Анализ и обобщение опыта и тенденций создания промышленных роботов в отечественной и зарубежной робототехнике показывает, что все большее распространение получает электромеханический привод промышленных роботов. Впоследние год
Вид материала | Документы |
СодержаниеРоботизированные технологические комплексы (ртк) 5.2. РТК в кузнечно-прессовом производстве 5.3. РТК в механообработке |
- Дипломная работа студента, 601.76kb.
- Исать собственные приложения для управления роботами на примере Lego nxt, а также использовать, 76.9kb.
- С применением grid-технологий, 81.79kb.
- История роботов, написанная роботом, 101.24kb.
- Sdfield> Самостоятельная подготовка, 455.42kb.
- Вдокладе описывается технология обучения распределенной системы автономных мобильных, 45.47kb.
- Внушающих уверенность жилищ люди живут в обличии роботов-суррогатов сексуальных, физически, 367.79kb.
- Возможное участие родителей, 108.84kb.
- Анализ работы шмо учителей физики, химии, биологии за 2010-2011 учебный год, 113.58kb.
- Лега В. П. Наука и вера, 152.3kb.
РОБОТИЗИРОВАННЫЕ ТЕХНОЛОГИЧЕСКИЕ КОМПЛЕКСЫ (РТК)
5.1. Структура, состав, назначение РТК
В этой главе приведены материалы, в которых содержатся ответы на три основных вопроса: что такое роботизированный технологический комплекс и какое место он занимает в общей проблеме автоматизации; какие бывают РТК с точки зрения их структуры; где и в каких условиях машиностроительного производства они применяются. В конце главы помещены данные об испытаниях, экономической эффективности применения и надежности промышленных роботов РТК.
Опыт издания и применения промышленных роботов в СССР и за рубежом однозначно свидетельствует о том, что один отдельно установленный промышленный робот может использоваться только с целью изучения его технических характеристик, для демонстрации, обучения обслуживающего персонала и т. д. Никакого значения в производственном плане такой робот не имеет.
Главная идея роботизированного технологического комплекса заключается в том, что промышленный робот должен использоваться в сочетании с определенным технологическим оборудованием, как, например, пресс, металлорежущий станок, сварочная установка и т. д., и предназначен для выполнения одной или нескольких конкретных технологических операций.
Впервые понятие роботизированный комплекс появилось в специальной литературе примерно в 1980 г. Некоторое время употреблялись термины робототехншеские или роботизированные системы, роботизированные технологические и роботизированные производственные комплексы и др.
В 1985 г. издан ГОСТ 26228—85 «Системы производственные гибкие. Термины и определения», в котором сказано:
«Роботизированный технологический комплекс (РТК) — совокупность единицы технологического оборудования, промышленного робота и средств оснащения, автономно функционирующая и осуществляющая многократные циклы.
Примечания.
1. РТК, предназначенные для работы в ГПС, должны иметь автоматизированную переналадку и возможность встраиваться в систему.
2. В качестве технологического оборудования может быть использован промышленный робот.
3. Средствами оснащения РТК могут быть: устройства накопления, ориентации, поштучной выдачи объектов производства и другие устройства, обеспечивающие функционирование РТК».
В этой формулировке обращает на себя внимание категоричность определения: «... единицы технологического оборудования, промышленного робота...», т. е. подразумевается одна единица технологического оборудования и один промышленный робот.
Если количество промышленных роботов и единиц технологического оборудования больше, то тогда это будет роботизированный технологический участок (РТУ) (ГОСТ 26228—85) — совокупность роботизированных технологических комплексов, связанных между собой транспортными средствами и системой управления, или несколько единиц технологического оборудования, обслуживаемых одним или несколькими промышленными роботами, в которой предусмотрена возможность изменения последовательности использования технологического оборудования.
Рассмотрим проблему автоматизации машиностроения с целью установить место, которое занимают в ней роботизированные технологические комплексы.
