Анализ и обобщение опыта и тенденций создания промышленных роботов в отечественной и зарубежной робототехнике показывает, что все большее распространение получает электромеханический привод промышленных роботов. Впоследние год
Вид материала | Документы |
- Дипломная работа студента, 601.76kb.
- Исать собственные приложения для управления роботами на примере Lego nxt, а также использовать, 76.9kb.
- С применением grid-технологий, 81.79kb.
- История роботов, написанная роботом, 101.24kb.
- Sdfield> Самостоятельная подготовка, 455.42kb.
- Вдокладе описывается технология обучения распределенной системы автономных мобильных, 45.47kb.
- Внушающих уверенность жилищ люди живут в обличии роботов-суррогатов сексуальных, физически, 367.79kb.
- Возможное участие родителей, 108.84kb.
- Анализ работы шмо учителей физики, химии, биологии за 2010-2011 учебный год, 113.58kb.
- Лега В. П. Наука и вера, 152.3kb.
5.5. РТК в сварочном производстве
Особенности процессов сварки с точки зрения применения промышленных роботов. Сварка — технологический процесс, широко применяемый во всех отраслях народного хозяйства для изготовления новых и ремонта эксплуатируемых механизмов, конструкций и оборудования. Преимущества сварных конструкций общепризнаны, их повсеместно применяют взамен литых, клепаных и кованых. Эти преимущества позволяют уменьшить расход металла, снизить затраты труда, упростить конструкцию оборудования и сократить сроки изготовления. Значительно расширяются возможности механизации основных технологических операций, появляются благоприятные перспективы автоматизации.
Разработано и внедрено множество различных видов и способов сварки (рис. 5.13). Сваркой соединяют различные металлы, их сплавы, некоторые керамические материалы, пластмассы и разнородные материалы. Широко применяется сварка металлов и их сплавов при сооружении новых конструкций, ремонте различных изделий, машин и механизмов, создании двухслойных материалов.
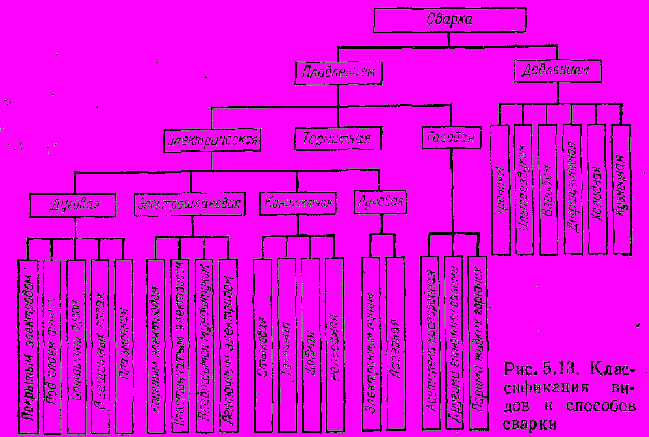
Рис. 5.13. Классификация видов и способов сварки
Сваривать можно металлы любой толщины. Сварку можно выполнять на земле, в космосе и под водой в любых пространственных положениях.
В настоящее время одной из наиболее актуальных является задача разработки, создания и внедрения систем комплексной автоматизации процессов сварочного производства. Значительная роль в решении этой задачи отводится промышленным роботам. На первом этапе выбор видов и способов сварки, где применение промышленных роботов наиболее целесообразно и оправдано, должен проводиться с учетом предварительно сформулированных критериев и оценок. К ним следует отнести: степень распространенности данного вида и способа сварки; невозможность пребывания человека в зоне сварки; гигиеническую оценку работы человека, в том числе и степень утомляемости; наличие вредной радиации, токсических выделений, высокой температуры и т. п.; технико-экономическую эффективность автоматизации; предпосылки создания систем комплексной автоматизации; необходимость выполнения комплекса движений и динамические характеристики (скорость, точность, перемещаемые массы и т. д.); обеспеченность предприятия кадрами специалистов.
Проведение исследования в этом плане вызывает определенные трудности. Некоторые критерии определяются чрезвычайно просто. Примером может служить электронно-лучевая сварка (ЭЛС), которая выполняется в вакууме 0,133...0,013 Па, так что пребывание человека в этих условиях невозможно. Некоторые критерии могут быть определены только соответствующим, иногда довольно сложным расчетом. К таким относятся технико-экономическая эффективность и предпосылки создания систем комплексной автоматизации. Обеспеченность предприятия кадрами специалистов относится к социальным факторам и должна оцениваться соответственно.
