Планирование материальных потребностей производства (material requirements planning mrp) Цели изучения: Завершив изучение данной главы, вы должны уметь Описать условия,
Вид материала | Решение |
- Планирование продаж планирование производства формирование графика выпуска продукции, 382.65kb.
- Планирование и контроль за всем циклом производства с возможностью влияния на него, 1206.53kb.
- Задачи изучения дисциплины Врезультате изучения данной дисциплины студенты должны, 107.67kb.
- Пояснительная записка врезультате изучения данных тем курса математики учащиеся должны, 237.64kb.
- История развития стандарта управления промышленным предприятием mrp, 399.66kb.
- Электронное научное издание «Труды мэли: электронный журнал», 129.87kb.
- Планирование на предприятии, 524.23kb.
- Задачи изучения дисциплины Реализация поставленной цели требует решение следующих задач:, 36.83kb.
- Московский Государственный Горный Университет утверждаю председатель умк по направлению, 54.53kb.
- «Место и роль картины в искусстве XX века», 157.29kb.
Комментарий. Студентов часто озадачивает один вопрос, связанный с концепцией кодирования по нижнему уровню: Что происходит, если компонент, который появляется на различных уровнях, «зарыт» на высшем уровне и не может быть опущен? Ответ на этот вопрос состоит из двух частей. Первая: кодирование по нижнему уровню не сводится к элементам на концах ветвей; см. рис. 13-8.
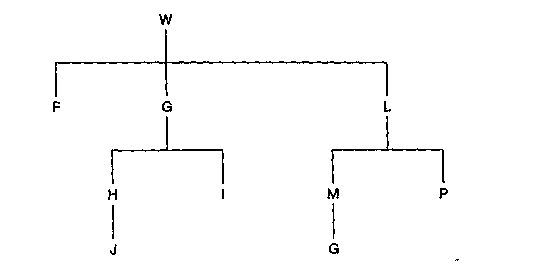
Рис. 13-8. Один компонент G «зарыт» на высшем уровне, что вроде бы мешает
кодированию по нижнему уровню
Родитель G и его компоненты (и подкомпоненты, если необходимо) могут быть все пущены, если это необходимо, для достижения совпадения с нижним уровнем. Вторая часть ответа базируется на том факте, что родитель G должен иметь одинаковые компоненты везде, где бы он не появлялся в структуре продукта. Другими словами, компоненты Н и 1 всегда необходимы для сборки одного элемента G. Если, по какой-либо причине, имеются исключения, то такому элементу G надо дать другое имя. Каждое имя представляет собой уникальный набор необходимых компонентов, независимо от того, где данный элемент появляется в структуре продукта.
Чрезвычайно важно, чтобы список материалов точно отражал состав продукта, так как ошибки на одном уровне разрастаются из-за умножений при определении количественных требований. Это, казалось бы, очевидно, — однако у многих компаний все же оказываются неверные данные по СМ. Это делает совершенно невозможным эффективное определение материальных потребностей производства; более того, корректировка этих записей может быть очень сложной и занять много времени. Но как бы то ни было, точность записей — основа для эффективного MRP.
Файл данных по материально-производственным запасам
Ф
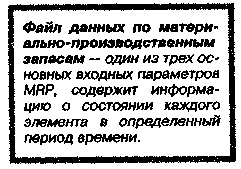
Так же как и список материалов, файл данных по материально-производственным запасам должен быть очень точен. Ошибочная информация о требованиях или времени производства может оказаться пагубной для MRP и создать хаос, когда образуется неправильный объем наличных запасов или не выполняются сроки поставки.
Функционирование MRP
MRP обрабатывает требования по конечному продукту, уточненные контрольным графиком, и «перестраивает» их в синхронизированные по времени требования по сборочным узлам, деталям и сырью, используя список материалов для смещения по времени производства. Временная синхронизация производственных потребностей отчетлива видна на диаграмме сроков сборочного процесса (рис. 13-9). Например, сырьевые материалы D, F и I должны быть заказаны в начале 2-ой недели, деталь С — в начале 4-ой недели, а деталь Н -— в начале 5-ой недели, чтобы обеспечить производство в соответствии с планом.
