Учебное пособие санкт-петербург 2 004 удк 669. 2/8; 669. 4 (075. 80) Ббк 34. 33
Вид материала | Учебное пособие |
- Учебное пособие Санкт-Петербург 2008 удк 005. 91: 004. 9(075. 8) Ббк 65. 291. 212., 97.7kb.
- Учебное пособие санкт-петербург 2005 удк 339. 9 (075. 80) Ббк, 703.64kb.
- Учебное пособие Санкт-Петербург 2011 удк 621. 38. 049. 77(075) Поляков, 643.33kb.
- Учебное пособие Ульяновск 2010 удк 004. 8(075. 8) Ббк 32. 813я73, 1559.86kb.
- Учебное пособие разработано в соответствии с государственным стандартом специальности, 1131.24kb.
- Учебное пособие санкт Петербург 2010 удк 001. 8 Ббк, 1217.72kb.
- Учебное пособие Санкт-Петербург 2011 удк 1(075., 3433.28kb.
- Учебное пособие Санкт-Петербург 2005 удк 662. 61. 9: 621. 892: 663. 63 Ббк г214(я7), 546.15kb.
- Учебное пособие удк 159. 9(075) Печатается ббк 88. 2я73 по решению Ученого Совета, 5335.58kb.
- Учебное пособие тверь 2008 удк 519. 876 (075. 8 + 338 (075. 8) Ббк 3817я731-1 + 450., 2962.9kb.
Рис.2.1. Технологическая схема переработки сульфидных свинцовых
концентратов с использованием шахтной восстановительной плавки
Автогенные процессы для переработки свинцовых концентратов начали разрабатывать и внедрять в промышленное производство в последние десятилетия в разных странах. Эти процессы базируются на реакциях (2.1)-(2.6).
Что касается гидрометаллургических процессов, то они пока еще практически не используются в производстве свинца.
2.3. ВЫПЛАВКА СВИНЦА РЕАКЦИОННЫМ СПОСОБОМ
Как отмечено выше, при выплавке свинца из сульфидных свинцовых концентратов методом реакционной плавки имеют место две группы основных реакций:
реакции частичного окисления сульфида свинца (2.1) и (2.2);
реакции, приводящие к образованию свободного свинца (2.3) и (2.4). На практике можно проводить все четыре реакции в одной реакционной зоне металлургического агрегата (например, это имеет место при горновой плавке) или раздельно. Во втором случае, например, можно провести частичный обжиг концентрата на агломашине, а затем получить свинец плавкой агломерата в короткобарабанной печи по реакциям (2.3) и (2.4).
Реакции (2.1) и (2.2) являются типичными реакциями окисления сульфидов металлов, поэтому детально рассмотрим только реакции (2.3) и (2.4), в результате которых получается свинец в виде свободного металла. Обе последние реакции обратимые и эндотермические, следовательно, их равновесие с повышением температуры смещается в правую сторону. Поскольку растворимость PbS, PbO, PbSO4 и Pb друг в друге при температурах реакционной плавки небольшая, то константы равновесия Kр реакций (2.3) и (2.4) можно выразить через парциальные давления SO2. Влияние температуры на равновесное парциальное давление
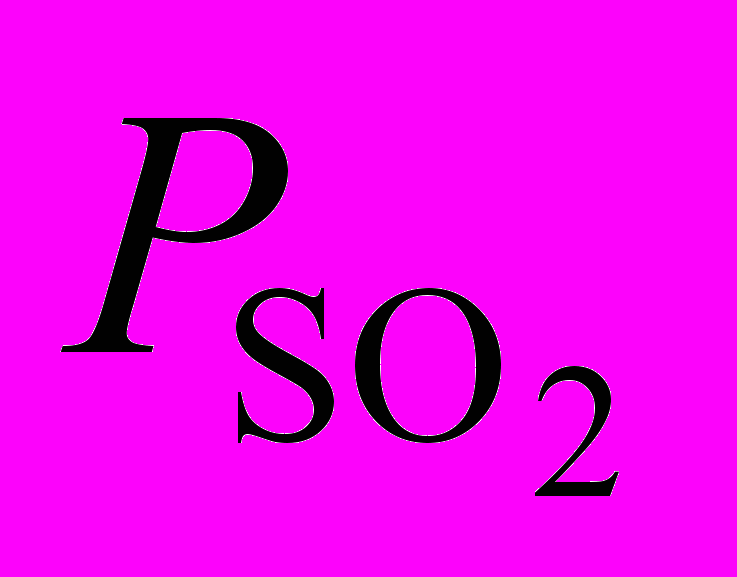
t, C | 692/609 | 755/655 | 800/700 | 847/723 | 870/– |
![]() | 0,8/4,0 | 5,08/20,8 | 13,3/56 | 72,5/98 | 111/– |
______________________ Примечание. В числителе и знаменателе – для реакций (2.3) и (2.4) соответственно. |
Установлено, что реакции (2.3) и (2.4) начинают протекать соответственно при температурах 550 и 600 С. Выплавку свинца реакционным способом в горнах (горновую плавку) ведут при 800-850 С. Парциальное давление SO2 в отходящих газах этого агрегата обычно не более 4-5 кПа, что во много раз меньше равновесного давления SO2 реакций (2.3) и (2.4) при этих температурах. Выплавку свинца реакционным способом в короткобарабанных печах ведут при температурах, достигающих 1100 С, т.е. в условиях еще более благоприятных для протекания реакций в правую сторону.
Реакционной плавкой в горнах или в короткобарабанных печах можно перерабатывать только высокосортные свинцовые концентраты, содержащие не менее 70-75 % свинца и небольшое количество примесей (особенно это касается SiO2, содержание которого не должно превышать 1-2 %).
Основной частью горна для выплавки свинца реакционным способом является отлитый из чугуна ящик-тигель длиной 2,4-2,5 м, шириной 0,35-0,5 м и глубиной 0,25 м с толщиной стенок около 50 мм. На боковых и задней стенке горна установлены кессоны, охлаждаемые водой или воздухом, а к передней стенке примыкает наклонная шихторазборочная рабочая плита. Тигель горна помещают на чугунной раме или на кирпичной кладке. вытяжной колпак над горном соединен газоходом с эксгаустером. В передней стенке колпака по всей ее длине имеется выемка высотой около 50 см, служащая для загрузки шихты и обслуживания горна. через фурмы в задней стенке горна подается воздух, необходимый для ведения процесса. Расплавленный свинец собирается на дне горна и сливается из него через выпускное отверстие в одной из торцевых стенок горна.
