Учебное пособие для студентов среднего профессионального образования Специальность 1701 "Монтаж и техническая эксплуатация промышленного оборудования (по отраслям)"
Вид материала | Учебное пособие |
- Учебное пособие для студентов нефтехимических колледжей и техникумов Специальность, 3210.24kb.
- Программа и контрольные задания для студентов заочного отделения Специальность: 1701, 688.94kb.
- Государственный образовательный стандарт среднего профессионального образования государственные, 1346.06kb.
- Федеральный государственный образовательный стандарт среднего профессионального образования, 1074.58kb.
- Методические указания и контрольные задания для студентов заочной формы обучения гоу, 2389.4kb.
- Методические указания и контрольные задания для студентов заочного отделения специальность:, 848.08kb.
- «Материаловедение», 179.95kb.
- Формирование профессионально-значимых качеств личности в условиях личностно-ориентированного, 51.94kb.
- Система управления качеством подготовки техников по специальности 150411 – Монтаж, 102.4kb.
- Примерная программа профессионального модуля проведение подземного ремонта скважин, 226.39kb.
1. Какие поверхности относят к фасонным?
2. Назовите инструмент, применяемый при фасонной обработке.
3. Какими способами ведут обработку фасонных поверхностей?
4. Как осуществляют контроль фасонной поверхности?
2 Работа на фрезерных станках
Тема 2.1 Рабочее место фрезеровщика.
Управление фрезерным станком
Студент должен
знать:
- основные узлы и детали фрезерного станка;
- типы фрез и их подбор;
- установку и проверку на биение;
- виды фрезерных работ;
- приспособления для установки инструмента и крепления заготовок.
уметь:
- производить настройку и наладку фрезерных станков на фрезерование деталей с применением простых приспособлений.
Оснащение рабочего места: горизонтально-фрезерный станок модели 6Р81 или вертикально-фрезерный модели 6Р12; образцы фрезерных работ, наборы режущего и измерительного инструментов и приспособлений, применяемых на фрезерных станках; инструкции и плакаты по технике безопасности и организации рабочего места фрезеровщика; принадлежности по уборке, смазке и уходу за станком.
Фрезерование является одним из наиболее распространенных методов обработки плоских и различных фасонных поверхностей, нарезания резьбы, шлицев, зубьев колес и других деталей.
На рисунке 2.1, а…м приведены примеры работ, выполняемых на фрезерных станках.
При работе на фрезерных станках нужно знать: правила управления и ухода за обслуживаемым станком; устройство, принцип работы и назначение важнейших частей фрезерного станка; наименование, маркировку и основные свойства обрабатываемых материалов; назначение и условия применения наиболее распространенных приспособлений и простого контрольно-измерительного инструмента; назначение, устройство, правила применения, заточки и хранения режущего инструмента при фрезерных работах; назначение и применение охлаждающих жидкостей, масел и вспомогательных материалов; правила пользования технологической документацией, рабочими чертежами и эскизами; основные сведения о допусках и посадках, квалитетах точности, параметрах шероховатости поверхности; назначение технологического процесса; способы выполнения основных фрезерных операций, простейшие расчеты, необходимые для налаживания станка для этих операций; определение наивыгоднейших режимов при фрезерной обработке; виды и причины брака при фрезерной обработке, меры его предупреждения и устранения; способы рациональной организации труда и рабочего места; инструкции по технике безопасности, противопожарные мероприятия и правила внутреннего распорядка на производственном участке.
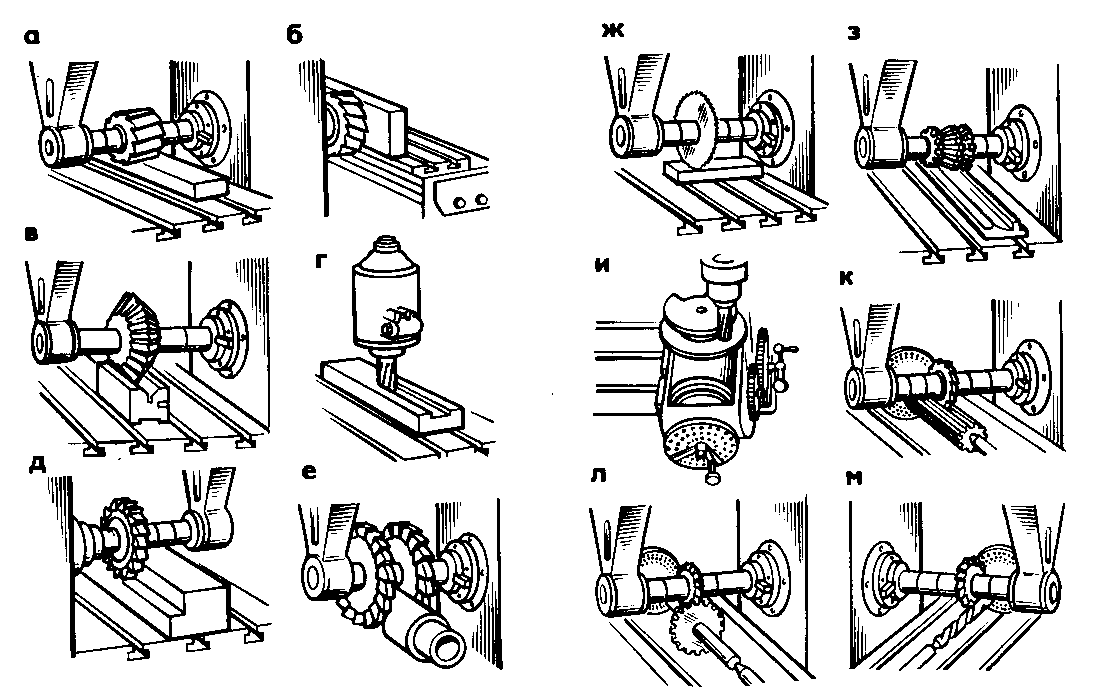
а - фрезерование плоской поверхности цилиндрической фрезой; б - фрезерование плоской поверхности торцовой фрезой; в - фрезерование наклонных поверхностей (призм) угловой фрезой; г - фрезерование паза концевой фрезой; д - фрезерование уступа дисковой трехсторонней фрезой; е - фрезерование набором двух дисковых трехсторонних фрез; ж - разрезание отрезной фрезой (пилой); з - фрезерование фасонной фрезой; и - фрезерование криволинейного контура концевой фрезой с применением делительной головки; к - фрезерование шлицевых канавок на валике; л - фрезерование зубчатого колеса; м - фрезерование винтовых канавок
Рисунок 2.1 Примеры работ, выполняемых на фрезерных станках
Рабочее место фрезеровщика состоит из фрезерного станка; технологической и организационной оснастки; элементов, обеспечивающих охрану труда и санитарно-гигиенические условия работы. На рис. 2.2 дан пример организации рабочего места около вертикально-фрезерного станка. Справа от рабочего расположен инструментальный шкаф 8 для хранения инструментов и приспособлений, слева - тара для заготовок 2 и обработанных деталей 1. Около станка должна находиться деревянная подножная решетка 9, высота которой подбирается по росту учащегося. Учитывая, что большинство фрезерных станков имеют дублирующие органы управления, решетка должна быть Г-образной формы для беспрепятственного перемещения рабочего вдоль фасада станка и с левой стороны.
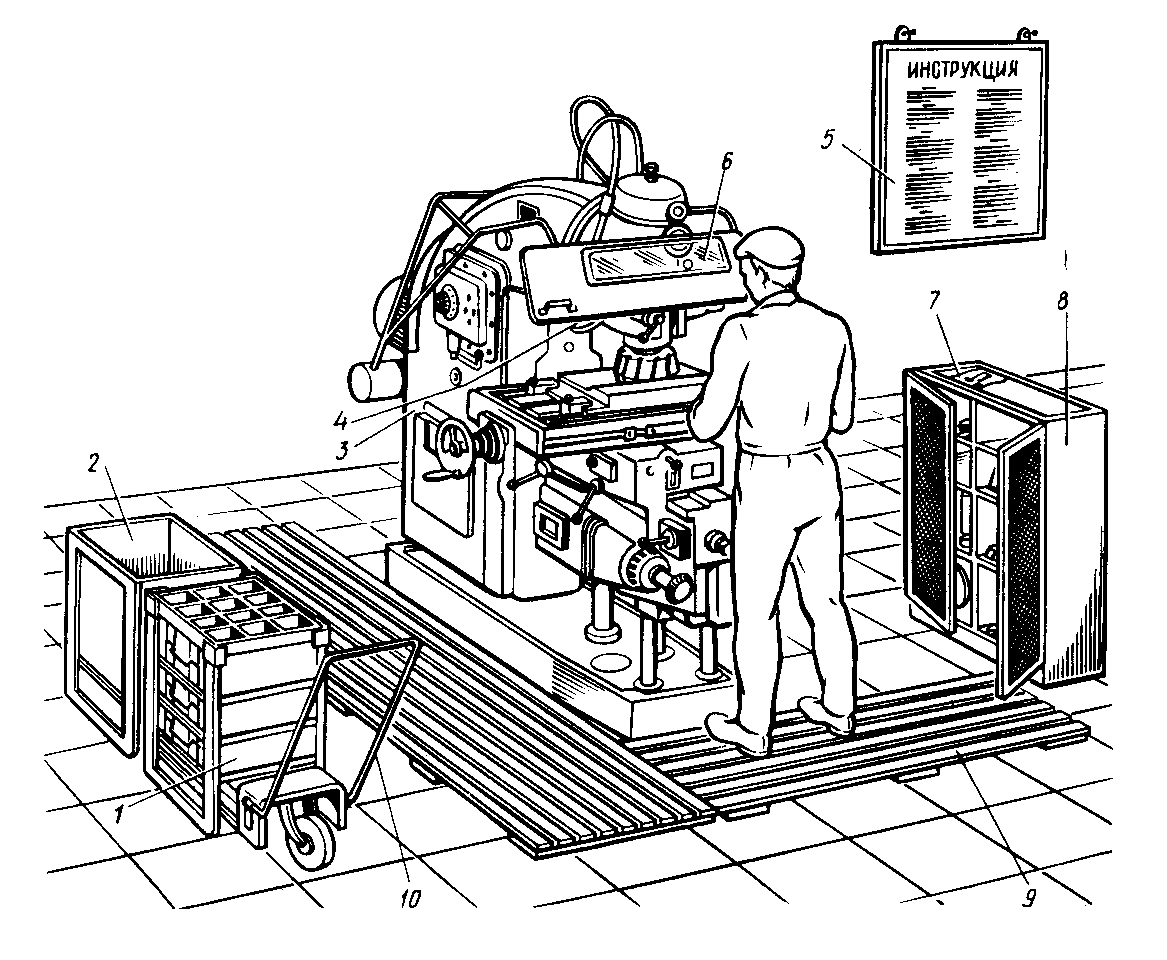
1 - тара для обработанных деталей; 2 - тара для заготовок; 3 - фрезерный станок; 4 - лампа местного освещения; 5 - инструкция по технике безопасности; 6 - защитный экран; 7 - место для технологической документации; 8 - инструментальный шкаф; 9 - подножная решетка; 10 - тележка для транспортировки тары
Рисунок 2.2 Рабочее место фрезеровщика
Для ежедневного ухода за станком и его смазки на рабочем месте должны находиться специальный шприц, масленка и щетка.
Такие приспособления, как делительные головки, поворотные столы и угольники, машинные тиски и т. п., следует хранить в учебных мастерских централизованно на специальных стеллажах или в шкафах.
Кроме общих правил техники безопасности, указанных в 1 части, при работе на фрезерном станке необходимо соблюдать следующие меры предосторожности:
1. Соблюдать порядок и чистоту на рабочем месте. Помещать инструмент, приспособления, заготовки и прочее на места, специально отведенные для них.
2. Применять защитные ограждения (экраны). В том случае, когда отсутствует ограждение рабочей зоны, необходимо работать в защитных очках.
3. Перед включением электродвигателя выключить (поставить в нейтральное положение) все рычаги управления.
4. При смене инструмента, установке и снятии приспособлений, уборке, чистке и смазке станка обязательно выключать электродвигатель.
5. Перед установкой на станок приспособлений очистить от стружки и масла базовые и крепежные поверхности для обеспечения правильной установки и прочности крепления.
6. Обрабатываемую заготовку устанавливать на станке правильно и надежно, чтобы во время рабочего хода станка были исключены возможности ее вылета из зажимного приспособления.
7. Заготовку закреплять за места, находящиеся как можно ближе к обрабатываемой поверхности. При креплении заготовки за необработанные поверхности применять тиски или приспособления с насечкой на прижимных губках.
8. Заготовку к фрезе подавать тогда, когда фреза получит рабочее вращение.
9. При смене обрабатываемой заготовки, ее измерении и осмотре остановить станок, отвести инструмент (стол станка) на безопасное расстояние, чтобы не повредить руку о режущие кромки.
10. Врезать фрезу в заготовку постепенно; механическую подачу включать до соприкосновения заготовки с фрезой. При ручной подаче не допускать резких перемещений стола.
11. При фрезеровании не вводить руки в опасную зону вращения фрезы.
12. Пользоваться только исправной и заточенной фрезой. Перед установкой фрезы проверить надежность и прочность крепления зубьев и пластин в корпусе фрезы, правильность заточки, отсутствие трещин, прижогов и выкрошенных мест.
13. Выколачивать фрезу из шпинделя (оправки) специальной выколоткой, не поддерживать ее незащищенной рукой - применять для этого рукавицу или эластичную прокладку.
14. При установке фрезы (фрезерной оправки) отверстие шпинделя, хвостовик оправки или фрезы, переходную втулку тщательно очистить, устранить забоины и протереть ветошью.
15. Фрезерную оправку или фрезу закреплять в шпинделе ключом только после включения коробки скоростей во избежание проворачивания шпинделя.
16. Во время работы станка не открывать и не снимать ограждения и предохранительные устройства.
17. Останавливая станок, выключить подачу, отвести заготовку от фрезы и выключить вращение шпинделя.
