Планирование материальных потребностей производства (material requirements planning mrp) Цели изучения: Завершив изучение данной главы, вы должны уметь Описать условия,
Вид материала | Решение |
- Планирование продаж планирование производства формирование графика выпуска продукции, 382.65kb.
- Планирование и контроль за всем циклом производства с возможностью влияния на него, 1206.53kb.
- Задачи изучения дисциплины Врезультате изучения данной дисциплины студенты должны, 107.67kb.
- Пояснительная записка врезультате изучения данных тем курса математики учащиеся должны, 237.64kb.
- История развития стандарта управления промышленным предприятием mrp, 399.66kb.
- Электронное научное издание «Труды мэли: электронный журнал», 129.87kb.
- Планирование на предприятии, 524.23kb.
- Задачи изучения дисциплины Реализация поставленной цели требует решение следующих задач:, 36.83kb.
- Московский Государственный Горный Университет утверждаю председатель умк по направлению, 54.53kb.
- «Место и роль картины в искусстве XX века», 157.29kb.
Глава 13
ПЛАНИРОВАНИЕ МАТЕРИАЛЬНЫХ ПОТРЕБНОСТЕЙ ПРОИЗВОДСТВА (MATERIAL REQUIREMENTS PLANNING — MRP)
Цели изучения:
Завершив изучение данной главы, вы должны уметь
- Описать условия, которым в наибольшей степени подходит MRP (планирование материальных потребностей производства)
- Описать исходные, выходные данные и природу процесса MRP
- Объяснить, как требования в контрольном производственном графике переводятся в материальные потребности в элементах нижнего уровня
- Обсудить выгоды и требования MRP
- Объяснить, как система MRP может быть полезна при планировании потребностей производственных мощностей
- Описать в общих чертах потенциальные преимущества и некоторые возможные трудности при использовании MRP
- Описать MRP-2 и объяснить, как оно соотносится с MRP
Содержание главы
Зависимый и независимый спрос
Общий обзор MRP
Входные данные для MRP
Контрольный график
Файл списка материалов
Файл данных по материально-производственным запасам
Функционирование MRP
Обновление данных в системе
Выходные параметры MRP
Обсуждение других проблем
Резервный запас
Определение размера партии
Планирование требований по производственным мощностям
Преимущества MRP и необходимые требования для ее функционирования
MRP-2
Заключение
Ключевые термины
Решение задач
Вопросы для обсуждения и повторения
Упражнения по написанию служебных записок
Задачи
Избранная библиография
Экскурсия на производство: Мебельное производство Стикли
Комментарии двух менеджеров по опыту применения MRP в своих компаниях: Я не знаю как мы обходились до сих пор без MRP Наше планирование перешло из состояния полного хаоса к относительной стабильности. Мы достигли значительного сокращения размера запасов и цен, и при этом уровень обслуживания клиентов в самом деле существенно повысился. Мы более чем удовлетворены MRP, он позволяет нам планировать, вместо того, чтобы тратить все наше время на преодоление одного кризиса за другим. Я настоятельно рекомендую всем компаниям-производителям применять MRP или другой подобный ему подход.
Мы так много хорошего слышали о MRP, что нам не терпелось его применить но пока что, как нам кажется, мы буксуем. Мы и близко не подошли к его внедрению, а уже давно превысили все запланированные сроки и конца расходам не видно. Все разочарованы особенно начальство. Сейчас даже ведутся разговоры о том чтобы оставить эту дурацкую затею.
Эти две точки зрения отражают диапазон типичных реакций на попытки фирм-производителей внедрить и использовать планирование материальных потребностей. В этой главе мы рассмотрим основные положения этой темы, включая необходимость этого подхода, основные концепции планирования потребностей производства, преимущества и ограничения, а также некоторые причины трудностей, с которыми сталкиваются компании. За этими темами последует описание MRP-2, расширенного подхода к ресурсному планированию, который включает в себя и MRP.
Глава 11 была посвящена управлению запасами при условии независимого спроса. В этой главе в центре внимания будет управление материально-производственными запасами, которые имеют зависимый или производный спрос.