В книге «Роботизированные производственные комплексы» Ю. Г. Козырева и др. (М. : Машиностроение, 1987) приводятся следующие пять уровней автоматизации:
— первый уровень — автоматизация цикла обработки, заключающаяся в управлении последовательностью и характером движений рабочего инструмента с целью получения заданной формы обрабатываемой детали. Наиболее полное воплощение автоматизация этого уровня получила в станках с ЧПУ;
— второй уровень — автоматизация загрузочно-разгрузочкых операций (установки и снятия детали со станка), позволяющая рабочему обслуживать несколько единиц технологического оборудования, т. е. перейти к многостаночному обслуживанию. Наибольшей универсальностью и быстротой переналадки характеризуются промышленные роботы, используемые для автоматизации вспомогательных и транспортных операций. Второй уровень автоматизации все чаще обеспечивается созданием роботизированных технологических комплексов;
— третий уровень — автоматизация контроля, ранее выполняемого человеком: состояния инструмента и своевременной его замены; качества обрабатываемых изделий; состояния станка и удаления стружки, а также подналадки технологического процесса (адаптивное управление). Такая автоматизация освобождает человека от постоянной связи с машиной и обеспечивает длительную работу оборудования по обработке деталей одного типоразмера при минимальном участии или далее без участия человека в течение одной-двух смен.
Третий уровень автоматизации обеспечивается созданием адаптивных РТК., а также гибких производственных модулей. Согласно ГОСТ 26228—85, гибкий производственный модуль (ГПМ) — единица технологического оборудования для производства изделий произвольной номенклатуры в установленных пределах значений их характеристик с программным управлением, автономно функционирующая, автоматически осуществляющая все функции, связанные с их изготовлением, имеющая возможность встраивания в гибкую производственную систему;
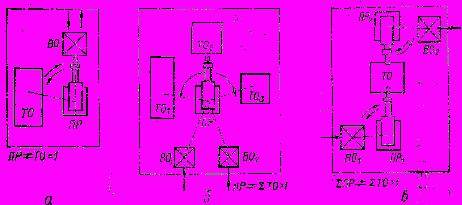
Рис. 5.1. Роботизированные технологические комплексы: а — однопозицнонный; п — групповой: ч — многопознционный
— четвертый уровень — автоматизация переналадки оборудования. На существующем оборудовании переналадка осуществляется вручную, что требует значительного времени. Поэтому важной задачей является совершенствование систем переналадки оборудования — применяемых приспособлений, инструмента и оснастки, а также методов задания циклов и режимов обработки. В идеале следует стремиться к созданию автоматических систем переналадки оборудования для выпуска новых изделий;
— пятый уровень — гибкие производственные системы (ГПС). Поскольку описанию ГПС специально посвящена гл. 6, то отметим только то, что, по существующему мнению, такая форма организации производственного процесса является высшей.
Приведенная классификация не претендует на исчерпывающую полноту и стройность, но очень четко показывает место роботизированных технологических комплексов в общей проблеме автоматизации машиностроительного производства.
В состав роботизированного технологического комплекса входят:
1) технологическое оборудование (пресс, металлорежущий станок, установка для термообработки и т. д.);
2) промышленный робот;
3) вспомогательное, транспортное оборудование. Роботизированные технологические комплексы бывают: однопоаиционные (рис. 5.1, а), имеющие наиболее простую структуру (ТО — технологическое оборудование, ПР — промышленный робот, ВО — вспомогательное оборудование); групповые (рис. 5.1, б) и многопозиционные (рис. 5.1, в).
Эта классификация не охватывает всех возможных структур РТК и может рассматриваться как классификация типовых структур.
Следует отметить, что, несмотря на относительную простоту однопозиционных РТК, они весьма распространены, поэтому рассмотрим их подробнее.
