Учебное пособие для студентов среднего профессионального образования Специальность 1701 "Монтаж и техническая эксплуатация промышленного оборудования (по отраслям)"
Вид материала | Учебное пособие |
- Учебное пособие для студентов нефтехимических колледжей и техникумов Специальность, 3210.24kb.
- Программа и контрольные задания для студентов заочного отделения Специальность: 1701, 688.94kb.
- Государственный образовательный стандарт среднего профессионального образования государственные, 1346.06kb.
- Федеральный государственный образовательный стандарт среднего профессионального образования, 1074.58kb.
- Методические указания и контрольные задания для студентов заочной формы обучения гоу, 2389.4kb.
- Методические указания и контрольные задания для студентов заочного отделения специальность:, 848.08kb.
- «Материаловедение», 179.95kb.
- Формирование профессионально-значимых качеств личности в условиях личностно-ориентированного, 51.94kb.
- Система управления качеством подготовки техников по специальности 150411 – Монтаж, 102.4kb.
- Примерная программа профессионального модуля проведение подземного ремонта скважин, 226.39kb.
Контрольные вопросы:
- Расскажите о конструктивной компоновке токарно-винторезного станка?
- Как оборудуется рабочее место токаря?
- Какая связь между организацией рационального рабочего места токаря и
безопасностью его труда?
- Перечислите основные виды токарной обработки?
- Какой режущий инструмент применяют при обработке на токарных станках?
- Как крепится режущий инструмент на токарно-винторезных станках?
- Расскажите о приспособлениях для крепления заготовок и вспомогательном
инструменте для токарных станков?
Тема 1.2 Черновое и чистовое обтачивание цилиндрических
поверхностей с установкой заготовки в патроне и центрах
Студент должен
знать:
- устройство патрона;
- разновидности центров.
уметь:
- устанавливать кулачки в патроне;
- закреплять заготовки в патроне и центрах;
- пользоваться лимбами продольной и поперечной подачи;
- вести черновое и числовое обтачивание цилиндрических поверхностей;
- осуществлять контроль обработки.
Оснащение рабочего места: токарно-винторезный станок 1К62; патрон трехкулачковый; планшайба; центры; хомутик; плакаты; образцы токарных работ; набор резцов (проходные, упорные и подрезные); набор измерительных инструментов для контроля наружных цилиндрических поверхностей (кронциркуль, штангенциркуль с отсчетом по нониусу 0,1 мм, измерительная линейка); чертежи обрабатываемых деталей; технологические карты с указанием режима резания (скорость резания или частота вращения шпинделя, подача и глубина резания); стальные и чугунные заготовки диаметром 60…100 мм и длиной до 150 мм, крючок для отвода и удаления стружки; защитные очки; щетка; масленка; шприц; ветошь.
Обтачивание цилиндрических наружных поверхностей, уступов и канавок на заготовках подразделяется на предварительное (обдирочное), когда достигаются 12-й квалитет точности выполнения работ (5-й класс точности) и шероховатость поверхности с параметрами R z = 40…160 мкм, и окончательное обтачивание, в результате чего достигаются 9…11-й квалитеты точности выполнения работ (3…4-й классы точности) и шероховатость поверхности с параметрами Rа 0,8…2,5 мкм. Приемы выполнения работ подробно разбираются на соответствующих занятиях по обтачиванию наружных поверхностей и отрезке заготовок.
Упражнение по предварительному обтачиванию наружной цилиндрической поверхности с ручным движением подачи резца при установке заготовки в трехкулачковом самоцентрирующемся патроне заключается в следующем:
- Установить трехкулачковый патрон на шпиндель станка.
- Расположить на рабочем месте весь необходимый режущий, измерительный и вспомогательный инструмент, чертеж детали и технологическую документацию.
- Установить и закрепить проходной резец в резцедержателе.
- Настроить коробку скоростей станка на требуемую частоту вращения шпинделя n (об/мин) по скорости главного движения резания ν (м/мин), указанной в технологической документации или рекомендованной мастером для данного вида обрабатываемого металла, применяемого инструмента, глубины резания и скорости движения подачи. Частоту вращения шпинделя станка определяют по формуле
n=1000 v/ (π D) или n = 318 v/D.
Скорость главного движения резания может быть назначена по различным материалам по выбору режимов резания.
При работе с измененными условиями резания на скорость главного движения резания, выбранную по справочникам, надо вводить поправочные коэффициенты, учитывающие другую марку металла, корку или окалину на обрабатываемой заготовке, измененные углы заточки режущей части инструмента, применение охлаждения и т.п.
