Федеральное агентство по образованию бийский технологический институт (филиал)
Вид материала | Учебное пособие |
- Федеральное агентство по образованию бийский технологический институт (филиал), 981.77kb.
- Федеральное агентство по образованию бийский технологический институт (филиал), 1531.98kb.
- Федеральное агентство по образованию Бийский технологический институт (филиал), 2694.55kb.
- Федеральное агентство по образованию бийский технологический институт (филиал), 2134.54kb.
- Федеральное агентство по образованию бийский технологический институт (филиал), 1660.78kb.
- Федеральное агентство по образованию бийский технологический институт (филиал), 1946.38kb.
- Решением Ученого совета, 125.93kb.
- Федеральная целевая программа "Развитие электронной компонентной базы и радиоэлектроники", 3538.74kb.
- Бийский технологический институт (филиал), 2586.35kb.
- Министерство образования и науки федеральное агентство по образованию майкопский государственный, 102.13kb.
Пневмотраспортный сушильный агрегат состоит из калориферной установки, вентилятора, пневмотранспортной трубы и конфузорно-диффузорной воронки.
Калориферная установка обеспечивает необходимый подогрев воздуха, поступающего на сушку. Нагнетательный вентилятор подает на сушку требуемый объем воздуха, перемещая воздух и целлюлозу в пневмотранспортной трубе с заданной скоростью. Конфузорно-диффу-зорная воронка предназначена для питания пневмотранспортной трубы целлюлозой.
В пневмотранспортной сушильной трубе происходит интенсивная термическая обработка частиц целлюлозы. Температура транспортируемого воздуха колеблется в зависимости от исходного целлюлозного материала от 70 до 110 С. Целлюлоза, перемещаясь вместе с нагретым воздухом по пневмотранспортной трубе, подсушивается до требуемой влажности.
Из пневмотранспортной сушильной трубы подсушенная целлюлоза поступает в приемные бункеры.
Смешение кислот. В производстве нитратов целлюлозы имеются две технологические схемы смешения кислот: периодического действия и непрерывного действия.
Для приготовления кислотных смесей в производстве нитратов целлюлозы используют свежие концентрированные азотную и серную кислоты, отработанную кислотную смесь, олеум и меланж.
При составлении свежих тройных нитрационных кислотных смесей применяют свежую серную и слабую азотную кислоты. Массовая концентрация слабой азотной кислоты должна быть 45–55 %. Кислоты из хранителей через мерники в соответствии с расчетом заливаются в смеситель кислот: вначале серная кислота, затем при работающих лопастях смесителя определенными порциями азотная кислота. Выделяющееся тепло при смешивании кислот вращающимися лопастями равномерно распределяется по всей массе кислоты.
Температура кислоты в смесителе не должна превышать 50 °С, выше 50 °С заливка азотной кислоты прекращается. После смешения всех порций полученная нитрационная кислотная смесь отбирается для анализа. Если нитрационная кислотная смесь не отвечает требуемому составу, производится ее корректировка. Кислотная смесь исправляется олеумом и крепкой азотной кислотой. Если при анализе получены удовлетворительные результаты, то нитрационная кислотная смесь перекачивается в расходные баки.
При изготовлении нитрационной кислотной смеси из отработанных и свежих кислот в смеситель кислот вначале закачивается предварительно очищенная на фильтре, отработанная нитрационная кислотная смесь, затем при работающих лопастях смесителя заливаются све-жие кислоты. При этом, не дожидаясь результатов анализа отработанной нитрационной кислотной смеси, производят дозировку свежих кислот, руководствуясь предыдущими результатами анализов этой отработанной кислотной смеси, подлежащей освежению. Такая авансовая дозировка сокращает полный оборот смесителя и увеличивает его производительность. Время, необходимое для равномерного перемешивания кислот в смесителе, составляет 30 мин, его отсчет производится с момента окончания заливки в смеситель последней порции свежих
кислот.
Смесители кислот. Основным аппаратом на фазе смешения кислот является смеситель. На заводах эксплуатируются два типа смесителей: вертикальные и горизонтальные.
На старых действующих производствах установлены вертикальные смесители (рисунок 12).
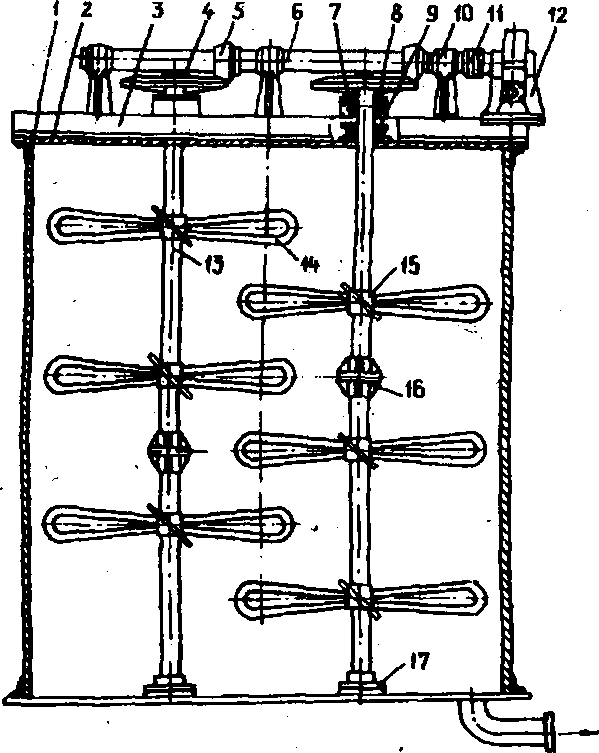
Рисунок 12 – Вертикальный смеситель кислот
Сеситель состоит из корпуса цилиндрической формы 1, закрывающегося крышкой 2. В смесителе имеются два вертикальных ва-
ла 13, вращающихся в одну сторону. На каждом валу крепятся разъемными муфтами 15 по три четырехлопастных мешалки 14. Для удобства в эксплуатации валы разъемны и соединяются разъемными муфта-
ми 16. Валы смонтированы на трех подшипниках: шариковом 7, скользящем 17, упорном 8. В крышке валы уплотнены сальниковыми уплотнениями 9. Для жесткости на крышке смесителя установлена рама 3, на которой находится привод смесителя. Привод смесителя состоит из горизонтального вала 6 на трех подшипниках 10, на валу крепятся две конические шестерни 5. На концах вертикальных валов имеются большие конические шестерни 4. Горизонтальный вал муфтой 11 соединен с редуктором 12. В крышке смесителя имеется люк для его осмотра.
В дне имеется патрубок для откачки приготовленной кислотной смеси.
