Анализ и обобщение опыта и тенденций создания промышленных роботов в отечественной и зарубежной робототехнике показывает, что все большее распространение получает электромеханический привод промышленных роботов. Впоследние год
Вид материала | Документы |
СодержаниеПерспективы развития промышленных роботов 7.2. Адаптивные роботы Устройства управления адаптивными роботами Манипуляторы адаптивных роботов. |
- Дипломная работа студента, 601.76kb.
- Исать собственные приложения для управления роботами на примере Lego nxt, а также использовать, 76.9kb.
- С применением grid-технологий, 81.79kb.
- История роботов, написанная роботом, 101.24kb.
- Sdfield> Самостоятельная подготовка, 455.42kb.
- Вдокладе описывается технология обучения распределенной системы автономных мобильных, 45.47kb.
- Внушающих уверенность жилищ люди живут в обличии роботов-суррогатов сексуальных, физически, 367.79kb.
- Возможное участие родителей, 108.84kb.
- Анализ работы шмо учителей физики, химии, биологии за 2010-2011 учебный год, 113.58kb.
- Лега В. П. Наука и вера, 152.3kb.
ПЕРСПЕКТИВЫ РАЗВИТИЯ ПРОМЫШЛЕННЫХ РОБОТОВ
7.1. Промышленные роботы агрегатного типа
История развития техники свидетельствует о том, что степень универсальности оборудования неразрывно связана с видом производства. Рассматривая машиностроительное производство (по своей природе дискретное) в такой последовательности — индивидуальное, мелкосерийное, серийное, крупносерийное, массовое, можно заметить, что целесообразность применения универсального оборудования падает от начала к концу этой последовательности, а целесообразность применения специализированного оборудования, наоборот, увеличивается.
Действительно, многолетний опыт создания и эксплуатации универсального и специализированного оборудования однозначно говорит о том, что специализированное оборудование обладает значительно большей производительностью, чем универсальное, но требует большего времени на разработку и значительных капитальных затрат. Кроме того, существенным недостатком специализированного оборудования является малая эксплуатационная гибкость, что i е позволяет использовать его в условиях многономенклатурного производства. Универсальное же оборудование менее производительно, но зато обладает большими эксплуатационными возможностями и поэтому широко применяется в индивидуальном, мелкосерийном и серийном производстве.
Возникает естественный и своевременный вопрос: как объединить преимущества универсального и специализированного оборудования и примирить их противоречия? История развития техники показывает, что такой путь есть — это так называемый агрегатный (модульный) принцип построения оборудования.
Модульный принцип основан на системном подходе, который должен предусматривать одновременный анализ и обобщение большинства известных задач по автоматизации данного производства. На этой основе разрабатывается комплекс технических средств, функционально взаимодополняющих друг друга и позволяющих компоновать из них широкую номенклатуру автоматизированного оборудования, которое обеспечивает выполнение любой из рассмотренных частных задач. Одновременно должен быть разработан комплекс организационно-технических мероприятий, создающих возможность изготовления, комплектации, эффективной эксплуатации и ремонта этих технических средств.
Разработка агрегатного комплекса технических средств значительно сложнее разработки отдельных моделей оборудования. Это положение может вызвать соблазн приступить к решению только конкретных задач и не нести затрат на создание агрегатного комплекса. Такая сиюминутная выгода оборачивается большими потерями в течение многих последующих лет, так как новые задачи повлекут за собой новые разработки, мало использующие то, что было создано ранее. Агрегатный комплекс технических средств может и должен развиваться как непрерывно совершенствуемая и наращиваемая система, и это, несомненно, даст большой экономический эффект.
Создание агрегатных комплексов — основа технической политики многих передовых отраслей промышленности СССР. Наибольшее количество агрегатных комплексов создано или создается в рамках Государственной системы приборов и средств автоматизации (ГСП): АСВТ, КТС, ЛИУС, АСЭТ, АСАТ, АСКР, АСИВ, АСИП и др. По такому же пути идет создание Единой серии ЭВМ (ЕС ЭВМ). Большие успехи в области разработки агрегатных технических средств достигнуты станкостроением СССР. В настоящее время большинство многооперационных станков и автоматических линий собирается из агрегатных узлов и устройств управления.
Японская фирма «Мицубиси» ведет работы в этом направлении и опубликовала материалы в 1974 г. Робот этой фирмы создан по агрегатной (модульной) схеме (рис. 7.1). Каждый элемент его движения (модуль) в значительной степени самостоятелен. Элементы можно объединять в различные варианты. Фирма приводит следующие преимущества робота агрегатной конструкции:
1) элементы всех движений имеют модульную конструкцию, что позволяет по желанию потребителей выбрать конструкцию оптимального типа;
2) обеспечивает взаимозаменяемость двухпозиционного гидравлического и пневматического сервоприводов;
3) возможна конструкция робота, скомпонованного в прямоугольно-цилиндрической системе координат;
4) диапазон перемещения руки широк благодаря телескопической конструкции;
5) существует реальная возможность упрощения робота при использовании только одной или двух координат;
6) обеспечивается высокая точность позиционирования;
7) упрощается ремонт робота в процессе эксплуатации.
