Повышение эффективности производства специальной автотехники в условиях гибкого производства путем рационализации управления ресурсами
Вид материала | Диссертация |
- Т. П. Заглада Создание системы управления нормированием труда, применение новых методов, 136.62kb.
- Тематика курсовых работ по курсу «Организация производства», 25.9kb.
- Автореферат диссертации на соискание ученой степени, 344.2kb.
- Повышение экономической эффективности производства высокобелкового зерна (на материалах, 371.2kb.
- Литературы Понятие и экономическое, 39.08kb.
- Повышение эффективности производства продукции садоводства в специализированных организациях, 398.96kb.
- Содержание: Введение, 302.8kb.
- Повышение эффективности производства энергопредприятий, 182.13kb.
- Концепция эффективного развития сельскохозяйственного производства и создания цивилизованного, 180.11kb.
- А. Б. Коростелев, А. В. Тарасов, Парецкий, 208.73kb.
ГЛАВА 2.Разработка и основные положения методики управления запасами на гибких и опытных производствах
2.1.Разработка методики управления запасами на гибких и опытных производствах с учетом приоритета заказа
Методические основы управления производственными запасами включают в себя следующие подсистемы управления более низкого уровня, исследуемые, как методики в настоящей главе: методика кластеризации, как способ передачи специалистами накопленного опыта в систему управления производством, и методики планирования запасов (закупок).
Методика рассматривается как совокупность реализующих конкретный метод последовательных действий по определенному алгоритму для достижения поставленных целей, например, методика классификации, или построения планов и др.[3.3].
В этой связи, методика создания системы управления запасами состоит из нескольких последовательных процессов, которые приводится в системе модулей решения задачи управления запасами на гибких и опытных производствах. (См. рис. 9).
Модуль
| ||||||||||||||||||||||||||||||||||||||||||||||||||||||||||||||||||||||||||||||||||||||||||||||||
Рис. 9. Общая схема разработанной методики управления запасами |
Выделение сборочных комплектов. Номенклатура большинства промышленных механосборочных предприятий многочисленна, однако, многие элементы, детали, потребляются, используются в комплексе, и, например, если используется корпус коробки передач то, значит, используются и шестерни, входящие в эту коробку передач, независимо от того, какую в какой производственной или инженерной разработке используется эта коробка передач.
Основная цель выделения сборочных комплектов - это укрупнение объектов управления. Кроме того, выделение сборочных комплектов разгружает модуль MRP, позволяя вести планирование укрупненными модулями. В процессе выделения сборочных комплектов происходит передача опыта, накопленного в предыдущие периоды (в том числе и до внедрения системы управления производством) в систему управления производством.
Под сборочным комплектом подразумеваются не только то, что входит в один комплект сборки, но и вообще все то, что в большинстве случаев после всех операций входит в одно целое.
Сборочные комплекты выделяются технологом на основе его практического опыта, кроме того, их можно сформировать, анализируя потребление запасов, которые потребляются одновременно, например, корпус коробки передач и шестерни коробки передач.
В дальнейшем в управлении сборочные комплекты должны управляться как одним видом запаса, например, при классификации ABC. Благодаря этому, сборочный комплект, состоящий из элементов, которые при классификации попали бы в группу С, сам попадает в группу А или В.
Источником информации при выделении сборочных комплектов являются опыт и знания производственного технолога.
При выделении сборочных комплектов надо учитывать, что некоторые виды сырья потребляются в нескольких разных сборочных комплектах. Поэтому компоненты, включенное в сборочный комплект, не удаляется из общего списка запасов.
Выделяются сборочные комплекты нескольких уровней - узел, компонента, часть:
- узел – радиатор, редуктор, компрессор пневмосистемы и т. п.;
- компонента – коробка передач, двигатель в сборе и т. п.
- часть - самая крупная составляющая, например, кабина грузовика в сборе, шасси, и т. п.
Классификация ABC. Для проведения анализа ABC материальных потоков по объему произведенных в год закупок, необходимо всю номенклатуру приобретаемого сырья и материалов расположить в порядке убывания стоимости их годового потребления. Затем в группу А относят все наименования, в списке начиная с первого, сумма стоимостей, которых составляет 75-80 % от суммарной стоимости всех потребленных за этот период материальных ресурсов. Опыт показывает, что обычно в эту группу попадает 10-20 % всей номенклатуры. К группе В относится примерно треть наименований ресурсов, сумма стоимостей которых составляет 10-15 %. Остальные позиции номенклатуры, (а это оставшаяся половина ресурсов), суммарная стоимость которых составляет лишь 5-10 %, относятся к группе С.
Общий алгоритм проведения анализа ABC приводится в рис. 10.
![]() |
Рис. 10. Порядок проведения анализа ABC |
При построении кривой по оси ОХ откладывают объекты управления в порядке убывания значимости их вклада в конечный результат, выраженные в процентах к общему количеству объектов. По оси OY отмечают вклад каждого объекта в конечный результат, исчисленный нарастающим итогом, также выраженный в процентах.
Ресурсы (материалы) класса А - это немногочисленные, но важнейшие ресурсы, на которые приходится большая часть денежных средств, вложенных в запасы. Размеры запасов по позициям группы А постоянно контролируют, точно определяют издержки, связанные с закупкой, доставкой и хранением, а также размер и момент заказа.
Ресурсы (материалы) класса В занимают срединное положение в формировании запасов предприятия, и по сравнению с группой А требуют к себе меньшего внимания. Здесь осуществляется обычный контроль и сбор информации о запасах, который должен позволить своевременно обнаружить основные изменения в использовании запасов.
Ресурсы (материалы) класса С, составляющие, как правило, большую часть ассортимента, относят к второстепенным. На долю этих ресурсов приходится наименьшая часть всех финансовых средств, вложенных в запасы. Точные оптимизационные расчеты размера и периода заказа с ресурсами данной группы не выполняются. Пополнение запасов регистрируется, но текущий учет уровня запасов не ведется. Проверка наличных запасов проводится лишь периодически, например, один раз в шесть месяцев [3.3, c.115-122].
Классификация XYZ. Сырье и запасы групп А, и В стоят значительно больше, и требуют более подробного анализа и классификации.
Группировка ресурсов при проведении XYZ-анализа осуществляется в порядке возрастания коэффициента вариации объема потребления запаса относительно среднего уровня потребления. При этом к категории X относятся ресурсы, которые характеризуются стабильной величиной потребления, незначительными колебаниями в их расходе и высокой точностью прогноза. Категория Y — это ресурсы, потребность в которых характеризуется известными тенденциями (например, сезонными колебаниями) и средними возможностями их прогнозирования. Наконец, ресурсы, относимые к категории Z, потребляются нерегулярно, точность их прогнозирования невысокая.
Принцип дифференциации ассортимента в процессе анализа XYZ иной — здесь весь ассортимент (ресурсы) делят на три группы в зависимости от степени равномерности спроса и точности прогнозирования.
В группу X включают ресурсы, спрос на которые равномерен, либо подвержен незначительным колебаниям. Объем расходования по ресурсам, включенным в данную группу, хорошо предсказуем.
В группу Y включают ресурсы, которые потребляются в колеблющихся объемах. В эту группу входят ресурсы, использующиеся в одном или нескольких проектах. Эту группу ресурсов прогнозируют на основе построения планов в модуле МRP.
В группу Z включают ресурсы, спрос на которые лишь эпизодически. Прогнозировать объемы потребления ресурсов группы Z сложно, например такими ресурсами могут быть запасные части оборудования, заменяемые в случае внезапной непредсказуемой поломки.
Коэффициент вариации
| ||||
Рис. 11. Кривая анализа XYZ |
Признаком, на основе которого конкретную позицию ассортимента относят к группе X, Y или Z, является коэффициент вариации спроса со стороны производства (v) по этой позиции. Среди относительных показателей вариации - коэффициент вариации является наиболее часто применяемым показателем относительной колеблемости [3.3, с. 616.]
