Учебное пособие к дисциплине для студентов заочной формы обучения по специальности 140211 «Электроснабжение»
Вид материала | Учебное пособие |
СодержаниеЧто собой представляет бесщелочное стекло? Полупроводниковые материалы. |
- Учебное пособие к дисциплине для студентов заочной формы обучения по специальности, 1219.34kb.
- Методические указания к дисциплине и задания к контрольной работе для студентов заочной, 126.92kb.
- Методические указания к дисциплине и темы рефератов для студентов заочной формы обучения, 102.72kb.
- Учебное пособие для студентов заочной формы обучения Санкт-Петербург, 1247.83kb.
- Методические указания к итоговому междисциплинарному экзамену по специальности «электроснабжение», 382.82kb.
- Н. Н. Кувшинова экология учебное пособие, 1072.88kb.
- Учебное пособие для самостоятельной работы студентов специальности 040600 «Сестринское, 1354.95kb.
- Методические указания: краткий курс лекций для студентов заочной формы обучения Санкт-Петербург, 1540.61kb.
- Учебное пособие Для студентов всех специальностей Москва 1999, 1603.73kb.
- Учебное пособие для студентов специальности «Экономика и управление на предприятии», 1271.5kb.
- Что собой представляет бесщелочное стекло?
- Что собой представляют платиновые и молибденовые стёкла? Каков их состав?
- К какому классу материалов по электрическим свойствам относятся стёкла?
- Сравните по оптическим свойствам оптические стёкла и оптические полимеры.
- Причины относительно невысокой прочности стёкол и методы, позволяющие повысить прочность.
5.3.3. Ситаллы.
Как следует из вышеизложенного, стёкла даже в специальных условиях кристаллизуются чрезвычайно медленно. Вместе с тем, из этого не следует, что SiO2 не может быть получен в кристаллическом состоянии. Это, как правило, достигается введением специальных веществ, являющихся искусственными зародышами кристаллизации. Такие материалы называются ситаллами.
Ситаллы – это поликристаллические материалы, получаемые направленной кристаллизацией стекла. Термин «ситалл» образован путём сокращения слов силикат и кристалл. В США этот материал называется «пирокерам». По химическому составу ситаллы отличаются от стёкол тем, что они содержат «каталитические добавки». Эти добавки вызывают появление в стекле после специальной обработки огромного количества центров кристаллизации и тем самым создают условия для образования мелкокристаллической структуры.
Структура ситалла состоит из зёрен одной или нескольких кристаллических фаз, скреплённых стекловидными прослойками.
Свойства ситаллов определяются не столько химическим составом, сколько структурой кристаллических фаз. Фазовый состав кристаллов разнообразен. Это могут быть шпинели, рутил, кварц, кристобалит, кордиерит, перовскит и т.д. Фазовый состав зависит от условий проведения направленной кристаллизации, природы зародышей кристаллизации и состава стекла. Содержание кристаллической фазы в ситаллах зависит от условий кристаллизации и составляет от 30 до 95 %. Размер кристаллов как правило не превышает 1 – 2 мкм.
Такие физико-химические параметры ситаллов, как плотность, ТКЛР, теплопроводность, модуль упругости и диэлектрическая проницаемость обладают свойством аддитивности, т.е. зависят от свойств и содержания фаз. Например, диэлектрическая проницаемость ситаллов может быть рассчитана, исходя из логарифмического закона смешения.
Регулируя в процессе кристаллизации фазовый состав кристаллов и их количество можно создавать материалы с заранее заданными свойствами. Так, для получения конденсаторных ситаллов с высокой диэлектрической проницаемостью добиваются образования в них кристаллов с перовскитовой структурой, обладающей высокой (титанаты бария, ниобаты и др.).
Такие свойства ситаллов, как жаропрочность, электропроводность, механическая прочность не подчиняются аддитивным закономерностям.
Электроизоляционные свойства ситаллов, как правило, превосходят свойства стёкол того же химического состава: ситаллы имеют более высокое v и электрическую прочность, более низкий tg.
В настоящее время синтезированы ситаллы с самыми разнообразными свойствами: химостойкие, термостойкие, обладающие близким к нулю ТКЛР, высокопрочные, электроизоляционные и др., превосходящие по свойствам лучшие марки стёкол и керамики. Также разнообразны и области применения ситаллов – от конструкционных и строительных материалов до микродеталей радиоэлектроники. В последнем случае важное значение имеют не только высокие электрические свойства ситаллов, но и их повышенная механическая прочность, возможность варьирования в необходимых пределах ТКЛР, а также хорошая шлифуемость - до 14 класса чистоты.
В строительстве используют более дешёвые шлакоситаллы, получаемые из доменных шлаков с добавлением кварцевого стекла, глины, сульфата натрия и катализаторов кристаллизации. Они успешно заменяют такие облицовочные материалы, как керамику, мрамор, гранит. Высокая химическая устойчивость шлакоситаллов позволяет применять их в качестве материала, пригодного для эксплуатации в агрессивных средах: кислотах, щелочах, водных растворах различных солей взамен кислотоупорной керамики и плит из каменного литья.
Вопросы для самопроверки.
- Какова фазовая структура ситаллов?
- Каковы пути регулирования свойств ситаллов?
- Области применения ситаллов.
5.3.4. Техническая керамика.
