Федеральное агентство по образованию бийский технологический институт (филиал)
Вид материала | Учебное пособие |
- Федеральное агентство по образованию бийский технологический институт (филиал), 981.77kb.
- Федеральное агентство по образованию бийский технологический институт (филиал), 1531.98kb.
- Федеральное агентство по образованию Бийский технологический институт (филиал), 2694.55kb.
- Федеральное агентство по образованию бийский технологический институт (филиал), 2134.54kb.
- Федеральное агентство по образованию бийский технологический институт (филиал), 1660.78kb.
- Федеральное агентство по образованию бийский технологический институт (филиал), 1946.38kb.
- Решением Ученого совета, 125.93kb.
- Федеральная целевая программа "Развитие электронной компонентной базы и радиоэлектроники", 3538.74kb.
- Бийский технологический институт (филиал), 2586.35kb.
- Министерство образования и науки федеральное агентство по образованию майкопский государственный, 102.13kb.
Технологический процесс смешения топливных масс и формирования зарядов определяется вязкостью топливной массы.
Высоковязкие топливные массы с содержанием полимера до 10 % в основном перерабатываются методом глухого или проходного прессования, при содержании до 15 % методом литья под давлением, при содержании полимера 15–20 % перерабатываются методом свободного литья. Принципиальная схема технологического процесса приготовления топливных масс и изготовления зарядов представлена на рисунке 53.
Технологический процесс изготовления зарядов СРТТ является сложным и многостадийным. Он включает в себя ряд фаз и операций, отличающихся как по физической сущности, так и аппаратурному оформлению.
Анализ принципиальной технологической схемы изготовления зарядов показывает, что независимо от габаритов заряда и способа его изготовления принципиальные отличительные признаки имеют место только на фазах смешения топливной массы и формования зарядов.
Операции подготовки компонентов и приготовления полуфабрикатов (РСП и паста), технологической оснастки и прессформ, корпусов, а также вулканизация (отверждение топливной массы) и концевые операции (распрессовка, контроль качества и механическая доработка зарядов) имеют место в каждом из способов производства.
С целью сокращения продолжительности технологического цикла изготовления зарядов технологией предусмотрено параллельное выполнение работ по следующим фазам и операциям:
- подготовка компонентов РСП и ее наработка;
- подготовка компонентов пасты и их смешение;
- подготовка технологической оснастки (прессформы) и корпуса и их сборка;
- ревизия аппарата смешения и его обкатка на холостом ходу.
3
4
7
6
5





1
10
9
8




2
14



15
18
17
16
13
12
11





1 – смешение топливной массы; 2 – формование (изготовление) заряда; 3 – подготовка компонентов рабочей смеси порошков (РСП); 4 – приготовление РСП; 5 − подготовка компонентов пасты; 6 – приготовление (смешение) пасты; 7 – изготовление передового образца из полуфабрикатов и выдача рекомендаций по их использованию; 8 − приготовление антиадгезива; 9 – подготовка технологической оснастки и прессформы;
10 – нанесение антиадгезива на технологическую оснастку и прессформу; 11 – приготовление клеевого состава; 12 – подготовка теплозащитного слоя корпуса; 13 – нанесение клеевого состава на поверхность теплозащитного слоя; 14 – сборка корпуса (прессформы) с технологической оснасткой; 15 – вулканизация (отверждение) топливной массы; 16 – распрессовка; 17 – контроль качества заряда; 18 – механическая доработка заряда
Рисунок 53 − Принципиальная технологическая схема изготовления зарядов СРТТ
Таким образом, технологическим процессом предусмотрено: к моменту начала смешения топливной массы должны быть наработаны РСП и паста, подготовлен аппарат смешения, а также должна быть подготовлена технологическая оснастка и собрана с корпусом.
Технологический процесс производства СРТТ в США представлен на рисунке 54 [49].
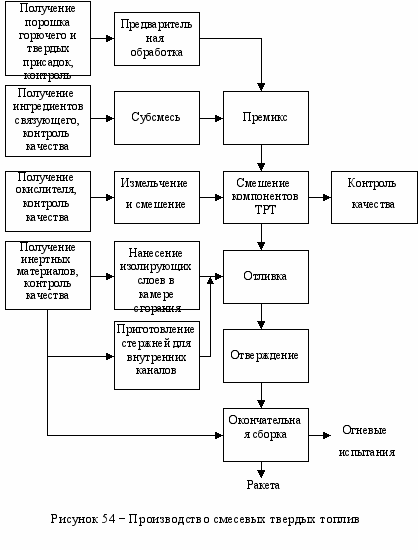
Как показывает анализ, и в технологическом процессе изготовления зарядов, разработанном в США, центральное место занимают операции смешения компонентов РТТ и отливка заряда.
2.7.2.1 Приготовление рабочей смеси порошков
Рабочая смесь порошков представляет собой механическую смесь минерального окислителя, отвердителя, эксплуатационной добавки и антислеживающего вещества. Все компоненты, входящие в состав РСП, должны иметь неорганическую природу.
Категорически запрещается вводить в РСП компоненты, име-ющие органическую природу, а также металлические горючие, сплавы металлов и их гидриды.
Основным компонентом РСП является окислитель, роль которого в большинстве рецептур как у нас, так и за рубежом (США, Франция) выполняет ПХА, выпускаемый в соответствии со строгими техническими условиями (ТУ). Наиболее трудоемкой операцией приготовления РСП является подготовка ПХА, т.к. от его влажности, формы частиц и их распределения по размерам зависят как реологические свойства топливных масс, так и физико-механические характеристики топлива.
Установлено, что наилучшие результаты достигаются при использовании ПХА с двух- или трехфракционным составом, т.к. такое распределение позволяет добиться плотной упаковки частиц и минимального расстояния между ними.
Получение требуемого распределения частиц по размерам и выполнение предусмотренных ТУ размеров и формы частиц являются важнейшими задачами процесса приготовления окислителя. Крупные фракции частиц ПХА поступают в специальном контейнере УК-1 или УК-1М (рисунок 55) с требуемым гранулометрическим составом и влажностью [48].
Транспортный контейнер УК-1 предназначен для транспортирования, хранения и смешения сухих порошкообразных ВМ в производствах ЭКС. Он имеет два варианта исполнения, которые отличаются друг от друга только формой защитных мембран (ЗМ) у вышибных поверхностей (ВП): прямоугольной и круглой. Транспортные контейнеры УК-1 могут изготавливаться как из нержавеющей стали (УК-1М), так и из алюминия (УК-1А). В целях обеспечения безопасности для каждого ВМ определяется свой коэффициент заполнения (КЗ) [52].
Конструктивно транспортный контейнер (ТК) УК-1 выполнен в виде жесткого металлического корпуса 3, сверху которого имеется загрузочный люк 2, а сбоку выгрузочный люк 5, закрываемый крышкой. Две боковые и задняя стенки контейнера имеют окна 1, которые закрываются защитными мембранами 4 (вставками − вышибными поверхностями). Герметичность соединения ЗМ и корпуса обеспечивается прокладкой 6, которая поджимается фланцем 7. Для предохранения ЗМ от разрушения при транспортировании и хранении (в случае удара) установлена крупноячеистая сетка.
