Введение в логистику
Вид материала | Реферат |
СодержаниеРис. 1 Блок-схема системы MRP1 Рис. 2 MRP1 как система «толкающего типа» Цены товарных бирж |
- 1. введение в логистику, 531.6kb.
- Тренинга, 62.37kb.
- В россии строятся складские терминалы или единичные логистические центры, которые, 104.2kb.
- Джон Р. Хикс. "Стоимость и капитал", 4314.44kb.
- Введение глава психологизм как особенность характерологии в рассказах Всеволода Иванова, 12.47kb.
- Лабунец Ольга Юрьевна мытищи 2009 г. Оглавление Введение 3 Использование видеофильмов, 263.17kb.
- Анализ и планирование трудовых показателей Аудит и контроллинг персонала Введение, 12.45kb.
- Программа курса. План семинарских занятий Методические рекомендации Новосибирск 1999, 340.75kb.
- Учебной дисциплины (модуля) Наименование дисциплины (модуля) Введение в спецфилологию:, 83.08kb.
- 1. Целеполагание в процессе менеджмента Введение, 49.78kb.
3.1. Понятие производственной логистики
Материальный поток на своем пути от первичного источника сырья до конечного потребителя проходит ряд производственных звеньев. Управление материальным потоком на этом этапе имеет свою специфику и носит название производственной логистики.
Задачи производственной логистики касаются управления материальными потоками внутри предприятий, создающих материальные блага или оказывающих такие материальные услуги, как хранение, фасовка, развеска, укладка и другие. Характерная черта объектов изучения в производственной логистике – их территориальная компактность.
Участников логистического процесса в рамках производственной логистики связывают внутрипроизводственные отношения. Такие системы носят название внутрипроизводственных логистических систем. К ним можно отнести: промышленное предприятие; оптовое предприятие, имеющее складские сооружения; узловую грузовую станцию; узловой морской порт и другие.
Внутрипроизводственные логистические системы можно рассматривать на макро- и микроуровнях.
На макроуровне внутрипроизводственные логистические системы выступают в качестве элементов макрологистических систем. Они задают ритм работы этих систем, являются источниками материальных потоков. Возможность адаптации макрологистических систем к изменениям окружающей среды в существенной степени определяется способностью входящих в них внутрипроизводственных логистических систем быстро менять качественный и количественный состав выходного материального потока, т.е. ассортимент и количество выпускаемой продукции.
На микроуровне внутрипроизводственные логистические системы представляют собой ряд подсистем, находящихся в отношениях и связях друг с другом, образующих определенную целостность, единство. Эти подсистемы: закупка, склады, запасы, обслуживание производства, транспорт, информация, сбыт и кадры обеспечивают вхождение материального потока в систему, прохождение внутрь нее и выход из системы. В соответствии с концепцией логистики построение внутрипроизводственных логистических систем должно обеспечивать возможность постоянного согласования и взаимной корректировки планов и действий снабженческих, производственных и сбытовых звеньев внутри предприятия.
Управление материальными потоками в рамках внутрипроизводственных логистических систем может осуществляться различными способами, из которых выделяют два основных: толкающий (“Materials Requirements Planning” - «планирование потребностей в материалах») и тянущий (концепция «just-in-time» - JIT («точно в срок»)), принципиально отличающиеся друг от друга.
3.2. Микрологистическая система MRP
Одной из наиболее популярных в мире логистических концепций, на основе которой разработано и функционирует большое число микро-ЛС, является концепция “Materials Requirements Planning” («планирование потребностей в материалах»).
Практические приложения, типичных для MRP систем, имеются в организации производственно-технологических процессов совместно с закупками материальных ресурсов.
MRP системы оперируют с материалами, компонентами, полуфабрикатами и их частями, спрос на которые зависит от спроса на специфическую готовую продукцию. Логистическая концепция, заложенная в основу MRP системы, сформулирована в середине 50-х годов, но только с появлением быстродействующих компьютеров, в 80-х годов ее удалось реализовать на практике в США.
