Повышение эффективности производства специальной автотехники в условиях гибкого производства путем рационализации управления ресурсами
Вид материала | Диссертация |
- Т. П. Заглада Создание системы управления нормированием труда, применение новых методов, 136.62kb.
- Тематика курсовых работ по курсу «Организация производства», 25.9kb.
- Автореферат диссертации на соискание ученой степени, 344.2kb.
- Повышение экономической эффективности производства высокобелкового зерна (на материалах, 371.2kb.
- Литературы Понятие и экономическое, 39.08kb.
- Повышение эффективности производства продукции садоводства в специализированных организациях, 398.96kb.
- Содержание: Введение, 302.8kb.
- Повышение эффективности производства энергопредприятий, 182.13kb.
- Концепция эффективного развития сельскохозяйственного производства и создания цивилизованного, 180.11kb.
- А. Б. Коростелев, А. В. Тарасов, Парецкий, 208.73kb.
1.2.Подходы к управлению запасами
Существует несколько различных подходов к управлению запасами. Наиболее эффективной с точки зрения оперативного управления является, на наш взгляд, подход, основанный на контроле минимального запаса, называемый также системой с фиксированным размером запаса, который прост и является своего рода классическим. В этой системе размер заказа является постоянной величиной, и повторный заказ подается при уменьшении наличных запасов до определенного критического уровня – точки заказа.
Как часто надо закупать тот или иной вид сырья? (какой размер закупки самый оптимальный?)
Для успешного управления сырьевыми запасами и обеспечения гарантированного запаса необходимо определить оптимальную периодичность заказа и его величину. В табл. 2 показаны преимущества и недостатки редкого и частого вида заказа.
Одной из основных проблем управления снабжением является определение оптимального объема поставки. Традиционная модель, модель EOQ (Economic Ordering Quantity, модель Оптимальной Партии Заказа), разработанная еще в начале ХХ века, исходит из следующей проблемной ситуации [3.3]. Политика закупок определяется для каждого вида материалов. При этом известны поставщики, условия поставки и годовая потребность. Требуется определить, какое количество материалов и в какой момент времени следует приобрести, а также найти объем материала, который необходимо будет приобретать через равные промежутки времени. Функции оптимизации - годовые затраты на поставку, хранение и неполученный процент от замораживания оборотных средств - должны быть минимальными.
Применение этой базовой модели требует соблюдения ряда начальных условий, что не ограничивает области ее использования. В некоторых случаях достаточно дополнить или видоизменить эту модель [3.3, с.29].
Таблица 2
Преимущества и недостатки редкого и частого заказа
Редкий заказ | Или | Частый заказ |
Преимущества - меньше заказов, меньше затрат труда, можно воспользоваться скидками | ОПТИМУМ | Преимущества - требуется меньше оборотных средств, нужен склад меньшего размера |
Недостаток - выводится из оборота денежные средства | Недостаток - затрачивается много труда на оформление заказов и проведение платежей | |
◣◣◣◣◣◣◣◣◣◣ | ◣◣◣◣◣◣◣◣◣◣◣◣◣◣◣◣◣ |
Эта система основана на выборе размера партии, минимизирующего общие издержки управления запасами. Последние состоят из издержек выполнения заказа и издержек хранения запасов.
Издержки выполнения заказа – это накладные расходы, связанные с реализацией заказа и зависящие от размера заказа. В промышленности эти издержки относят на подготовительно - заключительные операции [3.3].
![]() |
Рис. 4. Зависимость среднего остатка запасов от размера партии пополнения |
Рассмотрим два графика: (рис. 4). На первом графике размер партии поставки равен 40 единиц, и этого запаса хватает на двадцать дней, во втором случае размер партии поставки равен 20 единиц, и этого запаса хватает на десять дней. Какой из этих вариантов является лучшим? Ответ на этот вопрос дает модель оптимальной партии заказа.
Модель оптимальной партии заказа. Очевидно, что предприятию необходимо иметь некоторый объем запасов, но также очевидно и то, что ее прибыльность пострадает, если уровень запасов будет слишком низок или слишком высок. Каким же образом можно определить оптимальный уровень запасов? Наиболее часто используемый подход основан на понятии оптимальной партии заказа модель EOQ.
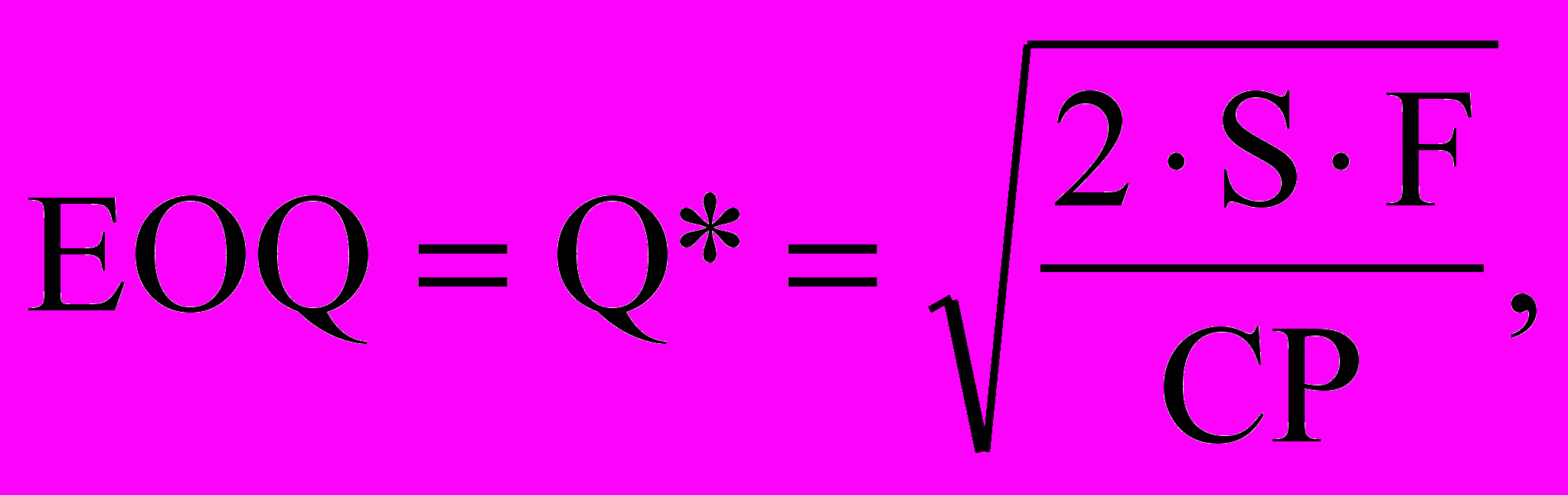
где: F — постоянные затраты по размещению и выполнению одного заказа;
S — годовая потребность в запасах;
С —годовые затраты по хранению, выраженные в процентах от стоимости средних запасов;
Р — цена приобретения единицы запасов.
