Филиппов Иван Иванович, к т. н., профессор учебно-методический комплекс
Вид материала | Учебно-методический комплекс |
- Корниенко Сергей Иванович, доктор исторических наук, профессор кафедры новейшей истории, 248.33kb.
- Алексунин Владимир Алексеевич, профессор, к э. н., профессор кафедры маркетинга и рекламы, 1296.15kb.
- Автор Баташов Сергей Иванович (Ф. И. О) учебно-методический комплекс, 414.78kb.
- Климов Иван Андреевич, доктор философских наук, профессор учебно-методический комплекс, 2577.41kb.
- Слонов Людин Хачимович Доктор биологических наук, профессор, профессор кафедры ботаники, 823.83kb.
- Литвинюк Александр Александрович д э. н., профессор должность профессор учебно-методический, 654.29kb.
- Панкратов Леонид Васильевич Д. т н., профессор учебно-методический комплекс, 948.73kb.
- Шевчук Иван Викторович, преподаватель учебно-методический комплекс, 654.01kb.
- Чиркун Сергей Иванович учебно-методический комплекс, 257.6kb.
- Парамонова Татьяна Николаевна д э. н., профессор Красюк Ирина Николаевна к э. н., доцент,, 1704.02kb.
ПОГРУЗКА ГРУНТА И ПОДЗЕМНЫЙ ТРАНСПОРТ
3.1. Погрузка грунта
Освобождение забоя выработки от взорванного грунта – одна из наиболее трудоемких операций, занимающая до 40% времени проходческого цикла. Эта операция состоит из погрузки грунта в транспортные средства и его перемещения к месту отвала.
Главным направлением механизации погрузочных работ в забоях подземных выработок является применение погрузочных машин, обеспечивающих надежную уборку грунта и при большой крупности кусков. Выбор типа погрузочной машины определяется размерами проходимой выработки, видом имеющейся энергии, требуемой производительностью погрузки и крупностью кусков взорванного грунта.
Погрузочные машины. При строительстве тоннелей применяют погрузочные машины периодического и непрерывного действия на колесном или гусеничном ходу. Машины периодического действия делят на две группы: с погрузкой непосредственно в вагонетку и погрузкой на транспортер машины.
Машины первой группы (например, ППН-2, рис. 3.26) имеют ковш 1, вращающийся в вертикальной плоскости и перебрасывающий грунт через корпус 2 машины в вагонетку. Для захвата грунта машина с опущенным ковшом и прицепленной сзади вагонеткой двигается к забою, внедряет ковш в грунт и одновременно его встряхивает. После наполнения ковша он опоражнивается в вагонетку при заднем ходе машины. Корпус машины смонтирован на поворотном круге, вследствие чего ковш может отклоняться в обе стороны от оси пути на 300 с увеличением фронта погрузки. Машина обладает небольшим сцепным весом и при погрузке грунта большой крупности часто буксует, что снижает ее производительность. Кроме того, она имеет узкий фронт погрузки, вынуждающий прибегать к ручной подкидке грунта в полосу действия машины. Неравномерность загрузки по длине ограничивает рациональный объем вагонеток вместимостью 1,2-1,3 м3.
Машины второй группы (например, ППН-5, рис. 3.27) состоят из корпуса 1 с продольным транспортером 2 и черпачного устройства со стрелой 3, отклоняющейся от продольной оси в обе стороны на 500. Разгрузочная часть транспортера может подниматься и опускаться от среднего положения на 500 мм, а сам транспортер поворачивается в плане на угол 12,50. Машина с прицепленной вагонеткой и опущенным ковшом 4 продвигается вперед, врезаясь в грунт. Заполненный ковш поднимается вверх и толчком опорожняется в желоб, откуда грунт поступает на ленточный транспортер шириной 600 мм, движущийся со скоростью 0,8 м/с. Наличие стрелы обеспечивает возможность взятия грунта на 175 мм ниже уровня откаточных путей, а поворот транспортера в плане – возможность погрузки на промежуточный продольный транспортер, расположенный сбоку от пути, по которому двигается машина.
Машина ППН-6 (рис. 3.28) отличается тем, что имеет ковшовое устройство 1 без стрелы, при повороте передней части корпуса 2 отклоняющееся от оси пути на 340 в обе стороны и опорожняемое на транспортер 3. Машина ППН-6 является самой мощной и производительной из отечественных машин периодического действия, имеет большую массу и обеспечивает хорошее внедрение в грунт значительной крупности.
В машинах ППН-5 и ППН-6 имеется выдвижная сцепка (см. рис. 3.27, 3.28), допускающая перемещение длинной вагонетки для ее равномерной загрузки (три положения под консольной частью машины). Поворот ковша в горизонтальной плоскости производится механически (так же как в ППН-2), в то время как в ППН-2 он осуществляется вручную.
Недостаток машин с погрузкой на ленточный транспортер – быстрый износ ленты транспортера при твердых скальных грунтах.
В настоящее время создан ряд конструкций машин непрерывного действия с нагребающими устройствами. Так, в ФРГ разработана машина, сгребающая грунт сверху вниз на скребковый транспортер, осуществляющий погрузку в вагонетки.
