Учебное пособие санкт-петербург 2 004 удк 669. 2/8; 669. 4 (075. 80) Ббк 34. 33
Вид материала | Учебное пособие |
Содержание2.8. Переработка цинксодержащих шлаков Рекомендательный библиографический список |
- Учебное пособие Санкт-Петербург 2008 удк 005. 91: 004. 9(075. 8) Ббк 65. 291. 212., 97.7kb.
- Учебное пособие санкт-петербург 2005 удк 339. 9 (075. 80) Ббк, 703.64kb.
- Учебное пособие Санкт-Петербург 2011 удк 621. 38. 049. 77(075) Поляков, 643.33kb.
- Учебное пособие Ульяновск 2010 удк 004. 8(075. 8) Ббк 32. 813я73, 1559.86kb.
- Учебное пособие разработано в соответствии с государственным стандартом специальности, 1131.24kb.
- Учебное пособие санкт Петербург 2010 удк 001. 8 Ббк, 1217.72kb.
- Учебное пособие Санкт-Петербург 2011 удк 1(075., 3433.28kb.
- Учебное пособие Санкт-Петербург 2005 удк 662. 61. 9: 621. 892: 663. 63 Ббк г214(я7), 546.15kb.
- Учебное пособие удк 159. 9(075) Печатается ббк 88. 2я73 по решению Ученого Совета, 5335.58kb.
- Учебное пособие тверь 2008 удк 519. 876 (075. 8 + 338 (075. 8) Ббк 3817я731-1 + 450., 2962.9kb.
Cu
0 20 40 60 80 Cu, %





t, C
1000
600
327,4
200
Pb


7,3 %
957 C
65 %
1084 C
327,4
325
0,06 % Cu
99,94 % Pb

325 C
Рис.2.7. Диаграмма состояния системы Cu-Pb
Тонкое обезмеживание свинца основано на большем сродстве серы к меди, чем к свинцу. Для проведения тонкого обезмеживания при температурах 330-350 С в свинец механической мешалкой с импеллером вмешивают серу из расчета примерно 1 кг серы на 1 кг удаляемой меди, разделив ее на несколько порций. Оборотные сульфидные съемы содержат 1-5 % меди и до 95 % свинца. Содержание меди в свинце снижается до 0,001-0,003 %.
Съемы с высоким содержанием меди подвергают переработке для извлечения части свинца и получения медьсодержащего штейна, который затем далее обычно перерабатывают конвертированием.
При проведении предварительного обезмеживания свинца в непрерывном режиме всплывшую на поверхность свинца медь переводят в форму сульфида меди (Cu2S) по реакции (2.11), добавляя в рафинировочную печь высокосортный сульфидный свинцовый концентрат. В этом случае медьсодержащим полупродуктом является штейн.
Удаление из свинца теллура основано на способности этого металла образовывать с натрием теллурид натрия (Na2Te), который имеет температуру плавления 953 С, плохо растворим в свинце и имеет плотность меньшую, чем плотность свинца. Для образования Na2Te в свинец при температурах 400-450 С вмешивают натрий в виде свинцово-натриевого сплава, содержащего 3 % натрия. Чтобы уменьшить потери натрия и лучше собрать с поверхности свинца Na2Te, на поверхность свинца загружают небольшое количество NаOH. Теллуровые съемы перерабатывают гидрометаллургическим методом для извлечения теллура.
Рафинирование свинца от мышьяка, сурьмы и олова (смягчение свинца) основано на большем сродстве к кислороду этих металлов, чем у свинца. На практике в качестве окислителя используют кислород воздуха или нитрат натрия (NaNO3). В первом случае процесс рафинирования проводят в отражательных печах, которые могут работать как в периодическом, так и в непрерывном режиме. Температуру свинца в печи поддерживают в пределах 800-900 С. Окисление примесей, а также частично и свинца тоже идет как за счет кислорода печной газовой фазы, так и за счет кислорода воздуха, продуваемого через свинец. Оксиды примесей и свинца образуют на поверхности свинца съемы, которые удаляют из печи гребками или выпускают в жидком виде.