Керамика – это материал, получаемый спеканием порошков заданного состава при температурах, существенно ниже их температуры плавления. Структура керамики близка к структуре ситаллов. И керамика и ситаллы состоят из кристаллических и аморфных фаз, но в керамике ещё имеются газовые фазы. Их присутствие в керамике обусловлено технологией. Технологический процесс производства керамических изделий включает много операций. Ключевыми операциями являются подготовка исходных компонентов, заключающаяся в измельчении сырья до заданного уровня, смешении компонентов, формовании изделия и обжиг. Формование керамического изделия часто проводится путём прессования. Чем выше давление прессования и чем мельче порошки, тем меньше пор в керамике, тем меньше содержание газовой фазы.
На пористость керамики также большое влияние оказывает режим спекания. Вообще, спекание – это очень сложный физико-химический процесс. Внешним признаком спекания является уменьшение размеров изделия и, соответственно, увеличение кажущейся плотности. Спекание порошка начинается обычно со «сваривания» зёрен в местах контакта. Сущность спекания заключается в самопроизвольном заполнении веществом свободного пространства внутри зёрен и между ними. При этом происходит уменьшение дефектности кристаллических решёток, снятия имеющихся напряжений в контактных участках материала. Движущей силой процесса спекания является стремление системы к уменьшению поверхностной энергии, в данном случае это выражается в уменьшении поверхности. Поэтому мелкозернистые порошки спекаются быстрее, чем крупнозернистые.
Одновременно с процессом спекания протекает рекристаллизация. Она заключается в образовании одних зёрен тела за счёт других. Состав кристаллических фаз при этом часто существенно изменяется. Если состав кристаллических фаз не изменяется, то рекристаллизация сводится к полиморфным превращениям, то есть, к образованию различных кристаллических модификацией одного и того же вещества. Если состав кристаллических фаз в процессе рекристаллизации изменяется, то это обусловлено либо диффузией компонентов и образованием твёрдых растворов, либо образованием новых веществ в результате химических реакций в смесях твёрдых веществ.
Механизм реакций в смесях твёрдых веществ очень сложен. Из курса химии известно, что твёрдые вещества химически не взаимодействуют друг с другом. Их химическое взаимодействие возможно только за счёт массопередачи путём внутренней диффузии, а коэффициент диффузии твёрдого в твёрдом очень мал – 10-8 – 10-16 м2/с. Таким образом, скорость чисто твёрдофазных реакций пренебрежимо мала. Практический опыт противоречит этим общим представлениям. Это связано с тем, что в действительности химические превращения при спекании керамических масс протекают при участии газовых и жидких фаз. Газовые фазы образуются, например, за счёт возгонки или диссоциации твёрдых веществ. Жидкие фазы образуются за счёт плавления одного из исходных компонентов или их эвтектических смесей.
В качестве примера такого процесса можно назвать взаимодействие оксидов цинка и алюминия с образованием шпинели
ZnO(тв) + Аl2O3(тв) = ZnAl2O4(тв)
ZnO(тв) ZnO(газ)
ZnO(газ) + Al2O3(тв) ZnAl2O4(тв) (ZnO.Al2O3)
В состав смеси обычно добавляют небольшие количества так называемых «минерализаторов» или «плавней», имеющих относительно низкие температуры плавления. Они химически инертны по отношению к реакционной смеси, однако существенно изменяют условия реакции и свойства получаемого продукта. Механизм действия минерализаторов заключается либо в создании центров кристаллизации, либо в изменении скорости кристаллизации (в частности, путём изменения вязкости системы и отвода тепла от неё), либо в изменении кристаллической решётки и, соответственно, свойств кристаллических тел. Реакции в кристаллических смесях широко используются при изготовлении керамических изделий со специфическими свойствами.
Областей применения керамики не меньше, если не больше, чем областей применения полимеров. Керамика – первый искусственный материал, созданный человеком. Уже в каменном веке человек использовал предтечу керамики – глиняную посуду, пока не обожжённую. Первые обожжённые изделия появились в каменном веке – это была посуда, строительные материалы, декоративные и бытовые изделия из фаянса. Расцвет керамики относится к ХХ веку – этот период порой называют веком пластмасс и керамики.
Кроме традиционных направлений керамика используется в транспорте, машиностроении, приборостроении, электротехнике, электронике, энергетике, химической технологии, медицине, обрабатывающих орудиях, текстильной промышленности – трудно найти область техники, где бы сейчас не использовалась керамика.
Термин «техническая керамика» отделяет керамику технического назначения от художественной керамики. Развитие технологии технической керамики вызвало появление керамики специального назначения, так называемой «тонкой технической керамики».
В основу классификации керамики положен признак наличия в ней определённого химического вещества, кристаллическая фаза которого преобладает в этом виде керамики. Область применения керамики является дополнительным признаком, так как одна и та же по своему составу керамика может использоваться в различных областях техники. В самом общем виде техническую керамику можно подразделить на следующие классы: 1) керамика из огнеупорных оксидов; 2) на основе силикатов и алюмосиликатов; 3) на основе двуокиси титана, титанатов, цирконатов и соединений с подобными свойствами; 4) на основе шпинелей; 5) на основе хромитов редкоземельных элементов; 6) на основе тугоплавких бескислородных соединений; 7) композиционные материалы.
5.3.4.1. Традиционная электротехническая керамика.