Более рационален боковой захват грунта с помощью нагбрегающих лап, расположенных на забирающей части машины, выполненной в виде наклонной стальной плиты с желобом посередине. Такие машины обычно перемещаются на гусеничном ходу и обладают хорошей маневренностью, позволяющей обслуживать выработки большой ширины. К ним относится машина ПНБ-3К(рис.3.29), обеспечивающая непрерывную погрузку разрыхленного взрывом грунта крупностью до 600 мм в транспортные средства с высотой погрузки до 3м. Машина имеет забирающую часть 1 шириной 2 м, наклоненную под углом 300 к подошве выработки, которая может опускаться ниже уровня гусениц 4 на 30 см и подниматься на 40 см. На плите забирающей части смонтированы ведущие диски 2 с нагребающими лапами, совершающими колебательные движения, в результате которых грунт направляется на желоб скребкового транспортера шириной 725 мм. Стрела 3 транспортера может поворачиваться в плане в обе стороны на 450 от оси машины, что облегчает погрузку грунта в транспортные средства.
Машина оснащена оросительной установкой с плоскоструйными форсунками, расходующими 40-50 л воды (под давлением не менее 0,5 МПа) на 1 м3 погруженного грунта.
Более удобна и производительна последняя модификация машины марки ПНБ-ЗД с забирающей частью шириной 2,5 м. В табл. 1.1 приведены основные характеристики современных погрузочных машин.
Выбор погрузочной машины определяется принятой схемой организации работ. При рельсовом транспорте наиболее целесообразны машины (ППН-5, ППН-6) с погрузкой на транспортер, обеспечивающие равномерную загрузку вагонеток большой вместимости с ковшом, позволяющим грузить крупные куски грунта.
Машины с непосредственной погрузкой в вагонетки находят применение лишь при проходки узких опережающих выработок. При безрельсовом транспорте рекомендуются погрузочные машины на гусеничном ходу, к котором относятся машины ПНБ-3 и тоннельные экскаваторы.
Тоннельные экскаваторы. В выработках большого поперечного сечения для погрузки грунта можно применять полноповоротные одноковшовые экскаваторы на гусеничном ходу. Габариты и конструкция тоннельных экскаваторов приспособлены для работы в подземных условиях.
Преимуществом экскаваторов перед погрузочными машинами является большой объем ковша (0,75-1,0 м3), перемещение на гусеничном ходу по неровной подошве выработки и возможность погрузки без перерыва на два пути, расположенных сбоку и сзади экскаватора. Большой объем ковша позволяет грузить крупные глыбы грунта, в связи с чем можно применять глубокие шпуры большого диаметра, что приводит к сокращению общей длины шпуров и расхода ВВ. Особенно целесообразно применение экскаваторов с погрузкой в автомобили-самосвалы, полностью исключающей необходимость в рельсовых путях.
Таблица 1.1
Характеристика | ППН-2 (ПМЛ-5) | ППН-5 (ППМ-4) | ППН-6 (МПР-6) | ПНБ-3К | ПНБ-3Д |
Вместимость ковша, м3 | 0,32 | 0,32 | 0,5 | ___ | ___ |
Число черпаний в 1 мин | 2-3 | 4-5 | 4 | | |
Фронт погрузки, м | 2,6 | 4,0 | 5,0 | Не ограничен | |
Максимальная крупность кусков грунта (при их содержании не более 10%, мм) | 400 | 400 | 600 | 600 | 600 |
Ширина колеи, мм | 600 | 750 | 900 | На гусеничном ходу | |
Техническая производительность, м3/мин | 0,8 | 1,25 | 1,6 | 3,0 | 3,5 |
Примером специального тоннельного экскаватора является экскаватор Э-7515 (рис. 3.30) с вместимостью ковша 0,75 м3 для погрузки кусков грунта крупностью до 650 мм при проходке выработок сечением более 40 м2 и шириной не менее 5,5 и делающий два черпания в 1 мин.
В выработках высотой не менее 6 м и шириной не менее 10 м можно применять экскаватор ЭП-1 с вместимостью ковша 1 м3 для погрузки кусков скальных грунтов крупностью до 900 мм на подземных работах в горной промышленности и делающий три черпания в 1 мин.