Этот тип смесителя имеет в зоне смешения кислот большое количество болтовых соединений и подшипники, что усложняет его эксплуатацию. Для данного типа смесителей достаточна частота вращения лопастей 18–20 об/мин. Увеличение частоты вращения лопастей требует увеличения мощности привода, кроме того, за счет более интенсивного выделения паров азотной кислоты увеличиваются потери кислоты отходящими газами.На некоторых производствах на фазах смещения кислотных смесей устанавливают горизонтальные цилиндрические смесители (рисунок 13) диаметром 2–3 м с двумя или тремя пропеллерными мешалками, при длине смесителя 5–6 м две мешалки, при длине 10–12 м – три. Рекомендуется частота вращения мешалок
n=120–200 об/мин.
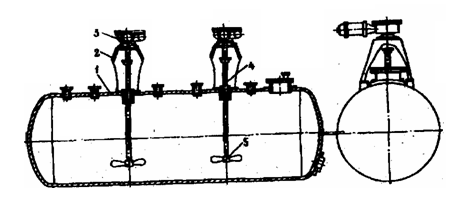
1 – корпус; 2 – стойка; 3 – редуктор; 4 – вал; 5 мешалка
Рисунок 13 – Горизонтальный смеситель кислот
Эти смесители конструктивно более просты и более удобны в эксплуатации.
Этерификация целлюлозы. Фаза нитрации целлюлозы – одна из важнейших при изготовлении нитратов целлюлозы. На этой фазе формируются основные параметры нитратов целлюлозы по содержанию азота, растворимости и вязкости.
Долгое время этерификацию целлюлозы проводили вручную в ваннах и горшках. Затем они были заменены более совершенными аппаратами нитрационными чашами братьев Томсон. Этот метод характеризуется тем, что в нем не применяется каких-либо аппаратов для отжима отработанных нитрационных кислотных смесей из нитратов целлюлозы. Удаление кислот производится вытеснением всей массы отработанной нитрационной кислотной смеси чистой водой. В дальнейшем получил широкое распространение метод этерификации целлюлозы в нитрационных центрифугах. По этому методу этерификацию целлюлозы и отжим ее отработанных нитрационных кислот производили в одних и тех же центрифугах. Этот метод был широко распространен, и только после 1918 г. его начали заменять более современным методом этерификации в нитраторах.
С 1931 г. нитрационные центрифуги в процессе реконструкции пороховых заводов начали заменяться нитрационными агрегатами, состоящими из четырех нитраторов и одной кислотоотжимочной центрифуги. Процесс этерификации целлюлозы в данном агрегате происходит в нитраторе, а отжим полученного нитрата целлюлозы от отра-ботанной нитрационой кислотной смеси в кислотоотжимочной центрифуге. В 1971 г. был разработан и внедрен бункер-дозатор для дозирования целлюлозы в нитраторы.
Периодически действующий нитрационный агрегат. На рисун-
ке 14 дана технологическая схема нитрационного агрегата.
Из пневмотранспортной сушильной трубы целлюлоза влажностью не более 5 % поступает в бункер-дозатор 1 с воздушной смесью, ударяясь об отражатель, теряет свою скорость и оседает равномерно по всей поверхности в бункере, а воздух отводится через камеру фильтров в атмосферу.
Периодически, через определенные интервалы времени (в соответствии с графиком работ нитраторов), шнек-дозаторы бункера производят объемное отмеривание навески целлюлозы заданной массы. Навеска целлюлозы по выгрузочной воронке поступает в нитратор 2, одновременно в нитратор подается нитрационная кислотная смесь.
После заполнения нитраторов целлюлозой и нитрационной смесью в течение установленного времени идет процесс этерификации. Затем из нитраторов реакционная смесь сливается по периодической технологии в кислотоотжимочные центрифуги 4, по непрерывной – в аппарат НУОК 7. По периодической технологии слив реакционной смеси в центрифугу регулирует аппаратчик с помощью сливного крана 3. По непрерывной технологии равномерность слива в аппарат НУОК осуществляется краном, подключенным к приводу.
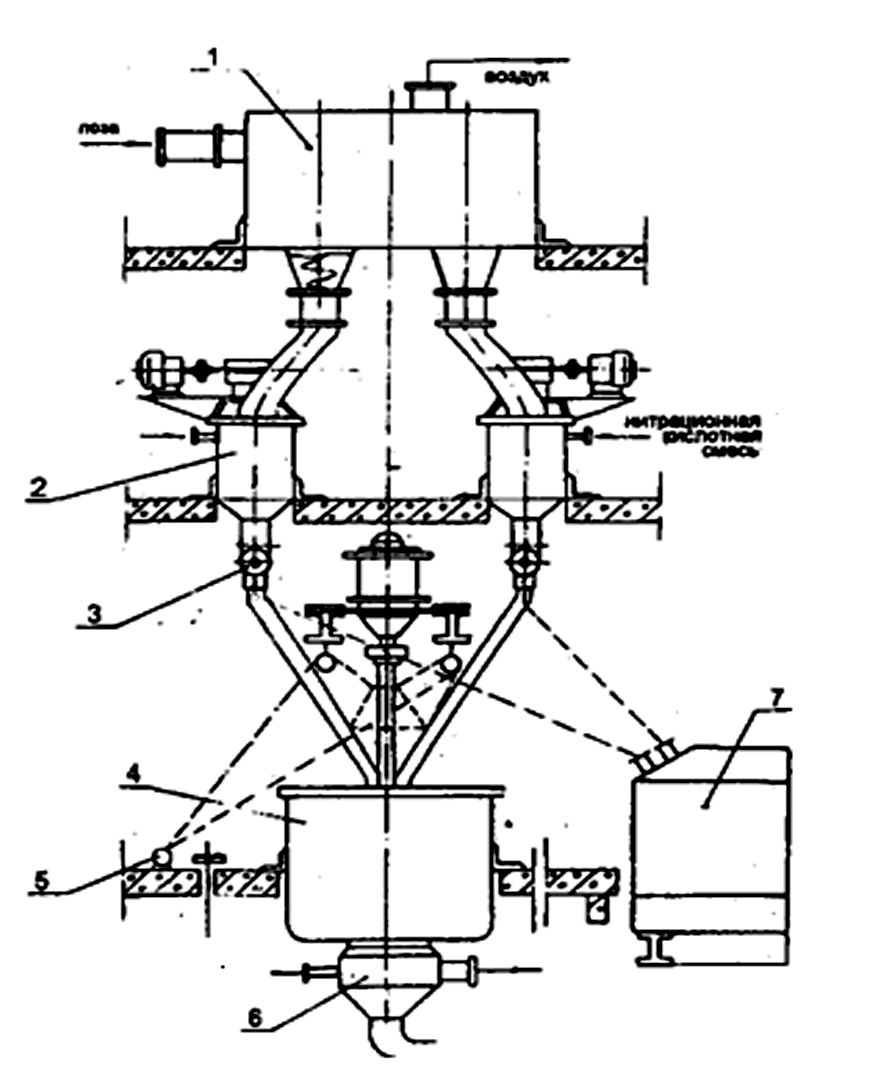
Рисунок 14 – Технологическая схема нитрационного агрегата
Реакционная смесь сливается в центрифугу на ее тихом ходу, затем центрифуга переключается на быстрый ход, по истечении заданно-го времени кислотоотжима автоматически отключается. Аппаратчик включает лебедку 5 подъема колокола. Одновременно с подъемом колокола автоматически открывается кран подачи транспортируемой кислоты в смывной аппарат 6. Когда в центрифуге идет рекуперация кислот, в смывной аппарат подается вода. Через отверстие в дне корзины центрифуги частично отжатый от отработанной нитрационной кислотной смеси нитрат целлюлозы выгружают в смывной аппарат. Из смывного аппарата нитрат целлюлозы с массовой долей в транспортной кислоте 2−3 % самотеком поступает в мутильник и затем в вытеснители для рекуперации кислот. В центрифугах, в которых наряду с кислотоотжимом производится рекуперация адсорбированных нитратом целлюлозы кислот, осуществляется гидравлическая выгрузка. При этом в корзину центрифуги подается вода, и водно-нитрационная взвесь с массовой долей 2–3 % поступает в мутильник и далее на фазу стабилизации.