18. По окончании работы на станке убрать стружку, протереть рабочие части и трущиеся поверхности обтирочным материалом и смазать, переместить продольный стол, салазки и консоль в среднее положение.
19. Сдавая рабочее место мастеру или дежурному по мастерским, обязательно сообщить о замеченных недостатках в работе станка.
Устройство фрезерных станков
На машиностроительных предприятиях фрезерные работы выполняют на консольно-фрезерных, вертикально-фрезерных с крестовым столом, фрезерных непрерывного действия, копировально-фрезерных, шпоночно-фрезерных, торцефрезерных, специальных и специализированных станках. Наиболее универсальными и широко распространенными в учебных мастерских являются консольно-фрезерные станки, которые в зависимости от расположения шпинделя делятся на: горизонтально-фрезерные (с неповоротным столом) моделей 6М80Г, 6Р81Г, 6Р82Г (рис. 2.3, а); горизонтально-фрезерные с поворотным столом (универсальные) 6Н81, 6Р82, 6Р830; вертикально-фрезерные 6М10, 6Р12, 6Р13 (рис. 2.3, б); широкоуниверсальные 6П80Ш, 6Р81Ш, 6Р82Ш (рис. 4.3, в). Все тренировочные упражнения и изучение приемов работы в данном пособии приводятся для консольно-фрезерных станков моделей 6Р12 и 6Р81Г.
О классификации моделей станков и значении каждой цифры и буквы в номере модели смотрите в 1 разделе.
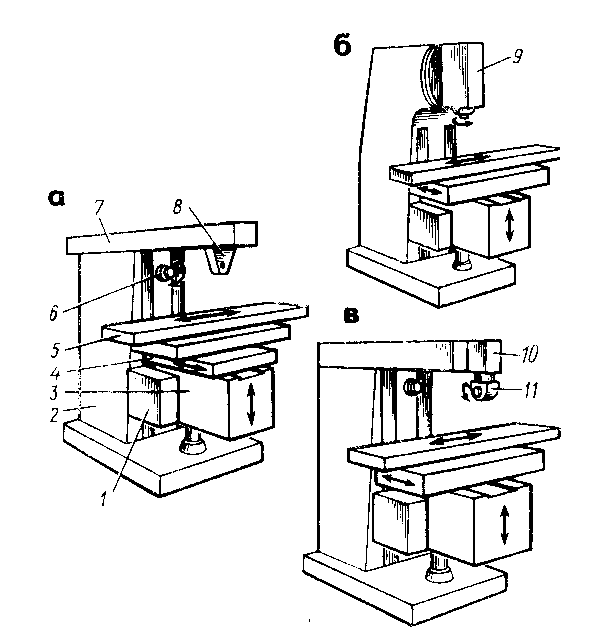
Рисунок 2.3 Консольно-фрезерные станки (стрелки
указывают направление движения)
Станки (рис. 2.3) состоят из станины, консоли, которая несет на себе каретку со столом, коробки скоростей со шпинделем, коробки подач и органов управления.
Станина 2, установленная на основании станка, служит для крепления всех узлов и механизмов станка. Некоторые узлы станка, такие, как коробка скоростей, шпиндель, механизм подачи движения к коробке подач, расположены внутри станины, другие узлы станка -консоль, стол, хобот (у горизонтально-фрезерных станков), насос для подачи охлаждающей жидкости - находятся на наружных поверхностях станины. На передней стенке станины имеются вертикальные направляющие для консоли, выполненные в виде ласточкина хвоста, а наверху - горизонтальные направляющие для хобота.
Коробка скорости движения подач 1 служит для изменения движения подач стола в продольном, поперечном и вертикальном направлениях с помощью передвижных блоков зубчатых колес и муфт. Сокращение вспомогательного времени производят механизмы ускоренных перемещений стола. Консольно-фрезерные станки имеют отдельные электродвигатели для привода коробки скоростей и коробки подач.
Хобот 7 имеется у горизонтально- и универсально-фрезерных станков и служит для правильной установки и поддержки фрезерной оправки. Хобот установлен в горизонтальных направляющих на верхней части станины и может быть закреплен с различным вылетом. Для увеличения жесткости при обработке тяжелых заготовок и при больших сечениях стружки применяют поддержки, которые связывают хобот с консолью.
Консоль 3 представляет собой жесткую чугунную отливку, установленную на вертикальных направляющих станины. Снизу она поддерживается стойкой, в которую вставлен телескопический винт подъема и опускания консоли. На консоли имеются горизонтальные направляющие для салазок.
Салазки 4 являются промежуточным звеном между консолью и столом станка. По верхним направляющим салазок движется стол в продольном направлении, а нижняя часть салазок перемещается в поперечном направлении по верхним направляющим консоли.
Стол 5 по направляющим салазок перемещается в продольном направлении. На столе укрепляют заготовки, зажимные, делительные и другие приспособления. Для этой цели рабочая поверхность стола имеет продольные Т-образные пазы. Перемещения стола, салазок и консоли сообщают заготовке продольную, поперечную и вертикальную подачи по отношению к фрезе, установленной на шпинделе.
Шпиндель 6, получающий движение от коробки скоростей, служит для вращения режущего инструмента. Передний конец, шпинделя имеет внутренний конус, в который вставляется фрезерная оправка с фрезой или непосредственно хвостовик торцовой фрезы. Вращение фрезерной оправки производится поводками, привернутыми к торцу шпинделя.
Коробка скоростей, расположенная в станине 2 станка, предназначена для передачи вращения от электродвигателя шпинделю станка и изменения частоты вращения последнего в соответствии с требуемой скоростью главного движения резания. Частота вращения шпинделя изменяется путем переключения подвижных зубчатых колес и блоков, расположенных на нескольких валах коробки скоростей и шпинделе, а также упругих муфт, включающих ту или иную пару зубчатых колес.
Хобот 7 с серьгами 8 служит для поддержания оправки с закрепленной на ней фрезой. Вылет хобота на требуемую длину осуществляют поворотом рукоятки торцового ключа. Для установки в шпиндель станка оправки с фрезой серьгу снимают с направляющих хобота.
Вертикальный консольно-фрезерный станок (рис. 2.3, б) в отличие от горизонтального имеет вертикально расположенный шпиндель с поворотной головкой 9, которая может поворачиваться в вертикальной плоскости на угол 0...45° в обе стороны. Назначение узлов и органов управления такое же, как и у горизонтально-фрезерных станков. Основной отличительной особенностью этих станков является отсутствие хобота.
Широкоуниверсальный консольно-фрезерный станок (рис. 2.3, в) в отличие от горизонтально-фрезерного станка имеет еще одну фрезерную головку 10, смонтированную на выдвижном хоботе, которую можно поворачивать под любым углом в двух взаимно перпендикулярных плоскостях. На этих станках возможна раздельная и одновременная работа обоими шпинделями. На поворотной шпиндельной головке монтируют накладную фрезерную головку 11, которая позволяет обрабатывать на станке заготовки сложной формы не только фрезерованием, но и сверлением, зенкерованием, развертыванием и растачиванием.
Кинематические схемы вертикально-фрезерного и горизонтально-фрезерного станков различаются только направлением расположения шпинделей, а конструктивное различие их состоит в том, что у вертикально-фрезерного станка отсутствует хобот и несколько изменена конструкция станины для установки поворотной шпиндельной головки. Кинематическая схема горизонтально-фрезерного станка модели 6Р82Г показана на рис. 2.4.
Станок имеет три вида движения: главное - вращательное движение шпинделя с фрезой; движение подачи - перемещение стола с закрепленной на нем заготовкой в продольном, поперечном и вертикальном направлениях; вспомогательное движение - ускоренное перемещение стола в тех же направлениях. Главное движение и движение подачи имеют раздельный привод, т.е. самостоятельные электродвигатели.
М
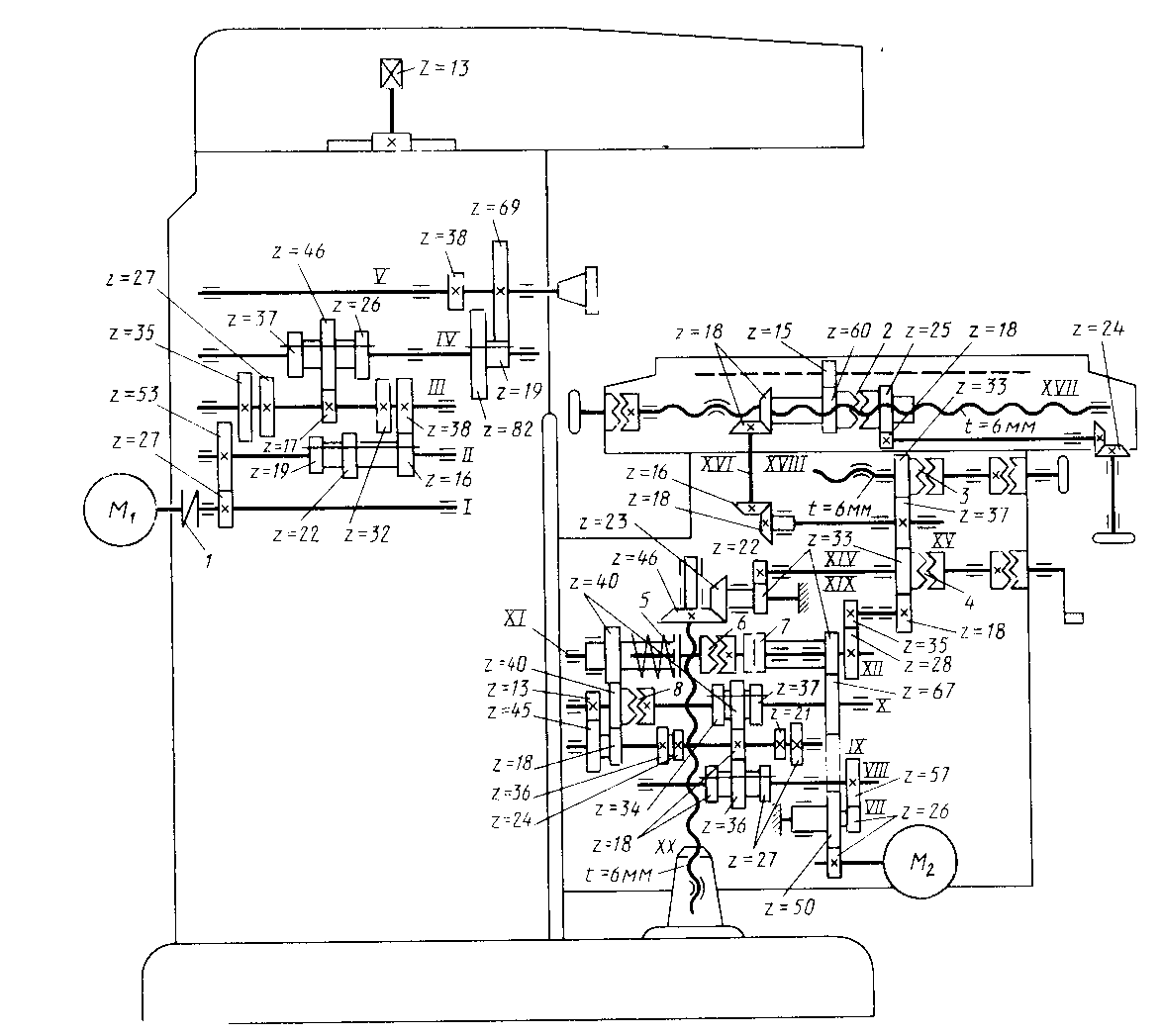
еханизм главного движения (шестеренная коробка скоростей) предназначен для сообщения шпинделю необходимой частоты вращения. Шпиндель станка получает движение от электродвигателя М1 (n = 1440 об/мин) через упругую муфту 1 и шестеренчатую коробку скоростей с помощью трех передвижных блоков зубчатых колес (z=19-22-16; z=37-46-26; z=19-82).
Рисунок 2.4 Кинематическая схема горизонтально-
фрезерного станка 6Р821
(арабскими цифрами обозначены числа зубьев зубчатых колес,
римскими - номера валов)
Коробкой скоростей шпинделю сообщается 18 различных частот вращений. Наименьшую nmin и наибольшую nmax частоты вращений шпинделя определяют по уравнениям:
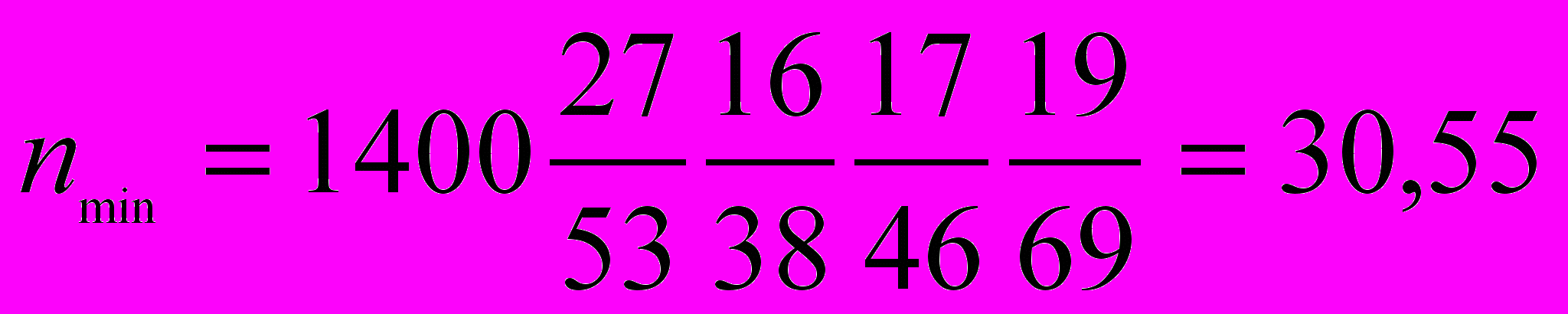
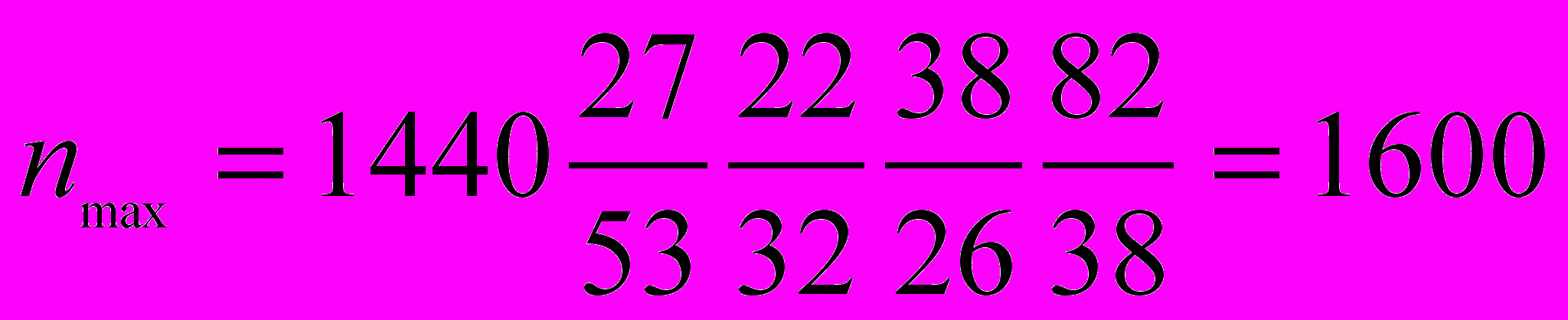
Изменение направления вращения шпинделя осуществляют реверсированием электродвигателя.