Производительность погрузки. Фактическая производительность погрузочной машины зависит от ее конструктивных характеристик и условий применения и в первую очередь от четкости организации работ. Производительность погрузочных машин выражают в метрах в кубе на час, при этом имеют в виду объем грунта в массиве, т.е. в ненарушенном состоянии. Производительность Р погрузочной машины определяют по формуле
Р=

Где - коэффициент использования машины с учетом времени на подготовку ее к работе, осмотр забоя, простои и задержки (=0,80 ÷ 0,85); кр – коэффициент разрыхления грунта, изменяющийся от 1,1 (мелкий песок) до 2,2 (весьма крепкие скальные грунты); t, t1, t2 – продолжительность соответственно рабочего цикла машины, замены груженой вагонетки порожней и груженного состава из n вагонеток порожнем, мин; V1 и V2 – вместимость соответственно вагонетки и ковша машины, м3; 1 и 2 – коэффициенты заполнения вагонетки (1 =0,9 ÷ 1,0) и ковша машины (для ковшей вместимостью 0,32 м3 и более 2=0,8÷0,9)
Приводимая обычно в каталогах техническая производительность Рт погрузки соответствует идеальным условиям (непрерывная переброска в отвал неразрыхляющегося материала при полном заполнении объема V2 ковша). Эта производительность может быть определена по формуле, являющейся частным случаем формулы (3.1),

производительность машины ПНБ-3Д также меньше технической (Рт=210 м3/ч) и зависит от продолжительности ее рабочего цикла, слагающегося из чистого времени погрузки по ширине забирающего устройства (t1) и времени перемещения машины в новую позицию со скоростью около 10 м/мин (t2). За время цикла (t1+ t2) машина может погрузить объем
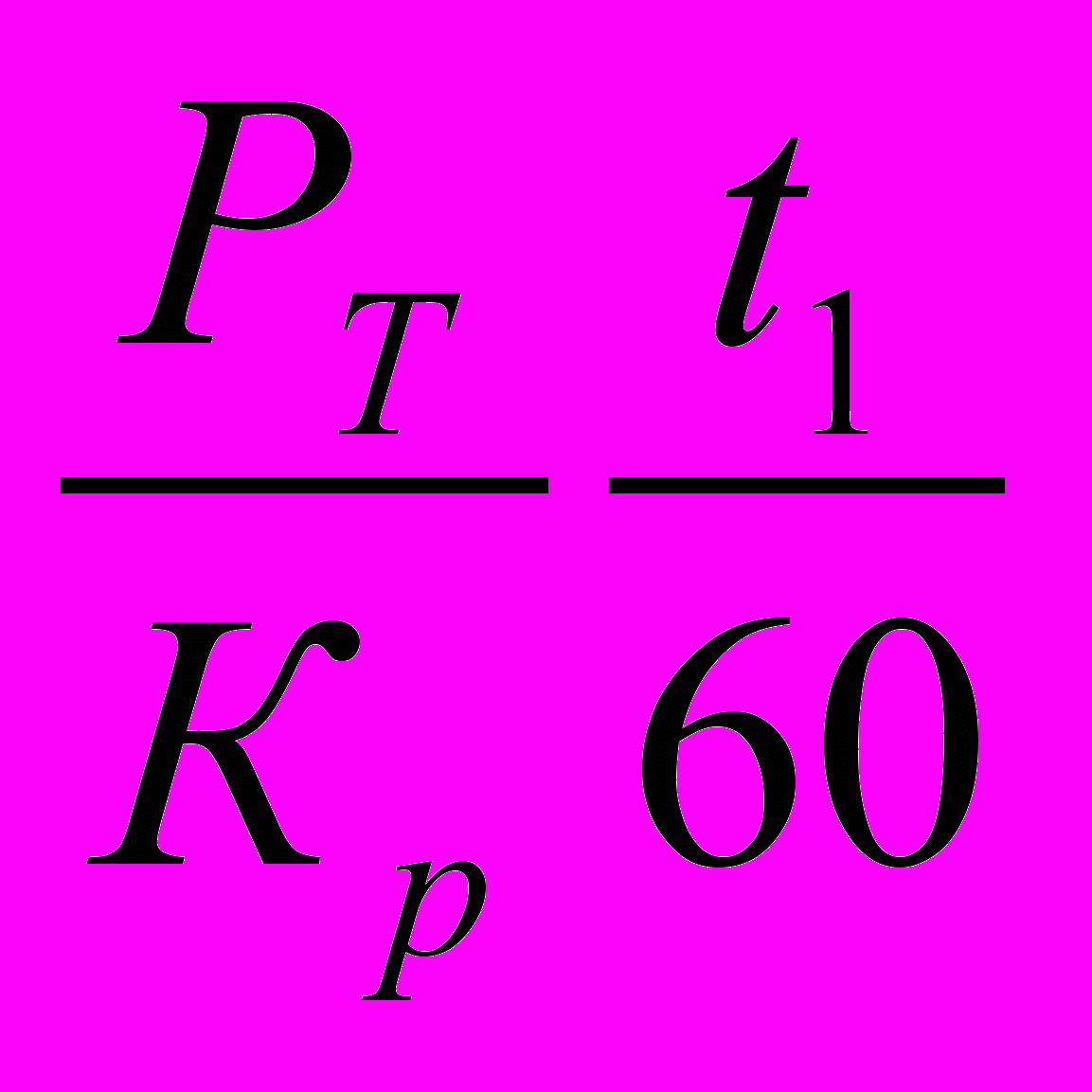

уменьшение времени, расходуемого на смену вагонеток, может быть достигнуто применением рациональных маневровых устройств у забоя выработки и использованием вагонеток-бункеров большой вместимости, снабженных транспортерами-питателями. В этом случае погрузку осуществляют в вагонетку-бункер непрерывно, а из нее с помощью скребкового питателя – в обычные вагонетки по мере их подачи.
При разработки выработки по частям грунт сбрасывают из верхней штольни или колотты непосредственно в вагонетки, находящиеся в нижней штольне. Для доставки грунта к месту сбрасывания целесообразно применять скреперные установки.
3.2. Откатка в подземных выработках
Рельсовый путь. К основным звеньям рельсового транспорта относятся рельсовый путь, вагонетки различного назначения и устройства для приведения их в движение. Работа рельсового транспорта в значительной степени зависит от состояния рельсового пути, качеству которого должно уделяться большое внимание. В подземных выработках применяют рудничные рельсы, вес которых на 1 м должен соответствовать весу подвижного состава и установленным скоростям движения.
Для электровозной откатки применяют рельсы длиной 8 м и массой 1м 18 кг при вместимости вагонеток до 1,5 м3 и 24 кг при большей вместимости. Применение большегрузных вагонов типа ВПК требует перехода к рельсам массой 33 кг. Деревянные или стальные шпалы располагают не реже чем через 0,75 м. Стыки рельсов устраивают на весу с накладками и при применении контактных электровозов соединяют рельсы контактными перемычками из медного провода сечением не менее 50 мм2.
Ширина колеи на прямой определяется типом подвижного состава и составляет 600, 750 или 900 мм. Ширина междупутья должна обеспечивать наличие зазора между составами на параллельных путях не менее 200 мм и увязываться с размерами стандартных стрелочных переводов, укладываемых между путями.
