Федеральное агентство по образованию бийский технологический институт (филиал)
Вид материала | Учебное пособие |
- Федеральное агентство по образованию бийский технологический институт (филиал), 981.77kb.
- Федеральное агентство по образованию бийский технологический институт (филиал), 1531.98kb.
- Федеральное агентство по образованию Бийский технологический институт (филиал), 2694.55kb.
- Федеральное агентство по образованию бийский технологический институт (филиал), 2134.54kb.
- Федеральное агентство по образованию бийский технологический институт (филиал), 1660.78kb.
- Федеральное агентство по образованию бийский технологический институт (филиал), 1946.38kb.
- Решением Ученого совета, 125.93kb.
- Федеральная целевая программа "Развитие электронной компонентной базы и радиоэлектроники", 3538.74kb.
- Бийский технологический институт (филиал), 2586.35kb.
- Министерство образования и науки федеральное агентство по образованию майкопский государственный, 102.13kb.
Широко изучалось использование в нитрационных кислотных смесях хлорированных углеводородов. В одной из первых работ в этой области Роговин и Парадия применили эмульсию азотной кислоты в четыреххлористом углероде и пентане с добавкой нафтенсульфоновых кислот (эмульгаторы). При использовании нитрующей кислотной смеси состава: 7,5 % азотной кислоты, 15 % серной кислоты, 75 % четыреххлористого углерода – получали нитраты целлюлозы с содержанием азота 10,9 %. Данный метод позволяет уменьшить расход азотной кислоты. При использовании смеси четыреххлористого углерода и азотного ангидрида можно получить стойкие высокоазотные нитраты целлюлозы с 14,1 % азота.
Ведутся работы по изучению этерификации целлюлозы азотной кислотой в присутствии хлористого метилена. Меняя соотношение компонентов нитрующей смеси, можно получать различные виды нитратов целлюлозы. Все нитраты целлюлозы, полученные в присутствии хлористого метилена, более стойки, чем образцы с тем же содержанием азота, полученные при использовании промышленных серно-азот-ных нитрационных кислотных смесей. Это позволяет упростить стабилизацию, сводя ее к многократным промывкам нитрата целлюлозы водой.
Наряду с хлорированными углеводородами для этерификации используются и другие индифферентные органические растворители. Так, высокоазотные нитраты целлюлозы могут быть получены при использовании смесей азотной кислоты с н-гептаном или нитробензолом. Особый интерес представляет процесс этерификации в нитрационных смесях, которые растворяют нитраты целлюлозы и в которых реакция может закончиться в гомогенной среде, например, в азотной кислоте и нитрометане. Нитраты целлюлозы в этом случае высаживают значительным количеством воды.
Гомогенно заканчивается этерификация и при использовании тройной системы – азотная кислота, хлористый метилен, хлороформ. При этом можно получать более однородные нитраты целлюлозы. Эти методы уже вышли из стадии лабораторных исследований.
1.9.4.4 Различные целлюлозосодержащие материалы,
используемые для изготовления целлюлозы
Вначале для изготовления целлюлозы применялся дорогостоящий хлопок. К 1904 г. целлюлозу начали изготовлять из линтера, снимаемого из хлопкового семени. Преимуществом линтера по сравнению с хлопком является его более низкая стоимость и легкость обработки при этерификации и последующем технологическом процессе.
Абель предложил также использовать хлопчатобумажные концы или угары с прядильных фабрик, которые предварительно должны пройти обработку. Для получения нитратов целлюлозы хлопок имеет наибольшее содержание α-целлюлозы. Другим наиболее целлюлозосодержащим видом сырья является древесина. Поэтому с самого начала промышленного производства НЦ, наряду с хлопковой целлюлозой, пытались применять древесную целлюлозу, в первую очередь в странах, не имеющих своего хлопка.
Еще в 1892 г. Орловский предложил для получения нитратов целлюлозы использовать древесную целлюлозу в виде тонкой бумаги. Однако при ее переработке в нитраты целлюлозы имелись трудности. Получаемые продукты не были хорошо проэтерифицированы, выход нитратов целлюлозы был на 15–20 % ниже. Поэтому во Франции и США применение древесной целлюлозы начали с ее переработки в смеси с хлопковой.
