Планирование материальных потребностей производства (material requirements planning mrp) Цели изучения: Завершив изучение данной главы, вы должны уметь Описать условия,
Вид материала | Решение |
- Планирование продаж планирование производства формирование графика выпуска продукции, 382.65kb.
- Планирование и контроль за всем циклом производства с возможностью влияния на него, 1206.53kb.
- Задачи изучения дисциплины Врезультате изучения данной дисциплины студенты должны, 107.67kb.
- Пояснительная записка врезультате изучения данных тем курса математики учащиеся должны, 237.64kb.
- История развития стандарта управления промышленным предприятием mrp, 399.66kb.
- Электронное научное издание «Труды мэли: электронный журнал», 129.87kb.
- Планирование на предприятии, 524.23kb.
- Задачи изучения дисциплины Реализация поставленной цели требует решение следующих задач:, 36.83kb.
- Московский Государственный Горный Университет утверждаю председатель умк по направлению, 54.53kb.
- «Место и роль картины в искусстве XX века», 157.29kb.
Обновление данных в системе
Д
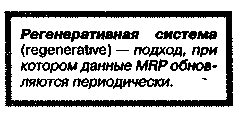
Регенеративная система является по своей сути пакетной системой, которая собирает все изменения (например, новые заказы, поставки), имеющие место в пределах определенного интервала времени (например, недели), и периодически обновляет систему. Используя эту информацию, разрабатывается скорректированный план производства (если необходимо) — точно таким же способом, каким был разработан и первоначальный план (например, используя список материалов уровень за уровнем).
В
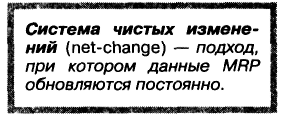
Номер недели
Конечный продукт | 1 | 2 | 3 | 4 | 5 | 6 | 7 |
W | | | 50 | | 70 | | 60 |
X | | | 200 | | | 100 | |
Y | | 30 | | | 80 | 90 | |
Рис. 13-14. Основной график производственного процесса
для конечных продуктов, в которых используется элемент G
Номер недели
Чистые требования для элемента G по: | 1 | 2 | 3 | 4 | 5 | 6 | 7 |
N | 40 | | 50 | | 40 | | |
М | 120 | | | 240 | | | |
Н | | | | 160 | 120 | | |
Итого | 160 | | 50 | 400 | 160 | | |
Общая потребность | 160 | | 50 | 400 | 160 | | |
Планируемые наличные запасы | 200 | 40 | 40 | 0 | 0 | | |
Чистая потребность | | | 10 | 400 | 160 | | |
Рис. 13-15. Чистые требования по элементу G
Регенеративная система больше подходит для относительно стабильных систем, тогда как система чистых изменений больше подходит для часто изменяющихся систем Очевидным недостатком регенеративной системы является потенциальный зазор между моментом получения информации и временем, когда эта информация может быть учтена в плане материальных потребностей С другой стороны, стоимость обработки информации при использовании регенеративной системы обычно меньше, изменения, происходящие в данный период времени, могут, в конечном счете, взаимоисключать друг друга, устраняя тем самым необходимость модификации и последующей ре-модификации плана Недостатки системы чистых потребностей относятся к стоимости компьютерной обработки информации, которая является неотъемлемой частью процесса модернизации системы, и постоянного движения в системе из-за множества незначительных изменений. Одним из способов избежать этого является внесение незначительных изменений периодически, а значительных изменений немедленно. Основным преимуществом системы чистых изменений является то, что руководство может в любой момент иметь текущую информацию для целей планирования и контроля.
Выходные параметры MRP
Система MRP может предоставлять руководству довольно широкий диапазон выходных параметров. Эти параметры часто подразделяются на первичные отчеты (primary reports), которые являются основными выходными параметрами, и вторичные отчеты (secondary reports), которые являются дополнительными выходными параметрами.
Первичные отчеты. Управление и планирование производства и запасов — это часть первичных отчетов. Обычно эти отчеты включают в себя следующее:
- Плановые заказы (planned orders) — график, показывающий величину и время будущих заказов.