Механизм движения подачи предназначен для получения различных рабочих скоростей движения подачи и быстрых перемещений стола, салазок и консоли в продольном, поперечном и вертикальном направлениях. Направление подачи также реверсируется электродвигателем.
Движение от электродвигателя М2 (n=1430 об/мин) через пары зубчатых колес
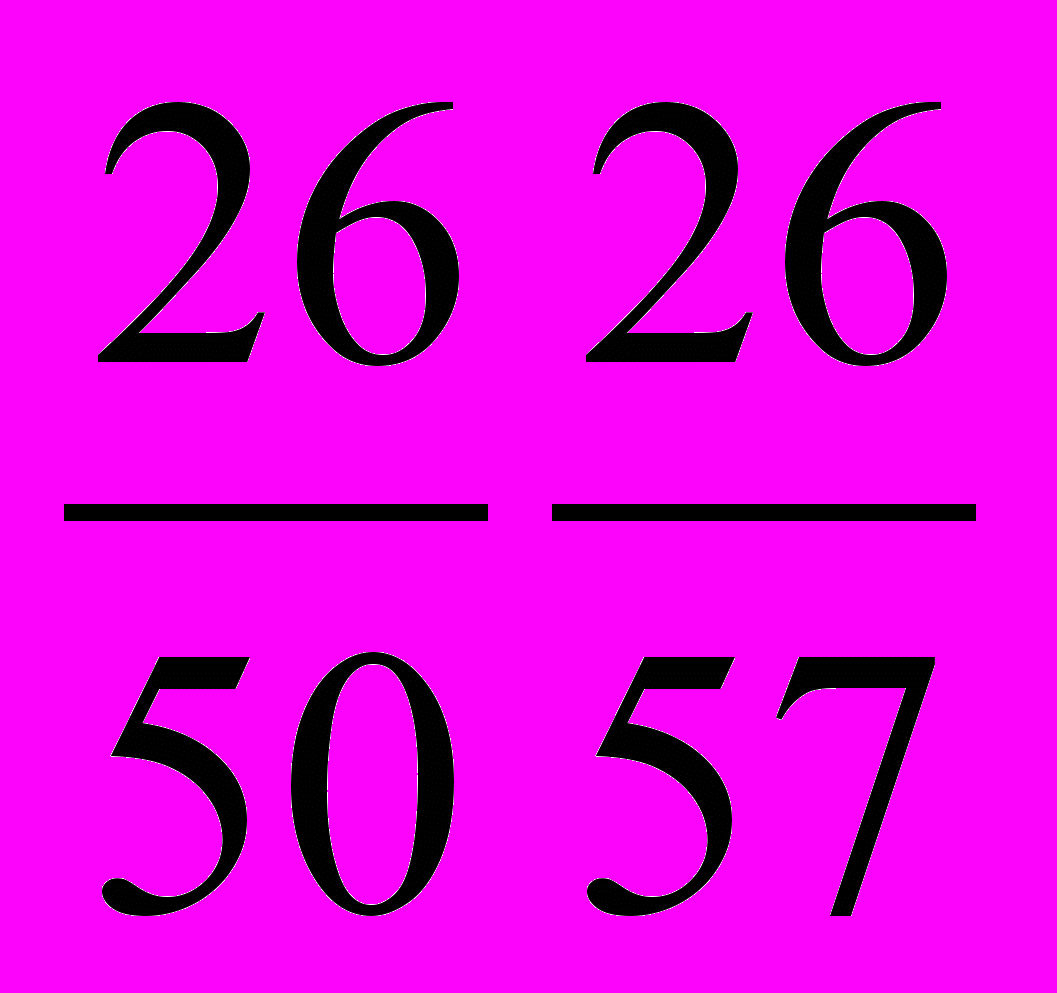
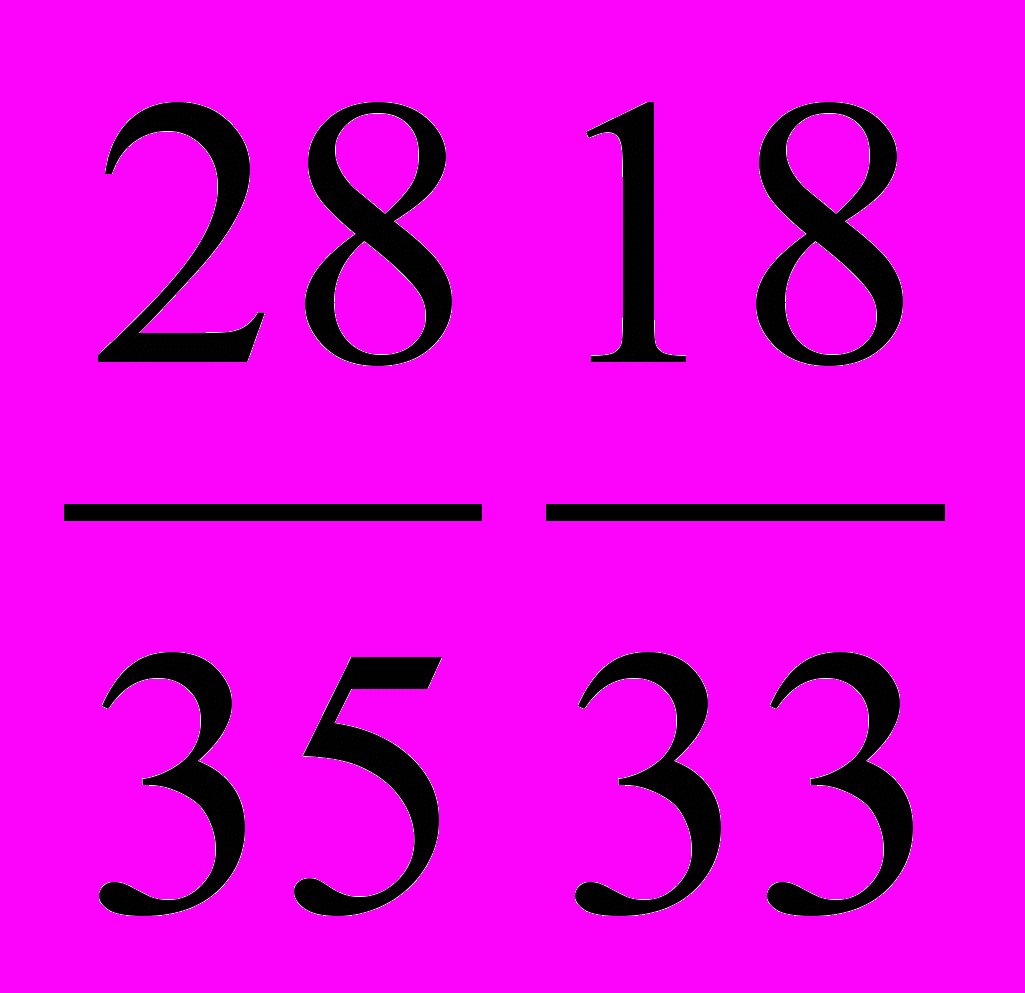
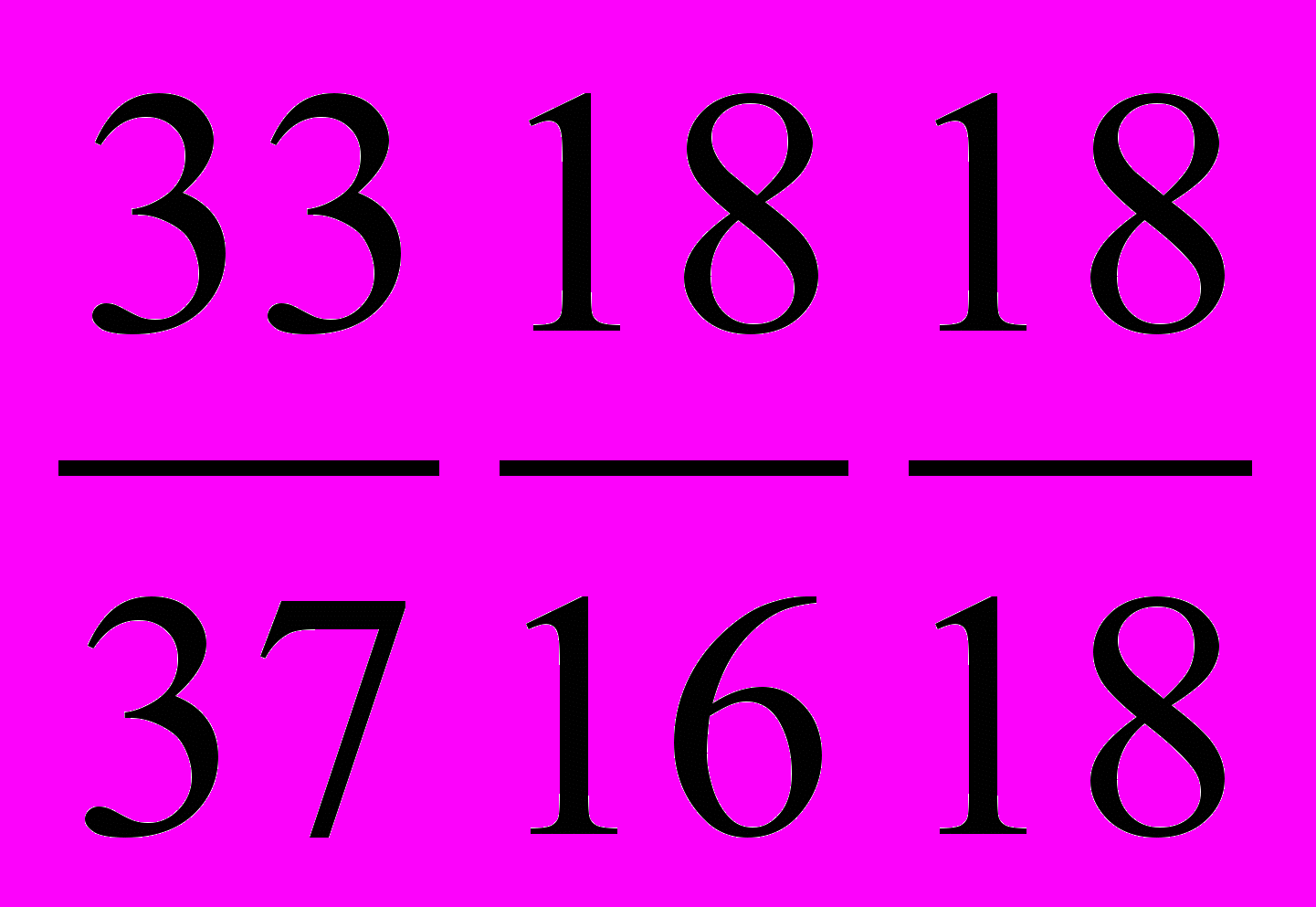
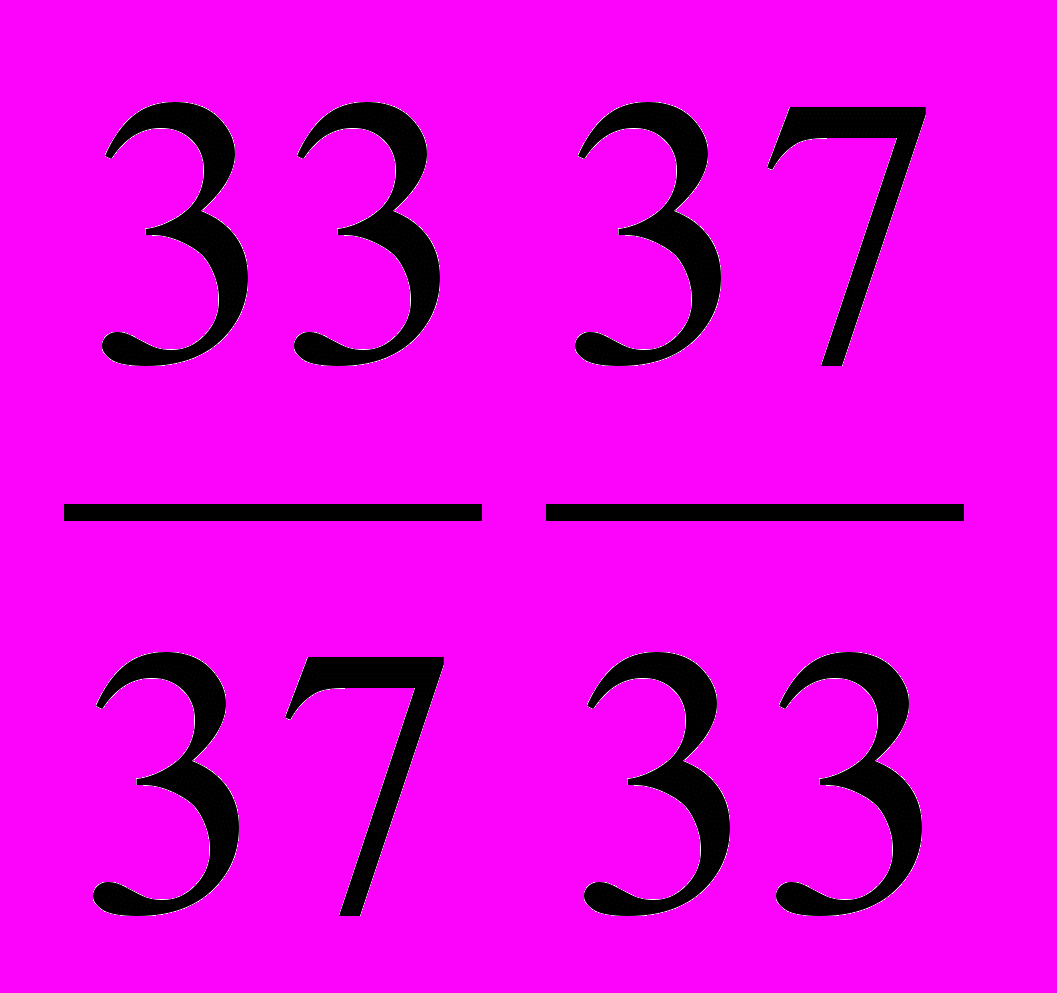
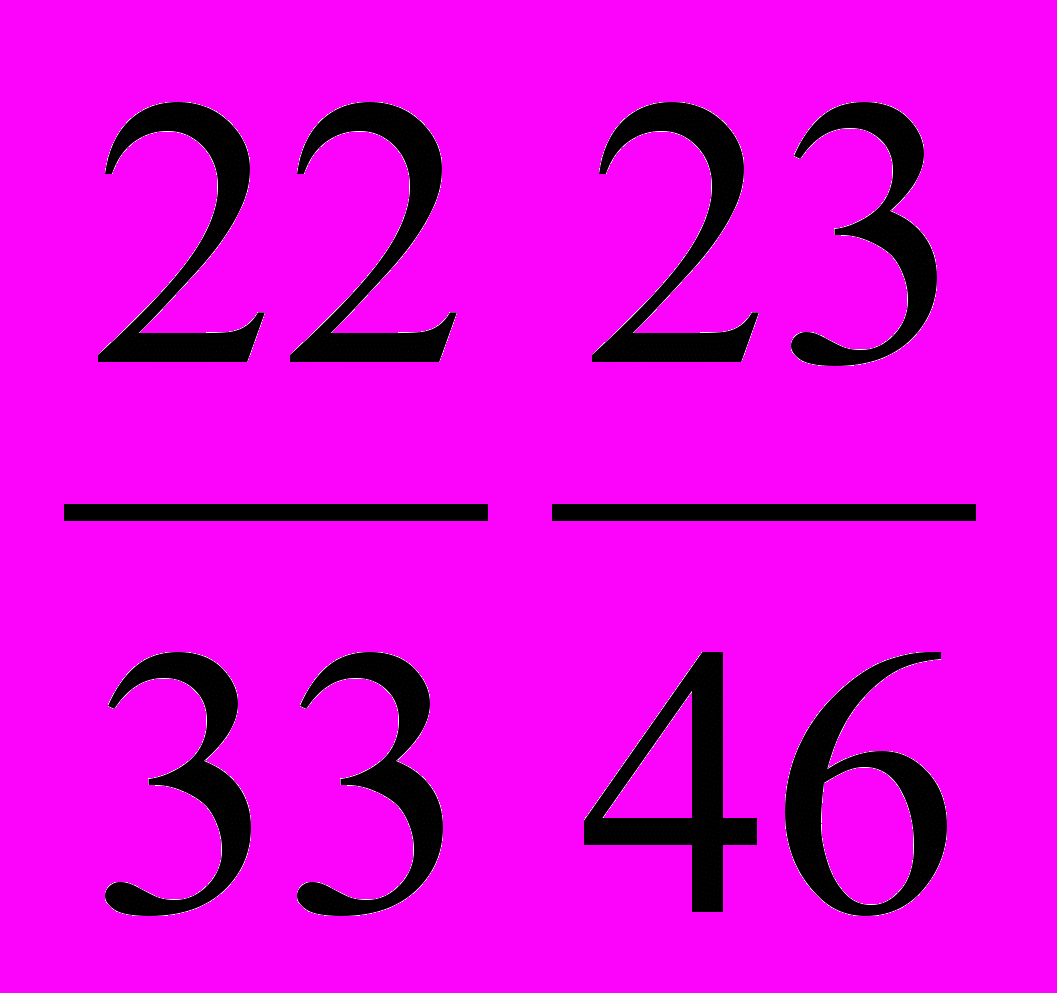
Движения продольной, поперечной и вертикальной подач включаются соответствующими кулачковыми муфтами. Коробка движения подач позволяет получить 18 различных скоростей движения подач. Уравнения для определения скоростей движения наименьшей и наибольшей подач, например продольной:


Диапазон изменения скоростей движения поперечных подач такой же, как и продольных, а вертикальных подач - 8,3...416,6 мм/мин.
Для быстрого перемещения стола, салазок или консоли используют более короткий участок цепи. Движение от электродвигателя, минуя коробку подач, передается сразу на ее последний вал XII через зубчатые колеса
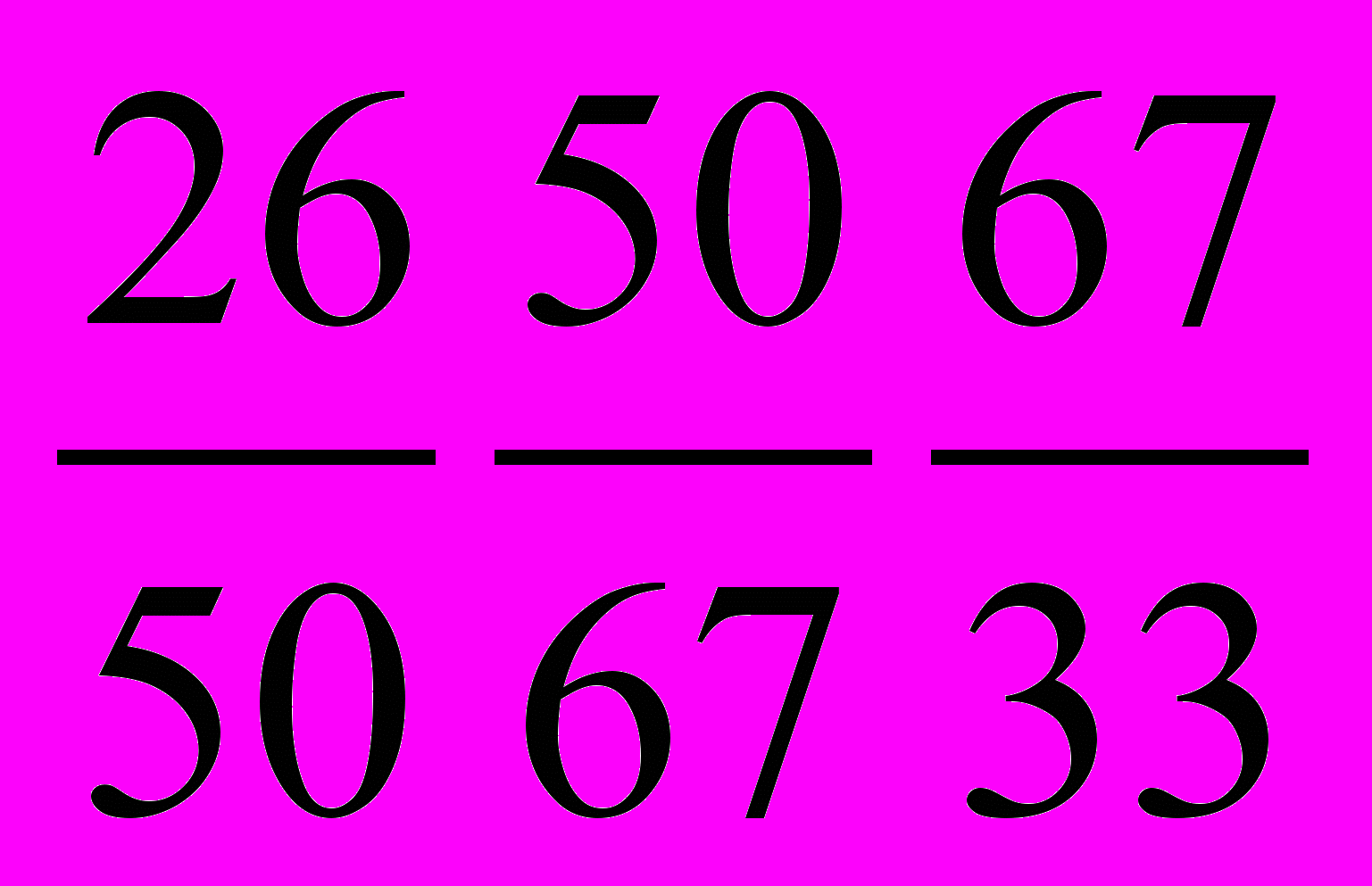
Скорость быстрого перемещения стола и салазок равна 3000 мм/мин, консоли - 1000 мм/мин.
Упражнение по изучению устройства консольно-фрезерного станка, его узлов. механизмов и органов управления проводится непосредственно на станке, за которым закреплен учащийся для выполнения следующих упражнений.. Особое внимание учащийся должен обратить на органы пуска и останова шпинделя и механизмов движения столов станка для предотвращения поломок и несчастных случаев.
Органы управления фрезерным станком, приспособления