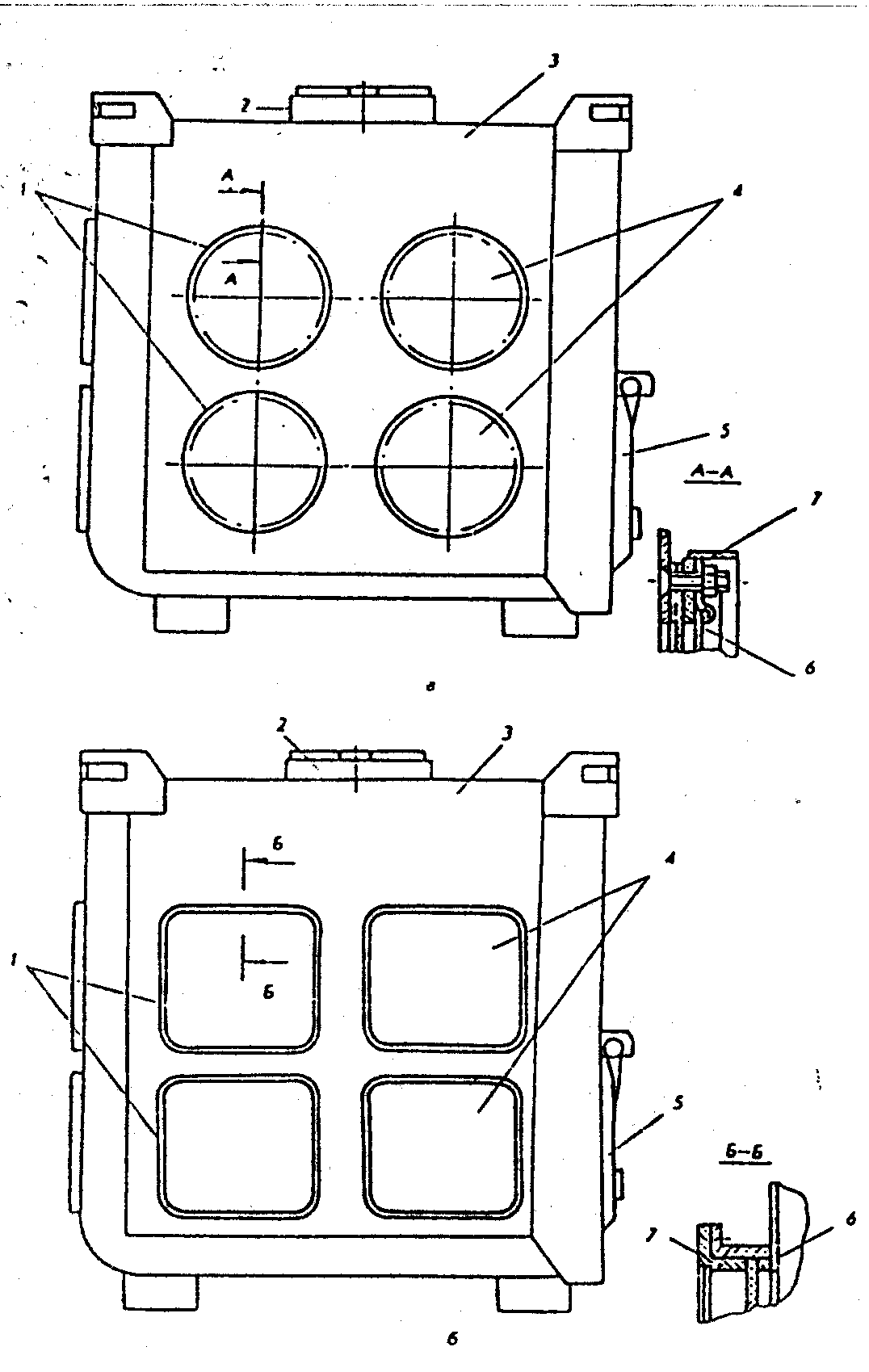
1 − окна; 2 − загрузочный люк; 3 − корпус; 4 − защитные мембраны;
5 − выгрузочный люк; 6 − резиновая прокладка; 7 − прижимной фланец
Рисунок 55 − Транспортный контейнер УК-1М: а − с круглыми
защитными мембранами; б − с квадратными защитными мембранами
Общая площадь поверхностей мембран составляет 21 % (для ряда ВМ 40 %) всей поверхности аппарата. В качестве материала для вышибных элементов используется электропроводящий полипропилен − СПП толщиной 3 мм. Применение данного материала продиктовано конструктивными соображениями: при достаточной жесткости и прочности этот материал имеет небольшую плотность (около 0,3 г/см3).
Технические характеристики ТК УК-1М:
Объем | около 1,13 м3. |
Диаметр загрузочного люка | 200 мм. |
Габаритные размеры выгрузочного люка | 780×380 мм. |
Габаритные размеры УК-1М, м: длина ширина высота | 1,3; 1,0; 1,2. |
Масса | 280 кг. |
Контейнер УК-1М выполнен из нержавеющей стали, кроме крышки выгрузочного алюминиевого люка, которая оснащена резиновой прокладкой. В загрузочный люк вставляется патрон с силикагелем для поглощения влаги. В крышке загрузочного люка закреплены два клапана, которые предназначены для уравнивания давления внутри контейнера с внешним атмосферным давлением. Описанная конструкция прошла широкие испытания, которые показали ее хорошую взрывобезопасность.
Для проведения операции смешения контейнер ставится на специальную раму с гидроприводом, которая осуществляет его вращение.
Созданный ТК УК-1 позволяет расширить область его применения, в частности, использования в технологических поточных линиях для межфазового транспортирования, приготовления РСП и накопления РСП.
Получение готовых смесей порошков в единых унифицированных контейнерах УК-1 и доставка их на фазу заполнения контейнерным способом значительно упрощают транспортирование, снижают потери продукта и опасность процесса, стабилизируют технологические параметры, обеспечивают гибкость и мобильность технологического процесса в части приготовления как малых, так и крупных партий полуфабрикатов. В этом случае контейнер УК-1 используется в качестве смесительной емкости или емкости для «освежения» (взрыхления) РСП после длительного хранения или транспортирования.
Мелкую фракцию с размером частиц менее 50 мкм получают измельчением «отсева» на специальных мельницах. Для приготовления РСП можно использовать контейнер КС-4А (рисунок 56) или смеситель ССК-1 (рисунок 57) [48].
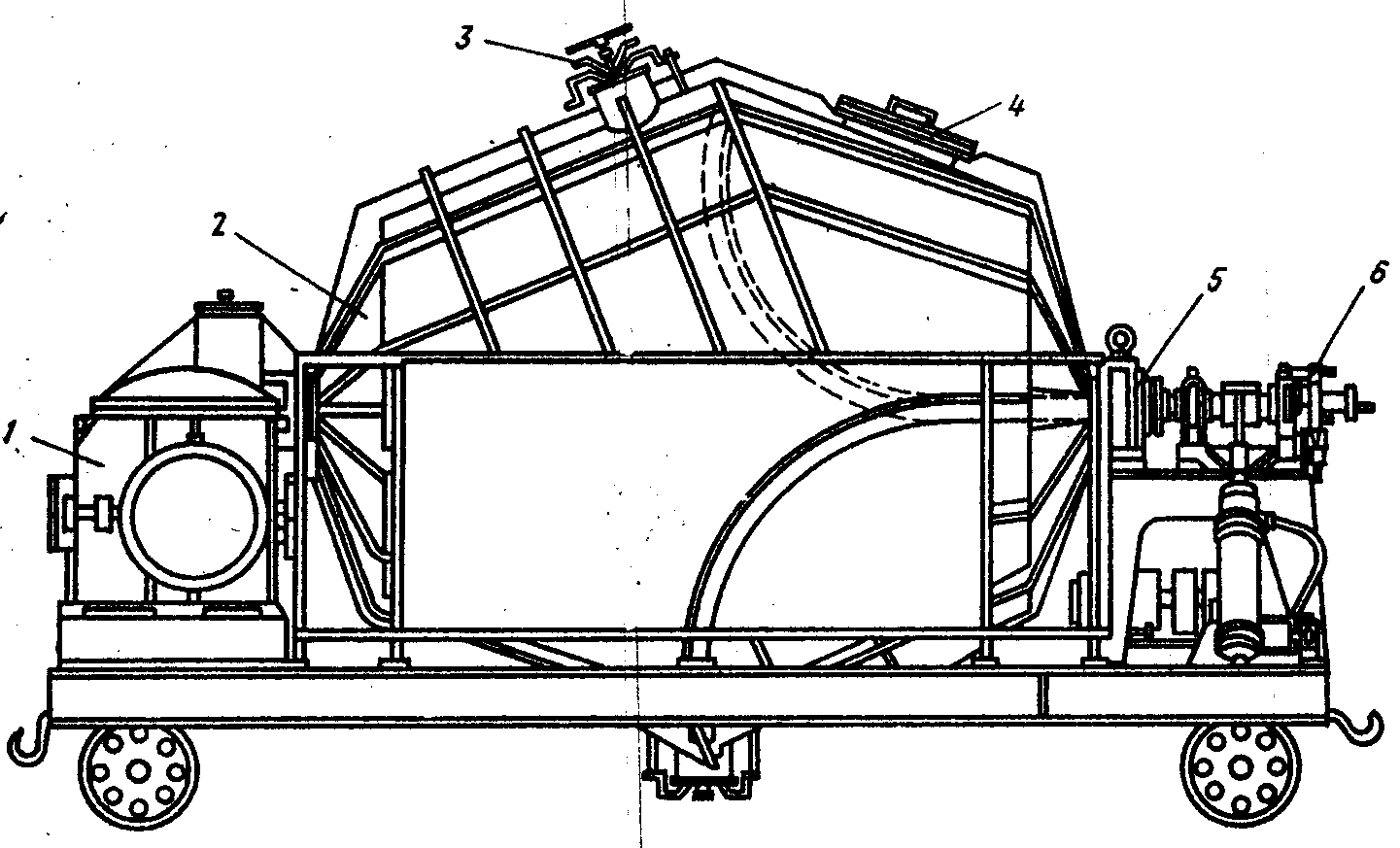
