Sdfield> Самостоятельная подготовка
Вид материала | Документы |
- Самостоятельная работа студентов подготовка к лекциям и практическим занятиям. Подготовка, 18.56kb.
- Методические разработки уроков по курсу оркисэ модуль «Основы светской этики», 42.99kb.
- Урок Культура и мораль Виды деятельности, 159.97kb.
- Примерный план выступления: Понятия культуры и морали. Что означает слово «культура»., 168.5kb.
- Sdfield> Класифікація державного, 402.98kb.
- Sdfield> берегите природу! сборник детских стихотворений, 224.01kb.
- Тема: «Алгоритм», 132.95kb.
- Учебно-методический комплекс дисциплины насосы и насосные станции основной образовательной, 337.32kb.
- Учебно-методический комплекс дисциплины насосы и насосные станции основной образовательной, 283.29kb.
- Никулина Ирина Евгеньевна, профессор Всего аудиторных занятий, час 36 самостоятельная, 117.87kb.
Самостоятельная подготовка
- Робототехнические комплексы кузнечно-прессовых операций.
- Автоматизация холодной штамповки.
- Обслуживание горячештамповочных процессов.
- Робототехнические комплексы литейного производства.
- Робототехнические комплексы гальванопокрытий.
- Роботизированные сварочные комплексы.
- Робототехнические комплексы нанесения лакокрасочных покрытий.
- Робототехнические комплексы сборочных операций.
РОБОТОТЕХНИЧЕСКИЕ КОМПЛЕКСЫ
КУЗНЕЧНО-ПРЕССОВЫХ ОПЕРАЦИЙ
Основными областями использования промышленных роботов в кузнечно-штамповочном производстве являются: автоматизация холодной листовой штамповки и обслуживание горячештамповочных прессов.
Автоматизация холодной штамповки
В настоящее время робототехнические комплексы создаются на базе различного кузнечно-прессового оборудования, серийно выпускаемого заводами машиностроительного комплекса. К такому оборудованию относятся:
- прессы однокривошипные открытые простого действия усилием 63—2500 кН;
- прессы однокривошипные закрытые двойного действия усилием 1000/630 кН;
- прессы кривошипно-коленные чеканочные усилием 4000, 10000 кН;
- прессы винтовые с дугостаторным приводом усилием 1000—4000 кН;
- прессы кривошипные горячештамповочные усилием 25000—40000 кН;
- прессы гидравлические для прессования изделий из реактопластов усилием 1600 кН;
- пресс-автоматы для прессования изделий из порошков твердых сплавов усилием 120 кН.
Отличительной особенностью листоштамповочных прессов является их большое быстродействие (до 60 и более ударов в минуту). Пределом быстродействия для выпускаемых в настоящее время промышленных роботов небольшой грузоподъемности можно считать 60—70, для более тяжелых — 10—20 циклов/мин, что в определенной мере ограничивает технические возможности прессов.
В то же время для холодной листовой штамповки, как правило, не требуется промышленных роботов с большим числом степеней подвижности и с высокой точностью. Последнее объясняется тем, что в большинстве случаев точная укладка заготовки достигается элементами штампа-ловителя, трафаретами и др. Обычно для таких роботов используются системы циклового управления.
Широкое использование промышленных роботов при автоматизации процессов холодной листовой штамповки объясняется следующими причинами:
- простотой конструкции механических прессов для холодной листовой штамповки; доработка, как правило, сводится к незначительным изменениям в системе их подключения;
- нет необходимости фиксировать заготовки в зоне обработки с помощью специальных зажимных устройств, как, например, при обработке резанием; следовательно, при автоматизации операций холодной листовой штамповки требуется не разработка специальных автоматических зажимных устройств, а лишь незначительное изменение конструкций штампов: введения фасок, дополнительных фиксаторов, трафаретов и т.д.;
- относительно высокой стойкостью штампов, что, как правило, исключает необходимость сплошного контроля качества изделий;
- простотой и однообразием манипуляций, выполняемых с заготовками при работе на универсальных прессах, что позволяет использовать промышленные роботы с цикловой системой управления и двумя — четырьмя степенями подвижности.