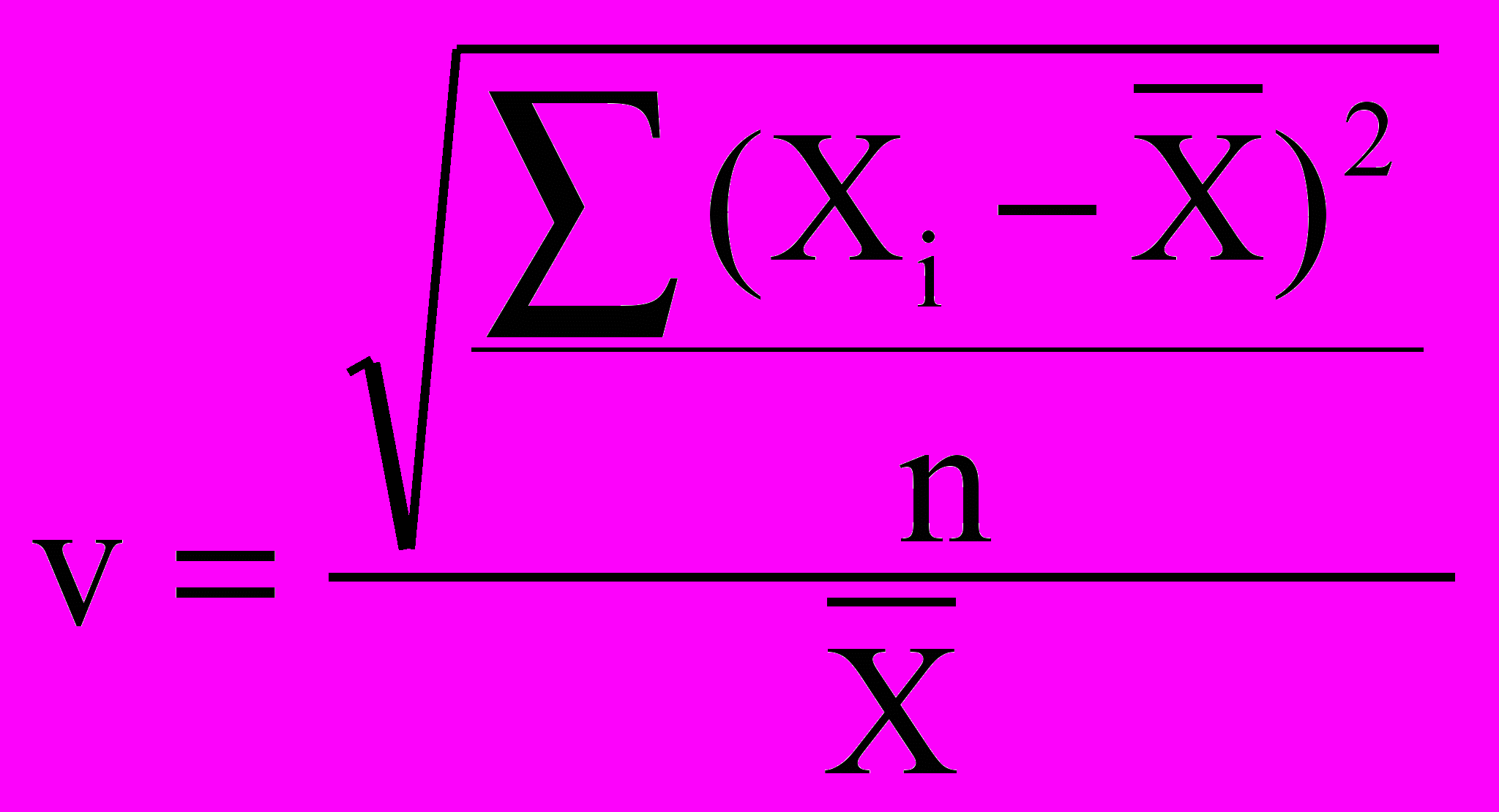
где:
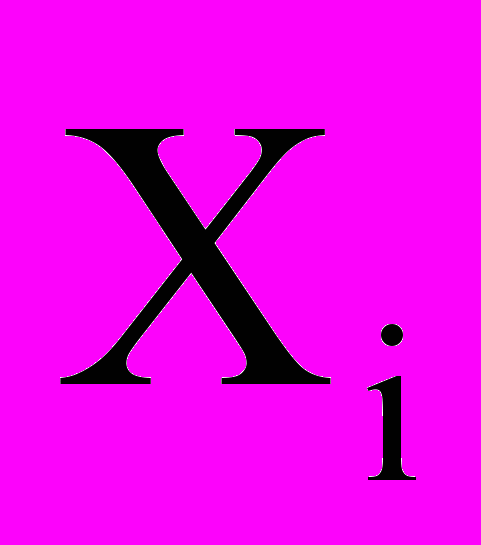
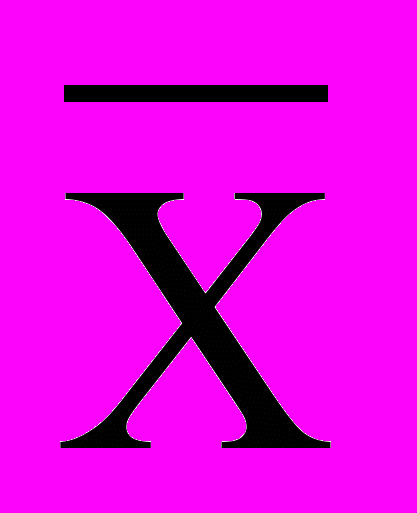
n — величина периода, за который произведена оценка.
![]() |
Рис. 12. Порядок проведения анализа XYZ |
Построение кривой XYZ осуществляется в прямоугольных координатах (рис. 11). По оси абцисс откладывают позиции ассортимента в порядке возрастания коэффициента вариации спроса, выраженные в процентах к общему количеству позиций ассортимента.
Величина коэффициента вариации изменяется в пределах от нуля до бесконечности. Разделение на группы X, Y и Z может быть осуществлено, на основе алгоритма, представленного в рис. 12.
Расчет и построение оптимального плана закупок управление группой X (А, В). Как уже сказано, в группу X включают ресурсы, спрос на которые равномерен, либо подвержен незначительным колебаниям. Объем расходования по ресурсам, включенным в данную группу, хорошо предсказуем. В управлении систематически потребляемыми ресурсами наиболее важная задача - эта задача наиболее оптимальной величины закупки.
В качестве критерия эффективности принятой стратегии управления запасами выступает функция затрат (издержек), представляющая суммарные затраты на хранение и поставку запасаемого продукта (в том числе потери от порчи продукта при хранении и его морального старения, потери прибыли от омертвления капитала и т. п., затраты на штрафы).
Управление запасами состоит в отыскании такой стратегии пополнения и расхода запасами, при котором функция затрат принимает минимальное значение.
Существует несколько различных подходов к управлению запасами. Наиболее эффективной с точки зрения оперативного управления является подход, основанный на контроле минимального запаса, называемый также системой с фиксированным размером запаса, которая проста и является своего рода классической. В этой системе размер заказа является постоянной величиной, и повторный заказ подается при уменьшении наличных запасов до определенного критического уровня – точки заказа.
Эта система основана на выборе размера партии, минимизирующего общие издержки управления запасами. Последние состоят из издержек выполнения заказа и издержек хранения запасов.
Издержки выполнения заказа – это накладные расходы, связанные с реализацией заказа и зависящие от размера заказа. В промышленности эти издержки относят на подготовительно-заключительные операции.
Несомненно, что предприятию необходимо иметь некоторый объем запасов, но также очевидно и то, что ее прибыльность пострадает, если уровень запасов будет слишком низок или слишком высок. Каким же образом можно определить оптимальный уровень запасов? Наиболее часто используемый подход основан на понятии оптимальной партии заказа (Economic Ordering Quantity, EOQ).
Смысл решения всех задач по оптимизации закупок заключается в минимизации суммарных издержек.
Перед разработчиками всех формул стоит вопрос, какие виды издержек включать в модель? Если в формуле Уилсона [3.3, с. 350] (см. формулу (1) глава 1), это только накладные расходы и издержки на хранение, то в формуле П.М.Ферейра (3) - это накладные расходы и издержки на хранение плюс потери от дефицита, а в формуле Матца-Карри-Фрэнка [3.3, c. 160] (4) - это накладные расходы, транспортные затраты и стоимость отвлечения ресурсов. Принцип построения этих формул аналогичен формуле Уилсона. Общая задача - это снизить суммарные накладные расходы, связанные с закупкой и содержанием запасов. Все выведенные таким образом формулы, обладают следующим общим свойством - партия оптимальна тогда, когда стоимость заказа равна издержкам на хранение или транспортным расходам в формуле Матца-Карри-Фрэнка. Это обосновано тем, что минимальная сумма расходов на хранение и приобретение достигается при их равенстве.
Формула Уилсона, не учитывает потери предприятия, связанные с капитализацией средств; потери предприятия, вызванные дефицитом сырья; транспортные расходы.
Формула Ферейра не учитывает потери предприятия, связанные с капитализацией средств; транспортные расходы.
Формула Матца-Карри-Фрэнка не учитывает потери предприятия, вызванные дефицитом сырья; складские расходы.
Ни одна из выше перечисленных формул (1), (3), (4) не учитывает издержки, вызываемые остановкой и пуском производства. В формуле (3) учитываются расходы, связанные с дефицитом сырья.