1 − привод ротора; 2 − ротор; 3 − загрузочный люк; 4 − лаз с вышибной крышкой; 5 − загрузочное сопло; 6 − коллектор
Рисунок 56 − Контейнер-смеситель КС-4А
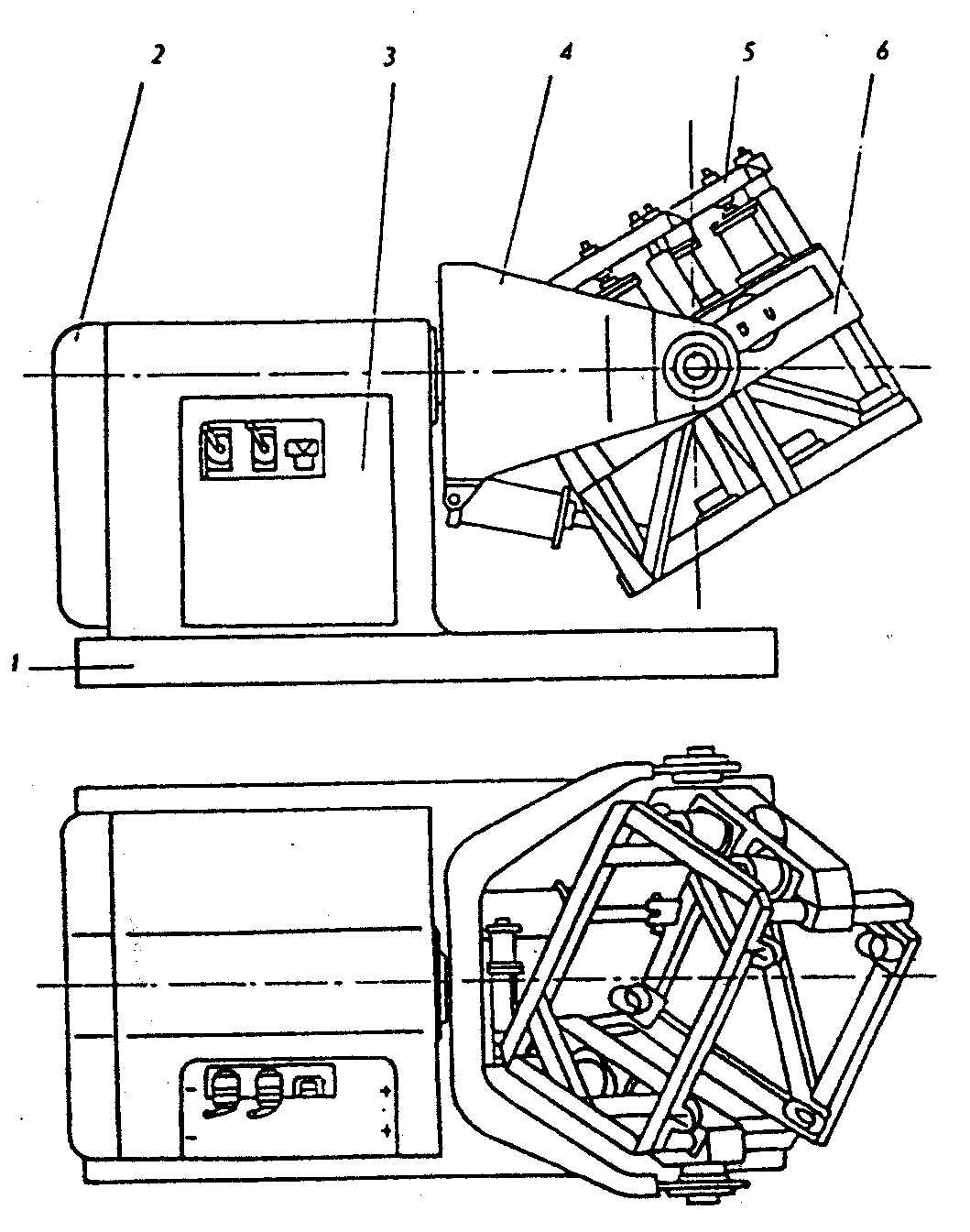
1 − корпус (сварная рамная конструкция); 2 – дверь для обслуживания привода; 3 – боковой люк; 4 – шарниры поводковой вилки;
5 – траверса; 6 – ложемент контейнера
Рисунок 57 − Смеситель ССК-1
В сравнении с двухопорной конструкцией в смесителе ССК-1 консольного типа (см. рисунок 56) представляется большая свобода при манипуляциях с контейнером во время работы. Все узлы смесителя ССК-1 закреплены на корпусе 1, который представляет собой сварную рамную конструкцию, обеспечивающую необходимую устойчивость и прочность при воздействии динамических нагрузок.
Ложемент 6 контейнера установлен в шарнирах 4 поводковой вилки, закрепленной на центральном валу. Внутри герметичного корпуса расположен привод, состоящий из электродвигателя с редуктором и цепной передачи. Здесь для удобства обслуживания предусмотрены дверь 2 и боковой люк 3. Надежное крепление контейнера в ложементе обеспечивается траверсами 5 верхнего и боковых прижимов. Траверсы перемещаются с помощью пневмоцилиндров. В рабочее положение под наклоном ложемент с контейнером устанавливается и фик-сируется также пневмоцилиндрами.
В начале работы ложемент смесителя устанавливается в исходное горизонтальное положение и электропогрузчик вкладывает в него контейнер с продуктом (рисунок 58, положение I).
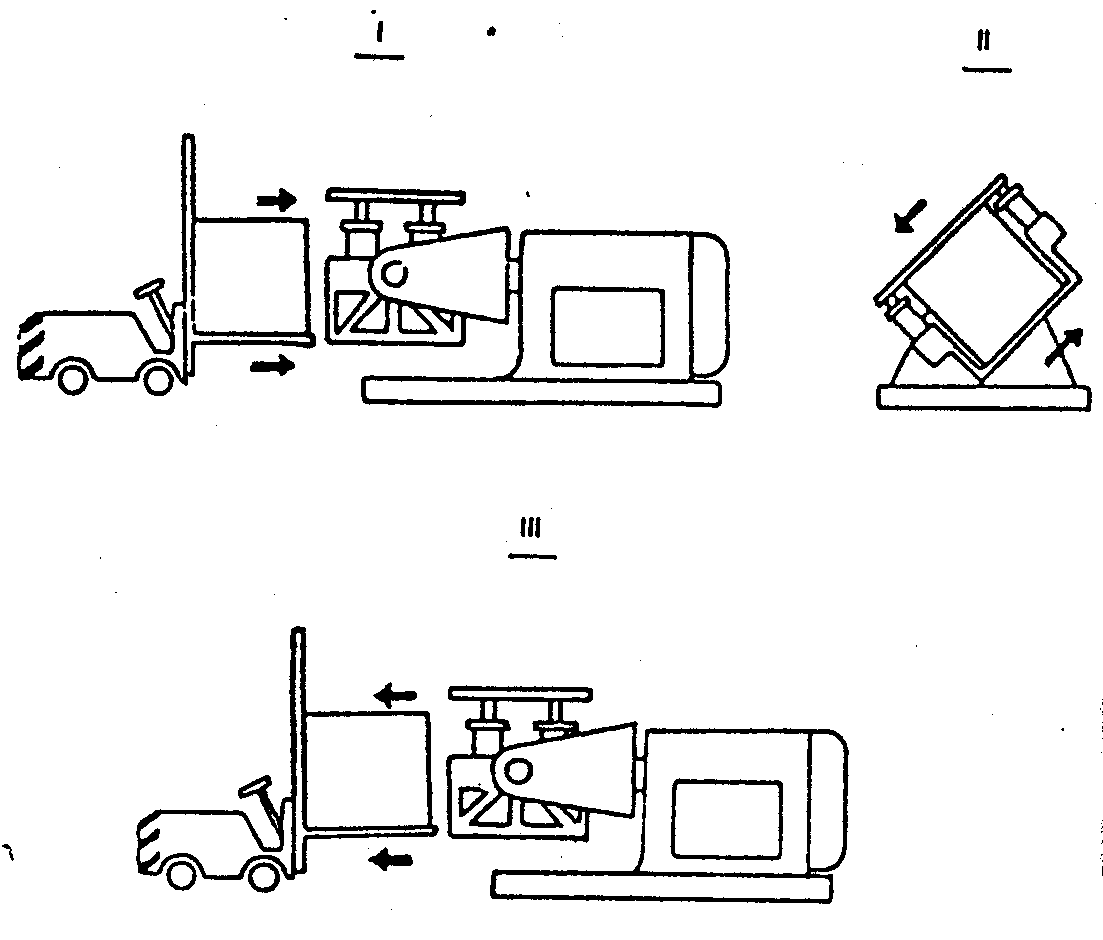
положение I − установка ТК в смеситель ССК-1; положение II − режим перемешивания; положение III − съем ТК
Рисунок 58 − Порядок работы смесителя ССК-1 с ТК УК-1
С пульта управления смеситель включается в работу. Контейнер зажимается, наклоняется и фиксируется в рабочем положении (см. рисунок 58, положение II). В конце операции фиксатор включает вращение контейнера.
По истечении заданного времени вращения электродвигатель отключается, происходят торможение и ориентация ложемента в горизонтальное, а затем в исходное положение. Контейнер освобождается, электропогрузчик снимает и увозит контейнер с готовой смесью (см. рисунок 58, положение III).
Смеситель работает в автоматическом режиме по заданному алгоритму в соответствии с циклограммой. Система управления состоит из пневматической и электрической частей. Предусмотрены все необходимые блокировки, исключающие возникновение аварийных ситуаций.
Информация о готовности к пуску, работе электро- и пневмосистем передается в помещение пультовой.
Схема технологического процесса приготовления РСП в США представлена на рисунке 59 [49].