В настоящее время наибольший объем деталей штампуется на однокривошипных открытых прессах простого действия усилием 160—2500 кН с количеством вторичных операций 1—3 и более.
На робототехническом комплексе при холодной листовой штамповке выполняются следующие технологические операции:
- подача верхней заготовки из стопы, уложенной в магазине, на уровень захвата ее рукой робота;
- захват заготовки из исходной позиции магазина и перенос ее в рабочую зону пресса;
- укладка заготовки в штамп;
- штамповка изделия;
- вынос отштампованного изделия из рабочей зоны пресса;
- сброс изделия в тару.
При выполнении указанных операций должна быть создана блокировка, исключающая
- захват из исходной позиции неориентированных заготовок;
- захват двух слипшихся заготовок;
- загрузка пресса новой заготовкой до выноса из штамповочного пространства ранее отштампованной заготовки;
- рабочий ход пресса в случае нахождения руки робота с захватом в штамповочном пространстве пресса.
Промышленные роботы, используемые для холодной листовой штамповки, отличаются следующими особенностями:
- В большинстве они имеют одну, чаще две руки. Однорукие промышленные роботы используются при однооперационной штамповке, когда отштампованная деталь удаляется из штампа автоматически с помощью сбрасывателей (механических или пневматических) или выпадает в отверстие матрицы.
Если автоматическое удаление детали из штампа невозможно, применяют двурукие роботы. Одна рука робота транспортирует заготовку из подающего устройства в штамп, другая удаляет деталь из штампа в тару или перемещает ее на транспортирующее устройство.
Применение промышленных роботов с большим числом рук (например, трех) рационально при обслуживании одним роботом двух прессов.
- Как правило, погрешность позиционирования промышленным роботом для холодной листовой штамповки находится в пределах ±0,1—0,5 мм и является вполне приемлемой, так как в штампах, используемых для работы с применением промышленных роботов, устанавливаются дополнительные ловители, фиксаторы.
- Время на переналадку РТК складывается из времени на перепрограммирование, смену захватов, переналадку вспомогательного технологического оборудования. Для отечественных роботов в зависимости от сложности переналадки и типа робота время на переналадку составляет от 20 мин до 1,5 ч. Следовательно, если переналадка выполняется каждую смену, то потери рабочего времени могут достигать 10—20 % и, естественно, требование к сокращению времени на переналадку является одним из важнейших.
- Кроме того, конструкция промышленных роботов для холодной листовой штамповки должна удовлетворять условиям сопряжения робота с основным и вспомогательным технологическим оборудованием РТК по кинематической структуре,
Определение структуры, состава и компоновки робототехнического комплекса начинается с анализа технологического процесса получения детали.
В состав робототехнического комплекса входят:
- основное технологическое оборудование (прессы — один или несколько),
- промышленные роботы (один или несколько),
- устройство подачи заготовок,
- тара для готовых деталей,
- межоперационное устройство,
- устройство управления.
В общем случае структура робототехнического комплекса холодной листовой штамповки определяется следующими основными организационно-технологическими факторами:
- операционностью деталей;
- геометрическими параметрами детали;
- изменением формы заготовки в процессе обработки;
- характером технологического процесса (прерывистый или непрерывный);
- уровнем автоматизации вспомогательных операций.
Робототехнические комплексы бывают однооперационными и многооперационными.
Однооперационный робототехнический комплекс представляет собой законченную технологическую систему, включающую все необходимые элементы (питатели, устройства приема готовых деталей и др.) и предназначенную для автоматического выполнения одной однопереходной операции холодной штамповки.
Однооперационные робототехнические комплексы отличаются:
- простотой структуры,
- относительной технологической простотой создания такой структуры;
- близкими значениями времени обслуживания роботом пресса и времени формообразования детали.
Многооперационный робототехнический комплекс характеризуется более сложной структурой.