Зависимый и независимый спрос
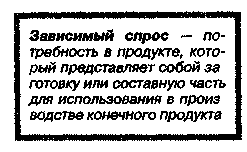
Независимый спрос достаточно стабилен, если учитывать определенные сезонные колебания, а вот зависимый спрос является скорее спорадическим, большой объем ресурсов используется только в определенные моменты, а в остальное время требуется маленький объем или не требуется вообще ничего. Например, фирма, которая производит садово-огородный инвентарь, может иметь большую номенклатуру продукции, а именно секаторы, газонокосилки и мини-тракторы. Предположим, что различное оборудование производится периодически — в один месяц косилки, в другой месяц — сеноуборочные машины, и в третий месяц — тракторы. Некоторые детали могут использоваться в большинстве из этих машин (например, гайки, болты и винты). Понятно, что необходимо иметь постоянный запас этих деталей, так как они всегда необходимы. С другой стороны, некоторые детали могут использоваться только при производстве одного вида машин. Следовательно, потребность в таких деталях существует только тогда, когда изготавливается машина данного вида, что может иметь место один раз за восемь, девять недель, в остальное время потребность в них равна нулю. Таким образом, этот спрос—спорадический. По этим причинам детали независимого спроса должны быть постоянно в наличии, а запас по деталям зависимого спроса необходимо возобновлять непосредственно перед началом производственного процесса, в котором они потребуются. Более того, предсказуемость использования деталей зависимого спроса означает, что нет практически никакой необходимости создавать для них резервный запас. Рис 13-1 показывает различия между производственными запасами предметов зависимого и независимого спроса.
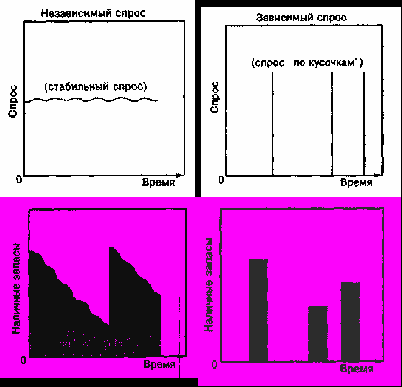
Рис. 13-1. Сравнительное представление для независимого и зависимого спроса
Общий обзор MRP
П
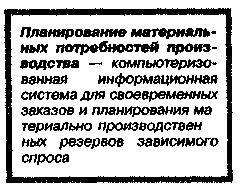
MRP — это не только технический прием, но своего рода философия — и настолько же контроль за производственными ресурсами, как и общий подход к планированию.
Исторически сложилось, что заказ деталей и планирование сборочных изделий наталкивались на две трудности. Первая из них—это огромный объем работы, чтобы создать плановые графики, отследить пути большого количества деталей и компонентов, и справиться с изменениями в графиках и заказах. Другая проблема — отсутствие разграничения понятий зависимого и независимого спроса. Слишком часто методы и приемы, разработанные для изделий независимого спроса, использовались для работы со сборочными изделиями, что приводило к созданию излишних производственных запасов. Соответственно, графики и планирование производственных запасов представляли основную проблему для производителей.
В 70-е годы производители начали осознавать важность разграничения между элементами зависимого и независимого спроса, и стали подходить к этим двум категориям по-разному. Многие фирмы сейчас взвалили ношу по ведению учета и определению материальных потребностей производства на компьютеры, используя MRP. Большая заслуга в рекламе MRP и обучении потенциальных пользователей принадлежит Джозефу Орлицки, Джорджу Плосслу, Оливеру Уайту, и Американскому обществу по контролю за производством и производственными запасами.
MRP начинается с создания графика конечного продукта, который затем преобразуется в график потребностей в узлах, деталях и сырьевых материалах, необходимых для производства конечного изделия в заданный период времени. Таким образом, MRP разработан для ответа на три вопроса: что нужно? сколько нужно? когда это потребуется?