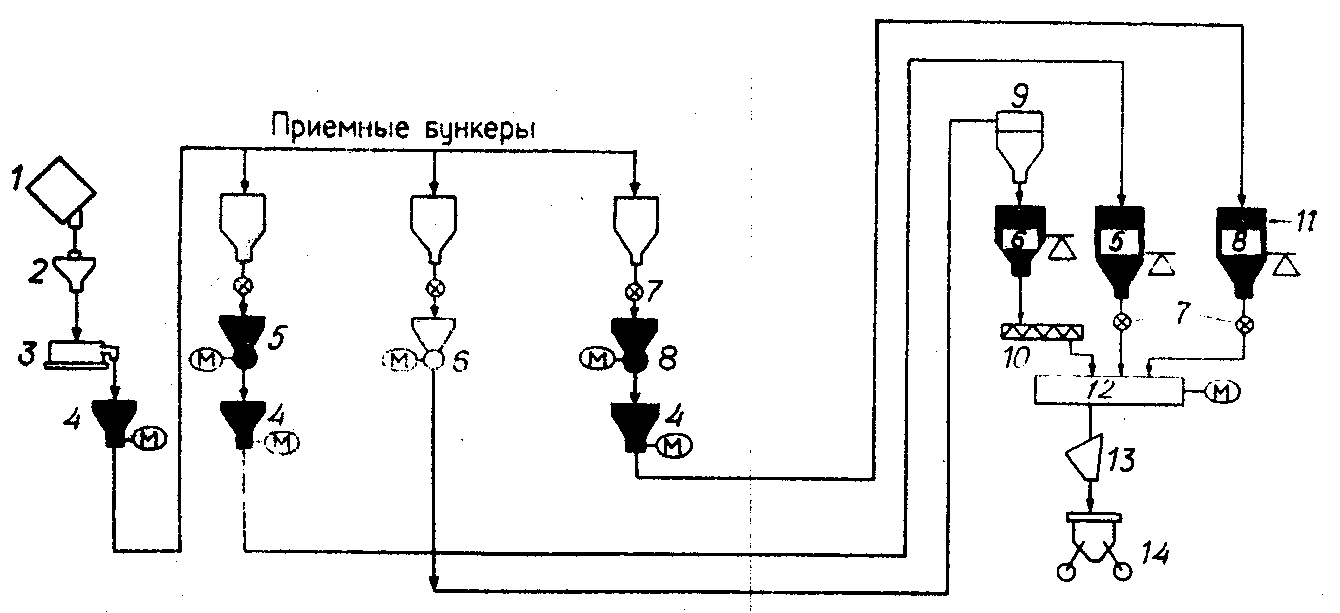
1 − питательный бункер с окислителем; 2 − загрузочное устройство;
3 – сито; 4 − псевдоожижитель; 5 − низкоскоростной
микропульверизатор; 6 − микрораспылитель; 7 − шаровой затвор;
8 − высокоскоростной микропульверизатор; 9 − циклон;
10 − транспортер; 11 − бункер для взвешивания; 12 − смеситель;
13 − контрольное сито; 14 − хоппер с окислителем
Рисунок 59 − Схема установки для приготовления окислителя ТРТ
2.7.2.2 Технологический процесс приготовления пасты
Паста − это высококонцентрированная суспензия. Технологический процесс приготовления пасты преследует две цели:
- флегматизацию энергетической добавки (металлические горючие или их сплавы, гидриды металлов);
- упрощение технологического процесса смешения топливной массы.
В зависимости от вязкости горюче-связующего смешение жидких компонентов с порошкообразными наполнителями может осуществляться по технологическим схемам:
- для низковязких горюче-связующих (вязкость ниже 100 Па·с) с использованием смесителя планетарного типа (рисунок 60);
- высоковязких (вязкость 10001500 Па·с) с использованием смесителя лопастного типа (Вернер-Пфляйдерера) с выгрузочным шнеком, расположенным в нижней части смесителя с последующим усреднением ее в накопительной емкости объемом 13 м3.
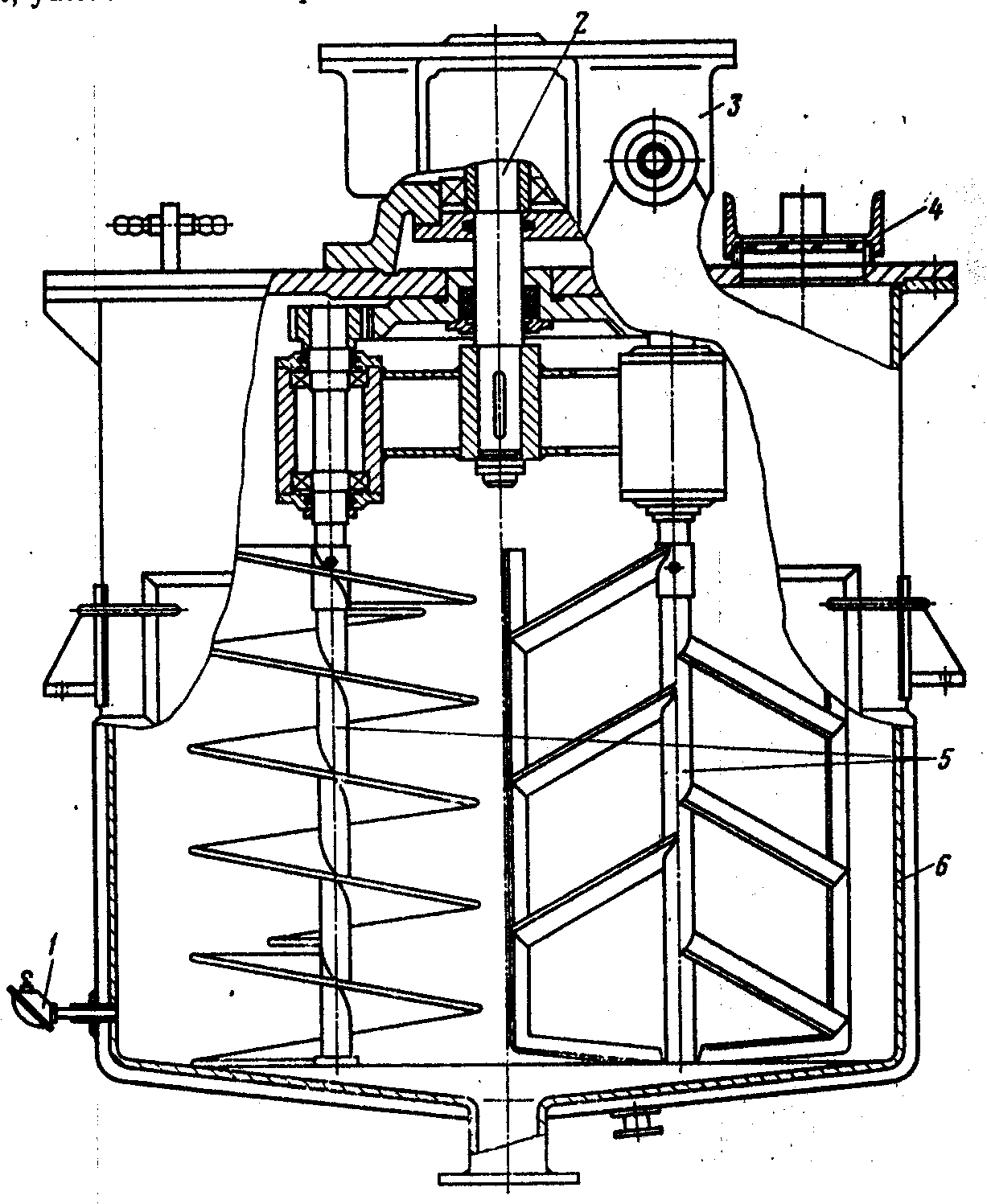
1 − термопара; 2 − вал; 3 − редуктор; 4 − люк; 5 − мешалки; 6 − корпус
Рисунок 60 − Схема планетарного смесителя
Процесс приготовления горючей основы ТРТ и материала для покрытия стенок камеры, разработанной в США, представлен на рисун-ке 61 [49].
На пункте приготовления горючего сначала осуществляется смешение компонентов полимерного связующего и различных добавок, используемых для улучшения физических свойств ТРТ и регулирования скорости горения. Такую смесь называют «субсмесью». Затем в нее добавляют металлический порошок и другие твердые компонен-
ты [49].