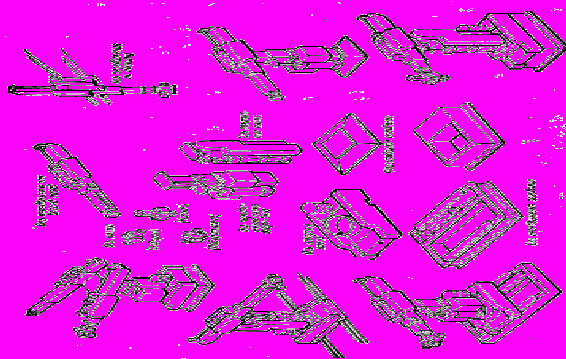
Рис. 7.1. Агрегатный комплекс "Мицубиси"
Таблица 7.1. Технические характеристики координатных модулей робота фирмы «Мицубиси»
Координатный модуль | Рабочий диапазон | Максимальная скорость |
Горизонтальный ходи руки | 1350 мм | 1000 мм/с |
Вертикальный ходи руки | 500 мм | 500 мм/с |
Поворот руки относительно горизонтальной оси | ±30º | 60 º/с |
Поворот руки относительно вертикальной оси | 250 º | 100 º/с |
Движение кисти | 180 º | 100 º/с |
Фиксированное основание | - | - |
Перемещение основания | 500мм | 500 мм/с |
Конечно, в приведенном перечне значительная доля преимуществ имеет рекламный характер, а в некоторых случаях и не является характерной именно для робота агрегатной конструкции, как, например, утверждение о высокой точности позиционирования. Однако было бы неверно преуменьшать ценность этой работы. Технические характеристики модулей робота фирмы «Мицубиси» приведены в табл. 7.1.
Агрегатная гамма роботов «Юнимейт» фирмы «Кавасаки» (Япония) отличается широким разнообразием основных технических характеристик, причем допускается комплектование всех модификаций манипуляторов различными типами устройств управления. Роботы имеют однотипную компоновку механических систем большой, средней и малой грузоподъемности; их основные технические характеристики приведены в табл. 7.2.
Таблица 7.2. Основные технические характеристики модулей механических систем
Показатели | Модуль механической системы | ||
тяжелый | средний | легкий | |
Грузоподъемность, кг | 45…135 | 35…75 | 10…20 |
Число степеней подвижности | 6 | 4…6 | <8 |
Погрешность позиционирования, мм | ±2,0 | ±1,0 | ±0,25 |
Объем рабочей зоны, м3 | 23,0 | 9,0 | 4,0 |
Продольный ход руки, мм | До 1320 | 800…1041 | 500…800 |
Скорость линейных перемещений, м/с | 0,915 | 0,762 | 1,2 |
Угловые перемещения, º/(º/с) | | | |
α/ω | 25/35 | 30/30 | 30/60 |
β/ω | 25/35 | 27/30 | 30/60 |
γ/ω | 230/110 | 220/110 | 220/110 |
φ/ω | 360/110 | 360/110 | 360/110 |
Система агрегатного построения МНИ, выпускаемая фирмами «Электролюкс» (Швеция) и «Роберт Буш» (Германия) содержит три агрегатные гаммы промышленных роботов со сквозной унификацией отдельных узлов. Все роботы имеют пневмопривод и работают по упорам.
Разработаны агрегатные системы на базе промышленных роботов типа «Пирин» (НРБ), PR-02 (РП), «Рено» и «Сиаки» (Франция).
До сих пор рассматривался только один аспект создания робота агрегатной конструкции — компоновка кинематики робота и совсем не упоминалось о втором, может быть более важном — создании агрегатной конструкции систем управления. Эта часть задачи, по мнению автора, более сложная.
Опыт, накопленный в промышленности, развитие методов и технических средств автоматического управления технологическими процессами, создание станков с программным управлением, анализ и обобщение опубликованных работ по созданию и эксплуатации промышленных роботов создают предпосылки для пересмотра некоторых концепций и выдвижения конструктивных предложений по дальнейшему совершенствованию промышленных роботов для автоматизации производства на основе агрегатного принципа.
Одним из важнейших факторов, определяющих состав агрегатного комплекса и количество возможных компоновок, является тип координатной системы базового манипулятора.