Формула (1) является моделью EOQ. Данная формула впервые была предложена Ф.У.Харрисом в 1913 г., но широкое распространение как модель экономически обоснованного размера заказа EOQ получила в связи с работами в 1934 г. английского экономиста Р.Х.Вильсона.
Данная модель основана на следующих предположениях:
- годовая потребность в запасах (годовой объем реализации) может быть точно спрогнозирована;
- объемы реализации равномерно распределены в течение года;
- не происходит задержек в получении заказов.
![]() |
Рис. 5. Определение оптимальной партии заказа |
Рис. 5 иллюстрирует основные предпосылки, на которых построена модель EOQ, а именно: часть затрат увеличивается с ростом объема запасов, в то время как другая часть снижается; оптимальным является размер заказа (и связанный с ним средний объем запасов), который минимизирует совокупные затраты. Прежде всего, как было отмечено ранее, средний объем запасов зависит от частоты размещения заказов и размера каждого из них: если запасы будут обновляться ежедневно, средний объем запасов будет гораздо ниже, чем в случае размещения заказа один раз в год.
Затем, как показано на рис. 5, затраты по хранению увеличиваются с увеличением объемов заказов: большие объемы заказов означают увеличение средних запасов, а следовательно, увеличение затрат по хранению, неполученного дохода на вложенный в запасы капитал, затрат на страхование и потерь от уценки. Напротив, затраты по размещению и выполнению заказов снижаются с увеличением размера партии: затраты на размещение заказов, затраты поставщиков на наладочные работы и затраты на обработку заказа уменьшаются при снижении частоты заказов, приводящей к увеличению объемов хранимых запасов.
Если сложить графики затрат по хранению запасов (ТСС, Total Carrying Cost - общие годовые затраты по хранению) и выполнению заказов (TOC, Total Ordering Cost - общие затраты по выполнению заказов), представленные на рис. 4, то их сумма будет представлять собой график общих затрат по поддержанию запасов (TIC, Total Inventory Costs - общие затраты по поддержанию запасов). Точка, в которой величина TIC принимает минимальное значение, определяет оптимальный размер партии (EOQ, Economic Ordering Quantity - оптимальная партии заказа).
Формула модели EOQ может быть записана иначе:
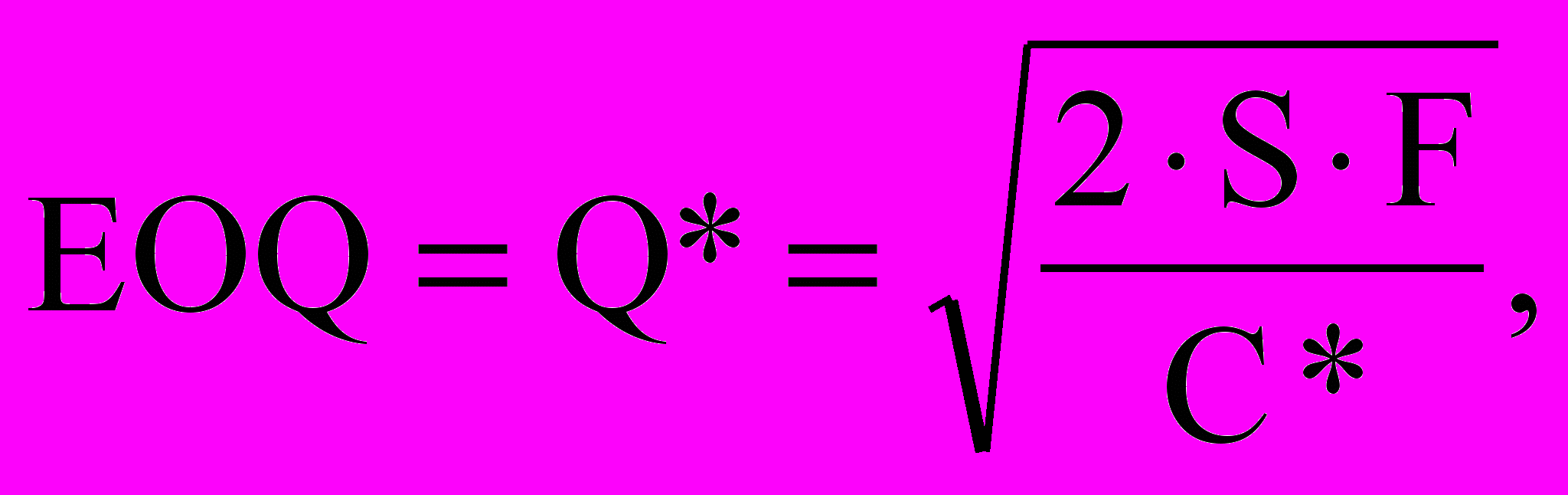
где: С* — годовые затраты по хранению единицы запасов, выраженные в денежных единицах [3.3, с.350].
