Анализ и обобщение опыта и тенденций создания промышленных роботов в отечественной и зарубежной робототехнике показывает, что все большее распространение получает электромеханический привод промышленных роботов. Впоследние год
Вид материала | Документы |
- Дипломная работа студента, 601.76kb.
- Исать собственные приложения для управления роботами на примере Lego nxt, а также использовать, 76.9kb.
- С применением grid-технологий, 81.79kb.
- История роботов, написанная роботом, 101.24kb.
- Sdfield> Самостоятельная подготовка, 455.42kb.
- Вдокладе описывается технология обучения распределенной системы автономных мобильных, 45.47kb.
- Внушающих уверенность жилищ люди живут в обличии роботов-суррогатов сексуальных, физически, 367.79kb.
- Возможное участие родителей, 108.84kb.
- Анализ работы шмо учителей физики, химии, биологии за 2010-2011 учебный год, 113.58kb.
- Лега В. П. Наука и вера, 152.3kb.
5.4. РТК в сборочном производстве
Сборка изделия — завершающий этап производства, во многом определяющий качество и стоимость продукции. В различных отраслях машиностроения трудоемкость сборочных работ составляет от 40 до 50 % общей трудоемкости изготовления изделий, что объясняется большим объемом операций и низким уровнем их автоматизации и механизации.
В условиях серийного и мелкосерийного производства, удельный вес которого составляет около 75 %, стоимость сборки существенно выше, чем в крупносерийном и массовом производстве, главным образом вследствие большого объема пригоночных и доводочных операций и значительной трудоемкости межоперационного и межцехового транспортирования.
Для более глубокого понимания процесса сборки как объекта роботизации рассмотрим некоторые основные положения, которые характеризуют этот производственный процесс.
Каждое изделие в машиностроении с технологической точки зрения состоит из элементов различной сложности, узлов и отдельных детален. Деталью называют часть изделия, выполненную из однородного материала и являющуюся первичным звеном сборки. Узлом называют часть изделия, представляющую собой любое соединение некоторого количества деталей, выполненное любым способом. Далее по степени сложности выделяют подгруппы и группы.
Различают конструктивные и сборочные элементы изделий.
Конструктивные элементы определяются функциональным назначением их в машине независимо от порядка выполнения сборки» сборочные — представляют собой узлы и детали машин, которые могут быть собраны отдельно и независимо от других элементов изделия.
Схему изделия средней сложности можно представить в виде иерархической структуры, на нижнем уровне которой расположены отдельные детали, а на верхнем — готовое изделие.
Все многообразие выполняемых при сборке соединений можно разделить на следующие четыре типа:
1) неподвижные разборные соединения;
2) неподвижные неразборные соединения;
3) подвижные разборные соединения;
4) подвижные неразборные соединения.
Неподвижные соединения обеспечивают неизменное взаимное положение собранных деталей или узлов. Подвижные соединения обеспечивают возможность определенного взаимного перемещения деталей. Разборными называют соединения, которые могут быть разобраны без особых затруднений и без повреждения сопряженных или крепежных деталей. Неразборными называют соединения, разборка которых в процессе эксплуатации не предусмотрена, а потому крайне затруднительна, требует больших усилий или сопровождается повреждением сопряженных деталей.
Анализ изделий машиностроения и технологических процессов их сборки показал, что около 70...90 % соединений деталей, выполняемых в процессе сборки,— типовые. Технологическая структура сборки, а точнее соединительных операций представлена ниже:
Виды соединений Удельный вес, %
С зазором 30…35
Резьбовые 30…40
Прессовые 10…15
Прочные 10…20
В процессе сборки человеку приходится выполнять весьма большой перечень разнообразных работ, в том числе обрубку, опиливание, шабрение, притирку, отделку абразивным инструментом, различную обработку отверстий (сверление, нарезание резьбы, зенкование, развертывание и др.), промывку и очистку деталей. Кроме того, при сборке применяются клепка, контактная точечная и дуговая сварка, склеивание деталей, соединение с натягом, разнообразные винтовые соединения.
Помимо перечисленных операций сборщик выполняет большое количество транспортных, вспомогательных операций, перемещая мелкие и крупные детали в пространстве — главным образом от лотков-накопителей к собираемому изделию.
В машиностроении различают три основных вида сборки:
1) по принципу индивидуальной пригонки;
2) по принципу полной взаимозаменяемости;
3) по принципу ограниченной взаимозаменяемости.
Кроме того, применяется так называемая селекционная сборка, которая осуществляется методом непосредственного подбора, методом предварительной сортировки деталей на группы и комбинированным методом.