Как уже отмечалось, большинство современных промышленных роботов, предназначенных для транспортирования изделий, имеет сферическую, рычажную и цилиндрическую систему координат региональных движений. Достоинства этих систем — малые металлоемкость и занимаемое пространство, удобный доступ к механизмам для подвода коммуникаций и обслуживания. Первые опыты по применению промышленных роботов такого типа для выполнения технологических операций (окраска, точечная и дуговая сварка) показали следующее. Манипуляторы со сферической, рычажной и цилиндрической системами координат можно эффективно применять для обработки изделий сложной формы, требующих не менее пяти степеней подвижности инструмента при позиционном перемещении и записи программы методом непосредственного обучения. При обработке более простых изделий при необходимости перемещения по прямым, параллельным одна другой, отчетливо проявляется недостаток сферической и цилиндрической систем — невозможность упростить кинематическую структуру и систему управления при движении по простейшим траекториям (прямым, окружностям), которые составляют подавляющее большинство требуемых траекторий движения инструмента.
Прямоугольная система допускает применение наиболее простых одно-, двух- и трехкоординатных компоновок механизмов региональных движений и позволяет оснащать любую из этих компоновок необходимыми механизмами локальных перемещений инструмента. Прямоугольная система координат позволяет применить устройство управления любой сложности — от простейших однокоординатных путевых устройств, используемых в силовых узлах агрегатных металлорежущих станков, до устройств управления контурного типа. К числу недостатков прямоугольной системы следует отнести большие металлоемкость и занимаемую площадь цеха.
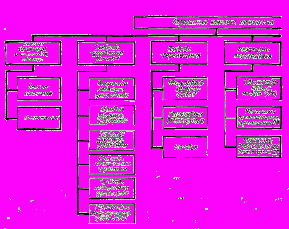
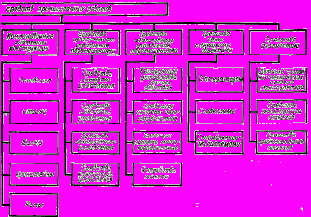
Рис. 7.2. Номенклатура агрегатного комплекса для сварки
Разработка номенклатуры агрегатного комплекса представляет собой наиболее ответственную часть начального этапа создания комплекса. Номенклатура определяется диапазоном технологических задач и видов производства. Целесообразно разрабатывать агрегатный комплекс, ориентируясь на более сложный вариант. В остальных, более простых вариантах некоторые узлы попросту не будут использоваться. Из технологических промышленных роботов наиболее сложен робот для дуговой сварки плавлением. Таким образом, необходимо создавать агрегатный комплекс с учетом специфики технологии.
Номенклатура агрегатного комплекса технических средств промышленных роботов для сварки представлена на рис. 7.2. В основу комплекса было положено следующее:
1) прямоугольная система координат региональных движений;
2) максимальное использование технических средств из агрегатных систем других отраслей машиностроения и приборостроения, и в первую очередь средств управления станками;
3) возможность создания манипуляторов целесообразной кинематической структуры с оптимальной по выбранным критериям системой управления для решения различных конкретных технологических задач;
4) возможность непрерывно наращивать номенклатуру технических средств и совершенствовать их.
Как видим, агрегатный комплекс состоит из девяти групп технических средств, каждая из которых состоит из ряда подгрупп. Деление на группы и подгруппы осуществлено по функциональным признакам.
В СССР разработана достаточно совершенная гамма электромеханических роботов модульного типа РПМ-25. Система модулей, приведенная на рис. 7.3, содержит: два транспортных модуля глобальных перемещений — напольного Тн и подвесного Тп исполнения; шесть модулей региональных движений — поперечного сдвига С, подъема П, качания К> вращательных перемещений В, двойного качания Д и радиального хода РХ; три модуля локальных ориентирующих движений — с одной Р1, двумя Р2 и тремя РЗ степенями подвижности. Кроме того, в агрегатную систему входят модуль неподвижного основания Н, а также операционные модули с захватными устройствами ЗУ1, ЗУ2 и ЗУС — одинарный, двойной и с поперечным сдвигом.
Возможные комбинации стыковки модулей показаны на рис. 7.3 направленными связями. В частности, комбинация из трех модулей прямолинейного перемещения позволяет получить компоновку робота РПМ-25, работающего в декартовой системе координат; использование модуля вращения В — компоновку с обслуживанием рабочей зоны в цилиндрической системе координат, использование модулей качания К и двойного качания Д — соответственно компоновки в сферической системе координат и антропоморфной шарнирной структуры.