Необходимость создания таких комплексов обусловлена наличием многооперационных технологических процессов (пробивка большого числа отверстий, гибка в разных плоскостях и т.д.).
Существенным фактором, оказывающим влияние на структуру робототехнического комплекса, являются геометрические параметры обрабатываемых деталей. Большое значение имеет высота готовой детали, поскольку вертикальное перемещение рук роботов, применяемых в холодной листовой штамповке, как правило, невелико и не превышает 50—100 мм.
В тех случаях, когда высота штампуемых деталей больше вертикального перемещения промышленного робота, штамповая оснастка должна иметь выталкиватели, поднимающие отштампованную деталь на определенную высоту.
Толщина заготовки определяет тип вспомогательного технологического оборудования и, в частности, подающих устройств.
Для заготовок из тонколистового материала (тоньше 0,8 мм) и больших размеров (больше 250х250 мм) затруднительно использовать шиберные подающие устройства, поэтому применяют магазинные устройства с верхней выдачей заготовки. В то же время для толстолистового материала не целесообразно использовать однопозиционные магазинные подающие устройства, так как это приводит к необходимости частого останова РТК для загрузки заготовок в кассету, тогда как в шиберное подающее устройство дополнительная загрузка заготовок может выполняться без останова робототехнического комплекса. В этом случае применяют многопозиционные магазинные подающие устройства.
В некоторых случаях при многооперационной штамповке на роботизированной линии возникает необходимость поворота детали при передаче ее с позиции на позицию. Следовательно, руки промышленного робота должны иметь возможность вращаться (ротации) вокруг своей оси. При однооперационной штамповке необходимость в ротации исключается и, следовательно, могут применяться роботы, имеющие только транспортирующие (региональные) степени подвижности.
Наиболее важной характеристикой промышленных роботов является грузоподъемность, однако выбор модели робота определяется не только массой детали. Так, очень часто габаритные размеры прессового оборудования, на котором штампуется деталь, а также штамповочная оснастка приводят к необходимости применения роботов несколько большей грузоподъемности.
Большое значение для успешной работы робототехнического комплекса холодной листовой штамповки имеет его конструкция, которая должна соответствовать следующим требованиям:
- после окончания процесса штамповки деталь должна оставаться в нижней части штампа, причем без потери ориентации в случае отсутствия механизмов удаления детали из штампа;
- штамп необходимо оснащать фиксаторами типа ловителей или трафаретов, причем угол заходной части фиксаторов может быть равен 30—60°, а высота фиксирующей части 0,75—0,9 толщины заготовки;
- штамп должен иметь автоматические выталкиватели для подъема детали из матрицы и съема ее с фиксаторов;
- выталкивание детали должно быть плавным и происходить без смещения заготовки в горизонтальной плоскости;
- конструкция штампа должна исключать возможность запрессовки отхода в деталь и наоборот (при разделительных операциях);
- по возможности заднее расположение направляющих колонок, что в некоторых случаях значительно сокращает продолжительность цикла штамповки;
- при переднем расположении направляющих колонок заготовка должна проходить с гарантированным зазором;
- штамп должен иметь такую открытую высоту, чтобы захват с заготовкой мог войти в зону штамповки, т.е. расстояние между зеркалом матрицы и верхней частью штампа должно быть равно сумме высоты (толщине) заготовки (детали), высоты захвата и гарантированного зазора;
- в конструкции штампа должна быть предусмотрена возможность контроля положения заготовки в штампе.
Особое значение при создании робототехнического комплекса холодной листовой штамповки имеет конструкция применяемых захватных устройств. Основное их назначение заключается в надежном захватывании заготовок и удержании их в определенном фиксированном положении при транспортировании из подающего устройства в штамп и из штампа в ориентирующее устройство или тару при заданных скоростях перемещения заготовки.
Большое разнообразие форм и свойств деталей обусловливает применение различных видов захватных устройств: вакуумных, механических, электромагнитных и др.