По непрерывной технологии из аппарата НУОК водная взвесь нитрата целлюлозы с массовой долей 2–3 % также поступает на фазу стабилизации.
Нитратор. В промышленности для нитрации целлюлозы используются лопастные нитраторы (рисунок 15).
Нитратор имеет эллиптическую форму, коническое днище и слив-ной патрубок. Он снабжен двумя лопастными мешалками 1, которые вращаются в разные стороны. В верхней части аппарата имеется люк для подачи целлюлозы, а также патрубок для подвода нитросмеси.
С внутренней части нитратора к патрубку подсоединен ороситель для подачи нитросмеси. Ороситель выполнен в виде трубы 3 с отверстиями, согнутый по контуру аппарата и заглушен в конце. Отверстия просверлены так, чтобы при пуске кислоты в ороситель кислота орошала загружаемую целлюлозу в нитратор. Такое орошение загружаемой цел-люлозы кислотной смесью предупреждает ее загорание.
Работа нитратора. До начала загрузки целлюлозы нитратор заполняется на 1/3 объема нитрационной кислотной смесью. Одновременно он подключается к вентиляционной системе для отсоса паров азотной кислоты и предупреждения их попадания из нитраторов в рабочее помещение, затем пускаются мешалки. С помощью бункеров-дозаторов равномерно небольшими порциями в нитратор загружается навеска целлюлозы. По мере загрузки целлюлозы из расходных баков через ороситель подается оставшаяся часть нитрационной кислотной смеси. Заливку нитрационной кислотной смеси производят так, чтобы после загрузки навески целлюлозы остатком кислоты смыть волокна целлюлозы со стенок нитратора и утопить волокна, плавающие на поверхности кислоты. При таком способе загрузки целлюлоза быстро погружается в кислоту, время загрузки 2–3 мин. В целях уменьшения уноса паров кислоты с отходящими газами после заполнения нитратора на линии отсоса задвижка закрывается. Однако значительны потери азотной кислоты с отходящими газами, особенно при этерификации нитратов целлюлозы, требующих высоких температур процесса этерификации (порядка 40–45 °С) и значительного времени (40–45 мин).
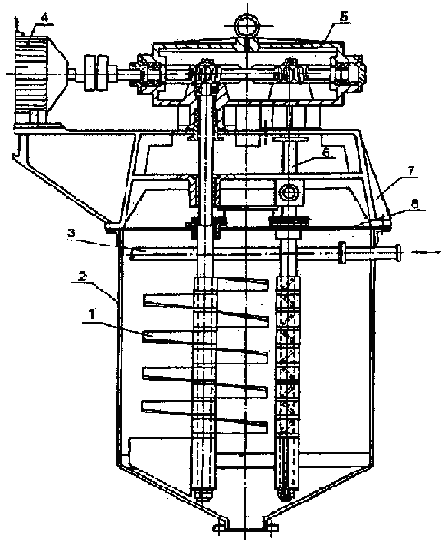
1 – лопасти; 2 – корпус; 3 ороситель; 4 – электродвигатель;
5 редуктор; 6 – вертикальный вал; 7 – кронштейн; 8 крышка
Рисунок 15 – Нитратор
При этерификации реакционная масса в нитраторе периодически или непрерывно, в зависимости от исходного сырья и нужной вязкости нитрата целлюлозы, перемешивается. Так, например, по окончании загрузки хлопковой целлюлозы лопасти продолжают работать еще
3–5 мин, затем их останавливают и пускают в середине процесса этерификации на 4–5 мин и за 3–5 мин перед разгрузкой.
При непрерывной работе лопастей в процессе этерификации хлопковой целлюлозы она подвергается сильной деструкции, что отрицательно сказывается на дальнейшей ее обработке. Однако при этерификации целлюлозы марки РБ допускается работа лопастей без остановки, так как целлюлоза всплывает на поверхность и может воспламениться.
По истечении времени этерификации, не останавливая лопастей, реакционную массу сливают в 2–3 приема (по периодической технологии) в кислотоотжимочную центрифугу, работающую на малой частоте вращения. По непрерывной технологии реакционная смесь сливается равномерно в круговой аппарат, для этого сливной кран имеет приводную систему.
Кислотоотжимочная центрифуга. Для отделения отработанных нитрационных кислотных смесей от нитратов целлюлозы по периодической технологии применяются кислотоотжимочные центрифуги с последующей рекуперацией адсорбированных нитратом целлюлозы кислот на вытеснителях.
На рисунке 16 приведена схема центрифуги.
На корзине центрифуги имеются отверстия диаметром 5 мм, с шагом 25 мм. Для лучшего отжима и меньшего уноса волокон НЦ с отработанными нитрационными кислотными смесями в процессе кислотоотжима в корзину центрифуги вставляется дренажная сетка кольчужного плетения и пробивная фильтрующая сетка толщиной листа 0,75 мм с диаметром 1,5–1,8 мм.
Центрифуга состоит из основания плиты 15, кожуха 14, корзи-
ны 13, крышки 12. На крышке располагаются для залива реакционной массы два патрубка 10 и люк, закрываемый крышкой 11 из двух половин. Вертикальный вал центрифуги 9 подвешен на опорном буферном подшипнике 1, установленном на плите 6. В опорной плите имеется гнездо для резинового буфера 5, в него вставляется стальной горшок 2. Верхняя часть вала крепится муфтой 5 с электродвигателем 4. Центрифуга имеет ручной ленточный тормоз, диск 7 которого смонтирован на вертикальном валу.