Конструктивные особенности модулей таковы: модули прямолинейных перемещений С, П и РХ выполнены на основе планетарных роликовых винтовых передач качания, отличающихся от обычных шариковых винтовых передач более высокой жесткостью и несущей способностью, а также возможностью работать с более высокой частотой вращения (что особенно важно для роботов с электроприводами). В качестве направляющих в модулях С и П применяются цилиндрические скалки с шариковыми сепараторами, в модуле РХ используются роликовые направляющие, закрепленные в базовом корпусе, по которым перемещается подвижное звено модуля, что обеспечивает компактность и легкость конструкции модулей.
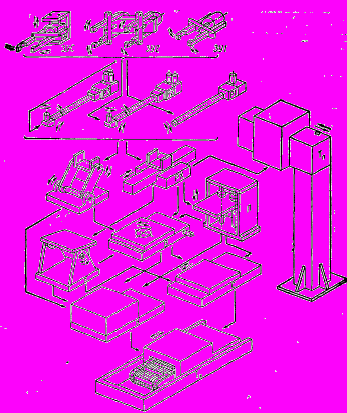
Рис. 7.3. Агрегатный комплекс типа РПМ-25
В модуле П обеспечивается частичная разгрузка за счет использования вертикального телескопического пневмоцилиндра. Для повышения безопасности работы в модулях П и РХ применены самотормозящиеся муфты дискового типа. В модулях с вращательным движением, а также в модулях Тв и Тп используются комбинированные червячно-зубчатые редукторы. Червячная ступень редуктора обеспечивает бесшумность работы при высоких оборотах двигателя и возможность самоторможения в необходимых случаях (в модулях В и Р применяются четырехзаходные червяки). В ступени редуктора с зубчатым зацеплением элементов используются безлюфтовые передачи по принципу замкнутого энергетического потока. При этом передаточное число второй ступени редуктора с зубчатым зацеплением выбирается из условий обеспечения минимального значения максимального люфта в червячной передаче, приведенного к исполнительному звену. Это минимальное значение не должно превышать дискретности применяемого датчика обратной связи и таким образом не будет оказывать влияния на точность работы механизма в целом.
В модуле двойного качания Д используются раздельные индивидуальные приводы для каждой из степеней подвижности, причем в качестве первой ступени редукции используется однозаходная червячная самотормозящаяся передача. Кинематические связи в этом модуле подобраны таким образом, что при работе двигателя качания первого исполнительного звена (второй двигатель заторможен) второе исполнительное звено совершает поступательное движение, не изменяя своей ориентации.
Привод основных движений робота РПМ-25 — электрический, постоянного тока, следящий, с обратной связью по положению и скорости. В качестве исполнительных используются двигатели постоянного тока МИ2 мощностью 3 кВт и 4МИ12 мощностью 980 Вт. Управление — тиристорное (тиристорное преобразовательное устройство ЭПТ-9М расположено в отдельной стойке). Привод операционных механизмов — пневматический с подводом воздуха под давлением через стыковочные поверхности модулей.
Технические характеристики модулей основных движений робота РПМ-25 приведены в табл. 7.3.
7.2. Адаптивные роботы
Общие положения. Промышленные роботы, или роботы первого поколения, отличаются тем, что имеют жесткую программу действия и не могут реагировать на изменения окружающей среды. Эта особенность ограничивает их возможности и несколько сужает область применения. В настоящее время успешно разрабатываются и находят применение более совершенные роботы второго поколения, или, как чаще их называют, адаптивные роботы. Роботы этого типа имеют соответствующие датчики внешней информации, более сложную систему управления и поэтому могут реагировать на изменения окружающей среды и вырабатывать ответную реакцию или действие. Иногда приходится слышать такое мнение! «Если роботы первого поколения менее совершенны, то следует вместо них применять более совершенные — адаптивные роботы».