Эта система располагает широким набором масштабных программ, которые обеспечивают согласование и оперативное регулирование снабженческих, производственных и сбытовых функций в режиме реального времени. Блок-схема системы имеет вид:
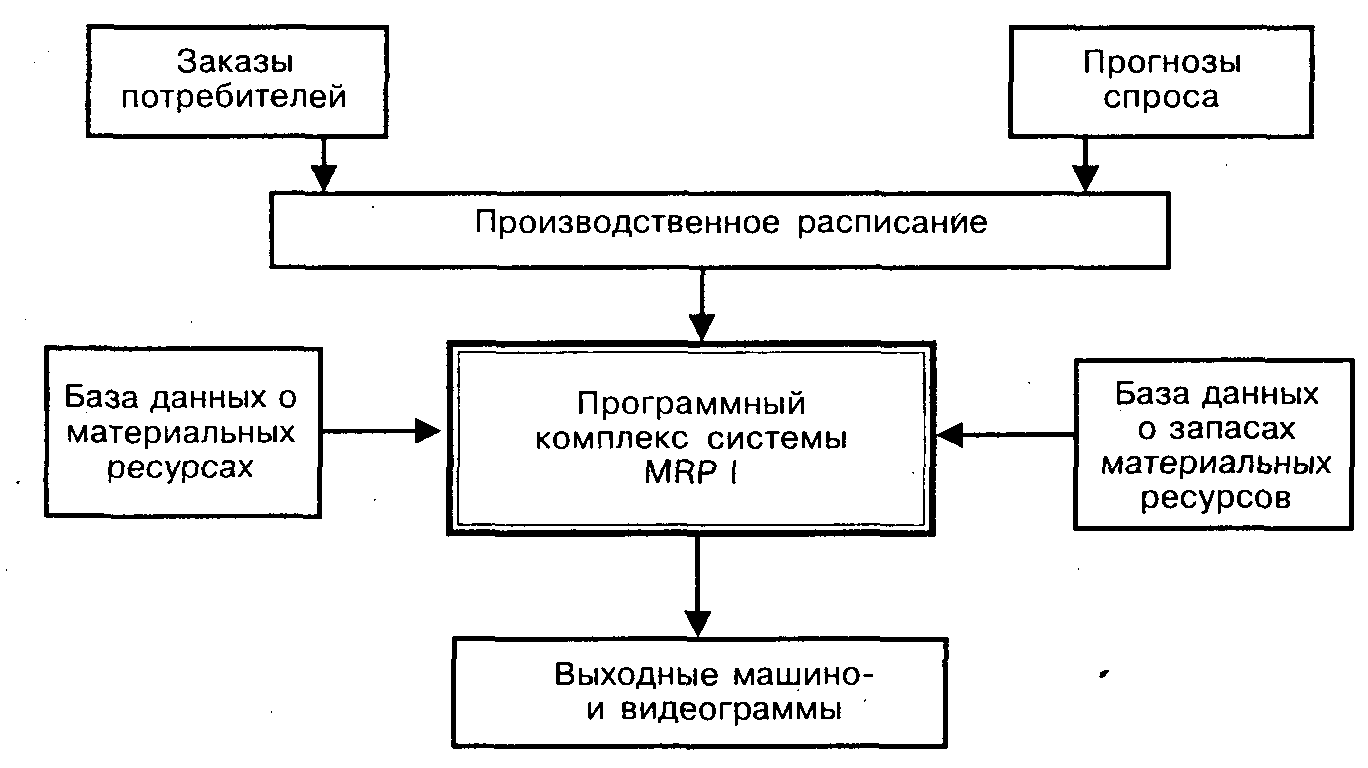
Рис. 1 Блок-схема системы MRP1
Входом MRP1 системы являются заказы потребителей, подкрепленные прогнозами спроса на готовую продукцию фирмы, которые заложены в производственное расписание (график выпуска ГП). Таким образом, в MRP1 ключевым фактором является потребительский спрос.
База данных о МР содержит всю требуемую информацию о номенклатуре и основных параметрах сырья, компонентов, полуфабрикатов и т.п. необходимых для производства (сборки) ГП или ее частей. Кроме того, в ней содержатся нормы расхода МР на единицу выпускаемой продукции, а также файлы моментов времени соответствующих МР на производственные подразделения фирмы.