Организационные формы сборки зависят от типа производства, размера выпуска, трудоемкости процесса сборки и других факторов. С точки зрения роботизации можно выделить три основные организационные формы сборки.
Стационарная сборка (рис. 5.9, а) выполняется на одном сборочном посту, к которому подаются все необходимые детали, узлы и материалы. Таким образом собирают самолеты, тяжелые изделия Типа турбин, металлорежущие станки и т. д. Транспортировка таких изделий по цеху либо невозможна, либо трудноосуществима и совершенно нецелесообразна.
Подвижная сборка (рис. 5.9, б) выполняется при перемещении собираемого изделия от одного сборочного поста к другому; на каждом из таких постов рабочие выполняют только одну определенную и повторяющую операцию. Детали, узлы и материалы подаются к соответствующим рабочим местам сборочного поста, оборудованного соответствующими инструментами и приспособлениями, необходимыми для выполнения работы.
Наиболее ярким и характерным примером подвижной сборки может служить сборка легковых и грузовых автомобилей на конвейере, широко распространенная на большинстве автомобилестроительных заводов всех стран. Кузова легковых и кабины грузовых автомобилей укреплены на специальном конвейере, который перемещается вдоль цеха. Рабочие-сборщики выполняют соответствующие операции, и с конца конвейера сходит готовая машина. Таким образом производят контактную точечную сварку кузовов.
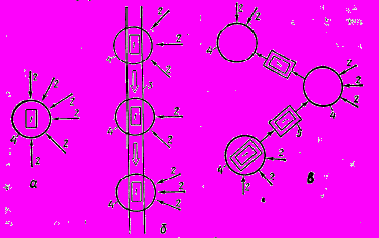
Рис. 5.9. Основные организационные формы сборки:
а — стационарная; б — подвижная; в — транспортная; 1 — собираемое изделие; 2 — комплектующие детали; 3 — конвейер; 4 — зона сборки; 5 — транспортный робот — робокар.
Следует обратить внимание на то, что подавляющее количество таких конвейеров движется непрерывно с определенной скоростью. Исследования, проведенные социологами, показали, что на постоянно движущемся конвейере рабочий работает лучше, чем на пульсирующем. Фиксированное время, отведенное для выполнения операции сборки, способствует излишнему утомлению человека. Обобщение опыта применения роботов на сборочных и сварочных операциях позволило сделать однозначный вывод: для успешного функционирования роботов значительно лучше пульсирующий конвейер. Программирование робота в движущейся системе координат возможно, но значительно сложнее. Кроме того, уменьшается точность позиционирования робота.
Транспортная сборка (рис. 5.9, в). В последние годы некоторые передовые автомобилестроительные фирмы отказываются от традиционных принципов подвижной сборки с применением конвейеров. Объясняется это тем, что сам принцип конвейерной сборки ограничивает возможности предприятия и затрудняет его перестройку на выпуск новой модели автомобиля.
Взамен традиционного конвейера создаются отдельные посты сварки и сборки, а изделие перемещается между ними по программе с помощью специальных транспортных роботов — робокаров. Вся система управляется единой ЭВМ, а на каждом робокаре есть своя бортовая ЭВМ. Такая многопостовая транспортная система сборки обладает высокой мобильностью и может быть в кратчайшие сроки переведена на выпуск другого типа изделия. Примером может служить известная система «Робогейт», созданная автомобильным концерном «Фиат» совместно со станкостроительной фирмой «Комау».
Во всех вариантах сборочного производства особое значение имеет разработка операционной и маршрутной технологии.
В настоящее время имеются совершенно очевидные достижения робототехники и роботостроения, но уровень использования роботов в сборочном производстве существенно ниже, чем в других производственных процессах. Такое положение, по-видимому, определяется некоторыми особенностями сборочных процессов, которые сводятся к следующим:
1) необходимость высокой точности ориентирования и позиционирования сопрягаемых деталей;
2) многовариантность технологического процесса сборки;
3) необходимость иметь постоянную обратную связь в ходе процесса сборки;
4) высокий уровень манипулирования деталями;
5) необходимость приложения фиксированных усилий в некоторых операциях;
6) необходимость определения базовых поверхностей;
7) большое количество специальных приспособлений и оснастки, применяемых в процессе сборки.
Можно сказать, что роботизация сборочных процессов связана с разработкой достаточно совершенной манипуляционной системы, заменяющей руки человека при осуществлении сложных координированных движений. Однако это обстоятельство не единственное, усложняющее применение роботов в сборочном производстве.