Электротехническую керамику подразделяют на 4 важнейших категории – магнитную, диэлектрическую, полупроводниковую и проводниковую, в том числе сверхпроводниковую. Все они характеризуются ионным строением кристаллических решёток. Рассмотрим вначале разновидность диэлектрической керамики – фарфоры. Основными компонентами фарфора являются пластичные глины и каолины, представляющие собой водные алюмосиликаты. Химическая формула каолина Аl2O3.2SiO2.H2O. В состав фарфоров входят также кварцевые материалы (SiO2), полевые шпаты (микроклин К2О.Аl2O3.6SiO2), глинозём (Al2O3), кальцит (СаСО3) и др.
Обожжённый фарфор состоит из кристаллов муллита 3Аl2O3.2SiO2 и кварца SiO2, промежутки между которыми заполнены стеклообразным материалом, образовавшимся в основном в результате расплавления полевого шпата.
Электротехнический фарфор содержит примерно 70% SiO2 и 25% Al2O3. Остальное приходится на К2О, Na2O, Fe2O3 и др.
Более высокими диэлектрическими свойствами обладает радиофарфор, стекловидная фаза которого облагорожена введением в неё тяжёлого оксида ВаО.
Дальнейшим усовершенствованием радиофарфора является ультрафарфор. Он содержит увеличенное количество глинозёма Аl2O3 и ВаО. Ультрафарфор используется как высокочастотный диэлектрик вплоть до СВЧ.
Близкой по составу и свойствам к фарфору является стеатитовая керамика. Она в основном состоит из силикатов Мg и изготавливается на основе тальковых минералов 3МgO.4SiO2. Н2О. Рецептура стеатитовой керамики и условия процесса спекания выбирают так, чтобы исключить полиморфные превращения силиката магния. Кроме силиката магния в рецептуру входят минерализаторы ZrO2, ZnO, ВаСО3 и МgСО3, связывающие кремнезём SiO2, выделяющийся в процессе разложения талька при его нагревании.
Свойства фарфоров представлены в таблице 5.4.
Таблица 5.4
Свойства | Электротехнический фарфор | Радиофарфор | Ультрафарфор | Стеатит |
Плотность, кг/м3 | 2500 | 2500 | 2600 | 2600-2800 |
| 6,5 | 6 | 6,3 | 5,5 |
tg.104 | 200 | 2 | 1 | 1,5 |
, Ом.м | 2.1012 | 1016 | 1012 | 1015 |
Епр, МВ/м | 35 | 15 – 20 | 20 – 25 | 20 - 30 |
Отличительной особенностью рассмотренных выше керамических материалов является очень быстрое ухудшение диэлектрических свойств с ростом температуры: возрастание tg, падение .
Все эти материалы имеют положительный коэффициент теплопроводности, лежащий в пределах (3 – 9).10-6К-1.
Относительно высокий ТКЛР и низкий коэффициент теплопроводности 1,2 – 3,5 Вт/м.К обусловливают невысокую стойкость к термоударам. В этом отношении большой интерес представляют керамики на основе чистых оксидов, а также шпинели (двойные оксиды МgO.Al2O3).
Керамика на основе ВеО (брокерит, броммелитовая керамика).
Температура плавления чистого ВеО = 2570 20 оС, энтальпия образования Н = - 616 2,5 кДж/моль. Удельная теплоёмкость возрастает с увеличением температуры от 1,25кДж/кг.К при 100 оС до 2,08 при 900 оС. Твёрдость по Моосу кристаллов ВеО составляет 9, микротвёрдость – 15,2 ГН/м2. Самым удивительным теплофизическим свойством бериллиевой керамики является необычайно высокая теплопроводность = 219 Вт/м.К – во много раз выше теплопроводности остальных видов керамики, превосходящей теплопроводность большинства металлов и уступающей только серебру, меди и алюминию. Это свойство в сочетании с хорошими электрофизическими свойствами ( = 7, tg = 3.10-4, = 1013 Ом.м), высоким коэффициентом замедления и отражения тепловых нейтронов, малым поперечным сечением захвата и большим сечением рассеяния определило области применения этой керамики. Это ядерная энергетика (конструкционный материал, матричный материал для ядерного горючего), металлургия редких металлов (тигли для плавления Ве, Th, Pt, Ti, U и др.), электронная техника (мощные приборы СВЧ, теплоотводы различных радиоэлектронных устройств). Разработана технология прозрачной керамики из ВеО, высокоплотной и, наоборот, с повышенной пористостью (до 82 %).
При работе с ВеО необходимо учитывать её высокую токсичность. Бериллиевые соединения поражают кожу, дыхательные пути, вызывая пневмонию, раздражают желудочно-кишечный тракт и нервную систему. Предельно-допустимая концентрация Ве в воздухе рабочих помещений в виде тех или иных соединений не должна превышать 0,001 мг/м3.
Керамика на основе МgО (периклазовая керамика).
МgО – существует только в одной модификации и кристаллизуется в кубической системе. Тпл= 2800 оС, плотность = 3580 кг/м3, твёрдость – 6 по Моосу, энтальпия образования = - 613 кДж/моль, средняя удельная теплоёмкость изменяется от 0,975 при 100 оС до 1,22 кДж/г.К при 1500 оС.
МgО получают разложением химически чистых соединений Мg(ОН)2, МgСО3 и др. МgО – более основной оксид, чем ВеО, способен взаимодействовать с водой, поэтому для приготовления шихты в качестве связок используют безводные растворы органических соединений – парафин, воск, олеиновую или стеариновую кислоты.
Спекание МgО производят в инертной или окислительной атмосфере при 1700 – 1800 оС. Добавки ZrO2, MnO2, Cr2O3, CaF2, B2O3, TiO2 cнижают температуру спекания.