Приведенные соображения позволяют в настоящее время приблизительно оценить перспективность применения промышленных роботов для автоматизации процессов сварки. Не исключено, что в ходе развития и решения этой проблемы появятся новые соображения, которые сейчас не попадают в поле зрения. На основании же изложенного можно сделать следующие выводы: 1) применение промышленных роботов целесообразно во всех случаях, когда человек не может находиться в зоне сварки без специального защитного оборудования (электронно-лучевая сварка, сварка взрывом, сварка в космосе и под водой), при этом технико-экономическая эффективность отойдет на второе место; 2) применение промышленных роботов целесообразно для автоматизации контактной точечной, дуговой, дуговой точечной и электронно-лучевой сварки.
Контактная и дуговая точечная сварка могут быть автоматизированы промышленными роботами с позиционными устройствами управления, а дуговая и электронно-лучевая — требуют создания устройств контурного управления. В условиях индивидуального и мелкосерийного производства механизировать и автоматизировать процессы сварки целесообразно с применением групповых технологических процессов.
Узлы и изделия сварочного производства целесообразно предварительно классифицировать по следующим признакам: материал сварной детали; сортамент заготовки; форма сварной детали; ее масса; вид сварки; тип сварного соединения. Следует отметить, что сварные детали, а в целом и сварочное производство имеют ярко выраженный отраслевой характер и поэтому нецелесообразно создавать единый классификатор для всех отраслей.
Весь комплекс операций сварочного производства можно разделить на шесть этапов: заготовительные, сборочные, сварочные, отделочные, вспомогательные (транспортные) и контрольные. Автоматизировать собственно сварочные операции наиболее трудно, остальные операции можно автоматизировать на основании опыта, полученного в других типах производств. В настоящее время наиболее широко применяются промышленные роботы для автоматизации контактной точечной и дуговой сварки.
Контактная точечная сварка. В тех случаях, когда свариваемые детали имеют небольшие размеры и массу, применяют стационарные одноточечные машины. Рабочий вводит деталь между электродами и перемещает ее, осуществляя сварку по заданному контуру. Если же изделие имеет большие размеры и массу, например кузов легкового или кабина грузового автомобиля, сварку выполняют с помощью подвесных сварочных клещей, которые сварщик перемещает по заданному контуру.
При создании роботов для контактной точечной сварки необходимо учитывать требования к сварному соединению, определяемые ГОСТ 15878—79.
Уровень автоматизации процесса контактной точечной сварки весьма высок. Однако суммарное время собственно процесса сварки не превышает 20...30 % продолжительности всего цикла. Все остальное время приходится на вспомогательные операции, связанные с перемещением сварочных клещей (изделия). Из этого следует, что для уменьшения общей продолжительности сварки, т. е. для повышения производительности труда, нужно сосредоточить усилия на автоматизации именно вспомогательных операций.
Уровень механизации и автоматизации вспомогательных операций в условиях мелкосерийного производства очень низок. Как правило, они выполняются вручную, связаны с затратами значительной мускульной энергии и относятся к категории тяжелого физического труда. Качество сварных соединений при ручном перемещении клещей часто не соответствует предъявляемым требованиям.
Вспомогательные движения при контактной точечной сварке (перемещение электрода в пространстве) как объект автоматизации можно охарактеризовать несколькими параметрами. Производительность этого процесса в первую очередь определяется количеством точек, сваренных в единицу времени при заданном качестве сварного соединения. В отличие от других способов, при контактной точечной сварке вспомогательные операции не совмещены во времени с собственно процессом сварки. Можно сказать, что перемещение при этом способе сварки осуществляется по позиционному методу — от точки к точке. Значение и соблюдение всех параметров этого перемещения (скорости, ускорения, траектории движения) желательны, но не обязательны, важен конечный результат.
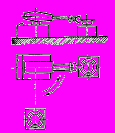
Рис. 5.14. Двухпозиционная компоновка для контактной точечной сварки промышленным роботом
Как известно, успешное применение первых промышленных роботов началось именно с контактной точечной сварки кузовов легковых автомобилей. Для изготовления кузова современного легкового автомобиля нужно сварить 5000...12 ООО точек в зависимости от модели и конструкции кузова. Если в условиях крупносерийного и массового производства эффективно применение многоэлектродных (многоточечных) машин, то в условиях серийного и мелкосерийного производства использование такого специализированного оборудования нецелесообразно. Поэтому сварка кузовов осуществлялась специальными подвесными сварочными клещами вручную. Все попытки автоматизировать эту утомительную и тяжелую операцию успеха не имели и только применение промышленных роботов позволило добиться блестящих результатов. В настоящее время в СССР и за рубежом есть автоматизированные производства с применением промышленных роботов для контактной точечной сварки.
Если деталь имеет небольшие размеры и массу, то обычно промышленный робот берет деталь из накопителя (предварительно ориентированную) и ведет сварку на стационарной сварочной машине, поворачивая и передвигая ее, чтобы получить заданную по программе сварку точек.