РТК работает следующим образом. Заготовка, предварительно ориентированная во вспомогательном оборудовании (ВО), захватывается рабочим органом промышленного робота, переносится в рабочую зону технологического оборудования и устанавливается в нужном положении. Иногда этот процесс достаточно активный, как, например, при обработке заготовки на токарном станке. Нужно остановить шпиндель станка, дать команду на открытие зажимного приспособления (патрона, цанги и т. д.), точно установить заготовку в зажимное приспособление, зажать его, отвести рабочий орган робота и включить станок на обработку детали. По окончании цикла обработки необходимо остановить станок, взять обработанную деталь и перенести во вспомогательное оборудование В02. Обработанные детали либо устанавливаются ориентированными в пространстве, либо помещаются в тару навалом.
Технологическое оборудование, рекомендованное для применения в составе РТК, должно быть достаточно распространенным и перспективным с точки зрения конструкции, технологичности, эксплуатационных параметров и степени автоматизации. Этот самостоятельный вопрос широко освещен в соответствующей литературе и поэтому не будем на нем останавливаться. Отметим лишь одно важное соображение. Технологическое оборудование должно иметь устройство числового программного или хотя бы циклового управления. Если это условие не соблюдено, то могут возникнуть непредвиденные трудности при стыковке ТО с промышленным роботом, которые приведут к неоправданным затратам времени и средств.
Вспомогательное оборудование предназначено для:
1) накопления определенного количества ориентированных заготовок на начальной позиции комплекса;
2) поштучной выдачи заготовки в определенную точку пространства для взятия ее схватом робота (при необходимости);
3) транспортирования заготовок и изделий между последовательно расположенным оборудованием внутри комплекса с сохранением ориентации;
4) переориентации заготовок и изделий, если это нужно;
5) хранения межоперационного задела и задела между комплексами.
Вспомогательное оборудование, входящее в состав транспортно-накопительной системы, как правило, не имеет между собой ни конструктивных, ни информационных связей и все команды получает от технологического оборудования и промышленных роботов. В качестве накопительных устройств в комплексе могут применяться лотки (скаты, склизы), шаговые конвейеры различного типа, цепные конвейеры, круговые накопительные устройства, тупиковые накопители, роликовые конвейеры и многоместная тара. Соответствующий тип транспортно-накопительного устройства выбирают, тщательно анализируя заготовку и изделия, особенности технологического оборудования и промышленных роботов.
В литературе часто встречается термин «бункерные загрузочно-ориентирующие устройства», который точнее определяет назначение этих устройств в функциональном плане, но не охватывает все возможные варианты, и поэтому в дальнейшем будем пользоваться термином «вспомогательные устройства». Вспомогательные устройства РТК можно разделить на несколько типов [8].
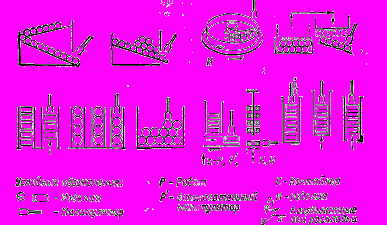
Рис. 5.2. Стационарные бункерные вспомогательные устройства РТК
Стационарные вспомогательные устройства, жестко устанавливаемые в определенном положении, предназначены для подачи ориентированных заготовок в зону обслуживания промышленного робота.
Во вспомогательных устройствах лоткового или бункерного типа (рис. 5.2) изделия могут предварительно загружаться оператором, подаваться в рабочую позицию под собственным весом или с помощью специальных устройств.
Подвижные (сменные) технологические приспособления, как правило, имеют прямоугольную, плоскую форму, на их верхней поверхности располагаются изделия в специальных гнездах (рис. 5.3).
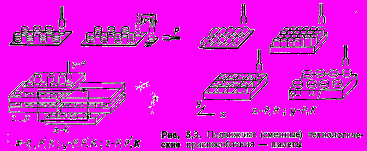
Рис. 5.3. Подвижные (сменные) технологические приспособления — паллеты
Такие устройства позволяют производить загрузку вне PTK, например, на складе, и могут быть поданы в рабочую зону автоматически, скажем с помощью робокара.
