Учебное пособие для студентов среднего профессионального образования Специальность 1701 "Монтаж и техническая эксплуатация промышленного оборудования (по отраслям)"
Вид материала | Учебное пособие |
- Учебное пособие для студентов нефтехимических колледжей и техникумов Специальность, 3210.24kb.
- Программа и контрольные задания для студентов заочного отделения Специальность: 1701, 688.94kb.
- Государственный образовательный стандарт среднего профессионального образования государственные, 1346.06kb.
- Федеральный государственный образовательный стандарт среднего профессионального образования, 1074.58kb.
- Методические указания и контрольные задания для студентов заочной формы обучения гоу, 2389.4kb.
- Методические указания и контрольные задания для студентов заочного отделения специальность:, 848.08kb.
- «Материаловедение», 179.95kb.
- Формирование профессионально-значимых качеств личности в условиях личностно-ориентированного, 51.94kb.
- Система управления качеством подготовки техников по специальности 150411 – Монтаж, 102.4kb.
- Примерная программа профессионального модуля проведение подземного ремонта скважин, 226.39kb.
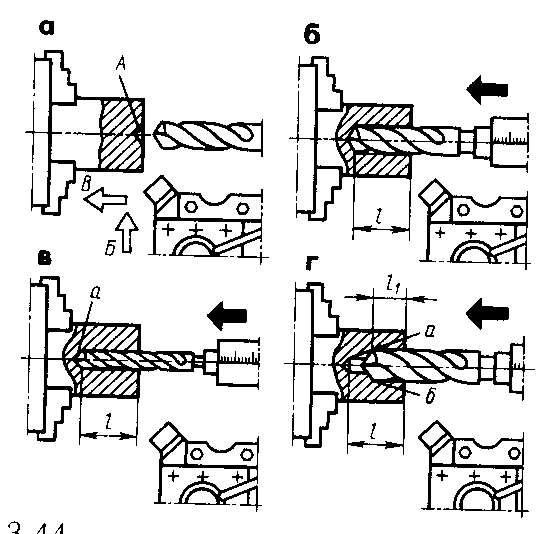
Рисунок 1.69 Приемы сверления отверстий
Для повышения производительности труда рекомендуется применять такую последовательность переходов: сначала сверлят отверстия большего диаметра на заданную длину, затем – отверстие малого диаметра.
На рис. 1.70,а приведена менее производительная последовательность обработки, так как в этом случае суммарная длина сверления составит 70+50+20=140 мм; во втором случае (рис. 1.70,б) длина сверления указанными сверлами равна 20+30+20-70 мм.
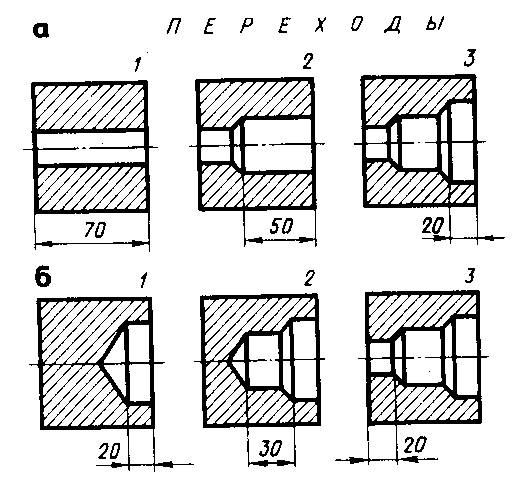
Рисунок 1.70 Последовательность сверления
ступенчатого отверстия
Сверление глухого отверстия с плоским дном выполняют за два перехода: сверлом с обычной заточкой с углом при вершине 2φ = 1180 (рис. 1.71,а) и сверлом со специальной заточкой такого же диаметра, что и для предварительного сверления, но с углом при вершине 2φ = 180 0 (рис. 1.71,б).
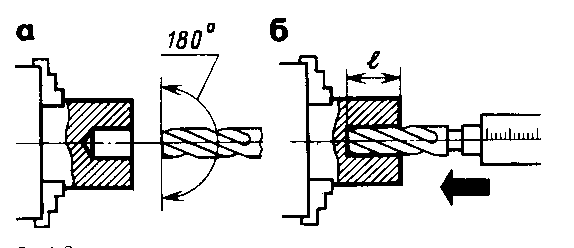
Рисунок 1.71 Сверление глухого отверстия с
плоским дном
Контроль длины отверстия или отдельной ступени можно осуществлять в процессе сверления по делениям на пиноли задней бабки станка или глубинометром штангенциркуля. При коническом дне отверстия (рис. 1.72, а) длину сверления l можно выдержать по метке 2, намеченной на сверле мелом или графитовым карандашом от режущей кромки 1 сверла, или по делениям 3 пиноли задней бабки. Измерение глубины просверленного отверстия штангенциркулем показано на рис. 1.72, б.
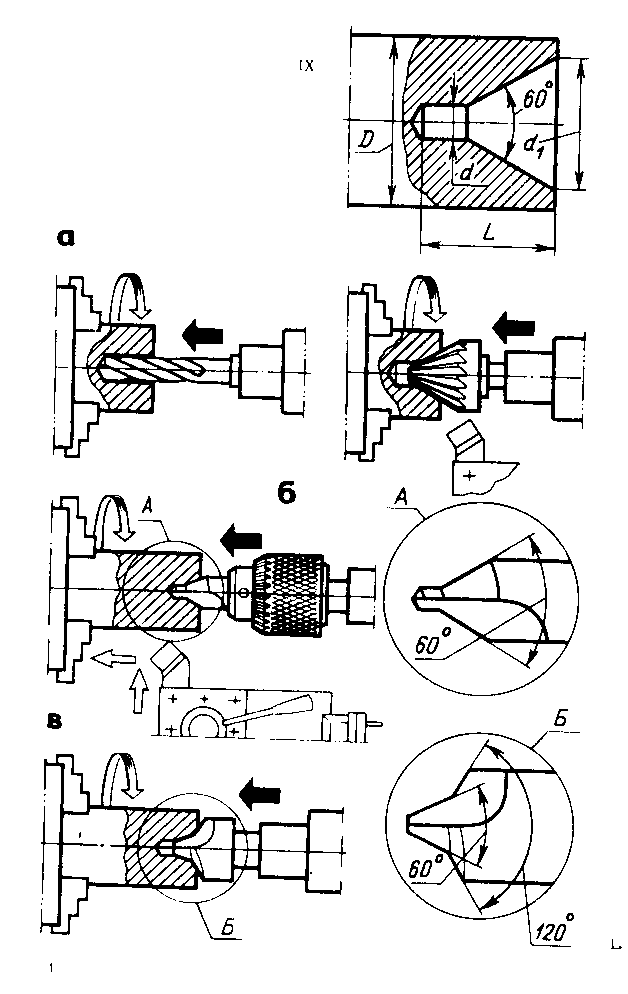
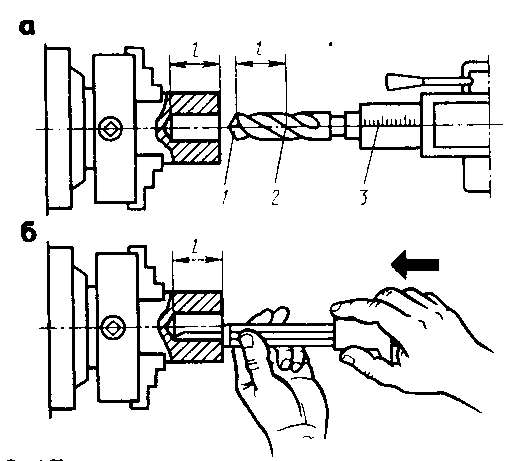
Рисунок 1.72
Способы контроля длины просверленного отверстия
Рисунок 1.73
Обработка центровых отверстий
Обработку центровых отверстий на торцовых поверхностях для установки заготовок в центрах станков осуществляют или последовательно сверлением и зенковкой, или за один прием комбинированным центровочным сверлом (рис. 1.72).
Первый способ (последовательное сверление и зенкование отверстия) (рис. 1.73, а).
1. Выбрать форму и требуемые размеры центровочного отверстия в зависимости от наружного диаметра d0 обрабатываемой заготовки.
2. Закрепить заготовку в трехкулачковом патроне.
3. Подрезать проходным отогнутым резцом торец заготовки.
4. Просверлить сверлом диаметром d, закрепленным в пиноли задней бабки, отверстие на заданную длину l.
5. Зенковать конусное отверстие с углом конуса 600 до диаметра d1.
Второй способ (центрирование комбинированным центровочным сверлом):
- Выбрать форму и размеры центровочного отверстия.
- Подрезать торец заготовки.
- Центровать комбинированным центровочным сверлом, закрепленным в сверлильном патроне в пиноли задней бабки (рис. 1.73, б).
Если центровочное отверстие должно иметь предохранительную фаску под углом 1200, то в первом случае ее выполняют обычным сверлом большого диаметра, а во втором – комбинированным центровочным сверлом с предохранительным конусом (рис. 1.73, в).
Упражнение по растачиванию гладких цилиндрических отверстий заключается в выполнении следующих приемов:
- Подобрать расточной проходной резец. Вылет из резцедержателя l должен быть больше, чем длина растачиваемого отверстия, на 5…10 мм.
- Установить и закрепить заготовку в трехкулачковом патроне.
- Установить и закрепить расточной проходной резец в резцедержателе суппорта станка.
- Настроить станок на требуемый режим резания (скорость резания, частоту вращения шпинделя, толщину снимаемого слоя и глубину резания) при предварительном растачивании.
- Поставить резец в исходное рабочее положение (на расстоянии 5…10 мм от торца заготовки), установить по лимбу резец на требуемую глубину резания и снять пробную стружку, проточив отверстие на 3…5 мм.
- Измерить штангенциркулем диаметр отверстия. Если действительный диаметр отверстия меньше заданного, вторично снять пробную стружку и так до получения требуемого диаметра. Измерение выполнить штангенциркулем с отсчетом по нониусу 0,1 или 0,05 мм.
- Расточить отверстие с ручным движением продольной подачи на всю длину заготовки.
- Расточить отверстие с механическим движением прямой продольной подачи, выбрать по таблицам или указанию мастера требуемую скорость движения подачи и настроить на нее станок. Вывести резец из отверстия и вторично проверить диаметр растачиваемого отверстия.
Растачивание отверстий с уступами отличается от растачивания гладкого цилиндрического отверстия расточным упорным резцом тем, что обработку выполняют за несколько проходов. Длина стержня резца должна быть такой, чтобы можно было растачивать на полную глубину все ступенчатое отверстие, а поперечное сечение головки и стержня резца должно быть меньше малого диаметра ступенчатого отверстия. Если высота уступа менее 5 мм и растачивание большего диаметра выполняют за один проход (t < 5 мм), то применяют резец с главным углом в плане φ = 90 0, подачу резца производят только в продольном направлении по стрелке А (рис.1.74,а). При растачивании глухих цилиндрических отверстий или сквозных отверстий с уступами высотой более 5 мм применяют резец с главным углом в плане φ = 95 0 , подача резца в этом случае производится сначала в продольном направлении по стрелке А, а при подходе резца к уступу - в поперечном направлении по стрелке Б (рис.1.74, б).

Рисунок 1.74 Растачивание отверстий с уступами
Размер от торца до уступа выдерживают различными способами: по риске на резце (рис.1.75,а), плоским упором, закрепленным в резцедержателе (рис.1.75,б), а также продольным упором, установленным на направляющих станины, или по продольному лимбу. Размер от торца заготовки до уступа 9или дна глухого цилиндрического отверстия) можно измерить различными измерительными инструментами: измерительной линейкой (рис. 1.76,а), глубиномером штангенциркуля (рис. 1.76, б), штангенглубиномером (рис. 1.76, в) или шаблоном (рис. 1.76, г).
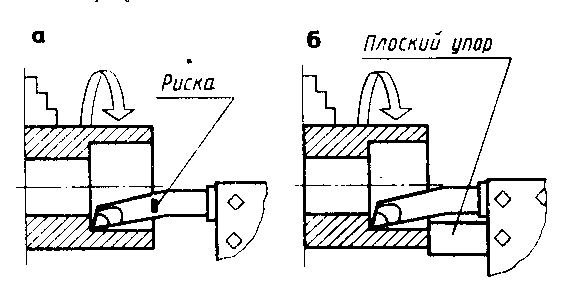
Рисунок 1.75 Способы контроля длины растачивания отверстия
Диаметр отверстия измеряют штангенциркулем. При использовании штангенциркуля с отсчет по нониусу 0,05 мм необходимо к показаниям штангенциркуля прибавлять толщину губок, указанную на них.
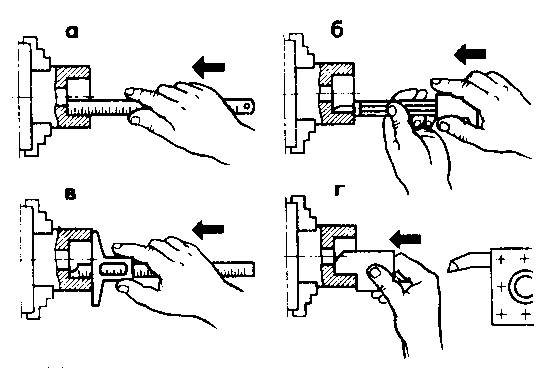
Рисунок 1.76 Измерение длины от торца
заготовки до уступа
Проверить полученный диаметр отверстия можно предельными калибрами-пробками. Проходная сторона пробки (ПР) должна проходить в отверстие без особых усилий, а непроходная сторона (НЕ) не должна проходить в отверстие.
При черновом растачивании стали принимают глубину резания до 3 мм; продольную подачу – 0,08 …0,2 мм/об; скорость резания – около 25 м/мин для резцов из быстрорежущей стали и 50…100 м/мин для твердосплавных резцов.
При чистовом растачивании глубина резания не превышает 1 мм, продольная подача – 0,05 … 0,1 мм/об, скорость резания – 40…80 м/мин для резцов из быстрорежущей стали и 150…200 м/мин для твердосплавных резцов.
Контрольные вопросы:
- Расскажите о способах крепления сверл на токарных станках.
- Когда применяют рассверливание, зенкерование и развертывание отверстий? Как выполняют эти операции на токарных станках?
- Какие резцы применяют для обработки глухих и сквозных отверстий на токарных станках?
- Чем лимитированы режимы резания при растачивании?
Тема 1.5 Нарезание резьбы
Студент должен
знать:
- конструкцию резьбонарезного инструмента.
уметь:
- сверлить отверстие и нарезать резьбу метчиком;
- нарезать различные по виду резьбы с помощью резьбовых резцов;
- замерять нарезанные резьбы резьбомерами, шаблонами, калибрами.
Оснащение рабочего места: то же, что и для темы1.2, кроме того, метчики машинные и машинно-ручные для нарезания метрической резьбы; плашки круглые; патроны для крепления метчиков на станках (предохранительные, быстросменные, плавающие и т.п.); плашкодержатели или патроны для плашек; калибры-пробки резьбовые; калибры-скобы; резьбовой микрометр; заготовки для нарезания внутренних и наружных резьб, предварительно обработанные под нарезание внутренней и наружной резьбы; масленки со смазывающей жидкостью, соответствующей обрабатываемому материалу.
Нарезание наружной и внутренней треугольной крепежной резьбы метчиками и плашками на токарных, токарно-револьверных и других станках – один из высокопроизводительных способов обработки. Резьбу нарезают окончательно за один или несколько проходов инструмента. Специальную настройку станка на нарезание резьбы не производят. Приемы работ просты, во многом сходны с приемами нарезания резьбы, освоенными учащимися при прохождении слесарной практики, и не требуют высокой квалификации. Наиболее целесообразно применять метчики и плашки для нарезания неточных крепежных резьб диаметром до 25…30 мм и с шагом не более 3 мм.
Плашка представляет собой кольцо с резьбой на внутренней поверхности и стружечными отверстиями, образующими режущие кромки.
Метчики применяются для нарезания внутренних резьб и делятся на слесарные, машинно-ручные, машинные гаечные и специальные. Машинные метчики применяют при нарезании резьбы на токарных, токарно-револьверных и сверлильных станках, а специальные и гаечные метчики – на различных гайкорезных автоматах. Метчик состоит из рабочей части, имеющей резьбовую поверхность и канавки для образования режущих кромок и хвостовика, который служит для закрепления инструмента в патроне. Обычно при нарезании резьбы на станке пользуются одним машинным метчиком, обеспечивающим получение резьбы за один проход. Для нарезания резьбы в заготовках из твердых металлов пользуются двумя или тремя метчиками (двух-и трехкомплектными). Первый – черновой, делает предварительную нарезку, а чистовой доводит резьбу до требуемых размеров и защищает ее.
При ввинчивании метчика или навинчивании плашки в нарезаемую поверхность заготовки зубья постепенно прорезывают винтовые канавки профиля резьбы. Толщина срезаемого слоя аz каждым зубом заборной части, а, следовательно, сила резания и крутящий момент зависят от числа зубьев, угла φ заборной части и шага резьбы (рис. 1.77)
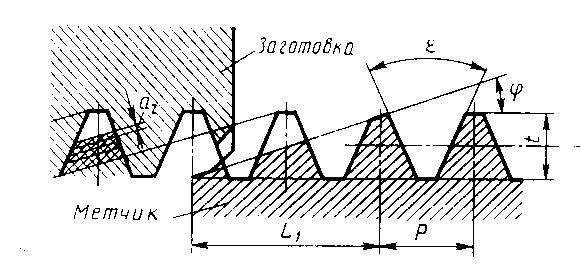
Рисунок 1.77
Для закрепления инструмента на станке и предохранения его от поломок и срыва резьбы в процессе нарезания, особенно в глухих отверстиях и на ступенчатых валиках, применяют предохранительные компенсирующие патроны различных конструкций и размеров. Основная особенность таких патронов – возможность перемещения инструмента на некоторое расстояние вдоль оси хвостовика и компенсирование некоторого рассогласования фактической подачи инструмента с шагом нарезаемой резьбы. На рис.1.78. показаны предохранительные патроны для крепления метчиков (рис. 1.78,а) и плашек (рис. 1.78,б) в пиноли задней бабки токарного станка.
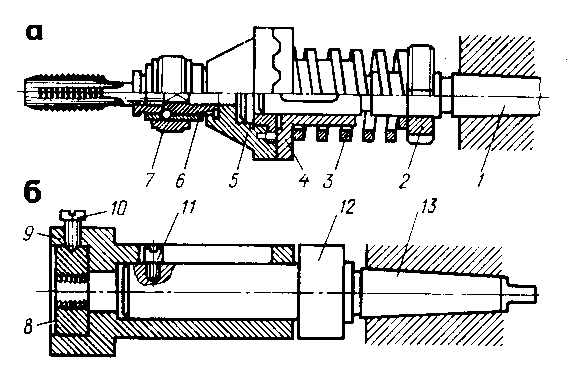
1 - хвостовик; 2 - гайка; 3 - пружина; 4 - муфта правая; 5 - муфта левая; 6 - быстросменная втулка; 7 - кольцо; 8 - плашка; 9 - корпус плашкодержателя; 10 - винты; 11 - шпонка; 12 - сменное кольцо;
13 - хвостовик
Рисунок 1.78 Предохранительные патроны
На этом занятии учащийся должен нарезать наружную и внутреннюю метрическую резьбу на нескольких различных по форме и размерам заготовках, применяя плашки и метчики; выполнить измерение резьбы различными контрольно-измерительными инструментами.
При установке плашки в плашкодержатель необходимо обеспечить плотное прилегание торца плашки к дну плашкодержателя. При отсутствии специальных патронов-плашкодержателей можно использовать стандартный слесарный плашкодержатель с двумя ручками, который вместе с плашкой прижимают пинолью задней бабки к заготовке, и, упирая одну из рукояток плашкодержателя в суппорт станка, нарезают резьбу (рис. 1.79,а).
На заготовках малого диаметра можно нарезать несколько первых ниток резьбы вручную, без применения пиноли задней бабки, а затем включить станок и, упирая ручку плашкодержателя в суппорт станка, закончить нарезание (рис. 1.79, б).
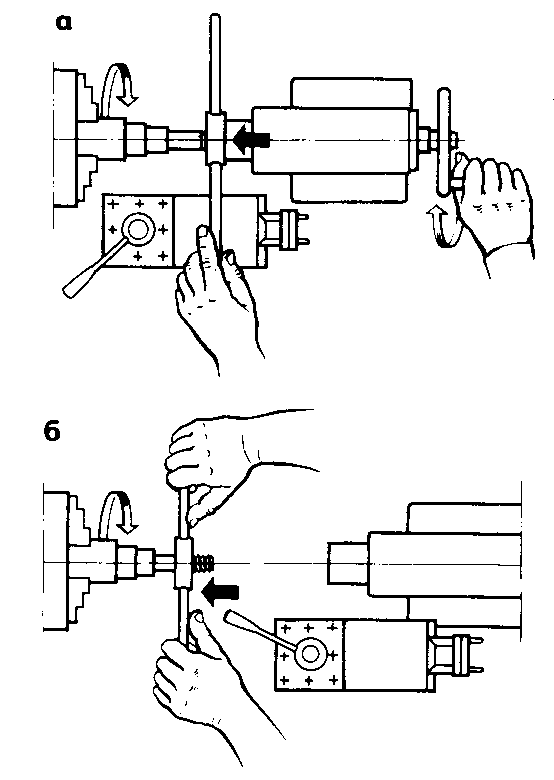
Рисунок 1.79 Нарезание резьбы плашкой
на токарном станке
При нарезании внутренней резьбы метчиками вместо специального компенсирующего патрона можно использовать слесарный вороток с квадратным отверстием для хвостовика метчика и центр, вставляемый в пиноль задней бабки, обеспечивающий поддержку и центрирование метчика. Одна рукоятку воротка должна при работе упираться в суппорт станка.
Инструменту в начальный период работы сообщают принудительную подачу на длину 3…5 резьбовых ниток с помощью ручного перемещения пиноли задней бабки. Дальнейшее перемещение инструмента вдоль оси происходит самостоятельно его на резьбовую поверхность (ввинчивание или навинчивания).
Для нарезания плашки наружной резьбы плашками и внутренней резьбы метчиками, так же как и при слесарной обработке, необходимо обработать стержень (наружную поверхность) или отверстие в заготовке под строго определенный диаметр. Если диаметр стержня занижен, а диаметр отверстия завышен, то нарезанная резьба имеет неполный профиль. Если диаметр стержня взят большего, а диаметр отверстия меньшего, чем требуется, размера, произойдет заклинивание, поломка режущего инструмента или срыв резьбы. Правильный выбор диаметра поверхности под обработку обеспечит получение резьбы полного профиля и с требуемой шероховатостью поверхности. Диаметры стержня и отверстия (диаметры сверла) для нарезания резьбы выбирают по специальным таблицам.
Чтобы облегчить врезание инструмента в металл, на конце заготовки снимают фаску шириной 1…3 мм.
На рис. 1.80. показаны приемы нарезания наружной треугольной резьбы плашкой, закрепленной в слесарный плашкодержатель. При выполнении этой операции необходимо соблюдать следующие условия: как только плашка начнет самоввинчиваться, надо прекратить принудительную подачу плашки пинолью задней бабки (рис. 1.80, а); нарезав резьбу, не доходя до уступа А на 1…1,5 шага нарезаемой резьбы (рис. 1.80. б), выключить станок, отвести пиноль в исходное положение, включить станок на обратное вращение и свинтить плашку (рис. 1.80, в).
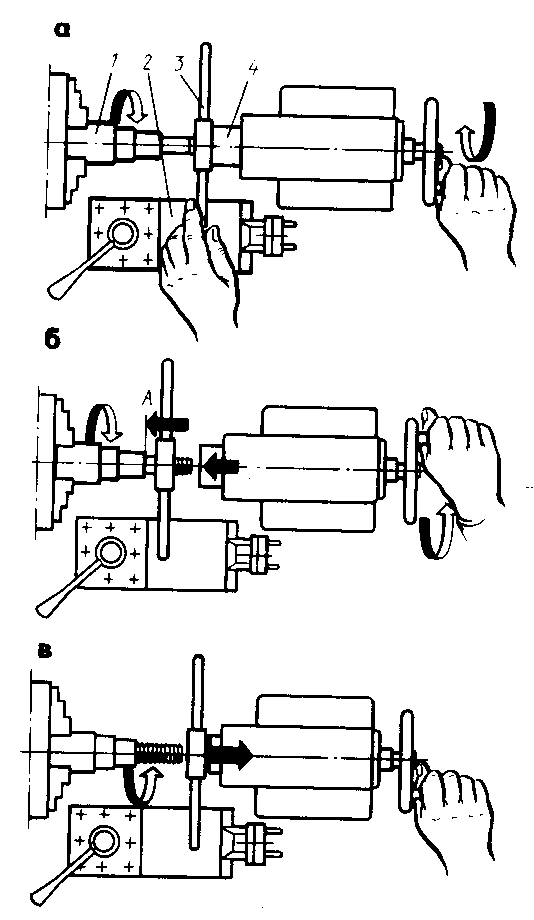
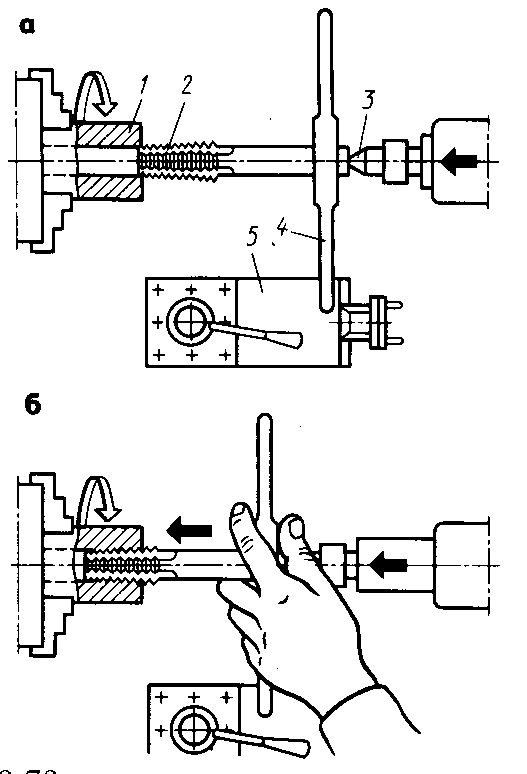
1 - заготовка; 2 - верхние салазки суппорта; 3 - плашкодержатель с плашкой; 4 - пиноль задней бабки
Рисунок 1.80
Приемы нарезания наружной треугольной резьбы плашкой
1 - заготовка; 2 - метчик; 3 - задний центр; 4 - вороток;
5 - верхние салазки суппорта
Рисунок 1.81
Приемы нарезания внутренней
треугольной резьбы метчиком
При нарезании резьбы не в упор выключать шпиндель можно в момент перемещения плашки на всю требуемую длину резьбы. Нарезанную резьбу проверить резьбовым калибром-кольцом или скобой.
На рис. 1.81. показаны приемы нарезания внутренней треугольной резьбы метчиком, поджатым центром задней бабки и с надетым на хвостовик воротком.
При выполнении этой операции необходимо соблюдать следующие требования: вводить заборную часть метчика в отверстие заготовки перемещением пиноли задней бабки (рис. 1.81, а), после начала самозатягивания метчика следить за тем, чтобы вершина заднего центра не выходила из центрового отверстия метчика (рис. 1.81, б).
Если надо нарезать резьбу в глухом отверстии, то станок выключает в тот момент, когда риска, нанесенная мелом на хвостовик метчика, приблизится к торцу заготовки. Удалять метчик из глухого отверстия следует путем обратного вращения шпинделя, предварительно отведя пиноль в исходное положение.
При нарезании резьбы в сквозном отверстии выключение вращения шпинделя производят при перемещении метчика на всю длину резьбы. Метчик удаляют из заготовки путем снятия ее из патрона (с противоположной стороны).
Нарезанную резьбу проверить резьбовым калибром-пробкой.
Скорость главного движения резания выбирают в зависимости от марки обрабатываемого материала, металла, из которого изготовлен инструмент, диаметра и шага резьбы. При нарезании резьбы метчиками в заготовках из стали рекомендуется скорость главного движения резания 3..12 м/мин, а из чугуна, бронзы и алюминия – 4…20 м/мин. При нарезании резьбы плашками рекомендуется следующие скорости главного движения резания: для стали – 3…4 м/мин, для чугуна и бронзы – 2…3 м/мин, для латуни – 9…15 м/мин. Обработку ведут с охлаждением.
Выбор смазочно-охлаждающей жидкости также зависит от обрабатываемого материала; например, при обработке стали применяют эмульсию, растительные, минеральные масла или сульфофрезол, при обработке чугуна применяют растительное масло, керосин или работают без охлаждения и смазки.
Нарезание резьбы резцами
Оснащение рабочего места: то же, что и для темы 1.2., кроме того, плакаты; резьбовые резцы для нарезания метрической резьбы; шаблоны для установки резьбовых резцов; заготовки для нарезания резьбы, предварительно обточенные под нарезание резьбы. Набор резьбовых валиков и деталей с внутренней резьбой и различные резьбовые измерительные инструменты (резьбомеры, калибри-кольца, предельные резьбовые скобы, резьбовые микрометры и др.) для тренировочных приемов по измерению наружной и внутренней метрической резьбы.
Нарезание резьбы резцами производится на токарно-винторезных станках, имеющих ходовой винт с разъемной гайкой, гитару сменных колес, коробку подач и реверсивный механизм. На станке можно нарезать различные резьбы – наружные и внутренние, правые и левые, однозаходные и многозаходные, крепежные и грузовые; по форме профиля – треугольные. Прямоугольные, трапецеидальные и др. Кроме того, на токарно-винторезных станках нарезают червяки.
Перед нарезанием резьбы заготовку обтачивают (растачивают) до определенного диаметра, который должен быть несколько меньше наружного диаметра резьбы. Это объясняется наличием упругих и пластических деформаций, возникающих в материале заготовки, от чего наружный диаметр отверстия уменьшается. Выбор диаметра заготовки производится по специальным таблицам.
Для нарезания резьбы применяют стержневые, призматические и круглые (дисковые) резцы и резьбовые гребенки. Более широкое применение находят стержневые резцы. У резцов для окончательной обработки передний угол γ = 0, у резцов для предварительной обработки резьбы, когда искажение профиля работы не имеет большого значения, применяют положительный передний угол γ =10…200. Угол профиля ε режущий части резца равен углу профиля резьбы (для метрической – 600, для дюймовой – 550). Угол профиля режущей части резца и установку его в резцедержателе измеряют шаблоном или угломером на просвет.
Для нарезания резьбы необходимо увязать вращение заготовки (шпинделя) со скоростью движения подачи резьбового резца (суппорта). Резьба нужного шага получится в том случае, когда за один оборот заготовки резец переместится в продольном направлении на один шаг (нитку) нарезаемой резьбы.
Современные токарно-винторезные станки с коробкой подач имеют очень простую настройку на заданный шаг резьбы. Настройка сводится либо к нахождению по таблице, прикрепленной в зависимости от модели станка к верхней или боковой стенке коробки подач, или на барабане настройки станка на требуемую резьбу нужного положения рукояток барабана коробки подач, либо чисел зубьев сменных зубчатых колес и установке их в нужное положение. Станки обычно имеют два комплекта сменных колес. Так, например, у станка модели 1К62 для нарезания крепежных метрических и дюймовых резьб служат сменные зубчатые колеса 42-50, для нарезания модульных и питчевых червяков – сменные зубчатые колеса 64:97 (см. рис. 1.7.).
В тех токарно-винторезных станках, в которых нет коробки подач, настройку производят только по расчету. К таким станкам прилагают комплекты сменных зубчатых колес из 17, 19, 38 и другого количества колес.
Резьбу нарезают за несколько предварительных и окончательных ходов, количество которых зависит от шага резьбы.
Применяют несколько способов (схем) подачи резьбового резца на глубину резания при каждом проходе. При нарезании резьбы с шагом Р > 2 мм резец подается в поперечном направлении перпендикулярно оси нарезаемой заготовки – радиальная подача (рис. 1.82,а). При нарезании резьбы с шагом Р > 2…2,5 мм для облегчения деформации и свободного выхода стружки из зоны резания применяют комбинированную подачу резца – одновременно поперечную и продольную (рис. 1.82, б). Вторая схема резания может быть также осуществлена с помощью подачи верхних салазок суппорта, повернутых к оси центров станка под углом 600 (рис. 1.82, в). Для получения более точной резьбы окончательные проходы желательно выполнять только с радиальной подачей – по первой схеме.
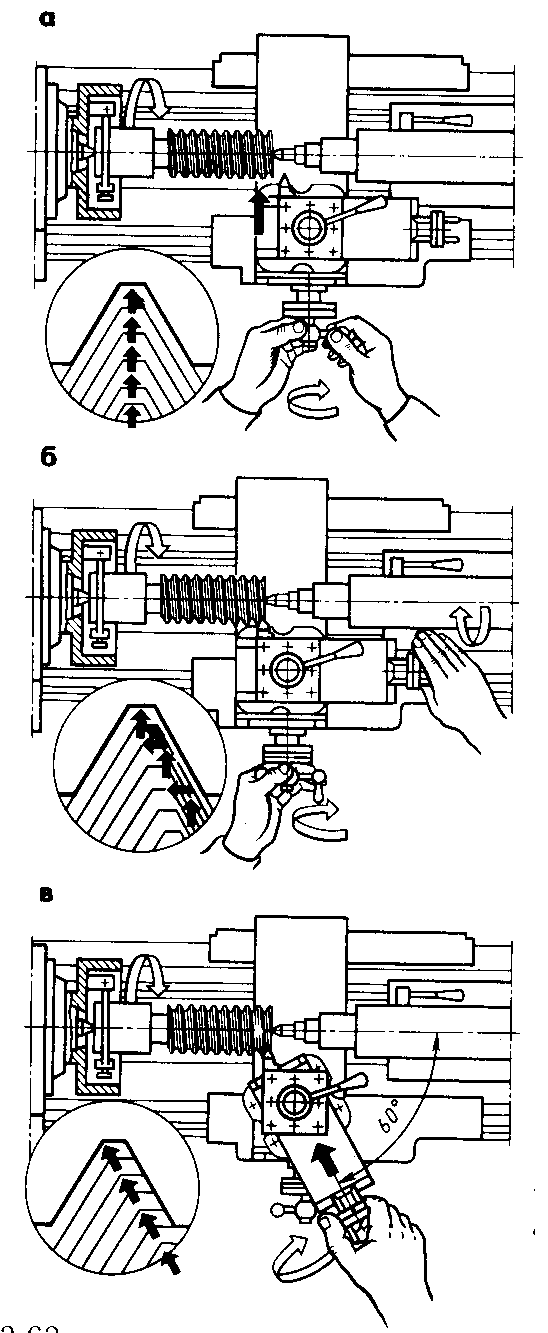
Рисунок 1.82 Схемы поперечных подач при
нарезании резьбы резцом
Возврат резьбового резца в исходное положение для выполнения очередного прохода осуществляют двумя способами, выбор которых зависти от шага нарезаемой резьбы и шага ходового винта станка.
При нарезании на токарно-винторезном станке различают кратную (четную) и некратную (нечетную) резьбы. Кратной называют резьбу, у которой отношение шага Рх резьбы ходового винта делится без остатка на шаг Рн нарезаемой резьбы или число ниток nн на 1” нарезаемой дюймовой резьбы делится без остатка на число ниток nх ходового винта. Некратной называют такую резьбу, у которой в результате указанного деления получаются дробные, а не целые числа.
При нарезании кратной резьбы возврат резца (суппорта) в первоначальное положение осуществляется путем выключения разъемной гайки ходового винта и быстрого перемещения суппорта вручную При нарезании некратной резьбы, после ввода резца от заготовки в поперечном направлении, переключают вращение шпинделя на обратный (ускоренный) ход, не размыкая разъемной гайки, и перемещают суппорт с резцом в исходное положение для выполнения очередного прохода.
Прямоугольную и трапецеидальную резьбу и червяки в зависимости от размеров нарезают одним или несколькими резцами (рис. 1.83, а…г).
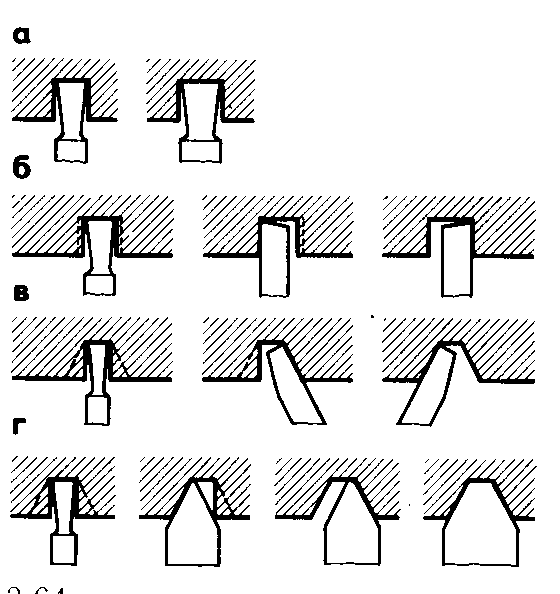
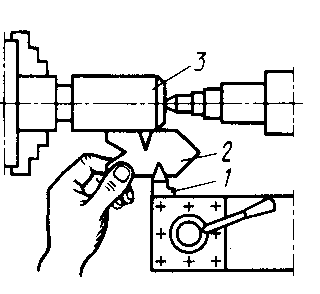
а - прямоугольной резьбы двумя резцами; б - прямоугольной резьбы тремя резцами; в, г - трапецеидальной резьбы тремя или четырьмя резцами
Рисунок 1.83 Схемы нарезания
прямоугольной и
трапецеидальной резьбы
Рисунок 1.84 Установка резьбового резца
на станке
При нарезании резьбы применяют различные смазочно-охлаждающие жидкости, которые поглощают теплоту, уменьшают трение трущихся поверхностей резца и заготовки, удаляют мелкие частицы стружки. При обработке стальных деталей используют эмульсию, масло, сульфофрезол; бронзовых и латунных – без охлаждения или сурепное масло; чугунных – без охлаждения или керосин.
Упражнение по нарезанию наружной треугольной (метрической) резьбы со свободным входом заключается в выполнении следующих приемов:
- Установить заготовку требуемого диаметра в центрах станка.
- Предварительно установить и закрепить резьбовой резец 1 (рис. 1.84) в резцедержателе, затем взять резьбовой шаблон 2 в левую руку и приставить его к поверхности заготовки 3. Перемещая салазки суппорта, ввести головку резца в треугольный вырез резьбового шаблона. В случае неплотного прилегания боковых сторон головки к стенкам профиля шаблона надо изменить установку резца в резцедержателе и окончательно закрепить резец.
- Настроить токарно-винторезный станок на заданный шаг нарезаемой резьбы, например Р=1 мм, для чего диск 5 барабана Б (см.рис. 1.7) за две рукоятки вытянуть на себя, затем повернуть его до ряда подач на таблице с шагом резьбы 1 мм, совместить риску диска с риской барабана Б и диск подать вперед в прежнее положение. Таблица резьб и подач укреплена на боковой поверхности барабана Б.
Затем повернуть барабан 6 до совмещения графы таблицы «Резьбы метрические» и проверить наличие установки сменных зубчатых колес 42:50. По таблице резьбы и подач по стрелке А от шага резьбы 1 мм, обозначенным жирным четырехугольником, устанавливаем, что рукоятку 3 следует поставить в положение Б – «Нормальный шаг»; по стрелке Б от 1 мм рукоятку 2 поставить влево на ряд чисел оборотов 12,5…2000; рукоятку 4 поставить в положение Д – «Нормальный шаг – правый».
4. Для проверки правильности настройки станка на нарезание заданной резьбы необходимо суппорт отвести в сторону задней бабки, настроить станок на минимальную частоту вращения шпинделя, пустить станок и по длине следа перемещения суппорта за определенное число оборотов шпинделя определить правильность настройки. Проверку настройки станка можно сделать резьбомером после пробного прохода на дефектной заготовке.
5
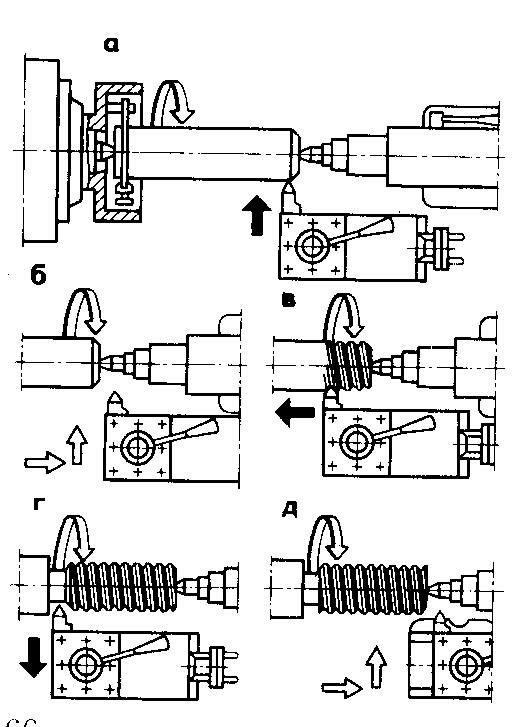
. Настроить станок на требуемую частоту вращения шпинделя, для чего по таблицам нормативов или указанию мастера подобрать скорость главного движения резания для предварительного (а затем окончательного) нарезания резьбы и количества проходов. По скорости главного движения резания и диаметру заготовки определить частоту вращения шпинделя.
Рисунок 1.85 Приемы нарезания наружной
треугольной резьбы
6. Установить резец на требуемую глубину резания для первого прохода, для чего пустить станок и, вращая рукоятку винта поперечной подачи, подвести резец до касания с поверхностью заготовки (рис. 1.85,а).Затем отвести резец вправо на 10…15 мм за пределы торца заготовки, подать резец в поперечном направлении на заданную длину в зависимости от шага нарезаемой резьбы для первого прохода (0,3…0,5 мм), после чего лимб установить на нуль (рис. 1.85,б).
7. Приступить к нарезанию резьбы, для чего сделать первый проход, включив станок и разъемную гайку ходового винта (рис. 1.85,в). Как только резец пройдет весь участок заготовки, предусмотренный для нарезания резьбы, и начнет входить в канавку заготовки для выхода резьбы, остановить станок, вывести резец из канавки на себя (рис. 1.85,г), возвратить его в исходное рабочее положение для второго и последующих проходов (рис. 1.85. д). При втором и последующих проходах поперечную подачу уменьшать на 0,3…0,1 мм.
Отводить резец на себя в конце каждого прохода и перемещать его в исходное рабочее положение надо рукояткой винта движения поперечной подачи, устанавливая каждый раз лимб на нулевое деление.
Для чистового нарезания наружной треугольной резьбы необходимо выполнить следующие приемы:
- Установить в центрах (или в патроне) заготовку с предварительно нарезанной резьбой.
- Установить и закрепить чистовой резьбовой резец.
- Подобрать по таблицам требуемую скорость главного движения резания и настроить станок на найденную частоту вращения шпинделя.
- Ввести резьбовой резец во впадину предварительно нарезанной резьбы и, вращая соответствующие рукоятки продольной и поперечной подач верхних и нижних салазок суппорта, добиться плавного и равномерного прилегания режущих кромок резца к боковым сторонам профиля резьбы, после чего, включив станок и разъемную гайку, переместить суппорт на несколько витков в продольном направлении.
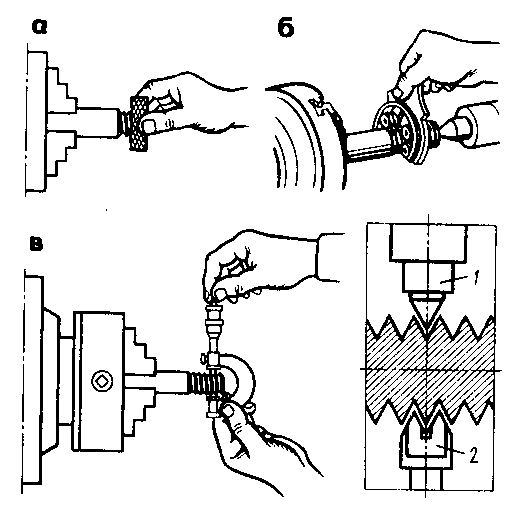
1 - призматическая вставка пятки; 2 - конусная вставка микрометрического винта
Рисунок 1.86 Способы контроля наружной резьбы
- Сделать первый проход для окончательного нарезания резьбы.
- Окончательно нарезать резьбу, сделав второй, третий и т.д. проходы резца, подавая резец на требуемую глубину резания только движением прямой поперечной подачи на 0,1...0,2 мм.
- Проверить нарезанную резьбу калибром-кольцом (рис. 1.86,а), резьбовой скобой (рис. 1.86,б) или резьбовым микрометром (рис. 1.86, в). О способах применения контрольно-измерительного инструмента для проверки резьб см. в разделе 1.
При нарезании внутренних резьб применяют те же приемы установки и выверки резьбовых резцов, выполнения предварительных и окончательных проходов.
- Установить заготовку в трехкулачковом самоцентрирующемся патроне.
- Предварительно обработать торец и отверстие заготовки для нарезания внутренней треугольной резьбы (рис. 1.87, а), применив для этого расточной упорный резец с главным углом в плане φ = 950.
- Настроить станок на шаг нарезаемой резьбы и на требуемую частоту вращения шпинделя.
- Установить и закрепить резьбовой резец в резцедержателе по шаблону (рис. 1.87. б), нанести на резце мелом риску А на расстоянии от вершины головки, равном длине резьбы.
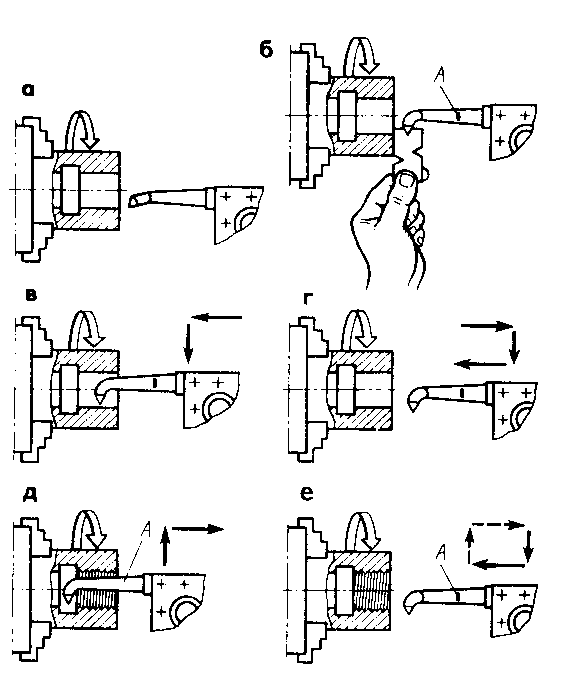
Рисунок 1.87
Приемы нарезания внутренней треугольной резьбы
- Установить резец на врезание для первого прохода, для чего пустить станок и подвести резец до касания вершины его головки с поверхностью отверстия заготовки (рис. 1.87, в). Остановить станок и отвести резец вправо от торца заготовки на 10…15 мм, движением поперечной подачи подать резец на требуемую глубину резания (0,1…0,5 мм), затем лимб установить на нулевое деление (рис. 1.87,г).
- Сделать первый проход для чего пустить станок и включить разъемную гайку. Как только риска А на резце начнет приближаться к торцу, остановить станок, вращением винта поперечной подачи отвести резец от нарезаемой поверхности и включить станок на обратное вращение шпинделя (рис. 1.87, д), остановить станок при выходе резца из отверстия на 10…15 мм от торца и обратной поперечной подачей переместить резец в исходное рабочее положение, поставив лимб на прежнее нулевое деление.
- Подать резец на врезание по лимбу на 0,1…0,3 мм, сделать второй и последующие проходы до получения требуемых размеров (рис. 1.87, е).
- Проверить нарезанную резьбу соответствующими калибром-пробкой.
При чистовом нарезании резьбы применяют чистовой резец с передним углом γ = 0 0, который устанавливается так же, как и черновой резец. Врезание за каждый проход 0,02 ..0,1 мм.
При нарезании обязательно применять смазочно-охлаждающую жидкость.
Контрольные вопросы:
- Назовите основные элементы резьбы.
- Чем отличаются однозаходные резьбы от многозаходных?
- Назовите способы и инструмент для нарезания наружной и внутренней резьбы?
- Как измеряют резьбы?
Тема 1.6 Обработка наружных и внутренних
конических поверхностей
Студент должен
знать:
- основные параметры конических соединений;
- способы обработки конических поверхностей.
уметь:
- производить обработку конических поверхностей;
- контролировать размеры конических поверхностей.
Оснащение рабочего места: то же, что и для темы 1.2., кроме того, резцы расточные с различной длиной стержня: резцы специальные широкие; сверла, развертки конические; набор измерительных инструментов для контроля наружных и внутренних конических поверхностей (штангенциркуль, конические калибры, втулки, пробки, универсальные угломеры, шаблоны, измерительная линейка); плакаты, чертежи обрабатываемых деталей с наружными и внутренними коническими поверхностями; технологические карты с указанием режима резания; стальные и чугунные заготовки с предварительно обработанными для данного занятия поверхностями; мел кусковой; тампон с краской для калибров; щетка-сметка; защитные очки.
Обработку конических поверхностей на токарных станках выполняют различными способами: поворотом верхней части суппорта; смещением корпуса задней бабки; поворотом конусной (копировальной) линейки; широким резцом. Применение того или иного способа зависит от длины конической поверхности и угла уклона конуса.
Обработка наружного конуса способом поворота верхних салазок суппорта целесообразна в тех случаях, когда необходимо получить большой угол уклона конуса при сравнительно небольшой его длине. Наибольшая длина образующей конуса должна быть несколько меньше хода каретки верхнего суппорта.
Обработка наружного конуса способом смещением корпуса задней бабки удобна для получения длинных пологих конусов с малым углом уклона (3…50).Для этого корпус задней бабки сдвигают в поперечном направлении от линии центров станка по направляющим основания бабки. Обрабатываемая заготовка закрепляется между центрами станка в поводковом патроне с хомутиком.
Обработку конусов с помощью конусной (копировальной) линейки, закрепленной с задней стороны станины токарного станка на плите, применяют для получения пологого конуса значительной длины. Заготовку крепят в центрах или в трехкулачковом самоцентрирующемся патроне. Резец, закрепленный в резцедержателе суппорта станка, получает одновременное перемещение в продольном и поперечном направлениях, в результате чего обрабатывает коническую поверхность заготовки.
Обработку наружного конуса широким резцом применяют при необходимости получения короткого конуса (l < 25 мм) с большим углом уклона. Широкий проходной резец, режущая кромка которого длинней образующей конуса, устанавливают в резцедержатель так, чтобы главная режущая кромка резца составляла с осью заготовки угол α, равный углу уклона конуса. Обработку можно вести как с продольной, так и с поперечной подачей.
На чертежах деталей часто не указывают размеры, необходимые для обработки конуса, и их необходимо подсчитывать. Для подсчета неизвестных элементов конусов и их размеров (в мм) (рис. 1.88) можно пользоваться следующими формулами:
а) конусность К=(D-d) / 2l или tg α = К/2;
б) угол уклона конуса tg α = (D-d) / (2l) = K/2;
в) уклон i = K/2= (D-d) / (2l) = tg α;
г) большой диаметр конуса D = Kl+d = 2ltg α;
д) меньший диаметр конуса d=D-Kl = D-2ltg α;
е) длина конуса l = (D-d) K= (D-d) / (2 tg α).
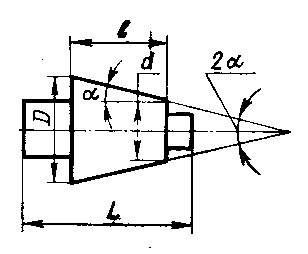
D - большой диаметр конуса; d - малый диаметр конуса; L - длина детали; l - длина конуса; α - угол уклона конуса; 2α - угол при вершине конуса
Рисунок 1.88 Элементы конуса
Обработку внутренних конических поверхностей на токарных станках выполняют также различными способами: широким резцом; поворотом верхней части (салазок) суппорта; поворотом конусной (копировальной) линейки. Внутренние конические поверхности длиной до 15 мм обрабатывают широким резцом, главная режущая кромка которого установлена под требуемым углом к оси конуса, осуществляя продольную или поперечную подачу. Этот способ применяют в том случае, когда угол уклона конуса большой, а к точности угла уклона конуса и шероховатости поверхности не предъявляют высоких требований. Внутренние конусы длиной > 15 мм, при любом угле наклона обрабатываются поворотом верхних салазок суппорта с применением ручной подачи. Наибольшая длина образующей конуса должна быть несколько меньше хода каретки верхнего суппорта. Обтачивание внутренних конических поверхностей с помощью конусной линейки применяют при обработке заготовок любой длины с малым углом уклона конуса (примерно до 120).
Независимо от способа обработки конуса резец обязательно устанавливают точно по высоте центров станка.
Упражнение по обтачиванию наружных конических поверхностей смещением корпуса задней бабки заключается в выполнении следующих приемов:
- Определить смещение корпуса задней бабки (мм):
H = L (D-d) / (2l)
г
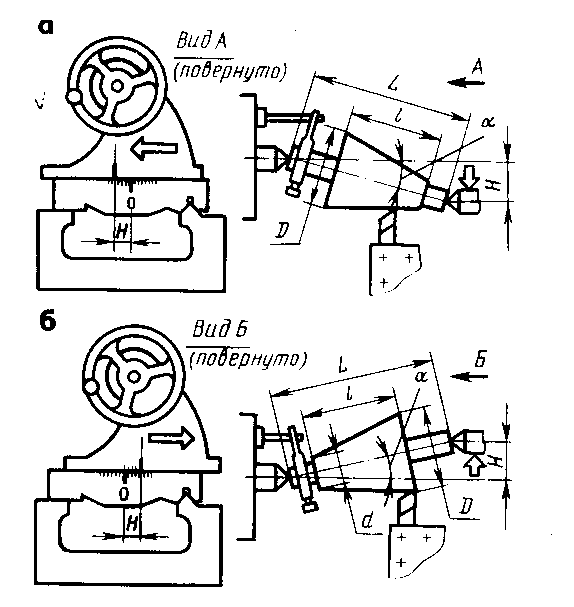
де D и d – диаметры конуса; L – общая длина заготовки; l – длина конуса.
Рисунок 1.89 Обработка конических поверхностей
смещением корпуса задней бабки
2. Сместить корпус задней бабки по направляющим ее основания. При смещении корпус задней бабки на себя (рис. 1.89, а) конус своим большим диаметром обращен к передней бабке; при смещении от себя (рис. 1.89, б) большой диаметр конуса обращен к задней бабке. Отсчет смещения Н задней бабки производят по делениям, нанесенным на торцовой поверхности корпуса задней бабки от риски 0 (плоскость оси центров).
Правильность смещения задней бабки корректируют пробным обтачиванием и проверкой полученного угла конуса.
3. Установить и закрепить заготовку и проходной резец. Заготовку устанавливают в центрах. Задний центр из-за смещения оси вращения заготовки целесообразно применять с шаровой вершиной (сферической) или вращающейся. Вершину головки проходного резца установить обязательно на уровне линии центров станка.
4. Обточить коническую поверхность детали предварительно, предусмотрев припуск для окончательного прохода. Обработку выполнить с прямой продольной механической подачей резца.
5. Проверить конусность обработанной поверхности заготовки и установить правильность настройки станка.
6. Обточить коническую поверхность окончательно, для чего настроить станок на требуемый режим резания.
7. Проверить обработанную коническую поверхность по размерам с помощью штангенциркуля и конического калибра-втулки.
Упражнение по обтачиванию наружных конических поверхностей широким резцом.
Схема обработки конической поверхности широким резцом показана на рис. 1.90, а. Главную режущую кромку резца затачивают и устанавливают под углом α, равным половине угла конуса с помощью шаблона. Коническая поверхность может быть образована движением как поперечной, так и продольной подач. Чтобы предотвратить смещение суппорта вдоль станины от действия сил резания на суппорт, его необходимо закрепить зажимным болтом. Если зажимного (стопорного) болта на суппорте нет, то надо выключить механизм подачи и включить либо механическую продольную подачу (ходовой вал), либо разъемную гайку (ходовой винт). Длина режущей кромки резца должна быть несколько больше длины образующей конуса. Указанным способом можно обрабатывать заготовки, длина конической поверхности которых не превышает 20…25 мм.

Рисунок 1.90 Схемы обработки конусов широким
резцом (а) и поворотом верхних салазок
суппорта (б)
Упражнение по обтачиванию наружных конических поверхностей поворотом верхних салазок 1 суппорта (рис. 1.90, б) заключается в выполнении следующих приемов:
1. Установить и закрепить в трехкулачковом патроне заготовку с предварительно обработанной цилиндрической поверхностью и проходной резец в резцедержателе. Вершину головки резца установить обязательно на уровне линии центров станка.
2. Если на чертеже размер угла уклона конуса α не указан, то угол поворота верхней части суппорта определяют по данным чертежа обрабатываемой детали. Тангенс угла уклона конуса
tgα = (D-d) / (2l) или tgα = K / 2
Угол уклона конуса находят по таблице тангенсов углов.
3. Повернуть верхнюю поворотную часть суппорта на требуемый угол уклона конуса так, чтобы риска нижнего фланца совпадала с делением градуированной шкалы 2 поворотного фланца, равного углу уклона конуса α. Если конус детали вершиной обращен в сторону задней бабки, то верхнюю поворотную часть суппорта повернуть от себя; если вершина конуса обращена в сторону передней бабки, то верхнюю часть суппорта повернуть на себя.
4. Обточить коническую поверхность детали предварительно, предусмотрев припуск для окончательного прохода. Подача резца осуществляется вручную, путем вращения винта верхних салазок суппорта плавно, обеими руками по часовой стрелке.
5. Проверить конусность предварительно обработанной поверхности заготовки и установить правильность настройки станка.
Конусность проверить следующими способами: измерением диаметров оснований конуса штангенциркулем; калибром –втулкой, по меловым или карандашным линиям (при повороте калибра-втулки линии должны стираться равномерно по всей длине); универсальным угломером, по плотности прилегания измерительных поверхностей угломера к образующей конической поверхности детали.
6. Обточить коническую поверхность окончательно, для чего настроить станок на требуемый режим резания и установить чистовой проходной резец.
7. Проверить размеры обработанной конической поверхности штангенциркулем, для чего измерить диаметры оснований конуса. Полученная разность диаметров должна равняться разности диаметров оснований конуса, указанных на чертеже при одинаковом расстоянии между диаметрами.
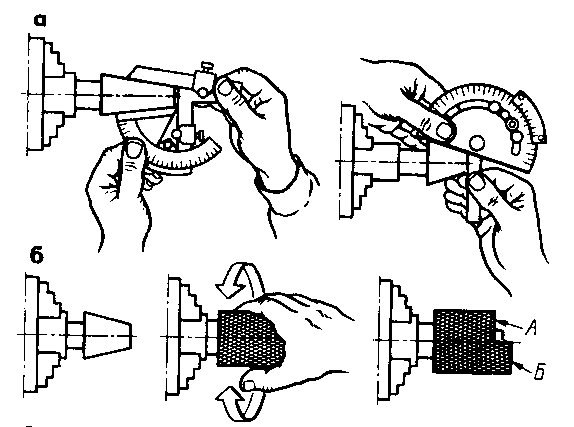
Рисунок 1.91 Способы контроля конической
поверхности
Правильность конической поверхности проверяют универсальным угломером по плотности прилегания измерительных поверхностей (рис. 1.91,а); калибром-втулкой по меловым линиям, «на краску» и предельными калибрами-втулками с двумя рисками или с уступом между торцами А и Б (рис. 1.91, б). Контроль конусов калибрами-втулками является комплексным методом, позволяющим одновременно проверить угол конуса, диаметры и длину. Годность изделия определяют осевым перемещением калибра до сопряжения с проверяемой поверхностью и проворачиванием его вокруг оси. При проверке «на окраску» равномерность слоя красящего вещества на конусной поверхности обрабатываемой заготовки характеризует точность угла конуса. Положение торца заготовки относительно размера между контрольными рисками или торцами А и Б уступа характеризует размер диаметров и длины. При правильном выдерживании размеров конической поверхности торец заготовки не должен выходить за пределы торцов А и Б уступа калибра втулки. Если торец заготовки не доходит до торца А, то заготовку следует дополнительно обточить, а если торец заготовки выходит за торец Б, то ее размеры занижены, что является неисправимым браком.
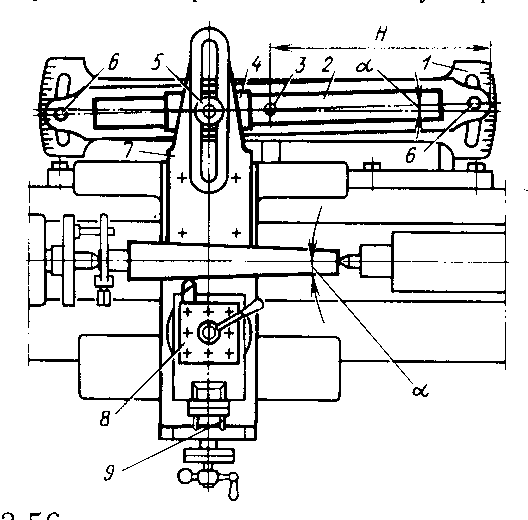
Рисунок 1.92 Обработка конической поверхности с
применением конусной линейки
Упражнение по обтачиванию наружных конических поверхностей с применением конусной линейки (рис. 1.92) заключается в выполнении следующих приемов:
- Определить угол уклона конуса
tgα = (D-d) / (2l)
Если шкала поворота на торце конусной линейки задана не в градусах, а в миллиметрах, то число делений на которое надо повернуть линейку,
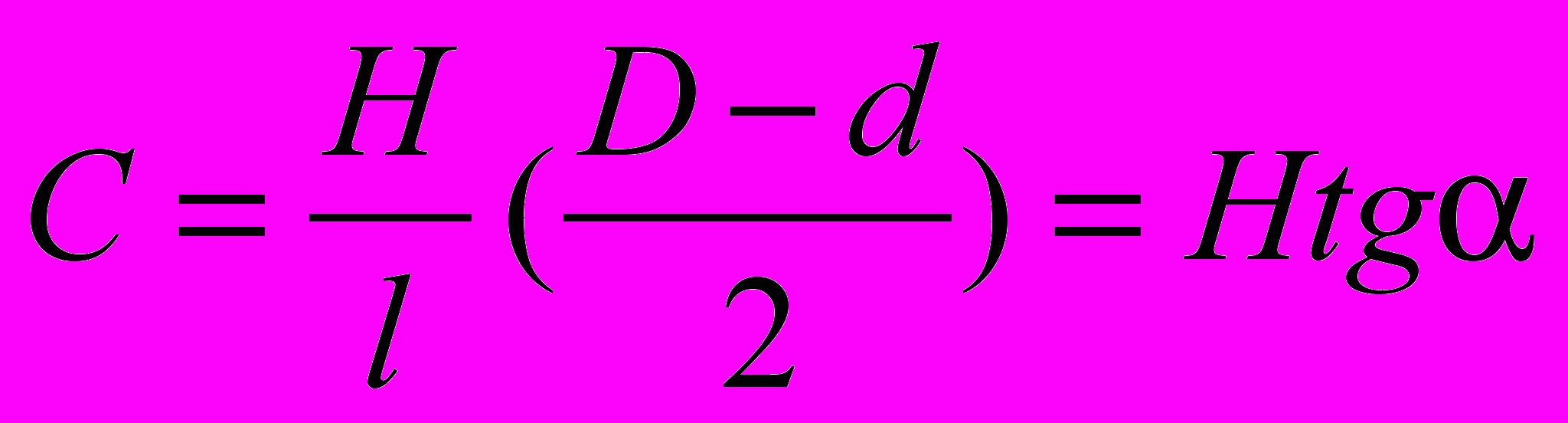
где Н – расстояние от оси вращения линейки до торца, на котором нанесена шкала, мм.
2. Наладить станок на обтачивание наружной конической поверхности, для чего необходимо ослабить гайки 6 (рис. 1.92), повернуть линейку 2 около ее оси 3 на угол α (пользуясь) градуированной шкалой на плите 1), повернуть верхнюю повортную часть (салазки) суппорта 8 на угол 900 к оси заготовки, закрепить гайкой 5 поперечные салазки 7 суппорта с ползуном 4. При отсутствии специального паза для гайки надо временно удалить из поперечных салазок 7 суппорта.
3. Установить и закрепить заготовку в трехкулачковом патроне или в центрах.
4. Обточить предварительно коническую поверхность детали. Резец подавать на требуемую глубину резания, вращая рукоятку с лимбом 9 винта верхней поворотной части суппорта.
Продольное механическое перемещение резец получает от ходового вала станка, а поперечное – от конусной линейки.
5. Проверить конусность обработанной поверхности заготовки.
6. Обточить коническую поверхность окончательно.
7. проверить размеры обработанной конической поверхности с помощью конического калибра-втулки, универсального угломера или штангенциркуля.
Упражнение по растачиванию конических поверхностей с помощью поворота верхних салазок суппорта заключается в выполнении следующих приемов:
1. Просверлить отверстие под растачивание (рис. 1.93, а), для чего взять сверло диаметром на 2…3 мм меньше малого диаметра d обрабатываемого конического отверстия и закрепить его в пиноли задней бабки. Если заготовка уже имеет отверстие, полученное при предварительной обработке, то в зависимости от припуска вместо сверления производят рассверливание, зенкерование или непосредственно растачивание отверстия.
2. Расточить коническое отверстие предварительно, для чего повернуть верхние салазки суппорта на себя на требуемый угол уклона конуса α, переместить верхние салазки в крайнее левое положение, настроить, установить и закрепить расточной проходной резец (рис. 1.93, б), подвести резец к заготовке и проточить отверстие на длине 2…3 мм, проверить полученный размер и расточить отверстие начерно. Салазки подавать равномерно, вращая рукоятку их винта обеими руками по ходу часовой стрелки.
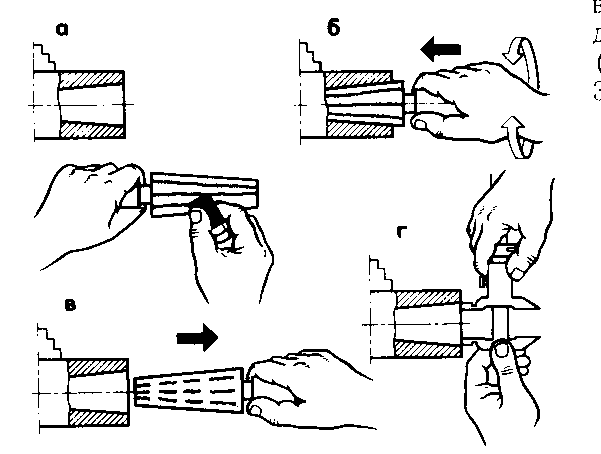
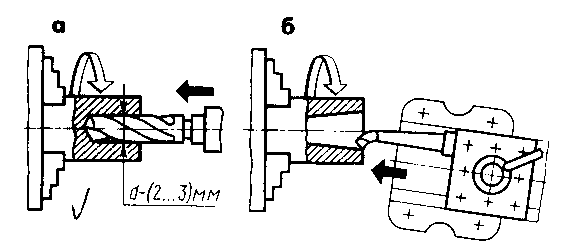
Рисунок 1.93 Обработка внутренней конической
поверхности поворотом верхних
салазок суппорта
Рисунок 1.94 Способы контроля внутренней
конической поверхности
3. Проверить конусность обработанной поверхности отверстия заготовки с помощью конического калибра-пробки по меловым линиям или «по краске», для чего на калибр-пробку нанести несколько продольных меловых линий (рис. 1.94, а) и калибр ввести в отверстие заготовки, а затем два-три раза провернуть в ней (рис. 1.94,б). Если меловые линии стерлись равномерно, то конусность конического отверстия выдержана правильно. Если меловые линии стерлись посредине поверхности калибра, то это значит, что резец установлен выше или ниже линии центров станка и его необходимо установить правильно и продолжить растачивание отверстия.
Если линия стерлась со стороны большего диаметра конуса калибра-пробки (рис. 1.94, в), то поворотную часть суппорта надо несколько повернуть по ходу часовой стрелки (увеличить угол уклона конуса α) и снова снять пробную стружку, и так поступать до получения требуемой конусности отверстия.
4. Расточить коническое отверстие окончательно, для чего настроить станок на требуемый режим резания, установить расточной чистовой проходной резец. Растачивая отверстие ручной подачей, необходимо добиться равномерного вращения рукоятки винта верхних салазок обеими руками, что обеспечивает получение гладкой и чистой поверхности.
5. Проверить конусность и размеры окончательно расточенного конического отверстия и сравнить их с размерами, указанными на чертеже детали. Правильность их можно проверить с помощью штангенциркуля и конического калибра-пробки. При измерении диаметра большего основания конуса толщину измерительных губок штангенциркуля прибавлять к прочитанному размеру (рис. 1.94, г).
При проверке конического отверстия калибром-пробкой (комплексным методом) годность изделия определяют осевым перемещением калибра до сопряжения с проверяемой поверхностью отверстия и поворачиванием его вокруг оси. Точность угла конуса и прямолинейность образующей характеризуются видом и степенью стирания меловых линий или слоя краски с поверхности калибра, а размер диаметров и длины характеризуется положением торца обрабатываемой заготовки относительно размера или торцами уступа на коническом калибре-пробке.
Если не выдерживается хотя бы один из контролируемых параметров, то для его исправления необходимо применить соответствующий прием исправления брака, рекомендованный при выполнении предыдущего упражнения (предварительное растачивание).
Н
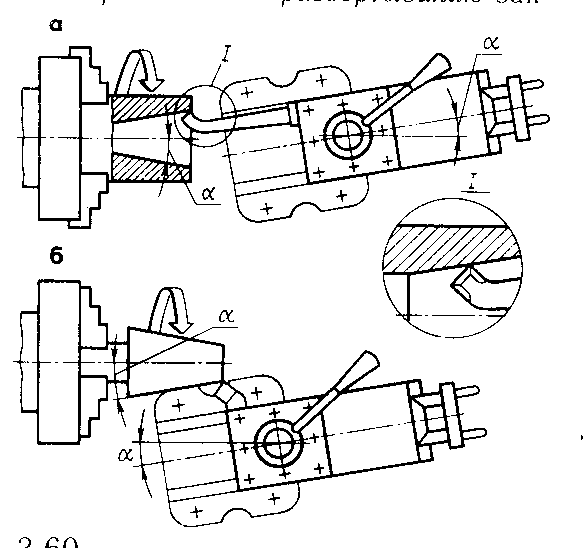
а рис. 1.95 приведены возможные дефекты при обработке конических отверстий. Если конусность выдержана, а диаметр отверстия меньше требуемого (обе риски на калибре видны, рис. 1.95, а), дефект может быть исправлен путем дополнительного растачивания; если конусность выдержана, а диаметр отверстия больше требуемого (обе риски на калибре ушли за пределы заготовки, рис. 1.95. б), дефект неисправим; если диаметр большего (или меньшего) основания конического отверстия выдержан, а конусность не выдержана в результате неправильной установки верхней поворотной части суппорта, дефект неисправим (рис. 1.95, в).
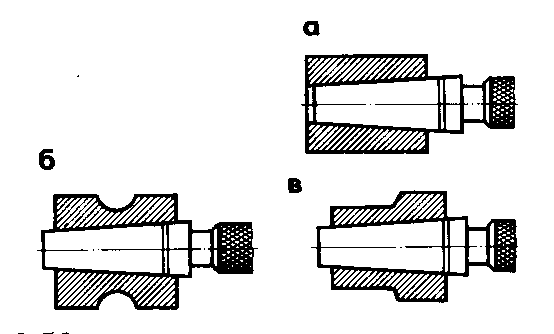
Рисунок 1.95 Возможные дефекты при обработке
конических отверстий
Рисунок 1.96 Обтачивание внутренней (а) и наружной (б)
сопрягаемых поверхностей без переналадки
верхних салазок суппорта
Упражнение по растачиванию конических отверстий с применением конусной линейки заключается в выполнении приемов, приведенных в предыдущем занятии при обтачивании с применением конусной линейки. Различие в наладке станка для обработки наружных и внутренних конусов состоит в изменении направления поворота конусной линейки. Для обработки наружных конусов правую часть линейки 2 (см. рис. 1.92) нужно повернуть в направлении от резца (центра), а при обработке отверстий – повернуть на угол α в направлении к резцу (центру). Затем установить и закрепить заготовку, расточной проходной резец, расточить отверстие предварительно. Конусность и размеры проверяют, как и при обработке конусных отверстий, с помощью верхней поворотной части суппорта.
Расточить коническое отверстие окончательно, для чего настроить станок на требуемый режим резания и установить расточной проходной резец. Проверить конусность и размеры конического отверстия калибром-пробкой.
Для точной обработки двух конических поверхностей (наружной и внутренней) рекомендуется использовать настройку станка, применяющуюся для обработки наружной конической поверхности. В этом случае растачивания конического отверстия выполняют тем же (прямым) вращением шпинделя, но резцом, обращенным к противоположной стороне поверхности отверстия и установленным режущей кромкой (передней поверхностью) головки резца вниз (рис. 1.96).
Развертывание конических отверстий. Внутренние конусные поверхности малых размеров в сплошном металле после сверления обрабатывают комплектом из трех конических разверток. Черновая развертка (рис. 1.97, а) при обработке образуют ступенчатое отверстие: получистовая развертка (рис. 1.97, б) со стружкоделительными канавками срезает уступы, образованные черновой разверткой; чистовая (рис. 1.97. в) защищает неровности, оставшиеся после обработки второй разверткой, и калибрует конус. Развертывание выполняют с применением соответствующей для данного металла смазачно-охлаждающей жидкости.
Упражнение по развертыванию заключается в выполнении следующих приемов:
1. Просверлить отверстие под развертываемое отверстие, для чего взять сверло диаметром на 0,5…1 мм меньше малого диаметра конического отверстия (рис. 1.98, а).
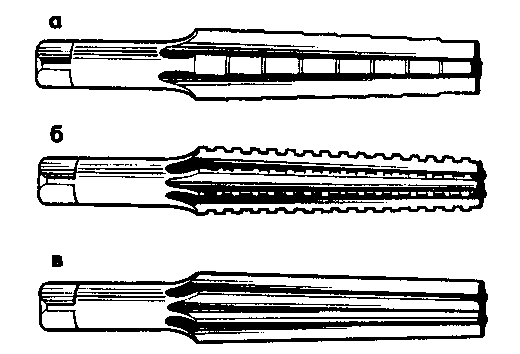
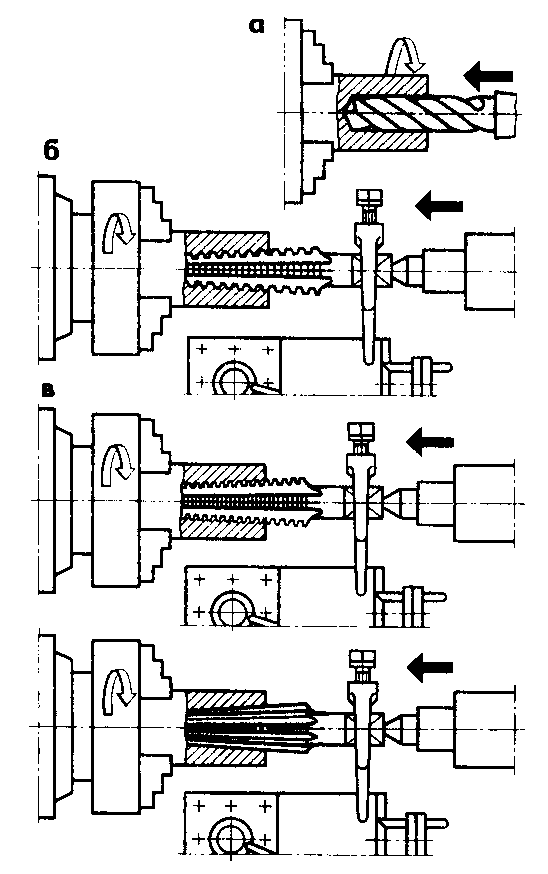
Рисунок 1.97 Комплект конических разверток
Рисунок 1.98
Развертывание конических отверстий
2. Подобрать режим резания для развертывания и настроить станок; для определения частоты вращения шпинделя надо брать больший диаметр конического отверстия.
3. На квадраты хвостовиков разверток надеть хомутики или воротки. Отрегулировать положение заднего центра, вставить черновую развертку вместе с хомутиком в отверстие заготовки, а центровым отверстием установить ее на задний центр. Хвостовик хомутика (или рукоятки воротка) должен упираться в поверхность верхних салазок. Поддерживая развертку левой рукой за хвостовик, прижать ее к центру задней бабки (рис. 1.98, б).
4. Включить станок. Правой рукой, вращая маховичок задней бабки, перемещать развертку вдоль оси отверстия на длину, соответствующую требуемому диаметру большего основания конического отверстия (с учетом припуска на последующее развертывание). Затем остановить станок и, поддерживая левой рукой хвостовик развертки за хомутик, вывести ее из отверстия.
Выполнить эти же приемы последовательно получистовой (рис. 1.98, в) и чистовой (рис. 1.98,г) развертками, оставляя для получистового развертывания припуск 0,5…1 мм, а для чистового – 0,1…0,2 мм.
5. После каждого перехода проверять размеры отверстия соответствующим коническим калибром-пробкой.
При развертывании отверстия необходимо выполнять следующие правила техники безопасности: не вводить и не выводить развертку на ходу станка; не удерживать руками хвостовик хомутика или рукоятку воротка, они должны быть прижаты к поверхности верхних салазок; не удалять из отверстия стружку, масло и грязь руками; не измерять размеры развертываемого отверстия на ходу станка.
На этом занятии учащийся должен обработать несколько заготовок с различными значениями углов уклона конуса α, применяя требуемый способ обработки конических поверхностей, и выполнить контроль обработанной детали.
Контрольные вопросы:
- Что называется конусностью и как она обозначается?
- Какие существуют методы обработки наружных и внутренних конических поверхностей?
- Как производится контроль конических поверхностей?
Тема 1.7 Технология обработки фасонных поверхностей
0бщие сведения. Поверхности деталей (как наружные, так и внутренние) относят к фасонным, если они образованы криволинейной образующей, комбинацией прямолинейных образующих, расположенных под различными углами к оси детали, или комбинацией криволинейных и прямолинейных образующих. На токарных станках фасонные поверхности получают:
• ручным или автоматическим поперечным и продольным движением подачи резца относительно заготовки с подгонкой профиля обрабатываемой поверхности по шаблону;
• фасонными резцами, профиль которых соответствует профилю обработанной детали;
• с помощью приспособлений и копирных устройств, позволяющих обработать поверхность заданного профиля;
• комбинированием перечисленных выше методов.
Фасонные поверхности на длинных деталях, заданный профиль которых получается с помощью шаблона, копира и приспособлений, обрабатывают проходными резцами из быстрорежущей стали или твердого сплава.
При обработке галтелей и канавок радиусом R < 20 мм на стальных и чугунных деталях применяют резцы, режущая часть которых выполнена по профилю обрабатываемой галтели или канавки.
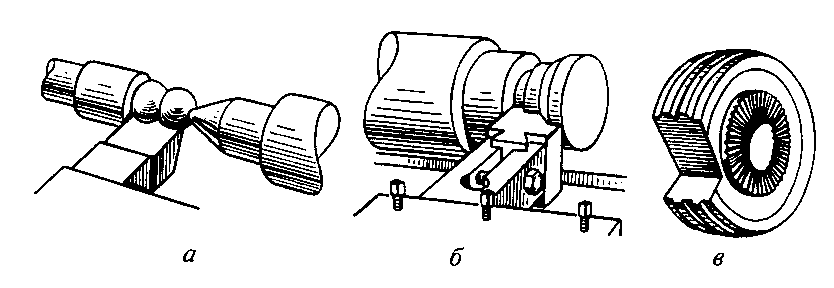
а - цельный; б - с механическим креплением режущей части; в - дисковый
Рисунок 1.99 Фасонные резцы
Для обработки галтелей и канавок радиусом R > 20 мм режущую часть резцов выполняют с радиусом округления, равным (1,5...2)R. При этом используют как продольное, так и поперечное перемещение суппорта.
Для повышения производительности обработки фасонных поверхностей сложного профиля применяют фасонные резцы (рис. 1.99). Ширина фасонных резцов не превышает 60 мм и зависит от жесткости системы станок - приспособление - инструмент -обрабатываемая деталь (СПИД) и радиального усилия резания.
Обработка проходными резцами. При небольшой партии заготовок и соответствующей подготовке рабочего фасонную поверхность можно обрабатывать проходным резцом при его одновременном продольном и поперечном движении, осуществляемом вручную.
При выборе резца форма его вершины и расположение режущих кромок должны позволить обработать фасонную поверхность с заданными углами наклона и радиусами.
Для приобретения навыка одновременного продольного и поперечного перемещения резца по заданной траектории следует предварительно (перед обработкой фасонной детали) выполнить несколько упражнений, что позволит освоиться с особенностями управления станком при фасонной обработке. Для этого в патроне или в центрах устанавливают готовую деталь с фасонной поверхностью сложного профиля. Перемещая суппорт координированным вращением его рукояток, следят за тем, чтобы вершина резца перемещалась в непосредственной близости (с одинаковым зазором до 1 мм) от поверхности детали.
Убедившись в надежности управления станком, переходят к обработке детали с фасонной поверхностью. На рис. 1.100, а показана последовательность обработки описанным способом фасонной поверхности заготовки рукоятки. Заготовку закрепляют в трехкулачковом патроне, используя для этого поверхность А (рис.1.100, б), и обрабатывают проходным резцом хвостовую часть рукоятки, состоящую из поверхностей В, С, D, и Е. Установив рукоятку в патроне по поверхности G (рис. 1.100, в), обрабатывают фасонную часть рукоятки. С помощью шкалы на станине станка производят разметку (вдоль оси заготовки) наибольшего и наименьшего диаметров фасонной поверхности рукоятки, а затем проходным резцом снимают черновой припуск в несколько проходов (см. заштрихованные участки на рис. 1.100, в).
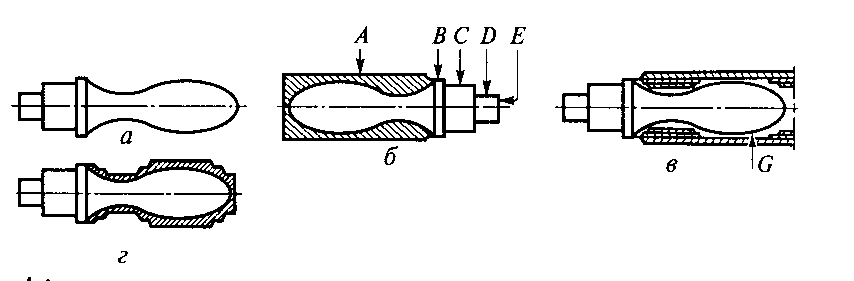
а - готовая деталь; б, в и г - полуфабрикаты для получения детали;
А, В, С, D,E и G - обрабатываемые поверхности
Рисунок 1.100 Последовательность обработки фасонной поверхности рукоятки проходным резцом с применением продольной и поперечной подач
Окончательный съем припуска (рис. 1.100, г) выполняют в несколько проходов. Вначале аккуратно снимают гребешки плавным перемещением резца вдоль оси обрабатываемой детали и возвратно-поступательным перемещением поперечных салазок суппорта. Затем к невращающейся заготовке прикладывают шаблон с профилем готовой детали, измеряют наибольший и наименьший диаметры фасонной поверхности и определяют места, с которых необходимо снять припуск. Для облегчения условий труда и повышения его производительности опытные рабочие используют автоматическую продольную подачу, перемещая вручную только поперечный суппорт.
Для повышения производительности и точности обработки фасонных поверхностей проходным резцом применяют копир (рис. 1.101). Фасонную поверхность рукоятки 2 обрабатывают резцом 1, поперечное перемещение которого осуществляется по копиру 5 пальцем 4 в соответствии с его профилем. Вместе с пальцем 4 в поперечном направлении перемещается тяга 3 и связанный с ней суппорт с резцовой головкой. При этом винт поперечного движения подачи выводится из зацепления с гайкой поперечного суппорта, а движение продольной подачи может осуществляться автоматически.
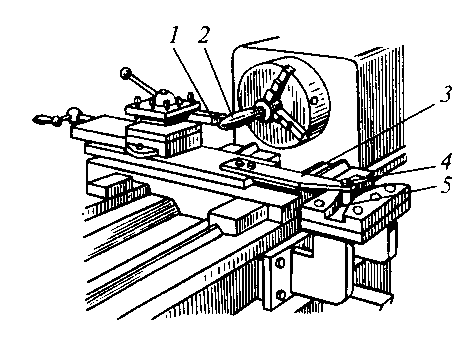
1 - резец; 2 - рукоятка; 3 - тяга; 4 - палец; 5 - копир
Рисунок 1.101 Обработка фасонных поверхностей
по копиру
Обработка фасонными резцами. Для обработки галтелей, резьбы и других фасонных поверхностей применяют фасонные резцы. Профиль режущей кромки фасонных резцов полностью совпадает с профилем обрабатываемой поверхности, поэтому передняя поверхность резца устанавливается точно на линии центров станка. Фасонные резцы затачивают по передней поверхности. Это необходимо учитывать при повторной установке резцов. В горизонтальной плоскости резец должен быть установлен перпендикулярно к линии центров станка; правильность установки проверяют угольником, который одной стороной прикладывают к цилиндрической поверхности детали, а другой - к боковой поверхности резца, при этом между угольником и резцом должен быть равномерный просвет. Применение призматических и круглых фасонных резцов позволяет обрабатывать фасонные поверхности сложного профиля.
Призматические радиальные фасонные резцы устанавливают на поперечном суппорте или в револьверной головке с горизонтальной осью вращения. Они предназначены для работы с поперечным движением подачи. Режущую кромку резца необходимо устанавливать по центру обрабатываемой детали. Задние углы α создают соответствующей установкой резца в державке, что является преимуществом этой конструкции.
Фасонные круглые резцы с винтовыми образующими режущих кромок обеспечивают получение меньшей шероховатости обрабатываемой поверхности по сравнению с круглыми резцами с кольцевыми образующими. Резцы с винтовыми образующими — это высокопроизводительный инструмент, который применяется на станках с револьверными головками.
Подача фасонного резца должна быть равномерной и не превышать 0,05 мм/об при ширине резца 10... 20 мм и 0,03 мм/об при ширине резца более 20 мм. Подача зависит от жесткости детали.
Контроль фасонной поверхности. Фасонную поверхность детали контролируют, как правило, шаблоном. Отклонения от фактического профиля могут быть вызваны следующими причинами: неточностью профиля резца или погрешностью его установки, а также деформацией детали при обработке, вызванными чрезмерно большими подачами.