База данных о запасах информирует систему и управляющий персонал о наличии и величине производственных, страховых и других требуемых запасов МР в складском хозяйстве фирмы, а также о близости их к критическим уровням с точки зрения необходимости их пополнения. Кроме того, в этой базе содержатся сведения о поставщиках и параметрах поставки МР.
Формализация процессов принятия решений в системе MRP1 производится с помощью различных методов и алгоритмов теории исследований операций в зависимости от потребительского спроса и комплексной информации, получаемой из базы данных о МР и их запасах. На основании математических моделей, программные модули системы, первоначально анализируют спрос на ГП, и далее определяют общий объем и ассортимент МР, для удовлетворения спроса. Затем программы вычисляют цепь требований на исходные МР, полуфабрикаты, НП, основанную на информации о соответствующих уровнях запасов, и размещают заказы на объемы входных МР для участков производства ГП. Заказы зависят от специфицированных по номенклатуре и объемах требований в МР и времени их доставки на соответствующие рабочие места и склады.
После завершения всех необходимых вычислений в информационно-компьютерном центре фирмы формируется выходной комплекс машинограмм системы MRP1, который в документном виде передается персоналу производственного и логистического менеджмента для принятия решений по организации обеспечения производственных участков и складского хозяйства фирмы необходимыми МР. Типичный набор выходных документов системы MRP1 содержит:
- заказ МР от поставщика;
- изменения, которые необходимо внести в производственное расписание;
- схемы доставки МР, объемы поставок и т.п.;
- аннулированные требования на ГП, МР;
- состояние MRP1 системы.
Для микрологистической системы «толкающего» типа характерно производство деталей, компонентов, полуфабрикатов и сборки из них ГП в соответствии с жестко заданным производственным расписанием. В результате МР, НП как бы «выталкиваются» с одного звена внутрипроизводственных ЛС на другое, а затем ГП дистрибутивная сеть (рис. 2).
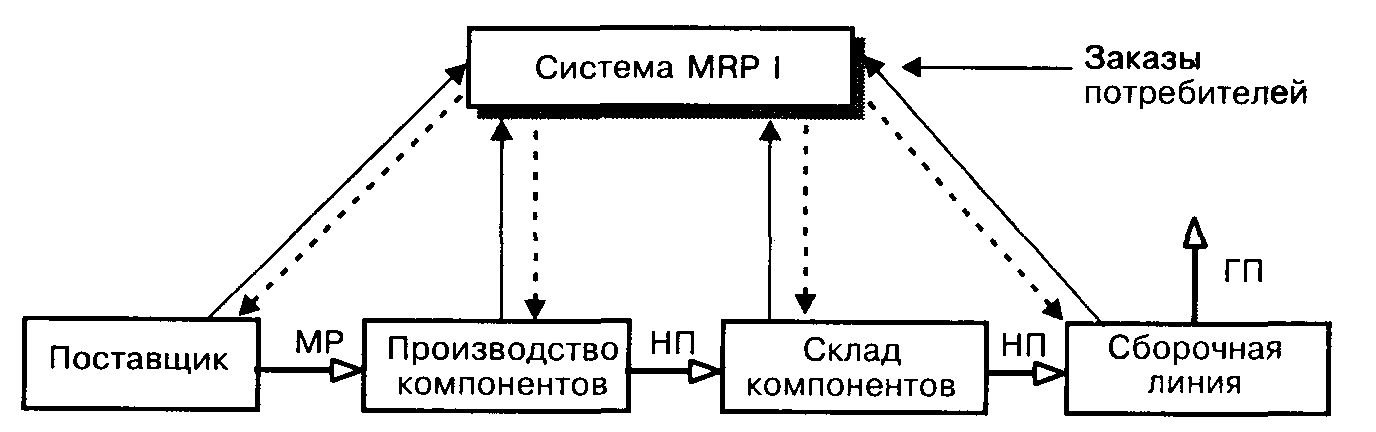
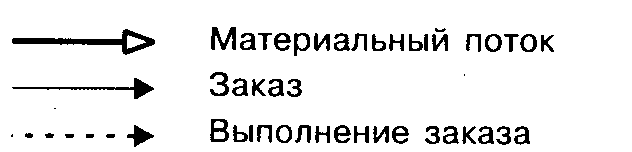
Рис. 2 MRP1 как система «толкающего типа»
В такой системе предотвратить сбой в производственном процессе сложно, а также учесть изменение спроса можно только путем создания избыточных производственных и (или) страховых запасов между ЗЛС, которые называются обычно буферными запасами. Наличие таких запасов замедляет оборачиваемость оборотных средств фирмы, увеличивает себестоимость производства ГП, но обеспечивает большую устойчивость ЛС при резких колебаниях спроса и ненадежности поставщиков МР по сравнению с ЛС.