Лишь в Германии и Австрии во время войны 1914–1917 гг. впервые была применена древесная целлюлоза для изготовления нитратов целлюлозы в виде тонкой гофрированной бумаги алигнина без дополнительного облагораживания. Эта форма целлюлозы применялась и на отечественных заводах, при этом, по сравнению с линтером, выход нитратов целлюлозы и производительность основных аппаратов на
10–15 % выше.
Была установлена возможность использования отбеленной сульфитной древесной целлюлозы с высоким содержанием α-целлюлозы, полученной из древесины хвойных деревьев. Физическая форма целлюлозы имеет большее значение для удовлетворительного и экономического ведения этерификации, чем ее химическая чистота. Отечественными и зарубежными учеными проводились работы по изысканию наиболее оптимальных форм целлюлозы.
Древесная целлюлоза, применяемая для изготовления нитратов целлюлозы, должна удовлетворять следующим требованиям:
- иметь хорошие сорбционные свойства;
- материал во время этерификации должен сохранять форму, не должен распадаться на отдельные волокна. Это обеспечит соответствующий выход нитратов целлюлозы;
- нитраты целлюлозы после этерификации должны сорбировать по возможности малые количества отработанных кислотных смесей, при этом расход кислот сокращается;
- насыпная плотность целлюлозного материала должна быть оптимальной. С повышением плотности увеличивается единовременная загрузка аппаратуры, а, следовательно, и ее производительность. При этом уменьшаются модуль этерификации и количество кислот, находящихся в обороте.
В 1928–1930 гг. во Франции был отработан процесс получения древесной целлюлозы в виде пушистой хлопкообразной массы, сос-тоящей из отдельных рыхлых жгутиков длиной до 10 мм, толщиной до 1–4 мм. Этот материал изготовлялся из высокооблагороженной древесной целлюлозы с содержанием около 96 % α-целлюлозы.
В 40-х годах в отечественной промышленности была обработана и нашла широкое применение в качестве сырья облагороженная сульфитная целлюлоза марки ЦА, которая по форме напоминает пушистую хлопковую массу, состоявшую из отдельных жгутиков. Эта целлюлоза широко применяется и в настоящее время для изготовления нитратов целлюлозы в пороховой промышленности. Однако тонкая рыхлая бумага алигнин и более уплотненная целлюлоза марки ЦА не в полной мере отвечают предельным технологическим требованиям к целлюлозе. Для изготовления ЦА нужны специальные цехи, которые почти бездействуют в мирное время. Кроме того, она неоднородна по вязкости, содержанию непронитрованного остатка, форме жгутика, неоднородна по плотности и размерам жгутика, поверхности целлюлозы разных партий отличаются друг от друга, что отрицательно сказывается на этерификации.
Форма древесной целлюлозы постоянно изменялась. В 1938 г. А.П. Закощиков, П.Д. Герасимов, Р.А. Малахов и другие разработали рациональные методы этерификации уплотненной целлюлозы в форме бумаги, измельченной на соответствующие элементы. Были установлены рациональные требования к ее свойствам в нитрующих кислотных смесях необходимое содержание азотной кислоты. Целлюлоза в форме бумаги перспективный материал. Целлюлоза РБ имеет большую, чем ЦА, насыпную массу (в 2 раза), что позволяет увеличить производительность отдельных фаз производства нитратов целлюлозы. Благодаря компактности РБ сокращаются складские помещения и транспортные расходы. Однако реакционная способность уплотненной целлюлозы ниже, чем целлюлозы ЦА. Кроме того, плотная форма затрудняет обратную диффузию кислот и отбор тепла гидратации. Увеличивается время этерификации, и повышается степень денитрации нитратов целлюлозы. Основной недостаток бумаги из сульфитной облагороженной целлюлозы – неравномерность полотна по плотности и толщине.