Теплопроводность периклазовой керамики умеренная – 28 Вт/м.К, но значительно более высокая, чем у фарфоров, поэтому и стойкость к термоударам более высокая. ТКЛР с ростом температуры повышается в диапазоне от 11,7.10-6 до 14,2.10-6. Механические свойства периклазовой керамики достаточно высокие – предел прочности при сжатии сж = 1200 – 1500 МПа, изг в зависимости от технологии изменяется от 130 – 140 до 250 МПа, модуль упругости Е = 2,9.105 МПа.
Периклазовая керамика – хороший диэлектрик, = 8 – 9, v в зависимости от чистоты исходного продукта лежит в интервале от 10-15 до
10-17 Ом.м.
Периклазовая керамика используется как огнеупорная, в тиглях из которой можно с высокой степенью чистоты плавить металлы, которые не восстанавливают МgО, например, Fe, Zn, Al, Sn, Cu, а также тяжёлые редкоземельные металлы. Может использоваться для футеровки высокотемпературных печей и аппаратов, работающих до 2000 оС, для изготовления пирометрических изделий (капилярные трубки, бусы), высокотемпературных изоляторов.
Прозрачная магниевая керамика используется для окон в высокотемпературных печах, устройствах инфракрасного контроля, натриевых лампах, химических реакторах. Однако способность к гидратации, выражающаяся в потемнении полированных поверхностей, летучесть при высокой температуре и сравнительно невысокая механическая прочность несколько ограничивают её использование.
Керамика из оксида алюминия – корундовая керамика.
Оксид алюминия Аl2O3 может существовать в трёх основных кристаллических модификациях - , и , причём - и - формы представляют собой чистые оксиды, а -форма представляет собой условное обозначение группы алюминатов с высоким содержанием Аl2O3. Кроме них, зафиксированы ещё несколько кристаллических модификаций, большинство из которых при 1200 оС переходят в -форму (корунд). Основным структурным мотивом в корунде служит алюмокислородный октаэдр. В природных условиях встречается только -форма в виде минерала корунда, рубина, сапфира. Твёрдость корунда по шкале Мооса – 9, по шкале Роквелла – 90. Плотность корунда в зависимости от наличия в нём примесей колеблется от 3980 до 4010 кг/м3. Температура плавления составляет 2050 оС, энтальпия образования 1,7 МДж/моль.
Именно керамика, содержащая более 95% -Аl2О3 называется корундовой керамикой. В качестве минерализаторов используют МgO, MnO2, TiO2, ZrO2. Наиболее эффективно работает TiO2 , который образует твёрдый раствор с -Аl2О3 и снижает температуру спекания с 1700 – 1750 оС до 1500 –1550 оС, одновременно способствуя интенсивному росту кристаллов корунда.
Добавка МgO, наоборот, задерживает рост кристаллов корунда и обеспечивает высокую плотность, т.к. не происходит образование пор. Мелкокристаллическая структура керамики обеспечивает лучшие механические свойства, такая керамика (микролит, ЦМ 332) используется для изготовления резцов для обработки металлов, деталей для протяжки проволоки, фильеры, нитеводители и другой износостойкий инструмент, а также абразивные материалы – абразивные круги, абразивные шлифовальные шкурки и т.п. Кроме того, такая керамика (поликор) обладает светопроницаемостью в видимой и инфракрасной части спектра, однако, если количество МgO превышает 0,6% (предел образования твёрдого раствора), светопропускание резко падает. Поликор обладает хорошими диэлектрическими свойствами: tg = 3 . 10-5, = 1016 Ом . м, = 10 – 12, Епр = 15 МВ/м. Коэффициент теплопроводности - 32 Вт/м . К, ТКЛР 8 – 8,5 . 10-6 К-1. Поликор обладает высокой стойкостью к термоударам – он выдерживает до 4 теплосмен (800 оС – 20 оС).
Светопроницаемая (прозрачная) керамика применяется в натриевых лампах, для окон устройств инфракрасного контроля, для изготовления подложек СВЧ – микросхем, корпусов микросхем, изоляторов авто- и авиасвечей зажигания, установочных деталей, высокотемпературных реле, вакуумплотных спаев, антенных обтекателей в авиа- и ракетостроении и др.
Пористая корундовая керамика с пористостью до 90% служит хорошим теплоизолирующим материалом при температурах до 1700 – 1750 оС, применяется в качестве деталей костных имплантантов (биокерамика).
Керамика из -Аl2O3 (Na2O . 11Al2O3), благодаря присутствию в ней оксида натрия используется для приготовления твёрдых электролитов. Электросопротивление такой керамики при комнатной температуре составляет 1 – 5 . 102 Ом . см, а при 500 оС – 10 – 25 Ом . см. Такие материалы используют в высокоэффективных химических источниках тока, в частности, в энергоёмких натриево-серных аккумуляторах, перспективных для создания электромобиля.
Другой областью применения керамика из -Аl2O3 – плавленные огнеупоры (в сочетании с корундом) для футеровки стекловаренных печей.
Кварцевая керамика.
Кварцевая керамика – условное название изделий, получаемых методами керамической технологии из порошкообразного стекла с содержанием SiO2 99,5%. Это - единственный керамический материал, основу которого составляет не кристаллическая, а аморфная, стекловидная фаза. Создание кварцевой керамики – вынужденная мера и вызвана большими технологическими трудностями при формовании изделий из кварцевого стекла в связи с большой вязкостью расплава кремнезёма даже при 2000 оС.