3.3. Логистическая концепция «just-in-time»
Наиболее широко распространенной в мире микрологистической концепцией является концепция «just-in-time» - JIT («точно в срок»).
Появление этой концепции относится к концу 50-х годов, когда японская компания “Toyota Motors”, а затем и другие автомобилестроительные фирмы Японии начали активно внедрять микрологистические системы KANBAN. Название «just-in-time» концепции несколько позже дали американцы, попытавшиеся также использовать этот подход в автомобилестроении. Первоначальным лозунгом концепции JIT было потенциальное исключение запасов материалов, компонентов и полуфабрикатов в производственном процессе сборки автомобилей и их основных агрегатов. Исходной постановкой было то, что, если производственное расписание задано, то можно так организовать движение материальных потоков, что все материалы, компоненты и полуфабрикаты будут поступать в нужное место (на сборочное место - конвейер) и точно к назначенному сроку для производства или сборки ГП. При такой постановке страховые запасы, имобилизирующие (обездвиживающие) денежные средства фирмы, оказывались не нужны.
С логистической позиции JIT – это довольно простая бинарная логика управления запасами без какого-либо ограничения к требованию минимума запасов. Главным моментом в JIT концепции является то, что потоки МР должны быть тщательно синхронизированы с потребностью в них, задаваемой производственным расписанием выпуска ГП. Подобная синхронизация есть не что иное как координация двух базисных логистических активностей: снабжения и производственного менеджмента. В дальнейшем идеология JIT была успешно продвинута в дистрибьюцию, системы сбыта ГП, а в настоящее время и в макрологистические системы.
Учитывая широкую экспансию JIT подхода в различных сферах современного бизнеса, можно дать следующие определения: «JIT – это современная концепция построения ЛС в производстве (операционном менеджменте), снабжении и дистрибьюции, основанная на синхронизации процессов доставки МР, НП, ГП в необходимых количествах, к тому времени, когда ЗЛС в них нуждаются, с целью минимизации затрат, связанных с запасами».
В идеальном случае МР, НП, ГП должны быть доставлены в определенную точку логистической цепи (канала) именно в тот момент, когда в них есть потребность (не раньше, не позже), что исключает излишние запасы, как в производстве, так и в дистрибьюции. Многие современные ЛС, основанные на JIT подходе, ориентированы на снижение времени логистических циклов, что требует быстрой реакции ЗЛС на изменение спроса и, соответственно производственной программы.
Логистическая концепция JIT характеризуется следующими основными чертами:
- минимальными (нулевыми) запасами МР, НП, ГП;
- короткими логистическими (производственными) циклами;
- небольшими объемами производства ГП и пополнения запасов (поставок);
- подбором надежных поставщиков и перевозчиков;
- эффективной информационной поддержкой;
- высоким качеством ГП и логистичекого сервиса.
Внедрение концепции JIT в мире привело к изменению традиционного подхода производственного менеджмента к управлению запасами. Работу в таких логистических системах можно представить как двухбункерную систему управления запасами, так как запас хранится как бы в двух складах-бункерах. Вначале один бункер в этой системе используется для удовлетворения спроса в производстве или сбыте, соответственно, МР и ГП. Окончание запасов в этом бункере является точкой заказа. В этот момент для снабжения потребителя открывается второй бункер, одновременно поставщику направляется заказ. В момент прибытия заказанных МР, ГП во втором бункере должен оставаться не ниже страхового. При распределении поступившего заказа вначале полностью заполняется второй бункер. Оставшееся количество используется для заполнения первого.
