Федеральное агентство по образованию бийский технологический институт (филиал)
Вид материала | Учебное пособие |
- Федеральное агентство по образованию бийский технологический институт (филиал), 981.77kb.
- Федеральное агентство по образованию бийский технологический институт (филиал), 1531.98kb.
- Федеральное агентство по образованию Бийский технологический институт (филиал), 2694.55kb.
- Федеральное агентство по образованию бийский технологический институт (филиал), 2134.54kb.
- Федеральное агентство по образованию бийский технологический институт (филиал), 1660.78kb.
- Федеральное агентство по образованию бийский технологический институт (филиал), 1946.38kb.
- Решением Ученого совета, 125.93kb.
- Федеральная целевая программа "Развитие электронной компонентной базы и радиоэлектроники", 3538.74kb.
- Бийский технологический институт (филиал), 2586.35kb.
- Министерство образования и науки федеральное агентство по образованию майкопский государственный, 102.13kb.
2.7 Смесевые ракетные твердые топлива
Одной из наиболее молодых, быстроразвивающихся и мощных составляющих энергетических конденсированных систем (ЭКС) является смесевое ракетное твердое топливо (СРТТ).
СРТТ многокомпонентная гетерогенная грубодисперсная высоконаполненная взрывчатая система, состоящая из окислителя, связующего-горючего и специальных добавок (энергетических, технологических и эксплуатационных) и получаемая путем механического смеше-ния компонентов с последующим превращением в моноблок, способный к закономерному горению.
Таблица 3 − Рецептуры и свойства составов цветных огней на баллиститной основе
Наименование компонента и свойств состава | Содержание компонентов, %, и значения характеристик для состава огня | ||||||||
красного №1 | зеленого | желтого № 1 | белого | лилового | голубого | желтого № 2 | желтого искристого | красного № 2 | |
Баллиститная основа | 73 | 3 | 78 | 78 | 56 | 56 | 97,5 | 87 | 92 |
Металлическое горючее | 10 | 10 | 16 | 16 | 16 | 16 | - | - | - |
Цветопламенная добавка | 10 | 10 | 6 | 6 | 14 | 22 | 2,5 | 5 | 4 |
Усилитель цвета пламени | 7 | - | - | - | 14 | 6 | - | - | - |
Искрообразователь | - | - | - | - | - | - | - | 8 | 4 |
I, кд | 2000 | 2500 | 1500 | 1800 | 1350 | 1920 | 210 | 1150 | 100 |
U, мм/с | 1,5 | 1,5 | 1,4 | 1,6 | 1,8 | 1,5 | 0,8 | 1,2 | 0,8 |
Р, % | 98 | 86 | 96 | - | - | - | 98 | 96 | 96 |
Родоначальником СРТТ был дымный порох (ДП). Китайцы первыми начали применять его в качестве твердого топлива для ракет. Ракета в качестве стабилизатора имела шест длиной 2,5 м. В качестве оболочки-корпуса применили бамбуковые трубки. Индусы в качестве корпуса-оболочки уже использовали железный корпус. В 1799 г. индусы в боевых действиях применяли ракеты против англичан при обороне г. Серингапатама. Для массированного использования ракет там был создан корпус ракетных стрелков численностью до 5000 человек. Масса ракет составляла от 3 до 6 кт [59].
В Европе первые ракеты также появились с изобретением пороха. Англичане освоили технологию изготовления ракет на дымном порохе в 1804 г. Дальность полета ракет составляла 2,5 км. Ракеты имели железный корпус, а с целью увеличения площади горения заряд имел канал. На вооружение они были приняты в 1806 г. (использовались при осаде г. Булони и в 1807 г. при обстреле г. Копенгагена). Масса ракеты составляла от 3 до 17 кг. Вслед за Англией ракеты на вооружение принимают в Австрии, Франции, Пруссии.
Русская ракетная техника шла своим самостоятельным путем, и есть сведения, что Россия намного опередила Западную Европу. Уже в начале XVII в. были хорошо известны способы изготовления боевых ракет. В 1680 г. в Москве основано первое «ракетное заведение», состоящее из нескольких лабораторий, занимающихся приготовлением специальных ракетных порохов и отдельных частей ракет [59].
В 1807 г. была разработана сорокачетырехмиллиметровая сигнальная ракета на ДП, которая находилась на вооружении более 100 лет. Широкое применение пороховые ракеты, разработанные русскими учеными А.Д. Засядько и К.И. Константиновым, нашли во время русско-турецкой войны в 18281829 гг., в боевых операциях на Кавказе в 1850 г. и при обороне Севастополя от иностранных захватчиков в 1854–1855 гг. [59].
Ракеты на ДП утратили свое значение по двум причинам:
- вследствие неудовлетворительного значения энергетических характеристик пороха;
- вследствие малой точности ракет.
Появление нарезной артиллерии, позволившей значительно повысить точность попадания, окончательно свело на нет интерес к ДП.
В период второй мировой войны в связи с тем, что баллиститные пороха были дефицитными, а некоторые их свойства не позволяли использовать эти пороха в качестве источника энергии ракет, усилия научных работников многих стран были направлены на разработку механически прочных СРТТ.
В 1942 г. в Артиллерийской академии им. Ф.Э. Дзержинского были разработаны литьевые составы СРТТ на основе аммонийной селитры и органических горюче-связующих веществ типа поливинилацетата, а в 1946 г. А.А. Шмидт впервые обосновал возможность получения твердых топлив на базе полимеризующихся веществ. Он предсказал реальные пути данного направления и его перспективность. К наиболее ранним работам в этом направлении относятся исследования
Г.В. Калабухова [57]. В 1948 г. им были предложены СРТТ на основе перхлоратов аммония и калия и горючей высокополимерной связки, состоящей из коллоксилина, полистирола и каучука. Однако по энергетическим характеристикам и прочности разработанные составы уступали баллиститным порохам. Заряды изготавливались глухим и проходным прессованием.
Первые американские СРТТ были получены в лаборатории Калифорнийского технологического института.
В их состав входили:
перхлорат калия или нитрат аммония – 75 %;
битум − 18 %;
нефтяное масло − 7 %.
В дальнейшем с целью повышения энергетики в качестве окислителя стали использовать перхлорат аммония (ПХА) и металлический алюминий, а для улучшения физико-механических характеристик топлива были применены каучукоподобные горюче-связующие вещества. Так, на основе тиокола (полисульфидный каучук) и ПХА были разработаны СРТТ для оперативно-тактической ракеты «Серджент» массой около 4 тонн и дальностью полета до 150 км. Затем на основе полиуретана и ПХА было создано топливо для оперативной ракеты «Першинг» с дальностью полета до 700 км, а также стратегической ракеты «Полярис» массой около 13 тонн и дальностью полета до 4000 км. В дальнейшем на основе ПХА и сополимера полибутадиена с акриловой кислотой было разработано топливо, использованное для изготовления зарядов к межконтинентальной ракете «Минитмен» с дальностью полета до 10000 км.
Все эти ракеты были разработаны и приняты на вооружение в период с 1953-1963 гг. В конце 1970 г. армия, Военно-Морской Флот и авиация США имели 600 ракет «Полярис» на подводных лодках и 1000 ракет «Минитмен», установленных в шахтах на боевых позициях.
В СССР разработкой и использованием СРТТ в широком плане стали заниматься с 1958 г. В 1959 г. в Артиллерийской академии
им. Ф.Э. Дзержинского было получено и исследовано в лабораторном масштабе полиуретановое топливо. В этом же году разработано в промышленном масштабе СРТТ на основе тиокола и ПХА. Несколько позже созданы СРТТ на основе простых и сложных полиэфиров, акрилонитрильных каучуков, бутилкаучука и карбоксильных каучуков [57].
Начиная с 1961 г. усилия исследователей были направлены на повышение удельного импульса СРТТ, увеличение уровня физико-меха-нических характеристик и стабилизацию процесса горения.
С.П. Королев создал первую твердотопливную ракету РТ-1 на баллиститном порохе с дальностью полета 2500 км при стартовой массе 34 тонны, используя вкладные заряды диаметром 800 мм. Только перейдя на СРТТ, он смог создать вторую твердотопливную ракету
РТ-2 (8К-98), имеющую дальность полета уже 9500 км при стартовой массе 51 тонна [57, 63, 65, 66]. Первый пуск ее состоялся 4 ноября 1966 г., а на вооружение она была принята в 1968 г.