Количества, которые получаются из переработки списка материалов, называются общей (валовой) потребностью; они не принимают в расчет имеющихся наличных запасов или заказов в процессе исполнения. Материалы, которые в действительности нужно получить для соответствия количеству, указанному в контрольном графике, называются чистыми материально-производственными потребностями (net requirements) .
Определение чистых материальных потребностей (неттинг — netting) составляет ядро MRP. Оно выполняется путем вычитания из величины общей потребности суммы наличных запасов и запланированных поставок по графику, а затем к полученному результату прибавляются требования по резервному запасу, если они необходимы:

(Для упрощения расчетов, резервные запасы опускаются в примерах и задачах.) Чистые требования иногда корректируются, чтобы включить допуск на непроизводительные траты и материальные потери, хотя Для упрощения расчетов это не включается в большинство задач и примеров.
Распределение поставок по времени и размерам (т.е. заказ материалов у поставщиков или их производство в рамках компании) определяется по заказ-релизам. График получения заказанных материалов определяется плановыми заказами. В зависимости от политики компании в сфере заказов, заказ-релизы могут выпускаться по общему количеству материала (например, 50 единиц), или же по количеству на определенное время. Хотя возможны и другие варианты, эти два применяются наиболее широко. Пример 2 иллюстрирует различие между этими двумя стратегиями заказов, а также основные концепции синхронизации материальных потребностей по времени в системе MRP. При рассмотрении примера вам могут помочь следующие термины:
Общие требования (Gross requirements): Общая предполагаемая потребность в деталях или сырье на каждый период времени, без учета наличных запасов. Для конечного продукта это количество отображено в контрольном графике производственного процесса; для компонентов это количество эквивалентно заказ-релизам их непосредственных родителей
Поступления по графику (Scheduled receipts): Открытые заказы, запланированные для поступления от поставщиков или из других источников к началу определенного периода.
Планируемые наличные запасы (Projected on hand) : Ожидаемый размер запасов, которые должны быть в наличии к началу каждого периода: поступления по графику плюс оставшиеся запасы с прошлого периода.
Чистые потребности (Net requirements) : Действительное количество материала, необходимое на каждый период времени.
Плановые поступления (Planned-order receipts): Количество, ожидаемое для поступления на начало периода, в котором оно показано При непрерывной организации поставок это количество будет эквивалентно чистым требованиям. При поставках партиями это количество может превосходить чистые требования. Любой излишек прибавляется к наличным запасам на следующий период времени.