Первичными входными параметрами для MRP являются:
список материалов, определяющих состав конечного продукта;
контрольный график, определяющий, сколько потребуется конечного продукта,
и когда;
файл информации о производственных ресурсах, который указывает количество наличных запасов и заказов.
Эта информация обрабатывается для определения чистых производственных потребностей для каждого периода запланированного производственного цикла.
Выходные параметры процесса MRP включают графики заказов, накладные, возможные изменения, заключения по производственному контролю, планированию и по непредвиденным ситуациям. Эти темы обсуждаются более подробно в последующих разделах. Структурная схема системы MRP приведена на рис. 13-2.
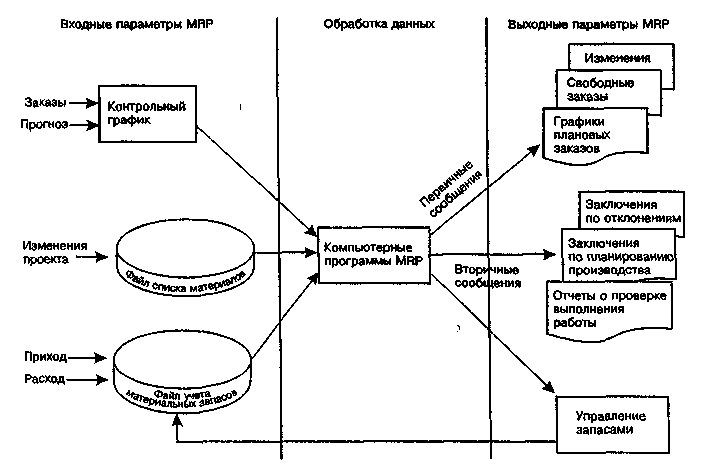
Рис. 13-2. Структура MRP
Входные данные для MRP
Система MRP имеет три основных источника информации: контрольный график, файл списка материалов и файл материальных ресурсов (см. рис. 13-2). Давайте рассмотрим каждый из этих входных параметров.
Контрольный график
К
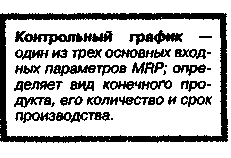
Номер недели
Предмет: х | 1 | 2 | 3 | 4 | 5 | 6 | 7 | 8 |
Кол-во | | | | 100 | | | | 150 |
Рис. 13-3. Контрольный график для конечного продукта X
Показатели в контрольном графике происходят из различных источников, включая заказы от потребителей, экономические прогнозы, заказы со складов для создания сезонных запасов, и внешний спрос.
Контрольный график делит плановый период на последовательность временных интервалов, которые часто выражены в неделях. Однако необязательно, чтобы временные интервалы были одинаковой длины. Фактически, краткосрочная (до 6 месяцев) часть контрольного графика может быть выражена в неделях, а долгосрочная в месяцах и даже в кварталах. Обычно, планы для более отдаленных периодов времени не настолько точны, как для краткосрочных требований.
Х
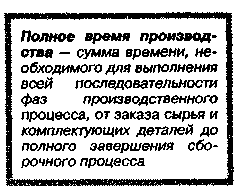
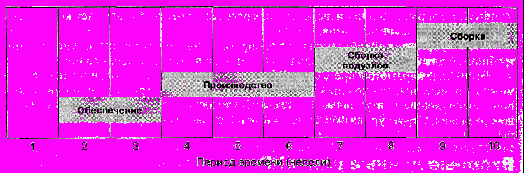
Рис. 13-4. Интервал планирования должен перекрывать полное время производства
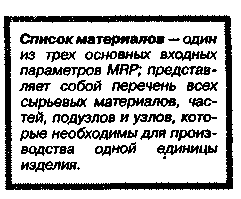
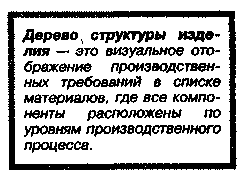
Обычно исходный контрольный график составляется на основе того, что требуется, а не того, что возможно осуществить, — поэтому начальный график может быть выполним, а может быть и невыполним, исходя из ограниченных возможностей производственной системы. Более того, контрольный график, который на первый взгляд может казаться вполне выполнимым, может оказаться совершенно нереальным, когда конечный продукт переводится в термины обеспечения, производства и сборки. К несчастью, система MRP не может отличить реальный контрольный график от нереального. Следовательно, часто бывает необходимо пропускать предложенный контрольный график через обработку системой MRP, для того чтобы получить более детальную картину требований, которые затем сравниваются с реальными возможностями производства. Если оказалось, что данный контрольный график нереален, то можно принять решение по увеличению производственных мощностей (например, за счет сверхурочной работы или субподряда), или же пересмотреть график. В последнем случае может получиться несколько новых вариантов, каждый из которых пропускают через систему MRP, пока не добьются реального плана. На этом этапе контрольный график «замораживается», по крайней мере, на ближайшее время, — таким образом устанавливается твердый график, на основе которого можно планировать потребности производства.