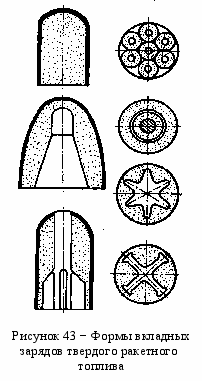
Прочно скрепленный с корпусом заряд изготавливается заливкой топливной массы непосредственно в камеру сгорания. Скрепление заряда с корпусом осуществляется с помощью специальных защитно-крепящих (клеевых) слоев (рисунок 44) [77].
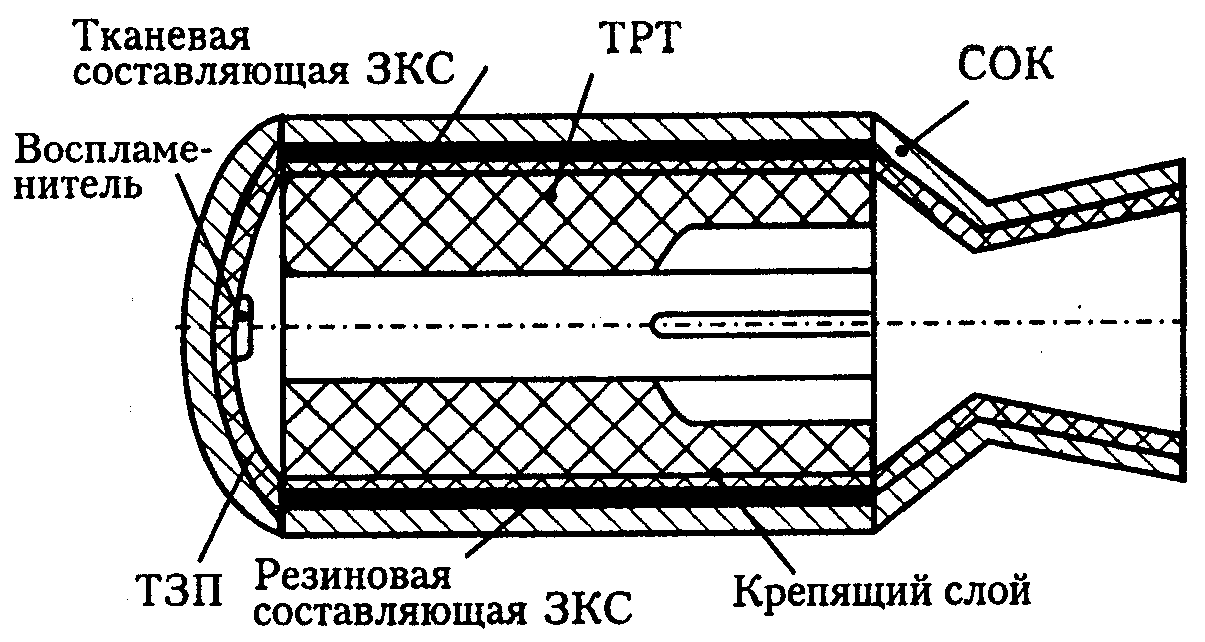
ТРТ − твердое ракетное топливо; ТЗП − теплозащитное покрытие;
ЗКС − защитно-крепящий слой; СОК − сопловой блок
Рисунок 44 − Схема крепления с помощью защитно-крепящих слоев
Размеры и конструктивная форма заряда выбираются из условия обеспечения требуемого значения секундного расхода топлива, временных и тяговых характеристик, нагрузок, температурных режимов эксплуатации и применения. Требуемая зависимость текущего значения поверхности горения от величины сгоревшего свода обеспечивается формой канала (цилиндрический, звездообразный, щелевой, цилиндро-конический и др.), а также введением специальных компенсаторов горения в виде проточек частичного или полного открытия торцов и др.
Совершенство заряда в значительной степени определяется коэффициентом объемного заполнения камеры сгорания, минимизацией отношения текущего значения поверхности горения к среднеинтегральной величине, технологичностью изготовления, стойкостью к воздействию внешних факторов. Маcсовые параметры зарядов изменяются в широких пределах: от долей грамма до нескольких сотен тонн.
Применение СРТТ не ограничивается вооруженными силами. Они параллельно широко стали применяться для освоения космоса и в народном хозяйстве [19].
Использование СРТТ в мирных целях. Ракетные двигатели на твердом топливе (РДТТ) находят широкое применение в мирных целях в народном хозяйстве как вспомогательные двигатели для решения самых разнообразных задач в ракетно-космической технике [19].
РДТТ наиболее часто применяются в системе аварийного спасения космонавтов и летчиков, для торможения и ускорения космического аппарата, отделения ступеней ракеты-носителя, сброса полезного груза, стабилизации и коррекции траектории космического аппарата (КА), коррекции орбиты КА, посадки КА на планеты, старта ракет-носителей и возвращаемых КА в системах «Шаттл», в качестве двигателей метеорологических ракет, служащих для подъема аппаратуры в верхние слои атмосферы, противоградовых и противолавинных.
Преимуществами РДТТ, обеспечивающими их широкое применение в ракетно-космических аппаратах, являются высокая воспроизводимость параметров, в том числе точность выполнения требований по полному импульсу тяги, высокий коэффициент массового совершенства, длительные гарантийные сроки применения и относительная безопасность при хранении и эксплуатации.
Для отделения ступеней ракеты применяются малогабаритные РДТТ самых разнообразных конструкций, тип которых определяется выполняемой задачей. Заряд из СРТТ, вариант снаряжения вкладной или жесткоскрепленный, представлен на рисунке 45.
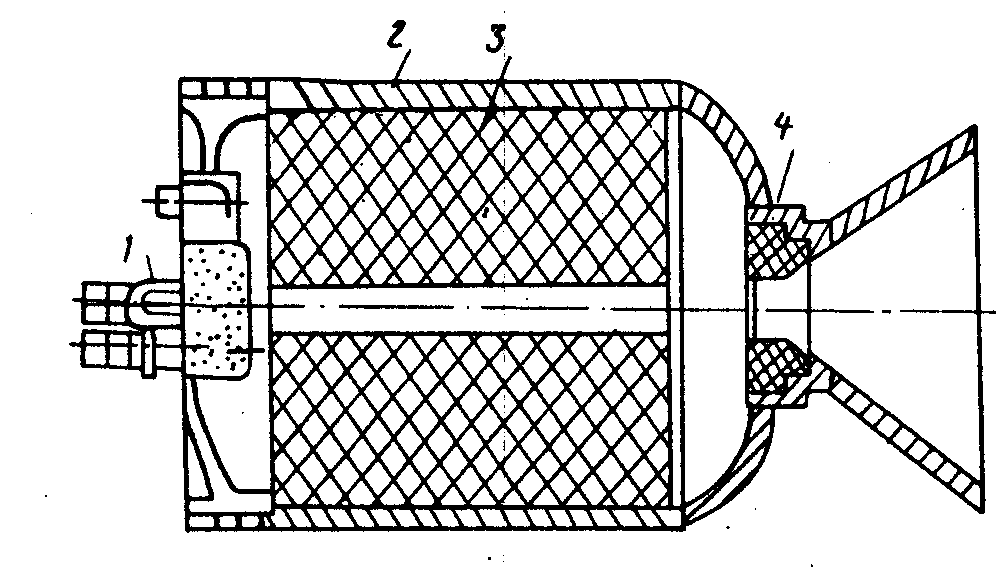
1 − воспламенитель; 2 − обечайка камеры; 3 − заряд СРТТ;
4 − сопловой блок
Рисунок 45 − Малогабаритный РДТТ
Тормозные двигатели применяются для торможения при спуске самых разнообразных космических аппаратов. Для этих целей в основном применяются РДТТ сферического типа, например, сферические РДТТ серии ТЕ-М (США) фирмы «Тиокол Паудер» использовались для торможения при спуске космического корабля «Джемени», при посадке космического аппарата «Сервейер» на луну и др. Конструкция тормозного двигателя типа ТК-М-385 представлена на рисунке 46.