Заказ-релизы (Planned-order releases): Показывают планируемое количество заказов на каждый период времени; эквивалентно общему количеству плановых поступлений, с учетом времени производства. Это количество определяет общие требования производства на следующем уровне производственного или сборочного процесса. Когда заказ выполнен, он удаляется из заказ-релиза и переходит в раздел поступлений по графику
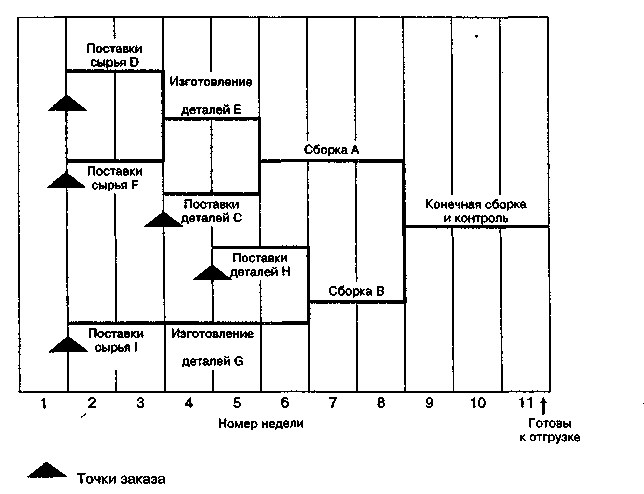
Рис. 13-9. Временная диаграмма сборочного процесса, показывающая сроки заказов, необходимые для обеспечения планового выпуска готовой продукции
Эти количества используются в синхронизированном плане следующего формата:
№ недели | 1 | 2 | 3 | 4 | 5 | 6 | 7 | 8 |
| | | | | | | | |
Материал: | | | | | | | | |
Общие потребности пр-ва | | | | | | | | |
Поступления по графику | | | | | | | | |
Планируемые наличные запасы | | | | | | | | |
Чистые потребности пр-ва | | | | | | | | |
Плановые поступления | | | | | | | | |
Заказ-релизы | | | | | | | | |
ПРИМЕР 2
Предприятие, которое производит деревянные ставни и книжные полки, получило два заказа на ставни: один на 100 шт и другой на 150 шт. Заказ на 100 единиц должен быть выполнен на начало 4-ой недели текущего графика и заказ на 150 единиц — на начало 8-ой недели. Каждый ставень состоит из 4-х сборных деревянных секций и двух рам. Деревянные секции изготавливаются на предприятии, и их производство занимает одну неделю. А рамы заказываются, и время их доставки — 2 недели. Сборка ставней требует одну неделю. В первую неделю (т.е. на начало недели) получение по графику составляет 70 деревянных секций Определите размер и временные интервалы заказ-релизов, необходимых для удовлетворения требований по отгрузке готовой продукции при каждом из приведенных условий:
- Непрерывная организация поставок (т.е размер заказа эквивалентен чистой производственной потребности).
- Поставки партиями с размером партии 320 единиц для рам и 70 единиц для деревянных секций.
Решение:
а) Разрабатываем контрольный график производственного процесса:
№ недели | 1 | 2 | 3 | 4 | 5 | 6 | 7 | 8 |
Количество | | | | 100 | | | | 150 |
б
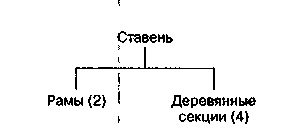
) Разрабатываем дерево структуры продукта:
в) Используя контрольный график, определяем общую производственную потребность в ставнях. Затем вычисляем частую потребность. При непрерывной организации поставок, определим величину запланированных поступлений и временные интервалы поставок для соответствия контрольному графику производственного процесса (см. рис. 13-10).
Так как контрольный график требует, чтобы 100 ставней были готовы к отгрузке, и не планирует наличный запас ставней на начало 4-ой недели, то чистые потребности составляют также 100 ставней. Следовательно, плановые поступления для недели 4 равны 100 ставням. Так как на сборку ставня требуется одна неделя, то это значит, что заказ-релиз должен быть в начале недели 3. Следуя той же логике рассуждений, 150 ставней должны быть собраны в течение недели 7, для того чтобы начать их отгрузку в начале недели 8.