Фирма “Toyota Motors” добилась выдающихся результатов, применяя концепцию JIT, которая позволила ей в 60-х годах сократить ведущее время основного логистического цикла поставки новых автомобилей до одного месяца, тогда как ведущие американские автомобилестроительные фирмы имели цикл от 6 до 9 месяцев.
Производство ГП небольшими партиями за относительно короткие производственные циклы сокращают, связанные с ними циклы снабжения МР от поставщиков.
ЛС, использующие JIT идеологию, являются тянущими системами, в которых размещение заказов на пополнение запасов МР или ГП происходит только тогда, когда их количество в определенных ЗЛС достигает критического уровня. При этом запасы «вытягиваются» по каналам физического распределения от поставщика МР в систему дистрибьюции. Принципиальная схема работы ЛС, использующая JIT концепцию:
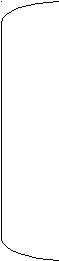
-
Система управления
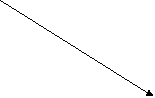
команда на изготовление ы
десяти единиц продукции н
о
к


























ы
т
заказ на материал заказ на 10 загот. заказ на 10 деталей а



Рис. 3
Согласно рис. 3 предприятие получило заказ на 10 единиц ГП. Этот заказ система управления передает в цех сборки. Цех сборки для выполнения заказа, запрашивают 10 деталей из цеха №1. Передав из своего запаса 10 деталей, цех №1 с целью восполнения запаса заказывает у цеха №2 10 заготовок. В сою очередь, цех №2 , передав 10 заготовок, заказывает на складе сырья материалы для изготовления переданного количества, также с целью восполнения запаса. При чем персонал отдельного цеха в состоянии учесть гораздо больше специфических факторов, определяющих размер оптимального заказа, чем это смогла бы сделать центральная система управления.
Короткие составляющие логистических циклов в JIT системах способствуют концентрации поставщиков МР вблизи главной фирмы, осуществляющей процесс производства или сборки ГП. Фирма старается выбрать небольшое количество поставщиков, отличающихся высокой степенью надежности поставок, так как любой сбой в поставках может нарушить производственное расписание. О том, насколько важна надежность поставщиков, говорит тот факт, что американские и европейские производители смогли внедрить концепцию JIT только через 10-15 лет после японцев из-за низкой надежности поставщиков. В концепции JIT поставщики становятся по существу партнерами производителей ГП в их бизнесе.
В практической реализации концепции JIT ключевую роль играет качество. Японские автомобилестроительные фирмы, первоначально внедряя концепцию JIT и микрологистическую систему KANBAN в производство, принципиально изменили подход к контролю и управлению качеством на всех стадиях производственного процесса и последующего сервиса.
Для эффективной реализации JIT технологии должны работать с надежными телекоммуникационными системами и информационно-компьютерной поддержкой.
4. Управление закупками
4.1. Цель и задачи логистического менеджмента закупок
Обеспечение фирмы-производителя необходимыми видами МР за рубежом получило название управление закупками, а в нашей стране – закупочная логистика.
Основной целью логистического менеджмента закупок является надежное качественное обеспечение производственных подразделений фирмы МР, необходимых для выполнения заданного производственного расписания, которое должно быть сформулировано при этом в маркетингово-логистической стратегией фирмы на рынке сбыта ГП, чем достигается интеграция базисных логистических активностей. Однако достижение этой цели может быть выполнено с различными затратами ресурсов, поэтому перед логистическим менеджером возникают проблемы оптимизации, как в цепи «снабжение - производство», так и в полной логистической цепи «снабжение – производство - сбыт».
В любой зарубежной фирме-товаропроизводителе существует типичный набор логистических активностей, связанных с управлением закупками, характеристика которых представлена в таблице 3.
При решении задач логистического менеджмента закупок (ЛМЗ) главное внимание должно быть уделено сокращению общих затрат, связанных с этой ключевой активностью, так как затраты на управление закупками по различным отраслям составляют от 40 до 60 % в структуре себестоимости производства ГП. Наибольший удельный вес в затратах, связанных с закупками. Занимаю: собственно цена МР, затраты на управление запасами МР (складирование, грузоперевозку, хранение и пр.).