Применение данного вида целлюлозы было затруднено из-за отсутствия станка для резки целлюлозного полотна. В 1950 г. такой станок был создан (автор В.В. Кузьмин) и внедрен в промышленность.
С внедрением данного станка в пороховой промышленности началось широкое использование древесной целлюлозы уплотненной формы в виде бумаги.
Однако древесная сульфитная целлюлоза отличается повышенной жесткостью волокна, содержит много органических минеральных примесей, поэтому невозможно применение соответствующих нитратов целлюлозы в производстве, например, баллиститных ракетных порохов. Такие нитраты целлюлозы не обеспечивают стабильной баллистики наиболее ответственных изделий и непригодны для изготовления лаков.
За последнее время повысились тактико-технические требования к зарядам артиллерийских выстрелов и требования к выпускаемым порохам. Важным вопросом является улучшение химической чистоты древесной целлюлозы, доведение ее до уровня хлопковой.
Вместе с тем развитие пороховой промышленности требует новых сырьевых ресурсов. Высококачественные сорта беленой предгидролизной сульфатной целлюлозы имеют преимущества по сравнению с сульфитной. Поэтому для расширения сырьевой базы можно применять сульфатную целлюлозу. Ее в большом количестве выпускает целлюлозно-бумажная промышленность.
В отличие от сульфитной для варки сульфатной целлюлозы применяются не кислые растворы бисульфита кальция и свободная сернистая кислота, а щелочные растворы, содержащие в своем составе гидроксид натрия, сернистый натрий и ряд других солей. Сульфитную целлюлозу изготовляют из древесины ели, пихты и других, сульфатную – из лиственных пород деревьев, запасы которых у нас значительно большие.
Работы по изучению использования сульфатной целлюлозы в производстве нитратов целлюлозы для изготовления пироксилиновых и баллиститных порохов были начаты еще в довоенные годы. Были выпущены образцы в виде РБ, переработанные в пороха, которые отвечали всем тактико-техническим требованиям.
Сульфатная целлюлоза была рекомендована для внедрения в пороховую промышленность, однако из-за отсутствия производственной базы это решение не было реализовано.
В настоящее время для изготовления нитратов целлюлозы используются хлопковая и древесные сульфитная и сульфатная целлюлозы.
Хлопковая целлюлоза. В хлопковой целлюлозе содержание
α-целлюлозы больше, чем в древесных, что определяет ее химическую чистоту. Отсутствие в ней гидрофобных примесей (смол, лигнина) улучшает ее смачивающие свойства, увеличивает выход нитратов целлюлозы, а также обусловливает сохранение ее физико-химических свойств при длительном хранении. Благодаря высокой реакционной способности и химической чистоте хлопковую целлюлозу можно использовать для изготовления качественных нитратов целлюлозы, в основном, высококачественных коллоксилинов для производства баллиститных порохов, коллоксилинов типа BHBA, ПСВ, целлулоидного, пироксилина № 2, ацетил-целлюлозы.
Сульфитная древесная целлюлоза. Эта целлюлоза содержит меньшее количество α-целлюлозы по сравнению с хлопковой и значительное количество гидрофобных примесей (смол, лигнина). Эти примеси под действием кислорода воздуха и света способны изменяться, что приводит к нестабильности ее свойств при хранении (целлюлоза гидрофобизируется – «стареет»). Так, например, после 5–7 месяцев хранения смачиваемость целлюлозы значительно уменьшается, что отрицательно сказывается на процесс этерификации. Сульфитная целлюлоза ЦА и РБ выпускается двух марок: марки «К» для изготовления коллоксилинов; марки «П» – для изготовления пироксилина № 1.
Сульфатная древесная целлюлоза. Эта целлюлоза характеризуется лучшей степенью облагораживания, чем сульфитная, и содержит меньше целлюлозных гидрофобных примесей. Впитывающие свойства сульфатной целлюлозы в отличие от сульфитной в течение длительного времени не изменяются. По основным показателям (содержание
α-целлюлозы, смол, впитываемость для РБ, смачиваемость для ЦА) эта целлюлоза приближается к хлопковой. Степень набухания сульфатной целлюлозы больше, чем сульфитной, ее реакционная способность выше. По скорости этерификации, количеству адсорбированных кислот и скорости фильтрации она также приближается к хлопковой целлюлозе.