- Проверить (измерить штангенциркулем или линейкой) соответствие размеров полученных заготовок чертежу обрабатываемых деталей. Для определения припусков на предварительную и окончательную обработку необходимо пользоваться специальными таблицами припусков на механическую обработку. По результатам замеров определить требуемые глубину резания, на которую следует подать резец, и число проходов.
- Установить резец на требуемую глубину резания, для чего подвести его ручным движением подачи к вращающейся заготовке до соприкосновения вершины резца с ее поверхностью и затем переместить резец вправо так, чтобы его вершина находилась на расстоянии 8…10 мм от торца заготовки (рис. 1.45, а).
- Выключить вращение шпинделя.
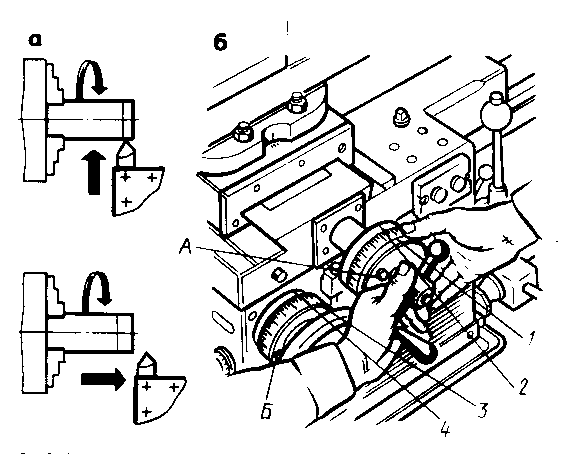
1 - кольцо лимба поперечной подачи; 2 - нулевой штрих для лимба поперечной подачи; 3 - кольцо лимба продольной подачи; 4 - нулевой штрих для лимба продольной подачи; А, Б - стопорные винты
Рисунок 1.45 Прием установки резца на требуемую
глубину резания
- Подать резец на требуемую глубину резания по лимбу поперечной подачи, для чего, удерживая рукоятку винта левой рукой , правой повернуть кольцо 1 лимба до совпадения его нулевого штриха 2 с риской и закрепить лимб стопорным винтом А (рис. 1.45, б), после чего подать резец по лимбу на требуемое количество делений и вновь установить лимб на нулевое деление.
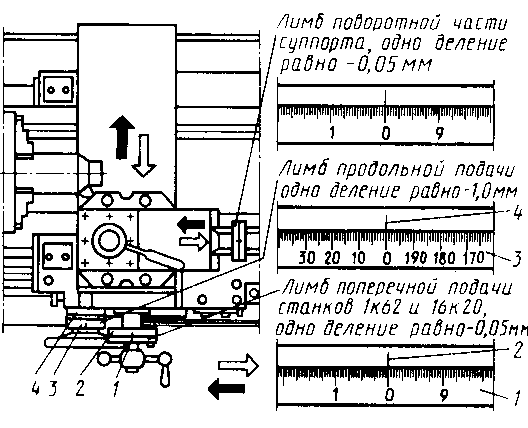
Рисунок 1.46
Цена деления лимбов суппорта токарно-винторезного станка 1К62
На рисунке 1.46 показаны кольца лимбов 1 и 3, нулевые штрихи 2 и 4 и цена делений лимбов суппорта токарно-винторезного станка 1К62. При пользовании лимбом поперечной подачи надо помнить, что цена деления лимба равна 0,05 мм на диаметр, следовательно, при повороте лимба на одно деление резец подается на глубину резания t=0,025 мм, а диаметр наружной поверхности уменьшится не на 0,025 мм, а на 0,05 мм. Точный поворот рукоятки лимба в нужное положение следует делать осторожно, легким ударом руки по рукоятке на подходе к требуемому делению (рис. 1.47, а). Если же лимб случайно все-таки повернули на большее число делений, то для исправления ошибки нельзя поворачивать рукоятку в обратном направлении до совпадения с требуемой риской (рис. 1.47, б). Рукоятку необходимо повернуть на полный оборот назад и только затем вновь подвести к нужному делению (рис. 1.47, в). На отработку этого приема необходимо обратить особое внимание, так как он применяется при работе на большинстве металлорежущих станков (фрезерных, строгальных, шлифовальных и др.).
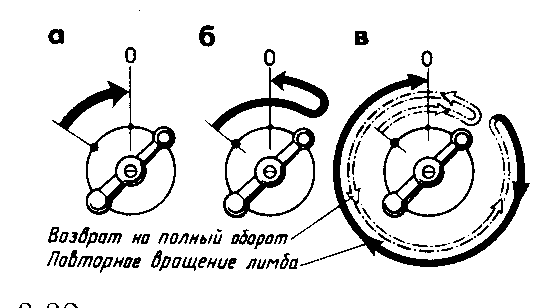
Рисунок 1.47 Правила вращения
рукоятки с лимбом
- Включить вращение шпинделя.