- Выполнение заказа (order releases)—разрешение на выполнение плановых заказов.
- Изменения (changes) в плановых заказах, включая отмену заказа и пересмотр даты или величины заказа.
Вторичные отчеты. Планирование и контроль за исполнением входят во вторичный отчет.
- Отчеты по контролю за исполнением (perfomance-control reports) используются для оценки работы системы. Они помогают менеджерам тем, что показывают отклонения от планов (включая пропущенные поставки и отсутствие запасов) и снабжают информацией, которая может быть использована для определения стоимости исполнения.
- Отчеты по планированию (planning reports) полезны для прогнозирования будущих требований по запасам. Они включают обязательства по закупкам и другие данные, которые могут использоваться для оценки будущих материальных потребностей производства.
- Отчеты об исключительных ситуациях (exception reports) обращают внимание на основные несоответствия, такие как опоздавшие или просроченные заказы, слишком большой процент брака, ошибки в отчетности и требования на несуществующие детали.
Широкий диапазон выходных параметров, как правило, позволяет пользователю адаптировать MRP к своим специфическим требованиям.
Обсуждение других проблем
Кроме основных сведений о входных параметрах, выходных параметрах и самом процессе MRP, менеджер должен ознакомиться с другими аспектами MRP. Они включают: поддержание резервного запаса, выбор размера партии и возможность использования MRP для незавершенного производства.
Резервный запас
В принципе, системы управления запасами при зависимом спросе не требуют резервного запаса на уровнях ниже конечного продукта. Это одно из основных преимуществ подхода MRP. Теоретически, резервный запас не требуется, так как необходимое для работы количество материала можно спроектировать, как только будет разработан контрольный график. Однако на практике возможны исключения. Например, «заторы» в производственном процессе или неоднородный процент брака могут вызвать нехватку материалов на следующем уровне процесса. Кроме того, нехватка материалов может возникать, если задерживаются поставки, а также если сроки производства или сборки оказываются больше, чем ожидалось. На первый взгляд, эти условия должны потребовать использования резервного запаса для поддержания стабильности производства, — но проблема усложняете я, когда дело касается многоуровневой продукции (сборной продукции), так как нехватка любого компонента задержит здесь выполнение конечной сборки. И в то же время, основное преимущество MRP теряется, если надо поддерживать резервный запас для всех элементов нижних уровней.
Система MRP предлагает различимо пути решения таких проблем. Первым шагом менеджера является выявление наиболее нестабильных процессов и операций и определение уровня этой нестабильности При изменениях в сроках производственного процесса, вместо концепции резервных запасов часто используется концепция резервного времени. Это заключается в том,]что план поставок разрабатывается с достаточным опережением по времени, чтобы исключить или значительно сократить возможность задержки в выполнении заказа. Когда изменения касаются количественных показателей, то может потребоваться некоторый резервный запас, — однако менеджер должен тщательно взвесить необходимость и стоимость поддержания такого экстренного запаса. Часто менеджеры выбирают путь поддержания резервного запаса для конечного продукта, который подвержен случайному спросу, а также для выборочных операций нижнего уровня, когда недостаточно создания резервного времени.
Определение размера партии
В
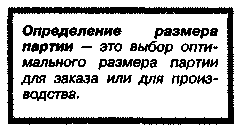
Основная цель управления запасами для систем с зависимым и независимым спросом — минимизация стоимости выполнения заказа (стоимости обеспечения производства) и стоимости поддержания запаса. При независимом спросе, потребности часто распределяются равномерно в пределах планового периода (например, 6 месяцев, год). Зависимый спрос, как правило, более неоднороден и его плановый период гораздо короче (например, 3 месяца), поэтому целесообразные размеры партии определить труднее. Рассмотрим ситуацию, приведенную на рис. 13-16. Периодические потребности изменяются от 1 до 80 единиц, и размер спроса не повторяется на всем протяжении показанного периода.