Разгрузочное отверстие корзины закрывается конусообразной крышкой-колоколом 8. При сливе реакционной смеси в центрифугу и отжиме НЦ разгрузочное отверстие закрыто колоколом, по окончании отжима лебедкой 16 колокол поднимается и открывается разгрузочное отверстие корзины. Одновременно открывается кран подачи транспортной жидкости в смывной аппарат. После разгрузки колокол опускается, закрывает разгрузочное отверстие центрифуги, перекрывается подача транспортной жидкости в смывной аппарат.
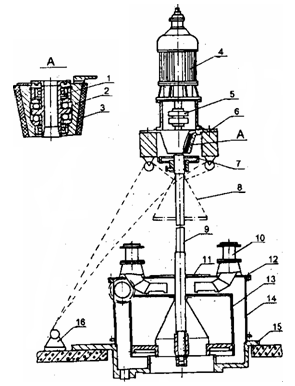
Рисунок 16 – Кислотоотжимочная центрифуга
Смывной аппарат предназначен для приемки выгружаемых из центрифуги частично отжатых от кислоты нитратов целлюлозы.
Работа центрифуги. По истечении установленного времени этерификации в нитраторе реакционная смесь сливается в центрифугу. Слив реакционной смеси производится на тихом ходу (частота вращения 350 об/мин) центрифуги в два или три приема в зависимости от исходной марки целлюлозы. Затем оставшаяся часть отработанных нитрационных кислот в нитратах целлюлозы частично извлекается на быстром ходу центрифуги (960 об/мин). Центрифуга переключается автоматически с тихого на быстрый ход. Содержание одного нитратора соответствует закладке одной центрифуги.
Основная масса отработанной кислотой смеси сливается и поступает в сборник отработанных нитрационных кислот. Время отжима зависит от технической характеристики центрифуги, исходной марки целлюлозы и марки нитрата целлюлозы. После отключения центрифуга тормозится и останавливается. Центрифуги, в которых производится рекуперация адсорбированных отработанных нитрационных кислот, разгружаются гидравлическим способом.
Вытеснение адсорбированных кислот в вертикальных вытеснителях. После отжима на центрифуге нитраты целлюлозы содержат от 1,0 до 1,25 тонны адсорбированных кислот на 1 тонну нитрата целлюлозы. Для удаления адсорбированной кислоты из волокон НЦ используется принцип вытеснения одной жидкости другой. Жидкость меньшей плотности, поступая сверху на обрабатываемый материал, в котором адсорбирована жидкость большей плотности, вытесняет последнюю, занимая тот же объем в пространстве между волокнами.
Отжатый от кислот НЦ из центрифуги выгружается в смывной аппарат. Одновременно в смывной аппарат подается транспортная кис-лотная смесь с массовой долей 45–50 %. Реакционная смесь из смывного аппарата поступает через мутильник в вытеснитель. После загрузки вытеснителя нитратом целлюлозы и стока транспортных кислот адсорбированные им кислоты вытесняются более слабыми кислотами с массовой долей 25–28 %, а затем водой.
При вытеснении адсорбированных кислот происходит частичная денитрация нитратов целлюлозы. Чтобы уменьшить денитрацию НЦ, орошающую кислотную смесь, воду охлаждают до 15–17 С.
Непрерывный способ нитрования целлюлозы. Нитрование цел-люлозы предварительно осуществляется в периодически действую-щих нитраторах-дозаторах, которые работают циклично и поочередно на один круговой аппарат непрерывного удаления отработанных кислотных смесей (НУОК), в котором избыток нитросмеси отделяется за счет естественного стока (рисунок 17).
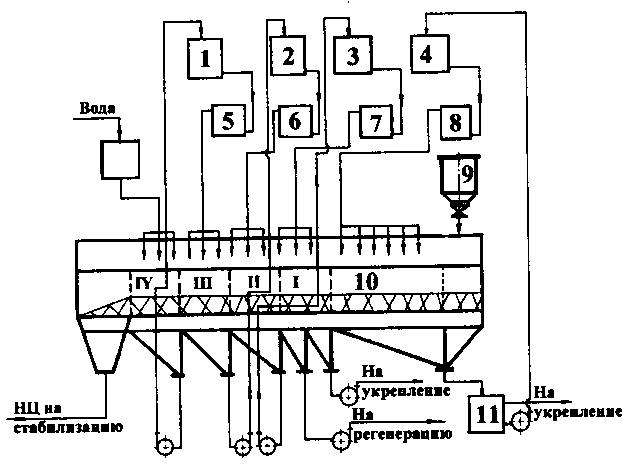
1–4 – напорные баки орошающих кислот; 5–8 – холодильники
орошающих кислот; 9 – нитратор-дозатор; 10 – аппарат НУОК;
11 – бак-сборник отработанной кислоты
Рисунок 17 – Технологическая схема окончательного нитрования
целлюлозы и рекуперации удержанных кислот на аппарате НУОК
Над аппаратом установлено четыре нитратора. По истечении времени предварительной этерификации (15–20 мин) из нитраторов-дозаторов поочередно (согласно графику работы) производится слив реакционной массы (при непрерывно работающих мешалках) в аппарат НУОК.
В аппарате НУОК, имеющем диаметр 7,6 м (см. рисунок 17), НЦ равномерно распределяется на дне перфорированного кольцевого транспортера, медленно вращающегося в закрытом кожухе.
По мере его вращения новые порции нитрата целлюлозы из других нитраторов подаются на его ложное дно. Продукт укладывается специальной гребенкой ровным слоем определенной высоты (25–40 см) и орошается по всей поверхности из оросительных желобов.
Отработанная кислотная смесь стекает через перфорированное дно в соответствующее отделение неподвижного кольцевого поддона, разделенного перегородками, и самотеком поступает через кислотный фильтр в бак-сборник отработанной кислоты 11, затем насосом подается в напорный бак 4 орошающих кислотных смесей и самотеком через холодильник 8 поступает в зону окончательной проточно-ороситель-ной этерификации, длительность которой составляет 15–25 мин. Избыток отработанной кислоты направляется на фазу смешения кислот для укрепления и дальнейшего использования в производственном цикле.
Зона рекуперации кислот в аппарате НУОК разделена на четыре секции-ступени вытеснения отработанных кислот кислотами убывающей концентрации, а затем водой.