Радиусы кривых назначают равными длине не менее семи жестких баз подвижного состава при ручной и канатной откатке и не менее десяти жестких баз при электровозной откатке. Желательно наличие двух путей по всей длине тоннеля со съездами через 200-300 метров для обеспечения маневров подвижного состава. При одном пути через 150-200 м устраивают разминовки, длина которых должна обеспечивать размещение наиболее длинного возможного состава. В качестве переводных устройств используют смонтированные на стальных плитах односторонние и перекрёстные съезды (ширина междупутья 1200 и 1500 мм), а также переносные устройства, перемещаемые по мере продвижения забоя.
Наращивание рельсов у забоя наиболее просто выполняют при помощи выдвижных звеньев 1, смонтированных на металлических шпалах 2 (рис. 3.31). По мере продвижения забоя звенья переносят вперёд, а на их место настилают постоянные откаточные пути.
Переносные рельсовые пути в призабойном пространстве допускаются на протяжении не более 30 м. Весьма целесообразно устраивать стальную платформу, служащую основанием для рельсовых путей у забоя и перемещаемую по мере его продвижению. В этом случае обеспечивается надёжное основание для работы погрузочной машины, а наращивание сначала рубок, а затем рельсов полной длины производят за платформой после её передвижения.
Безрельсовый транспорт. Прогрессивным направлением в организации подземного транспорта является применение автомобилей-самосвалов в сочетании с погрузкой грунта экскаваторами или машинами ПНБ-3 на гусеничном ходу. Преимущество автомобилей-самосвалов заключается в их независимости от энергетических коммуникаций (контактного провода, труб сжатого воздуха) и отсутствии необходимости в рельсовых путях, вагонетках, электровозах и разгрузочных устройствах на месте отвала грунта.
Поэтому, в настоящее время, тоннели больших сечений (автодорожные, двухпутные железнодорожные, строительные тоннели крупных гидроэлектростанций), как правило, строят с применением автомобильных транспортных средств. При транспортировании грунта и материалов автомобилями-самосвалами обеспечиваются комплексная механизация процесса проходки и возведения обделки и сокращение сроков строительства, но возникает необходимость усиления вентиляции подземных выработок, так как выхлопные газы двигателей внутреннего сгорания содержат ядовитые компоненты (окись углерода, акролеин, окиси азота, сернистый газ).
Наиболее распространённые при строительстве тоннелей большого сечения дизельные автомобили-самосвалы МАЗ-503 (грузоподъёмность 7 тонн, скорость движения в тоннеле 15 км/ч) оборудованы жидкостными нейтрализаторами, снижающими суммарную токсичность выхлопных газов на 65-70%. Используются также автомобили-самосвалы МоАЗ-64011 (грузоподъёмность 20 тонн, скорость движения в тоннеле 12 км/ч), оборудованы двухступенчатой очисткой выхлопных газов.
Для двухполосного движения автомобилей-самосвалов тоннель должен иметь ширину не менее 6 м. Для их поворота при изменении направления движения служит стальная плита размером 8х3 м и толщиной 15-20 мм, укладываемая на пол выработки и переносимая по мере продвижения забоя. Автомобиль-самосвал поворачивается на плите на 1800 с помощью лебёдки и подходит под погрузку задним ходом.
Очень удобны думперы (автомобили-самосвалы с поворотом сиденья и механизмом управления на 1800), совершающие челночные движения по тоннелю. Например, думпер ДР-60 производства ВНР грузоподъёмностью 6 тонн имеет скорость движения по тоннелю 14,7 км/ч.
При необходимости доставки грунта на небольшое расстояние от забоя целесообразны шахтные самоходные вагоны на пневматических шинах с донным скребковым транспортёром, загружаемые через открытый торец. Так, вагон ВС-15 грузоподъёмностью 15 тонн, имеющий длину 7,5 м, ширину 2,0 и высоту 1,65 м, перемещается с грузом со скоростью 7 км/ч. Эти вагоны используют электрическую энергию от сети с помощью имеющегося на барабане гибкого кабеля, запас которого обеспечивает радиус движения вагона до 200 м.
Глава 4
СООРУЖЕНИЕ ТОННЕЛЕЙ ГОРНЫМ СПОСОБОМ
4.1. Проходка тоннелей в скальных грунтах
Процессы сооружения. Сооружение тоннеля состоит из двух основных процессов: проходки, т.е. раскрытия выработки, с установкой в случае необходимости временной крепи, и возведения обделки. В зависимости от характера сооружения и геотехнических условий эти процессы выполняют в различной последовательности и по-разному развертываются по длине выработки, чем определяется способ производства работ.
Временную крепь, применяемую при проходке в скальных грунтах, устанавливают по контуру выработки, оставляя свободным ее внутреннее пространство. Контурная крепь создает благоприятные условия для комплексной механизации всех основных работ по сооружению тоннеля и способствует значительному увеличению темпов работ, а также уменьшению сроков и стоимости строительства. К наиболее распространенным системам контурной крепи относятся стальная арочная, анкерная и набрызг бетонная крепи.
Стальная арочная крепь. Применяемые в качестве временной крепи стальные арки из прокатных (обычно двутавровых) профилей в случае необходимости могут быть включены в состав бетонной обделки как жесткая арматура. В зависимости от способа производства работ и устойчивости стен выработки применяют стальную арочную крепь нескольких типов. При раскрытии выработки за один прием применяют крепь типов 1 и 2. Крепь типа 1 состоит из двух элементов, опирающихся на подошву выработки (рис.4.1, а, слева). В больших выработках каждый элемент крепи типа 1 может быть разбит на две части для удобства перевозки (рис.4.1,.а, справа). Крепь типа 2 состоит их двух элементов, опирающихся на уступы грунта за проектным контуром выработки (рис.4.2,б). Крепь типа 3 используют при раскрытии выработки в два приема, т.е. при проходки с опережающей калоттой, применяемой в менее прочных скальных грунтах. Крепь типа 3 состоит из четырех элементов (рис.4.1 в). В этом случае, применяемом при недостаточно устойчивых стенах выработки, арки калотты устанавливают на продольные рандбалки 4 из положенных на бок двутавров, наличие которых связано с необходимостью подводки стоек под верхнюю крепь после взрыва штроссы.