Если деталь имеет большие размеры и массу, затрудняющие ее переориентацию в пространстве, то деталь устанавливают в специальном устройстве — позиционере, а робот, оснащенный специальными сварочными клещами, ведет ее сварку по заданной программе. Поскольку замена детали требует некоторого времени, целесообразно создавать двухпозиционную компоновку (рис. 5.14). Замена детали в одной позиции происходит в то время, когда идет сварка в другой.
Сварка кузова легкового или кабины грузового автомобиля представляет собой очень сложный технологический процесс, который невозможно выполнить в одной позиции одним (или двумя) роботами и одним типом сварочных клещей. Необходимы специализация инструмента и разделение всего процесса на серию последовательных этапов. Заметим, что и при ручной сварке применяется конвейер, который перемещает изделие в пространстве, а рабочие выполняют разные, в известной степени специализированные, операции сварки последовательно. Так организованы и роботизированные автоматические линии. Конвейеры применяют пульсирующие, изделие в каждой позиции должно быть зафиксировано в точном положении специальным позиционером, весь процесс сварки кузова делится на отдельные этапы, конечно равные по времени. В каждой позиции устанавливают два робота (слева и справа), а иногда и более (снизу и сверху), применяют специализированные клещи.
Использование непрерывно движущегося конвейера для создания таких линий не исключено, но на сегодняшний день нецелесообразно. Это приведет к необходимости программировать процесс перемещения в движущейся системе координат, что значительно сложнее. Кроме того, при непрерывно движущемся конвейере существенно усложняется обеспечение необходимой точности позиционирования.
Целесообразность создания автоматических роботизированных линий подчеркивается еще и тем, что идеально решается задача транспортирования изделия от одной позиции к другой. Обеспечивается и весьма высокий экономический эффект применения таких линий. На рис. 5.15 показан один из вариантов удачной компоновки автоматической роботизированной линии, когда роботы расположены на разных уровнях, что повышает эффективность их применения и позволяет экономить производственные площади, сокращая длину линии. Создание и применение автоматических линий такого типа отнюдь не исключает применения промышленных роботов для контактной точечной сварки в более простых вариантах для сварки несложных изделий.
Дуговая сварка плавлением — один из наиболее распространенных видов сварки, широко применяемый во всех отраслях народного хозяйства при изготовлении металлоконструкций. Сваркой плавлением можно соединять практически все используемые для изготовления конструкций металлы и сплавы любой толщины.
Дуговая сварка плавлением сложна с точки зрения происходящих в ней процессов и возможности автоматизации. Действительно, при сварке протекают электрические и тепловые процессы, происходят перенос жидкого металла, остывание и кристаллизация металла, могут появляться различные дефекты сварного соединения, имеют место так называемые сварочные (тепловые) деформации. До настоящего времени не разработана адекватная математическая модель этого процесса, что затрудняет создание методов его автоматизации и, в частности, роботизации.
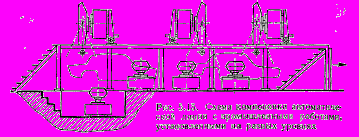
Рис. 5.15. Схема компоновки автоматической линии с промышленными роботами, установленными на разных уровнях
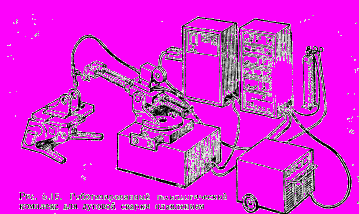
Рис. 6.16. Роботизированный технологический комплекс для дуговой сварки плавлением
Для осуществления дуговой сварки с помощью промышленного робота нужно иметь определенное оборудование, которое и составит роботизированный технологический комплекс в наиболее простом исполнении. На рис. 5.16 показан такой комплекс, причем для лучшего понимания структуры его составные части показаны необъединенными в блоки. Так, источник питания и блок управления процессом сварки, как правило, объединяют в один шкаф. РТК создан на базе серийного манипулятора рабочего органа (горелки) «Универсал-15», устройства управления УКМ-772 и манипулятора изделия, который устанавливает и поворачивает изделие в положение, удобное для сварки.
В последнее время четко обозначилась тенденция создания специального манипулятора изделия с рациональным распределением координат управления между манипулятором рабочего органа и манипулятором изделия.