В четвертой секции зоны рекуперации нитрат целлюлозы орошается водой, которая подается в строго расчетном количестве. Из поддона четвертой секции слабые кислотные смеси (при концентрации
30–40 % масс.) через напорный бак 1 и холодильник 5 поступают на орошение нитрата целлюлозы в третьей секции, из нее кислотные смеси (при концентрации 50–60 % масс.) через напорный бак 2 и холодильник 6 орошают нитрат целлюлозы второй секции, а затем (при концентрации 65–75 % масс.) поступают через напорный бак 3 и холодильник 7 на орошение нитрата целлюлозы в первой секции.
Таким образом, вытесненная кислота каждой последующей ступени является орошающей кислотой предыдущей ступени вытеснения.
Отработанная кислотная смесь из первой секции разделяется на два потока: первая, более концентрированная фракция (67–75 % от общей массы вытесненной кислоты), направляется на фазу смешения кислот для укрепления, а оставшаяся часть поступает на фазу регенерации кислот.
Температура орошающих кислот в зоне проточной этерификации не более 10 С, в зоне рекуперации 6–10 С. Такой режим создается для уменьшения процесса денитрации нитратов целлюлозы.
Для улова паровоздушной смеси, содержащей пары и туман Н2SO4, HNO3 и оксиды азота, нитраторы и аппарат НУОК подключены газовоздуховодами к абсорбционной установке.
Стабилизация нитратов целлюлозы. Нитраты целлюлозы, полученные промышленным сернокислотным способом, имеют низкую химическую стойкость и способны к самопроизвольному разложению даже при умеренных температурах. Это объясняется тем, что при нитровании целлюлозы наряду с реакцией этерификации протекают побочные реакции с образованием химически нестойких продуктов. Кроме того, внутри нитроцеллюлозного волокна имеется свободная (закапсулированная) серная кислота.
Многочисленными работами было установлено, что нестабильность нитратов целлюлозы обусловлена наличием:
- химически связанной серной кислоты в виде сульфо- и сульфонитроэфиров;
- закапсулированной серной кислоты;
- нитросахаров, то есть нитрованных низкомолекулярных продуктов гидролиза и окисления целлюлозы.
Чем ниже степень этерификации НЦ, тем больше содержание в них сульфо и сульфонитроэфиров.
Высокоазотные нитраты целлюлозы имеют только следы связанной серной кислоты, но в то же время содержат до 0,5 % от массы НЦ свободной серной кислоты.
Фаза стабилизации – одна из основных в производственном цикле изготовления нитратов целлюлозы. Она преследует две цели:
- собственно стабилизацию, обеспечивающую требуемую химическую стойкость нитратов целлюлозы путем удаления из них нестойких примесей и побочных веществ, ухудшающих их стойкость;
- формирование технологических показателей нитратов целлюлозы, обеспечивающее требуемую вязкость, степень полимеризации, растворимость и дисперсность нитратов.
Стабилизация НЦ включает следующие операции:
- обработку нитратов целлюлозы в кислой среде при повышенных температурах;
- обработку НЦ в щелочной среде при повышенных температурах;
- измельчение волокон НЦ в щелочной среде;
- окончательную промывку НЦ в щелочной или нейтральной среде.
Стабилизация нитратов целлюлозы по периодической технологии. Пироксилины № 1и № 2 в основном обрабатываются по периодической технологии, включающей предварительную стабилизацию в чанах горячей промывки путем варки в кислой, затем в щелочной средах, измельчение в измельчительных машинах и окончательную стабилизацию в лаверах.
Чан горячей промывки. Чаны горячей промывки можно подразделить на две группы: без механизма гидроразмыва нитратов целлюлозы и с механизмом гидроразмыва нитратов целлюлозы. Чан с механизмом гидроразмыва нитрата целлюлозы (рисунок 18) представляет собой вертикальный цилиндрический резервуар 2 из нержавеющей стали.

1 – сопло для подачи пора; 2 – корпус чана; 3 – ложное дно;
4 – теплоизоляция; 5 – циркуляционные трубы; 6, 9 – подшипники;
7 – пустотелый вал; 8 – сопла, 10 – труба
Рисунок 18 – Чан горячей промывки
Наружная поверхность цилиндрической части теплоизолирована досками 4. На высоте 0,2 м от дна установлено ложное дно с отверстиями диаметром 2−3 мм. В пространстве между ложным дном и днищем чана подогревают воду до требуемой температуры паром, который вводится в воду, при этом лучше используется тепло, так как паровой конденсат смешивается с нагреваемой водой и их температуры выравниваются. Чаны имеют по две циркуляционные трубы 5 в местах ввода пара. Имеются чаны с четырьмя циркуляционными трубами. Нагретая в междонном пространстве, вода поднимается по этим трубам вверх и орошает поверхность нитратов целлюлозы. В верхней части циркуляционные трубы имеют козырьки, которые направляют струи горячей воды к центру чана и тем самым распределяют ее по всей поверхности нитратов целлюлозы. Горячая вода из верхних слоев нитратов целлюлозы по мере охлаждения опускается в нижние слои, при этом, омывая их волокна, поступает в поддонное пространство, где подогревается и снова по циркуляционным трубам поднимается наверх.
После вытеснения кислот из нитратов целлюлозы последние подаются массонасосами в чаны горячей промывки. После заполнения чана нитратом целлюлозы и слива транспортной воды проводят кислую варку. Чан заполняется чистой водой, требуемая кислотность среды обеспечивается кислотами, содержащимися в НЦ, и в начале варки она составляет 0,1–0,3 %, а затем может увеличиваться до 0,5 %. Варка ведется при температуре 97–100 С. После окончания кислой варки кислые отработанные воды сливаются, а нитрат целлюлозы промывается горячей водой. Затем заливают снова горячую воду для проведения щелочной варки.
Для создания требуемой щелочности (0,01–0,03 %) в чан подают необходимое количество содового раствора. Щелочная варка проводится при температуре 90–95 С.
Отработанные кислые и щелочные воды поступают через фильтр на станцию нейтрализации.
Стабилизация нитратов целлюлозы по непрерывной технологии. В основу непрерывного процесса заложена стабилизация нитратов целлюлозы при высоких температурах и давлении в непрерывнодействующем трубчатом автоклаве.
Непрерывнодействующий автоклав – это многогранная система, состоящая из аппаратов предварительного нагрева, предназначенных для нагревания нитроцеллюлозной водной взвеси до заданных температур и доведения ее до массовой доли 3–5 %, питающего чана, в котором поддерживается постоянный уровень массы, двух питающих массонасосов высокого давления, работающих последовательно и создаю-щих в автоклаве 0,7–0,9 мПа (вторая пара насосов резервная), и трубчатого автоклава.
В аварийных случаях для охлаждения автоклава предусматривается подача воды с температурой 25–30 °С в зону выдержки, а также взамен пара в зону подогрева. Для поддержания определенного давления, а следовательно, и необходимой температуры в трубчатом автоклаве в его конце установлены тормозные насосы или тормозные сопла, создающие обратное давление 0,35–0,5 мПа. При установке тор-мозных насосов требуемое обратное давление достигается изменением частоты их вращения.