Таблица 7.3. Технические характеристики модулей основных движений робота РПМ-25
Наименование модуля | Характер движения | Пределы перемещения модуля | Скорость перемещения модуля | Номинальный момент на выходе, Нм | Номинальная сила на выходе, Н | Точность позиционирования | |||||
С аналоговым датчиком | С кодовым датчиком | ||||||||||
По углу поворота, рад | По длинне, м | рад/с | м/с | мм | рад*103 | мм | рад*103 | ||||
Модуль поворота В | - | 5,3 | - | 2,4 | - | 800 | - | - | ±0,8 | - | ±0,2 |
Модуль подъема П | - | - | 0,8 | - | 0,4 | - | 5000 | ±0,4 | - | ±0,1 | - |
Модуль поперечного сдвига С | - | - | 0,1 | - | 0,8 | - | 2000 | ±0,5 | - | ±0,125 | - |
Модуль качания К | - | 1,05 | - | 0,7 | - | 2500 | - | - | ±0,25 | - | ±0,6 |
Модуль радиального хода РХ | - | - | 0,1 | - | 0,5 | - | 3200 | ±0,5 | - | ±0,125 | - |
Модуль двойного качания Д | Вперед-назад | 1,68 | - | 1,14 | - | 1400 | - | - | ±0,4 | - | ±0,1 |
Вверх-вниз | 1,3 | - | 0,57 | - | 2800 | - | - | ±0,4 | - | ±0,1 | |
Рука с тремя степенями подвижности | Вращение | 6 | - | 2,56 | - | 170 | - | - | ±1,6 | - | ±0,4 |
Сгибание | 3,14 | - | 1,6 | - | 250 | - | - | ±1,0 | - | ±0,25 | |
Вращение конечного звена | 6 | - | 3,5 | - | 125 | - | - | ±2 | - | ±0,5 | |
Рука с одной степенями подвижности (грезоподъем-ность 100 кг) | - | 6 | - | 2,56 | - | 170 | - | - | ±2,0 | - | ±0,5 |
Основании подвижное (напольный вариант) | - | - | 10 | - | 1,5 | - | 700 | ±1,2 | - | ±0,3 | - |
В большинстве случаев это мнение ошибочное по следующим соображениям:
— во-первых, в большом количестве технологических процессов окружающая робот среда хорошо организована и не меняется. Примером может служить штамповочное производство, где детали, как правило, совершенно одинаковы и условия выполнения процесса во времени не меняются. Применение промышленных роботов для автоматизации таких процессов полностью оправдано и целесообразно;
— во-вторых, адаптивные роботы имеют специальные датчики внешней информации и значительно более сложную систему управления. Это приводит к тому, что адаптивные роботы значительно сложнее промышленных, а следовательно, и дороже. Обслуживание таких роботов требует специалистов высокой квалификации.
Из этого следует вывод, что промышленные и адаптивные роботы будут существовать независимо и каждый тип роботов найдет (и уже нашел) свою рациональную область применения. Возможно, что по мере совершенствования адаптивных роботов, повышения надежности работы и снижения стоимости удельный вес их в промышленности будет увеличиваться.
В настоящее время область применения адаптивных роботов более-менее четко очерчена и проблема их создания и совершенствования сформулирована. Проблему создания адаптивных роботов можно разделить на пять частных задач:
1) определение понятия «окружающая среда», ее состава и параметров;
2) выбор из числа имеющихся или создание новых датчиков внешней информации;
3) использование серийных или создание новых технических средств — устройств управления;
4) разработка математического обеспечения функционирования робота — алгоритмов и программ;
5) использование существующих или создание новых манипуляторов.
Окружающая среда. В настоящее время понятие «окружающая среда» или «внешняя среда» достаточно установилось. Под этим понимают воздух, водные бассейны, леса, живую природу и процессы, происходящие в ней. Такое представление об окружающей среде формировалось человеком, его глазами, его образом жизни и взглядами в течение многих сотен лет. Стремительное развитие робототехники вызывает необходимость определить и сформировать понятие внешней среды для роботов, а она, как это будет показано, существенно отличается от общеизвестного понятия.
В качестве примера опишем внешнюю среду адаптивного робота для дуговой сварки — ее состав, основные параметры и особенности. Выбор такого примера обоснован тем, что окружающая среда для адаптивного дугового робота достаточно сложна, все или почти все другие варианты промышленного применения проще. Поэтому перейти от сложного к простому методом исключения параметров не составит больших трудностей. Обобщенное описание внешней среды позволит создать фундамент для разработки адаптивных роботов различного типа и сделать важный шаг в создании теории адаптивных роботов.