Разработано несколько вариантов компоновок РТК для дуговой сварки. Самый простой состоит из одного робота и специализированного сварочного приспособления. Такая позиция проста в организации и требует минимальных изменений на предприятии, однако плохо использует рабочее время робота. Избавиться от этого
недостатка можно размещением нескольких однотипных приспособлений в пределах зоны обслуживания робота. В этом случае установка изделия на одной позиции происходит во время сварки изделия на второй. Достаточно перспективно применение поворотных столов различного типа, которые позволяют максимально использовать время работы промышленного робота (рис. 5.17)
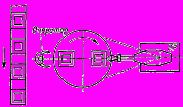
Рис. 5.17. Роботизированный технологический комплекс для дуговой сварки с поворотным столом
Дальнейшим совершенствованием роботизированных технологических комплексов для автоматизации дуговой сварки плавлением будет совмещение рабочих позиций с транспортными устройствами, подающими и убирающими изделие из зоны сварки. В большинстве случаев целесообразно РТК снабжать техническими средствами и программным обеспечением пространственной адаптации, что связано со случайным отклонением линии стыка свариваемых кромок от заданного чертежом положения. В некоторых случаях необходимы также технические средства и программное обеспечение технологической адаптации — корректировка режима сварки для компенсации случайных отклонений параметров свариваемого соединения (сечения разделки, зазора, превышения кромок и т. д.) от расчетных значений.
5.6. РТК в литейном производстве
Процессы литейного производства сопряжены с перемещением больших масс (ковша и металла), температура расплавленного металла очень высока, труд рабочего весьма утомителен и однообразен, уровень механизации и автоматизации, особенно в условиях мелкосерийного и серийного производства, весьма низок. Все это, естественно, привлекает внимание специалистов в области роботостроения и требует конструктивного решения.
За последние годы выпуск литья под давлением возрос в 10 раз. Среднегодовой прирост производства литья под давлением в 1,5... 2 раза опережает прирост всей промышленной продукции. Перспективы развития этого литья требуют создания комплексно-механизированных и автоматизированных установок на базе машин литья под давлением. Все это обусловило целесообразность создания роботизированных технологических комплексов в составе: машины литья под давлением (кокильной машины); промышленного робота для заливки металла; манипулятора для обдувки и смазки пресс-форм и пресспоршня и промышленного робота для съема отливок.
Автоматизация процессов литейного производства на основе использования промышленных роботов — качественно новый этап автоматизации этого производства. Роботизированные технологические комплексы в литейном производстве впервые были созданы для литья под давлением. Это объясняется тем, что рабочие, обслуживающие машины литья под давлением, кроме управления машиной выполняют несколько трудных ручных, так называемых внемашинных, операций — заливку металла, обдувку и смазку пресс-форм, установку отливки в пресс. Производительность машин литья под давлением очень велика — примерно 120 заливок/ч. В то же время утомляемость рабочего ведет к нарушению технологического режима, ухудшению качества литья, снижению производительности оборудования.
Технологический процесс литья в хокили очень похож на процесс литья под давлением. Он также включает заливку металла вручную, съем и передачу изделия для очистки и обрубки. В настоящее время ведутся работы по роботизации этих процессов.
В литейном производстве широко применяют машины с холодной камерой прессования. Жидкий металл в такие машины заливают вручную. Работы по механизации и автоматизации этих процессов ведутся давно, однако полностью были автоматизированы лишь машины, на которых отливали сравнительно легкие детали с массой до нескольких десятков граммов. Более крупные машины переоборудованы для полуавтоматической работы с сохранением ручных операций. Задача заключается в том, чтобы роботизировать и этот тип машин, перейти на автоматический цикл.
Конструктивное выполнение машин для литья под давлением g точки зрения расположения и характера зоны заливки металла и съема отливки довольно однотипно, что позволяет находить общие решения для их стыковки с манипуляторами и промышленными роботами. К заливочным манипуляторам и промышленным роботам предъявляются следующие требования:
1) доза не должна зависеть от изменения уровня металла в печи;
2) металл должен заливаться непосредственно в заливочное окно, без применения длинных желобов и чаш;
3) в камеру прессования металл должен заливаться без значительных переналадок при переходе от центрального к нижнему литью;
4) в ковш металл должен набираться чистым, без шлаковых пленок;
5) механизмы манипулятора должны быть надежно защищены от брызг расплавленного металла.
Уже накоплен некоторый опыт по созданию и применению манипуляторов и промышленных роботов для автоматизации процессов литья, выработаны типовые компоновки. На рис. 5.18 показана одна из типовых компоновок РТК для литья. Комплекс состоит из! манипулятора / для смазки пресс-форм; электропечи 2 (САГ-0,25-Х); манипулятора 3 (А97.40) для заливки металла; шкафа 4 с электрооборудованием; пульта управления 5; промышленного робота 6 (А97.20); блокировочной площадки 7; установки 8 для охлаждения; пресса 9 и машины 10 (71111) для литья под давлением. Отдельные агрегаты связаны общим устройством управления. Элементы автоматики и органы управления размещены в общем для комплекса электрошкафу и центральном пульте управления. Промышленный робот имеет пять управляемых координат и движение зажима.