Для перемешивания шихты служит специальный механизм, который циклически перемещается вдоль передней стенки горна. Шихта горновой плавки состоит из высококачественного свинцового концентрата, известняка (2-3 % от массы концентрата, крупность 3-5 мм) и каменного угля или кокса (4-8 % от массы концентрата, крупность 5-15 мм). Продуктами плавки являются черновой свинец, серый шлак, пыль и газы. Производительность горна по шихте 15-25 т в сутки. Чем выше содержание свинца в концентрате, тем выше его извлечение в черновой металл и больше производительность горна по свинцу. Например, при переработке концентрата, содержащего 75 % свинца, металл распределяется следующим образом, %: черновой свинец 65-70, серый шлак 10-15, пыль 15-25.
Короткобарабанная печь состоит из клепаного стального кожуха диаметром и длиной 3 м (на некоторых заводах применяют удлиненные до 8 м печи Дершеля), положенного горизонтально и футерованного высокоглиноземистым (65-70 % Al2O3, 20-25 % SiO2) огнеупорным кирпичом. Кожух печи опирается на ролики и может медленно вращаться вокруг горизонтальной оси специальным приводом. В одной из торцевых стен печи имеется отверстие, закрываемое крышкой, которое служит для загрузки шихты в печь. В отверстии противоположной стенки печи установлена пылеугольная горелка или мазутная форсунка. Через это же отверстие удаляют из печи и отходящие газы.
Печь работает в периодическом режиме. Процесс плавки длится около 4 ч. Плавят агломерат с содержанием свинца 70-80 % и с отношением в нем масс серы и кислорода около 1 : 1. За один цикл получают 4-5 т свинца. Извлечение свинца из агломерата в черновой металл 85-87 %, около 8 % свинца переходит в пыль и остальной свинец уходит в шлак. Общее извлечение свинца из агломерата с учетом переработки шлака и пыли достигает 97-98 %. При работе на буром каменном угле расход его составляет 12-15 % от массы загрузки. Часть тепла отходящих газов используют для получения пара в котле-утилизаторе.
2.4. АГЛОМЕРИРУЮЩИЙ ОБЖИГ
СВИНЦОВЫХ КОНЦЕНТРАТОВ
Агломерирующий обжиг сульфидных свинцовых концентратов является первой стадией переработки таких материалов по двухстадийной технологии (см. рис.2.1). Целью агломерирующего обжига концентрата является удаление из него серы и получение кускового спеченного материала – агломерата. В современной практике свинцового производства для агломерирующего обжига практически повсеместно используют прямолинейные спекательные машины.
Спекательная машина представляет собой бесконечную движущуюся ленту, состоящую из большого числа чугунных или стальных тележек (паллет) с решетчатым дном, плотно примкнутых друг к другу. На паллеты загружают ровный слой шихты высотой 100-400 мм (чаще 200-300 мм). Перфорированное дно паллет позволяет просасывать или продувать воздух и газы через слой шихты. По верхним рабочим (горизонтальным) направляющим паллеты движутся под действием приводного механизма. На разгрузочном конце машины паллеты по изогнутым направляющим переводятся на наклонные направляющие, по которым они под действием силы тяжести или дополнительным приводом (на больших машинах) возвращаются к головной части агломашины. Для облегчения сбрасывания агломерата с паллет на разгрузочном конце машины, в месте перехода паллет с горизонтальных направляющих на наклонные, предусмотрен разрыв между паллетами, вследствие чего паллета, подошедшая к месту разгрузки, скатывается по дуговым направляющим и ударяется о паллету, находящуюся внизу. Во время удара агломерат отделяется от решетки и попадает на наклонный грохот, над концом которого установлена зубчатка для дробления больших кусков агломерата.
Для нагрева шихты до температуры воспламенения служит зажигательный горн, установленный над слоем шихты в загрузочном конце машины перпендикулярно движению паллет. Раскаленные газы зажигательного горна просасываются через слой шихты, нагревая его верхнюю часть до температуры воспламенения. Топливом в зажигательном горне обычно служат мазут или природный газ, но можно использовать и твердое топливо.
На заводах работают два вида спекательных машин: с просасыванием воздуха через слой шихты и с подачей дутья под давлением под колосники паллет. В машинах с просасыванием воздуха через слой шихты паллеты с зажженной шихтой далее перемещаются над камерами разрежения. В машинах с дутьем под колосники сначала насыпается тонкий слой (25-50 мм) шихты, который проходит под зажигательным горном и воспламеняется. После этого на него насыпается основной слой шихты (150-250 мм) и паллеты с шихтой далее движутся над дутьевыми камерами. В машинах с просасыванием газов разгрузочная часть укрыта колпаком. В машинах с дутьем колпаком укрыта вся часть машины, расположенная над дутьевыми камерами. Из нее эксгаустером отсасывают реакционные газы.
Процесс агломерирующего обжига начинается сразу после воспламенения нагретого до соответствующей температуры слоя шихты, развиваясь в остальной части слоя шихты за счет тепла, выделяемого при окислении сульфидов металлов, содержащихся в шихте (рис.2.2). Процесс окисления имеет место в сравнительно узкой зоне, которая в машинах с просасыванием газов перемещается сверху вниз, а в машинах с дутьем воздуха – снизу верх. В зоне обжига и спекания температура достигает максимальных величин (1000-1100 С) и часть шихты при этом переходит в расплавленное состояние. Жидкая фаза смачивает нерасплавившиеся частицы шихты и цементирует их после затвердевания при снижении температуры в слое шихты. В результате этих процессов и получается агломерат.