Стыки между элементами крепи устраивают при помощи стальных пластин 3 (рис.4.2), приваренных к торцам арок и соединяемых болтами 2. Для обеспечения совместной работы крепи и окружающего грунта производят расклинивание зазора между арками и контуром выработки через 100-150 см с обязательной постановкой клиньев 1 по обе стороны от замкового сечения. Продольная связь между ребрами обеспечивается распорками квадратного сечения с размером сторон 10-15 см и стальными стяжками диаметром 16-20 мм, расположенными чрез 120-150 см.
С целью предупреждения выпадания из кровли кусков грунта по ребрам укладывают доски с промежутками не менее 10 см, чтобы оставшиеся за обделкой они обеспечивали примыкание бетона к грунту. В устойчивых скальных грунтах при коэффициенте крепости f 2 вместо затяжки допускается закрепление поверхности выработки между арками набрызг-бетонном.
Анкерная крепь. Рассмотренные виды контурной крепи ограничивают развитие остаточных деформаций окружающих грунтов и, следовательно, рост горного давления, поддерживая кровлю выработки снизу. При этом элементы крепи подвергаются в основном сжатию.
На совершенно ином принципе основано применение анкерной крепи, нашедшей широкое применение в горной промышленности и успешно внедряемой в тоннелестроении. Принцип устройства и работы анкерной крепи заключается в следующем (рис. 4.3). В шпур, пробуренный в кровле (или стене) выработки, вводят стальную штангу 3, на одном конце которой имеется анкерная головка 1, а на другом – резьба для навинчивания гайки 4. При помощи анкерной головки 1 обеспечивается надежное закрепление штанги в шпуре, после чего на ее нижний конец надевают опорную шайбу 5 и завинчиванием гайки достигают натяжение штанги с силой N . При этом происходит обжатие грунта в объеме, ограниченном линиями 2, и предотвращается отделение блоков грунта под действием их собственного веса. Одновременно в результате обжатия на контакте между пластами возникают силы трения, препятствующие взаимному сдвигу пластов и частиц грунта, нарушенного раскрытием выработки.
Прочность и жесткость кровли, усиленной анкерами, значительно возрастают. Затяжка штанг способствует повышению несущей способности кровли, создает возможность ее использования для восприятия давления грунтов, расположенных над выработкой. Анкерная крепь является крепью принципиально нового типа, так как она не только поддерживает кровлю сверху, но и превращает ее в конструктивный элемент, способный выдержать значительные нагрузки.
Жесткость анкерной крепи больше, чем жесткость других видов крепи, так как в ней отсутствуют обминаемые элементы и сопряжения (шайбы выполнены из металла). Деформации могут происходить лишь при недостаточной прочности заделки анкерной головки, которая в этом случае имеет возможность продольного смещения. Однако при правильном выборе параметров смещение заделки может быть исключено.
Наряду с указанными достоинствами анкерная крепь обладает по сравнению с другими видами крепи следующими преимуществами: некоторое увеличение производительности машин и механизмов, работающих в совершенно свободной выработке; возможность механизации крепежных работ с уменьшением затрат времени и увеличением скорости проходки; сокращение расходов на перевозку крепежных материалов; устранение опасности повреждения крепи при взрывании; уменьшение сопротивления выработки движению воздушной струи и улучшение проветривания выработки.
Анкерную крепь используют в грунтах с широким диапазоном крепости (f 4) и различной степенью трещиноватости. Условиями ее успешного применения являются: расположение анкерной головки в ненарушенном устойчивом грунте; своевременная установка (до развития существенных остаточных деформаций кровли) и достаточное предварительное напряжение. Важное значение имеет также отсутствие поступления воды в шпур, так как при увлажнении некоторые грунты размягчаются и анкерная головка начинает скользить в заделке. Поэтому бурить шпуры для анкеров рекомендуется без промывки, а при промывке просушивать шпуры сжатым воздухом. Качество заделки анкерной головки в значительной степени зависит от твердости грунта, влияющей на выбор конструкции анкера.
Применению анкерной крепи обычно предшествуют ее испытания в производственных условиях с проверкой правильности принятых параметров крепи и надежности деталей конструкции анкера.
По принципу закрепления в грунте различают цельнометаллические (клинощелевые и распорные) анкеры, имеющие контакт со стенками шпура на коротком участке (в замке), а также железобетонные (набивные, «Перфо») и сталеполимерные, имеющие контакт со стенками шпура по всей его длине.
Наиболее распространенные (рис.4.4) клинощелевые анкеры изготавливают из мягкой стали. Такой анкер состоит из штанги 2, имеющей на одном конце резьбу для навинчивания натяжной гайки 4, а на другом конце – прорезь шириной 3-4 мм для клина 1, обеспечивающего закрепление анкера в грунте. Клин обычно на 10-20 мм короче прорези, его грани наклонены под углом 8-90, а конец имеет ширину около 2 мм.
Для установки на место штангу со вставленным в прорезь клином вводят в шпур до упора в его дно, после чего по концу штанги, выступающему из шпура, наносят удары при помощи отбойного молотка (резьбу предохраняют о повреждения специальной насадкой). При этом клин, входя в прорезь, раздвигает в стороны концы штанги, которые внедряются в стенки шпура (на глубину до 5 мм в грунтах с f=5÷6) и прочно закрепляются в грунте.