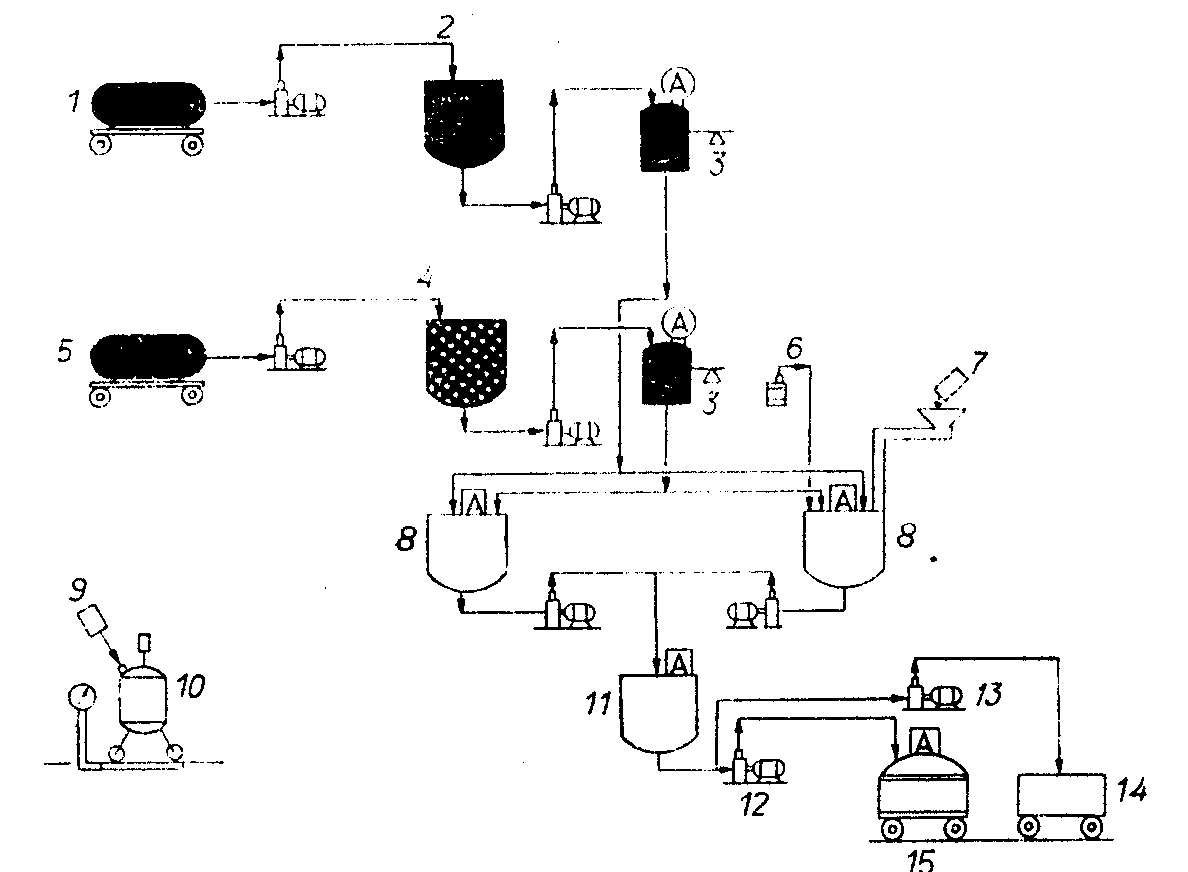
1 − автоцистерна с пластификатором; 2 − резервуар для хранения
пластификатора; 3 − бункер для взвешивания; 4 − резервуар для
хранения жидкого горючего; 5 − автоцистерна с жидким горючим;
6 − дополнительные жидкие ингредиенты; 7 − питатель твердых
ингредиентов; 8 − резервуар приготовления премикса; 9 − ингредиенты изолирующего материала; 10 − передвижной смеситель;
11 − бак-сборник премикса; 12 − перекачивающий насос;
13 − дозирующий насос; 14 − вертикальный тигель со смесью;
15 − передвижной бак с премиксом
Рисунок 61 − Процесс приготовления горючей основы ТРТ
и материала для покрытия стенок камеры
2.7.2.3 Подготовка технологической оснастки
Технологическая оснастка в сборе с корпусом (прессформой) предназначена для формования заряда и определяет его геометрические размеры.
Оснастка делится на основную и вспомогательную. К основной относится та оснастка, рабочие поверхности которой соприкасаются с топливной массой, на нее наносится антиадгезионное покрытие.
Антиадгезионное покрытие − это тонкая пленка, получаемая нанесением раствора силиконового каучука на поверхность оснастки. Наибольшее применение нашел диметилсилоксановый каучук СКТ-40 в виде 7 и 15%-ного раствора в бензине. Наносится послойно. В раствор вводится отвердитель и катализаторы.
2.7.2.4 Подготовка корпусов
Для обеспечения скрепления заряда СРТТ с корпусом и теплозащитным покрытием на последнее наносят клеевой состав. Одним из наиболее эффективных способов надежного крепления заряда к корпусу через ТЗП является совулканизация, протекающая на контактной границе.
Клеевой состав готовится в лопастном смесителе и наносится на поверхность теплозащитного покрытия с помощью установки УП-1 послойно.
Подготовленный корпус с технологической оснасткой собирается на специальном стенде.
2.7.2.5 Смешение топливной массы и формование зарядов
В настоящее время наибольшее применение для изготовления зарядов СРТТ нашли две технологические схемы:
способ литья под небольшим давлением;
свободное литье.
Способ литья под небольшим давлением. Этот способ позволяет перерабатывать топливные массы с общим содержанием наполнителя до 90 % масс.
Особенности отработанной технологии позволяют изготавливать вкладные и прочно скрепленные с корпусом двигателя заряды СРТТ простых и сложных геометрических форм с использованием прецизионного литья без последующей механической обработки, а также получать односоставные, двухсоставные и многослойные заряды.
Максимальный диаметр изготавливаемых моноблочных зарядов СРТТ составляет 2,5 м при массе более 50 тонн. Возможно получение зарядов с массой более 80 тонн диаметром свыше 3 м и со значительно более широкими пределами по габаритам для секционных зарядов, состоящих из отдельных топливных блоков [83].
Технологический процесс смешения топливных масс и формования зарядов по методу литья под давлением проводится в смеситель-ных аппаратах непрерывного действия (СНД). Установка СНД (рисунок 62) позволяет совмещать подачу порошкообразных и жидких компонентов и их непрерывное смешение. Компоненты топлива, дозируемые через синхронную весоизмерительную систему, из расходных емкостей и контейнеров поступают в предварительный смеситель, где происходит смешение порошкообразных и жидковязких компонентов.
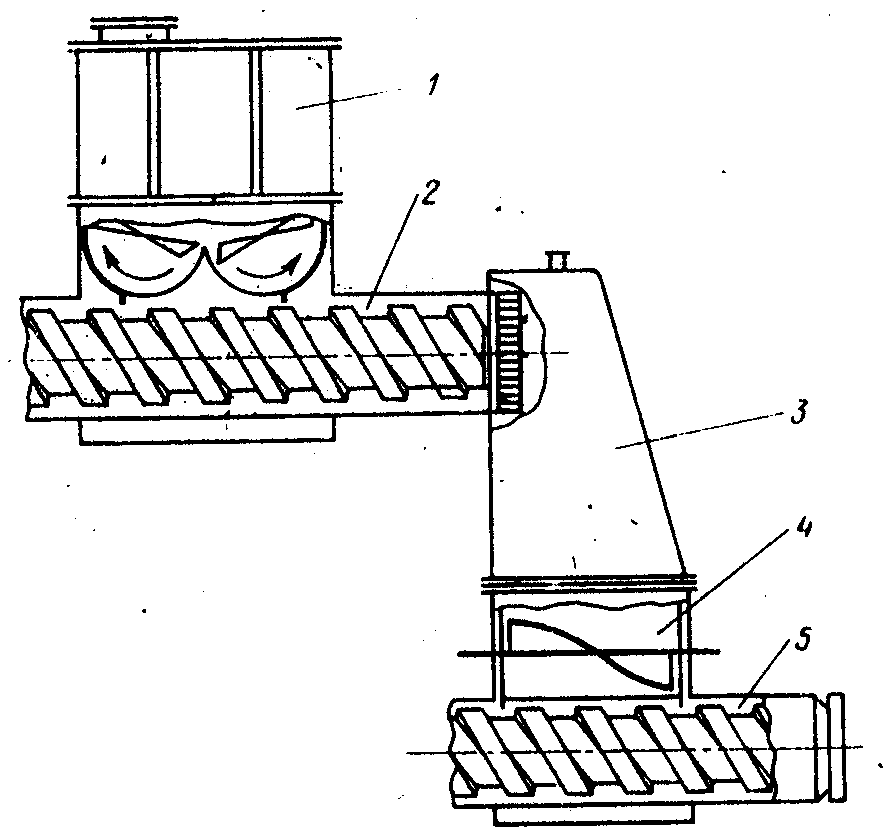
1 − предварительный смеситель; 2 − шнек предварительного
смесителя; 3 − вакуумная камера; 4 − вакуумный смеситель;
5 − шнек вакуумного смесителя
Рисунок 62 − Схема аппарата СНД
Полученная смесь поступает в основной аппарат смешения, в котором происходит усреднение и вакуумирование массы. Напорным шнеком готовая топливная масса нагнетается в прессформу или корпус двигателя (рисунок 63). Крупногабаритные заряды формуются при вертикальном положении корпуса двигателя с подачей массы снизу. Процесс осуществляется автоматически с помощью дистанционного управления. Метод литья под давлением применяется при производстве зарядов массой до 50 тонн [83].
Несмотря на то, что схема зарекомендовала себя положительно, в производстве у нее выявились и свои недостатки: сложность в связи с сочетанием большого комплекса дозирующих, передающих механизмов, аппаратов с механическими перемешивающими органами; смешение и формование в одном здании, что приводило к скоплению в нем большой массы топлива; сильное механическое воздействие на массу перемешивающими устройствами, что увеличивало опасность процесса.
