Учебное пособие для студентов среднего профессионального образования Специальность 1701 "Монтаж и техническая эксплуатация промышленного оборудования (по отраслям)"
Вид материала | Учебное пособие |
- Учебное пособие для студентов нефтехимических колледжей и техникумов Специальность, 3210.24kb.
- Программа и контрольные задания для студентов заочного отделения Специальность: 1701, 688.94kb.
- Государственный образовательный стандарт среднего профессионального образования государственные, 1346.06kb.
- Федеральный государственный образовательный стандарт среднего профессионального образования, 1074.58kb.
- Методические указания и контрольные задания для студентов заочной формы обучения гоу, 2389.4kb.
- Методические указания и контрольные задания для студентов заочного отделения специальность:, 848.08kb.
- «Материаловедение», 179.95kb.
- Формирование профессионально-значимых качеств личности в условиях личностно-ориентированного, 51.94kb.
- Система управления качеством подготовки техников по специальности 150411 – Монтаж, 102.4kb.
- Примерная программа профессионального модуля проведение подземного ремонта скважин, 226.39kb.
Фрезерование криволинейных контуров и фасонных поверхностей
Многие детали машин имеют не только прямолинейные и плоские поверхности, но и различные криволинейные контуры, состоящие из отрезков прямых, дуг окружностей различного диаметра и других кривых. Криволинейные контуры можно фрезеровать на вертикально-фрезерных станках: по разметке комбинированием продольной и поперечной ручной подач; по разметке с помощью поворотного круглого стола; по копиру в специальных приспособлениях.
Фрезерование комбинированием ручных подач заключается в том, что предварительно размеченную заготовку, а при необходимости с просверленными отверстиями для крепления и ввода инструмента закрепляют одним из разобранных на предыдущих занятиях методов на столе фрезерного станка. Перемещая ручной подачей стол одновременно в продольном и поперечном направлениях, подводят заготовку под вращающуюся концевую фрезу так, чтобы фреза снимала слой металла в соответствии с размеченным криволинейным контуром. Чтобы фреза своим торцом не задевала рабочую поверхность стола станка или приспособления, заготовку обязательно устанавливают на подкладку.
Криволинейные контуры формы дуги окружности рекомендуется обрабатывать на поворотном круглом столе с движением ручной подачи, который является обязательной принадлежностью вертикально-фрезерного станка. Поворотный круглый стол с ручной подачей (рис. 2.45) своим основанием крепится с помощью болтов в Т-образные пазы стола станка. Вращение от рукоятки 4, насаженной на валик 3, через червячную пару передается на поворотную часть стола 2 (планшайбу). Градуированная шкала на боковой поверхности стола служит для отсчета его поворота (с закрепленной заготовкой) на требуемый угол.
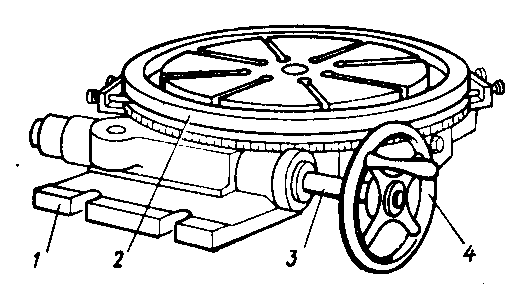
Рисунок 2.45 Поворотный круглый стол
с ручной подачей
Положение оси вращения поворотного стола фрезерного станка относительно оси шпинделя станка определяют совмещением осей стола и концевой фрезы, для чего в центровое коническое отверстие поворотного стола вставляют центрирующий штифт или центр. Для получения требуемого радиуса контура на заготовке стол станка движением поперечной подачи смещают на радиус контура плюс радиус фрезы.
Правильность установки заготовки относительно оси поворотного стола можно проверить путем легкого касания заготовки вращающейся фрезой в двух диаметрально противоположных положениях, т.е. при повороте стола на 180°. Теперь, если подвести заготовку любой точкой к вращающейся фрезе и продолжать поворачивать стол за рукоятку 4, то фреза обработает на ней дугу окружности радиусом, равным расстоянию от центра стола до этой точки заготовки.
Чем дальше расположена точка боковой поверхности от оси стола, тем большую окружность опишет она при вращении стола. Следовательно, при этом методе обработки контур на заготовке получается без комбинирования двух подач и его точность зависит только от правильной установки заготовки на столе (от правильного радиуса поворота заготовки). Для обеспечения контроля в процессе фрезерования заготовка должна быть предварительно размечена.
При обработке большой партии одинаковых заготовок с криволинейным контуром пользуются специальным копировальным приспособлением или применяют копировально-фрезерные станки.
Упражнение по фрезерованию криволинейных контуров формы дуги окружности в сочетании с отрезками прямых на деталях, аналогичных с шаблоном, показанным на рис. 2.46, а, б.
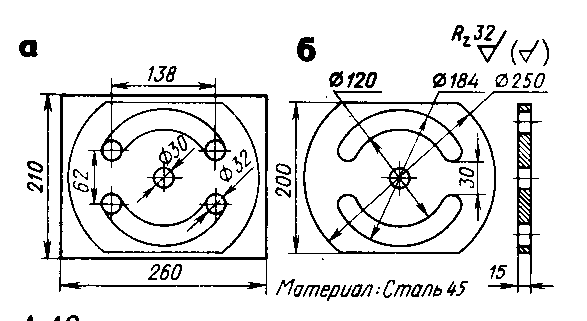
Рисунок 2.46 Чертежи заготовки (а) и обработанной детали (б) с наружными и внутренними криволинейными контурами
Заготовку перед фрезерованием предварительно разметить и просверлить отверстия - центральное диаметром 30 мм для крепления ее на круглом столе и четыре вспомогательных диаметром 32 мм для ввода концевой фрезы. Обработку проводят на вертикально-фрезерном станке с применением поворотного круглого стола.
Процесс обработки состоит из двух самостоятельных операций: фрезерования наружных прямолинейных и криволинейных (радиусных) участков и фрезерования внутренних замкнутых криволинейных пазов.
Выполнение первой операции:
1. Выбрать концевую фрезу. При обработке наружных выпуклых контуров диаметр фрезы не играет большой роли, поэтому берем фрезу диаметром 32 мм, используя ее и для фрезерования внутренних пазов. Закрепить фрезу в шпинделе станка.
2. Установить и закрепить на поворотном столе заготовку, для чего в центральное отверстие круглого стола вставить центрирующий штифт диаметром 30 мм и закрепить заготовку болтами, пропущенными через любые два отверстия в ней. Под заготовку подложить две подкладки (рис. 2.47).
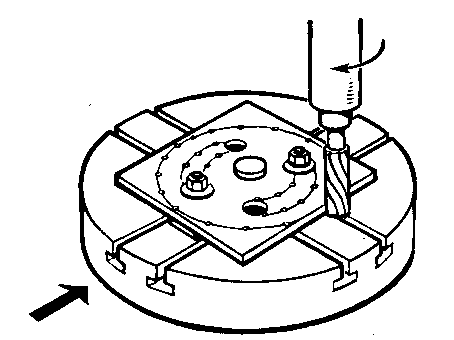
Рисунок 2.47 Фрезерование наружного прямолинейного и радиусного контура (1-я операция)
3. Настроить станок на требуемый режим фрезерования.
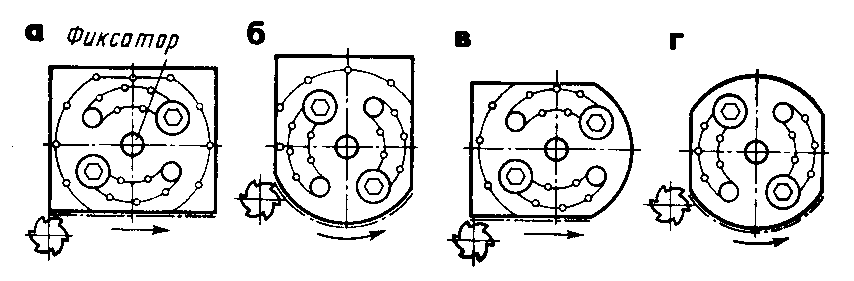
Рисунок 2.48 Последовательность фрезерования наружного контура (1-я операция)
4. Фрезеровать наружный контур заготовки в такой последовательности:
фрезеровать прямолинейный участок с одной стороны по разметке (рис. 2.48, а); этот переход можно выполнить, включив движение механической продольной подачи; фрезеровать криволинейный участок с одной стороны по разметке при ручном вращении круглого стола (рис. 2.48, б); фрезеровать прямолинейный участок с другой стороны, повернув круглый стол на 180° относительно положения первого прямолинейного участка (рис. 2.48, в); фрезеровать криволинейный участок с другой стороны (рис. 2.48, г). Обработку можно вести и в другой последовательности: сначала фрезеровать прямолинейные участки, а затем - криволинейные.
Выполнение второй операции:
1
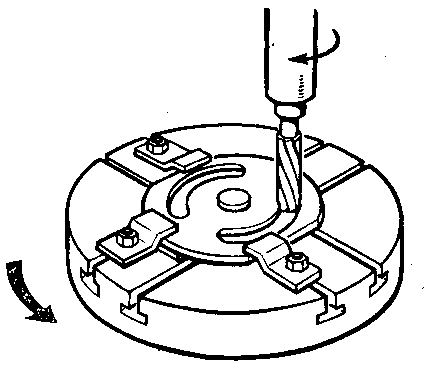
. Фрезеровать внутренние круговые пазы, для чего заготовку закрепить на круглом столе прихватами, как показано на рис, 2.49, подложив под нее подкладки (вне зоны фрезерования).
Рисунок 2.49
Фрезерование внутренних круговых пазов (2-я операция)
2. Вращением рукояток вертикальной, продольной и поперечной подач подвести фрезу к заготовке и вставить ее в предварительно просверленное отверстие, поднять стол и, застопорив консоль станка, приступить к обработке по разметке первого внутреннего паза ручной круговой подачей (рис. 4.50, а).