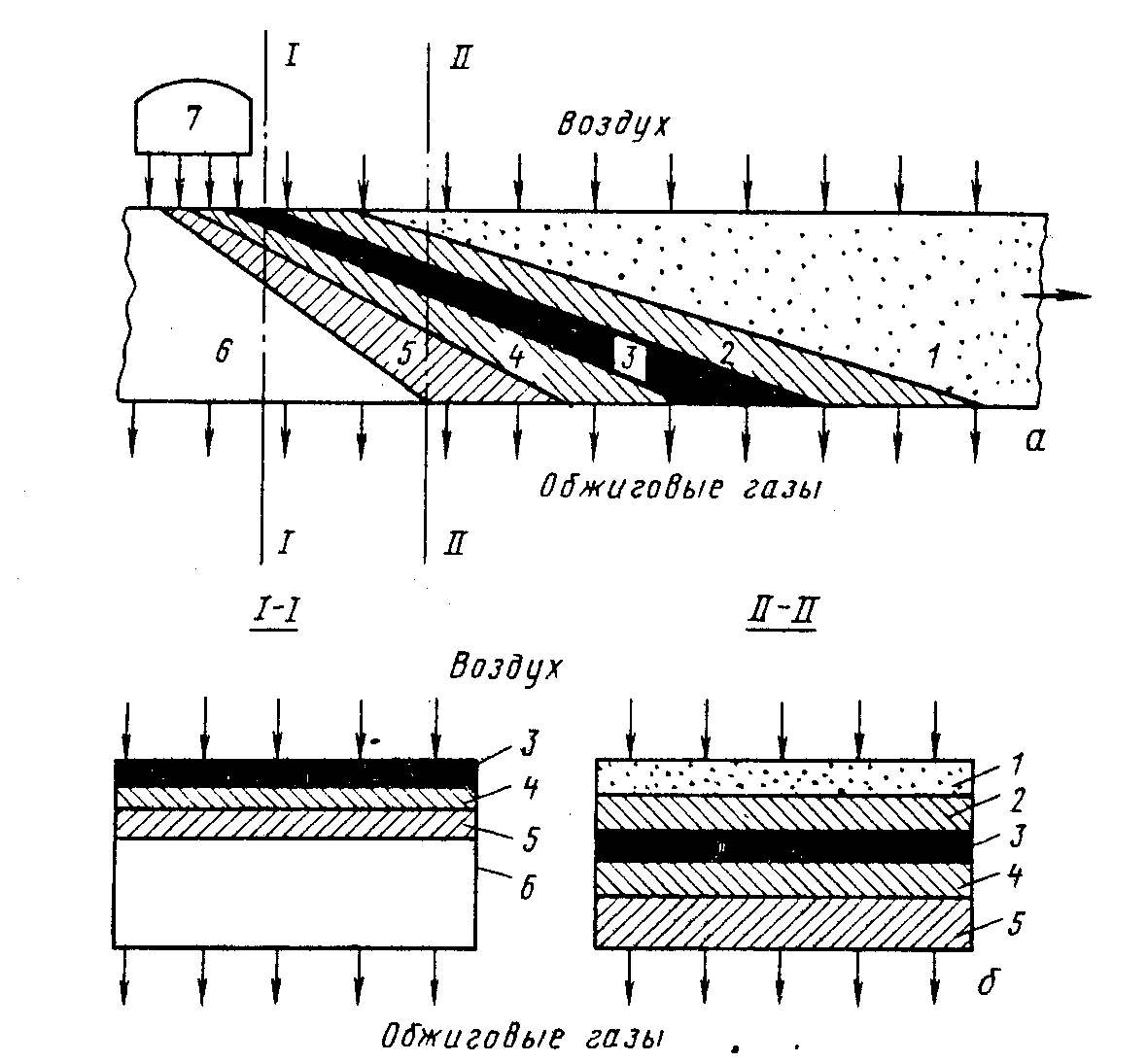
1
2
4
5
6
7
I
II
Воздух
II
Обжиговые газы
I
II–II
I–I
Воздух
3
4
5
6
1
2
3
4
5
Обжиговые газы



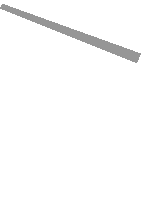
3

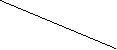


Рис.2.2. Схема распределения зон в слое шихты на агломашине,
работающей с просасыванием воздуха через слой шихты
1 – охлажденный агломерат; 2 – зона охлаждения горячего агломерата и нагрева
воздуха; 3 – зона реакции; 4 – зона подогрева шихты до воспламенения; 5 – зона
подсушивания шихты; 6 – холодная влажная шихта; 7 – зажигательный горн
При высоких температурах в зоне обжига и спекания окисление сульфида свинца идет главным образом по реакции (2.1). Образующийся при этом PbO может взаимодействовать с кремнеземом с образованием силикатов свинца (mPbO nSiO2), которые могут переходить в жидкое состояние уже при температурах 700-800 С. Глет может взаимодействовать также и с другими оксидами шихты, например, с Fe2O3 с образованием ферритов (хPbO yFe2O3). В небольших количествах может образоваться и сульфат свинца PbSO4. в некоторой степени имеют место также реакции (2.3) и (2.4). Таким образом, в агломерате свинец может присутствовать в виде свободного металла и в виде различных соединений: PbO, mPbO nSiO2, хPbO уFe2O3, PbSO4, PbS и др. Другие металлы также будут находиться в агломерате в виде подобных соединений.
Вертикальная скорость перемещения зоны нагрева шихты до температуры воспламенения и скорость перемещения зоны обжига связаны определенной зависимостью. Нормальное протекание процесса возможно только в случае, когда первая (v1) равна или несколько больше второй (v2). На практике часто v1 = 1,52 см/мин, а v2 = 11,2 см/мин.
Шихта аглообжига состоит из сульфидных свинцовых концентратов, флюсов и других материалов (полупродукты, оборотные материалы и пр.). Шихту готовят так, чтобы получить агломерат, удовлетворяющий требованиям его плавки в шахтной печи. Агломерат должен быть прочным и пористым; иметь высокую температуру начала плавления и небольшой интервал температуры его размягчения; содержать мало серы (чаще всего 1,1-2,0 %), если не требуется получать при последующей плавке агломерата в шахтной печи штейн; по химическому составу соответствовать требованиям шахтной плавки.