При выполнении сборочных операций робот часто должен делать выбор между запланированной последовательностью действий и последовательностью, обусловленной сложившимися в данный момент условиями сборки. Такие ситуации можно разделить на два класса.
К первому относятся те случаи, когда выбор связан с обнаружением допущенной при сборке ошибки, например взятие другой детали, и исправлением этой ошибки. Второй класс образуют те ситуации, когда выбор последовательности действий связан с координацией и синхронизацией процесса. Так, например, при завершении очередного этапа сборки робот может подать соответствующий сигнал внешним устройствам и продолжать операцию или может ожидать внешний сигнал о дальнейшей работе.
Если при сборке робот выполняет одну определенную последовательность операций, которая может быть прервана при возникновении ошибки или другой непредвиденной ситуации, то такой порядок будет называться фиксированным.
Можно представить себе режим с переменным порядком, когда последовательность операций определяется не только общей технологией сборки, но и сложившейся ситуацией, что позволяет роботу выбрать рациональный или даже оптимальный по выбранным критериям качества вариант. Конечно, при таком режиме работы робота требуется большой объем внешней информации и высокий уровень интеллекта робота. Такой режим позволяет роботу изменить план проведения сборки или перейти к сборке другого узла, если возникла непредвиденная задержка, а не ждать, когда придет оператор.
В стратегическом плане можно выделить два подхода к применению роботов на сборочных операциях.
Первый подход предусматривает строгую дисциплину подготовки производства и высокий уровень его управления. Необходимо обеспечить точную синхронизацию работы всего сборочного участка, своевременную подачу деталей и материалов в строго ориентированном пространственном положении, иначе говоря, предельно высокую организацию окружающей (внешней) среды робота. При соблюдении этих требований возможно и оправдано применение промышленных роботов, т. е. роботов первого поколения или простейших адаптивных роботов, например с тактильными датчиками. Конечно, такие роботы должны отвечать требованиям по точности позиционирования, манипуляционным характеристикам, грузоподъемности и соответствующим параметрам ЗУ.
Следует отметить, что такой подход может потребовать существенной перестройки производства, он возможен и экономически оправдай при изготовлении изделий крупными партиями. Для мелкосерийного и индивидуального производства такой путь вряд ли приемлем, так как расходы на организацию внешней среды могут оказаться весьма значительными.
При втором подходе, когда детали отличаются некоторой нестабильностью размеров и форм и когда нельзя предусмотреть все возможные ситуации, следует применять адаптивные роботы или роботы с искусственным интеллектом, оснащенные системами технического зрения, тактильными и другими датчиками. Это позволяет имитировать аналогичные действия человека-сборщика и принимать решения в зависимости от сложившейся ситуации.
Необходимо отметить, что автоматизация предъявляет к объектам сборки специфические требования по их технологичности: взаимозаменяемость сборочных единиц, которые, в свою очередь, могут быть собраны независимо друг от друга; возможность проведения последовательной сборки, характеризуемой наличием одной или нескольких базовых деталей, с которыми последовательно сопрягаются присоединяемые детали; минимальное число направлений сборки, простота траекторий движений соединения; максимальная свобода доступа сборочного инструмента.
К деталям, предназначенным для автоматической сборки, предъявляют следующие требования: простота конструкции, обеспечивающая удобство складирования и ориентации; наличие на сопрягаемых поверхностях направляющих элементов, облегчающих соединение за счет самоустановки деталей; наличие ярко выраженных базовых поверхностей, размеры которых, а также расположение относительно сопрягаемой поверхности должны быть выдержаны о необходимой точностью; стойкость к повреждениям при воздействии сборочного инструмента и оснастки; унифицированность и стандартность; гарантированное качество.
Тип и конфигурация базовой детали определяют конструкцию сборочного приспособления и схему базирования. Условия собираемости, выбор базовых поверхностей при захватывании и установке присоединяемой детали, а также последовательность сборки зависят от пространственного расположения поверхностей сопряжения. Наиболее подготовлены к автоматической сборке две типовые группы комплектов, которые могут быть разделены в процессе расчленения сложного собираемого объекта на составные части в соответствии со схемой сборки.