Период
| 1 | 2 | 3 | 4 | 5 |
Потребности | 70 | 50 | 1 | 80 | 4 |
Совокупные потребности | 70 | 120 | 121 | 201 | 205 |
Рис. 13-16. Потребности в детали К
Менеджеры могут достичь экономии посредством группирования объемов заказа и объемов работ. Например, в случае, когда дополнительные затраты, возникающие из-за содержания дополнительного запаса деталей, пока они не израсходовались, приводят к экономии в затратах на выполнение заказа. Временами этот процесс может быть очень сложным, по целому ряду причин. Во-первых, объединение повторяющихся запросов в единый заказ, особенно для конечных продуктов или элементов среднего уровня, вызывает эффект каскадности (cascading effect) вниз по всему дереву структуры продукта. То есть, для того чтобы достичь группирования, элементы нижних уровней дерева также должны быть сгруппированы, и при этом надо принимать в расчет стоимость их заказа и поддержания запаса. Во-вторых, неоднородный периодический спрос и относительно короткий плановый период требуют постоянного перерасчета и корректировки размеров заказа. Неудивительно, что методы определения размеров заказа (партии) лежат в диапазоне от самых сложных, которые пытаются учитывать все возможные затраты, — до самых простых, которые легко понять и применять. В определенных случаях, простые методы оказываются подходящими для минимизации стоимости, хотя обобщения делать трудно. Давайте рассмотрим некоторые из этих моделей.
Непрерывная организация заказов ( Lot - for - Lot Ordering). Пожалуй, самый простой из всех методов — непрерывная организация заказа (lot -for - lot ordering). Размер партии заказа на каждый период устанавливается эквивалентно производственным потребностям на данный период. Этот метод был приведен в примере 2. В данном случае не только очевидны размеры заказа (order size), но также фактически исключаются издержки хранения (holding costs) для компонентов, переносимых на следующий период. Следовательно, непрерывная организация поставок сводит к минимуму вложения в создание материальных запасов. Два основных недостатка этой системы: во-первых, она, как правило, включает заказы различного объема, при этом невозможно использовать преимущества заказов фиксированного объема (например стандартными контейнерами или другими стандартизованными способами); во-вторых, необходимо осуществлять новый заказ при каждом процессе. Если затраты на выполнение заказа можно будет значительно сократить, этот метод поможет подобрать размер партии с минимальной стоимостью.
Модель экономически целесообразной величины заказа (Economic Order Quantity Model). Иногда используется модель целесообразной величины заказа. Она помогает свести затраты к минимуму — при условии, что потребности достаточно регулярны. Это может относиться к компонентам нижнего уровня, общим для различных родителей, и к сырьевым материалам. Однако чем более неравномерна производственная потребность, тем этот подход менее применим. Так как спрос наиболее неравномерен обычно на уровне конечного продукта, данная модель более применима для материалов нижних уровней, чем для конечной продукции.
Заказы с фиксированным периодом (Fixed-Period Ordering). Данный тип заказов охватывает заранее определенное количество периодов (например, два или три). В одних случаях, диапазон выбирается приблизительно; в других случаях, просмотр данных предшествующего спроса может помочь более рациональному выбору длины фиксированного периода. Существует простое правило: план должен перекрывать интервал в два периода. Правило может быть изменено, если здравый смысл подсказывает лучший путь. Например, взгляните на рис. 13-16. При использовании правила двух периодов, величина поставок в 120 единиц покрывает первые два периода. Следующие два периода перекрываются заказами объемом 81 единица. Однако производственные потребности в периоды 3 и 5 очень малы, и разумно было бы объединить их с 80-ю единицами 4-го периода, результирующий спрос — 85 единиц.
Модель элемент-период (Part-Period Model). Модель элемент-период представляет собой еще одну попытку сбалансировать расходы на выполнение заказов и на поддержание запасов. Термин элемент-период (part-period) означает поддержание запасов деталей или частей в пределах определенного количества периодов. Например, если создан запас на 10 деталей на два периода, то величина элемент-период должна равняться 10 2 = 20. Эффективная величина элемент-периода (ЭЭП) может быть вычислена как отношение затрат на заказы к стоимости содержания одной единицы в один период. Таким образом, мы имеем следующую формулу:

Для того, чтобы определить размер заказа, который ближе всего к ЭЭП, оцениваются различные размеры заказов за плановый период и определяется количество элемент-периодов для каждого размера заказа. Тот вариант, который ближе всего к ЭЭП, выбирается как оптимальный размер партии. Оцениваемые размеры поставок основываются на совокупных производственных потребностях. Пример 3 иллюстрирует этот подход.