Поскольку флотационные свинцовые концентраты представляют собой мелкий материал, то флюсы и другие материалы также дробят и измельчают до крупности 1-6 мм, а оборотный агломерат дробят до крупности менее 6-8 мм.
В современной практике свинцового производства используют в основном два метода подготовки шихты аглообжига: бункерный и штабельный. В первом случае в закрытом складе имеется 15-20 (или более) небольших бункеров емкостью 50-60 м3, в которых содержатся различные материалы. Материалы из бункеров в нужных пропорциях с помощью питателей подают на сборный ленточный транспортер.
При штабельном способе на специальных площадках закрытого склада создается большой запас усредненной проанализированной и откорректированной шихты. Штабель имеет форму усеченной пирамиды длиной 60-70 м, шириной около 16 м и высотой 5-6 м и содержит 7000-8000 т шихты. При закладке штабеля отдельные составляющие шихты подаются на площадку штабеля послойно транспортером. Шихтарник обычно имеет три одинаковых отсека, в одном из которых идет закладка штабеля шихты, второй заложен и ведется его опробование, третий вырабатывается специальной шихтопогрузочной машиной.
При любом способе подготовки шихты перед загрузкой на паллеты агломашины ее хорошо перемешивают и увлажняют. Оптимальная влажность шихты увеличивается от 4-6 до 10-12 % с уменьшением крупности шихты.
Степень спекания шихты определяется температурой в зоне обжига и количеством жидкой фазы, образующейся в ней. Температура в зоне обжига и количество выделяющегося тепла зависит от содержания сульфидов в шихте и интенсивности протекания окислительных процессов. Если количество сульфидов в шихте слишком большое и скорость окислительных процессов также весьма велика, то спекание шихты может произойти задолго до полного окисления сульфидов металлов и полученный агломерат будет содержать много серы. Следовательно, необходимо регулировать количество сульфидов (или топлива) в спекаемой шихте, а также условия их горения.
Смесь свинцовых концентратов и флюсов обычно содержит 11-13 % серы, иногда больше. Практика показала, что из такой шихты невозможно сразу получить агломерат с содержанием серы ниже 4 %, что является недостаточным по условиям плавки продукта обжига в шахтной печи. Существует два варианта решения этой проблемы: вести обжиг в две стадии или добавить в шихту материалы с низким содержанием серы.
По двухступенчатой технологии шихту сначала быстро обжигают на агломашине для предварительного удаления части серы. полученный агломерат имеет низкое качество и содержит 5-7 % серы. Этого достаточно, чтобы провести второй обжиг и получить агломерат хорошего качества. Продукт первого обжига перед подачей на второй обжиг дробят и увлажняют.
При одноступенчатом обжиге для снижения содержания серы в первичной шихте до 6-7 % к ней добавляют необходимое количество оборотного агломерата, полученного в этом же процессе. Оборотный агломерат предварительно дробят. На практике преимущественно используют одноступенчатую технологию для аглообжига сульфидных свинцовых концентратов.
Для того чтобы агломерат получился не слишком легкоплавкий, содержание свинца в шихте обычно поддерживают не выше 45-50 %.
В настоящее время на свинцовых заводах используют агломашины с площадью спекания 20-162 м2 и шириной слоя шихты 1-3 м. Удельная производительность по шихте на единицу площади спекания составляет 20-30 т/(м2сут). В зависимости от содержания серы в перерабатываемых свинцовых концентратах производительность агломашин по годному агломерату, поступающему в шахтную плавку, составляет 5-22 т/(м2сут).
Обжиговые газы, которые получаются в головной части агломашины, могут содержать до 10-11 % SO2, тогда как газы, получаемые в разгрузочном конце машины, содержат не более 0,5-1 % SO2. Чтобы использовать газы аглообжига для производства серной кислоты отбирают часть наиболее богатых газов, что позволяет извлекать от всех газов аглообжига 60-75 % серы в виде серной кислоты. Возможна также организация рециркуляции бедных газов путем подачи их в головную часть агломашины. В этом случае степень извлечения серы из газов может достигать 85-90 %.
2.5. ШАХТНАЯ ПЛАВКА СВИНЦОВОГО АГЛОМЕРАТА
Шахтная плавка является вторым переделом при переработке сульфидных свинцовых концентратов по двухступенчатой технологии (см. рис.2.1). Шихта шахтной печи состоит из свинцового агломерата, кокса и других материалов (оборотных полупродуктов, добавочных флюсов, железного скрапа). Цель плавки – как можно полнее извлечь свинец из шихты в виде чернового металла, в котором концентрируются также золото и серебро; ошлаковать пустую породу и перевести в шлак как можно больше цинка, присутствующего в шихте. Часто при плавке получают еще один жидкий продукт – штейн, в который также переходит часть металлов.
Современная шахтная печь (рис.2.3) состоит из вертикальной шахты прямоугольной формы в поперечном сечении, опирающейся на стенки внутреннего горна. Стенки шахтной печи сужаются книзу. Верхняя часть печи называется колошником. Она служит для загрузки шихты в печь и удаления отходящих газов из печи. Шахта современных шахтных печей делается полностью кессонированной с водяным или испарительным охлаждением кессонов. Обычно кессоны устанавливаются в два ряда: верхний ставится вертикально, а нижний ряд наклонно, с сужением ширины печи книзу, образуя заплечики. Такая форма шахты печи замедляет скорость движения шихты в области плавильной зоны, способствует высокотемпературному режиму сгорания кокса в области фурменного пояса печи и более равномерному распределению газового потока по сечению печи. За счет снижения скорости газового потока в верхней (расширяющейся) части шахты печи снижается пылеунос шихты.
Фурмы, через которые в печь вдувается воздух, необходимый для ведения процесса плавки, располагаются в боковых стенках нижнего ряда кессонов на высоте 300-400 мм от их нижнего края. Печи прямоугольного сечения имеют в области фурм ширину 1-1,7 м и длину 4-8 м (площадь поперечного сечения 4-13 м2). Высота шахты печи 4-6 м. Имеются также печи с шахтой переменного сечения и двумя рядами фурм, имеющие ширину в области нижнего ряда фурм 1,3-1,5 м, а в области верхнего ряда фурм – 2,6-3 м. Раньше использовались также печи круглого или овального поперечного сечения диаметром 1-1,5 м (редко до 2 м).