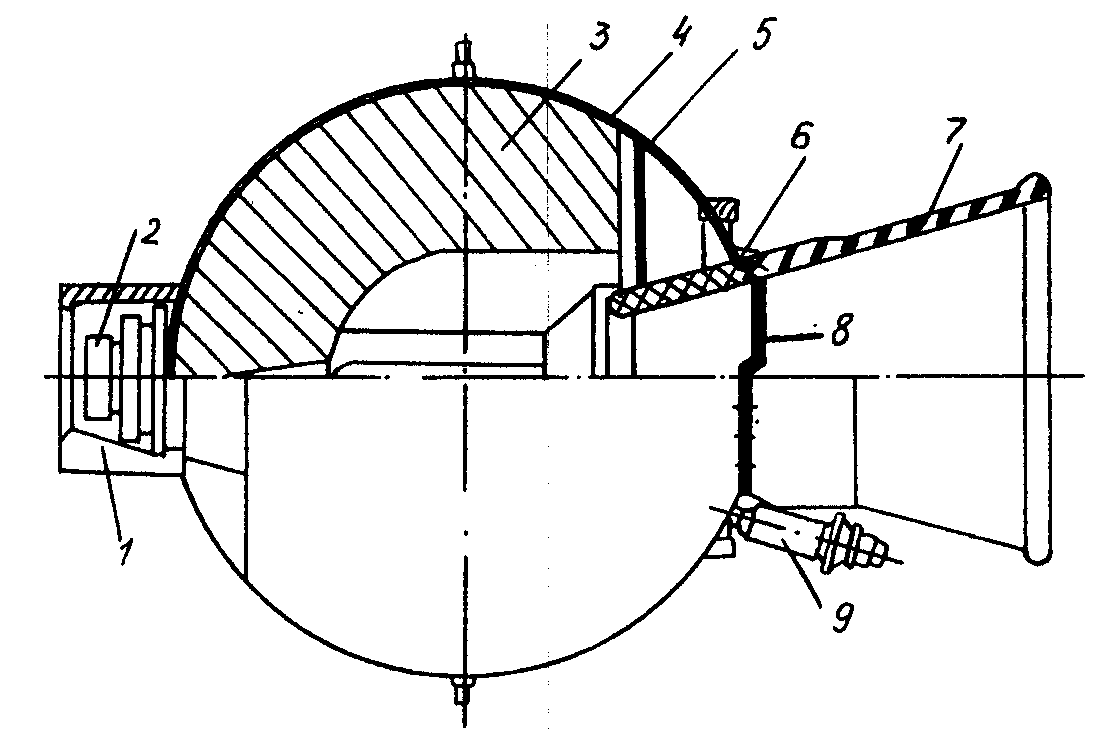
1 − защитный кожух; 2 − блок центровочного зеркала; 3− заряд
твердого топлива; 4 − теплоизоляционное покрытие; 5 − корпус;
6 − вкладыш; 7 − расширяющаяся часть сопла; 8 − резиновая заглушка;
9 − воспламенительное устройство
Рисунок 46 – Тормозной РДТТ типа ТК-М-385
Заряд твердого топлива выполнен в виде восьмилучевой звезды из полисульфидного топлива, состоящего из ПХА и связки с добавлением 2 % алюминия.
Коррекция орбиты космического аппарата необходима для обеспечения его межорбитальных переходов и выполнения различных маневров на орбите. К двигателям такого типа относятся апогейные и пирогейные РДТТ, обеспечивающие переход КА с одной орбиты на другую.
Апогейный ракетный твердотопливный двигатель типа FW-5, применяемый в США, представлен на рисунке 47 [19].
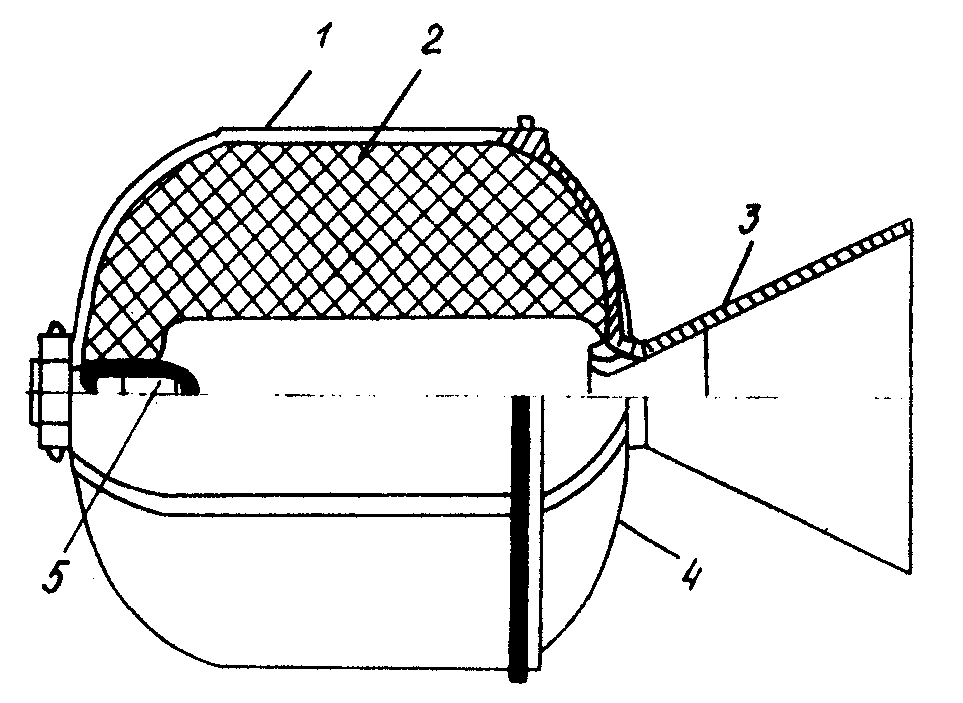
1 − теплоизоляция; 2 − заряд твердого топлива; 3 − сопловой блок;
4 − корпус; 5 − воспламенительное устройство
Рисунок 47 − РДТТ типа FW-5
Корпус изготовлен из титанового сплава. В двигателе используется СРТТ на основе полиуретанового связующего, ПХА и алюминия.
В качестве теплозащитного материала в корпусе используется состав на основе фенольной смолы.
На рисунке 48 изображен РДТТ аналогичного назначения MAGE-1. Его корпус изготовлен из композиционного материала «Кевлар-49», заряд − из алюминизированного топлива.
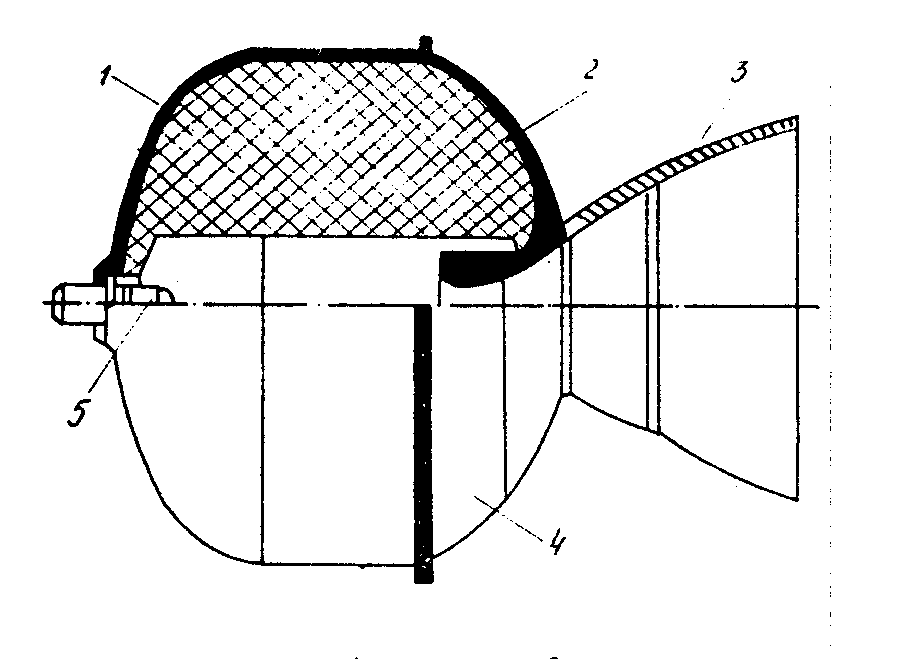
1 − теплоизоляция; 2 − заряд твердого топлива; 3 − сопловой блок;
4 − корпус; 5 − воспламенительное устройство
Рисунок 48 − РДТТ типа MAGE-1
На рисунке 49 изображен перспективный апогейный РДТТ (США) серии STAR-48 фирмы «Тиокол Кемик», позволяющий увеличивать удельный импульс тяги в пустоте на 59,0–88,5 кн·с/кг при коэффициенте объемного заполнения до 0,935.
