Государственного Рязанского Приборостроительного завода, специализирующегося на изготовлении сложных радиоэелектронных систем и бортовой техники 23 лекция
Вид материала | Лекция |
- Лекция 1 Виды математических моделей сложных систем, 201.52kb.
- Атмосфера: военная, 615.07kb.
- Лекция № Методы количественного оценивания систем (продолжение) Оценка сложных систем, 156.28kb.
- Концепция Регионального семинара Актуальные проблемы сложных систем в науке и образовании, 25.37kb.
- Лекция Развитие компьютерной техники, 430.69kb.
- Учебная программа по дисциплине основы технической эксплуатации и защиты вычислительных, 119.22kb.
- Лекция История развития баз данных, 160.99kb.
- Сложных технических систем, 363.08kb.
- Рабочей программы дисциплины Методы управления развитием сложных технических систем, 23.23kb.
- Рабочая программа для специальности: 220400 Программное обеспечение вычислительной, 133.96kb.
Оценка предотвращения тепловых повреждений
На начальном этапе проектирования необходимо наряду с анализом электронной схемы проводить тепловой анализ проекта, т.к. в системе присутствуют тепловые потоки от переходов в определенную среду. Предельная температура переходов для полупроводников обычно составляет 150оС. Чем ниже рабочая температура перехода, тем выше надежность устройства. Снизить tо С переходов во время работы оборудования можно с помощью теплоотводов, вентиляторов или отверстий для естественной вентиляции. Эти же меры применяются и для охлаждения элементов схемы- конденсаторов, резисторов и т.д. Дополнительным испытанием на тепловыделение могут быть предельные теплоэенергетические нагрузки, которые должны быть выявлены в начале процесса проектирования. На тепловую нагрузку влияет и температура окружающей среды. Для предотвращения влияния рассчитывается рабочий диапазон, а также проверяются тепловые испытания компонентов и всего устройства в целом.
Особенности анализа проекта
Тепловой анализ проекта является неотъемлемым этапом проектирования, который выполняется в самом начале процесса проектирования, т. к. на более поздних стадиях проекта наличие теплового воздействия может вызвать угрозу для всего проекта.
Первым, и наиболее важным моментом, я вляется выбор таких элементов, которые соответсвуют рабочему диапазону температур, заданному в тех задании.
Второе – равномерное размещение тепловыделяющих элементов на коммутационном поле.
Третье – установка теплопроводов и организация вентиляциию необходимо учитывать, что мероприятия по сбережению нормального теплового режима не должны приводить к увеличению стоимости всего устройства.
К другим рекомендациям по обеспечению нормального теплового р-тия относят:
- Чувствительные к нагреванию элементы необходимо размещать отдельно от интенсивных источников света (конденсаторы и полупроводниковые приборы) такие как проволочные резисторы, диоды, транзисторы, регуляторы напряжения
- Должны быть созданы хорошие условия для воздухопроницаемости
- Необходимо иметь ввиду, что интенсивность охлаждения теплопровода тем выше, чем больше площадь поверхности
- При необходимости можно делать вентиляционные отверстия, диаметр которых не должен приводить к источнику помех
- Расчет тепловыделения необходимо производить для наиболее жестких условий эксплуатации
- Необходимо учитывать, что установка теплоотводов и вентиляторов сама по себе полглощает внутреннее производство устройства, что ухудшает вентилляцию.
- Требования к охлаждению должны определяться назначением оборудования к обеспечению его надежности
- Расчет тепловых процессов в системе производится с помощью автоматизированных систем, которые определяют необходимость моделирования тепловых режимов
- Как правило, проводится съемка рабочего макета печатной платы с помощью тепловизора в условиях предельной нагрузки с целью выявления наиболее тепловыделяющих частей и их расформирования на площади платы
При разработке платы необходимо учитывать как тепловые воздействия, возникающие при работе схемы, так и тепловые воздействия, которым будет подвергяться плата или устройство в процессе пайки.
Способы оценки надежности и качество функционирования электронного оборудования
Надежность изделия необходимо прогнозировать до его запуска в производство. Для прогнозирования необходимы следующие мероприятия:
- Обеспеченность инструкциями, измирительными приборами и испытательными стендами
- Контроль качества материалов, полуфабрикатов и деталей, поставленных внешними производителями
- Классификация дефектов и качественных характеристик выпускаемых изделий
- Систематический выборочный контроль изделий по показателям качества
- Контроль над особыми условиями и видами производства
- Наблюдение за нестандартными методами и учет статуса их годности
- Проведение специальных испытаний без разрушения проверяемых изделий
При сопоставлении запланированного качества , определенного конструкторской технической документацией, и качества готового изделия, соответствующее классификации дефектов, опредеяется регламентирующими документами:
- Технологическими инструкциями (карты, маршруты)
- Инструкции по приемке изделия, т. е. их проверки, контроля и аттестации
Таким образом, формируется требование к стандартному уровню качества.