Сульфатная целлюлоза применяется для изготовления коллоксилинов «Н», лаковых коллоксилинов и других видов нитратов целлюлозы.
Композиционная бумага (КБ). Композиционная бумага состоит из 60 % целлюлозы из линта аэрохимического съема и 40 % древесной целлюлозы марки РБ и по своим физико-химическим показателям соответствует целлюлозе марки РБ. Рекомендованная для внедрения в пороховую промышленность, композиционная бумага позволяет использовать короткошпательный линт в промышленности.
1.9.4.5 Технология изготовления нитратов целлюлозы
Технологический процесс изготовления нитратов целлюлозы складывается из следующих операций:
- подготовка целлюлозы;
- подготовка рабочей кислотной смеси;
- нитрация целлюлозы;
- рекуперация кислот;
- стабилизация нитратов целлюлозы;
- смешение частных партий НЦ в общие;
- отжим НЦ от воды.
Подготовка целлюлозы. Подготовка целлюлозы к этерификации заключается в ее механической обработке с последующей сушкой. Известно, что форма и физическое состояние целлюлозы оказывают на результаты этерификации не меньшее влияние, чем степень ее химической чистоты или состав нитрационной кислотной смеси. Целлюлоза рыхлой формы марок ХЦ и ЦА поступает в производство в виде кип, а плотной формы в виде бумаги марки РБ в рулонах. Для придания целлюлозе хорошей смачиваемости нитрационными кислотными смесями и обеспечения равномерности ее этерификации предварительно все марки целлюлозы измельчаются и подсушиваются до влажности не более 5 %.
Хлопковую целлюлозу и древесную целлюлозу ЦА разрыхляют на кипорыхлителях, а древесную целлюлозу РБ разрезают на резательных станках СРЦ-К (автор В.В. Кузьмин).
Ранее рыхление кип и сушку целлюлозы осуществляли на отдельных аппаратах с последующим транспортированием на фазу этерификации.
В настоящее время на всех заводах установлены измельчительные станки целлюлозы вместе с пневмотранспортными сушильными агрегатами. Такие установки обеспечивают непрерывность процесса рыхления кип целлюлозы или резки бумаги, сушки и транспортирования подсушенной целлюлозы на фазу этерификации.
Установка (рисунок 9) состоит из кипорыхлителя 4 и резательного станка типа СРЦ-К 9, пневмотранспортного агрегата, включающего калориферную установку с вентилятором 1, конфузорно-диффузорные воронки 5, пневмотранспортную сушильную трубу (собственно сушку), приемные бункеры 7, 8, камеру улова пыли 3, вентилятор 2 для выброса отходящего воздуха в атмосферу.
Подготовка целлюлозы марок ХЦ и ЦА к этерификации. До подачи на этерификацию кипы целлюлозы марок ХЦ и ЦА должны быть разрыхлены, после чего она должна быть однородна по величине частиц и не иметь в своем составе неразрыхленных комков. Разрыхлением целлюлозе придается не только улучшенная реакционная способность, но обеспечивается транспортабельность ее в пневмотранспортной трубе. Рыхление целлюлозы осуществляется на кипорыхлителях.
Кипорыхлитель (рисунок 10) имеет три быстро вращающихся в одном направлении рыхлительных барабана, два из которых разрыхляют кипу целлюлозы, а один выбрасывает разрыхленную целлюлозу в разгрузочную воронку.
Кипорыхлитель состоит из механизма рыхлительных барабанов 1 и транспортера подачи кип целлюлозы к механизму рыхления 2. Рыхлительный механизм включает корпус 14, в котором смонтированы три рыхлительных барабана 9, 15, 18 с закрепленными на поверхности рыхлительными зубьями. Всем трем барабанам передается вращение от электродвигателя 13 через клиноременную передачу 12.