Предлагается формула нахождения оптимальной величины заказа EOQ, учитывающая все вышеперечисленные потери и издержки. Она имеет вид:

где: B - потеря от дефицита единицы материала в единицу времени (руб);
C - годовые затраты по хранению, выраженные в процентах от стоимости средних запасов;
F - постоянные затраты по размещению и выполнению одного заказа (руб);
K - издержки, связанные с остановкой и пуском производства (руб);
P - стоимость единицы запаса (руб);
R - предполагаемая ставка банковского процента (ставка оценки вложения);
S - общая потребность в сырье на период (в единицах);
T - транспортные расходы на единицу материала за год (в руб).
Для вывода формулы (10) принимаются следующие допущения:
- скорость расхода запасов всегда неизменна в единицу времени;
- объем партии пополнения всегда постоянный;
- время разгрузки и время от принятия решения до прихода заказа будем считать равным нулю.
Плата за ресурсы, складские расходы и транспортные расходы прямо пропорциональны и зависят от количества приобретаемого и перевозимого сырья и задаются формулой:
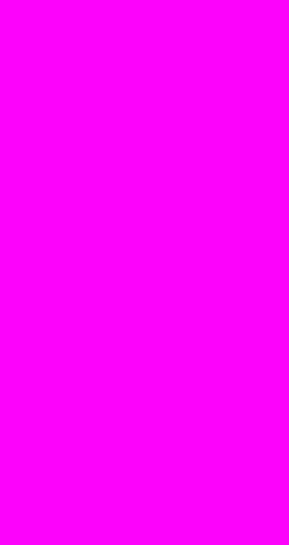
где:
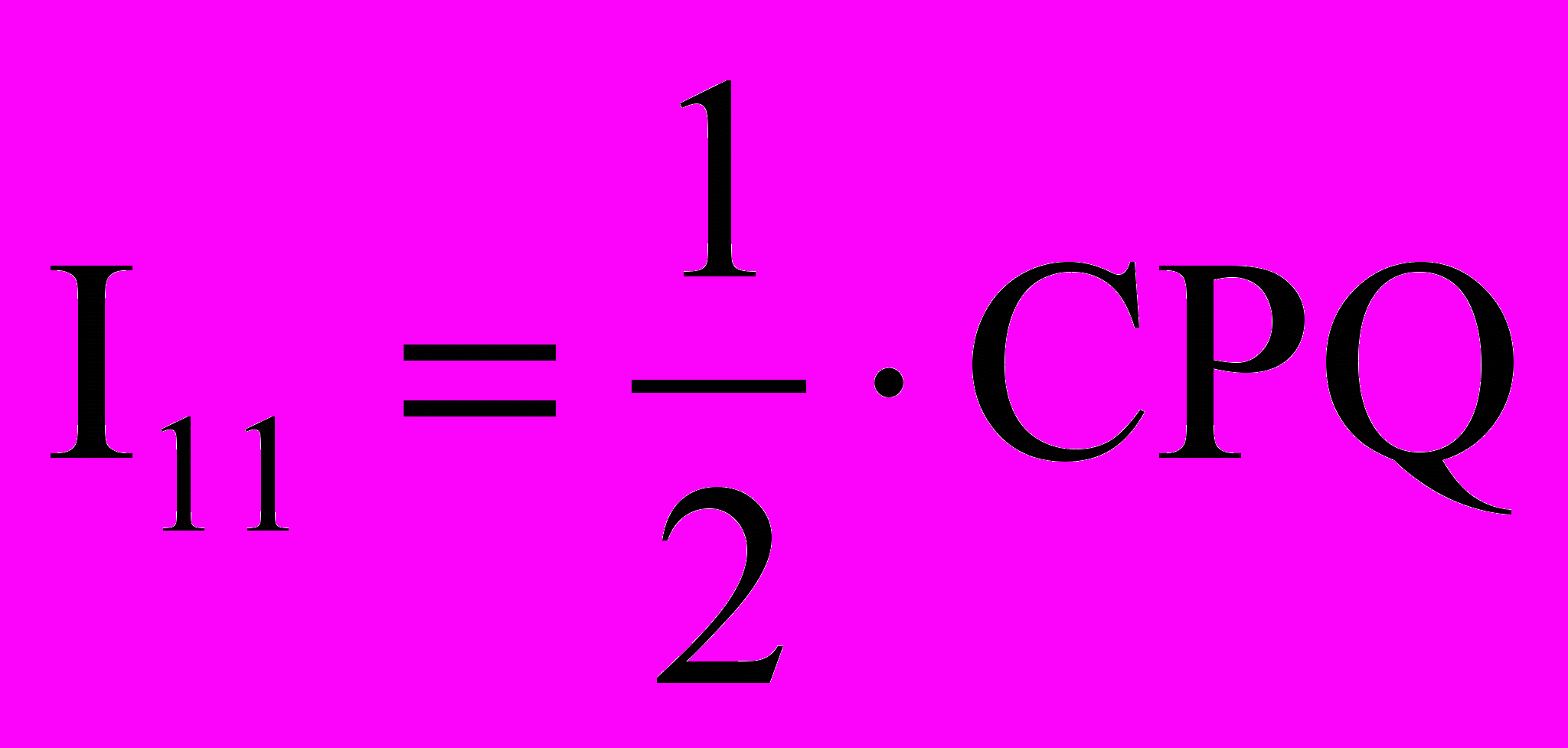
издержки, связанные с обслуживанием склада и растущие от увеличения величины заказа.
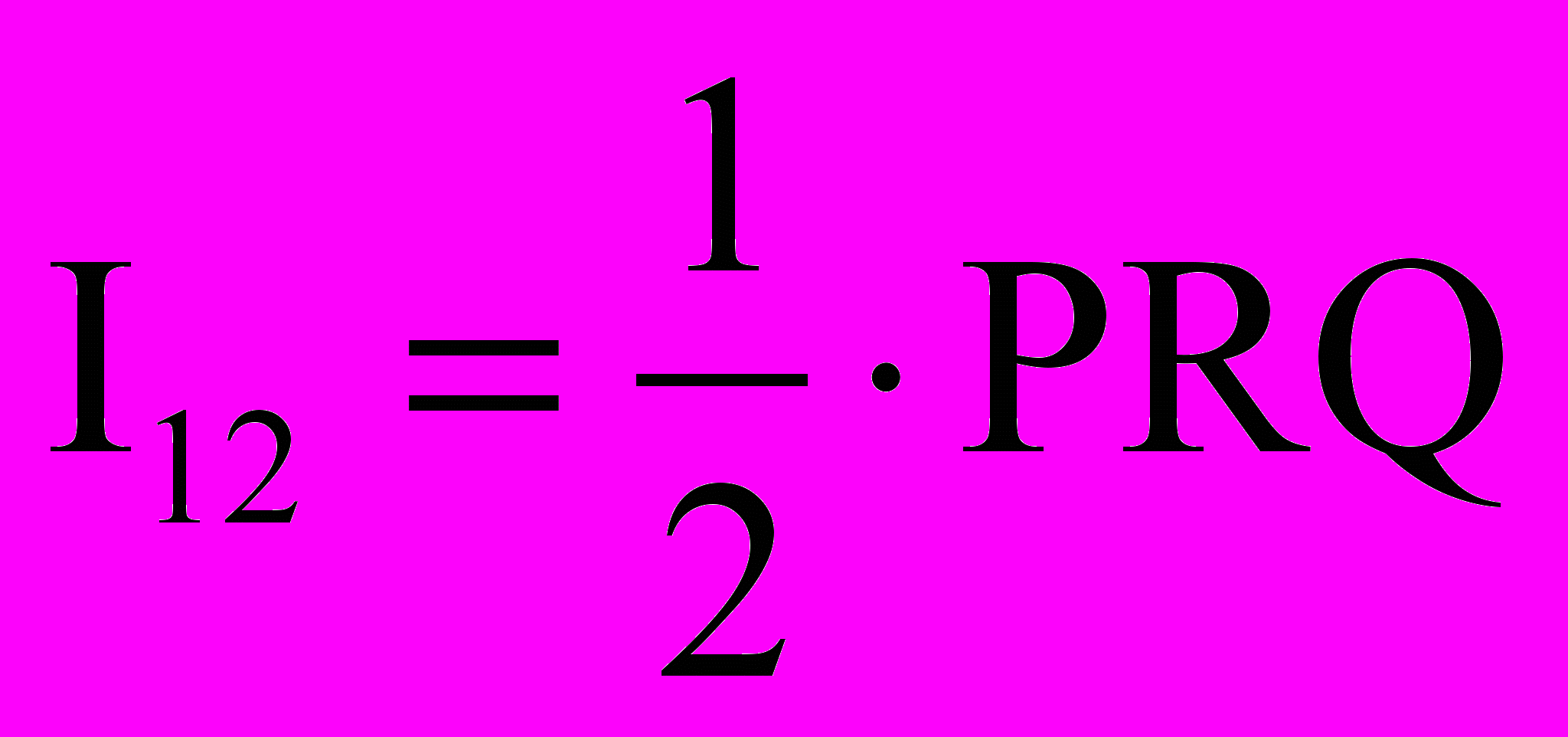
затраты на отвлечение ресурсов, (R – доход, который можно было бы получить, инвестировав денежные средства, в процентах). Затраты на отвлечение ресурсов предполагают по среднему уровню запаса, поскольку при списании материалов ресурсы возвращаются с выручкой и плата за их использование уменьшается.