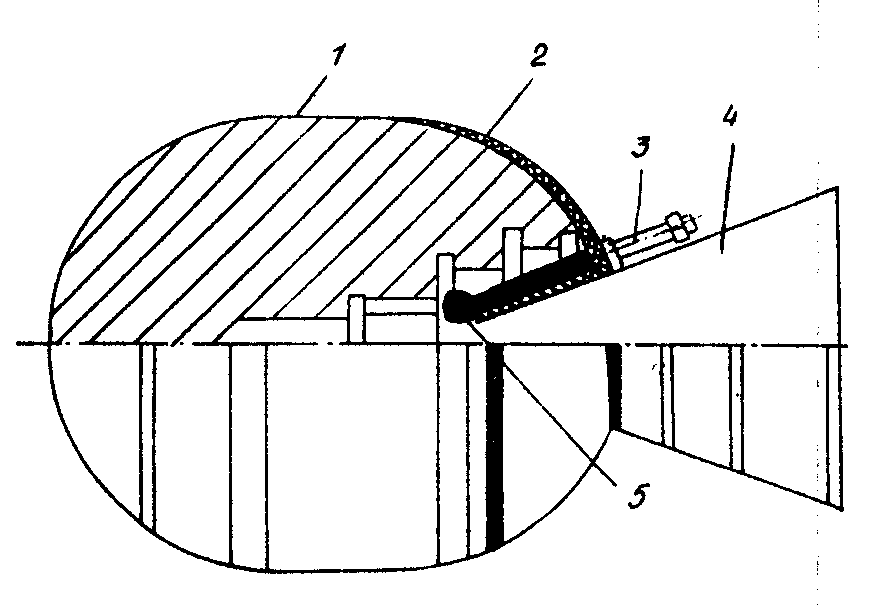
1 − корпус; 2 − теплозащитное покрытие; 3 − тороидальный
воспламенитель; 4 − сопловой блок; 5 − графитовый вкладыш
Рисунок 49 − Апогейный РДТТ серии STAR-48
Эти двигатели обладают следующими преимуществами:
- заряд из СРТТ на основе полибутадиенового каучука имеет цилиндрическую форму с радиальными щелевыми пропилами и заполняет всю переднюю часть корпуса;
- корпус выполнен из титанового сплава с теплозащитой из композиционного материала углерод-углерод.
Особое значение при конструировании малогабаритных РДТТ уделяется выбору топлива. Наиболее полно предъявляемым требованиям удовлетворяют СРТТ, в которых в качестве связующего-горю-чего применяются полиуретаны или углеводородные каучуки, а в качестве высокотеплопроводных добавок − алюминий. Термодинамические характеристики СРТТ могут быть повышены применением как более мощных окислителей, так и гидридов металлов, например, алюминия [19].
Некоторые характеристики СРТТ, применяемые в малогабаритных двигателях РДТТ в США, приведены в таблице 4.
Серьезным недостатком СРТТ на основе ПХА является их токсичность, т.к. при его сгорании выделяется большое количество токсичного хлора и хлористого водорода. Например, при старте корабля «Спейс Шаттл» при работе твердотопливных ускорителей в атмосферу выбрасывается около 2 тонн хлора и 210 тонн хлористого водорода, которые оказывают вредное воздействие на окружающую среду. Поэтому, чтобы облегчить использование СРТТ в мирных целях, ведутся большие работы как у нас, так и за рубежом по замене ПХА на экологически чистые окислители: аммонийная соль динитроазовой кислоты (АДНА), аммиачная селитра [19, 68].
Таблица 4 − Основные характеристики топлив для РДТТ
Характеристика | Топливо | |
ТР-Н1154 | ТР-Н1178 | |
Массовая доля, % связующего на основе полибутадиена с концевыми гидроксильными группами и эпоксидной смолы | 18 | 18 |
окислителя (ПХА) | 77 | 69 |
алюминия | 2 | 10 |
катализатора (Fe2O3) | 3 | 3 |
Скорость горения при давлении 14,0 МПа, мм/с | 26,9 | 23,8 |
Показатель степени в формуле закона скорости горения | 0,34 | 0,38 |
Плотность, г/см3 | 1,675 | 1,710 |
В США разработано дешевое и экологически чистое СРТТ для двигателей крупных космических ускорителей, в котором в качестве основных компонентов используются нитрат аммония, гексоген, октоген и связующее на основе полиглицедилазида, пластифицированного нитроэфирами [19].
В ФГУП «Союз» создано экологически чистое СРТТ «Центр», неблагоприятные свойства которого, в частности, фазовая нестабильность аммиачной селитры, устранены за счет ввода в кристаллы модифицирующей добавки. В нем используется активное связующее с температурой кристаллизации минус 50 С на основе эвтектической смеси с нитроэфирами. Использование аммиачной селитры и бутадиен-нит-рильного каучука снижает стоимость топлива.
Однако применение аммиачной селитры вместо ПХА заметно снижает энергетику СРТТ, ограничивает его использование в изделиях, где значение единичного импульса играет решающую роль. Кроме того, применение нитрата аммония ограничивается его повышенной гигроскопичностью.
Разработанные экологически чистые топлива находят применение в качестве зарядов для метеорологических ракет, в газодинамических буровых аппаратах, пороховых аккумуляторах давления.
В настоящее время все большее число ракет-носителей, применяемых для запуска различного типа спутников, используют в качестве ускорителей РДТТ. Так, например, в ракете «Титан-3С» (США) для старта кроме основных жидкостных ракетных двигателей (ЖРД) используются в качестве ускорителей два мощных РДТТ диаметром 3 м и длиной 25,8 м, развивающих тягу в пустоте до 540·104 н при времени работы 110 с. Применение их позволило увеличить массу нагрузки, выводимой на орбиту, до 11,4 тонн. Стартовая масса ракеты составляет 700 тонн.
Мощные ускорители, работающие на СРТТ с массой заряда от 100 до 200 тонн, стали применяться для запуска французских ракет «Ариан-2» и «Ариан-4», служащих для выведения на орбиту искусственных спутников Земли.
Фирмами IIS (США) и SEP (Франция) разработан усовершенствованный вариант такого типа двигателя, обеспечивающего при среднем давлении в камере 33,9·105 Па удельный импульс тяги 2970 кн·с/кг.
Заряд прочно скреплен с корпусом двигателя и имеет канал, не доходящий до переднего днища корпуса. Такая конструкция позволяет повысить коэффициент объемного заполнения до 0,92 и обеспечить достаточно небольшую площадь поверхности горения. Заряд изготавливается из высокоимпульсного твердого топлива на основе ПХА и полибутадиенового каучука (10 %), алюминия (20 %) и октогена (12 %).
Эффективным направлением конверсии многих заводов по производству СРТТ является изготовление на их основе стартовых ускорителей для мощных ракет-носителей и космических кораблей, выводящих на орбиту различные КА. Ускорители имеют очень большую массу (от 150 до 400 тонн), их изготовление обеспечивает загрузку заводов по производству СРТТ в мирное время. Обычно два таких ускорителя закрепляются по бокам основного корпуса ракеты и обеспечивают ее подъем, а после выработки топлива отделяются от ракеты с помощью специальных РДТТ сброса и падают на землю.
Типовой стартовый РДТТ имеет пять-шесть взаимозаменяемых секций, собираемых одна над другой и образующих общий корпус двигателя [19].
Схема стартового двигателя к ракете-носителю «Титан-3С», с помощью которого выводятся на орбиту различные спутники США, приведена на рисунке 50.
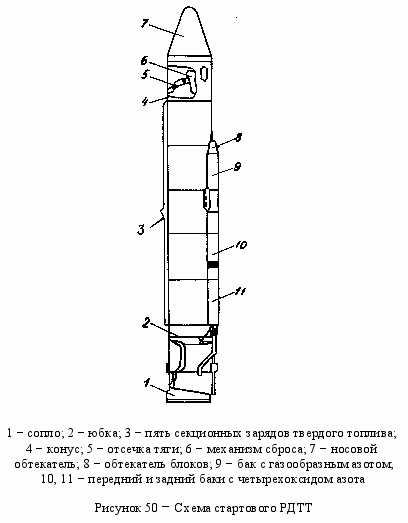
Она состоит из пяти секций диаметром 3,0 м и длиной 3,0 м. Масса каждой секции составляет 33,0 тонны. Заряд прочно скреплен с корпусом каждой секции и изготовляется из СРТТ, содержащего ПХА, алюминий и связующее на основе полибутадиена, метакриловой кислоты и акрилонитрила. Такое СРТТ при давлении в камере 6,06,2 МПа обеспечивает удельный импульс тяги 2480. Корпус двигателя сварной (из мостовой стали). На внутреннюю поверхность наносится теплозащитное покрытие из синтетического каучука с кремниевым наполнителем.