Щелочное рафинирование свинца (процесс Гарриса) проводят при 420-450 С в котле, в который устанавливают специальный аппарат (рис.2.8). В реакционный цилиндр аппарата заливают расплавленную каустическую соду (обычно она содержит некоторое количество NaCl, который в процессе не участвует) и туда же небольшими порциями в качестве окислителя подают NaNO3. Насосом, погруженным в свинцовую ванну, непрерывно перекачивают свинец, пропуская его через щелочной плав. Примеси (As, Sb, Sn) окисляются и образуют с натрием соли (соответственно Na3AsO4, Na3SbO4 и Na2SnO3), тогда как свинец практически не окисляется. Соли примесей задерживаются в щелочном плаве, который с ростом содержания в них солей примесей постепенно загустевает. При достижении допустимого содержания примесей в плаве из реакционного цилиндра его сливают в приемный ковш. Для слива плава закрывают клапан реакционного цилиндра, а свинец продолжают в него подавать. Щелочной плав перерабатывают гидрометаллургическим методом для регенерации NaOH и извлечения примесей в виде товарных продуктов (обычно Na3SbO4 , Ca3(AsO4)2, CaSnO3).
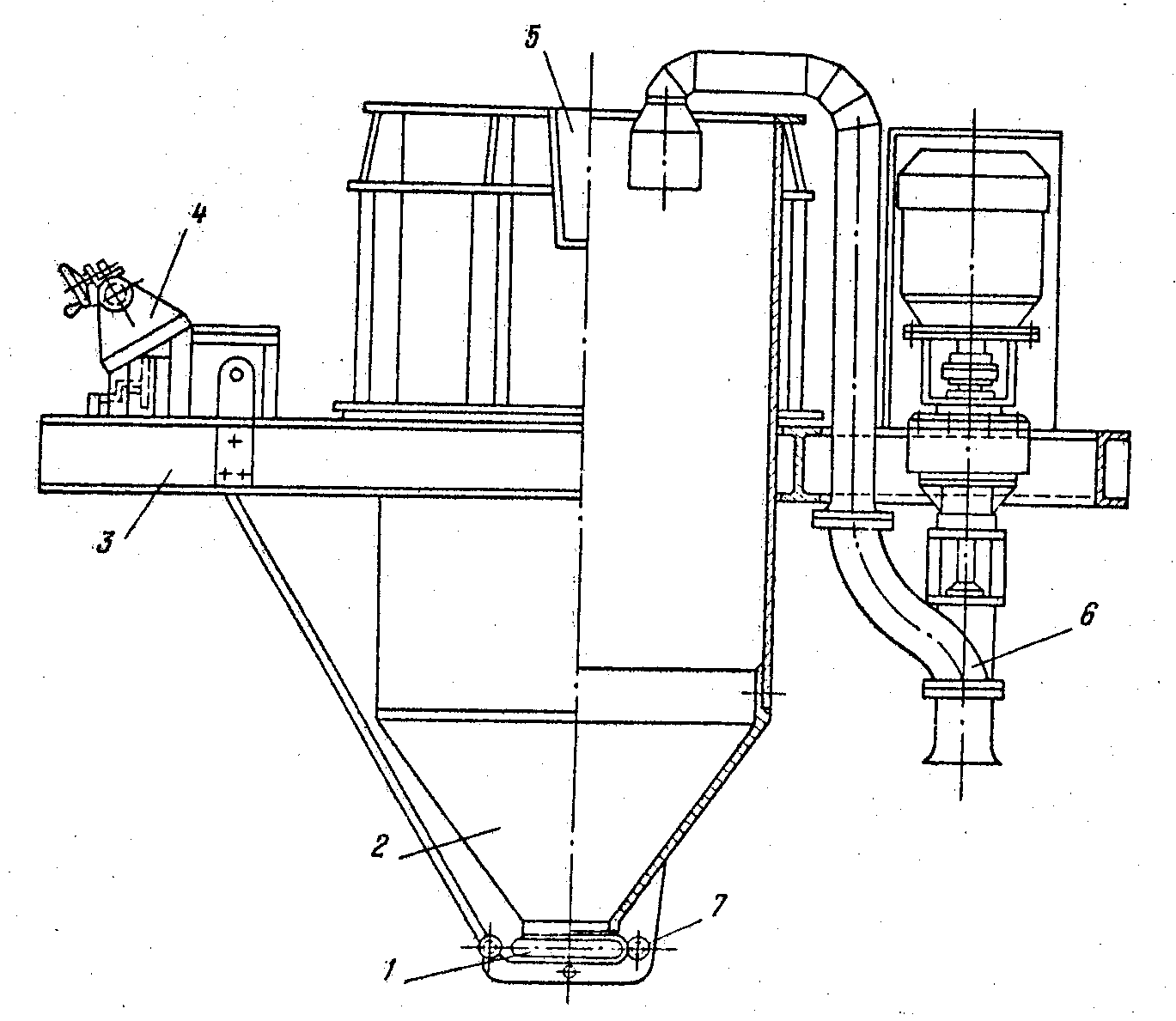
1
3
7
6
2
4
5
Рис.2.8. Аппарат для щелочного рафинирования свинца
1 – клапан; 2 – реакционный цилиндр; 3 – опорная рама; 4 – механизм открывания
и закрывания клапана; 5 – желоб для слива плава; 6 – насос для перекачки свинца;
7 – запорное устройство
Обессеребривание свинца повсеместно сейчас проводят вмешиванием цинка в расплавленный свинец (Паркесс-процесс). Метод основан на следующих свойствах компонентов процесса:
ограниченная растворимость цинка и свинца друг в друге в жидком состоянии;
более высокое сродство серебра и золота, чем свинца, к цинку;
способность цинка образовывать с серебром и золотом ряд соединений и твердых растворов, имеющих более высокие температуры плавления, чем свинец (Ag2Zn3 – 665 C, Ag2Zn5 – 636 C, AuZn – 744 C, Au3Zn5 – 651 C, AuZn3 – 490 C), и плотность, меньшую плотности свинца, а также плохо растворимых в свинце.