С
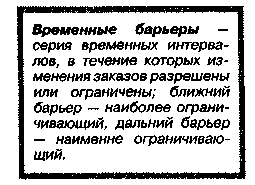
Некоторые компании устанавливают два защитных барьера: первый — это защитный интервал для краткосрочных производственных потребностей, а второй — защитный интервал для долгосрочного планирования. Например, защитный интервал для производственных потребностей может быть 4 недели с момента установления, в то время как защитный интервал для планирования может быть 10 недель. В ближнем интервале заказы от потребителя имеют преимущества перед прогнозированием. За защитным интервалом по планированию возможно включение новых заказов в контрольный график. В период между защитным интервалом по производственным потребностям и защитным интервалом по планированию, руководство должно вплотную заняться сбытом, когда планируется внести изменения, — если только не ожидаются дополнительные производственные мощности.
Файл списка материалов
С
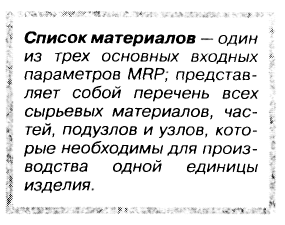
Перечень в файле СМ является иерархическим; он показывает количество каждого элемента, необходимого для завершения одной единицы изделия на каждом последующем уровне сборки. Внутреннюю структуру СМ можно представить яснее, рассмотрев дерево структуры изделия, которое дает визуальное представление о подузлах и компонентах, необходимых для сборки продукта.
На рис. 13-5 показаны диаграмма сборки стула и дерево структуры изделия для с
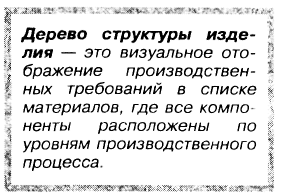
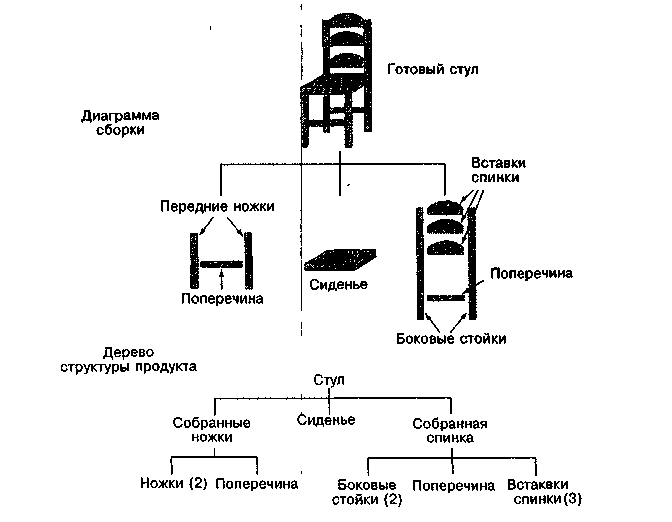
Рис. 13-5. Диаграмма сборки и дерево структуры продукта для стула
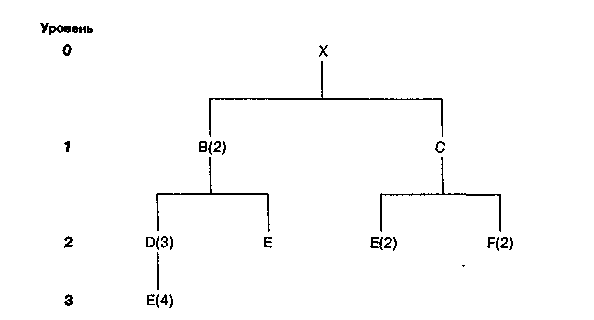
Рис. 13-6. Дерево структуры конечного продукта X
Дерево структуры изделия полезно для иллюстрации того, как СМ используется для определения количеств каждого из элементов (производственных потребностей), необходимых для получения требуемого числа конечных продуктов.