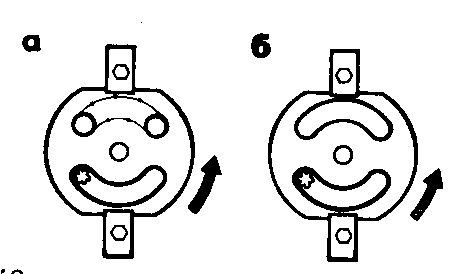
Рисунок 2.50
Последовательность фрезерования внутренних круговых пазов (2-я операция)
3. По окончании прохода опустить стол в исходное положение и вывести фрезу из паза.
4. Для обработки второго паза вращением рукояток движения круговой и вертикальной подач ввести фрезу в следующее отверстие заготовки и таким же образом профрезеровать второй паз (рис. 4.50, б).
Контроль размеров обработанной детали производят штангенциркулем.
Упражнение по фрезерованию криволинейного контура детали, аналогичной прихвату, показанному на рис.2.51, а, б.
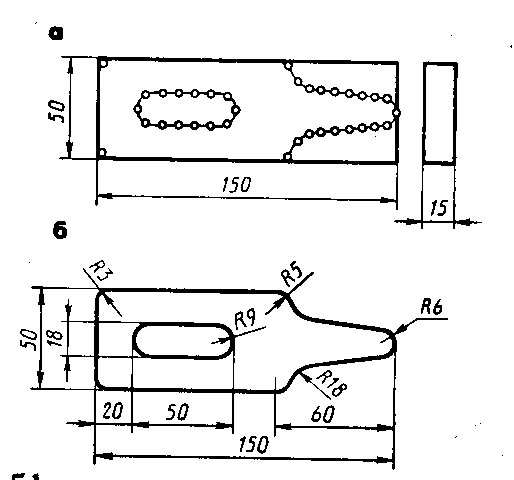
Рисунок 2.51 Чертеж заготовки (а) и обработанной
детали (б)
Обработка проводится комбинированием продольной и поперечной ручных подач по предварительной разметке на вертикально-фрезерном станке в следующей последовательности:
1. Выбрать концевую фрезу в зависимости от минимального радиуса закругления внутреннего контура детали, требуемого по чертежу (например, для R = 18 мм выбираем концевую фрезу диаметром 36 мм). Закрепить ее в шпинделе станка.
2. Установить и закрепить на столе станка заготовку, применив для этого прихваты или другие зажимные приспособления. Под заготовку должна быть положена параллельная подкладка (рис. 2.52, а).
3. Настроить станок на требуемый режим фрезерования. При обработке криволинейного профиля с движением ручной подачи, приведенные в нормативах значения скорости подач следует уменьшить на 20...30%.
4. Установить стол станка на глубину резания, учитывая, что припуск надо снимать постепенно за несколько проходов во избежание поломки фрезы. Фрезерование производят с одновременной ручной продольной и поперечной подачами соответственно направлению линии разметки за несколько проходов, оставив припуск 1...2 мм (рис. 2.52, б). Окончательный проход производят по линии разметки; радиусные внутренние закругления образуются непосредственно заданным диаметром фрезы. Обработку противоположной стороны заготовки производят с повторной установкой и закреплением ее на столе станка.
Фрезерование центрального паза в детали шириной 18 мм производят по способу фрезерования замкнутого паза концевой фрезой диаметром 18 мм с установкой заготовки на две подкладки.
Контроль размеров обработанной детали производят штангенциркулем.
Цель данного занятия выработка навыков фрезерования криволинейных поверхностей с ручной одновременной продольной и поперечной подачами.
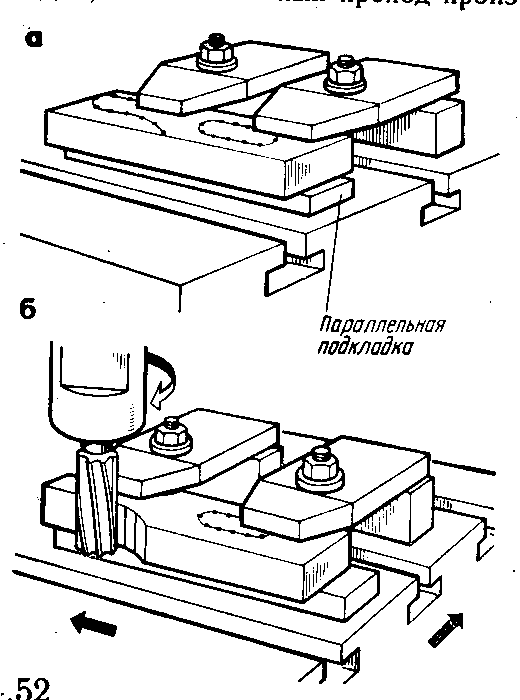
Рисунок 2.52 Прием установки и фрезерования заготовки по контуру
Тема 2.3 Фрезерование с применением делительной головки
Оснащение рабочего места: горизонтально-фрезерный станок модели 6Р81 (или другой модели консольного типа): универсальная делительная головка УДГ-Д-250 или другая, соответствующая применяемому типоразмеру станка с принадлежностями; плакаты - общий вид и кинематическая схема делительной головки; образцы фрезерных работ, выполненных с помощью делительной головки; фрезы; контрольно-измерительный и вспомогательный инструмент, необходимый для занятия; заготовки в виде валов, дисков и других форм, требующие фрезерования граней, зубьев и пазов.
Делительные головки являются важнейшими принадлежностями консольно-фрезерных станков, которые расширяют их технологические возможности. Делительные головки используют при изготовлении различных инструментов (фрез, разверток, метчиков, зенкеров), фрезеровании зубчатых колес, пазов и шлицев, зубьев на торцах (зубчатых муфт), нормализованных деталей машин (головок болтов, граней гаек) и других деталей.
Делительные головки служат для периодического поворота заготовки вокруг ее оси на определенный угол (деление на равные и неравные части); установки заготовки под требуемым углом относительно стола станка; непрерывного вращения заготовки при фрезеровании винтовых канавок большого шага на режущем инструменте или винтовых зубьев зубчатых колес.
Различают делительные головки для непосредственного деления (делительные приспособления), оптические делительные головки и универсальные делительные головки. Универсальные делительные головки делятся на лимбовые и безлимбовые. Наиболее распространены, в том числе и в учебных мастерских техникумов, лимбовые головки, которые пригодны для выполнения всех видов деления.
Делительная головка устроена следующим образом (рис. 2.53): на чугунном основании 20 со стяжными дугами 9 установлен поворотный корпус 10, который можно поворачивать вокруг своей оси на угол в пределах 7...10° вниз и 0...100° вверх. Угол поворота устанавливают по шкале с нониусом 12. В корпусе расположен шпиндель со сквозным отверстием, на переднем конце которого можно закрепить центр 21, либо поводковый или кулачковый патрон и диск 8 (лимб) для непосредственного деления.
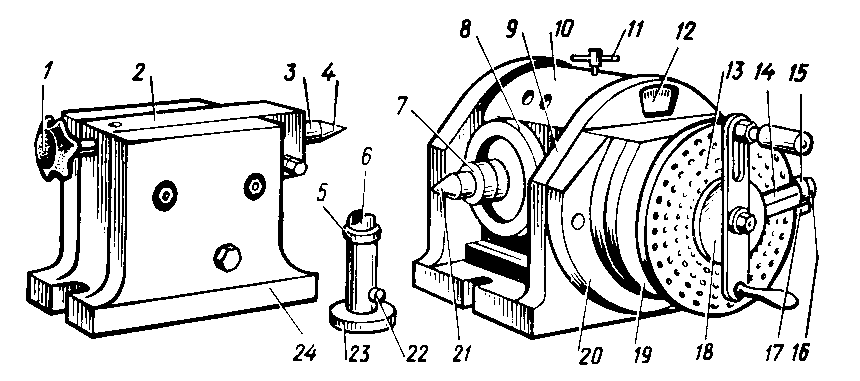
1 - маховичок бабки; 2 - корпус бабки; 3 - пиноль; 4 - полуцентр; 5 - гайка люнета; 6 - винт с призмой; 7 - шпиндель головки; 8 - диск (лимб) для непосредственного деления; 9 - стяжные дуги; 10 - поворотный корпус; 11 - зажим; 12 шкала с нониусом; 13 - основной делительный диск (лимб); 14 - линейки сектора раздвижные; 15 - втулка; 16 - вал привода головки; 17 - стопор делительного диска; 18 - основание раздвижного сектора; 19 - крышка подшипника; 20 - основание; 21 - центр; 22 - болт стопорный; 23 - корпус люнета; 24 - основание бабки
Рисунок 2.53 Универсальная делительная головка
Некоторые конструкции делительных головок на диске непосредственного деления имеют три делительных круга с 24, 30 и 36 отверстиями, что позволяет производить непосредственное деление на 2, 3, 4, 6, 8, 10, 12, 15, 18, 24, 30 и 36 частей. На заднем конце шпинделя устанавливают оправку для сменных зубчатых колес. В средней части шпинделя расположено червячное колесо, которое при необходимости стопорится зажимом 11.
При обработке длинных, заготовок на стол фрезерного станка ставят поддерживающую заднюю бабку, состоящую из основания 24, регулируемого по высоте корпуса 2, маховичка 1, пиноли 3 и полуцентра 4.
При обработке длинных нежестких заготовок в качестве дополнительной опоры применяют люнет (домкратик), состоящий из корпуса 23, винта 6 с призматическим вырезом, накатной гайки 5 и стопорного болта 22 для закрепления винта в требуемом положении.
На боковой стороне делительной головки имеется основной делительный диск (лимб) 13, с двух сторон которого засверлены отверстия по концентрическим окружностям. С одной стороны диска могут быть окружности с 24, 25, 28, 30, 34, 37, 38, 39, 41, 42, 43 отверстиями, а с другой - с 46, 47, 49, 51, 53, 54, 57, 58, 59, 62, 66 отверстиями. При работе головкой этого типа необходимо пользоваться то одной, то другой стороной диска, для чего его снимают с валика и закрепляют нужной стороной. К делительному диску с помощью пружины прижат раздвижной сектор 18, состоящий из раздвижных линеек 14. Вращение шпинделю передается от рукоятки с фиксатором, которая перемещается по делительному диску.