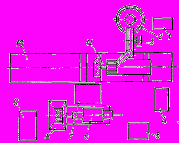
Рис. 5.18. Типовая компоновка РТК с машиной литья под давлением А97
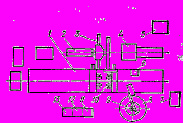
Рис. 5.19. Типовая компоновка автоматической линии для литья под давлением
Типовая компоновка автоматической линии для литья изделий 10 под давлением на базе пресса 711Б08 приведена на рис. 5.19. В состав линии входят: манипулятор 9 (ЛМ-35) для заливки металла; механизм 6 обдува и смазки пресс-форм и пресс-плунжера; пресс 4 (П-16) для обрубки облоя; бак 2 охлаждения; электропечь 8 (САГ-0,16); машина 1 (711Б08) для литья под давлением; манипулятор 3 (РМ-2); насосная установка 5; электрошкафы 7, 11, 12, 13.
Создание роботизированных технологических комплексов и роботизированных линий для автоматизации различных технологических процессов — важный этап в создании роботизированных участков, цехов и заводов.
Можно с уверенностью утверждать, что этот путь приведет к созданию гибких автоматизированных производств (ГАП), способных обеспечить высокую экономическую эффективность в условиях мелкосерийного и серийного производства.
5.7. Роботизированные технологические линии
Промышленные роботы достаточно широко применяются в автоматических линиях. Прежде всего это относится к контактной точечной сварке кузовов легковых автомобилей и кабин грузовых машин, но постепенно распространяется и на процессы гальваностегии, окраски и сборки.
Первая автоматическая линия промышленных роботов (1970 г.) была создана для сварки кузовов легкового автомобиля «Вега» на одном из заводов фирмы «Дженерал моторе» в г. Лордстауне (США). В составе линии 26 роботов «Юнимейт», которые выполняют контактную точечную сварку кузова автомобиля, перемещающегося на пульсирующем конвейере. Каждый робот имеет индивидуальное управление и может сваривать по нескольким программам. Выбирается программа по специальному магнитному маркеру на подходящем очередном кузове. Такая система позволяет пустить по конвейеру несколько моделей кузовов. Перед сваркой кузов фиксируется в строго определенном положении. По данным фирмы, роботы работают более чем 2 смены в день, заменяя около 50 чел. и окупая себя в течение 18 мес. Точность постановки сварных точек ±1,5 мм, производительность сварки около 60 точек/мин.
В 1970—1971 гг. западногерманская фирма КУКА спроектировала, изготовила и установила на заводе «Даймлер-Бенц» в г. Штутгарте автоматическую линию промышленных роботов для контактной точечной сварки боковин легкового автомобиля «Мерседес». Эта линия состоит из двух параллельных потоков для сварки правой и левой боковин и включает в себя 12 роботов фирмы «Юнимейшн», закупленных в США. Отличительная особенность этой линии — сочетание пульсирующего конвейера со специальными кантователями, поворачивающими и фиксирующими боковину в вертикальном положении, наиболее удобном для сварки.
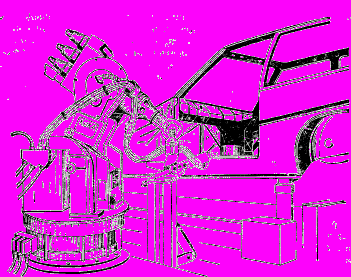
Рис. 5.20. Участок роботизированной технологической линии на Запорожском автомобильном заводе
Так была решена задача точного позиционирования изделия перед сваркой. Весь технологический процесс сварки боковин разбит на шесть участков, причем на каждом из них сваривается несколько десятков точек с темпом 15...20 точек/мин частично специализированными клещами.
В 1988 г. на Запорожском автомобильном заводе (ЗАЗ) пущены в эксплуатацию несколько роботизированных технологических линий в кузовном производстве (рис. 5.20). Эти линии созданы совместно с фирмой «Комау».
Научно-исследовательский, конструкторско-технологический и проектный институт робототехники Минавтопрома (г. Киев) совместно со специалистами ПО АвтоКРАЗ разработал и внедрил три роботизированных технологических комплекса для контактной точечной сварки типа РТК-1, оснащенных промышленными роботами ПР-601/60 производства ПО АвтоВАЗ, для доварки кабины грузового автомобиля КРАЗ (рис. 5.21). РТК обеспечивает сварку 700 точек в цикле длительностью 14 мин, т. е. работает с производительностью приблизительно 50 точек/мин.
Одно из необходимых условий создания роботизированной линии — пульсирующий конвейер. Возможность создания роботизированной линии на базе непрерывно движущегося конвейера не исключена, но тогда необходимо обеспечить работу робота в движущейся системе координат, что создает дополнительные и серьезные трудности при программировании и вряд ли оправдано.