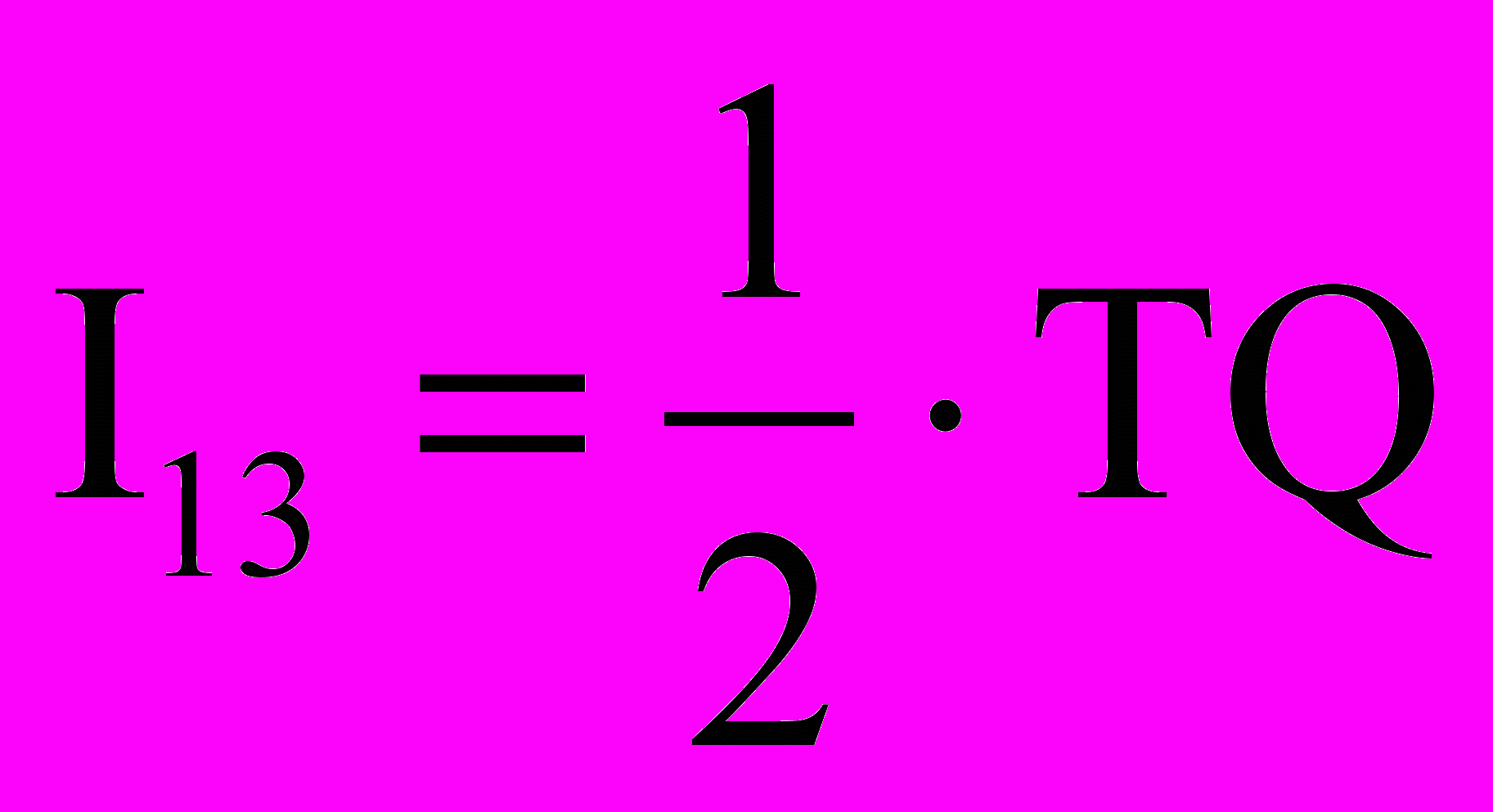
издержки, связанные с транспортировкой запасов (T - транспортные расходы на единицу материала за год).
Издержки, связанные с выполнением заказа, а также издержки, связанные с остановками и пуском (в случае работы с дефицитом) производства, обратно зависят от величины партии пополнения и с ростом партии в расчете на единицу запаса, уменьшаются и задаются формулой:
I2 = I21+ I22 + I23, (15)
где
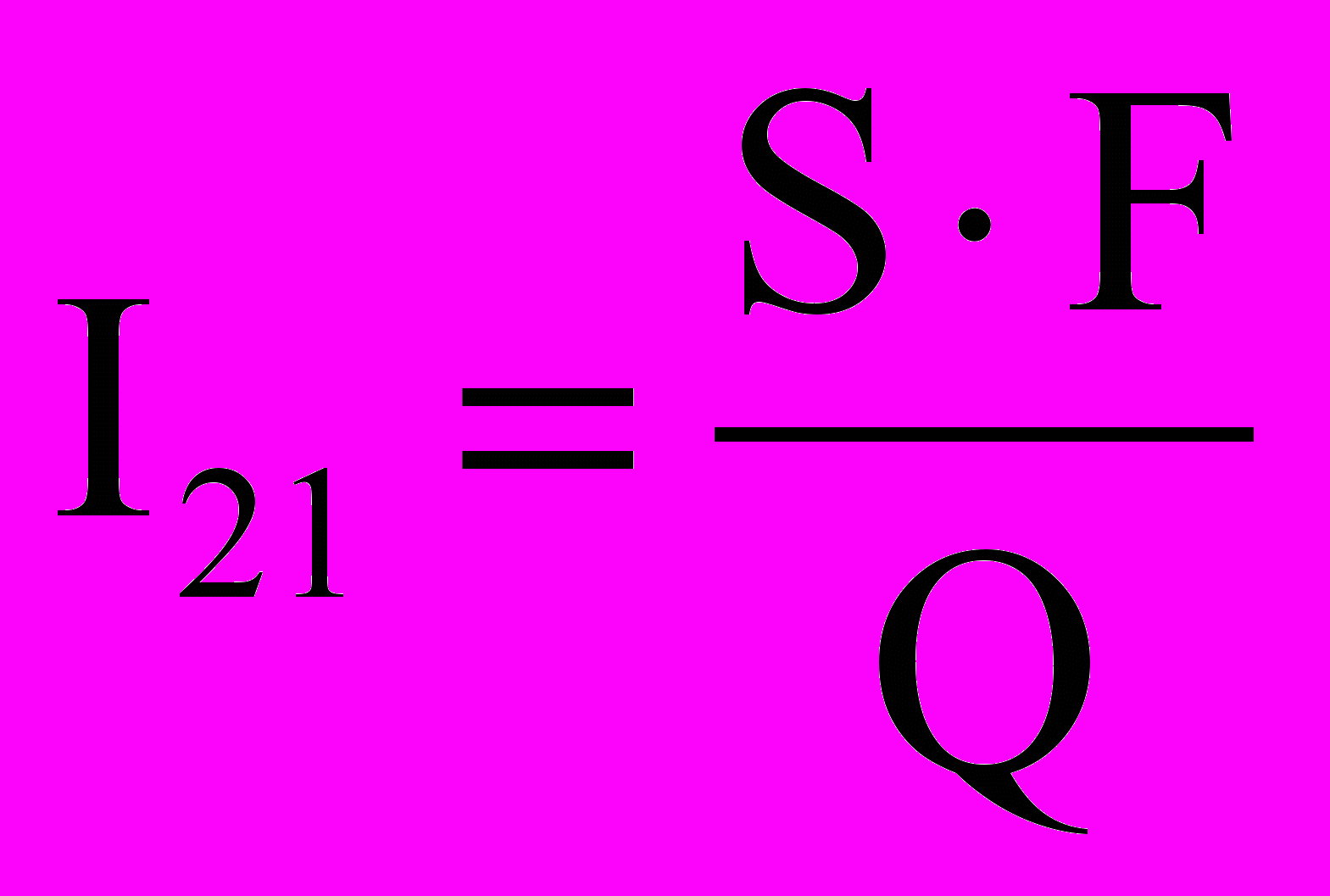
издержки, вызываемые размещением заказов, растут с увеличением количества заказов
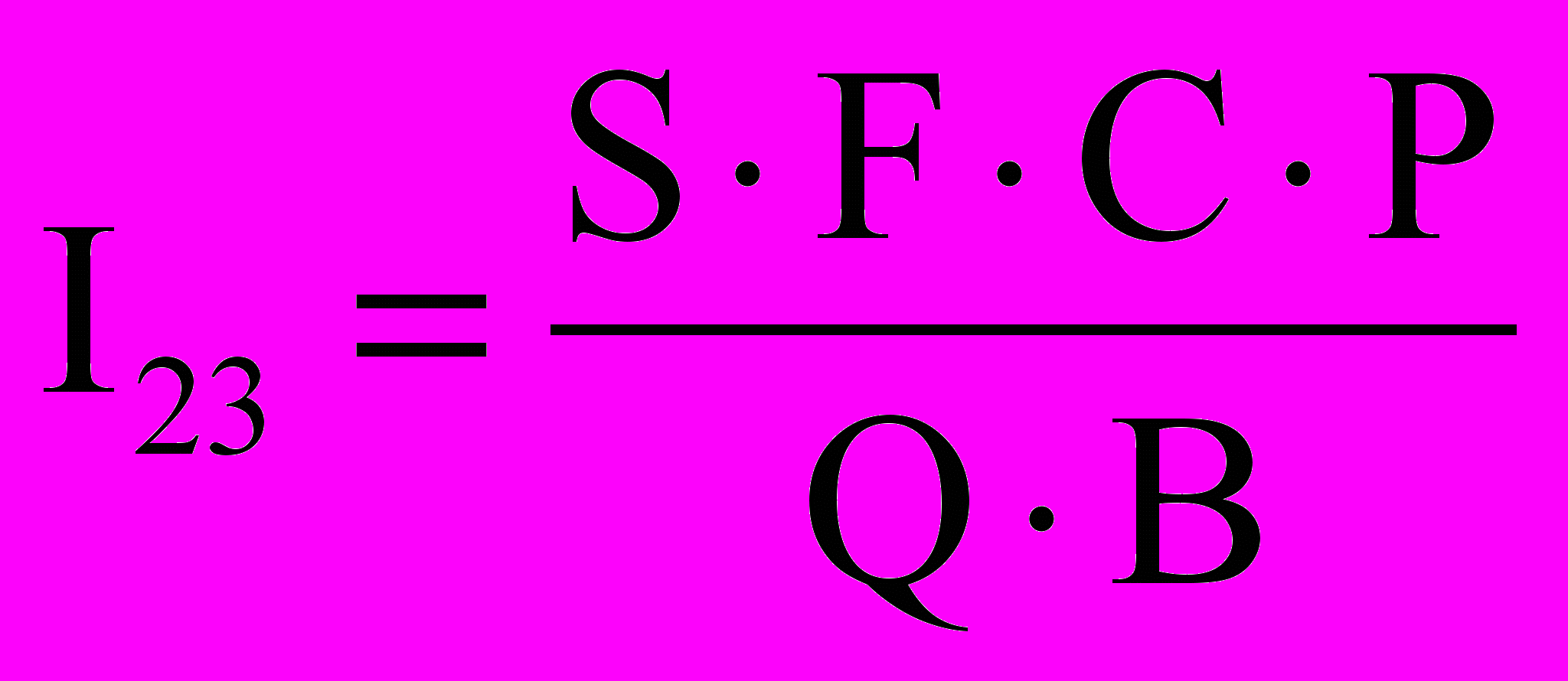
издержки, вызываемые систематическим дефицитом, в случае если используется модель управления запасами с дефицитом (остановками производства), растут с увеличением величины заказа (B - потеря от дефицита единицы материала в единицу времени).
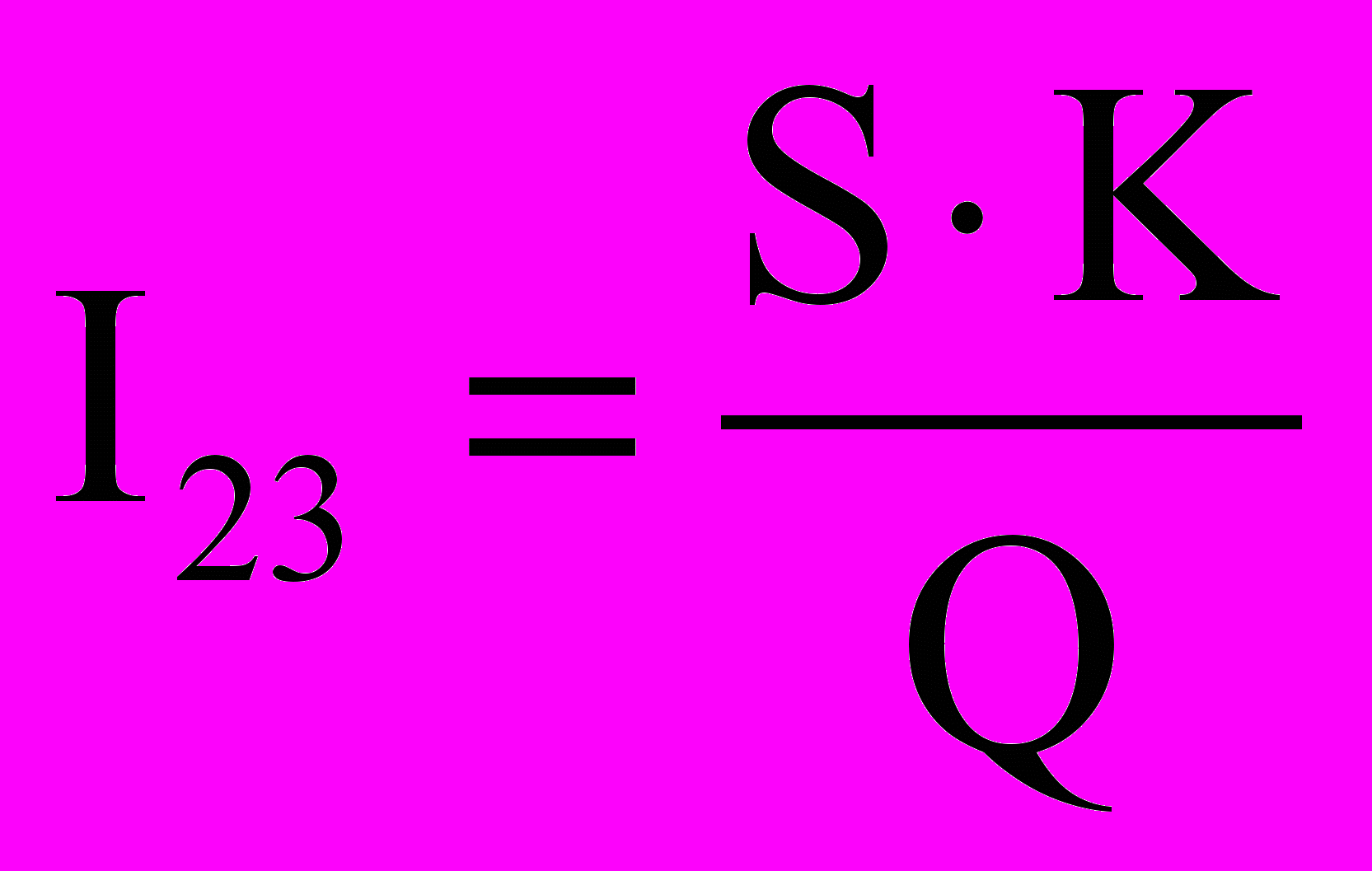
издержки, вызываемые остановками и последующим пуском производства, в случае, если используется модель управления запасами с дефицитом (остановками производства), растут с увеличением количества заказов (K – издержки, связанные с остановкой и пуском производства).
Таким образом, суммарные издержки на приобретение запасов складываются из платы за отвлечение ресурсов, транспортных расходов, складских расходов, расходов на пуск и остановку производства и накладных расходов, связанных с осуществлением заказа. (TIC, Total Inventory Costs - общие затраты по поддержанию запасов). Точка, в которой величина TIC принимает минимальное значение, определяет оптимальный размер партии EOQ.
TIC = I1 + I2, (19)
или:

Для определения EOQ берем производную по Q и приравниваем полученное выражение к нулю. Математический смысл производной заключается в нахождении точки нулевого наклона касательной к кривой минимума совокупной функции издержек TIC.

откуда получаем формулу (10).