Вакуумные захватные устройства имеют преимущественное применение при работе с плоскими листовыми заготовками, а также с заготовками пространственной формы, имеющими плоские участки поверхностей для захватывания их присосками.
Рабочие поверхности захватов не должны изменять геометрическую форму и качество поверхности деталей при их захватывании.
Работа вакуумного захвата основана на том, что воздух, подаваемый под давлением через эжектор, создает вакуум в объеме, образованном камерой эластичной присоски и плоскостью заготовки. Присоски крепятся с помощью винта и гайки, что позволяет с наименьшими затратами времени их заменить. Такое конструктивное исполнение дает широкую возможность выбора присосок различных диаметров в зависимости от геометрических параметров заготовок.
Механические захваты клещевого типа обычно снабжаются сменными губками, конструкция которых зависит от формы исходных заготовок и получаемых деталей.
Существующая в настоящее время тенденция к дальнейшему повышению уровня механизации и автоматизации листоштамповочного производства позволяет сформулировать дополнительные требования к технологическому оборудованию:
- возможность автоматической перепрограммируемой смены штампов;
- автоматизация сбора и удаления отходов из зоны обработки;
- наличие устройства программируемого изменения хода ползуна;
- наличие автоматизированной системы контроля целостности штамповочной оснастки.
Робототехнические комплексы холодной листовой штамповки условно можно разделить на три группы:
- роботизированная позиция — РТК, состоящий из одной единицы основного технологического оборудования, обслуживаемого роботами;