ПРИМЕР 3
Используйте метод элемент-период для определения размеров заказа для приведенного графика потребностей:
| Период | |||||||
| 1 | 2 | 3 | 4 | 5 | 6 | 7 | 8 |
Потребности | 60 | 40 | 20 | 2 | 30 | - | 70 | 50 |
Совокупная потребность | 60 | 100 | 120 | 122 | 152 | 152 | 222 | 272 |
Затраты на выполнение заказа для данного элемента составляют $80 за производственный цикл, а стоимость содержания единицы элемента — $0,95 за период
Решение:
- Сначала вычисляем ЭЭП. ЭЭП = $80/$0,95 = 84,21, эта величина округляется до 84.
- Затем попытаемся найти суммарные размеры партий, начиная с 60, до тех пор пока величины деталь-период не приблизятся к ЭЭП. Продолжим этот процесс на плановый период. Это приводит нас к следующему (см. таблицу ниже)
Период | Размер партии | Дополнительный запас (текущий) | | Периоды (текущие) | = | Детальные периоды | Совокупные деталь-периоды |
1 | 60 | 0 | | 0 | | 0 | 0 |
| 100 | 40 | | 1 | | 40 | 40 |
| 120 | 20 | | 2 | | 40 | 80 |
| 122 | 2 | | 3 | | 6 | 86* |
5 | 30 | 0 | | 0 | | 0 | 0 |
| 100 | 70 | | 2 | | 140 | 140* |
8 | 50 | 0 | | 0 | | 0 | 0 |
* Ближайшее к 84
Вычисления деталь-периодов показывают, что 122 единицы должны быть заказаны и получены к началу периода 1, и 100 единиц — должны быть заказаны и получены к началу периода 5. Следующая партия должна быть подготовлена к периоду 8, но на данный момент не хватает информации для определения ее размеров. Размеры партий, рассматриваемые за период 1, соответствуют совокупным производственным потребностям. Как только оптимальный размер партии определен, совокупные потребности приравниваются к нулю, а затем снова суммируются, начиная со следующего периода. В данном случае, размер заказа, равный 122 единицам, покрывает первые четыре периода, так что следующая совокупная потребность вычисляется для периода 5. Следующая партия распространяется до периода 7, и расчеты возобновляются с периода 8.
Процесс работает хорошо для первого размера партии, так как общее число деталь-периодов приближается к ЭЭП, но эффект неравномерного спроса явно сказывается на втором размере партии в 100 единиц (140 деталь-периодов — величина не слишком близкая к 84).
При выборе метода определения размера заказа следует принимать во внимание характер производственных потребностей (степень единообразия), относительную значимость соотношения между текущими издержками и стоимостью выполнения заказа, а также любые другие соображения, оказывающие влияние на заказы Не существует единственного метода, который одинаково подходил бы во всех случаях.
Несмотря на то, какой именно метод используется, всегда существует возможность корректировки размеров заказа, благодаря допускам на усушку и брак, установленной руководством максимальной и минимальной величине заказа (например, не заказывать более пятимесячного запаса), ограничениям на обработку и отгрузку (например, 200 ед. на производственный цикл или 12 дюжин на отгрузку), что требует округления размеров заказа (обычно в большую сторону), и других подобных факторов.
Планирование требований по производственным мощностям (Capacity Requirements Planning)
Одна из важнейших характеристик MRP — способность помочь менеджеру в планировании требований производственной мощности. Как уже отмечалось, контрольный график, который кажется выполнимым на первый взгляд, может оказаться нереальным с точки зрения требований по ресурсам, необходимым для производства и/ или сборки элементов нижнего уровня.