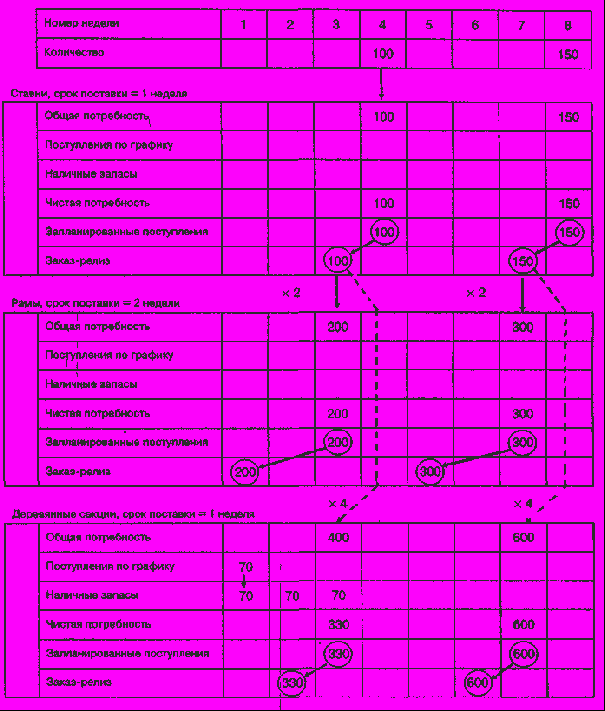
Рис. 13-10. MRP график при непрерывном виде поставок
Заказ-релиз на 100 ставней в начале недели 3 означает, что 200 рам (общая потребность) должны быть готовы к этому сроку. Поскольку их наличный запас не предполагается, то чистая потребность составляет 200 рам, поэтому необходимо плановое получение 200 рам к началу недели 3. С учетом двухнедельного срока поставки, это означает, что 200 рам должны быть заказаны в начале недели 1. Подобным же образом, заказ-релиз на 150 ставней на неделе 7 вызывает общую производственную потребность и чистую потребность, равные 300 рамам для недели 7, и их плановое получение к этому сроку. Двухнедельный срок поставки означает, что рамы должны быть заказаны в начале недели 5
Кроме того, заказ-релиз на 100 ставней к началу недели 3 вызывает общую производственную потребность в 400 деревянных секций на это же время Однако предполагается иметь в наличном запасе 70 деревянных секций, поэтому чистая производственная потребность составит 400 - 70 = 330. Это означает плановое получение 330 деревянных секций к началу недели 3. Так как время производства составляет одну неделю, производственный процесс должен начаться в начале недели 2.
Аналогично, заказ-релиз на 150 ставней на неделе 7 вызывает общую производственную потребность на этот срок, равную 600 деревянным секциям. Так как не предполагается иметь наличные запасы деревянных секций, то чистая потребность также составляет 600, и плановое получение составляет 600 единиц. Срок изготовления равен одной неделе — это означает, что в начале недели 6 по графику запланирован выпуск 600 секций.
г) При поставке партиями, единственное отличие заключается в том, что плановые получения, возможно, превысят чистую производственную потребность. Излишек записывается как плановый наличный запас на последующий период времени. Например, на рис. 13-11, заказ на рамы составляет 320 единиц. Чистая производственная потребность для недели 3 составляет 200 единиц; таким образом, образуется излишек, равный 320 - 200 = 120 единиц, которые становятся плановым наличным запасом на следующую неделю. Аналогично, чистая производственная потребность в рамах составляет 180 единиц, что на 140 единиц меньше, чем размер заказа (320 единиц); снова излишек становится плановым наличным запасом на неделю 9. То же самое происходит и с деревянными секциями: излишек плановых поступлений на неделях 3 и 7 добавляется к наличному запасу на недели 4 и 8 соответственно. Заметьте, что размер заказа должен быть кратен размеру партии; для недели 3 это 5 70 и для недели 7 - 9 70.
Другая сторона процесса определения материальных потребностей производства для сборочных компонентов дается на рис. 13-12.
Пример 2 полезен для описания некоторых важных особенностей процесса MRP, но в нем несколько преуменьшена огромность задачи по отслеживанию материальных потребностей производства, особенно в тех случаях, когда одни и те же узлы, детали и сырье используются для изготовления разных изделий. Различия во времени требований и в необходимых количествах, пересмотры, вызванные задержкой поставок, большое количество лома и боя, и отмененные заказы — все это влияет на процесс MRP.
Рассмотрим, например, элемент G, который используется для производства конечного продукта W, X и Y, как это показано на деревьях структуры на рис. 13-13. Для простоты предположим, что все сроки производства для этих продуктов составляют одну неделю. Контрольный график производственного процесса для этих продуктов показан на рис. 13-14. Заметьте, что здесь представлены общие потребности для производства данных конечных продуктов: чистая будет меньше на величину наличного запаса. Это же положение действительно для чистых потребностей по подузлам N, М и Н. Каждый из этих факторов следует принимать во внимание при расчете чистой производственной потребности для G ._Общая потребность для G выглядит примерно так же, как на графике на рис. 13-15; при этом чистая производственная потребность для G равна сумме этих величин, за вычетом наличного запаса G, который также показан на рис. 13-15. (Примечание: наличные запасы конечного продукта не приводятся, как не приводятся они и для родителей N, М и Н. Однако дело не в вычислениях, а в том, что общая производственная потребность для элемента G определяется чистыми потребностями для производства всех его родителей. Смотри нижнюю часть рис. 13-15.)