и режущий инструмент, элементы режима резания
Оснащение рабочего места: фрезерный станок консольного типа; плакат общего вида фрезерного станка с органами управления, приспособления; наборы режущих и измерительных инструментов; машинные тиски, делительная головка, призмы, центра, прихваты, оправки, втулки, фрезы, штангенциркули, рейсмасы и др.; щетка-сметка, защитные очки.
Органы управления большинства моделей фрезерных станков являются кнопочно-рукояточными с дублирующим расположением, что дает возможность управлять станком, находясь спереди или сбоку от него.
На рисунке 2.5 показано размещение органов управления вертикального консольно-фрезерного станка модели 6Р12.
Станок имеет механизмы управления автоматическим циклом работы станка. Настройка станка на автоматический цикл работы обеспечивает движение узлов станка в определенной последовательности с определенной скоростью в требуемом направлении на необходимое расстояние.
В
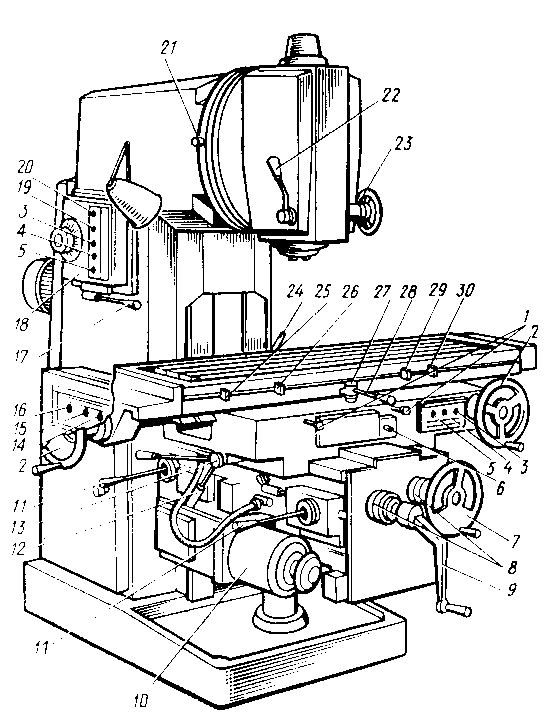
единичном производстве управление скоростью движения продольной подачи и быстрым перемещением стола производится вручную. В серийном производстве станки могут быть настроены на полуавтоматический скачкообразный (быстро вправо - рабочая подача вправо - быстро влево или вправо - стоп) и автоматический маятниковый (быстро вправо - рабочая подача вправо - быстро влево - рабочая подача влево - быстро вправо и т.д.) циклы обработки. Для этой цели в боковом Т-образном пазу стола устанавливают в определенной последовательности и на определенном расстоянии кулачки 25, 26, 29 и 30 (см. рис. 2.5), один из которых, воздействуя на выступы рукоятки 24 переключения продольного хода, реверсирует движение стола, другие, поворачивая маховик 23, включают быстрый ход стола.