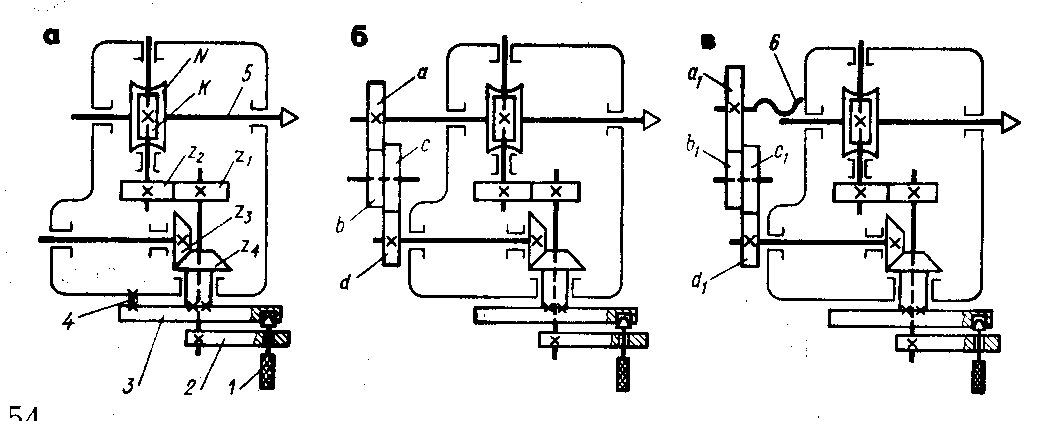
а - для простого деления; б - для дифференциального деления; в - для фрезерования винтовых канавок: 1 - фиксатор; 2 - рукоятка; 3 - делительный диск (лимб); 4 - стопор; 5 - шпиндель делительной головки; 6 - червяк
Рисунок 2.54 Кинематическая схема лимбовой делительной головки и ее настройка
Применяют следующие способы наладки универсальных делительных головок: для непосредственного деления, простого деления, дифференциального деления, фрезерования винтовых канавок. Кинематические схемы делительной головки для различных способов наладки показаны на рис. 2.54, а...в.
На данном занятии учащиеся знакомятся с устройством делительных головок; изучают их кинематические схемы; выполняют установку, выверку и закрепление их на столе фрезерного станка; поворачивают шпиндель делительной головки на заданный угол по нониусу; устанавливают для обработки длинных заготовок поддерживающую заднюю бабку и люнет; производят смену делительных дисков (лимбов) и установку раздвижного сектора на требуемое число отверстий. При наличии в учебной мастерской нескольких типов делительных головок каждый учащийся знакомится со всеми типами головок.
Фрезерование методом непосредственного деления выполняют на горизонтально-фрезерном станке с универсальной делительной головкой (для этой работы можно использовать упрощенную делительную головку).
Заготовку закрепляют в трехкулачковом патроне, установленном на шпинделе делительной головки. Поворот обрабатываемой заготовки осуществляется вращением шпинделя. Отсчет угла поворота производится по делительному диску (лимбу), установленному на шпинделе головки. При непосредственном делении червяк головки должен быть выведен из зацепления с червячным колесом. Поворот обрабатываемой заготовки осуществляют вращением шпинделя. Отсчет угла поворота производят по градуированному на 360° диску. Угол поворота шпинделя (в град) при делении на z частей определяется по формуле
α = 360 / z
Например, надо определить угол поворота шпинделя при фрезеровании заготовки с 8 гранями. По формуле определяем угол поворота шпинделя:
α = 360°/ z = 360° / 8 = 45°.
Если диск вместо градуировки на шкале имеет отверстия, то поворот шпинделя осуществляют на соответствующее число промежутков между отверстиями на выбранном делительном круге диска
n = a / z.
где а - число отверстий выбранного круга на диске. Данный метод позволяет поворачивать заготовку на 30, 45, 60, 90, 120 и 180°, т.е. производить деление на 12, 8, 6, 4, 3, 2 части.
Например, надо определить, на сколько промежутков между отверстиями делительного круга с 36 отверстиями следует повернуть шпиндель головки при фрезеровании шести граней гайки. По формуле определяем число промежутков
n = 36 /z = 36 / 6 = 6.
Во избежание ошибок и удобства отсчета при повороте рукоятки используют раздвижной сектор, состоящий из двух раздвижных линеек 1 и 3 (рис.2.55), которые служат для фиксации угла поворота на требуемое число промежутков. Настройку сектора производят в следующем порядке: с помощью отвертки освобождают винт 2, скрепляющий линейки сектора 1 и 3, и раздвигают их до требуемого числа промежутков а (шагов) между отверстиями, затем в одно из отверстий, например А, вводят фиксатор, подводят линейку 1 сектора к стержню фиксатора. Отсчитав необходимое количество промежутков а между отверстиями, фиксатор подводят к последнему отверстию В и закрепляют сектор винтом 2. Теперь каждый раз после фрезерования очередной поверхности (грани, зуба, паза и т.п.) при данном положении фиксатора следует повернуть рукоятку делительной головки по ходу часовой стрелки, ввести стержень фиксатора в отверстие В и снова повернуть сектор в том же направлении до соприкосновения с линейкой 3. (Сектор в новом положении на рис. 2.55 показан штриховыми линиями.)
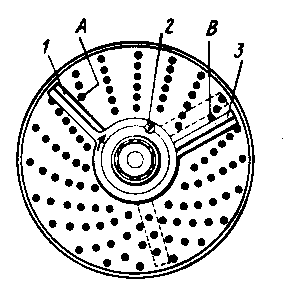
Рисунок 2.55 Делительный диск
(лимб) с раздвижным сектором
Фрезерование граней на круглой заготовке набором дисковых фрез на горизонтально-фрезерном станке методом непосредственного деления заключается в выполнении следующих приемов:
1. Установить и закрепить две дисковые фрезы, использовав набор простановочных колец.
2. Установить и закрепить универсальную делительную головку с трехкулачковым патроном.
3. Определить, на какое число отверстий надо поворачивать рукоятку делительной головки.
4. Настроить станок на требуемый режим резания.
5. Установить требуемые расстояния между режущими боковыми ребрами фрез, добиваясь симметричного расположения их относительно оси заготовки. Правильность установки стола можно проверить, обработав пробную заготовку или стальной пруток того же диаметра. Для этого сделать первый проход (обработать две противоположные грани), стол отвести назад продольной подачей, повернуть шпиндель делительной головки на 180° (пол-оборота) и снова пропустить пробную заготовку между фрезами. Если пробная заготовка свободно пройдет между фрезами и ни одна фреза не снимет с нее стружку, значит, стол установлен правильно и не требует корректировки поперечной подачей. После проверки установки стола закрепить (застопорить) поперечные салазки и приступить к обработке.
6. Произвести контроль размеров обработанной заготовки. Для этого упражнения объектами работы выбирают заготовки болтов, стержней, валиков, на которых необходимо отфрезеровать четыре или шесть граней, или заготовки зенкеров, разверток, фрез, муфт для фрезерования на них требуемого числа зубьев.
Инструментом может служить набор из двух дисковых фрез (рис. 2.56); концевая фреза, установленная в шпинделе горизонтально-фрезерного станка (рис. 2.57); при использовании вертикально-фрезерных станков - торцовая фреза (рис. 2.58).
При фрезеровании канавок, пазов или граней на конической или торцовой поверхностях заготовки (рис. 2.59), например, при фрезеровании зубьев угловой фрезы, зубьев муфты и прочих деталей, шпиндель делительной головки должен быть наклонен на угол α так, чтобы впадина канавки (линия ab) получилась параллельной поверхности стола станка, т.е. горизонтальной.
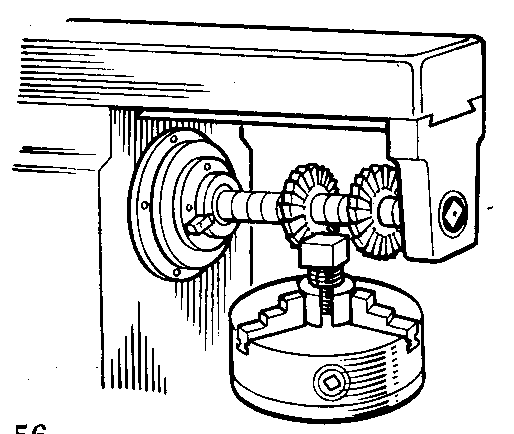
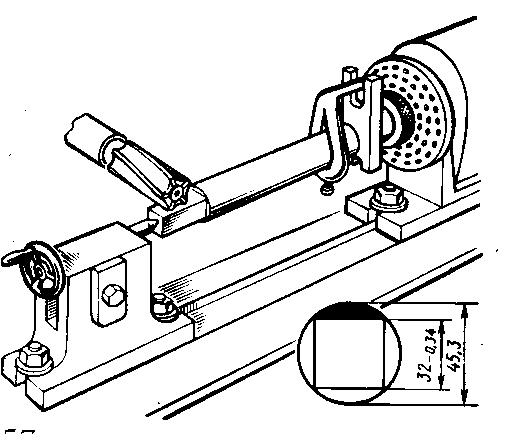
Рисунок 2.56
Установка двух дисковых фрез
для фрезерования граней квадрата
Рисунок 2.57
Фрезерование квадрата концевой фрезой на горизонтально-фрезерном станке
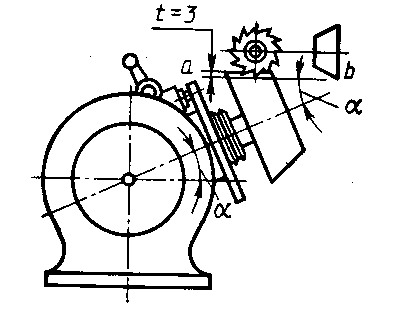
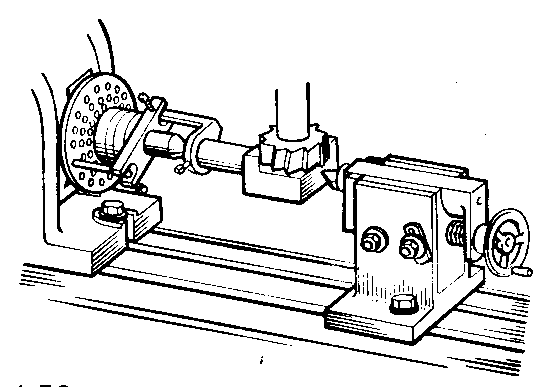
Рисунок 2.58
Фрезерование квадрата торцовой фрезой на вертикально-фрезерном станке
Рисунок 2.59
Фрезерование зубьев на конической поверхности
Фрезерование с применением делительной головки
методом простого деления
Фрезерование методом простого деления производят также на горизонтально-фрезерном станке с универсальной делительной головкой. Боковой делительный диск (лимб) 3, имеющий концентрические окружности с отверстиями (см. рис. 2.54, а), должен быть зафиксирован (закреплен) стопором 4, а червяк введен в зацепление с червячным колесом. Поворот шпинделя производят вращением рукоятки 2 с фиксатором 1 относительно делительного диска. В этом случае вращение от рукоятки передается через зубчатые колеса z1 / z2 с передаточным отношением i = 1 и червячную пару K / N, где K = 1 - число заходов червяка; N = 40 - число зубьев червячного колеса, которое называется характеристикой делительной головки. Передаточное отношение головки i = K / N = 1 / 40; следовательно, для деления окружности на z равных частей шпиндель должен повернуться на 1/z часть оборота, т.е. согласно кинематической цепи рукоятка должна быть повернута на

Количество оборотов рукоятки делительной головки N/z можно представить в виде суммы двух слагаемых:
n = N/z = A + b/a,
где А - число целых (полных) оборотов рукоятки; b - число шагов (промежутков между соседними отверстиями), на которое должна быть дополнительно повернута рукоятка; а - число отверстий в одном из концентрических рядов отверстий делительного диска.