Вращающиеся вспомогательные устройства представляют собой вращающийся круглый стол с шаговым приводом. Заготовки располагаются по периферии стола в специальных гнездах или на штырях в зависимости от ее конфигурации. На рис. 5.4 показаны различные варианты компоновки таких накопителей. Недостаток накопителей такого типа — их ограниченная емкость.
Транспортные вспомогательные устройства представляют собой цепной, многозвенный конвейер, перемещающийся в горизонтальной плоскости на двух звездочках, одна из которых — ведущая — с шаговым приводом (рис. 5.5). Преимущество таких накопителей — относительно большая емкость и возможность соединения с другим РТК или иным оборудованием.
Несмотря на то, что такие бункерные загрузочно-ориентирующие устройства (в этом случае термин соответствует их функциональному назначению) характеризуются высокой степенью автоматизации и освобождают рабочего от процедуры установки изделий, они не могут применяться во всех случаях из-за хрупкости и повышенной сцепляемости заготовок, требований к качеству поверхности и т. д. Как правило, эти устройства осуществляют первичное ориентирование и поштучное отделение заготовок.
Существует несколько способов выноса деталей из навала, в том числе карманчиковый, крючковый (штырьевой), секторные лопастной, щелевой, отбор под действием собственного веса и т. д. Достаточно широко применяются вибрационные бункерные устройства, которые наряду с рядом преимуществ имеют и некоторые недостатки (вибрации, повышенный шум, сложность настройки и т. д.).
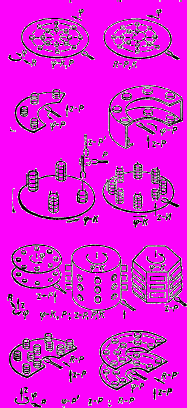
Рис. 5.4. Вращающиеся накопители
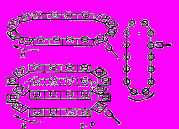
Рис. 5.5. Транспортные накопители (конвейеры) РТК
5.2. РТК в кузнечно-прессовом производстве
Промышленные роботы давно и успешно применяются в кузнечно-прессовом производстве. Это объясняется тем, что процессы кузнечно-прессового производства весьма кратковременны и промышленный робот достаточно полно загружен. Кроме того, в кузнечно-прессовом и штамповочном производстве очень велик удельный объем вспомогательных и транспортных операций, особенно когда изделие обрабатывается последовательно на нескольких прессах. Наконец, одной из важных причин широкого применения промышленных роботов в этом производстве является желание понизить опасность и травматизм, связанные с особенностями производства. Нельзя не отметить и тот факт, что заготовки часто имеют высокую температуру и острые края, повышающие трудность и опасность их транспортирования. Гуманное желание освободить человека от однообразной, монотонной и трудной работы требует от разработчиков особого внимания к этому типу производства.
Роботизированные технологические комплексы в кузнечно-прессовом и штамповочном производстве создают для автоматизации следующих операций: холодной листовой штамповки; горячей и холодной объемной штамповки; ковки; штамповки изделий из пластмасс и порошков.
Методом холодной листовой штамповки выполняются некоторые разделительные и формообразующие операции. Поскольку для разделительных операций исходной заготовкой, как правило, служит непрерывный материал (ленты, рулоны, полосы, прутки и т. д.), с которым использование современных конструкций промышленных роботов пока нецелесообразно, создание роботизированных технологических комплексов предусматривается только для формообразующих штамповочных операций, выполняемых на штучных заготовках.
При создании РТК в листоштамповочном производстве промышленные роботы должны выполнять вспомогательные и транспортные операции по переносу заготовки из подающего устройства в рабочее пространство штампа пресса и удалению изделия после штамповки в приемное устройство или в последующий пресс. Исходными заготовками для листоштамповочных РТК могут быть плоские и объемные штучные заготовки, имеющие правильную геометрическую форму и позволяющие использовать подающее устройство с поштучной выдачей заготовок в соответствующий схват робота.