К гнезду основных стандартных оценок качества относят:
- Допустимый процент дефектов на одно изделие, если оно спорное при дефектных изделий на партию из 100 штук, если изделие простое.
- Уровень среднего выходного качества, которое устанавливают на основе расчета плана выборочного контроля при ускоренных испытаний.
- Допустимое число взвешенных дефектов, приходящихся на одно изделие.
Для расчета причинных оценок используют:
- Статистические данные за некоторые предшествующие периоды расчета средних значений параметров качества и обоснования стандартных норм.
- Данные накопленные в процессе опытов, исследований для расчета норм качества для изделия и аналогов.
- Внесение параметров , характеристик, технические требования, предъявленные к качеству изделия, в т.ч. данные анализа затрат на обеспечение качества.
Современная практика показывает, что:
- Общий уровень качества изделия при положительных стандартах примерно на 25% ниже, чем при действующем стандарте.
- Целесообразно установить стандарт используя данные , разносторонних периодов до 80% расчетов среднего значения.
- Наиболее предположительный для расчета стандартов являются данные ,полученные на основе опытов и испытаний. Стандарты, основанные на технических требованиях, нормах и рассчитанные ранее значения параметров дают больший выигрыш потребителю и ограничивают производителя.
- Экономически выгодные оценки, нормы и стандарты качества, учитывающие min затрат на обеспечение качества, рассчитываются путем поиска оптимальных решений в конкретных устройствах, изделиях.
Надежность изделия.
Надежность изделия должна обеспечиваться во время всего срока эксплуатации изделия. Динамика процесса эксплуатации изделия, представляется 3-мя фазами: отладка, эффективная нормальная работа, старение (период ремонтов).
Отладка: характеризуется коротким периодом t, резким сокращением числа отказов, благодаря замене некачественных деталей, устранению ошибок сборки.
Эффективная работа: характеризуется длительным временем, включающим гарантийный срок безотказной работы на этом этапе, уровень отказов очень низкий и они носят случайный характер. Этот период обеспечивает ценовую политику производителя и риск потребителя.
Старение: характеризуется высоким уровнем отказов в связи с износом элементов , старением материалов, изменением их прочностных свойств.
Отказ на каждом этапе эксплуатации изделия оценивается с помощью отдельных законов распределения случайных величин. Для отклонения первой фазы наиболее часто используется j- распределение. Для второй фазы – экспоненциальное распределение. Для третьей фазы- нормальное распределение или суперпозиция нормального распределения.
Для оценки надежности выполняются преобразования распределения для получения точности распределения вероятности отказов.
J-распределение
Xt exp (-xt)
F (х) =----------------------
Г (a -1)* b k-1
Прочность распределения:
Θt-1 exp (-Θ/е)
F(х) = --------------------
Г (d)- t-d
x- случайная величина
a, b - параметры распределения
Г – гамма функция
T – формообразующий характер кривой распределения
d – частота появления отказа
Θ – период службы изделия
Лекция 12
План выборочного контроляизделия по сроку службы можно представить в виде планов контроля безотказности, добавив внешнюю нагрузку, и приняв в качестве допущения, что после фазы отладки следующая фаза подготовки экспонентациального распределения. При этом возможны следующие варианты организации испытаний с целью оценки безотказности как среднего срока службы изделия:
- Испытания заканчиваются после фиксации заранее установленного срока отказов. При этом используется знание приемлимого и неприемлимого срока службы изделий для сравнения
- Испытания заканчиваются по истечение заданного времени t с заменой или без замены оставшихся элементов. Извне задаются следующие параметры: объем выборки N, приемлимый срок службы изделия, установленное время проведения испытаний
По результатам испытаний для определенного вида изделий могут составляться сводные данные для различных режимов и периодов эксплуатации. Если далее оценивается надежность изделия, относящегося к типу изделий, для которых уже составлены справочные данные по испытанию, выбираются соотвествующие показатели надежности без нового проведения испытаний, что экономит временные затраты при производстве изделия
Отбраковочные технологические испытания как средства повышения надежности партии интегральных микросхем
Качеству и надежности интегральных микросхем предъявлены высокие требования вне зависимости от того, где они используются. Посчитано, что при доле дефективности партии интегральных микросхем в пределах 0,01%, т.е. 100 схем на 1 млн. Доля постоянных отказов печатных плат, на которых смонтировано 100 интегральных микросхем, составляет более 9%. При дефективности партии ИС в пределах 1% выход годных печатных плат составляет 63,4 %, т.е. брак составит 3,4 %.