- Обточить поверхность заготовки на длину 3…5 мм с ручной подачей резца, осуществляя равномерное вращение маховика фартука суппорта против хода часовой стрелки.
- Отвести резец от заготовки и переместить в исходное положение, выключить вращение шпинделя, измерить диаметр обработанного участка заготовки штангенциркулем. Если диаметр получился больше заданного размера, необходимо подсчитать, на сколько делений лимба движения поперечной подачи каретки суппорта нужно подать резец, чтобы получить требуемый размер диаметра обработанной поверхности, после чего выполнить вторичный проход и вновь измерить полученный размер. При получении требуемого размера диаметра приступают к обработке заготовки на заданную длину, добиваясь равномерного перемещения суппорта ручной подачей. По окончании обтачивания необходимо резец отвести от обработанной поверхности заготовки движением продольной подачи вправо возвратить в исходное положение. Выключить станок, открепить и снять обработанную заготовку.
Упражнение по обтачиванию наружной цилиндрической поверхности с механической подачей резца при установке заготовки в трехкулачковом самоцентрирующемся патроне заключается в выполнении приемов, предусмотренных в предыдущем упражнении. При получении требуемого размера диаметра путем съема пробной стружки на длине 3…5 мм, как описано выше, приступают к обработке заготовки на заданную длину с механической подачей резца, для чего необходимо:
- Настроить станок на скорость движения прямой продольной подачи, величина которой указана в технологической документации, в справочниках по режимам резания или рекомендована мастером для данного вида обработки. При предварительной (черновой) обработке, когда к качеству обработанной поверхности не предъявляют высокие требования, можно выбирать большую скорость движения подачи. При окончательной обработке, когда требуется получить поверхности определенной шероховатости, выбирают меньшую скорость движения подачи.
- Включить вращение шпинделя станка.
- Включить прямую продольную подачу и обточить заготовку на требуемую длину. Для выдерживания заданной длины обработки применяют следующий прием: стержень глубинометра штангенциркуля выдвигают на требуемую длину и концом штанги упирают в торец заготовки. Резец перемещают до совмещения его вершины с концом стержня глубинометра (рис. 1.48, а). Затем поперечной подачей резец перемещают до тех пор, пока его вершина немного врежется в заготовку и обозначится круговая риска, до которой и следует обтачивать заготовку (рис. 1.48,б). При подходе резца к риске на расстоянии 2…3 мм необходимо выключить механическую продольную подачу, а резец довести до риски вручную, после чего отвести его от обработанной поверхности и выключить станок. Это упражнение можно выполнить, применяя лимб продольной подачи.
- Измерить длину обработанной поверхности линейкой (рис. 1.48, в) или стержнем глубинометра штангенциркуля (рис.1.48, г), диаметр – штангенциркулем с отсчетом по нониусу 0,1 мм (рис. 1.48, д). Технику измерения деталей см. 1 часть.
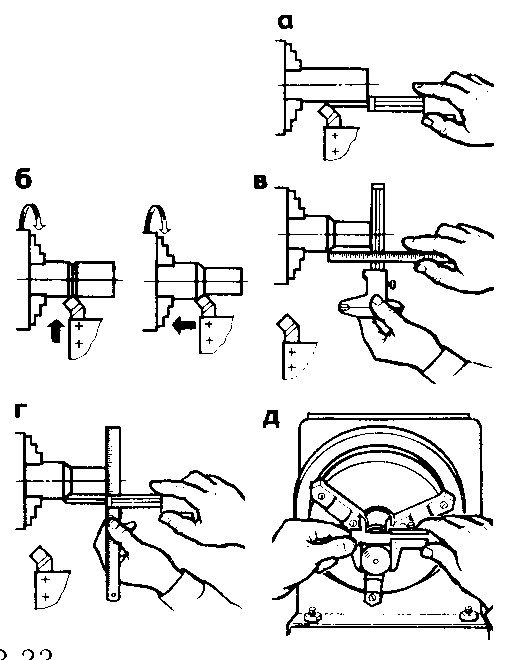
Рисунок 1.48 Приемы обтачивания цилиндрической
поверхности на заданную длину
Для выдерживания заданной длины обработки применяют также упоры. Продольный упор ограничивает продольное перемещение суппорта. Упор закрепляют болтами на передней направляющей станины, обеспечивая определенную длину перемещения суппорта. Как только суппорт дойдет до упора, от перегрузки автоматически выключается продольная подача. При обтачивании ступенчатого вала вместо постоянного упора применяют мерные прутки или плиты и многопозиционные упоры, меняя которые можно обеспечить обработку каждой ступени валика на требуемую длину и диаметр. Применять упоры можно только на станках с автоматическим выключением подачи при перегрузке.