- роботизированный участок — РТК, состоящий из одного робота и обслуживаемых им двух, трех единиц основного технологического оборудования (двух-трех-операционная обработка);
- роботизированная линия, состоящая из нескольких РТК, соединенных передающими устройствами (многооперационная штамповка).
Простейшая структура роботизированной позиции приведена на рис. 29, а. В такой компоновке применяются роботы с автоматическим удалением отштампованной детали в тару. Такой РТК обладает наибольшей производительностью, так
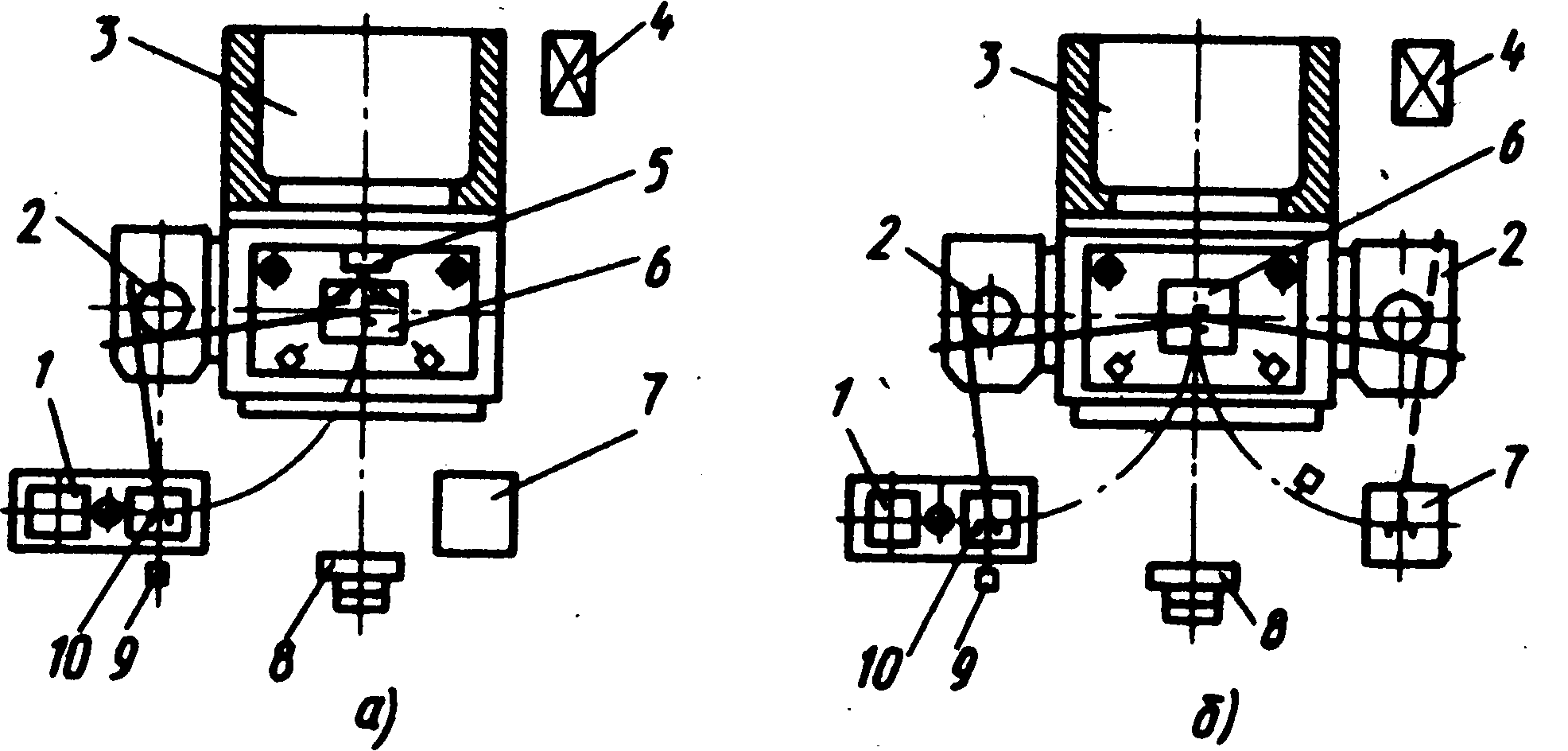
Рис. 29. Структура роботизированных позиций:
а—с одним промышленным роботом, б—с двумя промышленными роботами; 1 — подающее устройство, 2 — промышленный робот, 3 — пресс, 4 — пульт управления, 5 - система сдува; 6 — штамп, 7 — тара. 8 — система управления роботом, 9 — датчик контроля. 10 — захват
как после установки детали в штамп робот сразу же продолжает перемещение за последующей заготовкой, причем траектория перемещения руки робота может не содержать движения "рука вперед" и "рука назад". Кроме того, такая компоновка удобна для оператора при замене штамповой оснастки и отладке робототехнического комплекса.
Роботизированная позиция оснащается двумя роботами, если роботом удаляют деталь. Такая позиция обладает тем преимуществом, что значительно облегчает доступ наладчика в зону штамповки, а это сокращает время на переналадку штамповой оснастки и всего комплекса.
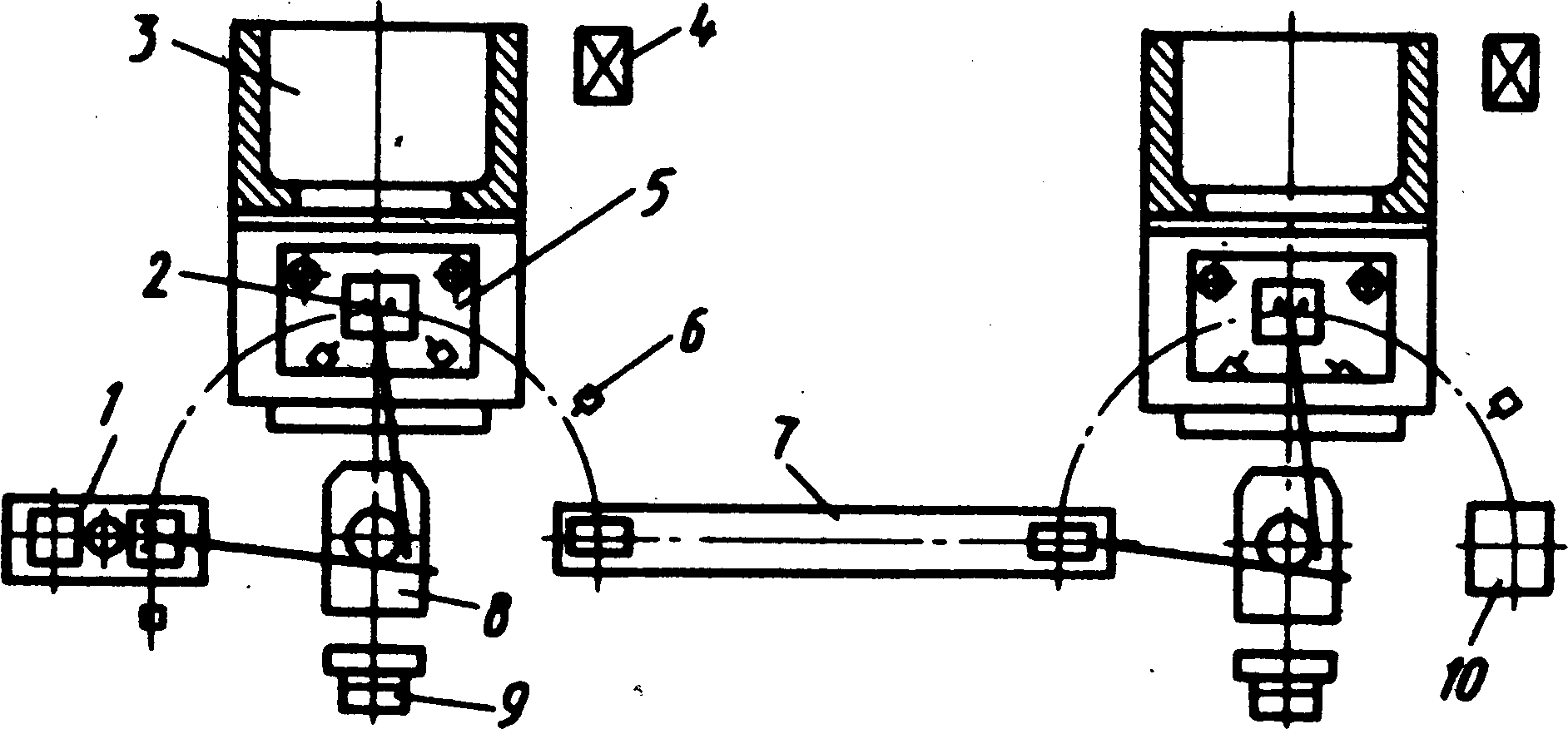