1-зажимы стола; 2-маховики ручного продольного перемещения стола (дублирующие); 3-кнопки «Быстро стол» (дублирующие); 4-кнопки «Пуск шпинделя» (дублирующие); 5-кнопки «Стоп» (дублирующие); 6-переключатель ручного или автоматического управления продольным перемещением стола; 7-маховик ручного поперечного перемещения стола; 8-лимбы механизмов поперечных и вертикальных перемещений стола; 9-рукоятка ручного вертикального перемещения стола; 10-механизм переключения движения подач; 11-рукоятки включения поперечного и вертикального движения подач стола; 12, 13-зажимы салазок на направляющей; 14-переключатель направления вращения шпинделя «влево—вправо»; 15-переключатель насоса охлаждения «включено-выключено»; 16-переключатель включения станка в электросеть «включено-выключено»; 17-рукоятка переключения скоростей шпинделя; 18-механизм переключения зубчатых колес коробки скоростей; 19-кнопка «импульс шпинделя» (толчковая); 20-переключатель освещения; 21-механизм поворота головки (дублирующий); 22-зажим гильзы шпинделя; 23-маховик выдвижения гильзы шпинделя; 24-рукоятка для зажима консоли на станине; 25, 30-кулачки, определяющие величину хода стола и его реверс; 26, 29-кулачки, переключающие величину скорости движения подачи стола (быстро-рабочая подача); 27-звездочка механизма автоматического цикла; 28-рукоятка включения продольных перемещений стола
Рисунок 2.5 Органы управления и основные части вертикально-
фрезерного станка 6Р12
На рисунке 2.6 даны схемы установки кулачков для различных циклов работы фрезерного станка. Для полуавтоматического цикла работы расстановка кулачков на столе показана на рис. 2.6, а. При включении станка стол движется быстро вправо до тех пор, пока кулачок 3 не повернет звездочку 4, в результате чего стол продолжает движение в ту же сторону, но уже с медленной рабочей подачей. В конце хода стола кулачки 1 и 2, поворачивая одновременно соответственно звездочку 4 и рукоятку 5, включают быстрое обратное движение стола. В конце обратного хода стола кулачок 6 устанавливает рукоятку 5 в среднее положение и стол останавливается. Для повторения цикла работы станка необходимо снова нажать кнопку «Пуск». Кулачок 7 играет роль предохранителя (кулачки 21 и 26 на рис. 2.5) и никогда не должен сниматься со станка, так как он ограничивает крайнее положение стола.
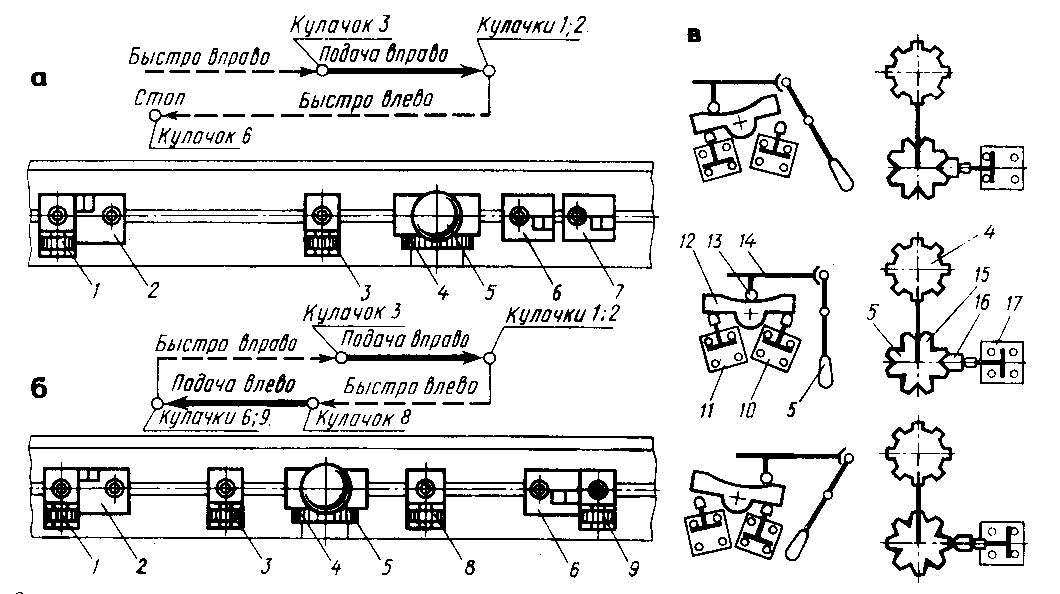
Рисунок 2.6 Схема установки кулачков для полуавтоматического
и автоматического циклов работы фрезерного станка
Автоматический маятниковым цикл работы станка обеспечивается расстановкой кулачков по схеме рис. 2.6, б. При включении станка стол движется быстро вправо до тех пор, пока кулачок 3 не подойдет к звездочке 4 и не повернет ее. После этого устанавливается медленная скорость движения рабочей подачи стола в ту же сторону. В конце хода стола кулачки 1 и 2, воздействуя одновременно на звездочку 4 и рукоятку ,5, реверсируют направление движения стола и включают ускоренное обратное перемещение. При обратном движении стола сначала кулачком 8 поворотом звездочки 4 устанавливают медленную скорость движения рабочей подачи стола, а в конце хода кулачки 6 и 9 реверсируют движение стола и включают ускоренное обратное перемещение. Далее цикл повторяется, прервать его можно нажатием кнопки «Стоп».
Правый и левый кулачки различаются лишь положением рычажков. При необходимости рычажки можно переставить в другую сторону. При работе с ручным управлением кулачки (кроме предохранительных) рекомендуется снимать или переставлять на нерабочую часть стола.
При одновременном фрезеровании комплекта заготовок, у которых обрабатываемые поверхности расположены на некотором расстоянии друг от друга, станок может быть настроен для работы по скачкообразному циклу: быстро вправо - рабочая подача вправо -быстро вправо - рабочая подача вправо и т. д.- быстро назад - стоп.
Схемы передачи движения от рукоятки 5 и звездочки 4 до соответствующих конечных выключателей 10, 11 и 17 приведены на рис. 2.6, е. Рукоятка 5, отклоняясь от среднего (нейтрального) положения, через тягу 14 и палец 13 качает рычаг 12, который нажимает на конечные выключатели 10 и 11, замыкая один и размыкая другие контакты, в результате чего осуществляется реверс (изменение направления вращения) электродвигателя подачи, а значит, и стола.
Звездочка 4 связана с дисковым кулачком 15, который имеет по окружности четыре глубокие и четыре неглубокие впадины, которые чередуются между собой. Шток 16, попадая при повороте кулачка в глубокую впадину или на наружную окружность кулачка, замыкает контакты конечного выключателя 17, в результате срабатывает электромагнит ускоренного хода стола станка. Когда шток находится в неглубокой впадине кулачка, контакты конечного выключателя разомкнуты и стол перемещается с рабочей (медленной) подачей.
Заготовка, устанавливаемая на фрезерном станке, должна занимать определенное положение по отношению к фрезе (шпинделю станка). Для закрепления заготовок применяются различные приспособления.
В простейшем случае заготовку закрепляют непосредственно на столе станка. Для крепления заготовки к столу пользуются прихватами (рис. 2.7), которые прижимают болтами 2, заведенными в Т-образные пазы стола.
На рис. 2.7, а показаны различные формы прихватов и способ закрепления заготовки прихватом (рис. 2.7, б). Прихват 3 одним концом опирается на заготовку 1, а другим на подкладку 4. Завертывая ключом гайку, прижимают один конец прихвата к подкладке, а другой к заготовке.
При закреплении заготовки прихватами необходимо соблюдать следующие правила: болт, крепящий прихват, надо устанавливать возможно ближе к заготовке; прихват должен опираться на подкладку одинаковой высоты с заготовкой или иметь изогнутый выступ для опоры на стол или подкладку меньшей высоты; конец прихвата, опирающийся на заготовку, не должен находиться над ее частью, которая не касается плотно поверхности стола; чем больший припуск фрезеруется с заготовки, тем сильнее должны быть затянуты болты.
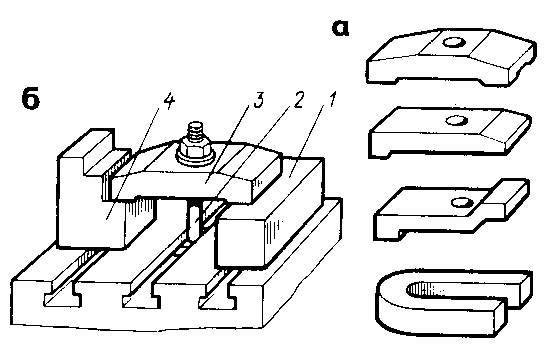
Рисунок 2.7 Прихваты для закрепления заготовок
на столе фрезерного станка
П
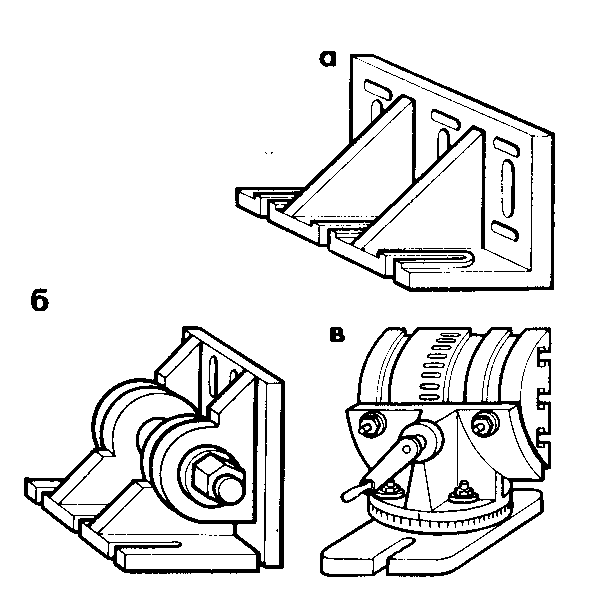
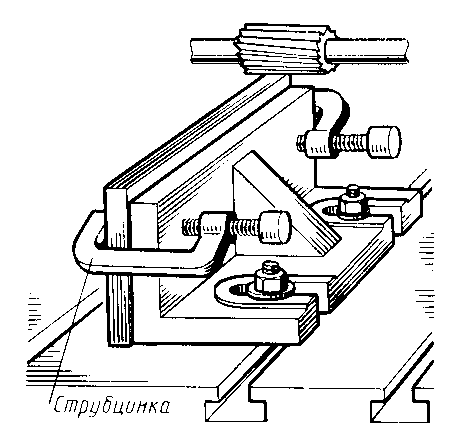
ри фрезеровании заготовки, две обрабатываемые стороны которой должны быть расположены под определенным углом, пользуются угловыми плитами (угольниками), которые могут быть жесткими (рис. 2.8, а), поворотными (рис. 2.8, б) и универсальными (рис. 2.8, в). Заготовку закрепляют на угловой плите посредством прихватов или струбцинок (рис. 2.9).
Рисунок 2.8 Угловые плиты для закрепления
заготовок на столе фрезерного станка
Рисунок 2.9 Закрепление заготовки на угловой плите
Цилиндрические заготовки для фрезерования в них шпоночных канавок, пазов и лысок удобно закреплять в призмах, которые вместе с обрабатываемой заготовкой крепят к столу станка прихватками (рис. 2.10).
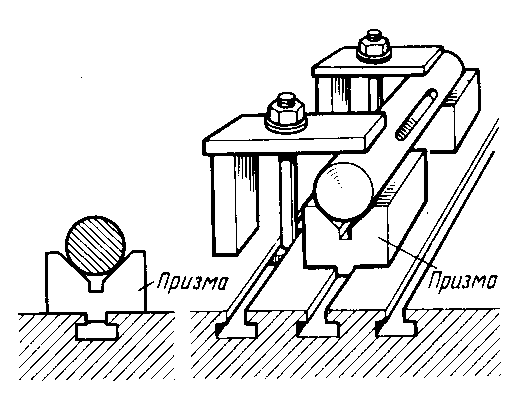
Рисунок 2.10 Закрепление вала в призмах
Для закрепления заготовок на фрезерных станках большое распространение получили различные по конструкции и размерам машинные тиски (рис. 2.11). Машинные тиски могут быть простыми неповоротными (рис. 2.11, а), поворотными (рис. 2.11, б), корпус которых можно поворачивать вокруг вертикальной оси, универсальными (рис. 2.11. в), позволяющими осуществлять поворот заготовки вокруг двух осей, и специальными (рис. 2,11, г) для закрепления в призме валов. Тиски своим основанием крепятся болтами на столе фрезерного станка. Специальные тиски можно устанавливать вертикально либо повернув на угол 90° в горизонтальной плоскости.
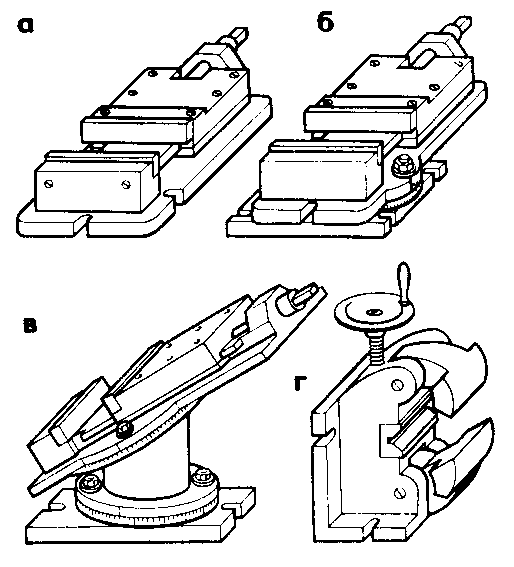
Рисунок 2.11
Тиски машинные
Поворотные и универсальные машинные тиски имеют поворотный корпус с градуированной шкалой для фрезерования плоскостей (скосов) под любым требуемым углом.
При закреплении заготовок в тисках надо развести губки на ширину, несколько большую ширины заготовки. Если высота заготовки меньше высоты губок тисков, то надо взять одну (рис. 2.12. а) или две (рис.2.12, б) стальные подкладки с правильно обработанными параллельными плоскостями и подложить их под заготовку, затем поворотом рукоятки тисков зажать заготовку и ударами медного молотка осадить ее. При неплотном прилегании заготовки к подкладкам или направляющим тисков ее следует осадить еще ударами медного молотка и дополнительно закрепить.
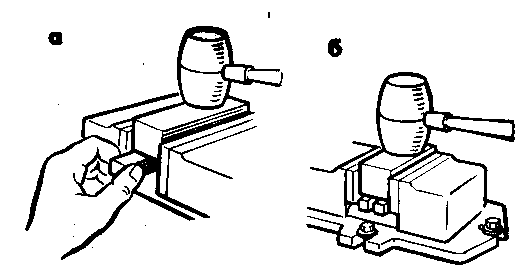
Рисунок 2.12 Установка заготовки в машинных
тисках
Если нижняя сторона заготовки не может служить установочной базой при фрезеровании верхней поверхности, то установку заготовки проверяют рейсмасом, добиваясь параллельности верхней поверхности заготовки и стола станка (рис. 2.13, а, б).