Выпускается как плотная, так и пористая кварцевая керамика с пористостью до 80 – 85%. При обжиге, начиная с 1200 оС, начинается процесс кристаллизации кварцевого стекла. Образуется высокотемпературная -форма кристобалита. При охлаждении -форма переходит в низкотемпературную -форму (180 – 270 оС). Это сопровождается уменьшением объёма на 5,2% и, соответственно, повышением истинной плотности с 2210 до 2330 кг/м3.
КЛТР кварцевой керамики (~ 0,5 .10-6 К-1) почти на порядок ниже, чем у других видов оксидной керамики. Это определяет её высокую стойкость к термоударам, хотя её теплопроводность и не высока (0,7 – 1,4 Вт/м. К).
Диэлектрические свойства кварцевой керамики достаточно высоки: = 3 – 3,7; tg = 6 . 10-4.
Кварцевая керамика может длительно эксплуатароваться при температурах до 1200 – 1300 оС. Она используется как теплоизолятор в тепловых агрегатах, труб для подачи расплавленного алюминия, форм для литья металлов, изготовления обтекателей в ракетной и космической технике и др.
6.2.6. Керамика из диоксида циркония ZrO2
ZrO2 – устойчивое соединение, проявляет полиморфизм, существует в трёх модификациях – моноклинной, тетрагональной и кубической. Моноклинная устойчива при низких температурах, при нагревании до 1200 оС переходит в тетрагональную форму, устойчивую только при высоких температурах. Этот переход сопровождается усадкой на 7,7 %. При охлаждении ниже 1000 оС происходит обратный переход с соответствующим изменением объёма и плотности. При температуре от 1900 до 2700 оС устойчивой формой является кубическая. Плотность моноклинной формы 5560 кг/м3, твёрдость по Моосу = 6,5, температура плавления Тпл = 2700 оС. Циклические изменения температуры приводят к разрушению керамики. Для стабилизации кубической модификации создают твёрдые растворы ZrO2 c CaO, MgO, Y2O3 и др. Такой материал называется «стабилизированным диоксидом циркония», однако, он плохо сопротивляется тепловым ударам. Оказалось, что хорошую стойкость к термоударам проявляет материал, сохраняющий в кубической модификации небольшое количество тетрагональной модификации ZrO2. На рис.5.1 представлены кривые изменения ТКЛР различных модификаций.
Свойства изделий из спечённого ZrO2 связаны со степенью стабилизации, видом и количеством введённого стабилизатора. В целом можно сказать, что керамика обладает большой прочностью при нормальных температурах и сохраняют достаточно высокую прочность до 1300 – 1500 оС. Так, сж при 20 оС составляет 2100 МПа, а при 1400 оС – 1300 МПа.
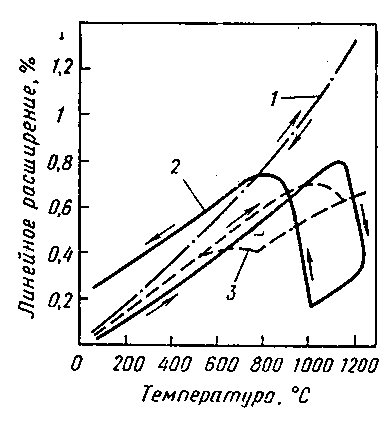
Рис. 5.2. Термическое расширение диоксида циркония.
1 – кубического стабилизированного; 2 – моноклинного нестабилизированного; 3 – частично стабилизированного (стрелками отмечено направление процесса нагревания и охлаждения).
Интересна зависимость теплопроводности циркониевой керамики от температуры. Если у большинства керамик с ростом температуры снижается, то у ZrO2- керамики остаётся практически постоянной.
Диэлектрические свойства диоксида циркония невысоки. Уже при 1000 – 1200 оС он фактически представляет собой проводник. Проводимость имеет ионный характер благодаря образованию кислородных вакансий при замещении ионов Zr+4 двухвалентными и трёхвалентными ионами. Наибольшая проводимость достигается при стабилизации диоксида циркония оксидом скандия Sc2O3.
Циркониевая керамика используется в качестве твёрдых электролитов для работы при высоких температурах, например, в топливных элементах, где температуры достигают 1000 – 1200 оС, в МГД-генераторах, в высокотемпературных нагревателях для разогрева в печах до 2200 оС. В качестве огнеупоров используется при высокотемпературных плавках ряда металлов и сплавов, в частности, Pt, Ti, Rh, Pd, Ru, Zr и др. Благодаря низкой теплопроводности, отличной химической стойкости и большой твёрдости и прочности ZrO2- керамика используется в ракетных, реактивных и других двигателях, в атомном реакторостроении.
6.2.7. Керамика из оксида иттрия Y2O3.
Оксид иттрия до 2300 оС не проявляет полиморфных превращений. Тпл = 2410 – 2415 оС. Плотность кристаллов – 5030 кг/м3, удельная теплоёмкость составляет 0,105 кДж/кг . К, энтальпия образования Н = -1910 кДж/моль, потенциал Гиббса G = -1820 кДж/моль. В окислительной атмосфере (воздух) оксид иттрия стабилен вплоть до Тпл. Стойкость к термоударам спечённой керамики невысока. Это обусловлено малой теплопроводностью (8,5 Вт/м.К) и относительно высоким ТКЛР = 8 – 9 . 10-6 К-1. По электрическим свойствам иттриевая керамика относится к хорошим изоляторам: v при 500 оС составляет 8 . 1010 Ом.м, = 14.