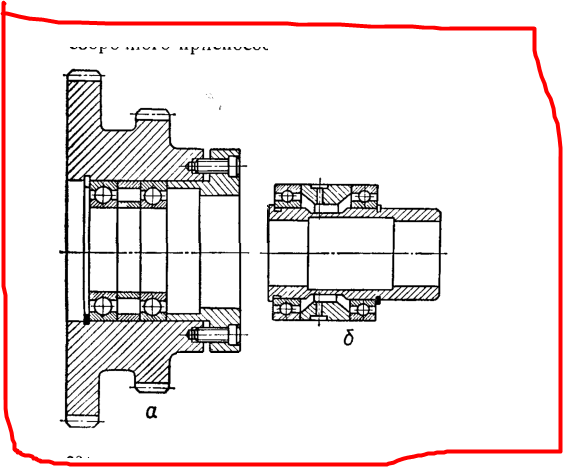
Рис. 5.10. Комплект сборочной единицы: а — с охватывающей базовой деталью; б — с базовой деталью типа «вал»
Одна из таких групп (рис. 5.10, а) представляет собой комплект о охватывающей базовой
деталью, в которую последовательно устанавливаются распорные втулки, уплотнительные манжеты, пружинные кольца и другие детали или предварительно собранные комплекты или изделия, например подшипники качения. В качестве базовых могут служить детали коробчатой формы, фланцы, блоки зубчатых колес и т. п.
Вторая группа комплектов представляет собой сборочную единицу (рис. 5.10, б) с базовой деталью типа вала, втулки, на которую устанавливаются отдельные детали или предварительно собранные комплекты и изделия.
Выделение из изделий типовых комплектов позволяет применить методы групповой технологии и повысить эффективность автоматизации сборки в серийном производстве.
В современном машиностроении наметились тенденции к увеличению удельного веса сборки в общей трудоемкости изготовления изделия и приближения к серийному и мелкосерийному производству. Такое положение требует перехода от специализированного оборудования к легко переналаживаемому автоматическому оборудованию. Один из видов такого оборудования — сборочные роботизированные технологические комплексы, оснащенные промышленными роботами.
Применение промышленных роботов в составе РТК для автоматической сборки изделий предусматривает выполнение роботами основных и вспомогательных операций процесса сборки. К основным относят операции соединения деталей различного типа, нарезание резьбы, завинчивание, зенкование и т. д., к вспомогательным — все операции транспортирования и перемещения деталей в пространстве.
Одна из характерных задач процесса сборки — сопряжение двух детатей типа «вал — втулка». При выполнении этой операции неизбежно возникает необходимость относительного ориентирования этих деталей.
На рис. 5.11 представлена классификация различных способов относительного ориентирования сопрягаемых деталей. В соответствии с этой классификацией все многообразие различных способов сборки можно разделить на две большие группы: 1) сборка при жестком базировании; 2) сборка при плавающем базировании.
К первой группе относится способ с использованием базирующих устройств и способ непосредственного ориентирования детали в захватном устройстве робота.
Способ с использованием базирующих устройств применим в тех случаях, когда гарантированный зазор между валом и отверстием втулки, установленной в базирующем устройстве, удовлетворяет условию
∑δ≥ δ 1 + δ 2 + δ 3 (5.1)
где δ1 — погрешность позиционирования робота; δ2 — погрешность установки втулки в приспособлении; δ3 — погрешность изготовления приспособления.
В теоретическом плане эти положения подробно рассмотрены в гл. 2. Способ ориентирования сопрягаемых деталей при таких условиях наиболее прост и не требует применения специальных мер.
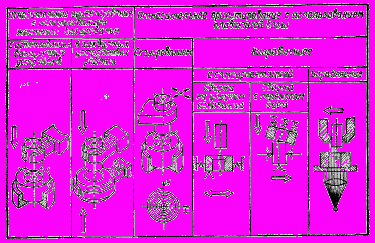
Рис. 5.11. Классификация способов относительного ориентирования сопрягаемых деталей
Однако этот способ предусматривает использование роботов с высокой точностью позиционирования рабочих органов и применим для сборки узлов, имеющих большие зазоры между сопрягаемыми деталями. Заметим, что приведенные соображения относятся не только к деталям типа тел вращения, но и к прямоугольным деталям призматической формы. Очевидно, что в этом случае необходимо учитывать еще одну координату — взаимный угол поворота сопрягаемых деталей, что несколько усложняет задачу.
Способ непосредственного ориентирования деталей применяют в тех случаях, когда условие (5.1) не выполняется, т. е. ошибки позиционирования робота и установки детали превышают суммарный зазор и вероятность правильного сопряжения резко уменьшается. В этих случаях целесообразно использовать соответствующие способы с плавающей базой или специальные технологические приемы.
Специфика условий выполнения с помощью промышленных роботов операций соединения разнообразных по конструкции деталей обусловливает необходимость создания специализированного сборочного инструмента достаточно широкой номенклатуры. Инструменты снабжаются устройствами, обеспечивающими выполнение необходимых для соединения деталей движений: поисковых, силовых, контрольных.