Анализ чувствительности EOQ. Под EOQ не стоит понимать какое-либо жестко заданное количество запасов, отклонения от которого недопустимы. Можно доказать, что отклонение от EOQ до определенного предела не оказывает существенного влияния на величину общих затрат по поддержанию запасов и, следовательно, EOQ не следует рассматривать как единственную в своем роде величину. В качестве анализа чувствительности EOQ приводим пример из [3.3, с.358]. В табл. 3 показаны расчеты, определяющие чувствительность совокупных затрат к изменению величины закупки. Можно заметить, что колебания заказываемого количества единиц от 5000 до 8000 вызывают увеличение общих затрат не более чем на 3,4 %. Таким образом, можно устанавливать размеры заказа в пределах довольно широкого диапазона без существенного увеличения затрат.
Таблица 3
Чувствительность совокупных затрат к изменению величины закупки
Объем заказа, ед. | Общие затраты по поддержанию запасов, дол. | Отклонение от оптимального уровня, % |
3000 | 10512 | +31.4 |
4000 | 8960 | +12.0 |
5000 | 8275 | +3.4 |
6000 | 8023 | +0.3 |
6500 | 8000 | 0.0 |
7000 | 8019 | +0.2 |
8000 | 8170 | +2.1 |
9000 | 8423 | +5.3 |
10000 | 8750 | +9.4 |
Применение формулы Вильсона не ограничивается данной моделью. Учитывая, что данная формула не учитывает возможность возникновения дефицита запасов, П.М.Ферейр в своих исследованиях использовал производную от формулы Вильсона, позволяющую рассчитывать рациональную партию с учетом минимизации потерь от дефицита.
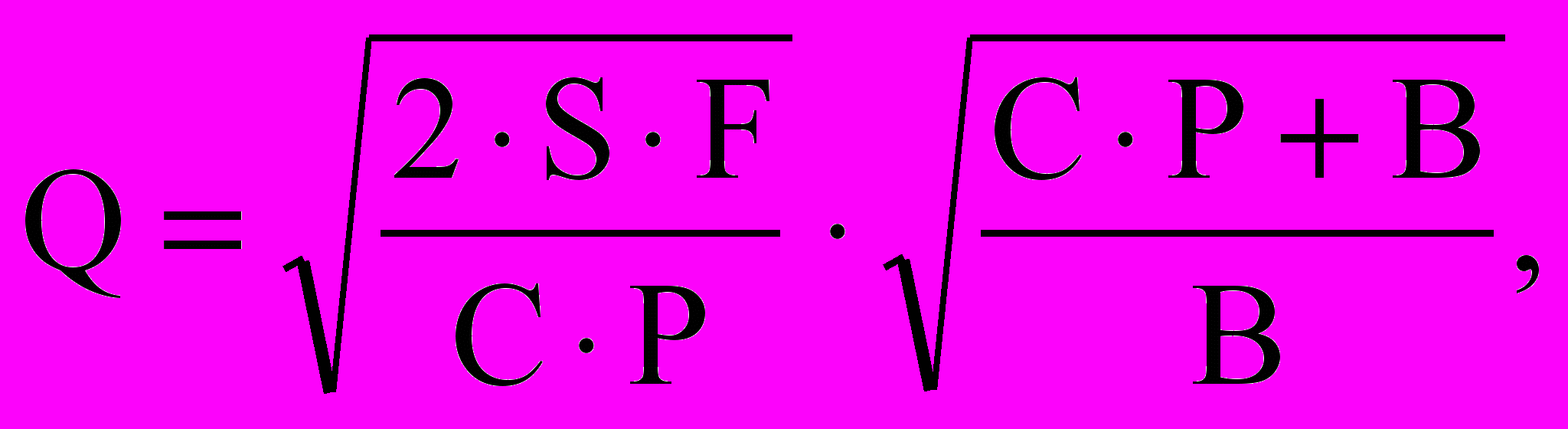
где: B - потеря от дефицита единицы материала в единицу времени.
Данная формула является производной от формулы Вильсона, поскольку при очень большой величине В, т.е. повышение штрафа за дефицит превращает вторую дробь в 1, что приводит данную формулу к первоначальному виду формулы Вильсона.
Формула Вильсона, не учитывает потери предприятия, связанные с капитализацией средств. Для расчета оптимальной партии с учетом банковского процента целесообразно использовать методику Матца-Карри-Фрэнка, которая имеет следующий вид [3.3, с.160]:
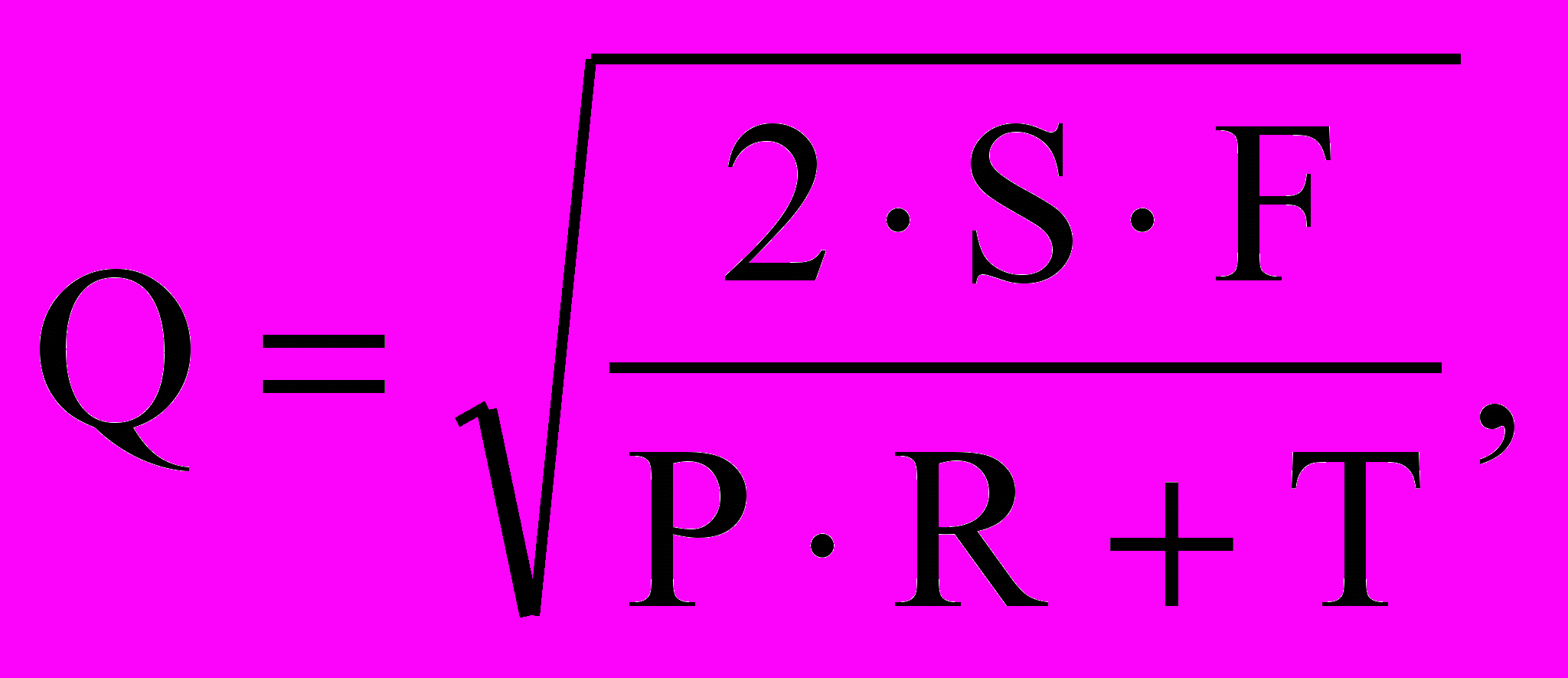
где: S - общая потребность в сырье на период в единицах;
F - стоимость выполнения одной партии заказа;
P - стоимость единицы запаса;
R- предполагаемая ставка банковского процента;
Т - транспортные расходы на единицу материала за год.
В формуле Матца-Карри-Фрэнка предполагается, что предприятие при осуществлении закупок несет три вида издержек:
издержки, связанные с отвлечением финансовых ресурсов на приобретение единицы запаса – P-R в размере средней ставки банковского процента;
- издержки, связанные с транспортировкой единицы запаса – Т;
- издержки на выполнение заказа - условно-постоянные расходы, не зависящие от размера заказываемой партии - F.
Проведенное исследование позволило рассчитать оптимальный размер партии закупки, однако в наших условиях, когда возникают непредвиденные ситуации, в которых даже математические формулы остаются бессильными, рекомендуем рассчитывать оптимальную партию закупки по формуле Матца-Карри-Фрэнка, но с учетом страхового запаса. В этом случае хозяйство сможет более эффективно использовать имеющиеся транспортные, трудовые и финансовые ресурсы, а также высвободить из оборота дополнительные денежные средства и направить их на другие цели.