На практике процесс обессеребривания в периодическом режиме проводят в обычных котлах, вмешивая цинк и снимая серебристую пену шумовкой. В непрерывном режиме процесс обессеребривания проводят в вертикальном котле специальной формы. Свинец пропускают через слой цинка, находящийся в верхней части котла, а обессеребренный свинец выводят из нижней части котла через сифон.
Обессеребривание свинца в периодическом режиме обычно проводят в две стадии (иногда в три). Первую стадию проводят при температуре около 500 С, вмешивая в свинец оборотную пену от второй стадии и некоторое количество цинка. Богатую серебристую пену снимают при той же температуре. Ее состав следующий, %: Ag 5-10; Zn 20-25; Pb 65-75. На второй стадии в свинец при температурах 425-450 С вмешивают весь остальной цинк, необходимый для обессеребривания свинца. После вмешивания цинка температуру свинца снижают до 330-340 С и с его поверхности снимают оборотную (бедную) пену. Остаточное содержание серебра в свинце может быть менее 5 г/т. Общий расход цинка зависит от содержания серебра в свинце и часто составляет 1,5-2 % от массы свинца.
Богатую серебристую пену перерабатывают в несколько стадий. Сначала путем ликвации в котле из нее удаляют часть свинца и получают более богатую пену, содержащую 10-15 % Ag, 30-35 % Zn и 50-60 % Pb. Основные составляющие этой пены имеют различные температуры кипения (Zn – 906 С, Pb – 1750 С, Ag – 2212 С, Au – 2947 C), поэтому следующей операцией является удаление из пены и извлечение в виде металла цинка путем дистилляции пены при температурах 1100-1200 С в ретортных или электрических печах. Сконденсированный цинк возвращают в операцию обессеребривания. Другим продуктом дистилляции является свинец, обогащенный благородными металлами.