Процесс объемной штамповки включает в себя следующие операции: получение исходной заготовки; нагрев ее до температуры ковки; штамповку; отделение отходов от поковки, термообработку поковки; очистку ее поверхности, а иногда и калибровку.
Автоматизация технологического процесса горячей штамповки предусматривает организацию ориентированной передачи заготовки и полуфабриката по всем позициям, установку заготовки в штампы, включение пресса, а также нанесение технологической смазки на рабочую поверхность штампа. Весь перечисленный объем вспомогательных операций может выполняться современными промышленными роботами при условии обеспечения ориентированной подачи заготовки на исходную позицию пресса в положении, удобном для захвата роботом и выталкивания изделия после выполнения каждого перехода с соблюдением тех же условий.
В качестве исходного материала при объемной штамповке используются штучные заготовки, отрезанные из проката круглого, квадратного или прямоугольного сечения, которые могут захватываться и удерживаться универсальными устройствами, используемыми промышленными роботами.
Захват и перенос деталей промышленным роботом после штамповки возможен при наличии у детали соответствующего расположения базовых поверхностей. Это накладывает ограничения на номенклатуру деталей, штамповка которых может быть автоматизирована с использованием промышленных роботов. Применение промышленных роботов может вызвать и некоторые изменения формы детали— введение технологических прибылей, платиков и т. д. В свою очередь, к промышленным роботам, применяемым на операциях объемной штамповки, предъявляются специальные требования по тепло-, пыле- и виброзащищенности, которые должны обеспечивать надежность работы комплекса. Планировка робототехнического комплекса в кузнечно-прессовом и штамповочном производстве должна осуществляться с учетом типа пресса, модели промышленного робота, конкретных конструкций вспомогательных механизмов и формы изделия. Для этих целей часто используются двурукие роботы.
Составные части РТК должны иметь:
1) возможность управления работой прессов, роботов и вспомогательного оборудования с помощью системы программного управления;
2) возможность переналадки на штамповку различных изделий; продолжительность переналадки желательно иметь не более 60... 90 мин, что позволит использовать комплексы в серийном и даже мелкосерийном производстве;
3) обезжиривание перед загрузкой на исходную позицию листовых заготовок из немагнитного материала в о избежание их слипания;
4) минимальные заусенцы во избежание сцепления заготовок;
5) искривление заготовок из плоскости, не превышающее 2 % длины и ширины заготовки.
Промышленные роботы должны иметь: возможность быстрой смены ЗУ при переходе на штамповку нового изделия; регулировку, обеспечивающую быструю перестройку на работу с новыми изделия-
ми, а также разъемы и места подключения энергоносителя и линий связи с технологическим оборудованием и вспомогательными устройствами.
Типичная компоновка роботизированного технологического комплекса в кузнечно-прессовом производстве приведена на рис. 5.6. В состав такого РТК входят: магазинное устройство 7, выдающее плоские заготовки на исходную (загрузочную) позицию промышленного робота; двурукий промышленный робот 5 с цикловым программным управлением, загружающий заготовки в штамп и снимающий с него отштампованные полуфабрикаты; пресс 1, выполняющий собственно технологическую операцию; ЗУ 2 манипулятора пневматического или электрического типа (для плоских заготовок); приемная тара 3 с тележкой; устройство 6 циклового программного управления комплексом и ограждение 4, исключающее возможность проникновения человека в опасную зону во время работы РТК.
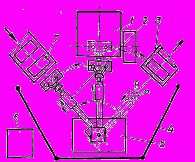
Рис. 5.6. Типовая компоновка РТК в кузнечно-прессовом производстве
5.3. РТК в механообработке
Механическая обработка — это завершающий этап производственного процесса перед сборкой. Поэтому механическую обработку проходит большинство заготовок и полуфабрикатов.