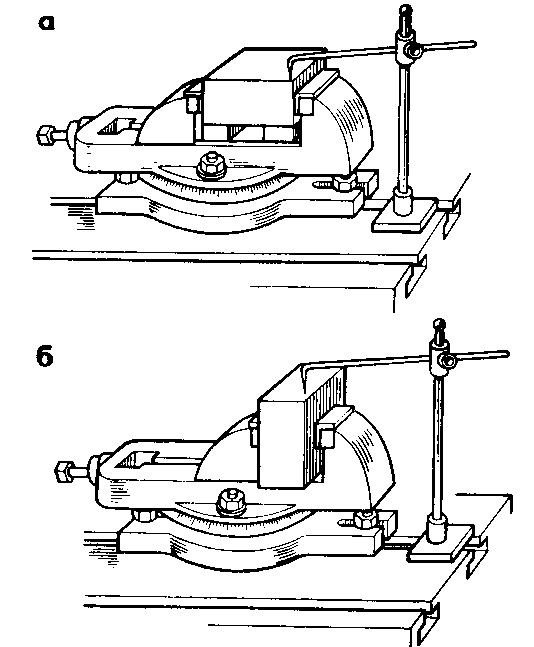
а - широкой стороны; б - узкой стороны
Рисунок 2.13 Проверка установки
заготовки рейсмасом
Для сокращения времени на установку, выверку и зажим заготовок на машиностроительных предприятиях применяют специальные зажимные приспособления, которые могут иметь быстродействующий винтовой, эксцентриковый, пневматический, гидравлический или пневмогидравлический зажимы. Особо целесообразно применять специальные приспособления при обработке больших партий одинаковых заготовок. Зажимные приспособления следует устанавливать на столе станка так, чтобы сила резания, возникающая при обработке заготовки, воспринималась неподвижными частями приспособления (неподвижной губкой тисков) и способствовала прижатию заготовки к опорной поверхности приспособления.
Направления вращения фрезы и движения подачи стола станка при фрезеровании цилиндрической (или дисковой) фрезой показаны на рис. 2.14, а, б; при фрезеровании торцовой (или концевой) фрезой - на рис. 2.14, в. г.
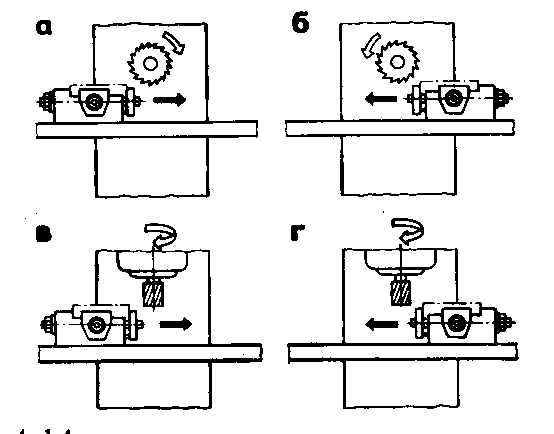
Рисунок 2.14 Направление вращения фрезы и
движения подачи при фрезеровании
Режущим инструментом, применяемым на фрезерных станках, являются фрезы. Режущие зубья фрезы могут быть расположены как на цилиндрической поверхности, так и на торце, причем каждый зуб представляет собой простейший резец (рис. 2.15, а).
Элементы зуба фрезы, геометрические элементы и основные поверхности, образуемые на обрабатываемой заготовке (рис. 2.15, б), мало чем отличаются от соответствующих элементов при работе обычным резцом при точении.
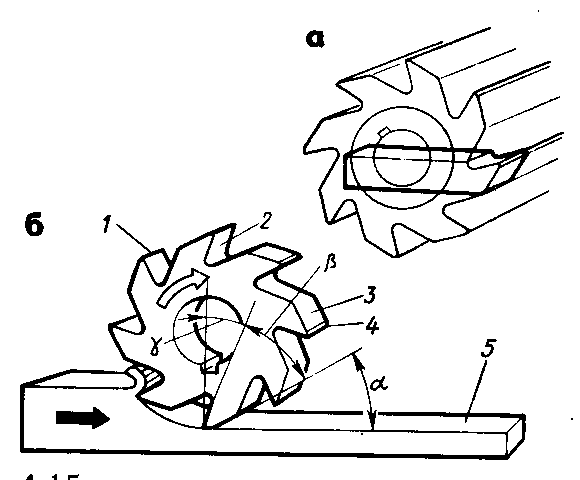
1 - режущая кромка; 2 - передняя поверхность; 3 - задняя поверхность; 4 - ленточка; 5 - обработанная поверхность заготовки
Рисунок 2.15 Геометрические элементы режущей
части цилиндрической фрезы
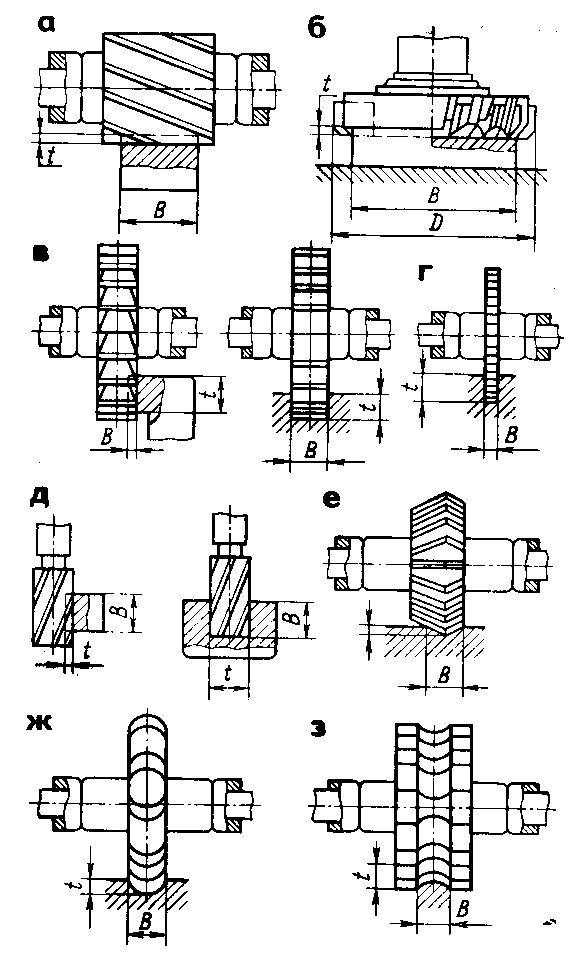
а - цилиндрические; б - торцовые; в - дисковые трехсторонние и пазовые; г - прорезные и отрезные; д - концевые; е - угловые; ж - фасонные с выпуклым профилем; з - фасонные с вогнутым профилем; t - глубина резания; B - ширина фрезерования; D - диаметр фрезы
Рисунок 2.16 Типы фрез и элементы срезаемого слоя металла
На рис.2.16, а...з показаны наиболее часто встречающиеся типы фрез и элементы срезаемого слоя металла.
По направлению зубьев различают фрезы прямозубые и с винтовыми (левыми или правыми) зубьями.
По конструкции зубьев фрезы бывают с острозаточенными и затылованными зубьями. В основном применяют фрезы с острозаточенными зубьями, так как они обладают большой стойкостью, обеспечивают меньшую шероховатость обрабатываемой ими поверхности и проще в изготовлении.
У затылованных фрез задняя поверхность зуба образуется путем ее затылования по определенной кривой (чаще по спирали Архимеда) на специальных затыловочных станках. Эти фрезы относятся к фасонным (канавочным, резьбовые, зуборезные и др.).

Рисунок 2.17 Схемы заточки зубьев фрезы
Фрезы с острозаточенными зубьями обычно затачивают по задним поверхностям (рис.2.17, а). По передней поверхности зуба заточку производят редко, но обязательно при первой заточке в процессе изготовления и при большом износе. Затылованные фрезы перетачиваются только по передней поверхности зуба, в результате чего она всегда остается радиальной и профиль режущей кромки фрезы сохраняется постоянным (рис. 2.17, б).
Фрезы делают цельными, составными, сборными (со вставными ножами из быстрорежущей стали или с пластинами твердых сплавов). Сборные фрезы более экономичны, так как корпуса их изготовляют из дешевой конструкционной стали и служат продолжительное время, а ножи после многократной переточки или поломки заменяют новыми комплектами (рис. 2.18, а. б).
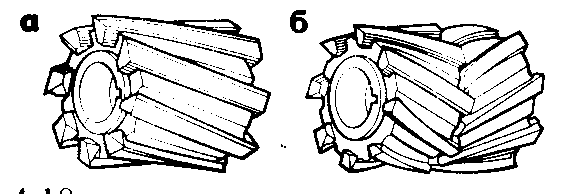
а - одинарная; б - спаренная
Рисунок 2.18 Цилиндрические сборные фрезы со вставными ножами
Геометрические элементы и углы заточки фрез определяют по аналогии с углами резцов в зависимости от обрабатываемого материала, материала зубьев фрезы и других условий обработки из соответствующих справочников.
Режимы резания при фрезеровании. Ширина фрезерования В измеряется в направлении оси фрезы. Она задается в чертеже (эскизе) заготовки. В случае обработки нескольких заготовок, закрепленных параллельно в одном зажимном приспособлении, ширина фрезерования равна ширине всех заготовок. При обработке набором фрез ширина фрезерования равна суммарной ширине всех сопряженных поверхностей.
Глубина резания t (глубина фрезерования, толщина срезаемого слоя) измеряется в плоскости, перпендикулярной оси фрезы. При повышенных требованиях к точности обработки и шероховатости поверхности обработку ведут в два перехода - один черновой и один чистовой. При снятии больших припусков возможна обработка за два черновых прохода.
Скорость движения подачи vs при фрезеровании определяют двумя взаимосвязанными между собой величинами: подачей на один зуб фрезы Sz (мм/зуб); подачей на один оборот фрезы So = Sz z (мм/об).
При черновом фрезеровании значение скорости движения подачи зависит от обрабатываемого материала, материала режущей части фрезы, мощности станка, жесткости системы станок-приспособление-инструмент-деталь и углов заточки фрезы. При чистовом фрезеровании скорость движения подачи зависит от шероховатости обработанной поверхности. При торцовом фрезеровании на выбор скорости подачи большое влияние оказывают форма стружки и способ установки торцовой фрезы относительно заготовки (рис, 2.19, а...г). Несимметричное фрезерование более производительно, чем симметричное.
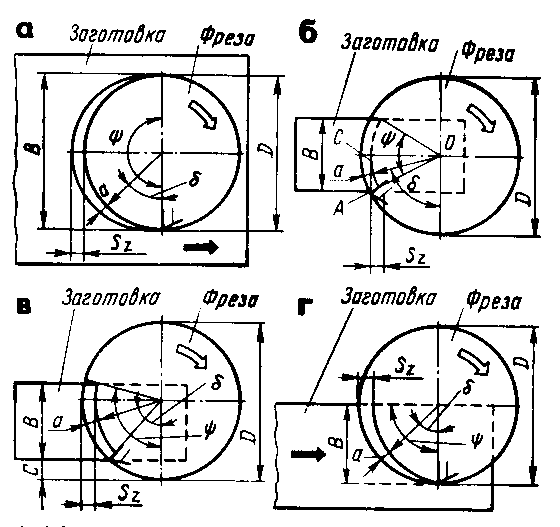
а - при полном симметричном фрезеровании; б - при неполном симметричном фрезеровании; в, г - при несимметричном фрезеровании
Рисунок 2.19 Форма стружки при фрезеровании торцовой фрезой
Настройку станка на требуемую скорость движения подачи и скорость главного движения резания (частоту вращения шпинделя» производят по данным, указанным в технологической документации или рекомендованным мастером для данного вида обрабатываемого металла, применяемого инструмента, глубины резания и шероховатости поверхности.
Скорость главного движения резания v при фрезеровании также может быть выбрана по общемашиностроительным нормативам режимов резания в зависимости от вида обработки, требуемого периода стойкости фрезы до затупления, материалов обрабатываемой заготовки и инструмента, выбранной скорости движения подачи и ряда других факторов.
Нормативы состоят из отдельных карт для торцовых, цилиндрических, концевых, дисковых, прорезных, шпоночных, полукруглых и угловых фрез при обработке наиболее часто встречающихся черных и цветных металлов и сплавов. Кроме того, в этих картах даются поправочные коэффициенты на скорость главного движения резания для измененных условий обработки, например для других механических свойств обрабатываемого металла, наличия литейной корки или окалины, измененных геометрических параметров и материала фрез и др.
По найденной скорости главного движения резания подсчитывают частоту вращения фрезы (шпинделя станка) (об/мин):
n = 1000v / (πD).
Найденную частоту вращения фрезы корректируют по кинематическим данным (паспорту) станка и затем подсчитывают действительную скорость главного движения резания (м/мин):
vд = πDnпас /1000.