Легко показать, что из формулы (10).можно получить формулы (1), (3), (4):
- если принять К = 0, R = 0, Т = 0, и В стремится к бесконечности, то получаем формулу Уилсона (1);
- если принять К = 0, T = 0, R = 0, то получаем формулу П.М.Ферейра (3);
- если принять К = 0, С = 0 и В стремится к бесконечности, то получаем формулу Матца-Карри-Фрэнка (4).
Кроме указанного подхода широко в практике управления распространен и другой подход.
Можно рассматривать вложения в запасы, так же как и любое другое инвестиционное решение, принимаемое на предприятии. В этом случае становятся важными критерии выбора вложений капитала.
Закупка сырья – это такое же инвестиционное решение, как и закупка оборудования или ценных бумаг.
Задачу оптимальной величины закупки сырья решает модель оптимальной партии заказа (Economic Ordering Quantity, EOQ) [2, с.349-358]. Однако, рассматривая возможный сценарии закупок на некоторый промежуток времени, можно установить, что формула EOQ является не столь оптимальной, т. е. ее не следует рассматривать как единственную.
Рассматривая сценарий закупки сырья как инвестиционное решение, можно применить к нему критерии эффективности. Однако, надо учесть, что это инвестиционное решение не связано с получением дохода, а лишь с уменьшением совокупных издержек. Соответственно, такие критерии эффективности, как срок окупаемости, учетная доходность (ARR), внутренняя доходность (IRR), и индекс рентабельности (PI) не применимы [[3.3], с.214-220]. Основным оценочным критерием выбора варианта является чистая текущая стоимость (Net Present Value, NPV), так как остальные критерии – производные от нее [3.3, с. 229].
Алгоритм расчета NPV таков:
Рассчитывается приведенная, или текущая, стоимость каждого элемента денежного потока, дисконтированная по цене капитала данного проекта.
- Значения DCF суммируются, тем самым находится NPV проекта.
NPV может быть определен следующим образом:
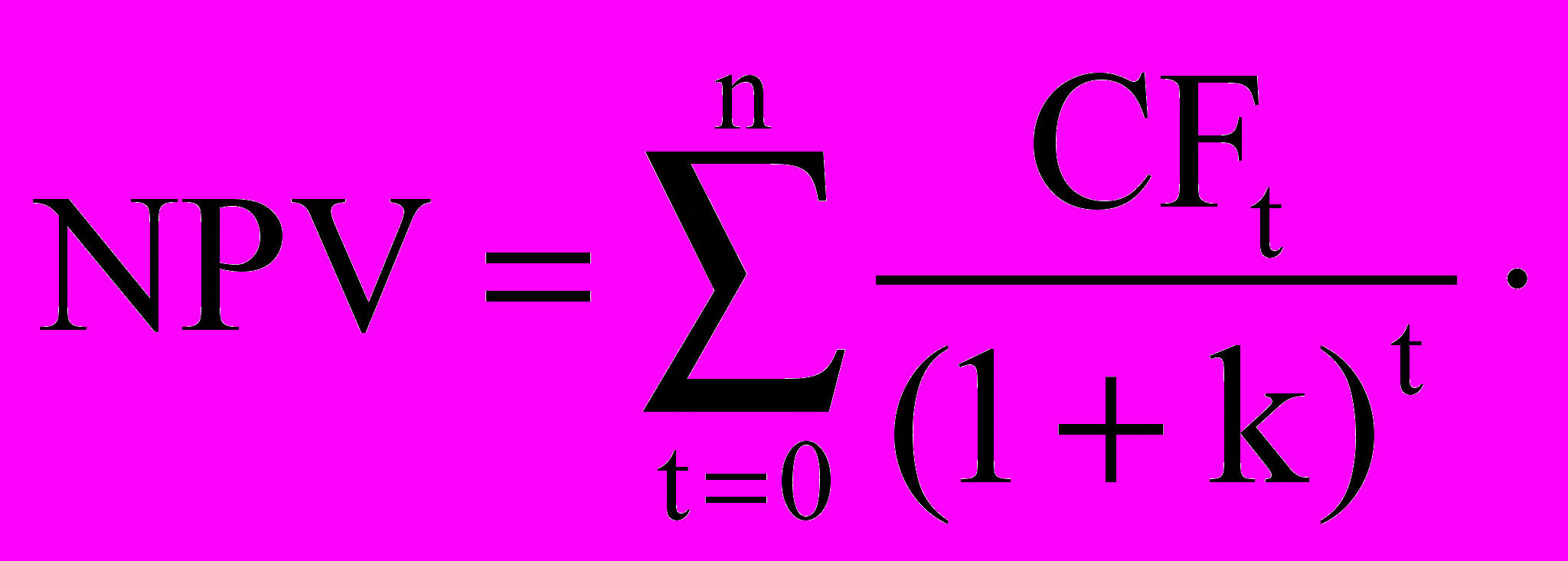
Здесь CFt — ожидаемая разность между притоком и оттоком денежных средств за период t;
k — цена капитала проекта в процентах.
Отток денежных средств (расходы по проекту, такие как, затраты на приобретение оборудования или строительство зданий) трактуется как отрицательный элемент денежного потока. Заметим, что формула (17) не привязана к точному временному интервалу, так как приток и отток могут происходить в любой период, принятый за основу, — поквартально, помесячно, еженедельно или даже ежедневно; в этом случае суммирование идет уже не по годам, а по кварталам, месяцам, неделям или дням соответственно.
Логика критерия NPV достаточно очевидна. Нулевой NPV означает, что генерируемого проектом денежного потока вполне достаточно для возмещения вложенного в проект капитала и для обеспечения требуемой отдачи на этот капитал. Если NPV> 0, тогда проект генерирует прибыль, и после расчетов с кредиторами по фиксированной ставке оставшаяся прибыль накапливается исключительно для акционеров фирмы.