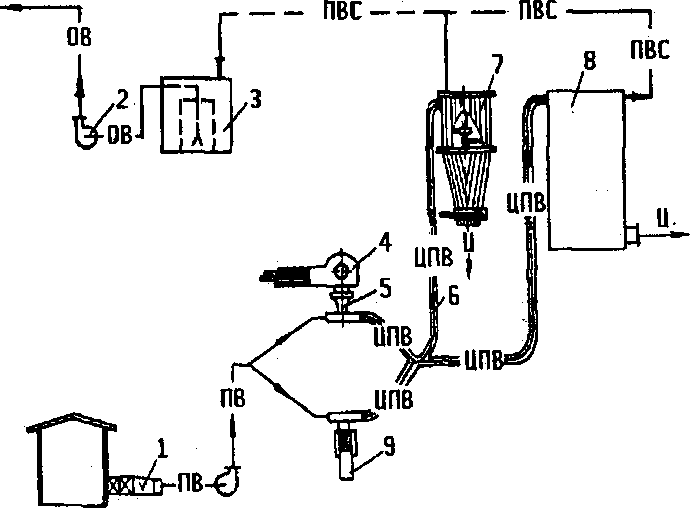
ПВ подогретый воздух; ЦПВ целлюлоза с подогретым
воздухом; ПВС паровоздушная смесь; ОВ осветленная вода
Рисунок 9 Технологическая схема фазы измельчения и сушки
целлюлозы
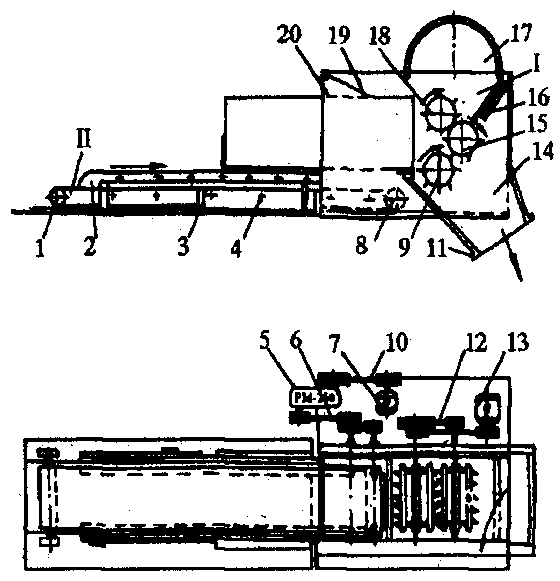
Рисунок 10 Кипорыхлитель
Рыхлительные барабаны закрыты кожухом-ловушкой 17, в котором имеется на шарнирах наклонная плоскость 16. Ловушка в нижней части заканчивается патрубком 11, присоединенным к загрузочному патрубку конфузорно-диффузорной воронки. Транспортер подачи кип к рыхлительному агрегату состоит из рамы 3, на которой смонтированы приводной 8 и натяжной 1 барабаны транспортерной ленты 2, и поддерживающих роликов 4. Для направления движения кипы целлюлозы со стороны рыхлительного механизма имеются боковые щеки 20, на которых смонтирована защитная заслонка 19. Вращение от электродвигателя 7 приводному барабану передается через клиноременную передачу 10 на редуктор 5 и клиноременную передачу 6 на приводной вал транспортера.
Работа кипорыхлителя. Распакованная кипа целлюлозы укладывается на транспортер вдоль оси движения транспортерной ленты 2 и подается в рыхлительный механизм. С помощью зубьев, закрепленных на передних рыхлительных барабанах 9, 18, при вращении последних кипа разрыхляется и разрыхленная целлюлоза попадает в ловушку 17, из ловушки по наклонной плоскости 16 – под воздействие барабана 15. Часть целлюлозы нижним барабаном 9 увлекается в патрубок 11, на пути вновь подхватывается зубьями барабана 15. Пройдя многократную обработку, разрыхленная целлюлоза марки ЦА и марки ХЦ поступает в загрузочный бункер конфузорно-диффузорной воронки пневмотранспортной сушильной трубы.