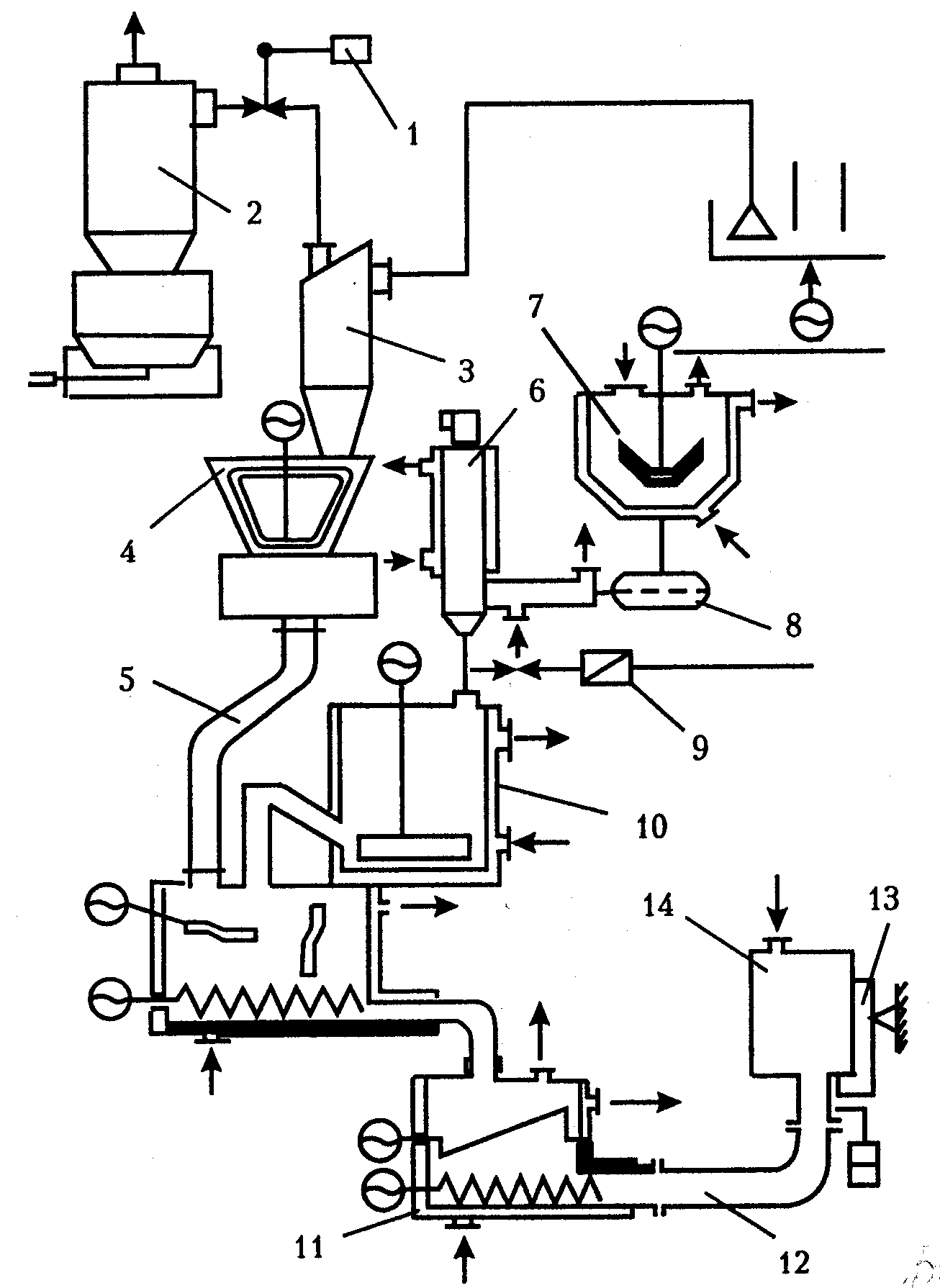
1 − вакуум-насос; 2 − емкость порошкообразных компонентов;
3 − циклон; 4 − дозатор сыпучих компонентов; 5 − течка;
6 − импульсный дозатор; 7 − реактор; 8 − фильтр; 9 − дозатор
связующего; 10 − форсмеситель; 11 − смеситель типа «Вернер»
с напорным винтом; 12 − массопровод; 13 − опора; 14 − прессформа
Рисунок 63 − Принципиальная схема технологического процесса
с использованием смесителя СНД
Встал вопрос обеспечения безопасности процесса смешения. Он был решен при использовании объемных смесителей барабанного типа («пьяная бочка»). Сущность смешения компонентов топлива в этих аппаратах заключается в том, что масса смешивается за счет перетекания ее в барабане при кинематическом его движении вокруг горизонтально расположенной диагонали цилиндра, опирающегося на цапфы.
Способ свободного литья. Технологическая схема изготовления СРТТ способом свободного литья в аппаратах барабанного типа представлена на рисунке 64 [87].
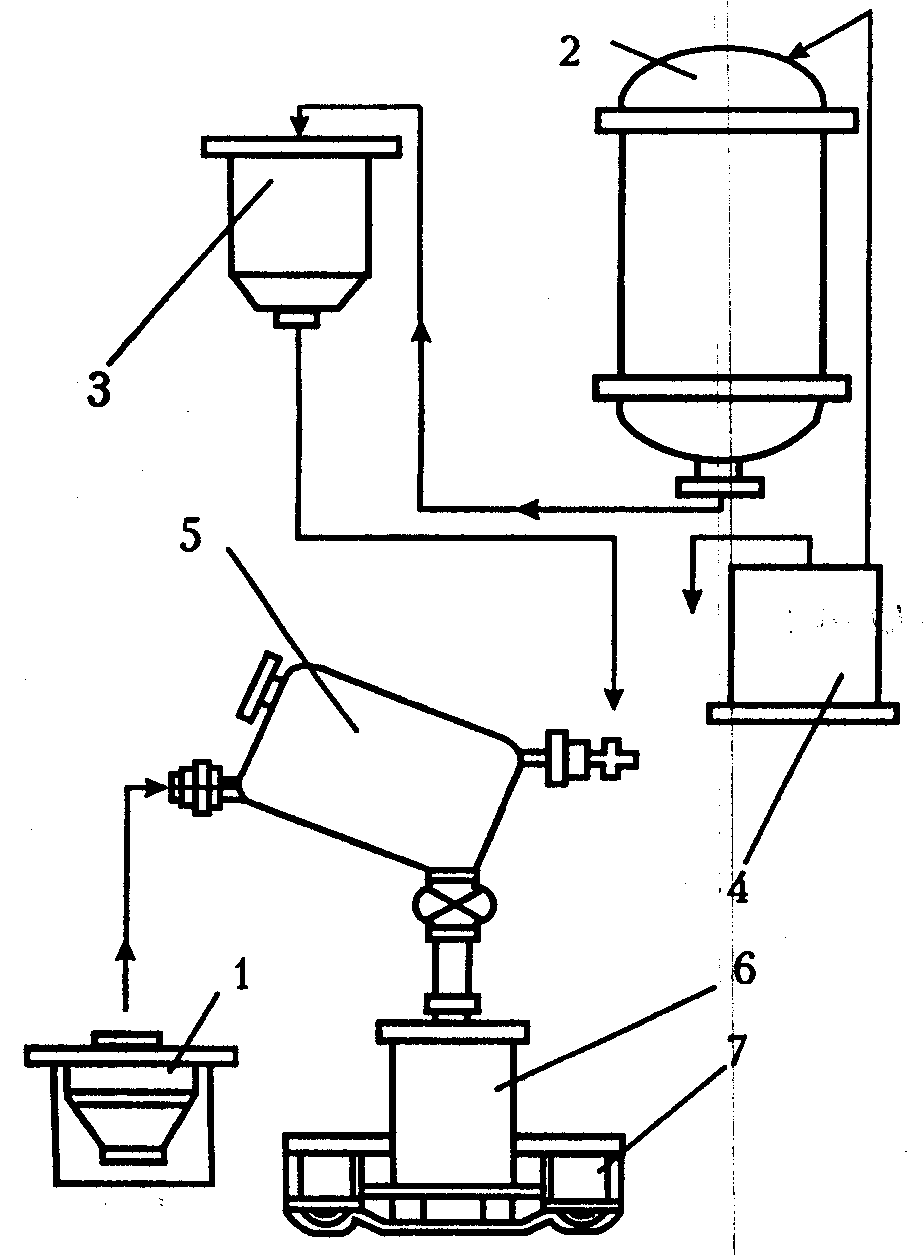
1 − контейнер окислителя; 2 − реактор жидковязких компонентов;
3 − мерник связующего; 4 − емкость для алюминия; 5 − смеситель;
6 − изложница; 7 − транспортная платформа
Рисунок 64 − Технологическая схема изготовления СРТТ
способом свободного литья
Для переработки топливных масс по методу свободного литья в настоящее время используются как периодические, так и непрерывные установки смешения, причем процесс периодического смешения имеет определенные преимущества перед непрерывным, обусловленные возможностью обеспечивать более высокую точность дозирования компонентов и лучшее усреднение состава по объему.
По окончании процесса смешения к смесителю подается прессформа или корпус двигателя в сборке с технологической оснасткой, после чего происходит формование заряда в результате свободного слива массы из смесителя. Прессформа или корпус двигателя размещаются при формовании в специальных шахтах.