Керамика из Y2O3 c плотностью, близкой к теоретической, является наиболее прозрачной с высоким светопропусканием (до 80 %). Она применяется для изготовления ИК-окон летательных аппаратов, в качестве смотровых окон высокотемпературных печей. Другие области применения – электровакуумная техника, атомная энергетика (контейнерный материал), тигли для восстановления урановых соединений, стабилизационный материал для циркониевой керамики, конструкционный материал и др.
5.3.4.2. Конденсаторная керамика - на основе диоксида титана, титанатов, цирконатов и других соединений с подобными свойствами.
В современной высокочастотной технике успешно применяют керамические конденсаторы, изготавливаемые на основе диоксида титана ТiO2 (рутил). Исходные массы для производства конденсаторной керамики содержат также оксиды других металлов. Меняя соотношение между этими оксидами, регулируют свойства керамики: её диэлектрическую проницаемость e, тангенс угла диэлектрических потерь tgd и др. При спекании ТiO2 с другими оксидами часто протекают химические реакции, приводящие к образованию титанатов. Некоторые титанаты обладают очень большими значениями диэлектрической проницаемости и проявляют сегнетоэлектрическими и пьезоэлектрическими свойствами. Некоторые свойства конденсаторной керамики этого типа представлены в таблицах (5.2 и 5.3).
Таблица 5.2.
Свойства конденсаторной керамики с низкой диэлектрической проницаемостью.
Материал | e | ТКe . 108 | tgd. 106 (1МГц) |
Титанат магния МgTiO3 | 15 | 200 | 1,5 |
Титанат магния и стронция (твёрдый раствор) MgxSr1-xTiO3 | 30 | 100 – 150 | 3 |
Рутил ТiO2 и плавень | 75 | - 750 | 5 |
Рутил ТiO2 + титанат кальция СаТiО3 + плавень | 120 – 160 | -2200 - -3300 | 5 |
Таблица 5.3.
Свойства конденсаторной керамики с высокой диэлектрической проницаемостью.
Материал | e |
Титанат бария и стронция ВахSr1-xTiO3 (твёрдый раствор) + плавень. | 1000 - 2000 |
Титанат бария ВаТО3 + цирконат кальция СаZrO3 + кремнезёмный плавень | 2000 - 3000 |
Титанат бария и церия ВахСе1-хТiO3 (твёрдый раствор) + редкоземельный плавень | 5000 - 6000 |
Титанат бария + цирконат кальция + редкоземельный плавень | 8000 - 10000 |
Вопросы для самопроверки.
1. От чего зависит стойкость керамики к термоударам?
2. Основные стадии технологического процесса производства керамики.
3. Электротехническая керамика – основные представители, области применения.
4. Высокоогнеупорная оксидная керамика.
5. Корундовая керамика – особенности строения, свойства, области применения.
6. Твёрдые электролиты на основе оксидной керамики – основные представители, свойства, области применения.
7. Конденсаторная керамика с низкой и высокой диэлектрической проницаемостью.
- Полупроводниковые материалы.
Полупроводниковые материалы подразделяются на химические элементы и химические соединения. В Периодической системе имеется 12 элементов, обладающих полупроводниковыми свойствами: B, C, Ge, Sn (серое), P, As, Sb, S, Se, Te, I. Техническое значение имеют Si и Ge.
6.1. Элементарные полупроводники.
Кремний по распространённости в земной коре (27 %) занимает второе место после кислорода. Встречается главным образом в виде диоксида кремния SiO2 (кремнезём), а также в виде кремневых кислот – силикатов. В технике Si получают восстановлением кремнезёма углём в присутствии железа в электрических печах. Получаемый таким образом технический кремний содержит 5 – 8 % примесей. Для достижения полупроводниковой чистоты (содержание примесей ниже 10-9 %) технический кремний вначале доводят до химической чистоты путём перевода его в летучее соединение, которое очищают физическими методами (ректификацией) и затем восстанавливают водородом. Дальнейшая очистка проводится кристаллофизическими методами.
В кремнии в качестве донорных примесей вводят элементы V группы Периодической системы элементов: мышьяк As, сурьму Sb, фосфор Р, а в качестве акцепторных примесей – элементы Ш группы: алюминий А1 и бор В. Ширина запрещённой зоны кремния – 1,12 эВ. Это позволяет использовать его до 125 оС.
Кремний – основной материал современного полупроводникового приборостроения. Он применяется для изготовления диодов, триодов, транзисторов, интегральных схем, управляемых вентилей для регулировки токов и наряжений на выходе мощных выпрямителей, туннельных диодов и фотодиодов, фототранзисторов, варикондов (управляемых конденсаторов) и пр.
Германий в противоположность кремнию является редким и рассеянным элементом. Он в незначительных количествах присутствует во многих сульфидных рудах и извлекается главным образом из отходов медного, свинцового, и цинкового производств. Химическая часть производства германия многостадийна и включает последовательные превращения
Ge → GeO2→ GeCl4 → GeO2 → Ge
Химически чистый германий затем подвергается очистке зонной плавкой, после чего вводят легирующие примеси: акцепторные – галлий Ga, индий In или донорные - ванадий V, сурьму Sb. Ширина запрещённой зоны германия – 0,72 эВ, поэтому допустимая рабочая температура германия ниже, чем у кремния и составляет 75 оС.