Недостатки системы управления запасами с фиксированной величиной заказа. Применение системы управления запасами с фиксированной величиной заказа в отечественной практике несколько затруднительно, поскольку специфика нашей экономики не позволяет рассчитать некоторые составляющие для расчета.
Так, в отечественной практике, как правило, нет возможности определить стоимость заказа, которая за рубежом включает постоянные расходы, связанные с заказом одной партии, и потому не зависящей от ее размера, такие как, телеграфные, командировочные и другие расходы, уменьшающиеся в расчете на единицу материалов при увеличении размера заказываемой партии. Кроме того, затраты связанные с хранением производственных запасов, часто, не зависят от размера запасов, поскольку большинство предприятий имеют собственные склады и издержки на хранение (отопление, освещение, вентиляция складских помещений и т.д.) практически не зависят от заполнения склада. В этом случае возникает следующая ситуация: с увеличением партии закупки накладные расходы в расчете на единицу запаса уменьшаются, а расходы на хранение не зависят от количества хранимого сырья, т.е. чем больше партия закупки, тем лучше.
Применение формулы Вильсона наиболее целесообразно, на предприятиях оптовой торговли, не имеющих собственных складских помещений и уплачивающих арендную плату за аренду склада пропорционально объему хранимого сырья.
Система с фиксированной периодичностью проверки/заказа. Имеются и другие системы управления запасами, например система с постоянным уровнем запасов. В этой системе издержки управления запасами в явном виде не рассматриваются, и фиксированный размер заказа отсутствует. Через постоянные промежутки времени проводится проверка состояния запасов, и если после предыдущей проверки было израсходовано какое-либо количество запасов, то подается заказ. Размер заказа равен разности между максимальным уровнем, до которого происходит пополнение запасов, и фактическим уровнем в момент проверки. Работу алгоритма можно отобразить графически (рис. 6).
Максимальный уровень запасов определяется по формуле [3.3, с.310-316]:

где: М - максимальный уровень запасов;
В – страховой запас, ед.;
S – средний ожидаемый сбыт (расходование), ед. в сутки;
L – время доставки заказа, суток;
R – длительность промежутка времени между проверками, суток.
![]() |
Рис. 6. Работа по алгоритму S-s |
Для определения размера заказа применяется одно из двух правил [3.3, с.312]. В случае, если время доставки меньше длительности промежутка времени между проверками уровня запасов, то размер заказа равен разнице между максимальным запасом (М) и размером наличного запаса в момент проверки (J).
В случае, если время доставки больше длительности промежутка времени между проверками уровня запасов, то размер заказа равен разнице между максимальным запасом (М) и размером наличного запаса в момент проверки (J) минус уже заказанный, но еще не доставленный запас q0.