Планирование требований по производственной мощности — это процесс определения краткосрочных потребностей производственных мощностей. Необходимыми входными данными являются заказ-релизы для MRP, текущая загрузка цеха производства, информация по распределению и сроки производственных процессов. Выходные параметры включают отчеты по загрузке для каждого производственного участка. Когда отчеты отражают отступление от плана (перегрузки или недогрузки), менеджеры могут принять определенные меры, такие как введение альтернативных технологических карт, изменение или исключение партий поставок или требований по резервным запасам, и разделение партий. Сдвиг производственного процесса вперед или назад является весьма трудной задачей из-за предварительных требований и наличия или отсутствия компонентов.
Структура процесса планирования по мощности представлена на рис. 13-17. Процесс начинается с готового или опытного графика производственного процесса, который следует проверить на выполнимость и при необходимости внести изменения, пока график еще не утвержден. Представленный график обрабатывается с помощью MRP для определения вытекающих из него материальных потребностей производства. Затем они преобразуются в требования по ресурсам (т.е. по мощности), часто в форме серий отчетов по загрузке для каждого подразделения или производственного участка, — здесь сравниваются известные и предполагаемые требования по объемам с планируемой пропускной способностью. Природа таких отчетов по загрузке показана на рис. 13-18. Он показывает ожидаемые требования по ресурсам (т.е. использование ресурсов) для текущей работы, запланированные заказы, и ожидаемые поставки на планируемый период. Имея информацию подобного рода, менеджеру легче определить, достаточны ли существующие производственные мощности для удовлетворения данных требований. Если мощности достаточны, то часть производственного графика, определяющая данные требования, может быть «заморожена», т.е. утверждена. На рис. 13-18 отчет по загрузке предусматривает заказ-релизы за 4-ый период, которые вызовут перегрузку. Однако есть возможность скорректировать производственные потребности небольшим перемещением некоторых заказов на следующий период. Сходным образом, перегрузка возникает в период 11, но здесь также можно сместить некоторые процессы на соседний период времени. В случае, когда производственные мощности недостаточны, менеджер имеет возможность их увеличить (включением в график сверхурочных работ или переводом персонала из других подразделений, или заключением субподрядов на некоторые виды работ) — если это возможно и целесообразно, или же пересмотреть контрольный график производственного процесса, изменяя его до тех пор, пока он не станет выполнимым и реальным.
Если требуется пересмотр контрольного графика производственного процесса, это, как правило, означает, что менеджер должен внести приоритеты в планы поставок, т.к. определенные заказы будут осуществлены позднее намеченных сроков.
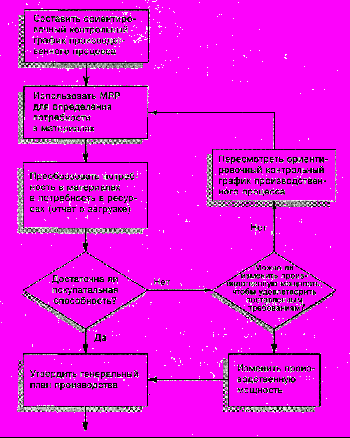
Рис. 13-17. Использование МНР как помощь в планировании требований
по производственным мощностям
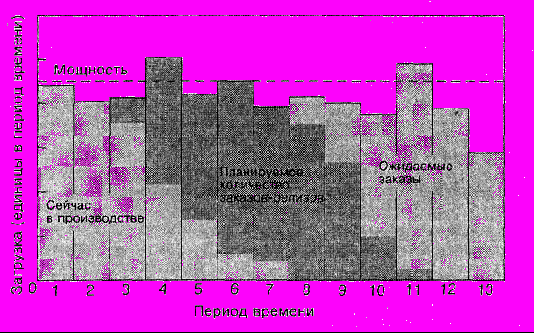
Рис. 13-18. Отчет по предполагаемой загрузке подразделений
Важным аспектом планирования требований по производственной мощности является перевод количественных требований в машино- и трудозатраты. Это осуществляется путем перемножения количественных требований за каждый период на стандартные значения машино- и/или трудозатрат для одного узла. Например, если планируется производство 100 единиц изделия А, и для каждой единицы стандартное значение времени трудозатрат 2 часа, а машинозатрат 1,5 часа, следовательно:
Трудозатраты: 100 единиц 2 часа/ед. = 200 трудочасов
Машинозатраты: 100 единиц 1,5 часа/ед. = 150 машиночасов
З

атем данные требования по производственной мощности можно сравнить с имеющейся мощностью производственного участка, чтобы определить, в какой степени производство данного продукта использует имеющиеся мощности. Например, если производственный участок имеет мощность 200 трудочасов и 200 машиночасов, тогда загрузка по затратам труда будет 100%, так как все имеющиеся мощности потребуются для производства продукта Однако машинные резервы будут недозагружены, недостаточны для производства.