Долгое время германий был основным полупроводниковым материалом. Первые точечные диоды были изготовлены в 1945 г. из германия. До сих пор из германия изготавливают диоды, триоды и другие традиционные элементы, однако всё в меньшем объёме. В настоящее время германий широко используется в новых приборах – в приборах с гетеропереходами (например, nGe – pGaAs), в транзисторах с оптической связью (рGaAs – nGaAs – pGe), в лавинопролётных приборах и т.д., а также в фотодиодах, фототранзисторах, датчиках Холла.
Сплавы кремния с германием при всех соотношениях имеют структуру твёрдых растворов замещения, т.е. их атомы статистически распределены в узлах кристаллической решётки. Параметры кристаллической решётки плавно изменяются с изменением состава сплава. Эти сплавы проявляют полупроводниковые свойства, причём ширина запрещённой зоны изменяется в зависимости от состава не линейно; подвижность электронов уменьшается при переходе от Ge к Si. Изготовление твёрдых растворов – это один из эффективных путей управления основными свойствами полупроводниковых веществ. Зная фазовую диаграмму состояния системы, можно направленно создавать вещества с заранее заданными свойствами. Например, пусть требуется полупроводник с шириной запрещённой зоны ΔЕ = 1 эВ. Из рис. ХУ видно, что этим значением обладает сплав состава 80 % Si – 20 % Ge. Из фазовой диаграммы состяния системы следует, что кристаллы такого состава можно вырастить из расплава, содержащего 50 % Si.
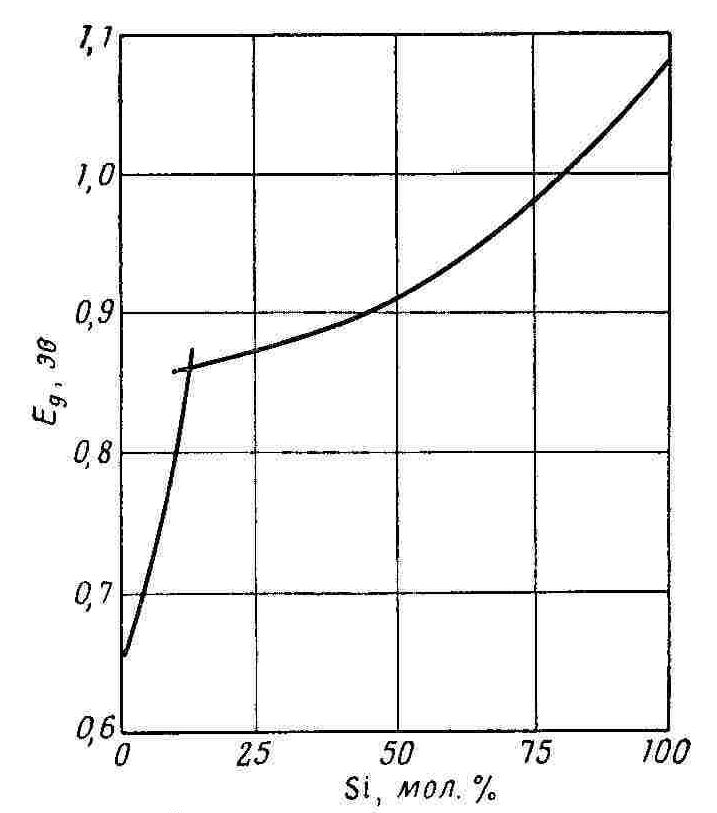
Рис. 6.1. Зависимость ширины запрещённой зоны от состава сплава германий – кремний.
6.2. Полупроводниковые соединения.
Карбид кремния SiC – единственное бинарное соединение элементов ΙV группы Периодической системы элементов. Структура кристаллов SiC аналогична структуре алмаза, а прочность связи Si – C лишь немного меньше прочность связи С – С в алмазе. Этим объясняется высокая твёрдость карбида кремния (9,6 по шкале Мооса), высокая химическая стойкость.
Получают карбид кремния взаимодействием диоксида кремния с углеродом при высоких температурах SiO2 + 3C = SiC + 2CO. Образовавшийся SiC растворяют в расплаве кремния или хрома и выкристаллизовывают. Окончательную очистку проводят путём сублимации при 2400 – 2600 оС, в результате чего образуются кристаллы размером до 20 мм.
В зависимости от количества примесей удельное объёмное сопротивление SiC может изменяться от 1015 до 10-3 Ом.м. SiC – широкозонный полупроводник, ΔЕ = 2,86 эВ, причём температура слабо влияет на ширину запрещённой зоны. Так, при 500 оС ΔЕ = 2,66 эВ. В качестве донорных примесей используются элементы V группы – азот N, фосфор Р, мышьяк Аs, сурьма Sb, висмут Вi, а в качестве акцепторных – элементы ΙΙΙ группы – бор В, алюминийА1, галлий Ga, индий In и элементы ỊỊ группы – кальций Са и магний Мg.
Высокая термическая устойчивость и стойкость к радиации определяют применение карбида кремния в полупроводниковых приборах, работающих в экстремальных условиях, а большая ширина запрещённой зоны позволяет использовать его в качестве люминофора, проявляющего люминесценцию в видимой части спектра.
В карбиде кремния проявляется только электролюминесценция р-n – переходов при энжекции электронов из n-области в р-область, а ловушки создаются примесями атомов N, Al, B, Ga, Be, Sc. В зависимости от вида примеси излучение происходит в красной, жёлтой или зелёной частях спектра.