Для сокращения этих составляющих затрат необходима целенаправленная политика фирменного логистического менеджмента, включая комплекс мероприятий, среди которых можно указать:
- совершенствование планирования потребности и нормирование расхода МР для производственных подразделений фирмы;
- устранение потерь от брака (политика «ноль дефектов») в производстве и потерь МР при доставке от поставщиков;
- максимальное сокращение отходов производства и эффективное использование вторичных МР;
- исключение, по возможности, промежуточного складирования МР при доставке их от поставщиков;
- доставка МР от поставщиков как можно большими партиями с максимальным использованием грузовместимости транспортных средств и минимальными тарифами;
- минимизация уровней запасов МР на всех уровнях складской системы фирмы и пр.
Общая стратегия управления закупками МР в фирме складывается из учета приоритетов и взаимодействия в основном финансового, оперативного и логистического менеджмента. На Западе известны основные критерии (показатели), определяющие политику фирмы в этих сферах. В частности, для финансового менеджмента такими критериями являются: минимальные затраты на закупки МР, минимальные потребности в дополнительных инвестициях (например, в складское хозяйство, транспорт), минимальные финансовые риски (связанные с недополучением прибыли, кредитными отношениями и т.п.), максимальная скорость отбора капитала, вложенного в МР и др.
Основными требованиями операционного менеджмента является полное удовлетворение плановых заявок в номенклатуре и объемах поставок МР, синхронизация сроков их доставки с производственным расписанием, качество исходных МР, отсутствие сбоев в поставках, то есть требований надежности закупок и доставки МР в производственные подразделения фирмы.
Задачами логистического менеджмента закупок являются координация и увязка требований финансового, операционного и других видов менеджмента в разрезе общей логистической стратегии фирмы, связанной с управлением материальными потоками. Оптимизационные решения логистического менеджмента при этом традиционно включают минимизацию общих издержек управления закупками и запасами МР, оптимизацию запасами МР, уменьшение логистических рисков (от несоблюдения параметров поставок) и оптимальный выбор поставщиков.
Стратегия закупок МР, базируется на рассмотренных критериях, анализе рынка поставщиков и установленных временных приоритетах. К числу важнейших приоритетов относятся:
- конкурентоспособность (лидерство) поставщиков на конкурентных МР;
- возможность представления ими ценовых скидок при длительных взаимоотношениях;
- соответствие поставок логистической стратегии фирмы;
- максимальное снижение затрат на доставку от поставщиков и хранение МР (близость к производственным подразделениям фирмы, отсутствие промежуточного складирования);
- возможность партнерства в бизнесе и пр.
4.2. Задача выбора поставщика
Одной из основных в менеджменте закупок МР является проблема выбора поставщика. Важность ее объясняется не только тем, что на современном рынке функционирует большое количество поставщиков одинаковых МР, но главным образом тем, что поставщик должен быть надежным партнером товаропроизводителя в реализации его логистической стратегии.
Анализ поставщиков конкретного ассортимента (вида) МР и их последующий выбор должен осуществляться в соответствии с определенным набором критериев. Эти критерии, а также их ранжирование (приоритет) должны устанавливаться высшим менеджером фирмы-производителя, исходя из стратегических и тактических целей бизнеса. К числу важнейших критериев выбора поставщика относятся: качество поставляемых МР и сервиса, возможности (способности) удовлетворить требование фирмы-производителя, расположение (дислокация), сопутствующий сервис и другие.
Среди наиболее важных критериев отбора находится, конечно, качество. Качество поставляемых МР должно удовлетворять производственные подразделения фирмы по спецификации, техническим и конструктивным параметрам, физическим и химическим свойствам и т.д., то есть полностью удовлетворять соответствующих оговоренных заранее стандартов, отраженных, как правило, в сертификатах. Логистические менеджеры фирмы, отвечающие за закупки, должны сравнивать фактические параметры поставляемых МР со стандартными (или оговоренными в договорах на поставку). Это сравнение осуществляется обычно на этапе входного контроля. При оценке качества МР могут дополнительно исследоваться жизненный цикл изделия, ремонтопригодность, требуемая техническая поддержка (сервис), легкость в использовании, сохраняемость и т.п.