Для создания предварительного натяжения штанги на нижнем конце анкера пневматическим сболчивателем затягивают гайку, под которую помещают элемент, распределяющий давление на большую площадь кровли (квадратная опорная шайба 3, отрезок швеллера).
Для надежной заделки клинощелевого анкера необходимо обеспечивать при бурении проектную глубину и диаметр шпуров. Рекомендуется уменьшать разность диаметров шпура и штанги, которая не должна быть более 5-6 мм, и ширину прорези для клина.
Набрызгбетон. В практике современного тоннелестроения получил широкое распространение набрызгбетон марок В-50, В-60, применяемый для современного контурного крепления, возведения постоянных подземных конструкций. Эту полупластичную смесь портландцемента (обычно пуццоланового марки не ниже В-50), песка, гравия1, крупностью до 25-30 мм, и ускорителя схватывания и твердения наносят на поверхность выработки с помощью специальных пневматических машин.
Набрызгбетон отличается от обычного бетона повышенным содержанием цемента (250-350 кг/м3 в сухой смеси и 300-450 кг/м3 в материале обделки с учетом частичного отскока песка и гравия и уплотнения смеси при нанесении), более тщательным подбором гранулометрического состава заполнителей и технологией укладки, в процессе которой происходит интенсивное уплотнение набрызгбетона, обеспечивающее его значительное сцепление с поверхностью выработки.
1 Применение в качестве крупного заполнителя щебня вызывает резкое повышение износа оборудования
Набрызгбетон мало отличается от торкретбетона, однако введение в его состав ускорителя схватывания и твердения придает ему новые, весьма ценные свойства. Так, набрызгбетон можно наносить сравнительно толстыми слоями (до 15 см) без их оплывания, отскок быстросхватывающейся смеси невелик (до 10-15% от стен, до 20% от свода). Набрызгбетон имеет высокую прочность и водонепроницаемость уже при толщине 8-10 см, его сцепление со скальной поверхностью достигает 1,5-2,0 МПа и ограничивается лишь расчетным сопротивлением осевому растяжению (1,0-1,2 Мпа для марок В-30, В-40).
Покрытие из набрызгбетона толщиной 10-15 см обеспечивает надежное закрепление контура выработки, если грунт может оставаться не поддержанным в течение времени, нужного для нанесения и затвердения слоя. Быстрое закрепление кровли приостанавливает развитие в ней остаточных деформаций и рост горного давления и позволяет уменьшить толщину сооружаемой впоследствии постоянной обделки.
Через 3-4 ч. после нанесения набрызгбетона возможно продолжение взрывных работ, вследствие чего его применение не замедляет проходки. Особенно эффективно применение набрызгбетона в сочетании с анкерной крепью.
Постоянная обделка из набрызгбетона в выработке, закрепленной анкерами, может быть выполнена в удалении от забоя без помех для проходческих работ. К ее достоинствам относится отсутствие необходимости в опалубке и последующем нагнетании цементного раствора. В прочных грунтах возможно возведение обделки из набрызгбетона толщиной 15-20 см по стальной сетке, подвешенной к долговечным анкерам (железобетонным или сталеполимерным).
Использование в качестве временной крепи набрызгбетона, наносимого непосредственно по контуру выработки, допускается в грунтах с коэффициентом крепости f 4. Более распространено нанесение набрызгбетона по сетке из проволоки диаметром до 7 мм с ячейками размерами не менее 100х100 мм, подвешенной к анкерам. В таком виде слой набрызгбетона допускается в качестве постоянной тоннельной обделки в скальных монолитных и слабо трещиноватых грунтах с коэффициентом крепости f7. Наличие сетки повышает несущую способность слоя на 30-40%.