РДТТ к системе «Шаттл». Космическая система «Шаттл» (массой более 2000 тонн), предназначенная для вывода на орбиту пилотируемых и спускаемых кораблей «Челенджер», «Атлантик», «Дискавери», «Колумбия» и других, представляет собой связку, в которую вхо-дит орбитальный корабль с экипажем, два твердотопливных ускорителя для разгона корабля на начальном участке траектории и топливный бак одноразового использования. Последний является основным элементом системы, к которому крепятся спускаемый корабль и ускорители, возвращаемые на Землю и используемые повторно.
Основной особенностью этой системы в отличие от отечественной системы «Энергия-Буран» является то, что на ней установлены два ускорителя, работающие на твердом топливе. В системе «Энергия-Буран» стартовые ускорители работают на жидком топливе.
Твердотопливный ускоритель представляет собой РДТТ секционного типа, имеет диаметр 3,7 м, длину 45,5 м и массу в снаряженном состоянии около 590 тонн, а после выгорания топлива − 78 тонн. Масса твердого топлива составляет примерно 500 тонн. Время его работы больше 2 мин, суммарная тяга свыше 26 Мн.
В качестве твердого топлива применяют СРТТ, в состав которого входят ПХА, порошкообразный алюминий, полибутадиеновое связу-ющее, оксид железа и другие добавки. Форма заряда, жестко скрепленного с корпусом, − цилиндрическая, с внутренним каналом обеспечивает соблюдение необходимого закона нарастания тяги, который создает наиболее выгодный режим перегрузок (не более 3) для космонав-тов. После выгорания топлива корпуса ускорителей отделяются от корабля на высоте 7090 км, а затем при достижении плотных слоев атмосферы срабатывает парашютная система, обеспечивающая их приводнение. Поднятые из воды корпуса ускорителей восстанавливаются и вновь заполняются топливом.
Твердотопливные ускорители используют и во Франции на мощной ракете-носителе для запуска космических объектов, в том числе пилотируемых кораблей многоразового использования «Гермес», «Ариан-5».
Применение твердотопливных ускорителей, имеющих достаточно значительную массу топлива, как в системе «Шаттл», так и в ракетных носителях типа «Титан-3С» создало хорошие предпосылки для конверсии заводов, производящих твердое ракетное топливо в США, обеспечивая их загрузку в мирное время без изменения технологического процесса и оборудования.
Двигатели системы аварийного спасения космонавтов. Все ракеты-носители, служащие для вывода на орбиту космических объектов с космонавтами на борту, снабжаются системами аварийного спасения людей в момент запуска и активного полета.
Основой этой системы является РДТТ специальной конструкции, использующей твердые ракетные топлива баллиститного и смесевого типа. Например, в трехступенчатой ракете-носителе «Союз» третья ступень представляет собой блок длиной 8 м и диаметром 2,6 м, к которой через переходник пристыкован космический корабль, закрытый сверху обтекателем диаметром 3,0 м. На вершине обтекателя находится двигательная установка аварийного спасения корабля, имеющая форму большого гриба (рисунок 51) [19].
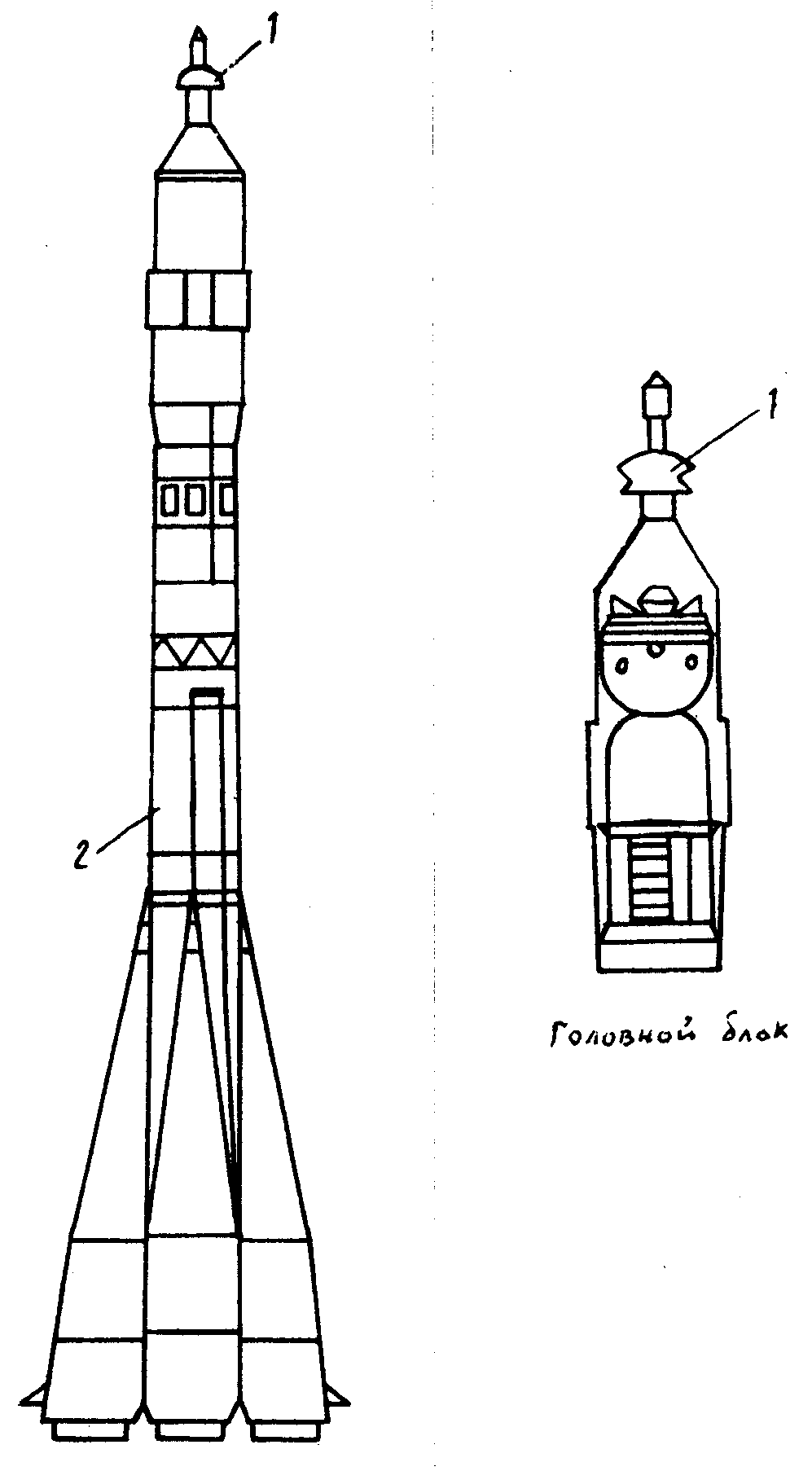
Головной блок
1 − двигательная установка; 2 − ракета «Союз»
Рисунок 51 − Двигательная установка аварийного спасения
на корабле «Союз»
Назначение установки в случае отказа ракеты, еще не израсходовавшей огромной массы топлива, − мгновенно увести космонавтов от очага неизбежного пожара и взрыва на расстояние, с которого возможен спуск на парашюте в безопасное место.
Система аварийного спасения (САС) корабля «Союз» комплектуется следующим образом: в носовой части ракеты монтируется аварийная двигательная установка, состоящая из твердотопливных ракетных двигателей трех типов.
Непосредственно на головном обтекателе устанавливается основной двигатель, включающийся в случае аварии и быстро отводящий верхнюю часть головного обтекателя с отсеком и спасаемым аппаратом корабля от ракеты.
Двенадцать сопел этого мощного двигателя расположены по кругу в его верхней части и развернуты под углом 30 градусов от продольной оси. Над ними находится небольшой обтекатель в виде полусферы, под которым спрятаны четыре двигателя управления. Они включаются вслед за основным, обеспечивая разворот и увод спасаемой части в сторону от опасной зоны. Еще выше находится двигатель разделения, который, включаясь последним, обеспечивает отделение головного обтекателя и его увод от спускаемого аппарата. После этого вводится основной парашют, и спускаемый аппарат совершает спуск и мягкую посадку так же, как при возвращении из штатного полета. Торможение при посадке осуществляется тормозными РДТТ, работающими на твер-дом топливе [19].