Этот свинец перерабатывают купелированием. Процесс купелирования заключается в окислительном плавлении обогащенного благородными металлами свинца на поду небольшой отражательной печи при температурах, превышающих температуру плавления глета (883 С). Под воздействием вдуваемого в печь воздуха свинец и другие неблагородные металлы окисляются и удаляются из печи в виде сплава оксидов, тогда как благородные металлы остаются в свободном виде. На практике процесс купелирования свинца проводят при 900-1100 С. Схематически его можно представить реакцией
Pb(Ag + Au) +
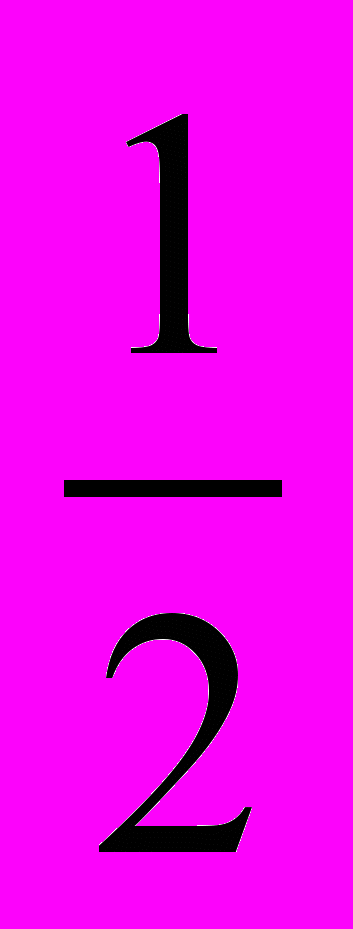
Продуктами процесса купелирования являются глет, восстановлением которого получают свинец, и серебро или сплав серебра с золотом (металл Доре), которые разливают в слитки и направляют потребителю или на аффинажные заводы.
После проведения обессеребривания свинца вмешиванием цинка в свинце остается 0,6-0,7 % этого металла, поэтому необходимо провести обесцинкование свинца. Известно несколько способов, которыми можно провести очистку свинца от цинка: окислительное, щелочное, хлорное и вакуумное рафинирование.
Окислительное и щелочное рафинирование в принципе аналогично процессам рафинирования свинца от мышьяка, сурьмы и олова.
Хлорный метод рафинирования свинца от цинка основан на предпочтительном взаимодействии хлора с цинком по сравнению со свинцом. Процесс проводят при температуре 380-400 С в специальном аппарате, обеспечивающем возможность контакта газообразного хлора с рафинируемым свинцом. Полупродуктом процесса являются хлоридные съемы, состоящие в основном из ZnСl2. После их рафинирования получают товарный хлорид цинка. Этот способ рафинирования используется редко из-за токсичности хлора.
Вакуумное рафинирование свинца от цинка основано на большей летучести цинка по сравнению со свинцом. Для обесцинкования свинца этим методом его перекачивают насосом в котел, закрытый сверху стальным колоколообразным сосудом, имеющим водоохлаждаемую крышку. Внутренняя полость сосуда соединена с вакуум-системой. Для обновления поверхности свинца аппарат оборудован мешалкой. При проведении процесса температуру свинца поддерживают около 600 С. Остаточное давление внутри рабочего пространства составляет 7-30 Па. В этих условиях из свинца преимущественно возгоняется цинк, который затем конденсируется на поверхности водоохлаждаемой крышки. За 4-8 ч пребывания металла в указанных условиях из свинца удаляется 85-95 % цинка и не более 0,4 % свинца. После завершения процесса в полости аппарата снимают вакуум, аппарат вынимают из котла и с крышки отбивают свинцово-цинковый сплав, содержащий 60-90 % цинка. Остаточное содержание цинка в свинце 0,01-0,06 %. Цинково-свинцовый сплав используют при обессеребривании свинца.