Таблица 7.4. Основные параметры внешней среды для адаптивных роботов (дуговая сварка)
Параметр | Влияние на работу робота | Формализированная модель | Ограничения, нормированные условия эксплуатации | Язык описания | Примечания |
Освещенность | - | - | Для нормальной работы фотоэлектрических и телевизионных приборов необходим достаточен уровень освещенности | Может быть представлена количественно в люксах | Подлежит рассмотрению при наличии в системе робота фотоэлектрических и телевизионных приборов |
Влажность | Возможно изменение коррозионной стойкости и изоляционных свойств | - | 98 % при температуре 35 ºС и более низких температурах без конденсации влаги и 100 %: конденсацией влаги | Может быть представлена количественно в процентах | Создание роботов для эксплуатации в условиях водной среды является самостоятельной и важной проблемой |
Давление | Возможно изменение фрикционных свойств материалов | - | В условиях вакуума гидросистема неприменима. Должно быть 1... 300 кПа | Может быть представлена количественно в килопаскалях | - |
Температура окружающей среды | Возможны изменения: статических и динамических характеристик СУ; статической точности; фрикционных свойств материалов | - | Для всеклиматического тсполнеиия +55 -60 °С | Может быть представлена количественно в градусах | - |
Помехи | Могут вызвать сбои в СУ робота и, как следствие, нарушение программы | - | - | Могут быть представлены количественно в децибелах относительно 1 мкВ | Защита от помех является актуальной и трудной задачей |
Колебания напряжения электропитания | Могут вызвать: сбои в работе; изменение статических и динамических характеристик СУ | - | +10…-15% | Могут быть представлены в процентах от номинального напряжения | - |
Транспортные устройства и манипуляторы изделий | Определяют: точность позиционирования, быстродействие и производительность комплекса | Общей модели нет. Существуют модели для некоторых конкретных задач | - | - | - |
Сварные соединения изделия | Определяют: степень сложности программы; длительность цикла сварки; количество проходов; способ сварки; сварочное оборудование; значительные отклонения осн стыка от заданной требуют применения следящих систем | - | - | - | - |
Технология сварки | Позволяет выбрать: режим сварки; технологический прием сварки | Уравнение регрессии относительно толщины свариваемых материалов, зазора и диаметра электродной проволоки | Для существующей модели: однопроходная сварка СО2, низкоуглеродистые и низколегированные стали; 3... 10 мм (толщина металла); плоское расположение шва | Таблица коэффициентов регрессии | Технология сварки для роботов непрерывно развивается и совершенствуется |
Тепловые сварочные деформации | Могут вызвать необходимость в коррекции программы | Уравнения связи между компонентами напряженного состояния и деформаций | Приводящие к изменению параметров технологии сварки | Линейные и угловые изменения в миллиметрах или радианах | Приращения могут быть исчислены вря знании картины температурного поля |
Человек-оператор | Определяет: точность позиционирования робота; рациональное построение программы | Существуют несколько моделей в зависимости от способа обучения | Необходима соответствующая квалификация оператора -сварщика | Соответствие класса сложности изделия классу квалификации оператора. Необходим язык диалога человека и робота | В каждом конкретном случае должен быть решен вопрос выбора рационального освещения |
Чтобы изложить материал компактно и наглядно, примем табличную форму (табл. 7.4). По вертикали перечислим основные параметры внешней среды адаптивного робота для дуговой сварки, по горизонтали — некоторые характеристики, дающие представление о формализованной, математической модели, ограничения и возможный язык описания, позволяющий ввести данные в устройство управления роботом.
Все параметры внешней среды можно разделить на две группы. К первой относятся те параметры, которые не зависят от поведения робота и корректировка которых не всегда возможна. Это освещенность, влажность, давление, температура, помехи и колебания напряжения электропитания. Ко второй группе отнесены параметры, которые робот или человек-оператор может менять. Это конструкция транспортных устройств, тип заготовки под сварку, технология сварки, тепловые деформации и, конечно, человек-оператор.
Подробный анализ данных, приведенных в табл. 7.4, уточнение и сравнение их с конкретными, имеющимися в предлагаемом для автоматизации технологическом процессе, позволит сделать ценные выводы, в том числе определить тип, принцип работы и конструкцию датчиков внешней информации, желаемый или требуемый уровень автоматизации и общую структуру робота.
В литературе по робототехнике часто употребляются понятия детерминированной — хорошо организованной, упорядоченной и недетерминированной — плохо организованной окружающей среды.
Под детерминированной понимают такую среду, в которой все окружающие робот предметы неподвижны и положение их во времени не меняется. Кроме того, неизменны такие параметры внешней среды, как, например, температура, освещенность, уровень радиации, помехи и т. д. Такая внешняя среда, или «сцена», может быть однажды описана и модель ее введена в память робота заранее.
Недетерминированная, неорганизованная внешняя среда характеризуется непредсказуемыми изменениями во времени параметров, внешней обстановки и расположением предметов. Информация о такой внешней среде должна вводиться в память робота постоянно, иначе он не сможет в ней ориентироваться.
Сказанное выше относится к роботу, который в пространстве неподвижен. Если же робот перемещается, то, естественно, будет меняться окружающая среда (хотя сама по себе она может быть хорошо упорядоченной), и в такой ситуации необходимо постоянно вводить информацию в память робота.
Возможен такой случай, когда параметры внешней среды и расположение окружающих робот предметов изменяются предсказуемо, т. е. по известным законам. В качестве примера можно привести изменение освещенности на планете в зависимости от ее вращения вокруг оси. Такая ситуация требует более глубокого изучения и в рамках настоящей книги ее мы не рассматриваем.