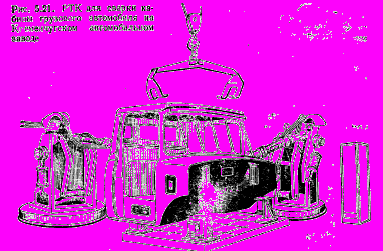
Рис. 5.21. РТК для сварки кабины грузового автомобиля на Кременчугском автомобильном заводе
Второе необходимое условие создания роботизированной линии с пульсирующим конвейером — обеспечение необходимой, заданной точности позиционирования изделия в момент остановки конвейера. Как правило, это требование удовлетворяется применением специальных устройств, именуемых позиционерами.
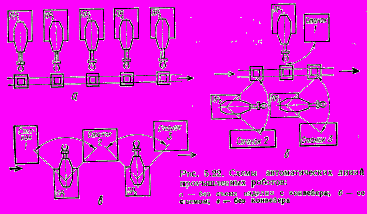
Рис. 5.22. Схемы автоматических линий промышленных роботов:
а — без съеме изделия с конвейера; б — со съемом; в — без конвейера
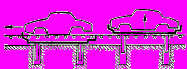
Рис. 5.23. Схема устройства позиционера
Создание и применение роботизированных линий — важнейшее направление робототехники, открывающее большие перспективы в производственном и экономическом отношениях.
Автоматические роботизированные линии можно разделить на три группы, или три типовые схемы.
1. Роботизированную линию, состоящую из пульсирующего конвейера и последовательно расположенных возле него роботов, каждый из которых выполняет свою технологическую операцию (рис. 5.22, а). Особенность этой схемы состоит в том, что изделие с конвейера не снимается. Такая схема широко применяется при контактной точечной сварке кузовов легковых автомобилей и кабин грузовых машин.
2. Роботизированную линию, состоящую из пульсирующего конвейера, последовательно расположенных роботов и технологического оборудования (рис. 5.22, б). При этой компоновке изделие с конвейера снимается роботом и переносится на технологическое оборудование. Такая компоновка, требующая очень четких и согласованных действий конвейера, роботов и технологического оборудования, применяется в металлообработке.
3. Роботизированную линию, не имеющую конвейера, которая состоит из последовательно расположенного технологического оборудования и промышленных роботов (рис. 5.22, в). Такая схема близка к схеме роботизированного технологического комплекса (особенно при малом количестве технологического оборудования) и может применяться в различных процессах машиностроительной промышленности.
В тех случаях, когда нужно обеспечить весьма точную установку изделия, а конвейер не соответствует этим требованиям, применяют специальные позиционеры. Принцип работы позиционера заключается в том, что изделие снимается и приподнимается над конвейером в специальном приспособлении, которое, поддерживая изделие на базовых поверхностях, обеспечивает его ориентирование о высокой степенью точности (рис 5.23). Высота подъема изделия невелика, конструкция конвейера может быть создана с использованием электромеханических или гидравлических приводов.
5.8. Испытания промышленных роботов
В нашей стране создано много промышленных роботов различного типа. Серийное производство их и широкое внедрение на различных предприятиях требуют унификации методов приемки, испытаний и экспериментальных исследований. В связи с этим в ЭНИИМСе Минстанкопрома совместно с Государственным научно-исследовательским институтом машиноведения разработана методика испытания промышленных роботов. Эта методика должна служить основой при разработке программ и методик испытаний конкретных моделей промышленных роботов с учетом их конструктивных особенностей. Она должна использоваться и при составлении разделов «Правила приемки», «Методы контроля» технических условий на опытные и серийные образцы промышленных роботов.
Промышленным роботам, как новому классу машин, присущи особенности, которые значительно отличают их от традиционных средств автоматизации производственных процессов. Основные особенности и требования к контролю следующие:
1. Возможность быстрой переналадки последовательности, скорости и содержания манипуляционных действий при перемещении предметов. Вследствие этого необходимо проверять: время перепрограммирования; время смены ЗУ; усилие захватывания; чистоту поверхности детали после ее зажима в ЗУ.
2. Во1можность выполнения основных технологических операций производственного процесса, операций «взять — перенести — положить» (вспомогательные, транспортные) или тех и других. Следовательно, нужно проверять погрешность позиционирования, технологические и другие характеристики.
3. Сложность исполнительных устройств, представляющих собой пространственные механизмы со многими степенями подвижности и незамкнутой кинематической цепью, небольшая жесткость исполнительных устройств в сравнении с обслуживаемым оборудованием и напряженные динамические режимы работы (скорости до 1,5 м/с при относительно небольших перемещениях, интенсивные разгоны и торможения). Соответственно этому особенно требовательно нужно проверять и исследовать динамические свойства манипуляторов, в том числе влияние на функциональные возможности промышленных роботов вибраций и колебаний исполнительных органов. Целесообразно определять оптимальные, по выбранным критериям, соотношения между грузоподъемностью, точностью позиционирования и скоростью перемещения рабочих органов.