Термостойкие топлива для газогенераторов СРТТ. Для интенсификации добычи нефти стал широко применяться метод торпедирования скважин специальными зарядами. Пороховые газы создают каналы и трещины в горной породе, способствуя притоку нефти. Но используемые для этих целей пороха баллиститного типа имеют определенные ограничения: например, могут использоваться только в тех скважинах, где температура не превышает 110 С (т.е. до глубины
3 км). Разработанные составы на основе ПХА и неактивных углеводородных связующих устраняют этот недостаток. Они сохраняют работоспособность после их выдержки при температуре 150 С в течение 6 часов и могут 10 лет храниться при температуре 50 С. Критическая температура при диаметре шашки 150–200 мм составляет 170–200 С. Выделяющаяся при горении этого топлива соляная кислота, попадая в пласт и реагируя с породой, может способствовать интенсивному развитию трещин. Изготовление зарядов из этих топлив может производиться на существующем оборудовании по технологии заводов по производству СРТТ [19, 56].
СРТТ − источник аэрозолей. Одним из перспективных методов тушения пожаров в помещениях для хранения спирта, керосина, ацетона, продуктов в магазинах, винных погребах, в отсеках кораблей является аэрозольный, т.е. мгновенное заполнение помещения аэрозольной средой, почти не содержащей кислорода, в результате чего и прекращается горение.
Этот метод, запатентованный Кюном еще в конце XIX столетия, в дальнейшем был значительно усовершенствован и получил широкое распространение. «Банки Кюна» заполнялись пиротехническим составом, который имел ряд значительных недостатков: например, слеживаемость, недостаточный уровень физико-механических характеристик и др. Взамен его были разработаны новые типы порохов − источников аэрозолей, специально предназначенных для системы пожаротушения и предотвращения взрыва газовоздушных смесей. Этот новый класс порохов получил название ПАС (пороховые, аэрозольные, смесевые). Особенностью этих составов является высокая экономическая эффективность; расход огнетушащего состава 2090 г/м3 вместо 200700 г/см3, применяемых ранее, экологическая чистота, высокая надежность и постоянная готовность к применению, наличие совершенной технологии по методу свободного литья (вязкость массы находится в пределах
(28)·104, живучесть более 24 ч).
Разработано несколько составов (например, ПАС-8, ПАС-11), в которые входят в качестве основного компонента нитраты К, Na и углекислые К и Na, NaCl, KCl, K2Cr2O7, перхлораты К, Na, NH4, а в качестве связующего − нитроцеллюлоза, каучуки, полиэфирные, эпоксидные или резольные смолы. Температура горения их колеблется в пределах 910–1495 К, массовая доля твердой фазы 13–39 % [54].
Твердое топливо как источник газа помимо РДТТ может применяться и в других областях техники: для вращения турбины, приведения в действие пневмосистем, заполнения эластичных оболочек и т.д. Но их широкому применению препятствует высокая температура сгорания. Наиболее низкокалорийные твердые топлива дают газ с температурой 1400–1500 К, тогда как традиционные для техники материалы (металл, пластик, резина) выдерживают температуру 300–400 К. Следовательно, нужно снижать температуру продуктов горения топлива. По мнению В.А. Шандакова и В.Ф. Комарова [50, 51], температуру газов можно снизить, если создать заряд в виде материала со сквозной пористостью. Зона горения находится со стороны глухого торца камеры сгорания (рисунок 52) [53].
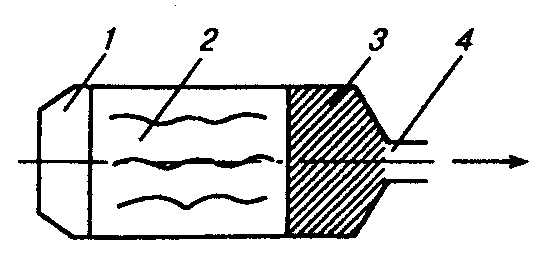
1 − глухой торец камеры сгорания; 2 − заряд ТТ; 3 − фильтр; 4 − сопло
Рисунок 52 − Схема сжигания пористого заряда ТТ в камере сгорания
Развивающееся в ней давление через поры в заряде выталкивает газ и продвигает жидкие продукты сгорания через тело пористой топливной шашки, подогревая ее до температуры газификации, т.е. подогретым телом служат продукты сгорания ТТ. При полном теплообмене газ перед фронтом тепловой волны будет иметь температуру, равную начальной температуре заряда. На практике она составляет 300–330 К.
Достоинства таких твердых топлив еще и в том, что в качестве газообразных продуктов сгорания можно получить индивидуальные газы, например, N2, O2 , H2 с чистотой 98,0–99,0 %. Область применения таких устройств весьма широка: средства спасения человека на земле и воде, аварийные пневмосистемы, средства пламеподавления и пожаротушения, грузоподъемные устройства и устройства вытеснения и далее медицинская помощь.
В технике можно использовать и высокую температуру, например, в нефтегазодобывающей промышленности.
Нефтяная скважина со временем угасает из-за закупорки пор нефтяного пласта выносимыми нефтью твердыми частицами, углеродами парафинового ряда и смолистыми веществами. Существовал метод воздействия на нефтеносный пласт давлением воды, но это дорого. Если же в заполненной жидкостью скважине в зоне нефтяного пласта создать при сжижении ТТ кратковременно давление выше давления горных пород, то удается не только прочистить закупоренные поры давлением и температурой задавливаемых в пласт газов, но и создать новые поры. Надо лишь очень быстро сжечь ТТ, воспользовавшись инерционностью столба жидкости над ним.
Для увеличения дебита скважины применяют гидрореагирующие составы при термохимической обработке.
Твердые топлива можно использовать в качестве химического реактора для синтеза различных веществ. Например, если в качестве окислителя взять смесь нитрата алюминия Al(NO3)3 с нитратами кобальта, хрома, железа, получим смешанный оксид AlxOy синего, зеленого и красного цвета − светостойкий пигмент для красок.
Если взять смешанные нитраты циркония и иттрия, получим основу жаростойкой керамики − стабилизированный диоксид циркония. Используя смешанные нитраты бария, меди и иттрия, получают сверхпроводящую керамику [19].
Гидрореагирующие составы применяют для наддува понтонов при подъеме затонувших объектов. Основными характеристиками гидрореагирующих составов являются количество тепла, выделяющегося при сгорании зарядов при взаимодействии с водой, количество воды, необходимое для сгорания одного состава и газопроизводительность.
Пороховые аккумуляторы давления. Пороховые аккумуляторы давления (ПАД) − твердотопливные энергетические устройства, служащие для преобразования химической энергии твердого топлива в энергию сжатого газа.
Типовая конструкция ПАД включает корпус, состоящий из высокопрочной оболочки, днища, соплового выпускного устройства и опор-ных элементов для заряда, сам твердотопливный заряд, воспламенитель и средства инициирования запуска.
ПАД по сравнению с системами сжатия холодного газа имеет ряд существенных преимуществ:
- компактность;
- быстродействие;
- меньшие массово-габаритные характеристики;
- хорошие эксплуатационные свойства при различных атмос-ферных воздействиях;
- высокая надежность работы.
Они нашли широкое применение в различных пневмо-вытесни-тельных системах гражданского и специального назначения. Например, выброс ракетных сигналов из пусковых шахт, наддув различных емкостей, быстрое открытие и закрытие крышек, люков, затворов, наддув нефтяных скважин, экстренное торможение [56, 80–82].
2.7.1 Принципиальный состав СРТТ и назначение
компонентов
СРТТ − это многокомпонентная композиция, каждый компонент которой выполняет конкретную и важную роль независимо от его содержания в рецептуре.
2.7.1.1 Окислители
Роль окислителя в СРТТ многофункциональна, но прежде всего он является поставщиком активного (свободного) окисляющего агента (O2, F2). Кроме того, окислитель оказывает огромное влияние на плотность и объем газообразных продуктов горения топлива, так как вводится в состав до 70,0–72,0 % и определяет токсичность продуктов горения.
Роль окислителя могут выполнять соли азотной кислоты (нитраты), соли хлорной кислоты (перхлораты) и нитросоединения органических веществ. При их разложении выделяется определенное количество активного окисляющего агента [57].
В таблице 5 представлены реакции разложения некоторых окислителей и содержание в них свободного кислорода в отсутствии горючих компонентов.