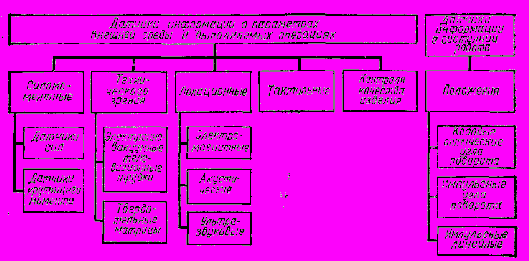
Рис. 7.4. Классификация датчиков информации адаптивных роботов
Обязательное условие успешного функционирования адаптивного робота — связь с окружающей средой. Если окружающая среда имеет неупорядоченный характер, т. е. не строго организована и меняется во времени, а в контуре управления присутствие человека невозможно либо нежелательно, то возникает необходимость в самостоятельной обработке роботом информации об окружающей среде и принятии решения. При этом особая роль отводится задаче очувствления робота, т. е. создания специализированных датчиков внешней информации и разработки способов ее обработки.
Датчики информации. Возможность активно взаимодействовать с внешней средой, измерять ее параметры, необходимые для качественного выполнения технологической операции, позволяет существенно снизить затраты на подготовку производства и расширить область применения адаптивных роботов.
Наиболее перспективные области применения адаптивных роботов — механическая сборка, электродуговая и, иногда, контактная точечная сварка, кислородная резка, абразивная зачистка и шлифование, операции упаковки, установка и съем деталей с конвейера, операции распознавания и сортировка изделий, разбор неориентированных деталей и контроль качества изделий.
Создание и серийный выпуск адаптивных роботов для автоматизации перечисленных процессов немыслимы без своевременной разработки и производства средств очувствления, — датчиков, пригодных для различных условий эксплуатации роботов в промышленности.
Датчики адаптивных роботов (рис. 7.4) можно условно разделить на две группы: 1) датчики информации о параметрах внешней среды и выполняемых операциях; 2) датчики состояния узлов самого манипулятора. Первая, наиболее многочисленная группа средств очувствления сформирована на основании анализа технологии выполнения перечисленных процессов. Основными классификационными признаками приняты физические параметры окружающей среды. В соответствии с принятой классификацией первая группа разделена на пять основных типов систем — сило-моментные, технического зрения, локационные, тактильные и контроля качества изделия.
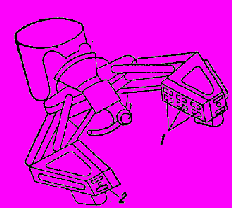
Рис. 7.5- Специальное захватное устройство, оснащенное тактильными датчиками
Следует отметить, что датчикам технического зрения часто отдается предпочтение как наиболее информативному и совершенному методу получения информации. Общий принцип действия таких систем состоит в том, что телевизионная камера (одна или несколько) обозревает рабочее пространство и передает информацию в ЭВМ, которая ее обрабатывает и выдает описание сцены, попавшей в поле зрения камеры. Это описание может сравниваться с имеющейся в памяти ЭВМ математической моделью и использоваться в дальнейшем для целенаправленного действия исполнительного устройства робота по соответствующей программе.
Это наиболее совершенный и сложный вариант. Существует большое количество различных решений и конструкций, которые относятся к адаптивным роботам, но не имеют искусственного зрения.
Примером может служить специальное захватное устройство, оснащенное тактильными датчиками, построенными на основе микропереключателей (рис. 7.5). На наружных сторонах его губок установлены шесть датчиков, с помощью которых фиксируется соприкосновение с объектом. На внутренних поверхностях губок установлены датчики давления 1, которые позволяют определить усилие удержания предмета. Два фотодиода 2 обеспечивают локацию объекта и наведение на него захватного устройства. Такое устройство осуществляет поиск, некоторое опознавание объекта и его удержание.
Изящное решение внешнего устройства, дающего возможность «видеть» двухмерное изображение предмета, основано на применении специального дискретного поля (рис. 7.6), или, иначе говоря, матрицы. Эта матрица установлена в зоне действия робота и выполняет роль сетчатки искусственного глаза. Использование в качестве чувствительных элементов электроконтактных, фотоэлектрических, пневматических и электромагнитных датчиков позволяет «видеть» двухмерное изображение объекта, т. е. поверхность объекта, которая соприкасается с чувствительным полем.
Точность «изображения» объекта зависит от количества чувствительных элементов. Информация о включенных элементах передается в устройство управления, обрабатывается и на рабочий орган робота подается команда управления с учетом позитивного положения объекта. Если чувствительные элементы будут бесконтактными, например фотоэлементы, то можно создать трехмерное очувствленное устройство и получить объемное изображение.
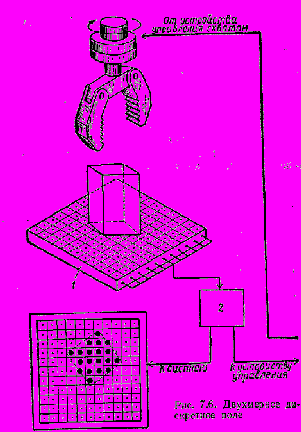
Рис. 7.6. Двухмерное дискретное поле
К датчикам информации о состоянии узлов и систем манипулятора в первую очередь относится комплекс измерительных средств, обеспечивающих высокую точность позиционирования приводных систем манипулятора. Среди них наиболее часто применяются цифровые датчики углового и линейного положения звеньев манипулятора, датчики скорости и датчики крутящего момента.