1 - упор; 2 - крепежные болты; 3 - винт упора; 4 - диск поворотный; 5 - барабан; 6 - винты упорные мерные; 7 - регулировочная головка винта
Рисунок 1.49 Продольный многопозиционный упор
На рисунке 1.49 показан многопозиционный продольный упор для обработки ступенчатых деталей в серийном производстве. Для обтачивания очередной ступени заготовки на заданную длину диск 4 с установленными на нем винтами 6 поворачивают по ходу часовой стрелки на четверть оборота. Для выдерживания заданных размеров диаметров применяют поперечные упоры, устанавливаемые на поперечные нижние салазки суппорта станка.
Упражнение по обтачиванию наружных цилиндрических поверхностей длинных заготовок с поджатием задним центром можно выполнять двумя способами.
Первый способ. Заготовку с предварительно обработанными центровыми отверстиями установить одним концом в трехкулачковом самоцентрирующемся патроне, другим на задний центр и поджать пинолью задней бабки.
Затем обточить конец, расположенный у заднего центра, на длину 40…50 мм, переставить заготовку обточенным концом в патрон, другим на задний центр (рис. 1.50) и закончить обработку всей поверхности вала.
Второй способ. Заготовку с предварительно обработанными центровыми отверстиями и закрепленным хомутиком устанавливают в поводковый патрон на передний и задний центры и поджимают пинолью задней бабки (рис. 1.51, а). Затем необходимо обточить не менее 2/3 длины заготовки, измерить диаметры d1 и d2 обработанной поверхности заготовки. Если имеется конусность (d1≠d2), то перемещением корпуса задней бабки в поперечном направлении устранить ее. Переставить хомутик на обработанный конец заготовки, установить заготовку необработанным концом к заднему центру и обточить окончательно (рис. 1.51, б).
Для обработки цилиндрической поверхности заготовки полностью за один установ необходимо вместо поводкового патрона и хомутика применить специальный передний центр (рифленый, плавающий с рифленым поводком, самозажимной или обратный) и задний центр – вращающийся.
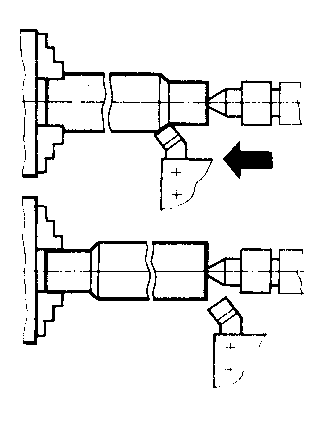
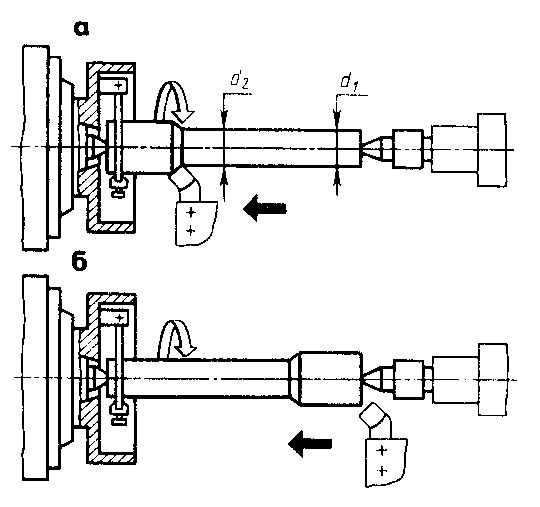
Рисунок 1.50 Обтачивание заготовок, закрепленных в патроне с поджатием задним центром
Рисунок 1.51 Обтачивание заготовок
в центрах
Упражнение по обтачиванию наружных цилиндрических поверхностей с уступами (ступенчатых валов) заключается в выполнении приемов, предусмотренных в предыдущих упражнениях, и подразделяется на предварительную обработку без подрезания торцов поверхности и окончательную с подрезанием торцовых поверхностей. Предварительное обтачивание цилиндрических поверхностей с уступами производят проходным правым резцом с главным углом в плане φ = 45 0. После обработки 1-й ступени на требуемую длину и диаметр наносят вторую круговую риску (рис. 1.52, а), устанавливают резец на требуемую глубину резания и производят обработку 2-й ступени (рис. 1.52.,6).