где Т — требуется, И — имеется в наличии.
Недозагрузка может означать, что незадействованные мощности можно использовать для другой работы; перегрузка означает, что имеющиеся в наличии мощности. Для того, чтобы исправить положение, можно изменить график производства, или же ввести сверхурочные работы.
Преимущества MRP и необходимые требования для ее функционирования
Преимущества: MRP дает определенные преимущества при планировании стандартных производственных и сборочных процессов, включая:
- Возможность поддерживать низкий уровень материальных запасов производства.
- Возможность отслеживать материально-производственные потребности.
- Возможность оценивать данные по материальным потребностям производства, полученные из конкретного контрольного графика производственного процесса.
- Возможность распределения времени и сроков производства.
На типичном производственном предприятии масса людей использует информацию, полученную с помощью MRP. Разработчики производственного плана, естественно, являются первыми пользователями MRP. Руководители производства, которые должны распределять рабочую нагрузку между подразделениями и принимать решения по графикам работы, и заводские мастера, которые отдают непосредственные указанияI по рабочему процессу и отвечают за выполнение производственных графиков, — все они в большой степени опираются в своей работе на выходные данные MRP. Другими пользователями информации являются представители по работе с заказчиками, которые должны предоставлять заказчику информацию по отгрузке и доставке продукции, а также менеджеры по закупкам и менеджеры по управлению запасами. Эффективность MRP в значительной степени зависит от применения компьютерной техники, что позволяет постоянно владеть свежей информацией по материальным потребностям.
Необходимые требования для работы программы: Для эффективного функционирования системы MKF необходимо иметь:
- Компьютер и необходимое программное обеспечение для выполнения вычислений и ведения записей.
- Точные и свежие данные:
Контрольный график
Список материалов
Инвентаризация запасов
- Полный объем данных в файлах.
Точность данных абсолютно необходима для успешного функционирования MRP. Неточности в файле инвентарных записей и в файле списка материалов могут привести к неприятным сюрпризам, начиная от отсутствия необходимых деталей, слишком больших заказов по одним элементам и недостаточных заказов по другим, — и заканчивая полной невозможностью придерживаться графика производственного процесса. Все это приводит к неэффективному использованию ресурсов, просроченным поставкам и низкому уровню обслуживания потребителя. Более того, использование MRP может оказаться в этом случае слишком трудным и дорогостоящим. Следовательно, для компаний, которые собираются внедрять систему MRP, очень важно учитывать все эти факторы и сопоставить их с преимуществами MRP.
К сожалению, многие фирмы, стремящиеся установить систему MRP, недооценивают важность приведенных доводов. Во многих случаях оказывается, что список материалов устарел, так как в нем не отражались своевременно изменения в дизайне изделия. Это приводит к тому, что список комплектующих не отражает реальных требований по сборке конечного продукта. Нередко бывает, что многие фирмы могут
обнаружить в своих списках одинаковые комплектующие под разными номерами, что делает очень трудным осмысленное ведение записей. Более того, многие фирмы наталкиваются на сопротивление производственных мастеров и других сотрудников, которые приводят следующий аргумент: «Мы 30 лет работали без этого, так зачем же нам лишние хлопоты?»
Эти препятствия могут привести к тому, что внедрение системы MRP займет не один год, при этом следует учесть затраты на теоретическое и практическое обучение сотрудников, убеждение и корректировку ошибок и неточностей отчетности.
В целом, введение системы MRP приводит к большому прогрессу в области планирования и управления запасами, но это не панацея от всех бед. Соответственно, производители начинают применять более широкий подход к планированию ресурсов. Одним из таких подходов является MRP-2.