Толщина набрызг бетонного покрытия может быть определена в соответствии с ВСН 126-78 или по формуле, применяемой при проектировании подземных гидротехнических сооружений,
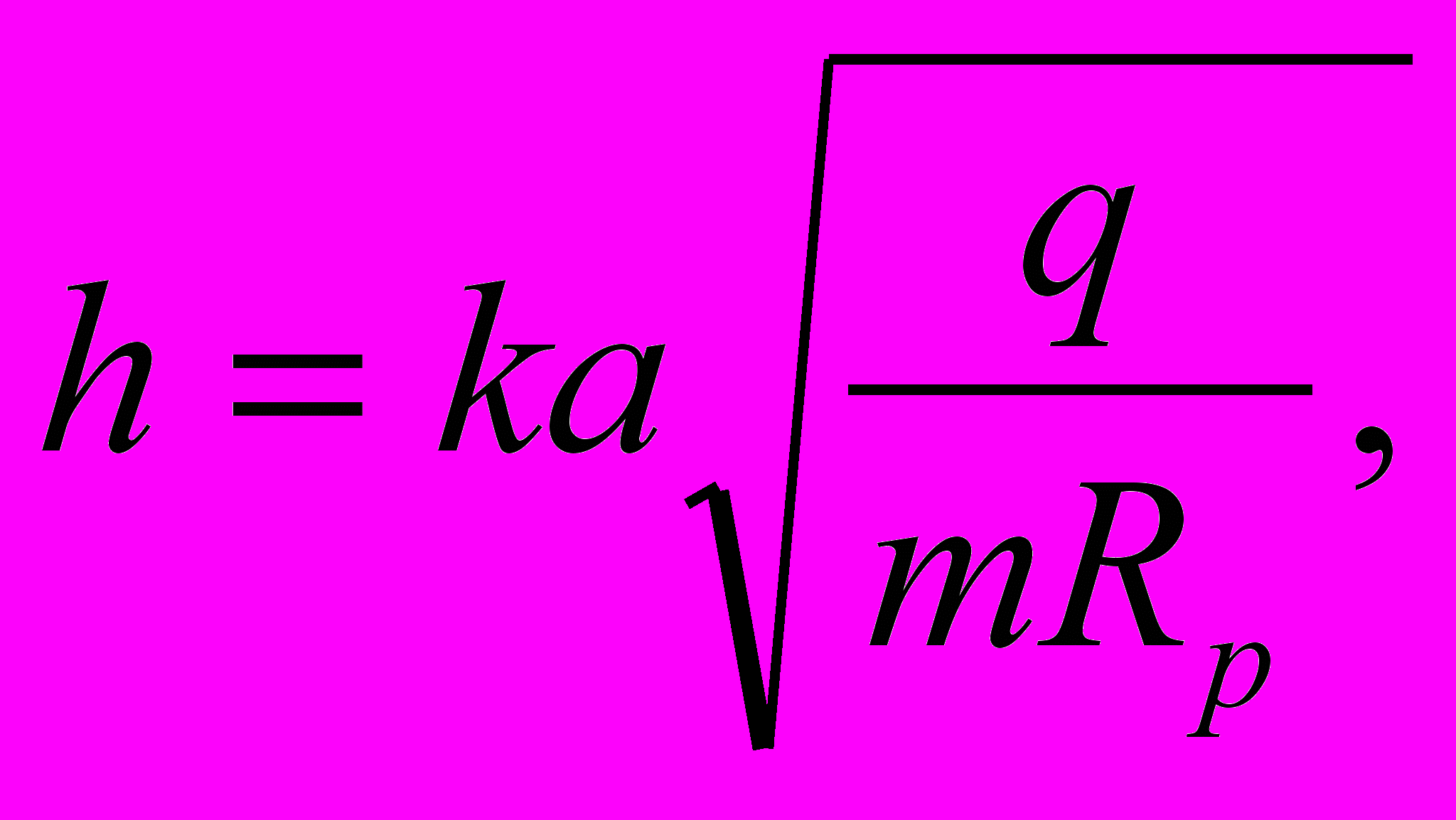
где k – коэффициент, принимаемый в зависимости от вида крепи (при крепи из набрызгбетона k=0,35; при покрытии из набрызгбетона по сетке, прикрепленной к анкерам, и расстоянии между рядами анкеров a=0,8÷1,5 м k=0,25). При нанесении слоя непосредственно на грунт принимают расстояние между анкерами равным В/6, где В – ширина выработки, но не менее 1 м; q – расчетная интенсивность горного давления, кН/м2; m – коэффициент условий работы, принимаемый равным 0,75 для неармированных и 1,0 для армированных покрытий; Rр – расчетное сопротивление набрызнбетона растяжению, принимаемое равным 1,2 –1,6 Мпа для армированных и 1,0-1,4 Мпа для неармированных покрытий.
Для постоянных обделок полученную по формуле 4.1 толщину увеличивают на 30-40 %.
Особенности проходки в скальных грунтах. Проходку в скальных грунтах ведут почти исключительно буровзрывным способом, при котором выполнению цикла работ соответствует продвижение забоя на глубину заходки.
После взрывания забой оказывается заваленным грунтом, а кровля выработки у забоя – без поддержки и, следовательно, подвергается остаточном деформациям под действием развивающихся в ней растягивающихся напряжений. Нарастание деформаций происходит тем быстрее, чем меньше крепость грунта и больше степень его трещиноватости и размеры выработки. Эти факторы определяют период, в течение которого кровля может быть безопасно оставлена без поддержки.
В весьма крепких скальных грунтах выработки часто оставляют без временной крепи до сооружения постоянной обделки.
В крепких скальных грунтах, устойчивость которых обеспечена в течение сравнительно продолжительного периода, временную крепь устанавливают после уборки грунта во вермя бурения на следующую заходку (со специальной тележки или буровой рамы, подтянутой к забою). За счет совмещения операций сокращается продолжительность проходческого цикла и увеличивается скорость продвижения забоя.
В менее крепких скальных грунтах временную крепь устанавливают после уборки грунта перед обуриванием забоя на следующую заходку. В грунтах средней крепости, слабых скальных и полускальных длительное оставление кровли без крепления может вызвать значительные ее деформации с отслоением и выпаданием отдельных глыб, что связано с нарастанием горного давления. Поэтому крепь ставят сразу после проветривания и оборки кровли.
Изложенные соображения влияют на выбор системы крепи и способа проходки, так как продолжительность периода между раскрытием выработки и установкой временной крепи определяет удобства организации производственного процесса.
При проходке в скальных грунтах применяют только поточную систему развертывания работ по длине выработки. При этом в зависимости от степени устойчивости и крепости грунтов забой выработки продвигают вперед всем сечением или расчленяют на части, последовательность взрывания которых определяет способ проходки тоннеля. Обделку бетонируют, как правило, в полностью раскрытой выработке.
Наиболее распространенными способами производства работ по сооружению тоннеля в скальных грунтах являются способы сплошного забоя и нижнего уступа; менее распространен способ центральной штольни.
Способ сплошного забоя. При этом способе, применяемом для проходки тоннелей высотой до 10 м с монолитной обделкой, в устойчивых скальных грунтах с коэффициентом крепости не менее 4, раскрытие выработки производят за один прием, в случае необходимости (трещиноватые выветрелые грунты) с временной крепью, которую устанавливают после уборки взорванного грунта с буровой рамы (подмостей), подтянутой к забою.