В математической записи это выглядит так:
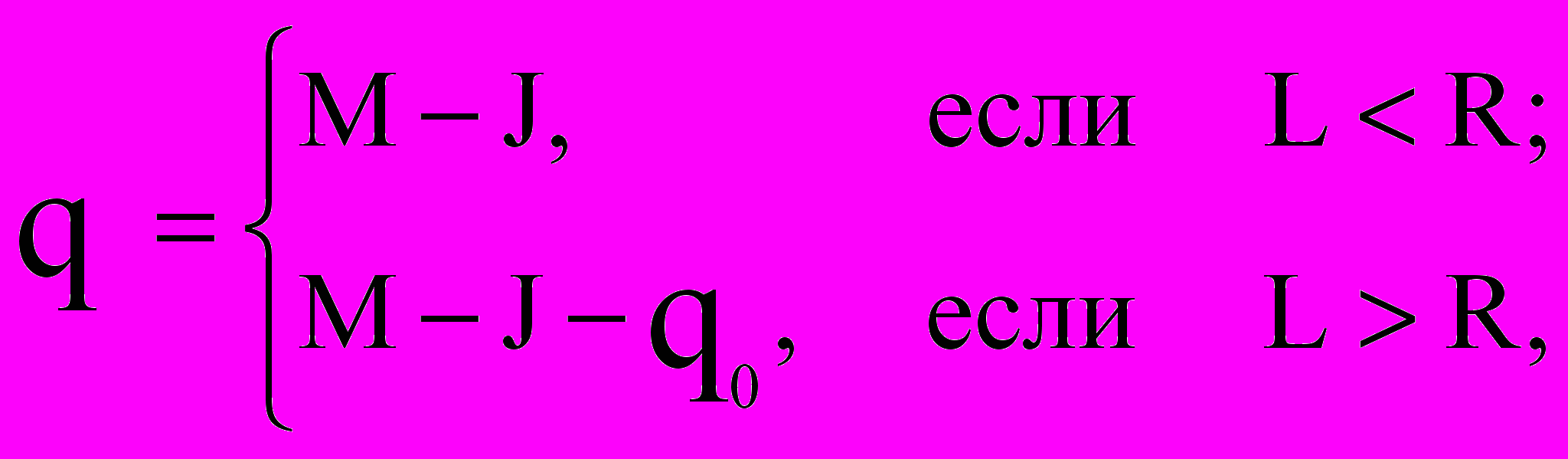
где: J – размер наличного запаса в момент проверки ед.;
q0 –заказанное количество, ед.
Уровень М, до которого происходит пополнение склада, является минимальным уровнем запасов, при котором обеспечивается определенная защита от дефицита и выполняется принятый план периодических проверок и заказов. Он достигается в том случае, когда в интервале от момента подачи до момента его получения отсутствует сбыт. Размер заказа зависит от величины сбыта после последней проверки.
Средний уровень запасов Jср. составляет [3.3, с.311]:
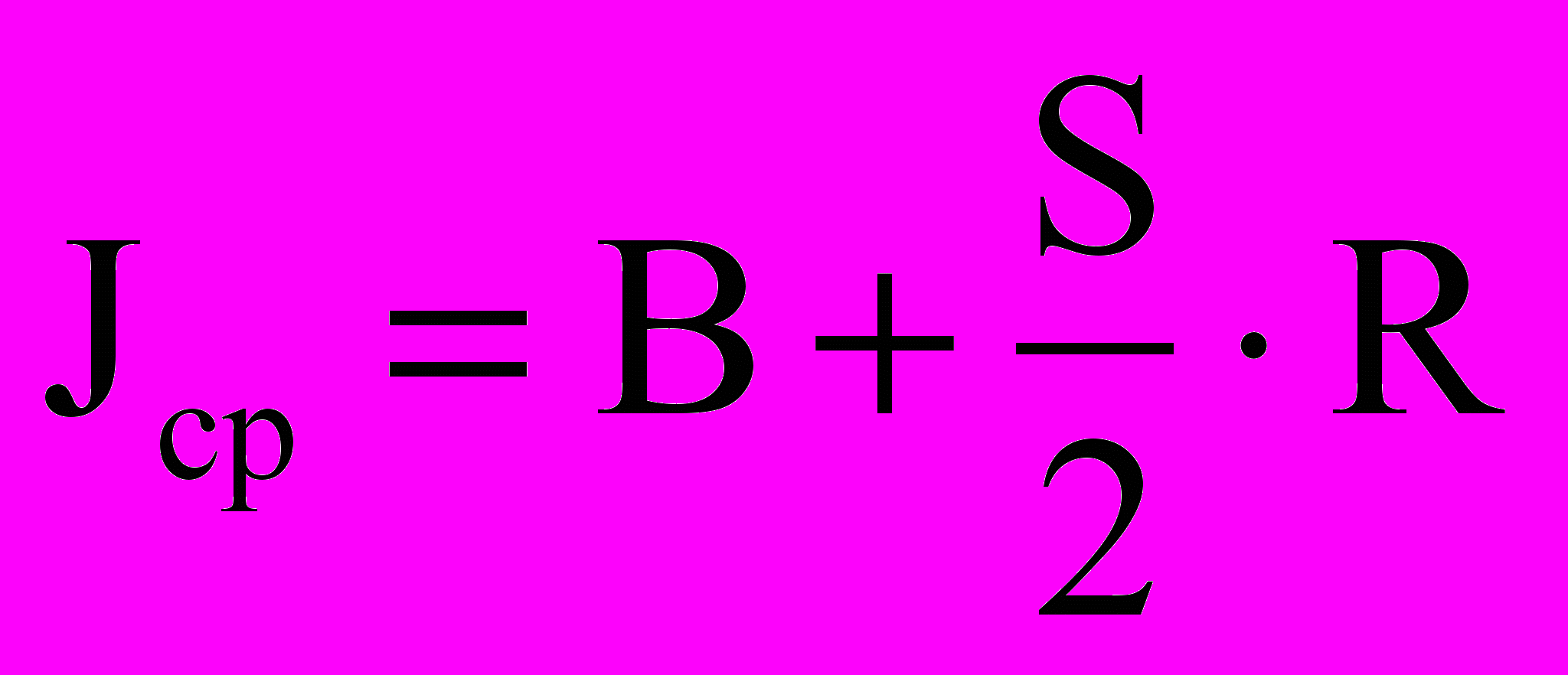
Размер резервного запаса В можно определить, рассматривая распределение сбыта (расходования) за определенный промежуток времени.