Изготовление зарядов СРТТ методом свободного литья имеет следующие преимущества: высокую взрывобезопасность процесса, обусловленную разрывом фаз смешения и формования; возможность формования зарядов любых форм и массы; высокую воспроизводимость и стабильность химического состава (среднеквадратичные отклонения основных компонентов составляют 0,2–0,3 %).
Управление технологическими процессами получения топливных масс, формования и отверждения зарядов осуществляется дистанционно с широким использованием автоматизированных систем.
Контроль качества зарядов включает проверку химического состава топлива, его механических характеристик и скорости горения, прочности скрепления топлива со стенками корпуса двигателя и сплошности этого скрепления, монолитности заряда, его геометрических и весовых характеристик и т.д.
Изготовление малогабаритных зарядов производится на полуавтоматах заливки (ПАЗ) [67].
А.А. Рогожиным впервые в стране были разработаны полуавтоматы заливки (ПАЗ-1, 2, 3 и 4). Создание этих ПАЗ решило проблему промышленного производства малогабаритных зарядов из СРТТ.
Весь процесс производства ведется без присутствия человека и контролируется с пульта управления по телеканалам.
Разработано и внедрено четыре типоразмера ПАЗ.
ПАЗ-1 для изготовления зарядов массой до 2,5 кг диаметром
61 мм и длиной 460 мм.
ПАЗ-2 для изготовления зарядов массой от 4,6 до 40,0 кг диаметром от 60 до 200 мм и длиной до 1500 мм.
На ПАЗ-2М можно изготавливать более 20 типов зарядов и одновременно заполнять одну, две или четыре изложницы.
ПАЗ-3 позволяет изготавливать заряды массой до 100 кг.
ПАЗ-4 предназначены для изготовления зарядов массой более 100 кг.
Создание и использование полуавтоматов типа ПАЗ явилось большим достижением в производстве СРТТ. Эти полуавтоматы позволили автоматизировать процесс изготовления малогабаритных ракетных зарядов, значительно снизить трудоемкость, обезопасить людей на всех опасных фазах.
Отверждение топливной массы − это процесс перехода ее из вязкого или вязкотекучего состояния в упругое. Это изменение связано со структурированием. Образование конденсационно-кристаллизаци-онной структуры в топливе происходит за счет линейной, пространственной или линейной и пространственной полимеризации (поликонденсации) в зависимости от природы связующего.
Химическое и физическое структурообразование протекает с изменением объема, как правило, с уменьшением его, а также с выделением тепла.
Отверждение проводят в специальных камерах или колодцах. Изделия, формуемые литьем под давлением, отверждаются в камерах, а свободным литьем − в колодцах.
Отверждение топливной массы начинается с момента подачи теплоносителя (горячей воды) в технологическую иглу и в камеру (колодец) горячего воздуха.
В процессе отверждения контролируется давление внутри корпуса, температура горячей воды, подаваемой в иглу, а также горячего воздуха, подаваемого в камеру (колодец).
Технологический цикл процесса отверждения состоит из трех стадий:
- прогрев топливной массы;
- собственно отверждение;
- охлаждение заряда до давления в корпусе не более 0,1 МПа.
Продолжительность стадий прогрева и охлаждения определяется габаритами изделия, а собственно отверждения − системой вулканизации.
2.7.2.6 Распрессовка
На фазе распрессовки удаляется формующая технологическая оснастка из заряда.
При распрессовке выполняются следующие операции:
- разборка соединительных элементов: хомутовых, бандажно-болтовых и др.
- снятие отсекателя;
- снятие крышки;
- извлечение технологической иглы;
- выталкивание заряда из прессформы (при изготовлении заряда в изложнице).
Основные параметры, контролируемые при распрессовке:
- усилие, необходимое для отрыва деталей оснастки по давлению масла в системе гидроцилиндров;
- скорость отрыва или удаления деталей оснастки;
- усилие и скорость при выталкивании заряда из прессформы.
Для распрессовки зарядов применяются следующие оборудование и приспособления:
- гидравлические стационарные и передвижные пресс-станции;
- гидроцилиндры различных типов;
- маслостанция;
- платформа с регулируемым ложементом;
- подъемно-перегрузочные устройства.
2.7.3 Методы контроля качества изделий
Контроль (технический контроль) − проверка соответствия изделия установленным техническим требованиям.
Основные виды дефектов:
- раковины (полости округлой формы);
- трещины (нарушение сплошности в виде разрывов полимерного материала);
- инородные включения (структуры, отличающиеся по составу от основного материала);
- пористость (скопление мелких полостей округлой формы);
- отслоения (нарушения сплошности на границе наполнитель−ТЗП корпуса;
- расслоения (нарушения сплошности в толще корпуса и на границе ТЗП−корпус).
Классификация методов неразрушающего контроля изделий.
В основу классификации методов неразрушающего контроля изделий положены физические процессы взаимодействия физического поля с объектом контроля. С точки зрения физических явлений, на которых они основаны, можно выделить четыре основных вида неразрушающего контроля: радиационный, акустический, электромагнитный и оптический.
Каждый из видов контроля подразделяют на методы по рассматриваемым признакам (таблица 10). Наиболее широко для неразрушающего контроля изделий различных габаритов и конструкций используются радиационный и акустический методы. В значительно меньшей степени распространены электромагнитный и оптический методы.
Таблица 10 − Классификация методов неразрушающего контроля
изделий
Вид контроля | Методы контроля | ||
по характеру взаимодействия физических полей с объектом контроля | по первичному информативному параметру | по способу получения первичной информации | |
Радиационный | Прошедшего излучения | Плотность потока | Сцинтилляционный Радиографический Рентгенографический |
Акустический | Прошедшего излучения Отраженного излучения Импедансный Собственных колебаний | Амплитудный Временной | Пьезоэлектрический |
Вихретоковый | Отраженного поля | Амплитудный Фазовый | Параметрический |
Оптический | Отраженного излучения | Амплитудный | Визуально-оптический |
2.7.3.1 Радиационный контроль
Радиационные методы контроля основаны на различии в ослаблении ионизирующего излучения или прохождении его через бездефектный и дефектный участки контролируемого изделия. Используются следующие виды ионизирующего излучения: гамма-излучение (радиоактивный изотоп Со60); тормозное излучение (бетатрон); рентгеновское излучение (промышленные рентгеновские установки).
Гамма-сцинтилляционный метод. Гамма-сцинтилляционный метод применяется при контроле вкладных и скрепленных с корпусом изделий для выявления внутренних дефектов в наполнителе (нарушений сплошности или однородности). Гамма-излучение, прошедшее через контролируемое изделие, преобразуется сцинтилляционным детектором в электрические сигналы, которые после соответствующей обработки регистрируются в виде дефектограммы. Амплитуда электрического сигнала пропорциональна интенсивности прошедшего через изделие гамма-излучения. Путем последовательного сравнения зарегистрированной в виде электрических сигналов интенсивности определяют наличие или отсутствие дефектов.
Гамма-сцинтилляционный дефектоскоп состоит из радиоизотопного источника гамма-излучения (типа РИД-41 или ГУП-Со-50-2С); электронно-регистрирующей аппаратуры (ГДСД-М, ГУЗД-2900 или ГД-700 и т.п.).
Диапазон контролируемых толщин наполнителя от 100 до 1100 мм.
Чувствительность контроля (объем минимального выявляемого дефекта) от 0,05 до 8 см3. Чувствительность указана для источника гамма-излучения радиоактивного изотопа Со-60 активностью 50 г-экв Ra при производительности контроля 2 м2/ч и отношении сигнал/шум, равном 2.
Погрешность определения глубины залегания дефекта не более 10 %.
Настройка электронно-регистрирующей аппаратуры производится с помощью имитаторов дефектов (дефектометров), изготавливаемых из материала наполнителя или из материала, отличающегося по плотности не более чем на 0,5 г/см от плотности наполнителя.
В настоящее время разработана унифицированная радиометрическая аппаратура РД-11Р, предназначенная для замены РД-10Р.
Радиографический метод контроля. Радиографический метод используется преимущественно при контроле изделий, скрепленных с корпусом, для обнаружения внутренних дефектов наполнителя и отслоений наполнителя от корпуса на участках изделия, не пригодных для контроля гамма-сцинтилляционным и ультразвуковым методами, а также для определения конфигурации и глубины залегания дефектов, обнаруживаемых вышеуказанными штатными методами. В качестве источника тормозного излучения применяется бетатрон Б-5Д-25 с максимальной энергией излучения 25 МэВ и мощностью дозы 80 Р/мин на расстоянии 1 м от мишени. В качестве детектора излучения используется рентгенографическая пленка РТ-1 или РТ-5.
Чувствительность радиографического метода контроля сплошности и однородности наполнителя зависит от характера, местоположения и ориентации дефекта и составляет 1,5–2,5 % контролируемой толщины наполнителя. Оценка чувствительности производится с помощью имитаторов дефектов, изготавливаемых в виде дисков с центральным отверстием. Плотность материала имитатора дефекта не должна отличаться от плотности материала наполнителя более чем на 0,1 г/см3. Выраженное в процентах отношение толщины имитатора дефекта, выявляемого при контроле (различаемого на радиографическом снимке), к контролируемой толщине наполнителя определяет чувствительность метода.
Минимальное раскрытие выявляемого отслоения зависит от диаметра изделия и составляет 0,2–0,5 мм.