SiC применяют в качестве светоизлучателей для световых эталонов, опорных источников света в измерительных устройствах, цифровых и знаковых светодиодах, приборах с управляемой геометрией светового поля и т.д.
Полупроводниковые соединения типа АΙΙΙВV. В этой формуле АΙΙΙ – это А1, Ga или In, а ВV – Р, As или Sb. Наибольшее значение имеют GaAs – арсенид галлия, InSb – антимонид индия, GaP – фосфид галлия. Все эти вещества чаще всего получают прямым синтезом из элементов, например, In + Sb = InSb, с последующей очисткой кристаллофизическими методами. Химическая связь в этих соединениях ковалентная с большим вкладом ионности. Ширина запрещённой зоны наибольшая у фосфидов (ΔЕGaP = 2,25 эВ, наименьшая – у антимонидов ( ΔЕInSb = 0,17 эВ). В настоящее время основная область применения этих материалов – оптоэлектроника, т.е. электроника, использующая превращение электрического сигнала в световой или светового в электрический (переход типа электрон – фотон).
К приборам оптоэлектроники относятся инжекционные лазеры, светоизлучающие диоды, СВЧ-генераторы, формирователи и преобразователи изображения, фотокатоды, элементы интегральной оптики и пр.
Антимонид индия InSb – узкозонный полупроводник, акцепторной примесью является Zn, донорными - S, Se, Te. При комнатной температуре все примеси ионизированы и проявляется собственная проводимость. По этой причине InSb не примени м для изготовления традиционных полупроводниковых приборов. Отличительной особенностью антимонида индия является рекордно большая подвижность носителей заряда Un = 80000 см2/В.с. Это определило применение InSb в качестве материала для датчиков Холла. Кроме того, InSb применяется для производства фотосопротивлений, фотодиодов, фотоэлектромагнитных детекторов для ИК-спектра, туннельных диодов (требуется охлаждение жидким азотом).
Арсенид галлия GaAs – среднезонный полупроводник, ΔЕ = 1,43 эВ. Акцепторные примеси Zn, Cd, Cu, донорные - S, Se.. Чаще всего используется для эпитаксиального наращивания на полупроводниковые подложки при изготовлении приборных структур по групповой технологии. Подложками могут служить арсенид галлия другого типа проводимости, германий, селенид цинка и др. Приборы с арсенидом галлия могут работать до 300 оС – выше наступает собственная проводимость. Одно из применений GaAs – инжекционные лазеры, имеющие преимущество в сравнении с диэлектрическими лазерами: работа без охлаждения, высокий КПД, возможность амплитудной модуляции с частотой до 1 ГГц, миниатюрность. Арсенид галлия широко применяется для изготовления светодиодов, тунельных диодов, диодов Ганна, полевых транзисторов, солнечных батарей, мощных выпрямителей.
Фосфид галлия GaP относится к широкозонным полупроводникам, поэтому он применим для изготовления полупроводниковых приборов, работающих при высоких температурах, а также в качестве люминофоров, излучающих в видимой части спектра. Люминофоры на основе GaP являются самыми эффективными. Донорными примесями для GaP служат О, S, Se, Te, Sn, акцепторными - Mg, Zn, Cd, Be, C.
Твёрдые растворы соединений АΙΙΙВV. Полупроводники этой группы часто используются не как индивидуальные соединения, а в виде сплавов со структурой твёрдых растворов замещения. Для этих целей используются соединения, отличающиеся друг от друга природой АΙΙΙ или ВV. Широкое распространение получили такие твёрдые растворы, как арсенид-фосфид галлия GaAsxP1-x, арсенид-антимонид галлия GaAsxSb1-x, арсенид-фосфид индия InAsxP1-x, арсенид галлия-индия GaxI1-xAs, арсенид алюминия-галлия AlxGa1-xAs и др. Основные области применения таких материалов – полупроводниковые приборы с гетеропереходами, фотоумножители, электронно-лучевые трубки.
Халькогенидные полупроводники. К этой группе полупроводников относятся соединения типа АΙΙВV1 и А1VBV1 , где АΙΙ – Zn, Cd, Hg, A1V – Pb+2, BV1 – S, Se, Te.
Химическая связь в этих соединениях имеет ионно-ковалентный характер, причём в рядах AΙΙS → AΙΙ Se → AΙΙ Te и ZnBV1→ CdBV1 → HgBV1 ионность связи уменьшается. Соответственно, уменьшается прочность связи и связанные с ней характеристики: Тпл и ширина запрещённой зоны ΔЕ. Наибольшая ширина запрещённой зоны в этой группе – у сульфида цинка ZnS – 3,7 эВ.
Халькогениды ртути (кроме HgS) и свинца являются узкозонными полупроводниками.
Тип проводимости чаще всего формируется в результате отклонения состава полупроводника от стехиометрического. При избытке металла проявляется электронная проводимость, при избытке халькогенида – дырочная.
Широкозонные полупроводники ZnS, ZnSe, ZnTe, CdS, CdSe обладают фоторезистивным эффектом, фото- и электролюминесценцией. Узкозонные полупроводники применяются для изготовления датчиков Холла, высокочувствительных приёмников излучения, ИК-лазеров.
Вопросы для самопроверки.
1. Почему кремний можно использовать до более высоких температур, чем германий?
2. Какие возможности открываются при изготовлении твёрдых растворов полупроводников?
3. Каковы области применения карбида кремния?
4. Сравните между собой антимонид индия, арсенид галлия и фосфид галлия.