Отличительные особенности процессов механообработки с точки зрения роботизации:
1) относительно большое машинное время обработки изделий (от десятков секунд до нескольких десятков минут);
2) отсутствие высоких температур нагрева заготовок;
3) достаточно точная форма заготовок и особенно изделий.
Номенклатура деталей, обработка которых технически возможна и целесообразна на автоматизированных комплексах «станок — робот», определяется следующими факторами:
1) конструктивными параметрами деталей;
2) видом и состоянием заготовки, поступающей на обработку;
3) техническими требованиями, предъявляемыми к детали;
4) габаритными размерами и массой детали.
Детали, предназначенные для обработки в системе «станок — робот», должны иметь следующие параметры:
1) однородные по форме и расположению поверхности для базирования и захвата, позволяющие без дополнительной проверки устанавливать их на станок, где для базирования и закрепления используется широкоуниверсальная технологическая оснастка (центры, патроны, пневмотиски и др.);
2) ясно выраженные базы и признаки ориентации, позволяющие организовать транспортирование и складирование заготовок около станков в ориентированном виде с использованием стандартной вспомогательной оснастки;
3) возможность унифицировать процессы обработки и типы оборудования для применения группового метода обработки.
В методических рекомендациях «Автоматизированные технологические комплексы «оборудование — робот» (М-: НИИМаш, 1981.— 104 с.) приведены подробная классификация и номенклатура деталей, рекомендуемых для обработки в роботизированных технологических комплексах. Ограничения по геометрической форме деталей диктуются не столько применением промышленных роботов, сколько трудностями транспортирования деталей, сохранения их ориентированного положения при использовании стандартной тары и приемопередающих механизмов.
Автоматизация механообработки за счет применения промышленных роботов может развиваться по пути создания: 1) роботизированных технологических комплексов на базе имеющегося оборудования и 2) отлаженных комплексов на заводах-изготовителях на базе современного технологического оборудования. Оба направления могут развиваться параллельно, но второй путь нам кажется перспективнее.
Автоматизация станков методом стыковки их с роботами требует обязательно некоторой модернизации станков-автоматов и упорядочения хранения и транспортирования заготовок и изделий. Поэтому особенно важно проводить предварительный технологический анализ и создавать технологическую и техническую документацию для подготовки и применения промышленных роботов.
Технологический процесс обработки деталей в роботизированном технологическом комплексе характеризуется:
1) максимально возможной концентрацией операций на станках в ЧПУ, что позволяет сократить число остановок в процессе производства, улучшает качество изделия за счет повышения точности, сокращает время производственного цикла;
2) оснащением станков легко переналаживаемой оснасткой, обеспечивающей без значительной переналадки высокоточное базирование и надежное крепление детали в процессе обработки;
3) тщательной подготовкой баз на обрабатываемых изделиях, гарантирующей получение и сохранение заданных чертежами технических требований.
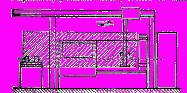
Рис. 5.7 Схема РТК с горизонтальной компоновкой направляющей робота
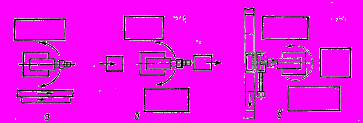
Рис. 5.8. Схемы компоновок РТК для обслуживания металлорежущих станков
Для роботизированных технологических комплексов в первую очередь нужно использовать станки с ЧПУ и цикловым программным управлением, а также станки-полуавтоматы. Совместная работа станка с промышленными роботами требует доработки его электрической схемы, чтобы обеспечить возможность обмена необходимой информацией между станком и роботом. Обмен осуществляется с помощью команд (ответов).
В механообработке существует много различных компоновок роботизированных технологических комплексов. Горизонтальная компоновка направляющей робота, расположенной над станками, показана на рис. 5.7. Три варианта компоновок РТК с обычными напольными промышленными роботами, обслуживающими один или несколько станков, приведены на рис. 5.8.