Скорость движения подачи за одну минуту (минутную подачу) определяют по формуле
vs = Sм = Sz znпас,
после чего найденное значение vs корректируют по паспортным данным станка (Sм пас ) и далее подсчитывают действительную подачу на зуб:
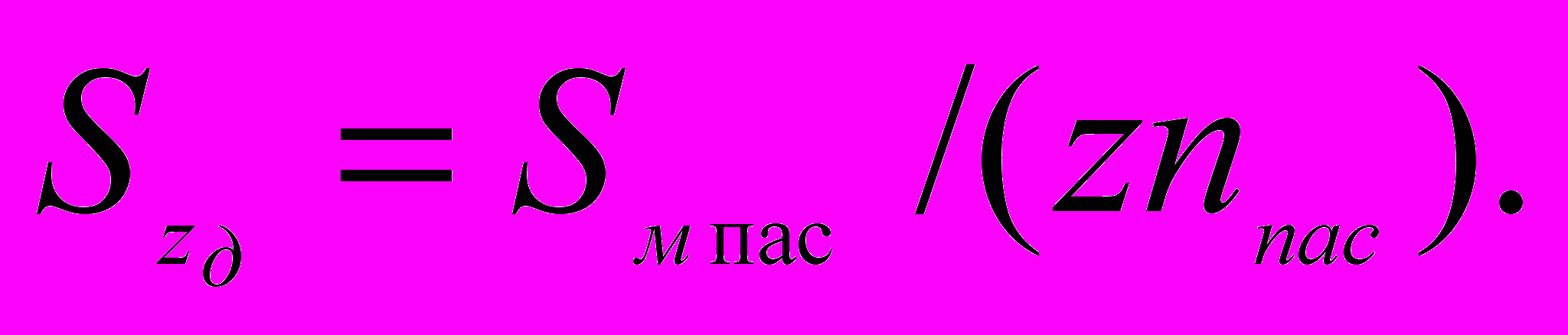
При корректировании по паспортным данным станка необходимо выбирать ближайшие меньшие значения частоты вращения шпинделя станка и скорости минутной подачи, чтобы фактические режимы резания не превышали выбранных по нормативам во избежание преждевременного износа фрезы и худшей шероховатости обработанной поверхности.
После установления режима резания определяют основное (машинное) время на фрезерование, в течение которого заготовка подвергается процессу снятия стружки. Основное (машинное) время (мин) при фрезеровании определяют по формуле, общей для всех видов обработки:
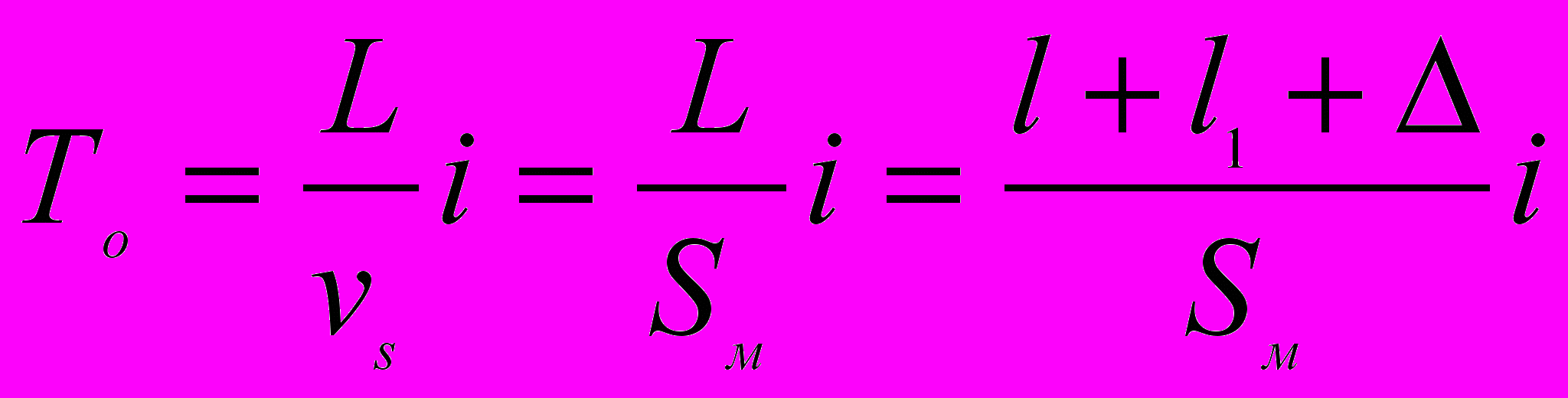
где L - длина перемещения заготовки (или инструмента) с учетом врезания и перебега,
мм;
vs = Sм - скорость движения подачи или минутная подача заготовки (или инструмента),
мм/мин;
l - длина обработанной поверхности, мм;
l1 - путь врезания, мм;
∆ = 1...5 мм - перебег (выход) фрезы.
На рисунке 2.20 показаны схемы для определения врезания l1 (мм) и перебега ∆ фрезы при различных способах фрезерования:
при работе цилиндрическими, дисковыми, отрезными и фасонными фрезами рис. 2.20, а (из треугольника ОКМ)
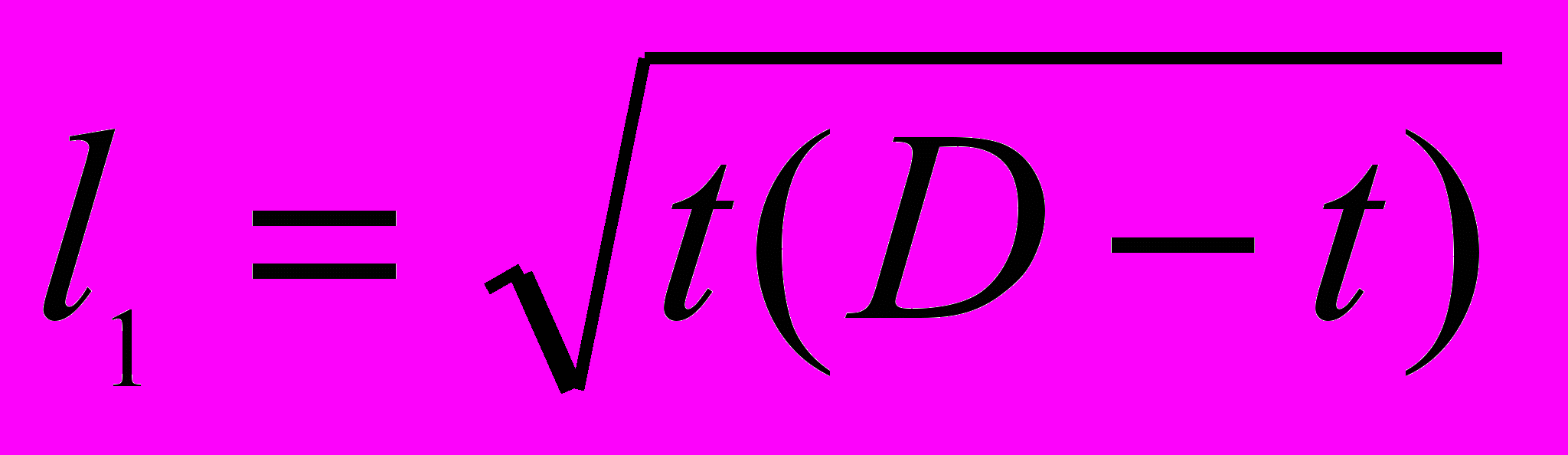
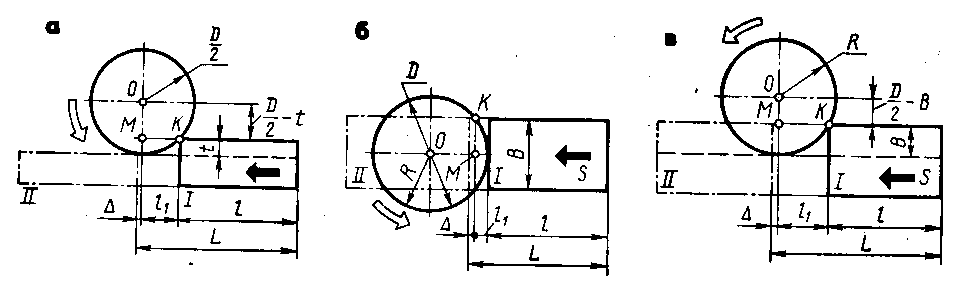
1 - начальное положение; II - конечное положение заготовки
Рисунок 2.20 Схемы элементов пути, проходимого заготовкой
при симметричной работе торцовыми и концевыми фрезами - рис. 2.20, б (из треугольника ОКМ)

при несимметричной работе торцовыми и концевыми фрезами - рис. 2.20. в (из треугольника ОКМ)
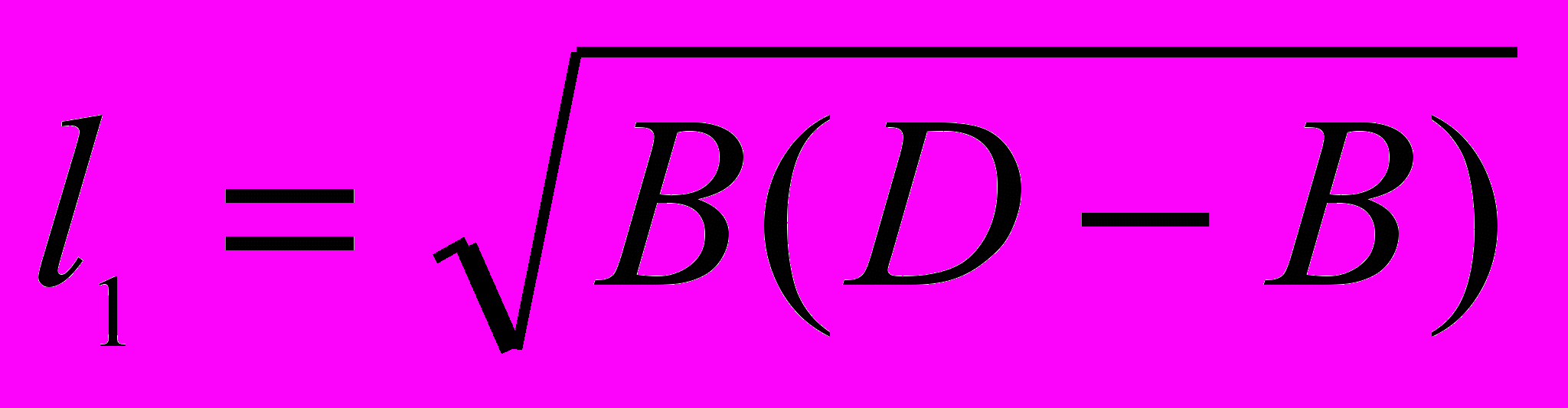
Перебег фрезы ∆ принимают 1...5 мм.
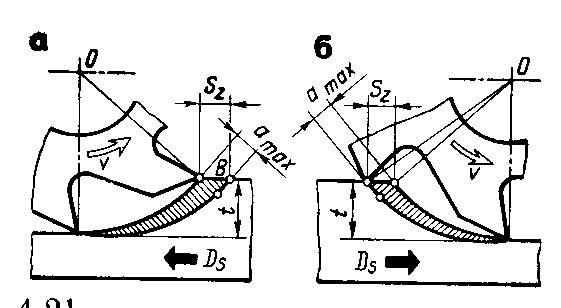
Рисунок 2.21 Способы фрезерования
Фрезерование может быть осуществлено двумя способами: против подачи (встречное фрезерование), когда направление подачи противоположно направлению вращения фрезы (рис. 2.21. а), и по подаче (попутное фрезерование), когда направления движения подачи и вращения фрезы совпадают (рис. 2.21, б). При встречном фрезеровании нагрузка на зуб фрезы возрастает от нуля до максимума, причем зубья фрезы работают из-под «корки», выламывая корку снизу, и стремятся оторвать заготовку от стола станка, что при больших сечениях среза приводит к дрожанию (вибрации) и ухудшению шероховатости обработанной поверхности. При попутном фрезеровании заготовка прижимается к столу, каждый зуб фрезы начинает резать максимальную толщину слоя. При наличии у заготовки окалины (корки) зуб ударяется о нее, что приводит к быстрому разрушению режущей кромки. Попутное фрезерование улучшает шероховатость обработанной поверхности и дает более высокую точность, уменьшает вибрации. Но для успешного применения попутного фрезерования необходимо плотное (без люфта) соединение ходового винта с разъемной гайкой стола, отсутствие корки или окалины на заготовках.
Упражнение. После вводной беседы учащийся знакомится с образцами различных типов фрез и их геометрическими параметрами, определяет режимы резания и основное (машинное) время для заданных условий обработки, устанавливает и закрепляет различные по форме и размерам заготовки на столе фрезерного станка с помощью прихватов, тисков и приспособлений. Затем, пользуясь различными органами управления станком, производит настройку на требуемую скорость движения подачи, частоту вращения шпинделя, глубину резания и длину хода стола с различными циклами работы.
Тема 2.2 Фрезерование плоских поверхностей
Оснащение рабочего места: горизонтально-фрезерный станок модели 6Р81 (или другой модели аналогичных габаритов) с защитным экраном; цилиндрические и торцовые фрезы; наборы прижимных прихватов; машинные тиски; оправки требуемого диаметра; штангенциркуль; рейсмас; штангенрейсмас; микрометр; масленка; шприц для смазки станка; ветошь; щетка-сметка; защитные очки; размеченные стальные и чугунные заготовки; чертежи на обрабатываемые детали; технологические карты с указанием режима резания.
Большинство деталей имеют поверхности в форме плоскостей, например направляющие станины станка, поверхность основания тисков, контрольные и разметочные плиты, поверхности установочных угольников, грани болтов и гаек, квадраты хвостовиков инструментов и т. п. Фрезерование плоских поверхностей можно производить главным образом цилиндрическими фрезами на горизонтально-фрезерных станках, а торцовыми и концевыми фрезами как на горизонтально-, так и вертикально-фрезерных станках.
Подготовка к обработке плоской поверхности на горизонтально-фрезерном станке состоит из следующих основных этапов и приемов:
1. Установить и закрепить фрезу, для чего:
поворотом рукоятки поставить хобот станка в крайнее переднее положение, отвернув предварительно зажимные винты (рис. 2.22, а);
снять серьгу, предварительно отвернув винт (рис. 2.22, б);
вставить оправку коническим концом в отверстие шпинделя, совместить пазы во фланце справки с сухарями на конце шпинделя и закрепить оправку затяжным винтом (шомполом). Конический хвостовик оправки должен плотно входить в коническое отверстие шпинделя (рис. 2,22, в).
надеть на оправку установочные кольца и фрезу, добиваясь того, чтобы фреза оказалась как можно ближе к станине станка, насколько это позволяют обрабатываемая заготовка и применяемое зажимное устройство (рис. 2.22, г). Следует обратить внимание на соответствие направления вращения шпинделя направлению винтовых канавок зуба фрезы. Если направление резания цилиндрической фрезы не совпадает с направлением вращения шпинделя, то следует снять фрезу с оправки и повернуть ее другим торцом.