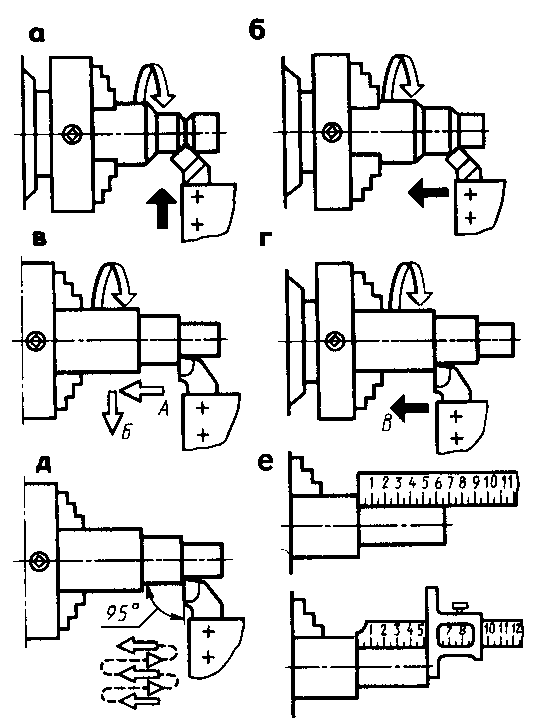
Рисунок 1.52 Приемы обтачивания цилиндрических
поверхностей с уступами
Окончательную обработку поверхностей производят проходным упорным резцом с главным углом в плане φ = 90 0, для чего цилиндрическую ступенчатую заготовку устанавливают и закрепляют в трехкулачковом самоцентрирующемся патроне, проходной упорный резец ручным движением поперечной подачи перемещают до соприкосновения вершины головки резца с поверхностью заготовки, обеспечив требуемую глубину резания для получения заданного меньшего диаметра вала, затем за один проход продольной ручной подачей по стрелке А протачивают 1-ю ступень на длину, указанную на чертеже (рис. 1.52, в). Отводят резец от отработанной поверхности заготовки движением поперечной подачи по стрелке Б, устанавливают вершину резца на размер, обеспечивающий получение следующего диаметра вала, и с движением продольной ручной подачей по стрелке В (рис. 1.52,г) протачивают 2-ю ступень на требуемую длину, после чего снова отводят резец и выключают станок.
После обработки каждой ступени вала измеряют длину ступени (рис. 1.52, е) измерительной линейкой, стержнем глубинометра штангенциркуля, штангенглубинометром или шаблоном, а диаметр ступени – штангенциркулем. Если высота уступа ступенчатого вала, или глубина резания, менее 5 мм, обработку выполняют за один проход. Если высота уступа более 5 мм, то обработку ведут за два прохода и более, а резец устанавливают под углом φ = 95 0, (рис. 1.52, д).
На этом занятии учащийся должен обработать несколько заготовок с различными размерами уступов и перепадами диаметров ступеней, требующих обработки за один или несколько проходов; выполнить измерение обработанных поверхностей различными измерительными инструментами.
Особенности обработки твердосплавными резцами. Для наружного продольного чернового и чистового точения применяют проходные резцы. В настоящее время конструкция резцов с напаянными твердосплавными пластинами устарела. За рубежом около 80 % применяемых проходных твердосплавных резцов имеют сборную конструкцию, у нас в стране - только 20 % (рис. 1.53). По сравнению с напаянными резцами сборные имеют следующие преимущества: сокращение расходов на переточку; уменьшение вспомогательного времени на смену и подналадку резцов; экономия твердого сплава.