Существует еще одна система управления запасами, называемая системой с двумя уровнями, или S-s системой. По существу это система с постоянным уровнем запасов, для которой установлен нижний предел размера заказа. В такой системе рассматривается максимальный уровень запасов М, вычисляемый по формуле (11) и, кроме того, используется точка заказа, вычисляемая по формуле [3.3, с.312]:
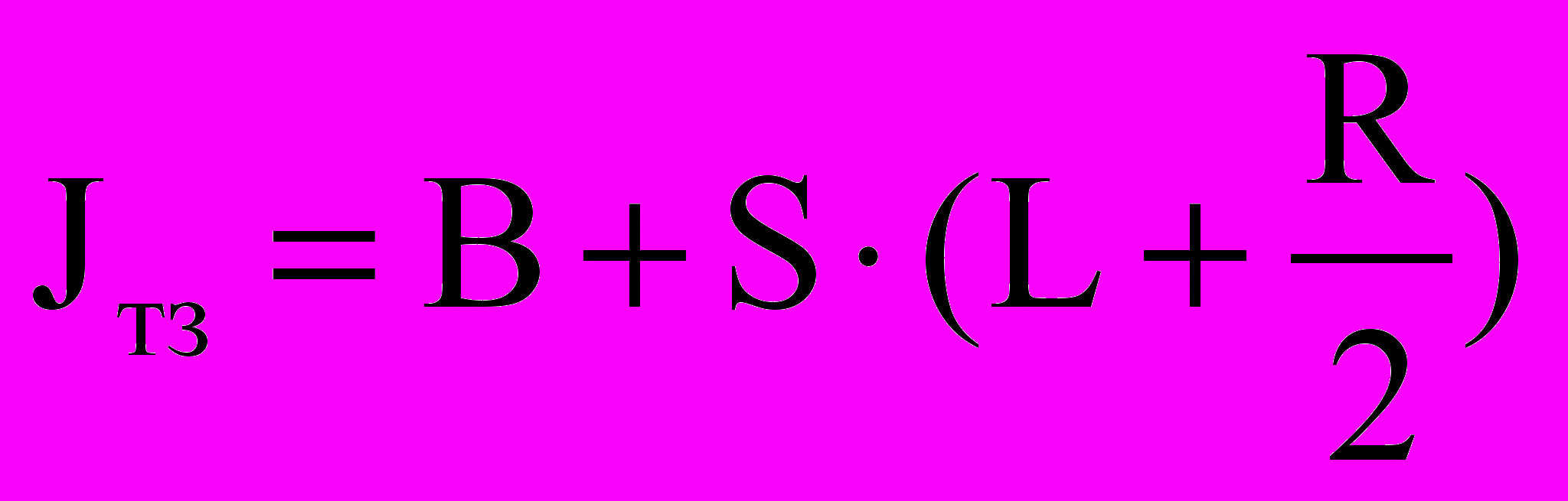
где: Jтз – точка заказа;
В – страховой запас, ед.;
S – средний ожидаемый сбыт (расходование), ед. в сутки;
L – время доставки заказа, суток;
R – длительность промежутка времени между проверками, суток.
Недостатки системы управления запасами с фиксированной периодичностью заказа и системы управления запасами с двумя уровнями. Эти системы управления запасами имеют такие же недостатки, как и система с фиксированной величиной заказа, однако это системы больше приспособлены для производств с часто изменчивым спросом на сырье. Возможно, применение этих систем управления запасами к сырью с низкой стоимостью, хранение значительных запасов, которых не представляет больших финансовых затруднений (группа сырья категории С). Однако, это управление с запасами с использованием системы с фиксированной периодичностью заказа связано с существенно большими расходами на совершение заказов.
Системы планирования потребностей в материалах и календарного планирования производственных ресурсов. Управление производством и производственными запасами давно и успешно автоматизируют. Одним из наиболее распространенных методов управления производством и дистрибуции являются системы планирования потребностей в материалах (MRP, Material Requirements Planning) и календарного планирования производственных ресурсов (MRP II – Manufacturing resources Planning) – это первое и второе поколение средств, которые позволяют корпорациям лучше управлять своими производственными системами (путем распределения материалов и составления графика производства) [3.3].
MRP II - это общепринятая на Западе идеология, технология и организация управления промышленными предприятиями. В свою очередь just-in-time (JIT) - это и метод управления, и своеобразная философия управления. JIT как философия управления ориентирована на организацию бездефектного производства при минимуме издержек. Индекс II подчеркивает «второй уровень» данной методологии по сравнению с MRP.
Системы класса MRP II должны планировать деятельность служб сбыта, снабжения и производства как сквозной график взаимосвязанных заказов; включать в себя средства бюджетирования и развитую систему управленческого учета, а также содержать систему бухгалтерского учета международного класса или иметь интерфейс с такой системой, работающей как в российских, так и в западных (GAAP, IAS) стандартах бухгалтерского учета и отчетности.
В системе класса MRP II должны четко выделяться следующие базовые блоки [3.3, с.22]:
Разработка плана на основе заказов клиентов и прогноза спроса. Этот организационно-алгоритмический процесс включает процедуру быстрой проверки выполнимости плана по ресурсам, так называемое «приблизительное планирование мощности».
- Планирование производства, т.е. формирование плана-графика изготовления партии изделий собственного производства и плана-графика закупки материалов и комплектующих. При этом работают вполне определенные алгоритмы расчета размеров заказов и дат запуска заказов на основе сетевых моделей. На этом этапе выполняется также расчет загрузки ресурсов или балансировка плана-графика по ресурсам.
- Оперативное управление. Процедуры проверки укомплектованности и запуска заказов, управление ходом производства через механизмы производственных циклов, приоритетов, размеров заказов. Учет выполнения операций и заказов.