Рис. 30. Структура роботизированной линии с двумя промышленными роботами:
1 — подающее устройство, 2 — захват, 3 — пресс, 4 ~ пульт управления прессом, 5 — штамп, 6 - датчики контроля, 7 — передающее устройство, 8 — промышленный робот, 9 — система управления РТК, 10 — тара
Возможна такая компоновка роботизированной позиции с применением двух роботов с одной рукой (рис. 29, б), которой присущи достоинства и недостатки РТК, описанных выше.
Роботизированная линия двухоперационной штамповки с применением роботов сверхлегкого типа приведена на рис. 30. При необходимости эта линия может быть дополнена до трех и более роботизированных позиций.
Современные промышленные роботы в холодноштамповочном производстве могут действовать только в хорошо организованной среде.
Наряду с технологическими мероприятиями роль организатора среды в значительной степени выполняют вспомогательные устройства, служащие для подачи заготовок под робот в ориентированном виде и последующей их передачи без потери ориентации, смазывания заготовок перед штамповкой, удаления отходов, контроля протекания производственного процесса и других операций.
Каждый робототехнический комплекс представляет собой совокупность универсальных автоматических устройств, соединенных между собой электрическими связями и образующих единый механизированный комплекс, который позволяет обрабатывать двух-операционные детали, а также путем наращивания соответствующих составляющих устройств — многооперационные детали. Его можно трансформировать и на две самостоятельные позиции (без дополнительных устройств) для обработки однооперационных деталей.