Таким образом, деление на 1/z часть окружности заготовки производят поворотом рукоятки на А целых оборотов и еще на часть оборота, равную b/a, отсчитываемую по концентрическому кругу с числом отверстий а, после чего рукоятку стопорят фиксатором 1.
Например, надо подобрать делительный круг и угол раствора линеек сектора для фрезерования зубчатого колеса с z = 37, Определяем количество оборотов рукоятки головки:
n = N / z = 40 / 37 = 1 + 3 / 37 об.
Следовательно, нужно взять диск, на котором имеется 37 отверстий и после фрезерования каждой поверхности поворачивать рукоятку на один полный оборот и три промежутка между отверстиями, на которые разворачивают сектор.
Другой пример: надо определить круг и угол разворота линеек сектора для фрезерования зубчатого колеса с z = 35. Определяем количество оборотов рукоятки:
n = N / z = 40 / 35 = 1 + 5 / 35 = 1 + 1 / 7 об.
Так как диска с 35 отверстиями нет, то подбираем диск с числом отверстий, кратным 7, например 49, тогда
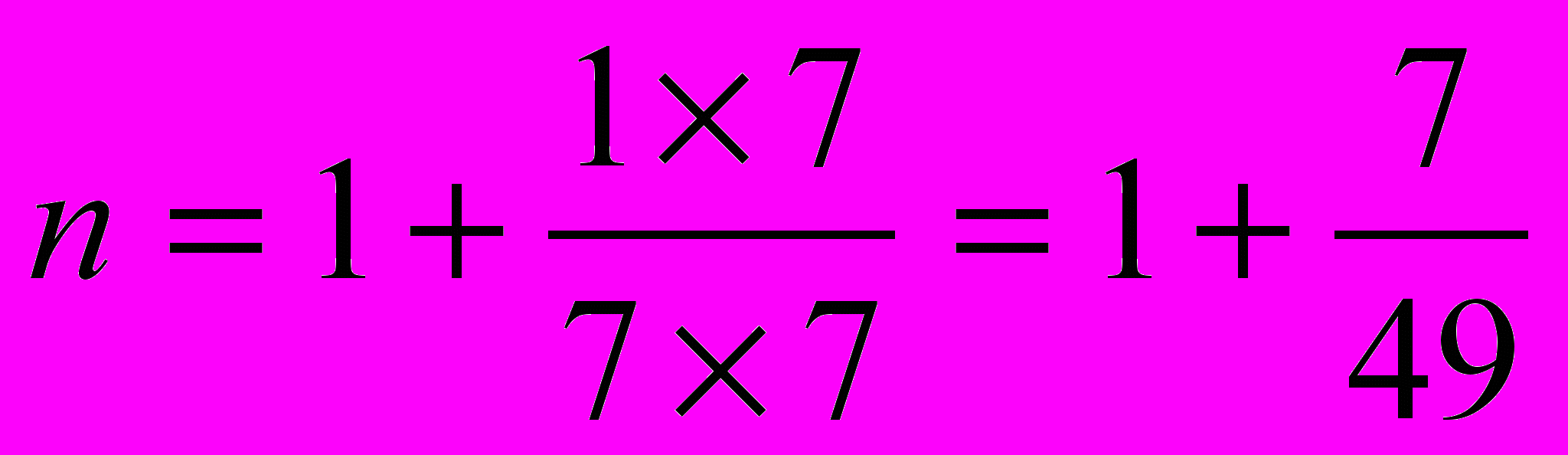
т. е. производим один полный оборот рукоятки и 7 промежутков между отверстиями на круге с 49 делениями.
Фрезерование с применением делительной головки
методом дифференциального деления
Дифференциальное деление применяется тогда, когда простое деление осуществить невозможно, так как на делительном диске нет окружности с необходимым количеством отверстий, например нельзя разделить на 61, 67, 71, 73, 79, 83 и некоторое другое число частей.
П
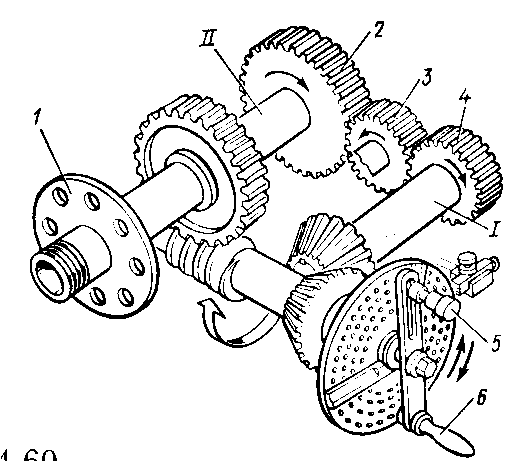
ри дифференциальном делении шпиндель делительной головки (см. рис. 2.54, б) соединяют гитарой сменных зубчатых колес
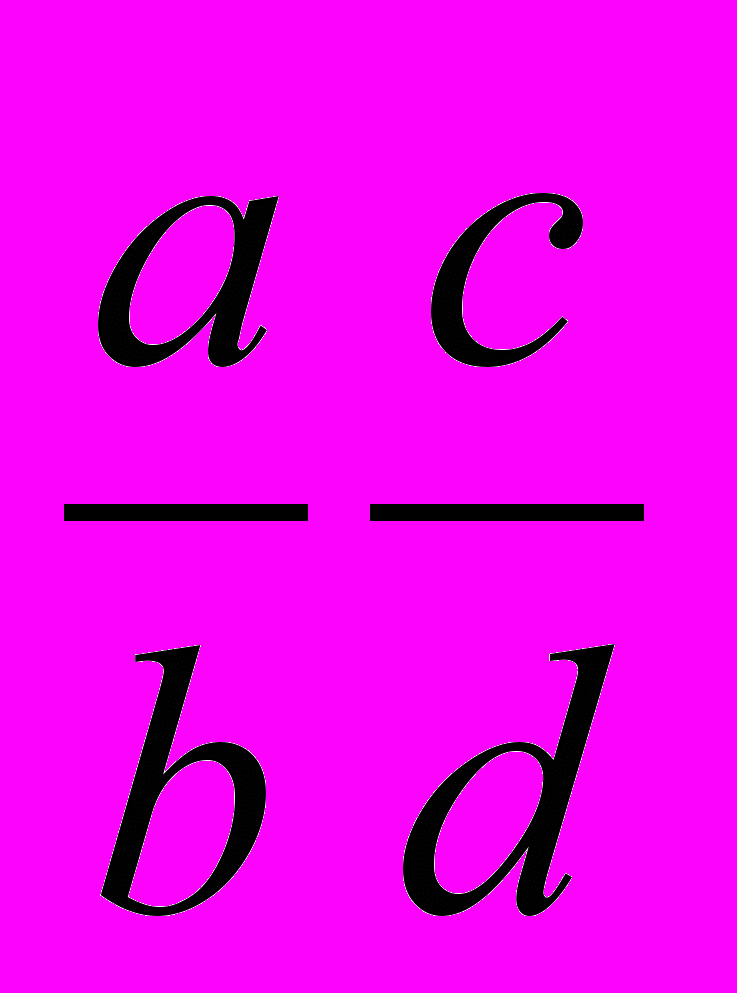
Рисунок 2.60 Схема передачи движения при
дифференциальном делении
Схема передачи движения при дифференциальном делении показана на рис. 2.60. На концы валика 1 и валика II, вставленного в заднее коническое отверстие шпинделя I, надевают сменные зубчатые колеса гитары 2 и 4. Между сменными зубчатыми колесами, надетыми на валики / и //, можно ввести одно или два промежуточных (паразитных) зубчатых колеса 3. В зависимости от подбора сменных колес и количества промежуточных колес делительный диск 5 вращается с большей или меньшей скоростью в том же направлении, что и рукоятка 6, или в противоположном.
Для облегчения расчетов вместо заданного числа делений z, которое нельзя осуществить способом простого деления, задаются произвольным вспомогательным числом делений х, которое должно быть близким к z (больше или меньше - безразлично).