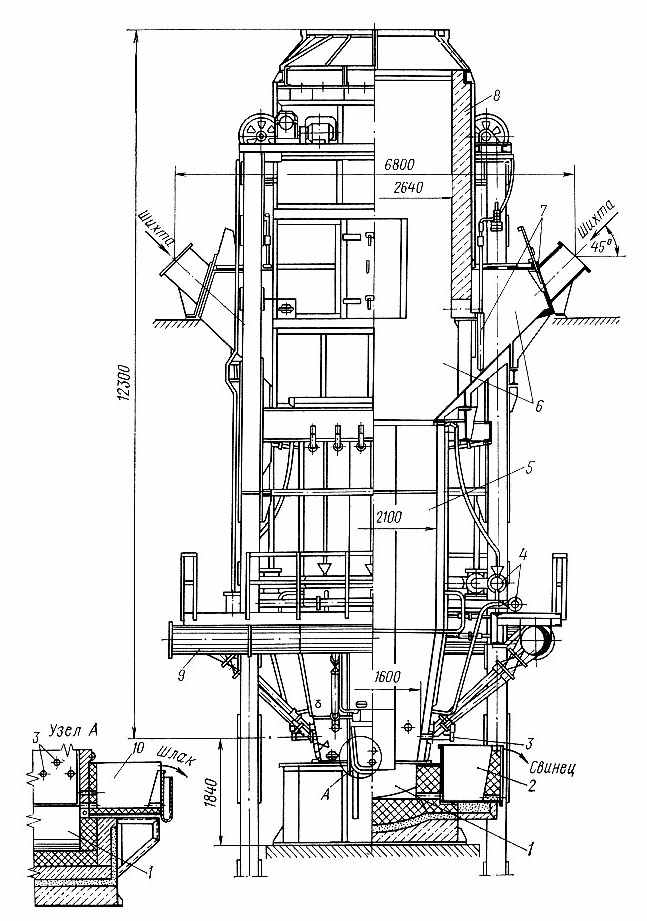
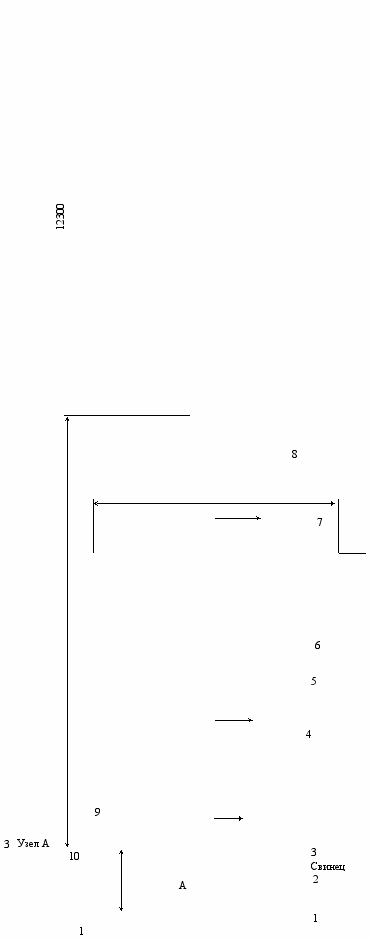
Рис.2.3. Поперечный разрез шахтной печи
1 – горн; 2 – сифон для выпуска чернового свинца; 3 – фурма; 4 – коллекторы систем
водяного охлаждения; 5 – шахта печи; 6 – колошник; 7 – загрузочный шибер; 8 –
шатер колошника; 9 – коллектор для подвода дутья; 10 – сифон для выпуска шлака
Горн (тигель) шахтной печи выложен внутри огнеупорным кирпичом, снаружи окружен железным кожухом и располагается на фундаменте печи. Горн служит для приема расплавленных продуктов плавки. Объем горна зависит от содержания свинца в шихте и поперечного сечения печи, глубина горна (0,5-0,75 м) – от производительности печи по черновому свинцу. В одной из длинных сторон горна делают сифон, представляющий собой наклонный канал сечением до 300 300 мм, через который расплавленный черновой свинец непрерывно вытекает из горна снизу в приемный ковш, расположенный снаружи печи.
Шлак и штейн выпускают из горна через летку, расположенную в торцевой стенке горна и в выемке торцевого кессона немного выше уровня свинца в горне. Выпуск шлака и штейна из горна может осуществляться непрерывно через устройство с гидрозатвором или периодически. Разделение шлака и штейна на самостоятельные продукты проводят либо в передвижном отстойном горне, либо в стационарном электрообогреваемом отстойнике.
Шихту, состоящую из агломерата, кокса и других материалов, порциями, называемыми колошами, послойно (сначала обычно кокс, затем флюсы и обороты, последним агломерат) загружают в печь. Шихта постоянно под действием собственной силы тяжести движется вниз навстречу восходящему газовому потоку, образующемуся, главным образом, в области фурм в результате горения кокса. В этой области печи имеют место максимальные температуры (до 1400-1500 С). По мере движения вниз шихта постепенно нагревается. В ней происходят физико-химические превращения за счет химического и термического воздействия на шихту газового потока и взаимодействия между собой отдельных составляющих шихты. В области фурменной зоны шихта полностью переходит в расплавленное состояние.
Главными химическими процессами при шахтной плавке свинцового агломерата являются восстановление, осаждение, сульфидирование и горение углеродистого твердого топлива.
Восстановительные процессы в общем виде можно представить реакциями
MeO + C = Me + CO;
MeO + CO = Me + CO2 ,
главной из которых является вторая реакция.
Процессы осаждения протекают по реакции
MeS + Fe = Me + FeS, (2.7)
в которой в качестве сульфида основным участником является PbS.