Наибольшее применение находят сборочные инструменты для выполнения типовых операций. К таким инструментам относятся:
— захватные устройства для перемещения и установки деталей без точного их ориентирования, с большими зазорами (для установки базовых деталей в приспособление, укладки прокладок, удаления собранных изделий);
— инструмент для захватывания, перемещения и присоединения деталей с малыми зазорами или небольшими натягами (в том числе инструменты со встроенным механизмом компенсации погрешности взаимного положения сопрягаемых поверхностей);
— инструмент для захватывания, перемещения и установки нежестких деталей (например, резиновых манжет);
— инструмент для захватывания, перемещения и установки упругих деталей, например пружинных колец (в том числе инструменты со встроенным механизмом предварительной деформации);
— инструмент для выполнения резьбовых соединений (в том числе с контролем крутящего момента или других параметров);
— инструмент для установки деталей на вал, включая инструмент со встроенным механизмом дополнительной ориентации присоединяемой детали по базовой;
— инструмент для сборки с пластической деформацией детали (клепки, развальцовки и др.);
— контрольно-измерительные головки различного типа.
Как уже было сказано ранее, важным направлением при роботизации процессов сборки является применение адаптивных роботов.
В качестве примера дадим описание роботизированного технологического сборочного комплекса для сборки неразъемных соединений [41, с. 230].
Как следует из приведенных выше соображений, неразъемные соединения получают различными способами, в том числе за счет клепки.
На рис. 5.12, а представлена схема РТК для сборки узла «рычаг» (рис. 5.12, б), входящего в состав путевого переключателя серии ВК-200, основанного на использовании двух промышленных роботов РС-5 и РО-7.
Собираемый узел состоит из трех деталей — оси, ролика и планки. Два варианта исполнения узла, нестабильность размерных параметров и конфигурации планки, затрудняющая использование традиционных и простых средств автоматического ориентирования, как, например, трафареты, направляющие втулки и т. д., обусловливают целесообразность включения в РТК ориентирующего робота РО-7.
В основе РТК заложена представленная на рис. 5.12, в схема непрерывной сборки деталей с предварительным наклоном осей. Последовательность сборки следующая. Робот РС-5 захватывает по большому диаметру ось, извлекает ее из выходного лотка загрузочно-ориентирующего устройства 2 движением в направление v и перемещает под выходным лотком ориентирующего устройства 3. Вследствие вибрации захватного устройства 4 ролик наживляется, а затем и полностью надевается на ось (см. рис. 5.12, а). При наличии в захватном устройстве двух деталей (оси и ролика), образующих подузел, оно перемещается до остановки под лотком 1.
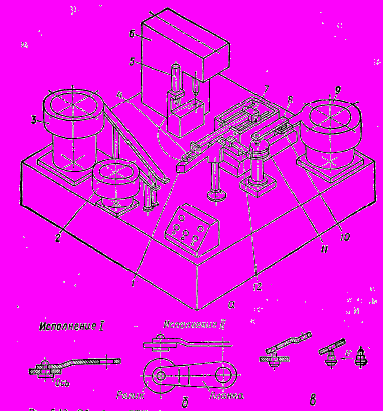
Рис. 5.12, Общий вид РТК (а) для узла «рычаг» (б) и схема его сборки (в)
Если подузел не укомплектован роликом или не произошла под-сборка, встроенный в захватное устройство струйный датчик фиксирует его отсутствие и после временной выдержки выдает команду на сброс несобранных деталей и начало нового цикла сборки.
Укладка в лоток / планки осуществляется роботом 11 (РО-7), рука 8 которого, находясь над выходным лотком ориентирующего устройства 9, захватывает планку, поступившую после первичного ориентирования на позицию распознавания 10, и при необходимости передает ее второй руке 12, находящейся над лотком 1, для до-ориентирования. Если планка расположена на позиции 10 должным образом, рука 8 сразу выгружает ее в лоток 1.
Затем поворотом руки робота 7 планка, которая удерживается в процессе транспортирования на позиции клепки электромагнитом захватного устройства 4, извлекается концом оси из лотка 1.
Укомплектованный узел поворотом промышленного робота устанавливается в рабочей зоне пресса 6 и перехватывается за планку электромагнитом, установленным на конце штока пневмоцилиндра 5; происходит операция клепки. Сброс готового узла осуществляется за счет его собственного веса.
Несмотря на то, что изделие «рычаг» состоит всего из трех деталей и процесс сборки его весьма прост, этот РТК достаточно наглядно иллюстрирует основные характерные особенности сборочных комплексов.