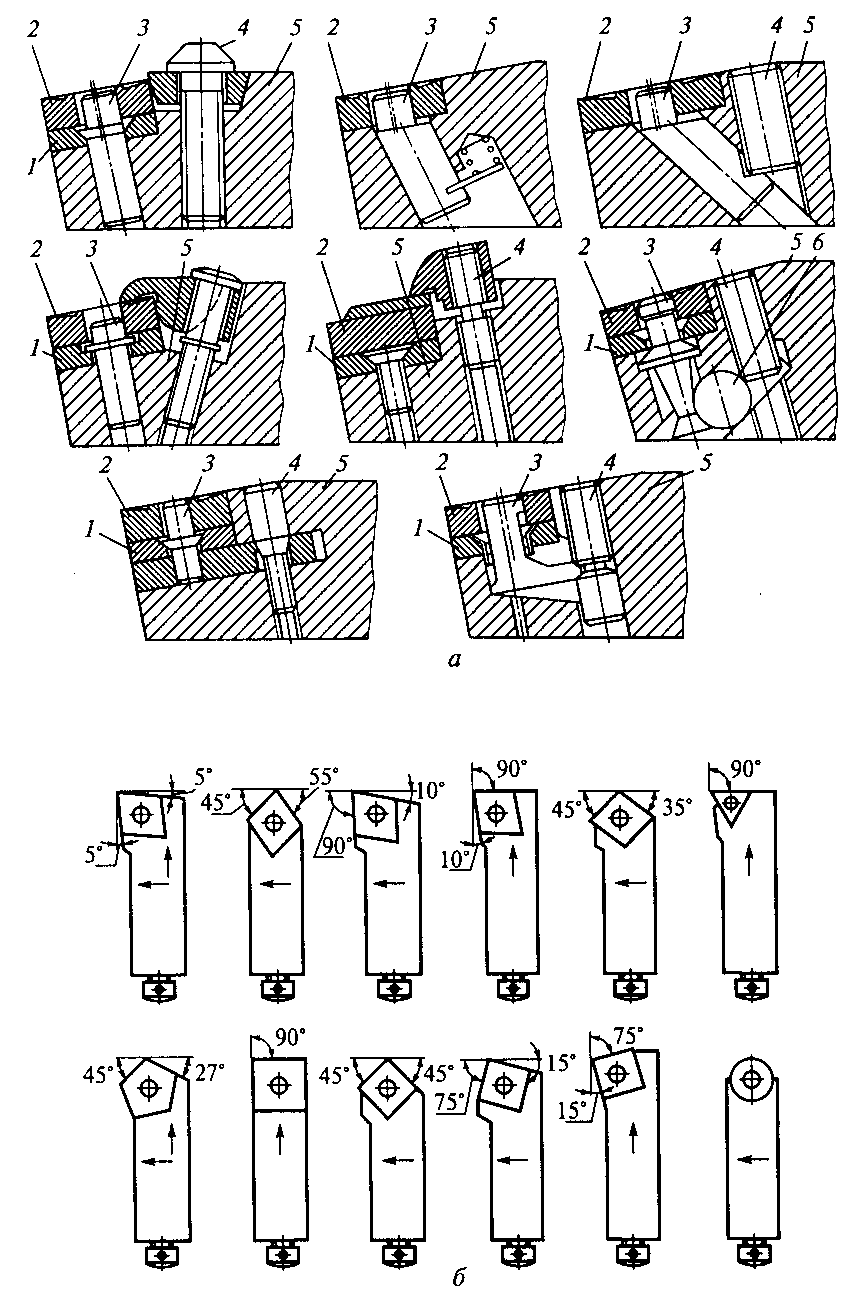
1 - подкладка; 2 - пластина; 3 - штифт; 4 - винт; 5 - державка; 6 - шарик
Рисунок 1.53 Проходные резцы сборной конструкции (а) и типовые резцовые вставки с механическим креплением многогранных и цилиндрических твердосплавных пластин (б)
Прямые проходные резцы изготовляют с главным углом в плане φ = 45, 60 и 75° (рис. 1.54). Отогнутые проходные резцы (рис. 1.55, а и б) имеют угол φ = 45°. Они широко применяются для продольного и поперечного точения (т.е. для подрезки торцов). Упорные проходные резцы (рис. 1.55, в) имеют угол φ = 90°. Они пригодны для обработки деталей с уступами небольших размеров и нежестких деталей.
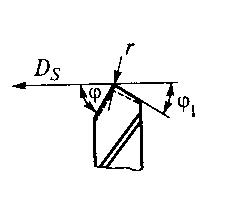
φ и φ1 - главный и вспомогательный углы в плане;
r - радиус скругления при вершине резца; Ds - направление движения подачи
Рисунок 1.54 Прямой проходной резец
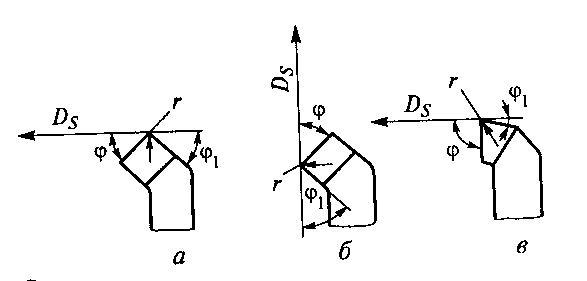
Рисунок 1.55 Проходные отогнутые (а и б) и
упорные (в) резцы
Особенности обработки резцами из быстрорежущих сталей. Резцы из быстрорежущих сталей имеют такую же форму передней поверхности, как у сборных резцов с пластинками твердого сплава того же назначения, но имеют отличные от них углы резания и размеры элементов головки.