Степень рыхления можно регулировать скоростью транспортерной ленты, с увеличением скорости степень рыхления уменьшается, и, наоборот, с уменьшением скорости степень рыхления увеличивается.
Подготовка целлюлозы марки РБ к этерификации. Механическая подготовка полотна бумаги к этерификации сложнее, чем подготовка рыхлых форм целлюлозы. Высокая механическая плотность бумаги требует сложных конструкций измельчительных механизмов.
На этерификацию полотна бумаги влияют не только технологические, но и физические факторы, т.е. не только плотность, влажность бумаги, величина ее элементов, но и состояние поверхностей нитруемых элементов. Впитывающие свойства полотна бумаги со стороны образующих его плоскостей имеют меньшую степень, чем свежеобразованные торцевые поверхности. Реакционная способность у вновь образованной поверхности зависит от чистоты среза: чем чище поверхность среза, тем выше его реакционная способность. Чистота среза также необходима и для обеспечения одновременной пропитки кислотами волокон целлюлозы, расположенных в этой поверхности, лучшей отдачей кислоты при ее вытеснении. Кроме того, высокая степень чистоты характеризуется и меньшим количеством пыли. Таким образом, механическая подготовка полотна бумаги к этерификации должна заключаться не только в увеличении ее поверхности, но и в обеспечении ее высокой реакционной (впитывающей) способности. Это достигается раскрытием глубинных слоев материала в полотне бумаги при чистом срезе, обеспечивающем перерезание отдельных волокон в направлении, перпендикулярном их расположению, а также образованием такой формы отдельных элементов, в которой вновь образованная торцевая поверхность имеет наибольшую величину по сравнению с ее основной поверхностью.
Наиболее выгодна форма элемента сечки в виде ромба. Общая реакционная площадь частицы при этом возрастает на 27 % по сравнению с квадратной при одновременном увеличении торцевого параметра на 27 %.
Таким образом, механическая подготовка полотна бумаги перед этерификацией сложна и ответственна. Сложность этой операции заключается в том, что 1 м2 бумаги надо разрезать не менее чем на 10800 отдельных элементов, которые имеют площадь 10–25 мм2 и чистый срез, сохраняющий исходную плотность, и обладают хорошей реакционной способностью. Для получения чистого среза бумажного полотна необходимо иметь минимальные зазоры между режущими лезвиями около 1012 мкм. Решающим фактором является скорость резания. Для резки бумаги наиболее подходят дисковые ножи. Степень чистоты среза также зависит и от механической прочности бумажного полотна, которая определяется его поверхностной плотностью (г/м2), средней плотностью (г/м3), влажностью и толщиной бумажного полотна.
Для придания бумажным элементам ромбовидной формы продольно разрезанное полотно должно располагаться по оси его движения под углом, затем поступать под валки дисковых ножей, и полоски разрезаются в поперечном направлении, образуя бумажные элементы ромбовидной формы заданных размеров. Был разработан и внедрен в промышленность станок для резки бумаги типа СРЦ-К, отвечающий этим требованиям.
Станок СРЦ-К (рисунок 11) состоит из узла раскатов, на которых устанавливаются бумажные рулоны 10, узла продольной резки с гребенкодержателем 2. Над узлом продольной резки имеются валки подачи 9 бумажного полотна в механизм продольной резки.
Под механизмом продольной резки находится бункер-укладчик 12. Для резки «зиг-полотна» имеется механизм поперечной резки 15. Вращение всех узлов осуществляется от электродвигателя 5 через редуктор 8. Механизму продольной резки вращение передается от редуктора, механизму поперечной резки – через промежуточный приводной вал 3 и коническую зубчатую передачу. Электродвигатель имеет автоматическое пускорегулирующее устройство 6 с реле времени и кнопками «пуск» и «стоп» 7. Все узлы станка расположены на плите 4.