Правильный выбор типа датчика определяет успех в создании адаптивного робота.
Устройства управления адаптивными роботами можно отнести к классу мини-ЭВМ или к специализированным вычислительным машинам в зависимости от сложности алгоритма управления, необходимого быстродействия, объема памяти и т. д. В некоторых случаях, например при создании адаптивного робота типа «глаз — рука», может появиться необходимость использования средних ЭВМ со стереотелевизионным датчиком. В каждом случае выбору типа ЭВМ должен предшествовать тщательный анализ исходных данных.
Использование серийных ЭВМ (или их отдельных блоков) для управления адаптивными роботами наиболее целесообразно, так как позволяет применять отработанные модели и экономит время на разработке и создании специальной ЭВМ.
Наиболее распространены в нашей стране и странах — членах СЭВ мини-ЭВМ серии СМ ЭВМ. В основу машин этого типа положен так называемый принцип общей шины. Общая шина включает в себя провода для параллельной передачи адреса, данных и управляющих сигналов. К этой шине подключают центральные процессоры, оперативные запоминающие устройства и все периферийные устройства. Каждое периферийное устройство, как и оперативное запоминающее устройство, снабжается так называемым буферным регистром, который включается в общее поле памяти ЭВМ.
В минимальный комплекс машины СМ-3 входят (кроме процессора с быстродействием около 200 тыс. опер./с) оперативное запоминающее устройство емкостью 16 К, внешняя память (на магнитных дисках и лентах) емкостью в несколько М-байт и четыре устройства ввода-вывода. СМ-4 комплектуется двумя центральными процессорами и соответственно обладают расширенными возможностями оперативной и внешней памяти. Описания и технические данные машин этого типа имеются в соответствующих справочниках.
В некоторых случаях могут быть оправданы разработка и создание устройства управления специального типа для адаптивного робота. Примером может служить созданное НПО ЛЭМЗ устройство УКМ-772 для процесса дуговой сварки плавлением (см. гл. 4). Это устройство имеет встроенную микроЭВМ «Электроника-60», много вводов внешней информации и выводов каналов управления. Благодаря наличию микроЭВМ устройство может управлять адаптивным роботом по довольно сложной программе. Естественно, что должно быть разработано соответствующее программное обеспечение.
Разработку и создание специализированного устройства управления следует тщательно обосновать и аргументировать.
Разработка математического (пограммного) обеспечения адаптивного робота — центральная, наиболее сложная задача. Ей посвящено множество исследований, опубликованных работ, других материалов, поэтому подробно останавливаться на этой задаче не будем. Однако следует все же отметить, что разработке математического обеспечения адаптивных роботов должны предшествовать формулирование параметров окружающей среды, разработка адекватной математической модели управляемого процесса, выбор из числа существующих или разработка нового проблемно-ориентированного языка для описания процесса и ввода исходных данных, выбор математического аппарата и, в частности, формулирование задачи оптимизации по выбранным критериям качества. Выполнение всех этих работ требует специалистов высокой квалификации и соответствующего времени.
Манипуляторы адаптивных роботов. Как уже отмечалось (см. гл. 2), в настоящее время разработано много манипуляторов, отличающихся компоновкой, количеством управляемых координат, точностью позиционирования и приводом. Нет сомнений, что изложенные ранее соображения о кинематике и динамике манипуляторов можно использовать и при создании адаптивных роботов. Однако не следует думать, что не может возникнуть и новых соображений и идей.
К числу новых положений, не рассмотренных в гл. 2, относится задача создания манипулятора, подвижного в пространстве. Принято считать, что подвижные роботы принадлежат к роботам с искусственным интеллектом. Однако жизнь вносит свои коррективы и уже сейчас есть образцы промышленных роботов, корпус которых перемещается по программе вдоль направляющих. Такое конструктивное решение позволяет расширить область применения роботов. Для решения задачи создания подвижного в пространстве манипулятора нужно выбрать способ перемещения робота, тип привода этой координаты и обеспечить управление. Перемещение всего робота в пространстве приведет к усложнению его динамики и, возможно, к уменьшению точности позиционирования.
Второй особенностью манипуляторов адаптивных роботов может быть усложнение конструкции схвата, в частности, оборудование его соответствующими датчиками.
В итоге можно сказать, что манипулятор конкретного адаптивного робота следует выбирать из числа имеющихся или создавать новый в зависимости от конкретных технических требований.