Резцы с плоской передней поверхностью и положительным передним углом γ рекомендуется применять при обработке чугуна, бронзы и стали с подачей So < 0,2 мм/об. Резцы с плоской передней поверхностью с фаской применяют при обработке сталей с подачей Sо > 0,2 мм/об. Резцы с криволинейной передней поверхностью с фаской (радиус кривизны поверхности R = 3...18 мм, ширина фаски b = 2,5... 15 мм) применяют при обработке сталей. У этих резцов передний угол γ = 20... 25°, задний угол α = 8...12°.
Чистовая обработка. Для получения поверхности с малой шероховатостью, точной по форме и размерам заготовку подвергают чистовой обработке.
Если требуемую шероховатость поверхности нельзя получить обычным проходным резцом, то применяют специальные (чистовые) резцы, предназначенные только для чистовой обработки.
Установка резца относительно оси заготовки при чистовой обработке должна исключать возникновение дефектов на обработанной поверхности, что достигается установкой вершины резца по оси заготовки или несколько ниже ее. Вылет резца (при закреплении) должен быть минимально возможным.
Особенности обработки резцами с минералокерамическими пластинами. Резцы с неперетачиваемыми минералокерамическими пластинами (типа ЦМ-332) применяют для чистовой и получистовой обработки стали (в том числе закаленной), чугуна, цветных металлов и их сплавов и неметаллических материалов. Минералокерамические пластины обладают очень низкой теплопроводностью и склонны к образованию трещин при быстром нагревании и особенно при быстром охлаждении. Пластины крепят механическим способом (аналогично креплению твердосплавных многогранных пластин). При установке пластины нельзя допускать, чтобы она выступала за головку резца более чем на 1 мм. Пластины разрушаются, как правило, при входе инструмента в зону резания и выходе из нее, поэтому отводить резец от детали нужно только при выключенной подаче. Для обработки напроход применяют резцы с пластинами из оксидно-карбидной минералокерамики (рис. 1.56, а)
Пластины из оксидно-карбидной минералокерамики типа ВЗ, ВОК-60 и ВОК-63 выпускают треугольной, квадратной, ромбической и круглой форм.
Режущие пластины треугольной формы используют для предварительной чистовой обработки. Наиболее широко распространены пластины квадратной формы, используемые как для черновой (при толщине пластины 8 мм), так и для чистовой (при толщине пластины 4 мм) обработки.
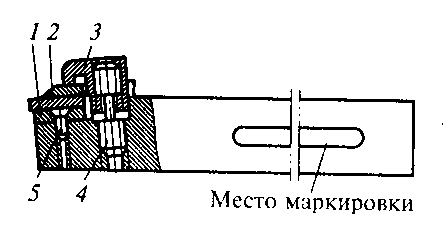
1 - опорная пластина из твердого сплава; 2 - режущая пластина из минералокерамики; 3 - прихват; 4 - дифференциальный винт; 5 - винт
Рисунок 1.56 Конструкция резца с
минералокерамической пластиной
Пластины ромбической формы с углом ромба 75 или 80° в основном применяют для черновой обработки, а с углом ромба 55° - для продольного точения по копиру. Пластины круглой формы чаще применяют при обработке гладких поверхностей без уступов. При обработке резцами, оснащенными режущей минералокерамикой, особое внимание следует обращать на стружколомание и удаление стружки из зоны резания. Это обеспечивается регулированием вылета накладного стружколома относительно режущей кромки пластины и установкой накладного стружколома под углом 30...35° относительно режущей кромки.
Особенности обработки резцами со вставками из эльбора и поликристаллических сверхтвердых материалов (СМ). Резцы из эльбора-Р и СМ применяют при необходимости повышения производительности (v = 400...800 м/мин) и улучшения качества обработки деталей из высокопрочных и закаленных сталей, чугуна, твердых сплавов и т.п. Конструкция резца, оснащенного вставкой из СМ, показана на рис. 1.56, б. Рабочие поверхности резца после заточки должны быть доведены. Обязательным условием эффективного использования инструмента, оснащенного вставками из эльбора-Р и СМ, является его переточка на специализированном оборудовании.
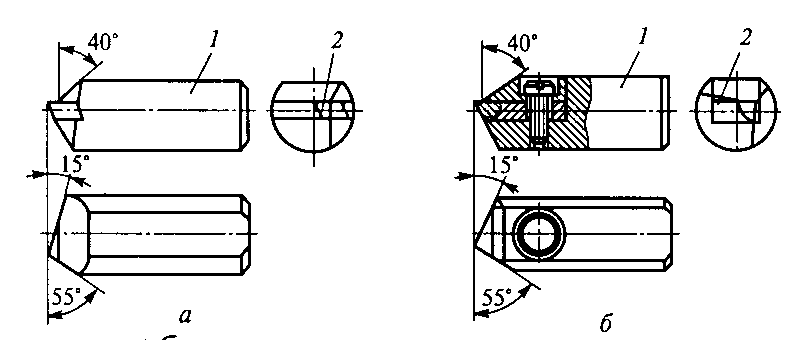
1 - державка; 2 - вставка из СМ
Рисунок 1.56, б Конструкция резца, оснащенного
вставкой из СМ, впаянной (а) и
механически закрепленной (б)
Контроль деталей. Наиболее распространенным инструментом для измерения размеров деталей, полученных после черновой и получистовой обработки, является штангенциркуль (рис. 1.57).