Обслуживание горячештамповочных процессов
Внедрение роботов на большинстве операций, связанных с горячей, формовкой металлов, было обусловлено в первую очередь безопасностью обслуживания и контролем качества.
Так, например, условия работы в кузнечно-прессовых цехах считаются самыми тяжелыми для рабочих. Надо вынимать из горячих печей тяжелые поковки, устанавливать их в штампы быстродействующих прессов, а зачастую и менять их положение внутри пресса и укладывать готовую продукцию. Это тяжелые и опасные операции.
Именно в этой области задолго до программируемых управляемых роботов стали применять телеоператоры, что позволило избавить человека от непосредственного контакта с горячештамповочными прессами, однако при этом уменьшились гибкость и чувствительность управления. Чтобы в полной мере использовать возможности промышленных роботов, рекомендуется внести ряд дополнительных изменений в типовой процесс горячей штамповки.
Существующие роботы лишены органов чувств и не могут заглянуть в горячую печь и опознать детали, случайным образом распределенные в ее рабочем пространстве. Система технического зрения или другая сенсорная система для решения этой задачи должна будет надежно работать в условиях повышенных температур, масляного тумана и масляных паров. Наиболее тривиальным подходом в этом случае является использование нидукционных печей вместо печей отражательного типа, куда детали подаются на конвейере, нагреваются по отдельности и затем в ориентированном виде снимаются роботом.
Аналогичным образом в некоторой модернизации нуждаются и ковочные штампы.
Для процессов горячей штамповки характерно, что после удара пуансона заготовка может остаться на верхней или нижней поверхности штампа. Человек-оператор в данный конкретный момент может увидеть, где находится деталь, вынуть ее и провести соответствующие манипуляции. Без зрительных возможностей робот не может сделать это, и даже при наличии современных систем технического зрения скорость координации между зрением и действием руки робота относительно мала. Наилучшее решение в данном случае состоит в разработке такой конструкции ковочных штампов, когда деталь всегда будет иметь одну и ту же известную ориентацию.
Кроме того, в процессе выполнения операции штамповки форма самой детали изменяется. Чтобы справиться с этой проблемой, робот должен быть оснащен более гибкими или регулируемыми захватными устройствами.
В массовом производстве для автоматизации горячей штамповки используются специализированные горячештамповочные автоматы или горячештамповочные прессы, оснащенные грейферными перекладчиками.
В серийном переналаживаемом производстве промышленные роботы являются наиболее прогрессивным видом технологического оборудования для автоматизации горячештамповочных технологических процессов.
Основным видом роботизированного кузнечно-прессового оборудования в настоящее время являются кривошипные горячештамповочные прессы, где на основе промышленных роботов автоматизируются все вспомогательные операции:
- загрузка нагревательных устройств,
- транспортирование нагретой заготовки в зону формообразования,
- передача поковки из ручья в ручей,
- транспортирование и укладка в обрезной пресс,
- складирование поковки и отходов.
В процессе горячей штамповки, ковки и т.д. нашли применение промышленные роботы с четырьмя — шестью степенями подвижности и относительно большой памятью устройств программного управления, причем для роботов, работающих в массовом и крупносерийном производстве, достаточно четырех степеней подвижности за счет применения спецоснастки и других приспособлений.
Преобладающей тенденцией в отечественном роботостроении является стремление создать специализированные роботы, основные конструктивные особенности и технические характеристики которых сводятся к повышению быстродействия, теплозащитным конструкциям рук и захватов.
При этом учитываются следующие факторы, специфические для процесса горячей штамповки:
- резкое изменение конфигурации и габаритов поковок;
- - контроль положения поковок в штампе;
- смазка гравюр штампов;
- контроль температуры поковок;
- синхронизация работы технологического оборудования (нагревательные устройства, штамповочные и обрезные прессы, передающие устройства и т.д.).
РОБОТОТЕХНИЧЕСКИЕ КОМПЛЕКСЫ
ЛИТЕЙНОГО ПРОИЗВОДСТВА И ГАЛЬВАНОПОКРЫТИЙ