MRP-2
В
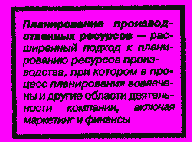
Слишком часто производство, маркетинг и финансы функционируют без полной информации о работе других подразделений фирмы и без контактов с ними. Для наибольшей эффективности необходимо, чтобы все подразделения фирмы сосредоточились на ряде общих задач. Основной задачей MRP-2 является объединение в процессе планирования приоритетных и других функций, таких как кадры, техническое обслуживание и служба закупок,
MRP является ядром процесса (см. рис. 13-19) Процесс начинается со сбора данных по требованиям из всех источников (например, заказы фирмы, прогнозы, требования по поддержанию резервного запаса). Сотрудники производственного и финансового отделов и отдела по маркетингу совместно работают над созданием контрольного графика производственного процесса. Хотя производственники вносят основной вклад в разработку производственного графика и несут основную ответственность за его выполнение, однако службы маркетинга и финансов также вносят свою лепту и имеют свои обязанности. Основание для объединения усилий всех функциональных сфер — увеличение вероятности создания действительно работающего плана. Более того, поскольку каждая из этих функциональных сфер участвует в создании такого плана, они будут иметь лучшее представление о нем и больший стимул для его выполнения.
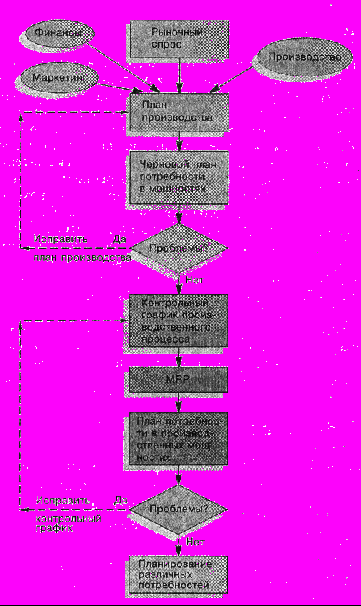
Рис. 13-19. Обзор MRP-2
Помимо чисто производственных ресурсов, необходимых для материального обеспечения плана, необходимы и финансовые ресурсы, которые также следует планировать, и в количественном отношении и во времени. Подобным же образом, маркетинговые ресурсы также в различной степени нужны на протяжении всего процесса Для того чтобы план работал, все необходимые ресурсы должны быть готовы в нужный момент. Зачастую первоначальный план пересматривается на основе оценки доступности различных ресурсов Как только эти ресурсы определены, основной график производственного процесса может быть утвержден.
С этого момента вступает в действие MRP, определяя материальные и временные требования производства. Затем должно быть проведено более детальное планирование требований по объему, чтобы определить, удовлетворяет ли план более специфическим требованиям конкретных производственных мощностей. После этого могут еще раз потребоваться изменения в контрольном графике производственного процесса.
Когда график развертывается и начинается реальная работа, различные формы отчетов помогут менеджерам контролировать процесс и вносить необходимые изменения в производственный график.
На самом деле, все это непрерывный процесс, где основной график производственного процесса обновляется и пересматривается по мере необходимости, для достижения общих производственных целей. Бизнес-план, который управляет ходом всего процесса, обычно тоже подвергается изменениям, хотя они случаются реже, чем изменения на нижних уровнях (т.е. в контрольном графике производственного процесса).
Наконец, следует отметить, что большинство систем MRP-2 имеют функцию моделирования, что позволяет менеджерам отвечать на различные вопросы типа «а что, если», так что они могут лучше оценить возможные вариативные решения и их последствия.
Заключение
Планирование материальных потребностей производства (MRP)—информационная система, которую используют для управления поставками по предметам зависимого спроса (т.е. компонентам сборочной продукции). Процесс планирования начинается с рассмотрения заказов потребителя,—совместно с другими планами они используются для разработки контрольного графика производственного процесса, который показывает сроки изготовления и количество конечной продукции. Конечная продукция разбивается на простейшие элементы с использованием списка материалов, и разрабатывается план материально-производственных потребностей, который показывает необходимое количество и график поставки или производства компонентов.