Надежность ИС характеризуется кривой зависимости интенсивности отказов λ(t)
λ

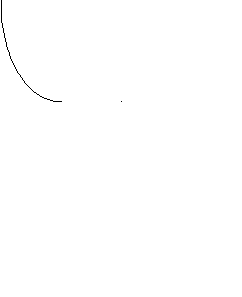
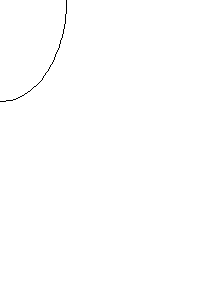















I 1000 II 150 000 III t
I – период приработки (ранние отказы) – 1000 ч
II – период нормальной работы (случайные отказы)
III – период старения (интенсивные отказы) – 150 000 ч
В настоящее время общепринятыми являются 2 направления увеличения надежности выпускаемых микросхем
- Выявление и удаление изделий с отказами действительными и потенциальными из готовой партии поставки потребителям
- Устранение причины отказов засчет совершения конструкции и технологии изготовления, т.е. воздействие на процесс производства посредством обратной связи, т.е. передача информации от людей, использующих интегральные микросхемы в производстве, что ведет к разработке бездефектных технологий.
Этот метод является более перспективным.
Одним из эффективных способов повышения надежности партии интегральных микросхем является выходной контроль партии на заводе-изготовителе, т.е. проведение браковочных испытаний. Считается, что случайных отказов ИС не бывает. Каждый имеет причину и является средством предложенной нагрузки. Для того, чтобы отбраковочные испытания были эффективны, необходимо знать, какие нагрузки ускоряют появление разного рода отказов.










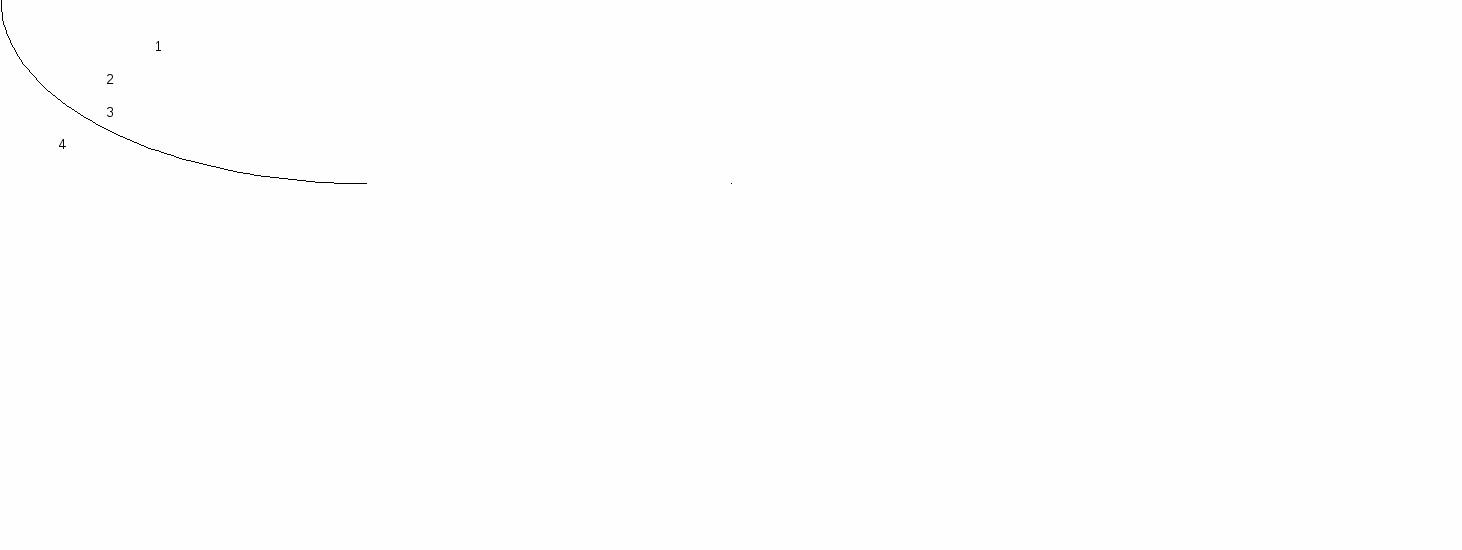
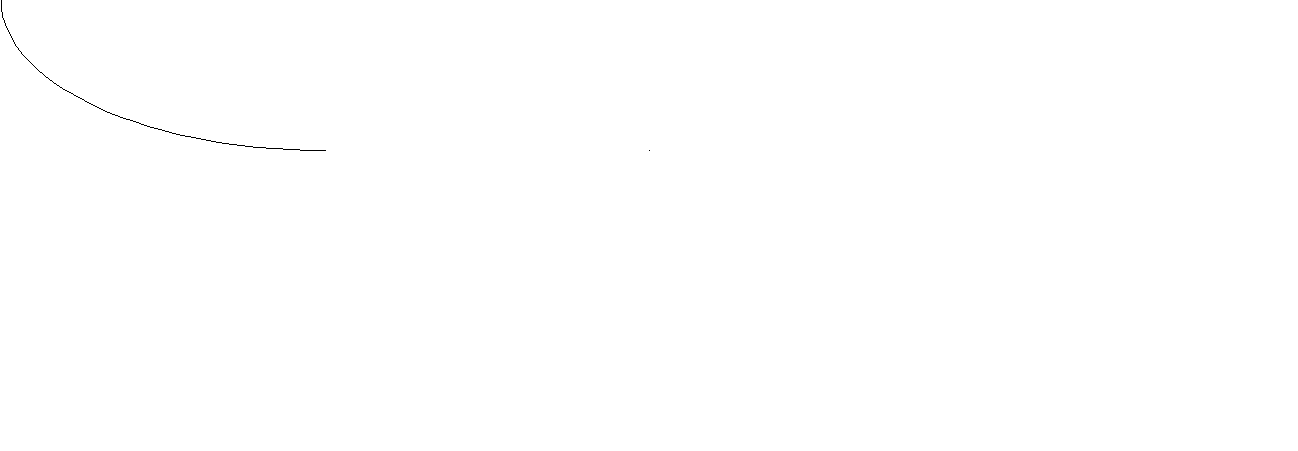
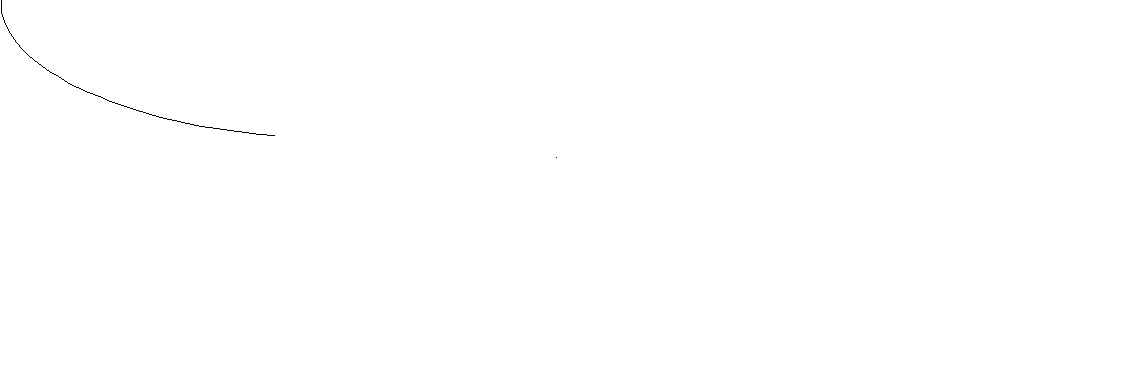
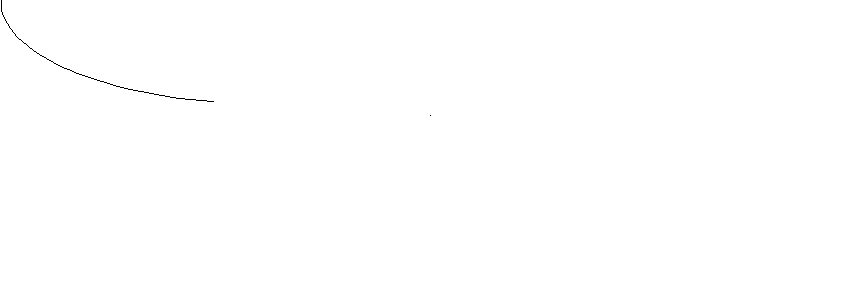
10-6
10-8
a 0 10 100 1000 10 000 t
График выполнения отбраковочных испытаний на интенсивность отказов.