В основе процессов сульфидирования лежит более высокое сродство серы к меди, чем к железу и некоторым другим металлам. Укажем основные реакции этого типа:
Cu2O + FeS = Cu2S + FeO; (2.8)
2Cu + FeS = Cu2S + Fe; (2.9)
2Cu + ½ S2 = Cu2S; (2.10)
2Cu + PbS = Cu2S + Pb. (2.11)
Процессы горения углеродистого топлива оказывают очень большое влияние на работу шахтной печи. В качестве восстановителя и топлива при шахтной плавке используют кокс, что обусловлено следующими его свойствами, благоприятными для применения в шахтных печах:
достаточно высокая калорийность (26000-32000 кДж/кг);
хорошая механическая и термическая прочность;
сравнительно высокая температура воспламенения (600-750 С);
достаточная пористость (49-53 %);
требуемый гранулометрический состав.
Углерод кокса может взаимодействовать с кислородом дутья по следующим четырем реакциям:
С + О2 = СО2 + 393,5 кДж;
2С + О2 = 2СО + 221,1 кДж;
2СО + О2 = 2СО2 + 565,9 кДж ;
СО2 + С = 2СО – 172,4 кДж.
Первые три являются экзотермическими, а последняя – эндотермической. Горение углерода кокса при шахтной свинцовой плавке происходит при недостатке кислорода. В этих условиях в зависимости от соотношения между углеродом и кислородом можно получить газовую фазу с различным отношением СО : СО2, соответствующим требованиям процесса плавки.
Рассмотрим поведение некоторых компонентов шихты при плавке. Как было отмечено ранее, свинец может находиться в агломерате частично в виде свободного металла, но, главным образом, в виде соединений (PbO, mPbO nSiO2, xPbO yFe2O3, PbSO4, PbS). Свободный свинец переходит в расплавленное состояние, когда температура шихты достигает температуры его плавления (327,4 С). Для восстановления PbO по реакции (2.6) необходимо иметь весьма небольшое парциальное давление СО в газовой фазе (см. рис.1.4). Восстановление оксида свинца из шлака можно представить реакцией
(PbO)шлак + CO [Pb] +CO2,
константа равновесия которой
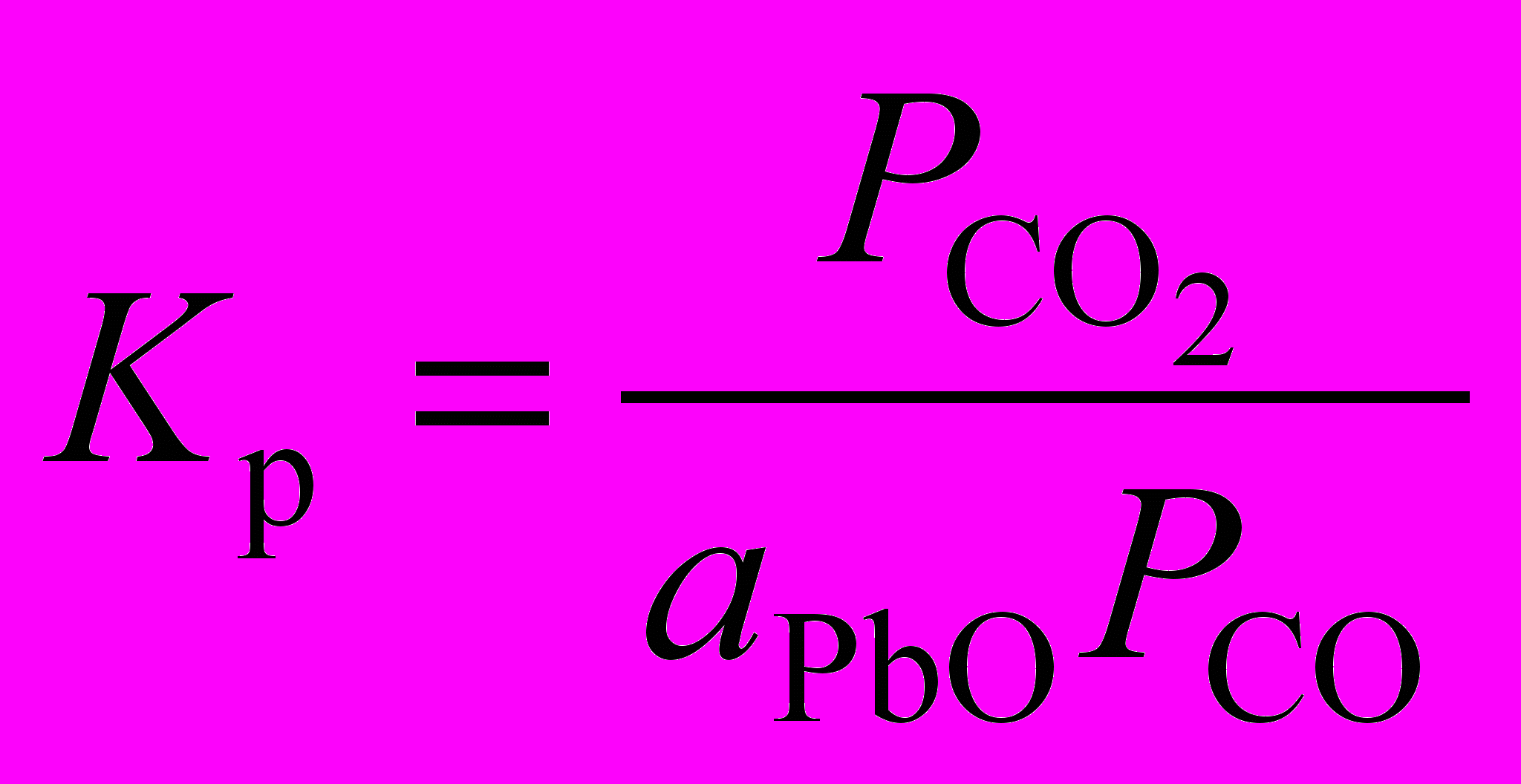
Соответственно
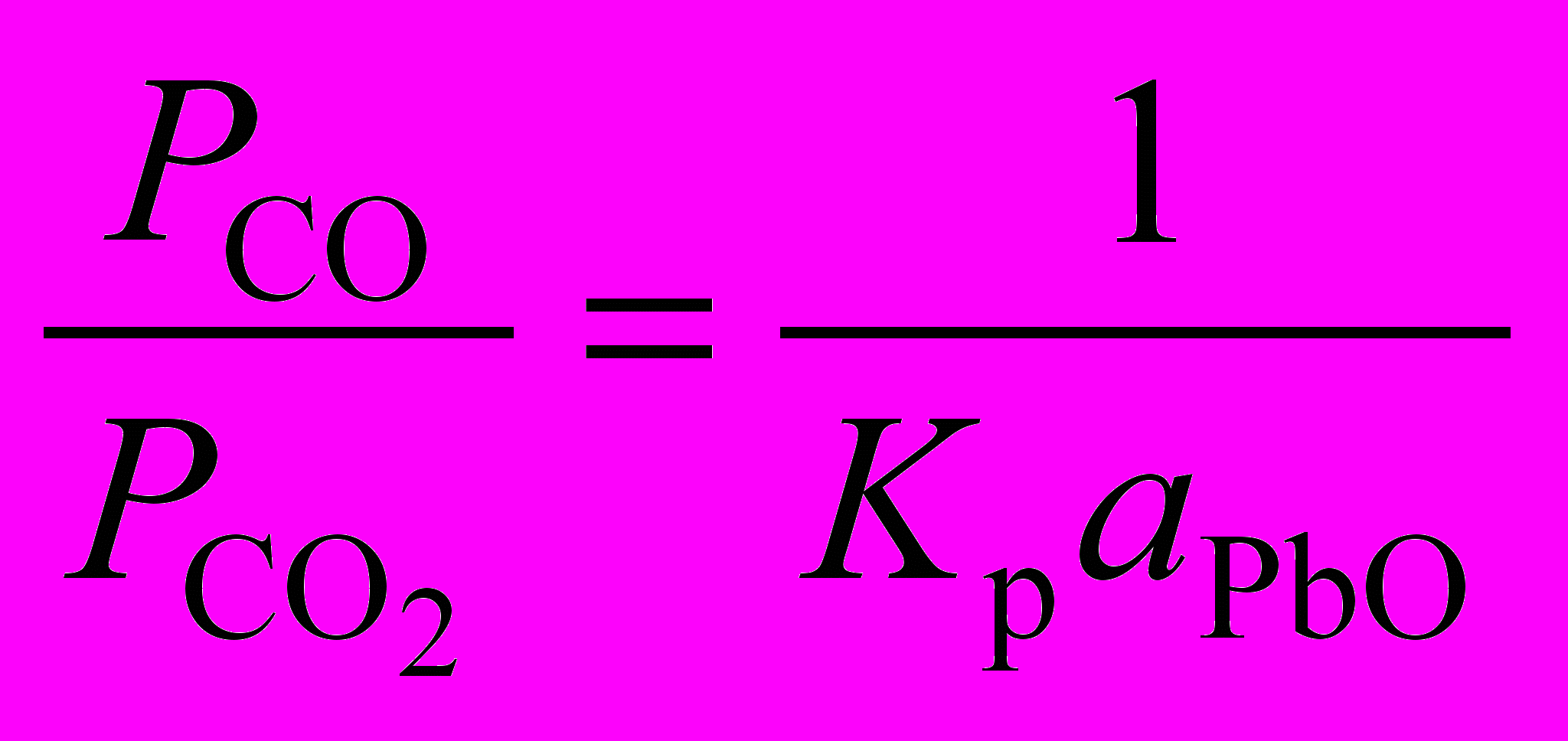
Из выражения (2.12) видно, что чем меньше активность PbO в шлаке (или содержание PbO в шлаке), тем больше будет равновесное парциальное давление СО в газовой фазе (см. рис.1.4).
Сульфат свинца может переходить в форму PbO или PbS по реакциям:
PbSO4 = PbO + SO2 +
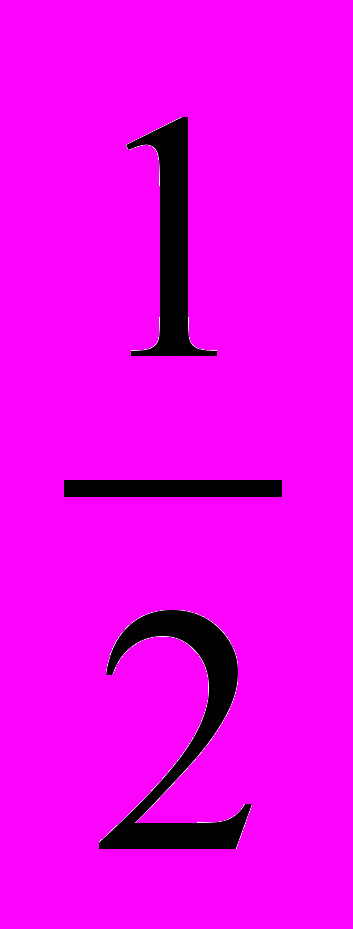
PbSO4 + 4CO = PbS + 4CO2.
Сульфид свинца может взаимодействовать с железом по реакции (2.7), а также с PbO или PbSO4 по реакциям (2.3) и (2.4).
Железо может находиться в шихте, главным образом, в виде оксидов (FeO, Fe3O4, Fe2O3, mFeO nSiO2 и др.), в небольших количествах в виде FeS (иногда в виде FeS2, когда в шихту плавки добавляют пирит) и в виде металлического железа.
Металлическое железо добавляют в шихту при необходимости в виде железного скрапа в количестве 1-2 % от массы шихты для того, чтобы извлечь более полно свинец из шихты по реакции (2.7).
Сульфидное железо принимает участие в реакциях сульфидирования меди (2.8)-(2.10) и др., а непрореагировавшее FeS переходит в штейн.
Оксиды железа могут восстанавливаться последовательно по реакциям:
3Fe2O3 + CO = 2Fe3O4 + CO2;
Fe3O4 + CO = 3FeO + CO2; (2.13)
FeO + CO = Fe + CO2, (2.14)
равновесные парциальные давления СО для которых приведены на рис.1.4. Из него видно, что Fe2O3 легко должен восстанавливаться до Fe3O4. Для протекания реакции (2.13) вправо необходимо иметь более высокое содержание CO в газовой фазе. Поскольку Fe3O4 имеет высокую температуру плавления (около 1600 С), то при наличии его в шлаке температура плавления шлака повышается. По этой причине необходимо восстановить Fe3O4 до FeO. Но восстанавливать FeO до свободного металла по реакции 2.14 нельзя, так как железо практически не растворимо в свинце, имеет температуру плавления 1535 С и поэтому будет образовывать настыли в горне печи.
Основываясь на поведении соединений свинца и железа, процесс шахтной плавки организуют таким образом, чтобы отношение СО : СО2 в газовой фазе в зонах печи, где при температурах 600-1300 оС протекают основные восстановительные процессы, составляло около 1 : 1. Как видно из рис.1.4, в этих условиях оксиды меди и кадмия также будут восстанавливаться. Кадмий, имеющий температуру кипения 767 С, переходит в газовую фазу. Кремнезем (SiO2) не восстанавливается и целиком уходит в шлак. Оксиды цинка, в основном, уходят в шлак (до 10-15 % цинка возгоняется и переходит в пыль). Оксиды мышьяка, сурьмы, олова, висмута восстанавливаются и переходят в черновой свинец, мышьяк и сурьма частично возгоняются. Золото и серебро концентрируются в черновом свинце, но часть их переходит и в штейн.
Состав жидких продуктов плавки следующий, %:
черновой свинец – Pb 91-98; Cu 1-5; Sn 0,01-0,5; Sb 0,2-2; As 0,1-2; Bi 0,002-0,4; Zn до 0,4; Fe до 0,25; S 0,1-0,3; Au 1-30 г/т; Ag 1000-6000 г/т;
шлак – SiO2 18-28; FeO 25-40; CaO 6-20; ZnO 10-25; Pb 0,8-2,5; Cu 0,2-1; S 1-3;
штейн – Cu 5-30; Pb 8-36; Zn 1,5-10; Fe 15-50, S 14-26, Au до 4-5 г/т, Ag до 3000-4000 г/т.
Основные показатели работы шахтных печей:
удельная производительность по шихте на 1 м2 сечения печи в области фурм 40-100 т/сут;
расход кокса от массы шихты 8-13 %;
прямое извлечение свинца в черновой металл 90-96 %;
объем вдуваемого воздуха на 1 м2 сечения печи в области фурм 13-38 м3/мин.
2.6. АВТОГЕННЫЕ ПРОЦЕССЫ
Автогенные процессы в металлургии свинца начали разрабатывать и внедрять в промышленную практику в различных странах в последние десятилетия. Среди них можно назвать: процесс КИВЦЭТ-ЦС и его модификацию КФ-КФ (СССР), процесс Q-S-L (США и Германия), процесс Оутокумпу (Финляндия), процесс Айзасмелт (Австралия) и др.
Во всех этих процессах шихта, состоящая из свинцовых концентратов и флюсов, плавится в окислительной атмосфере за счет тепла, выделяющегося при окислении сульфидов и (если это необходимо) за счет дополнительного тепла от сжигания топлива. В этой стадии технологии часть сульфида свинца за счет протекания реакций (2.3) и (2.4) превращается в свободный металл, а остальной свинец концентрируется, в основном, в шлаке в форме оксида. Оксидный свинец затем извлекают из шлака, восстанавливая его до металла. Для этой цели могут быть использованы различные углеродсодержащие материалы.
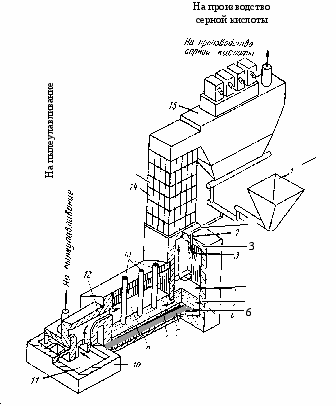
Рис.2.4. Схема установки КИВЦЭТ-ЦС
1 – бункер для шихты; 2 – горелка; 3 – факел; 4 – плавильная камера; 5 – шлак; 6 – штейн;
7 – черновой свинец; 8 – сифон; 9 – электропечь; 10 – конденсатор; 11 – черновой цинк; 12 – газоход; 13 – электроды; 14 – охладительный стояк для газов; 15 – электрофильтр ЭВС-7
В качестве примера автогенных процессов в металлургии свинца рассмотрен процесс КИВЦЭТ-ЦС (рис.2.4), в котором шихту, высушенную до содержания влаги 0,5-1 %, вдувают технологическим кислородом (содержание кислорода по объему 95-98 %) через горелку в факельную зону печи. В факеле происходит воспламенение сульфидов металлов, их окисление и плавление шихты.
Температура в факеле 1200-1400 С. В ходе окислительного плавления шихты до 35-40 % свинца получается в виде металла. Газы, отсасываемые из этой зоны, содержат 40-55 % SO2 по объему и легко могут быть переработаны с получением в качестве продукта серной кислоты, жидкого SO2 или серы.
В электротермической зоне, отделенной от факельной перегородкой, происходит восстановление из шлака оксидов свинца и цинка (или только оксида свинца) до металла за счет подаваемого в эту зону кокса. Поскольку оксид свинца восстанавливается из шлака значительно легче, чем оксид цинка, то предпочтительнее проводить восстановление оксидов этих металлов из шлака раздельно, например, сначала восстанавливать свинец из шлака в электропечи, а цинк затем извлекать из шлака фьюминг-процессом. Удельная производительность этого агрегата по проплаву шихты на 1 м2 поперечного сечения факельной зоны 73-100 т/сут.
2.7. РАФИНИРОВАНИЕ ЧЕРНОВОГО СВИНЦА
Примеси, присутствующие в черновом свинце, могут ухудшать его свойства, поэтому такой металл не удовлетворяет требованиям потребителей. Кроме того, некоторые из примесей (золото, серебро и висмут) представляют сами по себе большую ценность. По этим причинам необходимо рафинировать черновой свинец от примесей. Рафинирование свинца проводят двумя способами: пирометаллургическим методом и электролитическим рафинированием в водных растворах.
При рафинировании свинца от примесей пирометаллургическим методом примеси из него удаляют последовательно. Принципиальная технологическая схема рафинирования чернового свинца этим методом приведена на рис.2.5. На некоторых заводах порядок удаления примесей может быть иным, могут также отсутствовать отдельные операции из-за низкого содержания примесей в свинце.