В применении к запасам, формула дисконтированной стоимости запаса или дисконтированных издержек запаса (ДИЗ) имеет вид:
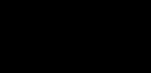
где

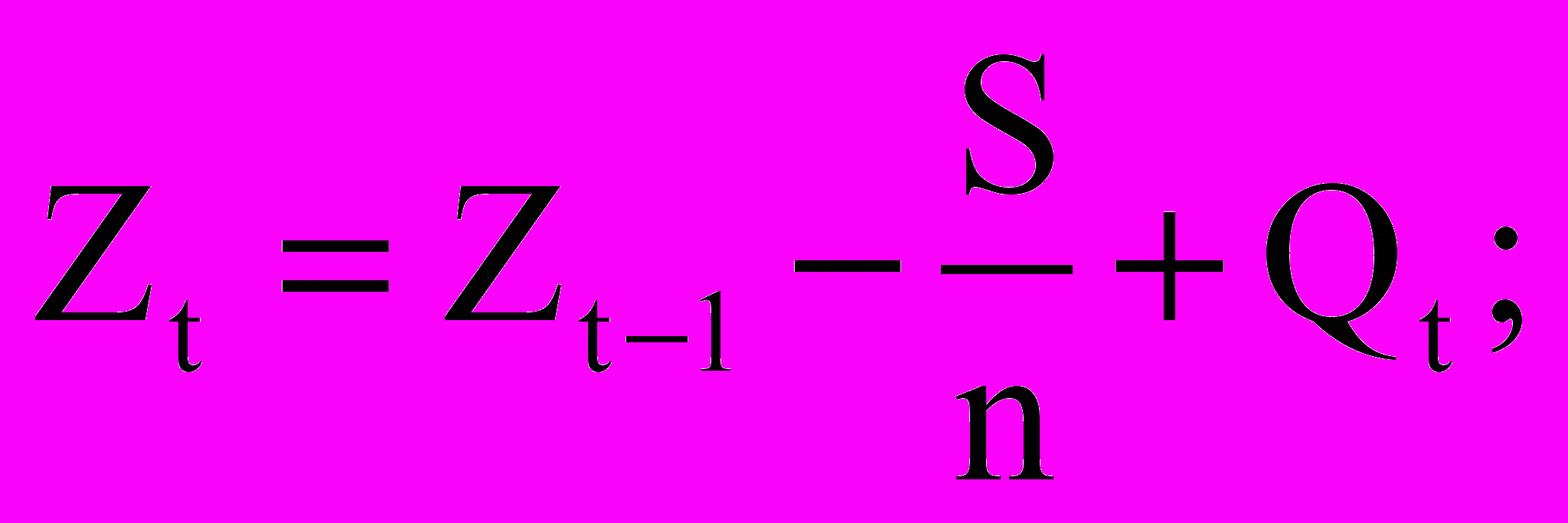
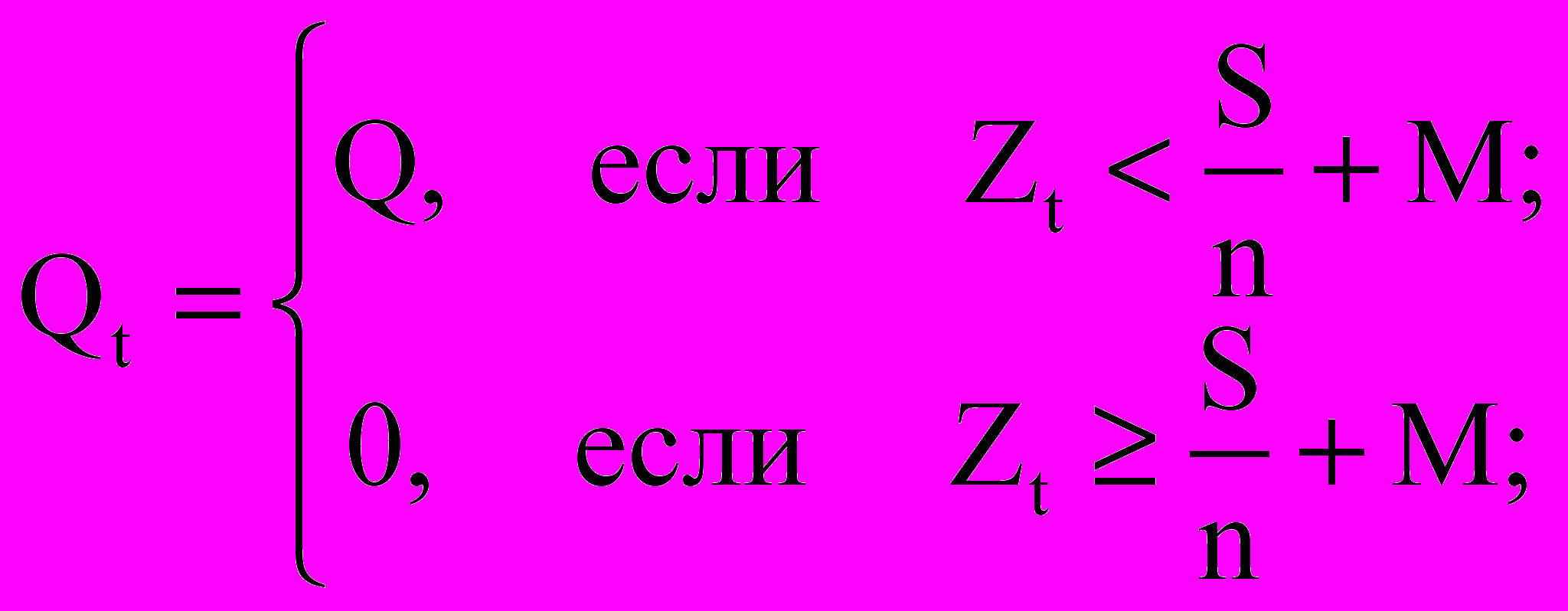
C - годовые затраты по хранению, выраженные в процентах от стоимости средних запасов;
F - постоянные затраты по размещению и выполнению одного заказа (руб);
M - страховой запас (в единицах);
n - общее количество периодов в рассматриваемом сценарии;
P - стоимость единицы запаса (руб);
Q - величина заказа (в единицах);
Qt - величина заказа в текущем периоде (в единицах);
R - предполагаемая ставка банковского процента на весь период сценария (ставка оценки вложения);
R/n - предполагаемая ставка банковского процента на один период;
S - общая потребность в сырье на весь сценарий (в единицах);
S/n - потребность в сырье на период (в единицах);
T - транспортные расходы на единицу материала за один привоз (руб);
Z0 - запас в начале сценария (в единицах);
Zt - запас в текущем периоде (в единицах).
Пример, иллюстрирующий критерий эффективности ДИЗ. Рассмотрим пример со следующими параметрами:
C =0,75 | n =12 | P =1 руб. | S/n =8 333 |
S =100 000 | Z0 =10 000 | F =5 000 руб. | M =8 334 |
R =0,35 | T =0, 10 руб. | R/n =0,0292. | |
Определим значение ДИЗ при различных величинах заказа Q и сравним их.
Оптимальная партия заказа EOQ, вычисляемая по формуле Уилсона [3.3, с. 350] (1), имеет значение 36515. Величина ДИЗ при этом равна 134 763.
Формула Матца-Карри-Фрэнка [3.3, c. 160], (4) дает значение Q = 18 508. Величина ДИЗ при этом значении Q равна 126385.
Нами предложенная формула (10) обобщает формулу Уилсона и формулу Матца-Карри-Фрэнка и дает значение Q = 28868, а величина ДИЗ при этом равна 131975.
Посредством перебора различных значений Q при данных значениях параметров, в формуле (23) (параметры приведены в примере), находим минимальное значение ДИЗ 123 659 при величине Q = 24555.
Далее, определим значение ДИЗ при различных значениях величины заказа Q. Для сравнения возьмем значения Q равных 100 000: потребление сырья за весь сценарий; Q = 50 000: половина потребления сырья за весь сценарий; значение Q = 36 515 получено по формуле Уилсона (1); значение Q = 28 868 получено нами по формуле (10); значение Q = 24 555 получено при минимальном значении ДИЗ, значение Q = 18 508 получено по формуле Матца-Карри-Фрэнка (4) ; Q = 16 667 - двойной объем потребления сырья за один период; Q = 8 334 – потребление сырья за один период.
Полученные значения ДИЗ приведены в таблицах табл. 4- 13.
Таблица 4
Значение Q = 100 000
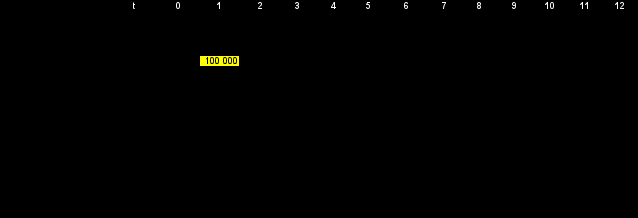
Таблица 5
Значение Q = 50 000
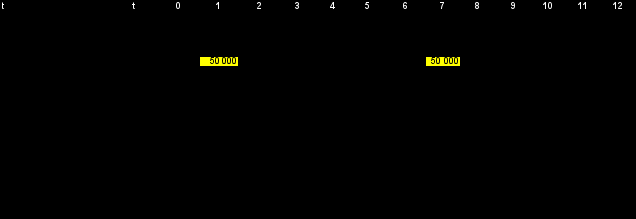
Таблица 6
Значение Q = 100 000
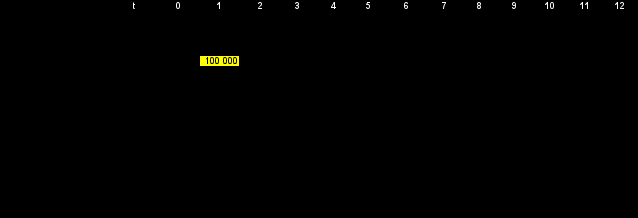
Таблица 7
Значение Q = 50 000
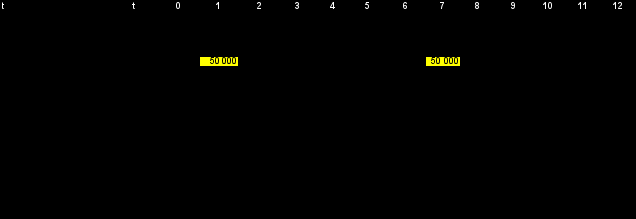
Таблица 8
Значение Q = 36 515
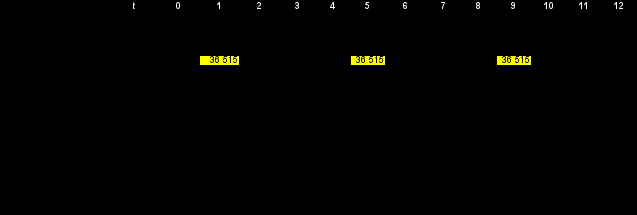
Таблица 9
Значение Q = 28 868.