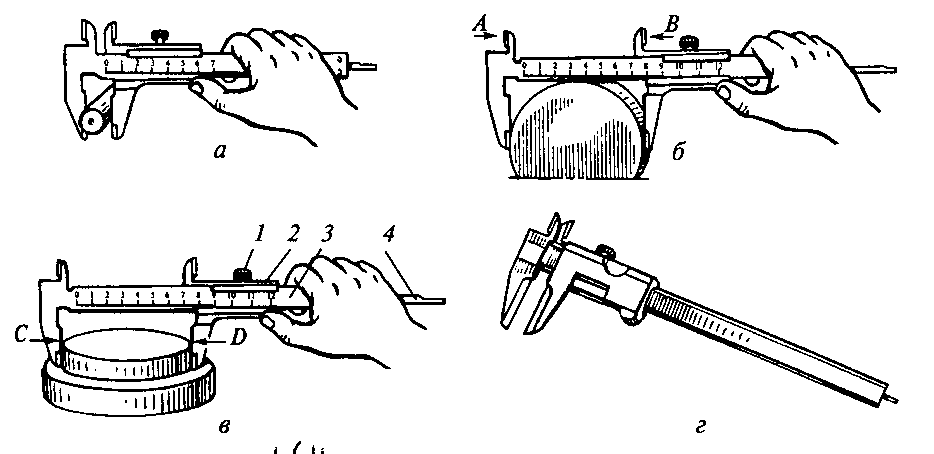
а - правильное измерение небольшого диаметра; б - неправильное измерение;
в - правильное измерение большого диаметра; г - штангенциркуль с цифровой индикацией; А и В - губки для измерения внутренних поверхностей; С и D - губки для измерения наружных поверхностей; 1 - винт; 2 - каретка нониуса;
3 - линейка; 4 - ножка для измерения уступов и углублений
Рисунок 1.57 Измерения штангенциркулем
Губки С и D предназначены для измерения наружных, а губки А и В - для измерения внутренних поверхностей, с помощью ножки 4 измеряют уступы и углубления. Размер с точностью до 1 мм измеряют по линейке 3, а с точностью до 0,1 мм - по нониусу на каретке 2. После замера губки фиксируют винтом 7.
Наиболее удобным для определения размеров является штангенциркуль с цифровой индикацией (рис. 1.57, г).
В условиях серийного производства детали измеряют предельными регулируемыми (рис. 1.58, а) и нерегулируемыми (рис. 1.58, б) скобами. Особенностью скоб различных конструкций является то, что с их помощью оценивают два размера обработанной детали: первый - с наибольшим отклонением, а второй - с наименьшим. Размер с наибольшим отклонением обозначается ПР (проходной), а размер с наименьшим отклонением - НЕ (непроходной). В регулируемых скобах размеры НЕ и ПР настраивают перемещением измерительных головок.
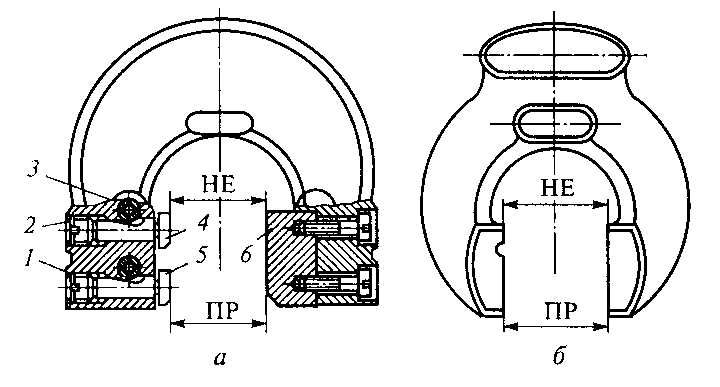
1, 2 и 3 - винты; 4, 5 - измерительные головки; 6 - опорная поверхность; ПР и НЕ - соответственно проходной и непроходной размеры
Рисунок 1.58 Предельная скоба регулируемая (а)
и нерегулируемая (б)