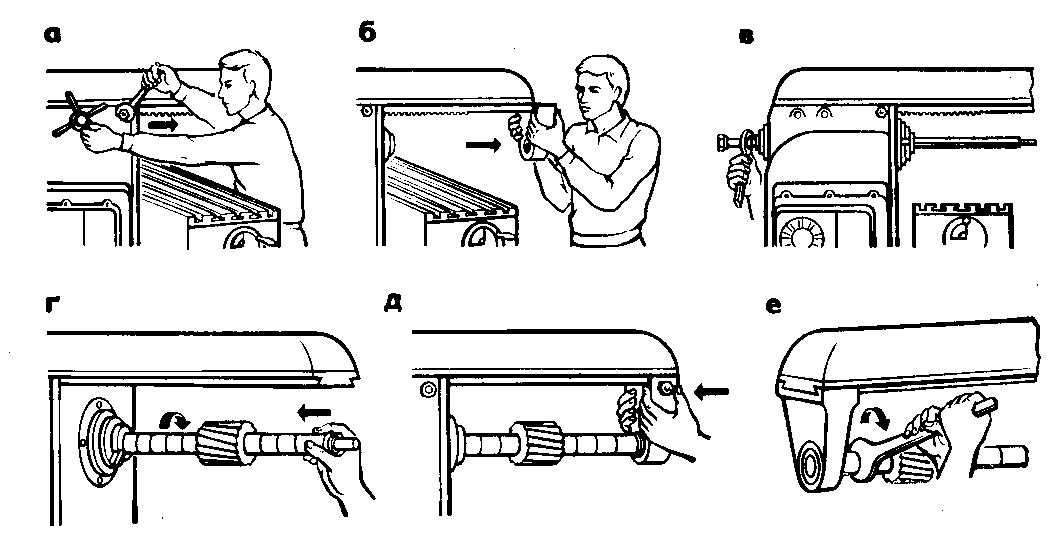
Рисунок 2.22 Приемы установки и закрепления фрезы на станке
При работе на горизонтально-фрезерном станке следует применять фрезы с левым направлением винтовых канавок при правом вращении шпинделя станка и, наоборот, фрезы с правым направлением винтовых канавок при левом направлении вращения шпинделя. Это объясняется тем, что в случаях с разноименным направлением винтовых канавок фрезы и направлением ее вращения осевая сила Рх направлена в сторону шпинделя, т.е. более жесткой опоры, в противном случае осевая сила Рх, вытягивает фрезу с оправкой из гнезда шпинделя и давит на менее жесткую опору-серьгу (табл. 2.1);
надев фрезу, надо надеть на оправку остальные установочные кольца и затянуть гайку на конце оправки (оставив открытой шейку оправки);
установить серьгу так, чтобы конец оправки (шейка) вошел в подшипник серьги (рис. 2.22, д);
закрепить фрезу на оправке, завернув ключом гайку (рис. 2.22, е);
закрепить хобот и смазать подшипник серьги;
проверить биение фрезы и оправки, для чего включить станок; если фреза бьет, остановить станок и исправить установку или заменить фрезу или оправку. Для проверки биения фрезы и оправки следует пользоваться индикатором, закрепленным в штативе.
2. Установить и закрепить на столе станка зажимное приспособление, необходимое для крепления заготовок определенных габаритных размеров и формы (машинные тиски, прихваты с болтами, угловая универсальная плита и др.). Затем установить заготовку.
3. Настроить станок на режим фрезерования, который состоит из следующих элементов: ширины фрезерования, глубины резания, скорости минутной подачи и скорости главного движения резания.
Ширина фрезерования В равна ширине обрабатываемой заготовки, а ширину фрезы берут несколько больше ширины фрезеруемой поверхности. Глубина резания t зависит от припуска на обработку h и количества проходов (черновых и чистовых). Подачу на зуб Sz назначают в зависимости от требуемой шероховатости поверхности детали и выбирают по нормативам режимов резания или по указанию мастера. Скорость главного движения резания v зависит от механических свойств материала обрабатываемой заготовки, качества ее поверхности, материала фрезы, скорости подачи, ширины и глубины фрезерования и также выбирается по нормативам режимов резания или по указанию мастера.
Таблица 2.1 Направление вращения шпинделя с осевой силы Рх
при работе цилиндрическими фрезами с винтовыми зубьями
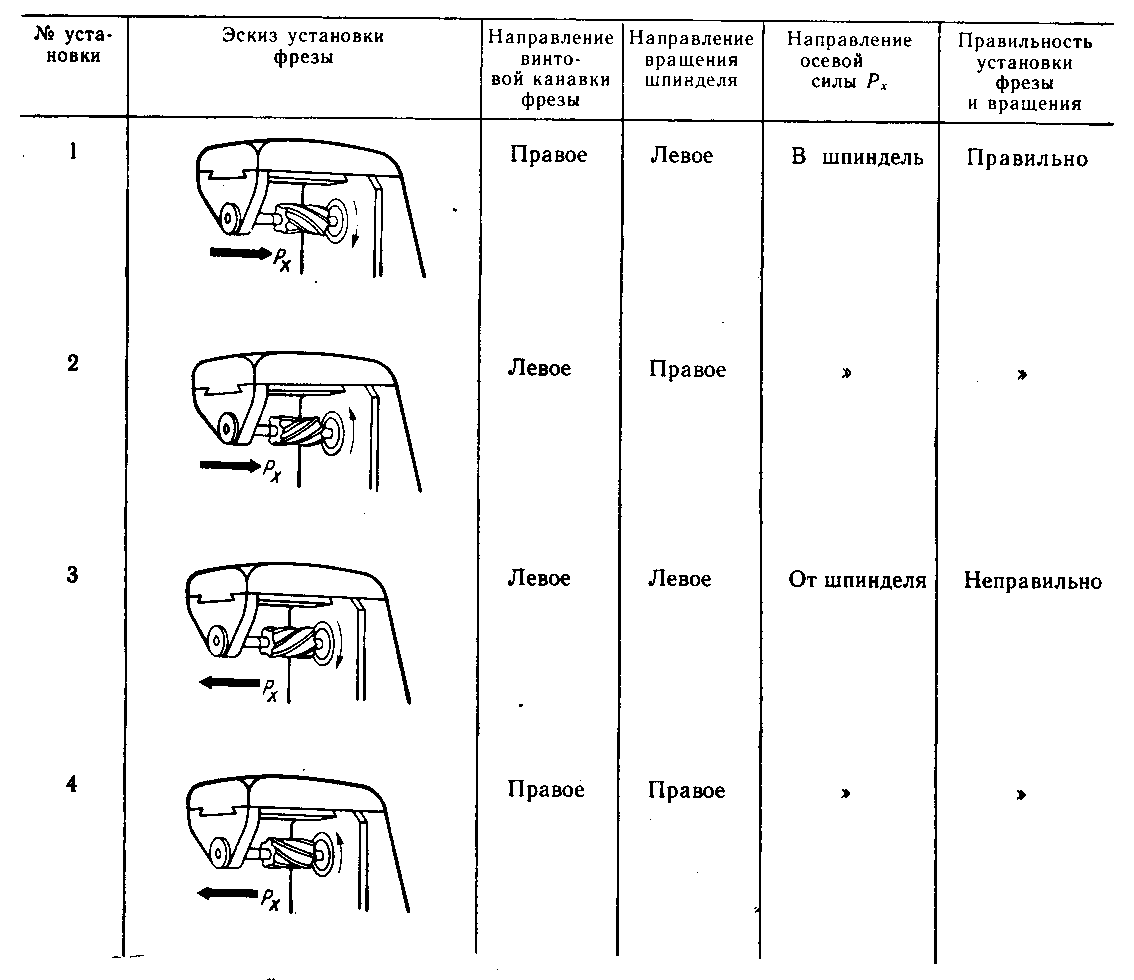
Далее в зависимости от диаметра фрезы Dф и принятой скорости резания определяют частоту вращения шпинделя и скорость минутной подачи по формулам, и принимают ближайшее меньшее значение, которое имеется на данном станке.
Настройку коробки скоростей и подач на заданную частоту вращения шпинделя и скорость минутной подачи стола осуществляют путем установки рукоятки переключения скоростей и подач в соответствующие положения.
4. Установить стол на глубину резания t, для чего ослабить затяжку стопорных винтов (зажимов) стола, при вращающемся шпинделе осторожно подвести вручную стол вместе с закрепленной заготовкой под фрезу до момента легкого касания. Ручным перемещением стола в продольном направлении вывести заготовку из-под фрезы.
Вращением рукоятки вертикальной подачи (см. поз. 9 на рис. 2.5) поднять стол на высоту, равную глубине резания. Отсчет перемещения стола производят по лимбу, т.е. кольцу с делениями. Отсчет по лимбу можно вести от любого деления шкалы, но для удобства и упрощения отсчета, после того как фреза коснулась обрабатываемой заготовки, лимб следует поставить в нулевое положение, т.е. риску лимба с отметкой 0 совместить с визирной риской.
Ценой деления лимба называется расстояние, на которое переместится стол станка, если рукоятку винта подачи стола повернуть на одно деление лимба. Если, например, цена деления лимба равна 0,05 мм и лимбовое колесо имеет 40 делений, то за один оборот рукоятки ручного подъема стола он переместится на 0,05 х 40 = 2 мм. Чтобы поднять стол на 3 мм, нужно повернуть лимб на 3:0,05 = 60 делений, т.е. полтора оборота.
Подводить лимб до нужного деления надо очень плавно и по возможности без рывков.
Установку стола станка на требуемую глубину резания можно выполнить по разметке, т.е. по линиям, нанесенным на боковых сторонах заготовки. Размеченную заготовку устанавливают в тиски или другое зажимное устройство так, чтобы линия разметки была горизонтальна и выступала над губками тисков по возможности одинаково с обеих сторон. Окончательное закрепление заготовки производят после проверки установки ее с помощью иглы рейсмаса, проводя его иглой (чертилкой) вдоль линии разметки (рис. 2.23) и выравнивая заготовку ударами молотка.
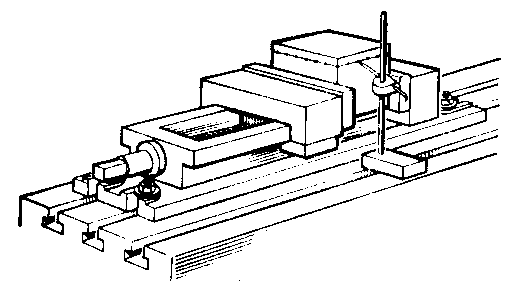
Рисунок 2.23 Установка размеченной заготовки в
машинные тиски с помощью рейсмаса
Установку на глубину резания по линии разметки производят пробными проходами так, чтобы припуск срезался до половины накерненных углублений.
Для установки глубины резания можно использовать готовые детали, а также установы («габариты»), которые устанавливаются на столе станка в непосредственной близости от обрабатываемой заготовки (рис. 2.24, а...в).
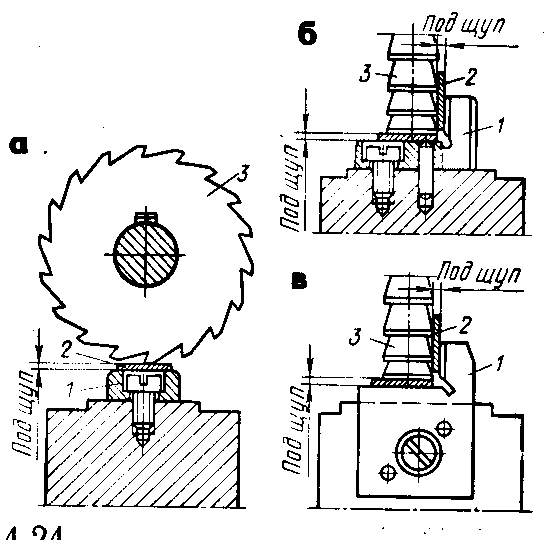
а - высотного, б - углового, в - торцового
Рисунок 2.24 Примеры применения установов ("габаритов")
Установ 1 представляет собой стальную закаленную пластину или угольник (иногда призму), закрепленную винтами на корпусе приспособления. Между установом и режущей кромкой зуба фрезы 3 оставляют зазор «под щуп», в который помещают мерный щуп 2 толщиной 3...5 мм. Если обработку одной и той же поверхности производят за два прохода, предварительный и окончательный, то для установки стола на требуемую глубину резания от одного и того же установа применяют щупы разной толщины, а разница их толщины равна глубине резания окончательного прохода. Установы чаще применяют при фрезеровании уступов, канавок, пазов и т.п.
После установки фрезы на требуемую глубину резания застопорить консоль и салазки поперечной подачи и установить кулачки включения механической подачи на требуемую длину фрезерования.
После окончания наладки и настройки станка плавным вращением маховика продольной подачи стола (см. поз, 2 на рис. 2.5) подвести обрабатываемую заготовку к фрезе. Не доводя 5 мм до края заготовки, включить станок, механическую подачу, охлаждение и приступить к работе.
По окончании прохода выключить продольную подачу стола, охлаждение и вращение фрезы, удалить щеткой стружку, а стол немного опустить, чтобы не испортить фрезой обработанной поверхности при обратном ходе, затем отвести стол вручную в исходное положение и измерить штангенциркулем размеры обработанной детали, которые должны соответствовать размерам, заданным на чертеже (эскизе) или в операционной карте. В случае необходимости произнести исправление размера путем дополнительного прохода.
При фрезеровании плоскости за несколько рабочих ходов (проходов) станок можно настроить на автоматический цикл работы, для чего в боковом Т-образном пазу стола установить в определенной последовательности и на определенном расстоянии кулачки.
Прямолинейность обработанной поверхности заготовки проверяют измерительной линейкой, параллельность противоположных плоскостей - штангенциркулем или микрометром, а перпендикулярность боковым поверхностям и торцам - угольником или универсальным угломером.