Таблица 5 − Реакции разложения окислителей
Химическая формула окислителя | Реакция разложения | Количество кислорода в 1 кг на 1 кг вещества | Растворимость в воде в граммах на 100 г раствора | |
при 20 С | при 100 С | |||
KClO3 | 2KClO3 = 2KCl + 3O2 | 0,39 | 7 | 36 |
NaClO3 | 2NaClO3 = 2NaCl + 3O2 | 0,45 | 50 | 97 |
KClO4 | KClO4 = KCl + 2O2 | 0,46 | 1,7 | 74 |
NaClO4 | NaClO4 = NaCl + 2O2 | 0,52 | 66 | 75 |
NH4ClO4 | 2NH4ClO4 = 4H2O + Cl2 + +2O2 + N2 | 0,34 | 18 | - |
KNO3 | KNO3 = K2O + N2 + 2,5O2 | 0,40 | 24 | 71 |
NaNO3 | 2NaNO3 = Na2O + N2 + +2,5O2 | 0,47 | 47 | 63 |
NH4NO3 | NH4NO3 = 2H2O + N2 + +0,5O2 | 0,2 | 64 | 91 |
Требования, предъявляемые к окислителям:
1. Максимальное содержание свободного (активного) окисляющего агента (O2, F2) − не менее 30 % и легкое выделение его при горении топлива.
2. Минимальная теплота образования. Чем она меньше, тем выше значение единичного импульса топлива
J = 9,3264
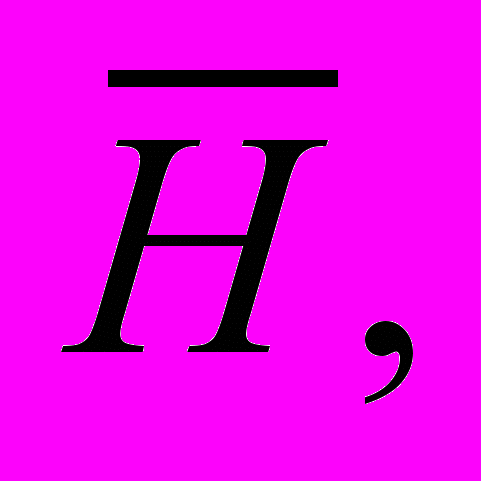
где
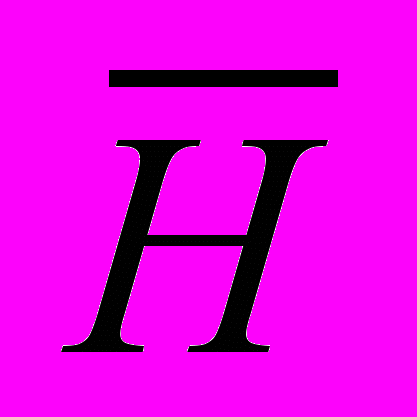
3. Стабильность свойств при температуре переработки, хранении и эксплуатации изделий. Окислитель не должен разлагаться и изменять своего агрегатного состояния.
4. Окислитель должен иметь: хорошую адгезию к связующему-горючему; минимальную чувствительность к механическим воздействиям; максимальную плотность; широкую сырьевую базу и низкую стоимость.
5. Он должен совмещаться без химического взаимодействия и выделения газообразных продуктов в процессе смешения топливной массы при хранении и эксплуатации изделий.
В таблице 6 приведены некоторые свойства солей и нитросоединений органических веществ, которые могут выполнять роль окислителя СРТТ.
Исходя из перечисленных требований, предъявляемых к окислителям, и анализа физико-химических свойств, представленных в таблице 6, можно сделать следующие рекомендации:
- С точки зрения содержания активного окисляющего агента наиболее выигрышно смотрятся перхлораты нитрония, нитрозила, лития и нитрат лития, но ни один из них не нашел применения в СРТТ, так как сильно гигроскопичны, а перхлораты нитрония и нитрозила нестойки.
- Поскольку рабочим телом в ракетном двигателе являются газообразные продукты горения топлива, то наиболее выгодно по объему газообразных продуктов, образующихся при разложении, применение нитрата аммония (0,980 м3/кг). Но он гигроскопичен и имеет низкое содержание свободного кислорода (20 %). Нитрат аммония нашел при-менение в качестве окислителя в составах для пороховых аккумуляторов давления. Заряды невелики по размерам и их можно хранить в герметично закрывающейся таре или полиэтиленовых пакетах.
3. Важным показателем для компонентов СРТТ является плотность, так как она определяет показатель весового качества ракетного двигателя. Максимальную плотность имеют соли бария, но при их разложении выделяется небольшой объем газообразных продуктов. Они широко применяются для изготовления пиротехнических изделий, так как сами и их оксиды придают пламени интенсивную зеленую окраску.
По комплексу характеристик в качестве окислителя СРТТ нашел широкое применение перхлорат аммония, хотя и выделяет при разложении небольшое количество свободного кислорода (34 %).
Таблица 6 − Физико-химические свойства солей и нитросоединений органических веществ
Наименование окислителя | Химическая формула | Молекулярная масса | Плотность, г/см3 | Температура плавления, С | Объем газов, выделяемых при разложении 1 кг вещества, м3 | Количество свободного кислорода, % | Физическая стабильность и химическая стойкость | |
1 | 2 | 3 | 4 | 5 | 6 | 7 | 8 | |
Нитрат лития | LiNO3 | 69,0 | 2,38 | 252 | 0,568 | 58,0 | Очень гигроскопичен | |
Нитрат натрия | NaNO3 | 85,0 | 2,20 | 308 | 0,439 | 47,1 | Гигроскопичен | |
Нитрат калия | KNO3 | 101,0 | 2,11 | 336 | 0,386 | 39,6 | малогигроскопичен | |
Нитрат аммония | NH4NO3 | 80,0 | 1,72 | 169 | 0,980 | 20,0 | Гигроскопичен | |
Нитрат бария | Ba(NO3)2 | 261,0 | 3,20 | 592 | 0,138 | 30,6 | малогигроскопичен | |
Перхлорат нитрония | NO2ClO4 | 145,5 | 2,25 | 180 р | 0,616 | 66,2 | Очень гигроскопичен, малостоек | |
Перхлорат нитрозила | NOClO4 | 129,5 | 2,17 | 50 р | 0,605 | 61,8 | сильно гигроско-пичен, нестоек | |
Гидразин диперхлорат | N2H4(ClO4)2 | 232,0 | 2,02 | 176 | 0,774 | 35,8 | Сильно гигроскопичен, высокая чувствительность к механ. возд. несовместим с комп. СРТТ | |
Перхлорат лития | LiClO4 | 106,4 | 2,43 | 236 | 0,422 | 60,2 | гигроскопичен | |
Перхлорат натрия | NaClO4 | 122,5 | 2,02 | 482 | 0,365 | 52,3 | гигроскопичен | |
Перхлорат калия | KClO4 | 139,0 | 2,52 | 610 | 0,322 | 46,2 | негигроскопичен | |
Перхлорат аммония | NH4ClO4 | 117,5 | 1,95 | 150 р | 0,790 | 34,0 | малогигроскопичен | |
Перхлорат бария | Ba(ClO4)2 | 336,4 | 2,34 | 505 | 0,270 | 38,0 | малогигроскопичен | |
Гексонитроэтан | C2(NO2)6 | 304,0 | 1,86 | 55 р | 0,516 | 53,3 | нелетуч, нестоек, склонен к тепловому самовоспла-менению | |
Октоген | C4H8N8O8 | - | 1,92 | 278,5–280,0 | - | - | - | |
Гексоген | C3H6N6O6 | - | 1,82 | 204,5–205,0 | - | - | - | |
Примечание − р − начало реакции разложения |
Перхлорат калия нашел применение в плазмообразующих составах. Остальные компоненты, представленные в таблице 6, применения в составах СРТТ не нашли, так как гигроскопичны. В последнее время в составах СРТТ широко применяются гексоген, октоген, а также
АДНА [52, 68, 72–73].
Свойства ПХА и способы его производства [61-62]. ПХА – белое кристаллическое вещество. Плотность 1,88–1,95 г/см3. Температура начала разложения 150 С (при длительном воздействии).
Он существует в двух кристаллических модификациях: ромбической и кубической. Обычная кристаллическая форма − ромбическая, при температуре 240 С переходит в кубическую, при этом увеличивается объем кристаллов и поглощается тепло. Ромбическая модификация представляет собой кристаллический порошок белого цвета с плотностью 1,95 г/см3.
ПХА склонен к электризации, причем его элекризуемость возрастает с увеличением дисперсности. Так, фракция с размером частиц 200300 мкм электризуется до потенциала 1,0–2,6 кВт, а фракция с размером частиц до 100 мкм – до 6,0–11,0 кВт. Увеличение его влажности с 0,04–0,07 % до 5,0–6,0 % снижает сравнительную электризуемость с 8,0–11,0 кВт до 0,4–1,7 кВт.