Удаление висмута из свинца (иногда в этой операции нет необходимости) проводят в две стадии, используя в качестве реагентов кальций, магний и сурьму. В первой стадии (предварительное обезвисмучивание) процесс ведут при 360-380 С, вмешивая в свинец сначала металлический кальций (или свинцово-кальциевый сплав, содержащий 2-4 % кальция), а затем металлический магний. Этот процесс основан на том, что при совместном вмешивании в свинец кальция и магния образуется тройное соединение Bi2Ca3 2Bi2Mg3, имеющее высокую температуру плавления (температура плавления самостоятельных Bi2Ca3 и Bi2Mg3 соответственно 1350 и 823 С) и плохо растворимых в свинце. Висмутсодержащие дроссы снимают с поверхности свинца. После предварительного обесвисмучивания содержание висмута в свинце снижается примерно до 0,02 %. Чтобы снизить содержание этого металла в свинце до 0,005 % проводят тонкое обезвисмучивание, для чего в свинец вмешивают при 340-350 С 0,2-0,3 кг сурьмы на 1 т свинца. Снятые в этой операции дроссы являются оборотными.
После удаления висмута в свинце еще остаются цинк, кальций, магний, сурьма (0,03-0,07 % каждого, а цинка при отсутствии обесцинкования до 0,5 %), поэтому проводят окончательное рафинирование свинца. Чаще всего для этого используют щелочное рафинирование свинца, при котором свинец нагревают в котле до 400-450 С, затем устанавливают в котле мешалку, загружают NaOH или Na2CO3 и небольшими порциями подают NaNO3. Примеси окисляются и переходят в сухие дроссы. Их снимают и направляют в шихту аглообжига. Выход съемов 3-4 % от массы свинца. Содержание в них свинца 45-55 %.
Окончательно рафинированный свинец, содержащий до 99,99 % основного металла, на разливочной машине ленточного или карусельного типа разливают в чушки массой 40-50 кг и направляют потребителю.
2.7.2. ЭЛЕКТРОЛИзный процесс
Электролитическое рафинирование свинца так же, как и другие процессы электролиза, базируется на различии электродных потенциалов свинца и присутствующих в нем примесей. Такие примеси, как цинк, железо, никель и кобальт, имеют стандартный электродный потенциал более электроотрицательный, чем свинец, поэтому они будут переходить в раствор при растворении анода вместе со свинцом, но не будут выделяться на катоде. Мышьяк, висмут, медь, сурьма, серебро, золото, имеющие более электроположительный стандартный потенциал, чем свинец, будут оставаться на поверхности анода в виде шлама. Олово, имеющее стандартный электродный потенциал, близкий к таковому для свинца (соответственно –0,136 и –0,126 В), может легко осаждаться на катоде вместе со свинцом. Поэтому олово необходимо удалить перед электролизом свинца огневым методом. Обычно перед электролизом проводят огневым методом обезмеживание свинца, а иногда рафинируют свинец пирометаллургическим путем также от сурьмы и мышьяка.
В качестве электролита обычно используют водный раствор PbSiF6 (60-100 г/л Pb) и H2SiE6 (80-110 г/л). Аноды отливают из чернового свинца массой 150-250 кг в виде пластин шириной 600-700 мм, длиной 700-950 мм и толщиной 25-35 мм. Катодные основы – тонкие листы толщиной 0,6-1 мм – получают из чистого жидкого свинца наращиванием на вращающемся водоохлаждаемом барабане, небольшая часть которого погружена в расплавленный свинец.
Ванны для электролиза имеют прямоугольную форму, сделаны из бетона и футерованы изнутри асфальтом или другим материалом, способным противостоять корродирующему воздействию электролита. Число катодов в ванне может достигать 20-41 (анодов 19-40). Расстояние между центрами одноименных электродов 100-110 мм.
Основная электрохимическая реакция на катоде
Pb2+ + 2e = Pb0.
Водород на катоде в реакции (1.13) практически не выделяется из-за большого перенапряжения разряда Н3О+ на поверхности свинцового катода (при 25 С и плотности тока 100 А/м2 оно составляет 1,09 В).
Главная электрохимическая реакция на аноде
Pb – 2e = Pb2+.