- Складской учет.
Основной задачей стандартов MRP II является управление производством, прежде всего серийного типа.
Действительно, совместное планирование материальных потоков и производственных мощностей позволяет поднять всю систему планирования на новый уровень, так как удается определить финансовые результаты сформированного производственного плана весьма точно, что невозможно при «частичном» планировании (т.е. становится возможным сравнить плановые поступления от продаж с необходимыми для организации производства прямыми затратами, необходимые косвенные затраты при этом считаются обеспеченными).
В системы этого класса должны входить средства, позволяющие смоделировать весь ход производства при данном варианте основного плана, чтобы увидеть возможные будущие проблемы и узкие места.
Эти системы разработаны в США и поддержаны американским Обществом по контролю за производством и запасами – American Production and Inventory Control Society (APICS). Это общество регулярно издает документ «MRP II Standard System», в котором описываются основные требования к информационным производственным системам.
Концепция MRP, появившаяся в 50-х гг., ориентирована на будущее. Пополнение запасов в MRP базируется на прогнозируемых нуждах, рассчитанных, в частности, исходя из календарного плана-графика и запланированного резерва. Базовая идея MRP осталась той же и ныне.
Одно время считалось, что новая идея JIT (Just-In-Time – «точно в срок») заменит MRP. Но это было скорее изменение в менталитете менеджеров, чем в бизнес - вычислениях. С помощью JIT руководители фирм надеялись идентифицировать и устранить потери (определяемые как «все, что увеличивает цену, не расширяя функциональности»). В ответ на эту инициативу предприятия уменьшили запасы. Поменяли даже планировку заводов, чтобы снизить эксплуатационные расходы, начали автоматизировать производство и добиваться целей максимально эффективным способом.
Обратная связь | Планирование | Выполнение | Финансы |
![]() | |||
Рис. 7. Схема управления запасами предприятия по модели MRP II |
MRP II – это набор проверенных на практике разумных принципов, моделей и процедур управления и контроля, служащих повышению показателей экономической деятельности предприятия, входящего в корпорацию. Идея MRP II опирается на несколько простых принципов, например, разделение спроса на зависимый и независимый. MRP II Standard System содержит описание 16 групп функций системы [3.3]:
|
|
|
|
|
|
|
|
|
|
|
|
|
|
|
|
С накоплением опыта моделирования производственных и непроизводственных операций эти понятия постоянно уточняются, постепенно охватывая все больше функций.
Задачей информационных систем класса MRP II является оптимальное формирование потока материалов (сырья), полуфабрикатов (в том числе находящихся в производстве) и готовых изделий. Система класса MRP II имеет целью интеграцию всех основных процессов, реализуемых предприятием, таких как снабжение, запасы, производство, продажа и дистрибуция, планирование, контроль за выполнением плана, затраты, финансы, основные средства и т.д.
Стандарт MRP II делит сферы отдельных функций (процедур) на два уровня: необходимый и опциональный. Для того, чтобы программное обеспечение было отнесено к классу MRP II, оно должно выполнять определенный объем необходимых (основных) функций (процедур).
Эта система обеспечивает управление и контроль за всеми материальными, информационными и финансовыми потоками как внутри самого предприятия, так и в цепи «Поставщики – Производители – Потребители».
Нужно сказать, что MRP II традиционно рассматривается как средство, направленное на среднее и долгосрочное планирование. Сегодня клиенты развивают производственные планы на основе относительно статичной информации о продажах. Между тем нужен быстрый отклик на нужды пользователя, влекущий, естественно, оперативные изменения в системах планирования и управления.
MRP II постепенно превращается в средство планирования в реальном времени. Производители не могут более оперировать «в вакууме», они должны видеть картину в целом. Современные концепции должны помочь им прошагать от принципа «получить заказ и быстро выполнить» к интегрированным потокам информации, которые связывают воедино клиентов, процесс производства и поставщиков [3.3].
Таким образом, можно проводить координацию спроса и предложения ресурсов на определенном уровне планирования и ресурсов на высших уровнях планирования.
Недостатки систем управления предприятия класса МRP. Несмотря на все перечисленные достоинства, эти системы имеют и ряд недостатков:
- значительный объем вычислений, подготовки и предварительной подготовки большого объема исходной информации;
- возрастание логистических издержек на обработку заказов;
- нечувствительность к кратковременным изменениям спроса;
- значительное число отказов из-за большой размерности.
Эти недостатки накладываются на общий недостаток систем толкающего типа: недостаточно строгое отслеживание спроса с обязательным наличием страховых запасов.
Однако MRP достаточно эффективны по сравнению с «точно во время» при достаточно больших производственных циклах в условиях неопределенного спроса [3.3].
Идеология «Точно – во время» или система поставок «точно в срок». Относительно новый подход к контролю запасов — система поставок точно в срок (just-in-time) впервые был применен японскими фирмами и стал пользоваться большой популярностью во всем мире. Just-in-time (JIT) - это и метод управления, и своеобразная философия управления. JIT как философия управления ориентирована на организацию бездефектного производства при минимуме издержек.
Смысл этой системы состоит в том, чтобы обеспечить доставку поставщиками своей продукции «с колес» на сборочную линию, в то время как на территории предприятия поддерживается минимальный уровень производственных запасов. Некоторые американские производители приняли на вооружение эту систему и остались довольны результатами, хотя ее внедрение в Соединенных Штатах в значительной степени осложняется большими расстояниями.
Функционирует она следующим образом. Производитель устанавливает производственный график с использованием системы планирования потребностей в материалах, описанной выше, и определяет свои потребности в деталях и материалах. Поставщик обязан поставить сырье по принципу «с колес» на сборочную линию. Эффективность обеспечивается за счет подключения поставщика к компьютерной системе заказчика, и в своей деятельности он больше напоминает подразделение компании-заказчика, чем самостоятельную фирму. Поставщик доставляет материалы к моменту возникновения потребности в них в производстве, а на случай задержки поставки по какой-либо причине, поддерживается минимальный запас этой продукции [3.3, c.441-442].