ПХА способен увлажняться. Его гигроскопическая точка при
20 С составляет 96,0 %. При относительной влажности воздуха 75,0 % влажность ПХА за 4–6 ч достигает равновесного состояния 1,5 %.
В связи с изменением гигроскопичности ПХА при изменении условий хранения может слеживаться. Слеживаемость и плохая сыпучесть затрудняют его переработку (фракционирование, дозирование, транспортировку). Он налипает на рабочие органы дозатора, что влияет на точность дозирования. Образование агломератов может быть причиной непромесов в топливной массе. Для снижения слеживаемости используют антислеживающие добавки.
ПХА растворим в воде, спиртах, а также в глицерине, ацетоне. Не растворим в бензине, толуоле, дибутилфталате, нитрометане, этиловом эфире, этиленгликоле и в абсолютном большинстве горюче-связующих веществ.
Химическая активность ПХА определяется тем, что это соль очень сильной кислоты и слабого основания. Вследствие этого водные растворы проявляют кислую реакцию, под действием концентрированных соляной и азотной кислот происходит полное разложение ПХА.
Щелочи легко вступают с ПХА в обменную реакцию. Вследствие чего нельзя использовать в контакте с ним материалы и вещества с основными свойствами. В сухом состоянии ПХА не взаимодействует с металлами, во влажном оказывает корродирующее действие. Это является следствием образования хлорной кислоты
NH4ClO4 + H2O = HClO4 + NH4OH,
которая корродирует металл. Поэтому все оборудование, предназначенное для переработки ПХА, должно быть изготовлено из нержавеющей стали.
ПХА − термически стойкое соединение, только при длительном нагревании при температуре 150 С можно добиться его разложения.
С повышением температуры и в присутствии примесей скорость распада растет.
Скорость и глубина разложения ПХА существенно изменяются в присутствии катализаторов. Например, добавка 1 % ферроцена повышает скорость распада ПХА в 2 раза, а добавка 1 % фтористого лития замедляет низкотемпературную стадию его распада.
Взрывчатые характеристики. ПХА способен детонировать от капсюля-детонатора № 8, если диаметр заряда превышает 60 мм и его плотность близка к единице. Увлажнение ПХА резко понижает его восприимчивость к детонации. Скорость детонации ПХА при изменении диаметра заряда от 60 до 90 мм возрастает с 2340 до 2780 м/с.
С увеличением степени дисперсности ПХА скорость детонации растет.
ПХА молочувствителен к тепловому импульсу. Свободно насыпанный на поверхность в количестве до 100 кг не воспламеняется от мощного луча огня.
Чувствительность ПХА к механическим воздействиям зависит от его дисперсности, влажности, присутствия примесей и условий испытаний.
Токсичность. ПХА относится к весьма токсичным веществам. Соединения хлорной кислоты блокируют поступление йодидов из крови в щитовидную железу. При воздействии ПХА на организм развивается острая или хроническая интоксикация, наблюдается расстройство кровообращения и дистрофическое изменение мышц сердца, почек, печени. Снижается деятельность вегетативной нервной системы.
ПХА влияет на кальциевый обмен − приводит к разрушению костной ткани эмали. Допустимая концентрация ПХА в воде водоемов
3 мг/л. Максимальная концентрация в смеси производственных и хозяйственно-фекальных вод не должна превышать 150 мг/л. Предельно допустимая концентрация (ПДК) в воздухе 0,001 г/м3.
Производство ПХА. Промышленностью освоено два способа получения ПХА:
- нейтрализацией хлорной кислоты газообразным аммиаком;
- обменной реакцией между перхлоратом натрия, аммиаком и соляной кислотой.
Основным сырьем для получения ПХА по методу нейтрализации являются: соляная кислота, газообразный аммиак и дистиллированная вода.
Технологический процесс состоит из трех стадий:
- Получение технической (48–50%-ной) хлорной кислоты электролизом водного раствора соляной кислоты.
- Очистка хлорной кислоты от соляной электрохимическим методом.
- Получение ПХА взаимодействием хлорной кислоты с аммиаком.
Обменный метод получения ПХА применяется на большинстве действующих заводов. Основное сырье: хлорид натрия, аммиак, соляная кислота.
Технологический процесс получения ПХА состоит из следующих стадий:
1. Электрохимическое окисление хлорида натрия до хлората натрия.
2. Электрохимическое окисление хлората натрия до перхлората натрия.
3. Обменная равновесная реакция в растворе между перхлоратом натрия, аммиаком и соляной кислотой.
Получают ПХА трех марок: К, С, М (крупный, средний, мелкий), отличающихся между собой гранулометрическим составом.
В производстве СРТТ используется перхлорат аммония с округлой формой частиц с целью снижения вязкости топливных масс и повышения уровня физико-механических характеристик топлива [6162].
2.7.1.2 Связующие-горючие
Связующее-горючее в составе СРТТ выполняет следующие функ-ции:
- обеспечивает определенный уровень реологических характеристик топливной массы в сочетании с окислителем и энергетической добавкой;
- связывает в единое целое компоненты топлива, придавая заряду необходимый уровень физико-механических характеристик;
- является дополнительным источником тепловой энергии и газообразных продуктов горения топлива.
Количество горюче-связующего вещества в составе СРТТ определяется прежде всего содержанием активного окисляющего агента. Чем больше активного кислорода в окислителе, тем больше можно взять связующего-горючего для обеспечения стехиометрического соотношения компонентов. Если связующее-горючее в своем составе содержит активные группы −NO2, −ONO2, −F2 и др., то его количество для получения стехиометрического соотношения может достичь
30 % масс. и есть возможность получить топливную массу с низкой вязкостью. Чтобы обеспечить однородность состава топлива, устойчивость ее структуры и высокие физико-механические характеристики топлива, количество связующего должно быть не менее 10 % масс. Кроме того, количество связующего-горючего оказывает большое вли-яние на реологические свойства топливной массы и определяет способность ее переработки. Так, при содержании связующего-горючего в рецептуре в количестве 10 % масс., топливная масса может перерабатываться глухим прессованием, при содержании 10–15 % масс. − приходным прессованием, 10–20 % масс. − литьем под небольшим давлением, 15–20 % свободным литьем.
Связующее-горючее может представлять собой смесь горючего со связующим (металл+смола) или соединением, обладающим одновременно свойствами горючего и связующего (битумы, каучуки). Низкомолекулярные горюче-связующие как компоненты СРТТ малопригодны. Практический интерес в качестве связующих-горючих СРТТ представляют высокомолекулярные соединения [63–64, 75–76].
Требования, предъявляемые к связующим-горючим:
1. Связующее-горючее должно быть вязкой жидкостью или твердым полимером, способным образовывать с низкомолекулярным веществом термодинамически устойчивые системы, способные к восприятию большого количества наполнителя (окислитель, специальные до-бавки). Низкая вязкость связующего-горючего может привести к расслаиванию топливной массы и не позволит выполнить требования по уровню физико-механических характеристик.
2. Связующее-горючее должно иметь:
- хорошие смачивающую способность и адгезию к наполнителю;
- низкую температуру стеклования;
- высокое отношение водорода к углероду;
- отсутствие в составе элементов, дающих агрессивные продукты горения;
- малую теплоту образования, а продукты окисления большую теплоту образования;
- оптимальную плотность;
- высокую физическую и химическую стабильность с целью обеспечения требуемого гарантийного срока хранения изделия;
- широкую сырьевую и промышленную базу, что гарантирует низкую стоимость.
3. Связующее-горючее должно обладать требуемой «живучестью» (жизнеспособностью) при переработке топливной массы и способностью отверждаться при температуре 40–60 С без существенного выделения тепла и с минимальной усадкой.
4. В отвержденном состоянии оно должно иметь высокие физико-механические характеристики и обладать упруго-эластичностью для обеспечения сохранения сплошности изделия, сопротивляемости сжатию и растяжению.
5. В целях безопасной переработки должно обладать низкой чувствительностью к механическим воздействиям.
Основные представители связующих-горючих. Одним из первых каучуков, нашедших применение в качестве связующего-горючего СРТТ, был полисульфидный каучук − тиокол. Он является продуктом взаимодействия дихлордиэтиленформаля с тетрасульфидами щелочных металлов. Отличительный признак тиокола − наличие меркаптановых групп −SH.
В производстве СРТТ нашли применение тиоколы марок НВТ-1 и Т-2.
Тиокол НВТ-1
H


S S