Надежность поставщика также является одним из ключевых показателей, определяющих его способность удовлетворять на достаточно длительном промежутке времени требования фирмы-производителя к качеству МР, срокам и объемам поставок. Очевидно, что надежность является комплексным показателем, отражающим все стороны процесса закупок МР.
Большое значение при выборе поставщика имеют его возможности или способности удовлетворять определенным требованиям потребителей. Сюда относятся производственные мощности (объемы производимых МР), используемое технологическое оборудование, складская система и дистрибьютивная сеть поставщика, наличие возможностей доставки МР в больших количествах, уровень организации и контроля за поставками и т.п. Анализ этих показателей позволяет логистисческому менеджеру оценить потенциальные способности удовлетворять намеченной стратегической цели бизнеса и логистической стратегии фирмы.
Следующую сферу параметров оценки поставщика составляют финансовые условия. Главное место здесь занимает цена поставляемых МР. Однако в некоторых случаях на первый план выступают и другие финансовые условия, например, способность поставщика предоставлять рассрочку платежа, поставлять МР в кредит и т.п. Важную роль играют и ценовые скидки, например, за многократные заказы МР у одного и того –же поставщика. При выборе поставщика в анализе финансовых условий обязательно должна входить оценка его финансовой устойчивости, производимая с помощью независимого аудитора.
Кроме определенных количественных критериев оценки поставщика существует большая группа количественных показателей, которые играют важную роль в процессе выбора, но трудно поддаются определению. К таким показателям относится имидж поставщика, отсутствие негативных сообщений о нем от партнеров по бизнесу или в средствах массовой информации, доброжелательность, способность к контакту и длительным партнерским отношениям и т.п. Негативная оценка хотя бы по одному из таких показателей может вычеркнуть поставщика из списка возможных партнеров.
Не последнюю роль в выборе поставщика играет его географическое положение. Важность этого критерия определяется, прежде всего, транспортными расходами на доставку МР. Партнерство с близлежащими поставщиками обеспечивает, как правило, доставку МР с баз промежуточного хранения, лучшие условия для хранения, лучшие условия для внедрения JIT подхода, более короткие производственные циклы, большую надежность поставок и пр.
Очевидно, что расстановка приоритетов при выборе поставщика зависит от очень большого числа факторов и, прежде всего, от маркетинговой и логистической стратегии фирмы-производителя. Укрупненно их можно свести к трем основным: цена, качество, надежность (сервис) поставок МР.
Фактор цены как самих МР, так и затрат, связанных с управлением закупками, является преобладающим для большинства фирм, так как напрямую определяет прибыль. Поэтому, прежде всего, поставщики определяются по ценовому критерию. Обычно менеджер по закупкам пользуется четырьмя базовыми процедурами определения цен МР потенциальных поставщиков: ценам товарных бирж, прайс-листами, ценовыми котировками и переговорами напрямую с поставщиками.
Цены товарных бирж используются логистическим менеджером только для биржевых товаров, таких как зерновые, масличные культуры, цветные, черные металлы, нефть и нефтепродукты, необработанная древесина и ряд других. Цены товарных бирж являются наилучшими на момент котировки ориентирами, так как определяются из условия равновесия спроса и предложения.
Издаваемые поставщиками каталоги содержат подробные прайс-листы на все виды предлагаемых МР. В зависимости от статуса покупатели могут получить скидку на отдельные виды продукции. Кроме того, скидка определяется объемом закупок.
За рубежом менеджеры по закупкам часто используют метод ценовых котировок. Это особенно практикуется для поддержания конкуренции среди поставщиков и снижения цен. Процесс начинается с того, что покупатель посылает предполагаемым поставщикам «требования на квоты». Каждое «требование на квоты» содержит всю необходимую информацию о требуемых спецификациях МР и способах удовлетворения этих спецификаций. Возвращаемая поставщиками информация содержит данные о затратах на изготовление отдельных видов МР, на доставку и сопутствующий сервис, цены поставщиков, исходя из рентабельности. Сравнивая эти данные для различных поставщиков, менеджер по закупкам выбирает оптимального поставщика, обеспечивающего наилучший вариант по цене и сервису.
Системе установленных критериев может отвечать несколько поставщиков. Тогда необходимо их ранжировать, используя непосредственные контакты с представителями поставщиков.