4. Возможность одновременной отработки движений по нескольким степеням подвижности, в том числе при перемещении предметов по заданной пространственной траектории. Такая особенность требует проверять параметры промышленных роботов при одновременном выполнении движений по нескольким координатам, в том числе погрешности отработки криволинейной пространственной траектории.
5. Промышленный робот — источник повышенной опасности. В силу этого необходимо весьма жестко проверять все блокировки устройства, обеспечивающие безопасную и безаварийную работу и проведение испытаний.
Виды испытаний. Промышленные роботы подвергаются испытаниям, регламентированным ГОСТ 26053—84 «Роботы промышленные. Правила приемки. Методы испытаний». Устанавливаются следующие виды испытаний:
— для опытных образцов (опытных партий) — приемочные, предварительные (по ГОСТ 15.001—88);
— для установочной серии (первой промышленной партии) — квалификационные (по ГОСТ 15.001—88);
— для ПР серийного производства — приемосдаточные, периодические, типовые.
Объем и содержание основных контрольных испытаний ПР приведены в табл. 5.1.
Таблица 5.1. Объем и содержание основных контрольных испытаний ПР (по ГОСТ 26053—84)
Наименование этапа испытаний | Номенклатура осуществляемых проверок и проверяемые параметры | Виды испытаний | ||
Приемоч-ные | Приемо-стандарт-ные | Перио-дические | ||
Подготовка к проведению испытаний | Условия проведения испытании | + | + | + |
Наличие необходимых средств измерений, проверка правильности их подсоединения | + | + | + | |
Проверка технологической документации | Комплектность технической документации | + | х | х |
Проверка ПР в исходном состоянии | Комплектность образца | + | + | + |
Габаритные размеры ПР | + | + | - | |
Масса ПР | + | + | - | |
Точность изготовления ПР, обработка основных деталей | + | + | + | |
Качество сборочно-монтажных работ | + | + | + | |
Отделка образца | + | + | + | |
Сопротивление изоляции | + | + | + | |
Сопротивление заземления | + | + | + | |
Электрическая прочность изоляции | + | + | + | |
Правильность подключения к электро-, гидро- и пневмосетн | + | + | + | |
Проверка системы смазки | + | + | + | |
Испытания на холостом ходу | Возможность перемещений по степеням подвижности | + | + | + |
Действие механизмов, обеспечивающих безопасную и безаварийную работу | + | + | + | |
Проверка возможности работы во всех режимах, обеспечиваемых системой управления | + | + | + | |
Число программируемых точек | + | - | + | |
Максимальные перемещения | + | + | + | |
Испытания под нагрузкой | Номинальная грузоподъемность | + | + | + |
Усилие захватывания | + | - | - | |
Время перемещения по степеням Подвижности | + | + | + | |
Время захватывания, время опускания | + | + | + | |
Максимальные скорости | + | - | + | |
Максимальные ускорения | + | - | + | |
Максимальная абсолютная погрешность позиционирования: по степеням подвижности; | + | + | + | |
всего ПР | + | + | + | |
Погрешность отработки траектории | + | + | + | |
Уровень радиопомех | + | - | + | |
Уровень шума | + | - | + | |
Испытания на безотказность | + | х | + | |
Проверка правильности выполнения технологических операций | + | + | + | |
Нагрев подшипников | + | о | - | |
Давление рабочего тела | + | - | - | |
Нагрев рабочей жидкости | + | х | - | |
Герметичность гидро- и пневмо-системы | + | + | + | |
Составление заключения по результатам испытания | | + | + | + |
Примечание «+» — испытание проводят в полном объеме; «X» — испытание каждого ПР проводят в ограниченном объеме, согласно программам и методикам испытаний конкретных ПР; «О» — испытание проводят выборочно, согласно программам и методикам испытаний конкретных ПР; «—»— испытание не проводят.
По месту и условиям проведения различают лабораторные, стендовые, полигонные (испытания на опытных роботизированных участках) и эксплуатационные испытания; по продолжительности проведения и объему — расширенные, нормальные, ускоренные (форсированные и сокращенные). Промышленные роботы могут подвергаться сравнительным испытаниям — испытаниям аналогичных или одинаковых образцов, проводимым в идентичных условиях для сравнения их параметров и характеристик.
В зависимости от поставленной цели испытания промышленных роботов могут быть контрольными или исследовательскими. Контрольные испытания проводят для проверки качества промышленного робота, исследовательские — для экспериментального изучения различных свойств.
Объем контрольных испытаний должен быть минимальным, но достаточным для оценки качества испытываемых образцов. Испытания проводят при наиболее неблагоприятном сочетании проверяемых параметров (максимальные скорости и вылеты исполнительных устройств, максимальная грузоподъемность и т. д.) и, как правило, с использованием простейших измерительных средств.
Объем исследовательских испытаний обычно определяется задачами, для решения которых эти испытания проводят. Они предусматривают более детальное исследование основных параметров и технических характеристик для уточнения паспортных данных ПР, установления оптимальных соотношений между ними и разработки рекомендаций по совершенствованию конструкций. Исследовательские испытания выполняют с помощью различных измерительных средств, включая измерительные преобразователи и регистрирующую аппаратуру, а также измерительные системы и комплексы.
Контрольные испытания. Все параметры, проверяемые в процессе контрольных испытаний, можно разделить на шесть групп! 1) параметры назначения и применения; 2) основные параметры и размеры; 3) параметры безопасной и безаварийной работы; 4) эксплуатационные параметры; 5) параметры надежности; 6) технологические параметры.
Программа контрольных испытаний ПР в общем случае включает в себя следующие основные этапы: 1) проверку подготовки к проведению испытаний; 2) проверку технической документации; 3) испытания промышленных роботов в трех состояниях — а) при неподвижных механизмах и отсутствии нагрузки на выходных элементах; б) при движении механизмов и отсутствии нагрузки на выходных элементах; в) при движении механизмов и наличии нагрузки на выходных элементах.
В настоящее время значительную часть промышленных роботов выпускают в составе роботизированных комплексов, что существенно ускоряет и облегчает внедрение ПР в производство. Общие требования к испытаниям роботизированных комплексов аналогичны требованиям к испытаниям промышленных роботов. Как правило, в состав роботизированного комплекса входят оборудование и промышленные роботы, выпускаемые серийно или рекомендованные к серийному производству. Поэтому испытания комплекса должны включать в себя проверку тех параметров, которые характеризуют свойства комплекса в целом, несерийного вспомогательного оборудования, входящего в состав комплекса, устройств технологического оборудования, модернизированных при создании комплекса.
К основным параметрам, характеризующим свойства роботизированного комплекса, относятся: количество единиц обслуживаемого оборудования, в том числе основного технологического; выполняемые операции, производительность; время загрузки-разгрузки, не перекрываемое временем работы основного оборудования; максимальные и минимальные характерные размеры обрабатываемых изделий; время переналадки; коэффициент технического использования; занимаемая площадь; масса составных частей.
Перечень параметров, которые характеризуют несерийное вспомогательное оборудование, входящее в роботизированный комплекс, и модернизированные устройства технологического оборудования, зависит от состава входящего в комплекс оборудования и объема работ по модернизации.
Исследовательские испытания. Программа исследовательских испытаний включает следующее: подготовку опытного образца к испытаниям; статические испытания; сокращенные и расширенные динамические испытания; испытания на надежность.
Статические испытания предусматривают определение жесткости исполнительных органов и несущих систем, люфтов и зазоров в кинематических цепях механизмов.
Динамические испытания наиболее трудоемки и предусматривают определение наибольшего числа характеристик и параметров по сравнению с другими видами испытаний. В зависимости от объема проводимых исследований и их сложности динамические испытания подразделяют на сокращенные и расширенные. К числу параметров, определяемых в процессе динамических испытаний, относятся: быстродействие, быстроходность; грузоподъемность; погрешность позиционирования; погрешность отработки траектории; нагрузки на детали механизмов и привода; ходы исполнительного органа; зона обслуживания; воспроизводимость заданного закона движения; вибрационные характеристики и уровни шума; температурные поля и деформации; расход энергии, сжатого воздуха, охлаждающей и рабочей жидкости; ресурс и другие характеристики надежности.
Испытания на надежность промышленных роботов проводятся для определения фактических значений показателей надежности. Программа и методика этих испытаний должны разрабатываться на основе ГОСТ 27.410—87 «Надежность в технике. Методы контроля показателей надежности и планы контрольных испытаний на надежность».
Основные разделы испытаний:
1) входной контроль; приводятся перечни нормируемых показателей, деталей и соединений для контроля износа и определения ресурса;
2) испытание на безотказность; приводятся критерии отказов, порядок их регистрации и анализа, методы обработки данных по отказам;
3) испытание на ремонтопригодность с указанием перечня узлов и деталей, по которым необходимо провести разборочно-сборочные работы и операции технического обслуживания для оценки ремонтопригодности;
4) ресурсные испытания с указанием количества и периодичности измерений остальных параметров, износа деталей и соединений; методы определения характера и распределения износа;
5) календарный план испытаний;
6) перечень средств испытаний.
Проведение соответствующих испытаний промышленных роботов и роботизированных комплексов позволяет определить их параметры, качество и эксплуатационные характеристики и, как следствие, область применения.