При делении на х частей простым способом при N = 40 количество оборотов рукоятки было бы
nп = N/x = 40/x,
но в то же время делительный диск, связанный с рукояткой передачей
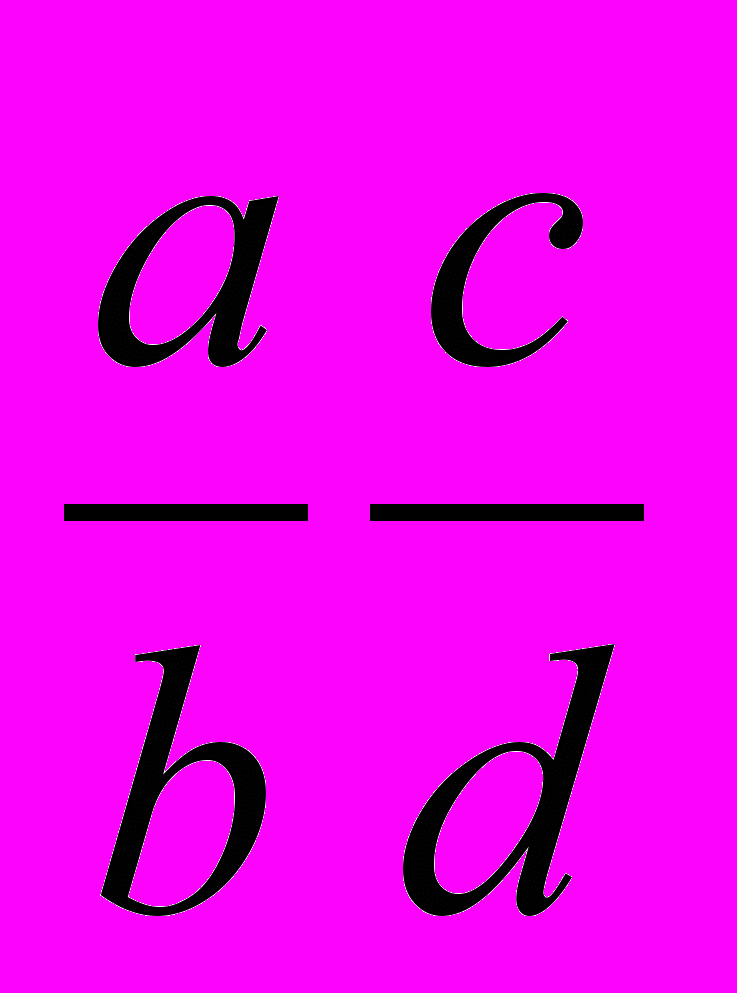
nд =
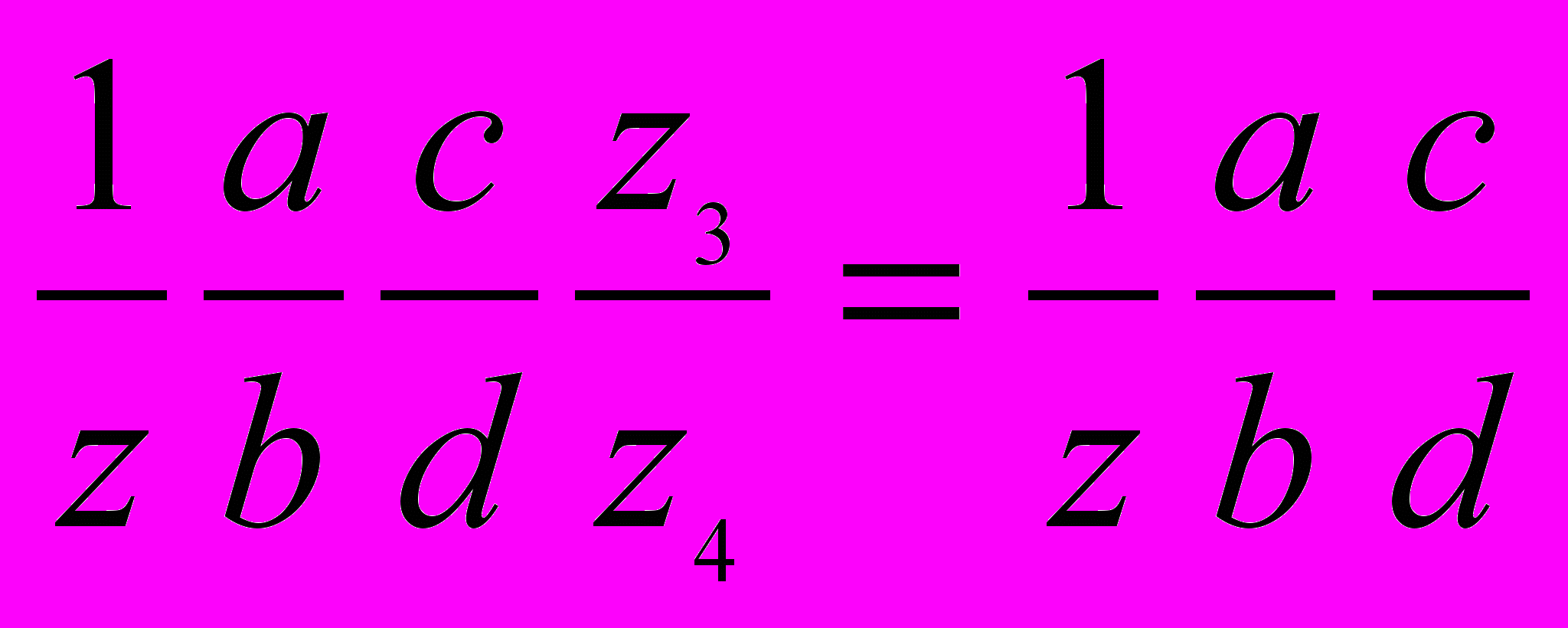
так как передаточное отношение конических колес Z3 / Z4 = 1.
Теперь количество оборотов np рукоятки для деления заготовки на 1/z часть можно выразить в виде алгебраической суммы двух движений: количество оборотов рукоятки относительно делительного диска nп и вместе с диском nд
np = nп + nд =
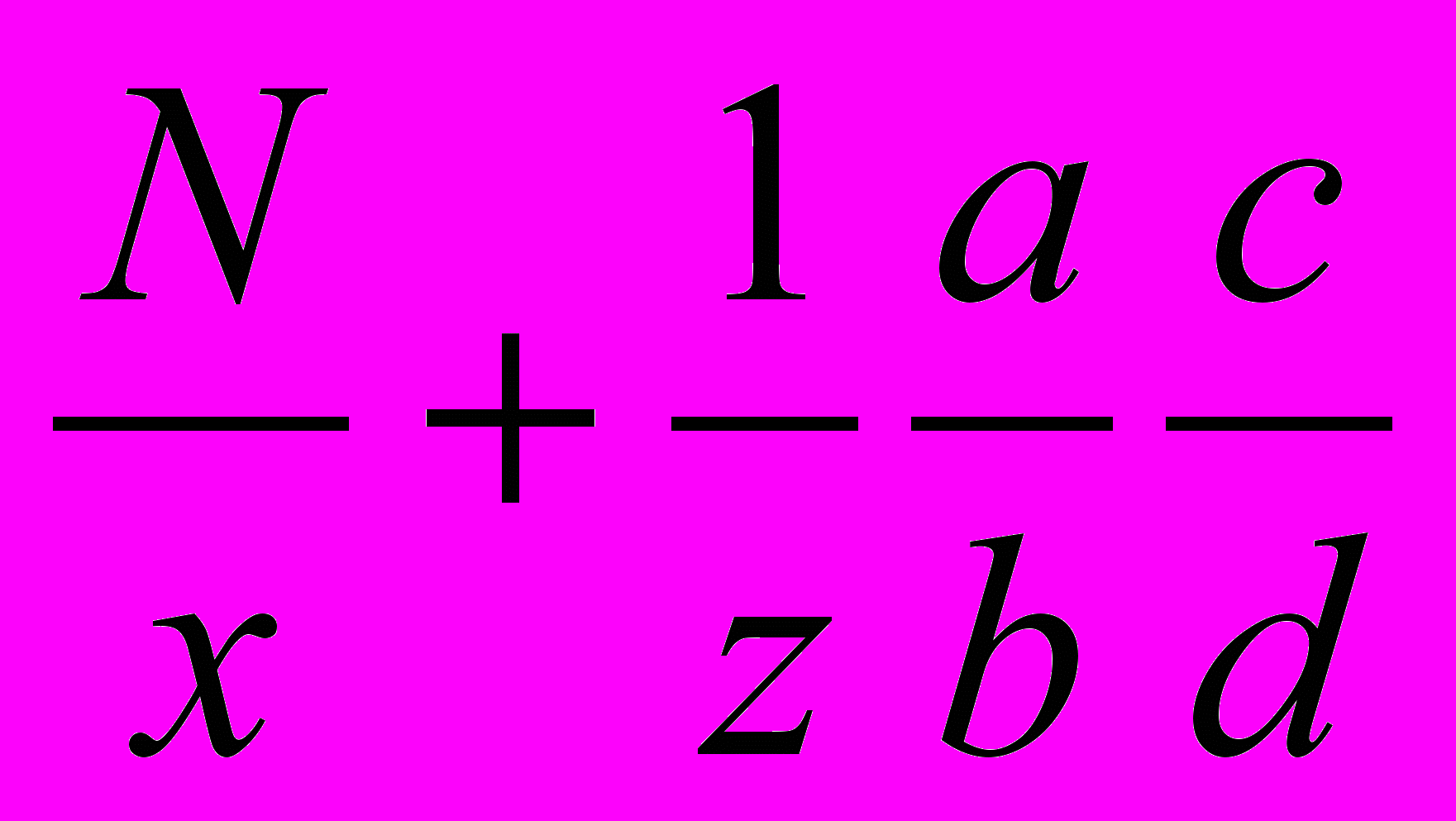
откуда после преобразований получим передаточное отношение сменных колес гитары:
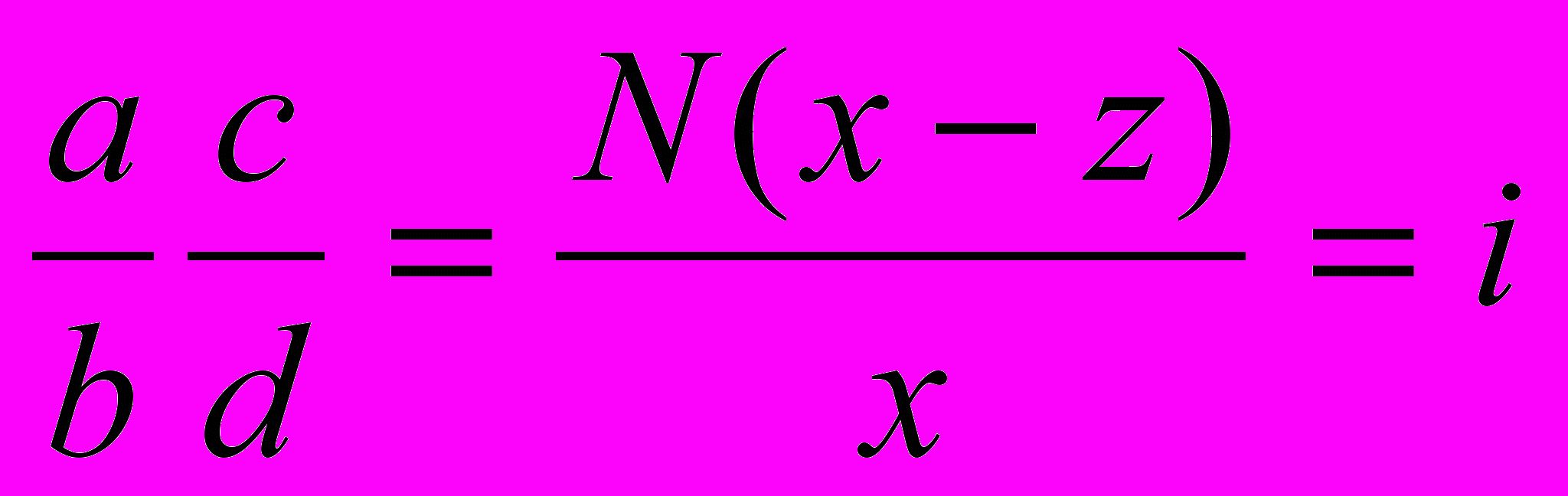
Таблица 2.2 Число промежуточных зубчатых колес в гитаре делительной головки
при дифференцированном делении
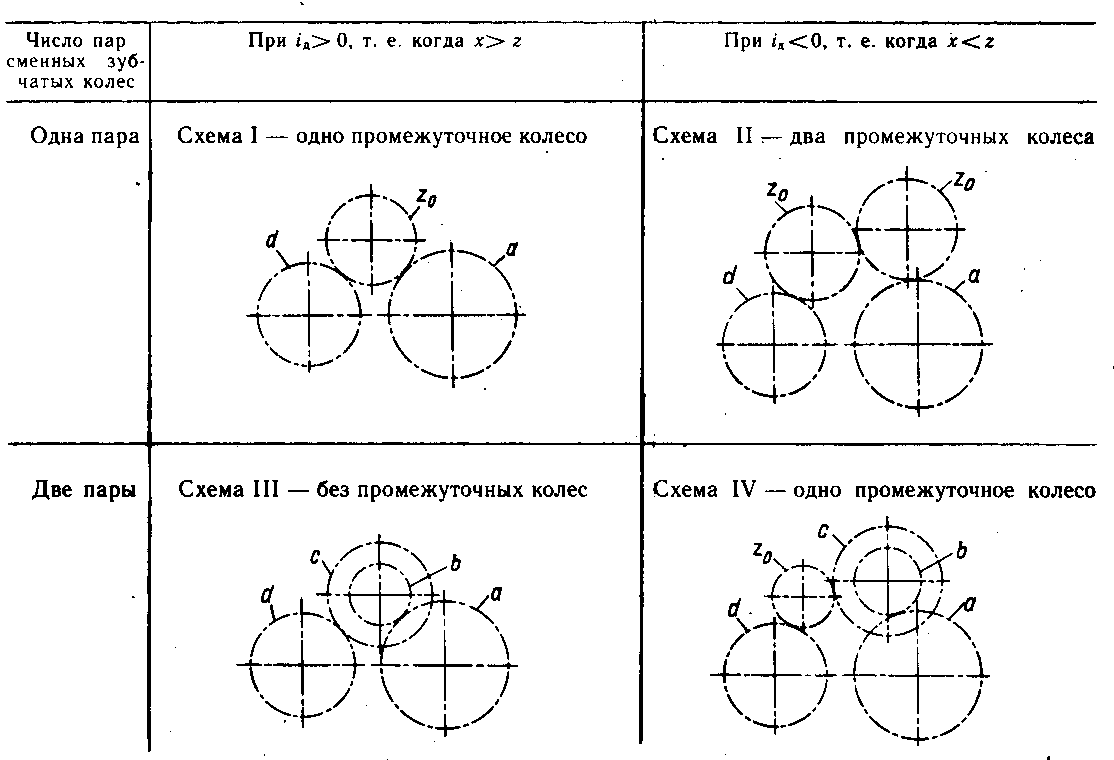
Примечания: 1.Зубчатое колесо а устанавливают на шпиндельном валике,
а колесо d на валике привода головки.
2. Зубчатые колеса zo и z'o - промежуточные.
Если передаточное отношение сменных колес положительное, то делительный диск должен вращаться в ту же сторону, что и рукоятка, а если отрицательное, то навстречу рукоятке. Для обеспечения указанного соотношения направлений вращения рукоятки и делительного диска в набор сменных зубчатых колес вводят промежуточные зубчатые колеса, число которых и схемы установки указаны в таблице 2.2.
Упражнение. Определить количество оборотов рукоятки и сменные зубчатые колеса для фрезерования заготовки зубчатого колеса с числом зубьев z = 61.
Принимаем ближайшее вспомогательное число x = 60.
По формуле для простого деления находим количество оборотов рукоятки, необходимый делительный диск и число промежутков на делительном круге для установки сектора:
nп =
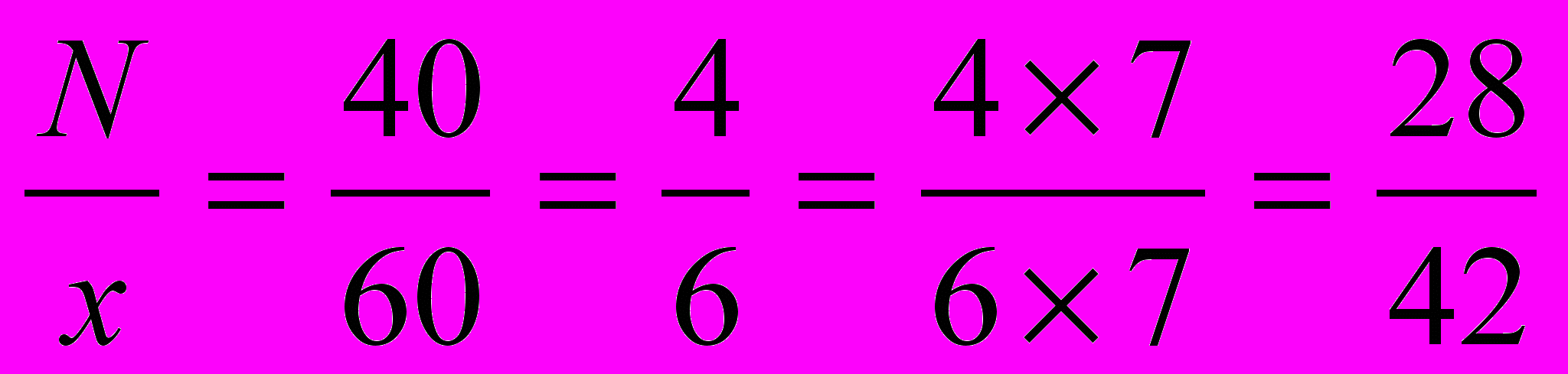
следовательно, выбираем диск с кругом, имеющим 42 отверстия, и устанавливаем сектор на 28 промежутков этой окружности.
По формуле для дифференциального деления находим передаточное отношение сменных колес гитары:
iд =

Следовательно, нужно взять сменные колеса с 60 и 40 зубьями (рис. 2.61). Ставят их на гитару делительной головки так, чтобы колесо а = 40 (ведущее) оказалось на шпинделе, а колесо d = 60 (ведомое) - на валике привода делительной головки.
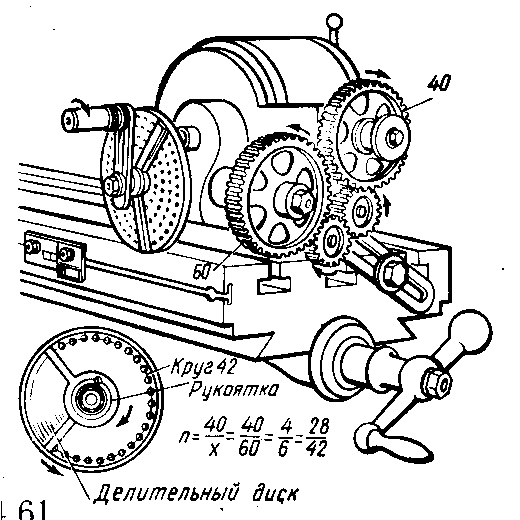
Рисунок 2.61 Настройка делительной головки
для деления на 61 часть
Так как передаточное отношение получилось отрицательным, то в передачу вводят два промежуточных колеса: zо и z'o, которые устанавливают на пальцы гитары согласно схеме II таблицы 2.2.
Другой пример: надо определить количество оборотов рукоятки и сменные зубчатые колеса для фрезерования заготовки зубчатого колеса с числом зубьев z = 111.
Принимаем ближайшее вспомогательное число х = 120. По формуле для простого деления
nп = N/x = 40/120 = 1/3 = 22/66,
следовательно, выбираем диск с кругом, имеющим 66 отверстий, и устанавливаем сектор на 22 промежутка этой окружности.
По формуле для дифференциального деления находим передаточное отношение сменных колес гитары:

Следовательно, нужно взять сменные колеса с 60, 50, 40, 25 зубьями и установить на гитару делительной головки так, чтобы колесо а = 60 было на шпинделе, b = 25 и с = 50 - на промежуточном пальце гитары и d = 40 - на валике привода делительной головки (рис. 2.62).
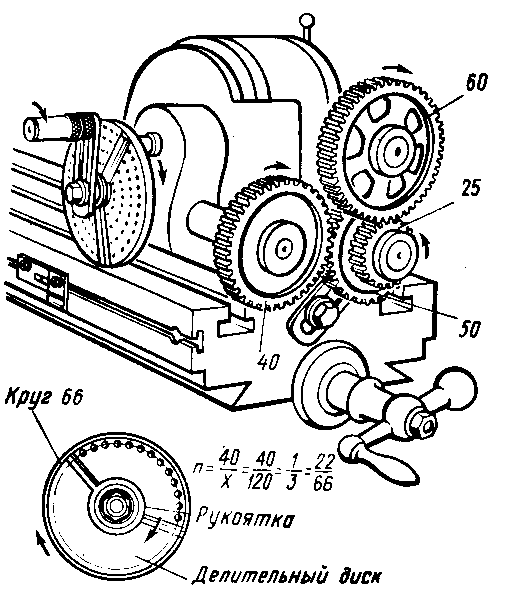
Рисунок 2.62 Настройка делительной
головки для деления на 111 частей
Колеса 60 и 50 - ведущие, колеса 25 и 40 - ведомые, т.е. устанавливаются на гитаре по схеме III таблицы 2.2.
Рассмотрим еще пример, когда надо определить количество оборотов рукоятки делительной головки, подобрать делительный диск и сменные зубчатые колеса для гитары, для фрезерования заготовки зубчатого колеса с z = 227.
Примем ближайшее вспомогательное число х = 220. По формуле для простого деления
nп = N/x = 40/220 = 2/11 = 2x6/11x6 = 12/66 об,
следовательно, выбираем диск с кругом, имеющим 66 отверстий, и устанавливаем сектор на 12 промежутков этой окружности.
По формуле для дифференциального деления находим передаточное отношение сменных колес гитары:
iд =

Следовательно, нужно взять сменные колеса с 70 и 55 зубьями, поставить их на гитару делительной головки так, чтобы колесо а = 70 (ведущее) оказалось на шпинделе, а колесо d = 55 (ведомое) - на валике привода делительной головки.
Так как передаточное отношение получилось отрицательное, то в гитару необходимо внести два промежуточных колеса, которые устанавливают на палец гитары согласно схеме II таблицы 2.2.
Контрольные вопросы:
- Какие операции выполняют на фрезерных станках?
- Чем отличаются вертикально-фрезерные станки от горизонтально-фрезерных?
- Как оборудовано рабочее место фрезеровщика?
- Какие фрезы, применяются на фрезерных станках?
- Какие приспособления и оснастка на фрезерных станках?
- Как производят фрезерование плоскостей?
- Расскажите об обработке заготовки, имеющей сопряженные плоскости?
- Расскажите о технологии фрезерования пазов.
- В чем заключаются особенности обработки сложных фасонных поверхностей?
- Какими мерительными инструментами контролируют обработку на фрезерных
станках?
3 Работа на сверлильных станках
Студент должен:
знать:
- технику безопасности при сверлении на станках ручными, электрическими
машинами;
- инструменты и приспособления, применяемые при сверлении, зенкеровании и
развертывании;
- разновидности сверлильных станков;
- приемы сверления, зенкерования и развертывания.
уметь:
- производить наладку сверлильного станка и управлять им;
- выбирать конструкцию и геометрические параметры инструмента для заданных
условий обработки;
- рассчитывать припуски;
- рассчитывать и корректировать режимы обработки;
- производить контроль обработки отверстий.
Оснащение рабочего места, оборудование, инструменты и приспособления, применяемые при сверлильных работах, а также приемы обработки отверстий подробно рассмотрены в 1 части пособия (тема № 9). В данном разделе рассмотрим дополнительно:
- Основные типы сверлильных станков и их обозначение;
- Организация рабочего места сверловщика;
- Основные правила безопасности при работе на сверлильных станках.
Тема 3.1 Основные типы сверлильных станков
и их обозначение
Сверлильные станки предназначены для обработки отверстий в сплошном материале, рассверливания, зенкерования и развертывания уже существующих в заготовке отверстий, нарезания внутренних резьб, вырезания дисков из листового материала и выполнения подобных операций сверлами, зенкерами, развертками, метчиками и другими инструментами.
Основными параметрами станка являются наибольший условный диаметр сверления отверстия (по стали), вылет и максимальный ход шпинделя и т.д.
В зависимости от области применения различают станки универсальные и специальные, предназначенные для обработки конкретных изделий, например, путем их оснащения многошпиндельными сверлильными и резьбонарезными головками и автоматизации цикла работы с помощью электрических, гидравлических и других устройств (механизмов смены инструментов, например револьверных головок; многопозиционных поворотных столов с автоматически действующими зажимными приспособлениями; устройств контроля целости инструмента; других устройств, обеспечивающих надежную работу в условиях автоматизированного производства).
Существуют следующие основные типы универсальных станков:
вертикально-сверлильные одно- и многошпиндельные (рис. 3.1); радиально-сверлильные (рис. 3.2); горизонтально-сверлильные для глубокого сверления (рис. 3.3) и горизонтально-центровальные.
Сверлильно-расточные станки на основании классификации, приведенной в таблице 1.1, отнесены ко второй группе, внутри которой их делят на типы (см. таблицу 1.1): I - вертикально-сверлильные; 2 - одношпиндельные полуавтоматы; 3 -многошпиндельные полуавтоматы; 5 - радиально-сверлильные; 8 - горизонтально-сверлильные; 9 - разные сверлильные.
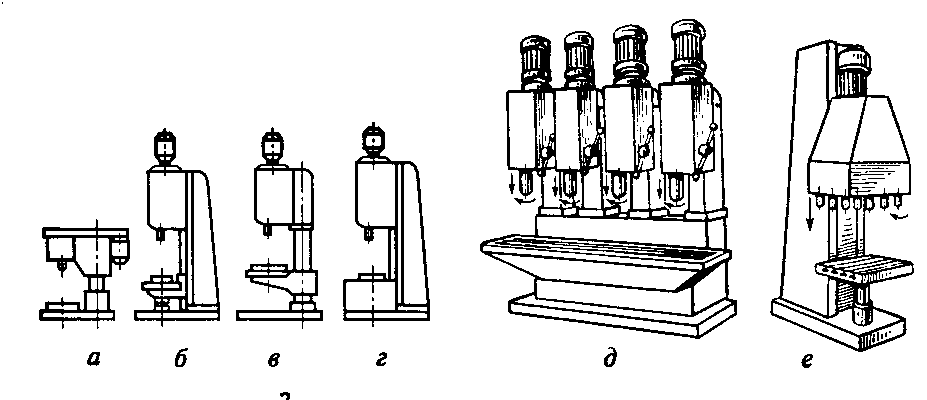
одношпиндельные: а - настольный; б - средних размеров на коробчатой основе; в - средних размеров на круглой колонне; г - тяжелый;
многошпиндельные: д - станки с постоянными шпинделями, имеющими одну общую станину; е - станки с переставными шарнирно соединенными шпинделями
Рисунок 3.1 Вертикально-сверлильные станки
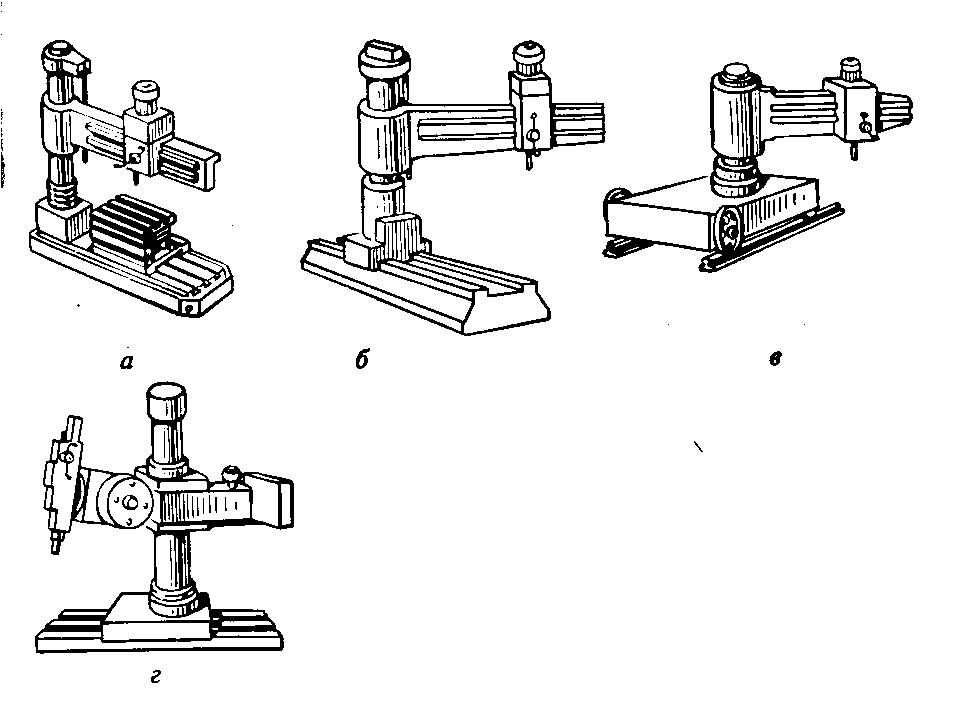
а - стационарный общего назначения; б - с колонной, перемещающейся по направляющим станины; в - передвижной по рельсам; г - переносной
Рисунок 3.2 Радиально-сверлильные станки
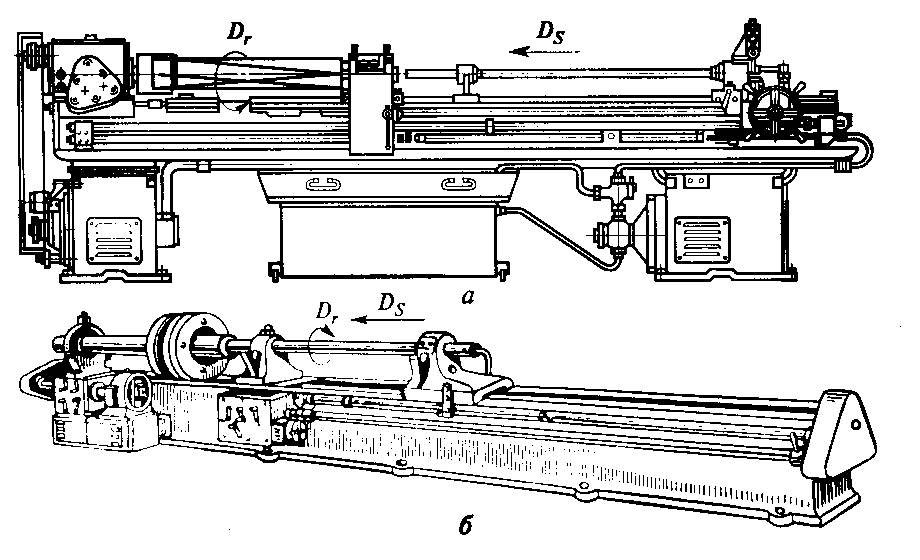
а - горизонтально-сверлильный для глубокого сверления вращающихся деталей;
б - горизонтально-сверлильный для глубокого сверления неподвижных деталей;
Dr - направление движения резания; DS - направление движения подачи
Рисунок 3.3 Станки для глубокого сверления
Модели станков обозначают буквами и цифрами. Первая цифра обозначает, к какой группе относится станок, вторая - к какому типу, третья и четвертая цифры характеризуют размер станка или обрабатываемой заготовки. Буква, стоящая после первой цифры, означает, что данная модель станка модернизирована (улучшена). Если буква стоит в конце, то это означает, что на базе основной модели изготовлен отличный от него станок.