Основными элементами MRP являются: синхронизация производственных потребностей по времени, расчет требований по компонентам и планы выпуска. Для успешного функционирования MRP требуется соответственная компьютерная программа, точные контрольные графики производственного процесса, списки материалов и данные по наличным запасам. Компании, которые не имеют достаточно точных баз данных или производственных графиков, испытывают значительные трудности при попытке внедрения MRP.
MRP-2—это подход к планированию следующего поколения, который включает MRP, но охватывает более широкую сферу планирования производственных ресурсов, так как он связывает между собой бизнес-планирование, планирование производства и разработку контрольного графика производственного процесса.
Ключевые термины
Дерево структуры продукта product structure tree
Зависимый спрос dependent demand
Заказ-релизы planned-order releases
Защитные временные интервалы time fences
Изменения changes
Кодирование по нижнему уровню low-level coding
Контрольный график производственного процесса master schedule
Общее время производства cumulative lead time
Общие производственные потребности gross requirements
Определение размера партии lot sizing
Отчеты об исключительных ситуациях exception reports
Отчеты по контролю исполнения perfomance-control reports
Отчеты по отгрузкеload reports
Отчеты по планированию planning reports
Осуществление заказа order releases
Пеггинг (определение родительских элементов) pegging
Планирование материальных требований material requirements planning
Планирование производственных ресурсов manufacturing resources planning (MRP-2) (MRP-2)
Планирование требований по объему capacity requirements planning
планируемые наличные запасы projected on hand
Плановые заказы planned orders
Плановые поступления planned-order receipts
Поставки по графику scheduled receipts
Регенеративная система regenerative system
Система чистых изменений net-change system
Список материалов bill of materials (BOM)
Файл инвентарных записей inventory records file
Чистая производственная потребность net requirements
Решение задач
Задача 1
Приведенное ниже дерево структуры изделия показывает компоненты, необходимые для сборки одной единицы продукта W. Перерисуйте дерево таким образом, чтобы оно соответствовало нижнеуровневому кодированию. Затем определите количество каждого компонента, необходимого для сборки 100 единиц W.
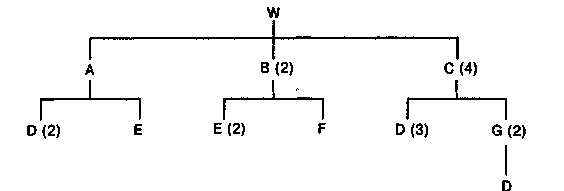
Решение:
Самый простой способ рассчитать требования по компонентам—сделать это прямо на дереве структуры, как показано на нижнем рисунке. Если использовать кодирование по нижнему уровню, то относительно просто сгруппировать одинаковые элементы для определения полных требований.
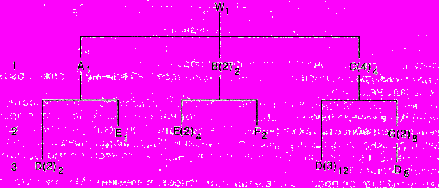
Итого:
Уровень | Предмет | (1W) Количество | (100W) Количество |
0 | W | 1 | 100 |
1 | А | 1 | 100 |
| B | 2 | 200 |
| C | 4 | 400 |
2 | Е | 5 | 500 |
| F | 2 | 200 |
| G | 8 | 800 |
3 | D | 22 | 2200 |
Задача 2
Ниже представлено дерево структуры изделия Е. Менеджер хочет знать материальные требования для поставляемых частей R, которые понадобятся для комплектации 120 единиц Е на начало недели 5. Время производства: 1 неделя для элементов уровня 0, 1 неделя для элементов уровня 1, и 2 недели для элементов уровня 2. Ожидается плановое получение 60 единиц М к концу недели 1 и 100 единиц R к началу недели 1. Способ поставки — непрерывный.
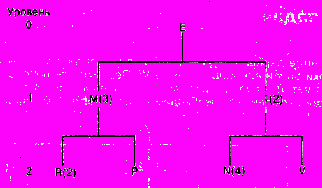
Решение: