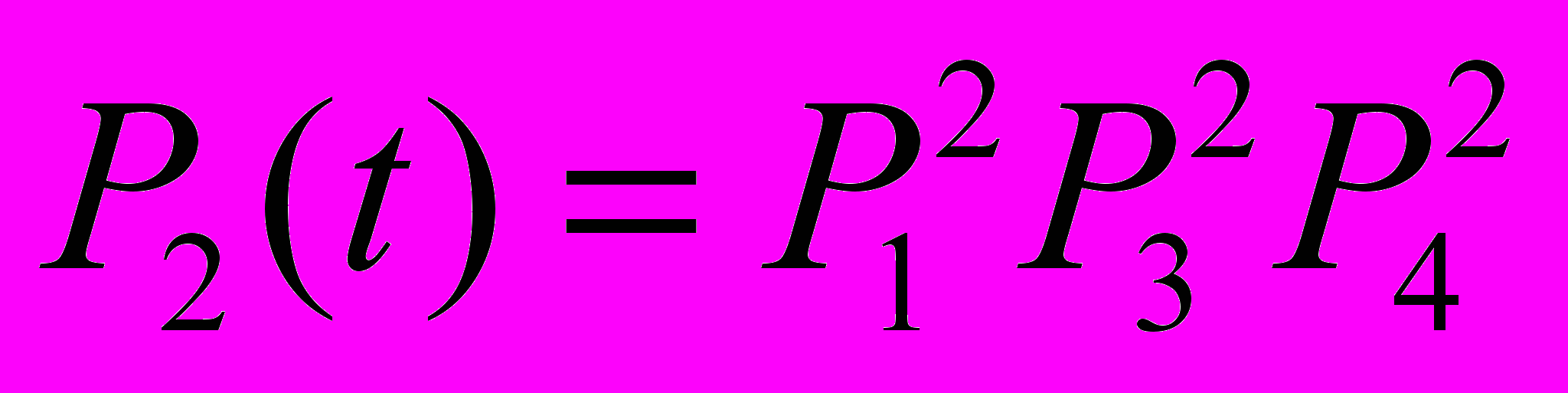

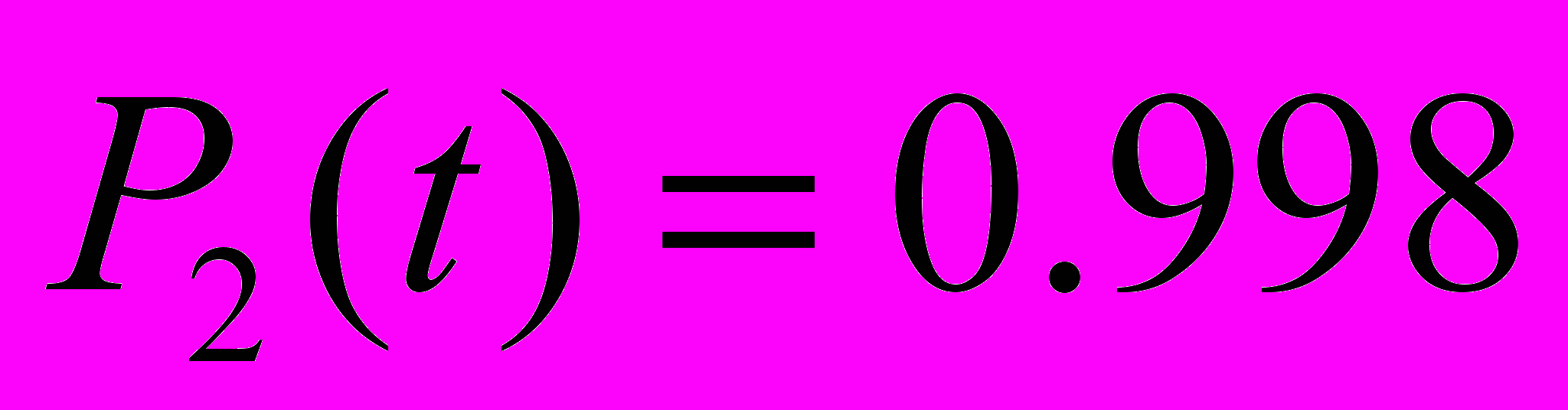

Полагаем, что для всех элементов закон распределения времени безотказной работы — экспоненциальный. В этом случае вероятность безотказной работы (і-го элемента за t часов определяется по формуле
В данном примере не учтено большое количество факторов, с которыми приходится сталкиваться в реальных системах (проведение технического обслуживания, наличие скрытых отказов и т. д.). В случае более сложной модели исследуемого процесса функционирования устройства управления пользуются методом статистического моделирования на ЭВМ.
В основе метода статистического моделирования лежит моделирование на ЭВМ различных случайных величин, характеризующих исследуемый процесс. В результате моделирования на основании полученного статистического материала дается количественное описание исследуемых случайных величин.
Количественная оценка надежности может быть использована для решения следующих задач:
1) выбор наилучшего (с позиций надежности) конструктивного варианта промышленного робота;
2) определение эффективности использования промышленного робота;
3) необходимость мероприятий по повышению надежности робота.
На последней задаче остановимся более подробно.
Методы повышения надежности промышленных роботов. Известны следующие основные методы повышения надежности:
1) использование более надежных комплектующих;
2) улучшение условий функционирования промышленных роботов;
3) введение различных видов резервирования;
4) использование технической диагностики;
5) проведение технического обслуживания.
Достоинства первых двух методов очевидны и, как правило, на этапе проектирования они используются в максимально возможной степени. В качестве примера можно упомянуть следующий факт. Наибольшая часть отказов промышленных роботов приходится на места сопряжения манипулятора с электронной системой управления и датчиками. Для повышения надежности вместо электронных линий связи используют оптические и волоконно-оптические.
Остановимся более подробно на третьем, четвертом и пятом методах.
Резервирование. Возможны следующие виды резервирования: временное, структурное, информационное.
Временное резервирование заключается в наличии некоторого временного запаса, в течение которого может осуществляться ремонт отказавшего оборудования.
Информационное резервирование предполагает использование резерва информации (например, неоднократную передачу управляющего воздействия).
Структурное резервирование заключается в применении резервных элементов структуры объекта.
Резерв может быть нагруженным и ненагруженным. Нагруженный резерв — это резерв, который содержит один или несколько резервных элементов, находящихся в режиме основного элемента. Ненагруженный резерв — это резерв, который содержит один или несколько элементов, находящихся в ненагруженном режиме до начала выполнения ими функций основного элемента.
Использование технической диагностики. Техническая диагностика является мощным средством повышения эффективности промышленных роботов. Анализ исследований электромеханических и механических систем показывает, что приблизительно 90 % отказов возникает вследствие скрытых внутренних дефектов и лишь 10 % — из-за неправильной эксплуатации. К дефектам, вызывающим отказы, относятся технологические погрешности изготовления и сборки, дефекты, появляющиеся в процессе эксплуатации, в результате старения и износа, воздействия вибраций, температуры и т. д.
Диагностика технического состояния промышленного робота должна проводиться как в процессе производства, так и в процессе эксплуатации. На этапе сборки могут быть допущены следующие технологические погрешности: отклонение формы; локальные дефекты; зазоры; разноразмерности.
Поэтому в процессе сборки должны контролироваться: дисбаланс; отклонения размещения элементов; перекосы; несоосности; биения.
В процессе эксплуатации проводится контроль следующих параметров: энергетических потерь; характеристик упругости; собственных вибраций.
Эффективный способ диагностирования — анализ тенденции изменения контролируемого параметра. Этот параметр может быть выбран: в механической части; в электромагнитной системе; в смазке.
Для диагностирования может использоваться также анализ состава рабочей жидкости в гидросистеме.
Нормальное отклонение перечисленных параметров составляет 1...3 % за 3...7 тыс. ч. В случае аварийной ситуации такое отклонение наблюдается через несколько десятков часов. Поэтому быстротечное нарастание дефекта служит признаком аварийной ситуации.
Для механической части дефекты узлов могут быть выявлены с помощью эталонных осциллограмм крутящих моментов.
Режущий инструмент контролируется виброакустическим методом с синхронизацией измерений по частоте впадения заготовки или инструмента.
Задача распознавания технического состояния робота может решаться как с прекращением функционирования, так и без прекращения функционирования. Второе направление — особенно важное. В литературе описан один из подходов к диагностированию механизмов, основанный на использовании объективных оценок их состояния, которые рассчитываются по значениям основных кинематических и динамических параметров, определяемых в ходе экспериментальных исследований.
В основу метода положено утверждение о том, что каждое техническое состояние промышленного робота характеризуется своим эталоном хэт(t) выбранного диагностического параметра и допуском на отклонение от него. В качестве диагностического параметра могут быть использованы скорость, ускорение, усилие, давление и т. д. Задача определения технического состояния сводится в этом случае к задаче экспериментального определения текущей реализации диагностического параметра х (t) и отнесения его к одному из состояний диагностируемого объекта.
Изменение состояния механических и электромеханических устройств можно контролировать по изменению частот их собственных колебаний.
Из всего изложенного выше следует, что процедура диагностирования робота — это трудоемкий процесс, усложняющийся тем, что неисправность любого узла непосредственно сказывается на работе связанных с ним элементов и, как правило, приводит к многоуровневому наложению последствий одного отказа. Поэтому для упрощения процедуры обслуживания и ремонта роботов в Японии была разработана автоматизированная диагностическая система. Перечислим ее основные достоинства.
1. Структурированное представление априорной информации о неисправностях и связанных с ними симптомах в виде правил вывода; использование методов искусственного интеллекта для поиска неисправностей.
2. Организация взаимодействия с оператором в интерактивном режиме. Система диагностики проверяет предположения оператора об источнике неисправности, формирует запрос на дополнительное выполнение тестовой процедуры или управляет ходом выполнения этой процедуры, а также выдает собственные предположения и заключения о виде неисправности.
3. В отличие от большинства подобных систем рассматриваемая диагностическая система может использоваться непосредственно в режиме «on-line», что дает возможность проводить дополнительное тестирование реального робота в процессе диагностики.
Реализованная диагностическая система представляет собой аппаратно-программный комплекс, состоящий из трех основных частей: собственно системы диагностики, сервоконтроллера и проверяемого робота с интерфейсными схемами. Экспертная диагностическая система ориентирована на работу с современными промышленными роботами, управляемыми от микроЭВМ. Процесс диагностики управляется оператором в режиме диалога. Структура данных диагностической системы используется при анализе состояний «отклонение от заданной траектории» и «неподвижность руки робота».
Техническая диагностика, определяя реальное состояние промышленного робота, позволяет рационально выбрать режим, параметры, а также перечень работ по восстановлению утраченных надежностных свойств робота. Среди этих работ важнейшей является техническое обслуживание.
Техническое обслуживание (ТО) заключается в проведении работ по восстановлению на еще не отказавшем объекте и делится на плановое и неплановое.
Плановое ТО заключается в проведении мероприятий по регулировке, корректировке систем позиционирования, смазке трущихся поверхностей, замене жидкости в гидроприводах и т. д. Для планового ТО заранее известен перечень работ, их периодичность и длительность.
Внеплановое ТО проводится по результатам диагностирования. Его характерной особенностью является то, что как периодичность, так и конкретный перечень работ, как правило, заранее неизвестны. Тем не менее, для внепланового ТО также должно быть спрогнозировано соответствующее материальное обеспечение (объем ЗИП, состав обслуживающего персонала, перечень необходимого оборудования для проведения ТО).
Отметим, что наибольший эффект в повышении надежности роботов может быть получен в том случае, если все перечисленные выше способы используются совместно, т. е. речь идет о создании рациональной системы технической эксплуатации робота, в которую составными частями входят следующие подсистемы: эксплуатационный персонал; техническое диагностирование; система ремонта и технического обслуживания робота; ЗИП (состав, размещение, порядок пополнения).
Надежность роботизированных технологических комплексов в целом должна описываться по основной их функции, заключающейся в выполнении требуемой технологической операции. Для каждого вида оборудования РТК должно быть сформулировано свое понятие функции и по отношению к этой функции должны быть показатели надежности.
Основной показатель надежности РТК — вероятность успешного выполнения требуемого цикла работ L (w). Разновидности этого показателя: Р (t) — вероятность успешного функционирования РТК в течение некоторого временного интервала, например, смены — если РТК на протяжении смены работает практически непрерывно; коэффициент оперативной готовности ko.r — kr Р (Δt) — если время ожидания запроса на выполнение некоторой операции превышает (время непосредственного выполнения этой операции).
Эти показатели надежности непосредственно зависят от показателей надежности всех видов оборудования, входящего в РТК.
Поэтому при задании показателей надежности отдельных видов оборудования необходимо осуществлять выбор показателей надежности таким образом, чтобы с помощью этих показателей можно было определить показатель надежности РТК в целом. Поясним это на некоторых примерах.
Для РТК, применяемого в кузнечно-прессовом производстве (см. рис. 5.6), можно отметить следующее. Время непрерывного функционирования РТК определяется продолжительностью разгрузки магазинного устройства 7. В период загрузки магазинного устройства при необходимости могут быть выполнены некоторые работы, относящиеся к ТО для РТК.
Приемную тару 3 и ограждения 4 можно считать практически абсолютно надежными элементами. Таким образом, для данного РТК основным показателем надежности является Р (τ) — вероятность безотказной работы РТК в течение времени τ, где τ — продолжительность разгрузки магазинного устройства 7. Этот показатель определяется по формуле
Р(τ)= Р5(τ)*Р1(τ)*Р2(τ)*Р6(τ),
где Р5(τ), Р1(τ), Р2(τ), Р6(τ),— вероятности безотказной работы за время τ двурукого промышленного робота, пресса, схвата манипулятора, устройства управления соответственно.
Для роботизированных технологических комплексов, приме-
няемых в механообработке, характерны (с точки зрения надежности) следующие особенности:
1) РТК некоторое время обрабатывает определенную разновидность деталей, а потом наступает период переналадки технологического оборудования;
2) при механообработке очень высокие требования предъявляются к точности позиционирования промышленного робота.
Отсюда следует: безотказность РТК характеризуется показателем Р (τ) — вероятностью безотказной работы за время τ, где τ — продолжительность обработки деталей из одной партии (без переналадки станка).
К основным видам отказов РТК относятся постепенные отказы по точности позиционирования. Поэтому должен быть обязательно исследован показатель Рпост(τ) — вероятность безотказной работы ПР за время τ, который в данном случае определяется как вероятность сохранения точности позиционирования.
Оценку показателей надежности РТК, как правило, осуществляют аналитическим методом или методом статистического моделирования и выполняют в два этапа. На первом этапе определяют показатели надежности отдельных видов оборудования. На втором этапе вычисляют значение показателей надежности для всего РТК в целом.
Повышение надежности РТК может осуществляться методами, описанными в разделе «Методы повышения надежности промышленных роботов».