Термин пеггинг (pegging — «протыкание») обозначает работу этого процесса наоборот; то есть определение родительских элементов, которые вызвали данный ряд материальных требований для некоторого элемента—такого как G. Хотя такой процесс может показаться довольно простым, с учетом использования структурных деревьев и графиков, — на самом деле, когда эта информация компьютеризуется, нужно приложить особые усилия для отслеживания потребностей конкретных родителей.
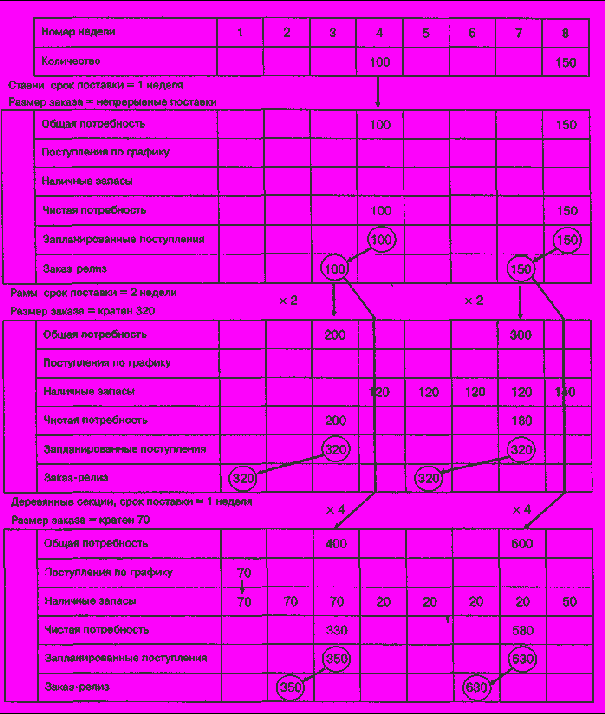
Рис. 13-11. MRP график при поставках компонент партиями
Важность компьютера становится очевидной, когда вы примете во внимание тот факт, что обычное предприятие выпускает не один, но множество видов продукции, для которых необходимо разрабатывать планы материально-производственных потребностей, причем каждый план со своим набором компонентов. Наличные запасы и заказы, графики, заказ-релизы и т.д , —все должно систематически пересматриваться и обновляться. Без помощи компьютера эта задача была бы практически безнадежной, с компьютером же, все это можно исполнить с гораздо меньшими трудностями.
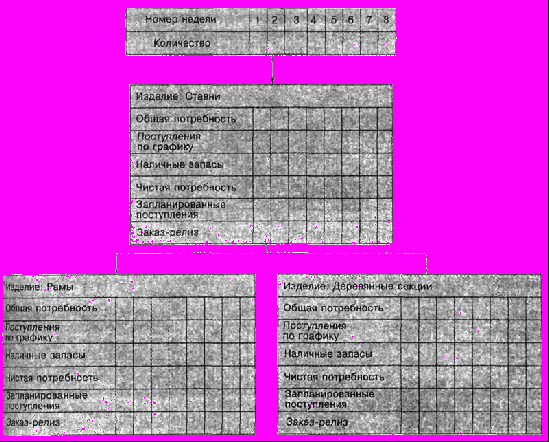
Рис. 13-12. Чистые требования на каждом уровне определяют валовые
требования на следующем
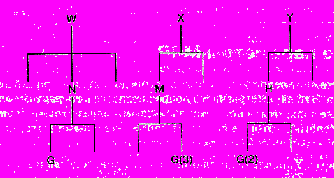
Рис. 13-13. Элемент G используется в производстве трех различных продуктов