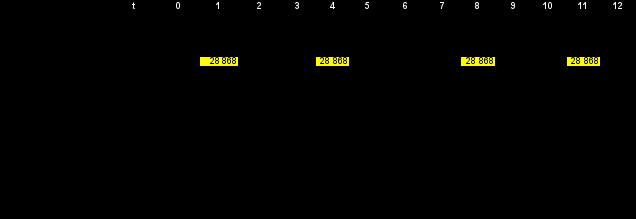
Таблица 10
Значение Q = 24 555
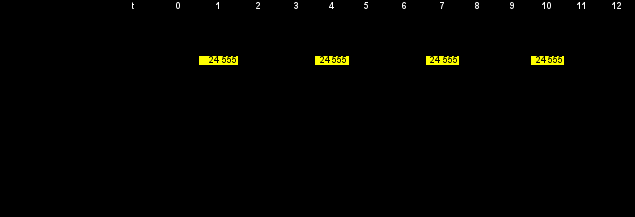
Таблица 11
Значение Q = 18 508
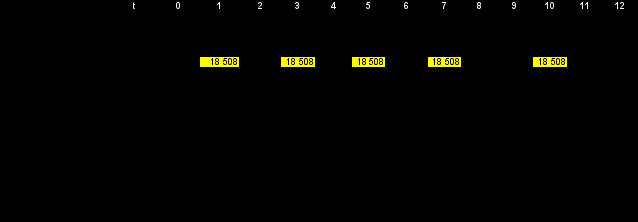
Таблица 12
Значение Q = 16 667
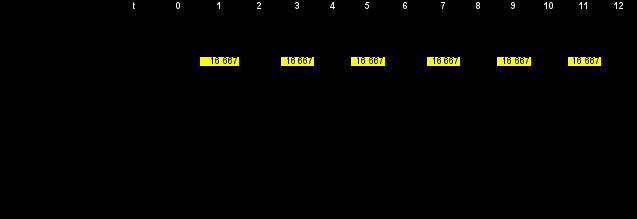
Таблица 13
Значение Q = 8 334
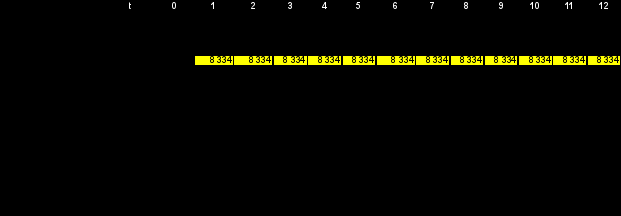
Из рассмотренных табл. 6 - 13 вытекает, что наименьшее значение ДИЗ по хранению и использованию производственных запасов достигается при значении величины заказа Q = 24 555, а не при значений заказа, полученных по формулам (1), (4) или (10).
![]() |
Рис. 13. График сравнения эффективности различных формул EOQ |
В последнем столбце в строке ДИЗ приведена корректировка величины ДИЗ на величину дисконтированного остатка запаса на конец сценария (строка Zt, 12 столбец), так как было принято предположение, что остаток запаса будет использоваться в дальнейшем в 13 периоде, и расходы, понесенные на этот запас не должны влиять на ДИЗ предыдущих периодов.
Данные таблиц можно проиллюстрировать в виде графика рис. 13.
Из графика видно, что кривая зависимости ДИЗ от величины заказа Q, имеет, по крайней мере, два минимума, а именно при значении Q = 24 555 и при значении Q = 50 000.
При величине заказа равной 100 000 производится одна закупка за весь сценарий, соответственно постоянные затраты по размещению и выполнению одного заказа (F) составляют 5 000, однако, это одна закупка производится в начале, и меньше всего дисконтируется. Складские и процентные расходы также значительны и составляют 61 417.
При величине заказа равной 50 000 производится две закупки за весь сценарий, соответственно постоянные затраты по размещению и выполнению одного заказа (F) будут больше, чем в предыдущем случае, однако, вторая закупка, благодаря дисконтированию, дешевле первой закупки на 10 257. Величина последующих складских и процентных затрат значительно меньше, чем в предыдущем случае и составляют 33 917. Все это приводит к уменьшению совокупных затрат.
При величине заказа равной 8 334 производится 12 закупок, расходы на закупки самые большие 70 001 (без дисконтирования). Расходы складские и процентные в этом случае наименьшие и составляют 11 005.
Самый оптимальный случай, как уже говорилось, получен подбором значения Q = 24 555, дает значение ДИЗ = 123 654.
Рассматривая сценарий закупки сырья как инвестиционное решение, применяя в качестве критерия эффективности ДИЗ, получен сценарий пополнения склада (табл. 10), отличающийся от других сценариев меньшей суммой дисконтированных издержек, чем другие варианты. В других сценариях взята за основу величина закупки, полученную по формуле Уилсона (1), (36 515 см. табл. 8); полученную нами по формуле (10), (табл. 9); полученную по формуле Матца-Карри-Фрэнка (4), (табл. 11). Все эти варианты «оптимальных» формул дают большее значение чистой совокупной текущей стоимости запасов.
Итоговым документом этого этапа является список заказов сырья с рассчитанными оптимальными датами закупки и величине закупки.
Классификация заказов на компоненты по приоритету (Управление группой Y (А, В)). Рассматривая опытное производство как процесс реализации множества параллельных проектов, можно проанализировать, что именно, может быть, наиболее важным для реализации каждого проекта в отдельности. Как уже сказано в описании производства, наиболее узким местом на опытном производстве являются не производственные мощности и наличие специалистов, а именно наличие нужных материалов или нужного сырья в определенное время. Является ли наличие (отсутствие) всех ресурсов одинаково важным для реализации проекта? Разумеется, нет. Существуют ресурсы, которые потребляются в моменты, которые можно немного задержать, что не приведет к задержке всего проекта. Эти ресурсы потребляются не на критическом пути. Соответственно, есть и ресурсы, которые потребляются в моменты, когда отсутствие этого ресурса вызовет задержку всего проекта. Такие ресурсы потребляются проектом на критическом пути – «компоненты критического пути» (СКП).
Выявление сырья критического пути возлагается на проектные группы (понятие критического пути см. [3.3]). На этой стадии определяется компоненты, необходимые каждой проектной группе. Проектные группы предоставляют списки заказов на компоненты с примерными датами, когда это сырье будет использовано на производстве. На основании классификации проектов производится классификация заказов. Кроме того, проектные группы присваивают приоритет СКП.
Заказы на компоненты (материалы) группы СКП — это немногочисленные, но важнейшие ресурсы. Отсутствие сырья в нужный момент времени этой категории немедленно скажется на сроках выполнения проекта, который использует эти компоненты.
Заказы на компоненты (материалы) группы α, β, γ принадлежат проектам, имеющим меньший проектный приоритет, в случае возникновения спроса на один и тот же ресурс (сырье со склада) его получит проект с большим приоритетом.
Классификация сырья по приоритету αβγ (альфа-гамма анализ). Имея классификацию заказов на компоненты по приоритету несложно произвести классификацию сырья по приоритету.
Анализ заказов сырья по приоритетам производится по тому же принципу, что и анализ АВС, только по другому основанию – суммарным приоритетам проектов, использующих это сырье. Этот анализ позволяет в дальнейшем учитывать приоритеты того или иного сырья в процессе управления.
Для классификации сырья по приоритету нужно учитывать, что на один вид сырья может быть несколько проектов потребителей, с разным приоритетом. В этом случае сырье получает приоритет самого приоритетного потребителя.
Для проведения классификация сырья по приоритету αβγ необходимо всю номенклатуру приобретаемого сырья и материалов расположить в порядке убывания приоритета. Затем в группу α относят все наименования, в списке начиная с первого, с самым высоким приоритетом общим числом не более 5 % от общего числа, к группе β относится треть заказов ресурсов. Остальные позиции номенклатуры (а это более половины ресурсов), относятся к группе γ.
Общий алгоритм проведения анализа αβγ приводится по рис. рис. 14.
![]() |
Рис. 14. Порядок проведения анализа αβγ |
Ресурсы (материалы) группы α — это немногочисленные, но важнейшие ресурсы, на которые приходится большая ответственности за завершение проектов вовремя. Величины запасов по этим ресурсам необходимо контролировать постоянно, заказы на эти ресурсы должны выполняться с наибольшей скоростью, а страховые запасы должны быть достаточными, чтобы покрыть существенное увеличение спроса. Не многочисленность этой группы запасов, и большая степень ответственности, возложенная на них, требуют установление персональной ответственности должностного лица по этой группе. Ресурсы данной группы должны пересматриваться и переучитываться каждый период планирования.
Ресурсы (материалы) группы β занимают срединное положение в формировании задержек запасов предприятия, и по сравнению с группой α требуют к себе меньшего внимания. Величины запасов по этим ресурсам контролируются в соответствии с классификацией АВС, заказы на эти ресурсы должны выполнятся с обычной скоростью, а страховые запасы должны быть умеренными.
Ресурсы (материалы) группы γ, составляют большую часть ассортимента, их относят к второстепенным. На долю этих ресурсов приходится наименьшая часть всех задержек производства. Величины запасов по этим ресурсам контролируются в соответствии с классификацией АВС, заказы на эти ресурсы должны выполняться с обычной скоростью, а страховые запасы должны быть немногочисленными.