Работа трубчатого автоклава. Нитраты целлюлозы с массовой долей 1,5–2 % поступают в аппараты предварительного нагрева. В этих аппаратах сливают транспортные воды, доводят массу до требуемой массовой доли и создают 0,1–0,3%-ную кислотность среды, для чего при необходимости из бачка в аппарат заливается 45%-ная азотная кислота. Подогревают содержимое аппарата до 90–95 °С. В системе устанавливается несколько аппаратов предварительного нагрева так, чтобы за время выработки одного аппарата последующий аппарат был подготовлен к выработке. Таким образом обеспечивается непрерывная работа автоклава. Из аппарата предварительного нагрева массонасосами водная взвесь перекачивается в питающий чан, в нем поддерживается постоянный уровень.
Одновременно из питающего чана массонасосами водная взвесь нитратов целлюлозы подается в трубчатый автоклав. В трубчатом автоклаве в зоне подогрева взвесь дополнительно подогревается до
135–155 °С. При этом температура обусловлена не получением их химической стойкости, а требуемой вязкостью. Затем в зоне выдержки при той же температуре взвесь находится в течение 10–15 мин, а в зоне охлаждения она охлаждается до 70–100 °С.
При автоклавной варке нитратов целлюлозы в кислой среде разрушаются сульфо- и сульфонитроэфиры, частично удаляются свободная серная кислота из высокоазотных нитратов целлюлозы и ее соли, а также снижается степень полимеризации, следовательно, и условная вязкость.
В конце трубчатого автоклава перед тормозными соплами в массопроводе взвесь разбавляется водой до массовой доли 1,5–2 % и через тормозные устройства поступает в приемные баки. В приемных баках сливаются слабокислые воды с последующей заливкой содовых вод из расчета создания 0,01–0,03 % щелочности среды для нейтрализации выделившихся кислот при кислой автоклавной обработке нитратов целлюлозы. Из приемных баков нитраты целлюлозы подаются в отделение измельчения. По такой схеме обрабатываются нитраты целлюлозы, условная вязкость которых 2–12 °Э (коллоксилины «Н», пироксилины № 2 и № 1).
Трубчатый автоклав представляет собой теплообменник «труба в трубе» в виде змеевика с размещенными друг над другом прямыми участками труб. Сама труба является массопроводом, а в межтрубные пространства подается теплоагент нагрева или охлаждения. Трубчатый автоклав разделен на зоны: I – зона нагрева; II – зона выдержки;
III – зона охлаждения. По всей длине зоны нагрева и выдержки теплоизолированы.
Измельчение нитратов целлюлозы. Цель операции измельчения волокон НЦ – удалить закапсулированные кислоты и получить необходимую степень дисперсности нитратов целлюлозы.
При измельчении нитратов целлюлозы изменяются не только геометрические размеры волокна, но и такие структурные характеристики, как удельная поверхность и др.
Измельченные нитраты целлюлозы имеют большую насыпную массу, чем неизмельченные. Это позволило увеличить производительность аппаратуры, применить непрерывно действующие аппараты в производстве как нитратов целлюлозы, так и порохов (водоотжимочные, обезвоживающие центрифуги и др.).
В зависимости от характера измельчения, формы и размеров частиц измельченных нитратов целлюлозы изменяются такие физико-химические показатели, как их сорбционная способность, характер и скорость взаимодействия растворителя и др. Степень измельчения нит-ратов целлюлозы существенно влияет на скорость пластификации волокон соответствующими растворителями. С повышением степени измельчения скорость пластификации увеличивается. Это в одинаковой мере относится и к пироксилиновым, и к баллиститным порохам.
Измельчительные машины. Для измельчения нитратов целлюлозы можно использовать аппараты как периодического действия (голландеры), так и непрерывного (конические или дисковые мельницы).
В настоящее время используют наиболее совершенные дисковые мельницы типа МД. Они широко распространены в целлюлозно-бу-мажной промышленности. Эти мельницы отличаются высокой окружной скоростью ротора, поэтому волокна нитратов целлюлозы, наряду с механической, подвергаются интенсивной гидродинамической обработке за счет турбулентных вихревых потоков. Напор, развиваемый ротором, больше, чем в конических мельницах. Это позволяет уменьшить размеры ячеек гарнитуры и расположить на поверхности диска большее количество ножей, а также измельчать нитраты целлюлозы при массовой доле до 20 %. Мельницы просты в обслуживании.
На рисунке 19 представлена технологическая схема непрерывного измельчения нитратов целлюлозы на мельницах типа МД-31.
Водную взвесь нитратов целлюлозы с массовой долей 4–5 % из смесителя 1 массонасосом 2 подают в измельчительную камеру первой дисковой мельницы 3, затем крыльчаткой, закрепленной на вращающемся диске, направляют к размалывающим дискам. Под действием центробежной силы масса проходит в зазор между дисками и рабочими поверхностями гарнитуры; волокна измельчают перерезанием, растиранием (гидродинамический эффект аморфизации).
Дисковая мельница выполняет функции не только измельчительного аппарата, но и центробежного насоса, поэтому перекачивает массу во вторую мельницу 4, из которой массу подают в лаверы 5 для дальнейшей технологической обработки.
Размалывающие диски (измельчительная гарнитура) закреплены на статоре и роторе. Определяющими в гарнитуре являются: толщина ножей ротора и статора, угол наклона ножей относительно друг друга и их длина, а также межножевой зазор между дисками (на первой стадии измельчения он может быть, например, 0,10–0,12 мм, а на второй – 0,07–0,08 мм). При использовании гарнитуры с тонкими ножами производится, главным образом, рубка волокна и уменьшение его размеров по длине, а применение толстых широких ножей приводит к истиранию волокон и увеличению их удельной поверхности.
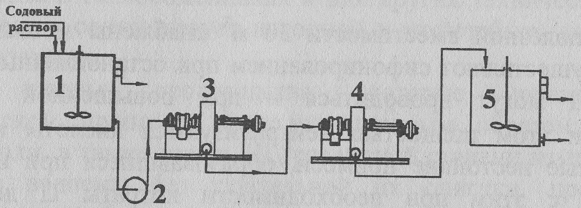
1 – смеситель; 2 – массонасос; 3, 4 – дисковые мельницы типа МД-31;
5 – лавер
Рисунок 19 – Технологическая схема непрерывного измельчения
нитроцеллюлозы
Измельчение проводят в щелочной среде, поэтому для ее поддержания (в пределах 0,01–0,03 % масс.) в смеситель подают содовый раствор. Если необходимо измельчать нитраты целлюлозы при концентрации, большей чем 4–5 % масс., то суспензию пропускают через сгуститель между первой и второй мельницами.