В процессе электролиза имеет место также реакция
Pb + H2SO4 +
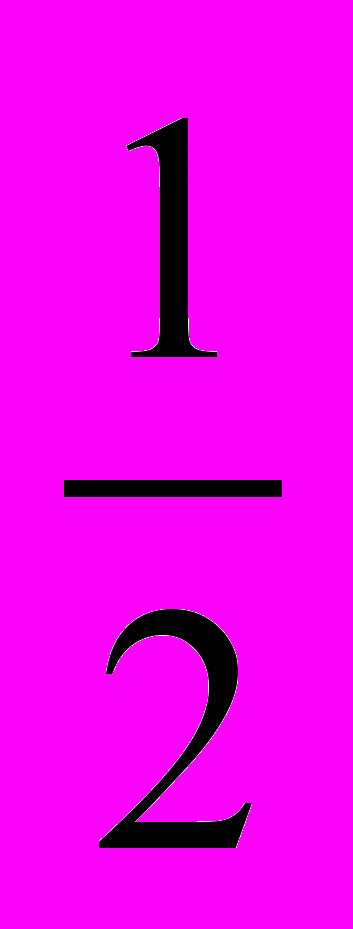
в результате которой в электролите постепенно увеличивается содержание свинца, а содержание свободной H2SiF6 снижается.
Для поддержания постоянства состава электролита часть электролита выводят из процесса и подвергают электролизу с нерастворимыми (графитовыми) анодами или добавляют к электролиту раствор серной кислоты. В этом случае имеет место реакция
PbSiF6 + H2SO4 = PbSO4 + H2SiF6.
В ходе процесса электролиза анод растворяется, а на его поверхности образуется корка шлама. Электрохимически растворенный свинец должен перейти через нее на пути к катоду. Внутри корки шлама содержание свободной Н2SiF6 становится все меньше и меньше, содержание свинца в виде PbSiF6, напротив, повышается. Это ведет к повышению электрического сопротивления на пути прохождения тока, и падение напряжения по мере увеличения толщины пленки растет. Если позволить этому явлению продолжаться, то может начаться переход с анода в раствор вместе со свинцом некоторых электроположительных примесей, которые затем будут выделяться на катоде и загрязнять свинец. Чтобы избежать этого, аноды периодически извлекают из ванны и очищают от шлама. Обычно напряжение на ванне в начале ведения процесса электролиза составляет около 0,35 В, а к концу растворения анодов оно повышается до 0,7 В.
Некоторые параметры и показатели электролитического рафинирования свинца следующие: катодная плотность тока 140-240 А/м2; выход по току 94-97,5 %; напряжение на ванне 0,35-0,7 В; расход электроэнергии 110-190 квтч/т свинца; температура электролита 30-45 С; скорость его циркуляции через ванну 12-30 л/мин.
Катоды, извлеченные из ванны, промывают водой и переплавляют в котле под слоем NaOH при 450 С. Чистота получаемого свинца 99,995-99,997 %.
Анодный шлам (выход его 1,5-3 % от массы свинца) отфильтровывают, сушат и перерабатывают плавкой в отражательной печи. Путем тщательного контроля окислительной атмосферы в печи сначала в виде оксидного шлака удаляют свинец, сурьму и мышьяк, тогда как висмут, медь, некоторые другие неблагородные и благородные металлы остаются в виде сплава. Этот материал перегружают в другую печь, где окисление продолжают до полного удаления оксидов всех неблагородных металлов в виде расплава. В свободном состоянии в виде сплава остаются золото и серебро. Сплав разливают в аноды для разделения золота и серебра электролизом. Оксидные шлаки плавят в восстановительной атмосфере, получая соответствующие сплавы металлов.
Если аноды представляют собой свинцово-висмутовый сплав (его производят при переработке висмутовой пены от обезвисмучивания свинца огневым методом), то после восстановительной плавки шлама получают черновой висмут, который затем рафинируют пирометаллургическим методом.