Давайте рассмотрим дерево структуры изделия, показанное на рис. 13-6. Конечный продукт X состоит из двух элементов В и одного элемента С. Кроме того, каждый элемент В требует три элемента D и один элемент Б, а каждый элемент D требует четыре элемента Е. Таким же образом, каждый элемент С изготавливается из двух элементов Е и двух элементов F. Эти производственные потребности представлены по уровням, начиная с уровня 0 для конечного продукта; затем идет уровень 1 для следующего уровня иерархии и т.д. Элементы каждого уровня являются составными частями для элементов более высокого уровня и, как в родословном дереве, «родителями» соответствующих элементов следующего уровня. Заметьте, что каждый компонент в дереве структуры изделия представлен строго в количестве, необходимом для полной сборки на последующем уровне.
ПРИМЕР 1
Используя данные, представленные на рио.13-6, проделайте следующее:
- Определите количество элементов В, С, D, E, F, необходимое для сборки одного изделия X.
- Определите количество этих компонентов, которое потребуется для сборки 200 изделий X.
Решение:
а.
Элемент | | Кол-во |
В | 2 В для X | = 2 |
D | 3 D для В 2 В для X | = 6 |
Е | 4 Е для D 3 D для В 2 В для X | = 24 |
Е | 1 Е для В 2 В для X | = 2 |
С | 1 С для X | = 1 |
Е | 2 Е для С 1 С для X | = 2 |
F | 2 Р для С 1 С для Х | = 2 |
Заметьте, что элемент Е встречается в трех различных местах. Общие требования по данному элементу можно определить путем суммирования всех величин для элемента Е, что даст 28.
б. Для сборки 200 единиц изделия X, количество каждого из компонентов должно быть умножено на 200. Например, должно быть 200(2) = 400 В, 200(6) = 1200 D, 200(28) = 5600 Е, и т.д.
Определение общих производственных потребностей — это более сложная задача, чем может показаться из приведенного примера. С одной стороны, многие продукты производства имеют значительно больше составных компонентов. С другой стороны, очень важен фактор времени (т.е. Когда компоненты должны быть заказаны или изготовлены); этот фактор необходимо включить в анализ. Наконец, по различным причинам, некоторые компоненты/подузлы могут уже быть в наличии (т.е. в существующих материально-производственных запасах). Следовательно, для определения общей производственной потребности, величина наличных компонентов должна быть отброшена (т.е. вычтена из видимых потребностей) для определения действительного количества.
К
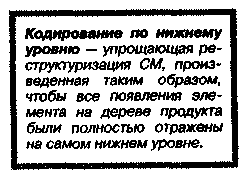
Рис. 13-7 показывает как компонент Е, который встречается на трех различных уровнях продукта Y, может быть сгруппирован на один уровень.
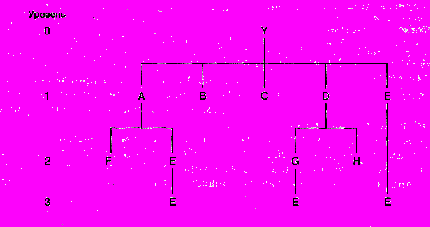
Рис. 13-7. Кодирование по нижнему уровню для компонента Е