Контроль осуществляется по одной из трех схем просвечивания: радиальной, диаметральной и хордовой в зависимости от цели контроля и конструкции изделия.
Контроль выборочный − количество снимков − определяется конструкторской документацией на изделие.
Рентгенографический метод. Рентгенографическому контролю подвергаются вкладные изделия с толщиной наполнителя в направлении просвечивания до 100 мм.
В качестве источников излучения используются рентгеновские аппараты, а в качестве детекторов излучения − рентгенографические пленки РТ-1, РТ-5 и РМ-1.
Чувствительность метода в зависимости от контролируемой толщины наполнителя составляет 1−2 %.
Для оценки чувствительности при контроле изделий с просвечиваемой толщиной до 70 мм применяется канавочный имитатор дефекта по ГОСТ 7512-75, а при контроле изделий с просвечиваемой толщиной от 70 до 100 мм − имитатор дефекта в виде кольца с центральным отверстием. Материал имитатора дефекта должен иметь плотность, отличающуюся не более чем на ±0,1 г/см3 от плотности наполнителя.
Рентгенографический метод может быть применен для контроля сплошности скрепления наполнителя с корпусом или покрытия с наполнителем малогабаритных изделий.
2.7.3.2 Акустический контроль
Акустический контроль основан на анализе параметров упругих колебаний, возбуждаемых в контролируемом изделии. Акустические методы неразрушающего контроля, использующие ультразвуковой диапазон частот, называются ультразвуковыми. В нашей отрасли наш-ли широкое применение теневой и зеркально-теневой ультразвуковые методы, а также ультразвуковой метод изгибных волн. Ограниченное применение имеют ультразвуковой эхо-метод и акустический спектральный и импедансный методы.
2.7.3.3 Ультразвуковые методы
Контроль сплошности и однородности изделий. Контроль сплошности и однородности изделий осуществляется с помощью униц-фицированной УЗ аппаратуры УЗД-Т-30М и унифицированных механических частей УЗД-150, УЗД-450 и УЗД-1000.
Аппаратура УЗД-Т-30М работает в импульсном режиме излучения с частотой посылок 1000 Гц.
Рабочие частоты УЗК − 80, 120, 160 и 320 кГц. Выбор частоты проводится в процессе опытной отработки изделия. Механические части обеспечивают контроль изделий диаметром от 20 до 1000 мм и длиной от 3000 до 600 мм.
Чувствительность контроля (площадь минимального выявляемого дефекта) от 0,25 до 6,0 см2.
Акустический контакт создается иммерсионным способом − изделие помещается в ванну с водой. Настройка и периодическая проверка работоспособности дефектоскопа осуществляется с помощью контрольных образцов, содержащих искусственные дефекты в виде сверлений различного диаметра. Контрольный образец изготавливают из бездефектного изделия или из бездефектной его части.
Регистрация результатов контроля производится на дефектограмму.
2.7.3.4 Методы дефектоскопии
Контроль дефектоскопом ЗТА-1П. Дефектоскопом ЗТА-1П контролируется сплошность скрепления наполнителя с корпусом и покрытия с наполнителем. Дефектоскоп ЗТА-1П состоит из электронного блока и излучающего и приемного преобразователей.
Скорость контроля дефектоскопом ЗТА-1П заключается в регистрации уменьшения амплитуды импульсного УЗ сигнала, прошедшего от излучающего преобразователя к приемному через дефектный участок по сравнению с амплитудой сигнала на участке без дефекта.
Уменьшение сигнала регистрируется визуально по экрану электронно-лучевой трубки дефектоскопа.
Контроль осуществляется теневым и зеркально-теневым методами. При контроле участков сплошности конфигурации возможна комбинация теневого и зеркально-теневого методов.
При теневом методе контроля УЗ сигнал проходит через толщу изделия по прямой от ИП к ПП. На экране ЭЛТ дефектоскопа наблюдается один сигнал, являющийся рабочим.
При зеркально-теневом методе УЗ сигнал от ИП приходит к ПП после отражения от границы раздела с воздухом, лежащей на пути прохождения сигнала. На экране ЭЛТ наблюдаются донный и иногда поверхностный сигналы.
При комбинации теневого и зеркально-теневого методов на экране ЭЛТ видны прямой и донный сигналы.
Наличие отслоения на пути прохождения прямого или донного сигнала приводит к резкому уменьшению амплитуды рабочего сигнала на экране ЭЛТ.
Минимальные размеры выявляемых отслоений − 30×30 мм.
Производительность контроля − 4,5 м2 /ч.
Рабочая частота УЗК − (405) кГц.
Ввод и вывод УЗК осуществляется контактным способом. Для улучшения акустического контакта на поверхность корпуса и покрытия наносится контактная среда (водный раствор карбоксиметилцеллюлозы или глицерин). Процесс контроля состоит в сканировании поверхности корпуса и покрытия излучающим преобразователем при неподвижном ПП.
По принципу действия дефектоскоп ЗТА-1П является индикатором наличия или отсутствия отслоений и не имеет блоков измерения размеров и глубины залегания дефектов.
Контроль дефектоскопом УКП-1. Дефектоскопом УКП-1 контролируются изделия вкладного варианта с покрытием типа ЭТС, ЭТХ и ЭТЛ.
Дефектоскоп состоит из электронного блока и искательной головки. Контроль основан на использовании упругих изгибных колебаний ультразвуковой частоты. Электрические колебания с генератора электронного блока поступают на излучающий преобразователь искательной головки, который превращает их в УЗ упругие колебания.
В точке контакта ИП с поверхностью покрытия возникают изгибные волны, которые распространяются по покрытию.
Наличие отслоения покрытия от наполнителя благоприятствует возбуждению изгибных волн с большей амплитудой, чем амплитуда волн на бездефектном участке. ПП искательной головки превращает воздействующие на него изгибные колебания в электрические сигналы, которые, пройдя приемный тракт электронного блока, усиливаются, выпрямляются и фиксируются миллиамперметром электронного блока или самопишущим миллиамперметром.
Технические данные дефектоскопа УКП-1:
- контролируемая толщина покрытия − до 10 мм;
- размеры минимального выявляемого отслоения − 40×40 мм;
- рабочая частота – (4010) кГц.
Дефектоскоп УКП-1 имеет автономное питание (две батарейки общим напряжением 9 В).
Настройка дефектоскопа для контроля и периодическая проверка его работоспособности производится с помощью стандартного образца, представляющего собой натурное изделие (или его часть) с искусственно созданными отслоениями покрытия от наполнителя, расположенными на участках с различной толщиной покрытия.
Контроль дефектоскопом УКП-1 производится автоматизированным и ручным способами. Скорость сканирования до 150 мм/с при шаге сканирования до 20 мм. Акустический контакт осуществляется сухим способом.
Контроль дефектоскопом УДМ-3. Дефектоскопом УДМ-3 контролируется сплошность скрепления покрытия из состава 230 с наполнителем. В данном случае реализуется УЗ эхо-метод.
При контроле используется раздельно-совмещенная испытательная головка с номинальной рабочей частотой УЗК 2,5 МГц. Ультразвуковые колебания вводятся в покрытие контактным способом с использованием глицерина в качестве контактной среды.
При наличии отслоения покрытия от наполнителя условия отражения УЗК от границы покрытие−наполнитель более благоприятны, чем в случае отсутствия отслоения. На экране ЭЛТ дефектоскопа появляется отраженный сигнал, и одновременно загорается сигнальная лампочка.
Чувствительность контроля (минимальное выявляемое отслоение) − круг диаметром 6 мм.
Максимальная контролируемая толщина 10 мм.
Цилиндрическая боковая поверхность контролируется механизированным способом, а торцевая – ручным способом.
Настройка дефектоскопа и периодическая проверка его работоспособности осуществляются по стандартному образцу, содержащему искусственно созданные отслоения покрытия от наполнителя.
Контроль дефектоскопом УВФД-1. Дефектоскопом УВФД-1 теневым методом контролируются органопластиковые и стеклопластиковые корпуса изделий для выявления расслоений в оболочке корпуса, ТЗП, манжете и отслоений на границах соединений указанных элементов.
Для использования дефектоскопа УВФД-1 в качестве теневой аппаратуры произведена его соответствующая доработка: испытательная головка разделена на два отдельных преобразователя, а в электронный блок дефектоскопа введен дополнительный каскад для обеспечения записи сигнала на самопишущий прибор.
Контроль обеспечивает выявление дефектов с минимальными размерами от 20×20 до 30×30 мм.
Акустический контакт обеспечивается сухим способом.
Контроль дефектоскопом ИАД-2. Дефектоскопом ИАД-2 контролируются корпуса изделий для выявления дефектов в соединении промежуточного и герметизирующего слоев с оболочкой корпуса и в самих слоях на глубине до 4 мм. Дефектоскоп реализует акустический импедансный метод, основанный на измерении силы реакции поверхности контролируемого изделия на стержень, помещенный на эту поверхность и совершающий колебания звуковой частоты.
При наличии в конструкции отслоения жесткость этого участка снижается, и, следовательно, снижается сила реакции на колеблющийся стержень, установленный на дефектный участок.
Размеры минимального выявляемого дефекта 15×15 мм.