2.8. ПЕРЕРАБОТКА ЦИНКСОДЕРЖАЩИХ ШЛАКОВ
Цинксодержащие шлаки свинцового производства (см. раздел 2.5) перерабатывают пирометаллургическим методом для извлечения из них цинка и свинца. На практике для этих целей используют три разновидности этого метода: вельц-процесс, электротермию и фьюминг-процесс. Все они основаны на возможности восстановить оксиды цинка и свинца из шлака до свободных металлов при высоких температурах и возогнать их. Вельц-процесссом (см. раздел 1.9) перерабатывают твердые шлаки. В двух других методах перерабатывают жидкие шлаки, добавляя к ним некоторое количество твердых шлаков (корки, шлаки старых отвалов). При переработке шлаков в электрических печах возогнанные металлы конденсируют в жидком состоянии, а в фьюминг-процессе (как и в вельц-процессе) возогнанные металлы улавливают в виде оксидов. Электрические печи для переработки таких шлаков используют редко из-за очень большого расхода электроэнергии.
Больше всего для переработки цинксодержащих шлаков свинцового производства применяют фьюминг-процесс. Переработку шлаков этим методом ведут в печи прямоугольной формы, стенки которой сделаны из водоохлаждаемых кессонов. Печи имеют следующие внутренние размеры: ширина 2-3 м, длина 3-8 м, высота 3-11 м. Расплавленный шлак продувают в печи смесью пылевидного каменного угля и воздуха, подаваемой в печь через фурмы, расположенные в кессонах боковых сторон печи на высоте 0,2-0,3 м от дна печи. Высота шлакового слоя в печи около 1 м над уровнем фурм. На некоторых заводах шлак продувают продуктами неполного сгорания природного газа в выносных топках, содержащими СО и Н2. Температура шлака в печи в период восстановления из шлака оксидов цинка и свинца оксидом углерода (II) и водородом составляет 1200-1300 С. Возогнанные из шлака цинк и свинец в газовой фазе за счет кислорода подсосов воздуха переходят в форму оксидов и уносятся из печи в виде возгонов газовым потоком, имеющим температуру 1200-1300 С. Охлаждение газов до температуры 300-350 С происходит сначала в котле-утилизаторе, а затем в экономайзере или в воздухоподогревателе. В этих аппаратах осаждается часть возгонов. Окончательно возгоны улавливают в рукавных фильтрах, в которые подают газы при температуре 120-150 С.
Шлаковозгоночная печь работает циклически. Цикл состоит из трех периодов: загрузка шлака в печь, продувка шлака, выпуск шлака из печи. Весь цикл длится 2-3 ч.
В зависимости от размеров печи за один цикл перерабатывают 35-95 т шлака. Расход угольной пыли 14-25 % от массы шлака. Извлечение из шлака в возгоны цинка и свинца соответственно 85-95 и 95-98 %. Возгоны содержат 55-75 % цинка и 6-17 % свинца. Остаточное содержание цинка в шлаке 1-3 %.
РЕКОМЕНДАТЕЛЬНЫЙ БИБЛИОГРАФИЧЕСКИЙ СПИСОК
1. Зайцев В.Я. Металлургия свинца и цинка / В.Я.Зайцев, Е.В.Маргулис. М.: Металлургия, 1985. 263 с.
2. Орлов А.К. Комплексное использование рудного сырья в металлургии тяжелых металлов / А.К.Орлов, Ю.М.Смирнов. Ленинградский горный ин-т. Л., 1984. 70 с.
3. Пискунов И.Н. Пирометаллургия цинка / И.Н.Пискунов, Ю.М.Смирнов. Ленинградский горный ин-т. Л., 1978. 83 с.
4. Пискунов И.Н. Металлургия свинца. Универсальный процесс / И.Н.Пискунов, А.К.Орлов. Ленинградский горный ин-т. Л., 1978. 94 с.
5. Пискунов И.Н. Выплавка свинца реакционным способом, рафинирование чернового свинца и переработка полупродуктов / И.Н.Пискунов, А.К.Орлов. Ленинградский горный ин-т. Л., 1979. 100 с.
6. Смирнов Ю.М. Гидрометаллургия цинка. Ленинградский горный ин-т. Л., 1978. 96 с.
ОГЛАВЛЕНИЕ
* Тепловые эффекты всех реакций приведены при 298 К.
* Для металла со степенью окисления (II).