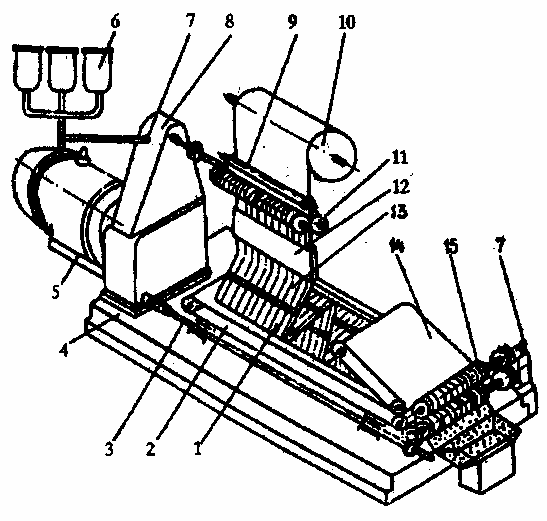
Рисунок 11 Станок СРЦ-К
Механизм продольной резки состоит из дисковых ножей диаметром 156 мм и толщиной 3 мм, смонтированных на валах. Меняя толщину ножей, можно получить сечку с разными размерами. На каждом валу имеется по 173 ножа, что составляет длину режущей части вала, равную 1050 мм из расчета резания полотна бумаги шириной 1 м. Между дисковыми ножами установлены распорные кольца толщиной
3 мм и наружным диаметром 100 мм. Они образуют между ножами пазы, в пространство которых помещены ножи соседнего валка. Конструкция дисковых ножей исключает их боковое смещение, так как по обе стороны ножей происходит процесс резания бумаги, и они взаимно уравновешиваются. Установленные зазоры между лезвиями ножей сох-раняются в течение работы и не изменяются при изменении толщины бумаги.
Вдоль осей по образующей поверхности ножей продольной резки имеются канавки квадратного сечения (3×3 мм), которые выводят ножи из зацепления, при этом бумага не прорезается, и продольные полоски скрепляются между собой поперечными перемычками шириной 3 мм через каждые 225 мм, и образуется «сетчатое полотно».
Режущие валы механизма поперечной резки аналогичны валам механизма продольной резки, за исключением того, что они не имеют на образующей поверхности ножей канавок для образования перемычек и короче первых на 200 мм. Укорочение вызвано необходимостью избежать прогиба валов, так как усиление изгиба при резке трех-четырех слоев «зиг-полотна» больше, чем при резке одного полотна. Глубина посадки ножей не должна быть более двух толщин разрезаемого полотна 0,4–0,5 мм для узла продольной резки и 1,2–1,5 мм для узла поперечной резки.
Скорость продольной резки принята 150–200 м/мин, поперечной резки – в три раза меньше.
Работа станка заключается в следующем: рулон бумаги устанавливается в механизм раската, и бумажное полотно заправляется в валики подачи (см. рисунок 11). Включением кнопки «пуск» станок запускается в работу, с помощью автоматического электропускателя постепенно нарастает частота вращения рабочих валиков до максимальной. После продольной резки полученное «сетчатое полотно» бумаги 13 поступает в бункер-укладчик 12. Накладываясь друг на друга, два направления движения полотна – колебательное в бункере-укладчике 12 и прямолинейное на нижнем транспортере 2 – на ленте последнего «сетчатое полотно» образуют «зиг-полотно» 1.
По мере продвижения «зиг-полотна» к дисковым ножам поперечной резки верхний транспортер 14 сжимает его, и в сжатом состоянии «зиг-полотно» поступает на резку. После поперечной резки бумаги получается сечка размером 3−3 мм или 6−6 мм.
Кипорыхлители и резательные станки являются также и дозаторами подачи целлюлозы в загрузочный бункер конфузорно-диффу-зорной воронки.
Равномерная влажность высушенной целлюлозы может быть достигнута при одинаковой начальной ее влажности и однородности массовой концентрации целлюлозы в воздухе. С повышением массовой концентрации процесс сушки ухудшается.