После измельчения нитраты целлюлозы поступают на окончательную стабилизацию.
Окончательная стабилизация. Нитраты целлюлозы, поступающие на фазу окончательной стабилизации, имеют значительный разброс физико-химических показателей (содержание азота, вязкость, дисперсность и др.). Различия в физико-химических показателях разных порций нитратов целлюлозы при их изготовлении обусловлены нестабильностью ведения технологического процесса. Например, НЦ, полученные после фазы нитрации, неоднородны по содержанию азота, после предварительной стабилизации – по вязкости и растворимости, после измельчения – по дисперсности и т.д. Масса нитратов целлюлозы одного лавера является частной партией. Если общая партия коллоксилинов «Н» состоит из частных партий нитратов целлюлозы одного вида, то однородность общей партии будет достигнута в смесителе общих партий. При изготовлении смесевых пироксилинов, которые состоят из разнотипных нитратов целлюлозы (пироксилина № 1, № 2), частные их партии перед смешением общей партии смесевого пироксилина должны быть усреднены. Таким образом, в лаверах, помимо окончательной стабилизации (лаверной промывки), происходит и усреднение частных партий пироксилина.
При изготовлении коллоксилинов «Н» лаверы одновременно служат накопителями частных партий перед смешением общих. Низковязкие коллоксилины, к которым предъявляются повышенные требования по их физико-химической однородности, например, коллоксилины целлулоидные, не формируются в общие партии из частных, каждая частная партия является общей.
В процессе окончательной стабилизации (лаверной промывки) нитратов целлюлозы полностью нейтрализуются кислоты и удаляются водорастворимые нестойкие примеси, образовавшиеся при измельчении и автоклавной обработке. Одновременно с этим при необходимости нитраты целлюлозы доводятся до требуемой вязкости и степени полимеризации. В зависимости от марки нитратов целлюлозы процесс лаверной стабилизации ведут как в щелочной, так и в нейтральной средах с подогревом и без подогрева.
Так, например, промывки пироксилина № 1 ведут в щелочной среде с содержанием щелочи 0,01–0,05 % при 70–90 °С, пироксилина № 2 – в нейтральной среде при 60–95 °С.
Операцию окончательной стабилизации ведут в лаверах (от французского слова laveur промывной аппарат) аналогично операциям, проводимым в чанах горячей промывки. Лаверы для окончательной стабилизации неизмельченных нитратов целлюлозы аналогичны чанам горячей промывки. Они также снабжены ложным дном для отделения воды, в некоторых имеются смесительные устройства. Лаверная промывка измельченных нитратов целлюлозы отличается от обработки не измельченных нитратов целлюлозы, отделение воды осуществляется сифонированием. Так как измельченные нитраты целлюлозы очень легко оседают на дно лавера, при промывке их необходимо перемешивать, для чего лаверы снабжены мешалками разного типа: лопастными с простым или планитарным приводами, винтовыми.
На рисунке 20 приведен один из лаверов с лопастными мешалками.
Он представляет собой цилиндрическую емкость 2, в дне которой имеются патрубок слива массы 16 и патрубок 1 для слива промывных вод в канализацию. В крышке лавера имеется люк для внутреннего осмотра, который в процессе работы герметично закрыт, патрубок для ввода нитратов целлюлозы взвеси, залива холодной и горячей воды, содового раствора, вмонтирован паропровод с пароструйным нагревательным соплом 15. В крышке также имеются два отверстия для ва-
лов 14, вращающихся в одну сторону.
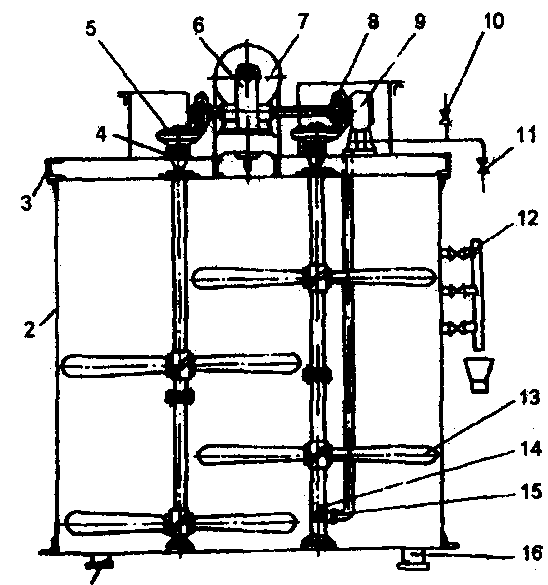
Рисунок 20 – Лавер
На каждом валу смонтировано по две четырехлопастные мешал-ки 13. Мешалки смонтированы так, что в промежутке между мешалками одного из валов находятся мешалки другого вала. Для удобства эксплуатации валы сделаны разъемными. Вал смонтирован на двух скользящих подшипниках, один из которых крепится на дне лавера, второй – на крышке. Для жесткости крышки на ней установлена ра-
ма 3, на которой монтируется привод лопастей. Привод состоит из червячного редуктора 6, на концах выходных валов – две малые конические шестерни 8. Удлиненный конец вала установлен на подшипни-
ке 9. На конце вертикальных валов крепятся большие конические шестерни 5, ступицы которых являются упорными кольцами упорного подшипника 4, смонтированного на раме. Редуктор эластичной муфтой соединен с электродвигателем 7. Частота вращения лопастей мешалок
20–25 об/мин. Для слива промывной воды на поверхности корпуса по вертикали устанавливаются сифонные пробковые краны 12. Верхний кран – на расстоянии около 0,5 м от верхней кромки лавера, ниже этого крана по вертикали на расстоянии друг от друга 250–300 мм еще тричетыре крана. Ниже всех кранов – воронка, через которую отбираются пробы сифонируемых вод для определения количества в них измельченных нитратов целлюлозы. Перед сливом промывных вод мешалки лавера останавливают и дают нитратам целлюлозы отстояться в течение 1,5–2 ч. За это время нитраты целлюлозы оседают на дно лавера, а отстоявшуюся промывную воду сливают. Для этого открывается верхний кран, затем последовательно краны, расположенные ниже, слив производят до требуемого уровня содержимого лавера после сифонирования. Плотность осевших нитратов целлюлозы зависит от времени отстаивания, с увеличением которого плотность их увеличивается, что может привести к поломке привода мешалок при очередном запуске лавера. Поэтому время отстоя не должно превышать 3–4 ч.