0 – момент поставки заказчику
1 – без отбраковочных испытаний
2 – когда только электрические испытания
3 – стабильная тренировка, циклическая t испытания и проверка электрических параметров
4 – 3 + тренировка в утяжеленных режимах
На сегодня применяют такие виды отбраковочных испытаний:
- Контроль внешнего вида
- Электрические испытания
- Повышение температуры
- Одиночные удары
- Многократные удары
- Цинтрифуга
- Испытания на герметичность
- Рентгеноскопия
- Теплоэнерготренировка
- Энергоциклы
- Повышение влажности
- Термоциклы
- Вибрация
Многие различные по природе дефекты приводят к одним и тем же механическим отказам. Многие одинаковые механизмы отказов ускоряются раздичными нагрузками и многие различные механизмы отказов одними и теми же механическими нагрузками. Термоциклы ускоряют отказы и выявляют негерметичность корпуса, а также выявляют напрямую места конструкции, склонные к образованию дефектов корпуса интегральной микросхемы. Кроме тепловых и термоциклических испытаний, используются механические испытания с постоянной или измененной нагрузкой, которые могут выявить дефекты монтажа кристаллов внутренних соединений и соединений корпуса ИС с внешними выводами.
В общетехнических (ОТУ) и технических условиях (ТУ), как правило, указывается состав обязательных отбраковочных испытаний, их режимы и последующие заводы-изготовители ИС расширили состав исптаний в начальный период серийного производства. Их число снижено по мере сбора статистики. Может корректироваться вся программа испытаний, но кроме тех, которые указывают как обязательные в ОТУ и ТУ.
Состав отбраковочных испытаний ИС в отечественной промышленности
Во всех отечественных регламентирующих документах по выпуску ИС указано, что в процессе изготовления должны проводиться 100% браковочные испытания. Состав обязательных 100% испытаний включает до 20 видов по СОТУ, не менее 10 видов по ОТУ на ИС с приемкой заказчика и не менее 10 видов по требованию на ИС широкого применения. Методичка и условия испытаний описаны в ОСТ.
Виды и методы отбраковочных испытаний
Вид испытания | Условия испытания | Состав испытания | ||
САТУ | ОТУ | ТУ | ||
Визуальный контроль кристаллов | Увеличение в 200 раз, в 100 раз и в 80 раз | + | + | + |
Контроль монтажа кристаллов | По технической документации | + | + | + |
Контроль прочности крепления кристаллов | Выборочно по 2 схемы от каждой установки в начале и через каждые 2 ч | + | - | - |
Контроль прочности сварного соединения | Выборочно по 2 схемы от каждой установки в начале и через каждые 2 ч | + | + | - |
Визуальный контроль сборки перед герметизацией | Увеливение не менее чем в 32 р | + | + | + |
Теплообработка сборки перед герметизацией | 48 ч при 150 градусах | + | + | + |
Герметизация | В контрольной инертной среде | + | - | - |
Термообработка для стабилизации параметров | 24 ч при верхнем значении температур | + | + | + |
Испытания на воздействие изменений температурной среды | 10 циклов от -60 до +150 градусов | + | + | + |
Испытание на воздействие линейного ускорения | 30 000g | + | - | - |
Контроль свободно-перемещаемых частиц внутри корпуса | По технической документации | + | - | - |
Промежуточные электрические испытания, контроль статических параметров при нормальных климатических условиях | По технической документации | + | + | + |
Электротермотренировка | 240 ч для МДПсхем и 168 ч для биполярных | + | + | + |
Промежуточные электрические испытания, контроль статических параметров при нормальных климатических условиях | По технической документации | + | + | + |
Электротермотренировка при обратном смещении | 72 ч по технической документации | + | - | - |
Проверка статистики, динамичных параметров при нормальных климатических условиях, пониженной температуре и повышенной температуре | По технической документации | + | + | + |
Рентгеновский контроль | По технической документации | + | - | - |
Проверка герметичности | По технической документации | + | + | + |
Контроль внешнего вида | По технической документации | + | + | + |