При проходке в скальных монолитных грунтах с коэффициентом крепости не менее 12 временное крепление выработки не производится. В этом случае (рис.4.5) отсутствует опережающая выработка. Поэтому при недостаточной изученности геологических условий для предупреждения прорыва воды или обрушения более слабых грунтов целесообразно бурить входящую в состав вруба опережающую скважину диаметром 75-100 мм на глубину до 20-50 м.
В скальных грунтах средней крепости, требующих закрепления кровли до уборки породы, кровлю временно поддерживают подхватами, подмешенными к ранее установленным стальным аркам, или закрепляют анкерной крепью, устанавливаемой с выдвижных платформ буровой рамы.
Критерием для возможности применения этого способа является безусловная устойчивость забоя без использования несущей забойной крепи.
Способ сплошного забоя характеризуется простой и четкой организацией работ, обеспечивающей снижение трудоемкости и высокие скорости проходки. Благодаря значительной площади сечения зажим взрываемого грунта уменьшается и применение глубоких заходок, необходимых для скоростной проходки, не вызывает повышенного расхода ВВ. Однако преимущества этого способа могут быть реализованы лишь при достаточной механо- и энерговооруженности.
При способе сплошного забоя (см. рис. 4.6) бурение шпуров и установку анкерной крепи производят с использованием самоходного бурового агрегата 1 (в данном случае “Фурукава”), уборку грунта -машиной 2 (типа ПНБ) в вагон 3 (ВПК-10), перемещаемый электровозом. Кровлю выработки закрепляют анкерами 4. Воздух подают к забою по вентиляционной трубе 5, подвешенной к кровле выработки. Бетонирование обделки производят в инвентарной опалубке на расстоянии от забоя, определяемом удобством производства работ.
Способ нижнего уступа. При проходке тоннелей высотой более 10 м в скальных грунтах с коэффициентом крепости не менее 4 или высотой менее 10 м в скальных грунтах с коэффициентом крепости от 2 до 4 применяют способ нижнего уступа (рис. 4.6), при котором проходка калотты опережает проходку штроссы на 30-50 м.
Опережающая калотта является рекогносцировочной выработкой, позволяющей при встрече с более слабыми, чем предполагалось, грунтами своевременно перестроить производственный процесс, не приостанавливая работ по расширению сечения. Наряду с этим забой высокой выработки расчленяются на две устойчивые и не требующие крепления части.
Разработку верхней части выработки производят способом сплошного забоя, допускающим высокий уровень механизации.
После проветривания и оборки забоя и кровли ее закрепляют анкерной крепью или временно (до окончания уборки) поддерживают балками-подхватами, подвешенными в случае арочной крепи к предыдущим аркам.
При устойчивых стенах выработки арочная крепь калотты опирается непосредственно на грунт или деревянные подкладки за пределами проектного контура. При неустойчивых стенах опорой для крепи служат стальные рандбалки, состоящие из звеньев, соответствующих глубине заходки, под которые после взрывания уступа подводят стойки. Промежутки между арками затягивают досками.
Высоту калотты назначают не менее 4 м из условия размещения проходческого оборудования и в случае необходимости возможности бетонирования свода.
При способе нижнего уступа (см. рис.4.6) бурение шпуров в калотте производят самоходной установкой 3 (например, СУ-2К), которая перед взрыванием отводится на безопасное расстояние от забоя. Уборку грунта ведут машиной непрерывного действия 1 (например, ПНБ-3Д) с погрузкой в самоходный вагон 2 (например, ВС-15 ), доставляющий грунт к нижнему уступу и сбрасывающий его вниз. На нижнем уровне машина непрерывного действия грузит грунт в состав из вагонов с донным конвейером 4 (например, ВПК-7 и ВПК-10), перемещаемый электровозом 5.
После уборки грунта оба забоя обуривают на следующую заходку.
Для уменьшения разброса взорванного грунта шпуры нижнего уступа целесообразно бурить горизонтально с помощью портального бурового агрегата 6 (ПБА-1 или “Фурукава”), который после преодоления участка, на котором необходимо применить способ нижнего уступа, используется для проходки выработки полным сечением.
Обделку обычно бетонируют целиком в удалении от уступа, определяемом удобствами организации работ. С целью ее упрощения иногда проходят насквозь верхнюю часть выработки с закреплением арочной или анкерной крепью. Только после этого проходят штроссу и бетонируют обделку.
Достоинства способа нижнего уступа - некоторая экономия ВВ по сравнению со способом сплошного забоя и возможность применения в слабых скальных грунтах. Недостатком способа нижнего уступа является усложнение организации работ по параллельной проходке в двух забоях ,взрывание в которых необходимо производить одновременно для сокращения общего времени на заряжание и проветривание. Дополнительные трудности возникают в связи с перекладкой (на время взрывания нижнего уступа) устройств, обеспечивающих переброску грунта из опережающего забоя к месту окончательной погрузки (если не применяются вагоны ВС) и необходимостью поддержания верхней крепи в месте уступа (при арочной крепи).
В тоннелях длиной до 300 м, кроме параллельной системы работ, может быть применена также последовательная система, при которой лишь после сбойки опережающих калотт, закрепляемых временной крепью или постоянной обделкой.
Способ ядра с податливой оболочкой. Применение в скальных и полускальных грунтах набрызгбетона в сочетании с гладким взрыванием и анкерной крепью явилось предпосылкой для создания нового способа работ, получившего широкое распространение за рубежом, особенно в Австрии, где он был разработан, в связи с чем и получил название новоавстрийского.