Сифонируемые промывные воды всегда содержат некоторые количества измельченных нитратов целлюлозы, поэтому они поступают не в канализацию, а в сборники, затем в отстойники для улова уносимых ими нитратов целлюлозы. Взвесь до заданных температур подогревается острым паром, поступающим в нижнюю часть лавера через пароструйное сопло 15. Для ускорения нагрева устанавливаются по два пароструйных сопла, расположенных в диаметрально противоположных сторонах лавера. На паровой линии вентиль 11 установлен выше уровня содержимого в лавере. Подогрев производится при работающих мешалках. Пуск пара при неработающих лопастях недопустим.
По окончании лаверной стабилизации подача пара в лавер прекращается. Одновременно открывается вентиль 10, что исключает возможность подхода жидкости из лавера к паровому вентилю 11.
Лаверы имеют полезную вместимость 20–35 м3 при загрузке в них 2,5–4 т нитрата целлюлозы, что составляет одну частную (малую) партию. В лавер закачивают нитраты целлюлозы с массовой долей
7–10 %. Сифонирование транспортных вод ведут до массовой доли
20–25 %.Так как обработка в лавере ведется при массовой доле взвеси 12–14 %, то это достигается заливкой в лавер свежей воды. Перекачку отстабилизированных нитратов целлюлозы из лаверов можно вести только по получении всех требуемых значений физико-химических показателей: стойкости, вязкости, растворимости, содержания азота, золь-ности.
Формирование общих партий нитратов целлюлозы и отжим их от воды. Эта операция необходима для усреднения физико-хими-ческих показателей НЦ (содержание азота, вязкости, дисперсности и др.). Их различия обусловлены возможным отклонением параметров технологического процесса на тех или иных фазах. Чем выше физико-химическая однородность партий НЦ, тем стабильнее процессы производства порохов и лучше показатели их эксплуатационных характеристик.
Процесс смешения нитратов целлюлозы осуществляется в водной среде при концентрации суспензии нитратов целлюлозы примерно
10 % масс. в аппаратах цилиндрической формы, снабженных мешалками различного типа. Вместимость смесителей 300–400 м3. По окончании процесса смешения отбирают пробы нитратов целлюлозы для полного физико-химического анализа (определение химической стойкости, содержания азота, вязкости, степени измельчения, растворимости и др.).
При положительных результатах по всем показателям смесевую партию нитратов целлюлозы отжимают от воды до влажности
28–32 % масс. или водную суспензию нитратов целлюлозы перекачивают непосредственно на производство порохов.
1.9.5 Тротил [3, 4]
Тротил (тринитротолуол или тол) получают нитрованием толуола. Химическая формула тротила:
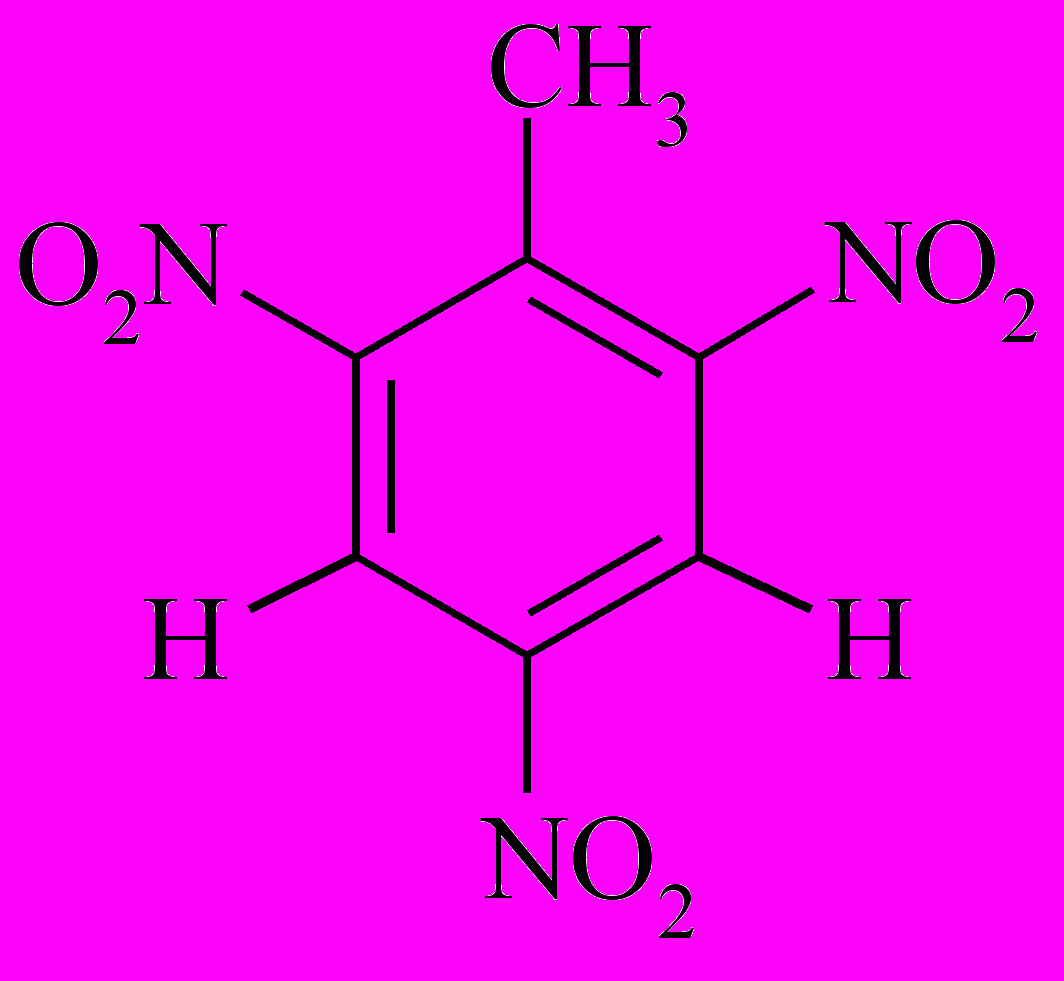
Реакция протекает ступенчато: сначала образуется мононитротолуол, затем динитротолуол, а при нитровании динитротолуола получается тринитротолуол. Плотность тротила равна 1660 кг/м3 (1,66 г/см3), он отличается высокой химической стойкостью, температура вспышки равна 290 °С. Скорость детонации при плотности 1620 кг/м3 равна
7000 м/с. Являясь достаточно сильным бризантным ВВ, обладает малой чувствительностью к механическим воздействиям. Тротил легко прессуется и дает отливки высокого качества. В чистом виде тротил используют для снаряжения артиллерийских снарядов и авиабомб, а также для изготовления подрывных средств.
Тротил широко применяется в виде сплавов с другими взрывчатыми веществами, например, с гексогеном. Наиболее широкое применение как для военных, так и для мирных целей нашли смеси тротила с аммиачной селитрой.