Например, станок модели 2Н118 - вертикально-сверлильный, максимальный диаметр обрабатываемого отверстия 18 мм, улучшен по сравнению со станками моделей 2118 и 2А118. Станок модели 2Н118А также вертикально-сверлильный, диаметр обрабатываемого отверстия 18 мм, но он автоматизирован и предназначен для работы в условиях мелкосерийного и серийного производств.
Кроме станков, изготовляемых серийно, станкостроительные заводы выпускают много специальных станков. Эти станки, как правило, обозначают условными заводскими номерами.
Тема 3.2 Организация рабочего места сверловщика
Рациональная организация рабочего места сверловщика предусматривает обеспечение полной безопасности работы, установление порядка и нормальных условий труда, а также поддержание чистоты на рабочем месте.
На рис. 3.4 показано рабочее место сверловщика, работающего на вертикально-сверлильном станке, а на рис.3.5 - на радиально-сверлильном станке.
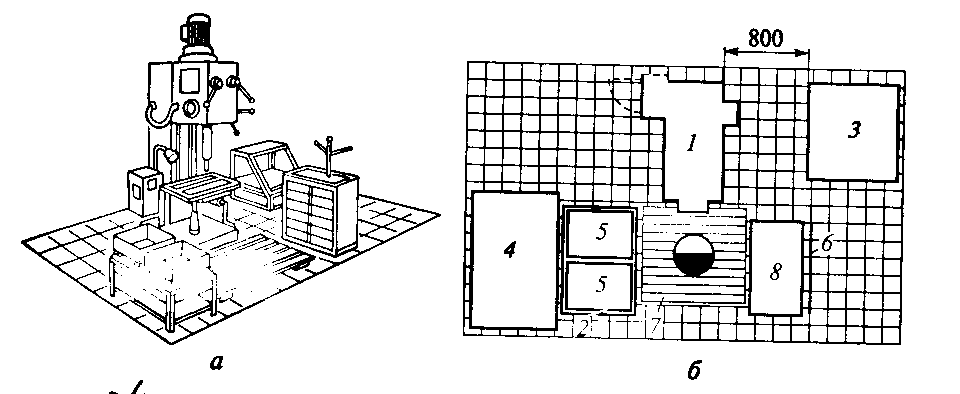
а - общий вид; б - вид в плане; 1 - сверлильный станок; 2 - приемный столик; 3 - стеллаж; 4 - стеллаж-подставка под настольное оборудование; 5 - тара с заготовками; 6 - планшет; 7 - деревянная решетка; 8 - инструментальная тумбочка
Рисунок 3.4 Рабочее место сверловщика, работающего на
вертикально-сверлильном станке
Кроме сверлильного станка 1 (см. рис. 3.4) на рабочем месте расположен приемный столик 2, на котором устанавливают тару 5 с заготовками, подлежащими обработке, а также предусмотрены стеллаж 3 для хранения приспособлений, инструментальная тумбочка 8 для режущего, измерительного и вспомогательного инструментов, стеллаж-подставка под настольное оборудование 4.
На инструментальной тумбочке установлен планшет 6 для рабочих чертежей и технологической документации. Около станка кладут деревянную решетку 7 под ноги, на которой устанавливают вращающийся, с регулируемой высотой стул для станочника.
Рабочее место сверловщика, работающего на радиально-сверлильном станке (рис. 3.5), организовано так же, как предыдущее. Помимо радиально-сверлильного станка 7 оно оснащено инструментальным шкафом для хранения инструмента 2, передвижным приемным столиком 4, подставками для корпусных деталей 5, стеллажами для хранения приспособлений 3, деревянной решеткой под ноги сверловщика 6 и планшетом 7 для рабочих чертежей и технологической документации. На деревянной решетке установлен вращающийся стул для сверловщика.
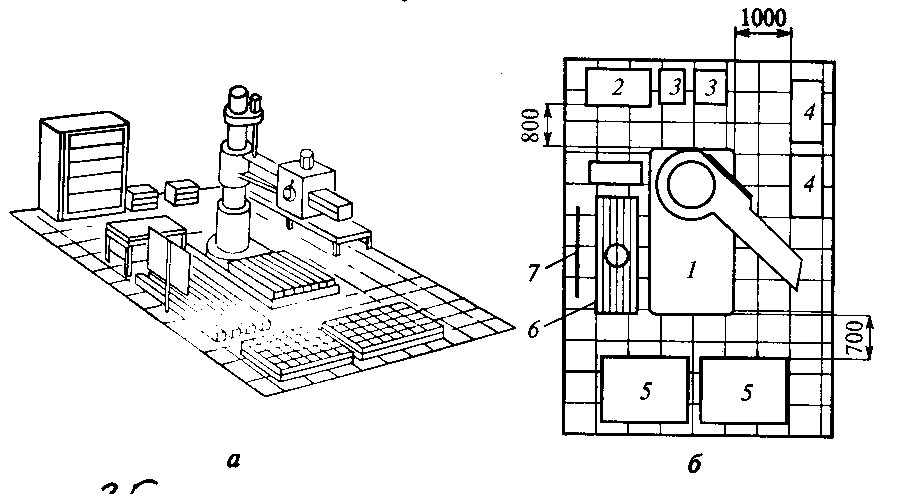
а - общий вид; б - вид в плане: 7 - радиально-сверлильный станок; 2 - инструментальный шкаф; 3 - стеллажи; 4 - передвижной приемный столик; 5 - подставки для корпусных деталей; 6 - деревянная решетка; 7 - планшет
Рисунок 3.5 Рабочее место сверловщика, работающего на
радиально-сверлильном станке
Тема 3.3 Основные правила безопасности при работе
на сверлильных станках
Если при работе на сверлильных станках не уделять необходимого внимания вопросам безопасности, то могут иметь место производственные травмы. К основным причинам производственных травм следует отнести несоблюдение техники безопасности при работе режущим инструментом, пользовании приспособлением и электрическим приводом. При работе на станке следует особое внимание уделять отлетающей стружке, обращению с деталями, заготовками и другими предметами.
Режущие инструменты. При сверлении практически не удается оградить вращающийся инструмент, поэтому важное значение имеет состояние спецодежды, исключающей возможность захвата ее вращающимся инструментом. Порванная, не застегнутая на все пуговицы одежда, не убранные под головной убор волосы, выпущенные наружу концы женских косынок, платков, галстуков служат причиной захвата сверловщика вращающимися частями станка или инструмента.
Ограждению подлежат все приводные и передаточные механизмы станка (зубчатые колеса, цепи, ремни, шкивы, валы), поэтому необходимо следить за установкой защитных ограждений, удобных при эксплуатации станка.
Сливная стружка. Сливная стружка часто является причиной порезов рук и ног. До сих пор не найдено универсального средства устойчивого ее дробления в процессе резания в широком диапазоне режимов резания. Травму можно получить как во время работы станка, так и при уборке рабочего места. Для освобождения станка и рабочего места от стружки следует использовать специальные захваты.
Отлетающая стружка и пыль хрупких металлов. При обработке бронзы, латуни, чугуна, различных сплавов и стали образуются элементная отлетающая стружка и пыль. Стружка может травмировать (обжечь) лицо и руки сверловщика, а пыль - засорить глаза. При обработке хрупких металлов и неметаллических материалов воздух рабочей зоны загрязняется пылью обрабатываемого материала, имеющего во многих случаях вредные составляющие (такие, как свинец, бериллий, асбест и др.). При обработке отверстий в заготовках из материалов, дающих мелкую стружку и пыль, обязательно следует надевать очки и устанавливать специальные пневматические стружкоприемники, соединяемые с отсасывающими устройствами.
Приспособления для закрепления заготовок. Несчастный случай может произойти из-за ненадежного закрепления заготовки или инструмента, в результате этого они могут сдвинуться и нанести травму. При закреплении заготовки и инструмента возможен срыв с болта или гайки «разработанного» ключа несоответствующего размера.
Заготовки и обработанные детали. Травмы иногда возникают при установке заготовки и съеме обработанной детали со станка вручную (падение заготовки на ноги, защемление рук между заготовкой и станиной станка). Ушибы ног или других частей тела часто происходят в результате неправильной укладки деталей, неудовлетворительного состояния полов и рабочих мест. Высота штабелей мелких деталей должна быть не более 0,5 м, средних - 1 м, крупных - 1,5 м.
Движущиеся части станков. Установку заготовки и съем обработанной детали производят при выключенном станке и на расстоянии от режущего инструмента, который может травмировать сверловщика при неосторожном движении.
Электрический ток. Ограждения, блокировки и заземление всегда должны быть в исправном состоянии в соответствии с действующими правилами.
Травмы могут возникнуть и при падении человека на поврежденном или загрязненном эмульсией, маслом или стружкой полу, при столкновении людей или наезде транспортных средств в механических цехах машиностроительных заводов. Поэтому сверловщик должен быть внимательным при работе на станке и во время перемещения по цеху.
Контрольные вопросы:
- В каких случаях применяют сверлильные станки?
- Расскажите об основных типах сверлильных станков?
- Расшифруйте модель сверлильного станка 2Н135?
- Как правильно организовать рабочее место сверловщика?
- Какие основные правила безопасности должен знать каждый сверловщик?
4 Работа на строгальных станках
Студент должен
знать:
- основные узлы и детали станка;
- конструкцию и геометрические параметры строгальных резцов;
уметь:
- пускать и останавливать станок;
- устанавливать заготовки и резцы;
- строгать поверхности на заданную ширину;
- контролировать качество поверхности;
- настраивать станок на требования режима резания.