Система «Канбан». Организационно-техническое содержание японского менеджмента включает в себя систему «Канбан» комплексное управление качеством, ориентацию только на потребителя, методы «участвующего управления» и «опережающего мышления», гибкую оргструктуру, систему управленческого контроля и др.
Впервые система «Канбан» была разработана и применена в автомобильной компании «Toyota». Суть этой системы сводится к отказу от производства продукции крупными партиями и созданию непрерывно-поточного многопредметного производства изделий разных моделей; при этом снабжение участков осуществляется столь малыми партиями, что по существу превращается в поштучное. Диспетчеризацию заказов выполняют сами рабочие. Система «Канбан» предусматривает уменьшение объема обрабатываемых партий, сокращение задела, практическую ликвидацию незавершенного производства, сведение к минимуму объема товарно-материальных запасов. В результате ликвидируются большинство складских помещений и высвобождаются производственные площади, ранее использовавшиеся для размещения задела.
Применение этой системы требует существенного сокращения времени переналадки и переоснащения производственного оборудования, а также выполнения ряда других предварительных условий, достижение которых стало возможным лишь на базе научно-технического прогресса. Внедрение системы «Канбан» требует больших затрат, однако после ее внедрения затраты с лихвой окупаются и достигается большой экономический эффект за счет рационального использования материалов, повышения производительности труда и качества продукции.
Такая система может применяться только при наличии определенных условий:
- местонахождение поставщика должно быть сравнительно недалеко от автомобилестроительного предприятия;
- наличие развитых систем связи, в частности использование системы электронного обмена данных между автомобилестроителем и субпоставщиком;
- субпоставщики второго уровня должны иметь интегрированные системы материально-технического обеспечения с субпоставщиком первого уровня.
При использовании системы синхронного снабжения фирмы - производители автомобилей, и не только японские, требуют от субпоставщиков организации доставки комплектующих изделий своими силами [3.3, с.416].
Анализ Парето или анализ АВС. Метод АВС связан с широко распространенным в природе явлением, известным, как правило “80–20”, которое впервые открыл и теоретически обосновал В.Парето (1897).
Суть принципа Парето состоит в том, что в процессе достижения какой-либо цели нерационально уделять объектам, образующим малую часть вклада, то же внимание, что и объектам первостепенной важности. При этом предварительно все управляемые объекты необходимо вначале оценить по какому-то параметру.
Представьте себе, что вы уронили 100 монет на лужайку. Первые 80 монет вы нашли довольно быстро, но на поиски каждой следующей у вас уходит все больше и больше времени, так как радиус поиска расширяется, трава на лужайке разной высоты и плотности и т.д. Расход времени на одну монету возрастает и, наконец, наступает такой момент, когда удельный расход времени на поиск одной монеты превысит стоимость монеты. Об этом надо помнить и вовремя остановиться.
В управлении запасами это правило проявляется следующим образом:
- 80 % стоимости продукции определяет 20 % входящих в нее компонентов;
- 80 % запасов дают 20 % наименований хранимых на складе запасов;
- 20 % поставщиков предприятия создают 80 % всей опасности потерь от связей с недобросовестным контрагентом.
Определение метода ABC, приведенное в работе [3.3] гласит: метод ABC - способ нормирования и контроля за состоянием запасов, заключающийся в разбиении номенклатуры N, реализуемых товарно-материальных ценностей на три неравнозначных подмножества А, В, и С на основании некоторого формального алгоритма. Графически метод ABC представлен на рис. 8.
Анализ Парето хорошо иллюстрируется диаграммой Парето (см. рис. 8), на которой по оси абсцисс отложены причины возникновения проблем качества в порядке убывания вызванных ими проблем, а по оси ординат - в количественном выражении сами проблемы, причем как в численном, так и в накопленном (кумулятивном) процентном выражении.
![]() |
Рис. 8. Графический метод ABC |
Ресурсы (материалы) класса А — это немногочисленные, но важнейшие ресурсы, на которые приходится большая часть денежных средств, вложенных в запасы. Размеры запасов по позициям группы А постоянно контролируют, точно определяют издержки, связанные с закупкой, доставкой и хранением, а также размер и момент заказа.
Ресурсы (материалы) класса В занимают срединное положение в формировании запасов предприятия и по сравнению с группой А требуют к себе меньшего внимания. Здесь осуществляется обычный контроль и сбор информации о запасах, который должен позволить своевременно обнаружить основные изменения в использовании запасов.
Ресурсы (материалы) класса С, составляющие, как правило, большую часть ассортимента, относят к второстепенным. На долю этих ресурсов приходится наименьшая часть всех финансовых средств, вложенных в запасы. Точные оптимизационные расчеты размера и периода заказа с ресурсами данной группы не выполняются. Пополнение запасов регистрируется, но текущий учет уровня запасов не ведется. Проверка наличных запасов проводится лишь периодически, например, один раз в шесть месяцев [3.3, c.115-122].
Выбор и использование одной из трех рассмотренных основных систем или использование иной системы зависит от следующих обстоятельств:
Если издержки управления запасами значительные и их можно вычислить, то следует применять систему с фиксированным размером заказа.
- Если издержки управления запасами незначительные, то более предпочтительной оказывается система с постоянным уровнем запасов.
- При заказе товаров поставщик налагает ограничения на минимальный размер партии. В этом случае желательно использовать систему с фиксированным размером заказа, поскольку легче один раз скорректировать фиксированный размер партии, чем непрерывно регулировать его переменный заказ.
- Однако, если налагаются ограничения, связанные с грузоподъемностью транспортных средств, то более предпочтительной является система с постоянным уровнем запасов.
- Система с постоянным уровнем запасов более предпочтительна и в том случае, когда поставка сырья происходит в установленные сроки.
- Система с постоянным уровнем и система с двумя уровнями часто выбираются тогда, когда необходимо быстро реагировать на изменение сбыта [3.3].